Поверхность. Рентгеновские, синхротронные и нейтронные исследования, 2022, № 8, стр. 80-86
Анализ смачивания и диффузионных процессов при контактном сплавлении припоев Zn–Cu–Al и Mg–Al со сплавом АМг3
И. В. Шутов a, b, *, Л. В. Камаева a, c, **, Е. А. Баталова b, c, М. Н. Королев b, М. Д. Кривилев a, b
a Удмуртский федеральный исследовательский центр УрОРАН
426067 Ижевск, Россия
b Удмуртский государственный университет
426034 Ижевск, Россия
c Институт физики высоких давлений им. Л. Ф. Верещагина РАН
108840 Троицк, Россия
* E-mail: shutiny@gmail.com
** E-mail: lara_kam@mail.ru
Поступила в редакцию 24.12.2021
После доработки 27.01.2022
Принята к публикации 30.01.2022
- EDN: SEQBXO
- DOI: 10.31857/S1028096022080167
Аннотация
Изучены процессы контактного плавления сплава АМг3 с твердыми припоями Zn–Cu–Al и Mg–Al. Получены микроструктуры шлифов сплавов после термических испытаний, исследованы процессы плавления и кристаллизации сплавов АМг3, Zn–Cu–Al и Mg–Al и определены температуры их фазовых переходов. Изучены процессы поверхностной эрозии подложки АМг3 в процессе контактного плавления подложки с припоями Zn–Cu–Al и Mg–Al. Проведенные исследования показали, что интенсивные диффузионные процессы, проходящие на границе припоя и подложки, приводят к глубокому плавлению подложки как при наличии оксидной пленки (для HTS-2000), так и при ее отсутствии (Mg66Al34). Контактное плавление припоев ведет к диффузионным эффектам в области соприкосновения, что способствует формированию комплексных микроструктур, состоящих из эвтектик, интерметаллидов и дендритов α-Al. Полученные результаты показывают возможность управления микроструктурой и свойствами зоны сплавления за счет выбора химического состава припоя и режимов термической обработки, а также выбора оптимального флюса. Экспериментальные данные свидетельствуют, что формирование интерметаллидных фаз без образования эвтектических структур охрупчивает зону паяного соединения. По этой причине важно выбрать оптимальный состав припоя и условия кристаллизации, при которых будет образовываться мелкодисперсная эвтектическая микроструктура.
ВВЕДЕНИЕ
Сплавы на основе системы Al–Mg–Mn, соответствующие марке АМг, широко используются в отечественном машиностроении, поскольку обладают высокими прочностными характеристиками и коррозионной стойкостью, хорошо поддаются формовке, не теряя при этом своих механических свойств [1]. Сплавы АМг широко используются в авиастроении и космической технике благодаря малому весу, высокому для Al-сплавов пределу текучести и трещиностойкости при вибрационных механических нагрузках [2, 3]. Марка АМг хорошо поддается сварке в защитной атмосфере в полуавтоматическом или автоматическом режиме. При этом структура сварного шва однородна, что обеспечивает конструкционную прочность всего изделия.
В ряде технических задач требуется получить металлургическое соединение тонкостенных (c толщиной менее 1 мм) Al-конструкций, где электродуговая сварка неприменима. Альтернативным способом является пайка твердым припоем (ПТП) в контролируемой атмосфере или в вакууме [4]. При этом возникает целый ряд физических проблем, включая нижеперечисленные: 1. Присутствие магния значительно повышает склонность к окислению расплава, что требует использования либо высокого вакуума, либо очищенной газовой атмосферы [5]. 2. При раскислении поверхности могут формироваться фториды магния, повышающие хрупкость металла. 3. Пайка реализуется при достижении условий смачивания, в основе которого лежат поверхностные реакции взаимодействия припоя с матричным материалом [6]. Подбор условий таких реакций крайне трудоемок, поскольку при взаимодействии флюса, припоя и матричного материала происходит одновременно несколько физико-химических процессов. При этом удаляется не только оксидная пленка, но также формируются хрупкие интерметаллидные фазы [7–9]. 4. Диффузионный перенос активных компонентов (Si, Zn и других) от поверхности в матрицу приводит к изменению химического состава поверхностного слоя, что смещает температуру кристаллизации и изменяет тип формируемой микроструктуры. В результате образуются крупнозеренные включения фазы α-Al, соответствующей твердому раствору [10].
Приведенный обзор показывает, что диффузионные, капиллярные и химические процессы играют важную роль при пайке твердым припоем. Таким образом, важно обосновать использование диффузионно-активных припоев, которые способствуют эрозии поверхности матричного материала, что приводит к повышению смачиваемости [11]. При ПТП сплавов АМг в основном используются припои с высоким содержанием цинка, а также системы Al–Si, Al–Сu–Si, Al–Mg–Si [4]. Совместимость сплавов с такими припоями характеризуется степенью химической эрозии, пористости и охрупчивания при их контакте с жидкими припоями. Выше температуры 500°С растворимость алюминия в цинке резко возрастает, поэтому цинковые припои при высоких температурах начинают активно взаимодействовать с паяемым материалом. Вместе с тем, температура нагрева при пайке должна быть выше температуры образования эвтектики Al–Zn, Al–Zn–Mg [12, 13].
Целью настоящей работы являлся анализ диффузионных процессов в поверхностном слое матричного материала из сплава АМг3 при его взаимодействии с припоями на основе Zn и системы Al–Mg. Результаты работы важны для понимания физических основ разработки для Al-сплавов новых припоев, обеспечивающих хорошую смачиваемость и формирование смешанной дендритно-эвтектической микроструктуры [14] с высокой механической прочностью.
МАТЕРИАЛЫ И МЕТОДЫ ИССЛЕДОВАНИЯ
В качестве исследуемого материала был выбран сплав АМг3, включающий Al 93.8–96%, Mg 3.2–3.8%, Mn 0.3–0.6%. Сплав АМг3 является широко применяемой системой в современных технологиях конструкционной промышленности. В работе использовали пластины АМг3 с регламентируемым стандартом ГОСТ 21631, которые укладывали внахлест, в месте стыка помещали пруток припоя HTS-2000 (рис. 1а). Микроструктура исходной пластины АМг3 (ГОСТ 21631) до термических испытаний приведена на рис. 1б. Материал HTS-2000 является универсальным припоем для сплавов на основе алюминия и магния. В состав HTS-2000 входят 97% Zn, 2% Cu и 1% легирующих добавок Al, Mg и Ag. Процессы, происходящие при контактном сплавлении сплава АМг3 и выбранного припоя (HTS-2000), сравнивали с аналогичными процессами при сплавлении заэвтектического сплава Mg–Al и АМг3.
Перед термическими испытаниями проводили исследования методом дифференциальной сканирующей калориметрии (ДСК) исходного сплава АМг3, припоя HTS-2000 и сплава Mg–Al. Анализ ДСК требуется для выявления точных температур фазовых переходов многокомпонентной системы и соответствующих им энтальпий ΔН, что необходимо для определения параметров пайки. ДСК сплавов проводили на установке DSC 404 C Pegasus фирмы Netzsch с рабочим диапазоном от 50 до 1500°С с погрешностью ±3°С. С учетом данных ДСК были выбраны следующие режимы:
1. При пайке АМг3 припоем HTS-2000 максимальная температура нагрева образцов составляла 450°C, нагрев до заданной температуры проводили со скоростью 15°C/мин, при максимальной температуре образцы выдерживали в течение 5 мин. Нагрев проводили в атмосфере азота чистотой 99.99%.
2. При пайке АМг3 сплавом Mg66Al34 нагрев проводили в атмосфере Ar (ОСЧ), после предварительного вакуумирования печи до 10–2 Па. До температуры 500°С скорость нагрева составляла 10°С/мин, после чего образцы выдерживали в течение 10 мин и затем охлаждали с печью.
После термических испытаний пластин АМг3, припоя HTS-2000 и сплава Mg–Al проводили анализ полученных микроструктур. Металлографический анализ позволяет выяснить механизм структурообразования при пайке и спрогнозировать возможность образования металлургического соединения. Образцы для металлографии травили в 5%-растворе азотной кислоты в этаноле. Микроструктурный анализ проводили с помощью оптической и растровой электронной микроскопии на микроскопах Neophot 32 Jena Zeiss c цифровой системой регистрации изображения и FEI Inspec S50 с энергодисперсионной приставкой (EDAX) при ускоряющем напряжении 20 кВ.
ОСНОВНЫЕ РЕЗУЛЬТАТЫ И ИХ ОБСУЖДЕНИЕ
Результаты анализа методом ДСК представлены на рис. 2. На ДСК-кривой нагрева сплава АМг3 наблюдается два эндотермических эффекта, которые полностью не разделяются между собой, причем площадь первого пика намного меньше, чем площадь второго, общая энтальпии процесса составляет 395 Дж/г. Температура начала второго эндотермического пика (~601°С) хорошо согласуется с диаграммой состояния системы Al–Mg [15] и соответствует началу плавления твердого раствора на основе алюминия с содержанием Mg 3.5 мас. %. Учитывая исходную микроструктуру сплава АМг3 (рис. 1б), в которой присутствуют включения сложного интерметаллида на основе Al–Mg–Mn, наблюдаемый нами первый эндотермический эффект при 585°С, по-видимому, соответствует высокотемпературному растворению вторичного интерметаллида. Таким образом, температура начала плавления данного сплава составляет ~600°C.
Исследования методом ДСК припоя HTS-2000 показали (рис. 2б), что на кривой нагрева наблюдается два эндотермических эффекта при температурах 285 и 381°С, которые хорошо согласуются с температурами фазовых равновесий в системе Zn–Al. Первый эффект при температуре ~285°C соответствует твердофазному превращению α-Al2(Zn) + α-Zn2(Al) → α-Al(Zn), энтальпия этого процесса 9 Дж/г. Второй эффект при температуре 381°С соответствует эвтектическому плавлению Al(Zn) + α-Zn(Al) → L (ΔH = = 118 Дж/г). Плавление сплава Mg66Al34 соответствует диаграмме состояния системы Mg–Al, данный сплав имеет состав, близкий к эвтектическому Al12Mg17 + Mg с небольшим количеством избыточного интерметаллида, поэтому плавится в две стадии (Тсолидус = 433°С и Тликвидус = 444°С), общая энтальпия процесса составляет 240 Дж/г.
Согласно проведенному анализу ДСК, температуры рекристаллизации сплава АМг3 находятся в пределах от 400 до 450°С, поэтому оба исследуемых сплава (HTS-2000 и Mg66Al34) могут быть использованы в качестве припоев. Учитывая определенные температуры плавления припоев, а также имеющиеся данные об особенностях образования микроструктур при контактном сплавлении Al и сплавов Al–Si, были выбраны соответствующие режимы термообработки для процессов пайки [14].
На рис. 3 представлен внешний вид образцов сплава АМг3 и припоя HTS-2000 после контактного сплавления согласно описанной выше схеме (рис. 1). Из рисунка видно, что в ходе термических испытаний происходило плавление припоя и его взаимодействие с подложкой АМг3, однако полного сплавления не произошло. Возможной причиной могло быть влияние оксидной пленки на поверхности припоя. После экспериментов на поверхности пластин АМг3 наблюдали глубокую эрозию (рис. 3а), что свидетельствует о взаимодействии припоя и АМг3 при высоких температурах.
Учитывая негативное влияние оксидной пленки на процессы пайки, в следующей серии экспериментов по контактному сплавлению АМг3 и Mg66Al34 проводили две серии испытаний: 1) по вышеописанной схеме (см. раздел материалы и методы исследования); 2) с добавлением флюса ВИ-2 (MgCl2 38–46%, KCl 32–40%, BaCl2 5–8%, CaF2 3–10%). Соответствующие термограммы процесса контактного плавления образца с флюсом и без флюса представлены на рис. 4.
Согласно рис. 4, независимо от того, используется флюс в процессе пайки или нет, в выбранных режимах термических испытаний припой полностью плавится, поэтому кривые ДСК на рис. 4 соответствуют диаграмме на рис. 2в. Наблюдаемый на рис. 4 (кривая 1) псевдоэкзотермический эффект при температурах выше 450°С связан с изменением условий смачиваемости между припоем и подложкой при полном плавлении без флюса. Резкое уменьшение величины теплового потока (ДСК-сигнала) происходит в результате резкого снижения площади контакта между припоем и подложкой, что связано с изменением формы припоя после его полного плавления под воздействием плотной оксидной пленки.
Результаты металлографических исследований после проведенных испытаний приведены на рис. 5. На снимках микрошлифов видно, что в зоне контактов с припоями HTS-2000 и Mg66Al34 при термических испытаниях происходит плавление как припоя, так и сплава АМг3 рис. 5а–5в. На рис. 5а представлена микроструктура сплава HTS-2000 после контактного плавления. Из рисунка видно, что характер микроструктуры изменяется в зависимости от удаленности от границ контакта с АМг3. В объеме припоя сохраняется его исходная структура, состоящая из первичных кристаллов твердого раствора на основе α-Zn(Cu, Al) и мелкодисперсных эвтектических колоний. По мере приближения к зоне контакта эвтектическая структура укрупняется, а количество твердого раствора на основе α-Zn становится меньше. В зоне контакта на поверхности припоя образуются достаточно крупные (30–60 мкм) округлые кристаллы с большим содержанием алюминия.
Рис. 5.
Микроструктура образцов после термических испытаний при сплавлении припоя HTS-2000 (а) и пластинки АМг3 (б), Mg66Al34 и АМг3 (в, г).
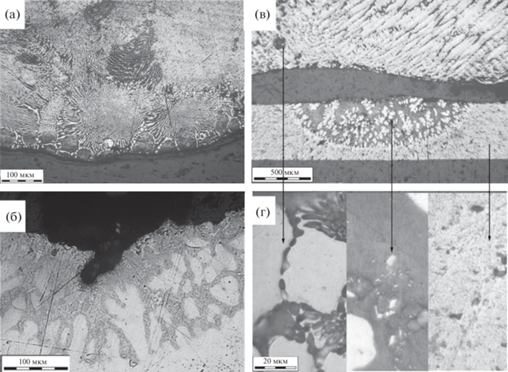
На микрошлифе образца АМг3 (рис. 5б) наблюдается крупная дендритная микроструктура α-Al c междендритным пространством, заполненным эвтектической микроструктурой и включениями. Характерный размер первичных ветвей дендритов α-Al составляет 50–100 мкм, что находится на верхнем пределе значений, допустимых для паяных соединений. На границе зоны оплавления наблюдается сплошной слой твердого раствора α-Al, что связано с диффузией легирующих компонентов сплава АМг в подложку. Плавление подложки происходит в результате диффузии Zn из припоя в пластину АМг3. Кристаллизация начинается с образования дендритов α-Al. Рост дендритов α-Al сопровождается вытеснением легирующих компонентов в расплав, что приводит к их накоплению на фронте кристаллизации. В результате этого на следующем этапе вокруг дендритов образуются сплошные кристаллы на основе легирующих элементов, которые являются ведущей фазой для эвтектики и инициируют ее кристаллизацию.
Сравнительный анализ микроструктуры сплавления припоев HTS-2000 и Mg66Al34 со сплавом АМг3 (рис. 5в, 5г) показал заметное сходство диффузионных процессов и механизмов образования микроструктуры при некоторых отличиях. Во-первых, на границе припоя и матричного материала наблюдается менее интенсивная диффузия Al в поверхностный слой припоя, поэтому микроструктура сплава Mg66Al34 не претерпевает существенных изменений. Во-вторых, в зоне сплавления на границе контакта подложки и припоя не наблюдается образование эвтектической структуры, а в результате контактного плавления сплава, обогащенного магнием (припой), и сплава, обогащенного алюминием (АМг3), образовывается последовательный ряд интерметаллидов системы Al–Mg (рис. 5г). Выбранные режимы термической обработки принципиально не изменяют исходную микроструктуру матричного материала (рис. 5г).
Полученные результаты показывают возможность управления микроструктурой и свойствами зоны сплавления за счет выбора химического состава припоя и режимов термической обработки, а также выбора оптимального флюса. Экспериментальные данные свидетельствуют, что формирование интерметаллидных фаз без образования эвтектических структур охрупчивает зону паяного соединения. По этой причине важно выбрать оптимальный состав припоя и условия кристаллизации, при которых будет образовываться мелкодисперсная эвтектическая микроструктура. Режимы термической обработки в процессе пайки должны способствовать направленной кристаллизации в зоне сплавления, когда размер зоны проплавления достаточно мал и препятствует образованию первичных дендритов α-Al. Полученные данные для припоев HTS-2000 и Mg66Al34 в выбранных режимах термообработки показывают, что выбранные времена выдержки сплавления образцов слишком длительные. На рис. 6 приведены изменения микроструктуры по глубине зоны сплавления для припоя Mg66Al34. Наблюдается увеличение доли α-Al при одновременном изменении микроструктуры междендритного пространства от смеси интерметаллидов (рис. 6а) до образования эвтектики (рис. 6в). Таким образом, хрупкая интерметаллидная фаза на границе припоя и подложки приводит к неудовлетворительным механическим свойствам паянного соединения.
Рис. 6.
Микроструктура пластинки АМг3 после термических испытаний пайки со сплавом Mg–Al вблизи поверхности (а), с повышением глубины (б) и (в).
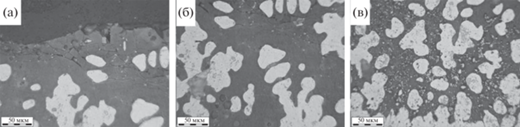
После термических испытаний на поверхности пластины АМг3 наблюдается глубокая эрозия в зоне контакта с припоем HTS-2000. Для анализа глубины проникновения цинка в области контакта проводили энергодисперсионный анализ образца АМг3 после термических испытаний (рис. 7). Элементный состав зоны представлен в табл. 1, 2: в первой области ~83.8 мас. % Zn и ~2.9 мас. % Cu; во второй области ~78.4 мас. % Zn и ~2.4 мас. % Cu. следовательно, Zn хорошо диффундирует в подложку АМг3, способствует изменению химического состава поверхности и влияет на образование сложной микроструктуры. Под действием термических напряжений на оксидной пленке, которая сдерживает припой в расплавленном состоянии, могут образовываться микротрещины, сквозь которые атомы цинка свободно диффундируют в подложку из АМг3 и вызывают ее подплавление.
Рис. 7.
Результаты энергодисперсионного анализа химического состава зоны сплавления сплава АМг3 с припоем HTS-2000.
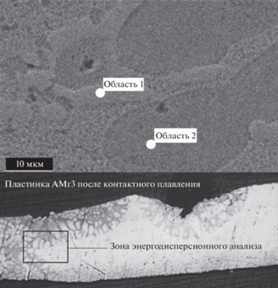
Таблица 1.
Элементный состав области 1
Элемент | мас. % | ат. % |
---|---|---|
O | 0.79 | 2.69 |
Mg | 3.20 | 7.15 |
Al | 8.09 | 16.30 |
Si | 0.56 | 1.08 |
Mn | 0.37 | 0.37 |
Fe | 0.20 | 0.19 |
Cu | 2.98 | 2.54 |
Zn | 83.81 | 69.67 |
Таблица 2.
Элементный состав области 2
Элемент | мас. % | ат. % |
---|---|---|
O | 0.97 | 3.08 |
Mg | 1.31 | 2.73 |
Al | 16.60 | 31.11 |
Si | 0.26 | 0.48 |
Cu | 2.49 | 1.98 |
Zn | 78.36 | 60.62 |
Таким образом, проведенные исследования показали, что интенсивные диффузионные процессы, проходящие на границе припоя и подложки, приводят к глубокому плавлению подложки как при наличии оксидной пленки (для HTS-2000), так и при её отсутствии (Mg66Al34). Поэтому при ПТП необходимо учитывать не только условия смачивания припоем подложки, но и механизмы кристаллизации в зоне проплавления.
ЗАКЛЮЧЕНИЕ
Пайка сплавов системы Al–Mg–Mn с припоями на основе Zn–Cu–Al и Mg–Al потенциально возможна, об этом свидетельствует образование зоны сплавления. Контактное плавление припоев приводит к диффузионным эффектам в области соприкосновения, когда компоненты припоя проникают в матричный материал и вызывают его плавление. Тем самым инициируется формирование комплексной микроструктуры, состоящей из эвтектики, интерметаллидов и дендритов α-Al.
Образование зоны сплавления при пайке твердым припоем недостаточно для формирования металлургического соединения. Дополнительным условием является обеспечение контактного угла смачивания менее 90° (желательно менее 15°), при котором возможно растекание припоя. Важным условием является использование специализированных флюсов, обеспечивающих удаление оксидной пленки, но не взаимодействующих с припоем и матричным материалом, однако и в этом случае необходимо точно определить температуру и время сплавления, при которых рост интерметаллидных фаз ограничен.
Список литературы
Hirsch J. // Mater. Trans. 2011. V. 52. № 5. P. 818. https://doi.org/10.2320/matertrans.L-MZ201132
Rajeshkumar R., Niranjani V.L., Devakumaran K., Banerjee K. // Materials Today: Proceedings. 2021. V. 46. № 7. P. 2214. https://doi.org/10.1016/j.matpr.2021.01.507
Searles J.L., Gouma P.I., Buchheit R.G. // Metall. Mater. Trans. A. 2001. V. 32. № 11. P. 2859.
Справочник по пайке. Под ред. И.Е. Петрунина. 3-е изд., перераб, и доп. М.: Машиностроение, 2003. 480 с.
Olefjord I., Stenqvist T., Karlsson A. // Proc. of the 4th International Conference on Aluminum Alloys. 1994. V. 1. P. 459.
Карамурзов Б.С., Кутуев Р.А., Понежев М.Х., Созаев В.А., Шерметов А.Х., Шокаров А.А. // Поверхность. Рентген., синхротр. и нейтрон. исслед. 2021. № 6. С. 109. https://doi.org/10.31857/S1028096021030055
Воробьев В.Л., Климова И.Н., Колотов А.А., Быков П.В., Баянкин В.Я. // Поверхность. Рентген., синхротр. и нейтрон. исслед. 2019. № 12. С. 50. https://doi.org/10.1134/S1028096019120355
Zhenglong L., Xinrui Z., Jinge L., Peng Li // J. Manuf. Process. 2021. V. 67. № 3. P. 226. https://doi.org/10.1016/j.jmapro.2021.04.065
Halim S.B., Bannour S., Abderrazak K., Kriaa W., Autric M. // Thermal Science and Engineering Progress. 2021. V. 22. P. 100838. https://doi.org/10.1016/j.tsep.2020.100838
Sekulic D.P., Galenko P.K., Krivilyov M.D., Walkerd L., Gao F. // Int. J. Heat Mass Transf. 2005. V. 48. № 12. P. 2372. https://doi.org/10.1016/j.ijheatmasstransfer.2005.01.034
Hawksworth D.K., Sekulic D.P., Yu C.-N., Fu H., Westergard R.G.J. // Proceedings of Vehicle Thermal Management Systems Conference. 12. 2015. V. 1. P. 107.
Диаграммы состояния двойных металлических систем: справочник. Под общ. ред. Н.П. Лякишева. М.: Машиностроение, 1996. 992 с.
Li Q., Yang-Zi Z., Qun L., Shuang-Lin Ch., Jie-Yu Zh., Kuo-Chih Ch. // J. Alloys and Compounds. 2010. V. 501. № 2. P. 282. https://doi.org/10.1016/j.jallcom.2010.04.089
Shutov I.V., Kamaeva L.V., Krivilyov M.D., Yu C.-N., Mesarovic S.Dj., Sekulic D.P. // J. Crystal Growth. 2020. V. 530. P. 125287. https://doi.org/10.1016/j.jcrysgro.2019.125287
Su H.L., Harmelin M., Donnadieu P., Baetzner C., Seifert H.J., Lukas H.L., Effenberg G., Aldinger F. // J. Alloys and Compounds. 1997. V. 247. № 1–2. P. 57. https://doi.org/10.1016/S0925-8388(96)02595-9
Дополнительные материалы отсутствуют.
Инструменты
Поверхность. Рентгеновские, синхротронные и нейтронные исследования