Теплоэнергетика, 2021, № 2, стр. 41-60
Обзор результатов зарубежных и отечественных исследований в области использования технологии сжигания твердых топлив в циркулирующем кипящем слое
Г. А. Рябов *
ОАО “Всероссийский теплотехнический институт”
115280 Москва, Автозаводская ул., д. 14, Россия
* E-mail: GARyabov@vti.ru
Поступила в редакцию 06.04.2020
После доработки 30.05.2020
Принята к публикации 24.06.2020
Аннотация
Представлен анализ современного состояния и развития технологии сжигания топлив в циркулирующем кипящем слое (ЦКС). Приведены основные отличительные черты технологии сжигания твердых топлив в ЦКС и этапы ее развития в мире. Показаны преимущества и недостатки технологии ЦКС по сравнению с традиционным факельным сжиганием. Представлены примеры наиболее крупных энергетических установок с котлами с ЦКС. Проанализированы последние исследования особенностей конструкции котлов с ЦКС для повышенных параметров пара и обеспечения наиболее высокой эффективности энергоблоков с котлами с ЦКС. Рассмотрены главные направления научных разработок в этой области (гидродинамика, сепарация, состав слоя и др.). Показано, что эффективность улавливания твердых частиц является основополагающим фактором увеличения их расхода и удержания мелких кальцинированных частиц в циркулирующем материале. Высокая концентрация в надслоевом пространстве топки приводит к повышению коэффициента теплопередачи и обеспечивает равномерное распределение температур в топке, требуемую степень реагирования частиц известняка с SO2 для наиболее эффективного связывания серы, а также более полное выгорание топлива (максимально возможное время пребывания частиц топлива в топке). Дан анализ исследований китайских ученых, их практических разработок и внедрения энергосберегающей технологии с малой массой частиц в слое. Представлены результаты последних исследований по минимизации как традиционных выбросов вредных веществ (оксидов азота и серы), так и других загрязнителей, включая парниковые газы. Рассмотрены проблемы, возникающие при сжигании топлива нескольких видов, в том числе биомассы. Приведены результаты исследований процессов агломерации слоя, загрязнения поверхностей нагрева и коррозии пароперегревателей котлов с ЦКС.
Начало промышленного внедрения технологии кипящего слоя (КС) пошло от патента Винклера (1922 г.), по которому было построено множество газификаторов, в том числе для получения моторных топлив из генераторного газа. В 40-х и 50-х годах прошлого века началось активное применение технологии КС для сжигания твердых топлив. Следует отметить значительный прогресс в использовании котлов с КС в СССР. В конце 40-х годов ХХ в. W.K Levis и E.R. Gilliland предложили технологию циркулирующего кипящего слоя, которая быстро нашла промышленное применение на нефтеперерабатывающих заводах в аппаратах каталитического крекинга, а с середины 70-х годов и для сжигания твердых топлив [1]. Первый энергетический котел с ЦКС тепловой мощностью около 70 МВт был пущен в эксплуатацию в Финляндии в 1979 г. В настоящее время технология сжигания и газификации топлива в ЦКС является общепризнанной промышленной и реализована на многих объектах. В частности, прямоточный котел с ЦКС паропроизводительностью около 1700 т/ч на суперкритические параметры пара установлен на ТЭС Baima в Китае. Технология ЦКС применяется на установках со связанными между собой реакторами, которые используются для пиролиза и газификации твердых топлив с твердым теплоносителем. При этом вырабатывается газ с высокой теплотой сгорания (около 14 МДж/м3). На таких установках, которые часто называют полигенерирующими системами, могут вырабатываться тепло и электроэнергия. Такие реакторы используются и при сжигании и газификации топлива в высокотемпературных химических циклах с оксидами металлов – носителями кислорода.
История развития технологии ЦКС, успехи ее применения и опыт эксплуатации подробно рассмотрены в [2, 3]. Новые тенденции и роль технологии ЦКС в условиях меняющегося энергетического рынка представлены в докладе E. Zabetta с соавт. на конференции CFB12 [4]. Основные изменения рынка связаны с возрастающими требованиями к экологической чистоте, повышению эффективности, надежности и соответствию требованиям быстрого изменения нагрузки. Постоянно увеличивающаяся доля использования возобновляемых источников энергии (ВИЭ) и требования по снижению выбросов парниковых газов также оказывают влияние на энергетический рынок.
Вопросы, связанные с современными требованиями к котлам с ЦКС и их преимуществами, рассмотрены в [5]. На конкретных примерах продемонстрированы технические решения, позволяющие сделать энергоблоки с котлами с ЦКС более эффективными (утилизация тепла уходящих газов, повышение параметров пара), улучшить их маневренные характеристики, снизить выбросы вредных веществ. Рассмотрены также преимущества технологии ЦКС, обусловленные топливной гибкостью (для сжигания могут быть использованы низкосортные топлива, обладающие различными характеристиками) и возможностью снизить выбросы парниковых газов.
В [6] на основе анализа зарубежных данных показано, что при сжигании низкосортных топлив, требующих “мокрой” системы сероочистки после традиционных пылеугольных котлов, себестоимость электроэнергии, выработанной на энергоблоках мощностью 150–200 МВт с котлами с ЦКС, в среднем на 7.9% ниже, чем на энергоблоках с традиционными котлами. При этом затраты на эксплуатацию и ремонт примерно одинаковы. Затраты на топливо для котлов с ЦКС несколько ниже (более высокий КПД котла с ЦКС для низкореакционных топлив и отсутствие подсветки мазутом), капитальные затраты меньше в среднем на 7.4%. Эти данные близки к приведенным в [7] применительно к энергоблокам мощностью 600 МВт, причем основные экономические преимущества связаны с топливной гибкостью.
ОСОБЕННОСТИ ТЕХНОЛОГИИ ЦКС
Основной характерной особенностью технологии сжигания твердых топлив в кипящем слое является наличие значительного количества инертного материала в топке. Далее кратко описаны гидродинамика и процессы при сжигании топлива в кипящем слое, а также условия образования вредных веществ и подавления их выбросов.
При скорости газа, превышающей скорость минимального псевдоожижения (сила лобового сопротивления соответствует силе тяжести), объем слоя увеличивается и образуются пузырьки газа. Этот режим соответствует пузырьковому кипящему слою. При дальнейшем росте скорости газа пузырьки сливаются, частицы в надслоевом пространстве объединяются в группы с высокой концентрацией. Этот процесс соответствует турбулентному кипящему слою. Если частицы возвращаются в слой, циркулируя по замкнутому контуру, то такой слой называется циркулирующим кипящим. В этом случае отсутствуют четкие границы между турбулентным слоем в нижней части топки и расположенной выше разбавленной фазой. Расход циркулирующего материала в сотни раз превышает расход газа в системе и нередко зависит от массы слоя при неизменных скорости газа и размерах частиц.
Особенность ЦКС, помимо наличия в нем контура циркуляции, заключается в том, что скорость газа превышает скорость витания почти всех частиц слоя, т.е. практически все частицы могут быть вынесены из слоя. Однако в переходной зоне турбулентного слоя, а также в надслоевом пространстве вблизи стен топки котла существуют возвратные токи, образующиеся вследствие неравномерности скорости газа, соударения частиц и обмена энергией между ними и образования агломератов (пакетов) частиц. Именно этот признак является решающим для того, чтобы отличать режимы с ЦКС от других режимов псевдоожижения или движения частиц в потоке газа (например, пневмотранспорта).
В пылеугольной топке при горении протекают реакции окисления мелких частиц топлива (70% размером менее 200 мкм), смешанных с воздухом и топочными газами. Объем факела – это зона наиболее высоких температур, которые достигают 2000°С. При этом время пребывания частиц в топке полностью определяется временем движения газов.
В механических топках используются крупные куски угля размерами до 35 мм. Некоторые топлива сжигаются на движущихся решетках различных конструкций при подаче воздуха, проходящего через фиксированный слой топлива. При этом температура слоя достигает 1600°С, а время пребывания частиц в топке определяется скоростью перемещения решетки. Размеры частиц топлива, предназначенного для сжигания в кипящем слое, – средние между размерами частиц топлива для сжигания в пылеугольных и механических топках. Их максимальный размер зависит от реакционной способности топлива и составляет от 6 до 25 мм. Для котлов с пузырьковым кипящим слоем характерна плотность слоя около 750 кг/м3, а с циркулирующим – 550 кг/м3 при температуре слоя 820–900°С. Поступающее в топку топливо быстро перемешивается с материалом слоя, нагревается до температуры воспламенения и загорается. Благодаря длительному времени пребывания топлива в зоне горения и высокой интенсивности процессов тепломассообмена эффективность сжигания в топке с кипящим слоем довольно велика, несмотря на значительно более низкую температуру процесса, чем при пылевидном сжигании.
Концентрация топлива в слое котла с ЦКС обычно очень мала. Для высокореакционных топлив, таких, как дрова, содержание углерода крайне трудно измерить. При сжигании бурых и некоторых каменных углей концентрация углерода в слое составляет не более 1%, при менее реакционных каменных углях и антраците – 2%. В отдельных случаях при крайне низкореакционных углях и отходах углеобогащения содержание углерода в слое может достигать 3%, при этом его степень конверсии превышает 96%.
В качестве наполнителя слоя применяют песок или известняк, которые используются также для связывания оксидов серы, или собственную золу сгоревшего топлива. Поэтому часть удаляемого слоя (дренаж слоя или шлак) состоит из золы топлива, сульфата кальция и известняка или песка (возможно использование других наполнителей). Как правило, доля дренажа слоя меньше, чем доля уносимого материала.
Одним из основных преимуществ сжигания топлива в ЦКС является возможность эффективного улавливания диоксида серы SO2 путем подачи известняка в слой. Условия в топке (температура и время пребывания частиц известняка в реакционной зоне) оказываются весьма подходящими для организации процесса адсорбции диоксида серы известняком и щелочными компонентами золы. Малые выбросы оксидов азота (менее 200–300 мг/м3) без использования специальных средств азотоочистки обусловлены низкой и стабильной температурой слоя и надслоевого пространства при организации ступенчатого подвода воздуха. Важным достоинством технологии ЦКС является возможность сжигания топлив различного качества в одном и том же котле.
К недостаткам технологии ЦКС традиционно относят усложнение конструкции котла, наличие большой массы футерованных элементов, длительный пуск котла из холодного состояния, повышенные расходы электроэнергии на собственные нужды вследствие использования высоконапорных вентиляторов (за исключением случаев с крайне высоким содержанием серы).
СОСТОЯНИЕ И РАЗВИТИЕ ТЕХНОЛОГИИ ЦКС ДЛЯ КРУПНЫХ ЭНЕРГЕТИЧЕСКИХ УСТАНОВОК
В настоящее время в мире эксплуатируется более 3000 котлов с ЦКС. В Европе наибольший прогресс при внедрении котлов с ЦКС достигнут в последние годы в Польше – более 15 котлов на энергоблоках мощностью свыше 100 МВт, из них три по 235 МВт и еще три по 260 МВт. В 2009 г. был введен в эксплуатацию энергоблок мощностью 460 МВт с котлом с ЦКС на ТЭС в Логиже. Этот проект являлся в то время крупнейшим в мире с первой установкой с котлом с ЦКС на сверхкритические параметры пара. Электростанция обеспечивала лучший в мире КПД энергоблоков с котлами с ЦКС – 43.3% (средний КПД по странам Европы в то время для всех энергоблоков на угле составлял 36%). На этом энергоблоке в качестве расчетного топлива сжигается уголь теплотой сгорания около 20.1 МДж/кг, зольностью 23%, влажностью 12% и содержанием серы 1.2%. Также используются биомасса (до 10%) и осушенные шламы (до 30%) теплотой сгорания 7.1–16.7 МДж/кг. Уголь по своим свойствам близок к энергетическим углям России. Выполнение требований по выбросам оксидов серы и азота (не более 200 мг/м3) было обеспечено со значительным запасом.
Самый крупный пользователь технологии ЦКС – Китай [8], где с начала 1990-х годов начали строиться котлы с ЦКС для энергоблоков 50–100 МВт при финансовой поддержке и по технологиям американских и европейских компаний. Китайские производители приспосабливают зарубежные проекты к требованиям снижения капитальных затрат и использованию более простых технических решений. Стремительное развитие технологии ЦКС в Китае стало возможным благодаря инвестиционным и исследовательским программам его центрального правительства. В 2013 г. пущен первый в мире энергоблок мощностью 600 МВт с котлом с ЦКС. С 2002 г. ежегодно вводятся в эксплуатацию энергоблоки общей мощностью более 1000 МВт с котлами с ЦКС. Конструкция котла с ЦКС показана на рис. 1.
Топка котла раздвоена в нижней части, с фронтовой и задней стен топки установлены по три охлаждаемых паром циклона с системами возврата и зольными теплообменниками. Топка в сечении имеет размеры 15 × 28 м, высоту – 55 м. Она разделена на две части перегородкой с перемычками для выравнивания давления. Основные эксплуатационные показатели энергоблока 600 МВт с котлом с ЦКС соответствуют проектным значениям и приведены далее:
Содержание, %: |
углерода в золе уноса ...................................4–6 |
углерода в донной золе .................................1–2 |
кислорода в уходящих газах .............................4 |
Температура уходящих газов, °С .................130–135 |
КПД котла, %: |
расчетный ............................................92.3–91.8 |
гарантированный .......................................91.96 |
Выбросы при ${{C}_{{{{{\text{O}}}_{2}}}}}$ = 6%, мг/м3: |
SO2 .............................................................192.04 |
NO .............................................................111.94 |
Крупные энергоблоки с котлами с ЦКС строятся в Южной Корее. В июле 2011 г. компания Sumitomo–Foster Wheeler получила заказ на сооружение прямоточных котлов с ЦКС давлением пара 26.7 МПа и температурой 603/603°С для двух дубль-блоков по 1100 МВт в Южной Корее. В ноябре 2016 г. был сдан в коммерческую эксплуатацию первый энергоблок мощностью 1100 МВт с двумя котлами с ЦКС, в мае 2017 г. пущены еще два котла второго энергоблока такой же мощности [9]. В котлах сжигаются битуминозный уголь теплотой сгорания 14.2–24.9 МДж/кг и биомасса теплотой сгорания 15.8–18.0 МДж/кг. Достигнуты все проектные показатели, причем благодаря подаче известняка в слой и установки некаталитического восстановления содержание оксидов серы и азота составляет менее 50 мг/м3. Динамические испытания котлов показали их полное соответствие требованиям энергосистемы Южной Кореи.
В последнее время наметились две тенденции в развитии технологии ЦКС. Первая из них характерна для энергетики Китая и ряда стран Азии, прежде всего Южной Кореи, и связана с введением в эксплуатацию крупных энергоблоков на низкосортных углях. При этом важным является стремление к повышению параметров пара, удешевлению стоимости котлов и снижению затрат электроэнергии на собственные нужды. Вторая тенденция определяется возможностью эффективного сжигания в котлах с ЦКС различных топлив, включая биомассу и бытовые отходы, а также совместного сжигания местных топлив и угля. Эта тенденция характерна и для некоторых европейских стран.
Повышение эффективности энергоблоков с котлами с ЦКС обусловлено прежде всего повышением параметров пара, снижением затрат электроэнергии на собственные нужды и снижением температуры уходящих газов. В Китае намечено сооружение энергоблока с котлом с ЦКС при температуре перегретого пара 620°С, ведутся разработки котлов с ЦКС для энергоблоков 600–800 МВт при температуре перегрева 650 и 720°С [10]. В одной из первых публикаций компании Sumitomo–Foster Wheeler по вопросам использования закритических параметров пара в котлах с ЦКС указывается, что наилучшее сочетание этих параметров достигается в схеме “Компакт-Дизайн” с зольными теплообменниками INTREX [11]. Предполагается, что при нагрузке 100–80% котел будет работать при давлении пара около 27 МПа, а при нагрузке менее 80% – на скользящем давлении.
Одна из наиболее серьезных проблем в процессе разработки крупных котлов с ЦКС – регулирование температуры промежуточного перегрева при пониженных нагрузках [8]. Для свежего пара в прямоточных котлах она легко решается изменением соотношения вода – топливо. При промежуточном перегреве приходится использовать разделенные параллельные газоходы в конвективной шахте с шиберным регулированием расхода газов, паровой байпас холодной ступени промежуточного пароперегревателя, впрыскивающие пароохладители в рассечку ступеней и теплообменники INTREX. В частности, размещение в нижних теплообменниках INTREX выходной ступени промежуточного пароперегревателя при организации в них циркуляции горячих топочных частиц и частичного байпасирования их расхода способствует, наряду с другими мероприятиями, поддержанию температуры промежуточного перегрева в широком диапазоне нагрузок.
В [12] выполнено сравнение двух вариантов котлов с ЦКС для энергоблока 800 МВт: первый при температуре перегретого пара 600°С, второй – 700°С. Оказалось, что компоновка и размеры котлов практически одинаковы. Повышение температуры перегрева привело к снижению площади испарительной поверхности и уменьшению высоты топки всего на 2 м. Несколько снизилась площадь поверхности (высота) ширм, применена менее теплопроводная футеровка в нижней части топки. Уменьшена площадь поверхности экономайзера и на 5% увеличена площадь поверхности воздухоподогревателя. Для повышения теплосъема по свежему пару увеличена площадь поверхности зольных теплообменников INTREX 3, 4 и конвективного промежуточного пароперегревателя на 25%, добавлены пакеты промежуточного перегрева в камеры теплообменников INTREX.
Дальнейшее увеличение температуры перегретого пара выше 600°С требует применения новых материалов для толстостенных элементов (стали Р92 и Р122), создание которых не завершено вследствие отсутствия данных относительно их поведения при длительной эксплуатации. Качество сварки и усталостная прочность свариваемых образцов также являются предметом дальнейших исследований.
Статья [13] посвящена выбору материалов (металлы и обмуровка) для котлов большой мощности с ЦКС на сверхкритические параметры пара. Проведено большое количество исследований для выявления наилучших материалов с целью показать их длительную надежность. Хотя некоторые материалы были определены как подходящие для котла на сверхвысокие и ультрасуперкритические параметры пара (650 или даже 720°С), коммерческий интерес к таким установкам в настоящее время низкий. Выигрыш в эффективности от повышения температуры до 650°С незначителен на фоне дополнительных затрат на новые материалы, а стали, пригодные к длительной работе при температуре 720°С, пока еще не выпускаются промышленностью серийно.
С использованием собственных методов и программы расчета котлов с ЦКС в ОАО ВТИ выполнен конструкторский расчет котла с определением геометрических параметров топки, компоновки и размеров циклонов, зольных теплообменников и поверхностей нагрева конвективной шахты [14]. В котлах с ЦКС температура уходящих газов снижается даже при сжигании сернистых топлив. При этом в теплообменниках применяются пластиковые трубы, а тепло уходящих газов может быть использовано для подогрева или увлажнения воздуха, а также для подогрева сетевой или питательной воды [15, 16].
НАПРАВЛЕНИЯ НАУЧНЫХ РАЗРАБОТОК
Наиболее важными направлениями современных исследований в области технологии ЦКС применительно к сжиганию углей является комплексное изучение вопросов гидродинамики топки, улавливания частиц в сепараторах и возврата их в топку. Эффективность улавливания твердых частиц – основополагающий фактор увеличения расхода циркулирующих частиц и удержания мелких кальцинированных частиц в циркулирующем материале. Высокая концентрация в надслоевом пространстве топки приводит к росту коэффициента теплопередачи и обеспечивает равномерное распределение температур в топке, требуемую степень реагирования частиц известняка с диоксидом серы SO2 для наиболее эффективного связывания серы, а также более эффективное выгорание топлива.
Компания Alstom выполнила ряд важных исследований в области усовершенствования конструкций циклонов [17, 18]. В установках с котлами с ЦКС, работающими с малозольными топливами или топливами, зола которых имеет слишком мелкий фракционный состав, высокая эффективность циклонов приобретает важное значение для снижения количества потребляемого песка и эксплуатационных затрат. Можно выделить некоторые общие особенности конструкции современных циклонов с повышенным коэффициентом улавливания:
входной патрубок циклона со стороны топки выполняется таким образом, чтобы предварительная сепарация происходила в самом патрубке путем отжатия потока частиц к внешней стенке патрубка;
достаточная длина входного патрубка;
наклон потока во входном патрубке вниз.
Существенное улучшение показателей работы котлов с ЦКС благодаря повышению эффективности улавливания в циклонах было обеспечено в результате реконструкции циклонов путем изменения формы их входных каналов на котлах ТЭС в г. Гейдельберг и г. Вахтберг (Германия) [18]. Котлы ТЭС в Вахтберге работают на рейнских лигнитах, имеющих низкое содержание золы (около 2.0%) и серы (около 0.2%), в то время как на установках ТЭС в Гейдельберге зольность и содержание серы сильно колеблются. В котлах в Вахтберге, кроме того, совместно с лигнитами сжигаются осадки сточных вод.
Задача заключалась в увеличения скорости движения твердых частиц даже в случае короткого входного патрубка (ТЭC в Вахтберге) и перенаправлении их потока к внешней стене входного патрубка без изменения габаритов и металлоконструкций циклонов. По результатам исследований на холодной модели и математического моделирования было показано, что в существующих циклонах формируются полоса твердых частиц возле внутренней стенки входного патрубка и застойная зона возле его внешней стенки. Как следствие, скорость твердых частиц увеличивается недостаточно. Замечено также, что твердая фаза скапливается у верхней образующей циклона, так как здесь центробежные силы недостаточны. Значительное улучшение существующего положения достигнуто простыми способами, такими как установка перегородок на входе в циклон, изменение профиля входного патрубка или направление его вогнутой верхней образующей вниз. С помощью внутренних элементов входного патрубка циклона поток направляется таким образом, чтобы исключить образование слоя твердой фазы на внутренней стенке. Скопление частиц в потолочной части устранено увеличением вихревой скорости в циклоне. Комбинацией этих методов удалось повысить расчетную эффективность циклона, в частности размер улавливаемых фракций снизить до 10–40 мкм.
Эксплуатационные данные по выбросам оксидов азота и серы энергоблоков 300 МВт в Китае [31]
Электростанция | Номер энергоблока | ${{\eta }_{{{\text{S}}{{{\text{O}}}_{x}}}}}$, % | ССа/СS | Концентрация, мг/м3 (при нормальных условиях) | |
---|---|---|---|---|---|
SO2 | NOx | ||||
Baima | 1 | 94.7 | 1.7 | 487 | 87 |
Qinhuangdao | 1 | 90.0 | 2.1 | 200 | 70 |
2 | 90.0 | 2.1 | 200 | 70 | |
Honghe | 1 | 95.0 | 1.7 | 327 | 65 |
2 | 95.0 | 1.7 | 327 | 65 | |
Kaiyuan | 7 | 95.5 | 1.9 | 275 | 147 |
8 | 94.0 | 1.9 | 280 | 149 |
Средний размер частиц циркулирующей золы уменьшился с 200 до 160 мкм. В результате сокращения добавки кварцевого песка удалось избежать излишне большого содержания SiO2 в циркулирующей золе, вызывающей эрозионный износ. Результаты обследования обмуровки циклонов после двух лет эксплуатации показали, что увеличение скоростей в их входных патрубках не привело к повышению ее износа. Помимо этого, профиль давления в верхней части топки также увеличился, что улучшило теплообмен и снизило температуру в топке примерно на 10°С. Смещение выхлопного патрубка относительно его оси (эксцентричное расположение патрубка) также повышает качество улавливания мелких фракций золы и, совместно с изменением конструкции входного канала, обеспечивает высокий КПД циклона.
Активное развитие технологии ЦКС в Китае инициировало большой объем теоретических работ в области исследования гидродинамики двухфазного потока в топке с ЦКС, горения в циркулирующем кипящем слое, теплообмена в топке с ЦКС и выбора параметров ожижения.
Одной из основных причин плановых и внеплановых остановов котлов является эрозионный износ их топочных экранов. Борьба с эрозионными процессами не всегда приводила к успеху. При попытке снизить массу слоя в топке увеличивался недожог и снижалась производительность котла [19]. Было установлено, что материал в слое может быть разделен на две группы [20]. К первой группе относятся крупные частицы, не способные долететь до верхней части топки. Количество материала этой группы должно быть достаточным для обеспечения необходимого времени пребывания топлива в топке. Ко второй группе относятся частицы мелких фракций. Их количество также должно быть достаточным для формирования “быстрого слоя” в верхней части топки.
Результаты серии экспериментальных работ позволили определить граничные условия по доле мелких фракций в слое. Авторы [21] считают, что предельная масса крупных фракций материала слоя ограничена размерами зерна угля и его классом. Чем ниже класс или меньше размер зерна угля, тем меньшая масса слоя необходима. По мнению автора статьи, эти выводы не вполне корректны для условий сжигания топлив с низким выходом летучих и большой зольностью, например антрацитового штыба. Поэтому следовало бы добавить еще один критерий выбора массы частиц крупных фракций – выход летучих.
Результаты исследований процесса сжигания различных углей показали, что доля частиц мелких фракций в слое, необходимых для формирования “быстрого слоя”, может быть существенно снижена до уровня, соответствующего перепаду давления в слое 3–5 кПа в зависимости от высоты топки. В зависимости от марки угля масса частиц слоя крупных фракций соответствует перепаду давления 1–3 кПа. В итоге массу слоя удалось снизить до значений, соответствующих перепаду 5–7 кПа для большинства типов углей.
В ходе исследований предложена концепция распределения удельного тепловыделения по высоте топки и влияния вида топлива и скорости газов на процесс сжигания. Выявлены восстановительные условия в зоне плотного слоя и область с недостатком кислорода в зоне горения в центральной области верхней части топки.
Основным вопросом стало обеспечение должного качества материала слоя благодаря модификации элементов системы улавливания и циркуляции частиц. На рис. 2 приведены показатели распределения по фракциям и эффективности улавливания [21, 22]. В новой концепции низкой массы слоя рассматриваются две зоны с быстрым ожижением в надслоевом пространстве.
Был разработан новый циклон с выходным патрубком, смещенным относительно продольной оси, и узким наклонным входным патрубком. Средний размер улавливаемых частиц составил менее 25 мкм, а средний диаметр циркулирующих (уловленных частиц) – менее 130 мкм. Кроме того, были изменены параметры затвора системы возврата слоя, используемые при проектировании, для его лучшего взаимодействия с новыми циклонами и снижения нагрузки на тягодутьевое оборудование. В результате доля крупных частиц в слое стала существенно меньше, чем в традиционных котлах с ЦКС, а доля мелких составила больше половины массы слоя.
Первым объектом, на котором были внедрены новые энергосберегающие технологии, стала ТЭЦ Datuhe (три котла по 75 т/ч). Котлы работали на твердых отходах углеобогащения и водоугольной суспензии. Затем эта технология была применена на котле с ЦКС производительностью 220 т/ч на ТЭЦ East Hailar. Третьим объектом для внедрения новых технологий стал котел с ЦКС производительностью 240 т/ч на ТЭЦ Xingan, работающий на бурых углях. Затем эта технология была внедрена на энергоблоке мощностью 300 МВт ТЭС Longyan с котлами, работающими на антраците. Итогом внедрения стали повышение эффективности сжигания топлива, отсутствие эрозионного износа топочных экранов, снижение затрат электроэнергии на собственные нужды с 9.0–7.0 до 4.6%. Для пылеугольных котлов такой же мощности, снабженных установками сероочистки, затраты электроэнергии на собственные нужды превышают 6%. На заводе Taiyuan Boiler были разработаны и лицензированы энергосберегающие котлы с ЦКС производительностью 75–800 т/ч. Они уже опробованы на каменных углях, лигнитах, антрацитах, отходах углеобогащения и позволили снизить затраты на вспомогательные нужды и уменьшить влияние эрозионных процессов для углей всех типов.
Разработка демонстрационного проекта котла с ЦКС для энергоблока СКД 600 МВт сопровождалась необходимостью решения следующих задач:
увеличение мощности котла и использование соответствующих ноухау для улучшения теплообмена и горения в двухфазном потоке;
устранение риска одновременного использования принудительной циркуляции в экранах пароводяного тракта с неизвестным распределением теплового потока по газовому тракту;
разработка системы автоматического управления работой пароводяного тракта СКД в условиях высокой инерции процессов в котле с ЦКС.
Были разработаны комплексные модели гидродинамики и теплообмена с целью определить температуру металла мембранных труб при различных нагрузках и расходах циркуляции для гладких и оребренных труб. Данные модели хорошо согласуются с эксплуатационными показателями реального котла. Масштабные исследования, выполненные на стендовых установках и котле энергоблока 600 МВт, позволили наметить технологические и конструктивные решения, которые реализуются на новых энергоблоках большой мощности [23, 24]. В [24] указывается, что основой для увеличения мощности и эффективности котлов с ЦКС является совершенствование гидродинамической структуры потока и теплообмена в топке. В связи с ограничениями объема топки и теплосъема настенными экранами предлагается установка в топке подвесных поверхностей нагрева различных типов, площадь которых составляет 25–40% общей площади поверхности нагрева.
Для снижения выбросов оксидов азота предусматривается запатентованная технология центрального подвода вторичного воздуха через канал с отверстиями, расположенный по всей высоте топки в центральной ее части. В [23] рассматриваются вопросы совершенствования конструкции котла с ЦКС для нового энергоблока мощностью 660 МВт. Для этого котла предлагается конструкция с четырьмя циклонами в ряд по задней стенке (рис. 3). Топка разбита на четыре равные части по числу циклонов и зольных теплообменников. Возврат частиц золы осуществляется по восьми линиям, топливо подается по четырнадцати питателям. Ввод известняка производится в систему возврата. Циклоны установлены в ряд вдоль задней стенки, в топке размещены подвесные поверхности нагрева, в зольных теплообменниках – поверхности пароперегревателей. Регулирование потоков золы осуществляется с помощью конических механических клапанов.
Большое внимание при разработке этого котла было уделено математическому моделированию. В [23] приведены результаты моделирования конструкции циклонов, диаметр которых равен 10.5 м. Циклоны выполнены круглыми из пароохлаждаемых панелей с цилиндрической и конической частью и снабжены выхлопными патрубками с завихрителями. Специальная форма входного патрубка и оптимальный диаметр выхлопного патрубка (4.4 м) обеспечивают повышенную эффективность улавливания частиц.
На эффективность работы котла с ЦКС оказывает влияние фракционный состав слоя. Котел с ЦКС по материальному балансу твердой фазы является системой с одним входом (топливо, известняк, зола рециркуляции) и двумя выходами (донная зола дренажа слоя и летучая зола, не уловленная в циклонах). Аналогично с [25] рассмотрено изменение состава материала слоя во времени после пуска котла при первоначальном заполнении слоя песком применительно к первому в Росси котлу с ЦКС. Опыт пуска и эксплуатации котла с ЦКС энергоблока № 9 Новочеркасской ГРЭС выявил проблемы, в значительной мере связанные с температурой материала слоя [5, 26]. Прежде всего, это повышенная температура слоя и температура на выходе из топки, а также большая неравномерность температур по сечению слоя. Основные причины – недостаточное количество материла слоя, который может участвовать в циркуляции, и излишняя доля крупных частиц. При увеличении доли циркулирующих частиц необходима добавка известняка (расход примерно 10 т/ч), что приведет к росту количества частиц размером 0.1–0.3 мм почти на 40%.
МИНИМИЗАЦИЯ ВЫБРОСОВ ВРЕДНЫХ ВЕЩЕСТВ
Сжигание топлива в ЦКС разрабатывали и развивали как технологию с малыми выбросами вредных веществ, в первую очередь оксидов азота и серы. Типичными для котлов с ЦКС при сжигании каменных углей и антрацитов являются концентрации NOx, равные 100–200 мг/м3 при нормальных условиях и содержании кислорода в уходящих газах ${{С}_{{{{{\text{О}}}_{{\text{2}}}}}}}$ = 6%. Для топлив с очень большим выходом летучих возможно увеличение концентрации NOx до 250 мг/м3. Исходя из анализа зарубежного опыта и результатов исследований ВТИ, можно заключить следующее:
повышение температуры слоя приводит к росту эмиссии оксидов азота, которая заметно проявляется при температуре более 850°С;
увеличение доли первичного воздуха также вызывает рост концентрации NOx, причем наибольшее ее повышение относится к режимам с долей первичного воздуха более 70% (доля всего воздуха, подаваемого в топку, соответствует избытку 1.2);
увеличение избытка воздуха (концентрации кислорода) на выходе из топки приводит к существенному росту концентрации NOx при снижении нагрузки котла и большом содержании кислорода.
При сжигании топлива в ЦКС доля азота, переходящая в NOx, существенно уменьшается с ростом содержания азота на горючую массу (рис. 4) [27].
Рис. 4.
Зависимость конверсии азота топлива в NOx от содержания азота CN на горючую массу при температуре слоя 800°С (5, 6) и 850°С (7), концентрации О2 10% по объему (5, 7) и 8% по объему (6) [27]. 1 – колосниковая решетка; 2 – топливо различных видов (Skreiberg, 1996); 3 – кипящий слой; 4 – печь (Hofbauer, 1994)
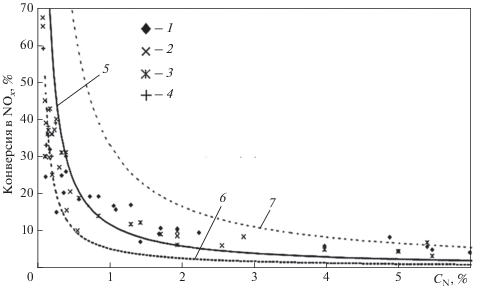
Обнаружено также влияние отношения мольных концентраций ССа и СS на выбросы NOx при сжигании антрацитового штыба. При увеличении значения ССа/СS от 1.5 до 4.0 выбросы NOx возрастают от 150 до 250 мг/м3. Процесс довольно сложный и недостаточно изученный, материнский азот топлива при выходе летучих переходит в газовую фазу в виде NH3 и НСN и далее в присутствии СаО и кокса частично превращается в NO через промежуточное образование N2O и частично восстанавливается до N2. При этом далее по высоте слоя концентрация N2O снижается, а концентрация NOx возрастает. С ростом избытка воздуха концентрация NOx, приведенная к нормальным условиям, при содержании кислорода 6% всегда увеличивается. Однако в исследованиях [16] отмечено снижение концентрации закиси азота N2O при увеличении избытка воздуха.
На рис. 5 приведены данные [28], свидетельствующие об изменении степени конверсии материнского азота топлива в NOx и N2O при различных температурах и условиях подвода вторичного воздуха соответственно. Показано, что степень конверсии топливного азота в N2O снижается при увеличении конверсии азота в NOx, что естественно. Конверсия азота в NOx составляла не более 50%, конверсия в N2O – не более 10%.
Рис. 5.
Влияние температуры слоя (а) и ступенчатого сжигания (б) на степень конверсии в NOx и N2O. Температура слоя, °С: 1 –800; 2 – 900; 3 – 950; сопла: 4 – нижние; 5 – верхние; 6 – верхние и нижние
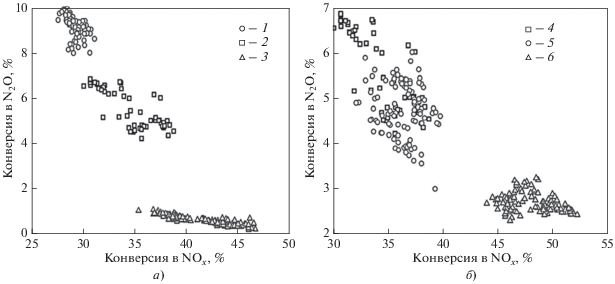
В России подробный анализ закономерностей образования оксидов азота в топках с КС и ЦКС выполнен в [29]. Автор [29] отмечает, что доля перехода азота топлива в оксиды зависит от его содержания в топливе, отношения констант реакций окисления азота и углерода и выхода летучих. В этой работе делается вывод, что степень превращения азота топлива в оксиды возрастает с увеличением содержания кислорода, предлагаются сложные зависимости для расчета концентрации NOх на выходе из слоя. Однако необходимо учитывать, что по высоте топки генерация оксидов азота возрастает по мере выгорания частиц кокса и одновременно снижается при восстановлении по реакции С + NOx, а также при разбавлении дымовых газов из-за присосов и вторичного воздуха.
Выбросы N2O для котлов с ЦКС не превышают 100 мг/м3 и снижаются с ростом температуры. Закись азота является в 200 раз более вредным компонентом парниковых газов, чем CO2, но ее концентрация за котлами с ЦКС в 10 000 раз ниже, чем концентрация СО2. Таким образом, вклад закиси азота по сравнению с другими парниковыми газами мал, поэтому интерес к проведению более подробных исследований образования и подавления выбросов N2O не очень высок.
Одним из основных преимуществ сжигания топлива в кипящем слое является возможность эффективного удаления диоксида серы SO2 путем подачи в слой известняка. При этом протекают следующие реакции:
Условия в топке котла с ЦКС благоприятны и для весьма эффективной адсорбции SO2 щелочными компонентами золы. Например, при сжигании канско-ачинских углей и эстонских сланцев подача известняка не требуется.
Детальный анализ механизма связывания серы известняком представлен в [28]. Показано, что сульфат кальция в форме расплава образует корку на поверхности оксида кальция и резко снижает дальнейшее прохождение реакции. Поэтому обеспечить использование CaO вряд ли возможно более чем на 40%. Оптимальная температура в топке находится вблизи 850°С. Увеличение значения ССа/СS в более чем 2.5 раза мало влияет на дальнейшее снижение выбросов оксидов серы. Опыты, выполненные на первом в России котле с ЦКС энергоблока № 9 Новочеркасской ГРЭС, подтвердили приведенные в [26] положения. При оценке эффективности улавливания оксидов серы принимали усредненные составы топлива, включая содержание серы на рабочую массу. Определяли расчетные значения расходов воздуха и газов, необходимых для полного сгорания при измеренном фактическом содержании кислорода в уходящих газах. Рассчитывали значение ССа/СS с учетом содержания CaCO3 в известняке.
На рис. 6 приведена зависимость степени связывания серы ${{\eta }_{{{\text{S}}{{{\text{O}}}_{x}}}}}$ от отношения ССа/СS. В режимах без подачи известняка отношение ССа/СS находится на уровне 0.2–0.3, а степень связывания составляет 4–9%. Наибольшая степень связывания серы относится к режимам с пониженными нагрузкой и температурой слоя [30].
Рис. 6.
Зависимость степени связывания оксидов серы от отношения ССа/СS, полученная в апреле 2018 г. (1) и ноябре 2017 г. (2)
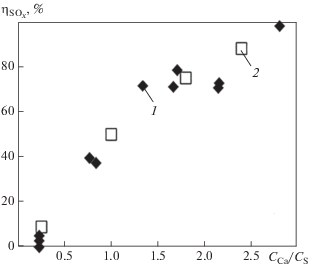
В [31] представлен анализ работы энергоблоков 300 МВт с котлами с ЦКС в Китае. Эксплуатационные данные по выбросам оксидов азота и серы приведены в таблице.
Снижение выбросов оксидов серы достигается улучшением качества материала слоя при размере частиц летучей золы менее 0.05 мм, донной золы – менее 0.2 мм. Частицы известняка должны быть более мелкими, что увеличивает площадь поверхности реагирования. При этом эффективность улавливания в циклонах повышается, что приводит к росту времени пребывания частиц в топке и более высокой эффективности использования известняка. Для некоторых регионов Китая с 2015 г. введено следующее требование – при строительстве новых электростанций выбросы вредных веществ от угольных котлов должны находиться на уровне установок со сжиганием природного газа. Выбросы должны составлять не более, мг/м3: оксиды азота 50, оксиды серы 35, твердые частицы 5. Такие решения уже реализованы на одном из котлов с ЦКС в Китае [32].
В [33] рассмотрено влияние условий подачи первичного воздуха на выбросы оксидов азота. Эксперименты были проведены на котле энергоблока 235 МВт ТЭС Тurow в Польше. Моделирование распределения первичного воздуха показало неравномерность его раздачи по поверхности слоя. Добиться повышения равномерности можно было увеличением сопротивления воздухораспределительной решетки, однако это решение было признано нецелесообразным, так как при его реализации возрастут затраты на собственные нужды энергоблока. Была выполнена модификация формы камеры раздачи первичного воздуха, установлены профили на входе в камеру, разделяющие потоки на три зоны с одинаковыми расходами. Результаты работ показали, что распределение температур по топке стало более равномерным, температуры в слое снизились примерно на 50°С, а выбросы оксидов азота уменьшились в среднем на 10%.
В [34] приведены результаты испытаний на котле суперкритических параметров пара энергоблока 600 МВт. На распределение кислорода по сечению оказывают влияние концентрация частиц в потоке над слоем и соотношение расходов первичного и вторичного воздуха. Интенсивность выгорания топлива на выходе из топки была выше, чем в ее средней части. При номинальной нагрузке концентрация кислорода снижается до расстояния около 1 м от стенки топки. Затем несколько растет и после расстояния 2 м концентрация О2 уменьшается с достижением минимального значения на расстоянии 4 м от стенки. Концентрации оксидов азота и серы несколько увеличивались при перемещении пробозаборных зондов от стенки в глубь топки, также заметно росла концентрация СО.
В [35] приведены данные о влиянии добавки аддитивов и летучей золы на снижение выбросов оксидов и закиси азота. Добавление Na2CO3 и CH3COONa может одновременно снизить оптимальную температуру восстановления NO и увеличить эффективность его удаления. Добавление CH3COONa отрицательно влияет на уменьшение выхода NO при температурах выше 950°С. Концентрация иона Na+ также мало влияет на эффективность связывания NO. Добавление летучей золы при температуре менее 800°С может значительно повысить эффективность связывания оксидов азота. Чем выше содержание активных оксидов (CaO, Fe2O3 и др.) в летучей золе, чем сильнее проявляется этот эффект. Эффективность удаления N2O зависит от концентрации иона Na+. Это каталитическое воздействие проверено опытом. В ЦКС такое воздействие существенно выше, так как содержание в нем частиц примерно на два порядка больше, чем при пылеугольном сжигании. Летучая зола может способствовать разрушению N2O, особенно при низкой температуре. Чем выше содержание активного оксида металла в золе уноса, тем сильнее каталитическое разложение N2O.
Как правило, удается поддерживать выбросы оксида углерода на уровне ниже 50 мг/МДж. Уровень выбросов других несгоревших углеводородов обычно значительно ниже – менее 10 мг/МДж в пересчете на метан. Увеличение концентрации СО связано с недостаточным временем пребывания частиц в надслоевом пространстве или низкими температурами газов в топке. Гарантийные значения выбросов СО не превышают 200 мг/м3 (при нормальных условиях).
При сжигании сланцев в котле с ЦКС на Эстонской ТЭС содержание ароматических углеводородов в дымовых газах оказалось намного ниже, чем у пылеугольного котла, что является, вероятно, результатом более длительного пребывания частиц топлива и продуктов сгорания в высокотемпературной зоне топки [36]. Например, в котлах с ЦКС содержание бенз(а)пирена ниже 11 нг/м3 (${{С}_{{{{{\text{О}}}_{{\text{2}}}}}}}$ = = 6%), в пылеугольном котле оно составляет 32–89 нг/м3. Подобный результат был получен и для ароматических углеводородов: в донной золе в пылеугольном котле их примерно 230 нг/кг, в котле с ЦКС – меньше 10 нг/кг. Выбросы тяжелых металлов, диоксидов и фуранов, ароматических углеводородов, полихлорируемых дифенилов при сжигании эстонского горючего сланца очень малы по сравнению с выбросами других топлив. Прежде всего, это результат эффективной организации горения сланца с выходом летучих примерно 90%. Содержание хлора в горючем сланце при этом менее 0.2%, и он почти весь остается в золе.
В [27] подробно рассмотрены вопросы образования HCl, который способствует коррозии пароперегревателей и образованию отложений. Хлор топлива окисляется преимущественно до HCl, однако имеются и другие важные факторы, которые могут приводить к образованию молекулярного хлора, включая реакции с алюмосиликатами. На рис. 7 показана схема возможных взаимодействий серы с хлоринами, тяжелыми металлами и щелочными элементами по данным [27, 37].
Хлорины и особенно Cl2 могут приводить к образованию диоксинов и фуранов. Медь и железо могут служить катализаторами образования фуранов. В котлах с ЦКС происходит существенное снижение этих выбросов даже при относительно низких температурах сжигания (время пребывания в реакционной зоне при температуре более 800°С не менее 3 с). При сжигании коммунальных отходов в котлах с ЦКС концентрации диоксинов и фуранов резко снижаются при добавлении углей.
В [38] приведены данные о выбросах ртути за котлом с ЦКС энергоблока 135 МВт в Китае, которые показывают, что ртуть в основном содержится в частицах летучей золы и удаляется на 98% в электрофильтре. Концентрация ртути в дымовых газах составляет 0.062 мкг/м3. Было определено, что летучая зола с относительно высоким содержанием углерода хорошо адсорбирует ртуть из дымовых газов. Этот эффект связан с развитой пористой структурой золы.
В [39] выполнено сравнение эмиссии ртути в котлах с ЦКС и пылеугольных, оснащенных электрофильтрами. Указывается, что средняя концентрация ртути в углях, сжигаемых в Китае, составляет 0.22 мг/кг. Ежегодный рост этого загрязнителя находится на уровне 4.8%. Ртуть в пылеугольных котлах присутствует в газовой фазе (более 90%), тогда как в котлах с ЦКС – в частицах донной и летучей золы. В работе [39] показано, что удаление ртути в котлах с ЦКС с электрофильтрами близко к 100%, а ее выход через дымовую трубу исследованного котла с ЦКС составлял 0.028 мг/ч. Эффективность удаления ртути из газов одного из пылеугольных котлов была равна 27.56%, другого – 33.59%.
Мелкие частицы и аэрозоли представляют большую опасность для легких человека. В [40] выполнено исследование образования этих частиц на лабораторной установке с ЦКС. Оказалось, что частицы крупнее 1 мкм в основном состоят из кальция, а частицы меньших размеров содержат много калия при сжигании биомассы.
ПРОБЛЕМЫ ПРИ СЖИГАНИИ БИОМАССЫ, МНОГОТОПЛИВНЫЕ КОТЛЫ С ЦКС
При использовании биомассы в качестве топлива для выработки тепла и электроэнергии замещается определенная часть ископаемого топлива и в большинстве случаев удается снизить выбросы вредных веществ, в том числе парниковых газов, в атмосферу. В настоящее время биомасса как топливо занимает четвертое место в мире по объемам производства и потребления энергии. Из нее производится около 15% общего объема тепловой энергии в странах ЕС. Согласно прогнозу [41], в 2030 г. с помощью возобновляемых источников энергии будет производиться около 50% общего объема потребляемой тепловой энергии. В 2050 г., по мнению экспертов Европейского совета по ВИЭ, возможно достичь 100% производства тепловой энергии из возобновляемых источников в странах ЕС. При этом вклад биомассы составит 45%.
Для условий России при относительно низких ценах на энергоресурсы специальное древесное топливо для производства тепловой и электрической энергии пока не находит широкого применения. Использование биомассы в качестве топлива актуально лишь для лесопромышленных и деревообрабатывающих предприятий, располагающих отходами переработки древесины, а также сельскохозяйственных предприятий. В этих условиях большое значение имеет зависимость технологии сжигания от свойств топлив и мощности установок [42].
Благодаря топливной гибкости технология ЦКС позволяет сжигать до 100% биомассы, и современные котлы часто проектируются на сжигание топлива минимум двух видов. Опыт освоения более 400 котлов с ЦКС позволил выработать концепцию современного биоЦКС-котла (Advanced Bio-CFB), принципиальная конструкция которого показана на рис. 8. Технические решения, примененные на этом котле, используются и в котлах, рассчитанных на совместное сжигание угля и биомассы.
Рис. 8.
Конструкция биоЦКС-котла [43]. 1 – топка; 2 – встроенный охлаждаемый сепаратор и опускной стояк; 3 – конвективная шахта; 4 – зольные теплообменники; 5 – ступенчатая решетка
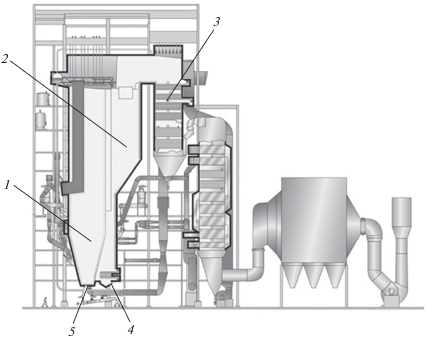
В биоЦКС-котле предотвращаются слипание слоя и шлакование вследствие нахождения в слое активного материала – добавки биомассы ухудшенного качества, обеспечения постоянной скорости газов в топке и контроля температуры слоя. Оптимальные конструкция конвективной шахты и температура газов в ней обеспечивают предотвращение шлакования и коррозии ее поверхностей нагрева.
В ОАО ВТИ выполнено расчетное исследование влияния совместного сжигания углей различных видов и биомассы на эффективность работы котла, а также на некоторые экологические показатели [44]. Установлено, что сжигание 10% биомассы (по тепловыделению) не приводит к существенному снижению эффективности брутто котла, однако прирост затрат электроэнергии на собственные нужды вызывает уменьшение эффективности нетто энергоблока в целом. Совместное сжигание может привести к увеличению топливных затрат, снижения которых можно добиться уменьшением потребления угля. Показано, что совместное сжигание угля и биомассы влияет на выбросы СО2, которые можно снизить на 18–22% при сжигании до 10% биомассы по тепловыделению.
Наиболее важными проблемами при сжигании биомассы и совместном сжигании биомассы и углей являются агломерация слоя, загрязнение и коррозия высокотемпературных поверхностей нагрева. Агломерация слоя – одна из самых распространенных проблем эксплуатации котлов с КС и ЦКС, прежде всего при сжигании сельскохозяйственных и некоторых промышленных отходов [45]. Она приводит к укрупнению материала слоя, ухудшению и даже прекращению ожижения. В [46] выполнен анализ зарубежных и отечественных исследований, направленных на выявление основных механизмов процессов агломерации в котлах с кипящим слоем при сжигании биомассы. Показано, что наибольшее влияние на процессы агломерации оказывают щелочные компоненты золы, которые, вступая в реакцию с силикатами, образуют легкоплавкие эвтектики. Поэтому важным является определение критической концентрации в слое натрия и калия (наиболее легкоплавкие эвтектики), при которой начинается спекание частиц. Данные по критической концентрации калия у разных исследователей довольно сильно различаются.
Обзор мер по предотвращению агломерации приведен в [45]. Для снижения негативного влияния агломерации слоя на процесс сжигания биотоплив необходимо увеличить расход его дренажа и обеспечить добавку свежего инертного материала. В [46] впервые был предложен подход к оценке требуемого расхода дренажа слоя, развитый затем в [47]. Для этого были записаны уравнения материального баланса и баланса соединений натрия и калия. Такой подход аналогичен расчетам баланса солей в барабане котла с естественной циркуляцией.
Соединения железа, содержащиеся в золе, также активно реагируют со щелочными соединениями, при этом температура размягчения образующихся материалов составляет 1135°C. Таким образом, при наличии в золе большого количества Fe2O3 щелочные компоненты могут реагировать, прежде всего, с Fe2O3, не образуя легкоплавких соединений. В слое из железной руды с концентрацией Fe2O3 равной 39% критическая концентрация калия увеличивается примерно в 3 раза. Это означает, что около 2/3 калия реагируют с оксидами железа, соответственно условная концентрация калия в слое, приводящая к агломерации, пропорционально снижается. Для предотвращения агломерации слоя при сжигании топлив с очень высоким содержанием оксидов натрия и калия можно применять оливиновый песок с содержанием оксидов кремния около 40% или ильменит. Оливин практически не взаимодействует с газообразными соединениями калия, но взаимодействует с соединениями кальция в топливе.
Загрязнение поверхностей нагрева не только приводит к снижению эффективности работы котла, но и влияет на выбросы вредных веществ. После обдувки поверхностей нагрева эмиссия NOх и SO2 почти не меняется, тогда как концентрация СО резко падает и затем медленно растет в период между обдувками. Отложения на поверхностях нагрева в топке не отмечались, за исключением ширм, они также образовывались при сжигании в кипящем слое биотоплив или твердых коммунальных отходов (ТКО). На образование рыхлых отложений в конвективной шахте, а также более прочных на поверхности пароперегревателя влияют, прежде всего, характеристики топлива.
В работе [48] приведены результаты исследований загрязнений на поверхности пароперегревателя одного из польских котлов с ЦКС тепловой мощностью 415 МВт. Котел был спроектирован для работы на смеси каменного угля, биомассы и водоугольной суспензии. Пароперегреватель котла состоит из трех ступеней, первая и третья ступени расположены в конвективном газоходе, вторая – в топке. Для исследований отложений были отобраны несколько образцов труб третьей ступени пароперегревателя из различных высокотемпературных зон. Был проведен детальный химический анализ отложений, определен их фракционный состав, выполнен микрорентгеновский спектральный анализ отложений и изучен их состав с помощью растрового электронного микроскопа. Проблемы образования отложений были связаны с наличием в образцах областей, богатых CaO. На поверхности труб или отложений происходит реакция взаимодействия частиц CaO и SO2 с выделением тепла:
Высокая концентрация серы и кальция наблюдается в местах агломерации твердых частиц. Главные элементы, формирующие золу (например, Si и Al), замечены в основном в периферийной области отложений, а при совместном сжигании биомассы с углем (зольность менее 10%) образуются такие щелочные элементы, как Na, K или P. Анализ результатов исследования отложений на специальном пробоотборнике (рис. 9) показал, что при наличии водоугольной суспензии образуются отложения в большем количестве.
Рис. 9.
Толщина отложений при сжигании топлива различных видов. 1 – уголь + сорбент + биомасса; 2 – уголь; 3 – уголь + + водоугольная суспензия + сорбент; 4 – уголь + водоугольная суспензия; 5 – уголь + водоугольная суспензия + сорбент + биомасса; 6 – уголь + сорбент; 7 – уголь + водоугольная суспензия + сорбент + биомасса + индикатор
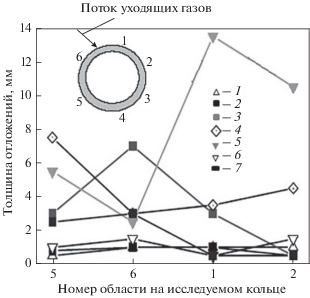
Самые толстые слои отложений были обнаружены на фронтовой и тыльной частях колец пробоотборника после сжигания смеси угля и водоугольной суспензии. При добавлении сорбента в топливо толщина отложений увеличивалась немного. При добавлении биомассы к данной смеси толщина отложений увеличивалась еще больше, особенно на тыльной части кольца пробоотборника. По результатам экспериментов сделаны следующие выводы:
образование отложений зачастую происходит из-за наличия оксида кальция;
на формирование отложений существенное влияние оказывают размеры частиц, распределение сорбента и топлива.
В [49] предложен индекс оценки способности к загрязнению поверхностей нагрева котлов в виде отношения массы, кг, оксидов щелочных металлов (K2O + Na2O) к единице тепла, ГДж, в топке. Если значение индекса превышает 0.17 кг/ГДж, то отложения на конвективной части уже возможны, при превышении 0.34 кг/ГДж они неизбежны. Для некоторых видов биомассы растительного происхождения значение индекса составляет примерно 1.0 кг/ГДж, тогда как для углей – не более 0.1 кг/ГДж.
Образование отложений связано с коррозией металла поверхностей нагрева котлов, в которых сжигается биомасса. Как показывают результаты зарубежных исследований, источниками этих процессов являются одни и те же химические компоненты топлива, т.е. хлор и щелочные металлы. Выявлено несколько механизмов коррозии при сжигании биомассы в паровых котлах. Некоторые исследователи утверждают, что основной причиной описанных проблем является высокое содержание (до 300 мг/м3) газообразных хлоридов, преимущественно HCl, в продуктах сгорания [50]. В других исследованиях главной причиной называется наличие в отложениях расплавленных эвтектических смесей хлоридов [51]. По результатам исследования [52] делается вывод, что причина высокой интенсивности загрязнения и коррозии – наличие хлоридов щелочных металлов на поверхности мелкодисперсной летучей золы. Существует также точка зрения, что одной из основных причин чрезвычайно высокой скорости коррозии является сульфатизация хлоридов в отложениях под воздействием SO2 [53].
Обычные пути снижения риска коррозии – это конструктивные решения: помещение отдельных секций пароперегревателя в зоны с менее коррозионно опасной средой (выносной теплообменник с кипящим слоем), использование коррозионно-стойких материалов, оптимизация схемы движения сред в пароперегревателе (прямоток, противоток) в отдельных пакетах для снижения температуры стенки. Пороговая температура металла при коррозии, вызываемой хлоридами щелочных металлов, равна 450°С. Для топлив с высоким содержанием хлора при более высоких температурах металла необходимо применять сталь с высоким содержанием хрома (более 25%). При сжигании хлорсодержащих и щелочесодержащих топлив риск коррозии пароперегревателя также может быть снижен проведением совместного сжигания биомассы с углем, торфом и шламами или использованием аддитивов, содержащих серу, сульфаты или алюмосиликаты. Основное количество образующегося диоксида серы SO2 в дальнейшем переходит в SO3. Оба этих оксида серы способны сульфатировать хлориды щелочных металлов, но скорость реакции для SO3 намного выше.
На основе этого механизма компания Metso разработала систему снижения высокотемпературной коррозии пароперегревателя с использованием впрыска в зону пароперегревателя сульфатного реагента Corro Stop, состоящего главным образом из Fe2(SO4)3. В [54] представлены результаты внедрения этой системы на котле Metso HYBEX мощностью 90 Вт с пузырьковым кипящим слоем при сжигании смеси коры, щепы, лесных отходов, опилок, осадка сточных вод и вторичной древесины на Каледонском бумажном комбинате в Шотландии. Принцип действия системы Corro Stop состоит в дозировании сульфата железа или сульфата алюминия в топочную камеру перед пароперегревателем. Реагент впрыскивается через основные сопла, расположенные на уровне аэродинамического выступа. Конструкция системы предусматривает также вспомогательные сопла вблизи вторичного пароперегревателя.
Первые в России исследования процессов коррозии пароперегревателей при сжигании ТКО проводили на котле-утилизаторе мусоросжигательного завода № 4 в Руднево (Москва) и стендовой установке ВТИ [55]. По результатам исследований предложено рассматривать протекание коррозионного процесса в две стадии. На первой стадии происходит разрушение оксидного слоя под воздействием HCl. Парциальное давление HCl вблизи поверхности металла существенно выше, чем парциальное давление в газах, вследствие процесса сульфатизации щелочных хлоридов ($2{\text{NaCl}} + {{{\text{H}}}_{{\text{2}}}}{\text{O}} + {\text{S}}{{{\text{O}}}_{{\text{3}}}}$ = ${\text{N}}{{{\text{a}}}_{{\text{2}}}}{\text{S}}{{{\text{O}}}_{{\text{4}}}} + {\text{2HCl}}$). Термодинамические условия не позволяют восстанавливаться оксидному слою, в отсутствие которого HCl напрямую взаимодействует с компонентами стали с образованием хлоридов (${\text{Fe}} + {\text{3HCl}}$ = = ${\text{FeC}}{{{\text{l}}}_{{\text{3}}}} + {{{\text{H}}}_{{\text{3}}}}$). Хлорид железа испаряется при температурах выше 300°C. В результате вышеописанных процессов образуется рыхлый слой продуктов коррозии с высокой диффузионной проницаемостью. Вторая стадия коррозионного процесса обусловлена протеканием каталитической реакции
при которой происходит регенерация HCl.
По причине высокой диффузионной проницаемости отложений и продуктов коррозии интенсивность коррозионного процесса можно определять только скоростью химических реакций. В результате практически для всех марок сталей вторая стадия коррозионного процесса характеризуется кинетическим режимом, т.е. экспоненциальное снижение интенсивности коррозии во времени не происходит.
Сложность и взаимосвязанность процессов агломерации слоя, загрязнения и коррозии поверхностей нагрева и эмиссий загрязняющих веществ побуждают ведущих производителей котлов для сжигания биомассы в КС искать комплексные подходы и технические решения по снижению соответствующих рисков. Попытка ранжировать различные топлива по степени их сложности для сжигания в зависимости от их состава представлена компанией Metso в [56]. На основе анализа различных топлив относительно перечисленных рисков и обобщения главных технических решений, направленных на их снижение, в [57] представлены разработанные компанией Metso концепции котла с ЦКС для четырех групп топлив.
Попытка суммировать результаты исследовательских и опытно-промышленных работ компании Sumitomo–Foster Wheeler и обобщить данные о влиянии различных компонентов топлив на агломерацию слоя, коррозию и загрязнение поверхностей нагрева при сжигании смесей биомасс различных видов в котлах сверхкритических параметров с ЦКС представлена в [58]. На рис. 10 показаны результаты сравнительных расчетов для различных биотоплив по корпоративным моделям агломерации, загрязнения и коррозии в ЦКС с использованием индекса вероятности PI, количественно характеризующего склонность топлив или их смесей к агломерации (AgglPI), загрязнению (FoulPI) и коррозии (CorrPI). Значения индекса в интервале 0–2 соответствуют низкой вероятности, 2–4 – средней вероятности, 4–6 – высокой вероятности, значения более 6 означают очень высокую вероятность реализации процесса.
Рис. 10.
Оценка склонности различных биотоплив к агломерации слоя (а), загрязнению (б) и коррозии поверхностей котла (в) на основе индекса вероятности [58]
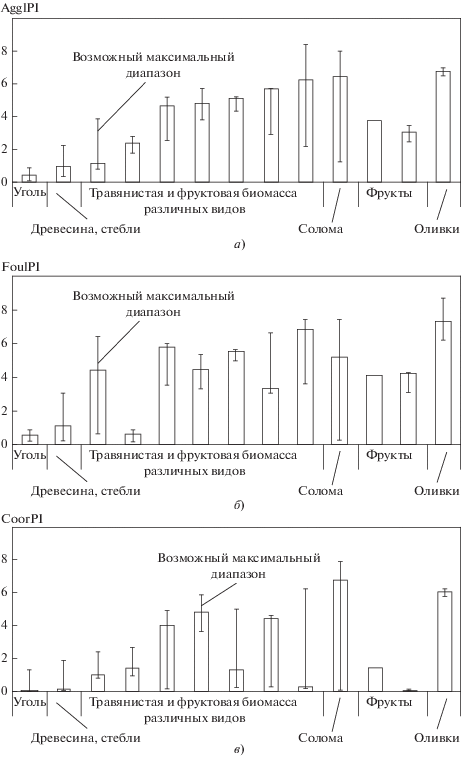
Вероятностная модель агломерации основана на гипотезе, что щелочные элементы K, Na и P в составе топлива вместе с частицами кварца SiO2 образуют легкоплавкие компоненты и/или эвтектики, приводящие к агломерации. Вероятностная модель загрязнения предполагает, что щелочные компоненты K и Na, а также щелочно-земельные Ca и Mg инициируют загрязнение, в то время как Al и Si, наоборот, снижают загрязняющие свойства топлива. Модель также различает прочные и рыхлые отложения. Твердые отложения включают в себя загрязнения, образуемые щелочами, и отложения сульфатированного Ca. Рыхлые отложения образуются оксидами Ca и несвязанными алюмосиликатами Zn и Pb. Вероятностная модель коррозии основывается на гипотезе, что коррозию поверхностей нагрева вызывает Cl, присутствующий в топливе. Если загрязнение низкое, то коррозия также низкая; если загрязнение высокое, коррозия может быть высокой или низкой в зависимости от доступности Cl для участия в коррозии. Основные результаты представленных в [58] исследований можно суммировать следующим образом:
температура пара для котлов с ЦКС может быть поднята до 600°С при содержании щелочных элементов в топливе до 1%. При этих условиях процессы агломерации слоя, коррозии и загрязнения поверхностей регулируются использованием подходящих смесей топлив (например, совместным сжиганием с углем) или применением аддитивов и альтернативных материалов–наполнителей слоя;
агломерация слоя, загрязнение и коррозия поверхностей котлов с ЦКС являются результатом сложных балансов между элементами золы топлива и материалов, используемых в котле; содержание K и Cl не является характеристикой, достаточной для оценки вероятности агломерации для данного топлива;
сопротивляемость сплавов коррозии при температурах, превышающих 600°С, не пропорциональна содержанию Cr или основных легирующих элементов (Cr, Ni, Mo, Mn). Другие свойства материалов, такие как наличие упрочняющих элементов и кристаллографическая структура, играют большую роль.
ВЫВОДЫ
1. В настоящее время технология сжигания и газификации топлив в ЦКС является общепризнанной промышленной и реализована на многих объектах энергетики. В Китае намечено сооружение энергоблока мощностью 660 МВт с котлом с ЦКС при температуре перегретого пара 620°С, ведутся разработки котлов с ЦКС для энергоблоков 600–800 МВт при температуре перегрева 650 и 720°С.
2. Наиболее важными направлениями современных исследований в области технологии ЦКС применительно к сжиганию углей является комплексное изучение гидродинамики топки, улавливания частиц в сепараторах и возврата их в топку. Эффективность улавливания твердых частиц – это основополагающий фактор при увеличении их расхода и удержании мелких кальцинированных частиц в циркулирующем материале.
3. Типичными для котлов с ЦКС при сжигании каменных углей и антрацитов являются концентрации NOx в выбросах, равные 100–200 мг/м3 при нормальных условиях и содержании кислорода в уходящих газах 6%. Для топлив с очень большим выходом летучих возможно увеличение концентрации NOx до 250 мг/м3.
4. Одним из основных преимуществ сжигания в кипящем слое является возможность эффективного удаления диоксида серы SO2 путем подачи в слой известняка. Вместе с тем, сульфат кальция в форме расплава образует корку на поверхности оксида кальция и резко снижает дальнейшее прохождение реакции. Поэтому обеспечить использование CaO возможно не более чем на 40% его содержания в известняке. Оптимальная температура в топке составляет примерно 850°С. Увеличение отношения молярных концентраций СCa/СS в 2.5 раза мало влияет на дальнейшее снижение выбросов оксидов серы.
5. Возможность эффективного сжигания различных топлив в котлах с ЦКС позволяет использовать их для совместного сжигания биомассы и ископаемого топлива. Для ряда европейских стран это может являться решающим фактором, если учитывать, что биомасса нейтральна по выбросам СО2. Сжигание до 10% биомассы по тепловыделению позволит снизить выбросы СО2 на 18–22%.
6. Наиболее важными проблемами при сжигании биомассы и совместном сжигании биомассы и углей являются агломерация слоя, загрязнение поверхностей нагрева и коррозии высокотемпературных поверхностей нагрева. Изучению сложных процессов взаимодействия между элементами золы биомассы и материалом слоя (агломерация), образования отложений и коррозии поверхностей под слоем отложений уделяется большое внимание.
Список литературы
US Patent 2.498.088. Conversion of hydrocarbons with suspended catalyst / W.K. Lewis, E.R. Gilliland. Standard Oil Dev. Co. Patented 1950, original application 1940.
Leckner B. Development of fluidized bed conversion of solid fuels – history and future // Proc. of the 22nd Intern. Conf. on FBC. Finland, Turku, June 14–17, 2015. P. 2–11.
Nowak W. Research development and perspectives of fluidized bed boilers in Poland // Proc. of the 22nd Intern. Conf. on FBC. Finland, Turku, June 14–17, 2015. P. 12–22.
Zabetta E., Kovacs J., Eriksson T. Role and challenges of CFB in a changing energy market // Proc. of the 12th Intern. Conf. on CFB. Krakow, Poland, May 23–26, 2017. P. 77–83.
Использование технологии сжигания твердых топлив в циркулирующем кипящем слое в мире и в России / Г.А. Рябов, Е.В. Антоненко, И.В. Крутицкий, О.М. Фоломеев, А.В. Беляев // Электрические станции. 2018. № 3. С. 11–17.
Применение котлов с циркулирующим кипящим слоем для замены устаревших пылеугольных котлов / Г.А. Рябов, Е.Н. Толчинский, И.И. Надыров, О.М. Фоломеев, С.Н. Трухачев, Д.А. Шапошник // Теплоэнергетика. 2000. № 8. С. 14–20.
Nuortimo K., Jantti T., Khryasheva A. Развитие технологии ЦКС для создания мощных энергоблоков // Электрические станции. 2018. № 3. С. 29–35.
Overview of the Samcheok Green Power 4 × 550 MWe supercritical circulating fluidized-bed steam generator project and its first years of operation / Sang Ho Lee, Timo Jäntti, Juhani Burke, Riku Parkkonen, Kalle Nuortimo // Proc. of the 23rd Intern. Conf. on FBC. Seoul, Korea, May 13–17, 2018. P. 118–127.
Application of CFD modeling tools to optimize 660 MW ultra supercritical CFB design / P.J. Chapman, I.F. Abdulally, S.G. Kang, P. Gauville // Proc. of the 11th Intern. Conf. on CFB and Fluidization Technology. Beijing, China, May 14–17, 2014. 1020–1026.
Scalling up to a 350 MW circulating fluidized bed boiler – heat engineering Foster-Wheeler corporation. Summer, 1997. Preprint Foster-Wheeler corporation.
Integration of ultra-supercritical OUT and CFB boiler technologies / S.J. Goidich, Z. Fan, O. Sippu, A.C. Bose // Proc. of the 19th Intern. Conf. on FBC. Austria, Vienna, May 21–23, 2006.
Robertson A., Goidich S., Fan Z. 1300°F 800 MWe USC CFB boiler design study // Proc. of the Intern. Conf. FBC-20. China, Xian, May 18–21, 2009. P. 125–131.
Dthellet Y., Dorier C., Houzet S. Refractory and metallic materials for a 600 MWe circulating fluidized bed boiler with advanced steam parameters // Proc. of the 6th Intern. Conf. on CFB. Germany, Wurzburg, August 22–27, 1999. P. 551–558.
Рябов Г.А. Котлы с циркулирующим кипящим слоем на сверхкритические параметры пара // Электрические станции. 2013. № 9. С. 14–22.
Adamczyk F. Integration of flue gas heat recovery system in the worldwide largest fluidized bed boiler Lagisza 460 MWe: Efficiency increase and CO2 reduction. VGB PowerTech, 12.2008.
Долгушин И.А., Рябов Г.А., Ханеев К.В. Утилизация тепла уходящих газов угольных ТЭЦ // Сб. д-окл. конф. с междунар. участием “VIII Всерос. семинар вузов по теплофизике и энергетике”. Екатеринбург, 12–14 ноября 2013 г. С. 211–215.
Mushelkrantz U., Mushelkrantz E. Improvements of cyclones in CFB power plants and quantative estimations of their effects on the boiler solid inventory // Proc. of the 6th Intern. Conf. on CFB. Germany, Wurzburg, August 22–27, 1999. P. 761–767.
Operating experience with measures for improvement of cyclone removal efficiency / B. Krohmer, B. Roper, J. Seeber, G.N. Stamatelopoulos // Proc. of the 19th Intern. Conf. on FBC. Austria, Vienna, May 21–24, 2006.
Effect of bed pressure drop on performance of CFB boiler / H. Yang, H. Zhang, S. Yang, G. Yue, J. Su, Z. Fu // Energy Fuels. 2009. V. 23. Is. 6. P. 2886–2890. https://doi.org/10.1021/ef900025h
Weiterentwicklung der zirkulierenden Wirbelschichtfeuerung (ZWSF) in China [An update of circulating fluidized bed combustion (CFB) technology in China] / H. Yang, G. Yue, J. Lu, Y. Zhang // VGB Power Tech. 2012. V. 12. № 12. P. 75–79.
Yue G., Mao J. An update and future of Chinese clean coal // Keynotes speech of 37th Intern. Tech. Conf. on Clean Coal & Fuel Systems. USA, Florida, June 3–7, 2012. P. 12–20.
Yue G. The formation of the CFB design theory and its practice in China // Proc. of the 22nd Intern. Conf. on FBC. Finland,Turku, June 14–17, 2015. P. 12–22.
The design of four cyclones in the 660 MW high efficiency ultra-supercritical / W. Zheng, M. Zhang, J. Lyu, Q. Liu, H. Yang // Proc. of the 23rd Intern. Conf. on FBC. Seoul, Korea, May 13–17, 2018. P. 128–134.
Current developments of large-size/supercritical CFB technology and its developing trend / L. Cheng, J. Ji, Q. Wang, Y. Wei, M. Fang, Z. Luo, M. Ni, K. Cen // Proc. of the 23rd Intern. Conf. on FBC. Seoul, Korea, May 13–17, 2018. P. 97–107.
The dynamic balance of bed material size distribution in start-up process for circulating fluidized bed boiler / Su-Xia Ma, Jun Guo, Wei-Ming Chang, Guang-Xi Yue, Hai Zhang // Proc. of the Intern. Conf. FBC22. Turku, Finland, 2015. P. 788–796.
The first year experience of once through CFB boiler operation of 330 MWe unit / G. Ryabov, D. Kuchmistrov, E. Antonenko, I. Krutitskiy, O. Folomeev, D. Melnikov, A. Beliaev // Proc of the 23rd Intern. Conf. on FBC. Seoul, Korea, May 13–17, 2018. P. 108–117.
Winter F. Formation and reduction of pollutants in CFB-C: from heavy metals, particulates, alkali, NOx, N2O, SOx, HCl // Proc. of the Intern. Conf. FBC-20. China, Xian, May 18–21, 2009. P. 43–48.
NOx and N2O emissions of burning coal with high alkali content in a circulating fluidized bed / Yi Cai1, L. Cheng, L. Xu, Q. Wang, M. Feng, Z. Luo, Q. Zhou, L. Nie, H. Su // Proc. of the 22nd Intern. Conf. on FBC. Finland, Turku, June 14–17, 2015. P. 496–503.
Мунц В.А. Закономерности горения топлив и образования оксидов азота в топках кипящего и циркуляционного кипящего слоя: дис. … докт. техн. наук. Екатеринбург, 1999.
Anthony E.J., Granatstein D.L. Sulfation phenomena in fluidized bed combustion systems // Prog. Energy Combust. Sci. 2001. № 27. P. 215–236.
Operational status of 300 MWe CFB boiler in China / J.F. Li1, J.H. Mi1, J.H. Hao, S. Yang, H.T. Huang, H.M. Ji, J.F. Lu, G.X. Yue // Proc. of the Intern. Conf. FBC-20. China, Xian, May 18–21, 2009. P. 243–246.
Цзянь Гао, Суэ Ин Чжан. Применение передовых технологий газоочистки, отвечающих экологическим требованиям Китая с ультранизкими выбросами вредных веществ // Сб. докл. III Междунар. конф. “Использование твердых топлив для эффективного и экологически чистого производства электроэнергии и тепла”. М.: ОАО ВТИ, 28–29 июня 2016 г.
Mirek P., Czakiert T., Nowak W. NOx emission reduction by the optimization of the primary air distribution in the 235 MWe CFB boiler // Proc. of the Intern. Conf. FBC-20. China, Xian, May 18–21, 2009. P. 162–166.
Experimental study on gas-solid diffusion characteristics in the furnace of a 600 MW supercritical CFB boiler / Jin Yan, Xiaofeng Lu, Quanhai Wang, Jianbo Li, Xiujian Lei, Xiong Zheng, Xuchen Fan, Changxu Liu, Zhen Xu, Sicong Sun // Proc. of the 23rd Intern. Conf. on FBC. Seoul, Korea, May 13–17, 2018. P. 193–202.
Experimental study of NO and N2O removal in CFB boiler: effects of sodium additives and fly ash / Xinjie Liao, Shihong Zhang, Jingai Shao, Teng Shen, Haiping Yang, Xianhua Wang, Hanping Chen // Proc. of the 23rd Intern. Conf. on FBC. Seoul, Korea, May 13–17, 2018. P. 359–368.
Kirso U., Laja M., Urb G. Polycyclic aromatic hydrocarbons (PAH) in ash fractions of oil shale combustion: fluidized bed versus pulverized firing // Oil Shale. 2005. V 22. Is. 4. P. 537–545.
Otsuka N. A thermodynamic approach on vapor-condensation of corrosive salts from flue gas on boiler tubes in waste incinerators // Corros. Sci. 2008. V. 50. Is. 6. P. 1627–1636. https://doi.org/10.1016/j.corsci.2008.02.004
Mercury emission and removal of a 135 MW CFB utility boiler / Y.F. Duan, Y.Q. Zhuo, Y.J. Wang, L. Zhang, L.G. Yang, C.Z. Zhao // Proc. of Intern. Conf. FBC-20. China, Xian, May 18–21, 2009. P. 189–194.
Wang Y.J., Duan Y.F., Zhao C.S. Comparison of mercury emissions between circulating fluidized bed boiler and pulverized coal boiler // Proc. of the Intern. Conf. FBC-20. China, Xian, May 18–21, 2009. P. 256–261.
Rajczyk R., Nowak W. PM2.5 and PM10 emission from biomass combustion in the circulating fluidized bed // Proc. of the Intern. Conf. on Circulating Fluidized Beds. Germany, Hamburg, May 13–16, 2008. P. 949–954.
RE-Thinking 2050. A 100% Renewable Energy Vision for the European Union Publication of European Renewable Energy Council 2010.
Опыт сжигания различных видов биомассы в России и Белоруссии / Г.А. Рябов, Д.С. Литун, Е.А. Пицуха, Ю.С. Теплицкий, В.А. Бородуля // Электрические станции. 2015. № 9. С. 9–17.
First operating experiences of 55 MWe Konin and 205 MWe Polaniec CFB boilers firing 100% biomass / M. Natunen, T. Jantti, D. Goral, K. Nuortimo // Vienna, Austria. Power-Gen Europe, June 4–6, 2013.
Долгушин И.А., Рябов Г.А., Седлов А.С. Исследование и совершенствование схемы ТЭС с котлом ЦКС в целях повышения эффективности и улучшения экологических показателей // Энергетик. 2014. № 8. С. 33–36.
Scala F. Particle agglomeration in fluidized beds: mechanisms, early detection and possible countermeasure // Proc. of the 12th Intern. Conf. on Fluidized Bed Technology. Krakow, May 23–26, 2017. P. 65–76.
Ryabov G.A., Litoun D.S., Dik E.P. Agglomeration of bed material: influence on efficiency of biofuel fluidized bed boiler // Therm. Sci. 2003. V. 7. Is. 1. P. 5–16. https://doi.org/10.2298/TSCI0301005R
Рябов Г.А., Литун Д.С. Агломерация при сжигании и газификации топлив в кипящем слое // Теплоэнергетика. 2019. № 9. С. 42–59. https://doi.org/10.1134/S0040363619090042
Kobyłecki R., Gołąb S., Krzemień L. Fouling in the backpass of a large-scale CFBC // Proc. of the Intern. Conf. CFB9. Germany, Hamburg, May 13–16, 2008. P. 1069–1074.
Murphy M.L. Repowering options: retrofit of coal-fired power boilers using fluidized bed biomass gasification // Energy Products of Idaho. 2001. P. 1–14.
Stott F.H. The influence of HCl on the oxidation of iron at elevated temperature // Mater. Corros. 2000. V. 51. Is. 5. P. 277–286. https://doi.org/10.1002/(SICI)1521-4176(200005)51: 5<277:AID-ACO277>3.0.CO;2-C
Makkonen P. Corrosion tests in combustion of recovered fuels in a modern CFB boiler // VTT Technical Research Centre of Finland. 2003. V. 8. Is. 8. P. 80–83.
Fey W., Thielan W., Meyer B. Combustion of biomass and residues under oxidizing and reducting conditions in fluidized bed // Proc. of the 6th Intern. Conf. on CFB. Germany, Wurzburg, August 22–27, 1999. P. 674–685.
Warnecke R. Einfluss von Strömung und chemischen Reaktionenim rauchgasseitigen Belag auf Korrosion an Überhitzer-Rohren in Müllverbrennungsanlagen [Influence of flow and chemical reactions in flue gas caused fouling on superheater tubes in waste-to-energy plants] // VGB PowerTech. 2004. № 9. S. 52–59.
Roppo J. Long term experiences of mitigation of superheater corrosion with the metso corrostop sulfate injection system // Proc. of the 21st Intern. Conf. on Fluidized Bed Combustion. Naples, Italy, June 3–6, 2013. P. 91–94.
Загрязнение и коррозия пароперегревателей котлов на ТЭС, сжигающих твердые бытовые отходы (ТБО) и биомассу / Е.Н. Зеликов, Г.А. Рябов, Э.П. Дик, А.Н. Тугов // Теплоэнергетика. 2008. № 11. С. 73–77.
Silvennoinen J. From fuel to solution by sophisticated fuel and process atmosphere characterization // Proc. of the 21st Intern. Conf. on Fluidized Bed Combustion. Naples, Italy, June 3–6, 2013. P. 187–194.
CFB boiler designs for demanding fuels / T. Luomaharju, P. Lehtonen, K. Jalkanen, P. Köykkä // Proc. of the 21st Intern. Conf. on Fluidized Bed Combustion. Naples, Italy, June 3–6, 2013. P. 1077–1084.
Supercritical steam from biomass mixtures with 1% alkali content / E.C. Zabetta, V. Barišić, J. Mahanen, K. Peltola // Proc. of the 21st Intern. Conf. on Fluidized Bed Combustion. Naples, Italy, June 3–6, 2013. P. 1085–1092.
Дополнительные материалы отсутствуют.
Инструменты
Теплоэнергетика