Приборы и техника эксперимента, 2021, № 3, стр. 60-67
РАЗРАБОТКА СИСТЕМЫ ПЛАЗМЕННОЙ ОЧИСТКИ ВХОДНОГО ЗЕРКАЛА ОПТИЧЕСКОЙ ДИАГНОСТИКИ ИТЭР “АКТИВНАЯ СПЕКТРОСКОПИЯ” НА ОСНОВЕ РАЗРЯДА С СЕТОЧНЫМ ПОЛЫМ КАТОДОМ
А. В. Рогов a, b, *, Ю. В. Капустин a, b
a Национальный исследовательский центр “Курчатовский институт”
123182 Москва, пл. Академика Курчатова, 1, Россия
b Автономная некоммерческая организация “Управляемый термоядерный синтез – международные проекты”
123182 Москва, пл. Академика Курчатова, 1, Россия
* E-mail: alex-rogov@yandex.ru
Поступила в редакцию 01.01.2021
После доработки 18.01.2021
Принята к публикации 20.01.2021
Аннотация
Представлены результаты исследования зависимости эффективности распыления макета Mo-зеркала от мощности газового разряда и давления рабочего газа (Ar) для трех вариантов заземления элементов разрядной ячейки системы плазменной очистки. Для очистки входного зеркала диагностики ИТЭР “Активная спектроскопия” планируется использовать газовый разряд на постоянном или среднечастотном импульсном токе. Разные схемы заземления электродов дают разную степень торможения ионов, покидающих разрядную ячейку и способных вызвать распыление стенок диагностического порта. Особенностью работы систем очистки внутривакуумных зеркал установки ИТЭР является близкое к разрядной ячейке расположение стенок диагностического порта и отсутствие протока рабочего газа через область чистящего разряда. Эти условия моделировались посредством размещения полноразмерного функционального макета разрядной ячейки внутри негерметичного газодинамического обтекателя, изготовленного, как и стенки диагностического порта ИТЭР, из нержавеющей стали. Показано, что наибольшая эффективность очистки достигается, когда катодные элементы разрядной ячейки (включая входное зеркало) электрически изолированы от стенок диагностического порта. Полученные результаты могут быть использованы при разработке плазменных систем очистки для других оптических диагностик ИТЭР.
ВВЕДЕНИЕ
Разрабатываемые в настоящее время системы плазменной очистки внутривакуумных диагностических зеркал установки ИТЭР основаны на использовании газового разряда двух типов: емкостного радиочастотного разряда (RF – radio frequency discharge, F ≥ 13.56 МГц) [1, 2] и разряда с осциллирующими электронами на постоянном или среднечастотном (F ≤ 100 кГц) однополярном импульсном токе (DC/PDC – direct current or pulse direct current discharge) с локализацией плазмы внутри сеточного полого катода [3].
Оба типа разряда реализуются в диодных распылительных системах, где одним из электродов является очищаемое зеркало. Аналогичные распылительные системы нашли широкое технологическое применение в микроэлектронике для ионного травления диэлектриков [4], очистки подложек перед вакуумным напылением [5] и для формирования тонкопленочных покрытий [6].
RF-системы обеспечивают возможность распыления металлов в химически активных газовых смесях и толстых диэлектрических материалов. При этом обеспечивается отсутствие на обрабатываемой поверхности микродуговых привязок, способных повысить ее шероховатость. Применение высокочастотного тока требует обеспечения согласования линии электропитания с нелинейным волновым сопротивлением газового разряда, зависящим от его режима (мощности, состава и давления газа, состояния поверхности электродов). В промышленном технологическом оборудовании для этой цели применяются автоматически регулируемые согласующие устройства, как правило, в виде П-образного LC-фильтра, один из элементов которого является регулируемым [7].
Во всех разработках RF-систем плазменной очистки для ИТЭР одним из электродов разрядной ячейки является зеркало, а вторым – стенки диагностического порта. В случае использования изолированного от стенок диагностического порта зеркала за счет соотношения площадей электродов плазма газового разряда приобретает положительный плавающий потенциал автосмещения [8] относительно зеркала. При этом на очищаемую поверхность воздействуют ионы, осциллирующие в переменном высокочастотном электрическом поле с энергией ~ 10 эВ, и ионы с энергией ~ 100 эВ, ускоренные под действием потенциала автосмещения. С учетом зависимости коэффициента распыления от энергии распыляющих ионов [9] основное распыление обеспечивается именно за счет автосмещения, т.е. механизм распыления токопроводящих материалов в RF-разряде аналогичен распылению в разряде постоянного тока.
Для диэлектрических материалов при положительном полупериоде RF-волны электронной бомбардировкой с поверхности снимается положительный заряд, образующийся на отрицательном полупериоде при облучении поверхности ионами. Благодаря этому в распылительных RF-устройствах обеспечивается эффективное распыление диэлектриков. При разной площади электродов величина потенциала автосмещения и соответственно средняя энергия распыляющих ионов, воздействующих на зеркало и стенки диагностического порта, значительно различаются. Этим обеспечивается преимущественное распыление электрода с малой площадью (зеркала).
В большинстве разрабатываемых для ИТЭР систем оптической диагностики требуется водяное охлаждение входного зеркала из-за высоких тепловых нагрузок, вызванных как радиационным потоком на отражающую поверхность, так и объемным энерговыделением за счет рассеяния термоядерных нейтронов. При условии электрической изоляции от стенок диагностического порта конструкция водоохлаждаемого зеркала значительно усложняется. В таких системах планируется использовать изоляцию зеркала с высоковольтной электрической развязкой в линии водяного охлаждения или применять изолирующий теплопроводный интерфейс между отражающим элементом зеркала и его водоохлаждаемым корпусом.
Другим подходом к решению этой проблемы является заземление зеркала через λ/4 высокочастотный изолятор [10]. При таком конструктивном решении постоянный потенциал автосмещения исчезает, и на поверхность зеркала будет воздействовать только низкоэнергетическая компонента распыляющих ионов высокочастотного разряда. В этих условиях происходит симметризация газового разряда, а энергия ионов оказывается близкой к пороговому значению энергии распыления (при распылении ионами Ar для Be – материала первой стенки – Eth-Be ≈ 50 эВ; для нержавеющей стали – материала диагностического порта – Eth-SS ≈ ≈ 30 эВ; для Rh и Mo – кандидатов для изготовления входного зеркала – Eth-Rh ≈ 30 эВ, Eth-Mo ≈ 40 эВ; для W – материала дивертора – Eth-W ≈ 50 эВ [9]). За счет этого обеспечивается крайне низкая скорость удаления загрязнений, а в условиях, когда коэффициент распыления материала зеркала меньше, чем материала стенок диагностического порта, может происходить не очистка, а загрязнение отражающей поверхности.
Также следует учитывать, что даже при полном согласовании линии электропитания с нагрузкой и одинаковой мощности, введенной в газовый разряд, скорость распыления в RF-разряде примерно в 2 раза меньше, чем при распылении в DC-устройстве [11].
Применение газового разряда с осциллирующими электронами за счет использования электростатической ловушки в виде полого катода дополнительно увеличивает эффективность DC-разряда при распылении токопроводящих загрязнений в системе очистки входного зеркала. Поскольку первая стенка установки ИТЭР будет изготовлена из Be, ожидается, что именно этот материал станет основным компонентом загрязнения. При распылении тонких диэлектрических загрязнений, которые могут образоваться при возникновении аварий, связанных с разгерметизацией вакуумной камеры реактора, будет использоваться режим PDC [12]. При распаде плазмы чистящего разряда в промежутках между отрицательными импульсами происходит нейтрализация положительного заряда на поверхности диэлектрика. Диапазон рабочих давлений и параметры плазмы для DC- и PDC-режимов аналогичны.
DC/PDC-СИСТЕМА ОЧИСТКИ ВХОДНОГО ЗЕРКАЛА ДИАГНОСТИКИ “АКТИВНАЯ СПЕКТРОСКОПИЯ”
В DC/PDC-системе очистки, разрабатываемой для системы оптической диагностики “Активная спектроскопия” [13], входное зеркало является одним из компонентов полого катода, его дополнительные элементы выполнены в виде сеточных электродов с прозрачностью ≈60%. Это обеспечивает выход продуктов эрозии из зоны распыления и их осаждение на стенках диагностического порта. Поворотная защитная шторка в закрытом состоянии также является одной из стенок полого катода, чем обеспечивается его замкнутая конфигурация при проведении очистки с использованием расположенного внутри анодного электрода. Все распыляемые элементы полого катода изготовлены из конструкционного материала входного зеркала, что препятствует изменению элементного состава отражающей поверхности входного зеркала за счет частичного переосаждения продуктов эрозии внутри полого катода. В этих условиях значительное влияние на эффективность очистки может оказывать распыление стенок диагностического порта вместе с осажденным на них в процессе очистки входного зеркала загрязнением. При этом часть продуктов эрозии может возвращаться на отражающую поверхность зеркала, снижая эффективность очистки.
Целью исследований, результаты которых представлены в данной работе, была экспериментальная проверка возможности повышения эффективности функционирования DC/PDC-системы очистки входного зеркала диагностики “Активная спектроскопия” путем уменьшения распыления стенок диагностического порта посредством торможения ионов, вышедших через сеточный катодный электрод за пределы разрядной ячейки. Эксперименты проводились на полноразмерном функциональном макете системы очистки при трех вариантах заземления электродов разрядной ячейки, обеспечивших разную степень торможения ионов.
Использовался режим без протока газа через разрядную ячейку. Этим моделировались условия миграции материала внутри диагностического порта установки ИТЭР. Схема размещения входного зеркала, компонентов системы очистки в диагностическом порту ИТЭР, а также оптическая схема диагностики “Активная спектроскопия” представлены на рис. 1 (ход лучей показан в режиме измерения – с открытой шторкой).
Рис. 1.
Схема размещения узла входного зеркала диагностики “Активная спектроскопия” в диагностическом порту ИТЭР. 1 – первая стенка; 2 – стенка диагностического порта; 3 – входное зеркало; 4 – сеточный полый катод коробчатой формы; 5 – калибровочный уголковый отражатель; 6 – ось вращения шторки; 7 – защитная поворотная шторка с сеточным окном для прохода оптического излучения при калибровке (складывается внутрь полого катода при открывании); 8 – второе зеркало.
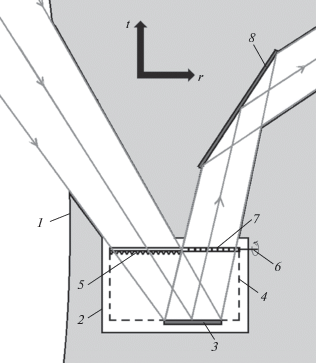
Конструкционный материал входного зеркала 3 и отражателя 5, расположенного на защитной шторке 7, – монокристаллический молибден [14]. Предусмотрена их одновременная очистка. Это предотвращает загрязнение уголкового отражателя (используется при калибровке диагностической системы) продуктами эрозии во время очистки отражающей поверхности входного зеркала. В связи с близким расположением первого зеркала к термоядерной плазме и вызванными этим большими тепловыми нагрузками входное зеркало снабжено водяным охлаждением.
ОБОРУДОВАНИЕ И МЕТОДИКА ЭКСПЕРИМЕНТА
Эксперименты проводились в цилиндрической вакуумной камере диаметром 340 мм и высотой 200 мм с безмасляной системой вакуумной откачки. В качестве разрядной ячейки использовался изготовленный из молибдена полноразмерный функциональный макет узла входного зеркала диагностики “Активная спектроскопия” (изготовитель ЗАО “Спектроскопия, оптика и лазеры – авангардные разработки”, г. Минск, Республика Беларусь). Сеточные катодные электроды изготовлены из молибдена толщиной 1 мм методом водоабразивной резки. Форма отверстий – шестигранник с характерным размером 5 мм. Ширина перемычек – 1.5 мм. В качестве полноразмерного макета входного зеркала использовалась квадратная Mo-пластина с размерами 100 × 100 × × 0.5 мм. Размеры коробчатого полого катода 240 × 150 × 120 мм. Одна из стенок была изготовлена из листового молибдена и моделировала защитную шторку диагностики. В качестве анода использовался диск диаметром 20 мм и толщиной 0.5 мм.
Измерение однородности распыления по поверхности образцов проводилось методом рентгенофлуоресцентного анализа [15] на спектрометре Clever-B23 со встроенным механизмом перемещения образцов. Использовалась следующая методика измерений: на макет входного Mo-зеркала при помощи планарного магнетрона осаждалось Cu-покрытие толщиной ≈ 1 мкм и измерялось распределение его толщины по поверхности образца. Далее выбиралось время распыления образца в DC/PDC-системе очистки, при котором максимальная толщина распыленного слоя была меньше исходной толщины покрытия, и проводилось повторное измерение толщины покрытия. Разница между этими двумя измеренными распределениями соответствовала профилю толщины удаленного в ходе распыления слоя и характеризовала равномерность очистки поверхности зеркала.
Исследование эффективности очистки и интенсивности распыления стенок проводилось для трех вариантов заземления разрядной ячейки, которое осуществлялось за счет изменения подключения электродов. Принципиальная электрическая схема подключения элементов разрядной ячейки и схема ее размещения в вакуумной камере представлены на рис. 2.
Рис. 2.
Схема экспериментального оборудования. 1 – стенки вакуумной камеры, 2 – вакуумный газодинамический обтекатель, 3 – сеточный катодный электрод разрядной ячейки, 4 – макет поворотной защитной шторки, 5 – макет уголкового рефлектора, 6 – макет входного зеркала, 7 – анод, 8 – изолятор, 9 – источник питания, 10 – линия газонапуска, 11 – вакуумная откачка; I1 – ток анода, I2 – ток через линию заземления анода, I3 – ток через линию заземления полого катода, U1 – разрядное напряжение, U2 – плавающий потенциал автосмещения.
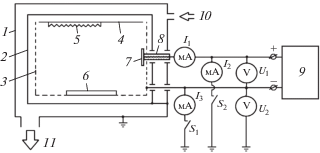
Исследовались следующие варианты коммутации электродов.
– Заземленный катод: S1 замкнут, S2 разомкнут. В этом режиме при пролете до стенки диагностического порта торможения ионов не происходит. С учетом требования водяного охлаждения входного зеркала диагностики “Активная спектроскопия” возможно непосредственное заземление входного зеркала, что позволяет упростить его конструкцию и повысить надежность. Измерение тока через линию заземления катода позволяет контролировать ионный ток на стенку и ее распыление.
– Изолированная разрядная ячейка: S1 и S2 разомкнуты. Торможение ионов происходит за счет формирования положительного плавающего потенциала (автосмещения) на заземленных стенках обтекателя относительно сеточного катодного электрода. Входное зеркало и катодные элементы разрядной ячейки должны быть электрически изолированы от стенок диагностического порта. Реализация такого подхода требует усложнения конструкции водоохлаждаемого зеркала. В этом режиме проводилось измерение зависимости потенциала автосмещения (U2) от напряжения разряда (U1), которая характеризует степень торможения распыляющих стенки диагностического порта ионов.
– Заземленный анод: S1 разомкнут, S2 замкнут. Происходит полное торможение ионов в промежутке “сеточный катод–стенка диагностического порта”. При этом имеется два разрядных промежутка: “анод–полый катод” и “полый катод–стенка диагностического порта”. В ходе экспериментов измерялся ток в цепи заземления (I2), обусловленный наличием разреженной плазмы в промежутке “сеточный катод–стенка”. Величина этого тока характеризует интенсивность паразитного распыления внешней стороны стенки полого катода при наличии плазмы в промежутке “полый катод–стенка” или при зажигании внешнего паразитного разряда.
Вакуумные условия без протока газа через разрядную ячейку при наличии переосаждения продуктов эрозии внутри диагностического порта ИТЭР моделировались с использованием негерметичного коробчатого газодинамического обтекателя, внутри которого на изоляторах размещалась разрядная ячейка. Малые отверстия обеспечивали выравнивание давления в вакуумной камере и внутри обтекателя. Вынос продуктов эрозии в зону обдува снаружи обтекателя в этих условиях был пренебрежимо мал. Расстояние между стенками полого катода и стенками короба составляло 20 мм, что соответствовало ожидаемому расстоянию до стенок диагностического порта. Стабилизация рабочего давления в вакуумной камере обеспечивалась посредством регулировки газонапуска при работающей вакуумной откачке.
Таким образом, применение газодинамического обтекателя позволяет моделировать вакуумные условия в диагностическом порту ИТЭР в режиме плазменной очистки с использованием стандартного вакуумного оборудования.
На рис. 3 представлены фотографии (на разных стадиях сборки) вакуумной камеры с разрядной ячейкой системы плазменной очистки диагностики “Активная спектроскопия”.
Рис. 3.
Оборудование для моделирования вакуумных условий и размещения системы очистки в диагностическом порту ИТЭР: а – без защитной шторки и крышки газодинамического обтекателя; б – со шторкой, но без крышки газодинамического обтекателя; в – в собранном виде. 1 – макет первого Mo-зеркала; 2 – сеточный полый Mo-катод; 3 – Mo-анод; 4 – макет защитной шторки; 5 – газодинамический обтекатель.
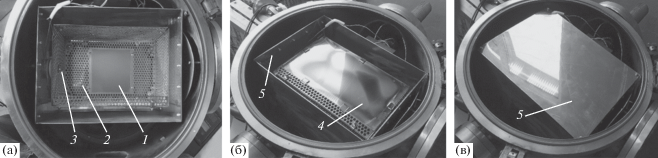
Распыление стенок контролировалось с использованием пластины из нержавеющей стали размером 100 × 100 × 0.5 мм, установленной на внутренней стенке короба-обтекателя, также изготовленного из нержавеющей стали (конструкционный материал стенок диагностического порта ИТЭР), напротив центральной зоны сеточного электрода. Эффективность и скорость процесса очистки оценивалась по результатам взвешивания измерительных марок и макета входного зеркала до и после распыления. При этом использовались аналитические весы CAS CAUW 220D с точностью измерения 0.01 мг.
РЕЗУЛЬТАТЫ И ОБСУЖДЕНИЕ
Разрядная ячейка с заземленным катодом
В разрядной ячейке с заземленным катодом было измерено давление зажигания и гашения разряда (при напряжении холостого хода источника питания 750 В, рабочий газ – Ar), которые соответственно составили Рз = 8.5 Па и Рг = 0.2 Па.
Результаты измерения вольт-амперных характеристик разряда с заземленным катодом и зависимостей тока на стенку газодинамического обтекателя от мощности разряда в диапазоне давлений от 0.6 до 5.3 Па представлены на рис. 4.
Рис. 4.
Вольт-амперные характеристики разряда с заземленным катодом (а) и зависимости тока I3 (тока распыляющих стенку ионов) через линию заземления полого катода от мощности разряда (б) в диапазоне давлений Ar от 0.6 до 5.3 Па.
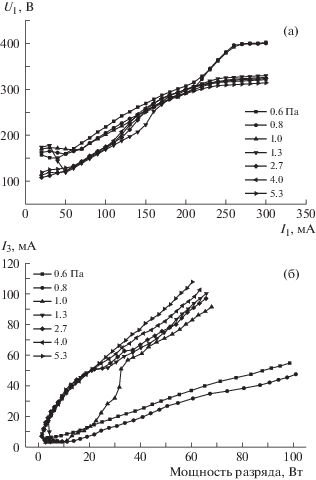
Согласно представленным данным, в диапазонах давлений от 0.6 до 1.0 Па и от 1.0 до 5.3 Па наблюдаются два существенно отличающихся режима газового разряда. При давлении 1 Па наблюдается переходный режим. В области пониженного давления происходит резкое уменьшение ионного тока на стенку. В связи с этим измерения скорости распыления макета зеркала и стенок газодинамического обтекателя проводились при двух давлениях: 0.6 Па и 1.3 Па, соответствующих этим двум режимам. Результаты измерений представлены на рис. 5.
Изолированная разрядная ячейка
В изолированной разрядной ячейке давление зажигания и гашения разряда составили соответственно Рз = 8 Па и Рг = 0.1 Па.
Результаты измерения вольт-амперных характеристик разряда и зависимости потенциала автосмещения от напряжения разряда в диапазоне давлений Ar от 0.6 до 5.3 Па представлены на рис. 6.
Рис 6.
Вольт-амперные характеристики разряда в изолированной разрядной ячейке (а) и зависимости потенциала автосмещения от мощности разряда (б) в диапазоне давлений Ar от 0.6 до 5.3 Па.
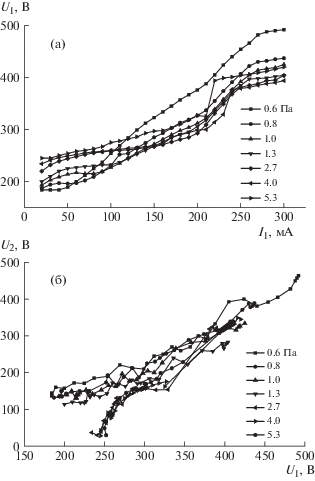
Измеренные зависимости скоростей распыления макета Mo-зеркала и нержавеющих стенок от мощности разряда при давлении аргона PAr = 5.3 Па представлены на рис. 7.
Рис. 7.
Зависимости скоростей распыления макета Mo-зеркала VMo и нержавеющей стенки VSS от мощности разряда в изолированной разрядной ячейке.
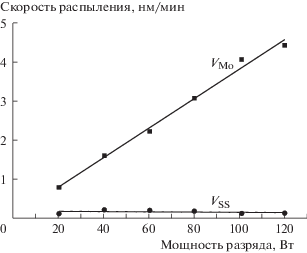
По мере увеличения мощности разряда скорость распыления зеркала линейно возрастает, в то время как скорость распыления стенок практически не меняется и остается пренебрежимо малой. Это объясняется тем, что при росте мощности разряда потенциал автосмещения приближается к разрядному напряжению, т.е. степень торможения ионов при пролете до стенки увеличивается.
Разрядная ячейка с заземленным анодом
В разрядной ячейке с заземленным анодом давление зажигания и гашения разряда составили соответственно Рз = 6 Па и Рг = 0.2 Па.
Вольт-амперные характеристики разряда с заземленным анодом и зависимости тока через линию заземления анода от мощности разряда в диапазоне давлений от 0.6 до 5.3 Па представлены на рис. 8.
Рис. 8.
Вольт-амперные характеристики разряда с заземленным анодом (а) и зависимости тока через линию заземления анода от мощности разряда (б) в диапазоне давлений Ar от 0.6 до 5.3 Па.
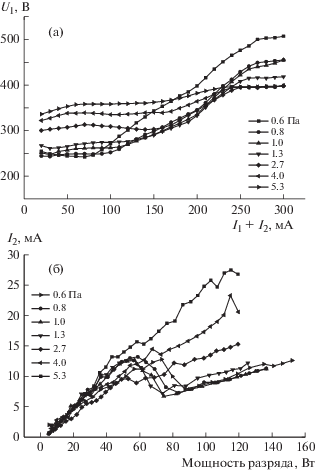
При давлении ниже 2.7 Па и мощности разряда более 80 Вт наблюдается резкое снижение тока через линию заземления анода. Предположительно, это связано с гашением внешнего паразитного разряда между сеточным катодом и стенкой. Измерение зависимости скорости распыления от мощности разряда, как и для изолированной ячейки, проводилось при давлении PAr = 5.3 Па. Результаты представлены на рис. 9.
Рис. 9.
Зависимости скоростей распыления макета Mo-зеркала VMo и нержавеющей стенки VSS от мощности разряда с заземленным анодом.
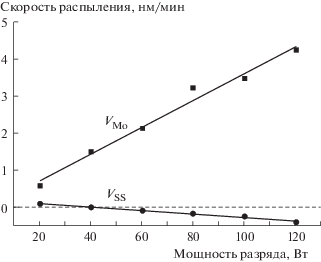
Видно, что при мощности разряда более 40 Вт осаждение преобладает над распылением на поверхности стенки напротив центра сеточного катодного электрода. Такая конфигурация разрядной ячейки обеспечивает наименьшее распыление стенок диагностического порта. Однако из-за малости этого эффекта измеренная эффективность распыления зеркала практически не отличается от варианта с изолированной разрядной ячейкой.
Результаты измерения равномерности распыления по поверхности макета зеркала представлены на рис. 10. Согласно рисунку, при одинаковой геометрии и идентичном расположении электродов наилучшую однородность очистки обеспечивает разрядная ячейка с заземленным анодом.
ЗАКЛЮЧЕНИЕ
Предложена методика проведения измерений с использованием газодинамического обтекателя, позволяющая моделировать отсутствие протока рабочего газа через разрядную ячейку, что соответствует ожидаемым в ИТЭР условиям, в стандартном вакуумном оборудовании. Для подавления распыления стенок диагностического порта и повышения эффективности и равномерности удаления загрязнений в DC/PDC-системе плазменной очистки оптической диагностики “Активная спектроскопия” наилучшей является конфигурация с заземленным анодом. Близкие к этой конфигурации значения по скорости очистки при несколько худшей однородности получены для изолированной разрядной ячейки. Система очистки с заземленными катодными элементами (включая входное зеркало и уголковый отражатель) может быть использована только при пониженных давлениях Ar (<0.7 Па). При этом скорость очистки уменьшается на ≈30%.
В связи с вышеизложенным предлагается изолировать элементы разрядной ячейки (включая входное зеркало и уголковый рефлектор) от стенок диагностического порта. Это позволит использовать все исследованные разрядные конфигурации в зависимости от эксплуатационных условий: изолированная разрядная ячейка потенциально может быть использована в режиме без отключения тороидального магнитного поля в ИТЭР; режим с заземленным анодом позволяет получить наилучшую однородность очистки и минимальное распыление стенок; режим с заземленным катодом может применяться в качестве аварийного при разрушении или сильном загрязнении изоляторов разрядной ячейки.
При разработке DC/PDC-систем плазменной очистки следует учитывать разницу в минимальных давлениях поджига и гашения разряда. Для инициации разряда при пониженном давлении могут применяться источники питания с начальным поджигающим импульсом повышенного напряжения, специальные системы импульсного газонапуска в область ионизации разрядной ячейки или радиоактивные элементы, обеспечивающие повышенную концентрацию электронов в межэлектродном промежутке.
Список литературы
Moser L., Marot L., Steiner R., Reichle R., Leipold F., Vorpahl C., Le Guern F., Walach U., Alberti S., Furno I., Yan R., Peng J., Ben Yaala M., Meyer E. // Physica scripta. 2017. V. 2017. № T170. P. 014047. https://doi.org/10.1088/1402-4896/aa8f30
Dmitriev A.M., Babinov N.A., Bazhenov A.N., Bukreev I.M., Kochergin M.M., Koval A.N., Kurskiev G.S., Litvinov A.E., Masyukevich S.V., Mukhin E.E., Razdobarin A.G., Samsonov D.S., Solokha V.V., Tolstyakov S. Yu., Andrew P., et al. // Physica scripta. 2017. T. 2017. № T170. P. 014072. https://doi.org/10.1088/1402-4896/aa95e5
Рогов А.В., Капустин Ю.В. // Успехи прикладной физики. 2016. Т. 4. № 3. С. 240.
Ветошкин В.М., Кобзиев В.Ф., Романов Э.А. Технология тонких пленок: учеб.-методическое пособие. Ижевск: Изд-во “Удмуртский государственный университет”, 2013.
Kersten H., Steffen H., Behnke J.F. // Surface and Coatings Technology. 1996. V. 86–87. P. 762. https://doi.org/10.1016/S0257-8972(96)03030-7
Welzel T., Ellmer K. // Journal of Physics D: Applied physics. 2013. V. 46. № 31. P. 315202. https://doi.org/10.1088/0022-3727/46/31/315202
Каганцов С.М., Фролов И.Ю., Соловьев А.В. // Межвуз. сб. научн. трудов “Методы и устройства передачи и обработки информации”. СПб.: Гидрометеоиздат, 2003. С. 34.
Upadhyay J., Peshl J., Popović S., Valente-Feliciano A.-M., Vušković L. // AIP advances. 2018. V. 8. P. 085008. https://doi.org/10.1063/1.5045692
Yamamura Y., Tawara H. // Energy dependence of ion-induced sputtering yields from monoatomic solids at normal incidence. Research report. NIFS-DATA-23. Nagoya, 1995.
Dmitriev A.M., Babinov N.A., Bazhenov A.N., Bukreev I.M., Elets D.I., Filimonov V.V., Koval A.N., Kueskiev G.S., Litvinov A.E., Mikhin E.E., Razdobarin A.G., Samsonov D.S., Senitchenkov V.A., Solovei V.A., Terechenko I.B. et al. // Fusion Engineering and Design. 2019. V. 146. Part A. P. 1390. https://doi.org/10.1016/j.fusengdes.2019.02.090
Вольпян О.Д., Кузьмичев А.И. // Прикладная физика. 2008. № 3. С. 34.
Берлин Е.В., Сейдман Л.А. Ионно-плазменные процессы в тонкопленочной технологии. М.: Техносфера, 2010.
Ключников Л.А., Крупин В.А., Коробов К.В., Нургалиев М.Р., Немец А.Р., Днестровский А.Ю., Науменко Н.Н., Тугаринова С.Н., Серов С.В., Деньщиков Д.С. // ВАНТ. Серия: термоядерный синтез. 2016. Т. 39. № 1. С. 95–104.
Orlovskiy I., Alekseev A., Andreenko E., Asadulin G., Gorshkov A. // Fusion Engineering and Design. 2017. V. 123. P. 1011. https://doi.org/10.1016/j.fusengdes.2017.02.057
Giurlani W., Berretti E., Innocenti M., Lavacchi A. // Coatings. 2019. V. 9. Is. 2. P. 79. https://doi.org/10.3390/coatings9020079
Дополнительные материалы отсутствуют.
Инструменты
Приборы и техника эксперимента