Поверхность. Рентгеновские, синхротронные и нейтронные исследования, 2022, № 6, стр. 103-107
Наплавка на сталь 3Х2В8Ф и 5ХНМ пучком электронов в вакууме насыщающих смесей, содержащих B4C И Al
У. Л. Мишигдоржийн a, *, А. П. Семенов a, **, Н. С. Улаханов a, А. С. Милонов a, Д. Э. Дашеев a
a Институт физического материаловедения Сибирского отделения Российской академии наук
670047 Улан-Удэ, Россия
* E-mail: druh@mail.ru
** E-mail: alexandersemenov2018@mail.ru
Поступила в редакцию 26.06.2021
После доработки 22.07.2021
Принята к публикации 27.07.2021
- EDN: RINVQV
- DOI: 10.31857/S1028096022030153
Аннотация
Рассмотрена модификация поверхностных свойств инструментальных штамповых сталей 3Х2В8Ф и 5ХНМ высокотемпературной обработкой стационарным пучком электронов насыщающих смесей, содержащих карбид бора и алюминий. Металлографический анализ на поперечных шлифах по глубине обработанных сталей показал, что в результате обработки сформированы однородные слои с высокой шероховатостью и без видимых признаков зональности (слоистости) толщиной до ~500 мкм. Модифицированные слои имеют отчетливую границу с основой. Повышение микротвердости от 350 до 1550 HV в приповерхностном слое происходит в результате фазовых (рентгенофазовый анализ выявил наличие фаз Fe2B, Fe3Al, FeAl3, AlB2, AlFe2B2) и структурных превращений (закалки) из жидкого состояния. Развиваются термические напряжения, способствующие фазовому наклепу и пластической деформации. Наблюдаются волновые колебания значений микротвердости по глубине модифицированного слоя. При этом установлено, что максимальная микротвердость после двухкомпонентного (B4C + Al) легирования выше, чем после легирования одним карбидом бора.
ВВЕДЕНИЕ
Успехи в области физики высоких плотностей энергии привели к разработке процессов модификации поверхностных свойств стали и сплавов наплавкой электронным пучком насыщающих [1, 2] или реагирующих [3] смесей. Ускоренный пучок электронов обладает широкими возможностями концентрации энергии в единице объема материала, перевода материала в неравновесное структурно-фазовое [4] нанокристаллическое состояние. Повышенный интерес к методу электронно-лучевой обработки металлов и сплавов обусловлен модификацией их поверхностных свойств [5–8], в частности, износостойкости, окалиностойкости, твердости, коррозионной стойкости и жаростойкости.
В настоящей работе рассматриваются процессы высокоскоростного легирования и модификации поверхностных свойств инструментальных штамповых сталей 3Х2В8Ф и 5ХНМ обработкой в вакууме пучком электронов. Легирование осуществлялось из насыщающих смесей, содержащих бор и алюминий.
МЕТОДИКА ЭКСПЕРИМЕНТА
В экспериментах применялась электронно-лучевая энергоустановка [9], которая укомплектована мощной электронной пушкой ЭПА-60-04.2 [10] с блоком управления БУЭЛ [11] и высоковольтным выпрямителем В-ТПЕ-2-30к-2 УХЛ4 [9].
Источником электронов служит вольфрамовый катод 1 (рис. 1) в форме диска диаметром 15 мм с полусферической эмитирующей поверхностью. На периферии плоского торцевого среза диска установлен кольцевой прямонакальный катод 2. Ток прямого накала составлял 28–30 А. При подаче электрического напряжения до 2 кВ между дисковым и кольцевым катодами диск накаляется до термоэмиссионных температур электронами, испускаемыми прямонакальным кольцевым катодом. Ток электронного накала изменяли до 4 А. Эмитируемые катодом 1 электроны ускоряются электродом 3 (ускоряющее напряжение 20 кВ), проникают в электромагнитную отклоняющую систему 4 и формируются в пучок 5. Электромагнитная отклоняющая система с помощью блока управления электронным пучком обеспечивает фокусировку электронного пучка (диаметр сканирующего электронного пучка ~1–2 мм) на объекте нагрева 6, перемещение пучка по окружности, прямой линии и разверстку в растр. Кроме того, электронный коммутатор, встроенный в блок, легко распределяет мощность нагрева, образуя одновременно несколько областей нагрева, и задает определенное время задержки электронного пучка на каждой из них. Порошки насыщающих смесей (карбид бора B4C, смесь 0.8B4C + 0.2Al) предварительно замешивали на органическом клее (цапонлаке) и наносили в виде пастообразной композиции 7 (рис. 1) толщиной 0.5–1.0 мм на тестовые образцы 6 в форме пластин площадью 2.5–4 см2 и толщиной ~1 см из стали 3Х2В8Ф и 5ХНМ. Нагрев насыщающих смесей (сверхбыстрое плавление насыщающей смеси) осуществляли стационарным пучком электронов с энергией 20 кэВ разверткой в растр по обрабатываемой поверхности с частотой ~50 Гц в течение 20–300 с. Параметры электронного пучка были следующие: ток 20 мА, ускоряющее напряжение 20 кВ и удельная мощность ~5.7 × 102 Вт/мм2. Остаточное давление в вакуумной камере 10–4–10–3 Па.
Рис. 1.
Схема эксперимента: 1, 2 –катоды, 3 – ускоряющий электрод, 4 – электромагнитная фокусирующая и отклоняющая система, 5 – пучок электронов, 6 – образец, 7 – насыщающая смесь.
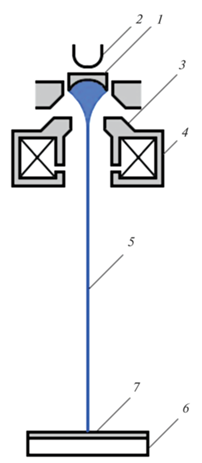
Фазовый состав полученных образцов исследовали на дифрактометре D2 Phaser фирмы Bruker. Анализ морфологии проводили методом растровой электронной микроскопии, элементный состав поверхности образцов определяли методом микрорентгеноспектрального анализа, при этом использовали растровый электронный микроскоп LEO 1430VP с энергодисперсионным анализатором INCA Energy 300 Oxford Instruments. Микроструктуру объектов исследовали с помощью металлографического микроскопа МЕТАМ РВ-21, укомплектованного цифровой камерой VEC-335 с программным комплексом NEXSYS ImageExpert Pro 3.0 для количественного металлографического анализа. Микротвердость сформированных слоев определяли на микротвердомере ПМТ-3 М, укомплектованном цифровой камерой с программой обработки изображений отпечатков NEXSYS ImageExpert MicroHardness 2. Нагрузка составляла 100 г.
РЕЗУЛЬТАТЫ И ОБСУЖДЕНИЕ
Модификацию поверхностных свойств стали 3Х2В8Ф и 5ХНМ бором и алюминием с высокими механическими и теплофизическими свойствами осуществляли расплавлением электронным пучком поверхности стали с легирующими элементами, предварительно нанесенными на обрабатываемый участок в виде пастообразной композиции. При давлении 10–3 Па температура образования боридов железа составляет около 900 К.
На рис. 2 представлена микроструктура поперечных шлифов обработанных сталей и рассмотрено их строение. Поверхность металла нагревается до температуры плавления и переходит в жидкое состояние. Скорость нагрева составляет порядка ~106 К/с. После воздействия электронного пучка поверхность охлаждается со скоростью ~106 К/с. Металлографический анализ показал, что в результате обработки сформированы однородные слои с высокой шероховатостью и без видимых признаков зональности (слоистости). Глубина легированного слоя на стали 3Х2В8Ф составила 320 мкм (B4C) и 600 мкм (0.8B4C + 0.2Al), а на стали 5ХНМ – 650 мкм (B4C) и 760 мкм (0.8B4C + 0.2Al). Слои имеют отчетливую границу с основой. После прекращения воздействия электронным пучком начинается процесс кристаллизации, в результате которого формируется дендритоподобная структура модифицированного слоя. Дендриты растут вдоль отвода тепла перпендикулярно тепловым полям. На поверхности дендритные образования, ориентированы под различными углами.
Рис. 2.
Микроструктура поверхности стали 5ХНМ (а), (б) и 3Х2В8Ф (в), (г): (а), (в) – наплавка B4C, (б), (г) – наплавка 0.8B4C + 0.2Al.
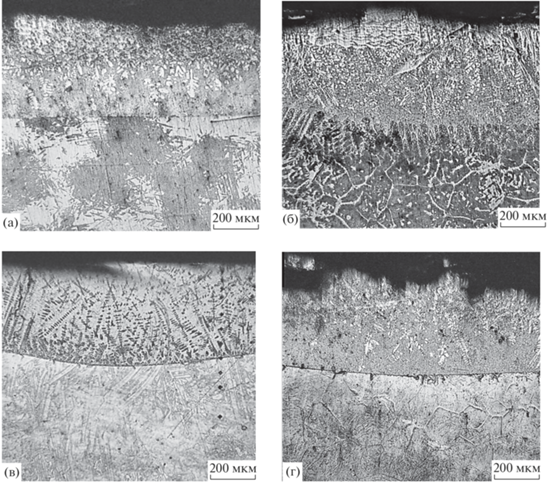
Распределение микротвердости на поперечных шлифах по глубине обработанных сталей представлены на рис. 3 и 4. Видно, на стали 3Х2В8Ф максимальная микротвердость после обработки насыщающей смеси состава B4C составила 900 HV, после обработки насыщающей смеси состава 0.8B4C + 0.2Al – 1550 HV. На стали 5ХНМ значения соотносятся как 1000 HV к 1100 HV соответственно. Микротвердость основного металла составляет 650–750 HV на стали 3Х2В8Ф и 350–400 HV на стали 5ХНМ. Наблюдается немонотонный характер [4] распределения микротвердости по глубине модифицированного слоя на поверхности стали. Повышение микротвердости в приповерхностном слое происходит в результате фазовых (рентгенофазовый анализ выявил наличие фаз Fe2B, Fe3Al, FeAl3, AlB2, AlFe2B2) и структурных превращений (закалки) из жидкого состояния. Развиваются термические напряжения, способствующие фазовому наклепу и пластической деформации [4]. Следующий слой повышенной микротвердости (рис. 3 и 4) образуется в результате закалки от высоких температур из области расплава. Области пониженной микротвердости являются структурами отпуска. Наблюдаемые волновые колебания значений микротвердости по глубине модифицированного слоя поверхности свидетельствуют о сложном структурно-фазовом состоянии. Необходимо отметить, что микротвердость после двухкомпонентного (B4C + Al) легирования выше, чем после легирования одним карбидом бора. Вероятно, это связано с образованием твердых содержащих алюминий фаз FeAl3, AlB2, AlFe2B2.
Рис. 3.
Распределение микротвердости по глубине на поверхности стали 3Х2В8Ф: 1 – наплавка B4C, 2 – наплавка 0.8B4C + 0.2Al.
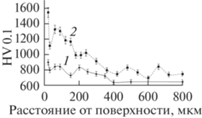
Рис. 4.
Распределение микротвердости по глубине на поверхности стали 5ХНМ: 1 – наплавка B4C, 2 – наплавка 0.8B4C + 0.2Al.
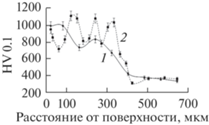
Микротвердость в слое и в основном металле на стали 3Х2В8Ф выше, чем на стали 5ХНМ. Это связано с влиянием легирующих элементов присутствующих в сталях. Известно, что встали 3Х2В8Ф содержится до 10% вольфрама в виде карбидов, что обуславливает ее высокие механические характеристики, в том числе микротвердость.
Модификация поверхностных свойств наплавкой насыщающих смесей электронным пучком способствует проявлению более пластичных свойств у сформированных слоев (в сравнении со слоями, полученными традиционной химико-термической обработкой [5]). Кроме того, поверхность стали после обработки электронным пучком имеет гетерогенную структуру, сочетающую твердые (хрупкие) и более пластичные структурные составляющие. Такое сочетание отчасти объясняет отсутствие термических трещин при нагреве поверхности стали до высоких температур ~2000 К. Нагрев до указанной температуры неминуемо приводит к оплавлению поверхности исследуемых сталей вместе с нанесенной пастой. В результате последующей кристаллизации формируется дендритная структура (преимущественно в верхних частях слоев). В работе [12] авторы объяснили морфологию и строение слоев с помощью фазовой диаграммы Fe–B, где каждую зону слоя рассматривали как сплав определенного состава. В случае со сложнолегированными сталями данный подход может быть использован частично или исключен полностью в связи с высоким содержанием легирующих компонентов. Возникает необходимость исследования тройных и четвертных фазовых диаграмм. Механизм формирования слоев на сталях 3Х2В8Ф и 5ХНМ еще предстоит исследовать.
ЗАКЛЮЧЕНИЕ
Применение высококонцентрированного источника энергии позволяет сравнительно быстро передавать энергию электронного пучка при его воздействии на поверхность обрабатываемого металла или сплава, нагревать зону контакта до высоких температур. Это способствует увеличению диффузии бора из насыщающей обмазки по поверхности и проникновению его в объем металла, взаимодействию и образованию бороалитированных слоев. Электронно-лучевое легирование карбидом бора и алюминием привело к формированию модифицированных слоев с преимущественным дендритным строением. Добавка алюминия к насыщающей композиции способствует увеличению толщины покрытия (на стали 3Х2В8Ф с 320 мкм до 600 мкм и на 5ХНМ с 650 мкм до 760 мкм) и повышению микротвердости (на стали 3Х2В8Ф с 900 HV до 1550 HV и на 5ХНМ с 1000 HV до 1100 HV) поверхности исследуемых сталей. Установлено, что микротвердость в слое и в основном металле на стали 3Х2В8Ф выше, чем на стали 5ХНМ за счет более высокого содержания карбидов в первой. Электронно-лучевая наплавка B4C + Al насыщающих смесей может использоваться для упрочнения режущих инструментов, испытывающих разогрев в процессе работы до высоких температур без существенного снижения эксплуатационных свойств.
Список литературы
Mishigdorzhiyn U.L., Ulakhanov N.S., Milonov A.S., Semenov A.P. // IOP CONF. SER. MATER. SCI. ENG. 2020. V. 759. № 012017. https://doi.org/10.1088/1757-899X/759/1/012017
Корнилов С.Ю., Ремпе Н.Г., Смирнягина Н.Н. // Физика и химия обработки материалов. 2017. № 5. С. 26.
Dasheev D.E., Smirnyagina N.N., Khaltanova V.M., Semenov A.P. // J. Physics: Conference Series. 2015. V. 652. № 012002. https://doi.org/10.1088/1742-6596/652/1/012002
Итин В.И., Коваль Н.Н., Месяц Г.А., Ротштейн В.П., Чухланцева И.С., Щанин П.М. Источники электронов с плазменным эмиттером. Новосибирск: Наука, 1983. С. 104.
Сизов И.Г., Смирнягина Н.Н., Семенов А.П. // Металловедение и термическая обработка металлов. 1999. № 12. С. 8.
Смирнягина Н.Н., Сизов И.Г., Семенов А.П., Ванданов А.Г. // Физика и химия обработки материалов. 2001. № 2. С. 63.
Смирнягина Н.Н., Сизов И.Г., Семенов А.П. // Неорганические материалы. 2002. Т. 38. №. 1. С. 48.
Новакова А.А., Сизов И.Г., Гвоздовер Р.С., Голубок Д.С., Киселева Т.Ю., Семенов А.П., Смирнягина Н.Н., Прусаков Б.А. // Поверхность. Рентген., синхротр, и нейтрон. исслед. 2003. № 3. С. 99.
Григорьев Ю.В., Семенов А.П., Нархинов В.П., Гырылов Е.И., Дружинин В.В., Кириллов Э.А., Смирнягина Н.Н. Комплексное использование минерального сырья Забайкалья. Улан-Удэ: Изд-во Бурятского научного центра СО РАН, 1992. С. 139.
Григорьев Ю.В., Карлов В.И., Мурашов А.С., Федоров В.И. // Приборы и техника эксперимента. 1989. № 2. С. 228.
Григорьев Ю.В., Петров Ю.Г., Позднов В.И. // Приборы и техника эксперимента. 1990. № 2. С. 236.
Мишигдоржийн У.Л., Сизов И.Г., Полянский И.П. // Обработка металлов (технология, оборудование, инструменты). 2018. Т. 20. № 2. С. 87
Дополнительные материалы отсутствуют.
Инструменты
Поверхность. Рентгеновские, синхротронные и нейтронные исследования