Теплоэнергетика, 2021, № 6, стр. 103-109
Безопасность и эксплуатационная надежность тепломеханического оборудования
Е. А. Гринь a, *, А. В. Пчелинцев a, К. К. Крейцер a, В. И. Бочкарев a, **, Р. Н. Калугин a
a Всероссийский теплотехнический институт
115280 Москва, Автозаводская ул., д. 14, Россия
* E-mail: EAGrin@vti.ru
** E-mail: VIBochkarev@vti.ru
Поступила в редакцию 12.10.2020
После доработки 21.10.2020
Принята к публикации 18.11.2020
Аннотация
Разработка и освоение в конце прошлого века новых жаропрочных хромистых сталей мартенситного класса обеспечили переход теплоэнергетики на температуру пара 600–620°С. Производство оборудования из этих сталей поддерживается необходимой нормативной базой, и имеется положительный опыт его длительной эксплуатации. Анализ и обобщение результатов испытаний сталей Р91 и Ди82 на длительную прочность показали соответствие полученных значений требованиям российских и европейских стандартов для их применения при повышенных параметрах пара. Однако при температурах менее 550°С жаропрочные свойства этих сталей несколько ниже уровня, регламентированного европейским стандартом. В результате регрессионного анализа массива экспериментальных данных предложена аппроксимация в виде многочлена пятой степени, устанавливающая зависимость ресурса от температуры и напряжения для сталей Р91 и Ди82. При проведении в ВТИ исследований получены основные закономерности развития процессов деформирования и разрушения таких сталей в условиях ползучести. Установлены конкретные соотношения между накопленной деформацией ползучести и степенью микроповрежденности металла в привязке к доле выработанного ресурса. Эти результаты легли в основу разрабатываемой классификационной шкалы микроповреждаемости хромистой стали в ходе длительной эксплуатации. Практическое использование этой шкалы открывает возможность оценить стадию выработки ресурса по результатам планового диагностирования, что способствует повышению эксплуатационной надежности оборудования, изготовленного из хромистых сталей мартенситного класса. В России и других промышленно развитых странах создана научно-техническая база для производства перспективного оборудования из новых хромистых сталей, обеспечивающих возможность его эксплуатации при температурах до 640°С. Требуется продолжить исследования служебных характеристик этих новых сталей в целях их дальнейшего совершенствования и последующего внедрения в производство.
В настоящее время для обеспечения служебных характеристик металла, минимально необходимых для надежной и безопасной эксплуатации тепломеханического оборудования ТЭС, актуальны два основных аспекта:
безопасность работы оборудования, введенного в эксплуатацию 40–50 лет назад, имеющего длительную и сверхдлительную наработку;
надежность оборудования, изготовленного из новых конструкционных сталей и запущенного в эксплуатацию в последнее десятилетие.
Каждый из этих аспектов характеризуется своей спецификой, и рассматривать их надо по отдельности. Еще один важный вопрос связан с материалами для оборудования, разрабатываемого на перспективу, в частности для энергоустановок на супер- и ультрасверхкритические параметры пара.
Проблеме безопасности и надежности длительно эксплуатируемого оборудования было посвящено немало исследований [1–4]. Можно констатировать, что применительно к указанному оборудованию к настоящему времени принципиально разрешены основные научно-технические вопросы, связанные с надежностью металла и стабильностью его служебных свойств. Однако, коль скоро такое оборудование продолжает работать и, судя по всему, будет эксплуатироваться еще немалое время, сохраняют актуальность задачи технического диагностирования старого оборудования и оценки его состояния по критериям эксплуатационной надежности металла.
В конце XX в. были освоены и нашли широкое применение паровые энергоблоки с перегревом пара до 600–620°C. Это стало возможным благодаря созданию и распространению жаропрочных сталей с содержанием хрома 9–10%. В странах Европейского союза и США это стали X10CrMoVNb9-1 (P91) и X10CrWMoVNb9-2 (P92), в России – стали 10Х9МФБ (Ди82) и 10Х9В2МФБР-Ш (при этом стали Р91 и Ди82, а также Р92 и 10Х9В2МФБР-Ш являются аналогами). Несколько позднее аналогичные стали были разработаны и освоены в Японии, Китае и некоторых других странах. Основными легирующими элементами этих сталей, помимо хрома, служат молибден, ванадий и ниобий, а стали Р92 и 10Х9В2МФБР-Ш дополнительно легированы вольфрамом и микролегированы азотом, бором и церием. Благодаря заданному химическому составу в сочетании со специальной термической обработкой создается структура отпущенного мартенсита, а также мелкодисперсных карбидов и карбонитридов, обеспечивающих дисперсионное твердение стали. В результате структурных превращений, реализуемых в ходе закалки и отпуска, формируется мартенситная структура с достижением оптимального баланса прочностных и пластических свойств. Повышению жаропрочных свойств хромистых мартенситных сталей способствует также высокая плотность дислокаций, стабилизированных частицами мелкодисперсных фаз. Эти стали позиционировались разработчиками как оптимальные к применению для необогреваемых трубопроводных систем: сталь Р91 и Ди82 до температуры 600°C, сталь Р92 и 10Х9В2МФБР-Ш – до 620°C. В России около 10 лет назад был введен в эксплуатацию первый паропровод из стали Р91 на одной из электростанций ПАО “Мосэнерго”, а немногим позднее – из стали Ди82 на энергоблоке № 3 Харанорской ГРЭС. В последующем эти стали использовались в качестве конструкционного материала на многих энергоустановках с расчетной температурой 570–580°С, а для отдельных элементов – до 600°С. Применение таких сталей для элементов с более низкой (до 560°C) температурой позволяет существенно увеличить ресурс оборудования и сократить его металлоемкость.
АНАЛИЗ ХАРАКТЕРИСТИК ДЛИТЕЛЬНОЙ ПРОЧНОСТИ ВЫСОКОХРОМИСТЫХ СТАЛЕЙ
Промышленное освоение хромистых сталей сопровождалось изучением их служебных свойств и структурных изменений при ползучести [5–10]. Повышенное внимание уделялось определению характеристик длительной прочности сталей Р91 и Р92 [5], в результате чего была создана база данных их жаропрочных свойств в рабочем диапазоне температур, которая дополнялась по мере получения новых экспериментальных данных с длительными временами экспозиции [5, 11]. В России работа по актуализации пределов длительной прочности стали Ди82/Р91 для различных температур и ресурсных баз была проведена и оформлена решением трех ведущих научно-исследовательских институтов: ЦНИИТМаш, ЦКТИ и ВТИ.
В ходе проведенной под эгидой Европейского комитета по ползучести (ECCC) работы по анализу и обобщению результатов испытаний на длительную прочность стали Р91, полученных в ведущих мировых исследовательских лабораториях [5], были практически устранены имеющиеся расхождения в жаропрочных свойствах этой стали [12]. В итоге существенно сблизились актуализированные данные по пределам длительный прочности, представленные в европейских нормах, стандарте ASME и принятые на текущее время в России.
В последнее десятилетие в ВТИ выполнен комплекс исследований сталей Р91, Ди82 и Р92, в том числе в рамках сертификационных испытаний поставляемых из-за рубежа паропроводов [13]. Полученные характеристики длительной прочности стали Р91 полностью соответствуют требованиям EN 10216-2 [12] для трубопровода свежего пара. Жаропрочность металла гибов из этих труб и элементов паропроводов горячего промежуточного перегрева хотя и оказалась несколько ниже требований [12], но находилась в пределах допускаемых отклонений. При этом показательно, что результаты испытаний металла всех вышеуказанных паропроводных элементов соответствовали регламентированной российским стандартом [14] длительной прочности сталей Р91 и Ди82. Длительная прочность сварных соединений элементов из стали Р91 ниже, чем основного металла, при этом их коэффициент прочности составляет не менее 0.7. Для металла и в определенной мере сварных соединений паропроводов из стали Р91 характерно довольно высокое сопротивление хрупкому разрушению [13].
Результаты обобщения жаропрочных испытаний сталей Р91 и Ди82, проведенных за последнее десятилетие в ВТИ, показаны на рис. 1. Кривая 1 представляет собой зависимость, аппроксимирующую массив приведенных экспериментальных данных, соотношением (апробированным для перлитных сталей) вида
(1)
$\lg {{\tau = }}\frac{1}{T}\sum\limits_{i = 0}^5 {{{A}_{i}}{{{\left( {\frac{{n\sigma }}{{10}}} \right)}}^{i}}} + 2\lg T - a,$Рис. 1.
Зависимости длительной прочности σ от параметра Трунина ${{\bar {P}}}$ сталей Р91и Ди82. 1 – экспериментальные данные и соответствующая регрессионная кривая; 2 – кривая согласно российским нормам; 3 – зависимость по актуализированным данным EN 10216-2
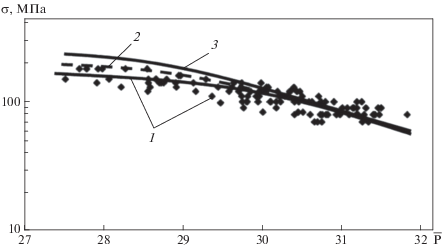
Кривая 2 – это аппроксимация длительной прочности сталей Р91 и Ди82 согласно российским нормам, кривая 3 – зависимость длительной прочности стали Р91, полученная пересчетом через параметр Трунина ${{\bar {P}}}$ соответствующей базовой кривой европейских норм в их актуализированной версии [5]. Определенные в результате регрессионного анализа экспериментальных данных коэффициенты в выражении (1) составили:
A0 ..........................................................45 598.546 |
A1 ..........................................................–6135.720 |
A2 .............................................................1090.115 |
A3 ..............................................................–99.116 |
A4 ..................................................................4.368 |
A5 ...............................................................–0.075 |
a ........................................................................36 |
Анализ данных, приведенных на рис. 1, свидетельствует о том, что в нижней и средней частях диаграммы длительной прочности результаты экспериментов (банк данных ВТИ) и аппроксимация 1 практически совпадают с кривыми длительной прочности в представленной интерпретации согласно российским (2) и европейским (3) нормам. При повышенных (более 110 МПа, см. рис. 1) значениях длительной прочности указанные три зависимости начинают расходиться, причем зависимость 1, аппроксимирующая массив экспериментальных данных, отклоняется от российских (2) и в еще большей степени от европейских (3) норм в сторону снижения характеристик длительной прочности. Участок диаграммы с расходящимися жаропрочными свойствами соответствует области температур ниже 550°С [15].
ОПЫТ ЭКСПЛУАТАЦИИ ОБОРУДОВАНИЯ, ИЗГОТОВЛЕННОГО ИЗ ВЫСОКОХРОМИСТЫХ СТАЛЕЙ
Важное место в обеспечении эксплуатационной надежности оборудования, изготовленного из хромистой стали, занимают проблемы повреждаемости металла и сварных соединений и оценка их состояния по результатам диагностирования. Наработка такого оборудования на электростанциях зарубежных стран достигла 200 тыс. ч, в России она приблизилась к 100 тыс. ч. Зарубежные публикации свидетельствуют о том, что опыт эксплуатации оборудования, изготовленного из высокохромистых сталей, в целом дал положительные результаты. Однако следует обратить внимание на имеющиеся повреждения деталей, выполненных из этих сталей [16–18]. Сталь Р91, которая, несомненно, обладает большей жаропрочностью, чем перлитные стали, и лучше сопротивляется ползучести при высоких температурах, в то же время является проблемной из-за своей невысокой технологичности. Это усложняет выполнение таких операций, как сварка и формообразование. Наибольшей повреждаемостью отличаются сварные соединения, в особенности разнородные соединения элементов, изготовленных из мартенситной и перлитной сталей [19]. Это объясняется различием свойств и структурными особенностями указанных сталей и спецификой их превращений в ходе термического цикла сварки [13].
Несмотря на сравнительно небольшие наработки изготовленного из хромистой стали оборудования, в России уже имеются сведения о повреждениях сварных соединений элементов, выявленных на отечественных ТЭС при монтаже и в процессе эксплуатации [20]. Как правило, эти повреждения вызваны нарушениями технологии сварки при монтаже. Проведенные в ВТИ исследования свидетельствуют о том, что разрушение сварных соединений паропроводов, выполненных из хромистой стали, в условиях ползучести локализуется в разупрочненной зоне примерно на расстоянии 1.5–2.5 мм от линии сплавления. Как правило, такое разрушение имеет межзеренную структуру и происходит без накопления заметной пластической деформации. Повреждение сварного соединения в условиях ползучести происходит из-за возникновения на межзеренных границах разупрочненной зоны микропор ползучести, их роста и выстраивания вдоль границ зерен с последующим образованием микротрещины [13, 19]. Процесс разрушения сопровождается охрупчиванием металла вблизи шва. Это особенно характерно для разнородных сварных соединений. Важными результатами исследований сварных соединений хромистых сталей, которые ведутся в ВТИ и других организациях, будут создание шкалы микроповрежденности при ползучести для зон сварных соединений, в том числе разнородных, а также разработка восстановительных технологий их ремонта при эксплуатации.
КИНЕТИКА НАКОПЛЕНИЯ ДЕФОРМАЦИИ И МИКРОПОВРЕЖДЕННОСТИ В ХРОМИСТОЙ СТАЛИ ПРИ ПОЛЗУЧЕСТИ
Разумеется, проблема эксплуатационной надежности оборудования, изготовленного из хромистых сталей, не ограничивается только сварными соединениями. С учетом специфики свойств мартенситной стали [17, 18] необходимо организовать системный эксплуатационный контроль изготовленных из нее элементов. Этот контроль должен включать микроструктурный анализ металла при различных наработках с изучением накопления поврежденности в мартенситной стали при длительном нагружении в условиях ползучести.
Цикл таких исследований был выполнен в Центре коллективного пользования ВТИ на металле паропроводного гиба диаметром примерно 324 мм из стали Р91 в состоянии поставки. Методически исследование было организовано следующим образом: проведение длительных испытаний на ползучесть в режиме периодического прерывания эксперимента по достижению очередного заданного уровня деформации ползучести, кратного 1%, изучение микроструктуры металла. Испытания образцов проводили в интервале температур 580–630°C при напряжениях от 80 до 150 МПа.
Результаты этих исследований представлены на рис. 2, где в относительных координатах показана кривая ползучести, построенная в обобщенной форме (без экспериментальных точек с разбросом по различным испытанным образцам). Предельная (конечная) деформация ползучести при разрушении образцов ${{\varepsilon }_{{\text{р}}}}$ варьировалась в умеренном диапазоне и составляла в среднем около 20%. Также на рис. 2 приведены фотографии микроструктуры металла, соответствующие различной накопленной деформации ε и долям выработки ресурса (указанная цена деления масштабной линейки соответствует 20 мкм).
Рис. 2.
Кривая ползучести и изменения микроструктуры (микроповрежденности) стали Р91/Ди82 по мере накопления деформации ползучести и исчерпания ресурса ${{{\tau }} \mathord{\left/ {\vphantom {{{\tau }} {{{{{\tau }}}_{{\text{р}}}}}}} \right. \kern-0em} {{{{{\tau }}}_{{\text{р}}}}}}.$ 1–5 – микроповрежденность металла на различных стадиях исчерпания ресурса; τ – текущее время испытания; ${{{{\tau }}}_{{\text{р}}}}$ ‒ время до разрушения образца, ч; ε –текущая деформация ползучести; ${{{{\varepsilon }}}_{{\text{р}}}}$ – конечная деформация ползучести с разрушением образцов
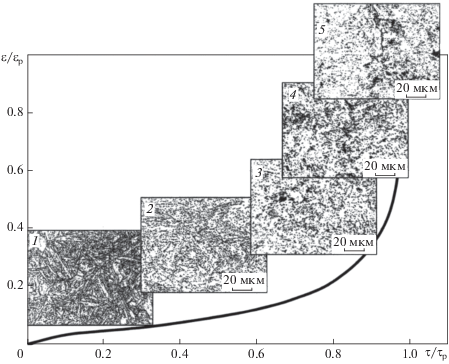
Анализ кинетики накопления микроповрежденности при развитии процесса ползучести свидетельствует: накопленная деформация на уровне 1%, что составляет около 0.05 по приведенной деформации (по оси ${\varepsilon \mathord{\left/ {\vphantom {\varepsilon {{{\varepsilon }_{{\text{р}}}}}}} \right. \kern-0em} {{{\varepsilon }_{{\text{р}}}}}}$), соответствует первой стадии кривой ползучести и доле выработки ресурса примерно 0.1. Микроповрежденность металла на этом этапе испытаний отсутствует – фото 1 на рис. 2. С увеличением деформации до 2 и далее до 3% приведенная деформация составляет 0.10–0.15 и кривая выходит на второй участок, т.е. на стадию установившейся ползучести. Здесь деформирование достигает 0.60–0.65 выработки ресурса. На этой стадии появляются сначала отдельные поры ползучести размером от 0.1 мкм, а далее по мере нарастания деформации их размеры и количество квазимонотонно увеличиваются. Местом зарождения микропор являются карбиды, и по мере увеличения концентрации пор они выстраиваются по границам зерен и блоков (фото 2). Эта стадия развития процесса захватывает почти весь участок стационарной (установившейся) ползучести. С наращиванием деформации до 4%, что составляет около 0.2 по шкале приведенной деформации $\left( {{\varepsilon \mathord{\left/ {\vphantom {\varepsilon {{{\varepsilon }_{{\text{р}}}}}}} \right. \kern-0em} {{{\varepsilon }_{{\text{р}}}}}}} \right),$ в микроструктуре прослеживается дальнейшее увеличение количества (плотности) микропор, а их размеры возрастают уже до 1.2 мкм (фото 3). Этой фазой процесса развития деградации металла заканчивается стадия стационарной ползучести и начинается плавный выход на третью стадию – ускоренной ползучести. Доля выработки ресурса на этом участке кривой ползучести составляет 0.75–0.80.
При достижении деформацией 5–6%, т.е. когда приведенная деформация равна примерно 0.25–0.30, процесс полностью входит в третью стадию ускоренной ползучести. Микроструктура металла на этой стадии характеризуется наличием цепочек слившихся микропор, выстроившихся по границам зерен, при этом порам свойственна неправильная конфигурация, а их размеры становятся весьма значительными (фото 4). На данной стадии процесса развития повреждения металла доля исчерпания ресурса составляет 0.8–0.9 полного времени до разрушения. Дальнейшее увеличение деформации (свыше 6% или при приведенной деформации более 0.3) на заключительном этапе испытаний происходит ускоренными темпами, что иллюстрируется резким подъемом кривой ползучести и, по сути, соответствует стадии предразрушения. На этой стадии в микроструктуре металла отмечаются отдельные, в том числе слившиеся, микротрещины (фото 5), что свидетельствует о потере металлом работоспособности. Оставшаяся доля ресурса металла до полного его исчерпания на этой стадии ползучести составляет менее 0.1.
Результаты таких исследований создают основу для разработки классификационных шкал микроповреждаемости хромистых мартенситных сталей в условиях ползучести и установления критериев по допустимому накоплению деформации и микроповрежденности в привязке к исчерпанию ресурса металла.
РАЗРАБОТКА И ОСВОЕНИЕ НОВЫХ МАТЕРИАЛОВ ДЛЯ ПЕРСПЕКТИВНОГО ОБОРУДОВАНИЯ
Дальнейшее развитие ТЭС неразрывно связано с повышением параметров пара и созданием необходимых для этого материалов. Несмотря на определенный пессимизм некоторых европейских стран в отношении перспектив тепловых электростанций, их использование и совершенствование будет неизбежной реальностью и предметом серьезных дорогостоящих работ. Исследователи из разных стран мира рассматривали температуры пара до 760°C и давления до 30–35 МПа. Несмотря на определенные успехи в этом направлении, промышленное использование оборудования с такими параметрами – вопрос не ближайших лет. В то же время в промышленно развитых странах сформирована научная и техническая основа для создания и практического применения энергоустановок с рабочей температурой до 650°C. Для изготовления высокотемпературного оборудования таких установок могут применяться уже освоенные хромистые стали с существенно повышенной жаропрочностью: как Р92 (X10CrWMoVNb9-2) и Е911 (X11CrMoWVNb9-1-1), так и отечественная сталь 10Х9В2МФБР. Для них существует необходимая нормативная поддержка, хотя отдельные служебные характеристики этих сталей со временем могут быть скорректированы [7, 9, 13, 16]. Их исследования надо продолжать для дальнейшего совершенствования и отработки системы критериев эксплуатационной надежности.
Существенным шагом в разработке новых сверхжаропрочных сталей для теплоэнергетики стала европейская программа COST 536, направленная на создание энергоблоков с температурой пара 640/650°C. В ходе ее выполнения были разработаны новые стали, наиболее перспективная из которых, марки VM12, в качестве легирующего элемента содержала кобальт. Затем на ее базе была создана более перспективная модификация – сталь VM12-SHC, уже опробованная в промышленной эксплуатации при температурах до 650°C. Аналогичного класса хромистая сталь марки 10Х9К3В2МФБР, также легированная кобальтом, разработана в России НПО ЦНИИТМаш. Ее аттестационные исследования позволяют рассчитывать на применение при рабочей температуре до 640–650°C [7].
ВЫВОДЫ
1. Имеется положительный опыт длительной эксплуатации хромистой жаропрочной стали, обеспечившей в конце прошлого века выход тепловой энергетики на более высокие параметры пара: давление свыше 26 МПа, температуру не менее 600°С. Обобщение экспериментальных данных по длительной прочности стали Р91/Ди82 подтверждает в целом ее соответствие требованиям отечественных норм.
2. Проведенные специалистами ВТИ исследования кинетики накопления деформации и микроповрежденности этой стали в условиях ползучести создали основу для разработки классификационной шкалы микроповреждаемости хромистой стали при длительной эксплуатации.
3. В промышленно развитых странах и в России разработаны хромистые стали нового поколения, пригодные для изготовления энергетического оборудования с температурой пара до 650°С. Для освоения и промышленного внедрения этих сталей необходимы всесторонние исследования их служебных характеристик и создание надежной нормативной поддержки.
Список литературы
Березина Т.Г., Трунин И.И. Взаимосвязь предельно допустимой деформации ползучести с поврежденностью материала паропроводов // Металловедение и термическая обработка металлов. 1980. № 12. С. 24–29.
Злепко В.Ф., Меламед М.М., Швецова Т.А. Особенности длительного разрушения теплостойких сталей в условиях ползучести // Металловедение и термическая обработка металлов. 1980. № 12. С. 16–21.
Бугай Н.В., Березина Т.Г., Трунин И.И. Работоспособность и долговечность металла энергетического оборудования. М.: Энергоатомиздат, 1994.
Maharaj C., Dear J.P., Morris A. A review of methods to estimate creep damage in low-alloy steel power station steam pipes // Strain. 2009. V. 45. P. 316–331. https://doi.org/10.1111/j.1475-1305.2008.00465.x
New ECCC assessment of creep rupture strength for steel grade X10CrMoVNb9-1 (Grade 91) / W. Bendick, L. Cipolla, J. Gabrel, J. Hald // Int. J. Pressure Vessels Piping. 2010. V. 87. Is. 6. P. 304–309. https://doi.org/10.1016/j.ijpvp.2010.03.010
Characterization of microstructures across the heart-affected zone of the modified 9Cr-1Mo weld joint to understand its role in promoting type IV cracking / K. Laha, K.S. Chandravathi, P. Parameswaran, K. Bhanu Sankara Rao, S.L. Mannan // Metall. Mater. Trans. A. 2007. V. 38(1). P. 58–68. https://doi.org/10.1007/s11661-006-9050-0
Дуб А.В., Скоробогатых В.Н., Щенкова И.А. Новые жаропрочные хромистые стали для перспективных объектов тепловой энергетики // Теплоэнергетика. 2008. № 7. С. 53–58.
Резинских В.Ф., Пчелинцев А.В. Исследование служебных характеристик стали 10Х9В2МФБР-Ш // Теплоэнергетика. 2010. № 1. С. 31–36.
Новые жаропрочные стали для блоков с суперсверхкритическими параметрами пара / В.Н. Скоробогатых, И.А. Щенкова, П.А. Козлов, Т.В. Тыкочинская, М.С. Нахабина, В.А. Дуб // Тяжелое машиностроение. 2011. № 3. С. 29–34.
Hald J. Microstructure and long-term creep properties of 9–12% Cr steels // Int. J. Pressure Vessels Piping. 2008. V. 85. Is. 1–2. P. 30–37. https://doi.org/10.1016/j.ijpvp.2007.06.010
Ямамото К. Угольные котлы для перспективных энергоблоков на суперсверхкритические параметры (ССКП) // Электрические станции. 2019. № 5. С. 8–11. https://doi.org/10.34831/EP.2019.1054.44166
CEN EN 10216-2:2013+A1-2019. Seamless steel tubes for pressure purposes – Technical delivery conditions. Part 2: Non-alloy and alloy steel tubes with specified elevated temperature properties. EN 10216-2. CEN, 2002. http://docs.cntd.ru/document/564111128
Исследования структуры и свойств металла главных паропроводов энергоблока ПГУ-420, изготовленных из высокохромистой стали марки 10CrMoVNb9-1 (Р91) / Е.А. Гринь, А.Е. Анохов, А.В. Пчелинцев, Э.-Т. Крюгер // Теплоэнергетика. 2016. № 7. С. 20–30. https://doi.org/10.1134/S004036361607002X
СТО ЦКТИ 10.003–2007. Трубопроводы пара и горячей воды тепловых станций. Общие технические требования к изготовлению (с изменениями № 1, 2, 3). Дата введения 01.09.2009. СПб.: ООО ИПП “Ладога”, 2010. http://docs.cntd.ru/document/1200064958
Длительная прочность металла и ресурсные характеристики паропроводов из хромистых сталей / Е.А. Гринь, В.И. Бочкарев, А.В. Пчелинцев, К.К. Крейцер // Электрические станции. 2019. № 5. С. 45–49. https://doi.org/10.34831/EP.2019.1054.44172
Boder M., Thumer J.R., Glassenap K. 9% chromium steel P91 and P92 in German power plants – from 1991 to the present day // VGB Power Tech. 2013. № 7. P. 51–58.
Попов А.Б. Некоторые особенности практического применения изделий из стали класса Р91 [1] (обзор публикаций) // Энергетик. 2015. № 2. С. 49–55.
Попов А.Б. Некоторые практические аспекты применения стали класса Р91 в российской энергетике // Энергетик. 2016. № 1. С. 49–55.
Formation mechanism of type IV failure in high Cr ferritic heat-resistant steel-welded joint / Y. Liu, S. Tsukamoto, T. Shirane, F. Abe // Metall. Mater. Trans. A. 2013. V. 44. P. 4626–4633. https://doi.org/10.1007/s11661-013-1801-0
Деменин М.Ф. О ремонте сварных соединений из хромистых жаропрочных сталей Т91/Р91 во время эксплуатации // Электрические станции. 2018. № 11. С. 24–27.
Дополнительные материалы отсутствуют.
Инструменты
Теплоэнергетика