Теплоэнергетика, 2021, № 6, стр. 68-76
Разработка малоэмиссионных камер сгорания энергетических ГТУ
А. Г. Тумановский a, Л. А. Булысова a, *, В. Д. Васильев a, **, М. Н. Гутник a, ***, М. М. Гутник a
a Всероссийский теплотехнический институт
115280 Москва, Автозаводская ул., д. 14, Россия
* E-mail: bulysov@mail.ru
** E-mail: basbas@mail.ru
*** E-mail: kc-vti@bk.ru
Поступила в редакцию 06.10.2020
После доработки 21.10.2020
Принята к публикации 18.11.2020
Аннотация
Представлены основные результаты исследований ВТИ в области малоэмиссионных камер сгорания газотурбинных установок (ГТУ). В последние годы с этой целью развивается сжигание в ограниченном объеме предварительно перемешанной топливовоздушной смеси (ТВС) в закрученном потоке, благодаря чему обеспечиваются бóльшая полнота сгорания топлива, устойчивая беспульсационная работа камеры сгорания в широком диапазоне изменения параметров и соответствие экологическим требованиям. Для решения возникающих при этом задач выработана методология оценки влияния температуры в зоне горения, скорости потока, давления в камере сгорания и других факторов на устойчивость горения. Рассмотрен комплексный подход специалистов ВТИ к изучению процессов, протекающих в камерах сгорания, с применением численных и экспериментальных исследований, который позволяет сократить стоимость и время проведения работ по доводке малоэмиссионных камер сгорания. Например, представлена зависимость между качеством получаемой топливовоздушной смеси, оцененным с помощью расчетов, и концентрациями оксидов азота, измеряемыми в эксперименте. Предложен расчетный параметр, связывающий параметры процесса в жаровой трубе и амплитуду вибрационного горения. Экспериментально показана хорошая корреляция предложенного параметра и измеренной амплитуды пульсаций давления. Несомненный интерес представляют приведенные в статье примеры изменения полей скорости и температуры, происходящие при повышении рабочего давления, которые необходимо учитывать при проектировании и стендовых испытаниях камеры сгорания. Представлены результаты разработок малоэмиссионных камер сгорания (МЭКС) ГТУ большой и средней мощностей. Рассмотрены возможности масштабирования камер для других ГТУ.
В настоящее время актуальной задачей является создание и массовое производство отечественных конкурентоспособных газотурбинных установок как для внутреннего, так и для внешнего рынка.
Работающие при высоких температурах и давлениях МЭКС – сложный и дорогостоящий компонент ГТУ. Высокие температуры газов на выходе из МЭКС (в настоящее время 1600°С и выше) приводят к образованию значительного количества оксидов азота (NOx). Для снижения выбросов NOx во всем мире и в ВТИ, в частности, отрабатываются традиционные процессы кинетического сжигания предварительно подготовленных смесей природного газа с воздухом, являющихся основным топливом энергетических ГТУ.
Процесс разработки МЭКС – многоаспектный. Помимо основных требований к работе на номинальных режимах при различных температурах атмосферного воздуха камеры сгорания должны обеспечивать полное сжигание топлива в широком диапазоне рабочих режимов по нагрузкам и наружным условиям, сохранять устойчивость при пусках и быстрых изменениях режимов, соответствовать нормативным требованиям по концентрациям NOx и СО в продуктах сгорания.
КОНСТРУКЦИИ МАЛОЭМИССИОННЫХ КАМЕР СГОРАНИЯ
Наряду с бурно развивающимися методами математического моделирования, при создании камеры сгорания требуется проведение экспериментальных исследований на стендах с использованием современных средств измерений, расшифровки и обработки полученных результатов. Необходимо обеспечивать адекватность моделирования процессов при изменениях размеров и давлений в камере сгорания (КС) вплоть до испытания полноразмерных жаровых труб и отсеков КС на стендах высокого (до 2.5 МПа) давления и в составе ГТУ.
Работы в ВТИ по совершенствованию и исследованиям камер сгорания ведутся с 1962 г. Сложность физико-химических процессов, специфика турбулентных течений в камере и многокомпонентности среды, тепло- и массообмен и другие факторы, не позволяли тогда получить корректные и адекватные модели для количественной оценки образующихся в камере сгорания вредных веществ. Поэтому в то время для описания процессов в камерах сгорания использовались простые полуэмпирические зависимости.
На том этапе были исследованы в основном особенности образования NOx в регистровых камерах сгорания с подачей всего необходимого для горения воздуха через фронтовое устройство. Экспериментальными исследованиями было установлено, что образование NOx определяется главным образом максимальными температурами факела и временем пребывания продуктов сгорания в зонах с этими температурами. При расчетах использовался термический механизм образования оксидов азота, который включает окисление N2 кислородом по цепи механизма Зельдовича и взаимодействия атомов N с радикалами OH:
Полученные значения эмиссии оксидов азота корректировались по данным, получаемым опытным путем. Оценивалось влияние конструктивных и режимных параметров на поправку расчетного значения.
Опытным путем было подтверждено повышение образования NOx с ростом давления.
Конструкции камер сгорания с диффузионным сжиганием топлива показаны на рис. 1.
Рис. 1.
Конструкции испытанных на стенде ОАО ВТИ камер сгорания. 1 – подвод топлива; 2 – подвод воздуха; 3 – завихритель; 4 – жаровая труба (ЖТ); 5 – отверстия смешения (ОС)
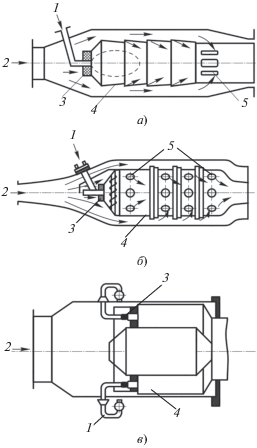
Как видно из рис. 1, а, одна часть воздуха перемешивается с топливом и направляется в объем жаровой трубы для горения. Другая часть воздуха, поступающая в ЖТ через мелкие отверстия (диаметр менее 1 мм), используется для пленочного охлаждения стенок жаровой трубы и минимально участвует в процессе горения. Далее по течению ТВС располагаются отверстия большего диаметра – отверстия смешения, служащие для формирования поля температуры на выходе из камеры сгорания. Здесь зона горения (или первая зона) занимает весь объем жаровой трубы до отверстий смешения. Камера сгорания такой конструкции может быть преобразована в малоэмиссионную.
На рис. 1, б отверстия для ввода воздуха в объем жаровой трубы служат для стадийного сжигания топливовоздушной смеси высокой концентрации на струях воздуха. В данном случае горения в первой зоне не наблюдается, так как для его осуществления воздуха слишком мало. Процессы воспламенения и горения происходят после первого ряда отверстий, и далее на каждых последующих рядах наблюдается догорание ТВС. Последние ряды отверстий могут служить на определенных режимах работы ГТУ как отверстия смешения. Такую камеру сгорания невозможно преобразовать в малоэмиссионную, не поменяв кардинально ее конструкцию.
На рис. 1, в показана камера сгорания, в которой весь воздух, поступающий в горелочное устройство, участвует в процессе горения и в жаровой трубе существует только одна зона – первая зона горения, в которой происходит сжигание хорошо перемешанной топливовоздушной смеси.
Таблица 1.
Температурная неравномерность при различных вариантах размеров и расположения отверстий смешения
Вариант отверстий смешения | Базовый | 2 | 3 | 4 | 5 |
Температурная неравномерность ${{\theta }}$, % | 1.30 | 1.29 | 1.23 | 1.23 | 1.13 |
Для снижения концентрации NOx в камере сгорания, показанной на рис. 1, а, специалистами ОАО ВТИ были уменьшены максимальные температуры в зоне выгорания топлива путем обеднения топливовоздушной смеси до коэффициентов избытка воздуха в первой зоне ${{\alpha }_{1}}$ = 1.8–2.2. Для этого были установлены фронтовые устройства, интенсифицирующие процесс выгорания, и сокращено время пребывания продуктов сгорания в зоне с максимальными температурами. После проведения исследований процесса горения в такой КС были разработаны фронтовые устройства, в которых образование NOx в рабочих режимах (бывают пусковые и переменные) уменьшилось в 1.8–2.5 раза для энергетических ГТУ (ГТ-25-700-II, ГТ-700-12М, ГТ-35-770, ГТ-100-750) и газоперекачивающих агрегатов нескольких типов [1–3].
Радикальным способом уменьшения количества образующихся термических NOx является впрыск воды или пара в зону горения. Были разработаны устройства их подачи, которые при отношении расхода воздуха ${{G}_{{\text{в}}}}$ к расходу топлива ${{G}_{{\text{т}}}}$ (водотопливное отношение) ${{{{G}_{{\text{в}}}}} \mathord{\left/ {\vphantom {{{{G}_{{\text{в}}}}} {{{G}_{{\text{т}}}}}}} \right. \kern-0em} {{{G}_{{\text{т}}}}}}$ ≈ 1.0 позволили снизить концентрацию NOx при сжигании как жидких, так и газообразных топлив в 3.5–4.0 раза.
При сжигании жидких газотурбинных топлив с содержанием азота более 0.5% впрыск воды в КС не давал значительного эффекта. В то время были проведены исследования особенностей рабочего процесса и образования оксидов азота в авиационных высокофорсированных камерах сгорания с последовательным вводом воздуха в зону горения (см. рис. 1, б). Несмотря на высокие теплонапряжения в камерах сгорания этого типа, удалось снизить образование NOx благодаря сокращению времени пребывания продуктов сгорания в зонах с максимальными температурами.
Для малоэмиссионного сжигания в этих КС природного газа, дизельного, газотурбинного и моторного топлив потребовалось изучение процессов начального воспламенения, а также было необходимо расширить диапазон устойчивого горения, определить влияние распределения воздуха по тракту камеры на ее основные характеристики и концентрацию NOx. Экспериментальные исследования влияния ${{{{\alpha }}}_{1}},$ его распределения между фронтовым устройством и боковыми отверстиями для подачи воздуха в зону горения, конструкции горелочного и форсуночного устройств на концентрацию NOx проводились при сжигании газообразных и жидких топлив в камерах сгорания более чем 30 вариантов. Оказалось, что в таких КС значение коэффициента избытка воздуха в первой зоне слабо влияет на конечный выход NOх. Для созданной в то время конструкции камеры сгорания путем оптимизации распределения воздуха по трактам (значения ${{\alpha }_{1}}$) без ухудшения основных показателей камеры и конструктивных изменений пламенной трубы, фронтового устройства и форсунок концентрацию NOx удалось снизить на 30–40%.
Стендовые испытания в ВТИ разработанной Невским заводом микрофакельной камеры сгорания с вводом всего воздуха через фронтовое устройство без деления его на зоны смешения, охлаждения и горения (см. рис. 1, в) подтвердили преимущества сжигания с высокими избытками воздуха. В результате чрезвычайно интенсивного процесса выгорания концентрации NOx в этой КС в 2–3 раза ниже, чем в камерах с обычным диффузионным сжиганием. Один из недостатков микрофакельной КС – заметное снижение полноты выгорания топлива при пониженных нагрузках. Для обеспечения полноты сгорания была проведена оптимизация распределения топлива по коллекторам и горелкам.
КОМПЛЕКСНЫЙ ПОДХОД К ИССЛЕДОВАНИЮ ПРОЦЕССОВ ГОРЕНИЯ
Начатые в 60-х годах XX в. теоретические и расчетные исследования, экспериментальные работы на стендах и испытания на ГТУ способствовали созданию комплексного подхода к исследованию процессов горения и разработке конструкций КС, доказавшего в дальнейшем свою эффективность. В частности, развитие хорошо изученной конструкции (прототипа) ГТУ с отработанными технологией изготовления и алгоритмами управления существенно сокращает время и финансовые затраты на производство по сравнению с новой разработкой. Для создания ГТУ мощностью, отличной от мощности прототипа, иногда возможно простое изменение количества жаровых труб без изменения основных параметров и конструкций горелочного устройства и жаровой трубы. Такое изменение, однако, не всегда может быть реализовано при необходимости привязки к заданным стыковочным размерам.
При масштабировании (увеличении или уменьшении) отработанной конструкции МЭКС под другую ГТУ важно для обеспечения повторяемости результатов и управляемости процессами сохранять условия подобия, т.е. геометрические, гидродинамические, термодинамические и прочие характеристики должны быть подобны.
Сопоставление и анализ подтвержденных экспериментом результатов расчетов позволяют при создании КС для ГТУ мощностью, отличной от мощности отработанной конструкции МЭКС, добиться в разных геометрических масштабах подобия [4] следующих процессов:
• гидродинамических – близости распределения воздуха по трактам горелочных устройств; равенства скоростей в проходных площадях элементов; равенства потерь давления на элементах; формирования зон стабилизации (рециркуляции), их положения в пространстве ЖТ и равенства долей массы рециркулирующего потока относительно общего расхода воздуха;
• термодинамических – коэффициентов теплопередачи, полей температур, выгорания топлива, распределения тепловыделения по длине и объему МЭКС и пр.
По мере развития технологий производства и разработки новых материалов, конструкции МЭКС, конечно, обновляются при сохранении ранее отработанных принципиальных решений. Показанная на рис. 2 конструкция МЭКС была отработана для ГТЭ-110М.
Рис. 2.
Схема распределения воздуха и топлива в МЭКС ГТ-110М. 1 – пилотная горелка (ПГ); 2 – основная горелка (ОГ); 3 – жаровая труба; 4 – отверстия смешения для подачи вторичного воздуха; 5 – распределительный кожух охлаждения; 6 – газосборник; в сечении 1–1 анализируется состав ТВС
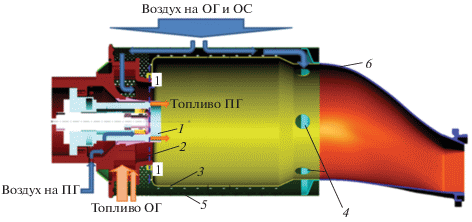
Основной принцип функционирования этой МЭКС – стабилизация пламени в предварительно закрученном потоке. Расположенная по оси жаровой трубы пилотная горелка служит для розжига КС и стабилизации горения на нагрузках ${{N}_{{\text{э}}}}$ < 50%. Бóльшая часть воздуха для горения подается в камеру сгорания через радиальный завихритель основной горелки (ОГ) (поз. 2). Топливо вводится через отверстия в лопатках завихрителя ОГ, объединенные в два независимых канала. Размеры завихрителя и топливоподающих отверстий были оптимизированы с помощью программного комплекса Flow Vision [5] для обеспечения однородности поступающей в зону горения топливовоздушной смеси и выполнения требования по эмиссии NOx < 50 мг/м3 (при нормальных условиях). Все значения приводятся к содержанию в уходящих газах 15% O2.
Путем перераспределения основного топлива между каналами завихрителями осуществляется управление положением фронта пламени, необходимым для устойчивого горения. Импактное охлаждение наружной поверхности наиболее теплонапряженной части жаровой трубы позволило снизить требуемый для этого расход воздуха. В выходной части жаровой трубы (газосборнике) имеются отверстия, через которые подается вторичный воздух, выравнивающий поле температур на выходе из КС.
При испытаниях МЭКС ГТ-110М были получены основные зависимости между параметрами, определяющими режимы ее работы. Эти зависимости связывают результаты расчетов и данные экспериментов. В качестве примера на рис. 3, а приведена зависимость концентрации NOx$\left( {{{C}_{{{\text{N}}{{{\text{O}}}_{x}}}}}} \right),$ измеренной на выходе из КС, от неоднородности ТВС смеси σ, оцененной в сечении 1–1 (см. рис. 2), а на рис. 3, б – измеренные концентрации NOx в заисимости от давления воздуха на входе КС при разных значениях ${{\sigma }_{{{{C}_{{{\text{C}}{{{\text{H}}}_{{\text{4}}}}}}}}}},$ также определенных в сечении 1–1 [6].
Рис. 3.
Зависимость эмиссии NOx от неоднородности топливовоздушной смеси на выходе из зоны предварительного перемешивания в сечении 1–1 (см. рис. 2) при давлении воздуха на входе в КС p = 340 кПа при 15% O2 (а) и от давления воздуха на входе в КС при разных значениях ${{\sigma }_{{{{C}_{{{\text{C}}{{{\text{H}}}_{{\text{4}}}}}}}}}}$ при 15% O2 (б). ${{\sigma }_{{{{C}_{{{\text{C}}{{{\text{H}}}_{{\text{4}}}}}}}}}}{\text{:}}$ 1 – 0.00517; 2 – 0.0098; 3 – 0.0169; 4 – 0.0262
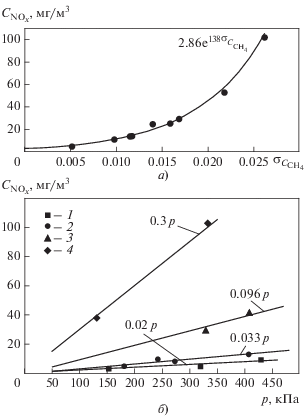
Неоднородность ${{\sigma }_{{{{C}_{{{\text{C}}{{{\text{H}}}_{{\text{4}}}}}}}}}}$ вычисляется по формуле
(1)
${{\sigma }_{{{{C}_{{{\text{C}}{{{\text{H}}}_{4}}}}}}}} = \sqrt {\frac{{\int\limits_S {{{{\left( {{{C}_{{{\text{C}}{{{\text{H}}}_{4}}}}} - \overline {{{C}_{{{\text{C}}{{{\text{H}}}_{{{{4}_{k}}}}}}}}} } \right)}}^{2}}\rho {{V}_{n}}{\text{d}}S} }}{{\int\limits_S {\rho {{V}_{n}}{\text{d}}S} }}} ,$Как в расчете, так и в эксперименте изменение неравномерности поля концентрации ${{\sigma }_{{{{C}_{{{\text{C}}{{{\text{H}}}_{{\text{4}}}}}}}}}}$ на выходе из зоны предварительного перемешивания (см. сечение 1–1 на рис. 2) создавалось перераспределением топлива между двумя основными каналами. Количественно полученные зависимости справедливы только в диапазоне исследованных режимов данной конфигурации КС, однако качественно они применимы значительно шире, например при разработке МЭКС для ГТУ других мощностей [4].
Следует отметить, что переменные для построения зависимостей выбираются из соображений физической понятности и минимального разброса данных относительно аппроксимирующих кривых.
Для разработки камеры сгорания ГТУ меньшей мощности, чем мощность ГТЭ-110М, на всех этапах, начиная с эскизного проекта, достижение расчетных параметров увязывают с конструкцией, доступными и перспективными технологиями и материалами, необходимым объемом испытаний на имеющихся экспериментальных стендах.
Использование современных программных продуктов, обеспечивающих проведение расчетных исследований процессов в МЭКС и анализ микропараметров, недоступных в эксперименте (рис. 4), позволяют получить необходимый результат, существенно сократив затраты и время на поиск правильного решения и дальнейшую его оптимизацию. В частности, расчетно-экспериментальный подход был применен для доводки полей температуры на выходе из камеры сгорания до поля, заданного техническим заданием. С использованием программного продукта Flow Vision была проведена оптимизация отверстий смешения и выбраны диаметр, положение и количество отверстий вторичного воздуха.
В таблице представлены рассчитанные значения окружной неравномерности температуры ${{\theta }}$ для пяти вариантов, которые различаются количеством, диаметром и распределением по окружности отверстий смешения при их идентичной суммарной площади проходного сечения, а также их расположением относительно вертикали.
Неравномерность поля температуры на выходе из КС определяли по формуле
(2)
${{\theta }} = \frac{{{{t}_{{\max \_{\text{вых}}}}} - {{t}_{{{\text{вх}}}}}}}{{{{t}_{{mean\_{\text{вых}}}}} - {{t}_{{{\text{вх}}}}}}},$Наилучший вариант расположения отверстий смешения (вариант 5) был изготовлен и испытан в [7]. Примеры расчетных и измеренных полей температуры на выходе из МЭКС приведены на рис. 5.
Рис. 5.
Поля температуры на выходе из газосборника: экспериментально измеренные (а, в) и рассчитанные (б, г). a, б – базовый вариант; в, г – вариант 5
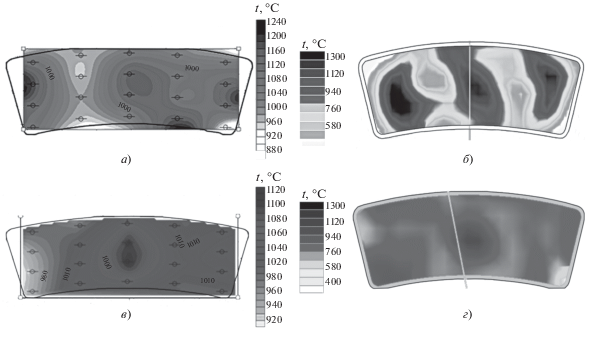
Организация устойчивого горения, не вызывающего пульсаций давления с недопустимыми амплитудами в объеме КС, – задача, с которой сталкиваются все разработчики МЭКС. Сложность ее решения обусловлена тем, что вызывающие их (пульсации) процессы нестационарного горения требуют специальных исследований. Например, для реализации методов лазерно-индуцированной флуоресценции (LIF и PLIF) [8] необходим доступ с высококачественной оптикой в зону горения, организовать который в условиях реальной МЭКС практически невозможно. Численные методы исследования динамических процессов горения в настоящее время интенсивно развиваются, но требуют значительных компьютерных мощностей, а для их верификации и настройки моделей следует проводить специальные эксперименты.
В то же время расчеты стационарных процессов в КС хорошо отработаны и доказали свою практическую применимость и надежность [9]. Физически понятную связь между стационарными параметрами, такими как распределение температуры, давления, плотности, скорости, тепловыделения в объеме жаровой трубы, и замеряемыми в эксперименте пульсациями давления [10] можно обосновать, если сформулировать ее в виде критериальной зависимости расчетного критерия устойчивости горения
(3)
${\text{Bu}} = \frac{{\max {\text{grad}}(t) \times \max {\text{grad}}(V)}}{{{\text{d}}{{l}_{{{\text{grad}}}}}}},$Представленная на рис. 6 зависимость отражает связь между процессами течения и горения (тепловыделения) в объеме КС. Ключевой является взаимосвязь между положением фронта пламени относительно сформированного горелочным устройством поля скорости, его неравномерностью, зонами рециркуляции и отрывными течениями, возбуждающими пульсации давления. Известны разные методы изменения процесса течения в КС и управления положением фронта пламени. На его положение и конфигурацию влияет, в частности, распределение расходов топлива в горелках, которое традиционно используется для расширения диапазона устойчивых рабочих режимов КС.
Рис. 6.
Зависимость между расчетным параметром устойчивости горения Bu и измеренными амплитудами пульсаций давления $A{\kern 1pt} '$ в МЭКС
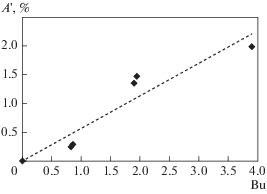
На рис. 7 показано изменение спектрального состава пульсаций давления, наблюдаемое при переходе к автоколебательному режиму горения.
ПЕРСПЕКТИВНЫЕ НАПРАВЛЕНИЯ ИССЛЕДОВАНИЙ
Развитие энергетических ГТУ достигло сейчас уровня, когда средние температуры газов на выходе из камер сгорания превышают 1600°C, после чего окисление оксидов азота резко интенсифицируется. Для выполнения в этих условиях действующих экологических требований в ВТИ проводятся исследования двухступенчатой схемы сжигания топлив [12].
Проведены как расчетные, так и экспериментальные исследования распределения топлива и избытка воздуха по ступеням, оптимальных размеров первой и второй зон горения, скоростей потока, времени пребывания, соотношений топлива по каналам, температур, полноты сгорания и пр. Достигнуто понимание особенностей и эффективности такой схемы сжигания, которая позволяет в 2 раза и более снизить эмиссию NOx по сравнению с традиционными схемами сжигания.
На рис. 8, а показана схема последовательного двухступенчатого сжигания топлива, на рис. 8, б – ее эффективность (снижение относительной концентрации $\overline {{{C}_{{{\text{N}}{{{\text{O}}}_{x}}}}}} $) по мере увеличения температуры на выходе из камеры сгорания. Относительная концентрация $\overline {{{C}_{{{\text{N}}{{{\text{O}}}_{x}}}}}} $ определяется как отношение концентраций NOx при последовательном двухступенчатом сжигании к полученной при одноступенчатом сжигании (одна зона горения).
Рис. 8.
Схема последовательного двухступенчатого сжигания топлива (а) и зависимость концентрации $\overline {{{C}_{{{\text{N}}{{{\text{O}}}_{x}}}}}} $ от температуры газов на выходе из КС (б)
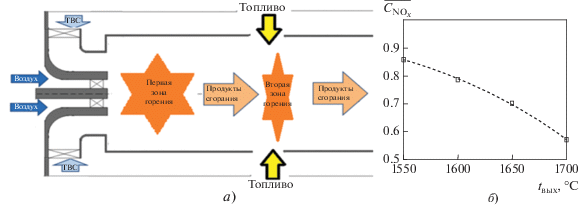
Преимуществами двухступенчатой (двухзонной) схемы являются также расширение малоэмиссионного горения в область низких нагрузок и обеспечение устойчивой работы МЭКС в широком диапазоне изменений климатических условий, а также составов топлив.
ВЫВОДЫ
1. Всероссийский теплотехнический институт традиционно проводит исследования камер сгорания энергетических ГТУ для обеспечения их надежной, экономичной работы в широком диапазоне режимов с минимальными выбросами вредных веществ.
2. Для решения возникающих при этом задач используются коммерческие программные продукты по трехмерному численному моделированию и экспериментальный стенд с давлением воздуха до 800 кПа, удовлетворяющий требованиям по расходам и температурам воздуха и природного газа в реальных камерах сгорания. Опыт института позволяет обеспечивать эффективное устойчивое и малоэмиссионное горение в камерах сгорания ГТУ в широком диапазоне режимов, при пуске и быстрых изменениях нагрузки.
3. Разработанная в ВТИ методика масштабирования позволяет при изменении геометрических размеров конструкции моделировать подобные процессы, протекающие в камере сгорания, тем самым переносить полученные результаты на МЭКС с диаметрами жаровых труб, отличающимися более чем в 2 раза от прототипа.
4. Знания о зависимостях между влияющими факторами и процессами горения дают возможность расширять диапазон мощностей малоэмиссионных режимов МЭКС с сохранением требуемых характеристик на выходе.
5. Начаты и развиваются исследования МЭКС для сжигания топлив с высокими температурами на выходе из камеры сгорания (до 1800°С) с эмиссией оксидов азота ниже нормативных значений.
Список литературы
Тумановский А.Г. Некоторые пути снижения оксидов азота в камерах сгорания // Теплоэнергетика. 1973. № 6. С. 9–13.
Тумановский А.Г. Некоторые особенности образования окислов азота в высокофорсированных камерах сгорания с последовательным вводом воздуха в зону горения // Теплоэнергетика. 1977. № 7. С. 65–70.
Христич В.А., Тумановский А.Г. Газотурбинные установки и защита окружающей среды. Киев: Технiка, 1983.
Опыт масштабирования конструкции МЭКС для применения в ГТУ разной мощности / Л.А. Булысова, А.Г. Тумановский, М.Н. Гутник, В.Д. Васильев // Электрические станции. 2020. № 4. С. 2–7. https://doi.org/10.34831/EP.2020.1065.4.001
https://tesis.com.ru/own_design/flowvision/
Васильев В.Д., Булысова Л.А., Берне А.Л. Влияние эпюры концентрации топливовоздушной смеси на динамические процессы в малоэмиссионной камере сгорания // Теплоэнергетика. 2016. № 12. С. 35–41. https://doi.org/10.1134/S0040363616120079
Математическое моделирование при создании и доводке малоэмиссионных камер сгорания / Л.А. Булысова, В.Д. Васильев, М.М. Гутник, М.Н. Гутник, А.Г. Тумановский // Газотурбинные технологии. 2010. № 9. С. 17–22.
https://www.smart-piv.com/en/applications/combustion/
Passive control of combustion instability in lean premixed combustors / R.C. Steele, L.H. Cowell, S.M. Cannon, C.E. Smith // J. Eng. Gas Turbines Power. 2000. V. 122. № 3. P. 412–419. https://doi.org/10.1115/1.1287166
Булысова Л.А., Горбань В.Н. Влияние перемешивания топлива и воздуха на процесс горения в малоэмиссионной камере сгорания // Теплоэнергетика. 2013. № 9. С. 15–20.
Факторы, определяющие форму пламени, и их связь с устойчивостью горения в малоэмиссионных камерах сгорания ГТУ / Л.А. Булысова, А.Г. Тумановский, М.Н. Гутник, В.Д. Васильев // Электрические станции. 2020. № 6. С. 2–5. https://doi.org/10.34831/EP.2020.1067.6.001
Экспериментальные исследования эмиссии NOx при последовательном сжигании топлива с диффузионной второй зоной / Л.А. Булысова, В.Д. Васильев, М.Н. Гутник, А.Л. Берне // Теплоэнергетика. 2019. № 6. С. 33–40. https://doi.org/10.1134/S004036361906002X
Дополнительные материалы отсутствуют.
Инструменты
Теплоэнергетика