Приборы и техника эксперимента, 2021, № 3, стр. 129-137
СТЕНД ЛАЗЕРНОГО КАТАЛИЗА
В. Н. Снытников a, *, Вл. Н. Снытников a, Н. С. Масюк a, **, Т. В. Маркелова a, В. Н. Пармон a
a Институт катализа им. Г.К. Борескова СО РАН
630090 Новосибирск, просп. Академика Лаврентьева, 5, Россия
* E-mail: valsnyt@gmail.com
** E-mail: nad0292@yandex.ru
Поступила в редакцию 27.10.2020
После доработки 06.11.2020
Принята к публикации 09.11.2020
Аннотация
В Институте катализа СО РАН создан стенд для изучения фотохимического и теплового воздействия инфракрасного лазерного излучения на двухфазную газопылевую среду из смесей легких углеводородов и каталитически активных наночастиц. Стенд содержит реакторы с потоками газов от 10 до 1000 л/ч и лазерным излучением интенсивностью от 10 до 105 Вт/см2, СО2-лазеры, аппаратуру анализа продуктов реакций и другую диагностическую технику, а также секцию лазерного синтеза оксидных нанопорошков производительностью до 1.5 г/ч. Один из СО2-лазеров – непрерывного излучения, мощностью до 120 Вт, другой – импульсно периодический с максимальной средней мощностью 450 Вт. Разработанные реакторы с лазерным излучением позволяют изучать ламинарные, вихревые и переходные течения газов с химическими реакциями. Для измерения температуры газа до 1100°С в поле излучения лазера до 103 Вт/см2 использованы термопары с электродами из молибдена и меди. Изучение воздействия лазерного излучения на химически активную среду ведется в комплексе с вычислительными экспериментами на кластере Института катализа и Сибирского суперкомпьютерного центра СО РАН.
ВВЕДЕНИЕ
Излучение СО2-лазера эффективно поглощается в газовых потоках этиленом, аммиаком, элегазом и рядом других соединений, а также наночастицами различной природы. Оно фотохимическим и тепловым образом способно стимулировать гомогенные и гетерогенные каталитические реакции у химически активных реагентов. Протекающие физико-химические процессы в среде с неравновесным излучением мы определяем как лазерный катализ [1–3].
Одной из востребованных задач лазерного катализа является получение водорода из легких алканов и создание технологии его производства на малотоннажных установках с улучшенными экологическими и экономическими показателями. В качестве сырья наиболее важно использование природного газа. Помимо водорода необходимо одновременно производить и многие другие высоко маржинальные полупродукты. Среди них этилен, пропилен, бутадиен и другие соединения.
Для создания новой химической технологии совместного получения водорода и указанных соединений требуются новые решения по активации метана и других легких алканов в смесях углеводородов с водородом. В числе перспективных идей решения этой проблемы предлагается использовать излучение СО2-лазеров для управления процессами пиролиза легких алканов [1–3]. Возможность лазерного управления пиролизом углеводородов связана со способностью этилена поглощать инфракрасное (и.к.) излучение на длине волны 10.6 мкм в полосе генерации СО2-лазера. Сам пиролиз носит пороговый характер по интенсивности и температуре стенок реактора. Кроме того, в качестве сенсибилизаторов поглощения лазерного излучения могут служить и наночастицы различной химической природы, в том числе имеющие каталитическую активность, с созданием в реакторе двухфазной газопылевой среды [4].
Ранее, в 70-х и 80-х годах двадцатого века, проводились многочисленные работы в направлениях лазерной фото- и термохимии [5, 6]. Для плотного газа с термическим нагревом излучением отмечалось, что процессы идут как фотохимические с протеканием многих нелинейных явлений, трудно поддающихся интерпретации [7]. Одна из причин этих трудностей состоит в неизотермичности газа с изменением по объему оптической плотности и поглощательной способности среды. Для такой среды важно выделить фотохимические процессы, индуцированные лазерным излучением, на фоне термических явлений, связанных с нагревом газовой смеси [8].
Решение этой сугубо нелинейной задачи, которая встречается также в нелинейной спектроскопии для лазерного излучения в многокомпонентных газовых средах [9], лежит на пути использования численных моделей CFD (Сomputational Fluid Dynamics) динамики химически активных сред с поглощением и переносом излучения [10]. Современные работы по воздействию лазерного излучения на среды связаны, в основном, с лазерным CVD (Chemical Vapour Deposition) [11], а также с суперкомпьютерным моделированием химических процессов в реакторах [12]. В настоящее время имеется большой спрос на экспериментальные данные в такой сложной области, как воздействие лазерного излучения на многокомпонентную двухфазную среду с наночастицами, поверхность которых обладает каталитической активностью.
В данной работе мы представляем созданный нами в Институте катализа (ИК) СО РАН стенд лазерного катализа, на котором изучаются фотохимические и тепловые воздействия на двухфазную газопылевую среду из реакционноспособных смесей углеводородов.
СОСТАВ СТЕНДА, ОБОРУДОВАНИЕ И ЕГО НАЗНАЧЕНИЕ
Экспериментальный стенд лазерного катализа состоит из пяти секций (рис. 1): лазерной, лазерного синтеза наночастиц, химического анализа, зоны реакторов, секции газоподачи. Рассмотрим каждую из них в отдельности.
Рис. 1.
Схема стенда лазерного катализа. 1 – лазерная секция; 2 – секция лазерного испарения; 3 – секция химического анализа; 4 – реакторные зоны; 5 – секция газоподачи; ИП – источник питания, Л – лазер, БК – блок контроля, ОП – оптический переключатель, ВН – вакуумные насосы, ИР – измеритель-регулятор расходов, ФП – формирователь потоков.

Лазерная секция
В эту секцию входят непрерывный и импульсно-периодический лазеры, блоки их питания, блоки контроля мощности и спектрофотометр.
Непрерывный газоразрядный СО2-лазер ЛГ100-2М создан в Институте катализа СО РАН и имеет максимальную выходную мощность до 120 Вт на частоте 944.2 см–1 (мода ТЕМ00) и диаметр пучка на выходе 8 мм. Частота генерации лазера попадает в диапазон частот, на которых поглощает этилен. Предусмотрена возможность перестройки резонатора с изменением частоты излучения от 938 до 949 см–1. Интенсивность лазерного излучения в реакционных зонах меняется как изменением общей мощности, так и путем изменения диаметра лазерного луча от 0.2 до 1.2 см с помощью специальных оптических схем.
Блок контроля (БК) излучения содержит делительные оптические элементы, трассирующий лазер с длиной волны 0.65 мкм и датчики мощности излучения. Непрерывный контроль мощности на выходе из лазера осуществлялся с использованием ZnSe делительной пластины с коэффициентом отражения 1%, и измерителем мощности излучения LM2 (“Карл Цейс”, ГДР).
С лазера предусмотрен вывод излучения в секцию лазерного синтеза наночастиц с помощью оптического переключателя.
Второй используемый лазер – газоразрядный импульсно-периодический СО2-лазер ROFIN SC 30 (Rofin-Sinar UK Ltd, England) с максимальной частотой импульсов 100 кГц и максимальной средней мощностью 450 Вт. Длина волны излучения 10.6 мкм. Диаметр лазерного луча на выходе из лазера – 8 мм. Непрерывный контроль мощности осуществлялся с использованием встроенного в лазер датчика и вольтметра В7-22А. Блок контроля позволял вводить в схему трассировочное излучение и измерять форму и частоту импульсов излучения (рис. 2). Для этого использовался и.к.-датчик ФСГ-22А (Ge–Au, 78 K). Временное разрешение датчика с учетом электрической схемы составило 0.65 мкс. Сигнал поступал на осциллограф С1-72.
Рис. 2.
Осциллограмма импульсов излучения длительностью 10 мкс в одном из режимов генерации ROFIN SC 30. Коэффициент заполнения – 42%; масштаб по горизонтали – 10 мкс/деление.
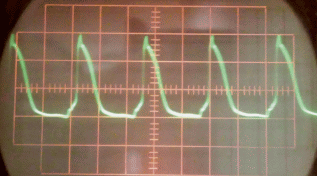
На стенде используются зеркала Cu с защитным покрытием CeF3, оптические окна и линзы из ZnSe с прозрачностью >99% для 10.6 мкм и зеркала на основе Si (ULO Optics, Israel). Переключение оптических трасс (ОП) на стенде осуществляется с помощью подвижных зеркал на высокоточных направляющих.
Спектр излучения обоих лазеров во всех экспериментах регистрировался на и.к.-спектрометре “Инфралюм” ФТ-801 (Симекс, Россия) с полосой чувствительности 550–5500 см–1 и спектральным разрешением 0.5 см–1. Спектрометр по оптическим трассам подключен к блоку контроля одного из лазеров.
Использование СО2-лазеров при пиролизе углеводородов на стенде лазерного катализа имеет несколько преимуществ [1]:
– позволяет снизить температуру стенок реактора по сравнению с традиционным и плазмохимическим пиролизом, который проходит при температуре выше 1000°C;
– уменьшает количество нежелательных продуктов, таких как графит, ацетилен, или более тяжелых продуктов конденсации;
– увеличивает выход целевых продуктов (водорода, этилена, пропилена и т.д.) без дальнейшего разложения продуктов до CO2 по сравнению с окислительным пиролизом.
Импульсно-периодическое излучение СО2-лазера позволяет снизить общую плотность мощности излучения и добиться быстрого охлаждения реакционной смеси с закалкой компонентного состава без применения специального оборудования. Секция позволяет изучать зависимость эффективности пиролиза от частоты генерации лазера.
Секция лазерного синтеза наночастиц
Секция включает в себя стальную вакуумируемую камеру объемом ~20 л с испарительным блоком внутри, оптическую систему контроля и подсветки, схему дозированной подачи различных газов или их смеси, аппаратуру для измерения давления (вакуума), узел ввода и фокусировки лазерного излучения, вакуумный пост на основе двух насосов 2НВР-5ДМ и азотной ловушки. Вакуумная камера с рабочим диапазоном давлений 10–2–103 Торр имеет окно ∅200 мм для установки испарительного блока с образцами, окна с оптическими фильтрами для контроля процесса, подвижный вакуумный ввод излучения с линзой из ZnSe ∅28 мм и возможным фокусным расстоянием 80–200 мм. Давление в камере контролируется вакуумметрами: модель 11201 (Россия) и ВИТ-2 с лампой ПМТ-4М.
Испарительный блок состоит из цилиндрической камеры (материал Д16Т) с лабиринтной коаксиальной системой сепарации наночастиц по размерам и выходом на фильтр для осаждения частиц нужного размера. Газ-носитель частиц вводится в испарительный блок через медное сопло соосно с фокусируемым на мишень излучением. Далее газ уходит через фильтр в систему вакуумной откачки. В экспериментах используются беззольные бумажные фильтры (АО “Экрос”, Россия) диаметром 110 мм, заменяемые после каждого испарения. Часть испарительного блока в зоне установки мишеней изготовлена из кварцевого стекла, обеспечивающего визуальный контроль процесса. Мишени (таблетки из оксидов различных материалов) помещаются в подвижные тигли с вакуумным вводом.
Характерные параметры установки: давление газа в режиме испарения 0.03–0.9 атм; расход газа 30–300 нл/ч; мощность подаваемого излучения 20–110 Вт; пятно фокусировки на мишени 0.3–2.0 мм; производительность процесса 0.5–1.5 г/ч; размеры получаемых наночастиц 2–30 нм (зависит от газа-носителя и его давления в камере).
Типичные материалы, используемые для получения нанопорошков: ZrO2, Al2O3, SiO2 и др., в том числе с легированием Cr, Mn, Fe, SiO2, сложные оксиды на основе Zr-Y-Yb, образцы метеоритов. Детальный анализ получаемых результатов проводится на комплексе диагностических установок ИК СО РАН.
На рис. 3 в качестве иллюстрации приведена типичная фотография нанопорошка CeO2, полученного при мощности лазерного излучения 110 Вт. Газ-носитель He/O2, суммарное давление 0.04 атм, расход He/O2 – 173 + 3.6 л/ч. Наночастицы представляют собой смесь ограненных нанокристаллитов размером 4–6 нм.
Отметим, что прототип установки и основные диагностики наноматериалов были ранее описаны нами в [13].
Секция химического анализа
Стенд оборудован газовыми хроматографами, позволяющими детектировать основные реагенты и продукты реакции пиролиза алканов: CH4, C2H4, C2H6, C2H2, C3H8, C3H6, C4H10, C5H6, C6H6, H2.
Анализ содержания водорода в смеси осуществляется с помощью газоанализатора “Тест-1” либо хроматографа ЛХМ-80 с насадочной колонкой 2 м × 3 мм, сорбент NaX, с Ar в качестве газа-носителя.
Анализ углеводородов С1-С6 проводился на газовом хроматографе “Кристалл 5000” (Хроматэк, Россия) с капиллярной колонкой Agilent Techno-logies 50 м × 0.53 мм, сорбент HP-Al-KCl, в потоке He в качестве газа-носителя.
Реакторные зоны
Все реакторы, использованные в стенде лазерного катализа, были сконструированы и созданы в ИК СО РАН. С помощью трех различных конструкций (рис. 4) были реализованы режимы ламинарного течения с расходом газов до 10 л/ч, вихревого течения и переходные режимы от ламинарного к турбулентному с расходом газов до 400 л/ч. Корпус всех реакторов выполнен из нержавеющей стали 12Х18Н10Т, толщина стенок 2 мм. Оптическими вводами лазерного излучения служили пластины из просветленного ZnSe с коэффициентом пропускания >99%. Все реакторы снабжены вводами для термопар, внешними нагревателями спирального типа мощностью от 300 до 1400 Вт со слоем теплоизоляции из минеральной ваты.
Рис. 4.
Схемы реакторов: а – с ламинарным течением до 10 л/ч и б – с вихревыми течениями газа (1 – оптические окна; 2 – вводы защитного газа; 3 – вводы смесей реакционных газов; 4 – газовые диафрагмы; 5 – вывод газовой смеси; 6 – термопарные вводы; 7 – зона нагревателя с теплоизоляцией); в – опытно-демонстрационного реактора (о.д.р.: 8 – цилиндрический стальной канал пиролиза; 9 – оптический канал для ввода излучения CO2-лазера; 10 – каналы подачи и предварительного нагрева газов; 11 – приемно-охлаждающий блок; 12 – выхлоп в атмосферу; 13 – вакуумный насос; 14 – выход на хроматограф “Кристалл-5000.2”; 15 – сменная стальная диафрагма; 16 – тепловые источники; 17 – оптические вводы).
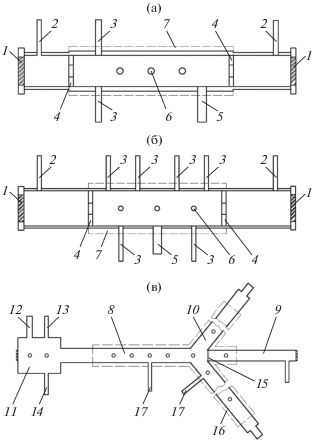
Прокачка газов осуществляется с помощью вакуумных мембранных насосов (Россия).
Реактор пиролиза с ламинарным течением и расходами до 10 л/ч
Проточный реактор был ранее описан в [1]. Число Рейнольдса изменяется от 3 до 5. Внутренний диаметр – 21 мм, общая длина – 300 мм, длина зоны поглощения – 70 мм (рис. 4а). Время контакта смеси при расходе 8 л/ч – 10 с. Реактор снабжен встречными вводами для подачи газовой смеси 3 и вводами защитного газа 2 для оптических окон 1 и для локализации зоны поглощения. Наряду с подачей защитного газа, для локализации этилена использовались диафрагмы 4. Выход газовой смеси и забор проб осуществлялся через вывод 5. Встречный ввод реакционной смеси позволяет организовать зону эффективного смешения, которая смещается потоком метана, организуя режим идеального вытеснения. Такая организация газовых потоков позволяет удержать этилен в нагреваемой зоне и направить смесь на выход из реактора. Температура стенки реактора изменялась в диапазоне от 600 до 1100 К.
Мощность лазерного излучения на выходе из реактора измерялась преобразователем ТИ-3 (Россия) с апертурой 23 мм, достаточной для улавливания всего выходящего излучения. Коэффициент преобразования 0.093 мВ/В, постоянная времени ≤10 с.
Конструкция этого реактора имеет ряд преимуществ:
– в реакторе формируется ограниченный в пространстве газовый слой реагентов с четкими границами [14];
– создается эффективная газовая изоляция окон [14];
– имеется возможность измерения температуры газа вблизи стенок и в объеме реактора, а также мощности лазерного излучения и состава газовой смеси на входе и выходе реактора.
Реактор пиролиза с вихревым течением и расходами до 40 л/ч
Число Рейнольдса в реакторе изменяется от 1 до 10. Диаметр реактора 21 мм, общая длина 300 мм, длина реакционной зоны – 70 мм (рис. 4б). Реактор снабжен шестью вводами для подачи газовой смеси 3 и двумя вводами защитного газа 2 для оптических окон 1. Выход газовой смеси и забор проб, также как и в реакторе с расходами до 10 л/ч, осуществлялся через вывод 5. Для локализации реакционной зоны, наряду с подачей инертного газа, использовались диафрагмы 4. Контроль мощности на выходе из реактора осуществлялся калориметром OPHIR AN/2 (Израиль).
Благодаря такому расположению вводов газовой смеси, потоки реагентов подаются навстречу друг другу. В реакторе при различных расходах реагентов образуются вихревые зоны, которые позволяют поддерживать постоянным количество превращенного вещества, эффективнее снимать тепло со стенок и увеличивать время контакта смеси. Благодаря этому можно получить значительную конверсию при достаточно больших расходах для данного объема реактора. С помощью такого ввода газа удалось получить вихревой режим течения при относительно небольших расходах.
Наличие завихрений подтверждается математическими расчетами (рис. 5). Математическая модель трехмерной динамики реакционно-способной газовой смеси разработана на основе базовой модели ламинарного реакционно-способного газового потока в пакете ANSYS Fluent (лицензия Сибирского cуперкомпьютерного центра (ССКЦ) СО РАН) [15]. Она представляет собой систему уравнений многокомпонентной газодинамики. Ламинарный поток газа описывается трехмерной моделью Навье–Стокса для идеального газа с химическими реакциями. На рис. 5 представлены результаты расчета для расходов 12 л/ч этана и 4 л/ч метана и температуры стенки в реакционной зоне 1000 К.
Опытно-демонстрационный реактор (о.д.р.) пиролиза с ламинарно-переходным течением с расходами до 1000 л/ч
Основным элементом о.д.р. (рис. 4в) является цилиндрический стальной канал пиролиза газов 8, соосный с оптическим каналом 9 для ввода излучения CO2-лазера. К основному каналу через стыковочный узел приварены под углом 75° два идентичных канала подачи и предварительного нагрева газов 10. Реакционный объем и каналы подогрева имеют внутренний диаметр 38 мм. Оптический канал изготовлен из трубы внутренним диаметром 32 мм и снабжен сменной стальной диафрагмой ∅6 мм 15, установленной на входе в стыковочный узел. Число Рейнольдса при расходах 50 л/ч изменяется от 10 до 400. На входе канала ввода излучения установлены окно из просветленного ZnSe и узел подачи защитного газа. На торцах труб для подогрева газов установлены блоки подачи реагентов и формирования газовых потоков, которые одновременно служат для ограничения входной температуры.
На выходе трубы пиролиза смонтирован приемно-охлаждающий блок 11 с элементами диагностики и выводами на вакуумный насос и выхлоп в атмосферу. О.д.р. имеет термопарные герметизированные вводы для детального измерения газовой температуры в реакционной зоне (включая приосевое сечение) и контроля температуры нагреваемых газов на выходе каналов 10). Также используются кварцевые герметизированные окна 17 для использования оптических пирометров. Канал пиролиза и трубы подогрева газов имеют три независимых тепловых источника омического типа с максимальной выделяемой мощностью 1400 Вт каждый и внешней теплоизоляцией из минеральной ваты (16).
Благодаря трем независимым тепловым источникам в реакторе можно варьировать длину реакционной зоны. Унифицированные узлы подачи исходных газов в о.д.р. и оптическая схема ввода излучения позволяют использовать диапазон расходов газа от 10 до 1000 л/ч и излучение как непрерывного, так и импульсно-периодического режима с максимальной импульсной мощностью до 700 Вт. Доля буферного, не участвующего в реакции защитного газа метана может быть уменьшена до 5 об. %.
Заложенные в конструкцию реактора технические решения показали свою пригодность для проведения масштабных экспериментов по пиролизу предельных углеводородов. Увеличение характерных расходов до 500 л/ч и более дает время контакта около 8 с, при котором на модельном реакторе с включением лазерного излучения конверсия этана составляет более 50%.
Температурная диагностика в реакторах
Пристеночная температура газа измерялась стандартными термопарами К-типа ∅0.3–0.5 мм, диапазон температур 10–1100°С. Данные регистрировались на устройстве контроля УКТ38 (ОВЕН, Россия) с точностью 1°С и на измерителе-регуляторе ТРМ202 (ОВЕН, Россия) с точностью 0.1°С.
Для измерения температуры в поле излучения лазера были разработаны новые термопары. Большинство выпускаемых термопар имеет в своем составе высокую концентрацию никеля или платины. Присутствие этих веществ в химически активной среде приводит к существенным изменениям параметров реакций в непосредственной близости от термопары. Поэтому для измерения температуры в области излучения была изучена возможность использовать проводники из меди и молибдена. Этот выбор обусловлен рядом условий. Во-первых, диапазон измеряемых температур должен находиться в пределах от 400 до 900°С. Во-вторых, термоэлектроды не должны оказывать влияния на изучаемые процессы в реакторе. В-третьих, материал термоэлектрода должен обладать устойчивостью к воздействию лазерного СО2-излучения высокой интенсивности и иметь низкий уровень поглощения излучения ≤2%. Спектральный коэффициент отражения этих материалов: ρМо = 0.982, ρCu = 0.985 при λ = 10.6 мкм.
Были собраны опытные образцы молибден-медных термопар (ТММ) с диаметром 0.18 мм, изготовленные методом лазерной сварки (Институт лазерной физики СО РАН, Россия). В тестовых испытаниях была получена воспроизводимая градуировочная кривая и установлены следующие технические характеристики ТММ:
– устойчивость к лазерному излучению ~300 Вт/см2;
– уровень поглощения излучения соответствует исходным материалам;
– минимальная каталитическая способность;
– работоспособность при температурах до 950°С;
– воспроизводимость градуировочной кривой от датчика к датчику в пределах ±2°С;
– рабочий ресурс порядка 20 ч (вследствие “водородной болезни” охрупчивается медь);
– чувствительность в диапазоне 500–600°С – 12.5 мкВ/°С.
Определение температуры производится по градуировочной кривой и сигналу с вольтметра В7-38.
В экспериментах по пиролизу этана с расходами газов до 50 л/ч основными термопарами для диагностики были хромель-алюмель (ТХА 0.3 мм) и медь-молибден (ТММ 0.18 мм) – в условиях воздействия лазерного CO2-излучения.
Пирометр ЭОП-66 (“Эталон”, Украина) с диапазоном измеряемых температур 800–10 000°С позволяет измерять в реакторах, снабженных окнами SiO2, температуру внутренних стенок. При установке в поток газа тонкой плоской мишени, слабо влияющей на процесс, например Mo ∅2 мм и толщиной 50 мкм, возможно измерить и газовую температуру. Характерная суммарная погрешность пирометра в области температур 800–1200°С составляет 5–9°С.
Для температурной диагностики также использовался двухцветовой инфракрасный пирометр M77S (Mikron Infrared, INK. USA). Пирометр получает и.к.-излучение объекта контроля на двух длинах волн в области 0.8 и 1.0 мкм, а показания температуры рассчитываются на основании соотношения интенсивности и.к.-излучения на этих двух длинах волн. Таким образом, точность измерения не зависит от изменения коэффициента излучения, степени поглощения и.к.-излучения на линии визирования или частичного заполнения зоны обзора объектом контроля при условии, что действие этих факторов будет одинаковым на каждой из двух длин волн, использующихся для измерения температуры (т.е. поддерживается постоянное соотношение интенсивности и.к.-излучения на двух длинах волн).
Через специальные смотровые окна пирометр может наводиться как на стенку реактора для контроля ее температуры, так и на мишень, расположенную в реакторе. По температуре свечения мишени возможно судить о температуре газа, наполняющего реактор, в месте расположения мишени. Пирометр работает при размерах цели 5% от поля обзора. Погрешность измерений ±0.5% от полной шкалы при температурах измерений 500–1400°С.
Секция газоподачи
На стенде предполагается использование как одного легкого алкана, так и двух- и трехкомпонентных смесей различных углеводородов, включая метан, этан, пропан, бутан, этилен и пропилен. Перед подачей в реакторную зону газы предварительно смешиваются либо формирователем потоков УФГП-4 (ИК СО РАН) с точностью задания не хуже 2% и максимальным суммарным расходом 100 л/ч, либо с помощью цифровых измерителей-регуляторов массового расхода газа Mass-View (Bronkhorst High-Tech BV, Netherlands). В последнем случае расходы по этану и пропану могли задаваться в диапазоне 10–1000 нл/ч, по этилену в диапазоне 1–50 нл/ч, по метану 10–780 нл/ч с точностью не хуже 0.5% от показаний +0.1% от полной шкалы.
Газопылевые потоки готовятся пропусканием газовых потоков на входе реактора через ячейку с предварительно насыпанным порошком из наночастиц.
Газы, используемые в экспериментах, поставлялись ИК СО РАН, чистота метана и этана >99.8%, этилена >99.9%. Газы использовались без дополнительной очистки.
ПРОГРАММЫ ЧИСЛЕННОГО МОДЕЛИРОВАНИЯ
Используемое на стенде излучение СО2-лазера распространяется в химически активной среде реакторного объема в нелинейном режиме. Лазерное излучение индуцирует фотохимические процессы и термические явления, связанные с нагревом газовой смеси. Для понимания роли каждого из этих процессов при изменении экспериментально задаваемых параметров необходимо иметь численную модель реактора с самосогласованными излучением и химическими процессами, а также с решением трехмерной задачи газовой динамики с учетом реальной геометрической формы реактора.
Такая численная модель CFD-динамики химически активных сред с поглощением и переносом излучения создана на основе пакета ANSYS Fluent [15]. В численной модели учтены трехмерная геометрия реактора, многокомпонентное течение газа с диффузией и перемешиванием, теплообмен со стенками, перенос и поглощение излучения в окнах и в газовой среде.
В расчетах решаются трехмерные по пространству уравнения Навье–Стокса для компонентов сжимаемого идеального газа с учетом диффузии компонентов смеси. Нагрев газа излучением учитывается в уравнении для плотности полной энергии. Расчет изменения интенсивности лазерного излучения в смеси газов осуществляется решением интегрально-дифференциального уравнения переноса излучения для поглощающей среды. Модель, реализованная в пакете ANSYS Fluent, дополнена коэффициентами теплопроводности, теплоемкости и вязкости веществ.
В упрощенном виде изменение интенсивности описывается как
(1)
$\begin{gathered} dI{\text{/}}dz = - \alpha I;\quad \alpha = {{\alpha }_{0}}{\text{/}}(1 + II_{s}^{{ - 1}}); \\ \alpha = n{{\sigma }_{0}}{\text{exp}}( - E{\text{/}}kT){\text{/}}(1 + II_{s}^{{ - 1}}). \\ \end{gathered} $Коэффициент поглощения среды α зависит от интенсивности излучения I в среде и α = nσ, где n – концентрация поглощающего газа, σ – сечение поглощения. Зависимость α от I в среде используется в виде, полученном в [9]. Is – интенсивность насыщения, n и α зависят от температуры среды, а изменение температуры и населенность уровней у активного компонента в среде определяется интенсивностью излучения.
В коэффициенте поглощения α = nσ учитывается его зависимость от температуры среды, мощности падающего излучения и концентрации этилена. Сечение σ задается в двухуровневом приближении. Для излучения с λ = 10.6 мкм сечение поглощения σ = σ0exp(–E/kT) [10], где σ0 = 0.76 ⋅ 10–17 см2 – сечение, которое определено из спектра пропускания смеси этилен/метан для ν = 944.2 см–1 при T0 = = 295 K по закону Бугера–Ламберта–Бера.
Химические процессы в реакторе рассчитываются как по брутто-схемам для основных наблюдаемых продуктов, так и по компактным кинетическим схемам, в том числе по собственным разработкам [12, 16]. Разработанные кинетические схемы радикальных цепных реакций имеют ряд преимуществ: они включают минимальное количество стадий, адекватно описывают пиролиз этана с высоким выходом этилена при 900–1150 К и имеют приемлемое время расчета трехмерных задач. В этих расчетах учитывается тепловой эффект от поглощения лазерного излучения и химических реакций в условиях изменения интенсивности излучения при прохождении его через реактор. Расчет химической кинетики без динамики газа проводится по программе ChemPak [17].
Как правило, в численном моделировании задаются экспериментальные значения входной мощности излучения, значения расходов газовых компонентов, температура стенок камеры и другие параметры. Для этих значений находится решение всей прямой задачи динамики газа с поглощением излучения. Задача считается решенной, если полученное пропускание по значению излучения на выходе реактора совпадает с экспериментом с точностью не хуже 2–3%.
В качестве альтернативного метода пакету ANSYS Fluent, привязанному к лицензии на ССКЦ СО РАН, для упрощенной геометрии течения без лазерного излучения разработана программа для дозвуковых течений реакционного многокомпонентного газа [18]. Численная модель реактора с применением компактной кинетической схемы радикальных цепных реакций рассчитала выходы этилена в реакторе при учете нагрева со стенок, которые совпали с экспериментальными значениями в пределах 2–5%.
РЕЗУЛЬТАТЫ
Преимуществом стенда лазерного катализа по сравнению с другими установками по изучению конверсии легких алканов является возможность целенаправленного управления радикальными цепными реакциями в реакторе. Это управление достигается за счет лазерного излучения, которое создает область нагретых реагентов непосредственно в газовом объеме, оторванном от стенок камеры. Эта область служит источником сверхравновесного количества радикалов в реакторе, что увеличивает выходы водорода и других целевых продуктов при пиролизе различных углеводородов в присутствии лазерного излучения. При постоянной мощности излучения увеличение интенсивности путем уменьшения диаметра луча в реакционной зоне приводит к увеличению конверсии [1].
На рис. 6 приведена экспериментально полученная на стенде зависимость конверсии пропана от пристеночной температуры для реактора с ламинарным течением. Расход газов ~8 л/ч, состав смеси СH4–C3H8 – 27–73%. Видно, что включение лазерного излучения увеличивает конверсию пропана и, соответственно, выход продуктов при заданной температуре стенок реактора. Еще одним преимуществом лазерной активации является снижение температурного порога реакций конверсии легких алканов.
ЗАКЛЮЧЕНИЕ
Для изучения воздействия лазерного излучения на каталитические процессы в газопылевой среде легких углеводородов создан стенд лазерного катализа. Этот стенд занял свободную нишу между установками, ориентированными на изучение гомогенного катализа в газовой фазе, и установками, направленными на исследования гетерогенного катализа с твердыми гранулами в потоке реагентов. На стенде реализована возможность синтеза наночастиц высокотемпературных оксидов, обычно используемых для приготовления катализаторов, в потоках инертных и химически активных газов. Излучение СО2-лазеров, которое может поглощаться этиленом и другими молекулами в газовой фазе, а также наночастицами различной природы, активизирует физико-химические процессы. На стенде изучаются процессы с вложением энергии лазерным излучением до 105 Вт/см2 и с различными газодинамическими режимами в потоках реагентов. Эксперименты стенда сопровождаются компьютерным моделированием. Оно необходимо для понимания нелинейных физико-химических процессов в реакционных потоках и для реализации масштабного перехода от лабораторных реакторов лазерной конверсии легких алканов к реакторам с большей производительностью по целевым продуктам. Исследования, проводимые на стенде лазерного катализа, актуальны для химической кинетики, химической газодинамики, неравновесной химической термодинамики, лазерной термохимии. Стенд лазерного катализа может найти свое место при создании новых технических устройств, в которых необходимо использовать лазерное высокоэнергетическое воздействие для активации химических реакций с большим суммарным эндотермическим эффектом.
Список литературы
Masyuk N., Sherin A., Snytnikov V.N., Snytnikov V.N. // J. Anal. Appl. Pyr. 2018. V. 134. P. 122. https://doi.org/10.1016/j.jaap.2018.05.017
Snytnikov V.N., Mishchenko T.I., Snytnikov Vl.N., Malykhin S.E., Avdeev V.I., Parmon V.N. // Research on Chemical Intermediates. 2012. V. 38. № 3–5. P. 1133. https://doi.org/10.1007/s11164-011-0449-x
Snytnikov V.N., Mishchenko T.I., Snytnikov Vl.N., Chernykh I.G. // Research on Chemical Intermediates. 2014. V. 40. № 1. P. 345. https://doi.org/10.1007/s11164-012-0967-1
Bardakhanov S.P. // Sedimentation and Sediment Transport. 2003. C. 137. https://doi.org/10.1007/978-94-017-0347-5_21
Басов Н.Г., Панкратов А.В. // Квантовая электроника. 1976. Т. 3. № 4. С. 814.
Бункин Ф.В., Кириченко Н.А., Лукьянчук Б.С. // Успехи физ. наук. 1982. Т. 138. № 1. С. 45.
Панфилов В.Н., Молин Ю.Н. // Успехи химии. 1978. Т. 47. № 6. С. 967.
Трахтенберг Л.И., Милих Г.М. // Квантовая электроника. 1982. Т. 9. № 12. С. 2537.
Демтредер В. Современная лазерная спектроскопия. Долгопрудный: Изд. дом Интеллект, 2014. С. 507.
Карлов Н.В., Кириченко Н.А., Лукьянчук Б.С. Лазерная термохимия. М.: Наука, 1992. С. 46.
Rabiee Golgir H., Li D.W., Keramatnejad K., Zou Q.M., Xiao J., Wang F., Lu Y.F. // ACS Applied Materials & Interfaces, 2017. V. 9(25). P. 21539. https://doi.org/10.1021/acsami.7b03554
Stadnichenko O.A., Snytnikov V.N., Snytnikov Vl.N., Masyuk N.S. // Chemical Engineering Research and Design. 2016. V. 109. P. 405. https://doi.org/10.1016/j.cherd.2016.02.008
Снытников В.Н., Снытников Вл.Н., Дубов Д.А., Зайковский В.И., Иванова А.С., Стояновский В.О., Пармон В.Н. // Прикладная механика и техническая физика. 2007. Т. 48. № 2. С. 172.
Snytnikov Vl.N., Snytnikov V.N., Masyuk N.S., Markelova T.V. // J. Quantitative Spectroscopy & Radiative Transfer. 2020. V. 253. P. 107. https://doi.org/10.1016/j.jqsrt.2020.107119
https://www.ansys.com/products/fluids/ansys-fluent
Nurislamova L.F., Stoyanovskaya O.P., Stadnichenko O.A., Gubaidullin I.M., Snytnikov V.N., Novichkova A.V. // Chemical Product and Process Modeling. 2014. V. 9. № 2. P. 143. https://doi.org/10.1515/cppm-2014-0008
Вшивков В.А., Скляр О.П., Снытников В.Н., Черных И.Г. // Вычислительные технологии. 2006. Т. 11. № 1. С. 35.
Жалнин Р.В., Масягин В.Ф., Пескова Е.Е., Тишкин В.Ф. // Инженерные технологии и системы. 2020. Т. 30. № 1. С. 162.
Дополнительные материалы отсутствуют.
Инструменты
Приборы и техника эксперимента