Теплоэнергетика, 2022, № 12, стр. 92-99
Технология получения детонационных покрытий на деталях энергетического оборудования, изготовленных из стали марки 12Х1МФ
М. К. Даутбеков a, c, *, Б. К. Рахадилов c, Л. Г. Журерова b, Д. Н. Какимжанов a, c, С. Л. Елистратов d, Т. А. Сегеда a
a Восточно-Казахстанский технический университет им. Д. Серикбаева
070010 Восточно-Казахстанская обл., г. Усть-Каменогорск, ул. Д. Серикбаева, д. 19, Республика Казахстан
b Восточно-Казахстанский университет им. С. Аманжолова
070020 Восточно-Казахстанская обл., г. Усть-Каменогорск, ул. 30-й Гвардейской Дивизии, д. 34, Республика Казахстан
c Товарищество с ограниченной ответственностью PLASMASCIENCE
070010 Восточно-Казахстанская обл., г. Усть-Каменогорск, ул. Д. Серикбаева, д. 37, Республика Казахстан
d Новосибирский государственный технический университет
630073 г. Новосибирск, просп. К. Маркса, д. 20, Россия
* E-mail: merkhatd@gmail.com
Поступила в редакцию 17.02.2022
После доработки 01.06.2022
Принята к публикации 06.06.2022
- EDN: SUESEX
- DOI: 10.56304/S0040363622120013
Аннотация
Представлены результаты экспериментальных исследований покрытий Cr3C2–NiCr, нанесенных способом детонационного напыления на теплоустойчивую сталь 12Х1МФ, в том числе влияния технологических параметров процесса нанесения покрытия Cr3C2–NiCr на его структуру и свойства. При испытаниях была использована детонационная пушка с одним дозатором. Напыление детонационной пушкой – это один из методов термического формирования защитного слоя на поверхности, отличающийся тем, что позволяет получать твердые, износостойкие и плотные микроструктурированные покрытия. В качестве горючего газа служила ацетилено-кислородная смесь, которая наиболее часто применяется при детонационном напылении порошковых материалов. Импульс азота или воздуха используется для продувки ствола после каждой детонации. Этот процесс повторяется много раз в секунду. Высокая кинетическая энергия частиц горячего порошка при ударе о подложку приводит к образованию очень плотного и прочного покрытия. Полученные покрытия имеют неоднородную слоистую структуру с порами и волнообразным расположением структурных составляющих со слоисто-пористой структурой толщиной 60–120 мкм. На границе раздела подложки и покрытия отсутствуют поры и трещины. В качестве основного параметра измерения шероховатости поверхности выбрано среднее арифметическое отклонение профиля Ra. Установлено, что при 64%-ном заполнении объема ствола детонационной пушки взрывчатой смесью поверхность обработанного образца обладает низкой степенью износа. Приведены результаты исследования влияния детонационного напыления на структурно-фазовый состав и трибологические свойства покрытий методом рентгеноструктурного анализа, согласно которым образуются фазы Cr3C2, Cr7C3, Cr3O6, Cr23C6 и CrNi3, определены микротвердость, шероховатость и трибологические свойства полученных покрытий.
В Республике Казахстан более 79% электроэнергии вырабатывается при сжигании угля, причем более половины тепловых электростанций (ТЭС) имеют средний срок эксплуатации свыше 30 лет. Большая часть оборудования выработала свой проектный и нормативный ресурсы, что обусловливает снижение надежности их эксплуатации. Актуальным остается вопрос предотвращения отказов имеющегося оборудования вследствие накопления его внутренних и внешних повреждений. В работе [1] сделано заключение о том, что возможна эксплуатация некоторых элементов оборудования, хотя установленный срок их службы существенно превышен, при условии назначения надлежащего контроля в процессе эксплуатации.
В настоящее время актуальной задачей является повышение надежности и долговечности изделий, эксплуатационные характеристики которых определяются свойствами их рабочих поверхностей. Одним из наиболее перспективных способов улучшения эксплуатационных свойств и увеличения долговечности изделий является нанесение на их поверхности функциональных покрытий с использованием различных технологий напыления [2, 3].
На коррозионные и эрозионные процессы на поверхностях нагрева оборудования (наружной поверхности труб) ТЭС влияют составы топлива и газообразных продуктов горения. Характеристики угля, используемого на тепловых электростанциях, не всегда соответствуют их проектным параметрам. При сжигании непроектного угля интенсивнее разрушается основное оборудование, так как его детали спроектированы и изготовлены из сплавов металлов, характеристики которых специально подбирались под химические параматры топлива конкретного вида. В свою очередь, замена проектного топлива приводит к изменениям условий функционирования котельных агрегатов и технологической схемы ТЭС [4].
Уголь низкого сорта может содержать ванадий, натрий и серу в качестве примесей. В процессе горения сера и натрий вступают в реакцию друг с другом с образованием Na2SО4. Ванадий взаимодействует с кислородом, в результате чего образуются V2O5 и комплекс ванадата (зола). Эти соединения накапливаются на поверхностях нагрева и приводят к их коррозии. Золовые отложения могут разрушить защитный оксидный слой, который образуется на материалах естественным путем, и вызывают деградацию материала вследствие горячей коррозии. Последствия данного процесса – прекращение работы оборудования и необходимость его ремонта. В целях преодоления этих негативных проявлений возможны замена материала, используемого в энергетических установках ТЭС, или формирование на поверхности нагрева нерастворимого покрытия, которое защищает материалы от коррозии.
ПРИМЕНЕНИЕ ПОКРЫТИЯ Cr3C2–NiCr
Покрытие Cr3C2–NiCr обладает стойкостью к окислению и коррозии и потому широко применяется для снижения износа элементов оборудования при воздействии высоких температур (500–900°C) и агрессивных сред [5]. Для нанесения покрытий из порошка Cr3C2–NiCr можно использовать различные методы газотермического напыления, такие как HVOF, Cold Spraying, детонационное напыление, атмосферное плазменное напыление и др. Однако вследствие пористости и недостаточной твердости покрытия возможен преждевременный выход из строя элементов конструкции работающих частей оборудования в условиях интенсивного эрозионно-коррозионого износа и адгезии [6]. Тем не менее покрытия, нанесенные методом детонационного напыления, по сравнению с покрытиями, полученными газотермической обработкой поверхности [7], более эффективно защищают от эрозии и коррозии, а также обладают повышенной жаропрочностью. С помощью детонационного напыления можно получать покрытия при меньшем нагреве подвергаемой обработке детали, что позволяет избежать деформации подложки в процессе напыления, а также исключить неблагоприятные явления, сопутствующие нагреву детали, такие как насыщение поверхности газами [8].
Авторы работы [9] обнаружили, что после нанесения покрытия Cr3C2–NiCr методом детонационного напыления значительно уменьшается интенсивность эрозионно-коррозионных процессов и окисления по сравнению с покрытиями, полученными методом HVOF. Это может быть связано с образованием оксидной пленки Cr2O3. При изучении покрытий Cr3C2–NiCr, полученных методом детонационного напыления [10, 11], определено влияние оксидной пленки Cr2O3 на окислительно-эрозионные свойства котельных сталей. Обнаружено, что образование богатой оксидом хрома накипи способствует лучшему сопротивлению котельной стали процессам окисления и эрозии.
Целью данной работы является исследование влияния технологических параметров детонационного напыления на фазовый состав, твердость и трибологические свойства покрытий на основе Cr3C2–NiCr на поверхностях деталей энергетического оборудования тепловых электрических станций.
МАТЕРИАЛЫ, ОБОРУДОВАНИЕ И МЕТОДЫ ИССЛЕДОВАНИЯ
В настоящей работе приведены результаты исследования покрытий из порошка Cr3C2–NiCr, нанесенных детонационным комплексом CCDS2000 (computer-controlled detonation spraying), включающим в себя систему электромагнитных газовых клапанов, которые контролируют количество взрывчатой смеси, расходуемой на каждый выстрел пушки, расход кислорода, а также управляют продувкой системы [12].
Общий вид детонационной пушки и ее принципиальная схема показаны на рис. 1. Ствол детонационной пушки заполняется газами, расход которых контролируется с помощью встроенного компьютера. После заполнения ствола в него подают определенную порцию взрывчатой смеси таким образом, чтобы образовалась слоистая газовая среда, состоящая из заряда взрывчатого вещества и газа-носителя (азота). При впрыскивании в ствол порошка (с помощью управляемого компьютером питателя) образуется газопорошковая среда. После того как часть порошка впрыснута в ствол, компьютер выдает сигнал на инициирование детонации с помощью электрической искры. Во взрывчатой смеси образуется детонационная волна, которая переходит в ударную волну. Продукты детонации, нагретые до 3500–4500°С, и газа-носителя, нагретого ударной волной до 1000–1500°С, направляются к выходу из канала ствола со сверхзвуковой скоростью. Время взаимодействия газов с распыляемыми частицами составляет 2–5 мс. Диаметр прямого ствола детонационной пушки равен 20 мм. В качестве напыляемого материала использовали композитный порошок фирмы H.C. Starck 584.054 Cr3C2–NiCr с частицами размером 10–45 мкм [12–14].
Рис. 1.
Общий вид детонационного комплекса ССDS2000 (а) и принципиальная схема установки (б). 1 – газораспределительная система; 2 – воспламенительная камера; 3 – ствол; 4 – манипулятор для подложки; 5 – дозатор порошка; 6 – компьютер; 7 – дистанция напыления
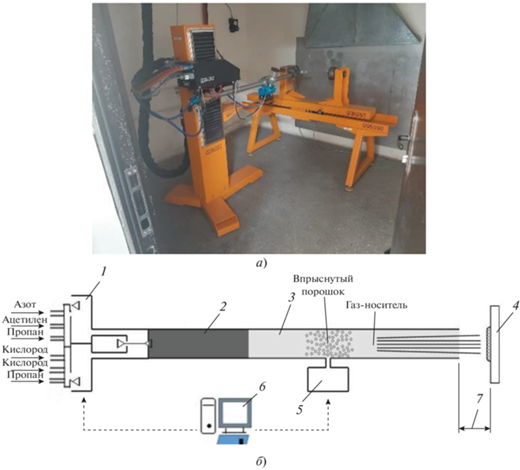
Образцы подложки были изготовлены из теплоустойчивой стали марки 12Х1МФ следующего химического состава, % [15]:
Углерод…………………......…….......................0.10–0.18 |
Кремний…………………….............................0.15–0.35 |
Марганец……………………............................0.30–0.60 |
Никель………………………..................................До 0.3 |
Сера……….........................……………......…….До 0.035 |
Фосфор……………………………........................До 0.035 |
Хром…………………………………........................0.9–1.2 |
Молибден………………………….....................0.50–0.65 |
Ванадий…………………………….....................0.25–0.35 |
Медь…………………………………..........................До 0.2 |
Железо………………………………................................96 |
Такая сталь используется для изготовления деталей, работающих в нагруженном состоянии в течение длительного времени, в том числе и для производства энергетического оборудования тепловых электростанций (поверхности нагрева котлов). Образцы перед нанесением покрытия подвергали пескоструйной обработке.
Для реализации восстановительных условий напыления при неполном сгорании с образованием интерметаллида было выбрано соотношение содержания O2/C2H2 = 1.856. По мере увеличения объема взрывчатой смеси (от 51 до 64% объема ствола) повышается температура нагрева частиц во время их движения внутри ствола [14]. При дистанции напыления 150 мм и количестве выстрелов 20 объем заполнения ствола составил: 51% для образца № 1, 58% для образца № 2, 64% для образца № 3.
Дифракционные исследования образцов выполняли с использованием традиционных методов рентгеновской дифракции – определения угловых положений, интенсивностей и профилей дифракционных отражений методом рентгеноструктурного анализа на дифрактометре X’PertPRO. Съемку дифрактограмм проводили с использованием CuKα-излучения (λ = 1.5418 Å) при напряжении в трубке 40 кВ, токе в трубке 30 мА, времени экспозиции 1 с, шаге съемки 0.02°. Расшифровку результатов проводили с помощью программы HighScore. Шероховатость поверхности покрытий оценивали с использованием среднего арифметического отклонения профиля Ra по ГОСТ [16] с помощью профилометра модели 130 на отрезке длиной 7 мм на поверхности образца. Микротвердость образцов измеряли в соответствии с [17] по методу Виккерса на микротвердомере “Метолаб-502” при нагрузках на индентор 1 Н и времени выдержки 10 с. Трибологические испытания на трение и скольжение проводили на трибометре TRB3 с использованием стандартной методики шар – диск (стандарты ASTM G 133-95 и ASTM G 99). В качестве контртела применяли шарик диаметром 6.0 мм из стали ШХ15. Испытание выполняли при нагрузке 10 Н, линейной скорости 2 см/с, радиусе кривизны износа 3 мм и пути трения 22 м.
РЕЗУЛЬТАТЫ ИССЛЕДОВАНИЙ
На рис. 2 представлены микроснимки поперечных сечений детонационного покрытия образцов на основе Cr3C2–NiCr, полученные с помощью металлографического микроскопа модели “Альтами МЕТ 5S”, которые демонстрируют высокую плотность на границе раздела подложки с покрытием. Наблюдаются слоисто-пористая структура толщиной 60–120 мкм и отсутствие пор и трещин на границе раздела.
Рис. 2.
Микроснимки поперечного сечения образцов № 1 (а), № 2 (б) и № 3 (в). Плотность покрытия, %: а – 51; б – 58; в – 64
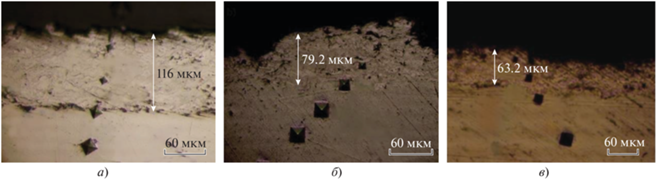
Графики распределения микротвердости по толщине покрытий Cr3C2–NiCr при разном объеме заполнения ствола пушки взрывчатой смесью приведены на рис. 3. Средняя микротвердость покрытий на основе Cr3C2–NiCr составляет (1130 ± 55) HV для образца № 1, (1006 ± 60) HV для образца № 2 и (1004 ± 60) HV для образца № 3.
Рис. 3.
Распределение микротвердости по глубине покрытия в зависимости от расстояния от поверхности покрытия l. Номер образца: а – l; б – 2; в – 3
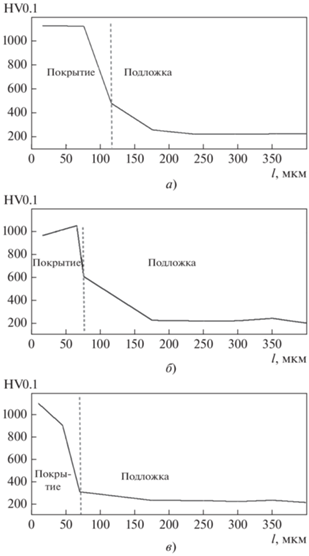
Наблюдается неравномерность микротвердости по глубине покрытия в разных режимах заполнения ствола. Незначительное снижение микротвердости установлено на поверхности покрытия образца № 2, а у образца № 1 микротвердость равномерная по толщине покрытия. В образце № 3 имеется небольшое увеличение микротвердости на поверхности покрытия. В образце № 2 на границе раздела подложки с покрытием средняя микротвердость составила 607.5 HV, что выше микротвердости покрытия образцов № 1, 3.
Данные измерения шероховатости покрытий на основе Cr3C2–NiCr приведены на рис. 4. Поверхности всех покрытий имеют неоднородную слоистую структуру с порами и волнообразным расположением структурных составляющих. В качестве основного параметра измерения шероховатости поверхности было выбрано среднее арифметическое отклонение профиля Ra. Разные значения этого показателя, возможно, связаны с различием воздействия ударной волны, которая приводит к уплотнению покрытия.
Рис. 4.
Микроснимки поверхности покрытий на основе Cr3C2–NiCr, полученных методом детонационного напыления образцов № 1 (а), № 2 (б), и № 3 (в). Rа: а – 5.34; б – 4.64; в – 5.12
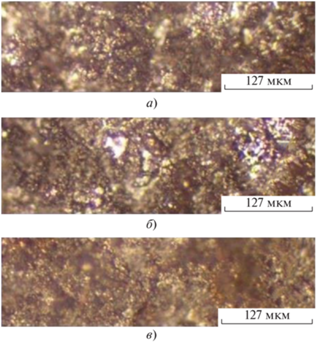
Результаты рентгенограммы поверхности представлены на рис. 5. В покрытиях образцов обнаружены Cr3C2, Cr3O4, Cr2O3 и Сr23С6. В зависимости от степени заполнения ствола газовой смесью интенсивность фазовых составов покрытий изменяется. К примеру, на дифрактограммах образца № 3 наблюдается увеличение интенсивности фаз Cr3C2, Cr23C6 и CrNi3. Это, возможно, обусловлено высокой температурой порошка при напылении, которая зависит от степени заполнения ствола. При высокой степени заполнения ствола температура в зоне реакции достигает 3000–4000°С в зависимости от расстояния от ствола детонационной пушки до подложки.
Рис. 5.
Рентгенограммы покрытий Cr3C2–NiCr на поверхности образцов № 1 (а), № 2 (б) и № 3 (в). 1 – Cr7C3; 2 – Cr3O; 3 – Cr23С6; 4 – Cr3C2; 5 – CrNi3
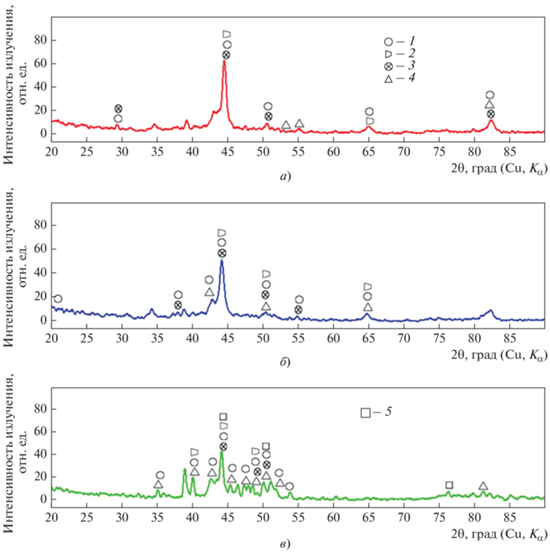
Для оценки износостойкости покрытий Cr3C2–NiCr были выполнены трибологические испытания. Объем износа, мм3, покрытия на образце № 1 составил примерно 0.12, на образце № 2 – 0.124, на образце № 3 – 0.115. Объем износа сравнительно низкий для образца № 3, что, согласно результатам рентгеноструктурного анализа, может быть вызвано интенсивностью фазы Cr3C2 и наличием интерметаллической фазы CrNi3.
Значение коэффициента трения покрытия находится в интервале 0.06–0.45 (рис. 6). Кривые коэффициента трения покрытий в начале процесса испытания (до наработки) имеют скачки. Это, видимо, связано с тем, что покрытия имели высокие значения шероховатости (Ra = 4.64–5.34).
ВЫВОДЫ
1. Основными структурными составляющими детонационных покрытий на основе Cr3C2–NiCr на поверхности теплоустойчивой стали марки 12Х1МФ являются Cr3C2, Cr3O4, Cr2O3, Сr23С6 и CrNi3.
2. Увеличение степени заполнения ствола газовой смесью O2/C2H2 с 51 до 64% может привести к формированию CrNi-фазы.
3. В зависимости от степени заполнения ствола покрытия имеют следующие характеристики: коэффициент трения 0.06–0.45, микротвердость 944–1185 HV, шероховатость Ra = 4.64–5.34, толщина слоисто-пористой структуры 60–120 мкм.
4. В зависимости от технологических режимов детонационного напыления изменяются микротвердость, шероховатость и трибологические свойства покрытия, что позволяет получать покрытия с заданными свойствами.
Список литературы
Zrili M., Aleksi R. The effect of long term exposure to elevated temperature on steam line steel properties thermal science // Therm. Sci. 2003. V. 7. No. 1. P. 33–46. https://doi.org/10.2298/TSCI0301033Z
Маркашова Л.И. Особенности структуры металлокерамических покрытий, полученных детонационным напылением // IX Междунар. симпозиум “Горение и плазмохимия”. Алматы, Казахстан, 13–15 сентября 2017 г. С. 127–130.
Reserach of the mechanic-tribological characteristics of Ti3SiC2/TiC coatings after annealing / D.B. Buitkenov, B.K. Rakhadilov, Zh.B. Sagdoldina, D. Erbolatuly // Eurasian J. Phys. and Functional Mater. 2020. V. 4. No. 1. P. 86–92. https://doi.org/10.29317/ejpfm.2020040109
Gerasimova N.P. Ash wear of boiler heating surfaces // Proc. of the Irkutsk State Techn. University. 2020. V. 24. No. 3. P. 596–605. https://doi.org/10.21285/1814-3520-2020-3-596-605
Bhatia R., Singh H., Sidhu B.S. Characterization of HVOF sprayed 75% Cr3C2–25% NiCr coating for erosion-corrosion resistance // J. Emerg. Trends Eng., Sci. Technol. 2014. V. 1. No. 1. P. 76–85.
Davis J.R. Handbook of thermal spray technology. ASM Intern. Materials Park, Ohio, USA, 2004.
Room- and high temperature wear resistance of MCrAlY coatings deposited by detonation gun (D-gun) and supersonic plasma spraying (SSPS) techniques / M. Kilic, D. Ozkan, M.S. Gok, A.C. Karaoglanli // Coatings. 2020. V. 10. No. 11. P. 1107. https://doi.org/10.3390/coatings10111107
Structure and properties of detonation coatings based on titanium carbosilicide / B.K. Rakhadilov, D.B. Buitkenov, B.T. Tuyakbaev, Zh.B. Sagdoldina, A.B. Kenesbekov // Key Eng. Mater. 2019. V. 821. P. 301–306. https://doi.org/10.4028/www.scientific.net/KEM.821.301
Kaur M., Singh H., Prakash S. Role of detonation gun spray Cr3C2–NiCr coating in improving high temperature corrosion resistance of SAE-213–T22 and SAE-347H steel in presence of Na2SO4–82% Fe2(SO4)3 salt deposits // Surface. Eng. 2009. V. 26. Is. 6. P. 428–439. https://doi.org/10.1179/026708409x12490360425963
Kumar M., Mudgal D., Ahuja L. Evaluation of high temperature oxidation performance of bare and coated T91 steel // Mater. Today: Proc. 2019. V. 28. P. 620–624. https://doi.org/10.1016/j.matpr.2019.12.232
Surface engineering analysis of d-gun sprayed cermet coating in aggressive environment / V.N. Shukla, Trivedi Harshit, Kumar Hemant, Anant Yadav // Mater. Today: Proc. 2017. V. 4. P. 10212–10215.
Computer-controlled detonation spray-ing: flexible control of the coating chemistry and microstructure / V.Y. Ulianitsky, D.V. Dudina, A. Shtertser, I. Smurov // Metals. 2019. V. 9. No. 12. P. 1244. https://doi.org/10.3390/met9121244
Influence of pulsed plasma treatment on phase composition and hardness of Cr3C2–NiCr coatings / D.N. Kakimzhanov, B.K. Rakhadilov, Yu. Tyurin, M.K. Dautbekov // Eurasian J. Phys. and Functional Mater. 2021. V. 5. No. 1. P. 45–51. https://doi.org/10.32523/ejpfm.2021050106
Influence of the detonation-spraying mode on the phase composition and properties of Ni–Cr coatings / M. Maulet, B.K. Rakhadilov, Zh.B. Sagdoldina, A.B. Kassymov, D.N. Kakimzhanov // Eurasian J. Phys. and Functional Mater. 2020. V. 4. No. 3. P. 184–189. https://doi.org/10.29317/ejpfm.2020040307
ГОСТ 20072-74. Сталь теплоустойчивая. Технические условия. М.: Госстандарт СССР, 1974.
ГОСТ 2789-73. Шероховатость поверхности. Параметры и характеристики. М.: Стандартинформ, 2018.
ГОСТ 9450-76. Измерение микротвердости вдавливанием алмазных наконечников. М.: Изд-во стандартов, 1976.
Дополнительные материалы отсутствуют.
Инструменты
Теплоэнергетика