Теплоэнергетика, 2022, № 11, стр. 16-27
Анализ теплотехнических характеристик теплосилового контура АЭС малой мощности на неводных рабочих веществах
А. А. Сухих a, b, *, И. С. Антаненкова b, Чан Куок Тхинь b
a НИЦ “Курчатовский институт”
123182 Москва, пл. Академика Курчатова, д. 1, Россия
b Национальный исследовательский университет “Московский энергетический институт”
111250 Москва, Красноказарменная ул., д. 14, Россия
* E-mail: sukhikhaa@mpei.ru
Поступила в редакцию 28.03.2022
После доработки 14.04.2022
Принята к публикации 28.04.2022
- EDN: VQCJFW
- DOI: 10.56304/S004036362211008X
Аннотация
Приведена предпроектная оценка перспектив разработки теплосиловых контуров атомных электростанций малой мощности (АЭСММ) на различных неводных рабочих веществах. Представлены результаты анализа вариантов исполнения II (турбинного) контура АЭСММ, I контур которой включает в себя микротопливный автономный расплавно-солевой реактор (МАРС). Рассмотрены тепловые схемы воздушной газотурбинной установки открытого типа без регенерации, газотурбинной установки с двухступенчатым сжатием воздуха в компрессоре и регенерацией, а также паротурбинной установки на октафторпропане (C3F8), работающей по органическому циклу Ренкина. Показана возможность достижения наибольшей термодинамической эффективности преобразования тепловой энергии на базе паротурбинной установки на октафторпропане при температурах до 650°С. Расчетный КПД цикла такой установки превышает 50%, а КПД безрегенерационной ГТУ составляет не более 33%. Проведено сравнение основных теплотехнических и массогабаритных характеристик оборудования теплосилового контура АЭСММ для предложенных вариантов исполнения. Выявлено, что главной технической проблемой при разработке и внедрении теплосилового оборудования II контура на основе ГТУ будут массовые и габаритные характеристики теплообменника активной зоны и регенератора “воздух – воздух” вследствие невысоких коэффициентов теплопередачи. Показано, что использование октафторпропана в качестве рабочего тела турбинного контура позволит существенно уменьшить массогабаритные характеристики основных аппаратов, а следовательно, снизить гидравлические потери в них и стоимость. Полученные результаты свидетельствуют о возможности снижения массы регенеративных аппаратов на октафторпропане в сравнении с воздушными аналогами до 15 раз. С учетом результатов проведенного анализа сформулирован перечень первоочередных технических задач, решение которых позволит успешно реализовать разработку теплоcилового контура АЭСММ.
В настоящее время актуальным является вопрос энергообеспечения удаленных и труднодоступных регионов России. В районах Крайнего Севера и приравненных к ним лишь незначительная часть территории находится в зоне действия энергетических систем. На остальной территории энергоснабжение потребителей осуществляется от автономных энергоисточников, основную долю которых составляют дизельные электростанции (ДЭС), работающие на привозном топливе. В наиболее удаленных населенных пунктах себестоимость производства энергии от ДЭС в 5−10 раз выше, чем на электростанциях локальных энергоузлов [до 18 руб/(кВт · ч)], прежде всего из-за транспортной составляющей. В качестве альтернативных автономных энергоисточников, применение которых позволит повысить эффективность энергоснабжения потребителей, могут выступать не только современные ДЭС и газотурбинные установки (ГТУ) с отбором тепла, но и мини-ТЭЦ, на которых используются местные виды топлива, а также атомные электростанции малой мощности.
Не исключено, что наилучшим решением всех технических и организационных проблем может стать строительство АЭСММ. Большим преимуществом таких электростанций являются значительно меньшие единовременные затраты на реализацию проекта, чем для крупных АЭС, а также существенное снижение большинства технических, радиационных и экономических рисков, что весьма важно и для привлечения инвесторов. Модульные АЭСММ менее подвержены воздействию стихийных бедствий и возникновению чрезвычайных ситуаций, чем крупные АЭС, эксплуатирующиеся в большинстве стран мира [1, 2].
Во многих странах построены единичные АЭСММ на основе различных технологий: с водо-водяными энергетическими реакторами, с реакторными установками на быстрых нейтронах с жидкометаллическими теплоносителями и теплоносителями на базе солевых расплавов [2]. Для преобразования тепловой энергии на этих АЭС используются как водопаровые циклы Ренкина, так и газовые циклы Брайтона открытого и закрытого типов (в том числе и на гелии, и на диоксиде углерода).
Среди возможных комбинаций типов ядерного топлива и теплоносителя, предназначенных для решения целевых задач создания ядерных энергоустановок (ЯЭУ) малой мощности для удаленных и труднодоступных регионов, особое место занимает вариант использования в I контуре графитовых твэлов на основе микротвэлов и расплавов солей – фторидов лития, натрия, бериллия, циркония. Работы по созданию таких реакторов ведутся в НИЦ “Курчатовский институт” с начала 70-х годов прошлого века. Анализ этих работ позволяет выделить два основных направления исследований по созданию реакторов: с жидким циркулирующим топливом [3, 4] и с использованием в качестве теплоносителя солевой композиции, а в качестве топлива ‒ шаровых твэлов [5, 6]. Последние отличаются повышенным уровнем радиационной и технологической безопасности.
Однако не менее актуальны вопросы разработки схемы турбинного контура АЭСММ и выбора наиболее оптимального рабочего тела ЯЭУ – преобразователя тепловой энергии, полученной от теплоносителя, в механическую. В настоящей работе представлены результаты анализа вариантов исполнения турбинного контура АЭСММ, I контур которой включает в себя реактор МАРС.
Основные характеристики I контура АЭСММ, необходимые для выполнения вариантных теплотехнических расчетов теплосиловых циклов, заданы в соответствии с исходными данными проекта реактора МАРС [6]:
Массовый расход теплоносителя |
через активную зону Gsm1, кг/с…………….......29.4 |
Температура теплоносителя, °C: |
на входе в активную зону $t_{{sm}}^{{in}}$………….....….550 |
на выходе из активной зоны $t_{{sm}}^{{out}}$……......…750 |
минимальная (незамерзания)…………......360 |
максимальная (при аварии)………....…….1300 |
Средняя/максимальная/предельная |
температура топлива при нормальных условиях, °С….............................. 800/1000/1250 |
11Теплофизические свойства возможных теплоносителей ЯЭУ представлены в табл. 1 [6].
Таблица 1.
Теплофизические свойства теплоносителей ЯЭУ
Показатель | Солевой расплав | |
---|---|---|
NaF–BeF2 | LiF–BeF2 | |
Молярный состав, мол. % | 57‒43 (эвтектика) | 48‒52 (эвтектика) |
Температура плавления, °C | 360 | 350 |
Удельная теплоемкость сsm, Дж/(кг · К) | 2172 | 2720 |
Теплопроводность λsm, Вт/(м · К) | 1.00 | 1.19 |
Плотность ρsm, кг/м3 | 2270‒0.37t | 2220‒0.4t |
Динамический коэффициент вязкости μsm, Па · с | 3.46 × 10‒5exp (5164/t) | 1.89 × 10‒5exp (6174/t) |
Давление насыщенных паров рs_sm | Не более133 Па при t ≤ 800°C Менее 130 кПа при 1300°C |
lgps_sm = 9.44‒10130/t |
ТУРБИННЫЙ КОНТУР АЭСММ НА БАЗЕ ГТУ ОТКРЫТОГО ТИПА
В качестве первого варианта исполнения турбинного контура АЭСММ можно рассмотреть ГТУ (рис. 1).
Рис. 1.
Принципиальная схема установки АЭСММ-ГТУ (а) и T, s- диаграмма термодинамического цикла турбинного контура (б). I – реактор; II – активная зона; III – теплообменный аппарат “расплав соли – воздух”; IV – главный циркуляционный насос; V – компрессор; VI –турбина; VII – электрогенератор; Т – температура; s ‒ энтропия
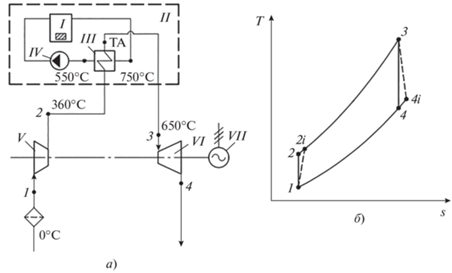
Для расчета тепловой схемы, помимо указанных на рис. 1 температур воздуха и расплава соли, было принято, что давление потока воздуха на входе в компрессор равно 0.1 МПа, внутренний КПД компрессора $\eta _{{0i}}^{{comp}}$ = 0.88, газовой турбины $\eta _{{0i}}^{{turb}}$ = 0.92. Внутренний КПД цикла ГТУ при данных значениях параметров составил $\eta _{i}^{{{\text{GTU}}}}$ = 0.335.
Расход воздуха в турбинном контуре ЯЭУ ${{G}_{{air}}},$ кг/с, вычисляется по уравнению теплового баланса теплообменного аппарата “расплав соли – воздух” активной зоны (Reactor Core), тепловая мощность которого (без учета тепловых потерь в I контуре) ${{Q}_{{RC}}}$, Вт, определяется как
(1)
${{Q}_{{RC}}} = {{G}_{{sm}}}{{с}_{{sm}}}\left( {t_{{sm}}^{{out}} - t_{{sm}}^{{in}}} \right) = {{G}_{{air}}}\left( {{{h}_{3}} - {{h}_{{2i}}}} \right),$При расчете параметров цикла ГТУ степень повышения давления выбирается таким образом, чтобы при заданной температуре перед турбиной (650°С) обеспечить температуру входящего в активную зону воздуха не ниже температуры затвердевания солевого расплава (360°С). Давление воздуха в активной зоне установки, определенное при заданных условиях, равнялось 1.54 МПа.
При выборе в качестве теплоносителя расплава соли NaF–BeF2 электрическая мощность АЭСММ-ГТУ составила 4.3 МВт при расходе воздуха ${{G}_{{air}}}$ = 40.2 кг/с.
ТЕПЛООБМЕННЫЙ АППАРАТ “РАСПЛАВ СОЛИ – ВОЗДУХ” АКТИВНОЙ ЗОНЫ АЭСММ-ГТУ
Компоновка труб и форма корпуса теплообменного аппарата (ТА) “расплав соли – воздух” должны быть выбраны на этапе проектирования АЭСММ-ГТУ. Корпус аппарата может иметь как цилиндрическую, так и прямоугольную форму.
Для оценки основных теплотехнических характеристик ТА был выбран прямоугольный корпус модуля с шахматной компоновкой n труб: n = = n1 (число труб по длине) × n2 (число труб по ширине), размещенных по углам равносторонних треугольников (рис. 2).
Рис. 2.
Конфигурация трубного пучка теплообменного аппарата “расплав соли – воздух” активной зоны АЭСММ-ГТУ. ${{S}_{1}}$, ${{S}_{2}}$ ‒ продольный и поперечный шаг труб; ${{\delta }_{1}}$ ‒ зазор между трубами в пучке; ${{L}_{1}}$, ${{L}_{2}}$ ‒ длина и ширина аппарата
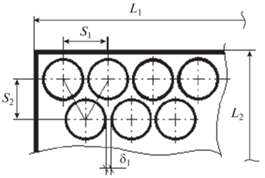
Формулы для расчета геометрических характеристик такого аппарата с трубами из жаропрочной нержавеющей стали ХН80МТЮ типоразмером D × δ = 0.032 × 0.003 м и результаты расчета при заданной средней скорости потока воздуха внутри труб ${{w}_{{air}}}$ = 20 м/с представлены в табл. 2.
Таблица 2.
Геометрические характеристики ТА “расплав соли – воздух” активной зоны АЭСММ-ГТУ
Характеристика | Формула для расчета | Значение |
---|---|---|
Площадь поперечного сечения для прохода воздуха, м2: | ||
теплообменного аппарата ${{f}_{{air}}}$ | Gair /(ρair wair) | 0.2934 |
одной трубы ${{f}_{{1air}}}$ | π(D – 2δ)2/4 | 5.31 × 10‒4 |
Число труб, шт.: | ||
в пучке n | fair /f1air | 550 |
по длине ТА ${{n}_{1}}$ | ‒ | 25 |
по ширине ТА ${{n}_{2}}$ | ‒ | 22 |
Зазор между трубами в пучке ${{\delta }_{1}}$, м | ‒ | 0.002 |
Шаг труб в пучке, м: | ‒ | |
продольный ${{S}_{1}}$ | D + δ1 | 0.034 |
поперечный ${{S}_{2}}$ | ${{\sqrt 3 {{S}_{1}}} \mathord{\left/ {\vphantom {{\sqrt 3 {{S}_{1}}} 2}} \right. \kern-0em} 2}$ | 0.0294 |
Площадь межтрубного просвета для прохода солевого расплава Fsm, м | ${{L}_{1}} \times {{L}_{2}} - n\frac{{\pi {{D}^{2}}}}{4}$ | 0.1249 |
Смачиваемый периметр P, м | nπD | 55.292 |
Эквивалентный диаметр для прохода солевого расплава ${{D}_{{sm}}}$, м | 4Fsm /P | 0.009 |
При выбранной компоновке труб скорость движения солевого расплава NaF–BeF2 в межтрубном пространстве составила wsm = ${{{{G}_{{sm}}}} \mathord{\left/ {\vphantom {{{{G}_{{sm}}}} {\left( {{{\rho }_{{sm}}}{{F}_{{sm}}}} \right)}}} \right. \kern-0em} {\left( {{{\rho }_{{sm}}}{{F}_{{sm}}}} \right)}} = $ 0.12 м/с, соответственно число Рейнольдса Resm = 228, что позволяет судить о том, что режим течения жидкости ‒ ламинарный. Коэффициент теплоотдачи солевого расплава можно оценить следующим образом: ${{\alpha }_{{sm}}} = {{{\text{N}}{{{\text{u}}}_{{sm}}}{{\lambda }_{{sm}}}} \mathord{\left/ {\vphantom {{{\text{N}}{{{\text{u}}}_{{sm}}}{{\lambda }_{{sm}}}} {{{D}_{{sm}}}}}} \right. \kern-0em} {{{D}_{{sm}}}}}$ = 407 Вт/(м2 · К), где число Нуссельта, соответствующее ламинарному режиму течения, составляет Nusm ≈ 3.66 [8].
Теплофизические свойства солевого расплава, необходимые для расчета скорости и коэффициента теплоотдачи, вычисляются по зависимостям, представленным в табл. 1, и определяющей температуре ${{\bar {t}}_{{sm}}} = \left( {t_{{sm}}^{{in}} + t_{{sm}}^{{out}}} \right){\text{/}}2$.
Расчет безразмерного коэффициента теплоотдачи к воздуху ${\text{N}}{{{\text{u}}}_{{air}}}$ следует проводить по формуле Петухова ‒ Кириллова:
(2)
${\text{N}}{{{\text{u}}}_{{air}}} = \frac{{\frac{\xi }{8}{{{\operatorname{Re} }}_{{air}}}{{{\Pr }}_{{air}}}}}{{1 + \frac{{900}}{{{{{\operatorname{Re} }}_{{air}}}}} + 12.7\sqrt {\frac{\xi }{8}} \left( {\Pr _{{air}}^{{2/3}} - 1} \right)}},$Для заданных параметров коэффициент теплоотдачи от стенки трубы к воздуху получен с использованием (2) и составил ${{\alpha }_{{air}}}$ = 250 Вт/(м2 · К).
Необходимая площадь поверхности теплообмена может быть определена по соотношению
где $\Delta \bar {t} = \frac{{\left( {t_{{sm}}^{{out}} - {{t}_{{2i}}}} \right) - \left( {t_{{sm}}^{{in}} - {{t}_{3}}} \right)}}{{\ln \frac{{t_{{sm}}^{{out}} - {{t}_{{2i}}}}}{{t_{{sm}}^{{in}} - t_{3}^{{}}}}}}$ ‒ среднелогарифмический температурный напор в ТА, °С; $k = \frac{1}{{\frac{1}{{{{\alpha }_{{sm}}}}} + \frac{\delta }{{{{\lambda }_{w}}}} + \frac{1}{{{{\alpha }_{{air}}}}}}}$ ‒ коэффициент теплопередачи от расплава соли к воздуху, Вт/(м2 · К); ${{\lambda }_{w}}$ – теплопроводность стенки трубы, Вт/(м ⋅ К).При среднелогарифмическом температурном напоре в ТА равном 140°С и коэффициенте теплопередачи 153 Вт/(м2 ⋅ К) получены следующие значения параметров:
Необходимая площадь поверхности теплообмена F, м2…....................................….596 |
Общая длина труб выбранного типоразмера D × δ, м………........................5928.5 |
Высота трубного пучка при установке шести таких теплообменных аппаратов, м……………......................................1.8 |
Масса трубного пучка каждого аппарата при известной плотности материала труб (${{\rho }_{w}}$ = 7950 кг/м3), т…................................2.1 |
Следует также предположить, что с учетом корпуса и арматуры масса аппарата увеличится на 20‒30%. Более точные оценки можно сделать только по результатам конструкторской разработки.
ТУРБИННЫЙ КОНТУР АЭСММ НА БАЗЕ ГТУ С ДВУХСТУПЕНЧАТЫМ СЖАТИЕМ В КОМПРЕССОРЕ И РЕГЕНЕРАЦИЕЙ
Применение многоступенчатого сжатия в компрессоре дает возможность снизить затраты мощности на привод компрессора, а использование регенеративного теплообменника для подогрева воздуха перед активной зоной позволяет существенно увеличить КПД турбинного контура по сравнению с одноступенчатой ГТУ. Однако при этом в контуре появляется дополнительное оборудование: мощный регенератор и промежуточный межступенчатый охладитель. Схема такого контура и конфигурация термодинамического цикла приведены на рис. 3.
Рис. 3.
Схема (а) и T, s-диаграмма термодинамического цикла (б) турбинного контура АЭСММ-ГТУ с двухступенчатым сжатием и регенерацией. I – реактор; II – активная зона; III – ТА “расплав соли – воздух“; IV – главный циркуляционный насос; V – компрессор (I ступень); VI – межступенчатый охладитель; VI – компрессор (II ступень); VIII – регенеративный подогреватель; IX – газовая турбина; X – электрогенератор; QRC – тепловая мощность ТА “расплав соли – воздух“; QR – тепловая мощность регенеративного теплообменника
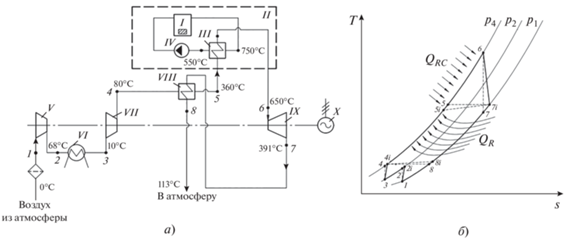
Для расчета параметров рабочих веществ в характерных точках тепловой схемы давление потока воздуха на входе в компрессор и внутренние КПД газовой турбины и ступеней компрессора $\left( {\eta _{{0i}}^{{comp}} = \eta _{{0i}}^{I} = \eta _{{0i}}^{{II}}} \right)$ приняты такими же, как в одноступенчатой ГТУ.
Температуру воздуха перед входом в активную зону (т. 5i на рис. 3) задавали равной 360°C (не ниже температуры затвердевания солевого расплава). Степень регенерации цикла ГТУ вычисляли по формуле
Температура и энтальпия уходящего в окружающую среду воздуха (т. 8i на рис. 3) могут быть определены из теплового баланса регенеративного подогревателя:
Результаты расчета такого цикла ГТУ приведены в табл. 3.
Таблица 3.
Результаты расчета цикла ГТУ с двухступенчатым сжатием и регенерацией (степень регенерации σ = 0.897)
Точка цикла | Давление p, МПа | Температура t, °C | Плотность ρ, кг/м3 | Энтропия s, кДж/(кг · К) | Энтальпия h, кДж/кг |
---|---|---|---|---|---|
1 | 0.1 | 0 | 1.2762 | 3.7962 | 399.29 |
2 | 0.2 | 59.9 | 2.0924 | 3.7962 | 459.39 |
2i | 0.2 | 67.9 | 2.0431 | 3.8202 | 467.47 |
3 | 0.2 | 10.0 | 2.4630 | 3.6326 | 409.09 |
4 | 0.4 | 72.1 | 4.0364 | 3.6326 | 471.37 |
4i | 0.4 | 80.5 | 3.9402 | 3.6569 | 479.86 |
5i | 0.4 | 360.0 | 2.1977 | 4.2568 | 768.38 |
6 | 0.4 | 650.0 | 1.5075 | 4.6684 | 1085.5 |
7 | 0.1 | 368.0 | 0.5431 | 4.6684 | 776.91 |
7i | 0.1 | 391.3 | 0.5242 | 4.7062 | 801.60 |
8i | 0.1 | 112.9 | 0.9024 | 4.1448 | 513.08 |
Характеристики ГТУ с двухступенчатым сжатием и регенерацией следующие:
действительная удельная работа компрессора ${{l}_{{comp}}} = \left( {{{h}_{2}} - {{h}_{1}}} \right){\text{/}}\eta _{{0i}}^{I} + \left( {{{h}_{4}} - {{h}_{3}}} \right){\text{/}}\eta _{{0i}}^{{II}}$ = 68.18 +70.77 = = 138.95 кДж/кг;
действительная удельная работа турбины ${{l}_{{turb}}} = \left( {{{h}_{6}} - {{h}_{7}}} \right)\eta _{{0i}}^{{turb}}$ = 283.9 кДж/кг;
удельные затраты тепла на нагрев рабочего тела в ТА ${{q}_{{RC}}} = {{h}_{6}} - {{h}_{{5i}}}$ = 317.12 кДж/кг;
внутренний КПД цикла $\eta _{i}^{{{\text{GTU}}}} = $ $ = \left( {{{l}_{{turb}}} - {{l}_{{comp}}}} \right){\text{/}}{{q}_{{RC}}}$ = 0.457.
При оставшихся неизменными тепловой мощности теплообменника (1) и расходе воздуха электрическая мощность АЭСММ-ГТУ с двухступенчатым сжатием и регенерацией увеличилась и составила 5.8 МВт. Тепловая мощность регенеративного подогревателя – 11.6 МВт. При использовании такой схемы значительно вырос КПД цикла турбинного контура (на 12.2%).
ВОЗДУХОПОДОГРЕВАТЕЛЬ АЭСММ-ГТУ С ДВУХСТУПЕНЧАТЫМ СЖАТИЕМ И РЕГЕНЕРАЦИЕЙ
Эффективность ГТУ существенно зависит от степени регенерации цикла и гидравлических потерь в основных теплообменных аппаратах. Среди главных требований к регенеративному подогревателю22 ГТУ – обеспечение хорошей теплопередачи при небольшом гидравлическом сопротивлении, компактность и низкая стоимость. Однако обеспечить одновременно высокую степень регенерации и малые габариты – довольно сложная задача. Поэтому выбор конструкции регенеративного подогревателя должен определяться, в первую очередь, возможностями увеличения в нем скорости потоков воздуха, а значит, и коэффициентов теплоотдачи при минимально возможном гидравлическом сопротивлении тракта.
В стационарных ГТУ чаще всего применяют трубчатые или пластинчатые регенераторы. Масса, габариты и стоимость пластинчатых регенераторов значительно меньше, чем у трубчатых, что вызывает повышенный интерес к разработке их конструкций с обеспечением герметичности между воздушной и газовой полостями. Примером регенератора такой конструкции является теплообменник из профильных штампованных стальных листов с овалообразными выступами. Размеры и форма выступов на листах принимаются такими, чтобы при наложении листов один на другой образовывались каналы для прохода воздуха и продуктов сгорания.
Для рассматриваемой схемы, в которой греющей и нагреваемой средами аппарата является воздух, т.е. снимается проблема загрязнения поверхности коксующимися компонентами выхлопных газов, аппарат пластинчатого типа становится наиболее оптимальным и обоснованным вариантом. Пластинчатый регенератор компонуется из профильных листов с выступами для формирования двуугольных каналов. В основной части теплообменника теплоносители движутся по противоточной схеме (рис. 4).
Рис. 4.
Двуугольные каналы между профильными листами проточной части пластинчатого теплообменника (а) и вид профильной поверхности (б). Каналы для прохода воздуха: 1 – нагреваемого; 2 – греющего; ${{d}_{0}}$ ‒ внутренний размер двуугольного канала; ${{f}_{0}}$ ‒ площадь проходного сечения одного канала; Δ – расстояние между овалообразными выступами; b1 – поперечный шаг между овалообразными выступами; b2 – продольный шаг между овалообразными выступами
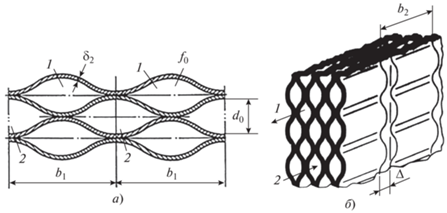
Методика расчета необходимой поверхности пластинчатых теплообменников при заданной тепловой мощности описана в [9]. Профильная поверхность теплообмена – двуугольная (овалообразные выступы). Геометрические характеристики каналов такого типа приведены в табл. 4.
Таблица 4.
Геометрические характеристики двуугольных каналов с овалообразными выступами (см. рис. 5)
b1, мм | b2, мм | d0, мм | b1/d0 | Δ, мм | δ2, мм | de, мм | ψ |
---|---|---|---|---|---|---|---|
15.0 | 60.0 | 8.00 | 1.875 | 52.0 | 1 | 7.30 | 1.075 |
7.5 | 15.0 | 3.06 | 2.451 | 12.9 | 1 | 2.75 | 1.075 |
5.0 | 10.0 | 1.78 | 2.809 | 8.6 | 1 | 1.42 | 1.075 |
Для расчета был выбран типоразмер пластины с максимальным сечением одного канала (b1/d0 = = 1.875). Значения рассчитанных параметров теплоносителей на входе в регенератор и выходе из него представлены в табл. 3. По средним температурам и давлениям (без учета потерь по тракту) можно определить теплофизические свойства нагреваемого и греющего воздуха [7]. Материал пластин – сталь 1Х18Н9Т [λp = 14.4 + 0.016${{\bar {t}}_{p}}$, где ${{\bar {t}}_{p}}$ − средняя температура стенки (пластины)].
Если обеспечить среднюю скорость нагреваемого воздуха ${{w}_{2}}$ = 3 м/с, то скорость греющего воздуха ${{w}_{1}}$ можно определить из условия равенства в элементе33 количества каналов и расходов через них (G1 = G2) нагреваемого (индекс 2) и греющего (индекс 1) потоков:
(4)
${{w}_{1}} = \left( {\frac{{{{\rho }_{2}}}}{{{{\rho }_{1}}}}} \right)\left( {\frac{{{{f}_{2}}}}{{{{f}_{1}}}}} \right)\left( {\frac{{{{G}_{1}}}}{{{{G}_{2}}}}} \right){{w}_{2}}.$Число Нуссельта для обоих потоков воздуха может быть рассчитано по соотношению
где ${{\operatorname{Re} }_{{1(2)}}} = \frac{{{{w}_{{1(2)}}}\,\,{{d}_{{e1(2)}}}}}{{{{\nu }_{{1(2)}}}}}$ ‒ число Рейнольдса; ${{d}_{{e1(2)}}}$ ‒ эквивалентный диаметр каналов (см. табл. 4); ψ – коэффициент, учитывающий кривизну каждого канала (см. табл. 4); ${{\nu }_{{1(2)}}}$ ‒ кинематический коэффициент вязкости греющего и нагреваемого воздуха.Для принятых параметров регенератора коэффициенты теплоотдачи и от греющего, и к нагреваемому воздуху составили ${{\alpha }_{{1(2)}}} = \frac{{{\text{N}}{{{\text{u}}}_{{1(2)}}}{{{{\lambda }}}_{{1(2)}}}}}{{{{d}_{{e1(2)}}}}}$ = = 71 Вт/(м2 · К)44.
Площадь поверхности воздухоподогревателя FR, как и площадь теплообменника активной зоны, вычисляется по уравнению теплопередачи (3) и для выбранной конструкции аппарата составляет 10 378 м2 [при полученных значениях коэффициента теплопередачи 35.2 Вт/(м2 · К) и среднелогарифмического температурного напора 31.8°С].
Количество каналов, необходимых для прохода воздуха в аппарате, определяется отношением площади проходного сечения всех каналов по каждому из потоков ${{f}_{{1(2)}}} = \frac{{{{G}_{{1(2)}}}}}{{{{\rho }_{{1(2)}}}\,{{w}_{{1(2)}}}}}$ к площади проходного сечения одного канала [9]:
Таким образом, необходимое количество каналов составит Zin = 80 600.
Габаритные размеры одного модуля воздухоподогревателя зависят от технологических возможностей штамповочного пресса при изготовлении одного листа и соответствующего числа каналов. Необходимая общая площадь поверхности теплообмена будет обеспечиваться количеством таких модулей и их компоновкой для раздачи теплоносителя. При наличии технологической возможности производства базового элемента размерами 1.5 × 2.0 м можно спроектировать модуль поперечным сечением 1.5 × 1.5 м и высотой 2 м. Число поперечных рядов будет ${{n}_{ \bot }} = 1500{\text{/}}({{d}_{{\text{0}}}} + {{\delta }_{2}})$ = = 167, а продольных ‒ ${{n}_{\coprod }} = 1500{\text{/}}{{b}_{1}}$ = 100. Суммарное количество каналов в одном модуле составит 16 700. Следовательно, для обеспечения параллельной подачи воздуха понадобится $Z = {{Z}_{{in}}}{\text{/}}\left( {{{n}_{ \bot }} \times {{n}_{\coprod }}} \right)$ = 5 модулей регенератора.
Площадь поверхности теплообмена одного модуля с внутренними размерами высота h × ширина B × длина L = 1.5 × 1.5 × 2.0 рассчитывается по соотношению [9]
(6)
${{F}_{{1m}}} = 2{{b}_{1}}\psi \left( {1 + \frac{{\Delta \left( {1 - \psi } \right)}}{{\psi {{b}_{2}}}}} \right)L\frac{h}{{{{b}_{1}}}}\frac{B}{{\left( {{{d}_{0}} + 2{{\delta }_{2}}} \right)}}$Общее количество модулей зависит от необходимой площади поверхности теплообмена ${{n}_{m}} = {{F}_{R}}{\text{/}}{{F}_{{1m}}}$ ≈ 12 шт. При округлении до 15 шт. обеспечиваются дополнительная площадь теплообмена и компоновка, кратная 5, т.е. подача воздуха параллельно идет в один ряд из пяти модулей и последовательно в три ряда по пять модулей в каждом.
Масса одного модуля без корпуса и арматуры составит ${{M}_{{1m}}} = {{\rho }_{w}}{{F}_{{1m}}}{{\delta }_{2}}$ = 7.3 т, а всего регенератора ‒ более 108 т.
ТУРБИННЫЙ КОНТУР АЭСММ НА БАЗЕ РЕГЕНЕРАТИВНОЙ ПТУ НА ОКТАФТОРПРОПАНЕ
Возможность использования в энергетических установках вместо водяного и газовых рабочих тел экологически безопасных и термодинамически эффективных фторуглеродов (СF4, C3F8, C4F8, C4F10, …) впервые была показана в [10]. В течение последних 20 лет опубликовано довольно большое количество работ, отражающих не только результаты исследований теплофизических свойств фторуглеродов [11, 12], но и результаты анализа эффективности энергетических установок, в которых применяются эти вещества в качестве рабочих тел [11, 13‒16], в том числе во II контуре АЭС.
В настоящей работе рассматривается возможность использования в качестве рабочего тела турбинного контура АЭСММ октафторпропана (C3F8) –наиболее термически устойчивого из ряда фторуглеродов. Его термостойкость позволяет поддерживать высокую температуру на входе в турбину. Проблемы предотвращения повышения рабочей температуры вещества сверх допустимых значений, обеспечения гибкого регулирования переменной нагрузки могут быть успешно решены применением новых динамических аккумулирующих систем [17].
Тепловая схема II контура АЭСММ с ПТУ на октафторпропане и конфигурация реализуемого термодинамического цикла изображены на рис. 5.
Рис. 5.
Тепловая схема (а) и T, s-диаграмма термодинамического цикла (б) установки АЭСММ-ПТУ на октафторпропане с регенерацией. I – реактор; II – активная зона; III – главный циркуляционный насос; IV – теплообменный аппарат “расплав соли – C3F8”; V − фторуглеродная турбина; VI − электрогенератор; VII − регенеративный подогреватель; VIII − насос; IX − конденсатор; QRC – подводимое к октафторпропану тепло от расплава соли; QR – тепло, передаваемое в регенеративном теплообменнике
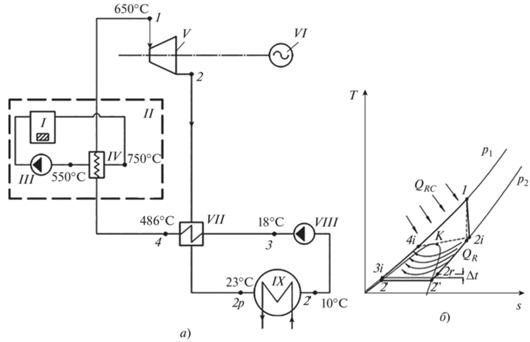
Расчет параметров цикла производился по программе [7] при заданных значениях давления октафторпропана перед турбиной p1 = 13 МПа и температуры в конденсаторе = 10°C (${{t}_{s}}$ ‒ температура насыщения), а также при значениях внутренних относительных КПД турбины
$\eta _{{0i}}^{{turb}}$ = 0.92 и насоса $\eta _{{0i}}^{{pump}}$ = 0.88. Температура октафторпропана перед турбиной принималась равной температуре
воздуха в рассмотренных ранее установках АЭСММ-ГТУ. Температура рабочего тела перед
активной зоной определялась по уравнению теплового баланса регенеративного теплообменника
с учетом принятого значения температурного напора на выходе из него $\Delta t = {{t}_{{2r}}} - {{t}_{{3i}}}$ = 5°С.
Результаты расчета параметров октафторпропана в характерных точках цикла приведены в табл. 5.
Таблица 5.
Результаты расчета параметров цикла турбинного контура на октафторпропане
Точка цикла | Давление p, МПа | Температура t, °C | Плотность ρ, кг/м3 | Энтропия s, кДж/(кг · К) | Энтальпия h, кДж/кг |
---|---|---|---|---|---|
1 | 13.0 | 650.0 | 282.9 | 2.4129 | 978.77 |
2 | 0.6 | 540.7 | 15.7 | 2.4129 | 852.88 |
2i | 0.6 | 549.1 | 15.5 | 2.4252 | 862.95 |
2'' | 0.6 | 10.0 | 54.6 | 1.3381 | 295.65 |
2' | 0.6 | 10.0 | 1405.6 | 1.0388 | 210.90 |
3 | 13.0 | 16.8 | 1481.3 | 1.0388 | 219.49 |
3i | 13.0 | 18.0 | 1477.3 | 1.0428 | 220.66 |
4i | 13.0 | 486.0 | 121.6 | 2.1739 | 776.61 |
2r | 0.6 | 23.0 | 50.3 | 1.3773 | 307.00 |
При полученных значениях параметров цикла были рассчитаны следующие его характеристики:
Удельная работа, кДж/кг: |
насоса ${{l}_{{pump}}} = \left( {{{h}_{3}} - {{h}_{{2'}}}} \right){\text{/}}\eta _{{0i}}^{{pump}}$…………….9.76 |
турбины ${{l}_{{turb}}} = \left( {{{h}_{1}} - {{h}_{2}}} \right)\eta _{{0i}}^{{turb}}$………….…115.82 |
Удельные затраты тепла ${{q}_{{RC}}} = {{h}_{1}} - {{h}_{{4i}}}$, кДж/кг …............….202.16 |
Внутренний КПД цикла $\eta _{i}^{{FTU}} = \left( {{{l}_{{turb}}} - {{l}_{{pump}}}} \right){\text{/}}{{q}_{{RC}}}$5…......................0.525 |
55Расход октафторпропана можно определить по уравнению теплового баланса для аппарата “расплав соли – C3F8”, тепловая мощность которого равна рассчитанной ранее по формуле (1) для аппарата АЭСММ-ГТУ при использовании NaF–BeF2.
Таким образом, при расходе октафторпропана в контуре ${{G}_{f}}$66 = 63.2 кг/с электрическая мощность ПТУ АЭСММ составит 6.7 МВт при тепловой мощности регенеративного теплообменника 35.1 МВт.
ТЕПЛООБМЕННЫЙ АППАРАТ “РАСПЛАВ СОЛИ – C3F8” АКТИВНОЙ ЗОНЫ АЭСММ-ПТУ
Конфигурацию трубных пучков теплообменного аппарата “расплав соли – C3F8” следует оставить такой же, как и для ТА “расплав соли – воздух”. Это целесообразно сделать для последующего сравнения их массогабаритных характеристик. Ожидается, что количество труб в поперечном сечении аппарата существенно уменьшится из-за использования рабочего тела, имеющего более высокую плотность. При этом методика расчета параметров процессов теплообмена аппарата “расплав соли – C3F8” останется такой же.
При заданной средней скорости движения потока C3F8 в трубах ${{w}_{f}}$ = 3 м/с рассчитанное по (2) значение коэффициента теплоотдачи от стенки трубы к октафторпропану, находящемуся в этом теплообменнике в состоянии перегретого пара, составило 1698 Вт/(м2 · К). Теплофизические и переносные свойства октафторпропана определялись при давлении p1 и средней температуре $\bar {t} = \left( {{{t}_{1}} + {{t}_{{4i}}}} \right){\text{/}}2$ (см. табл. 5) с использованием [7].
Расчет требуемого числа труб для раздачи C3F8 проводили (по аналогии с аппаратом, в котором в качестве рабочего тела используется воздух) с помощью отношения площади общего сечения для прохода октафторпропана к площади внутреннего сечения одной трубы, оно составило 126 шт. (принято 130 шт. для комплектации модуля $n = {{n}_{1}} \times {{n}_{2}}$ = 13 × 10 шт.).
Характерные геометрические размеры аппарата “расплав соли – C3F8” при идентичных рассмотренным ранее зазорах и шагах труб следующие:
Длина аппарата ${{L}_{1}}$, м ………………………......0.462 |
Ширина аппарата ${{L}_{2}}$ м ………………..….....0.3044 |
Площадь межтрубного зазора |
для прохода солевого расплава ${{F}_{{sm}}}$, м2.....0.0361 |
Смачиваемый периметр P, м……………..…..13.07 |
Эквивалентный диаметр для прохода |
расплава соли ${{D}_{{sm}}} = {{4{{F}_{{sm}}}} \mathord{\left/ {\vphantom {{4{{F}_{{sm}}}} P}} \right. \kern-0em} P}$……..……………0.011 |
При выбранной компоновке труб скорость движения солевого расплава в межтрубном пространстве составит ${{w}_{{sm}}} = {{{{G}_{{sm}}}} \mathord{\left/ {\vphantom {{{{G}_{{sm}}}} {\left( {{{\rho }_{{sm}}}{{F}_{{sm}}}} \right)}}} \right. \kern-0em} {\left( {{{\rho }_{{sm}}}{{F}_{{sm}}}} \right)}}$ = 0.42 м/с, число Рейнольдса Resm = 963, что свидетельствует о том, что в межтрубном пространстве ламинарный режим течения. Следовательно, коэффициент теплоотдачи солевого расплава, определенный по соотношению Nusm = 3.66, составит ${{\alpha }_{{sm}}}$ = = 333 Вт/(м2 · К).
При среднелогарифмическом температурном напоре в аппарате “расплав соли – C3F8” $\Delta \bar {t}$ = = 80.7°С получены следующие значения параметров:
Необходимая площадь поверхности теплообмена, м2…………..............................….588 |
Общая длина труб выбранного типоразмера D × δ = 32 × 2 мм, м ……......5845.4 |
Высота трубного пучка при установке 25 таких теплообменных |
аппаратов, м…………................................……..1.8 |
Масса труб, т……….........................................12.7 |
Когда коэффициент теплоотдачи со стороны солевого расплава ${{\alpha }_{{sm}}}$ в несколько раз меньше этого показателя со стороны октафторпропана ${{\alpha }_{f}}$, требуется интенсификация теплообмена. Наиболее удачным видится вариант развития наружной поверхности труб путем оребрения, например, посредством ее обработки по технологии деформирующего резания. Применение данной технологии позволит достичь значений коэффициента теплоотдачи со стороны солевого расплава примерно 1400 Вт/(м2 · К), а коэффициента теплопередачи ‒ около 700 Вт/(м2 · К). При этом необходимое количество теплообменных аппаратов с высотой трубного пучка 1.8 м уменьшится до 10 шт., а масса – до 5 т.
РЕГЕНЕРАТИВНЫЙ ПОДОГРЕВАТЕЛЬ ПТУ НА ОКТАФТОРПРОПАНЕ
В качестве базового принят тот же типоразмер элементов регенератора, что и для аппарата в схеме АЭСММ-ГТУ с двухступенчатым сжатием и регенерацией (по данным табл. 4 соотношение b1/d0 = 1.875).
Значения давлений и температур октафторпропана в регенераторе получены при расчете тепловой схемы установки и приведены в табл. 5. Теплофизические и переносные свойства греющей (индекс 1) и нагреваемой (индекс 2) сред определены с использованием программы [7] при известных давлениях потоков (без учета потерь) и средних температурах ${{\bar {t}}_{1}} = \left( {{{t}_{{2i}}} + {{t}_{{2r}}}} \right){\text{/}}2$ и ${{\bar {t}}_{2}} = \left( {{{t}_{{4i}}} + {{t}_{{3i}}}} \right){\text{/}}2$.
При заданной средней скорости нагреваемого потока ${{w}_{2}}$ = 3 м/с по соотношению (4) рассчитана скорость греющего потока (при f1 = f2, G1 = G2) и по изложенной ранее методике расчета определены тепловые и геометрические характеристики регенеративного аппарата ПТУ.
При вычисленных по (5) значениях коэффициентов теплоотдачи греющей ${{\alpha }_{1}}$ = 5746 Вт/(м2 · К) и нагреваемой ${{\alpha }_{2}}$ = 3700 Вт/(м2 · К) сред, коэффициенте теплопередачи ${{k}_{R}}$ = 2000 Вт/(м2 · К) и среднелогарифмическом температурном напоре $\Delta {{\bar {t}}_{R}}$ = 23°C необходимая площадь поверхности теплообмена регенератора составит ${{F}_{R}}$ = 766.834 м2.
При проектировании модуля с поперечным сечением 0.180 × 0.450 м число поперечных рядов составит ${{n}_{ \bot }} = 180{\text{/}}\left( {{{d}_{0}} + {{\delta }_{2}}} \right)$ = 20, а продольных – ${{n}_{\coprod }} = 450{\text{/}}{{b}_{1}}$ = 30. Необходимое количество каналов для движения греющего и нагреваемого потоков будет равно приблизительно 600, следовательно, проектируемые скорости и расходы будут обеспечиваться при последовательном соединении модулей.
Площадь поверхности теплообмена одного модуля с внутренними габаритами h × B × L = = 0.180 × 0.450 × 2.0 м, рассчитанная по соотношению (6), составит 32.74 м2, что позволит получить необходимое количество модулей для обеспечения теплообменной поверхности ${{n}_{m}} = {{F}_{R}}{\text{/}}{{F}_{{1m}}}$ ≈ ≈ 24 шт.
Масса одного модуля без корпуса и арматуры составит 260 кг, всего регенератора – 6.25 т.
ВЫВОДЫ
1. Наибольшая термодинамическая эффективность преобразования тепла, выделяющегося в активной зоне АЭСММ, достигается в паротурбинном контуре на октафторпропане (52%). Оценочные расчеты показывают, что при использовании для этой цели турбинного контура на базе открытого цикла ГТУ внутренний КПД цикла при температуре атмосферного воздуха 0°С будет равен 33%, на базе ГТУ с двухступенчатым сжатием и регенерацией (степень регенерации σ = = 0.897) – 45%.
2. Массогабаритные характеристики теплообменных аппаратов в активной зоне при переходе с воздуха в качестве рабочего тела на октафторпропан могут быть значительно уменьшены. Например, массу всех аппаратов контура (без корпуса и арматуры) можно уменьшить с 19 т (для ГТУ на воздухе) до 11 т (ПТУ на октафторпропане).
3. Применение регенерации в циклах для утилизации тепла активной зоны АЭСММ позволяет существенно повысить среднюю интегральную температуру подвода тепла и тем самым обеспечить высокую термодинамическую эффективность его преобразования. В схеме с регенеративной ПТУ на октафторпропане выходная мощность увеличивается почти на 60% по сравнению с мощностью одноступенчатой ГТУ.
4. Для теплообменных аппаратов, в которых греющей и нагреваемой средой является чистое рабочее вещество (воздух или октафторпропан), “снимается” проблема загрязнения поверхности коксующимися компонентами выхлопных газов, актуальная для традиционной ГТУ. Следовательно, пластинчатый тип их конструкции становится наиболее оптимальным и обоснованным вариантом, что дает возможность уменьшить металлоемкость, габариты и стоимость оборудования установки. Полученные результаты свидетельствуют о возможности снижения массы регенеративных аппаратов на октафторпропане в сравнении воздушными аналогами до 15 раз.
5. Результаты расчета основных теплотехнических характеристик турбинного контура АЭСММ-ПТУ на октафторпропане подтверждают возможность достижения не только высокой энергетической эффективности, экологической и технологической безопасности (вещество инертно, не подвергается радиолизу, находится в герметичном контуре), но и значительной степени компактности его оборудования.
Список литературы
Атомные станции малой мощности: новое направление развития энергетики / под ред. А.А. Саркисова. Ин-т проблем безопасного развития атомной энергетики РАН. М.: Наука, 2011.
Атомные станции малой мощности – главный путь снижения рисков и их последствий в ядерной энергетике: монография / П.Н. Алексеев, Ю.Н. Удянский, Т.Д. Щепетина, П.А. Фомиченко. М.: КДУ; Университетская книга, 2020. https://doi.org/10.31453/kdu.ru.91304.0123
Ядерная энергетика. Жидкосолевые ЯЭУ. Проблемы и перспективы. Экспертные оценки. М.: Энергоатомиздат, 1989.
Ядерная энергетика. Проблемы и перспективы. Экспертные оценки. М.: Энергоатомиздат, 1989.
Твэлы на основе сферических топливных частиц с защитным покрытием для реакторов повышенной безопасности / А.С. Черников, Л.Н. Пермяков, И.И. Федик, С.С. Гаврилин, С.Д. Курбаков // Атомная энергия. 1999. Т. 87. Вып. 6. С. 451‒462.
Микротопливный реактор с жидкосолевым теплоносителем МАРС для малой энергетики / П.Н. Алексеев, И.А. Белов, Н.Н. Пономарев-Степной, Н.Е. Кухаркин, С.А. Субботин, Ю.Н. Удянский, А.В. Чибиняев, Т.Д. Щепетина, П.А. Фомиченко // Атомная энергия. 2002. Т. 93. Вып. 1. С. 3‒13.
База данных о теплофизических и переносных свойствах веществ NIST REFPROP DATABASE Version 8.0.
Теоретические основы теплотехники. Теплотехнический эксперимент: Справ. серия. В 4 кн. Кн. 2: Теплоэнергетика и теплотехника / под общ. ред. А.В. Клименко, В.М. Зорина. 4-е изд., стер. М.: Издательский дом МЭИ, 2007.
Эффективность использования энергоресурсов при обеспечении транспорта газа / Б.А. Григорьев, В.В. Ремизов, А.Д. Седых, А.П. Солодов. М.: Изд-во МЭИ, 1999.
Гохштейн Д.П., Смирнов Г.Ф., Киров В.С. Некоторые особенности парогазовых схем с неводяными парами // Теплоэнергетика. 1966. № 1. С. 20‒24.
Сухих А.А. Исследование термодинамических свойств и теплотехнических характеристик фторорганических рабочих веществ: дис. … докт. техн. наук. М.: МЭИ, 2012.
Кузнецов К.И. Экспериментально-расчетное исследование термодинамических свойств октафторпропана и декафторбутана: дис. … канд. техн. наук. М.: МЭИ, 2009.
Сухих А.А., Милютин В.А., Антаненкова И.С. Термодинамическая эффективность фторуглеродов как рабочих тел в теплосиловых циклах АЭС // Электрические станции. 2010. № 10. С. 2–8.
Потенциал фторуглеродных газов как рабочих тел для АЭС / М.С. Моркин, В.В. Лемехов, А.А. Сухих, И.М. Мазурин // Надежность и безопасность энергетики. 2015. Т. 4. № 31. С. 46‒49.
Обзор результатов и методов комплексного исследования рабочих веществ фторорганического состава энергетических установок / М.С. Моркин, В.В. Лемехов, Ю.С. Черепнин, И.М. Мазурин, А.А. Сухих // Надежность и безопасность энергетики. 2017. Т. 10. № 2. С. 135–142.
Системный кризис при выборе рабочих тел энергетических установок / И.М. Мазурин, А.Ф. Королев, Р.Л. Герасимов, Д.И. Мазурин // Пространство и Время: Альманах. 2013. Т. 2. Вып. 1. [Электрон. науч. изд.]
Пат. 2680380 РФ, МПК G21D 5/00. Способ повышения мощности и безопасности энергоблока АЭС с реактором типа ВВЭР на основе теплового аккумулирования / Р.З. Аминов, В.Е. Юрин, М.А. Муртазов // Б.И. 2019. № 5.
Дополнительные материалы отсутствуют.
Инструменты
Теплоэнергетика