Теплоэнергетика, 2022, № 12, стр. 31-39
Получение глинозема из золы угольных электростанций
Л. М. Делицын a, *, Р. В. Кулумбегов a, О. С. Попель a, М. Г. Сульман b
a Объединенный институт высоких температур РАН
125412 Москва, Ижорская ул., д. 13. корп. 2, Россия
b Тверской государственный технологический университет
170026 г. Тверь, наб. Афанасия Никитина, д. 22, Россия
* E-mail: delitzin@ihed.ras.ru
Поступила в редакцию 31.03.2022
После доработки 02.05.2022
Принята к публикации 23.05.2022
- EDN: IZMAHA
- DOI: 10.56304/S0040363622120025
Аннотация
Энергетический сектор России, использующий уголь для генерации тепла и электроэнергии, – крупный источник золошлаков, отвалы которых занимают большие площади и одновременно являются причиной экологических проблем. При этом они содержат в себе глинозем и другие ценные продукты. В золоотвалах угольных электростанций Уральского региона на сегодняшний день накоплено около 350 млн т золы, количество которой ежегодно увеличивается на 7–8 млн т. Получение глинозема из золошлаковых отвалов на собственных предприятиях в условиях складывающейся конъюнктуры на мировом рынке представляет собой важнейшую задачу отечественной металлургической промышленности. Так, золы крупных тепловых угольных электростанций Уральского региона России: Троицкой, Рефтинской, Верхнетагильской и др. – содержат 28–32% глинозема и могли бы стать техногенным сырьем для производства алюминия, частично заместив импорт бокситов в Россию из зарубежных стран. В статье представлены результаты экспериментальных исследований, направленных на разработку технологии извлечения качественного глинозема из высокоглиноземной золы угольных электростанций. Изучено влияние различных технологических параметров на процесс получения целевого продукта. На первой стадии данного процесса в результате частичного обескремнивания золы раствором щелочи выделяют обогащенный глиноземный концентрат, который по своим физико-химическим свойствам близок к низкосортному бокситовому сырью. На второй стадии технологии методом спекания глиноземного концентрата с карбонатами натрия и кальция получают продукт с 97–98%-ным содержанием Al2O3, при этом степень извлечения глинозема из золы составляет 88–90%.
Алюминий – один из наиболее востребованных металлов в мировой промышленности, производство которого на сегодняшний день достигает 50–55 млн т/год. Ежегодный прирост потребления алюминия по разным источникам составляет 3–5% относительно предыдущего года. Благодаря широким возможностям применения в различных отраслях промышленности, этот металл является лидирующим конструкционным материалом XXI в. Потребление алюминия в России за 2021 г. составило примерно 1.2 млн т [1]. На энергетический сектор приходится 13–14% затрат алюминия с перспективами роста его использования. Из всех типов традиционного глиноземного сырья (бокситов, нефелиновых руд, аргиллитов, глины и др.) особое значение имеет зола тепловых электростанций (ТЭС), работающих на угле Экибастузского бассейна. К их числу относятся крупные тепловые электростанции Уральского региона: Троицкая, Рефтинская, Верхнетагильская и др., зола которых характеризуется высоким содержанием глинозема (28–32%). Транспортная доступность (наличие железнодорожного и автомобильного сообщения) и развитая инфраструктура позволяют рассматривать золоотвалы угольных электростанций как перспективное, крупномасштабное техногенное сырье для производства глинозема. Кроме того, из него можно дополнительно получить магнетитовый концентрат, флотационный углеродный концентрат, ряд кремнеземных продуктов и прочие полезные компоненты. Вовлечение в переработку золошлакоотвалов, содержащих подобные золы, также снижает экологическую нагрузку на окружающую среду.
В настоящее время основной источник глинозема – бокситовые руды, две трети которых импортируют из зарубежных стран. В золоотвалах угольных электростанций Уральского региона на сегодняшний день накоплено около 350 млн т золы, и ее количество увеличивается на 7–8 млн т/год. При среднем количестве Аl2O3 в золе 28% содержание глинозема в золоотвалах составляет около 100 млн т.
Приведенные данные свидетельствуют о важности решения задачи по вовлечению золы электростанций в производство глинозема. В настоящее время в мире отсутствуют готовая технология получения глинозема из золы и перерабатывающие его предприятия. Различные подходы к разработке технологии получения глинозема из золы рассматриваются в ряде публикаций [2–8 ]. В [9] по технологии близкой к предлагаемой в данной работе авторами был получен глинозем, который даже после дополнительной стадии глубокого обескремнивания отвечает требованиям алюминиевой промышленности. Степень извлечения глинозема составила 96%.
Цель данной работы – изучение закономерностей технологических параметров получения глинозема из золы ТЭС. Результаты исследования могут быть применены при разработке метода комплексного использования золы угольных электростанций.
ЭКСПЕРИМЕНТАЛЬНЫЕ ИССЛЕДОВАНИЯ
Для проведения экспериментов по изучению закономерностей получения глинозема из золы были использованы:
золы из золошлакоотвалов угольных Троицкой, Рефтинской, Верхнетагильской и Каширской ГРЭС, на которых применяется мокрое золоудаление;
едкий натр NaOH (Ч, ГОСТ 2263-79), карбонат натрия Na2CO3 (Ч, ГОСТ 83-79), карбонат кальция CaCO3 (ХЧ, ГОСТ 4530-76), CO2 газообразный (ГОСТ 8050-85)22.
Исходный материал – золошлаки – разделяли на фракции на лабораторном рассеве У1-ЕРЛ-10. Фракция класса крупности более 0.315 мм является отвальными хвостами (отбрасывается, т.е. направляется в отвал), а менее 0.315 мм (82–85%) соответствует рабочей фракции (используется для экспериментальных исследований). Очистку золы от углерода осуществляли во флотационной машине 237 ФЛ-А с объемом камеры 1.7 дм3. Загрузка золы составляла 0.5 кг, продолжительность основной флотации 5–10 мин. Модификатор, предназначенный для повышения эффективности флотации, вводился непосредственно перед подачей собирателя и вспенивателя и контактировал с пульпой в течение 1 мин. Время контакта собирателя – 1 мин, вспенивателя – 0.5 мин.
В качестве собирателей использовали вакуумный газойль марки Б (вид 2, ТУ 38.1011304-2004, АО “Газпромнефть–Московский НПЗ”) и керосин (ТУ 0251-015-57859009-2015, НижегородХимПром). Флотореагентоксаль Т-66 (ТУ 20.14.60-029-05766801-2016, ПАО “Нижнекамскнефтехим”) применяли как вспениватель. Модификатором служил сополимер ПАВ-2, представляющий собой высокомолекулярное поверхностно-активное вещество, имеющее углеводородный радикал высокой гидрофобности [10] и получаемое путем сополимеризации нонилфенола с оксидом этилена. Химическая формула сополимера ПАВ-2 имеет вид
Магнитную фракцию из золы удаляли с помощью универсального электромагнитного сепаратора УЭМ-1.
Предварительно очищенные от углерода и магнетита 300 г золы (остаточное содержание углерода – 2%, Fe2O3 – 1.69%) с целью удалить часть диоксида кремния SiO2 растворяли в 0.75 дм3 20%-ного раствора NaOH при постоянном перемешивании в верхнеприводной мешалке Stegler MB-6 (500 мин–1) в течение 180–360 мин при температуре 20–100°С. Образовавшуюся пульпу фильтровали на одноступенчатом вакуумном насосе VE-160. Глиноземный концентрат промывали дистиллированной водой (50–70°С) до нейтрального pH и высушивали при 105°С до получения постоянной массы. Высушенный глиноземный концентрат смешивали с Na2CO3 и CaCO3 и спекали при 1200–1250°С. Полученный спек выщелачивали водой (75°С). Глинозем из перешедшего в раствор алюмината натрия осаждали барботажем СО2 при 70–80°С согласно реакции
(1)
$\begin{gathered} 2NaAl{{O}_{2}} + 3{{H}_{2}}O + C{{O}_{2}} \to \\ \to A{{l}_{2}}{{O}_{3}}\,\centerdot 3{{H}_{2}}O + N{{a}_{2}}C{{O}_{3}}. \\ \end{gathered} $Выпавший осадок гидроксида алюминия отфильтровывали под вакуумом, промывали водой и удаляли из него влагу в сушильном шкафу СНОЛ-3.5/3.5-И5М при 105°С. Термическую обработку шихты осуществляли в муфельной печи “Накал” (модель ПЛ-514) при температуре 600–1300°C в течение 60 мин в атмосфере воздуха с открытой поверхностью в корундовых тиглях. Анализ продуктов реакции проводили с помощью атомно-абсорбционного спектрофотометра Perklin Elmer, плазменного спектрометра Jobin Yvon, рентгеноспектрального аналитического комплекса JMS-5300 и фотометра КФК-2. Фазовый состав золы определяли рентгеновским методом на дифрактометре ДРОН-2 (исследуемый образец подвергался Cu-Kα-излучению), идентификацию фаз проводили на базе данных Pcpdfwin-ICPDS. Гранулометрический состав золы определяли на лазерном анализаторе частиц Analysette-22 Compact. Химический анализ исследованных проб золы показал примерно одинаковое содержание основных химических компонентов и кремниевого модуля µSi (Al2O3/SiO2) (табл. 1).
Таблица 1.
Химический состав зол тепловых электростанций, % (по массе)
Компонент | Электростанция | |||
---|---|---|---|---|
Троицкая | Рефтинская | Верхнетагильская | Каширская | |
SiO2 | 57.75 | 57.40 | 61.20 | 49.40 |
Al2O3 | 28.40 | 27.30 | 28.90 | 17.70 |
Fe2O3 | 4.80 | 5.35 | 4.20 | 6.79 |
CaO | 0.95 | 1.40 | 0.72 | 1.97 |
MgO | 0.48 | 0.63 | 0.52 | 1.20 |
Na2O | 0.37 | 0.15 | 0.44 | 0.32 |
K2O | 0.50 | 0.55 | 0.55 | 1.52 |
TiO2 | 1.05 | 1.10 | 1.38 | 0.89 |
P2O5 | 0.59 | – | 0.27 | 0.31 |
S | 0.11 | 0.73 | 0.35 | Нет данных |
C | 5.00 | 5.40 | 1.50 | 19.83 |
µSi | 0.49 | 0.48 | 0.47 | 0.35 |
ОБЕСКРЕМНИВАНИЕ ЗОЛЫ
Наиболее перспективной среди известных технологий производства глинозема из низкосортных бокситов является спекательная [11], которая также может быть использована для переработки золы. Однако высокое содержание SiO2 не позволяет использовать золу для получения глинозема по технологии спекания с известняком без ее предварительного обескремнивания. В случае прямого спекания шихты расход известняка на 1 т исходной золы становится очень высоким, а извлечение глинозема из спеков – низким. Поскольку в золах μSi <0.5, для того чтобы она стала пригодной для производства глинозема, необходимо удалить из нее такое количество кремнезема, чтобы μSi стал не менее 1. Для подготовки золы к извлечению из нее Al2O3 наиболее технологичным является метод химического обогащения алюмосиликатного сырья, цель которого – разделение оксидов алюминия и кремния с использованием растворов NaOH [12–15]. Метод основан на различии в растворимости оксидов кремния и алюминия, содержащихся в золе, при определенной температуре и концентрации NaOH в растворе. Согласно [12], для обескремнивания золы экибастузских углей оптимальная концентрация NaOH составляет 200 г/дм3. Температура щелочного раствора оказывает существенное влияние на растворимость SiO2 (рис. 1).
Рис. 1.
Зависимость растворимости диоксида кремния $\chi {}_{{Si{{O}_{2}}}}$ от температуры t щелочного раствора для зол различных электростанций (СNaOH = 20%, время выщелачивания 360 мин). Электростанция: 1 – Рефтинская; 2 – Троицкая; 3 – Верхнетагильская; 4 – Каширская. Точки – значения, полученные экспериментально; линия – усредняющая кривая
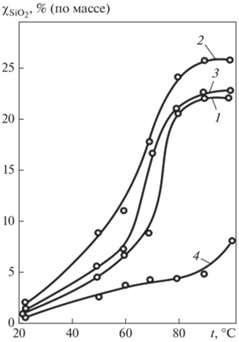
Наиболее высокую растворимость SiO2 показала зола Троицкой ГРЭС (см. рис. 1), поэтому дальнейшие эксперименты по изучению закономерностей получения глинозема проводились именно на ней. Поскольку химический состав зол Троицкой, Рефтинской и Верхнетагильской тепловых электростанций (см. табл. 1), сжигающих экибастузский уголь, почти одинаковый, результаты экспериментов с золой Троицкой ГРЭС в известной степени могут быть отнесены и к другим золам. Растворимость SiO2 золы Каширской ГРЭС значительно отличается от растворимости SiO2 зол уральских электростанций, что, вероятно, связано с различным фазовым составом зол и распределением частиц по размеру (рис. 2, 3). В золе Каширской ГРЭС преобладает рентгеноаморфное вещество, дающее в спектре два диффузных гало. Одно из них расположено в области брэгговских углов 2θ = 19°–32°. Наряду с рентгеноаморфным веществом в золе присутствуют кристаллические фазы, ведущие среди которых – глаукофан и кварц. В золе Троицкой ГРЭС кристаллическая фаза представлена муллитом и кварцем в соотношении 4 : 1.
Рис. 2.
Гранулометрическая характеристика золы Троицкой ГРЭС. [um] – диаметр частиц по логарифмической шкале; Q3(x) – процентное значение выхода каждой фракции, dQ3(x) – количество в образце частиц данного размера. 1 – кумулятивная кривая
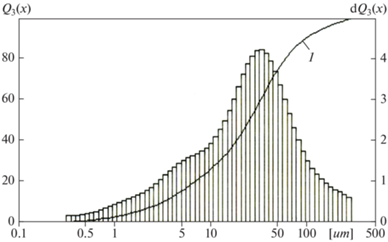
На примере золы Троицкой ГРЭС экспериментально были установлены оптимальная концентрация водного раствора NaOH и время выщелачивания для обескремнивания золы (рис. 4, 5). Полученные данные согласуются с данными, приведенными в работе [12].
Рис. 4.
Зависимость растворимости диоксида кремния $\chi {}_{{Si{{O}_{2}}}}$ золы Троицкой ГРЭС в щелочном растворе от концентрации NaOH (время выщелачивания 20 мин). Точки – значения, полученные экспериментально; линия – усредняющая кривая. Температура растворения золы, °С: 1 – 80; 2 – 100
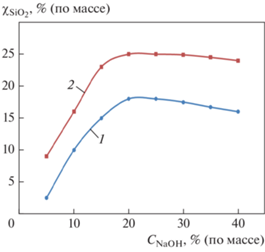
Рис. 5.
Зависимость растворимости диоксида кремния $\chi {}_{{Si{{O}_{2}}}}$ в щелочном растворе от времени выщелачивания τ и концентрации NaOH для золы Троицкой ГРЭС (температура щелочного раствора 100°С). СNaOH, %: 1 – 10; 2 – 20; 3 – оптимальное время растворения. Точки – значения, полученные экспериментально; линия – усредняющая кривая
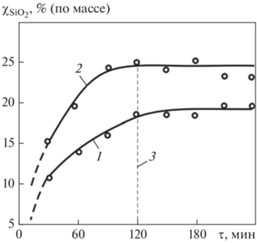
В процессе растворения золы в состав щелочного раствора переходит значительная часть SiO2 и в небольшом количестве Al2O3 и Fe2O3 – примерно 3.6 и 2.2% соответственно. Часть ионов натрия Na+ в результате реакции взаимодействия между компонентами системы переходит в состав глиноземного концентрата, в котором связывается, скорее всего, в виде не растворимых в щелочном растворе алюмосиликатов.
Определяющий фактор растворимости золы угольных электростанций в растворах NaOH – ее фазовый состав, зависящий от состава минеральной части углей, режимов горения угольного топлива в котлах, условий охлаждения золы-уноса и многих других причин. В составе всех зол в качестве основных веществ присутствуют стеклофаза (рентгеноаморфное вещество) и кристаллические фазы муллита, кварца, глаукофана, которые слабо растворяются в щелочном растворе. Поэтому достичь полного извлечения из золы кремнезема в раствор без ее дополнительной активации невозможно.
Один из способов повышения активации золы – ее термическая обработка. Поскольку основное количество SiO2 сосредоточено в стеклофазе, то при воздействии высоких температур она начинает перекристаллизовываться и превращаться в различные кристаллические модификации кварца (α-кварц, β-кварц, β-кристобалит, β-тридимит, γ-тридимит). Согласно детальным кристаллографическим исследованиям [16], перестройка кристаллической решетки кварца (чистая фаза, в отличие от золы) в процессе фазового перехода из низкотемпературной формы β-кварца в высокотемпературную α-кварца (β-кварц → α-кварц) происходит в интервале температур 550–580°С. Одновременно изменяются параметры кристаллической решетки SiO2.
Влияние термической активации золы Троицкой ГРЭС на ее растворимость в щелочном растворе не наблюдается вплоть до 600°С. Дальнейшее повышение температуры активации золы до 1200°С приводит к возрастанию растворимости SiO2 (табл. 2).
Таблица 2.
Влияние температуры термической обработки золы Троицкой ГРЭС на растворимость SiO2 и состав глиноземного концентрата после выщелачивания (масса исходной навески 42.4 г, температура выщелачивания 100°С, СNaOH = 20%, время выщелачивания 120 мин)
Температура, °С | Растворимость SiO2, % (по массе) | Содержание в глиноземном концентрате, % (по массе) | μSi | |
---|---|---|---|---|
SiO2 | Al2O3 | |||
20 | 27.9 | 39.50 | 38.00 | 0.96 |
600 | 29.5 | 38.10 | 38.90 | 1.03 |
700 | 34.0 | 34.00 | 41.50 | 1.22 |
800 | 33.2 | 34.70 | 41.00 | 1.18 |
900 | 35.0 | 33.05 | 42.07 | 1.27 |
1000 | 36.9 | 31.00 | 43.07 | 1.38 |
1100 | 38.3 | 29.00 | 44.60 | 1.54 |
1200 | 40.4 | 27.76 | 45.40 | 1.65 |
1300 | 39.2 | 28.40 | 45.07 | 1.58 |
Согласно фазовому анализу образцов золы Троицкой ГРЭС, увеличение растворимости SiO2 после термической активации, по-видимому, связано с тем, что термообработка при 1000°С приводит к диспергированию кристаллического кварца и некоторому увеличению количества муллита по сравнению с исходным уровнем. Однако многочисленные опубликованные данные свидетельствуют о том, что повышение температуры прокаливания твердых тел, в том числе минералов, как правило, влечет за собой рост среднего размера кристаллитов. Этот вопрос остается открытым и требует дополнительного инструментального изучения (с помощью различных физических методов).
В золе после термообработки появляется в небольшом количестве магнезиокарфолит Mg0.796Fe0.204Al2Si2O6(OH)4. Термообработка золы при достаточно высокой температуре не приводит к полному исчезновению кристаллогидратов. Основная часть материала после температурного воздействия, как и в исходной золе, находится в рентгеноаморфном состоянии.
Нерастворимый остаток по составу и свойствам кардинальным образом отличается от исходной золы. По существу, это новый продукт – глиноземный концентрат, который становится сырьем, подготовленным к получению из него Al2O3. Глиноземный концентрат представляет собой тонкий порошок, состоящий из мелкодисперсных шариков, средний диаметр которых в 1.5–2.0 раза меньше среднего диаметра стеклянных шариков в золе. В исходной золе шарики стекла и их сгущения в стеклофазе характеризуются гладкой оплавленной инертной поверхностью (рис. 6, а), после щелочной обработки вся поверхность шариков глиноземного концентрата оказывается изрыта ямками травления и становится химически активной. На некоторых участках зола выщелачивается настолько полно, что в ней остается только не растворимый в щелочном растворе каркас (рис. 6, б).
ПОЛУЧЕНИЕ ГЛИНОЗЕМА ИЗ КОНЦЕНТРАТА
Экспериментально установлено, что оптимальная температура спекания шихты, состоящей из глиноземного концентрата, Na2CO3 и CaCO3, для извлечения Al2O3 варьируется в диапазоне 1200–1250°С. Шихту готовили с избытком Na2CO3 и CaCO3 – с содержанием 10–13 и 3–5% соответственно (экспериментально установленные оптимальные пропорции) от стехиометрического соотношения. При спекании образуются водорастворимый алюминат натрия и практически не растворимый в воде двухкальциевый силикат по следующим реакциям:
(2)
$N{{a}_{2}}С{{O}_{3}} + A{{l}_{2}}{{O}_{3}} = N{{a}_{2}}O\,\,\centerdot A{{l}_{2}}{{O}_{3}} + C{{O}_{2}};$Алюминатный раствор по методике [11] разлагали барботажем CO2 до остаточного содержания Na2O $\centerdot $ Al2O3 в растворе не менее 5 г/дм3. В результате из раствора выпадали кристаллы гидроксида алюминия, оседавшие на дно реактора (рис. 7). Отфильтрованный на вакуум-фильтре осадок промывали водой, высушивали и подавали на приготовление шихты для выделения глинозема. Извлечение глинозема из золы составляло 88–90% (по массе). Около 3–5% глинозема оставалось в маточном растворе, остальное количество – в нерастворимой форме находилось в двухкальциевом силикате (белитовый шлам).
После прокаливания гидроксида алюминия при 700–800°С был получен обезвоженный глинозем, содержавший Al2O3 более 98% (по массе). Его химический состав, % (по массе), после прокаливания (при 700°С) представлен далее:
Na2O………………………………………….……Менее 0.10 |
MgO………………………………………….……………… 0.12 |
Al2O3……………………………………………………… 98.50 |
SiO2…………………………………….…………………… 0.52 |
K2O…………………………………….…………. Менее 0.10 |
CaO……………………………………………….………… 0.58 |
TiO2…………………………..…………………………… 0.008 |
Fe2O3…………………………………………….…………. 0.20 |
Таким образом, из зол угольных электростанций, богатых оксидом алюминия, может быть получен глинозем с содержанием Al2O3 более 98%. Содержание SiO2 в металлургическом глиноземе, согласно ГОСТ, должно быть менее 0.07% (по массе), что достигается путем добавления к алюминатному раствору соединений кальция согласно известной методике [17].
При расчете экономической эффективности переработки золы Троицкой ГРЭС для сравнения была взята структура себестоимости производства 1 т глинозема из бокситов по методу Байера и способу спекания (табл. 3). Способ спекания применяют для получения глинозема из высококремнистых бокситов с кремниевым модулем µSi < 5 и из нефелиновых руд.
Таблица 3.
Сравнительные экономические оценки себестоимости производства 1 т глинозема из бокситов и золы Троицкой ГРЭС
Вид затрат | Боксит | Зола | ||||
---|---|---|---|---|---|---|
Метод Байера | Способ спекания | Способ спекания | ||||
cтоимость, руб. | % | стоимость, руб. | % | стоимость, руб. | % | |
Боксит [18] | 8300 | 49.4 | 11300 | 33.5 | – | – |
Зола | – | – | – | – | 0 | 0.0 |
Известняк [19] | – | – | 600 | 1.8 | 2200 | 6.2 |
Известь [19] | 800 | 4.8 | 165 | 0.5 | 6600 | 18.6 |
Щелочь [20] | 4000 | 23.8 | – | – | 3000 | 8.5 |
Сода [20] | – | – | 3900 | 11.6 | 1200 | 3.4 |
Электроэнергия | 1400 | 8.3 | 4000 | 11.8 | 5000 | 14.1 |
Мазут [21] | 2300 | 13.7 | 13 800 | 40.8 | 19 000 | 49.2 |
Всего | 16 800 | 100.0 | 33 765 | 100.0 | 37000 | 100.0 |
Оплата труда (сотрудников предприятия) и условно-постоянные расходы (затраты на производство и реализацию продукции, не имеющие пропорциональной связи с количеством выпущенной продукции и сохраняющие относительно постоянную величину в планируемый период) при всех методах близки и поэтому в расчетах не учитывались. При использовании золы в качестве сырья затраты на нее исключаются, так как они учтены при генерации электроэнергии. При этом стоит отметить, что в качестве дополнительной продукции на 1 т глинозема можно получить 6.2 т белитового шлама, пригодного для производства портландцемента, цена на который составляет в среднем 4800 руб/т.
ВЫВОДЫ
1. Зола тепловых электростанций, работающих на угле Экибастузского бассейна, представляет собой крупный сырьевой ресурс для производства глинозема. Для того чтобы зола стала полноценным сырьем, на первой стадии обескремнивания ее необходимо подвергнуть переработке методом химического обогащения, которое позволяет получить глиноземный концентрат с μSi = 1.27–1.65.
2. На извлечение SiO2 в маточный раствор существенное влияние оказывают термическая активация золы и температура выщелачивания. Экспериментально установлена оптимальная концентрация NaOH для обескремнивания золы – 20%. В результате химического обогащения золы получается глиноземный концентрат с содержанием 45% Al2O3 и 28% SiO2. Обогащенный глиноземный концентрат представляет собой сырье, из которого методом спекания удается получить продукт с содержанием Al2O3 более 98%, после дополнительного обескремнивания соответствующий качеству металлургического глинозема. Извлечение глинозема по предложенной технологии составило 88–90%, что сопоставимо с другими технологиями. Так, при спекании золы-уноса (содержащей 52% оксида алюминия) с KHSO4 извлечение глинозема достигает 92% [6], при выщелачивании золы-уноса серной кислотой [7] – 94%, а при спекании с NH4HSO4 – 91% [8]. Практически по схожей технологии авторам [9] удалось достичь 96%-ного извлечения глинозема из золы, содержащей более 50% Al2O3. Следует отметить, что, в отличие от приведенных примеров, в золе Троицкой ГРЭС содержание SiO2 на 25–50% больше, чем в золе, использованной в [9].
3. Согласно экономическим оценкам, процесс получения глинозема из золы сопоставим с процессом его получения из высококремнистого боксита. По предложенной технологии, помимо целевого продукта, дополнительно выделяют белитовый шлам, широко используемый в строительной индустрии.
Список литературы
В 2021 году РУСАЛ поставил на внутренний рынок рекордные 1,2 млн тонн алюминия // Вести Братска – БСТ. [Электрон. ресурс.] https://bst. bratsk.ru/news/48485
Пат. РФ № 2027669, C1, МПК C01F 7/26. Способ переработки золы энергетических углей на глинозем и гипс / Б.Г. Хохлов, Л.П. Ни, В.Л. Романов, А.А. Мананков. Опубл. 27.01.1995. № 5041606/26 // Б. И. 1995. № 26.
Пат. РФ № 2605987, C, МПК B09B 3/00, C01B 33/12. Способ комплексной переработки золы от сжигания углей / И.В. Логинова, Л.И. Чайкин, А.А. Шопперт, С.В. Трубецкой. Опубл. 10.01.2017. № 2015129883. // Б. И. 2017. № 1.
Левченко В.Н. Опыт переработки золы-уноса Рефтинской ГРЭС // Материалы V междунар. конф. “Золошлаки ТЭС: удаление, транспорт, переработка, складирование”. Москва, 24–25 апреля 2014 г. М.: Издательский дом МЭИ, 2014. С. 91–94.
Особенности комплексной переработки летучей золы теплоэлектростанций / А.А. Лавриненко, И.В. Кунилова, Г.Ю. Гольберг, О.Г. Лусинян, В.Н. Кравченко // Научные основы и практика переработки руд и техногенного сырья: Материалы XXV Междунар. науч.-техн. конф., проводимой в рамках XVIII Уральской горнопромышленной декады. Екатеринбург, 2–11 апреля 2020 г. Екатеринбург: Изд-во “Форт Диалог-Исеть”, 2020. С. 338–341.
Alumina extraction from coal fly ash via low-temperature potassium bisulfate calcination / C. Guo, J. Zou, S. Ma, J. Yang, K. Wang // Minerals. 2019. V. 9. Is. 10. P. 585. https://doi.org/10.3390/min9100585
Thamilselvi J., Balamurugan P. Extraction of alumina from coal fly ash // Int. Res. J. Eng. Technol. 2018. V. 5. Is. 4. P. 2677–2681.
Wang Rc., Zhai Yc., Ning Zq. Thermodynamics and kinetics of alumina extraction from fly ash using an ammonium hydrogen sulfate roasting method // Int. J. Minerals, Metallurgy, Mater. 2014. V. 21. P. 144–149. https://doi.org/10.1007/s12613-014-0877-x
Alumina extraction from alumina rich fly ash generated from Inner-Mongolia Chinese coal / X.T. Liu, B.D. Wang, Y.F. Xiao, X.H. Wang, L.J. Zhao, G.Z. Yu, Q. Sun // Adv. Mater. Res. 2014. V. 1065–1069. P. 1725–1731. https://doi.org/10.4028/www.scientific.net/AMR.1065-1069.1725
Применение полимерных соединений различной структуры в качестве реагентов модификаторов при флотации каменноугольной мелочи / В.Н. Петухов, А.С. Сирченко, А.В. Саблин, А.А. Юнаш // Башкир. хим. журн. 2007. Т. 14. № 2. С. 108–112.
Лайнер А.И. Производство глинозема. М.: Металлургиздат, 1961.
Щелочное обогащение зол, полученных от сжигания экибастузских углей / Л.Г. Романов, Е.Ф. Осипова, С.А. Щербан, Х.Н. Нурмагамбетов, Б.Ш. Джумбаев // Труды Ин-та металлургии и обогащения. 1967. Т. XXIII. С. 63–66.
Сажин В.С. Новые гидрохимические способы получения глинозема. Киев: Наукова думка, 1979.
Абрамов В.Я., Стельмакова Г.Д., Николаев И.В. Физико-химические основы комплексной переработки алюминиевого сырья (щелочные способы). М.: Металлургия, 1985.
Еремин Н.И., Благовещенская Г.С., Беленина Г.А. Переработка аргиллитов на глинозем // Цветная металлургия. 1963. № 8 (229). С. 32–35.
Диаграммы состояния силикатных систем: справ. Вып. 1: Двойные системы / Н.А. Торопов, В.П. Барзаковский, В.В. Лапин, Н.Н. Курцева. М.; Л.: Наука, 1965.
Справочник металлурга по цветным металлам. Производство глинозема / А.А. Аграновский, В.И. Берх, В.А. Кавина, М.В. Левин, А.Н. Ляпунов, А.Э. Монтвид, И.Н. Муниц, В.Н. Чернин. М.: Металлургия, 1970.
Guinea bauxite prices rise after coup, mines report no immediate impact. Сайт Reuters. [Электрон. ресурс.] https://www.reuters.com/business/guinea-bauxite-prices-rise-political-turmoil-2021-09-06/
Прайс-лист. ЗАО “Известняк”. [Электрон. ресурс.] http://izvest.org/KATALOG.FILES/price.php
ГОСТ 5100-85. Сода кальцинированная. М.: Изд-во стандартов, 1985. [Электрон. ресурс.] https://bashagroneftehimiya.promportal.su/goods/1756476/soda-kalcinirovannaya-gost-5100-85
Моснефтебизнес. [Электрон. ресурс.] http://toplivo777.ru/katalog/mazut
Дополнительные материалы отсутствуют.
Инструменты
Теплоэнергетика