Приборы и техника эксперимента, 2022, № 1, стр. 14-43
УСТАНОВКИ ДЛЯ ЭЛЕКТРОРАЗРЯДНЫХ ТЕХНОЛОГИЙ И ИХ ТЕХНИЧЕСКИЕ ПРИМЕНЕНИЯ (обзор)
А. В. Харлов *
Институт сильноточной электроники СО РАН
634055 Томск, Академический просп., 2/3, Россия
* E-mail: akharlov@lef.hcei.tsc.ru
Поступила в редакцию 21.04.2021
После доработки 01.06.2021
Принята к публикации 08.07.2021
- EDN: NKLYLO
- DOI: 10.31857/S0032816221060173
Аннотация
Высоковольтная импульсная технология является одним из эффективных методов дезинтеграции и измельчения горных пород, разделения руд и синтезированных материалов, переработки строительных и упругопластических материалов. В отделе импульсной техники ИСЭ СО РАН с 2007 года ведутся исследования по разработке установок для электроимпульсных технологий. Были созданы установки с энергией от 100 Дж до 8 кДж, работающие в импульсно-пакетном режиме, с полной автоматизацией управления. Высоковольтный импульсный генератор может быть выполнен с использованием схемы Маркса или высоковольтного трансформатора. Оба варианта рассмотрены в этом обзоре. Представлены результаты проектирования и испытаний компактных генераторов, предназначенных для дробления материалов, хотя для них возможны и другие технологические применения.
1. ВВЕДЕНИЕ
В последние несколько десятилетий наблюдается всплеск интереса к использованию высоковольтной импульсной технологии для разрушения горных пород. Электроразрушение горных пород путем применения высоковольтных электрических импульсов является одним из эффективных методов дезинтеграции минералов [1–3]. В работе [4] исследовано разрушение гранита электроимпульсным способом для двухэлектродной системы в диапазоне изменения расстояний между электродами 10–300 мм и энергетического вклада на единицу длины межэлектродного промежутка 3.6–100 Дж/мм. В монографиях [5, 6] впервые систематизированы разработки технологий и технического оборудования на основе импульсных электрических разрядов, которые могут быть использованы для разрушения и измельчения горных пород, руд и синтезированных материалов. Основными преимуществами такой методики являются селективность процесса, высокая эффективность и возможность управления в широком диапазоне параметров [7–10]. Электроимпульсная техника дробления горных пород также рассматривается как экологичная альтернатива применению взрывчатых веществ. В работе [11] рассматривается минимизация расхода электрической энергии в процессе фрагментации электрическими импульсами.
Основные особенности электрической фрагментации заключаются в следующем: импульсный электрический разряд (длительностью от 100 нс до нескольких микросекунд), происходящий в смеси жидкости (часто – вода) с твердым диэлектриком, нагревает искровой канал до температуры порядка 104 К; искровой канал расширяется и генерирует ударную волну (обычно с амплитудой 109–1010 Па) в окружающий твердый материал, что приводит к деформации и последующему разрушению материала [12–14]. В работе [15] было установлено, что интенсивность ударной волны тесно связана с мощностью и энергией, рассеиваемой в плазменном канале. Более длинный плазменный канал и более быстрое расширение дуги могут привести к более высокой мощности и энергии, осаждаемой в плазменном канале, что может активировать более сильную ударную волну. В работе [16] исследовано влияние проводимости воды на ток разряда и ударные волны. Установлено, что пиковое давление ударных волн постепенно уменьшается с увеличением проводимости воды. Знание и контроль электрического пробоя жидкостей очень важны для успешного применения электроимпульсной техники. В работе [17] о преимуществах извлечения алмазов с помощью высоковольтных импульсов было указано, что такие извлеченные алмазы не имели механических дефектов и были чисто отделены от кимберлитовых матриц. Недавно было проведено сравнение [18, 19] извлечения минералов импульсами высокого напряжения с обычным измельчением при одинаковом удельном энерговкладе. В этих работах было показано, что к.п.д. выше у импульсной технологии.
Даже сегодня не существует исчерпывающей теории пробоя в жидкостях, хотя этот процесс очень широко изучался на протяжении последних пятидесяти лет с момента разработки сильноточных высоковольтных генераторов на основе импульсных линий формирования с жидким диэлектриком. Известные эмпирические соотношения Мартина [20, 21], описывающие электрическую прочность воды и трансформаторного масла, широко используются до сих пор (они введены более 40 лет назад!). Недавняя книга [22] посвящена описанию физических механизмов инициирования и распространения импульсных разрядов в жидкостях, а также основным законам, описывающим импульсную электрическую прочность жидкостей. Описание электрического пробоя и проводимости в жидкости рассмотрено в работах [23, 24]. К сожалению, в монографии [22] мало внимания уделено энергетическим характеристикам разряда. Обширный обзор по формированию стримеров в воде и других диэлектрических жидкостях дан в работе [25].
В 70–80-е годы в Томском политехническом институте, в Кольском научном центре АН СССР, ИСЭ СО РАН выполнены научные исследования закономерностей электрического пробоя твердых, жидких и газообразных сред. На основе результатов исследований были предложены и разработаны технические средства электроразрядных технологий. Современные направления исследований связаны с такими электроимпульсными технологическими применениями, как бурение скважин, дезинтеграция и раскрытие руд, разрушение бетона и железобетонных конструкций, утилизация электронных изделий и др. Исследовательские работы ведутся в России, Германии, Швейцарии, Японии, Китае и т.д. Достаточно полное представление по тематике можно получить по монографиям [5, 26] и приведенной там литературе. Вместе с тем ни в России, ни за рубежом производственное использование электроимпульсных установок пока еще не получило широкого распространения. Специфические требования к параметрам генератора определяются характером нагрузки, в качестве которой используется канал разряда в воде или в твердом теле. На начальных этапах фрагментации кускового материала до характерных размеров в несколько миллиметров наиболее эффективным является электроимпульсный (электродинамический) режим с пробоем через твердое тело. При этом одним из определяющих условий внедрения канала разряда в твердое тело, находящееся в жидкости, является высокая скорость нарастания напряжения, не менее 1012 В/с. Дальнейшее измельчение происходит в ударно-волновом (электрогидравлическом) режиме с прохождением разряда в воде с обрабатываемым материалом. После пробоя в твердом теле или в жидкости сопротивление плазменного канала быстро спадает до единиц ом и менее за время порядка 100 нс, в течение которого происходит вложение основной доли энергии в канал разряда. Необходимым условием эффективного вложения энергии является малое внутреннее сопротивление генератора. Перечисленным требованиям в наибольшей мере отвечают генераторы импульсов с выходным каскадом в виде заряжаемого до полного рабочего напряжения емкостного накопителя, который через коммутатор и передающую линию с малой индуктивностью разряжается на рабочий промежуток камеры дробления.
Одной из главных причин, продолжительное время сдерживавшей освоение электроразрядных технологий, являлось несовершенство электротехнического оборудования. Сравнительно недавно заметный прогресс произошел в наиболее сложной проблеме – создании высоковольтных конденсаторов с высокими удельными характеристиками и ресурсом работы. Здесь можно отметить керамические конденсаторы TDK серии UHV, успешно зарекомендовавшие себя в установках по электроимпульсному дроблению. В настоящее время известны две компании, поставляющие лабораторные электроимпульсные установки для дробления. Первая – это компания SELFRAG (с 2007 г., Швейцария). Установки SELFRAG LAB (сокращение от selective fragmentation – селективное дробление) поставлены во многие лаборатории мира [27, 28]. Эта установка создана на основе генератора Аркадьева–Маркса и ее параметры таковы: рабочее напряжение 90–200 кВ, частота 1–5 Гц (в пачке импульсов), длительность фронта импульса 150 нс. Вторая – компания ImpulsTec (с 2014 г., Германия), которая разработала установки серии EHF (Electrohydraulic Fragmentation, электрогидравлическое дробление). Эти установки работают только внутри Германии в нескольких исследовательских лабораториях; они сделаны на основе прямого разряда конденсаторной батареи на электродную систему в жидкости [29], их параметры таковы: рабочее напряжение 30–50 кВ, частота 1–10 Гц, энергия импульса 100–1000 Дж, длительность фронта импульса 1.5–2 мкс.
В отделе импульсной техники ИСЭ СО РАН в течение многих лет ведутся исследования по разработке установок для электроимпульсного дробления. Были созданы установки с энергией от 100 Дж до 8 кДж, работающие в импульсно-пакетном режиме, с полной автоматизацией управления [1, 30]. Около десяти установок различных версий было поставлено по контрактам в России и за рубежом. Параметры генераторов электроимпульсного дробления, разработанных в ИСЭ СО РАН, превосходят параметры генераторов компании SELFRAG и ImpulsTec. Во второй главе обзора будет дано описание физических принципов и технических аспектов электроимпульсных (э.и.) технологий, рассмотрены модели, связывающие параметры разряда с эффективностью разрушения, отмечены преимущества и недостатки метода. В третьей главе обзора будут описаны установки для электроразрядных технологий, разработанные в ИСЭ СО РАН, и проведено их систематическое сравнение с мировыми аналогами, показано преимущество установок ИСЭ СО РАН. В четвертой главе обзора описаны некоторые технологические применения и сравниваются эффективности различных режимов разрушения в зависимости от параметров разряда и разрушаемого материала. В отечественной и зарубежной литературе нет обзорных статей по этой тематике, отражающих современное состояние дел. Тематика обзора актуальна для физики плазмы, электрофизики, физики твердого тела, материаловедения и экологии.
2. ФИЗИЧЕСКИЕ ПРИНЦИПЫ И ТЕХНИЧЕСКИЕ АСПЕКТЫ Э.И.-ТЕХНОЛОГИЙ
2.1.1. Феноменология пробоя твердых диэлектриков
Методы электротехнологии на основе электровзрыва в конденсированной среде еще не имеют общепринятой терминологии и классификации. Процесс, использующий искровой разряд непосредственно в твердом диэлектрике, чаще всего называют электроимпульсным методом, электроимпульсной или электроразрядной технологией. В монографии [31] обобщены и наиболее последовательно изложены физические принципы э.и.-метода. По технологическим аспектам наиболее подробно положение дел освещено в упомянутых выше книгах Куреца и Цукермана [5, 6]. Феноменология единичного акта воздействия импульса напряжения на твердое тело может быть представлена следующим образом. Электрическое поле в толще твердого диэлектрика вызывает акты ионизации, происходит размножение носителей тока и, наконец, формируется канал сквозной электрической проводимости [32]. Далее в этом канале за 10–6–10–4 с выделяется электрическая энергия, запасенная во внешнем, обычно емкостном, накопителе; канал пробоя по мере выделения энергии расширяется, оказывая давление на окружающую среду подобно поршню и создавая переменное во времени и пространстве поле механических напряжений. Из-за интенсивной дивергенции волн, их взаимодействия со свободными границами и неоднородностями породы это поле имеет сложный характер с большим удельным содержанием сдвиговых и растягивающих напряжений. В картине разрушения преобладают радиальные изломы, распространяющиеся от канала пробоя, и концентрические трещины. Надо подчеркнуть, что высокое содержание растягивающих напряжений является очень важным преимуществом по сравнению с механическим способом дробления, где формируются напряжения сжатия, к которым горные породы очень устойчивы [33].
Следуя указанной последовательности явлений, для электроимпульсного способа разрушения твердых тел обычно выделяют две стадии: предпробивную (процесс инициирования электровзрыва) и канальную. В первой осуществляется формирование канала сквозной проводимости в толще разрушаемого тела, во второй происходят энергетический вклад в искровой канал, преобразование электрической энергии во внутреннюю энергию продуктов канала и далее в энергию поля механических напряжений, разрушение части материала [32, 34].
2.1.2. Инициирование электровзрыва в твердых диэлектриках
В схемах э.и.-разрушения, когда воздействию напряжения в разрядном промежутке одновременно подвергаются горная порода, окружающая жидкость и граница раздела сред, необходима определенная координация уровней напряжения пробоя отдельных компонентов системы для того, чтобы инициировать разряд в горной породе. Вместе с тем из опыта применения твердой, жидкой и газообразной изоляции известно, что твердые диэлектрики обладают наилучшими изоляционными свойствами, характеризуются наибольшими рабочими градиентами напряжения, в том числе при работе на постоянном токе и промышленной частоте. Поэтому для формирования канала пробоя в толще твердых диэлектриков, окруженных жидкостью (реже газом), используют специальные сочетания условий, отдельные явления и закономерности. Перечислим основные из них.
1. Относительное снижение пробивных градиентов поля у твердых диэлектриков по сравнению с жидкостями и газами в области малых длительностей импульса 10–7–10–6 с.
2. Аномальное снижение импульсной электрической прочности твердых диэлектриков при малом фронте импульса (порядка 30 кВ/мкс), не совпадающее с аналогичными явлениями в жидкостях и газах.
3. Прогрессирующее снижение разрядных градиентов у твердых диэлектриков в резко неоднородном поле с ростом межэлектродного промежутка.
4. Сочетание нормального эффекта полярности у твердых диэлектриков и обратного у жидкостей при некоторой длительности импульса напряжения, например, в области крутизны 10–100 кВ/мкс для большинства горных пород и жидкостей.
5. Снижение электрической прочности твердых диэлектриков, подвергнутых воздействию тепла, ультразвука, радиации.
6. Прогрессирующее снижение пробивных градиентов в твердых диэлектриках при многоимпульсном воздействии.
Очень важным для э.и.-технологий является эффект увеличения электрической прочности жидких диэлектриков при уменьшении времени воздействия по сравнению с твердыми диэлектриками. В области малых длительностей импульса она превосходит прочность твердых диэлектриков [34, 35]. Обобщенные вольт-временные характеристики для межэлектродных промежутков с одинаковой геометрией электродной системы подобны показанным на рис. 1. Для промежутков сантиметрового диапазона точка пересечения кривых находится в области 10–7–5 ∙ 10–6 с, при этом чем выше диэлектрические свойства жидкости и чем ниже твердого диэлектрика, тем при большей длительности импульса наблюдается пересечение. При воздействии на систему, приведенную на рис. 1, импульса с медленным фронтом tж будет пробит жидкий диэлектрик, а твердый диэлектрик после среза напряжения останется электрически ненарушенным. При воздействии быстрого импульса с фронтом tт, наоборот, подвергается пробою твердый диэлектрик. Для импульса с фронтом на пересечении кривых t0 пробой жидкого и твердого диэлектриков равновероятен.
Рис. 1.
Корреляция между динамической электрической прочностью Ed и временем нарастания импульса tUmax. ЭД – электродинамический и ЭГД – электрогидравлический режимы пробоя.
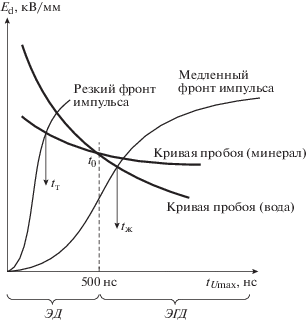
Однако практически для любой пары диэлектриков, в том числе и в случае применения в качестве жидкости технической воды, при некоторых значениях длительности импульса (для воды порядка 10–7 с, для жидкостей на нефтяной основе – 10–6 с) имеется определенная вероятность пробоя твердой компоненты, достаточная для ее практического использования.
Рассматривая критические условия инициирования электровзрыва в толще твердого диэлектрика, на косоугольной волне напряжения целесообразнее оперировать не полной длительностью импульса, а фронтом импульса. В используемой сейчас терминологии [26, 31] принято разделять два режима: электродинамический (ЭД – пробой по твердому телу) и электрогидравлический (ЭГД – пробой по жидкому диэлектрику). Для косоугольных импульсов напряжения в сантиметровом диапазоне разрядных промежутков критическим фронтом импульса для пары горная порода–диэлектрическая жидкость является значение 200–500 кВ/мкс, для комплекса горная порода – техническая вода 2000–3000 кВ/мкс. Для очищенной воды критический фронт импульса около 500 нс, как показано на рис. 1.
Негативное влияние скользящих разрядов при инициировании канала пробоя в твердых диэлектриках проявляется через динамику искажения электрического поля в промежутке в процессе развития актов ионизации на поверхности раздела фаз. Одним из основных факторов, определяющих вероятность пробоя, является конфигурация электрического поля в разрядном промежутке. Для всех типов электродных систем можно изыскать приемы по усилению поля в твердом диэлектрике за счет ослабления его в окружающей среде. Но при всех мерах по усилению поля в твердом теле инициирование электровзрыва в нем для сантиметрового диапазона разрядных промежутков на фронте импульсов требует средних градиентов напряжения 50–150 кВ/см при пробое в диэлектрических жидкостях и до 300 кВ/см для пробоя прочных пород в технической воде [36].
Важным резервом уменьшения импульсной электрической прочности горных пород, руд и других объектов э.и.-технологии является прогрессирующее снижение пробивных градиентов в твердых диэлектриках при многоимпульсном воздействии напряжения [37]. Большинство результатов относится к испытаниям при большом числе воздействий. Однако есть данные, что и в области единиц–десятков импульсов имеет место существенное снижение пробивных градиентов. Дополнительным путем снижения пробивных градиентов является использование при инициировании разрядов эффекта последовательного пробоя в многозазорном разрядном промежутке [38–40]. Таким образом, несмотря на многочисленные приемы инициирования электровзрыва в толще твердого диэлектрического тела, окруженного газом или жидкостью, техника их осуществления довольно сложна. Высокая электрическая прочность твердых диэлектриков, в том числе горных пород, руд и других объектов э.и.-технологии, часто вынуждает применять окружающую среду с повышенными диэлектрическими свойствами (жидкости на нефтяной основе, газы при больших давлениях и т.д.), что нетехнологично. Использование технической воды в э.и.-установках значительно упрощает технологию, что особенно важно для промышленных установок, но при этом требуется формирование коротких импульсов напряжения значительной амплитуды в условиях интенсивного растекания импульсных токов в воде [41].
2.1.3. Канальная стадия разряда
Рассматривая электрическую искру в твердом диэлектрике как источник разрушающих механических нагрузок, последовательность явлений после пробоя можно представить следующей схемой: выделение джоулева тепла – расширение искрового канала – формирование волн механических напряжений и поля деформаций – распространение волн – пластические релаксации в образце – зарождение и рост трещин. Для данной схемы выделим цепь последовательных групп параметров системы, каждая из которых детерминирована предыдущей, а также свойствами диэлектрика и электродной системы. В первом приближении следует назвать такие группы параметров: электрические характеристики разрядного контура; энергетические характеристики искрового канала; термодинамические и гидродинамические параметры искры; характеристики поля напряжений и деформаций в образце; параметры, отражающие интенсивность и характер нарушения сплошности объекта.
Отметим, что применительно к известным технологическим операциям, основанным на электровзрыве в твердых диэлектриках, диапазон амплитуд разрядного тока выражается величиной 103–105 А, длительность энерговклада 10–6–10–4 с. При этом характерное энергосодержание составляет 103–104 Дж/м, радиальный размер канала – 0.5–20 мм, длина 0.01–1 м, температура вещества в канале примерно 104 К, траектория подвержена значительным статистическим флуктуациям. Экспериментальные [42] и расчетные [43] оценки давления в искровом канале дают значения 109–1010 Па. Канал расширяется в диэлектрике в общем случае с переменной скоростью, зависящей от динамики энергетического вклада, свойств диэлектрика, интенсивности истечения продуктов канала в окружающую среду. В области режимов, соответствующих технологическим применениям электровзрыва, наблюдаются, как правило, дозвуковые скорости расширения искрового канала. Поршневое действие канала пробоя порождает ударные волны давления [44].
2.1.4. Энергетические характеристики канала
Следуя теории электрического разряда в жидкости, можно представить уравнение энергетического баланса канала в общем виде как
где pdV – работа, совершаемая каналом разряда против окружающей среды; Wвн – внутренняя энергия продуктов канала; Wп – суммарные потери за счет электромагнитного излучения, теплопроводности и потока вещества из канала в окружающую среду. Рассмотрим составляющие уравнения (1). Плазма канала отдает в окружающую среду энергию в виде электромагнитного излучения. Часть этой энергии, соответствующая ультрафиолетовой области, поглощается в ближней зоне вокруг канала и расходуется на плавление и испарение вещества на стенке канала, т.е. фактически не покидает канал [45]. В микросекундном диапазоне выделения энергии излучательными потерями можно пренебречь (температура канала невысока). Кроме фотонов унос энергии через стенку канала осуществляется также за счет теплопроводности. Простые оценки показывают, что эти потери при электрическом разряде в твердых телах по порядку величины, так же как и для подводного разряда, составляют несколько процентов. Температурные поля в твердом теле, обусловленные теплопроводностью, в режимах энерговыделения практического использования электровзрыва не вносят сколько-нибудь заметных термонапряжений.Быстрое выделение электрической энергии ведет к сильному разогреву вещества диэлектрика, его испарению, при этом число частиц в токовом шнуре заметно возрастает, вновь испаряющиеся частицы диссоциируют, ионизируются. В результате в канале образуется плотная низкотемпературная плазма, выступающая как рабочее тело, которое при расширении совершает работу над окружающей средой. Для точного расчета расширения канала и поля давлений необходимо использовать законы сохранения совместно с уравнением состояния. Такое численное решение очень затруднительно, поэтому распространены аппроксимации с нормировкой на экспериментально измеренный радиус канала rк(t) [46].
В разрядной цепи генератора канал пробоя выступает как активная электрическая нагрузка, процесс энерговыделения в которой можно описать следующими энергетическими характеристиками: разрядным током i; падением напряжения Uк на канале разряда; его активным сопротивлением Rк; мощностью Nк, Nк/lк, развиваемой в канале и на единице его длины соответственно; энергией Wк, Wк/lк, выделенной к данному моменту времени t в канале и на единице его длины lк соответственно. Электрическое активное сопротивление Rк искрового канала является базовой величиной для построения расчетных схем устройств и процессов э.и.-технологии разрушения и обработки материалов, а также для отыскания других электрических характеристик канала. При заданных начальных параметрах разрядной цепи нелинейная величина Rк/lк говорит о способности вещества канала к преобразованию энергии электрического поля в энергию теплового движения частиц, т.е. от Rк зависит динамика энерговыделения в объекте, подвергаемом разрушению. При расчете электрофизических установок Rк выполняет роль нагрузки для генератора импульсов.
Слабая степень теоретических знаний о кинетике плотной низкотемпературной плазмы в сочетании с практически непреодолимыми трудностями теоретического предсказания rк(t) без использования уравнения энергобаланса, включающего функцию Rк(t), вынуждает искать Rк(t) на эмпирической и полуэмпирической основах. Такой путь эффективен еще и потому, что техника опытного определения Rк(t) с погрешностью, допустимой для практического использования результатов, проста и легко воспроизводима. Учитывая столь многочисленные факторы, определяющие активное сопротивление канала пробоя в твердом диэлектрике, трудно надеяться на универсальный подход к предсказанию Rк(i, t) в широкой области вариации свойств диэлектрика и параметров разрядной цепи, тем более, если поставить задачу по отысканию несложных аппроксимаций с одним–двумя размерными коэффициентами, которые позволили бы применить аналитические методы решения переходных процессов и найти простые условия оптимизации параметров разрядной цепи генератора импульсов в э.и.-технологии.
Электропроводность σ плотной плазмы зависит от ее элементного состава, давления и температуры. Температура плазмы в широком диапазоне режимов энерговыделения и типов диэлектриков квазипостоянна, тогда как на давление и элементный состав существенно влияют свойства диэлектрика. Имеющиеся оценки [47] убедительно показывают, что в области температур Т = = 104–2 · 104 К и давлений Р ~ 107–109 Па электропроводность σ зависит слабо от состава плазмы и весьма заметно от давления. При этом можно отметить, что для уровня Р = 2 · 108 Па, Т = 1.8 · 104 К (характерных величин для технологического использования импульсных разрядов в твердых диэлектриках) σ ≈ 1.5 (Ом · м)–1. Характерными особенностями σ(Р) являются [47] слабый линейный рост в области Р = 105–5 · 108 Па и интенсивное нелинейное нарастание при Р > 5 · 108 Па.
Обобщая многочисленные результаты исследований электрических разрядов в жидкости, направленных на изучение зависимости гидродинамических параметров процесса от режима энерговклада, отметим следующее. Снижение длительности энерговклада и обеспечение условия для критического характера разряда – основные факторы повышения эффективности преобразования электрической энергии в энергию волны давления. Важным технически является то, что максимальный к.п.д. преобразования энергии наблюдается при критических разрядах, он достигает 20–30%. Поэтому при конструировании генераторов импульсов для электрогидравлической технологии обычно стремятся уменьшить индуктивность разрядной цепи, а длину рабочего промежутка по возможности выбирают такой, при которой достигается критический режим. Установлено, что при любом уровне энергии, введенной на единицу длины канала пробоя, имеется оптимальная длительность энерговклада, обеспечивающая максимальный технологический эффект. Этот вывод соответствует результатам исследований воздействия взрыва на горный массив. Длительность энерговклада, по крайней мере, время выделения основной доли энергии, тесно связана с характерной длительностью τв волны механических напряжений, генерируемых каналом пробоя. В ряде случаев оптимальным значением τв, обеспечивающим минимальные энергозатраты на разрушение, является время двойного пробега волны механических напряжений от канала пробоя до свободной поверхности разрушаемого материала или время распространения трещин от канала до откола на свободной поверхности. Однако задачи э.и.-технологии столь многообразны (как по объектам разрушения, масштабам разрушения в единичном акте воздействия электрического импульса, так и по требуемой степени измельчения), что оптимальная длительность энерговклада изменяется в очень широких пределах: от 100 нс (тонкое измельчение) до 100 мкс (отбойка камня от массива), а априорный выбор характерной длительности разряда – достаточно сложная проблема. Определяя при установленной (например, экспериментально) оптимальной длительности энерговклада режим изменения разрядного тока, следует по возможности исключать глубокие осцилляции тока, так как моменты перехода тока через ноль соответствуют появлению волн разгрузки вокруг искрового канала, раскрытию изломов, истечению продуктов канала в них и снижению эффективности энерговклада. Для оптимального периода Топт колебаний разрядного тока, вызывающего наибольшие по размерам зоны растрескивания, вклад второй и последующих осцилляций достаточно мал. Таким образом, задача оптимизации режима энерговклада состоит в установлении условий (соотношений активных и реактивных элементов), обеспечивающих максимум выделенной энергии за первую осцилляцию (в предположении Топт/2 ≈ τв) либо в общем случае к заданному моменту времени. При этом необходимо учитывать, что лишь часть активных элементов (канал пробоя твердых диэлектриков) потребляет полезную активную энергию. Не всегда возможно технически реализовать оптимальную длительность энерговклада в э.и.-технологии. Так, вследствие большого числа последовательно включенных элементов, разнесенных в пространстве, при надежной работе изоляционных промежутков обычно не удается обеспечить τв в диапазоне 10–7–10–6с.
В этом случае в разрушаемом материале не достигаются оптимальные пиковые механические нагрузки, и задачу оптимизации целесообразно свести к определению условий (соотношений активных и реактивных элементов), обеспечивающих максимальные давления в искровом канале. Это в свою очередь наблюдается при наибольшей скорости нарастания электрической мощности в искровом канале, а для максимума давления в излучаемой волне, видимо, требуется обеспечить наибольшее значение максимальной электрической мощности в искровом канале либо средней мощности за первую осцилляцию тока.
2.2. Технические аспекты э.и.-технологий
Проведенные работы выявили ряд существенных преимуществ э.и.-метода разрушения твердых тел по сравнению с традиционными механическими способами:
– относительно низкие удельные энергетические затраты, особенно для прочных и сверхпрочных материалов;
– избирательность разрушения неоднородных структур;
– отсутствие потребности в твердосплавном, алмазном и другом подобном дорогостоящем и дефицитном инструменте;
– широкие возможности по регулированию и автоматизации процесса, в том числе в направлении поиска оптимальных режимов.
Исследования технико-экономических показателей э.и.-дробления, выполненные на различных рудах, позволили выявить ряд преимуществ данной технологии по сравнению с механическим измельчением: возможность регулирования гранулометрического состава и получения узких заданных классов крупности, высокая степень избирательности разрушения, практическое отсутствие загрязнения готового продукта аппаратным железом, слабая корреляция разрушения с механическими характеристиками сырья [48].
Особенно важным достоинством способа является достигаемая при разрушении руд и кристаллосодержащих пород высокая сохранность формы кристаллов и селективность разделения компонентов руды. Благодаря этому в последующих процессах обогащения руд достигается значительное повышение извлечения полезного минерала, а при разделке пород с ограночным кристаллосырьем, слюдяных руд и искусственной слюды за счет сохранности крупных кристаллов выход продукции в стоимостном выражении повышается на 25–35%.
Электроимпульсный способ разрушения материалов отвечает главным требованиям современности – энергетической эффективности, комплексному использованию минерального сырья, экологической чистоте.
Такие преимущества обусловлены тем, что, в отличие от разрушения при химическом взрыве, при электровзрыве источник энергии находится вне зоны превращения, а процесс ввода энергии является управляемым и определяется электрическими импедансами разрядных цепей источников. Это создает благоприятные условия для управления траекторией канала пробоя, параметрами поля механических напряжений, генерируемых вокруг канала, и в конечном счете позволяет оптимизировать удельные затраты на разрушение. Способ электроимпульсной дезинтеграции материалов с высокой технологической эффективностью апробирован на разных рудах с крупнокристаллическими включениями. Особенно перспективен способ для руд, при измельчении которых необходимо предохранить кристаллосырье от разрушения (драгоценные камни, пьезооптическое сырье, слюда) [12].
Весьма перспективным является комбинированное использование электроимпульсного разрушения, электроразрядного разупрочнения и традиционных механических способов разрушения, что открывает дополнительные возможности для повышения технологических показателей при одновременном снижении энергоемкости процессов. Применение электровзрыва в толще твердых диэлектриков наиболее перспективно для разрушения крепких и сверхкрепких минеральных образований: горных пород, руд, когда традиционные методы механического воздействия не позволяют получить высокой производительности либо требуемого технологического эффекта [4]. Физико-механические характеристики у таких материалов находятся в достаточно сильной взаимосвязи с электрической прочностью. Наиболее прочные минералы, породы не уступают по электрической прочности лучшим изоляционным материалам, вследствие чего для инициирования разряда в них требуются достаточно высокие напряжения.
3. ГЕНЕРАТОРЫ ЭЛЕКТРОИМПУЛЬСНОГО ДРОБЛЕНИЯ ИСЭ СО РАН
3.1.1. Описание импульсного генератора
Генератор предназначен для использования в установке для исследования разрушения материалов с помощью высоковольтного импульсного разряда. На рис. 2 дана электрическая блок-схема установки, на рис. 3 показано общее расположение блоков генератора. В генераторе применена зарядка через импульсный трансформатор высоковольтного емкостного накопителя (емкостью примерно 10 нФ) до напряжения 300 кВ с последующим его подключением к нагрузке через искровой разрядник с давлением около 6 атм. Энергия импульса через коаксиальную маслонаполненную линию с волновым сопротивлением примерно 45 Ом подводится к камере для дробления. В каждом импульсе регистрируется и записывается напряжение зарядки высоковольтного (в.в.) накопителя, напряжение на электродах камеры дробления, ток в камере дробления. По этим данным рассчитывается энергия, выделяемая при разряде в камере дробления. Управление генератором и системой регистрации обеспечивается персональным компьютером.
Рис. 3.
Общее расположение блоков генератора. 1 – высоковольтный блок; 2 – газовый разрядник; 3 – передающая линия; 4 – камера дробления; 5 – опора.
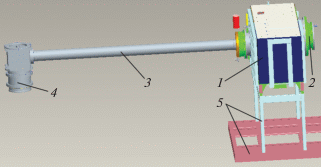
Работа установки протекает следующим образом: по команде от системы управления источник питания CCS-2 заряжает первичный накопитель С1 до заданного значения 1.5–2 кВ за 0.08 с; после зарядки пусковым импульсом Uп включается тиристорный ключ Д2; энергия от первичного накопителя С1 передается через в.в.-трансформатор Tр на конденсаторную батарею С2, заряжая ее до требуемого значения 200–300 кВ. Схема из диода Д1 (800 А, 3600 В) и резистора R1 сопротивлением 0.08 Ом размещается параллельно тиристорам. Она улавливает часть энергии импульса, которая не была передана нагрузке в случае пробоя газового разрядника ГР до максимального напряжения или в случае, когда пробоя вообще нет, и передает энергию обратно в С1. При напряжении, близком к максимальному, газовый разрядник ГР пробивается. В это время высоковольтная конденсаторная батарея С2 разряжается на нагрузку через линию передачи, формируя высоковольтный импульс на электродах камеры. Процесс повторяется до получения необходимого количества импульсов.
3.1.2. Низковольтный блок
Низковольтный блок генератора служит для накопления энергии импульса и передачи ее в высоковольтный блок. Его основные части – это накопительная конденсаторная батарея (С1, рис. 2) и тиристорный коммутатор Д2. Батарея емкостью 300 мкФ собрана из 12 параллельно включенных конденсаторов типа GLI-2150V емкостью 25 мкФ компании Vishay Esta. Максимальное зарядное напряжение +2 кВ. Накопленная энергия – до 600 Дж. В качестве тиристоров использованы быстродействующие тиристоры ТБ-353-1000А-1800V российского производства. Импульс тока низковольтного блока имеет максимальную амплитуду 11 кА и длительность 85 мкс. Импульс передается в в.в.-блок по двум специальным кабелям SILICABLE LMJ 0101060697 длиной 2 м.
Блок подмагничивания служит для приведения сердечника в.в.-трансформатора в исходное магнитное состояние в паузе между импульсами. Выход блока подсоединен к выходу низковольтного блока, и ток подмагничивания 100 А постоянно протекает по первичным обмоткам высоковольтного трансформатора. Блок контроля и управления обеспечивает следующие функции: проверку всех устройств и контактов безопасности перед разрешением на зарядку и срабатывание; регулирование задержки перед зарядкой конденсаторов в диапазоне 10 мс–10 с; управление зарядкой конденсаторов; установку времени ожидания перед следующей зарядкой при работе в режиме пачек; полный сбор параметров для каждого импульса. Система подготовки воздуха предназначена для наполнения разрядника сухим воздухом, продувки во время работы генератора и управления и сброса воздуха из разрядника по окончании работы.
3.1.3. Высоковольтный блок
Высоковольтный блок включает в себя импульсный трансформатор Тр, высоковольтную конденсаторную батарею С2, емкостный делитель напряжения, зарядный дроссель L1 и искровой разрядник ГР (см. рис. 2). Все указанные элементы собраны в металлическом баке, заполненном трансформаторным маслом. Конструктивно блок показан на рис. 4 и 5. Импульсный трансформатор Тр (1 на рис. 4) закреплен на плите из алюминия. Высоковольтный емкостный накопитель 2 установлен на опорных изоляторах. Зарядный дроссель L1 (3) расположен под высоковольтным емкостным накопителем. Зарядное напряжение от трансформатора 1 подводится к электроду 4 накопителя. Этот электрод соединяется с в.в.-электродом искрового разрядника. При возникновении пробоя между в.в.-электродом разрядника и заземленным фланцем разрядника на электроде 4 появляется импульсное напряжение, которое через проходной изолятор подается на вход передающей линии. Конструкция бака, всех элементов для подвода напряжения и выводов контролирующих сигналов позволяет вакуумировать объем бака при заполнении его трансформаторным маслом. На верхней крышке бака имеется смотровое отверстие для контроля уровня масла в баке.
Рис. 4.
Конструкция высоковольтного блока. 1 – высоковольтный импульсный трансформатор; 2 – высоковольтный емкостный накопитель; 3 – зарядный дроссель; 4 – электрод в.в.-накопителя; 5 – бак блока; 6 – опорные изоляторы; 7 – пластина емкостного делителя.
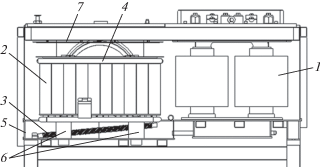
Рис. 5.
Разрез в.в.-блока в плоскости оси передающей линии. 1 – изолятор передающей линии; 2 – электроды передающей линии; 3 – конденсаторы в.в.-накопителя; 4 – верх в.в.-электрода накопителя; 5 – газовый разрядник; 6 – низ в.в.-электрода; 7 – шина между в.в.-накопителем и передающей линией.
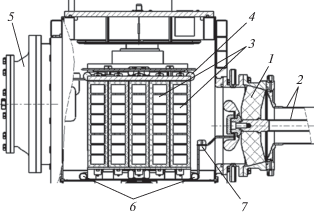
Зарядный дроссель L1 выполнен в виде соленоида, намотанного на каркасе из стеклотекстолитовых стержней. Выводы соленоида припаяны к концевым деталям, с помощью которых соленоид соединяется с электродом высоковольтного емкостного накопителя и баком в.в.-блока. Соленоид намотан медным изолированным проводом. Диаметр медной жилы ~2 мм, диаметр изоляции 3 мм. Индуктивность дросселя примерно 200 мкГн.
Устройство трансформатора показано на рис. 6. Трансформатор подвешен на плите 7 с помощью хомута 4, захватывающего магнитный сердечник 5. Сердечник стержневого типа с разрезом намотан из ленты ЭТ3425-0.08 мм шириной 110 мм. Поперечное сечение сердечника 110 × 92 мм2, размер окна 460 × 250 мм. На каждом стержне сердечника установлены одинаковые первичные и вторичные обмотки 7. Обмотки намотаны на стеклотекстолитовых каркасах и включены параллельно. Первичные обмотки – однослойные по восемь витков алюминиевой шины 4 × 40 мм. Концы первичных обмоток подсоединены к выводам 4 и 5.
Рис. 6.
Конструкция высоковольтного импульсного трансформатора. 1 – первичная обмотка; 2 – вторичная обмотка; 3 – каркасы первичных и вторичных обмоток; 4 – хомут; 5 – сердечник; 6 – текстолитовая плита; 7 – алюминиевая плита.
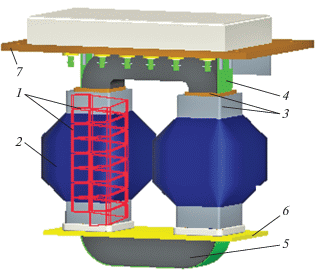
Вторичные обмотки в.в.-трансформатора – многослойные, они намотаны на стеклотекстолитовом каркасе. Общее количество слоев – 25. Все слои, кроме последнего, намотаны проводом ПЭТВ-2 диаметром 1 мм с шагом примерно 3.5 мм. Последний слой намотан виток к витку изолированным проводом с наружным диаметром 3 мм и диаметром медной жилы 2 мм. Межслойная изоляция состоит из чередующихся слоев трансформаторной бумаги толщиной 0.1 мм и лавсановой пленки толщиной 0.1 мм. Общая толщина изоляции между слоями обмотки 2 мм. В последних трех слоях обмотки дополнительно положена краевая изоляция из электротехнического картона, которая заполняет пространство между соседними слоями изоляции от края обмотки до внешнего края изоляции. Начала вторичных обмоток подсоединены к выводам, которые заземлены через шунты с величиной сопротивления 1 Ом. Концы вторичных обмоток подсоединены к в.в.-электроду емкостного накопителя.
Основные параметры трансформатора. Коэффициент трансформации 170; длительность импульса (полуволна) тока 85 мкс; амплитуда импульса тока первичной обмотки 10.6 кА, вторичной обмотки – 60 А; амплитуда импульса напряжения на вторичной обмотке (U1 = 2 кВ) – 330 кВ; омическое сопротивление первичной обмотки ~0.5 мОм, вторичной обмотки – 12 Ом; потери энергии в трансформаторе за импульс ~ 15 Дж.
Высоковольтный емкостный накопитель собран из керамических конденсаторов (3 на рис. 4) UHV-12A-1700-50 (1700 пФ, 50 кВ). Конденсаторы объединены в сборки по 8 штук последовательно и залиты эпоксидным компаундом. Заливка эпоксидным компаундом усиливает механическую прочность и внешнюю электрическую изоляцию конденсаторов. Сорок восемь таких сборок (т.е. всего 384 конденсатора) установлены между стальным основанием и в.в.-электродом (4, рис. 5) из дюралюминия и стянуты двумя капролоновыми шпильками. Емкость батареи 10.2 нФ. Концевые электроды сборок соединены с основанием и в.в.-электродом контактными проводами. Над электродом установлена дюралюминиевая пластина-экран, закрытая изоляционным барьером. Высоковольтный емкостный накопитель установлен в баке в.в.-блока на опорных изоляторах.
3.1.4. Искровой разрядник ГР
В установках для технологических применений с большой коммутируемой энергией необходимо решать проблему обеспечения надежной и стабильной работы газового разрядника в.в.-накопителя. В режимах с высокой частотой следования импульсов снижение напряжения пробоя и низкая стабильность срабатывания связаны с изменением химического состава рабочего газа, влиянием остаточной плазмы предшествующего разряда, а также нестабильностью возникновения инициирующих электронов из-за изменения состояния поверхности катода от импульса к импульсу. Разработан оригинальный частотный разрядник со стабилизацией напряжения самопробоя за счет специально создаваемого коронного разряда на электроде с отрицательным потенциалом. Так, в режиме работы разрядника с коммутируемой энергией до 500 Дж и частотой следования импульсов до 10 Гц достигнута стабильность срабатывания по напряжению на уровне 10% при времени нарастания напряжения на разряднике 100 мкс.
Конструкция разрядника приведена на рис. 7. В.в.-токоввод разрядника 1 закреплен в проходном изоляторе 2 из оргстекла. Изолятор зажат между фланцами 3 и 4 и крепится к фланцу 5, приваренному к стенке бака в.в.-блока. Разрядник закрывается фланцем 6. Разрядник работает в режиме самопробоя. Пробой происходит между электродом 9, выполненным в виде цилиндра ∅ 6 мм с плоским торцом, и электродом 8, который закреплен во фланце 6. В электроде 8 имеется сквозное отверстие ∅ 2 мм, через которое в зону разряда подается воздух с расходом порядка 1 л/с. Сброс воздуха из разрядника происходит через отверстие во фланце 6. Объем воздуха в разряднике составляет примерно 6 л. Разрядник опрессован давлением 8 ати. Допустимое рабочее давление воздуха 6 ати. Фланцы 3 и 4 разрядника выполнены из цельного блока металла, что обеспечивает высокую механическую прочность. Зазор между электродами 8 и 9 и давление в объеме разрядника устанавливаются в зависимости от выбранного режима работы.
Рис. 7.
Конструкция искрового разрядника. 1 – в.в.-токоввод; 2 – изолятор; 3–6 – фланцы разрядника; 7 – стенка бака; 8, 9 – электроды.
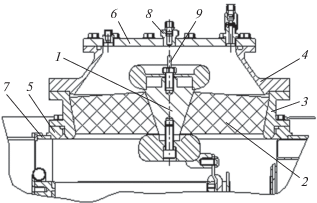
Такая конфигурация электрода с острой кромкой на в.в.-электроде 9 и продувкой воздухом во время работы позволила получить стабильную работу с низким разбросом пробивного напряжения во время серии выстрелов. Необходимо отметить, что при гладкой форме электродов разброс в пробивном напряжении значительно выше. Такое поведение работы разрядника можно объяснить эффектом стабилизации короны, который имеет место в электроотрицательных газах, таких как воздух и элегаз, и требует наличия большого усиления электрического поля на электроде [49, 50]. В условиях постоянного тока или медленно растущего зарядного напряжения (10 мкс и более) на электроде с большим усилением электрического поля развивается пространственный заряд, который предотвращает преждевременный пробой и позволяет полностью восстановить напряжение.
После заполнения разрядника сухим воздухом (точка росы –40°С) без продувки разрядника разброс в напряжении срабатывания разрядника увеличивается с увеличением числа включений. После полной смены воздуха в объеме разрядника весь цикл повторяется. Показано, что основной причиной разброса пробивного напряжения разрядника является наработка окислов азота в его объеме [51, 52]. Предложен метод оценки потока воздуха, при котором обеспечивается стабильная работа разрядника в частотном режиме. Установлены режимы продувки воздуха, обеспечивающие стабильность срабатывания не хуже 10%.
3.1.5. Передающая линия и камера для дробления материалов
Конструкция передающей линии приведена на рис. 8. Передающая линия выполнена в виде коаксиала из труб из нержавеющей стали. Внутренний проводник имеет диаметр 40 мм, внешний – 128 мм, длина линии 2.5 м. Линия крепится к баку в.в.-блока с помощью фланца 3. Центральный проводник передающей линии закреплен на изоляторе 4. На противоположном конце линии центральный проводник соединен с токовводом 5 проходного изолятора камеры дробления. Линия заполняется трансформаторным маслом, при этом волновое сопротивление линии составляет около 47 Ом. Масло в передающую линию заливается автономно и не имеет связи с маслом в баке в.в.-блока.
Рис. 8.
Передающая линия и камера дробления материалов. 1, 2 – проводники передающей линии; 3 – фланец для соединения с в.в.-блоком; 4 – переходный изолятор; 5 – токоввод: 6 – проходной изолятор; 7 – изолятор камеры дробления; 8 – в.в.-электрод камеры дробления; 9 – заземленный электрод; 10 – полость для размещения материала; 11 – съемный фланец.
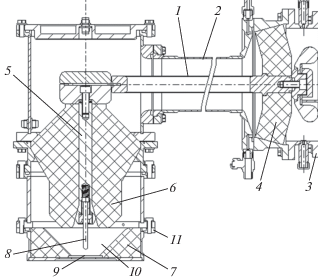
Конструкция камеры для дробления материалов также дана на рис. 8. Материал для дробления помещается в конусной полости 10 изолятора 7. Разряд происходит между электродами 8 и 9 через обрабатываемый материал. Расположение электрода 8 регулируется через пружинное крепление, расположенное внутри токоввода 5. Все элементы камеры дробления изготовлены из нержавеющей стали, в.в.-изолятор – из блочного полиэтилена. Камера для дробления испытана при давлении 3 атм. В камере для дробления имеются следующие датчики: емкостный делитель напряжения на центральном электроде камеры, экранированный индуктивный датчик тока камеры, установленный в корпусе камеры, и изолированный индуктивный датчик тока камеры, установленный на крышке камеры.
3.1.6. Результаты экспериментов и обсуждение
Осциллограммы зарядного напряжения на высоковольтном емкостном накопителе приведены на рис. 9. Амплитуда напряжения составляет около 240 и 290 кВ для зарядных напряжений 1.5 и 1.8 кВ соответственно. Кривые тока и напряжения нагрузки приведены на рис. 10а и 10б для работы на эквивалентной нагрузке и в режиме дробления породы. Напряжение и ток на рис. 10а демонстрируют экспоненциальный спад, характерный для разряда емкости на активную нагрузку. Временное поведение напряжения и тока одинаково на активной нагрузке, и там нет никакой задержки между напряжением и током. Формы сигналов в режиме дробления рис. 10б совершенно различны: в начале импульса происходит большой скачок напряжения, затем напряжение резко падает в момент полного пробоя, и ток возрастает. Амплитуда тока в режиме дробления примерно в три раза больше, чем в режиме активной нагрузки.
Рис. 9.
Осциллограммы напряжения на высоковольтном емкостном накопителе при зарядном напряжении 1.5 и 1.8 кВ на первичном накопителе.
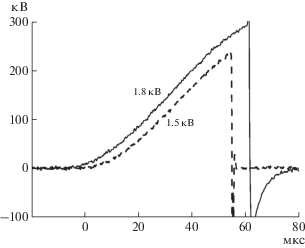
Рис. 10.
Напряжение нагрузки U и ток I (зарядное напряжение 1.8 кВ) при работе: а – на эквивалентной нагрузке; б – в режиме дробления породы.
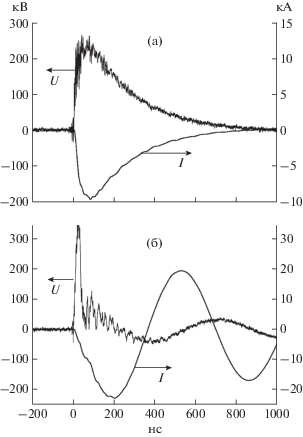
На рис. 11 приведены статистические функции распределения нормированного на единицу пробивного напряжения искрового промежутка при активной нагрузке 40 Ом (f1(U)) и в режиме дробления породы (f2(U)) серии из 1000 выстрелов с частотой 10 Гц при тех же параметрах выстрела (зарядное напряжение 1.8 кВ, давление воздуха в газовом разряднике 6.2 бар, искровой промежуток 18 мм). Анализ кривых на рис. 11 показывает, что при почти одинаковом напряжении 287 кВ пиковые значения обеих функций имеют ширину на половине максимума 8.72 кВ для режима дробления породы по сравнению с 5.6 кВ для активной нагрузки. Есть также “хвост”, удлиненный к достаточно низким напряжениям в функции распределения для режима дробления, в то время как для активной нагрузки вообще нет пробоев ниже 280 кВ. Некоторое расплывание функции распределения для режима дробления, вероятно, связано с увеличением энергии, рассеиваемой в газовом разряднике, в этом режиме. Но в худшем случае разброс пробивного напряжения в районе среднего значения 287 кВ не превышает 5%, что вполне хорошо для неуправляемого разрядника. В табл. 1 приведены основные параметры работы генератора при зарядных напряжениях 1.5 и 1.8 кВ для двух нагрузок. Фронт импульса напряжения (примерно 50 нс) одинаков для всех исследованных режимов работы.
3.2.1. Общее описание
Принципиальная электрическая схема генератора приведена на рис. 12. Высоковольтный емкостный накопитель С2 с емкостью примерно 20 нФ заряжается через импульсный трансформатор. После зарядки до напряжения 300 кВ в.в.-накопитель подключается к нагрузке через искровой разрядник ГР. Одно существенное различие от схемы на рис. 2 заключается в добавлении защитного индуктора L2 (220 мкГн, 40 Ом) в цепь разряда в.в.-накопителя. Он гасит колебания, возникающие после основного разряда.
Батарея С1 с полной емкостью 601.6 мкФ собрана из 128 параллельно включенных конденсаторов E53.M59-472T21 емкостью 4.7 мкФ компании Electronicon, которые конструктивно выполнены в виде четырех блоков, каждый из которых содержит по 32 конденсатора. Предусмотрена коммутация блоков для работы в режимах 0.25, 0.5 и 1 кДж. Для подключения и отключения блоков используются перемычки. Предельно допустимое зарядное напряжение +2 кВ. Максимальная запасаемая энергия – 1.2 кДж.
Высоковольтный источник питания 802L 2 кВ фирмы LAMBDA осуществляет зарядку первичной накопительной конденсаторной батареи С1 до заданного значения 1.5–2 кВ. После зарядки запускается тиристорный ключ Д2, и энергия от первичного накопителя С1 передается через в.в.-трансформатор Тр на высоковольтную конденсаторную батарею С2. Импульс тока низковольтного блока имеет максимальную амплитуду 16 кА и длительность 125 мкс.
3.2.2. Высоковольтный блок
В.в-блок состоит из блока в.в.-трансформатора и блока высоковольтного емкостного накопителя, размещенных на общей раме (рис. 13). Блок в.в.-трансформатора закреплен на раме неподвижно. Блок высоковольтного емкостного накопителя установлен на регулируемых опорах и колесах, что позволяет отстыковывать блок от блока трансформатора и перемещать его по раме.
3.2.3. Блок в.в.-трансформатора
Этот блок включает в себя импульсный трансформатор и защитный дроссель. Все указанные элементы собраны в металлическом баке 1, заполненном трансформаторным маслом. Конструкция бака для трансформатора и всех элементов для подведения напряжения позволяет вакуумировать объем бака при заполнении его трансформаторным маслом. На верхней крышке бака имеется смотровое окно для контроля уровня масла в баке.
Разработан импульсный трансформатор на напряжение до 300 кВ с секционированными вторичными обмотками с межвитковой изоляцией конденсаторного типа. За счет секционирования обмоток в совокупности с большой межвитковой емкостью в секции достигается выравнивание напряженности электрического поля вдоль секций и снижаются перенапряжения, возникающие при переходных процессах. Конструкция трансформатора позволяет за счет увеличения числа последовательных секций масштабировать трансформатор на более высокий класс напряжения до 500 кВ при сохранении напряженности электрического поля в межвитковой изоляции.
Конструкция трансформатора представлена рис. 14. Трансформатор подвешен на плите 1 с помощью хомута 2, охватывающего магнитный сердечник 4. Сердечник стержневого типа с разрезом, он намотан из ленты ЭТ3425-0.08 мм шириной 110 мм. Поперечное сечение сердечника 110 × 92 мм2, размер окна 556 × 250 мм. На каждом стержне сердечника установлены одинаковые первичные и вторичные обмотки.
Рис. 14.
Конструкция высоковольтного импульсного трансформатора. 1 – несущая плита; 2 – фиксирующий хомут; 3 – вторичные обмотки; 4 – сердечник; 5, 6 – выводы первичных обмоток; 7 – выводы вторичных обмоток.
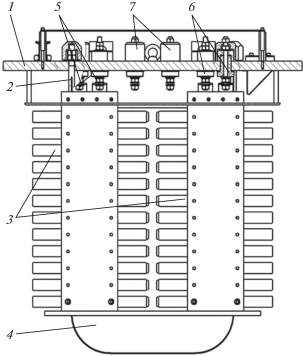
Первичные обмотки 1 – однослойные, содержащие по восемь витков алюминиевой шины 4 × 40 мм, они намотаны на стеклотекстолитовых каркасах. Концы первичных обмоток подсоединены к выводам 5 и 6.
Вторичные обмотки в.в.-трансформатора – секционированные (рис. 15). Каждая обмотка состоит из 12 секций 1, закрепленных на несущих стеклотекстолитовых пластинах 2. Секции объединены в 2 группы по 6 штук в каждой. Внутри группы секции соединены последовательно, а группы соединены параллельно таким образом, что верхняя и нижняя секции соединены с нулевым проводником, а высокое напряжение выводится со средних секций. Каждая секция состоит из 200 витков, намотанных алюминиевой лентой шириной 20 мм и толщиной 0.05 мм. Межвитковая изоляция – лавсановая лента шириной 30 мм и толщиной 0.1 мм. Снаружи и внутри секции установлены внешний 3 и внутренний 4 экраны, выполненные из алюминиевой шины 4 × 30 мм. Начала вторичных обмоток подсоединены к выводам 7 (рис. 14), которые заземлены через шунты сопротивлением 1 Ом. Концы вторичных обмоток подсоединены к электроду защитного резистора. Использование в секциях обмотки изоляции конденсаторного типа позволило снизить напряженность в межвитковой изоляции до 2.5 кВ/мм, что практически на порядок ниже, чем в первой конструкции трансформатора (рис. 6). Секционированные обмотки в совокупности с большой межвитковой емкостью в секции позволяют уменьшить перенапряжения, возникающие при разряде высоковольтного емкостного накопителя генератора.
Рис. 15.
Конструкция вторичной обмотки в.в.-трансформатора. 1 – секция обмотки; 2 – несущая пластина; 3 – внешний экран секции; 4 – внутренний экран секции.
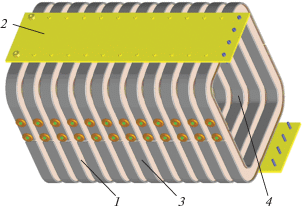
Импульс тока от низковольтного блока передается в в.в.-блок по двум кабелям SILICABLE. Жилы кабелей подсоединены к выводам 5 и 6 так, чтобы напряжение на вторичной обмотке имело отрицательную полярность.
Основные параметры трансформатора. Коэффициент трансформации 150; длительность импульса (полуволна) тока 110 мкс; амплитуда импульса тока: первичной обмотки 16 кА, вторичной обмотки 60 А; амплитуда импульса напряжения на вторичной обмотке (U1 = 2 кВ) – 300 кВ; омическое сопротивление: первичной обмотки ~0.5 мОм, вторичной обмотки 12 Ом; потери энергии в трансформаторе за импульс ~15 Дж.
3.2.4. Блок высоковольтного емкостного накопителя
Блок содержит высоковольтный емкостный накопитель 1, искровой разрядник 2, узел дробления 3, зарядный дроссель 4 и емкостный делитель напряжения 5 (см. рис. 16а). Все указанные элементы собраны в металлическом баке, заполненном трансформаторным маслом. На верхней крышке бака имеется смотровое окно для контроля уровня масла в баке.
Рис. 16.
Продольное сечение блока высоковольтного емкостного накопителя (а: 1 – конденсаторные сборки; 2 – искровой разрядник; 3 – узел дробления; 4 – зарядный дроссель; 5 – пластина емкостного делителя и сечение конденсаторной сборки; б: 6 – конденсаторы сборки; 7 – верхняя монтажная пластина; 8 – цанговая контактная пластина; 9 – корпус, выполненный из эпоксидного компаунда).
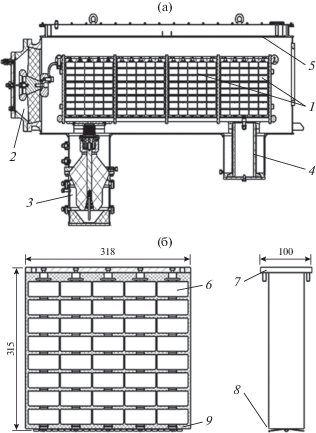
Высоковольтный емкостный накопитель выполнен в виде пространственной несущей конструкции – этажерки, состоящей из четырех секций (1). Каждая секция, в свою очередь, состоит из пяти конденсаторных блоков. Конденсаторный блок (рис. 16б) состоит из 40 керамических конденсаторов UHV-12A (1700 пФ, 50 кВ, производство компании TDK), соединенных последовательно-параллельно и залитых эпоксидным компаундом. Снизу на каждой сборке закреплена цанговая контактная пластина 8, которая обеспечивает контакт конденсаторов с нижними низковольтными стержнями. Высоковольтный емкостный накопитель установлен в баке на четырех опорах, закрепленных шарнирно в перегородках. Дополнительной опорой накопителя служит изолятор зарядного дросселя. Всего получается 800 конденсаторов с полной емкостью батареи 21.25 нФ. Изменение емкости производится удалением или установкой части конденсаторных сборок.
Камера для дробления и разрядник в основных чертах подобны описанным выше (см. рис. 8).
3.2.5. Результаты экспериментов и обсуждение
Осциллограммы зарядного напряжения на высоковольтном емкостном накопителе приведены на рис. 17. Амплитуда напряжения составляет около 290 кВ при зарядном напряжении 1.8 кВ. Длительность импульса больше примерно на 25 мкс при 1000 Дж запасаемой энергии.
Рис. 17.
Осциллограммы напряжения на высоковольтном емкостном накопителе при зарядном напряжении 1.8 кВ на первичном накопителе при запасаемой энергии, равной 500 и 1000 Дж.
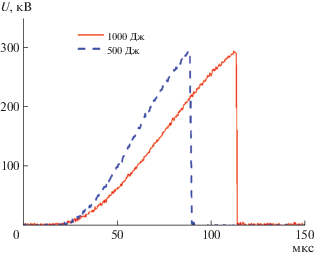
Кривые тока и напряжения нагрузки приведены на рис. 18а и 18б для работы на эквивалентной нагрузке и в режиме дробления. Напряжение и ток на рис. 18а демонстрируют экспоненциальный спад, характерный для разряда емкости на активную нагрузку, с небольшими колебаниями из-за переходных процессов. Временное поведение напряжения и тока одинаково на активной нагрузке, и там нет никакой задержки между напряжением и током. Формы сигналов в режиме дробления рис. 18б совершенно различны: в начале импульса происходит большой скачок напряжения, затем напряжение резко падает в момент полного пробоя, и ток возрастает. Амплитуда тока в режиме дробления почти в четыре раза больше, чем в режиме активной нагрузки. Фронт импульса напряжения (примерно 50 нс) одинаков для всех исследованных режимов работы. В табл. 2 приведены основные параметры работы генератора в зависимости от запасаемой энергии при зарядном напряжении 1.8 кВ.
3.3.1. Блок-схема установки
Блок-схема генератора для дробления материалов представлена на рис. 19. Установка состоит из шкафа электропитания и управления и блока импульсного генератора с камерой дробления.
Шкаф электропитания и управления содержит следующие блоки:
• высоковольтный источник питания, служащий для зарядки конденсаторов импульсного генератора;
• формирователь управляющего импульса – при срабатывании генератора формирует сигнал, поступающий в счетчик импульсов и через него в высоковольтный источник питания;
• счетчик импульсов включает высокое напряжение, осуществляет счет срабатываний генератора и выключает высокое напряжение после достижения заданного количества импульсов;
• замыкатель – элемент системы безопасности, обеспечивающий разряд конденсаторов генератора по окончании работы или в случае аварии;
• элементы воздушной системы, которые осуществляют подачу газа в разрядник генератора до заданного давления и сброс газа после пачки импульсов.
Все блоки и элементы располагаются в металлическом шкафу размером 0.55 × 0.55 × 1.15 м.
Используется высоковольтный источник питания с постоянным выходным током и максимальным выходным напряжением 50 кВ, со скоростью зарядки 8 кДж/с, с отрицательной полярностью выходного напряжения серии 802L-50КВ-NEG-400VAC (производство компании TDK-Lambda, США).
Блок импульсного генератора с камерой дробления выполнен в виде бака, заполненного трансформаторным маслом (рис. 20). В баке размещены генератор, собранный по схеме Маркса, опорный изолятор и узел проходного изолятора, к которому пристыкована камера дробления. Камера дробления заполнена водой и имеет полость, куда помещается разрушаемый образец. В камере имеются датчик тока, а также активный и емкостный делители напряжения.
Установка работает следующим образом. Оператор устанавливает на высоковольтном источнике питания необходимое зарядное напряжение генератора, на счетчике – число импульсов в пачке, период срабатывания генератора и давление газа в разряднике. При подаче команды “Старт” генератор начинает работать. Высоковольтный источник питания заряжает конденсаторы генератора до 25–50 кВ за 0.2–0.9 с. При достижении напряжения самопробоя разрядники генератора импульсных напряжений пробиваются, и импульс напряжения амплитудой 200–400 кВ передается на камеру дробления. Импульсы напряжения и тока камеры, снятые с делителей и датчика тока, регистрируются осциллографом.
Генератор импульсного напряжения собран по схеме Маркса (рис. 21). В генераторе 8 ступеней С1–С8. В каждой ступени генератора используются два параллельно соединенных конденсатора ИК-100-0.4. Это конденсатор с бумажно-масляной изоляцией, пропитанной касторовым маслом. Максимальное рабочее напряжение конденсатора 100 кВ, емкость 0.4 мкФ, внутренняя индуктивность 140 нГн. Габаритные размеры конденсатора 455 × 500 × 150 мм, его масса 32 кг. Ступени генератора заряжаются через зарядные дроссели L1R1–L16R16. Это воздушные дроссели с индуктивностью 145 мкГн и активным сопротивлением 29 Ом. Разрядники генератора S1–S8 – двухэлектродные искровые разрядники, заполненные сухим воздухом. Электрическая прочность промежутков разрядников регулируется изменением в них давления воздуха. Все 8 разрядников генератора монтируются в одном корпусе из стеклоэпоксидной трубы, образуя блок разрядников.
3.3.2. Конструкция импульсного генератора
Конструкция генератора приведена на рис. 22. Конденсаторы ступеней 1 установлены в контейнере 2. Контейнер выполнен из дельта-древесины, с одной стороны он закреплен на стенке бака 8 генератора, с другой опирается на изолятор из оргстекла 6. Над конденсаторами размещается блок разрядников 3 с прикрученными к нему зарядными дросселями 4. Все ступени генератора закрыты экранами 5 из алюминия, которые соединены с низковольтными выводами конденсаторов. Зарядное напряжение к конденсаторам ступеней подводится кабелем через разъем 9. Напряжение от генератора в камеру для дробления подается через проходной изолятор 7. Корпус генератора заполнен трансформаторным маслом. Объем масла около 1.5 м3, масса генератора составляет примерно 2.5 т.
3.3.3. Разрядники генератора
В генераторе используются двухэлектродные искровые разрядники, заполненные воздухом. Электрическая прочность промежутков разрядников регулируется изменением давления воздуха в них. Все восемь разрядников монтируются в одном корпусе из стеклоэпоксидной трубы ∅ 130 мм, образуя блок разрядников. Электродная система разрядника приведена на рис. 23. Электроды 1 закреплены на трубе 3 болтами 5. К контактам 2 подключаются зарядные дроссели и конденсаторные шины (см. рис. 22). Уплотнительные кольца 4 из фторопласта обеспечивают герметичность объема разрядника. Величина межэлектродного зазора в разрядниках составляет 8 мм. Электроды разрядников выполнены из меди. Для защиты от продуктов разряда внутренняя поверхность корпуса разрядника закрыта полосами лавсановой пленки толщиной 0.2 мм. Полосы плотно вставлены между уплотнительными кольцами 4 противоположных электродов.
Рис. 23.
Сборка электродной системы разрядника (а). 1 – медные электроды; 2 – контакты для соединения с конденсаторами; 3 – корпус; 4 – уплотнительные кольца, d – искровой зазор; б – трехмерный вид.
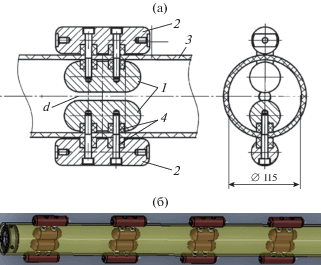
3.3.4. Зарядный дроссель
Это дроссель без ферромагнитного сердечника с индуктивностью 145 мкГн и активным сопротивлением 29 Ом. Обмотка дросселя выполнена нихромовым проводом на стеклопластиковой трубе. Концы обмотки закреплены в отверстиях электродов с помощью клиньев. Сверху нихромовый провод обмотан стеклонитью, пропитанной эпоксидным компаундом. Использование в соленоиде дросселя проводника из нихрома позволяет при малых потерях энергии при зарядке конденсаторов ступеней ограничить ток при саморазряде генератора на уровне 1.5–2 кА и обеспечить достаточную механическую прочность дросселя. Минимизация рассеянных магнитных полей в сильноточных индукторах и проблемы механической прочности исследовались автором в работах [53–55]. Внутреннее пространство генератора Маркса с размещением и соединениями конденсаторов, разрядников и индукторов показано на рис. 24.
3.3.5. Конструкция камеры для дробления
Камера для дробления изображена на рис. 25. Корпус камеры для дробления 1 выполнен в виде параллелепипеда с размерами 500 × 400 × 400 мм. В цилиндре 8, который соединяет камеру дробления и генератор, установлен проходной изолятор 3 из полиэтилена, зажатый фланцем 2. Напряжение от генератора через проходной изолятор по центральному проводнику 4 подводится к электроду 5. Разряд замыкается между электродами 5 и 7. В конусной полости изолятора 6 помещается материал для дробления. Корпус заполняется водой. В верхней части корпуса оставляется зазор с воздухом для уменьшения силы гидроудара на стенки камеры. В цилиндре 8 установлены емкостный делитель для измерения напряжения на электродах и индуктивный датчик тока. Напряжение на нагрузке после пробоя измеряется активным жидкостным делителем 12.
Рис. 25.
Камера дробления. 1 – корпус; 2 – фланец; 3 – изолятор; 4 – центральный токопровод; 5 – высоковольтный электрод; 6 – изолятор разрядной камеры; 7 – заземленный электрод; 8 – переходной цилиндр; 9, 10 – датчики; 11 – корпус делителя напряжения; 12 – водяная колонна активного делителя; 13 – вывод делителя.
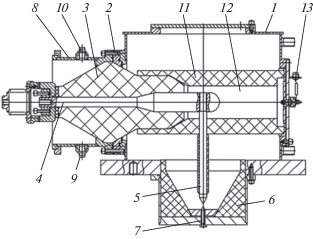
3.3.6. Режимы работы генератора
Генератор испытан при работе в двух режимах:
– режиме эквивалентной нагрузки;
– режиме дробления.
В режиме эквивалентной нагрузки сопротивление нагрузки образовано столбом воды между электродом и дном корпуса. Величина нагрузки составляет примерно 8 Ом. Зазор между высоковольтным электродом и дном корпуса равен 36 мм.
Конфигурация электродов камеры дробления при работе в режиме дробления материала приведена на рис. 25. Зазор между в.в.-электродом 5 и электродом 8 равен 20 мм. Испытания генератора проводились при давлении воздуха в разрядниках генератора 1, 1.5, 2, 2.5 и 3 ата. Напряжение самопробоя разрядников при этих давлениях составляло соответственно 20, 26, 32, 39 и 45 кВ. Характерные осциллограммы напряжения на нагрузке и тока в нагрузке с датчиков камеры дробления для этих режимов приведены на рис. 26, а в табл. 3 – основные параметры работы установки в режиме дробления. Из рис. 26б видно, что наблюдается ярко выраженная фаза в.в.-разряда с квазипрямоугольной формой импульса напряжения, в отличие от резкого пика напряжения для генераторов с меньшей энергией (рис. 10б и 18б). Из табл. 3 следует, что продолжительность высоковольтной фазы уменьшается при увеличении напряжения. Около 55% от первоначальной накопленной энергии рассеивается в зоне разряда для этого режима, остальное – в разрядниках, внутренних сопротивлениях конденсаторов и других активных элементах разрядной цепи.
Рис. 26.
Осциллограммы напряжения и тока при зарядном напряжении 20 и 45 кВ: а – в режиме эквивалентной нагрузки; б – в режиме дробления.
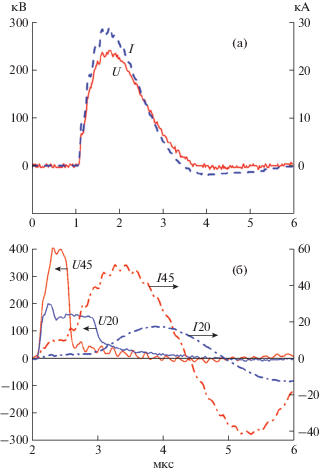
Таблица 3.
Основные параметры работы установки в режиме дробления (P – давление в разрядниках, U0 – зарядное напряжение)
P, атм | U0, кВ | Энергия батареи, Дж | Напряжение нагрузки, кВ | Ток нагрузки, кА | Длительность в.в.-фазы, нс |
---|---|---|---|---|---|
1 | 20 | 1280 | 190 | 17 | 1000 |
2 | 32 | 3277 | 280 | 34 | 800 |
2.5 | 39 | 4867 | 340 | 42 | 600 |
3 | 45 | 6480 | 410 | 51 | 500 |
3.4.1. Общее описание и блок-схема
Не исследованным ранее подходом является использование ступени линейного трансформатора (или сборки ступеней) как генератора дробления. Общий вид стенда ступени линейного трансформатора дан на рис. 27а, а детализация конденсаторного блока с одним снятым электродом – на рис. 27б. Схема сборки для N ступеней приведена на рис. 28а. В созданной ступени один конденсатор ИК-50-3 (емкость 3 мкФ) включается многоканальным искровым разрядником 4 на два параллельно включенных индуктора 6. Использован многоканальный многозазорный разрядник линейной геометрии, подобный описанному в работах [56, 57]. Конструкция индуктора подробно описана в [58, 59]. Вольт-секундный интеграл индукторов ступени примерно равен 40 мВ ∙ с. Вторичный виток, пропущенный через индукторы, позволяет удвоить напряжение на выходе ступени. Индуктивность разрядного контура ступени 0.12 мкГн, сопротивление 0.053 Ом. Волновое сопротивление ступени, приведенное к вторичной стороне трансформатора, составляет 0.5 Ом. Ступень испытана при зарядном напряжении 25–40 кВ. В режиме короткого замыкания получен ток 80 кА с временем до максимума около 0.9 мкс. Ступень может использоваться для создания линейных трансформаторов для нагрузок с переменным сопротивлением со временем высокоомного состояния нагрузки меньше 0.2 мкс.
Рис. 27.
Внешний вид: а – стенда ступени линейного трансформатора (1 – конденсаторный блок; 2 – генератор подмагничивания; 3 – пусковой генератор), б – конденсаторного блока с одним снятым электродом (4 – разрядник; 5 – конденсатор; 6 – индукторы; 7 – выходной электрод; 8 – нагрузка 1 Ом).
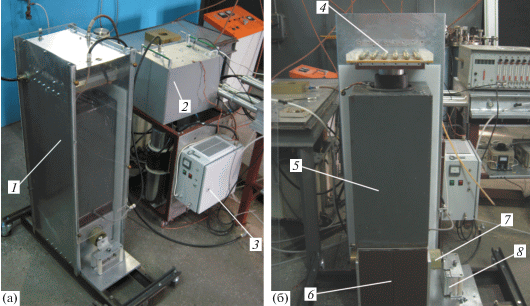
Рис. 28.
Схема сборки для N последовательных ступеней (а: С – конденсаторы, Т – индукторы, Д – диоды, Р – разрядники, ИП – источник питания, ПГ – пусковой генератор, ГМ – генератор подмагничивания); б – осциллограммы при работе блока с нагрузкой 1 Ом при зарядном напряжении 35 кВ. Масштаб по вертикали: для напряжения U = 10 кВ/деление, тока I = 10 кА/деление, энергии E = 0.3 кДж/деление, вольт-секундного интеграла магнитного сердечника S = 8 (мВ ∙ с)/деление; по горизонтали – 1 мкс/деление.
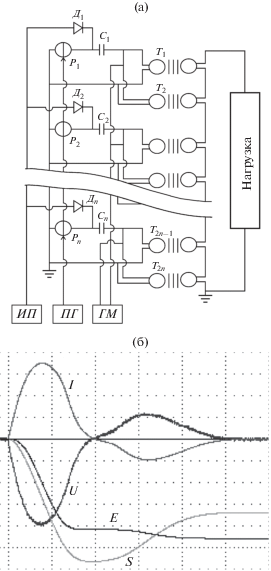
3.4.2. Особенности использования линейного трансформатора в схемах электроимпульсных технологий
Необходимо учитывать, что в генераторе по схеме линейного трансформатора длительность импульса ограничивается вольт-секундным интегралом сердечников, и изготовление генератора по данной схеме целесообразно при создании короткого импульса напряжения на нагрузке. В устройстве для электроимпульсного разрушения материалов длительность импульса высокого напряжения на электродах камер для дробления определяется временем до пробоя между электродами и может изменяться примерно от 0.1 мкс до нескольких микросекунд. Требуемая задержка в основном определяется обрабатываемым материалом: чем больше его электрическая прочность, тем больше время задержки до пробоя. Поэтому схема со ступенями наиболее перспективна для легко пробиваемых материалов, например, для отходов электроники (см. ниже разделы 4.3, 4.4).
Длительность импульса может варьироваться изменением индукторов, конденсаторов и числа ступеней. Вместо конденсатора ИК-50-3 могут быть использованы конденсаторные блоки [60, 61] или ступени LTD. Ранее нами были разработаны компактные ступени LTD с воздушной изоляцией [62–64]. Это позволяет варьировать длительность импульса, напряжение и ток нагрузки в широких пределах. На рис. 28б приведены осциллограммы при работе блока с нагрузкой 1 Ом. Напряжение достигает 40 кВ при токе 35 кА, выделившаяся энергия E равна 1.3 кДж при зарядном напряжении 35 кВ.
Основным преимуществом является то, что для одинакового энергозапаса схема со ступенью значительно проще, дешевле (примерно в три раза) и компактнее, чем описанные выше установки. Низкая цена обусловлена отсутствием большого количества дорогих керамических конденсаторов. Но для нее есть свои особенности в применениях, отмеченные здесь.
4. НЕКОТОРЫЕ ТЕХНОЛОГИЧЕСКИЕ ПРИМЕНЕНИЯ
4.1. Получение кварцевых концентратов высокой чистоты
Высокочистые кварцевые концентраты (в.ч.к.) – продукт измельчения природного кварца, очищенный от минеральных и химических примесей, с размером частиц 100–300 мкм и совокупным содержанием примесей (массовая доля) не более 20–30 ppm. Кроме того, отдельно в составе в.ч.к. регулируется содержание ключевых примесей – бора, фосфора, щелочных металлов. Кроме в.ч.к. также существуют ультрачистые кварцевые концентраты, в которых содержание примесей не превышает 10 ppm. Актуальность проблемы обусловлена потребностями оборонной промышленности, электроники и других областей в в.ч.к. и кварцевых стеклах на их основе для изготовления радиопрозрачных обтекателей высокоскоростных летательных аппаратов, крупногабаритной оптики для оснащения мощных лазерных установок и ламп накачки, кварцевых тиглей для выращивания монокремния и мультикремния для “солнечной” энергетики, кварцевых диффузионных труб и оснастки в производстве микроэлектроники, керамических наноматериалов, термостойких огнеупорных материалов на основе кварцевого стекла для оснащения отечественных предприятий черной и цветной металлургии и др. [65].
Промышленное производство в.ч.к. осуществляется из природного кварцевого сырья, обладающего высокой химической чистотой и низким содержанием минеральных примесей, легко поддающихся удалению в процессе обогащения. При этом актуальной проблемой при создании технологии производства в.ч.к. является предотвращение или минимизация влияния процессов дробления на химическую чистоту исходного материала.
Наличие селективного метода устранения загрязняющих минералов в кварце имеет решающее значение для достижения высокой чистоты кремниевого сырья для производства солнечных элементов из кремния. В работе [9] детально оцениваются и сравниваются эффекты электрической фрагментации с обычным механическим дроблением: в частности, для удаления мелкозернистых микроэлементов, которые часто ставят под угрозу перспективные кварцевые изделия высокой чистоты. Обсуждается также возможность комбинирования обоих методов измельчения. Исследовался объемный образец кварца гидротермальной жилы, содержащий незначительные примеси (<1%) мусковита и ортоклаза. Анализировались морфология частиц, распределение трещин и степень удаления примесных минералов методами оптической и электронной микроскопии. Электрическая фрагментация генерирует частицы со сферической геометрией и дает более высокий процент удаленных минералов. Механическое дробление, напротив, приводит к образованию удлиненных фрагментов с трещинами параллельно поверхностям фрагментов. Мусковит разрушается как по плоскостям спайности, так и по границам зерен, тогда как ортоклаз разрушается только по границам зерен. Были сделаны следующие заключения: 1) при электрической фрагментации образуется больше расколов, которые избирательно направляются в сторону минеральных включений; механическое дробление приводит к меньшему количеству расколов и их сильной поляризации параллельно границам зерен; 2) электрическая фрагментация увеличивает удаление посторонних микроэлементов и уменьшает появление внедренных частиц; 3) электрическая фрагментация более выгодна для получения как более крупных удаленных частиц, так и кварца с плотной случайной сетью расколов; электрическая фрагментация требует меньше энергии для обработки.
В традиционных механических методах измельчения рабочие мелющие органы оборудования подвержены высокому абразивному износу, приводящему к интенсивному загрязнению исходного материала. При электроимпульсном дроблении инструментом разрушения является высоковольтный электрический разряд, и вращающиеся рабочие узлы отсутствуют, что позволяет минимизировать унос массы узлов камеры дробления в измельчаемый материал [66]. В этой связи электроимпульсное дробление высокоабразивных особо чистых материалов предпочтительнее механического измельчения [67, 68].
4.2. Дробление твердых пород и композитов
В качестве примера можно привести генераторы для дробления бетона серии FRANКА (Карлсруэ, Германия) [10] – лабораторная установка FRANКА 0 с выходным напряжением до 250 кВ, энергозапасом 750 Дж и с частотой следования импульсов до 5 Гц, а также прототип промышленной установки FRANКА 2 с выходным напряжением до 350 кВ и производительностью до 280 кг/ч. Запасаемая энергия в генераторах по схеме Аркадьева–Маркса для целей электроимпульсного разрушения материалов может достигать примерно 10 кДж при выходном напряжении около 400 кВ и частоте следования импульсов около 1 Гц. Для повышения скорости нарастания напряжения на разрядном промежутке, удержания его на время задержки пробоя и увеличения эффективности вложения энергии в канал разряда на выходе генератора Аркадьева–Маркса устанавливают дополнительный обостряющий конденсатор в виде отрезка коаксиальной линии с выходным разрядником, непосредственно к которому подключают разрядную камеру.
В работе [4] проведены исследования закономерностей изменения основных характеристик электроимпульсного разрушения гранита как одной из наиболее распространенных крепких и очень крепких горных пород в широком диапазоне изменений расстояния между электродами и энерговклада на единицу длины межэлектродного промежутка. Процесс электроимпульсного разрушения горных пород – многофакторный и, в частности, зависит от свойств, строения и состава горной породы, характеристик жидкой среды, параметров импульса напряжения, механизма развития канала разряда в жидкой и твердой фазах и ряда других параметров. Одной из важных характеристик разрушения является глубина внедрения канала разряда.
Ряд работ посвящен обработке угольной руды. Уголь – это сложное вещество, содержащее множество видов минералов с широким распределением по размерам и компонентам в зависимости от сорта и месторождения. Так, в работе [8] исследована возможность дробления угля с использованием высоковольтных электрических импульсов в воздушной среде для повышения проницаемости пласта метана угольного пласта. Показано, что напряженность пробивного поля образца угля была примерно на порядок меньше, чем у воздуха. Результаты микроанализа показали, что проницаемость метанового пласта значительно увеличивалась высоковольтными электрическими импульсами. Полученные экспериментальные результаты свидетельствуют о том, что электроразрядная обработка является перспективной технологией повышения выхода метана в угольных шахтах. В работе [69] проводилось сравнение электроимпульсного дробления угля с механическим измельчением. Было показано, что коэффициенты образования легких чистых фракций угля и тяжелых отходов при электроимпульсном дроблении были выше, чем при механической обработке.
Полимерные композиционные материалы (п.к.м.) обладают уникальными свойствами, благодаря чему используются во многих отраслях промышленности. По типу полимерной матрицы п.к.м. делятся на реактопласты и термопласты (потребление п.к.м. по типу полимерной матрицы в мире оценивается следующим образом: 67% – реактопласты; 33% – термопласты). Среди полимерных матриц с экологической точки зрения термопласты желательны для использования в п.к.м., однако высокие вязкость расплава и стоимость сырья являются основными ограничениями их массового применения. Термопласты также требуют дорогостоящих технологий обработки, при которой используются высокие температуры (200–400°С) и давление. Реактопласты обладают низкой вязкостью, что делает их идеальными для недорогой обработки, удобной пропитки армирующих волокон, поэтому они являются наиболее распространенными. Основной объем приходится на п.к.м., армированные стекловолокном (более 80% стеклопластика), далее следуют угле- и арамидное (арамид – ароматический полиамид) волокно. Стеклопластик является преобладающим среди полимерных композиционных материалов благодаря отличным механическим и диэлектрическим свойствам в сочетании с малой плотностью. Он широко применяется в строительстве, электроэнергетике и нефтедобывающей промышленности.
Неизбежной глобальной проблемой является растущий объем композитных отходов. В отличие от монолитного материала, гетерогенная природа композитных материалов делает переработку очень сложной задачей. В то время как термопластичные композиты могут быть легко расплавлены и переформованы, термореактивные композиты имеют сшитые трехмерные структуры и требуют специальных процессов восстановления материала. В исследовании [70] высоковольтная фрагментация была изучена как потенциальный процесс переработки композитов. Затем она сравнивалась с механической переработкой. Исследование охватывало эффективность разделения композитных фаз, потребность в энергии и качество вторичной переработки. При высоковольтной фрагментации получались более чистые и длинные волокна и меньшее содержание смолы, чем у механически переработанных композитов.
4.3. Извлечение стратегически важных металлов из отходов электроники
Масштаб проблемы утилизации отработанных электронных печатных плат (э.п.п.), очевидно, огромен. Э.п.п. присутствуют в большинстве электрических и электронных устройств, и когда приборы достигают своей фазы окончания срока службы, ценные и опасные материалы из них должны быть переработаны соответствующим образом. В Европе объемы переработки составляют миллионы тонн. В России, к сожалению, до сих пор значительная часть отходов электроники оказывается на свалке. Это не просто потеря ограниченных материальных ресурсов (ценных металлов), но и загрязнение природы сложным видом отходов, которые при взаимодействии с окружающей средой образуют токсины, попадающие в почву и грунтовые воды. Концентрация драгоценных металлов в печатных платах превышает их концентрацию в добываемой руде более, чем в 10 раз. Отходы э.п.п. имеют высокую потенциальную ценность, поскольку содержат до двадцати видов цветных и редких металлов. Однако отходы э.п.п. также содержат ряд токсичных тяжелых металлов, включая свинец, кадмий, ртуть и никель, а также бромированные антипирены, которые представляют потенциальную опасность для почвы, окружающей среды и биологических организмов. Повторное использование отходов э.п.п. имеет первостепенную важность для охраны окружающей среды и переработки ресурсов.
Многие технологии были разработаны и рассмотрены научным сообществом. Так, в работе [71] на 20 страницах представлен только обзор международных патентов, касающихся переработки э.п.п. (с 1990-х годов). Описаны и рассмотрены основные технологии механической обработки, извлечения и очистки металлов, эксплуатации неметаллических фракций. В обзоре [72] обсуждаются методы плазменной обработки различных металлосодержащих отходов, включая э.п.п. Применение электроразрядных технологий для утилизации отработанных э.п.п. с целью извлечения металлов начато сравнительно недавно и находится на уровне лабораторных исследований. В настоящее время разработаны физические основы ряда применений технологии электроимпульсного разрушения материалов. Однако технологические вопросы извлечения металлов из отработанных э.п.п. электроимпульсным способом пока не проработаны. Имеются отдельные статьи (по большей части ученых из Китая), посвященные этой теме [73, 74]. Проблеме внесения аппаратных загрязнений при электроимпульсном дроблении посвящены лишь единичные исследования, что связано с ее актуальностью лишь для сравнительно узкой области технологического применения.
В работе [73] исследовалось извлечение меди из чистых печатных плат (без монтажа) электроразрядным способом с помощью установки SELFRAG Lab. Морфология поверхности и химический состав взвешенных частиц были проанализированы с помощью сканирующей электронной микроскопии. Полученные результаты показывают, что механизм высвобождения и дробления э.п.п. в основном включает образование и расширение разрядных каналов, трансформацию ударной волны, эффектов отражения и преломления, а также физико-химических реакций в среде высокого давления; среди всех них физико-химические реакции между металлом и органикой являются специфическими явлениями, которые существуют только при использовании высоковольтных электрических для процесса дробления отходов э.п.п. Кроме того, полученные результаты также показывают, что высоковольтные электрические импульсы способствуют узкофракционной концентрации металла. В частности, производительность дробления достигает своего наилучшего уровня, когда число импульсов достигает 400, при этом в частицах размером около 2 мм было накоплено 97.92% меди. В работе [74] та же экспериментальная техника электродинамической фрагментации (э.д.ф.) была применена для более детального исследования обдирки металла от отходов э.п.п. Во фракции 3–6 мм при э.д.ф. было 84.84% от общего количества частиц, в то время как при механическом дроблении оно равнялось только 8.84%. Этот результат показал, что степень обдирки для э.д.ф.-метода была выше, чем для традиционного механического дробления для относительно крупного диапазона размеров. Эффект удаления меди увеличивается с ростом напряжения и числа импульсов. При напряжении 160 кВ и числе импульсов 300 скорость зачистки меди составляла 98.56% и 92.58% во фракциях размерами 25 и 13 мм соответственно.
В работе [75] авторы применили фрактальную теорию к исследованию дробления материалов. Существующие теории показывают, что распределение дефектов, таких как микротрещины, микропоры, и эволюция механических напряжений близки к автомодельным, а такое поведение вызывает фрактальные характеристики распределения осколков фрагментации после макроскопического разрушения материалов. В работе [76] исследовалось извлечение меди из плат с навесным монтажом (материнские платы) электроразрядным способом с помощью установки SELFRAG Lab. Показано, что использование э.д.ф. позволяет селективно фрагментировать материалы. Извлеченные материалы могут быть дополнительно переработаны. Целью исследования была оценка преимуществ технологии э.д.ф. для вторичной переработки печатных монтажных плат. Печатные монтажные платы были обработаны э.д.ф. с разными параметрами и молотковой мельницей для сравнительного эксперимента. Выходящие продукты характеризовались методами оптической микроскопии и растровой электронной микроскопии. Для изучения развития трещин и степени обнажения слоев меди были исследованы выборки из различных стадий э.д.ф. Различные уровни энергии, используемые при обработке э.д.ф., привели к различным степеням повреждений плат – от удаления компонентов до возмущения всей структуры и уменьшения размера частиц. Э.д.ф. привела к образованию меньшего количества мелкодисперсных частиц, однако оптимальным подходом с точки зрения энергоэффективной постобработки исследуемых плат было сочетание одноступенчатой э.д.ф. для удаления монтажных компонентов с последующим измельчением чистых плат.
4.4. Утилизация фотоэлектрических модулей
Мир все больше и больше охватывает лихорадка производства так называемой “зеленой энергии”. Государствами выделяются сотни миллиардов долларов на производство и разработку все более совершенных солнечных панелей (фотоэлектрические модули), но мало кто задумывается о том куда же девать отработавшие свой ресурс панели, хотя вопрос этот очень острый. Не стоит также забывать, что солнечные панели выходят из строя не только после длительного срока работы. Они могут быть разрушены и в результате воздействия стихийных бедствий: град, ураган, землетрясение, торнадо, тайфун и т.д. В США и Европе уже тесно столкнулись с проблемой утилизации солнечных панелей. Просто собрать их и вывезти на свалку невозможно, так как в панелях содержатся свинец и кадмий. Взять и просто переплавить стекло также нельзя, поскольку в результате плавления выделяются все те же вредные вещества.
Подробный анализ состояния фотоэлектрических технологий на 2020 г. дан в обзоре [77]. Отмечены следующие положения:
• за последнее десятилетие глобальная совокупная установленная фотоэлектрическая мощность выросла в геометрической прогрессии, достигнув в 2019 году 591 ГВт;
• быстрый прогресс был обусловлен в значительной степени улучшением эффективности солнечных батарей и модулей;
• снижение совокупных затрат на электроэнергию, которые в настоящее время, как правило, меньше, чем другие источники энергии;
• описаны критические области развития основных технологий преобразования фотоэлектрических элементов, достижения, необходимые для установки фотоэлектрических элементов в масштабе тераватт;
• обобщены ограничительные краткосрочные и долгосрочные технические проблемы и выделены прорывы, необходимые для их решения;
• определены области развития, которые окажут наибольшее влияние на фотоэлектрические технологии в ближайшие годы.
В работе [78] обсуждаются важнейшие направления развития энергетики нашей страны. Отмечается, что в 2011–2012 гг. наступил паритет стоимости энергии тепловых электростанций на органическом топливе с ветряными и солнечными станциями. С 2017 года мощности вводимых возобновляемых источников энергии в мире превысили объемы вводимых мощностей традиционной энергетики. Поэтапно происходит переход от традиционных энергетических технологий на возобновляемые источники энергии, которые становятся более выгодными с экономической точки зрения и позволяют минимизировать отрицательное воздействие энергетики на окружающую среду. Рассматривается перспективность применения комбинированных схем с использованием возобновляемых источников энергии для ее получения. К сожалению, в России пока проблемы экологии остаются на втором плане.
Современные методы разделения композитных материалов, таких как фотоэлектрические модули, включают механическое измельчение и последующее использование агрессивных химических веществ и/или термическую обработку. В последние годы наблюдается растущий интерес к изучению альтернативных методов сепарации, таких как фрагментация высоковольтными разрядами. Основным преимуществом электродинамического дробления по сравнению с механическим измельчением является его повышенная селективность в процессе разделения, что позволяет улучшить эффективность процесса в целом. Однако вопросы технологии разделения фотоэлектрических модулей электроимпульсным способом дробления пока не проработаны. Необходима разработка комплекса научно-технических решений для электроразрядной технологии разделения солнечных панелей до миллиметровой и субмиллиметровой фракций, допускающих их относительно простую сепарацию на металлы и неметаллы. Электроимпульсной переработке солнечных панелей (производство которых стремительно растет, и при сроке их службы 20 лет к 2025 году будет необходимо утилизировать десятки миллионов тонн в год) посвящены единичные работы (первая публикация относится к 2018 г.). Первостепенная важность этого вопроса очевидна как по экономическим, так и по экологическим причинам. Проблема утилизации с каждым годом становится все острее, и если не начать решать ее сейчас, то разгребать этот солнечный мусор будет уже другое поколение.
В работе [79] метод э.д.ф. в сочетании с просеиванием и гравитационным разделением был применен к фотоэлектрической панели для селективного разделения и извлечения материалов. Сначала панель была разделена на слои стекла и подложки путем высоковольтного импульсного дробления с помощью микровзрывов или ударных волн, передаваемых в Al-электроде и Si-подложке (стадия первичного дробления). Затем стекло и подложка могут быть отделены высоковольтным импульсным дроблением. Электрод подложки может также быть отделен дальнейшим высоковольтным импульсным дроблением. После просеивания продуктов, полученных на стадии вторичного дробления слоя стекла, стекло в основном распределялось в диапазоне размерных фракций 45–850 мкм с небольшим количеством порошка кремния (Si). Однако очистка стекла (удаление порошка Si) может быть достигнута путем разделения по плотности. Основные металлы, такие как Cu, Sn и Pb, могут быть извлечены в крупногабаритной фракции (1.0–8.0 мм). Серебро (Ag), используемое в электродах, конденсировалось во фракциях продукта с размерами менее 20 мкм, 2.0–4.0 и 4.0–8.0 мм с общими содержанием более 3000 мг/кг. Однако количество серебра в этих фракциях составляло лишь 33.2% от первоначального значения в панели. Таким образом, для увеличения коэффициента извлечения серебра потребуются другие методы разделения. Разделение по плотности среды может привести к конденсации Ag из Si из стекла, и это представляет собой перспективный вариант для улучшения извлечения Ag из измельченных продуктов.
В работе [80] было проведено систематическое сравнение между различными типами режимов разряда, такими как электрогидравлическая и электродинамическая фрагментация. Целью данной работы было представление такого сравнения на основе электрогидравлической (ImpulsTec EHF-100) и электродинамической (SelFrag Lab модификация S2.1, SF) фрагментации фотоэлектрических модулей (медь-индий-кремний) для потенциального извлечения индия. После дробления отдельные фракции взвешивались, измельчались и определялось содержание индия методом рентгеновской флуоресценции. Показано, что как электрогидравлический, так и электродинамический способ подходит для эффективного разделения тонкопленочного фотоэлектрического композиционного материала на составляющие его слои. Результат разделения не зависит от уровня напряжения, а определяется только общей приложенной энергией импульса. Как правило, генерация разрядов с более высоким напряжением требует более сложной установки, поэтому электрогидравлическая фрагментация (э.г.д.) предпочтительнее э.д.ф. при более высоких напряжениях.
В работе [81] было проведено сравнение э.г.д. с традиционным дроблением. Э.г.д. исследовалась как начальная стадия переработки фотоэлектрических модулей для облегчения извлечения ценных металлов с основной целью получения освобожденных фракций, пригодных для извлечения таких материалов, как Si, Ag, Cu, Sn, Pb и Al. В частности, демонтаж фотоэлектрических панелей с использованием ударно-волновой технологии обеспечивает большую селективность за счет концентрации целевых металлов на конкретных фракциях частиц по размерам. Такое обогащение металлов в пределах определенных фракций повышает перспективы извлечения металлов, поскольку материалы с более высокой концентрацией облегчают их последующую переработку и извлечение с помощью современных промышленных процессов. Кроме того, э.г.д.-процесс также приводит к получению высокочистых Si-содержащих фракций, которые также могут быть более легко переработаны, что делает весь подход более экономически привлекательным и еще больше расширяет возможности замкнутого цикла переработки солнечных панелей. В целом, использование э.г.д. для переработки фотоэлектрических модулей предлагает простое альтернативное решение для комбинированного быстрого демонтажа-фракционирования ценных металлических и металлоидных компонентов из отслуживших панелей.
В работе [82] обсуждались подходы с использованием э.д.ф. при различных условиях разряда. Результаты показали, что разряд через поверхность и внутреннюю поверхность фотоэлектрических панелей приводит к абляции круглых отверстий, распылению металлических частиц и появлению дендритных каналов. Средний размер частиц уменьшался с увеличением числа импульсов и амплитуды напряжения. Учитывая энергозатраты, оптимальными условиями э.д.ф. в данной работе было 160 кВ для 300 импульсов с расходом энергии 192.99 Дж/г, дробление фотоэлектрических панелей на частицы величиной в среднем 4.1 мм (13.7% от исходного размера). По мере увеличения энергии между фракциями размером 0.1–2 мм распределялось все больше частиц. Селективные фрагментированные продукты, такие как Cu, Al, Pb, Ag и Sn, концентрируются на исследуемых фракциях размером до 1 мм. Наконец, обсуждалась гибридная модель энергопотребления дробления в сочетании с фрактальной теорией, из которой получена связь между энергией и средним размером частиц.
Работа [83] близка по подходам к работе [80]. В ней показано, что по мере увеличения напряженности поля и количества импульсов растет степень дробления продукта, которая сильно варьируется при различных размерах частиц. Когда высоковольтное дробление используется для разрушения фотоэлектрических панелей, трещины преимущественно образуются на границах раздела между материалами с большими различиями в диэлектрической проницаемости. Это приводит к разделению материалов в порядке Ag > Si > стекло. Скорость обогащения Ag была выше при условии меньшей напряженности поля и числа импульсов. Тем не менее, уменьшение напряжения и числа импульсов оказывает большее влияние на скорость восстановления. Поэтому для обеспечения восстановительного эффекта Ag зазор между электродами может быть соответствующим образом увеличен. Сортировочный тест был проведен на продукте с размером частиц менее 0.5 мм, и было получено чистое стекло (степень 98.99%). Измельченный продукт с размером частиц 0.5 мм был обработан сортировщиком Falcon, 93.78% серебра и 94.22% меди были успешно извлечены.
В заключение можно отметить статью [84], в которой наряду с экономическими и экологическими преимуществами солнечной энергетики рассматривается прибыльность бизнес-процессов по переработке фотоэлектрических модулей. Это позволяет, с одной стороны, сократить выбросы CО2 в атмосферу, но инвестиции представляют собой серьезные экономические потери. Экономически выгодной переработка становится при достижении некоторого критического объема. В Германии, несмотря на то, что там вклад солнечной энергетики был выше, чем в Италии, эксперты изучают альтернативные подходы с поставкой отработанных фотоэлектрических модулей из других стран. Интересным способом решения этого компромисса является создание многофункциональных центров переработки отходов, способных обрабатывать широкий спектр отходов (включая фотоэлектрические модули).
5. ЗАКЛЮЧЕНИЕ
Во введении была обоснована актуальность тематики и приведен анализ современного состояния исследований в данной области (с подробным обзором исследований по этой тематике и ссылками на публикации в научной литературе). В следующем разделе дано описание физических принципов и технических аспектов электроимпульсных технологий. В частности, приведены феноменология пробоя твердых диэлектриков и особенности импульсного пробоя жидких и твердых диэлектриков. Акцентированы наиболее важные аспекты для разработки установок для электроразрядных технологий. Также указаны основные преимущества электроимпульсного метода разрушения твердых тел по сравнению с традиционными механическими способами, а именно, относительно низкие удельные энергетические затраты, высокая степень избирательности разрушения, слабая корреляция разрушения с механическими характеристиками сырья, широкие возможности по регулированию и автоматизации процесса.
Далее, в разделе 3 приведены результаты разработки и экспериментальных исследований генераторов электроимпульсного дробления, разработанных в ИСЭ СО РАН. Особо можно выделить генератор с коммутацией низковольтного (600 мкФ) и высоковольтного (21 нФ) накопителей для работы в режимах 0.25, 0.5 и 1 кДж. Амплитуда напряжения составляет около 290 кВ при зарядном напряжении 1.8 кВ, при этом длительность импульса больше примерно на 25 мкс при 1000 Дж запасаемой энергии. Амплитуда тока в режиме дробления почти в четыре раза больше, чем в режиме активной нагрузки. Работа проводится в импульсно-пакетном режиме с полной автоматизацией управления. Здесь же применен оригинальный импульсный трансформатор на напряжение до 300 кВ с секционированными высоковольтными обмотками с межвитковой изоляцией конденсаторного типа. За счет секционирования обмоток в совокупности с большой межвитковой емкостью в секции достигается выравнивание напряженности электрического поля вдоль секций и снижаются перенапряжения, возникающие при переходных процессах.
Также можно отметить генератор на 8 кДж. Этот генератор импульсного напряжения собран по схеме Маркса. В генераторе 8 ступеней С1–С8. В каждой ступени генератора используется два параллельно соединенных конденсатора типа ИК-100-0.4. Хотя этот генератор выполнен по схеме Маркса, нестандартная конструкция коммутационного блока обеспечивает синхронное срабатывание. В генераторе используются двухэлектродные искровые разрядники, заполненные воздухом. Электрическая прочность промежутков разрядников регулируется изменением давления воздуха в них. Все восемь разрядников монтируются в одном корпусе из стеклоэпоксидной трубы диаметром 130 мм, образуя блок разрядников с взаимной подсветкой. Это один из самых мощных генераторов в мире, работающих в непрерывном режиме на частоте 0.5 Гц.
Также оригинальным подходом является использование ступени линейного трансформатора как генератора дробления. Схема со ступенями наиболее перспективна для материалов с пониженной электрической прочностью, например, для отходов электроники. Длительность импульса может варьироваться изменением индукторов, конденсаторов и числа ступеней. Основным преимуществом является то, что для одинакового энергозапаса схема со ступенью значительно проще, дешевле (примерно в три раза) и компактнее, чем описанные выше установки. Но для нее есть свои особенности в применениях, отмеченные здесь.
В последней главе обзора дано описание некоторых технологических применений и проведено сравнение эффективности различных режимов разрушения в зависимости от параметров разряда и разрушаемого материала. Рассмотрено получение кварцевых концентратов высокой чистоты. Наличие селективного метода устранения загрязняющих минералов в кварце имеет решающее значение для достижения высокой чистоты кремниевого сырья для производства солнечных элементов из кремния. В ряде исследований установлены преимущества э.и.-фрагментации: образуется больше расколов, которые избирательно направляются в сторону минеральных включений; э.и.-фрагментация увеличивает удаление посторонних микроэлементов и уменьшает появление внедренных частиц; э.и.-фрагментация требует меньше энергии для обработки.
Было рассмотрено дробление твердых пород и композитов. Процесс э.и.-разрушения горных пород зависит от свойств, строения и состава горной породы, характеристик жидкой среды, параметров импульса напряжения, механизма развития канала разряда в жидкой и твердой фазах и ряда других параметров. Было установлено, что э.и.-фрагментация перспективна для обогащения руд и угля. Гетерогенная природа композитных материалов делает переработку более сложной задачей. Тем не менее, э.и.-фрагментация исследовалась как потенциальный процесс переработки композитов. Затем она сравнивалась с механической переработкой. Исследование охватывало эффективность разделения композитных фаз, потребность в энергии и качество вторичной переработки. При высоковольтной фрагментации получались более чистые и длинные волокна и меньшее содержание смолы, чем у механически переработанных композитов.
Затем была рассмотрена утилизация отработанных э.п.п. При отправлении отходов электроники на свалку происходят как потеря ценных металлов, так и загрязнение природы сложным видом токсинов. Отходы э.п.п. имеют высокую потенциальную ценность, поскольку содержат до двадцати видов цветных и редких металлов. Однако отходы э.п.п. также содержат несколько токсичных тяжелых металлов, включая свинец, кадмий, ртуть и никель, а также бромированные антипирены, которые представляют потенциальную опасность для почвы, окружающей среды и биологических организмов. Повторное использование отходов э.п.п. имеет первостепенную важность для охраны окружающей среды и переработки ресурсов. Полученные результаты показывают, что механизм высвобождения и дробления э.п.п. в основном включает образование и расширение разрядных каналов, трансформацию ударной волны, эффектов отражения и преломления, а также физико-химических реакций в среде высокого давления. При этом физико-химические реакции между металлом и органикой являются специфическими явлениями, которые существуют только при использовании высоковольтных электрических импульсов для процесса дробления отходов э.п.п.
Утилизация фотоэлектрических модулей – это в принципе утилизация отходов электроники, но она заслуживала отдельного рассмотрения из-за масштаба проблемы, так как необходимо утилизировать миллионы и десятки миллионов тонн в год. Применению э.и.-фрагментации для утилизации фотоэлектрических модулей посвящены единичные работы. Тем не менее, уже установлено, что демонтаж фотоэлектрических панелей с использованием ударно-волновой технологии обеспечивает большую селективность за счет концентрации целевых металлов на конкретных фракциях частиц по размерам и способствует получению высокочистых Si-содержащих фракций. Селективные фрагментированные продукты, такие как Cu, Al, Pb, Ag и Sn, концентрируются на исследуемых фракциях размером до 1 мм. Показано, что по мере увеличения напряженности поля и количества импульсов увеличивается степень дробления продукта, которая сильно варьируется при различных размерах частиц. Когда высоковольтное дробление используется для разрушения фотоэлектрических модулей, трещины преимущественно образуются на границах раздела между материалами с большими различиями в диэлектрической проницаемости. Это приводит к разделению материалов в порядке Ag > Si > стекло.
Список литературы
Kovalchuk B.M., Kharlov A.V., Vizir V.A., Kumpyak V.V., Zorin V.B., Kiselev V.N. // Rev. Sci. Instrum. 2010. V. 81. P. 103506. https://doi.org/10.1063/1.3497307
Lisitsyn I.V., Inoue H., Nishizawa I., KAtsuki S., Akiyama H. // J. Appl. Phys. 1998. V. 84, p. 6262. https://doi.org/10.1063/1.368946
Timoshkin V.I., Mackersie J.W., MacGregor S.J. // IEEE Trans. Plasma Sci. 2004. V. 32. P. 2055. https://doi.org/10.1109/TPS.2004.835489
Важов В.Ф., Гафаров Р.Р., Дацкевич С.Ю., Журков М.Ю., Муратов В.М. // ЖТФ. 2010. Т. 80. Вып. 6. С. 79.
Курец В.И., Усов А.Ф., Цукерман В.А. // Электроимпульсная дезинтеграция материалов. Апатиты: Кольский научный центр, 2002.
Семкин Б.В., Усов А.Ф., Курец В.И. // Основы электроимпульсного разрушения материалов. Апатиты: КНЦ РАН. 1995.
Andres U., Timoshkin I., Jirestig J., Stallknecht H. // Powder Technology. 2001. V. 114. P. 40. https://doi.org/10.1016/S0032-5910(00)00260-6
Fazhi Yan, Baiquan Lin, Chuanjie Zhu, Chang Guo, Yan Zhou, Quanle Zou, Ting Liu // Powder Technology. 2016. V. 298. P. 50. https://doi.org/10.1016/j.powtec.2016.05.023
Martello E.D., Bernardis S., Larsen R.B., Tranell G., Sabatino M.D., Arnberg L. // Powder Technology. 2012. V. 224. P. 209. https://doi.org/10.1016/j.powtec.2012.02.055
Bluhm H., Frey W., Giese H., Hoppe P., Schultheis C., Strabner R. // IEEE Trans. on Dielectrics and Electr. Insul. 2000. V. 7. P. 625. https://doi.org/10.1109/94.879358
Doiphodea P., Chaturvedi S. // J. Appl. Phys. 2001. V. 89. P. 6024. https://doi.org/10.1063/1.1366659
Burkin V.V, Kuznetsova N.S., Lopatin V.V. // J. Phys. D: Appl. Phys. 2009. V. 42. P. 185204. https://doi.org/10.1088/0022-3727/42/18/185204
Burkin V.V, Kuznetsova N.S., Lopatin V.V. // J. Phys. D: Appl. Phys. 2009. V. 42. P. 235209. https://doi.org/10.1088/0022-3727/42/23/235209
Inoue H., Listitsyn I., Akiyama H., Nishizawa I. // IEEE Electr. Insul. Mag. 2000. V. 16. P. 19. https://doi.org/10.1109/57.845023
Yi Liu, Zhi-Yuan Li, Xian-Dong Li, Si-Wei Liu, Gu-Yue Zhou, Fu-Chang Lin // Phys. Plasmas. 2017. V. 24. P. 043510. https://doi.org/10.1063/1.4980848
Ben Liua, DeguoWanga, Yanbao Gu // Phys. Lett. A. 2018. V. 382. P. 49. https://doi.org/10.1016/j.physleta.2017.10.039
Andres U. // Mineral Processing and Extractive Metallurgy review. 1995. V. 14. P. 87. https://doi.org/10.1080/08827509508914118
Eric Wang, Fengnian Shi, Eммy Manlapig // Minerals Engineering. 2011. V. 24. P. 455. https://doi.org/10.1016/j.mineng.2011.12.005
Eric Wang, Fengnian Shi, Eммy Manlapig // Minerals Engineering. 2012. V. 27. P. 28. https://doi.org/10.1016/j.mineng.2010.12.011
Martin J.C. on Pulsed Power / Eds. T.H. Martin, A.H. Guenther, M. Kristiansen. NY: Plenum, 1996. P. 185. https://doi.org/10.1007/978-1-4899-1561-0
Adler R.J. Pulse Power Formulary. Albuquerque (NM): North Star Research Corporation, 2002. P. 26
Ушаков В.Я., Климкин В.Ф., Коробейников С.М., Лопатин В.В. Пробой жидкостей при импульсном напряжении. Томск: Изд-во НТЛ, 2005.
Gosse J.P. // IEEE Trans. Electrical Insulation. 1986. V. 21. P. 503.
Lewis T.J. // IEEE Trans. Dielectrics and Electrical Insulation. 1998. P. 306.
Kolb J.F., Joshi R.P., Xiao S., Schoenbach K.H. // J. Phys. D: Appl. Phys. 2008. V. 41. P. 234007. https://doi.org/10.1088/0022-3727/41/23/234007
Bluhm H. Pulsed Power Systems: Principles and Applications. Springer-Verlag Berlin, 2006. P. 288–305.
SELFFRAG Lab. http://www.selfrag.com/pdf/products_specificatioнc/tech-specification.pdf
Fengnian Shi, Eммy Manlapig,Weiran Zuo // Chem. Eng. Technol. 2014. V. 37. № 5. P. 765. https://doi.org/10.1002/ceat.201300660
https://www.impulstec.com/en/products
Kovalchuk B.M., Kharlov A.V., Kumpyak E.V., Sinebryukhov V.A. // J. Instrumentation. 2013. V. 8. P. P09012. https://doi.org/10.1088/1748-0221/8/09/P09012
Усов А.Ф., Семкин Б.В., Зиновьев Н.Т. Переходные процессы в установках электроимпульсной технологии. СПб.: Наука, 2000.
Богатенков И.М., Иманов Г.М., Кизеветтер В.Е., Костенко М.В., Кучинский Г.С., Михайлов Ю.А., Таджибаев А.И., Тиходеев Н.Н., Халилов Ф.Х., Шкуропат П.И., Шнеерсон Г.И., Янчус Г.И. // Техника высоких напряжений. СПб.: Изд-во Петербургского энергетического института повышения квалификации, 1998.
Воробьев А.А., Воробьев Г.А., Завадовская Е.К., Каляцкий И.И., Кривко В.В., Панин В.Ф., Семкин Б.В., Торбин Н.Н., Ушаков В.Я., Чепиков А.Т. // Импульсный пробой и разрушение диэлектриков и горных пород. Томск: Изд-во ТГУ, 1971.
Бортник И.М., Верещагин И.П., Вершинин Ю.Н., Кучинский Г.С., Ларионов В.П., Пинталь Ю.С., Сергеев Ю.Г., Соколова М.В. // Электрофизические основы техники высоких напряжений: учебник для вузов. М.: Энергоатомиздат, 1993.
Базуткин В.В., Ларионов В.П., Пинталь Ю.С. Техника высоких напряжений. М.: Энергоатомиздат, 1986.
Усов А.Ф. // Изв. РАН. Энергетика. 2001. № 1. С. 54.
Робежко А.Л., Важов В.Ф., Ефремова Г.В., Лебедев С.М., Ушаков В.Я. // Физика твердого тела. 1981. Т. 23. Вып. 11. С. 3360.
Kovalchuk B.M., Kharlov A.V., Zherlitsyn A.A., Kumpyak E.V. // Nucl. Instrum. and Methods in Phys. Res. A. 2019. V. 923. P. 97.
Kharlov A.V. // Rev. Sci. Instrum. 2020. V. 91. P. 111502. https://doi.org/10.1063/5.0012336
Харлов А.В. // ПТЭ. 2021. № 1. С. 5. https://doi.org/10.31857/S0032816220060099
Кучинский Г.С. // Электричество. 1981. № 10. С. 41.
Баятаков В.А., Ильюшенков Ю.Д., Тонконогов М.П., Шилин П.Е. // ЖТФ. 1976. Т. 46. Вып. 5. С. 987.
Буркин В.В., Макаров П.В., Семкин Б.В., Шубин Б.Г. // ЖТФ. 1975. Т. 45. Вып. 11. С. 2395.
Зельдович Я.Б., Райзер Ю.П. // Физика ударных волн и высокотемпературных гидродинамических явлений. М.: Наука, 1966.
Семкин Б.В., Шубин Б.Г. // ПМТФ. 1977. № 4. С. 38.
Зиновьев Н.Т., Семкин Б.В. // ЖТФ. 1978. Т. 48. Вып. 3. С. 624.
Ермаков В.В., Калиткин Н.Н. // Таблицы проводимости и теплопроводности плотной плазмы 11 веществ. М.: Изд-во ИПМ АН СССР, 1978.
Andres U. // International J. Mineral Processing. 2010. V. 97. P. 31. https://doi.org/10.1016/j.minpro.2010.07.004
Harrower J.A. †, MacGregor S.J., Tuema F.A. // J. Phys. D: Appl. Phys. 1999. V. 32. P. 790. https://doi.org/10.1088/0022-3727/32/7/007
Beveridge J.R., MacGregor S.J., Given M.J., Timoshkin I.V., Lehr J.M. // IEEE Trans. Dielectrics and Electrical Insulation. 2009. V. 16. P. 948. https://doi.org/10.1109/TDEI.2009.5211838
Ковальчук Б.М., Королев Ю.Д., Кумпяк Е.В. // ЖТФ. 2012. Т. 82. Вып. 8. С. 124.
Ковальчук Б.М., Королев Ю.Д., Кумпяк Е.В., Франц О.Б., Шемякин И.А. // ЖТФ. 2014. Т. 84. Вып. 12. С. 137.
Kharlov A.V., Kovalchuk B.M., Kumpyak E.V., Smorudov G.V., Tsoy N.V. // Laser and Particle Beams. 2014. V. 32. P. 471. https://doi.org/10.1017/S0263034614000408
Харлов А.В. // ПТЭ. 2017. № 6. С. 51. https://doi.org/10.7868/S0032816217060040
Kovalchuk B.M., Kharlov A.V., Zherlytsyn A.A., Kumpyak E.V., Tsoy N.V. // Rev. Sci. Instrum. 2016. V. 87. P. 063505. https://doi.org/10.1063/1.4954504
Kharlov A.V., Kovalchuk B.M., Zorin V.B. // Rev. Sci. Instrum. 2006. V. 77. P. 123501. https://doi.org/10.1063/1.2400667
Kovalchuk B.M., Kharlov A.V., Kiselev V.N., Kumpyak E.V., Zorin V.B., Chupin V.V., Morozov A.V. // Rev. Sci. Instrum. 2007. V. 78. P. 033501. https://doi.org/10.1063/1.2400667
Kovalchuk B.M., Kharlov A.V., Kumpyak E.V., Tsoy N.V. // Rev. Sci. Instrum. 2015. V. 86. P. 123504. https://doi.org/10.1063/1.4937359
Kharlov A.V., Kovalchuk B.M., Kumpyak E.V., Tsoy N.V. // J. Instrumentation. 2017. V. 12. P. T10009. https://doi.org/10.1088/1748-0221/12/10/T10009
Kovalchuk B.M., Kharlov A.V., Kumpyak E.V., Smorudov G.V., Zherlitsyn A.A. // Rev. Sci. Instrum. 2014. V. 85. P. 013501. https://doi.org/10.1063/1.4857475
Kovalchuk B.M., Kharlov A.V., Zorin V.B., Zherlitsyn A.A. // Rev. Sci. Instrum. 2009. V. 80. P. 083504. https://doi.org/10.1063/1.3193714
Kovalchuk B.M., Kharlov A.V., Kumpyak E.V., Smorudov G.V., Zherlitsyn A.A., Tsoy N.V., Vizir V.A. // Laser and Particle Beams. 2009. V. 27. P. 371. https://doi.org/10.1017/S0263034609000482
Kovalchuk B.M., Kharlov A.V., Kumpyak E.V., Zher-litsyn A.A. // Phys. Rev. STAccel. Beams. 2013. V. 16. P. 050401. https://doi.org/10.1103/PhysRevSTAB.16.050401
Kovalchuk B.M., Kharlov A.V., Volkov S.N., Zher-litsyn A.A., Zorin V.B., Smorudov G.V., Kiselev V.N. // Laser and Particle Beams. 2012. V. 30. P. 23. https://doi.org/10.1017/S0263034611000632
Белоусова Е.Б., Петров И.М. // Минеральные ресурсы России. Экономика и управление. 2010. № 1. С. 62.
Mueller G., An W., Berghofer Th., DelGiacco M., Eing Ch., Fetzer R., Flickinger B., Frey W., Giese H., Gottel M., Gusbeth Ch., Heinzel A., Hoppe P., Jianu A., Lang F. et al. // J. Korean Physical Society. 2011. V. 59. P. 3588. https://doi.org/10.3938/jkps.59.3588
Крастелев Е.Г., Калашников Ю.Д. // ПТЭ. 2016. № 2. С. 76. https://doi.org/10.7868/S0032816216010250
Крастелев Е.Г., Седин А.А., Тугушев В.И. // Ядерная физика и инжиниринг. 2014. Т. 5. № 11–12. С. 956. https://doi.org/10.1134/S2079562914090115
Ito M., Owada S., Nishimura T., Ota T. // Int. J. Miner. Process. 2009. V. 92. P. 7. https://doi.org/10.1016/j.minpro.2009.02.007
Mativenga P.T., Shuaib N.A., Howarth J., Pestalozzi F., Woidasky J. // CIRP Annals – Manufacturing Technology. 2016. V. 65. P. 45. https://doi.org/10.1016/j.cirp.2016.04.107
Rocchetti L., Amato A., Beolchini F. // J. Cleaner Production. 2018. V. 178. P. 814. https://doi.org/10.1016/j.jclepro.2018.01.076
Changming D., Chao S., Gong X., Ting W., Xiange W. // Waste Management. 2018. V. 77. P. 373. https://doi.org/10.1016/j.wasman.2018.04.026
Duan C.L., Diao Z.J., Zhao Y.M., Huang W. // Minerals Engineering. 2015. V. 70. P. 170. https://doi.org/10.1016/j.mineng.2014.09.018
Chenlong Duan, Jun Han, Shen Zhao, Zhonglin Gao, Jinpeng Qiao, Guanghui Yan // Waste Management. 2018. V. 77. P. 603. https://doi.org/10.1016/j.wasman.2018.06.003
Yuemin Zhao, Bo Zhang, Chenlong Duan, Xia Chen, Song Sun // Powder Technology. 2015. V. 269. P. 219. https://doi.org/10.1016/j.powtec.2014.09.006
Rémi Martino, Cédric Iseli, Stoyan Gaydardzhiev, Martin Streicher-Porte, Alexander Weh // Minerals Engineering. 2017. V. 107. P. 20. https://doi.org/10.1016/j.mineng.2018.05.015
Wilson G.M. J. // Phys. D: Appl. Phys. 2020. V. 53. P. 493001. https://doi.org/10.1088/1361-6463/ab9c6a
Зайченко В.М., Соловьев Д.А., Чернявский А.А. // Окружающая среда и энерговедение (ОСЭ). 2020. № 1. С. 33.https://doi.org/10.5281/zenodo.3738026
Akimoto Y., IizuкA A., Shibata E. // Minerals Engineering. 2018. V. 125. P. 1. https://doi.org/10.1016/j.mineng.2018.05.015
Pestalozzi F., Eisert S., Woidasky J. // Recycling. 2018. V. 3. P. 13. https://doi.org/10.3390/recycling3020013
Nevala S.M., Hamuyuni J., Junnila T., Sirvio T., Eisert S., Wilson B.P., Serna-Guerrero R., Lundström M. // Waste Management. 2019. V. 87. P. 43. https://doi.org/10.1016/j.wasman.2019.01.039
Bai-Peng Song, Meng-Yao Zhang, Yue Fan, Ling Jiang, Jun Kang, Ting-Tao Gou, Cheng-Lei Zhang, Ning Yang, Guan-Jun Zhang, Xiang Zhou // Waste Management. 2020. V. 101. P. 180. https://doi.org/10.1016/j.wasman.2019.10.015
Pengfei Zhao, Junwei Guo, Guanghui Yan, Guangqing Zhu, Xiangnan Zhu, Zhenxing Zhang, Bo Zhang // J. Cleaner Production. 2020. V. 257. P. 120442. https://doi.org/10.1016/j.jclepro.2020.120442
Cucchiell F., D’Adamo I., Rosa P. // Renewable and Sustainable Energy Reviews. 2015. V. 47. P. 552. https://doi.org/10.1016/j.rser.2015.03.076
Дополнительные материалы отсутствуют.
Инструменты
Приборы и техника эксперимента