Радиотехника и электроника, 2019, T. 64, № 2, стр. 206-210
Металлографический анализ при обеспечении качества производства многослойных печатных плат с межслойными соединениями в составе радиоэлектронных систем
Д. С. Воруничев 1, *, Э. А. Засовин 1
1 МИРЭА – Российский технологический университет
119454 Москва, просп. Вернадского, 78, Российская Федерация
* E-mail: vorunichev@mirea.ru
Поступила в редакцию 12.04.2018
После доработки 01.06.2018
Принята к публикации 11.06.2018
Аннотация
Рассмотрено современное состояние высокотехнологичной радиоэлектронной отрасли на примере продукции специального и двойного назначения. Показаны основные причины отказов космической радиоэлектроники. Дана оценка техническим требованиям современного производства печатных плат как одного из основных способов решения по отказам. Предложен комбинированный метод исследования дефектов и обеспечения качества производства многослойных печатных плат с межслойными соединениями в составе сложных радиоэлектронных систем.
ВВЕДЕНИЕ
Радиоэлектронная отрасль одна из самых высокотехнологичных отраслей России, которая представлена в основном продукцией специального и двойного назначения. К примеру, радиотехнические средства космической аппаратуры, традиционно относятся к высоконаукоемким, доля затрат на отраслевую науку в отгруженной продукции которой составляет свыше 10%. Радиоэлектроника в составе наземно-космических радиотехнических систем является ключевым звеном с которой связано множество проблем обеспечения безопасности ракетно-космической техники, риски катастроф, аварий, отказов ракетоносителей и космических летательных аппаратов [1].
Высокая степень наукоемкости, конструктивная и технологическая сложность радиоэлектронных средств космической аппаратуры обусловливают риски и угрозы безопасности ракетно-космической техники на всех этапах жизненного цикла [2].
1. АНАЛИЗ ПРИЧИН ОТКАЗОВ И ОЦЕНКА ТЕХНИЧЕСКИХ ТРЕБОВАНИЙ К СОВРЕМЕННОМУ ПРОИЗВОДСТВУ ПЕЧАТНЫХ ПЛАТ
Анализ статистики причин и последствий отказов космических аппаратов показывает, что основная их доля приходится на радиоаппаратуру (табл. 1), в которой чаще всего происходят отказы элементной базы и печатных плат (табл. 2).
Таблица 1.
Виды отказов космических аппаратов за 2007–2017 гг.
Место отказа | Фатальный отказ | Частичный отказ | Парированный отказ/сбой | Всего |
---|---|---|---|---|
Радиоаппаратура | 20 | 11 | 0 | 31 |
Программные средства | 3 | 2 | 16 | 21 |
Система электроснабжения | 15 | 3 | 2 | 20 |
Механическая неисправность | 5 | 8 | 2 | 15 |
Аппаратные средства | 3 | 0 | 3 | 6 |
Гироскопические устройства | – | 2 | 3 | 5 |
Двигательная установка | 2 | 2 | 0 | 4 |
Ошибка обслуживающего персонала | 1 | 0 | 0 | 1 |
ВСЕГО | 49 | 28 | 26 | 103 |
Таблица 2.
Классификация рисков и проблем безопасности для космической радиоэлектронной аппаратуры по уровням конструкторской иерархии
Конструкторская иерархия | Описание | Причины отказов |
---|---|---|
Наземно-космическая радиотехническая система | Комплекс управления космическими аппаратами включает в себя бортовой комплекс управления (бортовой сегмент) и наземный комплекс управления (наземный сегмент) | – отказы космических аппаратов – отказы радиоаппаратуры – отказы систем управления – отказы аппаратных средств бортовых компьютеров – отказы программных средств бортовых компьютеров |
Электронный модуль третьего уровня | Шкаф с установленными в него блоками электронной и радиоэлектронной аппаратурой | – отказы системы электропитания и кабельных систем – отказы радиоаппаратуры |
Электронный модуль второго уровня | Блок, основными конструктивными элементами которого является панель с печатными узлами, размещенными в один или несколько рядов | – отказы печатных плат – отказы элементной базы |
Электронный модуль первого уровня | Печатная плата, на которой установлена элементная база и соединители | – отказы элементной базы – отказы соединителей и разъемов – отказы печатной платы и проводящего рисунка – отказы разъемных и неразъемных соединений |
Электронный модуль нулевого уровня | Электрорадиоэлементы, в том числе интегральные микросхемы и микросборки | – отказы элементной базы |
Поскольку основные риски и причины отказов закладываются на этапе производства, одной из важнейших задач обеспечения качества является анализ и испытание для подтверждения соответствия перспективным требованиям многослойных печатных плат (МПП) с межслойными соединениями, которые составляют основу современной радиоаппаратуры космического назначения.
Мировой опыт показывает, что высокотехнологичная продукция редко имеет возможность обеспечения каждого этапа производственного процесса. Компании специализируются на одном бизнес-процессе. В настоящее время выделяют две бизнес-модели производства электроники.
1. Собственное производство – производственный цикл от маркетинга до поставки продукции происходит в рамках одного предприятия. Осуществляется выпуск собственной продукции.
2. Контрактное производство – независимая организация, которая на собственных мощностях производит продукцию по заказу (контракту). Изделие изготавливается и соответствует конструкторской документации заказчика. Как правило, собственная продукция не производится.
Технический уровень современного производства печатных плат должен обеспечивать их изготовление со стабильными характеристиками в соответствии с конструкторской документацией. Технический уровень конкретного производства определяется значением коэффициента технического уровня предприятия, расчет которого ведется по методики национального стандарта ГОСТ Р 53432-2009 [3], требования которого распространены на организации и предприятия, изготавливающие печатные платы для использования в радиоэлектронной аппаратуре. Оценка коэффициента технического уровня производителя печатных плат производится по пяти показателям.
1. Технологическая | Технологические возможности. Класс точности изготавливаемых печатных плат |
2. Производственная | Производственные мощности по выпуску МПП |
3. Техническое состояние оборудования | Срок службы. Степень износа |
4. Маска под пайку | Применение защитной маски. Отсутствие защитной маски |
5. Технический уровень кадров | Процент сотрудников, прошедших переподготовку за год |
Коэффициент технического уровня (КТУ) производителя печатных плат определяют как сумму баллов (по ГОСТ Р 53432-2009) по формуле
(1)
${\text{К Т У }} = {{{\text{Б }}}_{1}} + {{{\text{Б }}}_{2}} + {{{\text{Б }}}_{3}} + {{{\text{Б }}}_{4}} + {{{\text{Б }}}_{5}},$Для оценок повторяемости, воспроизводимости и правильности технологического процесса изготовления многослойных печатных плат (МПП) применяется следующее уравнение статистической модели:
где y – результат измерений, относительно которого предполагается, что он может быть вычислен
по соответствующей функции; μ – (неизвестное) математическое ожидание идеальных результатов;
δ – смещение, присущее методу измерений; B – лабораторная составляющая смещения; – отклонение от номинального значения xi; ci – коэффициент чувствительности, равный ${{\partial y} \mathord{\left/ {\vphantom {{\partial y} {\partial {{x}_{i}}}}} \right. \kern-0em} {\partial {{x}_{i}}}};$ e – случайная погрешность в условиях повторяемости.
Предполагается, что B и e подчиняются нормальному распределению.
2. МЕТАЛЛОГРАФИЧЕСКОЕ ИССЛЕДОВАНИЕ МПП С МЕЖСЛОЙНЫМИ СОЕДИНЕНИЯМИ
В радиоэлектронных системах, в том числе специального и двойного назначения, чаще всего происходят отказы следующих элементов:
1) элементная база (в том числе не предназначенная для эксплуатации в заданных условиях или выполненная по бессвинцовой технологии [4]);
2) печатная плата и проводящий рисунок.
Продолжающееся усложнение современной радиоэлектронной аппаратуры и ее элементов, одновременно с тенденцией по микроминиатюризации вынуждает разработчиков все чаще переходить на сложные многослойные и повышенной плотности печатные платы. Усложняются и методы контроля печатных плат. Особенно в части наиболее достоверного контроля металлизации МПП с межслойными соединениями. Самый доступный на сегодняшний день метод исследования и контроля металлизации – металлографический анализ металлизации при помощи микрошлифов. Металлографические исследования по соответствующим методикам позволяют с максимально достоверной точностью выявлять различные дефекты: нарушение формы геометрии элементов проводящего рисунка, подтравы металлизации, сколы, разрывы металлизации, полости и другие дефекты.
Поскольку спектр возможных дефектов широк, то возникают различные задачи [5, 6]: 1) наблюдение малоконтрастных элементов, чаще носящих скрытый характер (закись меди, наличие включений, царапин, разрывов); 2) наблюдение высококонтрастных элементов, поглощающих свет (дефекты металлизации, сколы, разрывы, полости).
Для металлографического исследования различных по характеру дефектов, предлагается использовать комбинацию из двух методов: исследование в светлом и темном поле [6]. Примеры исследования микрошлифов МПП с различными дефектами приведены на рис. 1–3. Исследование проводилось с помощью металлографического микровизора μVizo-МЕТ-221 с линейным увеличением от 10 до 4000 крат, методами “работа в темном поле” и “работа в светлом поле”. Для диагностики межслойных соединений плат применялось увеличение от 50…200 крат, которое позволяло при необходимости достигать точности измерения толщины металлизации покрытий ±0.7 мкм (при тщательном соблюдении всех требований к изготовлению микрошлифов). Исследовано 20 различных типов конструкций МПП с различным количеством слоев.
Рис. 1.
Разрыв сквозного металлизированного отверстия: a – метод “работа в темном поле”; б – метод “работа в светлом поле”.
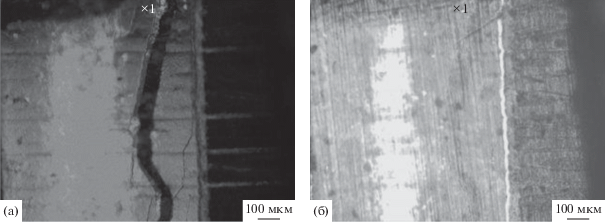
ЗАКЛЮЧЕНИЕ
Таким образом, представлена статистика по отказам сложных радиоэлектронных систем по уровням конструкторской иерархии. Наибольшее число отказов приходится на элементную базу и проводящий рисунок печатных плат. Учитывая широкий спектр возможных производственных дефектов проводящего рисунка плат, предложен комбинированный металлографический метод исследования, заключающийся в проведении оптического контроля слоев плат двумя методами работы: в светлом и темном поле. Сочетание двух методов исследования позволило с высокой достоверностью наблюдать как малоконтрастные, так и высококонтрастные элементы, поглощающие свет по микрошлифам.
Список литературы
Воруничев Д.С. // Матер. Междунар. науч.-техн. конф. “INTERMATIC-2016”. М.: МИРЭА, 2016. С. 221.
Воруничев Д.С. // Стандарты и качество. 2016. № 1. С. 53.
ГОСТ Р 53432-2009. Платы печатные. Общие технические требования к производству. М.: Стандартинформ, 2009.
Воруничев Д.С., Покровская М.В. // Вестник РГРТУ. 2014. № 4 (вып. 50). Ч. 2. С. 107.
Худак Ю.И. // Рос. технол. журн. 2017. Т. 5. № 3. URL: https://rtj.mirea.ru/upload/medialibrary/924/ rtzh_3_2017_full.pdf.
Костин М.С., Воруничев Д.С. Реинжиниринг радиоэлектронных средств: монография. М.: МИРЭА, 2018.
Дополнительные материалы отсутствуют.
Инструменты
Радиотехника и электроника