Расплавы, 2021, № 4, стр. 338-353
Исследование продуктов электролизного борирования поверхности инструментальных сталей с реверсированием тока в борсодержащем оксихлоридном расплаве на основе CaCl2
Е. С. Филатов a, b, *, Н. И. Шуров a, К. Р. Каримов a, Е. В. Никитина a, b, Д. О. Чухванцев a, Н. С. Семёнова b
a Институт высокотемпературной электрохимии УрО РАН
Екатеринбург, Россия
b Уральский федеральный университет им. Первого президента России Б.Н. Ельцина
Екатеринбург, Россия
* E-mail: e.filatov@ihte.uran.ru
Поступила в редакцию 19.10.2020
После доработки 02.12.2020
Принята к публикации 29.12.2020
Аннотация
Борирование – один из наиболее эффективных и перспективных методов поверхностного упрочнения стальных деталей машин и инструмента, работающих при повышенных статических и динамических нагрузках. В целях экономии энергоресурсов и отказа от дорогостоящих порошков бора, создания замкнутого цикла использования сырья и промывочной воды в ИВТЭ УрО РАН проведены исследования по разработке технологий по упрочнению деталей машин и инструмента методами электролизного борирования (электролизное, электролизно-циклическое, электролизное с применением реверсированного тока) расплавленных солях на основе хлорида кальция. Изучена кинетика образования боридных покрытий на порошковой стали (ЖГР) Cr11Ni6Cu15, 20Х13 в расплаве CaCl2 + 3 мас. % B2O3 при температурах 800, 850 и 900°C и времени выдержки 1, 2 и 3 ч, определены основные температурные, концентрационные и токовые параметры процесса борирования, обуславливающие получение качественного защитного покрытия. Методами рентгенофазового и микрорентгеноспектрального анализа исследованы продукты процесса борирования поверхности инструментальных сталей в расплаве на основе хлорида кальция с добавлением оксида бора с применением реверсированного тока. Металлографическим методом определен фазовый состав покрытия из продуктов электролизного борирования. Определена толщина, микротвердость и фазовый состав всех полученных боридных покрытий. Результаты по борированию предоставленных опытных деталей позволяют рекомендовать технологию нанесения покрытия для применения в промышленности.
ВВЕДЕНИЕ
В подавляющем большинстве случаев при эксплуатации деталей машин и механизмов разрушение их начинается с поверхности или в приповерхностных слоях, поэтому в решении проблемы надежности деталей важную роль играет химико-термическая обработка, которая позволяет путем легирования поверхностных слоев изделий придавать им требуемый комплекс свойств. Создание защитных покрытий является в ряде случаев наиболее эффективным, а иногда и единственно возможным средством решения сложных технических проблем повышения прочности, износостойкости, жаростойкости, коррозионной устойчивости металлов и сплавов. Применение защитных покрытий часто позволяет заменять дорогостоящие и редкие металлы менее дефицитными материалами без существенного изменения работоспособности деталей, узлов и конструкций.
Одним из наиболее эффективных и перспективных методов поверхностного упрочнения деталей машин и инструментов из стали, работающих при повышенных статических и динамических нагрузках, является борирование. Главное из преимуществ технологий борирования – это замена более дорогих сложнолегированных конструкционных, инструментальных и других машиностроительных сталей на менее легированные и более дешевые, что также способствует импортозамещению. Борированная поверхность значительно повышает износостойкость, поверхностную твердость и усталостную прочность деталей. При сравнительной оценке существующих методов борирования [10] в первую очередь необходимо учитывать их технологические достоинства и недостатки, производительность, скорость насыщения и стоимость (экономическую эффективность). Следует отметить, что в настоящее время не существует метода борирования, который бы по своим технико-экономическим показателям значительно превосходил все остальные. Каждый из методов борирования имеет достоинства и недостатки. Выбор метода должен проводиться с учетом характера и размеров обрабатываемых изделий, условий их работы, объемами производства.
С точки зрения технологической простоты наиболее выигрышным является жидкостное борирование [12]. Этот процесс осуществляется в тиглях из стали 20Х18Н12Т или другой жаропрочной стали, соотношение диаметра тигля к высоте должно быть не менее 1 : 3, разогрев осуществляется в шахтных печах сопротивления или в печах с газовым нагревом. Насыщение проводится в расплавленной буре (Na2B4O7) с добавкой 5–6 мас. % порошка бора или до 40 мас. % карбида бора. Однако расплавы, применяемые при жидкостном борировании, как правило, имеют повышенную вязкость, что приводит к заметному уносу дорогого расплава с обрабатываемыми деталями. Дороговизна порошков бора, низкая стойкость тиглей из жаропрочных марок сталей и большие затраты по энергоресурсам – это главные недостатки указанного способа борирования.
Борирование в порошкообразных смесях [3–20] имеет большое промышленное применение, как в России, так и за рубежом. Однако это обусловлено не столько достоинствами данного метода борирования, сколько нерешенными проблемами и технологическими недоработками других методов борирования. Борирование проводят в герметичных контейнерах из нержавеющих или жароупорных сталей с плавким затвором. Насыщению можно подвергать изделия любой конфигурации. Качество боридных слоев (чистота поверхности и сплошность), заметно ниже качества диффузионных слоев, полученных жидкостными и электролизными методами борирования. Экономическая эффективность порошкового борирования определяется кратностью использования смеси и используемым борсодержащим веществом. Стоимость обработки порошковым методом, как правило, выше, чем жидкостным.
Борирование из обмазок (паст). Развитие этого направления в борировании в значительной мере стимулируется потребностью создания приемлемой технологии упрочнения массивных и крупногабаритных изделий, в частности избирательного борирования отдельных участков деталей машин и механизмов [21]. При достаточной простоте, главный недостаток технологий борирования из паст и обмазок, это сползание обмазок с вертикальных поверхностей деталей при печном нагреве или ТВЧ, и, как правило, обгорание поверхности деталей.
Электролизное борирование нашло более или менее широкое промышленное применение. Оно высокопроизводительно, результаты хорошо воспроизводимы, качество получаемых боридных слоев высокое и т.д. Однако и этот способ борирования не лишен технологических недостатков. Необходима специальная энергоемкая установка. Насыщающей средой при электролизном борировании обычно является расплавленная бура. Чистая бура более агрессивна по отношению к материалам, из которых изготавливаются тигли, чем расплавы, используемые при жидкостном борировании. По этой причине стойкость стальных тиглей заметно ниже. Нахождение в расплаве графитовых анодов уменьшает полезную площадь зеркала расплава. Имеется трудность отмывки деталей от соли и катодного осадка.
В целях экономии энергоресурсов и отказа от дорогостоящих порошков бора, создания замкнутого цикла использования сырья и промывочной воды в ИВТЭ УрО РАН проведены исследования по разработке технологий по упрочнению деталей машин и инструмента методами электролизного борирования (электролизное, электролизно-циклическое, электролизное с применением реверсированного тока) в расплаве хлорида кальция с оксидом бора.
Технологии разрабатываются для электролизного борирования деталей в среднетемпературных электродных соляных ваннах типа СВС, серийно выпускаемых промышленностью для безокислительного разогрева металла под закалку, с односторонним расположением электродов, футерованных высокоглиноземистым кирпичом [22].
Борирующий расплав имеет следующий состав: хлорид кальция – 95–97 (мас. %) + + оксид бора – 3–5 (мас. %) [22].
Методы электролизного борирования в хлориде кальция с 3–5 (мас. %) оксида бора при температурах 800–950°С, разработанные в ИВТЭ, когда катодом служит стальная деталь, а анодом – графит, обеспечивают высокую скорость борирования. При этом, регулируя катодную плотность тока, можно получать однофазное или двухфазное боридное покрытие (табл. 1).
Таблица 1.
Толщина боридных слоев на Армко-железе и Ст. 20 при различных способах борирования в солевых расплавах при температуре 900°С
Метод | Сталь | Состав расплава, мас. % |
Время, ч | Режим | Толщина слоя, мкм |
---|---|---|---|---|---|
Жидкостное борирование | Армко-Fe | 79% NaB4O7 + + 15% NaCl + 6% B |
3 | Без электролиза | 120 |
Ст-20 | Без электролиза | 110 | |||
Электролизное борирование с реверсированием тока | Армко-Fe | CaCl2 + 3% B2O3 | 2 | iк = 0.2 А/см2, τ = 1.5 с; iа = 0.2 А/см2, τ = 0.4 с |
110–115 |
Ст-20 | 120 |
Электролизное борирование осуществляется при iк = 0.01–0.05 А/см2, время электролиза от 1 до 5 ч на требуемую толщину покрытия и фазовый состав.
Электролизно-циклическое борирование – электролиз при плотности тока iк = = 0.1–0.2 А/см2, время электролиза 1 мин, выдержка в расплаве без электролиза 8–14 мин. Число циклов – 8–20. Во время электролиза элементарный бор выделяется на деталь из оксида бора, а затем в период выдержки детали в расплаве без электролиза диффундирует в сталь с образованием боридов. Плотность тока, время электролиза, время нахождения детали в расплаве без электролиза и количество циклов подбирается экспериментально, зависит от марки стали детали, ее назначения и толщины покрытия.
Применение реверсированного тока увеличивает скорость электролизного борирования на 30%. Объяснение этому – обратимость электродных процессов при электролизе оксида бора, растворенного в расплаве хлорида кальция, и выделение значительного количества элементарного бора на стальном катоде. Параметры реверсированного тока должны обеспечивать только определенное активирование катодной поверхности и поддерживать на поверхности катода (стальной детали) оптимальный уровень концентрации активного бора.
Лучшие результаты боридных покрытий получены при плотностях катодного и анодного токов: iк = 0.2 А/см2, τ = 1.5 с и iа = 0.2 А/см2, τ = 0.4 с.
Ниже в табл. 1 приведены для сравнения боридные слои, полученные при различных способах борирования в солевых расплавах.
В предыдущих наших исследованиях [23–29] была показана принципиальная возможность получения боридных покрытий на сталях в солевых расплавах при бестоковом переносе и наложении постоянного тока для интенсификации процесса. Однако не было выявлены зависимость толщины и состава покрытия от температуры, химического состава сталей, а также времени процесса. В связи с этим целью настоящих исследований было: исследование кинетики борирования сталей гальвано-термодиффузионным методом при различных плотностях реверсированного тока, а также оценка эффективности борирования в расплавленных солях деталей из порошковой стали ЖГР (Cr11Ni6Cu15), стали 20Х13, с целью повышения коррозионной стойкости и абразивно-эррозионной стойкости деталей в коррозионных средах. Выбор сталей обоснован их широким применением в машиностроении, где требуется упрочнение поверхности деталей без использования дорогостоящих сплавов.
В качестве метода нанесения покрытия выбрано электролизное борирование с реверсированием тока как наиболее эффективное.
Работа включала следующие этапы:
1. Изучение кинетики насыщения при 800, 850 и 900°C и времени выдержки 1, 2 и 3 часа;
2. Металлографические исследования (измерение толщины и микротвердости) полученных покрытий;
3. Рентгенофазовый анализ покрытий;
4. Микрорентгеноспектральный анализ покрытий;
5. Борирование опытных деталей по выбранному режиму.
ЭКСПЕРИМЕНТАЛЬНАЯ ЧАСТЬ
Для проведения исследований была создана лабораторная установка, состоящая из соляной ванны с корундовым тиглем, программатора ПР-8 и выпрямителя тока на 10 А.
В корундовом тигле при температуре 900°С наплавляли 800 г расплава, содержащего 3 мас. % оксида бора и 97 мас. % хлорида кальция. Затем в расплав опускали графитовый анод и железный катод. Начальный импульс катодного тока 0.2 А/см2 в течение 15 мин задавали для очистки электролита от следов связанной воды, после чего железный катод удаляли из очищенного расплава, и на специальной подвеске погружали в него стальные образцы, изготовленные из исследуемых сталей. Затем после небольшой выдержки проводили электролизный синтез при выбранных параметрах. После завершения электролиза образцы извлекались из расплава и охлаждались на воздухе до комнатной температуры. Плотная пленка соли предотвращала образование окалины на поверхности деталей. После остывания образцы отмывали от соли в воде и исследовали различными методами, описанными ниже. На этом этапе исследования изучена кинетика насыщения исследуемых материалов бором при 800, 850 и 900°C и времени выдержки 1, 2 и 3 часа.
Обычно на практике борированные детали подвергают закалке для повышения твердости поверхности. Эта технология достаточно отработана, поэтому в настоящих исследованиях она не применялась.
Борированные образцы аттестовывались следующими методами:
1. Металлографический анализ. Борированные образцы запрессовывались в пластмассу по технологии фирмы “Struers” на термопрессе “LaboPress-1”, отрезались на алмазном станке “Minosecar 2”, шлифы полировались по технологии фирмы “Struers” на станке “LaboPol-4”, Травление шлифов для исследования структуры покрытий проводилось в 5–8% растворе азотной кислоты в спирте. Исследование шлифов производилось на металлографическом микроскопе “Reichert”, микротвердость (HV) измерялась на микротвердомере “ПМТ-3” при нагрузке 50 г.
2. Рентгенофазовый анализ покрытий. Производился на рентгеновском дифрактометре “Rigaku DMAX-D1200”.
3. Микрорентгеноспектральный анализ покрытий. Производился на рентгеновском микроанализаторе “Jeol”.
Аттестация борированной стали состава Cr11Ni6Cu15 (ЖГР)
Результаты металлографического исследования борированного образца из порошковой стали ЖГР приведены на рис. 1. Видно, что покрытие сплошное, полностью покрывает поверхность образца, хотя сам сплав пористый, в нем много раковин. Боридное покрытие состоит из двух фаз, имеющих игольчатую структуру. Так же наблюдается переходная зона между фазами боридов и основой толщиной до 5 мкм.
Рис. 1.
Микрофотография шлифа порошкового сплав Х11Н8Д20 (ЖГР) + В, температура – 850°С, время борирования – 3 ч. Толщина боридного слоя – 43 мкм. 1 – Фаза Fe2B – 23 мкм, HV50 = 8640 МПа; 2 – фаза FeB – 20 мкм, HV50 = 12 840 МПа; 3 – переходная зона – 3–5 мкм. Основа: HV50 = 2254 МПа.
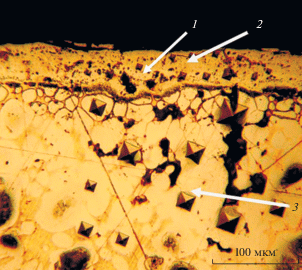
Проведенный рентгенофазовый анализ (РФА) образца выявил фазы FeB и Fe2B (рис. 2).
На рентгенограмме присутствуют слабые нерасшифрованные линии. Они принадлежат сложным боридам никеля и хрома, как основным легирующим элементам. Ниже приведены результаты микрорентгеноспектрального исследования, включающие фотографии с цифрового микроскопа, карты распределения элементов и точечные элементные анализы.
На рис. 3 приведены электронные фотографии шлифа борированного образца из стали ЖГР при увеличениях 100, 200, 500 и 1000. На фотографиях с меньшим увеличением показаны области, фотографии которых представлены с большим увеличением.
Рис. 3.
Электронные фотографии шлифа борированного образца стали ЖГР при увеличениях а) 100; б) 200; в) 500; г) 1000.
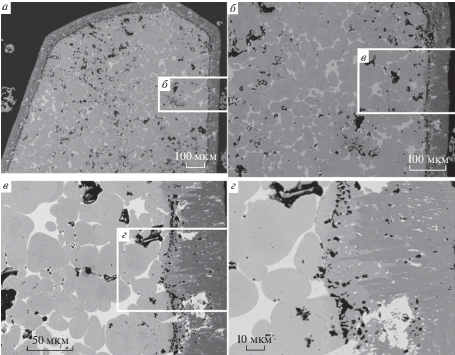
На рис. 4 приводятся карты распределения элементов по поверхности шлифа. Карта распределения элемента показывает схематичное изображение распределения его концентрации по выбранной поверхности. Для удобства элементы изображают разными цветами. Для количественного анализа карты всех элементов объединяют на одном изображении.
На рис. 5 и в табл. 2 приведены результаты качественного анализ по точкам.
Рис. 5.
Изображение шлифа борированного образца из стали ЖГР с указанием точек, в которых выполнен поэлементный анализ.
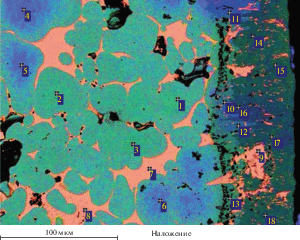
Таблица 2.
Результаты качественного анализа шлифа борированного образца из стали ЖГР, (мас. %)
Точка | B | Si | Cr | Mn | Fe | Ni | Cu | Итог |
---|---|---|---|---|---|---|---|---|
1 | 0.00 | 0.47 | 15.41 | 0.25 | 69.63 | 9.04 | 5.31 | 100.10 |
2 | 0.00 | 0.39 | 16.60 | 0.00 | 67.84 | 9.07 | 5.91 | 99.82 |
3 | 0.00 | 0.46 | 19.27 | 0.00 | 65.32 | 9.26 | 4.24 | 98.56 |
4 | 0.00 | 0.17 | 3.30 | 0.17 | 88.52 | 2.07 | 5.26 | 99.50 |
5 | 0.00 | 0.30 | 5.92 | 0.12 | 86.11 | 2.46 | 4.05 | 98.97 |
6 | 0.00 | 0.24 | 5.88 | 0.14 | 83.37 | 2.93 | 6.59 | 99.14 |
7 | 0.00 | 0.00 | 0.54 | 0.14 | 3.81 | 1.73 | 94.80 | 101.02 |
8 | 0.00 | 0.00 | 0.52 | 0.15 | 3.71 | 1.69 | 93.91 | 99.97 |
9 | 0.00 | 0.27 | 0.60 | 0.00 | 5.34 | 2.69 | 92.18 | 101.09 |
10 | 10.07 | 0.10 | 7.53 | 0.14 | 78.16 | 4.47 | 0.36 | 100.84 |
11 | 9.41 | 0.07 | 4.69 | 0.24 | 83.30 | 2.04 | 0.41 | 100.16 |
12 | 10.50 | 0.00 | 6.50 | 0.17 | 80.31 | 3.14 | 0.98 | 101.60 |
13 | 10.87 | 0.13 | 15.26 | 0.00 | 71.41 | 3.47 | 0.55 | 101.69 |
14 | 20.57 | 0.07 | 10.77 | 0.19 | 69.84 | 3.71 | 0.41 | 105.56 |
15 | 20.34 | 0.00 | 10.76 | 0.00 | 68.26 | 4.80 | 0.45 | 104.61 |
16 | 21.70 | 0.09 | 6.07 | 0.00 | 75.79 | 2.18 | 0.40 | 106.22 |
17 | 19.99 | 0.08 | 10.74 | 0.23 | 67.25 | 3.47 | 2.80 | 104.57 |
18 | 18.81 | 0.06 | 10.85 | 0.00 | 68.69 | 3.92 | 0.33 | 102.66 |
Проведенные микрорентгеноспектральные исследования позволяют сделать следующие выводы:
1. Боридное покрытие на стали ЖГР сплошное, равномерное. Покрывается вся поверхность образца (рис. 3), несмотря на то, что сплав пористый и имеет большое количество раковин. Это в свою очередь подтверждает достоинство, как метода, так и качества покрытия. В покрытии видны 2 фазы, имеющие игольчатую структуру. Толщина покрытия – до 50 мкм. Под покрытием видна переходная зона, толщина до 5 мкм;
2. Покрытие в основном содержит железо и бор. Основные легирующие компоненты – хром и никель.
3. Медь присутствует в материале основы в основном в виде связки. В покрытии характер ее распределения такой же.
4. Видимые дефекты сплава содержат большое количество кремния. Он же формирует переходную зону. В процессе борирования происходит его оттеснение от поверхности образца и концентрирование сразу под покрытием.
5. На стали при 900°С за 3 ч формируется покрытие толщиной до 70 мкм. Покрытие при этом сплошное, равномерное, без сколов.
6. Покрытие состоит из фаз Fe2B (микротвердость HV50 = 8640 МПа) и FeB (микротвердость HV50 = 12 840 МПа). Между покрытием и материалом основы выделяется переходная зона, в которой концентрируется кремний.
7. Аттестация борированной стали 20Х13.
8. Cталь 20Х13 борировали при 900°C, в течение 3 ч. Вместе с деталями борировались образцы-свидетели, из которых изготавливались металлографические шлифы.
Результаты металлографического исследования борированного образца из стали 20Х13 приведены на рис. 6. Видно, что покрытие сплошное, полностью покрывает поверхность образца. Боридное покрытие состоит из двух фаз, имеющих игольчатую структуру. Проведенный рентгенофазовый анализ образца выявил фазы FeB и Fe2B. Также наблюдается переходная зона между фазами боридов и основой толщиной до 5 мкм. Черная полоса, отделяющая покрытие от основы на фотографии шлифа – следствие химического травления шлифа.
Рис. 6.
Фото шлифа. Сталь 20Х13 + В, температура – 900°С, время борирования – 2 ч. Толщина боридного слоя – 43 мкм. 1 – фаза Fe2B – 23 мкм. HV50 = 12 293 МПа, 2, 5 – основа, HV50 = 3431 МПа, 3 – переходная зона – 3 – 5 мкм, HV50 = 2732 МПа; 4 – фаза FeB – 20 мкм, HV50 = 19 920 МПа.
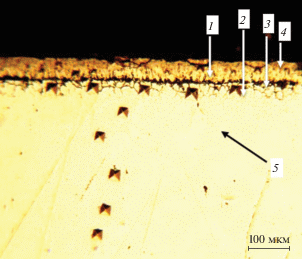
На рис. 7 приведены электронные фотографии шлифа борированного образца из стали 20Х13 при увеличениях 100, 200, 500 и 1000. На фотографиях с меньшим увеличением показаны области, фотографии которых представлены с большим увеличением.
Карты распределения элементов представлены на рис. 8.
Таблица 3.
Результаты качественного анализа шлифа борированного образца из стали 20Х13 (мас. %)
Точка | B | Si | S | Cr | Mn | Fe | Ni | Итог |
---|---|---|---|---|---|---|---|---|
1 | 0.00 | 0.30 | 0.00 | 12.99 | 0.41 | 85.64 | 0.00 | 99.34 |
2 | 0.00 | 0.35 | 0.00 | 13.00 | 0.54 | 85.28 | 0.18 | 99.34 |
3 | 0.00 | 0.30 | 0.00 | 16.03 | 0.30 | 81.45 | 0.16 | 98.25 |
4 | 0.00 | 0.16 | 0.00 | 28.57 | 0.63 | 67.58 | 0.00 | 96.94 |
5 | 0.00 | 0.18 | 0.00 | 27.30 | 0.56 | 69.34 | 0.19 | 97.56 |
6 | 0.00 | 0.25 | 0.00 | 17.51 | 0.44 | 79.62 | 0.25 | 98.08 |
7 | 0.00 | 0.24 | 11.96 | 7.46 | 23.02 | 51.49 | 0.15 | 94.32 |
8 | 0.00 | 0.14 | 5.21 | 24.79 | 7.82 | 59.25 | 0.20 | 97.40 |
10 | 0.00 | 2.44 | 0.00 | 5.36 | 0.39 | 90.43 | 0.66 | 99.27 |
11 | 0.00 | 2.39 | 0.00 | 5.97 | 0.26 | 89.37 | 0.60 | 98.59 |
12 | 0.00 | 2.45 | 0.00 | 5.29 | 0.33 | 90.36 | 0.61 | 99.05 |
13 | 9.01 | 0.00 | 0.00 | 13.47 | 0.40 | 76.08 | 0.23 | 99.20 |
14 | 10.77 | 0.00 | 0.00 | 14.75 | 0.46 | 76.34 | 0.00 | 102.31 |
15 | 12.80 | 0.00 | 0.00 | 12.68 | 0.37 | 78.89 | 0.24 | 104.97 |
16 | 11.68 | 0.08 | 0.00 | 22.05 | 0.45 | 68.56 | 0.18 | 103.00 |
17 | 12.72 | 0.00 | 0.00 | 18.66 | 0.44 | 72.02 | 0.00 | 103.83 |
18 | 8.90 | 0.10 | 0.00 | 17.73 | 0.41 | 72.93 | 0.00 | 100.07 |
19 | 20.35 | 0.00 | 0.00 | 11.59 | 0.36 | 71.54 | 0.18 | 104.02 |
20 | 17.28 | 0.00 | 0.00 | 10.18 | 0.35 | 72.23 | 0.00 | 100.04 |
21 | 18.45 | 0.00 | 0.00 | 8.99 | 0.31 | 74.12 | 0.18 | 102.05 |
22 | 19.89 | 0.00 | 0.00 | 17.48 | 0.26 | 66.05 | 0.00 | 103.68 |
23 | 19.03 | 0.00 | 0.00 | 22.94 | 0.35 | 60.69 | 0.00 | 103.01 |
24 | 19.13 | 0.07 | 0.00 | 21.08 | 0.26 | 61.89 | 0.16 | 102.59 |
Результаты точечного качественного анализа приведены на рис. 9 и в табл. 4.
Рис. 9.
Изображение шлифа борированного образца из стали 20Х13 с указанием точек, в которых выполнен поэлементный анализ.
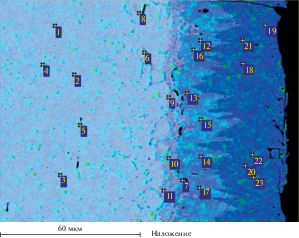
Таблица 4.
Толщина боридного покрытия и удельное увеличение массы на сталях в зависимости от температуры и времени насыщения в расплаве: хлорид кальция – 95–97 мас. %, оксид бора – 3–5 мас. %
Сталь | Температура, °С | Время борирования, час |
Толщина боридного слоя, мкм |
Удельное увеличение массы, г/дм2 | Унос расплава с деталями, г/дм2 |
---|---|---|---|---|---|
20Х13 | 800 | 1 | 6.2 | 0.06 | |
2 | 9.6 | 0.10 | |||
3 | 14.4 | 0.11 | |||
850 | 1 | 14.4 | 0.12 | ||
2 | 24 | 0.21 | |||
3 | 39 | 0.30 | |||
900 | 1 | 29 | 0.25 | ||
2 | 43 | 0.34 | |||
3 | 54 | 0.36 | 25 | ||
Порошковая сталь, (ЖГР) Cr11Ni6Cu15 |
800 | 1 | 15 | 0.25 | |
2 | 19 | 0.35 | |||
3 | 24 | 0.14 | |||
850 | 1 | 24 | 0.43 | ||
2 | 38 | 0.57 | |||
3 | 48 | 0.66 | |||
900 | 1 | 32 | 0.30 | ||
2 | 48 | 0.46 | |||
3 | 62.3 | 0.57 | 40 |
Результаты исследований позволяют сформулировать следующие выводы:
1. Покрытие имеет толщину до 50 мкм. Оно сплошное, равномерно покрывает поверхность, внешний вид деталей представлен на рис. 10. На рис. 11 представлена фотография шлифа борированной при 900°C в течение 3 ч детали из стали 20Х13. Покрытие также сплошное, равномерное. Покрыты все участки детали.
Рис. 11.
Металлографический шлиф борированого образца. 1 – фаза FeB, HV50 = 18 600 МПа; 2 – фаза Fe2B, HV50 = 12 700 МПа; 3 – переходная зона, HV50 = 2100 МПа; 4 – основа, HV50 = 4200 МПа.
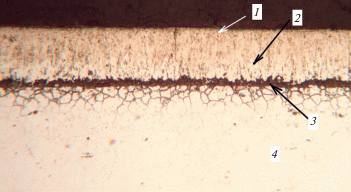
2. Покрытие двухфазное, имеет классическую для боридов железа игольчатую структуру. Микротвердость HV50 фаз FeB и Fe2B составляют 19 920 и 12 293 МПа соответственно;
3. Между иглами боридов и основой находится переходная зона толщиной менее 10 мкм, обедненная по хрому, но обогащенная по кремнию;
4. В покрытии присутствуют легирующие элементы (Cr, Si, Mn) в концентрациях меньших, чем в основе;
5. В материале основы хром распределен неравномерно, видны локальные малые области повышенной концентрации.
Общие результаты исследования приведены в табл. 4. Там же приведена величина уноса расплава с деталью. Эта величина замерялась при борировании деталей по разнице массы вынутой из расплава и отмытой детали. Расход бора на образование покрытия толщиной 40–80 мкм составил в среднем 0.6 г/дм2. Этой величине соответствуют значения увеличения массы детали, приведенные в табл. 4.
Анализ полученных результатов борирования позволяет рекомендовать оптимальные параметры процесса, представленные в табл. 5.
ЗАКЛЮЧЕНИЕ
1. Показана возможность борирования в расплаве CaCl2 представленных материалов.
2. Изучена кинетика образования боридных покрытий на деталях из порошковых сталей (ЖГР) Cr11Ni6Cu15, 20Х13 в расплаве, (мас. %): CaCl2 + 3–5B2O3 при температурах 800, 850 и 900°C и времени выдержки 1, 2 и 3 часа.
3. Проведены металлографические, рентгенофазовые, микрорентгеноспектральные анализы полученных покрытий. Определена толщина, микротвердость и фазовый состав всех полученных боридных покрытий.
4. Результаты по борированию предоставленных опытных деталей позволяют рекомендовать технологию нанесения покрытия для применения в промышленности.
Исследование выполнено при финансовой поддержке РФФИ в рамках научного проекта № 20-33-90279.
Список литературы
Крукович М.Г., Прусаков Б.А., Сизов И.Г. Пластичность борированных слоев. М.: Физматлит, 2010.
Kartal G., Eryilmaz O.L., Krumdick G., Erdemir A., Timur S. Kinetics of electrochemical boriding of low carbon steel // Applied Surface Science. 2011. 257. P. 6928–6934.
Ozdemir O., Omar M.A., Usta M., Zeytin S., Bindal C., Ucısık A.H. An investigation on boriding kinetics of AISI 316 stainless steel // Vacuum. 2009. № 83. P. 175–179.
Kartal G., Timur S., Arslan C. Effects of process current density and temperature on electrochemical boriding of steel in molten salts // J. Electron. Mater. 2005. № 34. P. 1538–1542.
Keddam M. Akinetic model for the borided layer by the pasteboriding process // Appl. Surf. Sci. 2004. 236. P. 451–455.
Keddam M., Ortiz-Dominguez M., Campos-Silva I., MartinesTrinidad J. A simple model for the growth kinetics of Fe2B iron boride on pure iron substrate // Appl. Surf. Sci. 2010. 256. P. 3128–3132.
Kartal G., Timur S., Eryilmaz O.L., Erdemir A. Influence of process duration on structure and chemistry of borided low carbon steel // Surf. Coat. Technol. 2010. 205. P. 1578–1583.
Kartal G., Timur S., Urgen M., Erdemir A. Electrochemical boriding of titanium for improved mechanical properties // Surf. Coat. Technol. 2010. 204. P. 3935–3939.
Keddam M. Computer simulation of monolayer growth kinetics of Fe2B phase during the paste-boriding process: influence of the paste thickness // Appl. Surf. Sci. 2006. 253. P. 757–761.
Yang H., Wu X., Yang Z., Pu Sh., Wang H. Enhanced boronizing kinetics of alloy steel assisted by surface mechanical attrition treatment // J. alloys and compounds. 2014. 500. P. 388–395.
Лахтин Ю.М. Основы металловедения: учеб. М.: Металлургия, 1988.
Ворошнин Л.Г., Лабунец В.Ф., Киндрачук М.В. Износостойкие боридные покрытия: справ. Пособие. Киев: Техника, 1989.
Бернштейн М.Л. Металловедение и термическая обработка стали. М.: Металлургия, 1991.
Гармаева И.А. Фазовый состав и кинетика формирования диффузионных слоев при борировании сталей: автореферат дис. … канд. техн. наук, 2008.
Ворошнин Л.Г. Борирование сталей и чугунов: справ. пособие, 1981.
Лившиц Б.Г. Металловедение и термическая оброботка: учеб. М.: Металлургия, 1989.
Солнцев Ю.П. Металловедение и технология металлов: учеб. М.: Металлургия, 1988.
Ткачев В.Н. Методы повышения долговечности деталей машин. Сельскохозяйственные машины: Учебное пособие для вузов. М.: Машиностроение, 1971.
Белый А.В., Карпенко Г.Д., Мышкин К.Н. Структура и методы формирования износостойких поверхностных слоев. М.: Машиностроение, 1991.
Гурьев А.М., Козлов Э.В., Игнатенко Л.Н., Попова Н.А. Физические основы термоциклического борирования. Барнаул: Изд-во АлтГТУ, 2000.
Ворошнин Л.Г. Борирование промышленных сталей и чугунов. Минск: Беларусь, 1981.
Ворошнин Л.Г., Алиев А.А. Борирование из паст. Астрахань. АГТУ. 2006.
Чернов Я.Б., Анфиногенов А.И., Шуров Н.И. Борирование сталей в ионных расплавах. Екатеринбург: УрО РАН, 2001.
Илющенко Н.Г., Беляева Г.И., Плотникова А.Ф. и др. Расплав для борирования. А.с. 533 671 (СССР). Заявл. 07.05.73; Опубл. в БИ 30.10.76. Бюл. № 40. МКИ С 23. С. 9/10.
Илющенко Н.Г., Беляева Г.И., Анфиногенов А.И., Чернов Я.Б. Способ химико-термической обработки металлов. А.с. 393373 (СССР). Заявл. 02.07.71; Опубл. в БИ 10.08.73. Бюл. № 33. МКИ С 23. С 9/10.
Чернов Я.Б., Анфиногенов А.И. Состав расплава для борирования. Патент 2 215 060. RU. Опубликовано 27.10.2003.
Чернов Я.Б., Анфиногенов А.И., Щемелев А.В., Прудников А.Н. и др. Расплав для жидкостного борирования стальных деталей. Патент 2 007 498 RU. Опубликовано 15.02.1994
Чернов Я.Б., Шуров Н.И., Каримов К.Р., Филатов Е.С. Способ электролизного борирования стальных изделий в расплаве, содержащем оксид бора. Патент RU № 247 837. Опубликовано 10.04.2013.
Чернов Я.Б., Филатов Е.С., Каримов К.Р., Чебыкин В.В. Гальвано-термодиффузионное борирование сталей // Труды Кольского научного центра. Химия и материаловедение. 2015. № 5. С. 300–303.
Чернов Я.Б., Филатов Е.С., Каримов К.Р. Термодиффузионное борирование в расплаве на основе хлорида кальция с добавкой оксида бора с применением реверсированного тока // Расплавы. 2016. № 4. С. 307–315.
Дополнительные материалы отсутствуют.