Теплоэнергетика, 2021, № 6, стр. 55-67
Опытно-промышленные испытания горнового газификатора
И. А. Рыжий a, *, А. В. Штегман a, А. Н. Тугов a, Д. А. Сиротин a, М. М. Гутник a, Е. А. Фоменко a, Д. В. Сосин a, К. В. Тимашков a, С. В. Алексеенко b, c, А. С. Заворин b, В. Е. Губин b, А. С. Матвеев b, Д. В. Гвоздяков b, К. Б. Ларионов b, С. А. Янковский b, К. В. Слюсарский b
a Всероссийский теплотехнический институт
115280 Москва, Автозаводская ул., д. 14, Россия
b Национальный исследовательский Томский политехнический университет
634050 г. Томск, просп. Ленина, д. 30, Россия
c Институт теплофизики им. С.С. Кутателадзе СО РАН
630090 г. Новосибирск, просп. Академика Лаврентьева, д. 1, Россия
* E-mail: ryzhy1987@mail.ru
Поступила в редакцию 20.05.2020
После доработки 22.10.2020
Принята к публикации 18.11.2020
Аннотация
Газификация является одной из перспективных технологий использования твердого топлива в энергетике, химической промышленности и ряде смежных отраслей. Несмотря на значительный задел в виде теоретических и экспериментальных работ в России, одним из ключевых факторов, ограничивающих внедрение технологий газификации, остается недостаток практического опыта в промышленных или приближенных к ним условиях. Для его получения осенью 2019 г. в г. Томск на базе научно-исследовательского центра “Экоэнергетика 4.0” сотрудниками Томского политехнического университета (ТПУ) впервые в России были проведены испытания разработанного в ОАО “Всероссийский теплотехнический институт” (ВТИ) опытно-промышленного горнового газификатора производительностью по топливу 4 т/ч с использованием углей четырех марок Кузнецкого и Канско-Ачинского бассейнов (антрацита, длиннопламенного, тощего и бурого), в результате которых была подтверждена работоспособность отдельных узлов и установки горновой газификации в целом. В ходе испытаний был получен синтез-газ с высокими показателями и теплотой сгорания 6.0–8.3 МДж/м3, которая позволяла рассматривать его в качестве топлива в установках парогазового цикла с обеспечением надежного и стабильного шлакоудаления. Экспериментально установлена возможность использования полученного при испытаниях горновой газогенераторной установки газа для синтеза жидких углеводородов методом Фишера – Тропша. Доказана возможность получения в газогенераторе кокса и полукокса. Оценка показателей надежности, произведенная с помощью программного комплекса ANSYS на основании данных испытаний, продемонстрировала удовлетворительные характеристики жизненного цикла установки – ожидаемый срок службы наиболее нагруженных элементов газификатора составил 68 тыс. ч.
На протяжении прошедших 50 лет потребление энергии в мире непрерывно растет [1] и, несмотря на незначительное снижение темпов роста в последнее время, будет сохраняться на высоком уровне и в обозримом будущем. Твердое топливо (преимущественно уголь) в настоящее время используется для выработки более четверти потребляемой в мире энергии [1] и примерно 40% вырабатываемой электроэнергии [2]. При этом ужесточение требований к экологической безопасности и экономичности технологий угольной энергетики, а также высокая волатильность мирового рынка угля последних лет [1] приводят к необходимости внедрения новых технологий для энергетики и глубокой переработки угля [3, 4], одной из которых является газификация твердого топлива [5, 6]. Наибольший интерес представляют технологии газификации с совместным производством энергии и получением побочных продуктов с высокой добавочной стоимостью [3]: синтез-газа, сорбентов, жидких углеводородов и др. Широкое внедрение подобных технологий позволит повысить конкурентоспособность угольной промышленности и способствовать развитию регионов угледобычи [5]. В настоящее время предложены различные подходы к решению указанной проблемы [7], однако большинство из них носят теоретический характер и на практике в нужной мере не реализованы.
ОПЫТ РАЗРАБОТКИ МЕТОДОВ ГАЗИФИКАЦИИ УГЛЯ
Существуют разные технологии газификации. Согласно общепринятой классификации по типу организации движения топлива в реакторе, их можно разделить на три вида: с плотным и кипящим (псевдоожиженным) слоем и в потоке. Несмотря на то что газификаторы давно успешно применяются в промышленном масштабе за рубежом [8, 9], число таких технологий ограничено [10, 11]. Некоторые проекты внедрения технологий газификации в энергетику в течение последних 10 лет оказались неудачными и были прекращены на этапе реализации, пусконаладочных или опытно-конструкторских работ пилотных объектов [12, 13], тем самым был продемонстрирован недостаток опыта промышленной эксплуатации подобных установок. Для решения данной проблемы был создан ряд опытно-промышленных установок газификации твердых топлив [14]. Однако накопленный ранее опыт показал, что обеспечение экономической целесообразности такой технологии возможно либо при получении конечного продукта с высокой добавочной стоимостью (водорода [15], метанола [16, 17] и др.), либо при использовании специфического сырья различного происхождения и состава [16, 18].
Первый подход реализован в виде поточных газификаторов угольной пыли с жидким шлакоудалением на парокислородном дутье [10, 11, 19]. Их преимущества – отсутствие смол в производимом газе и доказанная на практике возможность создания крупного газификатора угольной пыли (из-за весьма развитой поверхности реагирования), способного обеспечить мощность энергоустановки порядка 300 МВт [16, 19]. Однако процесс газификации угольной пыли имеет некоторые негативные особенности, которые отличают его от процесса сжигания. При поточном способе исключается возможность повышения качества генераторного газа вследствие реакции взаимодействия продуктов газификации с высококалорийными летучими компонентами топлива, поскольку эти компоненты выгорают на первой стадии процесса. Температура газов на выходе из реактора должна быть довольно высокой (по условиям шлакоудаления), что приводит к необходимости устанавливать дорогие теплообменники для снижения температуры готового продукта. По указанным причинам пылевые газогенераторы отличаются увеличенным расходованием кислорода и пониженным химическим КПД, они также крайне чувствительны к изменениям характеристик топлива. Расчет этих газификаторов довольно прост, так как в научной литературе уже сформирован подход к моделированию основных процессов с учетом результатов термогравиметрического анализа [14, 20], а дальнейшее развитие поточных технологий видится в повышении точности моделирования и формировании редуцированного механизма реагирования между продуктами газификации [20].
Газификаторы плотного слоя, в которых реализован второй подход, напротив, достаточно толерантны к изменениям характеристик топлива, имеют высокий химический КПД, но несколько худшие массогабаритные показатели, кроме того, им присущи некоторые недостатки в организации топливоподачи, шлакоудаления и др. [21]. Ввиду более сложной природы процесса слоевой газификации, на который оказывают влияние как тепломассоперенос в отдельных крупных частицах топлива, так и тепломассоперенос и химическое реагирование в пористом слое, моделирование слоевой газификации представляет собой весьма сложную задачу [22]. Несмотря на большое число подходов к описанию данного процесса, все они имеют существенные недостатки [14]. Поэтому для достоверного описания процессов в слоевом газогенераторе промышленного масштаба в настоящее время требуются экспериментальные данные, которые можно получить на соответствующем оборудовании. Ограниченное число опытно-промышленных установок такого типа в мире (в настоящее время только площадка Sotacarbo находится в стадии активной эксплуатации [18, 23]) сдерживает промышленное внедрение этой технологии.
Для преодоления указанных ограничений сотрудники ВТИ и ТПУ разработали и апробировали в промышленном масштабе аппарат, в котором реализован уникальный отечественный метод слоевой газификации, из-за сходства с доменным процессом названый горновым.
РАЗРАБОТКА И ИЗГОТОВЛЕНИЕ ЭКСПЕРИМЕНТАЛЬНОГО ОБРАЗЦА ПОЛУПРОМЫШЛЕННОЙ ГОРНОВОЙ ГАЗОГЕНЕРАТОРНОЙ УСТАНОВКИ
В ВТИ была накоплена база знаний по технологии горновой газификации, на теоретическом и стендовом уровнях изучена возможность применения получаемого синтез-газа в цикле парогазовых установок [24, 25]. На протяжении 2000-х годов основные процессы при горновой газификации исследовались на опытной установке с небольшим расходом угля (до 80 кг/ч) на территории Зуевской экспериментальной ТЭЦ [26]. В целом, экспериментальные исследования подтвердили эффективность технологии горновой газификации угля и стали основой для создания первой в России опытно-промышленной установки горновой газификации угля в г. Томск.
В 2014–2019 гг. совместными усилиями сотрудников ВТИ и ТПУ при поддержке Министерства науки и высшего образования РФ была создана и успешно испытана первая в России опытно-промышленная установка по глубокой переработке угля на основе технологии горновой газификации, размещенная на территории действующей Томской ТЭЦ-3. Технические характеристики экспериментального образца горновой газогенераторной установки (ЭО ГГГУ) в номинальном режиме работы приведены далее:
Расход, кг/ч: |
удаляемого шлака ..........................................430 |
золы, улавливаемой в циклоне .....................200 |
золы, улавливаемой |
в батарейном циклоне .....................................50 |
Расход (при 0°C, 0.1013 МПа), тыс. м3/ч |
воздуха ........................................................11–15 |
газа ..............................................................До 17 |
Температура, °С: |
пара ........................................................250–300 |
воздуха на входе в газогенератор ...................300 |
воздуха перед теплообменником ...................120 |
газа после газификатора ......................800–1100 |
газа после охладителя ............................500–600 |
газа за батарейным циклоном .......................150 |
Расход, т/ч: |
топлива ...........................................................4.0 |
пара ..........................................................0.7–1.0 |
Давление, МПа: |
избыточное в газификаторе ....................0.3–0.6 |
за редукционным устройством ...Не более 0.025 |
Трехмерная модель и общий вид опытно-промышленной установки горновой газификации угля приведены на рис. 1, принципиальная схема установки – на рис. 2. Газогенератор 5 представляет собой цилиндрический сосуд внешним диаметром 2200 мм и высотой 4830 мм, выложенный изнутри футеровочным кирпичом. Внутренний диаметр верхней части футеровки составляет 1720 мм, внутренний диаметр футеровки в области шлаковой летки – 1260 мм. В нижней части газификатора футеровка отсутствует, так как там располагается заполняемая водой шлаковая ванна, в которую поступает шлак из реакционной камеры. Перед началом работы газогенератора футеровка разогревается до температуры 800°С в течение суток с использованием горелки, в которой сжигается дизельное топливо.
Рис. 1.
3D-модель ЭО ГГГУ (а), внешний вид азотной установки (б), шлаковой ванны (в) и газогенератора (г). 1 – циклон; 2 – шлюз пыли циклона; 3 – парогенератор; 4, 6 – система шлюзования шлака и топлива; 5 – воздухоразделительная установка; 7 – газификатор; 8 – охладитель газов; 9 – теплообменник; 10 – батарейный циклон; 11 – факельная установка
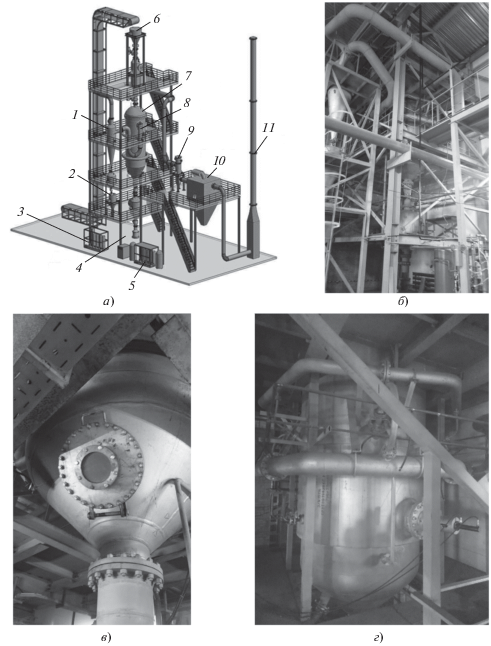
Рис. 2.
Принципиальная схема опытно-промышленной установки горновой газификации угля. 1, 3 – приемный бункер топлива; 2 – виброгрохот; 4 – бункер шлюзовой топливный; 5 – газификатор горновой; 6 – бункер шлюзовой шлаковый; 7 – охладитель газов; 8 – циклон; 9 – шлюз пыли циклона; 10 – редуцирующее устройство; 11 – рекуперационный теплообменник-воздухоподогреватель; 12 – батарейный циклон; 13 – факельная установка
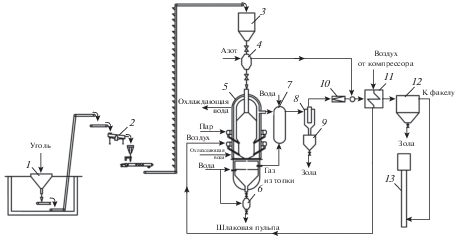
После виброгрохота 2 уголь фракции 5–50 мм подается конвейером в верхний топливный бункер 3, а затем в газогенератор 5. В качестве шлюзового агента используется азот, поступающий в бункер 4 из воздухоразделительной установки (генератора азота). В газификатор от компрессора подается сжатый воздух, подогретый до 300°С теплом уходящих газов, а также перегретый пар температурой 200–300°С от парогенератора. Рабочее давление в газогенераторе в ходе испытаний составляло 0.6 МПа.
Полученный генераторный газ температурой 800–1100°С направляется в охладитель газов 7, где с помощью автоматически регулируемого впрыска воды его температура снижается до 500–600°С. После этого синтез-газ поступает в циклон 8, являющийся первой ступенью очистки газа (от твердых частиц), далее в редукционное устройство 10, где его давление снижается, затем в рекуперационный воздухоподогреватель 11 и батарейный циклон 12, после которого он сжигается в факельной установке 13. На газопроводе предусмотрена возможность отбора газа на установку синтеза жидких углеводородов. В перспективе планируется использовать синтез-газ и продукты его сгорания в газотурбинной установке. Рубашки охлаждения газогенератора и охладителя газа, по которым в процессе разогрева и работы установки непрерывно циркулирует техническая вода, предотвращают риск повреждения этих наиболее теплонапряженных узлов опытно-промышленной установки.
Жидкий шлак с температурой более 1700°C, образующийся в очаге горения, стекает по створкам летки или чугунной решетки в шлаковую ванну, заполненную водой с температурой 160°C, а оттуда через шлюзовой шлаковый бункер 6 поступает в систему шлакоудаления и утилизируется. Для герметизации аппаратов шлакоудаления предусмотрено шлюзование аналогично шлюзованию угля. Пар, подаваемый в газогенератор, вырабатывается с помощью электродных парогенераторов и нагревается до требуемых параметров в установке, состоящей из 12 электропароперегревателей.
Общий вид газогенератора показан на рис. 3. Для проведения комплексных испытаний опытно-промышленной установки газификации угля в отдельном здании был создан специальный стенд (рис. 4), включающий в себя, наряду с ЭО ГГГУ цех приема и хранения угля, его измельчения и фракционирования, компрессорную станцию, собственную электроподстанцию со всей необходимой инженерной инфраструктурой. Общая площадь постройки составляет 1240 м2, общая площадь помещений – 2410 м2, максимальная высота всего сооружения – 28 м.
ИСПЫТАНИЯ УСТАНОВКИ ПРИ РАБОТЕ НА УГЛЕ РАЗЛИЧНЫХ МАРОК
В процессе подготовки к испытаниям опытной установки в условиях, максимально приближенных к промышленной эксплуатации, был выполнен комплекс пусконаладочных работ по отдельным узлам. Надежность и безопасность, удобство управления режимами эксплуатации обеспечиваются высоким уровнем автоматизации. Управление задвижками и регуляторами выполнялось дистанционно, показания приборов и датчиков, предусмотренных технологической схемой, выводились на единый щит управления (рис. 5).
В период с мая по ноябрь 2019 г. были проведены шесть серий испытаний при рабочих параметрах, соответствующих номинальному проектному режиму (давления, температуры в узловых элементах установки, состав генераторного газа и т.п.). Были отработаны все технологические процедуры цикла газификации от подачи топлива до выхода генераторного газа и эвакуации жидкого шлака. Общая продолжительность работы в эксплуатационных режимах составила более 200 ч. По результатам этих испытаний были намечены и разработаны технические решения и мероприятия по совершенствованию горновой газогенераторной установки.
В конце октября – начале ноября 2019 г. были проведены итоговые испытания установки на четырех марках твердого топлива: длиннопламенном угле (Д) шахты “Беловская”, тощем угле (Т) шахты “Алардинская”, буром угле (Б) разреза “Балахтинский” и антраците (А) шахты “Распадская”. На испытаниях присутствовали в качестве экспертов, а также операторов контрольных измерений состава генераторного газа представители академических институтов (Институт теплофизики им. С.С. Кутателадзе СО РАН, Федеральный исследовательский центр угля и углехимии СО РАН), заинтересованных организаций топливно-энергетического комплекса (ПАО “Интер РАО”, АО Холдинговая компания “СДС-Уголь”, ООО “Тепловодкомплекс”, ООО “Русатом Гринвей”, ООО “Шахтоуправление Майское”, ООО “Сибирский институт горного дела”, АО “Бийский котельный завод”, ООО “ПРОТЭН-ВУТ”) и органов власти (Департамент промышленности и энергетики администрации Томской области).
На начальном этапе испытаний осуществлялся разогрев футеровки газогенератора с использованием дизельной горелки по графику, представленному на рис. 6. После завершения разогрева футеровки газогенератора в течение 25 ч и проведения подготовительных процедур была задействована вся цепочка топливоподачи от приемных бункеров угля до круто наклоненного конвейера, в который была загружена в два приема первая партия угля марки Д: 2 т сначала и 2 т после того, как температура в газогенераторе стала повышаться. Суммарная загрузка равнялась номинальному часовому расходу.
После закрытия задвижки системы шлюзования топлива в газогенератор начал подаваться воздух с постепенным увеличением давления до значений, близких к максимальному (0.6 МПа). После стабилизации состава газа в тракте установились температуры, соответствующие проектным значениям: на выходе из газогенератора 900–1000°С, за охладителем газа 500–550°С, перед теплообменником 350–400°С. Достигнутая температура подаваемого в газогенератор воздуха была близка к проектной (280–300°С). При превышении нормативной температуры синтез-газа на выходе из газогенератора для протекания в восстановительной зоне требуемых реакций увеличивали расход подаваемого в газогенератор пара.
Состав генераторного газа фиксировался непрерывно в течение опыта поточным газоанализатором “Тест-1” (БОНЭР, Россия), подключенным к отбору между редукционным устройством и точкой смешения запирающего азота с синтез-газом. Показания газоанализатора в режиме реального времени выводились на щит управления, что позволяло обеспечить оперативный контроль процесса газификации. В дальнейшем в ходе опытов подачу угля в газогенератор осуществляли циклично: по 2 т 1 раз в 30–45 мин. График проведения испытаний показан на рис. 7.
Рис. 7.
График проведения испытаний ЭО ГГГУ. 1, 2 – загрузка и газификация топлива; 3 – получение полукокса
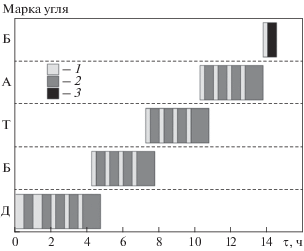
Поскольку производство полукокса является одним из перспективных направлений развития технологий глубокой утилизации угля, на заключительной стадии испытаний была проверена возможность его реализации с использованием оборудования ЭО ГГГУ. При последней загрузке топлива после получения синтез-газа в камеру газогенератора был подан уголь марки Б массой 2 т, который продувался минимальным расходом воздуха в течение 30 мин (см. рис. 7). Затем летку шлаковой ванны газогенератора открывали, частично прореагировавшее топливо попадало в воду и быстро охлаждалось до температуры, близкой к температуре окружающей среды. Было установлено, что твердая фаза произведенного продукта являлась аналогом полукокса, а оборудование ЭО ГГГУ пригодно для его получения. В ходе испытаний каждого из исследуемых углей выход жидкого шлака был устойчивым при его выгрузке с периодичностью два цикла за 1 ч. Горение синтез-газа на факельной установке (рис. 8) было стабильным на каждом из испытуемых углей.
При газификации угля каждой марки удалось получить синтез-газ с заявленными характеристиками (см. таблицу). На последнем этапе испытаний при газификации антрацита были проведены опыты по изменению баланса “водяной пар – воздух”, направленные на повышение содержания водорода в получаемом синтез-газе. Результаты опытов показывают, что содержание водорода в газе можно значительно увеличить вне зависимости от вида используемого угля.
Характеристика синтез-газа, полученного в ходе итоговых испытаний ЭО ГГГУ
Параметр | Требования к параметру в соответствии с техническим заданием на проектирование | Марка угля | |||
---|---|---|---|---|---|
Д | Б | Т | А | ||
Теплота сгорания синтез-газа, кДж/м3 | Не менее 4610 | 6063 | 8158 | 6038 | 8254 |
Расход синтез-газа, м3/ч | 17 000 | 17 102 | 17 030 | 17 345 | 17 276 |
Концентрация, % (по объему): | |||||
СО2 | 2.0–5.5 | 6.5 | 3.7 | 5.0 | 5.4 |
СН4 | 0.3–3.5 | 7.4 | 9.7 | 5.5 | 3.9 |
СО | 20–30 | 20.0 | 30.2 | 25.2 | 34.0 |
Н2 | 6.7–9.5 | 8.1 | 7.9 | 8.1 | 23.6* |
N2 | 45–50 | 49.9 | 35.5 | 40.5 | 26.1 |
Ввод воды непосредственно в зону реакции (с высоковлажным углем или другим способом) положительно сказывается на качестве синтез-газа. Проведенные эксперименты показали, что таким образом можно управлять содержанием метана в газе. Так, в отдельные моменты (в основном при подаче пара в камеру газогенератора) содержание метана в получаемом газе поднималось до 45%. Возможно, это связано с реакциями между углеродом топлива и водородом, выделяющимся при взаимодействии водяного пара с твердофазным углеродом и СО, а также с подавлением реакций окисления метана, выделяющегося при пиролизе топлива, вследствие вытеснения части воздуха из газогенератора водяным паром. Данный факт соответствует общему влиянию водяного пара на процесс газификации – снижению температуры и улучшению качества (увеличению содержания горючих компонентов СО, Н2 и СН4) синтез-газа как топлива на выходе из газогенератора и повышению его конкурентоспособности как исходного топлива при сжигании и как сырья для производства водорода. Возможности использования этих эффектов целесообразно более подробно исследовать при проведении дальнейших экспериментов.
При определении теплового КПД газификатора учитывали потери тепла со шлаком, с уносом (недожог) и в окружающую среду [27]. Для углей исследованных марок КПД составил 95.0–97.5%. В ходе испытаний было установлено, что система шлакоудаления стабильно функционирует на всех исследованных углях, что подтверждает работоспособность принятых технических решений, и твердая фаза получаемого продукта является аналогом полукокса (рис. 9). При этом следует отметить, что детальное изучение характеристик данного процесса при испытаниях не производилось.
Для оценки надежности конструкции газификатора были выполнены расчеты установки на прочность в условиях испытаний. В качестве исходных данных использовали наиболее высокие температуры и давления. В соответствии с техническими требованиями срок службы газификатора должен составлять не менее 50 тыс. ч (5.71 года). Для расчета ориентировочного срока службы при эксплуатационных параметрах применяли программу ANSYS Mechanical, с помощью которой на основе распределения давлений и температур определяли срок службы элементов газификатора (рис. 10). Как показывают полученные данные, наиболее нагруженными зонами являются зоны высоких температур обмуровки, крепления газификатора и газового тракта, например патрубка и охладителя газов. Несмотря на значительные нагрузки даже в самых напряженных участках металла газификатора, срок его службы составляет 67 992 ч (7.76 года).
ОПЫТ ПОЛУЧЕНИЯ ЖИДКИХ УГЛЕВОДОРОДОВ
Термодинамические расчеты и предварительные лабораторные испытания показали, что получаемый синтез-газ пригоден для реализации процесса синтеза жидких углеводородов (процесс Фишера – Тропша). Схема разработанной лабораторной установки получения жидких топлив с использованием синтез-газа приведена на рис. 11.
Рис. 11.
Технологическая схема лабораторной установки получения жидких топлив из генераторного газа. 1 – баллон с азотом; 2 – баллон с азотоводородной смесью; 3 – гравийный фильтр; 4 – нейтрализатор сероводорода; 5 – конденсатор жидких продуктов; 6 – реактор синтеза жидких углеводородов; 7 – лабораторный автотрансформатор
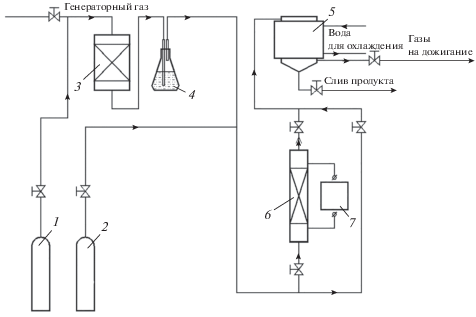
Азот предназначен для продува системы, создания инертной атмосферы и пассивации восстановленного катализатора. Азотоводородная смесь необходима для восстановления синтезированного железомедного катализатора с переводом его в активную форму, а также обеспечения отношения ${{{{{v}}_{{{{{\text{H}}}_{{\text{2}}}}}}}} \mathord{\left/ {\vphantom {{{{{v}}_{{{{{\text{H}}}_{{\text{2}}}}}}}} {{{{v}}_{{{\text{CO}}}}}}}} \right. \kern-0em} {{{{v}}_{{{\text{CO}}}}}}}$ = 2 (здесь ${{{v}}_{{{{{\text{H}}}_{{\text{2}}}}}}},$ ${{{v}}_{{{\text{CO}}}}}$ – объемы Н2 и СО) при синтезе жидких углеводородов. Гравийный фильтр 3 нужен для очистки газа от взвешенных частиц и конденсации в нем смолистых соединений. Вместо гравийного фильтра может быть использована пустотелая либо набитая ватой стеклянная колба. Нейтрализатор сероводорода, присутствующего в генераторном газе, 4 представляет собой стеклянную колбу с отверстиями для входа и выхода газа, заполненную смесью растворов едкого натра концентрацией 10% и фенолфталеина, имеющей фиолетовый цвет. В процессе нейтрализации происходят реакции улавливания сероводорода и поглощения диоксида углерода:
(улавливание сероводорода);
(поглощение диоксида углерода);
(поглощение диоксида углерода).
Обесцвечивание раствора в колбе свидетельствует об исчерпании ресурса поглотителя и необходимости его замены.
Реактор синтеза жидких углеводородов 6 – это основа технологической схемы. В нем протекает целевая реакция
Реактор представляет собой расширенный в верхней части кварцевый цилиндрический аппарат, внешний диаметр которого составляет 47 мм и внутренний – 43 мм, с перфорированной решеткой и термопарным карманом. Нагрев реактора осуществляется электрической печью. Конденсатор жидких продуктов 5 – теплообменный аппарат с водяным охлаждением и отводом сконденсировавшегося продукта. Регулирование силы тока на обмотке печи обеспечивается лабораторным автотрансформатором 7.
Проведенный в ходе испытаний эксперимент показал, что при достигнутом составе синтез-газа на ЭО ГГГУ может быть реализован процесс Фишера – Тропша. Были получены пробы углеводородов, относящихся к группе спиртов метильной группы. Необходимо отметить, что опыт был организован при давлении близком к атмосферному и неоптимальном соотношении ${{{{{v}}_{{{{{\text{H}}}_{{\text{2}}}}}}}} \mathord{\left/ {\vphantom {{{{{v}}_{{{{{\text{H}}}_{{\text{2}}}}}}}} {{{{v}}_{{{\text{CO}}}}}}}} \right. \kern-0em} {{{{v}}_{{{\text{CO}}}}}}}$ в синтез-газе. Тем не менее, результаты эксперимента подтверждают, что при проведении дальнейших исследований (при модификации исходной установки) может быть обеспечен стабильный выход жидких топлив из синтез-газа. Однако для получения более достоверных данных требуется установить дополнительный реактор для оптимизации соотношения ${{{{{v}}_{{{{{\text{H}}}_{{\text{2}}}}}}}} \mathord{\left/ {\vphantom {{{{{v}}_{{{{{\text{H}}}_{{\text{2}}}}}}}} {{{{v}}_{{{\text{CO}}}}}}}} \right. \kern-0em} {{{{v}}_{{{\text{CO}}}}}}}$ в получаемом газе. Модификация установки позволит:
провести опыты с катализаторами других типов;
увеличить давление в реакторе Фишера – Тропша и повысить качество конечного продукта;
оптимизировать состав синтез-газа с достижением близкого к оптимальному соотношения ${{{{{v}}_{{{{{\text{H}}}_{{\text{2}}}}}}}} \mathord{\left/ {\vphantom {{{{{v}}_{{{{{\text{H}}}_{{\text{2}}}}}}}} {{{{v}}_{{{\text{CO}}}}}}}} \right. \kern-0em} {{{{v}}_{{{\text{CO}}}}}}}.$
ПЕРСПЕКТИВЫ ПРОМЫШЛЕННОГО ВНЕДРЕНИЯ И ДАЛЬНЕЙШЕГО РАЗВИТИЯ ТЕХНОЛОГИИ ГОРНОВОЙ ГАЗИФИКАЦИИ
Успешные испытания первой в России опытно-промышленной горновой газогенераторной установки открывают новые возможности для дальнейшего совершенствования технологии глубокой переработки углей и создания высокотехнологичных промышленных комплексов. Производство подобных установок экономически целесообразно, если принять во внимание более низкую стоимость угля по сравнению со стоимостью природного газа и жидких топлив, особенно при использовании некондиционного угля или отходов его обогащения.
Достигнутые технико-экономические показатели этих установок представляют интерес для дальнейшего изучения, в том числе потому, что уголь является относительно дешевым топливом на мировом рынке, а его запасы огромны (150 лет при текущем объеме потребления). При этом традиционные способы сжигания угля не соответствуют современным требованиям экологической безопасности. Реализованные проекты опирались на государственную поддержку, направленную на повышение их коммерческой привлекательности и одновременное стимулирование развития инновационных технологий в энергетическом машиностроении.
Анализ рынка энергетического угля России выявил существенную дифференциацию цен на уголь, природный газ и электроэнергию, а также их соотношений по регионам страны. В этих условиях регион размещения промышленных комплексов газификации оказывает существенное влияние на эффективность применения газогенераторов по сравнению с традиционным сжиганием топлива на угольных ТЭС. Выбор региона имеет большое значение для эффективности проекта дальнейшего освоения сопряжения технологий газификации с парогазовым циклом электростанций.
Предварительный анализ с помощью разработанной финансово-экономической модели с учетом фактических данных, соответствующих режимам испытаний для угля марки Б, показывает, что получаемый синтез-газ конкурентоспособен с природным газом при стоимости угля 546 руб/т. При этом отпускная цена рассматриваемого угля от производителя в настоящее время составляет 500 руб/т. Таким образом, технико-экономические расчеты подтверждают эффективность газогенераторных установок при работе на местных углях с небольшими транспортными плечами (транспортное плечо – маршрут, который соединяет начальные и конечные пункты транспортировки груза). Дальнейшие стадии развития технологии и ее внедрение на объектах энергетики позволят оптимизировать эксплуатационные расходы и повысить эффективность эксплуатационных режимов газификации, сделав синтез-газ еще более конкурентоспособным с топливами других видов.
При наличии необходимых инвестиций комплексы на основе горновой технологии газификации могут быть введены в эксплуатацию в течение ближайших лет. При этом успешно освоенная опытно-промышленная установка может служить площадкой для отработки новых технических решений, причем в качестве исходного сырья можно использовать не только уголь, но и отходы различных видов. На базе ТПУ проводится комплекс фундаментальных и прикладных исследований по экологичной переработке некоторых отходов с получением полезной продукции [28]. Примером может служить технология термической конверсии отработанных автомобильных покрышек (шин) с выходом полезной продукции в твердой (технический углерод), жидкой (мазут) и газообразной (генераторный газ) фазах. Не менее интересны и предлагаемые подходы к энергетической утилизации отходов деревообрабатывающей промышленности с производством сорбентов, генераторного газа и жидкого топлива.
Расширение спектра используемого при газификации исходного сырья позволит повысить экономическую привлекательность газогенераторных установок, вовлечь в топливно-энергетический баланс регионов не задействованные сейчас ресурсы и снизить при этом антропогенную нагрузку на окружающую среду. Сделанные в результате испытаний выводы были использованы при формировании Программы развития угольной промышленности России на период до 2035 г. [29].
Результатом дальнейшего промышленного освоения технологии горновой газификации угля и отходов может быть создание высокотехнологичных производств различной направленности, в том числе получение:
синтетического газа для последующего использования в парогазовых установках либо для нужд ТЭС (замещение мазута при растопке котлов);
метанводородной смеси для использования в водородной экологически чистой энергетике;
тяжелых углеводородов, синтетических топлив и спиртов метильной группы;
кокса и полукокса для металлургии;
полезных продуктов c высокой добавленной стоимостью при использовании в качестве исходного сырья биомассы, промышленных отходов и др.
Можно с уверенностью утверждать, что в долгосрочной перспективе внедрение описанной технологии позволит снизить расход природного газа и нефтепродуктов в энергетике, обеспечить эффективное использование углей в регионах их добычи и создать ресурсоэффективное и экологичное направление в топливно-энергетическом комплексе страны.
ВЫВОДЫ
1. В условиях, соответствующих промышленной эксплуатации газификатора, апробирована технология горновой газификации твердого топлива, все элементы и системы которой продемонстрировали бесперебойную работу на протяжении периода испытаний.
2. В процессе газификации угля марок Б, Д, Т и А был получен синтез-газ, соответствующий требованиям к составу и качеству для дальнейшего применения в парогазовых установках.
3. Экспериментально установлено, что полученный синтез-газ может быть использован в качестве сырья для синтеза жидких углеводородов по технологии Фишера – Тропша.
4. Определены пути и конкретные технические решения по развитию стенда газификации твердых топлив и отдельных его элементов для исследований сырья различных видов (нефтяного кокса, торфа, древесной щепы, твердых отходов) и апробации технологий использования полученного синтез-газа для производства химикатов, жидкого топлива и водорода.
Список литературы
BP Statistical Review of World Energy / B. Looney. 2019.
Прогноз развития энергетики мира и России 2019 / под ред. А.А. Макарова, Т.А. Митровой, В.А. Кулагина. М.: ИНЭИ РАН – Московская школа управления “Сколково”, 2019. ISBN 978-5-91438-028-8.
Поручение Президента РФ Министерству энергетики. Пр-1707, п. 4, 2019.
Энергетическая стратегия Российской Федерации на период до 2035 г. https://minenergo.gov.ru/node/1026
Тумановский А.Г. Перспективы развития угольных ТЭС России // Теплоэнергетика. 2017. № 6. С. 3–13. https://doi.org/10.1134/S004036361706008X
Litvinenko V., Meyer B. Syngas production: Status and potential for implementation in Russian industry. Springer International Publishing, 2018. https://doi.org/10.1007/978-3-319-70963-5
Thermal dissolution of different-ranked coals in the anthracene fraction of coking tar / P.N. Kuznetsov, N.V. Perminov, L.I. Kuznetsova, S.M. Kolesnikova, E.S. Kamenskiy, N.I. Pavlenko, O.Y. Fetisova // Coke Chem. 2019. V. 62. Is. 4. P. 150–157. https://doi.org/10.3103/S1068364X19040033
Ольховский Г.Г. Газификация твердых топлив в мировой энергетике (обзор) // Теплоэнергетика. 2015. № 7. С. 3–11. https://doi.org/10.1134/S0040363615070073
Higman C. State of the gasification industry – the updated worldwide gasification database // 30th Annual Intern. Pittsburgh Coal Conf. Pittsburgh, Jan. 2013. V. 1. P. 226–247.
E-Gas TM Gasification Technology. McDermott International, Inc. https://www.mcdermott.com/getattachment
Hannemann F., De Hui W. Siemens fuel gasification technology status and new developments Siemens // Coal Convers Syngas. 2015. P. 1–17.
Australasia: Zerogen stalls // Chem. Engineer. 2011. № 836. P. 12–16.
Geuss M. $7.5 billion Kemper power plant suspends coal gasification // ARS Technica. 2017. № 6. https://arstechnica.com/information-technology
Patra T.K., Sheth P.N. Biomass gasification models for downdraft gasifier: A state-of-the-art review // Renewable Sustainable Energy Rev. 2015. V. 50. P. 583–593. https://doi.org/10.1016/j.rser.2015.05.012
Conversion of low-grade coals in sub- and supercritical water: A review / J. Yu, C. Jiang, Q. Guan, J. Gu, P. Ning, R. Miao, Q. Chen, J. Zhang // Fuel. 2018. V. 217. P. 275–284. https://doi.org/10.1016/j.fuel.2017.12.113
Pilot scale entrained flow gasification of Turkish lignites / A. Ünlü, U. Kayahan, A. Argönül, M. Ziypak, A. Akça // J. Energy Inst. 2017. V. 90. № 1. P. 159–165. https://doi.org/10.1016/j.joei.2015.09.001
Methanol-power production using coal and methane as materials integrated with a two-level adjustment system / L. Lv, L. Zhu, H. Li, B. Li // J. Taiwan Inst. Chem. Eng. 2019. V. 97. P. 346–355. https://doi.org/10.1016/j.jtice.2019.02.008
Experimental activities on Sotacarbo 5 MWth gasification demonstration plant / G. Calì, P. Deiana, C. Bassano, E. Maggio // Fuel. 2017. V. 207. P. 671–679. https://doi.org/10.1016/j.fuel.2017.04.061
Kimura N. Status of EAGLE project: Multi-purpose coal gasification technology development // J. Japan Inst. Energy. 2008. V. 87. № 4. P. 236–241.
Mularski J., Pawlak-Kruczek H., Modlinski N. A review of recent studies of the CFD modelling of coal gasification in entrained flow gasifiers, covering devolatilization, gas-phase reactions, surface reactions, models and kinetics // Fuel. 2020. V. 271. P. 117620–117622. https://doi.org/10.1016/j.fuel.2020.117620
Krishnamoorthy V., Pisupati S.V. A critical review of mineral matter related issues during gasification of coal in fixed, fluidized, and entrained flow gasifiers // Energies. 2015. V. 8. Is. 9. P. 10430–10463. https://doi.org/10.3390/en80910430
Review on modelling approaches based on computational fluid dynamics for biomass combustion systems: Focus on fixed bed and moving grate systems / A. Dernbecher, A. Dieguez-Alonso, A. Ortwein, F. Tabet // Biomass Convers. Biorefin. 2019. V. 9. Is. 1. P. 129–182. https://doi.org/10.1007/s13399-019-00370-z
The Sotacarbo gasification pilot platform: Plant overview, recent experimental results and potential future integrations / A. Pettinau, G. Calì, E. Loria, P. Miraglia, F. Ferrara // Appl. Therm. Eng. 2015. V. 74. P. 2–9. https://doi.org/10.1016/j.applthermaleng.2013.12.079
Сучков С.И., Бабий В.И., Абросимов А.А. Экспериментальная разработка системы газификации твердого топлива // Теплоэнергетика. 1998. № 6. С. 43–49.
Разработка отечественной ПГУ с газификацией угля / Г.Г. Ольховский, С.И. Сучков, П.А. Березинец, А.Н. Епихин, И.О. Крылов, И.Г. Луговская, А.А. Сомов, В.Н. Гудков, А.А. Заикин // Теплоэнергетика. 2010. № 2. С. 19–26.
Сучков С.И. Разработка энергетической технологии газификации твердого топлива: дис. … докт. техн. наук. М., 2011. https://www.dissercat.com/content/razrabotka-energeticheskoi-tekhnologii-gazifikatsii-tverdogo-topliva
Кузнецов Н.В. Тепловой расчет котельных агрегатов (нормативный метод). 2-е изд. М.: Энергия, 1973.
Kinetic characteristics of the oxidation of non-food municipal solid waste / K.B. Larionov, S.A. Tsibulskiy, K.V. Slyusarsky, A.A. Vedyagin, V.E. Gubin // Solid Fuel Chem. 2020. V. 54. № 1. P. 47–53. https://doi.org/10.3103/S036152192001005X
Программа развития угольной промышленности России на период до 2035 г. Утв. распоряжением Правительства РФ от 13.06.2020 № 1582-р.
Дополнительные материалы отсутствуют.
Инструменты
Теплоэнергетика