Теплоэнергетика, 2021, № 4, стр. 55-63
Повышение эффективности и увеличение ресурса системы плазменного розжига путем ее модернизации на Гусиноозерской ГРЭС
Д. В. Сосин a, *, А. В. Штегман a, И. А. Рыжий a, Е. А. Фоменко a, С. Д. Бор a, Ч. О. Цыренов b, А. В. Яковенко b, **
a Всероссийский теплотехнический институт
115280 Москва, Автозаводская ул., д. 14, Россия
b Филиал “Гусиноозерская ГРЭС” АО “Интер РАО – Электрогенерация”
671160 г. Гусиноозерск, Селенгинский р-н, Республика Бурятия, Россия
* E-mail: sosin_work@mail.ru
** E-mail: yakovenko_av@interrao.ru
Поступила в редакцию 01.06.2020
После доработки 24.07.2020
Принята к публикации 23.09.2020
Аннотация
Статья посвящена весьма актуальной проблеме – сокращению затрат на топливную составляющую при производстве электроэнергии на электростанциях России, а именно отказу от дорогостоящего мазута при растопках котла и переходу на использование угольной пыли для этой цели. Один из способов организации таких растопок – применение плазменной технологии для воспламенения угольной пыли. Данная технология основана на термохимической подготовке пылеугольного топлива с помощью электрической дуги, возникающей между электродами плазмотрона. Через дугу проходит поток воздуха, образующий плазму, которая, встречаясь с потоком аэросмеси, нагревает его, способствует выделению летучих веществ и воспламенению угольной пыли. Еще в 1994 г. на Гусиноозерской ГРЭС были проведены первые опыты по внедрению такой системы. Она оказалась эффективной, но обладала рядом существенных недостатков, которые ограничивали ее применение. Основным из них был низкий ресурс работы катода плазмотрона и муфельной горелки. В 2019 г. была организована работа по модернизации плазменной системы, направленной на увеличение ресурса основных узлов системы плазменного розжига. Для решения комплекса проблем специалистами ОАО ВТИ были предложены технические решения по конструкции муфельной горелки, системе очистки и автоматического регулирования подачи воды и воздуха на плазмотрон, разработан программный комплекс для управления работой системы безмазутного плазменного розжига и контроля за ее параметрами. Проведены монтаж и испытания модернизированной системы для одной из растопочных горелок котла ТПЕ-215. Специалистами ИФМ СО РАН была разработана конструкция плазмотрона и проведено его пусковое опробование. Рекомендовано результаты работы применить на остальных растопочных горелках котла. Настоящая статья посвящена опыту модернизации существующей системы безмазутного розжига на Гусиноозерской ГРЭС.
На всех электростанциях группы “Интер РАО”, на которых в качестве растопочного и резервного топлива используется мазут, ведется поиск путей сокращения его потребления, поскольку стоимость этого вида топлива довольно высока – примерно 14 000–15 000 руб/т. Для достижения этой цели инвестируются немалые средства в разработку различных технологий снижения расхода растопочного топлива [1, 2], таких как:
плазменная технология – в ее основе лежит термохимическая подготовка пылеугольного топлива с помощью электрической дуги, возникающей между электродами плазмотрона. Через дугу проходит поток воздуха, образующий плазму, которая нагревает поток смеси сушильного агента – в данном случае воздуха – и угольной пыли (аэросмесь), а также способствует выделению летучих веществ и воспламенению угольной пыли;
электрохимическая технология, которая основана на ионизации аэросмеси путем воздействия на нее высокочастотных электрических полей в предпламенной зоне пылеугольного факела. В результате ионизации в аэросмеси протекают электрохимические процессы, топливо становится химически активным, самовоспламеняется и горит;
муфельная технология – это термическая подготовка пылеугольного топлива в специальных предтопках перед подачей его в топочную камеру котла, происходящая благодаря предварительно разогретым стенкам муфеля;
технология микропомола угля – измельчения топлива до состояния угольной пыли с размером частиц 10–40 мкм, при этом топливо становится более активным и приближает горение пылеугольного топлива к показателям горения газомазутных топлив;
использование синтез-газа, получаемого в результате термического воздействия на уголь в специальных устройствах – газогенераторах.
В частности, специалистами ОАО ВТИ была успешно реализована малозатратная технология более раннего перехода на угольную пыль для Экибастузской ГРЭС-2 при растопке котла, которая заключалась в модернизации сепаратора мельницы, что позволило утонять пыль до R90 = 6% в начальный момент растопки и угрублять ее до номинального значения R90 = 15% после отключения подачи мазута (R90 – остаток на сите с ячейкой 90 мкм, получающийся при просеивании отобранной усредненной пробы пыли; характеризует тонкость помола угля в мельнице).
Системы безмазутного розжига с применением плазмотронов установлены на многих электростанциях стран Европы и Азии, некоторые из них приведены в таблице.
Плазменные топливные системы (ПТС) на ТЭС Евразии [3]
ТЭС, ее местоположение и год ввода в эксплуатацию | Тип × количество котлов с ПТС | Паропроизво-дительность котла, т/ч | Количество ПТС, шт. |
---|---|---|---|
Россия | |||
Гусиноозерская ГРЭС (г. Гусиноозерск, 1994–1995 гг.) | ТПЕ-215 × 2 БКЗ-640 × 2 |
670 640 |
8 7 |
Черепетская ГРЭС (г. Суворов, 1997 г.) | ТП-240 × 1 | 240 | 4 |
Нерюнгринская ГРЭС (г. Нерюнгри, 1997 г.) | КВТК-100 × 1 | 116 МВт | 2 |
Партизанская ГРЭС (г. Партизанск, 1998 г.) | ТП-170 × 1 | 170 | 2 |
Улан-Удэнская ТЭЦ-2 (г. Улан-Удэ, 1997 г.) | ТПЕ-185 × 1 | 160 | 2 |
Хабаровская ТЭЦ-3 (г. Хабаровск, 1998 г.) | ТПЕ-216 × 1 | 670 | 4 |
Украина | |||
Кураховская ТЭС (г. Курахово, 1998–1999 гг.) | ТП-109 × 1 | 670 | 4 |
Мироновская ГРЭС (г. Мироновка, 1989 г.) | ТП-230 × 1 | 230 | 2 |
Казахстан | |||
Алма-Атинская ГРЭС (г. Алма-Ата, 1996 г.) | БКЗ-160 × 1 | 160 | 2 |
Усть-Каменогорская ТЭЦ (г. Усть-Каменогорск, 1989 г.) | ЦКТИ-75 × 2 | 75 | 4 |
Алматинская ТЭЦ-2 (г. Алматы, 2011 г.) | БКЗ-420 × 1 | 420 | 6 |
Монголия | |||
Улан-Баторская ТЭЦ-4 (г. Улан-Батор, 1994 г.) | БКЗ-420 × 8 | 420 | 16 |
Эрдэнэтская ТЭЦ (г. Эрдэнэт, 1995 г.) | БКЗ-75 × 1 | 75 | 1 |
Китай | |||
Баодийская ТЭС (г. Баоди, 1995 г.) | Ч-200 × 1 | 200 | 3 |
Шаогуанская ТЭС (г. Шаогуан, 1999–2001 гг.) | F-220/100-W × 1 К-75 × 1 |
230 75 |
4 1 |
ТЭС “Золотая Гора” (г. Шеньян, 2007 г.) | BG-75/39-M × 1 | 75 | 2 |
ТЭС “Ганшун” (г. Шанси, 2009 г.) | BG-950/150 × 1 | 950 | 4 |
Северная Корея | |||
Восточно-Пхеньянская ТЭС (г. Пхеньян, 1993 г.) | Е-210 × 1 | 210 | 3 |
Словакия | |||
ТЭС “Вояны” (г. Велки-Капушаны, 2000 г.) | TAVICI × 1 | 350 | 2 |
Сербия | |||
Белградская ТЭС “Никола Тесла” (г. Обреновац, 2007 г.) | ТП-210 × 1 | 650 | 16 |
ПРЕДПОСЫЛКИ К ПРОВЕДЕНИЮ РАБОТЫ
Научно-исследовательские и конструкторские работы (НИОКР) по теме “Разработка горелки для плазменной системы розжига с увеличенным ресурсом и повышенной надежностью работы для нужд филиала “Гусиноозерская ГРЭС” АО “Интер РАО – Электрогенерация” были выполнены в 2018–2019 гг. в целях повышения общей надежности плазменной системы – как плазмотрона, так и муфельной горелки. На момент начала работы ресурс катода составлял 100–200 ч в зависимости от марки меди и эксплуатационных условий, а внутренняя часть муфельной горелки при неблагоприятных условиях могла расплавиться после одной растопки. Дополнительно была также поставлена цель разработать такие технические решения, которые позволили бы в дальнейшем полностью исключить сжигание мазута на растопочных режимах.
Существующая система плазменного розжига (рис. 1), внедренная на котле ТПЕ-215 ст. № 5 Гусиноозерской ГРЭС в 1994 г. [3], работает следующим образом: воздух прогоняется через специальное устройство – плазмотрон (рис. 2), где электрической дугой разогревается до температуры плазмы (1500–3000°С). Разогретая плазма поступает в специальное горелочное устройство – муфель (рис. 3), где она смешивается с потоком аэросмеси, который воспламеняется в небольшой части сечения. В процессе движения аэросмеси по каналу муфеля происходит распространение горения на все сечение муфеля и в топку направляется воспламененная угольная пыль с температурой 1200–1400°C, обогащенная продуктами пиролиза угля. Такая технология позволяет производить растопку котла без использования мазута – только путем подачи угольной пыли при условии, что температура аэросмеси достаточна для устойчивого воспламенения угольной пыли. Однако существующая система плазменного розжига имеет определенные недостатки, которые усложняют ее использование:
Рис. 1.
Система безмазутного плазменного розжига. 1 – анод; 2, 2 ' – закруточные кольца для воздуха, подаваемого на катод и анод; 3 – изолятор; 4 – катод; 5 – устройство запуска плазмотрона; 6 – тиристорный преобразователь; 7 – дроссель; 8 – геркон; 9 – электромагнитный клапан; 10 – электрическая дуга; G1, G2 – расход воздуха, подаваемого на катод и анод соответственно
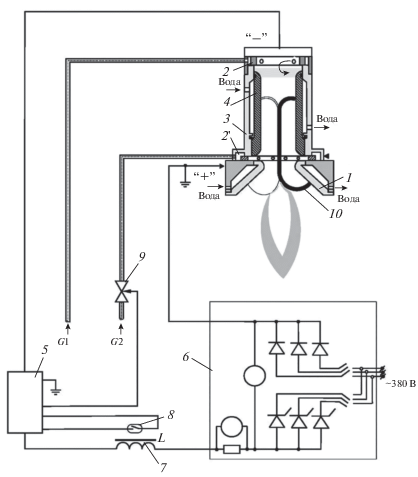
Рис. 3.
Муфельная горелка. 1 – внутренний канал; 2 – тепловая изоляция; 3 – место установки плазмотрона; 4 – водоохлаждаемая рубашка
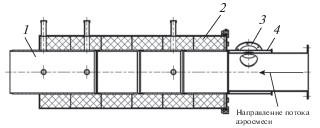
отсутствие дистанционного управления и контроля за работой системы плазменного розжига, что требует привлечения значительного количества персонала на проведение растопочных мероприятий;
несовершенство системы предварительной очистки охлаждающей воды и воздуха, что приводит к отказам плазмотрона из-за забития сопл и технологических проходов продуктами коррозии и различными механическими включениями;
низкая надежность муфеля, связанная с износом материала под действием высоких температур (рис. 4), и электродов плазмотрона под воздействием электрической дуги. Поскольку муфель изготовлен из нержавеющей или жаропрочной стали, его ремонт и восстановление требуют весьма значительных средств;
высокий механический недожог угольной пыли в начальный момент растопки;
отсутствие систем видеоконтроля факела в горелках котла;
необходимость проведения модернизации силовой части питания и элементов системы управления плазмотронов для обеспечения возможности дистанционного управления с блочного щита управления, повышения надежности и ремонтопригодности;
отсутствие средств подогрева как сушильного агента (первичного воздуха), так и угля, применяемого для растопки. При растопке котла из холодного состояния первое время приходится использовать мазут до момента достижения температуры, при которой происходит надежное воспламенение аэросмеси (около 60°С), и только после этого зажигать плазмотроны.
При проведении данной работы предполагалось устранить все указанные недостатки.
ОРГАНИЗАЦИЯ РАБОТЫ
Работа проводилась в три этапа. На первом этапе осуществлялись сбор исходных данных, разработка технических решений и создание рабочей конструкторской документации, на втором этапе – модернизация плазменной системы. На третьем этапе выполнялись доработка, гарантийные испытания опытного образца, корректировка и согласование документации.
На первом этапе работы при выборе путей модернизации системы безмазутного розжига котла (СБРК) были разработаны два варианта конструкции муфельной горелки – с каналом из сплава с высоким содержанием никеля и каналом из огнеупорных изделий (керамических полуколец). На оба варианта исполнения муфельной горелки получены патенты [4, 5]. Для обеспечения высокой надежности и ресурса горелки в качестве опытного образца был выбран муфель с внутренним каналом из хромоникелевого сплава.
Как уже было указано, низкая температура сушильного агента при растопке котла из холодного состояния – это одна из проблем реализации СБРК на Гусиноозерской ГРЭС. Для ее решения было предложено организовать байпасный подогрев части первичного воздуха, идущего в мельницу, в паровых калориферах. Воздух на них планировалось отбирать из общего воздуховода первичного воздуха после воздухоподогревателя, а сбрасывать на участке воздуховодов, идущих к мельнице. Воздух предполагалось нагревать паром из общестанционного коллектора пара собственных нужд (1.3 МПа), а конденсат сбрасывать в трубопровод отвода конденсата калориферов соответствующего котла.
Для повышения стабильности подачи рабочих сред, их очистки и контроля параметров была разработана новая схема питания плазмотронов воздухом и водой. На линиях подвода воды и подачи воздуха были параллельно установлены по два фильтра (для воздуха модульные фильтры 25 мкм Gamozzi MX3-1-F00, для воды косые сетчатые фильтры itap 192 с ячейкой 500 мкм) – один в работе, один в резерве. Степень загрязнения фильтров контролировалась по перепаду давления на них. Кроме того, на линии подвода воздуха был установлен редуктор, позволяющий сглаживать колебания давления в магистрали сжатого воздуха.
Была разработана система автоматического управления на базе контроллеров ОВЕН для дистанционного регулирования расходов воздуха, воды, а также для мониторинга таких параметров работы системы безмазутного розжига, как давление, температура и расходы охлаждающей воды и воздуха, подаваемого на плазмотрон, а также температуры аэросмеси и металла внутренней части муфельной горелки. Шкаф управления показан на рис. 5.
Рис. 5.
Чертеж технологического шкафа для регулирования подачи воды и воздуха на плазмотрон. 1 – вентиль запорный; 2 – косой фильтр; 3 – обратный клапан; 4 – клапан балансировочный; 5 – расходомер ультразвуковой; 6 – термоманометр; 7 – фильтр модульный; 8 – редуктор давления; 9 – клапан регулировочный; 10 – электрический привод; 11 – расходомер
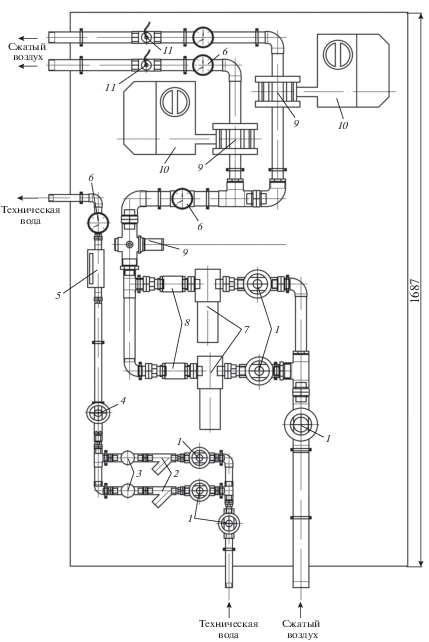
Для контроля факела проектом предусмотрена установка промышленных видеокамер над каждой растопочной горелкой.
По условиям НИОКР на втором этапе работы требовалось изготовить и смонтировать элементы СБРК для одной горелки. Помимо обязательной поставки новых плазмотрона и муфеля, необходимо было провести модернизацию существующей СБРК без использования предварительного подогрева воздуха паровым калорифером и при условии сохранения существующей системы питания плазмотронов (эти работы планируется выполнить в будущем). В ОАО ВТИ были изготовлены показанные на рис. 6 образец муфельной горелки, технологический шкаф питания плазмотронов воздухом и водой, шкаф системы управления СБРК, а также разработана оболочка управления системой АСУ ТП СБРК на базе программного обеспечения CoDeSys. В Институте физического материаловедения (ИФМ СО РАН) был изготовлен плазмотрон Циклон-800, после чего элементы СБРК были поставлены и смонтированы на энергоблоке № 5 Гусиноозерской ГРЭС. Непосредственно на котле произведены все подключения по рабочим средам, электрической части и контрольно-измерительным приборам. Проверена работоспособность плазмотрона, системы АСУ ТП, проведены пусконаладочные испытания по части подачи и регулирования рабочих сред.
На третьем этапе были выполнены испытания на работающем оборудовании с подачей угольной пыли в муфельную горелку и исправлены недостатки, не учтенные на стадии проектирования, а именно: доработаны место установки плазмотрона и сопряжение его фланцев с муфельной горелкой; также по согласованию со специалистами станции принято решение заменить тип кабелей для работы системы автоматического управления, проведены гарантийные ресурсные испытания системы безмазутного розжига котла, в соответствии с которыми она должна проработать не менее 24 ч (четыре потенциальные растопки котла).
Испытания проводили при минимальной нагрузке генератора турбины энергоблока № 5, составляющей 130 МВт. При этом в пылепроводе поддерживали скорость аэросмеси 20–25 м/с, необходимую для оптимального взаимодействия плазмы и угольной пыли. Коэффициент избытка воздуха в канале аэросмеси αаэр составлял около 0.3. Также проверяли возможности работы оборудования при различной токовой нагрузке плазмотрона. Всего было проведено четыре опыта при рабочем токе плазмотрона 250, 300 и 400 А. В процессе испытаний был реализован алгоритм, позволяющий существенно увеличить ресурс плазмотрона благодаря постоянному изменению положения точки примыкания электрической дуги к поверхности катода. При этом расход воздуха на катод непрерывно изменяли в автоматическом режиме от 15 до 22 м3/ч (при нормальных условиях) в зависимости от времени. Граничные значения расхода воздуха были получены опытным путем на основании внутреннего осмотра катода. Поскольку определить зону действия электрической дуги на поверхность катода можно, только вскрыв плазмотрон, то после каждого опыта плазмотрон снимали, разбирали и осматривали. При осмотре отмечалось, на каком участке поверхности катода происходил износ от воздействия электрической дуги. В зависимости от места расположения зоны износа принимали решение об увеличении/уменьшении минимального и максимального расхода воздуха, подаваемого на катод. После следующего испытания (с новыми расходами воздуха на катод) действия повторяли. Расход воздуха на анод был постоянным и составлял 35 м3/ч.
После каждого опыта (6–7 ч работы) производили осмотр плазмотрона и его чистку. Также в процессе опыта визуально контролировали состояние плазмотрона, выполняли пирометрию его поверхности и корпуса муфельной горелки с помощью пирометра Fluke. После 8 ч работы температура корпуса плазмотрона не превышала 65°С, а корпуса муфельной горелки – 140°С. Особое внимание при осмотре уделяли катоду плазмотрона и внутренней части муфельной горелки, так как это основные части СБРК, которые подвергаются износу.
Первые два опыта выполняли при рабочем токе плазмотрона 250 А (штатный режим для этого котла). После первого опыта (6 ч работы) износ катода был совсем незначительным, анодная и катодная камеры были чистыми, без следов мазута, после второго опыта стал заметен износ катода. За 12 ч работы (два опыта с током 250 А) глубина борозд от воздействия дуги на катод составила менее 0.5 мм (рис. 7). После 12 ч работы системы с током 250 А проверялась возможность работать с токами 300 и 400 А (по 6 ч). Однако по сравнению со штатным режимом работы износ катода оказался повышенным, поэтому экстраполяция результатов по скорости износа катода проводилась по опытным данным, полученным при рабочем токе 250 А. Таким образом, экстраполируя результаты испытаний относительно скорости износа катода при работе плазмотрона с током 250 А на реальные условия, можно с уверенностью сказать, что при толщине стенки катода 13 мм и текущих настройках воздушного режима минимальный срок его службы составит не менее 288 ч.
Следует отметить, что ширина поверхности катода, на которую воздействовала дуга, равнялась 3 см при безопасной рабочей поверхности катода 10–12 см (участок поверхности катода, на котором исключены прилипание дуги к завихрителю с одной стороны катода и срыв ее с другой стороны). Дело в том, что электрическая дуга притягивается к завихрителю и не может уйти от него в обратную сторону. В результате от ее воздействия завихритель быстро приходит в неработоспособное состояние. При более точной наладке воздушного режима, позволяющей более эффективно использовать поверхность катода благодаря выбору оптимальных расходов воздуха, минимальный срок службы может быть увеличен до 850 ч. После успешных испытаний с током 250 А было принято решение проверить работу плазмотрона на более нагруженных режимах (с токами 300 и 400 А). При увеличении тока дуги эффективность воспламенения угольной пыли возрастает, но повышаются износ электродов и нагрузка на схему питания плазмотрона.
Испытания показали, что существующее состояние оборудования позволяет надежно работать с током электрической дуги 300 А, а при увеличении тока до 400 А наблюдался разогрев дросселя, что создавало опасность выхода из строя системы электрического питания. Возможность выхода из строя системы электрического питания требует проверки в части эффективности воспламенения угольной пыли при холодном состоянии котла, поскольку на работающем котле ее воспламенение происходит также в результате воздействия горячих газов и лучистого потока из топки. Возможность такой проверки появится после модернизации всего комплекта растопочных горелок (4 шт.) и установки калорифера для подогрева первичного воздуха перед молотковой тангенциальной мельницей.
При визуальном осмотре внутренней части муфеля (рис. 8) было отмечено, что за все время испытаний его состояние не изменилось (темный прямоугольник на рис. 8, б – это отложение угольной пыли), что подтверждает правильность выбранного решения по ее исполнению. Таким образом, цель работы – увеличение ресурса плазмотрона и муфельной горелки – была достигнута.
ВЫВОДЫ
1. Модернизированная система безмазутного розжига котла, установленная на одной горелке, успешно прошла ресурсные испытания и показала свою работоспособность при работе с токами электрической дуги 250 и 300 А.
2. Для полноценных пусков котла без использования мазута следует провести дальнейшую модернизацию оставшихся трех горелочных устройств с учетом реализации всех предложенных технических решений по СБРК, разработанных на первом этапе работы, включая предварительный подогрев воздуха.
3. В дальнейшем для достижения наиболее эффективной и долговечной работы системы безмазутного плазменного розжига потребуются более тщательная наладка ее воздушного режима и модернизация системы питания плазмотронов.
Список литературы
Современные тенденции котлостроения: материалы II Междунар. науч.-практ. конф. студентов, аспирантов и молодых ученых. Барнаул, 22 марта 2018 г. Барнаул: Изд-во АЛТ ГТУ, 2018. С. 115–132.
Исследование возможностей использования синтез-газа для стабилизации горения факела пылеугольных котлов / В.В. Афанасьев, В.Г. Ковалев, В.А. Тарасов, С.Н. Алексеев // Вестник Чуваш. ун-та. 2012. № 3. С. 100–104.
Использование плазменно-топливных систем на пылеугольных ТЭС Евразии / Е.И. Карпенко, Ю.Е. Карпенко, В.Е. Мессерле, А.Б. Устименко // Теплоэнергетика. 2009. № 6. С. 10–14.
Пат. RU 193860 U1. Огнеупорный канал горелочного устройства для плазменного воспламенения топлива горелок теплового агрегата / А.В. Штегман, Д.В. Сосин, И.А. Рыжий, Д.В. Степанишин, Е.А. Фоменко, А.Ю. Толочков, Ю.М. Вьюшина. Патентообладатель АО “Интер РАО – Электрогенерация”. Заявка № 2019118742 от 17.06.2019 // Б.И. 2019. № 32. Опубл. 19.11.2019.
Пат. RU 193861 U1. Огнеупорный канал горелочного устройства для плазменного воспламенения топлива горелок теплового агрегата / А.В. Штегман, Д.В. Сосин, И.А. Рыжий, Д.В. Степанишин, Е.А. Фоменко, А.Ю. Толочков, Ю.М. Вьюшина. Патентообладатель АО “Интер РАО – Электрогенерация”. Заявка № 2019118744 от 17.06.2019 // Б.И. 2019. № 32. Опубл. 19.11.2019.
Дополнительные материалы отсутствуют.
Инструменты
Теплоэнергетика