Теплоэнергетика, 2021, № 2, стр. 16-27
Экспериментальные исследования влияния вращения ротора и закрутки потока перед уплотнениями на расход утечки
С. С. Дмитриев a, *, Б. Н. Петрунин a, М. Э. А. Э. Ахмед a, b
a Национальный исследовательский университет “Московский энергетический институт”
111250 Москва, Красноказарменная ул., д. 14, Россия
b Университет Банха, инженерный факультет Шупра, кафедра машиностроения
Банха, Египет
* E-mail: dmitriyevss@mpei.ru
Поступила в редакцию 07.02.2020
После доработки 04.06.2020
Принята к публикации 20.06.2020
Аннотация
Представлены результаты экспериментальных исследований влияния вращения ротора на утечку через уплотнения различных типов. При сравнительном исследовании моделей с остановленным ротором и ротором, вращающимся с частотой 50 Гц, показано, что вращение ротора практически не влияет на расход утечки и в расчетах расхода утечки через концевые и диафрагменные уплотнения паровых турбин вращение можно не учитывать. Приведены результаты экспериментальных исследований влияния на расход утечки параметров течения, а именно изменения осевой и окружной составляющих вектора скорости во входном кольцевом канале перед единичным кольцевым дросселем. При этом в процессе экспериментов осевая и окружная составляющие скорости менялись независимо и изменение это было весьма значительным. Проведенные исследования показали, что изменение как осевой, так и окружной составляющей скорости практически не влияет на расход утечки. Анализ полученных результатов позволяет сделать вывод, что влияние параметров течения перед уплотнением на утечку столь незначительно, что пренебрежение им в разработанных ранее и действующих по сей день расчетных методиках по определению расхода утечки в уплотнениях паровых турбин вполне обосновано и оправдано. В настоящее время проводятся исследования, позволяющие расчетным путем анализировать структуру потока в различных местах проточных частей турбомашин, в том числе в уплотнениях турбины. При этом использование современных расчетных методов позволяет не только определить вихревую структуру в окрестности уплотнения, но и оценить расход утечки, потери от утечки и даже КПД ступени при различном конфигурировании камеры перед уплотнением. Тем не менее следует с осторожностью относиться к практическим рекомендациям технического плана по изменению конфигурации уплотнений, базирующимся только на результатах расчетов. Обоснованность таких рекомендаций должна быть в обязательном порядке подтверждена соответствующими экспериментальными исследованиями.
Исторически на кафедре паровых и газовых турбин НИУ МЭИ всегда уделялось большое внимание экспериментальным исследованиям течений в уплотнениях турбомашин. В целях улучшения расходных характеристик исследовались самые разные конструкции концевых, диафрагменных и надбандажных уплотнений для паровых турбин. При этом всегда считалось [1], что вращение ротора и закрутка потока перед уплотнением практически не оказывают влияния на расход утечки.
До настоящего времени при расчете утечек через лабиринтные уплотнения паровых турбин применяется простая, неоднократно проверенная и хорошо себя зарекомендовавшая формула А. Стодолы, которая учитывает отношение давлений до и после уплотнения, давление и удельный объем рабочего тела перед уплотнением, количество дросселей и площадь уплотнения. Зависимости коэффициента расхода через уплотнения с различными формой и геометрической конфигурацией гребней для практического использования формулы Стодолы были получены на кафедре паровых и газовых турбин МЭИ в опытах Б.М. Трояновского. Влиянием вращения ротора и значением закрутки потока при практических расчетах расхода утечки через уплотнения с использованием формулы Стодолы обычно пренебрегают.
В последнее время для расчетного исследования течений в уплотнениях широко применяются различные программные комплексы, основанные на решении системы уравнений Навье–Стокса [2, 3]. В российской периодической научно-технической литературе также появились публикации [4, 5], посвященные расчетным исследованиям структуры потока в пространстве перед уплотнением. В них, в частности, утверждается, что, помимо качественного исследования вихревой структуры потока, расчетные исследования позволяют дать практические рекомендации по специальному конфигурированию пространства перед уплотнением, что сделает возможным реально снизить утечки и повысить экономичность всей ступени благодаря изменению вихревой структуры потока. При современном развитии численных методов можно проводить самые разнообразные расчетные исследования. Вместе с тем следует с осторожностью относиться к практическим рекомендациям технического плана, базирующимся только на результатах расчетов. Обоснованность таких рекомендаций должна быть в обязательном порядке подтверждена экспериментальными исследованиями.
Появились и экспериментальные исследования, в описании которых приводятся данные о заметном влиянии частоты вращения ротора на расход утечки через уплотнение, на основании чего, например, в [6] делается вывод о необходимости учета вращения при расчете утечки.
Целью экспериментальных исследований, результаты которых приведены далее, является определение степени влияния вращения ротора и параметров течения перед уплотнением, а именно независимого изменения осевой и окружной составляющих вектора скорости потока перед уплотнением, на расход утечки.
ЭКСПЕРИМЕНТАЛЬНЫЕ ИССЛЕДОВАНИЯ ВЛИЯНИЯ ВРАЩЕНИЯ РОТОРА НА РАСХОДНЫЕ ХАРАКТЕРИСТИКИ УПЛОТНЕНИЙ
При проведении сравнительных измерений расхода утечки через одну и ту же модель уплотнения при остановленном и вращающемся роторе и при всех прочих равных условиях определяется отношение весьма близких значений этих величин, что требует тщательной оценки неопределенности полученного результата. Для этой серии экспериментов использовали модернизированную экспериментальную часть стенда “Динамическая модель уплотнения” (ДМУ), конструктивная схема которой, а также схема измерений расхода через уплотнения приведены на рис. 1. Все механические элементы дросселей и других конструкций экспериментальных стендов были изготовлены на Опытном заводе НИУ МЭИ в соответствии с технологиями, применяемыми на предприятиях общего машиностроения. Шероховатость поверхностей роторных и статорных частей моделей уплотнений Rz находится в диапазоне 40–80 мкм.
Рис. 1.
Экспериментальная модель для изучения влияния вращения на расходные характеристики уплотнений и схема измерений. 1 – электродвигатель; 2 – муфта; 3 – подшипниковый узел; 4 – муфта; 5 – кольцевая радиальная сопловая решетка; 6 – термометр; 7 – спрямляющая пластина (12 шт.); 8 – выходное сопло; 9 – зонд для измерения избыточного давления полного торможения; 10 – вал-проставка; 11 – роторная часть модели уплотнения; 12 – статорная часть модели уплотнения; 13 – корпус; 14 – фторопластовое уплотнение
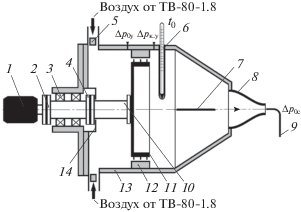
Вид и основные размеры четырех исследованных в работе моделей уплотнений представлены на рис. 2.
Рис. 2.
Модели уплотнений, использованные для исследования влияния вращения на расходные характеристики. I – уплотнение Келера; II – прямоточное уплотнение с двумя гребнями на роторе; III – прямоточное уплотнение с тремя волнообразными гребнями на роторе; IV – щелевое уплотнение
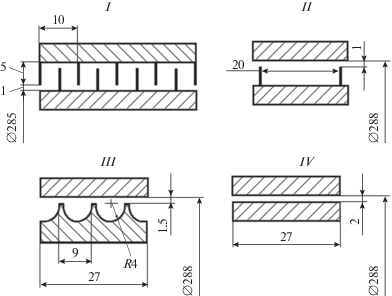
В корпусе 13 расположены роторная 11 и статорная 12 части исследуемого уплотнения. Роторная часть уплотнения приводится во вращение с помощью электродвигателя, который через муфту 2 соединен с валом подшипникового узла, соединенного, в свою очередь, через промежуточную муфту 4 с валом-проставкой 10 роторной части уплотнения (см. рис. 1).
Сжатый атмосферный воздух подается от турбовоздуходувки ТВ-80-1.8 с избыточным давлением 80 кПа в напорный трубопровод и через запорную задвижку поступает на экспериментальную установку. Пройдя через кольцевую радиальную сопловую решетку 5, воздух попадает непосредственно в камеру перед исследуемым уплотнением. Для предотвращения утечки из камеры устанавливается кольцевое фторопластовое уплотнение с нулевым зазором по отношению к фланцу вала-проставки. Воздух, пройдя через уплотнение, направляется на спрямляющее устройство, состоящее из двенадцати плоских пластин, установленных параллельно оси стенда (на рис. 1 показана одна пластина). Затем через суживающееся сопло 8 воздух выходит в атмосферу. Расход воздуха через уплотнение измеряли с помощью выходного сопла 8 по описанной далее схеме.
Сопло, спрофилированное по методу Витошинского, обеспечивает на выходе практически равномерное поле скорости потока. Тем не менее, следует учитывать влияние пограничного слоя в выходном сечении непосредственно у стенок. С этой целью было предварительно проведено траверсирование полей избыточного давления полного торможения по радиусу с помощью зонда 9, устанавливаемого в выходном сечении сопла. Измерения проводили водяным дифференциальным манометром с погрешностью до 20 Па. Избыточное давление для осредненного одномерного потока в выходном сечении сопла 8 определяли с учетом осевой симметрии потока по формуле
(1)
$\Delta p_{0}^{{{\text{оср}}}} = \frac{{\int\limits_0^{{{r}_{0}}} {\Delta {{p}_{{0r}}}2\pi r{\text{d}}r} }}{{\pi r_{0}^{2}}},$При сравнении полученного по формуле (1) результата с избыточным давлением полного торможения Δр0с, измеренным в выходном сечении на оси сопла зондом 9 (при r = 0), было установлено, что для безразмерных скоростей λ на выходе из сопла в диапазоне 0.3–0.8 выполняется соотношение
После этого для определения расхода с помощью сопла 8 в качестве избыточного давления полного торможения осредненного одномерного потока в выходном сечении сопла 8 использовали значение Δр0 = 0.996Δр0с.
Расход через сопло определяли по известной формуле
где ρ, с – плотность и скорость потока в выходном сечении сопла; Fc – площадь выходного сечения сопла 8.Плотность на срезе сопла находили с использованием уравнений адиабаты и состояния идеального газа при отношении давлений εс в сопле 8, определяемом по измеренному избыточному давлению полного торможения Δр0с в выходном сечении сопла, а также барометрическому давлению В в выходном сечении сопла и измеренной температуре полного торможения t0 перед соплом. Таким образом, плотность является функцией величин, измеренных в эксперименте, т.е. ρ = f1(Δр0с, В, t0).
Скорость осредненного одномерного потока c на срезе сопла вычисляли по формуле для одномерного потока идеальной сжимаемой жидкости по измеренным в эксперименте температуре t0 перед соплом 8 и отношению давлений εс в сопле. В итоге получили, что с также является функцией величин, измеренных в эксперименте, т.е. с = f2(Δр0с, В, t0).
Как показано на рис. 1, температуру полного торможения t0 измеряли перед соплом 8 ртутным термометром 6, имеющим погрешность до 1°С. Сам термометр помещали в специальную гильзу, закрепленную на корпусе стенда. Перед измерениями температуры в гильзу заливали машинное масло.
Корпус стенда 13 не был теплоизолирован, поэтому для корректного измерения температуры полного торможения эксперимент проводили следующим образом. Его начинали с подачи на стенд сжатого воздуха и установления требуемого аэродинамического режима. С помощью образцового манометра с классом точности 0.15 и пределом измерения 160 кПа на 400 делений измеряли избыточное давление Δр0у перед исследуемым уплотнением. Избыточное давление за уплотнением Δрк.у измеряли водяным дифференциальным манометром (погрешность до 20 Па) и при измеренном атмосферном давлении В определяли отношение давлений на уплотнении εу = (В + + Δрк.у)/(В + Δр0у). При этом значении εу и фиксированном положении запорной задвижки воздух прокачивали через стенд до тех пор, пока показания термометра не стабилизировались на одной и той же температуре в течение 10 мин. Полученное значение фиксировали. Одновременно проводили замер избыточного давления полного торможения на оси сопла Δр0с. После этого ротор приводили во вращение с частотой 50 Гц и снимали показания тех же параметров – t0 и Δр0с. Весь эксперимент с вращением занимал не более 2 мин. При этом окружная скорость вращения роторной части уплотнения составляла около 45 м/с. Число Рейнольдса для кольцевого уплотнения в соответствии с [7] рассчитывали по формуле
где δ – радиальный зазор в уплотнении (см. рис. 2); ν – табличный кинематический коэффициент вязкости воздуха при измеренной t0;– расходная составляющая скорости на выходе из уплотнения; G – расход воздуха через уплотнение, экспериментально определенный описанным выше способом; d – диаметр уплотнения (см. рис. 2).
Для всех приведенных исследований значения числа Рейнольдса находились в диапазоне (1.3–2.2) × 104, а отношение окружной скорости на периферии роторной части уплотнений к расходной скорости (u/срасх) было менее 0.5.
Далее, с учетом того что Fc = const при измерениях, проведенных для данного уплотнения как при вращающемся, так и при остановленном роторе, определяли отношение
Для оценки неопределенности искомой величины А в соответствии с [8] использовали известную формулу
которую с учетом вида функции А после дифференцирования можно записать следующим образом:
(2)
$\begin{gathered} \frac{{\Delta A}}{A} = \\ = \,\,{{\left[ {\frac{{{{\Delta }^{2}}\left( {{{\rho }_{{n = 50}}}} \right)}}{{\rho _{{n = 50}}^{2}}} + \frac{{{{\Delta }^{2}}\left( {{{c}_{{n = 50}}}} \right)}}{{c_{{n = 50}}^{2}}} + \frac{{{{\Delta }^{2}}\left( {{{\rho }_{{n = 0}}}} \right)}}{{\rho _{{n = 0}}^{2}}} + \frac{{{{\Delta }^{2}}\left( {{{c}_{{n = 0}}}} \right)}}{{c_{{n = 0}}^{2}}}} \right]}^{{{1 \mathord{\left/ {\vphantom {1 2}} \right. \kern-0em} 2}}}}. \\ \end{gathered} $Как уже упоминалось ранее, плотность и скорость потока определяли как результаты косвенных измерений, и для оценки неопределенностей величин ${{\Delta c} \mathord{\left/ {\vphantom {{\Delta c} c}} \right. \kern-0em} c}$ и ${{\Delta \rho } \mathord{\left/ {\vphantom {{\Delta \rho } \rho }} \right. \kern-0em} \rho }$ использовали стандартную процедуру логарифмирования и дальнейшего дифференцирования зависимостей ρ = f1(Δр0с, В, t0) и с = f2(Δр0с, В, t0) для расчета неопределенности при косвенных измерениях.
В рассматриваемом случае плотность, давление и температура жестко связаны уравнениями адиабаты и состояния. Поэтому их неопределенности можно считать взаимозависимыми. В этом случае после логарифмирования и последующего дифференцирования соответствующих уравнений следует сохранить знаки дифференциалов при суммировании составляющих при переходе к конечным приращениям [9].
Неопределенности при измерении барометрического давления и избыточного давления полного торможения не взаимосвязаны, поэтому оценку неопределенности при вычислении ${{\Delta {{\varepsilon }_{{\text{с}}}}} \mathord{\left/ {\vphantom {{\Delta {{\varepsilon }_{{\text{с}}}}} {{{\varepsilon }_{{\text{с}}}}}}} \right. \kern-0em} {{{\varepsilon }_{{\text{с}}}}}}$ проводили по формуле
(3)
$\frac{{\Delta {{\varepsilon }_{{\text{с}}}}}}{{{{\varepsilon }_{{\text{с}}}}}} = \frac{{\Delta B}}{B} + \frac{{\Delta B + \Delta \left( {\Delta {{p}_{0}}} \right)}}{{B + \Delta {{p}_{0}}}}.$С учетом (3) для оценки неопределенности ${{\Delta \rho } \mathord{\left/ {\vphantom {{\Delta \rho } \rho }} \right. \kern-0em} \rho }$ была получена формула
(4)
$\begin{gathered} \frac{{\Delta \rho }}{\rho } = \frac{{\Delta B + \Delta \left( {\Delta {{p}_{0}}} \right)}}{{B + \Delta {{p}_{0}}}} - \frac{{\Delta {{T}_{0}}}}{{{{T}_{0}}}} + \\ + \,\,\frac{1}{k}\left[ {\frac{{\Delta B}}{B} + \frac{{\Delta B + \Delta \left( {\Delta {{p}_{0}}} \right)}}{{B + \Delta {{p}_{0}}}}} \right], \\ \end{gathered} $Формула для определения скорости одномерного потока сжимаемой жидкости, использованная при вычислении скорости потока на выходе из сопла 8, есть, по сути, преобразованное уравнение движения осредненного одномерного потока. Поэтому температура полного торможения T0, от которой зависит критическая скорость потока, и отношение давлений ${{\varepsilon }_{{\text{с}}}}$ в сопле также жестко связаны. Вследствие этого их неопределенности также можно считать взаимосвязанными и сохранять знаки после логарифмирования и дифференцирования соответствующего уравнения при переходе к конечным приращениям. В результате для оценки неопределенности ${{\Delta c} \mathord{\left/ {\vphantom {{\Delta c} c}} \right. \kern-0em} c}$ была получена формула
(5)
$\begin{gathered} \frac{{\Delta с}}{с} = \frac{1}{2}\frac{{\Delta {{T}_{0}}}}{{{{T}_{0}}}} - \\ - \,\,\frac{1}{2}\frac{1}{{1 - \varepsilon _{{\text{c}}}^{{\frac{{k - 1}}{k}}}}}\frac{{k - 1}}{k}\varepsilon _{{\text{c}}}^{{\frac{{k - 1}}{k}}}\left[ {\frac{{\Delta B}}{B} + \frac{{\Delta B + \Delta \left( {\Delta {{p}_{0}}} \right)}}{{B + \Delta {{p}_{0}}}}} \right]. \\ \end{gathered} $В формулах (3)–(5) значения неопределенностей ΔВ при измерении барометрического давления, Δ(Δр0) при измерении избыточного давления полного торможения на выходе из сопла и Δt0 при измерении температуры полного торможения принимаются соответственно равными 136 Па, 20 Па и 1°С.
Зная измеренные значения В, Δр0 и t0, а также рассчитав плотность ρ и скорость с на срезе сопла для каждого исследования с вращающимся и остановленным ротором, можно найти А и с помощью (4) и (5) по формуле (2) вычислить неопределенность ${{\Delta A} \mathord{\left/ {\vphantom {{\Delta A} A}} \right. \kern-0em} A}.$ Результаты проведенных измерений и расчетов сведены в табл. 1. Из нее видно, что расход через все исследованные модели уплотнений (см. рис. 2) при вращающемся роторе несколько меньше, чем при неподвижном. Но разница эта пренебрежимо мала.
Таблица 1.
Влияние вращения на расход через исследованные модели уплотнений
Параметр | Модель | |||
---|---|---|---|---|
I | II | III | IV | |
εу | 0.647 | 0.786 | 0.891 | 0.973 |
$\frac{{\Delta A}}{A}$ | 0.015 | 0.008 | 0.008 | 0.008 |
$\frac{{{{G}_{{n = 50}}}}}{{{{G}_{{n = 0}}}}} = A$ | 0.986 ± 0.015 | 0.986 ± 0.008 | 0.992 ± 0.005 | 0.992 ± 0.005 |
Следует, однако, отметить, что полученный результат справедлив только для частот вращения, реально используемых в энергетических турбомашинах. Известны работы, в которых отмечается весьма заметное уменьшение расхода через уплотнение с ростом частоты вращения. В частности, в [10] экспериментально установлено, что с ростом частоты вращения от 0 до 100 Гц расход утечки через сверхмалый радиальный зазор 0.12 мм в сотовом уплотнении уменьшается на 4.8%, в прямоточном лабиринтном уплотнении с тем же радиальным зазором – на 2%. При очень больших частотах вращения фиксируется еще более значительное снижение расхода утечки. Так, в [11] показано, что при увеличении частоты вращения от 300 до 1300 Гц расход утечки снижается на 14%. Однако такие частоты вращения в энергетических машинах, как известно, не используются.
Таким образом, можно констатировать, что обнаруженное авторами при проведении экспериментов влияние вращения ротора на значение утечки столь мало, что его можно не учитывать в практических расчетах расхода утечки через концевые и диафрагменные уплотнения всех цилиндров паровых турбин со стандартной частотой вращения 50 Гц.
ЭКСПЕРИМЕНТАЛЬНЫЕ ИССЛЕДОВАНИЯ ВЛИЯНИЯ ПРОЦЕССА ТЕЧЕНИЯ ПЕРЕД ЕДИНИЧНЫМ ДРОССЕЛЕМ НА РАСХОДНЫЕ ХАРАКТЕРИСТИКИ
Эта часть работы выполнялась на аэродинамической трубе открытого типа ВАТ-1 и на экспериментальном стенде “Динамическая модель уплотнения”. В качестве рабочей среды также использовался сжатый воздух, поступающий от турбовоздуходувки ТВ-80-1.8.
Конструктивная схема исследований на аэродинамической трубе ВАТ-1 представлена на рис. 3. Роторная часть уплотнения кольцевого дросселя зафиксирована и соединена с центральной базой аэродинамической трубы, статорная часть установлена в обечайке, жестко соединенной с наружным фланцем успокоительного бака-ресивера. Воздух из ресивера подается на направляющую решетку пластин и затем, получив заданную ею закрутку, поступает в пространство перед кольцевым единичным дросселем.
Рис. 3.
Рабочая часть экспериментальной модели, установленной в аэродинамической трубе ВАТ-1. 1 – роторная часть уплотнения; 2 – статорная часть уплотнения; 3 – обечайка; 4 – направляющая решетка пластин
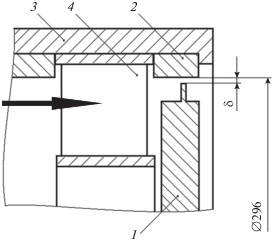
В этой части работы использовались кольцевые дроссели с радиальным зазором 1 и 5 мм. Толщина плоского гребня составляла 1 мм. В экспериментах были задействованы три съемные направляющие решетки, в каждой из которых пластины установлены под определенным углом α к плоскости, перпендикулярной центральной оси кольцевого дросселя: α =50 , 25 и 14°.
Расход воздуха G через единичный дроссель измеряли в подводящем тракте стенда ВАТ-1 с помощью стандартного суживающегося расходомерного сопла с диаметром выходного сечения 50.25 мм. Выхлоп производился в атмосферу. Расход определяли по формуле [12]
Избыточное давление перед мерным соплом Δр0с измеряли с помощью образцового манометра с классом точности 0.15 и пределом измерения 160 кПа на 400 делений. Одновременно термометром перед мерным соплом измеряли температуру полного торможения t0. Термометр помещали в стальную гильзу и устанавливали на расстоянии 1 м от сопла, в гильзу заливали машинное масло. Перепад давлений на сопле Δрс измеряли водяным дифференциальным манометром с погрешностью до 20 Па и при измеренном ртутным барометром с погрешностью до 136 Па атмосферном давлении В определяли отношение давлений на мерном сопле
Плотность ρ на выходе из мерного сопла рассчитывали по уравнению состояния по измеренным величинам
Для оценки неопределенности определения расхода также использовали формулу из работы [12]
При оценке неопределенности принимали Δ(Δрс) = 20 Па, а неопределенность при расчете плотности вычисляли описанным в первой части данной статьи способом. При значении расхода 0.5 и 0.1 кг/с неопределенность ΔG/G при расчете расхода составляла 0.5 и 0.6% соответственно.
Вообще говоря, в рассматриваемой конструктивной схеме исследований, представленной на рис. 3, утечка через дроссель – это лишь часть потока, поступающего в камеру перед дросселем. В нижней части решетки и в камере перед дросселем поток совершает сложное трехмерное вихревое движение, подобное движению в камере перед надбандажным уплотнением в реальной турбинной ступени. Характеристики этого движения и его влияние на исследуемое течение через дроссель практически невозможно оценить экспериментально. В связи с этим возникает проблема определения истинного отношения давлений на дроссель. За дросселем – атмосферное давление, измеряемое ртутным барометром. Истинное давление перед дросселем в условиях закрученного потока нельзя измерить с помощью обычного дренажа. Поэтому предварительно были проведены продувки с использованием всех трех направляющих решеток без дросселя и получены зависимости
где εр = [(B/(B + Δpp)] – отношение давлений на решетке; Gр – расход при установленной направляющей решетке; B – атмосферное давление; Δpp – измеренное избыточное давление в ресивере при данном Gр и установленной направляющей решетке.После этого были получены зависимости
где εр.д = B/(B + Δpp.д) – отношение давлений при последовательно установленных направляющей решетки и дросселе; Δpp.д – измеренное избыточное давление в ресивере при данном расходе Gр.д, измеренном при последовательно установленных направляющей решетки и дросселе. При этом отношение давлений, очевидно, можно представить в виде(6)
${{\varepsilon }_{{{\text{р}}{\text{.д}}}}} = \frac{B}{{B + \Delta {{p}_{{\text{д}}}}}}\frac{{B + \Delta {{p}_{{\text{д}}}}}}{{B + \Delta {{p}_{{{\text{р}}{\text{.д}}}}}}} = {{\varepsilon }_{{{\text{гр}}}}}{{\varepsilon }_{{\text{р}}}},$Если Gр.д = Gр, то при известных отношениях давлений εр.д и εр в соответствии с (6) легко определить εгр для данного расхода.
Результаты измерений представлены в виде G = f(εгр) на рис. 4. Здесь εгр – отношение давлений на дроссель, а Gр.д – расход через последовательно установленные направляющую решетку и дроссель. На обоих графиках (для δ = 1 и 5 мм) экспериментальные точки для чисто осевого течения (без закрутки потока) соединены линией.
Рис. 4.
Зависимость расхода через кольцевой дроссель от отношения давлений εгр при δ = 1 мм (а) и δ = = 5 мм (б). 1 – без закрутки (осевое течение); с закруткой при установочном угле пластин α: 2 – 50°; 3 – 25°; 4 – 14°
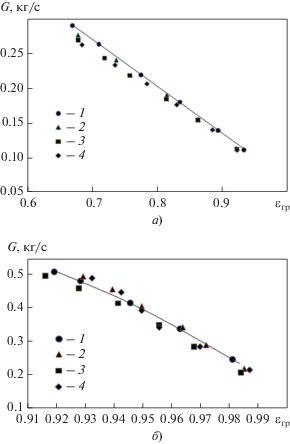
Как видно из рис. 4, а, при δ = 1 мм с уменьшением угла α, т.е. с ростом закрутки потока, при одном и том же значении εгр расход уменьшается незначительно. При максимальной закрутке потока перед уплотнением, соответствующей углу решетки α = 14°, это уменьшение составляет 5–6%. Для δ = 5 мм выявить какие-либо аналогичные закономерности оказалось невозможно. Как видно из рис. 4, б, экспериментальные точки для течения с закруткой группируются вблизи кривой для течения без закрутки, располагаясь и выше нее, и ниже.
В следующей части экспериментальной работы исследовали колебание расхода через единичный кольцевой дроссель при независимом изменении осевой и окружной составляющих скорости потока, поступающего в канал перед дросселем. На рис. 5 представлена конструктивная схема рабочей части для этих исследований, проведенных на стенде ДМУ. Единичный дроссель состоит из установленной в корпусе стенда сменной статорной части 4 и роторной части 8, которая выполнена неподвижной и соединена с корпусом стенда с помощью четырех установочных стержней 10. Сменные статорные части 4 позволяют выполнять радиальные зазоры δ, равные 1.5, 2.5, 3.5 и 5.5 мм. Толщина плоского гребня составляла 1 мм. Воздух от воздуходувки ТВ-42-1.4 с избыточным давлением 40 кПа поступал во входной кольцевой канал 1 (поток А) и двигался в осевом направлении. На выходе из входного кольцевого канала 1 предусмотрена возможность размещать направляющую кольцевую решетку пластин 2 для закрутки потока. Для максимальной закрутки потока на выходе из входного кольцевого канала использовали решетку пластин, расположенных под углом 14° к плоскости, перпендикулярной центральной оси.
Рис. 5.
Рабочая часть стенда “Динамическая модель уплотнения”. 1 – входной кольцевой канал; 2 – направляющая решетка пластин; 3 – комбинированный цилиндрический трехточечный зонд (приемник) полного давления и угломер; 4 – статорная часть уплотнения; 5 –термометр; 6 – зонд полного напора; 7 – сопло; 8 – роторная часть уплотнения; 9 – спрямляющая пластина; 10 – установочный стержень; 11 – внутреннее кольцо; 12 – кольцевой канал перед дросселем; 13 – осевой болт; 14 – шибер
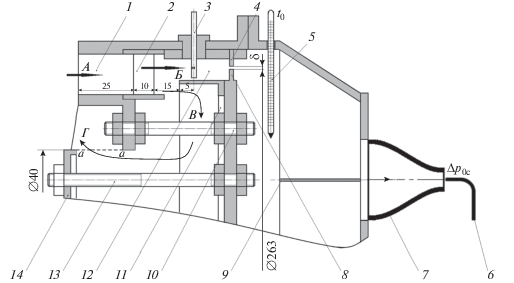
На выходе из канала 1 от основного потока А отделяется поток Б, поступающий в кольцевой канал 12 перед дросселем, образованный внешним корпусом и внутренним кольцом 11 (см. рис. 5). Здесь с помощью комбинированного трехточечного цилиндрического приемника 3 измеряются скорость и угол натекания потока перед дросселем. Трехточечный цилиндрический приемник наружным диаметром 2 мм для измерения значения и направления скорости потока был спроектирован, изготовлен и оттарирован в соответствии с рекомендациями [13]. В этой части работы были использованы то же выходное сопло и та же схема измерения расхода, которые применялись для определения расхода через модели уплотнения, показанные на рис. 2. После дросселя поток Б проходит спрямляющее устройство, состоящее из двенадцати плоских пластин 9, установленных параллельно оси стенда (на рис. 5 показана только одна пластина), и далее, через специально суживающееся сопло 7, спрофилированное по методу Витошинского, – в атмосферу. Измерение расхода потока Б производили по показаниям зонда полного давления 6, установленного на выходе из сопла 7.
Оценку неопределенностей выполняли по методике, которая была применена для измерения расхода при вращающемся и остановленном роторе через уплотнения, показанные на рис. 2, и изложена ранее.
В процессе эксперимента при фиксированном положении входной напорной задвижки перед стендом ДМУ открывали шибер 14. При этом через шибер проходил поток Г, вызывавший увеличение суммарного расхода через стенд ДМУ. Соответственно возрастала и осевая скорость в потоке А. Схема такого течения показана на рис. 5. С помощью внутреннего кольца 11, образующего совместно с внешним корпусом кольцевой канал 12 перед дросселем, отсекалась часть потока А (поток В), разворачивалась в центральной части стенда и удалялась через центральное отверстие во внешнем корпусе (поток Г ). Расход этого потока регулировался шибером 14, который можно устанавливать в различное положение вдоль осевого болта 13 и который при этом будет изменять выходную площадь а–а потока Г. Максимальная выходная площадь для потока Г определялась площадью самого шибера 14, диаметр которого был равен 40 мм за вычетом площади поперечного сечения осевого болта (М12), вдоль которого он перемещался, и составляла 1.15 × 10–3 м2. Выходная площадь дросселя для потока Б при наименьшем значении δ, равном 1.5 мм, составляла 1.24 × 10–3 м2 и, соответственно, 4.5 × 10–3 м2 при δ = 5.5 мм. Таким образом, выходная площадь дросселя для потока Б во всех экспериментах была больше, чем для потока Г.
При этом поток В должен повернуть на 180° для выхода через сечение а–а. В то же время путь, который проходит поток А после выхода из входного кольцевого канала 1 до входа в кольцевой канал 12 перед дросселем, весьма мал (см. размеры на рис. 5). Поэтому поток Б должен иметь скорость, почти равную скорости потока А. Это подтверждается проведенными по высоте канала измерениями скорости потока Б трехточечным цилиндрическим приемником 3 при различных степенях открытия шибера 14. С открытием шибера 14 скорость потока Б только возрастала.
Площадь поперечного (перпендикулярного оси) сечения кольцевого канала перед дросселем всего в 8–10 раз превышала площадь щели самого дросселя. Это позволило обеспечить по всей высоте входного кольцевого канала перед приемником 3 либо чисто осевое течение, при отсутствии направляющей решетки 2, либо закрученное по всей высоте канала течение при ее установке, что также было подтверждено измерениями скорости и направления потока по высоте канала с помощью трехточечного цилиндрического приемника 3.
Таким образом, когда на выходе из входного кольцевого канала 1 отсутствовала направляющая решетка 2, при открытии шибера 14 вместе со скоростью потока А возрастала и осевая скорость потока Б в кольцевом канале перед дросселем.
При установке на выходе из канала 1 направляющей решетки 2 с фиксированным углом закрутки рост скорости осевого потока А, определяемый открытием шибера 14, однозначно приводил к росту окружной составляющей скорости на выходе из решетки 2 и, соответственно, росту окружной составляющей скорости потока Б в кольцевом канале перед дросселем.
Естественно, при открытии шибера менялись все давления по тракту. Очевидно, что для сравнения следовало выбирать режимы с открытым и закрытым шибером при одном и том же отношении давлений на дросселе εд. Однако обычный метод определения давления перед дросселем путем измерения по дренажу в данном случае не подходит, особенно для закрученного течения, поэтому для определения εд использовали следующий метод.
В соответствии с [1] расход через дроссель можно представить в виде
где μmax – отношение критического расхода через щель к критическому расходу через сопло (для воздуха и абсолютно острой кромки дросселя μmax = 0.85); q – относительный расход через дроссель, равный отношению расхода через дроссель к критическому расходу через дроссель; G*c – критический расход через сопло с той же площадью выхода, что и у щели дросселя.Относительный расход q в соответствии с [1] определяли по формуле
(8)
$q = \sqrt {\frac{{1 - {{\varepsilon }^{2}}}}{{1 - {{\varepsilon }_{{{\text{2кр}}}}}}} - \frac{{{{\varepsilon }_{{{\text{2кр}}}}}{{{\left( {1 - \varepsilon } \right)}}^{2}}}}{{1 - {{\varepsilon }_{{{\text{2кр}}}}}}}} ,$предложенной для уплотнения с одним гребнем Г.С. Самойловичем, где ε2кр = 0.037, а ε = εд – искомое отношение давлений на единичном дросселе.
Критический расход через виртуальное сопло с той же площадью выхода, что и у щели дросселя, G*c вычисляется по известной формуле
где ${{F}_{{{\text{др}}}}} = \pi d{\delta ;}$ d – диаметр кольцевого дросселя (уплотнения); δ – радиальный зазор (см. рис. 5).Давление полного торможения р0 в формуле (9) определяли по показанию дренажа (фактически это давление в ресивере перед исследованной моделью) во входном кольцевом канале 1 (см. рис. 5), а температуру полного торможения t0 измеряли перед стандартным расходомерным соплом, установленным в подводящем к стенду трубопроводе, как это было реализовано при исследованиях на стенде ВАТ-1 и описано ранее.
Вторым членом в выражении (8) можно пренебречь ввиду малости ε2кр. Тогда формула (7) примет вид
(10)
$G = {{{\mu }}_{{\max }}}{{F}_{{{\text{др}}}}}\frac{{0.0404{{p}_{0}}}}{{\sqrt {{{T}_{0}}} }}\sqrt {\frac{{1 - {{\varepsilon }^{2}}}}{{1 - {{\varepsilon }_{{{\text{2кр}}}}}}}} .$С учетом связи удельного объема v и температуры Т через уравнение состояния идеального газа после некоторых преобразований выражение (10) примет вид формулы Стодолы
(11)
$G = {{{\mu }}_{{\text{у}}}}{{F}_{{{\text{др}}}}}\sqrt {\frac{{{{p}_{0}}}}{{{{v}_{0}}}}} \sqrt {1 - {{\varepsilon }^{2}}} ,$Для абсолютно острой кромки ${{{\mu }}_{{\text{у}}}}$ ≈ 0.6, что хорошо согласуется с теорией [1], но для реальных течений коэффициент расхода ${{{\mu }}_{{\text{у}}}}$ зависит от отношения толщины гребня и зазора между гребнем и стенкой и обычно определяется из эксперимента. Для определения ${{{\mu }}_{{\text{у}}}}$ использовали экспериментальные данные Б.М. Трояновского, опубликованные в [1]. При радиальных зазорах δ, равных 1.5, 2.5, 3.5 и 5.5 мм, и толщине плоского гребня 1 мм μу в формуле (11) соответственно примет значения 0.715, 0.685, 0.675 и 0.675.
Таким образом, зная измеренный по выходному соплу 7 расход G через дроссель для различных режимов, разных значений радиального зазора δ, с открытым и закрытым шибером 14, рассчитывали отношение давлений на дросселе и зависимости G = f(εд) по формулам (7)–(11).
Результаты экспериментальных исследований при изменении только осевой составляющей скорости в кольцевом канале перед дросселем без установки направляющей решетки 2 представлены в табл. 2. Здесь саз, сао – осевая составляющая скорости, измеренная в кольцевом канале 12 перед дросселем с помощью трехточечного цилиндрического приемника 3 с закрытым и открытым шибером 14, а Gш.о/Gш.з – отношение расходов через дроссель при открытом и закрытом шибере соответственно.
Таблица 2.
Влияние изменения осевой составляющей скорости на расход через единичный дроссель
Параметр | δ, мм | |||
---|---|---|---|---|
1.5 | 2.5 | 3.5 | 5.5 | |
εд | 0.9759 | 0.9866 | 0.9946 | 0.9972 |
саз, м/с | 27.3 | 24.6 | 25.4 | 23.2 |
сао, м/с | 47.2 | 50.8 | 48.3 | 50.5 |
Gш.з/Gш.о | 0.999 ± 0.015 | 0.998 ± 0.013 | 0.993 ± 0.003 | 0.987 ± 0.002 |
Результаты, приведенные в табл. 2, наглядно отражают степень влияния изменения осевой составляющей вектора скорости cа на расход утечки через дроссель. Как видно, с ростом осевой составляющей скорости перед дросселем в 1.5–2.0 раза расход через дроссель при δ, равном 1.5, 2.5 и 3.5 мм, оставался, тем не менее, практически неизменным или очень слабо возрастал. Только при δ = 5.5 мм, можно с некоторой долей вероятности утверждать об увеличении расхода.
Данные табл. 3 иллюстрируют влияние, главным образом, изменения окружной составляющей вектора входной скорости перед дросселем сu, поскольку использование направляющей решетки 2 с установочными углами пластин α = 14° позволяло во всех исследованных режимах обеспечить соотношение во входном канале перед дросселем сu/cа ≈ 0.92–0.96, т.е. зонд 3 практически измерял окружную составляющую вектора скорости перед дросселем. В табл. 3 сuз, сuо – окружные составляющие скорости, измеренные при установке направляющей решетки 2 во входном кольцевом канале перед дросселем с помощью трехточечного цилиндрического приемника с закрытым и открытым шибером 14.
Таблица 3.
Влияние изменения окружной составляющей скорости на расход через единичный дроссель
Параметр | δ, мм | |||
---|---|---|---|---|
1.5 | 2.5 | 3.5 | 5.5 | |
εд | 0.9711 | 0.9873 | 0.9920 | 0.9973 |
сuз, м/с | 19.3 | 17.2 | 20.1 | 26.4 |
сuо, м/с | 30.6 | 32.4 | 33.5 | 50.6 |
Gш.о/Gш.з | 0.999 ± 0.015 | 0.999 ± 0.015 | 0.992 ± 0.008 | 0.993 ± 0.005 |
Представленные в табл. 3 результаты свидетельствуют о практическом отсутствии влияния изменений окружной составляющей скорости входящего потока на расход через дроссель. Несмотря на то что окружная скорость увеличивалась значительно, в 1.6–1.9 раза, для всех исследованных зазоров изменение расхода через дроссель находилось в пределах погрешности измерений.
На рис. 6 представлены зависимости расхода через дроссель G = f(εд) при радиальных зазорах 1.5 и 5.5 мм. Зависимости получены уже описанным ранее способом для пяти фиксированных положений запорно-регулирующей задвижки на входе в рабочую часть стенда ДМУ (см. рис. 5). Сначала входную задвижку полностью открывали и проводили эксперименты по описанной схеме как для чисто осевого течения во входном канале перед дросселем (без направляющей решетки пластин), так и с установленной решеткой 2. Точно так же при таком положении задвижки при проведении этих экспериментов измеряли расход на выходе из установки с закрытым и открытым шибером 14. Всего было произведено пять измерений, каждый раз со все большим закрытием входной задвижки. При этом уменьшалось как давление во входном кольцевом канале 1, так и расход G через дроссель, который измеряли после выходного сопла 7.
Рис. 6.
Зависимости расхода через дроссель при различных условиях входа и положениях запорной задвижки перед стендом при δ = 1.5 мм (а) и δ = 5.5 мм (б) для чисто осевого течения перед дросселем (1, 2) и течения с закруткой перед дросселем (3, 4) с закрытым (1, 3) и открытым (2, 4) шибером
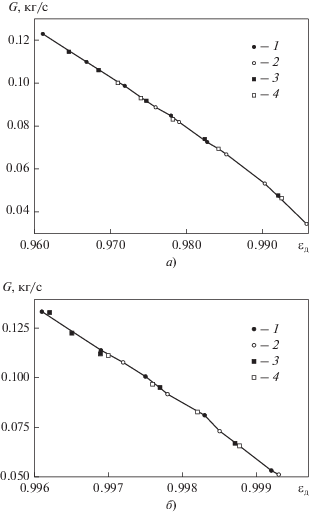
Точно так же, с использованием измеренного расхода G и зависимостей (7)–(11), в каждом эксперименте определяли отношение давлений на дросселе εд и полученные значения наносили на графики (см. рис. 6). Очевидно, что и для δ = = 1.5 мм, и для δ = 5.5 мм все экспериментальные точки – как для течения с закруткой, так и для чисто осевого течения перед дросселем, с закрытым и открытым шибером – с минимальным разбросом ложатся на одну кривую. Таким образом, можно с уверенностью утверждать, что параметры течения перед дросселем практически не влияют на расход утечки и он определяется только отношением давлений εд.
В целом анализ полученных результатов по влиянию изменения осевой и окружной составляющих скоростей потока в канале перед дросселем на расход утечки приводит к заключению, что влияние течения перед дросселем на утечку столь незначительно, что пренебрежение им в разработанных ранее и действующих по сей день расчетных методиках по определению расхода вполне обосновано и оправдано.
В настоящее время в процессе расчетных исследований поднимаются некоторые новые проблемные вопросы, в частности исследуется утечка через периферийные уплотнения различных конфигураций. Однако, как показано в уже упоминавшейся работе [11], результат расчета расхода утечки через одну и ту же модель уплотнения с одними и теми же размерами, но с применением различных моделей турбулентности дает расхождение примерно 10%, а увеличение числа ячеек в расчетной схеме от 0.5 до 2.5 млн – 16.5%. Кроме того, расхождение значений, представленных в [11], с данными по тому же уплотнению, но приведенными в [14] и рассчитанными в соответствии с широко распространенной за рубежом моделью Эгли, составляет 50%. Таким образом, результаты расчетных исследований в обязательном порядке подлежат проверке в эксперименте.
ВЫВОДЫ
1. Проведенные экспериментальные исследования показали, что в практических расчетах расхода утечки через концевые и диафрагменные уплотнения всех цилиндров паровых турбин со стандартной частотой вращения 50 Гц влияние вращения ротора можно не учитывать.
2. Для оценки влияния вращения на расход утечки через периферийные уплотнения турбомашин необходимо провести дополнительные экспериментальные исследования при реальных окружных скоростях, характерных для периферии турбинной ступени.
3. Экспериментально показано, что независимое изменение в широких пределах осевой и окружной составляющих скорости потока перед единичным дросселем практически не влияет на расход утечки через него, т.е. расход через дроссель зависит только от отношения давлений на дросселе.
Список литературы
Дейч М.Е., Самойлович Г.С. Основы аэродинамики осевых турбомашин. М.: Машгиз, 1959.
Influence of a honeycomb facing on the flow through a stepped labyrinth seal / V. Schramm, K. Willenborg, S. Kim, S. Wittig // J. Eng. Gas Turbines Power. 2002. V. 124. Is. 1. (Trans. of ASME). P. 140–146. https://doi.org/10.1115/1.1403460
Kim T.S., Cha K.S. Comparative analysis of the influence of labyrinth seal configuration on leakage behavior // J. Mech. Sci. Technol. 2009. V. 23. P. 2830–2838. https://doi.org/10.1007/s12206-009-0733-5
Афанасьев И.В., Грановский А.В. Расчетное исследование влияния формы бандажной полки на эффективность ступени газовой турбины // Теплоэнергетика. 2018. № 3. С. 15–22. https://doi.org/10.1134/S0040363618030013
Особенности вихревой структуры потока в окрестности бандажа с одним гребнем / И.В. Афанасьев, А.В. Грановский, Е.Ю. Марчуков, И.А. Манаев, А.Е. Шунин // Теплоэнергетика. 2019. № 7. С. 43–50. https://doi.org/10.1134/S0040363619070014
Бондаренко Г.А., Бага В.Н. Исследование течения в лабиринтном уплотнении: сб. науч. тр. Темат. вып.: Энергетические и теплотехнические процессы и оборудование // Вiсник НТУ XIII. 2015. № 15 (1124). С. 23–31. Харьков: НТУ ХПИ, 2015.
Impact of rotational speed on the discharge characteristic of stepped labirinhth seals / R. Paolillo, S. Moore, D. Cloud, J.A. Glahn // Proc. of GT2007. ASME Turbo Expo 2007: Power for Land, Sea and Air. Montreal, Canada, 14–17 May 2007. GT2007-28248. P. 1–8.
Горлач В.В., Егоров В.Л., Иванов Н.А. Обработка, представление, интерпретация результатов измерений: учеб. пособие / под ред. В.В. Горлача. Омск: Изд-во СибАДИ, 2006.
Новицкий П.В., Зорграф И.А. Оценка погрешностей результатов измерений. 2-е изд., перераб. и доп. Л.: Энергоатомиздат, 1991.
Experimental investigation of the sealing performance of honeycomb seals / H. Li-dong, Y. Xin, J. Yan, Z. Zhen-you // Chin. J. Aeronaut. 2001. V. 14. Is. 1. P. 13–17.
Investigation on rotor-labyrinth seal system with variable rotating speed / X. Jia, H. Zhang, Q. Zheng, S. Fan, Z. Tian // Int. J. Turbo Jet Eng. Nov. 2016. V. 36. Is. 1. P. 1–9. https://doi.org/10.1515/tjj-2016-0066
Преображенский В.П. Теплотехнические измерения и приборы: учеб. для вузов. 3-е изд., перераб. М.: Энергия, 1978.
Петунин А.Н. Методы и техника измерений параметров газового потока. М.: Машиностроение, 1972.
Egli A. Leakage of steam through labyrinth seals // Trans. of ASME. 1935. V. 57. Is. 3. P. 115–122.
Дополнительные материалы отсутствуют.
Инструменты
Теплоэнергетика