Теплоэнергетика, 2022, № 12, стр. 84-91
Сравнительные исследования процесса получения биоугля методами гидротермальной карбонизации и торрефикации в среде перегретого пара
Р. Л. Исьемин a, *, С. Н. Кузьмин a, В. В. Коняхин a, О. Ю. Милованов a, А. В. Михалёв a, Н. С. Муратова a, А. В. Небываев a, В. С. Кох-Татаренко a
a Тамбовский государственный технический университет
392032 г. Тамбов, Мичуринская ул., д. 112, корп. И, оф. 1, Россия
* E-mail: risemin@gmail.com
Поступила в редакцию 07.04.2022
После доработки 23.05.2022
Принята к публикации 30.05.2022
- EDN: UOMKAG
- DOI: 10.56304/S0040363622120037
Аннотация
Накопление куриного помета с подстилкой (древесных опилок или измельченной соломы), образующегося в больших количествах на птицефабриках (при производстве 1 кг мяса птицы получается 1–3 кг помета с подстилкой), представляет серьезную экологическую проблему. Птицефабрики – одни из самых крупных потребителей электрической энергии, которую можно генерировать путем сжигания помета с подстилкой, в том числе совместно с углем, в топках с пузырьковым или циркулирующим кипящим слоем. Для повышения эффективности и экологичности сжигания (сокращения выбросов оксида углерода) должны быть снижены влажность помета и содержание в нем летучих веществ, а также увеличена теплота его сгорания. Для этого помет с подстилкой перед горением можно подвергнуть предварительной обработке методом гидротермальной карбонизации или торрефикации. В настоящей работе проведено сравнение результатов исследований методов переработки смеси куриного помета и опилок в биотопливо в среде перегретого водяного пара. Термохимической обработке подверглись куриный помет и его смесь с древесными опилками в соотношении 1 : 1, 1 : 2 и 2 : 1. Гидротермальная карбонизация осуществлялась в лабораторном автоклаве периодического действия при температуре 220°С в течение 1 и 4 ч. Торрефикация биомассы осуществлялась в реакторе с кипящим слоем, образованном частицами биоугля, предварительно полученного в среде перегретого водяного пара при температурах 300 и 350°С. Было установлено, что методом гидротермальной карбонизации можно повысить содержание углерода в помете с подстилкой от 42 до 63%, а высшую теплоту сгорания от 16.7 до 17.8 МДж/кг. В свою очередь, методом торрефикации в перегретом паре в кипящем слое можно увеличить эти показатели до 75% и 18.8 МДж/кг соответственно. Процессы гидротермальной карбонизации и торрефикации требуют немалых затрат энергии. Для того чтобы повысить экономическую эффективность обоих процессов, исследуется возможность извлечения из отработанной воды (или конденсата) 5-гидроксиметилфурфурола, который рассматривается как ключевой реагент, так называемое “соединение-платформа”, для производства разнообразных практически важных веществ, включая полимеры, фармацевтические препараты, растворители и топлива. Установлено, что содержание 5-гидроксиметилфурфурола в этих водных средах составляет 0.02–0.80 г/дм3 и зависит от метода термохимической обработки биомассы и температуры, при которой протекал процесс.
Отходы птицеводства содержат смесь помета, подстилочного материала (древесные опилки или солому), остатки корма, мертвых птиц, разбитых яиц и перьев, удаленных из птичников. Эти отходы традиционно применялись как удобрение, однако их чрезмерное внесение в почву вызывает ее загрязнение нитратами и несбалансированную эвтрофикацию природных водоемов. Последняя может приводить к бурному развитию водорослей (цветению воды) и появлению в воде цианобактерий, которые в период цветения выделяют токсины (алкалоиды и низкомолекулярные пептиды), способные вызвать отравление людей и животных. Из-за эвтрофикации также возникает дефицит кислорода в водоемах и замор рыбы [1, 2].
Альтернативный, экологически приемлемый способ утилизации указанных отходов представляет собой их преобразование в энергию путем сжигания, газификации или пиролиза, а получаемый при этом побочный продукт – зола – может использоваться как удобрение [3–6].
В последние годы такой метод обработки биомассы, как гидротермальная карбонизация, стал привлекать внимание исследователей благодаря возможности получения биоугля или гидроугля, которые могут быть использованы в качестве биотоплива или адсорбента [7, 8], как активированный уголь [9–12].
Процесс гидротермальной карбонизации реализован в реакторах периодического действия и включает в себя следующие стадии [13, 14]:
загрузку воды и биомассы в реактор в необходимом соотношении;
нагрев реактора до требуемой температуры с подъемом давления внутри реактора для исключения вскипания воды;
гидротермальную карбонизацию биомассы в течение заданного времени;
быстрое охлаждение реактора;
сброс давления, выгрузку и сушку гидроугля.
Однако процесс гидротермальной карбонизации имеет следующие недостатки:
периодичность;
необходимость применения реакторов, работающих под высоким давлением;
потребление большого объема воды, которая в процессе переработки биомассы становится загрязненной и сама представляет собой отход, требующий утилизации.
Биоуголь может быть получен также методом торрефикации. По сути, торрефикация – это метод химической обработки, при котором биомасса нагревается в инертной среде до 300°C. Обычно процесс характеризуется низкой скоростью нагрева частиц (менее 50°C/мин) и относительно длительным временем пребывания в реакторе, которое в зависимости от сырья, технологии и температуры составляет от 30 до 120 мин [15, 16].
Торрефикация, так же как и гидротермальная карбонизация, позволяет увеличить теплоту сгорания биомассы, снизить затраты на ее измельчение для совместного сжигания с углем, повысить ее влагостойкость.
Но для осуществления обоих процессов требуются довольно большие финансовые вложения. В работе [17] указано, что стоимость пеллет, полученных из торрефицированной биомассы, составляет 25.72–32.81 евро/т, а из “сырой” биомассы – 1.53–16.85 евро/т.
Торрефицированные пеллеты содержат больше энергии, чем пеллеты, изготовленные из “сырой” биомассы. Поэтому доставка 1 ГДж энергии, полученной при их сжигании, составляет по различным расчетам от 1.88 евро [18] до 8.51 евро [19], тогда как стоимость доставки 1 ГДж пеллет, изготовленных из “сырой” биомассы, оказывается на 14% выше [20]. Однако снижение затрат на доставку не компенсирует всех затрат на торрефикацию биомассы, и надо искать пути повышения экономической эффективности этого процесса.
Для торрефикации в качестве газа-носителя может быть использован перегретый пар [21, 22]. Биомассу сушат с помощью перегретого пара при атмосферном давлении, а затем нагревают до 250°C в среде пара, не содержащей кислорода. Торрефикация перегретым паром имеет преимущества по сравнению с традиционным методом благодаря превосходным свойствам теплопередачи (теплоемкость перегретого водяного пара в 2 раза выше, а кинематическая вязкость в 2 раза ниже, чем у азота, при той же температуре).
Летучие компоненты, выделяющиеся в процессе торрефикации, содержат много ценных веществ. Однако для реализации традиционных технологий используется азот, поэтому летучие компоненты невозможно отделить от общего газового потока. Торрефикация в перегретом паре позволят легко отделить эти компоненты после конденсации отработанного пара. Ввиду ценности конденсата торрефикации, богатого органическими соединениями, и возможности производства из него ценных химикатов, стоимость производства торрефицированной биомассы может быть значительно снижена.
Во многих отношениях торрефикация биомассы в среде перегретого водяного пара становится близка процессу гидротермальной карбонизации.
Цель настоящей работы – выбор из двух описанных выше технологий оптимальной для получения биоугля (гидроугля) на примере переработки смеси куриного помета и опилок.
МЕТОДИКА ЭКСПЕРИМЕНТА
В эксперименте в качестве исходного сырья использовался куриный помет, а также смесь его с древесными опилками в соотношении 1 : 1, 1 : 2 и 2 : 1.
На рисунке представлена схема пилотной установки для торрефикации биоотходов в кипящем слое в среде перегретого водяного пара. Пилотная установка состоит из реактора для карбонизации в кипящем слое, бункеров для исходной биомассы и биоугля, циклона для отделения парогазового потока от частиц биоугля, выносимых из реактора, конденсатора парогазовой смеси. На рисунке не показаны котел для генерации пара и пароперегреватель. Реактор для торрефикации снабжен газораспределительной решеткой для ввода перегретого водяного пара под кипящий слой (на рисунке не показана). По высоте реактора расположены одна над другой три термопары для измерения температуры внутри него. Нижняя термопара расположена на расстоянии 40 мм от газораспределительной решетки, средняя термопара – на расстоянии 210 мм от нее, верхняя термопара – 410 мм. Головка каждой термопары установлена по центру реактора и при необходимости может перемещаться в радиальном направлении. Бункер для исходной биомассы снабжен крышкой для загрузки биомассы и шнековым питателем с мотор-редуктором, который оснащен частотным регулятором, позволяющим легко контролировать подачу биомассы в реактор. Бункер для сбора биоугля выполнен обогреваемым и снабжен шнеком с мотор-редуктором с регулируемым числом оборотов для выгрузки биоугля из реактора. Циклон для отделения частиц биоугля, выносимых из реактора, от парогазового потока также обогреваемый.
Перед началом эксперимента в реактор засыпали примерно 6 дм3 предварительно полученного из помета с опилками биоугля того состава, торрефикация которого исследовалась в эксперименте. Затем в бункер 1 засыпали 2 кг сырья, подлежащего торрефикации.
С помощью электронагревателей установка выводилась на рабочий режим. После выхода на него подавался насыщенный водяной пар, который, пройдя через пароперегреватель, поступал под решетку реактора. Температура под решеткой фиксировалась и составляла 300 или 350°С. Загрузка материала проводилась в течение 15–17 мин. С началом подачи исходного материала с помощью газоанализатора Vario Plus Industrial Syngas, находившегося за конденсатором, непрерывно осуществлялся отбор неконденсирующихся газов (диоксида углерода, оксида углерода, водорода и метана). После того как концентрация указанных веществ уменьшалась до значений, которые были до начала подачи биомассы в реактор, эксперимент прекращался и биоуголь направлялся в бункер 5. Затем вся установка продувалась холодным азотом и охлажденный биоуголь выгружался из бункера 5 для проведения химического анализа.
Гидротермальную карбонизацию помета и его смеси с опилками проводили в автоклаве из нержавеющей стали объемом 250 см3. Каждый эксперимент протекал при 220°С в течение 1 и 4 ч, при этом в автоклав загружалось 100 г исходной биомассы. Закрытый автоклав помещали в нагретую конвекционную печь. После завершения реакции его вынимали из печи и ставили в вытяжной шкаф при комнатной температуре для охлаждения продуктов реакции. Для отделения жидких продуктов от гидроугля применяли вакуумную фильтрацию. Отделенный гидроуголь промывали в 1 дм3 деионизированной воды и сушили в течение 8 ч при 120°С.
Выгруженный и охлажденный биоуголь и гидроуголь подвергали химическому анализу. По стандартным методикам [23–27] устанавливали содержание в них влаги, золы, углерода, водорода, серы и азота. Количество кислорода в биоугле и гидроугле равнялось разности между общим содержанием всех компонентов (100%) и процентным содержанием влаги, золы, серы, азота, водорода и углерода.
Теплоту сгорания биомассы определяли согласно [28].
При проведении вышеописанного анализа использовали следующие приборы: весы лабораторные AR-F220CE, шкаф сушильный ШСЗ, электропечь лабораторную SNOL 7.2/1100, калориметр бомбовый АБК-1.
Для количественного определения гидроксиметилфурфурола применяли метод газовой хромато-масс-спектрометрии.
В настоящей работе использован хромато-масс-спектрометр SHIMADZU GCMS-TQ8040. Для хроматографического разделения была взята капиллярная колонка SH-Stabilwax (30 м × 0.32 мм × × 0.1 мкм, полярная фаза на основе полиэтиленгликоля). Хроматографическое разделение проводилось при температуре инжектора 200°С и скорости газа-носителя гелия 1.4 см3/мин.
Идентификация осуществлялась с помощью программы библиотечного поиска NIST 17.
Для количественного определения гидроксиметилфурфурола предварительно по стандартным веществам были проведены калибровки.
РЕЗУЛЬТАТЫ И ИХ ОБСУЖДЕНИЕ
В табл. 1 представлены результаты химического анализа образцов биоугля и гидроугля, полученных методами торрефикации в среде перегретого водяного пара и гидротермальной карбонизации соответственно.
Таблица 1.
Результаты химического анализа образцов биоугля и гидроугля, полученных методами торрефикации в среде перегретого водяного пара и гидротермальной карбонизации соответственно
Вид исходного сырья | Температура обработки, °С | Продолжительность обработки | Содержание золы, % | Содержание углерода, % |
---|---|---|---|---|
Торрефикация | ||||
Помет и опилки в соотношении: | ||||
2 : 1 | 300 | 40 мин | 41 | 34 |
350 | 30 мин | 19 | 59 | |
1 : 1 | 300 | 40 мин | 29 | 50 |
350 | 30 мин | 31 | 49 | |
1 : 2 | 300 | 40 мин | 20 | 60 |
350 | 30 мин | 19 | 75 | |
Помет | 350 | 30 мин | 39 | 37 |
Гидротермальная карбонизация | ||||
Помет и опилки в соотношении 1 : 1 | 220 | 1 ч | 24 | 58 |
220 | 4 ч | 28 | 63 | |
Помет | 220 | 1 ч | 49 | 44 |
220 | 4 ч | 51 | 47 |
Анализ данных табл. 1 показывает, что в случае обработки биомассы методом торрефикации в среде перегретого водяного пара в кипящем слое существенное влияние на зольность получаемого биоугля и содержание в нем углерода оказывают исходный состав биоотходов и температура обработки. С увеличением доли опилок содержание золы в биоугле понижается от 41 до 19%, а содержание углерода увеличивается от 34 до 75%. При этом максимальное значение для углерода (75%) достигается при повышении температуры торрефикации до 350°С.
В полученном биоугле содержание водорода колеблется в пределах 3.63–5.00% и уменьшается с увеличением температуры обработки, содержание кислорода составляет 11.6–23.4% и сокращается с ростом температуры обработки, содержание серы находится в диапазоне 0.80–0.95%. Температура процесса на содержание серы не влияет, оно уменьшается при снижении доли помета в смеси. Содержание азота в результате торрефикации с повышением температуры процесса изменяется от 5.7 до 4.30% и тоже снижается при сокращении доли помета в смеси.
Теплота сгорания исходной смеси помета равнялась 16.7–17.0 МДж/кг и увеличивалась при росте доли опилок в ней. В результате торрефикации биомассы она достигала 18.8 МДж/кг (для смеси помета и опилок в соотношении 1 : 2).
В результате обработки биомассы методом гидротермальной карбонизации с повышением доли помета в смеси зольность получаемого гидроугля изменялась от 24 до 41%. С увеличением доли опилок в смеси и продолжительности обработки содержание углерода в гидроугле возрастало с 44 до 63%.
Схема пилотной установки для гидротермальной карбонизации биоотходов в кипящем слое в среде перегретого водяного пара. 1 – бункер для исходной биомассы; 2 – реактор для карбонизации в кипящем слое; 3 – циклон для отделения парогазового потока от частиц биоугля, выносимых из реактора; 4 – конденсатор парогазовой смеси; 5 – бункер для биоугля; 6 – датчик давления; 7 – термопары
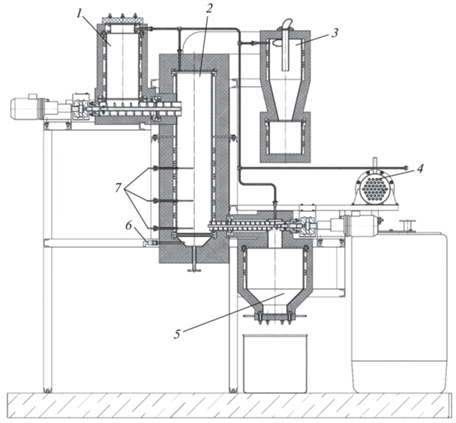
Максимальное содержание углерода в гидроугле составляло 63% при зольности 28%. Этот гидроуголь имел высшую теплоту сгорания 17.8 МДж/кг, которая была достигнута для смеси помета и опилок в соотношении 1 : 1.
Содержание азота, водорода, серы и кислорода в гидроугле близко к значениям соответствующих показателей, полученных для биоугля.
Биоуголь с максимальной теплотой сгорания может быть получен после обработки в течение 30 мин при температуре 350°С, а гидроуголь – в течение 4 ч при 220°С.
В табл. 2 представлены результаты исследования жидкой фазы (загрязненной воды, полученной при гидротермальной карбонизации биомассы, и конденсата после охлаждения отработанного пара процесса торрефикации). Из данных табл. 2 следует, что метод обработки биомассы (торрефикация в перегретом паре или гидротермальная карбонизация) оказывает влияние на содержание 5-гидроксиметилфурфурола в жидкой фазе. При обработке биомассы методом торрефикации его содержание в смеси составляет 0.19–0.80 г/дм3. Оно увеличивается с уменьшением доли помета в исходной смеси и сокращается с ростом температуры обработки. При обработке методом гидротермальной карбонизации содержание 5-гидроксиметилфурфурола в жидкой фазе составляет 0.02–0.08 г/дм3 и растет с повышением доли помета в исходной смеси.
Таблица 2.
Результаты химического анализа жидкой фазы
Вид исходного сырья | Температура обработки, °С | Продолжительность обработки | Содержание общего органического углерода, г/дм3 | Содержание 5-гидроксиметил-фурфурола, г/дм3 |
---|---|---|---|---|
Торрефикация | ||||
Помет и опилки в соотношении: | ||||
2 : 1 | 300 | 40 мин | 14 | 0.42 |
350 | 30 мин | 13 | 0.32 | |
1 : 1 | 300 | 40 мин | 10 | 0.54 |
350 | 30 мин | 9 | 0.19 | |
1 : 2 | 300 | 40 мин | 13 | 0.80 |
350 | 30 мин | 12 | 0.74 | |
Помет | 350 | 30 мин | 14 | 0.30 |
Гидротермальная карбонизация | ||||
Помет | 220 | 4 ч | 12 | 0.02 |
Помет и опилки в соотношении: | ||||
1 : 1 | 220 | 4 ч | 9 | 0.02 |
2 : 1 | 220 | 4 ч | 10 | 0.08 |
1 : 2 | 220 | 4 ч | 8 | 0.06 |
Для получения 5-гидроксиметилфурфурола метод торрефикации в кипящем слое в среде перегретого водяного пара является более предпочтительным, так как позволяет обеспечить концентрацию продукта примерно в 10 раз большую, чем при реализации метода гидротермальной карбонизации.
В настоящее время авторами статьи разработан комплекс оборудования, предназначенный для переработки смеси куриного помета и опилок методом влажной торрефикации в кипящем слое в среде перегретого водяного пара. Для его создания потребуются капитальные вложения в размере примерно 52 млн руб.
Комплекс оборудования имеет следующие характеристики:
Производительность по исходному помету, т/сут……....…........Не менее 1 |
Выход загрязненной воды на 1 кг биоугля, кг……..............................Не более 5 |
Расход перегретого водяного пара на технологический процесс, кг/ч……..................................................Не более 300 |
Избыточное давление водяного пара на выходе из пароперегревателя котла, МПа….......................................Не более 0.07 |
Расход твердого топлива на производство перегретого водяного пара (при низшей теплоте сгорания топлива 21 МДж/кг), кг/ч……..............................Не более 45 |
Обогрев реактора для влажной торрефикации……………...................Электрический |
При влажной торрефикации расход энергии распределяется следующим образом:
на сушку исходного сырья с 70 до 7% влажности – 33.24 кВт;
на генерацию пара – 262. 5 кВт;
на влажную торрефикацию биомассы – 25 кВт.
Таким образом, общий расход энергии на влажную торрефикацию смеси помета и опилок составляет 320.74 кВт.
Согласно имеющимся экспериментальным данным, приход энергии происходит:
при охлаждении парогазовой смеси с 300 до 100°С – 33.24 кВт;
при конденсации парогазовой смеси после сушки исходного сырья – 183 кВт (отработанный перегретый пар направляется в рубашку сушилки);
при влажной торрефикации помета с подстилкой, когда выход неконденсирующихся газов составляет 0.0015 дм3/с на 1 кг помета. Теплота сгорания этих газов составляет 1.26 МДж/м3. При сжигании неконденсирующихся газов, выделившихся при влажной торрефикации 50 кг/ч помета влажностью 5%, может быть получено 17.5 кВт тепловой энергии.
Тогда общий приход энергии будет равен 233.74 кВт (без учета теплоты сгорания биоугля), а энергоэффективность процесса составит 72.88%.
Комплекс оборудования для производства гидроугля 1 т/сут из биоотходов методом гидротермальной карбонизации был создан фирмой Grenol GmbH (Германия). Капитальные затраты на строительство этого комплекса составляют 3.5 млн евро.
В случае обработки смеси помета и опилок методом гидротермальной карбонизации сушка исходного сырья не требуется. Для гидротермальной карбонизации готовят смесь, содержащую примерно 1 часть обрабатываемого сырья и 8 частей воды и нагревают в реакторе до 220°С. На нагрев такой смеси при обработке 50 кг/ч помета потребуется примерно 104.5 кВт тепловой энергии. Затем смесь выдерживают при указанной температуре в реакторе в течение 4 ч. Все это время необходимо восполнять потери тепловой энергии в окружающую среду (примерно 5%), на что потребуется 21 кВт.
Таким образом, энергозатраты на процесс гидротермальной карбонизации 50 кг/ч помета составят 125.5 кВт.
После гидротермальной карбонизации будет получено примерно 45 кг/ч биоугля влажностью 70%, для снижения которой до 7% потребуется 30 кВт тепловой энергии. В таком случае общие затраты энергии на процесс будут равняться 155.5 кВт.
Использовать тепловую энергию отработанной (грязной) воды после процесса гидротермальной карбонизации затруднительно: эта вода имеет кислую реакцию (рН ≈ 4.5) и может вызывать кислотную коррозию теплообменного оборудования. В отработанной воде содержится значительное количество частиц биомассы, которая будет образовывать отложения на поверхностях теплообмена.
Считается, что “грязную” воду после гидротермальной карбонизации следует использовать для получения биогаза методом анаэробного сбраживания [29, 30], но для этого требуются дополнительные, причем немалые, капитальные затраты. То есть процесс гидротермальной карбонизации оказывается менее энергоэффективным, чем влажная торрефикация биомассы.
ВЫВОДЫ
1. Для улучшения топливных характеристик смеси помета и древесных опилок рекомендуется применять технологию торрефикации исходного сырья в кипящем слое в среде перегретого водяного пара, поскольку она позволяет увеличить высшую теплоту сгорания топлива на 12.6%, осуществить процесс обработки за 30 мин при давлении близком к атмосферному (избыточное давление не выше 0.07 МПа), получить достаточно высокую концентрацию 5-гидроксиметилфурфурола в конденсате отработанного пара.
2. Отработанный пар можно использовать как источник энергии для сушки исходного сырья.
3. Обработка смеси помета и древесных опилок методом гидротермальной карбонизации позволяет увеличить высшую теплоту сгорания топлива только на 6.6%, процесс длится 4 ч и протекает при избыточном давлении 2.3 МПа.
4. С учетом всех рассмотренных факторов можно констатировать, что влажная торрефикация обладает более высокой энергоэффективностью, чем процесс гидротермальной карбонизации.
Список литературы
Bitzer C.C., Sims J.T. Estimating the availability of nitrogen in poultry manure through laboratory and field studies // J. Environ. Quality. 1988. V. 17. Is. 1. P. 47–54. https://doi.org/10.2134/jeq1988.00472425001700010007x
Stevenson F.J. Cycles of soil: carbon, nitrogen, phosphorus, sulfur, micronutrients. N.Y.: Wiley, 1986.
Advances in poultry litter disposal technology – a review / B.P. Kelleher, J.J. Leahy, A.M. Henihan, T.F. O’Dwyer, D. Sutton, M.J. Leahy // Bioresour. Technol. 2002. V. 83. Is. 1. P. 27–36. https://doi.org/10.1016/S0960-8524(01)00133-X
Poultry litter gasification in a fluidized bed reactor: effects of gasifying agent and limestone addition / D.S. Pandey, M. Kwapinska, A. Gomez-Barea, A. Horvat, L.E. Fryda, L.P.L. Rabou, J.J. Leahy, W. Kwapinski // Energy Fuels. 2016. V. 30. Is. 4. P. 3085–3096. https://doi.org/10.1021/acs.energyfuels.6b00058
Updraft gasification of poultry litter at farm-scale – a case study / N.C. Taupe, D. Lynch, R. Wnetrzak, M. Kwapinska, W. Kwapinski, J.J. Leahy // Waste Manage. 2016. V. 50. P. 324–333. https://doi.org/10.1016/j.wasman.2016.02.036
Kumar M., Oyedun A.O., Kumar A. A review on the current status of various hydrothermal technologies on biomass feedstock // Renewable Sustainable Energy Rev. 2018. V. 81. Part. 2. P. 1742–1770. https://doi.org/10.1016/j.rser.2017.05.270
Liu Z., Zhang F.-S. Removal of lead from water using biochar’s prepared from hydrothermal liquefaction of biomass // J. Hazardous Mater. 2009. V. 167. Is. 1–3. P. 933–939. https://doi.org/10.1016/j.jhazmat.2009.01.085
Liu Z., Zhang F.-S., Wu J. Characterization and application of chars produced from pinewood pyrolysis and hydrothermal treatment // Fuel. 2010. V. 89. Is. 2. P. 510–514. https://doi.org/10.1016/j.fuel.2009.08.042
Sevilla M., Fuertes A.B., Mokaya R. High density hydrogen storage in superactivated carbons from hydrothermally carbonized renewable organic materials // Energy Environ. Sci. 2011. V. 4. P. 1400–1410. https://doi.org/10.1039/C0EE00347F
Sevilla M., Fuertes A.B. Sustainable porous carbons with a superior performance for CO2 capture // Energy Environ. Sci. 2011. V. 4. P. 1765–1771. https://doi.org/10.1039/C0EE00784F
Sevilla M., Maciá-Agulló J.A., Fuertes A.B. Hydrothermal carbonization of biomass as a route for the sequestration of CO2: chemical and structural properties of the carbonized products // Biomass Bioenergy. 2011. V. 35. Is. 7. P. 3152–3159. https://doi.org/10.1016/j.biombioe.2011.04.032
Sevilla M., Fuertes A.B. The production of carbon materials by hydrothermal carbonization of cellulose // Carbon. 2009. V. 47. Is. 9. P. 2281–2289. https://doi.org/10.1016/j.carbon.2009.04.026
Chen W.-H., Ye S.-C., Sheen H.-K. Hydrothermal carbonization of sugarcane bagasse via wet torrefaction in association with microwave heating // Bioresour. Technol. 2012. V. 118. P. 195–203. https://doi.org/10.1016/j.biortech.2012.04.101
Comparative assessment of wet torrefaction / Q.-V. Bach, K.-Q. Tran, R.A. Khalil, Ø. Skreiberg, G. Seisenbaeva // Energy Fuels. 2012. V. 27. Is 11. P. 6743–6753. https://doi.org/10.1021/ef401295w
Bergman P.C.A., Kiel J. H. A. Torrefaction for biomass upgrading // Proc. of the 14th European Biomass Conf. and Exhibition. Paris, France, 17–21 Oct. 2005.
Biomass conversion through torrefaction / A. Nordin, L. Pommer, M. Nordwaeger, I. Olofsson // Technologies for converting biomass to useful energy: combustion, gasification, pyrolysis, torrefaction and fermentation. Boca Raton, Florida: CRC Press, 2013.
Integrating torrefaction in the wood pellet industry: a critical review / L. Kumar, A.A. Koukoulas, S. Mani, J. Satyavolu // Energy Fuels. 2017. V. 31. Is. 1. P. 37–54. https://doi.org/10.1021/acs.energyfuels.6b02803
Status overview of torrefaction technologies / J. Koppejan, S. Sokhansanj, S. Melin, S. Madrali. IEA Bioenergy Task, 2012.
Logistics cost analysis between wood pellets and torrefied biomass pellets: the case of Portugal / R. Godina, L.J.R. Nunes, F.M.B.C. Santos, J.C.O. Matias // Proc. of the 7th Intern. Conf. on Industrial Technology and Management (ICITM). Oxford, UK, 7–9 March 2018. P. 284–287. https://doi.org/10.1109/ICITM.2018.8333962
Economic comparison of torrefaction-based and conventional pellet production-to-end-use chains / R. Ehrig, H.G. Gugler, C. Kristöfel, C.P. Pointner, I. Schmutzer-Roseneder, S. Feldmeier, M.K. Kolck, P. Rauch, C. Strasser, F. Schipfer, L. Kranzl, M.W. Wörgetter // Proc. of the 21st European Biomass Conf. and Exhibition. Copenhagen, Denmark, 3–7 June 2013. P. 1342–1349. https://doi.org/10.5071/21stEUBCE2013-3DO.2.1
Superheated steam as carrier gas and the sole heat source to enhance biomass torrefaction / D. Zhang, X. Chen, Z. Qi, H. Wang, R. Yang, W. Lin, J. Li, W. Zhou, F. Ronsse // Bioresour. Technol. 2021. V. 331. P. 124955. https://doi.org/10.1016/j.biortech.2021.124955
Roy B., Kleine-Möllhoff P., Dalibard A. Superheated steam torrefaction of biomass residues with valorisation of platform chemicals. Part 1: Ecological assessment // Sustainability. 2022. V. 14. Is. 3. P. 1212. https://doi.org/10.3390/su14031212
ГОСТ Р 54186-2010. Биотопливо твердое. Определение содержания влаги высушиванием. Часть 1: Влага общая. Стандартный метод. М.: Стандартинформ, 2010.
ГОСТ 32975.3-2014. Биотопливо твердое. Определение влаги высушиванием. Часть 3: Влага аналитическая. М.: Стандартинформ, 2019.
ГОСТ 32988-2014. Биотопливо твердое. Определение зольности. М.: Стандартинформ, 2015.
ГОСТ 32985-2014. Биотопливо твердое. Определение углерода, водорода и азота инструментальными методами. М.: Стандартинформ, 2019.
ГОСТ 33256-2015. Биотопливо твердое. Определение содержания общей серы и общего хлора. М.: Стандартинформ, 2015.
ГОСТ 33106-2014. Биотопливо твердое. Определение теплоты сгорания. М.: Стандартинформ, 2015.
Oliveira I., Blöhse D., Ramke H.-G. Hydrothermal carbonization of agricultural residues // Bioresour. Technol. 2013. V. 142. P. 138–146. https://doi.org/10.1016/j.biortech.2013.04.125
Effect of inoculum source and initial concentration on the anaerobic digestion of the liquid fraction from hydrothermal carbonization of sewage sludge / M.A. De la Rubia, J.A. Villamil, J.J. Rodriguez, A.F. Mohedano // Renewable Energy. 2018. V. 127. P. 697–704. https://doi.org/10.1016/j.renene.2018.05.002
Дополнительные материалы отсутствуют.
Инструменты
Теплоэнергетика