Теплоэнергетика, 2021, № 4, стр. 47-54
Экспериментальные исследования расходных характеристик разношаговых многогребенчатых уплотнений
С. С. Дмитриев a, *, Б. Н. Петрунин a, М. Э. А. Э. Ахмед a, b
a Национальный исследовательский университет “Московский энергетический институт”
111250 Москва, Красноказарменная ул., д. 14, Россия
b Университет Банха, инженерный факультет Шупра, кафедра машиностроения
Банха, Египет
* E-mail: dmitriyevss@mpei.ru
Поступила в редакцию 22.05.2020
После доработки 23.06.2020
Принята к публикации 26.08.2020
Аннотация
В паровых турбинах, производимых в России, разношаговые многогребенчатые уплотнения (РМУ) до настоящего времени не нашли широкого применения, хотя за рубежом их используют довольно часто. При модернизациях и создании новых паровых турбин в настоящее время применяются рабочие лопатки с цельнофрезерованным бандажом, что позволяет изготавливать многорядные периферийные уплотнения. В связи с этим вопрос о выборе оптимальной конфигурации РМУ приобретает важное практическое значение. Результаты, полученные в настоящей работе, позволили экспериментально оценить степень влияния различных сочетаний шагов гребней на роторе и статоре на расходные характеристики РМУ и разработать практические рекомендации по их применению. Минимальный расход утечки был зафиксирован для моделей РМУ с шагом на роторе шириной 2 мм. Применительно к надбандажным уплотнениям мощных паровых турбин были проведены сравнительные экспериментальные исследования моделей РМУ с проставками на роторе шириной 3 и 4 мм, на статоре – 4 и 5 мм. Наиболее оптимальной из исследованных в настоящей работе можно считать модельную пару с проставками на роторе и статоре шириной 4 и 5 мм соответственно, т.е. с шагами на роторе 4.8 и на статоре 5.8 мм. Экспериментально показано, что утечка в РМУ при прочих равных условиях меньше на 22–25%, чем в прямоточных уплотнениях. Применение РМУ позволяет обеспечить отсутствие задеваний ротора о статор при относительных радиальных и осевых смещениях ротора в переходных режимах. Кроме того, аэродинамические силы в РМУ, способные вызывать низкочастотные автоколебания валопровода, составляют примерно 60% аналогичных сил в традиционных радиальных уплотнениях. С учетом этих обстоятельств можно рекомендовать РМУ для применения вместо штатных радиальных надбандажных уплотнений в цилиндрах высокого (ЦВД) и среднего давления (ЦСД) в новых и модернизируемых паровых турбинах.
Наибольшие потери от утечек в ступенях паровых турбин происходят в надбандажных (периферийных) уплотнениях. В цилиндрах высокого давления действующих паровых турбин, производимых в России, применяются, как правило, ступени активного типа, периферийные уплотнения в которых выполняются прямоточными и имеют всего два или три гребня. При этом даже при простом увеличении числа гребней до 6–8 в прямоточном уплотнении при прочих равных условиях потери от утечки снижаются более чем в 2 раза.
Однако качество применяемых уплотнений определяется не только утечкой, но и их сопротивлением износу. При эксплуатации паровых турбин, особенно в переходных режимах, в штатных уплотнениях неизбежны задевания ротора о статор и соответствующий износ гребней уплотнений, что, естественно, приводит к увеличению потерь от утечки. В этой связи целесообразно применение осерадиальных уплотнений, износ которых в эксплуатации минимальный, и аэродинамические силы, способные вызывать автоколебания роторов, также минимальны. Однако при прочих равных условиях потери от периферийной утечки в осерадиальных надбандажных уплотнениях оказываются даже бо́льшими, чем в штатных радиальных уплотнениях с номинальными зазорами [1].
В соответствии с [1] наиболее целесообразным для надбандажных уплотнений в ЦВД является применение разношаговых многогребенчатых уплотнений, которые имеют минимальные потери от периферийной утечки, а аэродинамические силы в них существенно меньше аналогичных сил в традиционных радиальных уплотнениях. Следует также учесть, что использование РМУ позволяет предотвратить задевания ротора о статор при их относительных смещениях в переходных режимах, что позволяет сохранить установленные радиальные зазоры и, соответственно, обеспечить отсутствие зависимости утечки от этих смещений.
С учетом того что при создании новых и модернизации старых паровых турбин в последнее время в России применяются усовершенствованные рабочие лопатки с цельнофрезерованными бандажами, которые позволяют выполнять многорядные периферийные уплотнения, вопрос о выборе оптимальной конфигурации РМУ приобретает важное практическое значение. На кафедре паровых и газовых турбин Московского энергетического института всегда уделялось большое внимание экспериментальным исследованиям течений потока пара в уплотнениях турбомашин и проводились сравнительные исследования расходных и динамических характеристик радиальных лабиринтных уплотнений с РМУ [2]. В настоящей работе была поставлена задача экспериментально оценить степень влияния различных сочетаний шагов гребней на роторе и статоре на расходные характеристики РМУ и разработать практические рекомендации по их применению.
ОПИСАНИЕ ЭКСПЕРИМЕНТАЛЬНОЙ УСТАНОВКИ
Для решения поставленной задачи была спроектирована и изготовлена установка, конструктивная схема которой представлена на рис. 1. Гребни статора 3 и ротора 6 изготовлены из стального листа толщиной Δ = 0.8 мм. Внутренний диаметр гребней статора равен 102 мм, наружный диаметр гребней ротора – 100 мм, радиальный зазор составляет δ = 1.0 мм. Важно отметить, что все гребни выполнены из одного листа по одной технологии, что гарантирует их идентичность. Проставки статора 4 внутренним диаметром 112 мм изготовлены из листов толщиной 3, 4, 5 мм. Проставки ротора 7 выполнены из листов толщиной 2, 3, 4 мм. Их наружный диаметр равен 90 мм. Высота гребней ротора и статора составляет 10 мм. Статорная часть РМУ набирается из гребней статора 3, проставок статора 4 и зажимается гайкой 5. Аналогичным образом из гребней и проставок ротора собирается роторная часть, которая зажимается гайкой 8.
Рис. 1.
Конструктивная схема установки для исследования РМУ. 1 – корпус; 2 – вал; 3, 6 – гребень статора и ротора; 4, 7 – проставка статора и ротора; 5, 8 – гайка; 9 – термометр; 10 – сопло; 11 – зонд полного давления; lст, lр – длина статора и ротора с гребнями
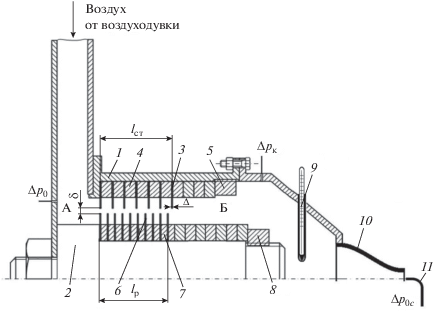
Корпус 1 и вал 2 выполнены соосными. Для моделирования прямоточного уплотнения с гладким ротором применяется труба наружным диаметром 100 мм, насаживаемая вместо гребней и проставок ротора на вал 2 и закрепляемая гайкой 8. Воздух от турбовоздуходувки ТВ-42-1.4 при максимальном избыточном давлении 40 кПа через запорно-регулирующую задвижку подводится в камеру А перед уплотнением. В процессе эксперимента для каждого варианта модели РМУ и прямоточного уплотнения измеряли избыточное давление Δр0 в камере А непосредственно перед уплотнением и в камере Б за уплотнением Δрк с помощью водяного дифференциального манометра с точностью 2 мм вод. ст. Атмосферное давление pат измеряли с помощью ртутного барометра с погрешностью 1 мм рт. ст. После этого рассчитывали абсолютные давления перед уплотнением р0 = (pат + Δр0) и за уплотнением рк = (pат + Δрк) и отношение давлений ε = рк/р0.
Для экспериментов в рамках поставленной задачи вращение ротора не требуется, так как его влияние начинает сказываться на расход воздуха через уплотнение только при (u/cр) > 1.0 (здесь u – окружная скорость потока на входе в уплотнение; cр – расходная, т.е. осевая, скорость потока через уплотнение) [3, 4]. При выбранных размерах моделей уплотнения условие (u/cр) > 1.0 может реализоваться только при очень большой частоте вращения ротора (более 1000 Гц), которая не реализуется в реальных энергетических турбомашинах.
Избыточное давление Δр0с на оси сопла 10 в его выходном сечении измеряли с помощью зонда полного давления 11 водяным дифференциальным манометром с погрешностью 2 мм вод. ст. Температуру перед соплом 10 измеряли термометром 9 с погрешностью 1°С.
Суживающееся сопло 10 выходным диаметром 30 мм, спрофилированное по методу Витошинского, обеспечивает практически равномерное и одномерное поле скорости потока на выходе из него, однако вблизи его стенки следует учесть наличие пограничного слоя. Для этого предварительно было проведено траверсирование полей избыточного давления полного торможения по радиусу выходного сечения сопла с помощью зонда 11. Измерения проводили водяным дифференциальным манометром с погрешностью до 2 мм вод. ст. С учетом осевой симметрии потока рассчитывали избыточное давление для осредненного одномерного потока в выходном сечении сопла 10
(1)
$\Delta p_{0}^{{{\text{оср}}}} = \frac{{\int\limits_0^{{{r}_{0}}} {\Delta {{p}_{{0r}}}{\text{d}}r2\pi r} }}{{\pi r_{0}^{2}}},$При сравнении полученного по формуле (1) результата со значением избыточного давления полного торможения Δр0с, измеренного в выходном сечении на оси сопла зондом 11 (при r = 0), было установлено, что на выходе из сопла при безразмерной скорости потока в диапазоне 0.05–0.15 выполняется соотношение
(2)
${{\Delta p_{0}^{{{\text{оср}}}}} \mathord{\left/ {\vphantom {{\Delta p_{0}^{{{\text{оср}}}}} {\Delta {{p}_{{0{\text{c}}}}}}}} \right. \kern-0em} {\Delta {{p}_{{0{\text{c}}}}}}} \approx 0.995,$поэтому в качестве избыточного давления полного торможения осредненного одномерного потока в выходном сечении сопла использовали значение
Отношение давлений εс в сопле 10 после проведенного таким образом осреднения потока на выходе из него вычисляли по формуле
(3)
${{\varepsilon }_{{\text{с}}}} = \frac{{{{р}_{{{\text{ат}}}}}}}{{{{р}_{{{\text{ат}}}}} + \Delta {{р}_{0}}}}.$Во всех исследованных случаях значение εс составляло не менее 0.995, что соответствовало безразмерной скорости на выходе из сопла не более 0.1. Скорость осредненного одномерного потока на срезе сопла с рассчитывали по формуле для одномерного потока идеальной несжимаемой жидкости, так как сжимаемостью потока можно было пренебречь [5]:
где ρ – плотность потока в выходном сечении сопла.Плотность рассчитывали по уравнению состояния
где R – универсальная газовая постоянная для воздуха; Т – температура воздуха в струе в выходном сечении, определяемая по уравнению изоэнтропы по измеренной температуре полного торможения перед соплом и отношению давлений εс.Расход через сопло G вычисляли по формуле
где Fc – площадь выходного сечения сопла 10.ОПИСАНИЕ РЕЗУЛЬТАТОВ ЭКСПЕРИМЕНТАЛЬНЫХ ИССЛЕДОВАНИЙ
При обработке экспериментальных данных для каждого варианта модели РМУ были получены зависимости G = f (ε) (рис. 2).
Рис. 2.
Расходная характеристика для моделей РМУ с проставками толщиной 4 мм для статора и 3 мм для ротора. Количество гребней: на статоре 1 – 5; 2 – 9; 3 – 14; на роторе 1 – 6; 2 – 11; 3 – 18
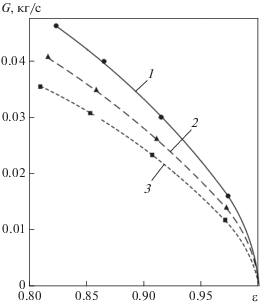
Специфика поставленной задачи состояла в исследовании большого числа вариантов моделей, составленных из разных роторных и статорных частей РМУ. Каждая конфигурация была испытана при четырех значениях ε. В любой из исследованных конфигураций количество гребней на роторе было больше количества гребней на статоре, а конфигурации РМУ подбирали таким образом, чтобы длина статора с гребнями lст отличалась от длины ротора с гребнями lр не более чем на 1 мм. В представленных далее результатах используется длина lmax с максимальным значением из пары lст и lр. Понятно, что целесообразно сравнивать по расходу варианты РМУ, в которых значения lmax различаются в наименьшей степени.
В табл. 1 приведены расходы для исследованных моделей РМУ, определенные при ε = 0.85 по зависимостям G = f (ε), показанным на рис. 2. Обозначение моделей РМУ, принятое в табл. 1, например Р36С45, означает модель РМУ с проставками шириной 3 мм на роторе, 4 мм на статоре и количеством гребней 6 и 5 на роторе и статоре соответственно.
Таблица 1.
Расход через сопло исследованных моделей РМУ при ε = 0.85
Номер модели | Конфигурация РМУ | lmax, мм | G, кг/с |
---|---|---|---|
1 | Р25С34 | 12.2 | 0.0415 |
2 | Р25С53 | 12.4 | 0.0410 |
3 | Р36С45 | 20.0 | 0.0425 |
4 | Р28С44 | 20.4 | 0.0368 |
5 | Р29С37 | 23.6 | 0.0355 |
6 | Р37С55 | 24.0 | 0.0405 |
7 | Р46С55 | 24.8 | 0.0420 |
8 | Р212С56 | 31.6 | 0.0365 |
9 | Р213С47 | 34.4 | 0.0335 |
10 | Р311С49 | 39.2 | 0.0373 |
11 | Р313С59 | 47.2 | 0.0340 |
12 | Р218С58 | 48.4 | 0.0323 |
13 | Р218С410 | 48.4 | 0.0310 |
14 | Р218С313 | 48.4 | 0.0305 |
15 | Р412С510 | 53.6 | 0.0343 |
16 | Р318С414 | 65.4 | 0.0313 |
17 | Р318С512 | 65.4 | 0.0315 |
18 | Р416С513 | 72.8 | 0.0300 |
На рис. 3 показана зависимость G = f (lmax), построенная по данным табл. 1. С ростом lmax суммарное количество гребней в моделях РМУ увеличивается. При этом расход через РМУ уменьшается, причем при lmax от 12 до 72 мм это уменьшение составляет примерно 30%. Однако это уменьшение существенно немонотонно и зависит от конфигурации РМУ. Хорошо видно, что в областях I, II и III имеется несколько конфигураций РМУ, в которых, несмотря на близкие значения lmax, расходы заметно различаются.
Рис. 3.
Зависимость расхода через сопло исследованных моделей РМУ от lmax при ε = 0.85. 1–18 – номер модели; I–IV – область исследования
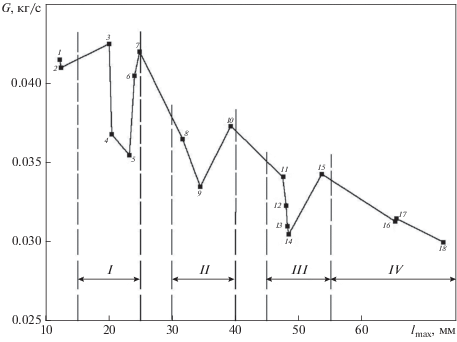
В области I расход в моделях Р28С44 и Р29С37 меньше примерно на 15–20% расхода в моделях Р36С45, Р37С55 и Р46С55. В области II в модели Р213С47 по сравнению с моделями Р212С56 и Р311С49 расход меньше примерно на 10%. Причем сравниваемые в областях I и II конфигурации РМУ (за исключением модели Р29С37 из области I) по суммарному количеству гребней практически не отличаются. При этом все конфигурации РМУ, имеющие меньший расход в этих областях, объединяет то, что ширина проставки на роторе у них составляет 2 мм.
В области III наименьший расход наблюдается в моделях Р218С58, Р218С410 и Р218С313. По сравнению с ними для моделей Р313С59 и Р412С510 расход больше примерно на 6–10%. В области III все конфигурации РМУ с меньшим расходом имеют на роторе проставки шириной 2 мм, но несколько большее суммарное количество гребней. В области IV у модели Р416С513 расход наименьший по сравнению с моделями Р318С414 и Р318С512.
Таким образом, наименьший расход при практически равном количестве гребней в областях I, II и III имеют модели РМУ с проставкой на роторе шириной 2 мм. Однако решение о практическом применении РМУ с такими проставками следует принимать на основе комплексного анализа всех характеристик уплотнений, среди которых не последнее значение имеют их стоимость и ремонтопригодность. В первую очередь, не следует забывать о стоимости изготовления рабочих лопаток с малыми шагами между гребнями на бандаже путем фрезерования. Нужно также учесть, что наименее удачной из исследованных моделей РМУ с проставками на роторе шириной 2 мм является сочетание Р2NС4M (здесь N – число гребней на роторе; М – число гребней на статоре). В такой конфигурации кратное количество гребней на роторе и статоре делает расходную характеристику уплотнения, как и в равношаговых многогребенчатых уплотнениях, существенно зависящей от осевого сдвига ротора и статора [2].
В процессе эксплуатации, особенно в переходных режимах, происходит заметный осевой сдвиг ротора турбины относительно статора. Причем этот сдвиг даже в допустимом диапазоне довольно значителен. Так, в соответствии с [6] предельные осевые перемещения ротора относительно статора в ЦВД и ЦСД базовой теплофикационной турбины РФ Т-110/120-12.8 составляют: на укорочение –1.2 мм, на удлинение +3.0 мм. В базовой теплофикационной турбине ПАО “Мосэнерго” Т-250/300-23.5 в ЦВД предельные осевые перемещения ротора относительно статора равны: на укорочение –1.8 мм, на удлинение +4.5 мм. В ЦСД-1 и ЦСД-2 этой турбины перемещения составляют: на укорочение –2.5 и –4.5 мм, на удлинение +3.5 и +4.0 мм. Для рабочих лопаток этих турбин с хордой большей 50 мм РМУ с проставками на роторе шириной 3 и 4 мм (модели РМУ Р318С414 и Р416С513, см. рис. 3, табл. 1) при практически одинаковом числе гребней имеют расход, почти одинаковый с расходом в модели РМУ Р218С313, обладающей наилучшими расходными характеристики из всех испытанных конфигураций РМУ с проставками на роторе шириной 2 мм.
В связи с этим применение РМУ с малыми шагами в периферийных уплотнениях мощных паровых турбин представляется маловероятным. Тем не менее, нельзя исключить применение РМУ с малыми шагами между гребнями в небольших паровых турбинах, где хорды рабочих лопаток меньше 25 мм и относительное смещение ротора и статора не столь критично.
В дальнейших исследованиях анализировали модели РМУ с проставками на роторе шириной 3 и 4 мм, на статоре – 4 и 5 мм. Сначала расходные характеристики этих моделей G = f (ε), полученные описанным выше способом, были приведены к единым режимным параметрам по ε. Были выбраны значения ε, равные 0.82, 0.89 и 0.96, и полученные результаты сведены в табл. 2, в которой все исследованные модели РМУ разделены на три группы. В каждой группе проставки на роторе и статоре одинаковые и модели различаются только количеством гребней на роторе и статоре и, соответственно, значениями lmax.
Таблица 2.
Расход через сопло исследованных моделей РМУ Gn/m, кг/с
Конфигурация РМУ | lmax, мм | ε | ||
---|---|---|---|---|
0.82 | 0.89 | 0.96 | ||
Р36С45 | 20.0 | 0.0455 | 0.0355 | 0.0197 |
Р311С49 | 39.2 | 0.0402 | 0.0295 | 0.0161 |
Р318С414 | 65.4 | 0.0344 | 0.0261 | 0.0137 |
Р37С55 | 24.0 | 0.0449 | 0.0337 | 0.0188 |
Р313С59 | 47.2 | 0.0379 | 0.0275 | 0.0147 |
Р318С512 | 65.4 | 0.0348 | 0.0253 | 0.0129 |
Р46С55 | 24.8 | 0.0449 | 0.0338 | 0.0190 |
Р412С510 | 53.6 | 0.0368 | 0.0275 | 0.0151 |
Р416С513 | 72.8 | 0.0327 | 0.0246 | 0.0121 |
Следует обратить внимание на то, что при практически равном суммарном количестве гребней при ε = const значения G3/4, G3/5 и G4/5 различаются несущественно. Однако значения lmax для этих конфигураций разные. Поэтому далее для каждой группы моделей при трех выбранных значениях ε были построены зависимости Gn/m = f (lmax), показанные на рис. 4. Как видно из рис. 4, расходные характеристики каждой группы моделей РМУ при одном и том же значении ε с небольшой погрешностью ложатся на одну линию, т.е. для моделей РМУ с проставками на роторе и статоре 3 и 4 мм, 3 и 5 мм и 4 и 5 мм они соответственно практически одинаковы. Как уже указывалось ранее, чем меньше шаг в РМУ, тем они дороже в изготовлении. Исходя из этого, наиболее оптимальной из исследованных можно считать модельную пару с проставками на роторе и статоре 4 и 5 мм соответственно, т.е. с шагами на роторе 4.8 мм и на статоре 5.8 мм.
Рис. 4.
Расходные характеристики исследованных моделей РМУ. 1 – G3/4; 2 – G3/5; 3 – G4/5; ε: 4 – 0.82; 5 – 0.89; 6 – 0.96
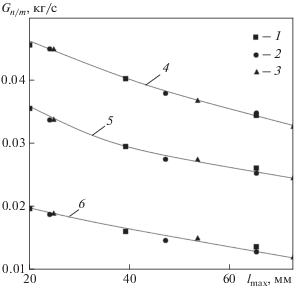
На следующем этапе исследований было проведено сравнение расхода через эту модель РМУ с расходами через прямоточные уплотнения. Для исследования моделей прямоточного уплотнения с гладким ротором была изготовлена труба наружным диаметром 100 мм, насаживаемая вместо гребней и проставок ротора на вал 2 и закрепляемая гайкой 8 (см. рис. 1), а статор набирался так же, как в моделях РМУ. Таким образом, радиальные зазоры оставались теми же, что и в моделях РМУ – δ = 1.0 мм. Исследования этих моделей были выполнены для обеспечения большей корректности сравнительного анализа, поскольку статорные части моделей РМУ и прямоточных уплотнений были одни и те же, что важно для идентичности коэффициентов расхода. Расходные характеристики прямоточных уплотнений были получены для проставок на статоре шириной 3, 4 и 5 мм при разных ε и представлены в виде зависимостей Gm = f (ε) (здесь m – ширина проставки на статоре). Пример таких зависимостей для прямоточных уплотнений с шириной проставки на статоре 5 мм и разным количеством гребней представлен на рис. 5.
Рис. 5.
Расходная характеристика для моделей прямоточных уплотнений с гребнями на статоре и проставками на нем шириной 5 мм. Количество гребней: 1 – 4; 2 – 9; 3 – 14
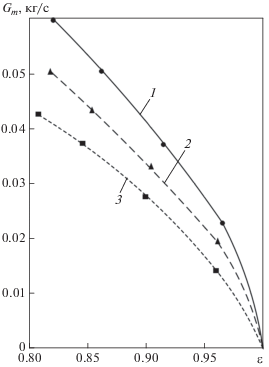
В дальнейшем, по аналогии с моделями РМУ, экспериментальные данные по полученным зависимостям Gm = f (ε) были приведены к тем же значениям по ε (0.82, 0.89 и 0.96), а полученные зависимости Gm от lmax показаны на рис. 6. Здесь же представлены расходные характеристики для модели РМУ с проставками шириной 4 мм на роторе и 5 мм на статоре (G4/5).
Рис. 6.
Расходные характеристики исследованных моделей РМУ и прямоточных уплотнений. ε: 1 – 0.82; 2 – 0.89; 3 – 0.96; 4 – G3; 5 – G4; 6 – G5; 7 – G4/5
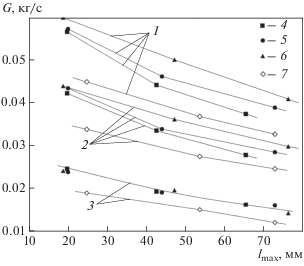
Хорошо видно, что чем меньше ширина проставки на статоре при одном и том же значении lmax, тем меньше расход при данном ε через модель прямоточного уплотнения. Это является иллюстрацией очевидного факта – большему количеству гребней на данной длине уплотнения соответствует меньшая утечка. Однако также хорошо видно, что с уменьшением lmax эта разница снижается. Кроме того, с уменьшением перепада давлений (ростом ε) эта разница также уменьшается и при ε = 0.96 расходные характеристики моделей прямоточных уплотнений с проставками на статоре шириной 3, 4 и 5 мм становятся практически одинаковыми.
Из рис. 6 также хорошо видно, что для всех случаев при ε = const расход через модель РМУ (G4/5) меньше расхода через модель прямоточного уплотнения любой конфигурации. Если сравнивать модель РМУ с проставками на статоре шириной 5 мм с моделями прямоточного уплотнения с аналогичными проставками на статоре, то во всем исследованном диапазоне изменения lmax при ε = 0.82 расход через РМУ примерно на 28% меньше расхода через прямоточное уплотнение, при ε = 0.89 – приблизительно на 25%, при ε = 0.96 – примерно на 22%.
Таким образом, во всех исследованных случаях расходные характеристики модели РМУ заметно лучше расходных характеристик моделей прямоточных уплотнений.
ВЫВОДЫ
1. Результаты экспериментальных исследований, представленные в настоящей работе, показывают заметное превосходство РМУ по расходу утечки перед аналогичными прямоточными уплотнениями.
2. По результатам проведенных исследований можно рекомендовать к применению пары (ротор–статор) с шагом 4 мм/5 мм при расходе через них, равном примерно 80% расхода через аналогичные по длине прямоточные уплотнения.
3. Применение РМУ обеспечивает отсутствие задеваний при относительных радиальных и осевых смещениях ротора и статора в переходных режимах, что позволяет сохранить установленные радиальные зазоры и, соответственно, независимость утечки от этих смещений. Кроме того, аэродинамические силы в РМУ, способные вызывать низкочастотные автоколебания валопровода, составляют примерно 60% аналогичных сил в традиционных прямоточных радиальных уплотнениях.
4. Применение РМУ целесообразно вместо штатных радиальных надбандажных уплотнений в ЦВД и ЦСД в модернизируемых и вновь строящихся паровых турбинах.
Список литературы
Костюк А.Г. Выбор лабиринтных уплотнений в паровых турбинах // Теплоэнергетика. 2015. № 1. С. 17–21. https://doi.org/10.1134/S0040363615010063
Коновалов Р.Н. Экспериментальные исследования расходных и динамических характеристик уплотнений для ступени с полным и парциальным подводом пара: дис. … канд. техн. наук. М.: МЭИ, 2003.
Leakage loss and heat transfer in high-speed rotating labyrinth seals / W. Waschka, S. Wittig, T. Scherer, S. Kim // Proc. of the Yokohama Intern. Gas Turbine Congress (IGTC-34). Japan, 1991. V. 2. P. 239–247.
Impact of rotational speed on the discharge characteristic of stepped labyrinth seals / R. Paolillo, S. Moore, D. Cloud, J.A. Glahn // Proc. of GT2007. ASME Turbo Expo 2007: Power for Land, Sea and Air. Montreal, Canada, 14–17 May, 2007. GT2007-28248. P. 1–8.
Петунин А.Н. Методы и техника измерений параметров газового потока. М.: Машиностроение, 1972.
Паровые турбины и турбоустановки Уральского турбинного завода / Г.Д. Баринберг, Ю.М. Бродов, А.А. Гольдберг, Л.С. Иоффе, В.В. Кортенко, В.Б. Новоселов, Ю.А. Сахнин. Екатеринбург: УТЗ, 2010.
Дополнительные материалы отсутствуют.
Инструменты
Теплоэнергетика