Радиотехника и электроника, 2022, T. 67, № 7, стр. 668-675
Разработка малогабаритной высокоскоростной системы измерительной дефектоскопии и ее испытание на макетных объектах
Б. А. Чичигин a, *, И. А. Гроо a
a Национальный исследовательский университет “МЭИ”
111250 Москва, ул. Красноказарменная, 14, Российская Федерация
* E-mail: boris_ch@mail.ru
Поступила в редакцию 21.04.2021
После доработки 12.02.2022
Принята к публикации 25.02.2022
- EDN: HRULUP
- DOI: 10.31857/S0033849422070075
Аннотация
Разработан подход к синтезу систем измерительного контроля формы труднодоступных деталей с получением информации о трехмерной форме. Рассмотрены существующие методы и установки для решения подобных задач. Получен прототип малогабаритной высокоскоростной системы измерительной дефектоскопии с применением предложенного подхода. Рассмотрен метод стереореконструкции с использованием структурированной лазерной подсветки, что позволяет получить информацию о трехмерной форме гладкой поверхности, изображение которой не обладает резким перепадом контраста. Проведено апробирование системы на макетных объектах.
ВВЕДЕНИЕ
В различных отраслях техники возникают задачи по контролю соответствия формы труднодоступных деталей как на этапе производства и эксплуатации, так и при продлении сроков эксплуатации. Надежность эксплуатации сложного технологического оборудования в значительной степени зависит от надежности работы его высоконагруженных деталей. В процессе эксплуатации такие детали могут подвергаться воздействию силовых, вибрационных, температурных факторов. На целостность высоконагруженных деталей оказывает влияние коррозия, изменение температуры, эрозия, напряжения, износ и т.д. [1].
Механические повреждения создают предпосылки для зарождения и развития дефектов, что совместно с высокой нагруженностью объясняет возможность ускоренного разрушения ответственных деталей технологического оборудования.
Для своевременного обнаружения и получения информации об отклонениях разработаны методы выполнения измерений, в частности измерений размеров повреждений (дефектов) [2], при проведении эндоскопии. Так, например, для измерений формы трехмерной поверхности широко применяются оптические и эндоскопические методы благодаря их неразрушающему характеру и высокой скорости измерения [3]. Разработаны видеоэндоскопические неизмерительные установки для контроля полостей [4].
Известен подход, основанный на стереорегистрации, применяемой для восстановления положения по глубине и оценки движения камеры [5]. Два независимых оптиковолоконных эндоскопа используются для захвата стереоизображений. Известна реализация с использованием бипризмы и одной светоприемной матрицы, что позволяет уменьшить габариты системы [6–8]. Из-за использования фотограмметрии осуществимость подхода зависит от текстуры объекта измерения и в случае малоконтрастной поверхности осложняется, при этом использование бипризмы уменьшает реальное разрешение стереоизображений и точность восстановления.
Известен подход, при котором на объект проецируется структурированное освещение, при этом система выполнена жесткой и не способна проникать по сложным траекториям в сложные технологическое оборудование [9].
В работе [10] был разработан видеоэндоскоп для промышленного применения, реализующий фазовый метод измерений. Система способна регистрировать пространственные трехмерные измерения поверхностей, при этом оснащена компактными сенсорными головками. Система ограничена продолжительностью измерения примерно 2 с, что ухудшает применимость для ручного эксплуатационного контроля11.
Известен гибкий измерительный эндоскоп, состоящий из проектора с оптоволоконной передачей изображения и камеры со светоприемной матрицей на дистальном конце. Диаметр наконечника эндоскопа составляет 16 мм, что затрудняет его использование для эксплуатационного неразрушающего контроля оборудования. Измерения планарных эталонных мишеней показывают стандартное отклонение 310 мкм [11]. Известно применение в медицине, при котором используется активный стереометод и на объект проецируется структурированное освещение в виде сетчатой структуры [12]. Однако точности такого метода недостаточно для эксплуатационного контроля ответственных деталей в виду неопределенности, возникающей между узлами структурированной подсветки.
Известны реализации измерительных эндоскопических систем с применением MEMS-технологий [13], при этом либо системы выполнены жесткими, что ограничивает их применение, либо на матрицу проецируется несколько изображений, что уменьшает разрешение, либо проводится разделение получения ракурсов по времени, что накладывает серьезные ограничения на производительность контроля и точность фиксации дистального конца эндоскопа относительно объекта контроля.
В данной работе для решения проблемы эксплуатационного контроля деталей ответственного оборудования без разбора и демонтажа был проведен комплекс теоретических и экспериментальных исследований, позволяющих разработать метод синтеза малогабаритных высокоскоростных систем измерительной дефектоскопии для проведения неразрушающего контроля оборудования в процессе эксплуатации.
1. КОНСТРУКТИВНАЯ РЕАЛИЗАЦИЯ СИСТЕМЫ ДЕФЕКТОСКОПИИ
Для решения задачи дефектоскопии сложного технологического оборудования критическим является габаритный размер их исполнительной части. Для реализации измерительных возможностей был выбран стереоскопический метод многоракурсного восстановления формы сложных объектов с дополнительной лазерной подсветкой.
Использование лазерной подсветки обусловлено особенностью применение стереоскопического метода – необходимостью поиска положения идентичных точек пространства на стереопаре, что затруднено при плавном изменении контраста изображения (рис. 1). В предложенной конструкции при дополнительном проецировании лазерных пятен на объект исследования идентичные точки можно выявить в автоматическом режиме.
Рис. 1.
Применение фотограмметрического метода восстановления формы объекта с плавно изменяющейся формой; а – фотография объекта в белом свете, б – результат восстановления формы объекта.
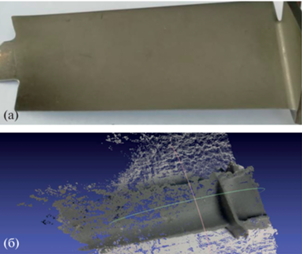
Для решения задачи сопоставления указанных точек в системе был применен лазерный импульсный проектор с возможностью проецирования на объект картины псевдохаотических мелких лазерных пятен (рис. 2).
Рис. 2.
Применение фотограмметрического метода восстановления формы объекта с использованием лазерной псевдохаотической подсветки, а – фотография объекта с проецированными лазерными пятнами, б – результат восстановления формы объекта.
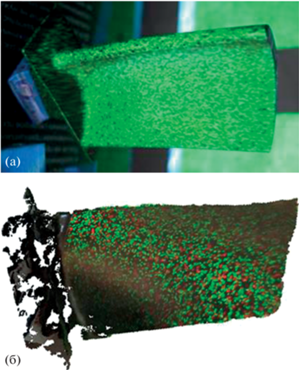
Для синтеза устройств дефектоскопии рассмотрим список общих требований, приводящих к предъявлению требований к отдельным узлам.
1. Траектория доставки определяет тип конструкции – жесткий или гибкий. Форма и размер технологических каналов для доступа к контролируемым деталям оборудования определяют требования к габаритным размерам системы по формулам:
где ax, ay – габаритные размеры системы; hx, hy – ограничения канала доставки по оси x и y соответственно. В ряде случаев система может быть выполнена несимметричной, например, если ограничения по одной оси отсутствуют или ограничения отличаются по осям [14].2. Траектория доставки определяет требования к длине эндоскопической системы и необходимость выполнять артикуляцию внутри оборудования для доступа к контролируемым деталям.
3. Минимальные размеры выявляемых отклонений определяют размер и расстояние между точками лазерного проектора и разрешение матрицы приемника, формирующего изображение.
4. Характер и форма объекта, а также наличие полостей вокруг объекта определяют рабочий отрезок объектива и направление обзора. Как правило, направление обзора прямое или имеет угол 90°.
5. Стационарность объекта контроля или его подвижность определяет требования к быстродействию матрицы и в ряде случаев к периоду освещения лазерного проектора.
Полученные требования позволяют реализовать систему, решающую задачу быстродействующей измерительной дефектоскопии.
С использованием результатов проведенной работы и требований пп. 1–5 был изготовлен прототип системы, представляющий из себя гибкую часть, на дистальном конце которой находится оптическая система, а на проксимальном конце система артикуляции и блок приема информации и управления освещением (рис. 3).
Рис. 3.
Функциональная схема прототипа системы дефектоскопии: 1 – миниатюрная оптическая стереоскопическая камера, 2 – источник белого света, 3 – импульсный источник лазерного излучения, 4 – ручки механической системы артикуляции, 5 – пульт управления артикуляцией, 6 – обрабатывающий микроконтроллерный блок, 7 – тросы артикуляции, 8 – линза, 9 – дифракционный оптический элемент, 10 – линза, 11 – оптоволокно лазерного потока, 12 – оптоволокно белого света, 13 – линии питания, 14 – линии передачи видеоданных.
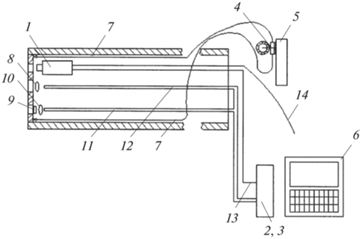
Прототип системы измерительной дефектоскопии представляет из себя оптическую систему, закрепленную на гибком средстве доставки и снабженную лазерным осветителем, формирующим на поверхности объекта структурированную подсветку известной формы.
Система контроля состоит из следующих частей:
– миниатюрной цифровой камеры, формирующей цифровое изображение объекта исследования,
– блока освещения белого света,
– лазерного осветителя,
– механической системы артикуляции;
– пульта управления артикуляцией;
– ПК для получения, обработки и отображения информации.
Вся исполнительная часть системы, которая доставляется внутрь контролируемого оборудования, убрана в гибкий тубус, наружный диаметр которого составляет 7.9 мм. Сечение исполнительной части системы круглое. Длина исполнительного органа системы дефектоскопии 2 м, гибкое исполнение. Исходя из условия расчета на прочность контролируемого оборудования при эксплуатации необходимо обнаруживать отклонения от 0.02 мм и больше. Направление обзора выбрано прямое. Контролируемые объекты могу вращаться.
Управление системой осуществляется путем поворота ручки на пульте управления артикуляцией, при этом вращение вызывает перемещение тросов, таким образом рабочая часть эндоскопа может изгибаться в двух взаимоортогональных направлениях.
Блок освещения в принятой реализации состоит из полупроводникового лазера мощностью 50 мВт и длиной волны 532 нм. Световой поток лазера направляется в оптическое волокно. На выходе из волокна лазерного светового потока расположена линза, чтобы придать потоку необходимую расходимость. В фокусном расстоянии линзы расположен дифракционный оптический элемент (ДОЭ), выполненный таким образом, чтобы формировать на поверхности объекта псевдохаотические пятна размером 9 мкм [15]. Угол проекции после ДОЭ составляет 60°. Лазер может работать в режиме как постоянного освещения, так и импульсного. В последнем случае он управляется генератором импульсов с возможностью менять период следования и скважность импульсов.
Используя цифровое изображение объекта и спроецированное на нее лазерное изображение лазерных пятен, компьютерный алгоритм проводит восстановление поверхности и в случае выявления несплошности проводит измерение ее площади, длины и ширины.
Дистальный конец состоит из двух миниатюрных видеокамер и блока лазерного освещения.
В качестве миниатюрной камеры применена камера собственной разработки на основе матрицы OV9724, имеющая габаритные размеры 3.9 × × 2.89 мм. Камера удовлетворяет по критерию минимальным габаритным размерам и имеет разрешение 1080 × 720, фокусное расстояние объектива камеры 1.66 мм, режим съемки 30 кадров/с. Поле зрения камеры составляет 65°.
Представленная система позволяет контролировать труднодоступные детали на предмет наличия дефектов, при этом выполняется оценка их размеров без проведения их демонтажа и разбора.
Данную систему можно использовать в качестве эксплуатационного контроля, а также при продлении ресурса и сборке сложного технологического оборудования.
Реализация прототипа системы приведена на рис. 4.
2. ПРОГРАММНАЯ РЕАЛИЗАЦИЯ ПРОТОТИПА СИСТЕМЫ ДЕФЕКТОСКОПИИ
Для проведения измерений параметров несплошности поверхности и параметров формы объекта контроля было разработано программное обеспечение, реализующее работу прототипа системы дефектоскопии.
Данное программное обеспечение позволяет:
– провести калибровку по объекту с известной формой в виде шахматной доски – с белыми и черными квадратами;
– получить изображение с оптической системы камеры и записать его на жесткий диск компьютера;
– восстановить трехмерный элемент поверхности объекта, наблюдаемый с одного ракурса;
– объединить элементы поверхности, наблюдаемые с разных ракурсов;
– автоматически выделить дефектные области на поверхности детали;
– рассчитать длину и ширину дефектов или параметры формы объекта.
Результаты выводятся в виде таблицы и сохраняются на жестком диске.
Принцип работы программного обеспечения изложен в работе [15]. При изготовлении прототипа программа была доработана и отлажена для получения изображений, их обработки и анализа с выдачей результатов измерений. При реализации прототипа программное обеспечение было доработано с целью реализации возможности наложения элементов объекта, полученных с разных ракурсов для получения полной информации о трехмерной форме объекта.
Данная функция программного обеспечения была реализована с использованием итеративного алгоритма приближения точек – Iterative Closest Point (ICP).
Алгоритм ICP состоит из двух базовых шагов: 1) установление соответствия между точками двух облаков, 2) решение вариационной задачи нахождения оптимального аффинного или ортогонального преобразования, совмещающего данные двух облаков точек.
Пусть есть два облака точек X и Y, тогда каждую итерацию в вариационной задаче классического алгоритма ICP для произвольного аффинного преобразования можно представить следующим образом:
1. Определение ближайших точек ∀xk ∈ X, yk = = {y ∈ Y|y(xk, y) = min}, где y (xk, y) – расстояние между парой точек в X и Y.
2. Вычисление веса wk для каждой пары точек. Определение лучшего преобразования, при котором матрица вращения R, матрица масштабирования S и вектор переноса T минимизируют выражение
(3)
$E\left( {R,T} \right) = \frac{1}{W}\sum\limits_{{{N}_{p}}} {{{w}_{k}}} {{\left\| {RS{{x}_{k}} + T - {{y}_{k}}} \right\|}^{2}},$(4)
$W = \sum\limits_{i = 1}^{{{N}_{{S{\text{и}}}}}} {\sum\limits_{j = 1}^{{{N}_{{T{\text{ц}}}}}} {{{w}_{{ij}}}} } ,$3. Полученное преобразование (R, T) применяется к X до тех пор, пока
(5)
$\left| {E{{{\left( {R,T} \right)}}_{i}} - E{{{\left( {R,T} \right)}}_{{i + 1}}}} \right| < \varepsilon ,$Для функционирования алгоритма изображений поверхность объекта фиксировалась с различных ракурсов с перекрытием 15…20%. Перекрытия использовались для сопоставления полученных фрагментов поверхности с наибольшей достоверностью. Алгоритм ICP работает итеративно, количество итераций для получения удовлетворительного результата – 40…60. Такое количество итераций не позволяет работать программе в режиме реального времени, программа функционирует с задержкой в 20 с на каждое наложение ракурса. На рис. 5 приведена иллюстрация работы алгоритма.
3. РЕЗУЛЬТАТЫ ИСПЫТАНИЙ ПРОТОТИПА СИСТЕМЫ ДЕФЕКТОСКОПИИ
Для определения разрешающей способности камеры использовалась штриховая мира ГОИ № 5, выполненная в соответствии с работой [16]. Мира снималась с расстояний 1, 1.5 и 2 см.
На рис. 6 представлено изображения миры, полученные на расстоянии 1.5 см. На изображениях различаются штрихи на 12-м элементе миры, их ширина 119.8 мкм [17]. Соответственно, линейная разрезающая способность камеры на расстоянии 1.5 см не хуже 84.8 мкм.
Проведена серия опытов для определения погрешности измерения длины объектов. Для этого использовались концевые меры с высотами 21.2, 18.0 и 8.5 мм.
Среднеквадратическое отклонение высоты детали вычисляли по формуле [18]
(6)
$\sigma = \sqrt {\mathop \sum \limits_{i = 1}^n \frac{{{{{({{x}_{i}} - {{x}_{{{\text{ист}}}}})}}^{2}}}}{n}} .$Результаты измерений с помощью прототипа системы дефектоскопии приведены в табл. 1.
Таблица 1.
Значения геометрических параметров при определении размеров объектов
Длина концевой меры, мм | СКО, мм | Относительная погрешность, % |
---|---|---|
21.2 | 0.61 | 3.4 |
18.0 | 0.73 | 4.0 |
8.5 | 0.56 | 6.6 |
Определив доверительный интервал выполнения измерений 95%, получаем, что все значения измерений лежат в интервале –2σ, +2σ.
Были выполнены тесты по получению параметров изделий сложной формы. Наложение облаков точек происходит с помощью итеративного алгоритма ближайших точек. На рис. 7 представлены результаты апробации алгоритма при совмещении нескольких облаков точек, полученных с разных ракурсов для синтеза модели объекта сложной формы. Принцип действия самого алгоритма приведен на рис. 8 .
Для получения информации о минимально выявляемом отклонении и возможности работы с объектами сложной формы тестирование проводилось на вращающемся колесе ступени компрессора авиадвигателя. На лопатки компрессора были искусственно нанесены отклонения различных размеров.
При последующей обработке было установлено, что минимально выявляемое отклонение имеет размеры по глубине 0.02 мм. Также форма сложных объектов, таких как лопатка компрессора, была полностью восстановлена с применением стереоснимков, полученных с шести ракурсов.
Представленное программно-аппаратное решение отличается возможностью работы с неконтрастными, плавно изменяющимися поверхностями объектов. Предложенное структурированное лазерное освещение позволяет восстанавливать облака точек с улучшенным пространственным разрешением – в данной реализации до 0.02 мм. Захват изображения для анализа происходит одномоментно, допускается вращение или движения объекта. Полученные ракурсы объединяются для сравнения с эталонной моделью.
ЗАКЛЮЧЕНИЕ
Таким образом, разработан подход к синтезу систем измерительной дефектоскопии. Апробирован подход и синтезирован опытный образец системы диметром 10 мм, для которого также разработано программное обеспечение. Проведены лабораторные испытания на модельных объектах. Показана возможность восстановления многоракурсного трехмерного изображения с возможностью получения количественной параметризации дефектов. Получены значения погрешностей при проведении оценки геометрических отклонений детали. Получено, что минимальная выявляемое отклонение имеет размеры по глубине 0.02 мм, при выполнении измерений геометрических величин погрешность составила 6.6%.
Авторы заявляют об отсутствии конфликта интересов.
Список литературы
Кеткович А.А., Яковлева Н.И., Чичигин Б.А. // Контроль. Диагностика. 2007. № 3. С. 32.
Raj B., Jayakumar T., Thavasimuthu M. Practical Non-destructive Testing. Sawston: Woodhead Publishing, 2002.
Schwenke H., Neuschaefer-Rube U., Pfeifer T., Kunzmann H. // CIRP Annals- Manufacturing Technology. 2002. V. 51. № 2. P. 685.
Lei Yang, Meng Chen, Qian Zhu et al. // Sensors and Actuators A: Physical. 2019. V. 296. P. 17.
Noonan D.P., Mountney P., Elson D.S. et al. // IEEE Int. Conf. on Robotics and Automation. Kobe. 12–17 May 2009. N.Y.: IEEE, 2009. P. 4463.
Gorevoy A.V., Machikhin A.S., Shurygin A.V. et al. // Тр. 26-й Междунар. конф. по компьютерной графике и зрению “Графикон”. Нижний Новгород, 19–23 сент. 2016. М.: ИПМ им. М.В. Келдыша, 2016. С. 253.
GE Inspection Technologies Videoprobe 3D Measurement Handbook: A guide to advanced 3D measurement technologies, techniques and applications for video borescopes used in remote visual inspection applications. GE Inspection Technologies721 Visions Drive Skaneateles, NY 13152, 315-554-2000 02/2016. Руководство по использованию.
Горевой А.В., Мачихин А.С., Хохлов Д.Д. и др. // Дефектоскопия. 2017. Т. 53. № 9. С. 44.
Hasegawa K., Noda K., Sato Y. // Intern. Conf. on Pattern Recognition. 2002. V. 2. P. 761, https://doi.org/10.1109/ICPR.2002.1048414
Korczewski Z. // Polish Maritime Research. 2013. V. 20. № 1. P. 23.
Furukawa R., Masahito A., Shinsaku H. et al. // Proc. 36th Annual Int. Conf. of the IEEE Engineering in Medicine and Biology Soc. (IMBC 2014) Chicago. 26–30 Aug. N.Y.: IEEE, 2014. P. 6944745.
Hanh N.D. Le, Hieu Nguyen, Zhaoyang Wang, Jin U. Kang // Proc. SPIE. 2017. V. 10054. P. 1005416.
Yang S.P., Seo Y.H., Kim J.B. et al. // Micro and Nano Syst. Lett. 2019. V. 7. P. 8.
Чичигин Б.А. // Фотоника. 2009. № 3. С. 30.
Чичигин Б.А., Гроо И.А. // Матер. Междунар. науч. конф. “Высокие технологии и инновации в науке”. Санкт-Петербург, 27 ноября 2018, С. 115.
ГОСТ 53469-2009 Оптика и оптические приборы. Эндоскопы и приборы эндотерапевтические медицинские. М.: Стандартинформ, 2011.
ГОСТ 19803-86 “Системы телескопические для оптических приборов. Визуальный метод определения предела разрешения”. М.: Изд-во стандартов, 1995.
Кобзарь А.И. Прикладная математическая статистика. Для инженеров и научных работников. М.: Физматлит, 2006.
Дополнительные материалы отсутствуют.
Инструменты
Радиотехника и электроника