Теплоэнергетика, 2021, № 9, стр. 79-84
Мониторинг рисков на основе ранней диагностики потенциальных повреждений энергооборудования
А. А. Дубов *
ООО “Энергодиагностика”
143965г. Реутов, Московская обл., Юбилейный просп., д. 8, пом. XII, Россия
* E-mail: mail@energodiagnostika.ru
Поступила в редакцию 11.08.2020
После доработки 29.10.2020
Принята к публикации 23.12.2020
Аннотация
В настоящее время с целью обеспечить безопасность промышленных объектов активно развиваются диагностика и мониторинг состояния потенциально опасного оборудования и рисков его эксплуатации. При этом оценка рисков в процессе эксплуатации различных технических устройств (ТУ) осуществляется на основе имеющейся статистики повреждений, которая накопилась за прошедший период работы ТУ, т.е. используется вероятностный подход. Такой подход является несовершенным и недостаточно объективным, так как оценка рисков делается на будущий период времени, когда состояние ТУ может существенно измениться и усталостные повреждения отдельных узлов оборудования могут произойти в тех зонах, которые, как правило, не совпадают с расчетными. В статье предлагается выполнять оценку рисков на основе ранней диагностики наиболее повреждаемых элементов оборудования ТЭС. Для реализации этой задачи необходимо более широкое использование методов неразрушающего контроля фактического напряженно-деформированного состояния в целях выявления зон концентрации напряжений (ЗКН) – основных источников повреждений и современных методов ранней диагностики: акустической эмиссии, магнитной памяти металла (МПМ), теплового контроля. Рассматривается пример ранней диагностики развивающегося повреждения из практики применения метода МПМ при контроле гиба паропровода. Показано, что для ТЭС с поперечными связями разница в экономическом ущербе при оценке риска может быть значительной при повреждении паропровода и повреждении котельной трубы.
Наиболее повреждаемыми элементами оборудования ТЭС являются поверхности нагрева (ПН) паровых и водогрейных котлов, гибы паро- и водоперепускных труб котлов, гибы паропроводов, лопатки и диски паровых турбин. Одна из причин высокой повреждаемости указанных элементов – отсутствие в широкой практике методов ранней диагностики развивающихся повреждений.
С этой целью применяется главным образом дефектоскопия с поиском недопустимых дефектов (при этом научно обоснованных норм на размеры допустимых дефектов, основанных на положениях механики разрушения, как правило, нет). Следует особо отметить, что распределение рабочих и остаточных напряжений, определяющих надежность технических устройств, и локализация этих напряжений до сих пор в широкой практике не контролируются.
При эксплуатации ТУ основными источниками повреждений металла являются зоны концентрации напряжений, в которых процессы коррозии, усталости и ползучести протекают наиболее интенсивно. При оценке ресурса энергооборудования необходимо исследовать в первую очередь структурно-механические свойства металла именно в ЗКН. В этой связи следует отметить недостаточную чувствительность традиционных методов неразрушающего контроля (НК) (ультразвуковой и магнитопорошковой дефектоскопии, радиографического метода) к определению дефектов на раннем этапе их развития, т.е. на уровне структурных изменений.
В настоящее время все большее распространение в практике ранней диагностики развивающихся повреждений получает метод магнитной памяти металла. Основное назначение этого метода – обнаружение ЗКН на элементах оборудования и в конструкциях в режиме экспресс-контроля с использованием специализированных приборов и сканирующих устройств.
Зоны концентрации напряжений – это не только заранее известные области, где из-за особенностей конструкции возникают различные условия для распределения напряжений, создаваемых внешней нагрузкой, но и случайно расположенные области, где в силу начальной неоднородности металла в сочетании с нерасчетными дополнительными рабочими нагрузками возникают большие деформации. Контроль состояния поверхности методом МПМ осуществляется без зачистки металла и искусственного намагничивания. Используется остаточная намагниченность, которая возникла естественным образом при изготовлении изделий и в процессе их эксплуатации.
Физические основы метода МПМ рассмотрены в [1], его возможности при диагностике котельных труб – в [2], а турбинного оборудования – в [3]. Методика контроля гибов котельных и паропроводных труб с использованием магнитной памяти металла описана в [4].
Как уже указывалось, основное назначение метода МПМ – определение фактического напряженно-деформированного состояния (НДС) различных узлов оборудования и выявление ЗКН. Здесь следует отметить, что еще в январе 2017 г. вступил в силу приказ Ростехнадзора № 316 от 28 июля 2016 г., на основании которого внесены изменения в федеральные нормы и “Правила проведения экспертизы промышленной безопасности” [5]. В соответствии с этими Правилами при проведении экспертизы технических устройств установлена необходимость контроля (изучения) их НДС.
Несмотря на то что российский стандарт по контролю состояния металла оборудования ТЭС [6] подготовлен и введен в действие в январе 2019 г., т.е. позже приказа Ростехнадзора № 316, четких рекомендаций о необходимости неразрушающего контроля НДС оборудования и о том, какими методами он должен проводиться, в стандарте нет.
Следует подчеркнуть еще раз, что без решения проблем, которые в настоящее время существуют при выполнении контроля фактического НДС различных ТУ, невозможно обеспечить их надежность [7]. Кроме того, все большее развитие получает риск-ориентированное управление техническим состоянием энергооборудования [8]. Поэтому методы ранней диагностики развивающихся повреждений, к которым относится и метод МПМ, крайне необходимы.
Для определения рисков при эксплуатации различных ТУ используется главным образом детерминированный подход. Оценка вероятности аварийных ситуаций осуществляется на основе имеющихся статистических данных повреждений, которые накопились за прошедший период эксплуатации ТУ. Такой подход является несовершенным и недостаточно объективным, так как оценка рисков делается на будущий период времени, когда состояние ТУ может существенно измениться и усталостные повреждения отдельных узлов оборудования могут произойти (и, как правило, происходят) в тех зонах, которые не совпадают с расчетными.
Еще в 2008 г. был опубликован ГОСТ Р 53006-2008 “Оценка ресурса потенциально опасных объектов на основе экспресс-методов. Общие требования”. Именно рекомендации данного стандарта направлены на реализацию объективного подхода при оценке ресурса и рисков потенциально опасных объектов. Принципиальным отличием такого подхода к оценке ресурса является выполнение 100%-ного обследования ТУ с выявлением всех потенциально опасных зон концентрации напряжений – источников возникновения повреждений при дальнейшей эксплуатации оборудования.
Выявленные в ЗКН с использованием традиционных методов дефектоскопии (ультразвуковой, радиографический, вихретоковый контроль и др.) недопустимые дефекты, как правило, подлежат удалению. Поверочные расчеты на прочность с оценкой остаточного ресурса в этом стандарте предлагается выполнять для ЗКН, остающихся в эксплуатации, с учетом фактических структурно-механических свойств металла, выявленных при обследовании в этих зонах.
На рис. 1 представлена структурная схема определения остаточного ресурса оборудования с использованием экспресс-методов неразрушающего контроля.
К экспресс-методам относятся пассивные методы НК, в которых используется внутренняя энергия металла конструкций:
акустической эмиссии;
магнитной памяти металла;
тепловой контроль.
Эти методы получили в настоящее время наиболее широкое распространение при проведении ранней диагностики повреждений оборудования и конструкций.
На основе комплексного диагностического обследования и расчетно-экспертной оценки, рекомендуемых стандартом ГОСТ Р 53006-2008, представляется возможным принять одно из решений по обеспечению надежности объекта контроля: ремонт, замена отдельных узлов, продление ресурса с назначенным сроком безопасной эксплуатации или вывод объекта из эксплуатации.
При проведении экспериментальных исследований установлено, что уровень напряжений в локальных ЗКН, размеры которых колеблются от десятков микрон до нескольких миллиметров, может значительно превышать не только предел текучести, но и предел прочности металла.
Опыт обследования различного оборудования трубопроводов, конструкций, вращающихся механизмов с использованием метода магнитной памяти металла показывает, что только в 5–10% всего объема металла оборудования наблюдается развитие повреждений в ЗКН после длительной его эксплуатации. Однако, как правило, заранее места образования ЗКН и уровень деградации металла в этих зонах не известны.
Далее рассматривается практический пример применения метода МПМ при контроле гибов паропровода.
На рис. 2, а представлена схема выполнения контроля гиба с использованием специализированного сканирующего устройства, а на рис. 2, б – результаты контроля методом МПМ растянутой зоны гиба ∅219 × 25 мм (сталь 15Х1М1Ф) пароперепускной трубы цилиндра высокого давления турбины ПТ-60. Данный гиб на момент контроля имел наработку около 200 000 ч. В зоне максимальной концентрации напряжений, которая характеризуется резким локальным изменением собственного магнитного поля рассеяния – напряженности магнитного поля Нр и ее градиента dН/dx, с наружной поверхности гиба была взята реплика для анализа структуры металла.
Рис. 2.
Результаты контроля методом МПМ растянутой зоны гиба ∅219 × 25 мм (сталь 15Х1М1Ф). а – схема выполнения контроля гиба; б – распределение напряженности магнитного поля Нр (1) и ее градиента dН/dx (2) по длине гиба x с его наружной поверхности; три линии соответствуют трем каналам измерений
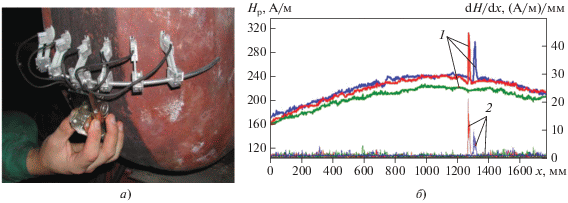
На рис. 3 показана структура металла гиба в месте взятия реплики, полученная на оптическом микроскопе с увеличением в 500 раз. Хорошо видны поры, объединенные развитой трещиной между ними. Такая структура с повреждением металла оценивается баллом 7 по шкале ВТИ [9]. На данном гибе рекомендовано сделать шлифовку поверхности для удаления поврежденного слоя металла. Следует отметить, что если своевременно не выявить эту поврежденную зону металла и не удалить ее, то в межремонтный период с большой долей вероятности может произойти разрушение гиба.
Рис. 3.
Структура металла в зоне реплики, взятой с поверхности гиба ∅219 × 25 мм (сталь 15Х1М1Ф), полученная с помощью микроскопа (500-кратное увеличение)
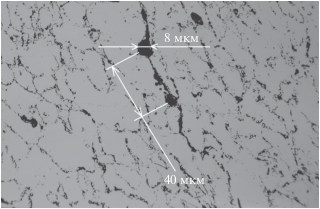
Методика оценки уровня напряжений и предельного состояния металла в ЗКН, выявленных методом МПМ по градиенту магнитного поля, представлена в работах [10, 11].
При реализации рекомендаций, содержащихся в ГОСТ Р 53006-2008, представляется возможным в большинстве случаев без выполнения сложных поверочных расчетов на прочность делать экспертную оценку ресурса на основе комплексного обследования оборудования и назначать срок безопасной эксплуатации.
Разработка методик оценки риска с учетом особенностей и требований к объекту контроля, существующих в теплоэнергетике [6], возможна с использованием рекомендаций указанного стандарта для конкретного оборудования. При этом оценка риска становится более конкретной, так как на основе 100%-ного обследования оборудования выявляются зоны потенциальных повреждений и степень их опасности для развития аварий.
Так, на современной тепловой электростанции повреждение котельной трубы, расположенной внутри топки котла, приводит к аварийному останову этого котла с простоем в ремонте примерно 3 сут. Расчет экономического ущерба от аварийного простоя котла в течение 2–3 сут не составляет проблемы, и такая методика расчета имеется на большинстве современных ТЭС. Если же повреждение происходит на паропроводе, соединяющем одновременно несколько энергетических котлов (ТЭС с поперечными связями), то расчет экономического ущерба при оценке риска становится уже значительно более сложным, так как повреждение паропровода, как правило, вызывает одновременный аварийный останов сразу нескольких котлов ТЭС (рис. 4). В отдельных случаях разрыв паропровода и развитие аварии могут привести к останову всей электростанции (посадка ТЭС на “0”). Экономический ущерб в таком случае на порядок больше. Таким образом, ранняя диагностика зон потенциальных повреждений технических устройств на опасных производственных объектах имеет большое значение и при оценке рисков.
Рис. 4.
Типовая схема ТЭС. К1–К4 – котлы; Т1–Т3– турбины; ◆ – условное обозначение места повреждения на внутренней поверхности трубы котла (К1), приведшего к его аварийному останову; ◆◆ – условное обозначение места повреждения паропровода ТЭС
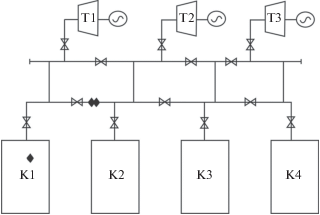
Известно [12], что критерии приемлемых рисков можно определить по выражению:
При оценке показателя Pi(τ) в настоящее время используется вероятностный подход, основанный на статистике уже случившихся повреждений и аварий. Применение методов ранней диагностики оборудования и конструкций, к которым относится, например, метод МПМ, позволит сделать оценку рисков более определенной.
ВЫВОДЫ
1. Для ранней диагностики энергооборудования в целях выявления мест потенциальных повреждений возможно применение метода магнитной памяти металла.
2. Методы ранней диагностики позволяют осуществить переход от вероятностной оценки рисков (на основе статистики уже случившихся повреждений энергооборудования) к более определенной оценке.
Список литературы
Власов В.Т., Дубов А.А. Физические основы метода магнитной памяти металла. М.: ЗАО “Тиссо”, 2004.
Дубов А.А. Диагностика котельных труб с использованием магнитной памяти металла. М.: Энергоатомиздат, 1995.
Дубов А.А. Диагностика турбинного оборудования с использованием магнитной памяти металла. М.: ЗАО “Тиссо”, 2009.
Дубов А.А. Метод контроля гибов котельных и паропроводных труб с использованием магнитной памяти металла // Теплоэнергетика. 2001. № 4. С. 31–36.
Федеральные нормы и правила в области промышленной безопасности “Правила проведения экспертизы промышленной безопасности”. Утв. приказом Ростехнадзора № 420 от 20.10.2020.
ГОСТ Р 58177-2018. Тепловые электрические станции. Оборудование тепломеханическое тепловых электростанций. Контроль состояния металла. Нормы и требования.
Дубов А.А. Контроль напряженно-деформированного состояния технических устройств // ТехНАДЗОР. 2017. № 6 (127). С. 16–18.
Антоненко И.Н. Риск-ориентированное управление техническим состоянием активов в энергетике // В мире неразрушающего контроля. 2020. Т. 23. № 1. С. 18–22. https://doi.org/10.12737/1609-3178-2020-10-14
СО 153-34.17.470. Инструкция о порядке обследования и продлении срока службы паропроводов сверх паркового ресурса. М.: ЦНТИ ОРГРЭС, 2004.
Дубов А.А., Дубов Ал.А., Колокольников С.М. Метод магнитной памяти металла и приборы контроля: учеб. пособие. 5-е изд. М.: ЗАО “Тиссо”, 2012.
Дубов А.А. Метрологические аспекты в методе магнитной памяти металла // Мир измерений. 2018. № 3. С. 42–45; № 4. С. 41–43.
Махутов Н.А., Гаденин М.М. Техногенная безопасность. Диагностика и мониторинг состояния потенциально опасного оборудования и рисков его эксплуатации: Федеральный справ. Информ.-аналит. изд. Т. 26. М.: НП “Центр стратегического партнерства”, 2012. С. 307–314.
Дополнительные материалы отсутствуют.
Инструменты
Теплоэнергетика