Поверхность. Рентгеновские, синхротронные и нейтронные исследования, 2022, № 7, стр. 51-56
Измерение индекса кристалличности высокочистого кварца на различных этапах обогащения и исследование его структуры методами рентгеноструктурного анализа и дифракции обратно рассеянных электронов
М. Д. Зимин a, *, А. П. Жабоедов a, С. С. Колесников b, А. И. Непомнящих a
a Институт геохимии им. А.П. Виноградова Сибирского отделения Российской Академии Наук
664033 Иркутск, Россия
b Иркутский национальный исследовательский технический университет
664074 Иркутск, Россия
* E-mail: zima.dom@mail.ru
Поступила в редакцию 12.08.2021
После доработки 14.10.2021
Принята к публикации 14.10.2021
- EDN: WKHOTO
- DOI: 10.31857/S1028096022070196
Аннотация
Методами рентгеноструктурного анализа и дифракции обратно рассеянных электронов исследована структура высокочистого природного кварца (суперкварцита). Установлено изменение индекса кристалличности, полученного по методике Мураты и Нормана, и примесного химического состава суперкварцита на различных технологических этапах обогащения: термодробления, ситования, химического травления, высокотемпературной прокалки. Обнаружено, что обогащение кварца при травлении смесью соляной и плавиковой кислот повышает индекс кристалличности на всех этапах, кроме предварительного термодробления и высокотемпературной прокалки (при 1300 и 1400°С). Максимального значения индекса кристалличности кварца достигают на первом этапе химического травления. Наибольшее очищение от примесей также происходит на первом этапе химического травления. Методом дифракции обратно рассеянных электронов обнаружены области повышенной локальной разориентации кристаллитов, которые сосредоточены на границах зерен, “малоугловых” границах (с углом разориентации менее 7°) и областях с повышенным содержанием флюидных включений, которые возможно наблюдать в оптическом микроскопе. “Ориентационная карта” и карта областей локальной разориентации кристаллитов были построены и проанализированы с помощью набора инструментов программного обеспечения MTEX для MATLAB. Определено, что макродефекты, имеющие дислокационную природу, обуславливают изменения индекса кристалличности.
ВВЕДЕНИЕ
Индекс кристалличности, полученный методом рентгеноструктурного анализа, широко используется для оценки структурного совершенства различных минералов (каолинита, слюды, кварца) и кристаллической фазы целлюлозы [1–11]. В случае кварца он применяется при исследовании кварцсодержащих пород, пыли и материалов как для чисто геологических задач, так и для технологической оценки кварцевого сырья [4–11]. Методически он является количественной оценкой степени уширения рефлексов квинтуплета 212, 203, 031 в диапазоне брэгговских углов 67°–69°, подобранного эмпирически Муратой и Норманом при изучении различных кварцсодержащих пород методом порошковой рентгеновской дифракции [4]. С помощью рентгеновской дифракции можно исследовать различные параметры кварцевых материалов: определить постоянные элементарной ячейки, рассчитать микронапряжения и плотность дислокаций (требуется гораздо больше времени на одно измерение [5–7, 12]), уширение рефлексов по Гауссу и Коши, область когерентного рассеяния (среднего размера кристаллитов) [5, 8, 12], измерить полуширину рефлексов 101, 110 [6, 9].
Физический механизм уширения линий дифракции рентгеновских лучей может варьироваться в зависимости от типоморфизма породы и различных этапов технологической обработки. Вклад в уширение могут давать размеры, ориентация и деформация зерен, плотность дислокаций, количество структурных примесей Al, Ti, OH-групп, щелочных металлов. Установить вклад каждого из перечисленных факторов в отдельности, применяя метод индекса кристалличности, – сложная задача. Поэтому оценка индекса кристалличности используется как вспомогательный метод [6] для исследования групп месторождений одного генезиса [10].
Суперкварциты являются нетрадиционным сырьем для высокочистых кварцевых концентратов и кварцевых стекол. Суммарное количество основных примесей в кварцевом концентрате из суперкварцитов менее 20 мд. Поэтому кварц из суперкварцитов содержит минимальное количество дефектов, связанных со структурными примесями, в сравнении с другими кварцевыми породами [13].
Для получения кварцевых концентратов из высокочистого кварца требуется проведение технологической обработки и обогащения в несколько этапов, таких как травление смесью растворов соляной и плавиковой кислот, высокотемпературная прокалка и высокотемпературное хлорирование [14]. Влияние данных процессов на индекс кристалличности кварца не исследовано. Известно, что при продолжительном истирании во время пробоподготовки перед измерениями индекс кристалличности образцов уменьшается. При выщелачивании в водном растворе Na(OH) кварцевого сырья наблюдается увеличение индекса кристалличности [6]. Но в этих работах было исследовано сырье для производства цемента, технологические требования к которому во много раз меньше, чем к высокочистому кварцу, и основной интерес представляла щелочная реакционная способность кварца.
Несмотря на относительно широкое использование индекса кристалличности и описание его связи с микронапряжениями, плотностью дислокаций и дефектами структуры, в литературе не продемонстрирована его связь с конкретными дефектами в структуре, кроме петрографического описания изображений шлифов кварцсодержащих пород в оптическом микроскопе и различного анализа данных порошковой рентгеновской дифракции [5–7].
Настоящая работа посвящена изучению индекса кристалличности высокочистого кварца из суперкварцитов при химическом травлении и высокотемпературной прокалке с целью связать его величину с конкретными дефектами структуры.
МЕТОДИКА И ЭКСПЕРИМЕНТАЛЬНАЯ ЧАСТЬ
Предварительная подготовка высокочистого кварца из суперкварцитов заключалась в дроблении породы до выделения фракции с кристаллитами размером менее 25 мм. Индекс кристалличности был измерен на следующих этапах технологической подготовки высокочистого кварца: термодробления в дистиллированной воде после нагрева в муфельной печи до 900°С в течение 30 мин, выделения фракции с кристаллитами размером 100–300 мкм с отсеиванием кристаллитов меньшего размера, химического травления в смеси растворов кислот 20% HCl : 10% HF в соотношении 3 : 1 (массовое соотношение жидкого к твердому 2 : 1) при 60°С в течение 2 ч, прокалки при температурах 1300 или 1400°С в течение 2 ч в чашке из кварцевого стекла. Если высокотемпературная прокалка происходила после химического травления, то проводили повторное химическое травление.
Дифрактограммы были получены на порошковом дифрактометре Bruker D8 ADVANCE. Условия съемки: излучение СuKα (зеркало Геббеля), U = 40 кВ, I = 40 мA, пределы измерений по 2θ 67°–69°, шаг 0.01°, время экспозиции 5 с. На основании полученных данных был рассчитан индекс кристалличности по методике Мураты и Нормана:
(1)
${\text{Индекс\;кристалличности}} = {{10aF} \mathord{\left/ {\vphantom {{10aF} {b,}}} \right. \kern-0em} {b,}}$Рис. 1.
Параметры для измерения индекса кристалличности по методике Мураты и Нормана по формуле (1).
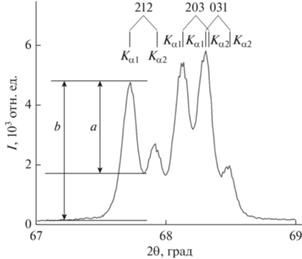
Концентрация примесей была определена в индуктивно-связанной плазме на масс-спектрометре Perkin Elmer NexION 300D. Метод основан на предварительном концентрировании примесей путем удаления основного элемента – кремния в виде тетрафторида, получении из раствора в азотной кислоте и последующем измерении интенсивности ионного тока (количества импульсов в единицу времени), возникающего при ионизации полученного раствора в индуктивно-связанной плазме масс-спектрометра [15].
Картирование поверхности суперкварцита методом дифракции обратно рассеянных электронов осуществлено в растровом электронном микроскопе Oxford Instruments JEOL JIB-Z4500. Шаг сканирования 2 мкм. Образец представлял собой полированную пластинку толщиной 0.5 мм без предварительного напыления, но с однородными следовыми количествами электропроводящего углеродного скотча на поверхности. Участки изображения, которые не идентифицировались как кварц, были экстраполированы по соседним значениям с помощью программного обеспечения HKL Channel 5. “Ориентационная карта” и карта областей локальной разориентации кристаллитов были построены и проанализированы с помощью набора инструментов программного обеспечения MTEX для MATLAB [16]. Локальная разориентация кристаллитов была рассчитана по формуле:
(2)
$\begin{gathered} ~{\text{Локальная\;разориентаци}}{{{\text{я}}}_{{i,j}}} = \\ = \frac{1}{{\left| {N\left( {i,j} \right)} \right|}}\mathop \sum \limits_{\left( {k,l} \right){\kern 1pt} \in {\kern 1pt} N\left( {i,j} \right)} \omega \left( {{{o}_{{i,j}}},{{o}_{{k,l}}}} \right), \\ \end{gathered} $Оптические изображения пластинки были получены с помощью микроскопа Olympus BX51.
РЕЗУЛЬТАТЫ И ИХ ОБСУЖДЕНИЕ
Изменение индекса кристалличности на различных этапах технологической подготовки изображено на рис. 2. На этапе термодробления изменение индекса кристалличности не обнаружено. На этапе выделения фракции с кристаллитами размером 100–300 мкм индекс кристалличности уменьшается, в том числе и при отсеве частиц размером менее 100 мкм, но на величину, близкую к границе погрешности измерений. Это можно объяснить появлением пылевидных частиц. Отсутствие изменения индекса кристалличности при выделении различных фракций показывает, что микронные размеры зерен не влияют на уширение линий рентгеновской дифракции. На первом этапе химического травления смесью кислот индекс кристалличности достигает максимального значения, что говорит о его чувствительности как к поверхностным дефектам, так и к наиболее растворимым кислотой областям. При последующей высокотемпературной прокалке индекс кристалличности уменьшается: при температуре 1400°С до исходного значения, при температуре 1300°С – в меньшей степени (рис. 2).
Рис. 2.
Индекс кристалличности фракции кварца с размерами кристаллитов 100–300 мкм (1) на различных этапах технологического обогащения: без термодробления (а) и после него (б) (X – химическое травление; 1300, 1400 – температура прокалки в °C). Для сравнения приведены индексы кристалличности фракций с зернами размером менее 100 (2) и 300 мкм (3).
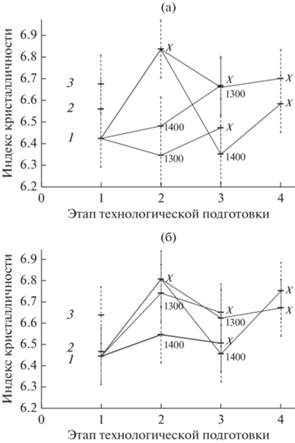
При температуре, близкой к 1400°С, наблюдается фазовый переход кварца в кристобалит. Трансформация начинается с поверхности, что может обуславливать уширение линий дифракции. Ранее было изучено изменение области когерентного рассеяния вблизи плоскости (101) при фазовом переходе кварца в кристобалит [17]. Авторы установили, что в начале фазового перехода в порошках с бóльшим средним размером зерен область когерентного рассеяния увеличивалась. Повторное химическое травление после высокотемпературного отжига снова увеличивает индекс кристалличности, но уже в меньшей степени, чем при первом химическом травлении. При высокотемпературной прокалке без термодробления и предварительного травления индекс кристалличности практически не меняется, но незначительно увеличивается при последующем химическом травлении. При высокотемпературной прокалке с термодроблением, но без предварительного травления, индекс кристалличности увеличивается, что является исключением в рамках данного эксперимента. При последующем травлении также не наблюдается его изменение. Это означает, что продолжительная термическая обработка может нивелировать влияние химического травления кислотами на индекс кристалличности.
В настоящей работе на каждом этапе технологической подготовки с прокалкой при 1400°С был определен примесный состав образцов (табл. 1). Самое большое количество примесей сконцентрировано во фракции с размером кристаллитов менее 100 мкм, что объясняется отсеиванием минеральных примесей (в основном серицита KAl2(AlSi3O10)(OH)2, в котором сосредоточена большая часть примесей K и Al) [18]. Высокотемпературная прокалка почти не влияет на примесный состав, кроме небольшого увеличения концентрации Ca и Al, которые, вероятно, попадают в кварц из огнеупорного материала печи. Химическое травление заметно снижает суммарное количество примесей, особенно при повторном травлении, до менее 20 мд. Между этапами высокотемпературной прокалки как с термодроблением, так и без него, несмотря на разницу индексов кристалличности, не обнаружено изменений в составе примесей. Это означает, что чувствительности метода оценки индекса кристалличности недостаточно для анализа примесей, которые могут изоморфно встраиваться в структуру кварца при нагреве. Ранее было отмечено увеличение индекса кристалличности при нагреве пород кремния и агата до 600°С, которое авторы [19] связывали с процессом перекристаллизации. Незначительное уменьшение концентрации Na на последних этапах химического травления было объяснено растворением областей с повышенным содержанием флюидных включений, в которых концентрируется Na [20].
Таблица 1.
Количество химических примесей после различных технологических этапов
Этапы | Элемент | фр. 300 мкм | фр. 100 мкм | фр. 100–300 мкм | 1400°С | 1400°С, Х | Х | Х, 1400°С | Х, 1400°С, Х |
---|---|---|---|---|---|---|---|---|---|
Количество вещества, мд | |||||||||
a | Al | 111 | 185 | 86.3 | 90.4 | 7.4 | 14.1 | 16.8 | 8.1 |
Ti | 3.2 | 4.1 | 2.5 | 3.0 | 1.1 | 2.0 | 2.0 | 1.6 | |
Na | 8.0 | 9.2 | 8.2 | 7.3 | 1.5 | 5.6 | 4.5 | 3.0 | |
K | 42.8 | 73.2 | 31.7 | 28.0 | 2.3 | 3.6 | 3.3 | 1.5 | |
Mg | 5.7 | 8.7 | 4.3 | 4.2 | 1.0 | 1.5 | 1.6 | 0.9 | |
Li | 0.32 | 0.27 | 0.30 | 0.84 | 0.74 | 0.27 | 0.60 | 0.58 | |
Fe | 2.9 | 6.6 | 1.7 | 2.0 | 1.0 | 0.4 | 0.4 | 0.3 | |
Ca | 2.7 | 7.6 | 1.7 | 1.8 | 4.6 | 2.0 | 2.6 | 2.4 | |
Σ | 176.2 | 294.4 | 136.7 | 137.6 | 19.7 | 29.4 | 31.8 | 18.4 | |
б | Al | 96.1 | 164 | 74.3 | 75.6 | 7.6 | 7.5 | 7.6 | 6.3 |
Ti | 1.8 | 3.0 | 1.7 | 1.7 | 1.6 | 1.1 | 1.2 | 0.9 | |
Na | 8.0 | 8.9 | 6.6 | 7.5 | 1.6 | 4.8 | 3.9 | 3.0 | |
K | 34.9 | 67.7 | 29.7 | 27.5 | 2.3 | 1.8 | 1.6 | 1.3 | |
Mg | 4.3 | 6.7 | 3.6 | 4.0 | 1.1 | 0.6 | 0.6 | 0.4 | |
Li | 0.31 | 0.30 | 0.29 | 0.73 | 0.68 | 0.29 | 0.50 | 0.55 | |
Fe | 2.1 | 4.5 | 1.5 | 2.0 | 0.8 | 0.2 | 0.3 | 0.2 | |
Ca | 2.6 | 4.9 | 2.2 | 2.4 | 4.3 | 1.9 | 3.3 | 3.0 | |
Σ | 150.1 | 259.8 | 119.8 | 121.4 | 20.0 | 18.2 | 18.9 | 15.6 |
Изображение суперкварцита, полученное в растровом электронном микроскопе (рис. 3), демонстрирует концентрацию локально разориентированных областей (рис. 3б) на границах и внутри зерен: на “малоугловых” границах с углом разориентации менее 7° (области 1 и 2), которые определяют по контрасту изображения на “карте областей ориентации” (рис. 3а), и в областях с повышенным содержанием флюидных включений (области 3–5). Флюидные включения, вероятно, захватываются при “залечивании” трещин в процессе метаморфизма. Скорее всего, эти макродефекты отвечают, в первую очередь, за величину индекса кристалличности кварца, так как растворение кварца при кислотном травлении происходит вдоль зерен и межзеренных “малоугловых” границ. Связь индекса кристалличности с этими макродефектами также объясняет его увеличение при щелочном травлении, описанное в работе Маринони и Брукманса [6]. В работе Ресслера и соавторов [21] показано, что растворение кварца при травлении гидроксидом натрия (pH 13.5) происходит вдоль зерна кварца и межзеренных границ. Поскольку природа образования “малоугловых” границ и большинства “высокоугловых” границ дислокационная, существует взаимосвязь индекса кристалличности с плотностью дислокаций.
ВЫВОДЫ
Показано, что химическое травление кварца смесью соляной и плавиковой кислот повышает индекс кристалличности на всех технологических этапах получения высокочистого кварцевого концентрата, кроме предварительной высокотемпературной прокалки после термодробления. Это может быть объяснено началом фазового перехода кварц–кристобалит. В процессе химического травления происходит очищение кварца как от минеральных, так и флюидных включений. Наибольшие области локальной разориентации кристаллитов в исходных суперкварцитах сосредоточены на границах зерен, “малоугловых” границах и участках с повышенной концентрацией флюидных включений. Увеличение индекса кристалличности в процессе химического травления можно объяснить более быстрым растворением кварца в областях с повышенной локальной разориентацией кристаллитов.
Список литературы
Aparicio P., Galan E. // Clays and Clay Minerals. 1999. V. 47. № 1. P. 12. https://doi.org/10.1346/CCMN.1999.0470102
Guggenheim S., Bain D.C., Bergaya F. et al. // Clays and Clay Minerals. 2002. V. 50. № 3. P. 406. https://doi.org./10.1346/000986002760833783
Park S., Baker J.O., Himmel M.E., Parilla P.A., Johnson D.K. // Biotechnol. Biofuels. 2010. V. 3. № 1. P. 1. https://doi.org./10.1186/1754-6834-3-10
Murata K.J., Norman M.B. // Amer. J. Sci. 1976. V. 276. № 9. P. 1120. https://doi.org/10.2475/ajs.276.9.1120
Садовничий Р.В., Михайлина А.А., Рожкова Н.Н., Инина И.С. // Тр. КарНЦ РАН. 2016. № 2. С. 73. https://doi.org/10.17076/geo126
Marinoni N., Broekmans M.A. // Cement and Concrete Res. 2013. V. 54. P. 215. https://doi.org./10.1016/j.cemconres.2013.08.007
Sharib Ahmed S.A.A. Abu, Abukhadra M.R. // Silicon. 2021. V. 13. № 3. P. 653. https://doi.org./10.1007/s12633-020-00458-6
Песков А.В., Алекина Е.В., Тарасова Е.Ю. // Успехи современного естествознания. 2020. № 11. С. 95. https://doi.org./10.17513/use.37521
Takagi H., Takahashi K., Shimada K., Tsutsui K., Miura R., Kato N., Takizawa S. // J. Struct. Geol. 2012. V. 35. P. 64. https://doi.org/10.1016/j.jsg.2011.11.008
Жабоедов А.П., Зимин М.Д., Непомнящих А.И., Сапожников А.Н. // Обогащение руд. 2020. № 1. С. 36. https://doi.org./10.17580/or.2020.01.07
Nagashima K., Tada R., Tani A., Toyoda S., Sun Y., Isozaki Y. // Geochem. Geophys. Geosystems. 2007. V. 8. № 2. https://doi.org./10.1029/2006GC001364
Meftah N., Mahboub M.S. // Silicon. 2020. V. 12. № 1. P. 147. https://doi.org./10.1007/s12633-019-00109-5
Федоров А.М., Макрыгина В.А., Непомнящих А.И., Елисеев И.А. // География и природные ресурсы. 2016. № 6. С. 55. https://doi.org/10.21782/GIPR0206-1619-2016-6(55-59)
Haus R., Prinz S., Priess C. // Quartz: Deposits, Mineralogy and Analytics. 2012. P. 29. https://doi.org./10.1007/978-3-642-22161-3_2
Непомнящих А.И., Волкова М.Г., Жабоедов А.П. и др. // Физика и химия стекла. 2018. Т. 44. № 2. С. 130. https://doi.org./10.1134/S1087659618020128
Bachmann F., Hielscher R., Schaeben H. // Solid State Phenomena. 2010. V. 160. P. 63. https://doi.org./10.4028/www.scientific.net/SSP.160.63
Pagliari L., Dapiaggi M., Pavese A., Francescon F. // J. Eur. Ceram. Soc. 2013. V. 33. № 15–16. P. 3403. https://doi.org./10.1016/j.jeurceramsoc.2013.06.014
Федоров А. М., Макрыгина В.А., Будяк А.Е., Непомнящих А.И. // Докл. акад. наук. 2012. Т. 442. № 2. С. 244. https://doi.org/10.1134/S1028334X12010126
Domanski M., Webb J.A. // J. Archaeolog. Sci. 1992. V. 19. № 6. P. 601. https://doi.org/10.1016/0305-4403(92)90031-W
Волкова М.Г., Непомнящих А.И., Федоров А.М., Махлянова А.М., Брянский Н.В. // Геология и геофизика. 2017. Т. 58. № 9. С. 1324. https://doi.org./10.15372/GiG20170905
Rößler C., Möser B., Giebson C., Ludwig H.M. // Cement and Concrete Res. 2017. V. 95. P. 47. https://doi.org./10.1016/j.cemconres.2017.02.015
Дополнительные материалы отсутствуют.
Инструменты
Поверхность. Рентгеновские, синхротронные и нейтронные исследования