Поверхность. Рентгеновские, синхротронные и нейтронные исследования, 2023, № 4, стр. 10-24
Ионно-лучевая модификация поверхности углеродных волокон
Н. Н. Андрианова a, А. М. Борисов a, b, *, Е. С. Машкова c, М. А. Овчинников c, И. В. Суминов b
a Московский авиационный институт (национальный исследовательский университет)
125993 Москва, Россия
b Московский государственный технологический университет “СТАНКИН”
127055 Москва, Россия
c Научно-исследовательский институт ядерной физики им. Д.В. Скобельцына
Московского государственного университета им. М.В. Ломоносова
119997 Москва, Россия
* E-mail: anatoly_borisov@mail.ru
Поступила в редакцию 12.09.2022
После доработки 28.10.2022
Принята к публикации 28.10.2022
- EDN: JUAKZG
- DOI: 10.31857/S1028096023040027
Аннотация
Углеродным волокнам находят применение в производстве автомобилей, самолетов, спортивных товаров, энергетике и биомедицине благодаря их уникальным свойствам, таким как высокая удельная прочность, высокая удельная жесткость, низкий коэффициент теплового расширения и низкая плотность. Были и остаются актуальными исследования и разработки как технологии получения углеродных волокон, так и их модификации для широкого круга применений. Проведенное обобщение накопленного опыта по модификации углеродных волокон показывает, что ионно-лучевая обработка позволяет получать различный по геометрии развитый рельеф поверхности, в частности, вискерообразный и гофрообразый, ориентированный поперек или вдоль волокна. Такая обработка выгодно отличается от обычной вискеризации волокна как многообразием геометрии границы раздела композита и подложки, так и отсутствием проблемы адгезии вискеров с волокном. Ионно-лучевая обработка позволяет модифицировать также структуру поверхностного слоя от аморфизованного до упорядоченного с разной степенью графитации. Облучение химически активными ионами приводит к функционализации углеродного волокна за счет образования, например, нитридов и оксидов углерода. Выбор ионов азота для технологии получения углерод-углеродных и углерод-керамических композитов представляется более предпочтительным, благодаря менее жестким требованиям к температуре облучаемого волокна. Для ионно-лучевого гофрирования поверхности углеродного волокна на основе полиакрилонитрила необходим лишь его нагрев выше температуры динамического отжига радиационных нарушений. К значительному увеличению производительности ионно-лучевой обработки приводит использование ионов гелия технологических плазменных ускорителей.
ВВЕДЕНИЕ
Углеродное волокно активно используют, благодаря таким уникальным свойствам, как высокая удельная прочность, высокая удельная жесткость, низкий коэффициент теплового расширения и низкая плотность. Углеродным волокнам находят применение в производстве автомобилей, самолетов, спортивных товаров, энергетики и биомедицины. Были и остаются актуальными исследования и разработки как технологии получения углеродных волокон, так и их модификации для широкого круга применений [1–12]. Сравнение по прочности, упругости и плотности высокопрочных неорганических волокон демонстрирует явное преимущество углеродных волокон перед другими высокопрочными волокнами [5], особенно в приложениях, где вес имеет решающее значение, например, в аэрокосмической отрасли.
Настоящая работа посвящена накопленному опыту модификации углеродных волокон, проблемам и перспективам ионно-лучевой модификации их поверхности.
ВИДЫ И СВОЙСТВА УГЛЕРОДНЫХ ВОЛОКОН
Углеродные волокна, производимые в настоящее время, можно разделить на три категории в зависимости от материалов прекурсоров: полиакрилонитрил (ПАН), пек и вискоза, каждый из которых имеет свои особенности и особые преимущества [3–5].
В настоящее время ПАН является наиболее предпочтительным прекурсором для производства волокон с высокими эксплуатационными характеристиками по ряду причин. Во-первых, углеродные волокна из ПАН находятся в среднем ценовом диапазоне. Во-вторых, они обладают самой высокой прочностью на разрыв среди всех углеродных волокон и имеют широкий диапазон модуля упругости, доступны в виде различных жгутов. Углеродные волокна из ПАН составляют большую часть производства углеродных волокон, стоимость их производства постоянно снижается.
Углеродные волокна из пека делят на две группы: волокна из изотропного пека, которые имеют низкие механические свойства и относительно низкую стоимость, и волокна из мезофазного пека, которые имеют очень высокий модуль упругости, но являются более дорогими. Волокна на основе пека производят с помощью относительно простого процесса, и их стоимость конкурирует со стекловолокном.
Углеродные волокна из вискозы не так прочны, как волокна из ПАН. Их используют в изоляционных материалах, а также в некоторых углерод-углеродных и абляционных композитах из-за хорошего соответствия свойствам карбонизированной матрицы.
Аналитические методы определения структуры углеродных волокон включают: дифракцию рентгеновских лучей, дифракцию электронов, рассеяние нейтронов, рамановскую спектроскопию, электронную и оптическую микроскопию.
Структура углеродных волокон из ПАН до сих пор до конца не изучена. Тем не менее, благодаря достижениям аналитических методов существуют некоторые точные данные о строении волокон из ПАН [3]. В отличие от хорошо упорядоченных параллельных плоскостей пиролитического графита, которые наиболее близко соответствуют структуре кристалла графита, структура углеродных волокон из ПАН является по существу турбостратной и состоит из небольших двумерных фибрилл или лент. Они уже присутствуют в ПАН-волокне и предпочтительно выровнены параллельно оси волокна. Структура волокна также может включать ламели и, вероятно, представляет собой комбинацию как фибрилл, так и ламелей. Малый размер кристаллитов, большое расстояние между слоями и общий структурный беспорядок являются факторами, которые способствуют уникальной и стабильной турбостратной структуре углеродных волокон из ПАН, которая не графитируется даже после высокотемпературной термообработки, вплоть до 3000°C. Углеродное волокно из ПАН после термообработки выше 2000°С содержит две основных фазы из фибрилл с включениями графита: фаза с широкими и толстыми лентами с повышенной степенью ориентации вдоль оси волокна и фаза из более узких, менее ориентированных и сильно переплетенных лент-фибрилл. Обе фазы имеют большое количество пор, микротрещин и других дефектов. Вторая фаза доминирует в центральной части волокна, первая на поверхности. В промежуточном слое присутствуют ленты обоих типов (рис. 1).
Рис. 1.
Схематичное строение углеродного волокна из ПАН: 1 – большая полость; 2 – ламеллярные структуры на включениях и полостях; 3 – области, характеризующиеся большой концентрацией напряжений; 4 – оболочка; 5 – промежуточный слой с радиальной ориентацией; 6 – ядро; 7 – небольшая пора; 8 – трещина; 9 – участок с мелкокристаллической структурой; 10 – неорганическое включение; 11 – радиально расположенные основные структуры [3].

Пек является побочным продуктом перегонки угля, сырой нефти или асфальта. Он подходит для производства углеродного волокна, является недорогим и легкодоступным [3–5]. Выход углерода при перегонке может превышать 60%, что значительно выше выхода для ПАН (~50%). Недорогие углеродные волокна производят из изотропного пека с низкой температурой размягчения. Прекурсор формуют из расплава, термоотверждают при относительно низких температурах и карбонизируют. Полученные волокна обычно имеют низкую прочность и модуль упругости (35–70 ГПа). Они подходят для применения в качестве изоляционных материалов и наполнителей.
Углеродные волокна из мезофазного пека обладают более высоким модулем упругости и средней прочностью. Они дороже волокон из ПАН. Структура поперечного сечения углеродных волокон мезофазного пека может быть одним из четырех типов, показанных на рис. 2, и определяется методом прядения, температурой стабилизации и парциальным давлением кислорода [5]. Часто происходит образование оболочечно-сердцевидной структуры, аналогичной структуре углеродного волокна из ПАН. Крупные кристаллы в термообработанных волокнах из мезофазного пека, близкие к кристаллу графита и выровненные вдоль оси волокна, предполагают мало центров рассеяния для фононов. Это означает, что эти волокна обладают высокой теплопроводностью вдоль оси волокна, поскольку передача тепла в кристалле графита происходит в основном за счет фононов. Однако высокая степень кристалличности приводит к низкой прочности на сдвиг и сжатие. Кроме того, эти углеродные волокна склонны к возникновению дефектов, таких как ямки, царапины, бороздки и канавки. Эти дефекты ухудшают свойства при растяжении, но существенно не влияют на модуль упругости и теплопроводность.
Рис. 2.
Поперечное сечение различных структур, наблюдаемых в углеродных волокнах на основе мезофазного пека: 1 – радиальная; 2 – луковичная оболочка с центрально-радиальным ядром; 3 – луковичная оболочка с разупорядоченным ядром; 4 – луковичная [5].

Волокна из вискозы были первыми углеродными волокнами, произведенными на коммерческой основе. Они были разработаны в 1960-х гг. специально для усиления абляционных компонентов ракет. Однако их трудно переработать в высокопрочные высокомодульные волокна, и поэтому в большинстве конструкционных применений они были заменены волокнами из ПАН или пека. Графитированные волокна из вискозы характеризуются почти полным отсутствием ориентированных слоев на поверхности [2]. Это существенно отличает их по структуре от волокон из ПАН, слоистая оболочка которых состоит из крупных кристаллитов с высокой радиальной ориентацией. Степень преимущественной ориентации углеродных волокон из вискозы может быть значительно увеличена путем растяжения карбонизированного волокна при очень высокой температуре (2700–2800°C), что приводит к получению высокопрочного и высокомодульного волокна. Однако для этого требуется сложное и дорогое оборудование, а выход годного волокна невелик. Вытяжку ПАН-волокна делают перед карбонизацией, что значительно дешевле и надежнее, чем вытяжка при очень высокой температуре.
Производимые в большом количестве низкомодульные углеродные волокна из вискозы в виде углеродной ткани или войлока находят очень широкое применение. Их назначение – теплозащита электротермического оборудования; наполнение дискретными волокнами пластмасс; радиопоглощение; электрохимическая экстракция металлов; электроды – носители катализаторов, в том числе для топливных элементов; применение в виде активированных тканей для молекулярных электрохимических источников тока и медицинских сорбентов со значительным объемом пор размером 20–30 нм; использование в качестве углеродных проводов для электрических нагревателей и специальных уплотнений [6]. Известно также применение углеродной ткани из вискозных волокон для получения жаростойких и жаропрочных материалов в виде углерод-керамических композитов [13–15].
МОДИФИКАЦИЯ ПОВЕРХНОСТИ УГЛЕРОДНЫХ ВОЛОКОН
Разработка прочных и жестких углеродных волокон явилась крупным достижением 1970-х гг. Были установлены основные принципы эффективной обработки поверхности волокон для армирования углепластиков [3].
Методы поверхностной обработки
Поверхностная обработка направлена на устранение дефектов на поверхности, что увеличивает прочность волокна до 50%. Обработка поверхности особенно сильно проявляется на повышении сдвиговой прочности композитов, составляющей 5–10% от продольной прочности на растяжение. Поверхностная обработка обеспечивает 30–40% прироста прочности на сдвиг за счет удаления дефектного слабо связанного пограничного слоя. Остальная часть прироста прочности происходит за счет химического взаимодействия и повышения шероховатости поверхности при селективном травлении с увеличением удельной поверхности. Наиболее актуальна обработка высокомодульных (более 400 ГПа) волокон. Увеличение шероховатости приводит к появлению помимо чисто сдвиговых напряжений, также растягивающих или сжимающих напряжений, если границы кристаллитов ориентированы под некоторым углом к оси волокна. Свойства композитов зависят в большой степени от адгезии между волокном и матрицей, которая в свою очередь определяется состоянием поверхности волокна.
Виды поверхностной обработки волокон делят: на увеличивающую содержание кислорода и химическую валентность, но мало изменяющую удельную поверхность волокна; на увеличивающую как удельную поверхность, так и содержание в ней соединений кислорода. Способы обработки поверхности волокон, кроме деления на окислительные и неокислительные, классифицируют как: газофазные и жидкофазные; низкотемпературные (<150°C) и высокотемпературные (>400°C); приводящие к увеличению или уменьшению массы волокон; химические или электрохимические [8].
Среди множества способов поверхностной обработки углеродных волокон ведущее место занимает окисление поверхности. В промышленном производстве эти способы обеспечивают увеличение прочности композита при сдвиге и поперечном растяжении в 2–4 раза.
Наиболее успешно используют окисление в газообразной или жидкой фазе, благодаря следующим преимуществам: недорогие реагенты; при травлении удаляется дефектный слабо связанный слой углерода толщиной 15–50 нм; образуются хемосорбированные кислородсодержащие группы, реагирующие с молекулами связующих. Окисление в газовой фазе проводят нагревом углеродного волокна до температуры 400–800°С при доступе воздуха с обогащением СО, СО2, Н2О. Во время этого процесса контролируют степень травления, чтобы не допустить чрезмерного снижения прочности волокна. К меньшей степени коррозии волокна приводит обработка при низких температурах озонированным воздухом, обработка в плазме кислорода или аммиака без нагрева волокна.
Химическую обработку проводят в водных растворах окислителей, например, азотной кислоты, солей кислот. Электрохимическое (анодное) окисление имеет преимущество при непрерывном технологическом процессе. Существует также способы повышения адгезии путем осаждения более активных форм углерода прививкой полимеров, осаждением пироуглерода.
Развитие методов поверхностной обработки углеродных волокон для армирования композитов отражено в монографии [11]. Cводка процессов и средств обработки поверхности представлена в табл. 1. Отметим, что большинство химических видов обработки направлены на увеличение удельной поверхности (поверхность, участвующая в контакте между адгезивом и субстратом) путем открытия имеющихся на поверхности углеродных волокон пор или получения новых. Модификация поверхности происходит также за счет появления на ней кислородосодержащих функциональных групп. Данные способы имеют как преимущества, так и недостатки, в том числе, и технологические.
Таблица 1.
Химические и физико-химические способы модификации поверхности [11]
Процесс обработки поверхности | Основные средства обработки | |
---|---|---|
Методы окисления | Окисление в растворе | HNO3, перманганат калия, соли хлорированной и хромовой кислот |
Электролитическое окисление | Различные электролиты | |
Окисление в газовой среде | На воздухе, в кислороде, озоне, галогеноподобных смесях, соединениях азота | |
Полимеризация прививкой | Органические и неорганические соединения, полимеры, усы | |
Воздействие физических полей | Ультразвук, магнитное поле, электростатический разряд, электронный разряд, ультрафиолетовое и радиационное облучение | |
Очистка поверхности | Отмывка растворителями, сушка, высокотемпературная обработка | |
Защита поверхности с одновременной активацией | Аппретирование |
На прочность композита при полимеризации методом прививки влияет не только адгезионная прочность, но и когезионная прочность прививки. Например, очень высокой прочностью обладают нанотрубки. Ультразвуковая обработка в процессе пропитки позволяет увеличить не только ее интенсивность, но и прочностные характеристики композита. Магнитное поле оказывает влияние на адгезионную прочность. На степень улучшения адгезионной прочности оказывают влияние тип полимера, режим обработки, магнитные свойства армирующего волокна. Увеличение адгезионной прочности под воздействием электростатического поля обусловлено влиянием на угол смачивания полимеров, ускорением удаления следов влаги и воздуха. Ультрафиолетовое и радиационное облучения оказывают влияние на адгезионное взаимодействие и способствуют увеличению числа химических связей на границе раздела матрицы и наполнителя. При модификации в электронном разряде образуются химически активные центры.
В настоящее время применение углеродных волокон не ограничивается только армированием композитов, расширяются и методы модификации волокон. В монографии [8] все методы модификации разделены на методы активации и пассивации поверхности, с изменением структуры волокна и без ее изменения. Среди методов без изменения структуры выделяют следующие.
Аппретирование – нанесение на поверхность тонкого слоя полимера со сродством к волокну и матрице в водных растворах и эмульсий. Основными целями аппретирования являются защита волокна и увеличение адгезии армирующего волокна к матрице. Аппреты имеют комплексный состав и должны образовывать на поверхности наполнителя близкую по молекулярным свойствам к полимерной матрице адсорбционную оболочку, оптимально насыщать поверхность наполнителя модификатором. Аппреты могут быть применены для углепластиков с температурой эксплуатации не выше 1000°С.
На поверхность волокон наносят также углеродные, керамические и металлические покрытия. Жаростойкие оксиды, карбиды и нитриды наносят обычно газофазным методом. Высокая термоокислительная стойкость волокна получается при покрытии оксидом кремния из газовой фазы с образованием пленки тетраэтоксисилана и термообработкой при 600°С. Более эффективным является карбид кремния. Пленки оксидов алюминия и магния, получаемые ионно-вакуумными методами, также повышают устойчивость волокна к окислению. При эксплуатации при высоких температурах необходимо решать проблемы совместимости волокна с барьерными керамическими покрытиями по коэффициенту термического расширения. Проводят также металлизацию углеродных волокон для получения металлокомпозитов различного назначения. Обычно используют электрохимические способы.
В методах модификации углеродных волокон с изменением структуры окислительное вытравливание неупорядоченных областей дает отдельный класс материалов – активированные углеродные материалы с развитой удельной поверхностью с мезопорами и микропорами [8]. Такие материалы можно назвать молекулярными сорбентами. Активированные углеродные волокна из вискозы не уступают гранулированному активированному углю.
В последнее время разрабатывают и развивают методы модификации поверхности углеродных волокон углеродными наноструктурами различной формы: нанотрубками и нановолокнами [16–21]. В отдельный вид выделяют композиты с вискеризованными волокнами. В таких материалах поверхность волокна покрыта углеродными усами (вискерами) [16–18]. Испытания показали, что вискеризация волокна углеродными нанотрубками приводит к двукратному увеличению межфазной прочности композитного материала при продольном сдвиге по сравнению с обычным волокнистым композитом [20].
Актуальными являются работы по созданию композитов с углеродными нанотрубками и графеновыми частицами [22–29]. В обзоре [22] отмечено, что после более чем двух десятилетий усилий по созданию композитов с нанотрубками в различных концентрациях и с различными комбинациями матриц остается открытым вопрос: как получить впечатляющие (повышенные) характеристики композитов с использованием углеродных нанотрубок или графена? Результаты исследований до сих пор не показывают конкурентные преимущества добавок углеродных нанотрубок или графеновых частиц в композитах. Армирование углеродными волокнами приводит к более высокой прочности или увеличению модуля упругости по сравнению с армированием наноматериалами. Сегодня предполагают, что углеродные нанотрубки идеально подойдут для тонких композитных структур (для которых углеродные волокна диаметром ≥1 мкм являются слишком толстыми) или для обеспечения гибкости и устойчивости в сверхгибких конструкциях. Разработка новых полимер-наноуглеродных композитов с заданными функциональными свойствами является также актуальной темой для космического материаловедения [27–29].
Ионно-лучевая модификация углеродного волокна
При ионно-лучевой модификации углеродного волокна используют такие явления взаимодействия ионов с поверхностью, как ионная имплантация, ионно-индуцированные дефекты, физическое и химическое распыление.
Ионная имплантация – это введение в твердые тела примесных атомов или создание радиационных повреждений с целью модификации физических и химических свойств имплантированного слоя, в том числе и с целью изменения структуры и морфологии облучаемой мишени. Типичные величины энергии ионов при имплантации – десятки и сотни кэВ, глубина проникновения ионов составляет десятки-сотни нм. Для характеризации облучения с заданным флуенсом рассчитывают профили концентрации имплантированных частиц и радиационных смещений ν в числе смещений на атом (СНА) от глубины х, отсчитываемой от поверхности изменяемого материала. Максимальная концентрация имплантированных частиц, также как и число СНА, ограничивается коэффициентом распыления облучаемого материала [30].
При ионной имплантации углеродных волокон использовали в основном ионы массой М1, большей массы атома углерода, при флуенсе порядка 1014–1016 ион/см2 [4]. Необходимо отметить, что изменения в структуре и свойствах углеродных волокон как в результате ионной имплантации, так и других типов ионного облучения, более сложно исследовать ввиду малого диаметра углеродных волокон по сравнению с размерами объемных графитовых мишеней, в том числе высокоориентированного пирографита, аналогом которого является высокотекстурированная оболочка углеродных волокон из ПАН. Возможно, это служит одной из причин практически полного отсутствия данных о морфологических изменениях поверхности углеродных волокон, подвергнутых ионной имплантации. Основное внимание уделяли анализу изменений структуры оболочки волокна в зависимости от массы иона и величины флуенса. Показано, что чем тяжелее ион и больше флуенс, тем значительнее повреждения решетки и для восстановления исходной структуры необходим высокотемпературный отжиг.
При флуенсе, большем, чем характерный для имплантации, облучение углеродных волокон приводит к изменению как структуры, так и топографии поверхности.
Так, в [31] изучено влияние облучения ионами углерода с энергией 40 кэВ и флуенсе от 1015 до 1019 ион/см2 на структуру и топографию поверхности высокомодульного углеродного волокна. Найдено, что основные структурные параметры (межплоскостное расстояние и размер областей когерентного рассеяния) снижаются до минимальных значений при флуенсе ~1017 ион/см2. При более высоком флуенсе размер областей когерентного рассеяния возрастает и при дозе ~1019 ион/см2 практически равен соответствующей величине для необлученного волокна. Рельеф поверхности после ионного облучения состоял из периодически повторяющихся продольных впадин и выступов, параллельных оси волокна.
В [32] проводили облучение поверхности высокомодульных углеродных волокон импульсными пучками ионов азота с энергией 30 кэВ. Поверхность исследовали с помощью растровой электронной микроскопии (РЭМ), спектроскопии резерфордовского обратного рассеяния и дифракции рентгеновских лучей. Найдено значительное изменение морфологии поверхности углеродного волокна, особенно при флуенсе 1017–1019 ион/см2. Шероховатость поверхности волокна увеличивалась до 0.4–0.5 мкм.
Систематические исследования воздействия высокодозного облучения ионами инертных газов и азота на структуру и морфологию поверхности углеродных волокон предприняты в [33–54]. Облучение проводили пучками сепарированных по массе ионов с энергиями от 10 до 30 кэВ и при флуенсе 1018–1019 ион/см2. Обобщение найденных закономерностей проведено в главе книги серии “Horizons in World Physics” в 2013 г. [39]. Обсуждение и интерпретация полученных результатов приведены в следующем разделе. Обнаруженное в этих исследованиях кардинальное изменение морфологии поверхности в виде гофрирования с шагом рельефа менее 1 мкм, характеризующееся гребневидными образованиями в виде призматических гофров, упорядоченно расположенными на поверхности волокна, положено в основу новых способов модификации углеродного волокна [56, 57].
Способ модификации поверхности углеродного высокомодульного волокна из ПАН, согласно патенту [56], предложен для применения в технологии получения углеродных волокон в виде нитей, жгутов в качестве армирующих наполнителей композиционных материалов с полимерной, углеродной и керамической матрицами различного назначения (конструкционные материалы, теплозащита летательных аппаратов, высокотемпературное термическое оборудование, производство спортивных изделий, в медицине). Цель предлагаемого способа – повысить адгезионное взаимодействие высокомодульных углеродных волокон из ПАН, как армирующего компонента, с матричными материалами композитов. Этого можно достичь за счет того, что после облучения углеродное волокно обладает модифицированной поверхностью, в виде субмикронного гофрирования.
Предлагаемое углеродное высокомодульное волокно с модифицированной поверхностью необходимо для создания композита, требуемая прочность которого формируется в процессе совмещения основных его компонентов: армирующих углеродных волокон и матричного материала. Оптимальное адгезионное взаимодействие, сцепление между матрицей и волокном позволяет максимально нагружать полученный композит.
Применение всевозможных аппретов, проведение активации поверхности волокон с целью обеспечения более сильной адгезии между поверхностью волокна и аппретом или матрицей повышают прочность композитов с полимерной матрицей, эксплуатируемой при невысоких (<1000°C) температурах. Композиты на основе углеродной и/или керамической матриц получают при высоких (>1500°C) температурах, в разы превышающих термостойкость применяемых аппретов. Поэтому их применение для модификации поверхности волокон при армировании жаростойких композитов теряет смысл.
Для изменения морфологии поверхности волокна важно наличие высокотекстурированной оболочки. Анизотропия радиационных размерных изменений в графите приводит к развитой гофрированной морфологии поверхности волокна.
Наибольший размер гофрировки волокна получен в том случае, когда облучение волокон проводили ионами инертных газов (неона, аргона) или молекулярного азота с энергией от 15 до 30 кэВ, при флуенсе не менее 1018 ион/см2 и температуре от 150 до 250°С (рис. 3) [56].
Рис. 3.
РЭМ-изображения высокомодульного углеродного волокна из ПАН до (а) и после (б) облучения ионами аргона с энергией 30 кэВ при флуенсе 1019 ион/см2 при температуре волокна 250°С.

Описанный способ модификации поверхности высокомодульных углеродных волокон посредством изменения их поверхностной морфологии в виде гребневидных гофров с помощью облучения ионами неона, аргона или молекулярного азота с энергией 10–30 кэВ имеет не слишком большую производительность из-за малого перечного сечения ионных пучков с энергиями 10–30 кэВ. Этот недостаток преодолели при модификации поверхности облучением высокомодульного углеродного волокнистого материала широкоапертурным полиэнергетическим пучком легких ионов гелия со средней энергией ионов не более 3 кэВ, источником такого излучения служит плазменный ускоритель с сечением пучка не менее 100 см2, плотностью тока не менее 2 мА/см2 [57]. В таких условиях облучения текстурированная оболочка волокна испытывает анизотропные размерные изменения, что приводит к пластической деформации в виде упорядоченного гофрирования (рис. 4). Модифицированная поверхность значительно повысит степень реализации физико-механических свойств волокнистого наполнителя в композите с полимерной матрицей. В случае углерод-керамических композиционных материалов применение высокомодульных углеродных волокнистых наполнителей с модифицированной поверхностью позволяет осуществить армирование высокожесткой керамической матрицы без возникновения при термоциклировании недопустимо высоких внутренних напряжений в композите [13, 14].
Рис. 4.
РЭМ-изображение волокнистого материала “Кулон” из ПАН после облучения широкоапертурным полиэнергетическим пучком ионов гелия от ионного источника класса ускорителя с анодным слоем при температуре волокна более 150°С. Напряжение разряда в ионном источнике 3.5–4.5 кВ, ток разряда 0.2 А при давлении в камере с напуском гелия 0.2 Па. Длительность облучения 2 ч. Диаметр ионного пучка 100 мм.

Реализация предлагаемого способа модификации поверхности высокомодульного углеродного волокнистого материала позволила получить значительное (на два порядка) увеличение удельной поверхности при уменьшении энергии ускоренных ионов не менее чем на порядок и более чем стократном увеличении площади облучаемого волокнистого материала и, соответственно, значительном увеличении производительности.
ЗАКОНОМЕРНОСТИ И ПЕРСПЕКТИВЫ ВЫСОКОДОЗНОЙ ИОННО-ЛУЧЕВОЙ МОДИФИКАЦИИ
Описанные новые способы модификации волокон [56, 57] разработаны на основе систематических экспериментальных исследований и установленных закономерностей модификации поверхности углеродных волокон высокодозным ионным облучением в цикле работ [33–55]. Такого рода исследования продолжают как для выявления оптимальных условий модификации углеродных волокон, так и установления механизмов процесса.
Эксперименты проводили на масс-монохроматоре НИИЯФ МГУ, позволяющем проводить облучение пучками сепарированных по массам ионов газов с энергиями от 10 до 30 кэВ [30]. Высокая плотность ионного потока позволяет проводить высокодозное, с флуенсом 1018–1019 ион/см2, облучение за относительно короткое время, не более 1 ч. Мишени закрепляли в камере столкновений на держателе, позволяющем изменять температуру мишеней от –180 до 1000°С, а также варьировать углы падения ионов на мишень θ в пределах от 0° до 89°. На рис. 5 приведена схема ионного облучения углеродных волокон.
Рис. 5.
Геометрия облучения углеродных волокон: θ – угол падения ионов на мишень относительно нормали (ось z) к макроскопической поверхности мишени; азимутальный угол поворота мишени φ – угол в плоскости (xy) между проекцией направления ионного пучка и осью x [40].
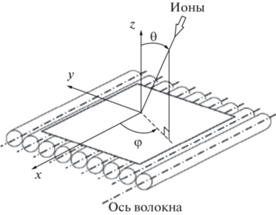
Образцы имели форму прямоугольных пластинок размерами 15 × 40 × 2 мм. Подготовка образцов состояла в ультразвуковой очистке, промывке в этаноле и вакуумном отжиге при температуре ~300°C. Облучение производили пучками ионов N+, ${\text{N}}_{2}^{ + }$ Ne+ и Ar+ c энергией от 10 до 30 кэВ. Плотность ионного тока достигала 0.4 мA/см2 при поперечном сечении пучка 0.35 см2. Для мониторинга состояния облучаемой поверхности в процессе облучения периодически измеряли коэффициент ионно-электронной эмиссии γ, определяемый как отношение тока электронов к току первичных ионов. Исследование кристаллической структуры поверхностного слоя материала проводили с помощью метода дифракции быстрых электронов на отражение на электронографе “ЭМР-102” при ускоряющем напряжении 50 кВ и токе пучка 50 мкА. Морфологию поверхности образцов до и после облучения исследовали с помощью растровых электронных микроскопов. Для исследований использовали также методы спектроскопии комбинационного рассеяния света и резерфордовского обратного рассеяния. Геометрию упорядоченных морфологических элементов измеряли с помощью лазерной гониофотометрии на специально разработанном стенде (рис. 6).
Рис. 6.
Схема измерения с помощью лазерной гониофотометрии. Пунктирной стрелкой отмечено направление ионного пучка при облучении мишени. На облученной области схематически показана ионно-индуцированная гофрообразная структура: L – период гофрированной структуры (шаг рельефа); Lг – длина гофра; β1, β2 – углы наклона граней гофров [48].
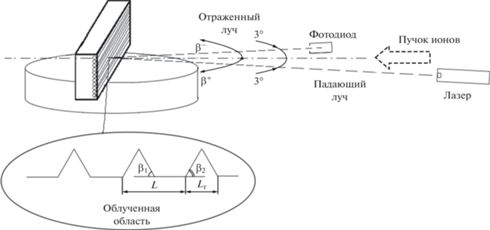
В [33, 36] в качестве мишеней использовали образцы однонаправленного композита КУП-ВМ (производство НИИграфит) на основе ПАН-волокна ВМН-4 с матрицей из бакелитового лака, фенольной смолы и пироуглерода. Температура высокотемпературной обработки материала составляла 2800°С, плотность композита 1.4 г/cм3. Армирующие углеродные волокна в материале были параллельны длинной стороне пластинок. Облучение производили пучком ионов ${\text{N}}_{2}^{ + }$ энергии 30 кэВ. Направление падения ионов было перпендикулярным оси углеродных волокон.
Установлено, что однонаправленная волокнистая морфология КУП-ВМ сохраняется при ионном облучении. На РЭМ-изображениях облученного композита можно отчетливо различить как волокна, так и матрицу (рис. 7). Картины дифракции при съемке вдоль и поперек углеродных волокон отражают анизотропию материала и отличаются друг от друга наличием (при съемке вдоль волокон) или отсутствием отражений базисными плоскостями графита. Облучение КУП-ВМ при комнатной температуре приводит к разупорядочению структуры, и дифракционная картина представляет собой аморфное гало (рис. 8в). Облучение при температурах выше некоторой температуры Ta (отмечена стрелкой на рис. 9) изменяет кристаллическую структуру. Электронограммы, полученных при Т > Tа при съемке как вдоль, так и поперек углеродных волокон, практически не отличаются и представляют собой систему из трех слегка размытых колец, характерных для изотропных графитов (рис. 8г). Таким образом было выявлено, что высокодозное ионное облучение приводит к потере анизотропии структуры поверхностного слоя композита КУП-ВМ.
Рис. 7.
РЭМ-изображения поверхности углерод-углеродного композита КУП-ВМ при съемке с наклоном образца 30° относительно нормали до (а) и после облучения по нормали ионами ${\text{N}}_{2}^{ + }$ энергии 30 кэВ при различных температурах: комнатная температура, на вставке изображение при съемке с поворотом образца вокруг нормали на 90° (б); Т = 100°C (в) и Т = 330°C (г), на вставке увеличенное в 20 раз изображение [33].

Рис. 8.
Электронограммы для углерод-углеродного композита КУП-ВМ: до облучения, направление пучка электронов параллельно (а) и перпендикулярно (б) углеродным волокнам композита; после облучения ионами ${\text{N}}_{2}^{ + }$ c энергией 30 кэВ при комнатной температуре (в) и при Т = 330°C (г) [33].

Рис. 9.
Температурные зависимости коэффициента ионно-электронной эмиссии γ при высокодозном облучении углерод-углеродного композита КУП-ВМ (1), высокоориентированного пирографита УПВ-1Т (2) и стеклоуглерода СУ-1300 (3) ионами ${\text{N}}_{2}^{ + }$ с энергией 30 кэВ [33].

Мониторинг облучения с помощью измерения ионно-электронной эмиссии позволяет, как и для других углеродных материалов [58, 59] определять температуру Ta, соответствующую скачку на зависимости γ(T), облучение ниже которой приводит к аморфному модифицированному слою, а выше – к изменению кристаллической структуры в результате рекристаллизации. Зависимость γ(Т) для композита КУП-ВМ проявляет двухступенчатый характер, обусловленный процессами динамического отжига радиационных нарушений в структурных составляющих композита. Положение “высокотемпературного” скачка на зависимости γ(T) КУП-ВМ является близким к значению Ta для высокоориентированного пирографита, тогда как “низкотемпературного” – к Ta для стеклоуглерода (рис. 9). Характер морфологии поверхности волокон сильно зависит от температуры, при которой проводили облучение. Облучение при комнатной температуре, когда происходит аморфизация, на поверхности волокон появляются продольные углубления, при повышении температуры, когда происходит рекристаллизация, можно наблюдать гофрирование волокон (рис. 7г). На увеличенном изображении, приведенном на вставке рис. 7г, видна правильная призматическая форма гофров, грани которых имеют шероховатость до 100 нм, а углы наклона гофров относительно оси волокна ~42°.
Зависимые от температуры облучаемого волокна эффекты аморфизации поверхностного слоя углеродного волокна из ПАН и гофрирования поверхности рекристаллизованного слоя были найдены также при высокодозном облучении композита КУП-ВМ ионами аргона и неона [35–38].
В [39–49] выявлено сильное влияние энергии ионов и существенные различия гофрирования в результате облучения ионами азота и ионами инертных газов. В последнем случае обнаружены экстремальные, с минимумом при 400°С, зависимости параметров гофрообразной структуры – доли поверхности волокна, покрытой гофрами, и угла их наклона (рис. 10). Найдено, в частности, что при высокодозном облучении ионами азота с энергией 15 и 30 кэВ и температуре облучаемого композита от 100 до 600°С, в отличие от облучения ионами инертных газов с такими же энергиями, основные параметры гофрированной структуры, такие как углы наклона гофров и их доля на поверхности волокна, практически не зависят от температуры композита. Переодичность гофров, как и в случае облучения ионами неона или аргона, составляет около 1 мкм. Углы наклона граней гофров относительно оси волокна составляют 30° и 40° при энергии ионов 15 и 30 кэВ соответственно. Предположительно, отличие температурных зависимостей углов наклона гофров и доли поверхности волокна, покрытой ими, от аналогичных зависимостей в случае облучения ионами инертных газов связано с особенностями динамического отжига радиационных нарушений в оболочке волокна из-за химической активности азота, с созданием связей С–N и большей долей аморфной составляющей, образующейся при облучении азотом.
Рис. 10.
Температурные зависимости углов наклона β граней гофров при облучении ионами ${\text{N}}_{2}^{ + }$ с энергией 30 (1) и 15 кэВ (2) и ионами Ar+ с энергией 30 (3) и 20 кэВ (4) углеродного волокна композита КУП-ВМ [49].

Диапазон углов наклона граней относительно оси волокна ионно-индуцированных гофров приходится на углы двойникования при пластической деформации кристаллитов графита оболочки углеродного волокна. Полученные температурные закономерности гофрирования позволили связать явление ионно-индуцированного гофрирования с анизотропными радиационно-индуцированными пластическими процессами формоизменения углеродных материалов, основными факторами которых являются уровень радиационных нарушений ν в числе смещений на атом (СНА) и температура T облучения [7]. При уменьшении уровня радиационных нарушений при соответствующем уменьшении энергии ионов эффект гофрирования уменьшается.
Происходящий при повышенных температурах динамический отжиг радиационных нарушений может и, как это следует из данных, полученных при облучении ионами неона или аргона при температуре облучения 400–450°С, существенно уменьшить эффект гофрирования. При достаточно низком уровне первичных радиационных нарушений гофрирование не происходит. Именно на эти температуры 400–500°С при нейтронном облучении графита приходится минимум радиационных дефектов [60] и минимум размерных изменений [61].
Достаточно высокий для гофрирования оболочки углеродного волокна из ПАН уровень радиационных нарушений ν при облучении ионами азота, неона или аргона достигается при энергиях порядка десятков кэВ, а для ионов гелия при энергиях около 1 кэВ. Это дает возможность гофрировать поверхность углеродных волокон из ПАН с помощью широкоапертурных высокопроизводительных ионных источников с низкими энергиями ионов [50, 57].
В работе [62] исследовали возможности гофрирования поверхности графитизированного и карбонизированного углеродного волокна из ПАН марки Zoltek PX35 ионами азота и аргона с энергией 30 кэВ, имеющего широкое коммерческое применение. Анализ поверхности и структуры образцов показал наличие гофрирования облученной поверхности как неграфитированного, так и графитированного волокна Zoltek PX35. Для облученных ионами азота неграфитированного и графитированного волокна характерен один и тот же наклон граней гофров, при отличающихся периодах следования и высотах гофров (рис. 11а, 11б).
Рис. 11.
РЭМ-изображения графитированного (а) и карбонизированного (б) волокна Zoltek PX35 после ионного облучения. Спектры комбинационного рассеяния света (в) графитированного (1, 2) и исходного (3, 4) волокна Zoltek PX35 до (1, 3) и после (2, 4) ионного облучения [62].

Облучение ионами азота как неграфитированного, так графитированного волокна Zoltek PX35 приводит к разупорядочению оболочки волокна, в результате которого спектры комбинационного рассеяния света после облучения становятся похожими на спектры для углеродного волокна из ПАН на начальном этапе карбонизации со значительной (до 6 ат. %) концентрацией азота. Это позволило предположить увеличение прочности на растяжение модифицированного слоя углеродного волокна при некотором уменьшении модуля упругости, имеющее место для других углеродных материалов.
Результаты работ [54, 55] показывают, что ионно-индуцированная гофрированная структура на поверхности углеродных волокон из ПАН является термостойкой, наличие такого рельефа приводит к значительному увеличению удельной поверхности и практически не влияет на механические свойства (рис. 12, табл. 2).
Рис. 12.
РЭМ-изображения углеродного волокна из ПАН после высокодозного облучения ионами Ne+ с энергией 30 кэВ при температуре 160°C (а) и последующей термообработке при температуре 2400°С (б) [54].

Таблица 2.
Диаметр, предел прочности (σ), модуль упругости (Е), относительное удлинение (ε) и удельная поверхность высокомодульного углеродного волокна из ПАН до и после высокодозного облучения ионами аргона энергии 30 кэВ при температуре 250°С [54]
Углеродное волокно | Диаметр, мкм | σ, ГПа | Е, ГПа | ε, % | Удельная поверхность, м2/г |
---|---|---|---|---|---|
Исходное | 4.6 ± 0.3 | 4.4 ± 0.6 | (4.6 ± 0.5) × 102 | 1.0 ± 0.1 | 0.5–1.5 |
После облучения | 4.9 ± 0.3 | 4.2 ± 0.7 | (4.5 ± 0.4) × 102 | 0.9 ± 0.1 | 107.0 |
В [51–53] приведены результаты исследования и сравнение ионно-индуцированной морфологии на поверхности углеродных волокон из вискозы и ПАН (рис. 13). Видно, что на поверхности волокон из вискозы образуется пористая губчатая структура с тонкими стенками. Ее кардинальное отличие от возникшей при тех же условиях облучения гофрированной структуры на поверхности волокон из ПАН обусловлено значительными различиями структуры углеродных волокон из ПАН и вискозы.
Рис. 13.
РЭМ-изображения углеродных волокон из вискозы в составе преформы композита “ФЭБУС” (а) и углеродных волокон из ПАН в составе композита КУП-ВМ (б) после облучения ионами Ar+ энергии 30 кэВ при температуре 400°С

Влияние структуры оболочки углеродного волокна на появление и тип поверхностного рельефа рассматривали также в [63–65]. Найдено, что в зависимости от формы профиля первичных радиационных нарушений (зависимости числа смещений на атом ν от глубины х в мишени) геометрические параметры периодического рельефа для углеродных волокон из ПАН могут изменяться [63]. Когда максимум радиационных нарушений находится в глубине мишени, направление чередования гофров изменяется и становится поперечным (гофрами, расположенными перпендикулярно оси волокна). Изменения рельефа поверхности углеродного волокна из ПАН, связанные с релаксацией ионно-индуцированных механических напряжений через пластические процессы двойникования, лучше всего иллюстрирует сравнение результатов облучения ионами гелия с энергией 3 и 30 кэВ (рис. 14).
Рис. 14.
РЭМ-изображения углеродных волокон из ПАН после облучения ионами He+ c энергией 30 (а) и 3 (б) кэВ при температуре >200°С. Профили смещений на атом (СНА) для случаев облучения ионами Ar+ с энергией 30 кэВ (1), He+ с энергией 3 кэВ (2) и He+ с энергией 30 кэВ. Флуенс облучения >3 × 1018 см–2 [63].

Сравнение результатов облучения углеродных волокон из ПАН и вискозы с различными значениями флуенса, показало значительную разницу в наблюдаемом рельефе [64]. Для углеродных волокон на основе ПАН изменение морфологии поверхности с увеличением флуенса включает последовательную трансформацию радиальной наноразмерной (<100 нм) гофрированной структуры в продольную субмикронного (0.1–1.0 мкм) размера. Для углеродного волокна из вискозы наблюдаются две стадии формирования морфологии: образование наноразмерного гребневидного рельефа без четкого направления роста и периодичности, а при увеличении флуенса облучения их распыление с появлением пористой губчатой структуры с тонкими стенками (рис. 15). Неоднородность структуры вискозного волокна и, с другой стороны, общая низкая степень совершенства его поверхностной структуры по сравнению с углеродными волокнами из ПАН обуславливают отсутствие значительных механических напряжений в оболочке и как следствие отсутствие ярко выраженных процессов релаксации через пластическую деформацию при ионном облучении.
Рис. 15.
Разновидности ионно-индуцированной морфологии поверхности углеродных волокон из ПАН (ВМН-4) и вискозы (ТГН-2МК), облученных ионами аргона с энергией 30 кэВ при температуре 200°C [64] при различных дозах: 0 (а); 1018 (б); 3 × 1018 см–2 (в).
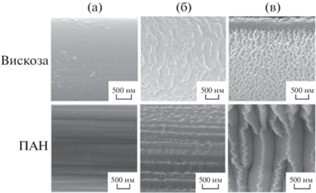
Влияние структуры оболочки материала на образование рельефа на поверхности углеродных волокон проявляется не только для углеродных волокон из вискозы. Облучение ионами C+ с энергией 30 кэВ не приводит к гофрированию поверхности, углеродные волокна из ПАН остаются гладкими, в отличие от облучения ионами инертных газов и азота [65]. Необходимая для ионно-индуцированного гофрирования текстура в имплантированном углеродном слое в описанных условиях облучения не формируется.
ЗАКЛЮЧЕНИЕ
Модификация углеродных волокон была и остается актуальной для широкой области прикладных задач. Предлагаемое углеродное высокомодульное волокно с модифицированной поверхностью необходимо для создания композита, требуемая прочность которого формируется в процессе совмещения основных его компонентов: армирующих углеродных волокон и матричного материала. Оптимальное адгезионное взаимодействие, сцепление между матрицей и волокном позволяет максимально нагружать полученный композит.
Проведенное обобщение накопленного опыта по модификации углеродных волокон показывает, что с помощью ионно-лучевой обработки можно получить развитый рельеф поверхности волокон с различной геометрией: как случайный вискерообразный, так гофрообразый, ориентированный поперек или вдоль оси волокна. Такая обработка выгодно отличается от методов вискеризации волокна как многообразием геометрии границы раздела композита и подложки, так и тем, что снимается проблема адгезии вискеров с волокном.
Ионно-лучевая обработка позволяет модифицировать также структуру поверхности от аморфизованной до упорядоченной с разной степенью графитации и дефектности. Облучение химически активными ионами может приводить к активизации поверхности за счет образования, например, нитридов и оксидов углерода.
При рассмотрении явления ионно-индуцированного гофрирования как перспективного метода модификации углеродного волокна для технологии получения углерод-углеродных и углерод-керамических композитов выявлено, что выбор ионов азота для реализации метода представляется более предпочтительным, благодаря менее жестким требованиям к температуре облучаемого волокна. Для гофрирования необходим лишь нагрев волокна выше температуры динамического отжига радиационных нарушений. К значительному увеличению производительности приводит метод с высокодозным облучением ионами гелия низких энергий.
Представляется, что ионно-лучевые методы модификации поверхности углеродных волокон могут быть полезными не только для композитов, но и для других применений.
Список литературы
Нагорный В.Г., Котосонов А.С., Островский В.С., Дымов Б.К., Лутков А.И., Ануфриев Ю.П., Барабанов В.Н., Белогорский В.Д., Кутейников А.Ф., Виргильев Ю.С., Соккер Г.А. Свойства конструкционных материалов на основе углерода. Справочник / Под ред. В.П. Соседова. М.: Металлургия, 1975. 336 с.
Островский В.С., Виргильев Ю.С., Костиков В.И., Шипков Н.Н. Искусственный графит. М.: Металлургия, 1986. 272 с.
Фитцер Э., Дифендорф Р., Калнин И., Ягер X., Хейес Б., Стензенбергер К., Адаме Д., Брунш К., Бергман X., Гастингс Г., Нагабхушанам Т., Зенг X., Ким С., Ри Б. Углеродные волокна и углекомпозиты. Пер. с англ. / Ред. Э. Фитцер. М.: Мир, 1988. 336 с.
Dresselhaus M.S., Dresselhaus G., Sugihara K., Spain I.L., Goldberg H.A. // Graphite Fibers and Filaments. Springer Series in Materials Science. Volume 5. Springer-Verlag Berlin Heidelberg, 1988. 382 p. https://www.doi.org/10.1007/978-3-642-83379-3
Pierson H.O. Handbook of Carbon, Graphite, Diamond and Fullerenes. Noyes Publ., Park Ridge NJ, 1993. 415 p.
Фиалков А.С. Углерод, межслоевые соединения и композиты на его основе. М.: Аспект Пресс, 1997. 718 с.
Virgil’ev Yu.S. Kalyagina I.P. // Inorganic Materials. 2004. V. 40. Suppl. 1. P. S33. https://www.doi.org/10.1023/B:INMA.0000036327. 90241.5a
Варшавский В. Я. Углеродные волокна М.: Варшавский, 2007. 500 с.
Мэтьюз Ф., Ролингс Р. Композитные материалы. Механика и технология. М.: Техносфера, 2004. 408 с.
Gibson R.F. // Compos. Struct. 2010. V. 92. P. 2793. https://www.doi.org/10.1016/j.compstruct.2010.05.003
Мелешко А.И., Половников С.П. Углерод, углеродные волокна, углеродные композиты. М.: САЙН-ПРЕСС, 2007. 192 с.
Yun G., Tang S.-Y., Lu H., Zhang S., Dickey M.D., Li W. // Small Sci. 2021. V. 1. Iss. 6. P. 2000080. https://www.doi.org/ 10.1002/smsc.202000080
Черненко Н.М. // Перспективные материалы. 1999. № 6. С. 78.
Черненко Н.М. // Современные проблемы производства и эксплуатации углеродной продукции. Челябинск: Библиотека А. Миллера, 2000. С. 217.
Черненко Д.Н., Черненко Н.М. Щербакова Т.С. Грудина И.Г. Углеродкерамический волокнисто-армированный композиционный материал и способ его получения // Патент RU № 2684538. Опубл. 09.04.2019.
Sager R.J., Klein P.J., Lagoudas D.C., Zhang Q., Liu J., Dai L. // Compos. Sci. Technol. 2009. V.69. P. 898. https://www.doi.org/10.1016/j.compscitech.2008.12.021
Garcia E.J., Wardle B.L., Hart A.J., Yamamonj N. // Compos. Sci. Technol. 2008. V. 68. № 9. P. 2034. https://www.doi.org/10.1016/j.compscitech.2008.02.028
Sharma S.P., Lakkad S.C. // Surf. Coat. Technol. 2010. V. 205. P. 350. https://www.doi.org/10.1016/j.surfcoat.2010.06.055
Wickss S.S., Guzman R., Wardle B.L. // Compos. Sci. Technol. 2010. V. 70. P. 20. https://www.doi.org/10.1016/j.compscitech.2009.09.001
Song Q., Li K.-Z., Li H.-L., Li H.-J., Chang R. // Carbon 2012. V. 50. P. 3949. https://www.doi.org/10.1016/j.carbon.2012.03.023
Wu S., Liu Y., Ge Y., Ran L., Peng K, Yi M. // Composites A. 2016. V. 90. P 480. https://www.doi.org/10.1016/j.compositesa.2016.08.023
Kinloch I.A., Suhr J., Lou J., Young R.J., Ajayan P.M. // Science. 2018. V. 362. P. 547. https://www.doi.org/10.1126/science.aat7439.
Chechenin N.G., Chernykh P.N., Vorobyeva E.A., Timofeev O.S. // Appl. Surf. Sci. 2013. V. 275. P. 217. https://www.doi.org/10.1016/j.apsusc.2012.12.162
Воробьева Е.А., Макаренко И.В., Макунин А.В., Трифонов В.А., Чеченин Н.Г. // Поверхность. Рентген., синхротр. и нейтрон. исслед. 2015. № 8. С. 29. https://www.doi.org/10.7868/S020735281508017X
Kobzev V.A., Chechenin N.G., Bukunov K.A., Vorobyeva E.A., Makunin A.V. // Materials Today: Proceedings. 2018. V. 5. № 12. P. 26096. https://www.doi.org/10.1016/j.matpr.2018.08.036
Kushkina K.D., Shemukhin A.A., Vorobyeva E.A., Bukunov K.A., Evseev A.P., Tatarintsev A.A., Maslakov K.I., Chechenin N.G., Chernysh V.S. // Nucl. Instrum. Methods Phys. Res. B. 2018. V. 430. P. 11. https://www.doi.org/10.1016/j.nimb.2018.05.038
Новиков Л.С., Воронина Е.Н., Черник В.Н., Чеченин Н.Г., Макунин А.В., Воробьева Е.А. // Поверхность. Рентген., синхротр. и нейтрон. исслед. 2016. № 6. С. 49. https://www.doi.org/10.7868/S0207352816060147
Vorobyeva E.A., Chechenin N.G., Makarenko I.V., Kepman A.V. // J. Composites Sci. 2017. V. 1. № 6. https://www.doi.org/10.3390/jcs1010006
Vorobyeva E.A., Evseev A.P., Petrov V.L., Shemukhin A.A., Chechenin N.G. // Moscow University Physics Bull. 2021. V. 76. № 1. P. 29. https://www.doi.org/10.3103/s0027134921010112
Mashkova E.S., Molchanov V.A. Medium-Energy Ion Reflection from Solids. Amsterdam: North-Holland, 1985. 444 p.
Лигачева Е.А., Галяева Л.В., Гаврилов Н.В. // Физика и химия обработки материалов. 2006. № 1. С. 46.
Ivanov M.V., Gavrilov N.V., Belyh T.A., Ligacheva E.A., Galijeva L.V., Ligachev A.E., Sohoreva V.V. // Surf. Coat. Technol. 2007. V. 201. P. 8326. https://www.doi.org/10.1016/j.surfcoat.2006.12.034
Андрианова Н.Н., Борисов А.М., Виргильев Ю.С., Машкова Е.С., Немов А.С., Питиримова Е.А., Тимофеев М.А. // Поверхность. Рентген., синхротр. и нейтрон. исслед. 2008. № 5. С. 59
Andrianova N.N., Borisov A.M., Mashkova E.C., Virgiliev Yu.S. // Nucl. Instrum. Methods Phys. Res. B. 2009. V. 267. P. 2778. https://www.doi.org/10.1016/j.nimb.2009.05.021
Авилкина В.С., Андрианова Н.Н., Борисов А.М., Виргильев Ю.С., Машкова Е.С., Питиримова Е.А., Тимофеев М.А. // Физика и химия обработки материалов. 2009. № 5. С. 21.
Andrianova N.N., Borisov A.M., Mashkova E.S., Virgiliev Yu.S. // J. Spacecraft Rockets. 2011. V. 48. P. 45. https://www.doi.org/10.2514/1.49462
Andrianova N.N., Borisov A.M., Mashkova E.S., Virgiliev Yu.S. // Nucl. Instrum. Methods Phys. Res. B. 2011. V. 269. P. 861. https://www.doi.org/10.1016/j.nimb.2010.12.063
Авилкина В.С., Андрианова Н.Н., Борисов А.М., Виргильев Ю.С., Машкова Е.С. // Поверхность. Рентген., синхротр. и нейтрон. исслед. 2012. № 8. С. 3
Andrianova N.N., Borisov A.M., Mashkova E.S., Parilis E.S., Virgiliev Yu.S. // Horizons in World Physics. NY, USA: Nova Science Publishers, Inc., 2013. V. 280. P. 171
Андрианова Н.Н., Борисов А.М., Виргильев Ю.С., Машкова Е.С., Петров Д.В. // Поверхность. Рентген., синхротр. и нейтрон. исслед. 2014. № 6. С. 6.
Андрианова Н.Н., Борисов А.М., Машкова Е.С., Шульга В.И. // Поверхность. Рентген., синхротр. и нейтрон. исслед. 2016. № 4. С. 51.
Аникин В.А., Борисов А.М., Макунин А.В., Машкова Е.С., Овчинников М.А. // Приборы. 2017. № 12. С. 46.
Andrianova N.N., Borisov A.M., Kazakov V.A., Mashkova E.S., Ovchinnikov M.A., Savushkina S.V., Chernenko N.M. // J. Phys.: Conf. Ser. 2017. V. 941. P. 012028. https://www.doi.org/10.1088/1742-6596/941/1/012028
Андрианова Н.Н., Аникин В.А. Борисов А.М., Машкова Е.С., Казаков В.А., Овчинников М.А., Савушкина С.В. // Изв. РАН. Сер. физич. 2018. Т. 82. № 2. С. 140.
Аникин В.А., Борисов А.М., Макунин А.В., Машкова Е.С., Овчинников М.А. // Ядерная физика и инжиниринг. 2018. Т.9. № 2. С. 122.
Borisov A.M., Chechenin N.G., Kazakov V.A., Mashkova E.S., Ovchinnikov M.A. // Nucl. Instrum. Methods Phys. Res. B. 2019. V. 460. P. 132. https://www.doi.org/10.1016/j.nimb.2019.03.045
Andrianova N.N., Borisov A.M., Makunin A.V., Mashkova E.S., Ovchinnikov M.A. // J. Phys.: Conf. Ser. 2019. V. 1396. P. 012003. https://www.doi.org/10.1088/1742-6596/1396/1/012003
Андрианова Н.Н., Борисов А.М., Казаков В.А., Макунин А.В., Машкова Е.С., Овчинников М.А. // Поверхность. Рентген., синхротр. и нейтрон. исслед. 2020. № 3. С. 20.
Андрианова Н.Н., Борисов А.М., Казаков В.А., Макунин А.В., Машкова Е.С., Овчинников М.А. // Изв. РАН. Сер. физич. 2020. Т. 84. № 6. С. 857.
Andrianova N.N., Anikin V.A., Borisov A.M., Gorina V.A., Makunin A.V., Mashkova E.S., Ovchinnikov M.A., Cheblakova E.G., Sleptsov V.V. // J. Phys.: Conf. Ser. 2019. V. 1313. P. 012001. https://www.doi.org/10.1088/1742-6596/1313/1/012001
Андрианова Н.Н., Бейлина Н.Ю., Борисов А.М., Машкова Е.С., Черненко Д.Н., Черненко Н.М. // Поверхность. Рентген., синхротр. и нейтрон. исслед. 2014. № 3. С. 15.
Андрианова Н.Н., Бейлина Н.Ю., Борисов А.М., Машкова Е.С., Черненко Д.Н., Черненко Н.М. // Вакуумная техника и технология. 2014. Т. 23. № 1. С. 85.
Borisov A.M., Makunin A.V., Mashkova E.S., Kazakov V.A., Ovchinnikov M.A., Sleptsov V.V. // J. Phys.: Conf. Ser. 2018. V. 1121. P. 012008. https://www.doi.org/10.1088/1742-6596/1121/1/012008.
Anikin V.A., Andrianova N.N., Borisov A.M., Mashkova E.S., Ovchinnikov M.A., Savushkina S.V., Chernenko D.N., Chernenko N.M. // J. Phys.: Conf. Ser. 2017. V. 941. P. 012029. https://www.doi.org/:10.1088/1742-6596/941/1/012029
Borisov A.M., Gorina V.A., Mashkova E.S., Ovchinnikov M.A., Cheblakova E.G., Chernenko D.N., Chernenko N.M. // Materials Today: Proceedings. 2018. V. 5. P. 26058. https://www.doi.org/10.1016/j.matpr.2018.08.029
Черненко Н.М., Черненко Д.Н., Бейлина Н.Ю., Елизаров П.Г., Борисов А.М., Машкова Е.С., Андрианова Н.Н. // Патент RU № 2 560 362. Опубл. 20.08.2015.
Борисов А.М., Андрианова Н.Н., Аникин В.А., Машкова Е.С., Овчинников М.А., Черненко Д.Н., Черненко Н.М., Шульгина Ю.М. // Патент RU № 2 689 584. Опубл.: 28.05.2019.
Borisov A.M., Mashkova E.S. // Nucl. Instrum. Methods Phys. Res. B. 2007. V. 258. P. 109. https://www.doi.org/10.1016/j.nimb.2006.12.078
Борисов А.М., Виргильев Ю.С., Машкова Е.С. // Поверхность. Рентген., синхротр. и нейтрон. исслед. 2008. № 1. С. 58.
Платонов П.А., Штромбах Я.И., Карпухин В.И., Виргильев Ю.С., Чугунов О.К., Трофимчук Е.И. // Атомноводородная энергетика и технология. Вып. 6. М.: Энергоатомиздат, 1984. С. 77.
Виргильев Ю.С., Чугунова Т.К., Макарченко В.Г., Муравьева Е.В. // Изв. АН СССР. Сер. Неорганические материалы. 1984. Т. 20. № 8. С. 1378.
Андрианова Н.Н., Борисов А.М., Высотина Е.А., Тимофеев М.А., Машкова Е.С., Овчинников М.А. // Поверхность. Рентген., синхротр. и нейтрон. исслед. 2021. № 3. С. 24.
Andrianova N.N., Borisov A.M., Mashkova E.S., Ovchinnikov M.A., Timofyev M.A., Vysotina E.A. // Vacuum. 2021. V. 188. P. 110177. https://www.doi.org/10.1016/j.vacuum.2021.110177
Andrianova N.N., Borisov A.M., Makunin A.V., Mashkova E.S., Ovchinnikov M.A., Vysotina E.A. // J. Phys.: Conf. Ser. 2020. V. 1713. P. 012005. https://www.doi.org/10.1088/1742-6596/1713/1/012005
Борисов А.М., Машкова Е.С., Тимофеев М.А., Овчинников М.А. // Поверхность. Рентген., синхротр. и нейтрон. исслед. 2022. № 5. С. 26.
Дополнительные материалы отсутствуют.
Инструменты
Поверхность. Рентгеновские, синхротронные и нейтронные исследования