Теплоэнергетика, 2022, № 4, стр. 64-69
Разработка технологий защитного оксидирования оборудования III контура реакторной установки БН-800
Б. А. Гусев a, *, А. А. Ефимов a, Л. Н. Москвин a, А. М. Алешин a, В. В. Мартынов a, А. Н. Максимова a
a Научно-исследовательский технологический институт им. А.П. Александрова
188540 Ленинградская обл., г. Сосновый Бор, Копорское шоссе, д. 72, Россия
* E-mail: gusev@niti.ru
Поступила в редакцию 07.07.2021
После доработки 06.08.2021
Принята к публикации 25.08.2021
- EDN: BSUNSM
- DOI: 10.1134/S0040363622040026
Аннотация
Представлены результаты разработки альтернативных технологий направленного защитного оксидирования рабочих поверхностей изготовленного из перлитных сталей оборудования испарительного и пароперегревательного модулей вертикального парогенератора (ПГ) Н-272 реакторной установки (РУ) БН-800, эксплуатируемого в условиях кислородно-аммиачного водно-химического режима. Формирование защитных оксидных пленок магнетита с заданными свойствами происходит при термолизе водных растворов комплексонатов и комплексов железа с различными лигандами в контакте с поверхностью сталей перлитного класса. Двухстадийные технологии направленного оксидирования основаны на применении растворов ацетата аммония или трилона Б. Установлены химические формы соединений железа в рабочих растворах для формирования качественных защитных пленок. На первой стадии образуются ассоциаты “оксидирующих” комплексов Fe(III) с атомами элементарного железа в активных центрах растворения металла. На второй стадии происходит термическое разложение ассоциатов с образованием зародышей кристаллов магнетита, сохраняющих возникшие в ассоциатах химические связи между атомами металла в кристаллической решетке стали и в растворенном комплексе Fe(III). Установлен интервал температур термического разложения ассоциатов первичных комплексов Fe(III) в контакте с атомами железа на поверхности стали для реализации процесса образования оксидных пленок. Обоснованы составы растворов и параметры процесса защитного оксидирования по ацетатной и комплексонной технологиям, установлены защитные свойства образующихся оксидных пленок. Разработана совмещенная технология комплексонного оксидирования с трансформацией отмывочного раствора в раствор направленного оксидирования, что позволяет резко снизить объемы образующихся жидких отходов. Даны рекомендации для выбора оптимального варианта технологии оксидирования с учетом теплотехнических характеристик оборудования.
Самопроизвольно образующиеся на поверхности сталей при коррозии оборудования в водных растворах оксидные покрытия не обладают необходимыми защитными свойствами, в первую очередь, из-за неоднородности их фазового состава, морфологии и структуры. В результате многочисленных исследований установлено, что наилучшие защитные свойства характерны для сформированных по специальным технологиям пленок магнетита, параметры кристаллической решетки которого наиболее близки параметрам решетки α-железа, составляющего основу перлитных сталей. К настоящему времени определились следующие направления формирования защитных оксидных пленок:
направленное оксидирование в процессе термолиза водных растворов комплексонатов и комплексов железа с различными лигандами при их контакте с поверхностью сталей для формирования пленки магнетита с заданными защитными свойствами [1–5];
частичное окисление поверхности металла солями неорганических кислот с последующей достройкой магнетитной пленки гидратированными ионами железа [6];
окисление поверхности металла на воздухе при повышенных температурах [7].
Опыт разработки технологий направленного оксидирования сталей на объектах тепловой и атомной энергетики и подходы к выбору составов оксидирующих растворов наиболее подробно обобщены и проанализированы в [1, 2]. Предпосылками этих обобщений явились более ранние публикации [3, 4]. Для успешного оксидирования необходимы наличие определенных химических форм железа в рабочем растворе и соответствующие температуры при реализации процесса. Оптимальными химическими формами железа для образования защитных оксидных пленок на поверхности сталей являются наноразмерные комплексы Fe(III) с оксилигандами начиная с аквагидроксокомплексов и кончая более прочными комплексами с анионами органических оксикислот, включая уксусную и этилендиаминтетрауксусную. Влияние температуры связано с тем, что процесс оксидирования является двустадийным. На первой стадии образуются ассоциаты “оксидирующих” комплексов Fe(III) с атомами элементарного железа в активных центрах растворения металла. На второй стадии происходит термическое разложение ассоциатов с образованием зародышей кристаллов магнетита, сохраняющих возникшие в ассоциатах химические связи между атомами металла в кристаллической решетке стали и в растворенном комплексе Fe(III). Поэтому для протекания процесса образования оксидных пленок необходимо создать условия для термического разложения ассоциатов первичных комплексов Fe(III) в контакте с атомами железа на поверхности стали.
Относительно антикоррозионных защитных свойств из известных оксидирующих растворов наиболее предпочтительными являются ацетатные и комплексонатные растворы. Сведения об оксидных пленках на поверхности стали, образующихся при контакте с этими оксидирующими агентами, приведены в табл. 1. Для образования этих пленок необходимо выполнение условий, указанных в табл. 2.
Таблица 1.
Морфология и фазовый состав защитных пленок на поверхности сталей при оксидировании различными агентами [5]
Оксидирующий агент | t, °С | Морфология пленки | ||
---|---|---|---|---|
слойность | фазовый состав/толщина слоя, мкм | |||
топотаксический | эпитаксический | |||
Ацетат аммония (NH4Ac) | 180–220 | Двухслойная | Fe3O4/3–5 | Fe3O4/5–10 |
Трилон Б (Na2H2Y) | 270–295 | Монослойная | Fe3O4/3–5 | Отсутствует |
Таблица 2.
Оптимальные условия образования оксидных пленок на поверхности стали [5]
Оксидирующий реагент | С, мг/дм3 | t, °С | τ, ч |
---|---|---|---|
Ацетат аммония (NH4Ac) | 5000–7000 | 180–220 | 2.5–5.0 |
Комплексон (Na2H2Y) | 300–5000 | 250–295 | 3.0–5.0 |
Выбор реагента для осуществления процесса оксидирования на конкретном объекте определяется возможностями поддержания требуемой температуры обрабатываемых поверхностей. Оксидные пленки, образовавшиеся после химической промывки с использованием трилона Б (комплексона III), обладают лучшими защитными свойствами.
Третий контур РУ БН-800 эксплуатируется при кислородно-аммиачном водно-химическом режиме, коррекцию которого осуществляют путем дозирования в теплоноситель раствора NH4OH и газообразного кислорода. В контуре остановленной РУ допускается поддержание температуры теплоносителя примерно 250°С в течение 3–5 ч. В этом случае возможно реализовать одноэтапную технологию, совмещающую химическую промывку и оксидирование поверхности ПГ, что сократит продолжительность процесса, позволит избежать промежуточной водной промывки контура и существенно снизит количество образующихся отходов.
Для проведения лабораторных исследований по оксидированию поверхности парогенератора РУ БН-800 использовали образцы сталей 10Х2М-ВД и 12Х1МФ в состоянии поставки в виде дисков диаметром 20 мм, толщиной 2 мм и стали 15ГС в виде фрагмента трубы размером 50 × × 20 × 3 мм. Стали 10Х2М-ВД и 12Х1МФ применяются в качестве конструкционных материалов теплообменных трубок (ТОТ) испарительного и пароперегревательного модулей и горячих коллекторов, сталь 15ГС – в качестве материала коллекторов питательной воды парогенератора Н-272. В контрольных опытах исследования проводили на образцах, вырезанных из теплообменных трубок испарительного модуля (ИТ) диаметром 15.5 × × 2.5 мм, длиной 10 мм и пароперегревательного модуля (ППТ) парогенератора диаметром 16 × 3 мм, длиной 10 мм.
Для стандартизации исходного состояния поверхности перед проведением оксидирования образцы подвергали химической промывке раствором трилона Б [4]. Исследования выполняли в растворе, имитирующем среду III контура ПГ Н-272. Эксперименты проводили в автоклавах объемом 68 см3, изготовленных из стали Х18Н10Т, заполненных раствором трилона Б (50 см3), в которые на держателе из нержавеющей стали помещали два-три исследуемых образца. Автоклавы устанавливали в термостатируемый сушильный шкаф и нагревали до необходимой температуры.
Для химической промывки использовали раствор трилона Б (5 г/дм3) при рН ≈ 9.8 и ${{С}_{{{{{\text{O}}}_{{\text{2}}}}}}}$ < < 0.5 мг/дм3 (здесь ${{С}_{{{{{\text{O}}}_{{\text{2}}}}}}}$ – концентрация кислорода). Промывку продолжали в течение 5–18 ч при температуре 150°С. Результаты коррозионных испытаний образцов стали в состоянии поставки после химической промывки приведены в табл. 3.
Таблица 3.
Результаты химической промывки образцов стали в состоянии поставки
Сталь | τ, ч | G1, г | G2, г | g, г/(м2 · ч) |
---|---|---|---|---|
10Х2М-ВД | 5 | 4.5386 | 4.5374 | 0.0111 |
12Х1МФ | 3.9335 | 3.9332 | 0.0028 | |
10Х2М-ВД | 18 | 4.5377 | 4.5374 | 0.0028 |
12Х1МФ | 3.9157 | 3.9147 | 0.0093 |
Для сталей в состоянии поставки увеличение продолжительности химической промывки растворами на основе трилона Б до 18 ч не привело к заметным изменениям скорости коррозии. Предположение о том, что длительное воздействие промывочного раствора на конструкционные материалы вызовет повышение скорости коррозии оборудования, не подтвердилось.
После химической промывки на поверхности образцов формировался слой отложений в виде тонкой пленки темно-серого цвета и легко удаляемого налета тонкодисперсных соединений железа черного цвета. По результатам визуального осмотра с использованием оптического микроскопа МПБ-2 при 24-кратном увеличении было установлено, что сплошной слой пленки на поверхности образцов отсутствует.
Образцы, обработанные в растворе трилона Б, в дальнейшем были использованы для отработки технологий оксидирования конструкционных материалов в ацетатном и комплексонатном растворах. Интервал температур при ацетатной технологии составлял 180–200°С [1]. Обработка поверхности продолжалась 3–5 ч, ${{С}_{{{{{\text{O}}}_{{\text{2}}}}}}}$ < 0.5 мг/дм3. При выполнении исследований использовали растворы NH4Ac (5 г/дм3), приготовленные на базе растворов HNO3 концентрацией 10–3 моль/дм3 (рН ≈ ≈ 6.0) и 5 × 10–3 моль/дм3 (рН ≈ 5.8).
В качестве критериев работоспособности разрабатываемых технологий использовали данные металлографического анализа и результаты коррозионных испытаний оксидированных образцов.
В табл. 4 приведены исходные данные для выбора оптимальных химико-технологических параметров по отработке ацетатной технологии оксидирования. В экспериментах варьировались составы растворов, продолжительность и температура обработки.
Таблица 4.
Исходные данные для выбора химико-технологических параметров ацетатной технологии оксидирования
t, °С | τ, ч | Внешний вид образцов |
---|---|---|
180 | 5 | Образцы сталей 12Х1МФ, 10Х2М-ВД и 15ГС покрыты полупрозрачной пленкой черного цвета |
200 | 4 | |
220 | 5 | |
180 | 3 | Образцы сталей 12Х1МФ, 10Х2М-ВД покрыты плотной пленкой черного цвета. Пленка на поверхности образца стали 15ГС не сплошная, есть пятна чистого металла |
Помимо приведенных в табл. 4 качественных характеристик оксидных пленок образцов были получены микрофотографии и определена структура ацетатных оксидных пленок, образовавшихся на поверхности сталей (рис. 1). Анализ изображений показывает, что на поверхности всех образцов сформировалась сплошная оксидная пленка толщиной от 1 до 5 мкм. В табл. 5 приведены результаты коррозионных испытаний образцов конструкционных материалов после их оксидирования раствором NH4Ac (5 г/дм3) на базе раствора HNO3 (10–3 моль/дм3) в течение 150 ч при температуре 200°С и ${{С}_{{{{{\text{O}}}_{{\text{2}}}}}}}$ ≈ 8 мг/дм3. Полученные данные показывают, что после оксидирования растворами ацетата аммония скорость коррозии сталей 10Х2М-ВД, 12Х1МФ и 15ГС меньше заложенной в проект и составляющей 1 мм за 30 лет (0.03 г/(м2 · ч), а скорость коррозии неоксидированных образцов выше проектной.
Рис. 1.
Оксидная пленка на поверхности образца стали 10Х2М-ВД (а), 12Х1МФ (б), 15ГС (в) после ацетатной обработки, увеличение 2000 крат
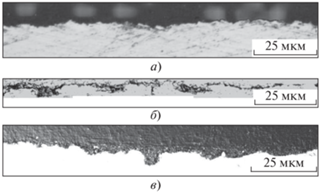
Таблица 5.
Результаты коррозионных испытаний о-бразцов конструкционных материалов
Марка стали | G1, г | G2, г | g, г/(м2 · ч) |
---|---|---|---|
Оксидированные образцы | |||
10Х2М-ВД | 4.2219 | 4.2216 | 0.0026 |
4.7756 | 4.7758 | 0.0019 | |
12Х1МФ | 4.7435 | 4.7419 | 0.0141 |
4.0395 | 4.0354 | 0.0363 | |
15ГС | 23.3923 | 23.3840 | 0.0235 |
24.2573 | 24.2565 | 0.0023 | |
Неоксидированные образцы | |||
10Х2М-ВД | 4.8497 | 4.8449 | 0.0424 |
12Х1МФ | 4.1456 | 4.1421 | 0.0309 |
15ГС | 24.6978 | 24.6444 | 0.1515 |
По результатам проведенных исследований были установлены оптимальные значения химико-технологических параметров ацетатной технологии оксидирования: t = 200°С, τ = 4–5 ч. К числу достоинств ацетатной технологии помимо вполне удовлетворительных антикоррозионных свойств образующейся на поверхности сталей оксидной пленки относится рабочая температура, которая легко поддерживается штатными средствами РУ БН-800. Но в то же время, как уже отмечалось выше, необходима водная отмывка контура после комплексонной химической промывки от продуктов коррозии. Поэтому наряду с ацетатной технологией оксидирования была рассмотрена возможность адаптировать к условиям РУ БН-800 комплексонную технологию оксидирования, лимитирующим параметром которой является температурный диапазон осуществления процесса 250–295°С. Главной задачей при разработке такой технологии являлось обоснование возможности оксидирования конструкционных материалов ПГ Н-272 при температуре 250°С – максимальной температуре, которую могут обеспечить штатные средства расхоложенной РУ БН-800. Для испытаний с учетом имеющегося опыта комплексонного оксидирования при более высоких температурах [1] были выбраны следующие растворы: трилон Б (5 г/дм3) + N2H4 (2 г/дм3) и трилон Б (10 г/дм3) + N2H4 (2 г/дм3). Оксидирование проводили при рН = 9.8–10.2, t = 250°С, продолжительность процесса составляла 5 ч. В табл. 6 приведены результаты коррозионных испытаний перлитных сталей при t = 200°C, ${{С}_{{{{{\text{O}}}_{{\text{2}}}}}}}$ < 0.5 мг/дм3 после комплексонного оксидирования. На рис. 2 показан характерный вид оксидной пленки для образца стали 12Х1МФ после комплексонной обработки.
Таблица 6.
Результаты коррозионных испытаний о-ксидированных сталей
Марка стали | τ, ч | G1, г | G2, г | g, г/(м2 · ч) |
---|---|---|---|---|
15ГС | 150 | 24.0407 | 24.0306 | Менее 0.002 |
12Х1МФ | 4.0290 | 4.0266 | 0.0241 | |
15ГС | 500 | 22.8048 | 22.8039 | 0.0008 |
24.4454 | 24.4395 | 0.0050 | ||
10Х2М-ВД | 500 | 4.1493 | 4.1451 | 0.0012 |
4.0089 | 4.0045 | 0.0012 | ||
12Х1МФ | 500 | 4.7758 | 4.7712 | 0.0013 |
4.8053 | 4.8013 | 0.0011 |
Рис. 2.
Оксидная пленка на поверхности образца стали 12Х1МФ после комплексонной обработки, увеличение 500 крат

Данные, представленные в табл. 6, свидетельствуют о том, что после комплексонного оксидирования скорость коррозии конструкционных материалов ниже проектных значений.
Результаты применения комплексонной технологии пассивации показали, что, несмотря на пониженную температуру обработки (t = 250°С), на рабочей поверхности образцов испарительного и пароперегревательного модулей ПГ образуется качественная защитная оксидная пленка из магнетита. Это подтверждают изображение поперечного шлифа на рис. 3 и данные коррозионных испытаний реальных образцов при t = 200°С, τ = = 150 ч, ${{С}_{{{{{\text{O}}}_{{\text{2}}}}}}}$ < 0.5 мг/дм3, вырезанных из различных по высоте участков ТОТ после комплексонной пассивации (табл. 7).
Рис. 3.
Оксидная пленка на поверхности образца ИТ после комплексонной обработки, увеличение 2000 крат

Таблица 7.
Результаты коррозионных испытаний о-бразцов ТОТ после комплексонной пассивации
Образец | G1, г | G2, г | g, г/(м2 · ч) |
---|---|---|---|
ИТ | 10.1378 | 10.1335 | 0.0312 |
10.1581 | 10.1555 | 0.0189 | |
8.8446 | 8.8446 | Менее 0.002 | |
8.9101 | 8.9102 | Менее 0.002 | |
ППТ | 9.0129 | 9.0091 | 0.0276 |
8.8396 | 8.8383 | 0.0094 | |
10.2105 | 10.2107 | Менее 0.002 | |
8.9636 | 8.9636 | Менее 0.002 |
Как следует из табл. 7, скорость коррозии образцов ТОТ испарительного и пароперегревательного модулей, обработанных растворами трилона Б, находится на уровне и ниже проектных значений.
Полученные данные по коррозионной стойкости защитных оксидных пленок послужили основанием для последующей проверки возможности реализации совмещенной технологии комплексонного оксидирования. Для этого после химической отмывки образцов раствором трилона Б исключается этап водной промывки, а промывочный раствор трансформируется в оксидирующий путем дополнительного ввода концентрата раствора трилона Б до достижения установленной ранее концентрации. Для имитации подобного процесса в лабораторных условиях в автоклав дополнительно вводили 5 см3 концентрата промывочного раствора, состоявшего из трилона Б (50 г/дм3) и NH4OH, и проводили оксидирование образцов при t = 250°С, рН ≈ 9.6, τ = 150 ч и ${{С}_{{{{{\text{O}}}_{{\text{2}}}}}}}$ < < 5 мг/дм3. Результаты экспериментов представленные в табл. 8.
Таблица 8.
Результаты коррозионных испытаний о-бразцов ТОТ после химической промывки, совмещенной с пассивацией
Образец | G1, г | G2, г | g, г/(м2 · ч) |
---|---|---|---|
ИТ | 10.1325 | 10.1317 | 0.0058 |
10.0773 | 10.0770 | 0.0022 | |
10.1561 | 10.1540 | 0.0152 | |
ППТ | 9.0037 | 9.0033 | 0.0029 |
8.7398 | 8.7394 | 0.0029 | |
9.2158 | 9.2153 | 0.0036 |
Данные табл. 8 подтверждают возможность реализации совмещенной технологии оксидирования, поскольку для всех образцов после оксидирования скорость коррозии ниже проектного значения. Использование совмещенной технологии промывки и пассивации растворами на основе трилона Б позволяет резко снизить объемы образующихся жидких отходов.
ВЫВОДЫ
1. Предложены два варианта технологии пассивации рабочих поверхностей оборудования III контура реакторной установки БН-800, изготовленного из перлитных сталей:
ацетатная технология растворами NH4Ac (5 г/дм3) + HNO3 (5 × 10–3 моль/дм3) при рН ≈ 6.0, температуре 200°С, продолжительности 3–5 ч;
комплексонная технология раствором трилона Б (5 г/дм3) при рН ≈ 10.0, температуре 250°С, продолжительности 3–5 ч.
Обе технологии обеспечивают снижение скорости коррозии на порядок относительно проектных значений – 0.003 г/(м2 · ч) вместо допустимых 0.03 г/(м2 · ч).
2. Ацетатная технология более привлекательна, поскольку более проста в обеспечении необходимого температурного диапазона осуществления процесса, комплексонная имеет преимущество из-за минимизации объема жидких отходов.
3. При принятии окончательного решения о выборе того или иного варианта технологии необходимо провести экономические расчеты при сопоставлении стоимости реагентов и затрат на переработку отходов.
Список литературы
Маргулова Т.Х. Применение комплексонов в теплоэнергетике. М.: Энергоатомиздат, 1986.
Пыхтеев О.Ю., Ефимов А.А., Москвин Л.Н. Направленное регулирование структуры и защитных свойств оксидных пленок, образующихся на поверхности сталей при контакте с водными средами // Технологии обеспечения жизненного цикла ядерных энергетических установок: Период. рецензируемый науч.-техн. сб. 2017. № 3 (9). С. 26–43.
Механизм термохимического оксидирования сталей в условиях комплексонного режима / А.В. Лавров, А.А. Ефимов, Л.Н. Москвин, Б.А. Гусев // Теплоэнергетика. 1994. № 7. С. 14–19.
Ефимов А.А., Москвин Л.Н. Совершенствование технологий химических промывок и оксидирования внутренних поверхностей контуров энергоблоков // Теплоэнергетика. 2009. № 7. С. 7–12.
Химические проблемы атомной энергетики. Т. 3: Химические технологии продления ресурса и повышения радиационной безопасности ЯЭУ. Коррозионные процессы в контурах ЯЭУ / Л.Н. Москвин, А.А. Ефимов, О.Ю. Пыхтеев, Б.А. Гусев; под ред. Л.Н. Москвина. СПб.: ВВМ, 2016.
Влияние способа обработки на защитные свойства оксидных покрытий / Б.К. Кутычкин, В.В. Прозоров, В.И. Павленко, Ю.И. Слепоконь // Вестник Белгор. ГТУ. 2012. № 4. С. 152–153.
Юркинский В.П., Фирсова Е.Г., Оковитый В.В. Влияние способа оксидирования сталей 20 и 12Х18Н10Т на пористость оксидных покрытий // Науч.-техн. ведомости Санкт-Петербург. гос. политехн. ун-та. Металлургия и материаловедение. 2013. Вып. 2. № 171. С. 133–136.
Дополнительные материалы отсутствуют.
Инструменты
Теплоэнергетика