Теплоэнергетика, 2022, № 4, стр. 54-63
Опыт химических промывок от отложений испарителей парогенераторов “натрий – вода” реакторной установки БН-600 Белоярской АЭС
В. Ф. Тяпков a, В. Б. Смыков b, *, К. Г. Легких b
a Всероссийский научно-исследовательский институт по эксплуатации атомных электростанций
109507 г. Москва, Ферганская ул., д. 25, Россия
b Физико-энергетический институт им. А.И. Лейпунского
249033 Калужская обл., г. Обнинск, пл. Бондаренко, д. 1, Россия
* E-mail: smykov@ippe.ru
Поступила в редакцию 15.06.2021
После доработки 19.07.2021
Принята к публикации 25.08.2021
- EDN: MBHHXB
- DOI: 10.1134/S0040363622040063
Аннотация
При эксплуатации парогенераторов любых типов происходит накопление отложений на поверхности конструкционных материалов. Эти отложения состоят из продуктов коррозии, различных нелетучих солей и оснований, органических примесей и других соединений. Основу химического состава этих отложений составляют оксиды железа, пропитанные водорастворимыми солевыми примесями. Данная среда является коррозионно-агрессивной и в конечном итоге может вызывать локальную коррозию конструкционного материала. В результате этого процесса снижаются расходы теплоносителя, уменьшается теплопередача, происходит локальная коррозия под отложениями и, как следствие, возникает течь парогенератора. Решение таких проблем сводится к промывке парогенератора моющим раствором, содержащим химически активные компоненты. Учитывая большой опыт реализации аналогичных мероприятий в разных отраслях промышленности, стоит выделить технологию эксплуатационных химических промывок (ЭХП) парогенераторов типа “натрий – вода”, которые имеют ряд особенностей как в эксплуатационном режиме, так и при проведении ЭХП, связанных с недопущением межконтурной разгерметизации. По этой причине технология проведения ЭХП требует непрерывного мониторинга процесса. За период эксплуатации реакторной установки (РУ) БН-600 испарители парогенераторов подвергали регулярным эксплуатационным химическим промывкам. Химические промывки проводятся с циркулирующим натрием во II контуре для непрерывного контроля межконтурной плотности промываемых испарителей. Применяемая технология химических промывок и состав химических растворов многократно показали свою химическую эффективность и безопасность. Обобщен опыт эксплуатации парогенератора реакторной установки БН-600. Сформулированы рекомендации по оптимизации контроля основных параметров ЭХП, on-line мониторингу процесса, изменению состава компонентов моющего раствора, а также способам его переработки.
Парогенераторы любых реакторных установок, работающих в водопаровой среде, подвержены накоплению продуктов коррозии, что приводит к снижению теплопередачи из-за отложений на поверхности труб и, как следствие, невозможности достижения расчетной выходной мощности. Однако для парогенераторов типа “натрий – вода” это не самый критичный исход. Гораздо более опасным является развитие локальной коррозии стали под отложениями вплоть до сквозного поражения металла труб и последующего взаимодействия натрия с водой – аварийной ситуации, требующей немедленной остановки реактора на длительное время. Например, на РУ “Феникс” в 1983 г. произошла разгерметизация двух модулей парогенератора “натрий – вода”. Время работы модулей составляло 79 700 ч без химических промывок, в номинальном режиме – 52 000 ч. В результате проведенных исследований было показано, что причиной данного инцидента являлось загрязнение отложениями подогревателя-испарителя [1]. Последующую химическую промывку проводили с помощью “жесткого” состава химического раствора (плавиковой кислотой с ингибитором).
Аналогичная ситуация произошла на РУ БН-350 в 1989 г. Парогенераторы № 4, 5 микромодульной конструкции “Надежность” также эксплуатировались без промывок и вышли из строя вследствие сквозных коррозионных разрушений в двух испарительных модулях [2]. Поэтому проведение химических промывок является необходимой технологией для обеспечения безаварийного ресурса любых парогенераторов АЭС.
Химические промывки всего парогенератора и отдельных частей парогенерирующих поверхностей проводятся на всех АЭС мира. В [3] отмечена высокая стоимость отмывки парогенераторов от отложений (0.5–5.0 млн дол. США). Материалы о разработках технологий и опыте химических промывок парогенераторов АЭС регулярно публикуются в научных журналах, в виде докладов представляются на научных конференциях, например [4]. В отечественной научно-технической литературе опыт проведения химических промывок парогенераторов типа “натрий – вода” на РУ БН-600 и БН-350 был отражен в статье, опубликованной 25 лет назад [2]. За прошедшие годы технология химических промывок на РУ БН-600 была усовершенствована. С пуском РУ БН-800 в 2015 г. неизбежно возникли вопросы о необходимости проведения ЭХП, составе промывочных растворов и химическом контроле их качества, пассивации, утилизации отработанных растворов и т.д.
ОПЫТ ПРОВЕДЕНИЯ ХИМИЧЕСКИХ ПРОМЫВОК ИСПАРИТЕЛЕЙ ПРЯМОТОЧНОГО ПАРОГЕНЕРАТОРА ПГН-200М РЕАКТОРНОЙ УСТАНОВКИ БН-600
За период эксплуатации РУ БН-600 с 1981 по 2021 г. все испарители парогенераторов подвергали регулярным химическим промывкам с периодичностью 1 раз в 3–4 года. Отложения в прямоточных парогенераторах типа “натрий – вода”, работающих в составе энергоблока с РУ БН-600, включают в себя, главным образом, продукты коррозии металлов конденсатно-питательного тракта, а также различные нелетучие соли и основания, продукты деструкции ионообменных материалов и органических примесей и другие соединения. Основу химического состава этих отложений составляют оксиды железа, пропитанные водорастворимыми солевыми примесями. Данная локальная химическая среда представляет собой коррозионно-агрессивный электролит с депассиваторами, который может вызывать локальную коррозию конструкционного материала трубного пучка, изготовленного из низколегированной ферритно-перлитной стали 10Х2М. Этим обусловливается необходимость проведения периодических химических промывок испарителей парогенераторов от накопленных за межпромывочный период эксплуатации отложений.
При работе парогенераторов на мощности межпромывочный период сначала составлял 15 000–20 000 ч, а в последние 10 лет был повышен до 25 000–30 000 ч. На энергоблоке № 3 Белоярской АЭС химические промывки проводятся при циркуляции натрия во II контуре при непрерывном контроле межконтурной плотности промываемых испарителей. Опыт проведения химических промывок РУ БН-600 показал, что за 40 лет отсутствовали случаи нарушения межконтурной плотности испарителей при реализации работ данного вида.
При систематических обследованиях состояния парогенерирующих поверхностей парогенератора ПГН-200М было установлено, что практически все примеси продуктов коррозии (более 95% по массе) и солей водного теплоносителя из III контура высаждаются в модулях испарителей. Причем “пик” удельной загрязненности находится в зоне перегрева пара, в которой развивается локальная (язвенная) коррозия металла труб испарителя. Для предотвращения язвенной коррозии, вызываемой присутствием меди в отложениях, межпромывочный период эксплуатации парогенератора ПГН-200М был снижен до 15 000–20 000 ч. Данное ограничение оправдало себя на практике. В основном пароперегревателе (ОП) и промежуточном пароперегревателе (ПП) образуется мало отложений продуктов коррозии. Они не вызывают опасений развития локальной коррозии нержавеющих труб модулей ОП и ПП, которые поэтому не подвергаются химическим промывкам.
На протяжении всего опыта эксплуатации РУ БН-600 при химических промывках парогенератора использовали три состава моющего раствора, которые определялись особенностями конструкционных материалов. Первые эксплуатационные промывки в 80-х годах прошлого века проводили в два этапа. На первом этапе промывку осуществляли раствором на основе соли этилендиаминтетрауксусной кислоты (ЭДТК) с ингибитором коррозии при рН 9.0 и температуре 165–180°С. Концентрированный моющий раствор (15–20 м3) быстро (в течение 0.5 ч) вводили в деаэратор контура промывки, заполненного водой, далее производилась циркуляция раствора до его срабатывания. После стабилизации значений контролируемых показателей (содержания железа, меди и водорода, рН, концентрации свободной ЭДТК, Red/Ox-потенциала) раствор дренировали. Промывочный контур заполняли обессоленной водой, промывали, после чего снова дренировали.
Промывку (пассивацию) на втором этапе осуществляли по замкнутому контуру “питательный электронасос (ПЭН) – подогреватель высокого давления (ПВД) – испарительные модули – деаэратор”. Для пассивации использовали перекись водорода с последующим добавлением аммиака. Однако применение перекиси водорода оказалось малоэффективным вследствие ее быстрого термического разложения. Эффективность удаления меди тоже оказалась низкой из-за недостаточной “медеeмкости” моющей композиции, а также низкой стойкости медно-аммиачного комплекса с ЭДТК, что приводило к повторному высаждению меди в контуре промывки.
Такую технологию использовали до 1985 г., после чего она была заменена на промывку в три этапа для повышения эффективности удаления меди из отложений. Кроме того, был применен постепенный ввод концентрированных растворов в контур промывки (на всас ПЭН) с расходом 5 м3/ч, что позволило обеспечить постоянный концентрационный “напор” моющих реагентов при растворении отложений. В соответствии с разработанным в Физико-энергетическом институте им. А.И. Лейпунского составом моющего раствора (ацетат аммония с нитритом натрия) был организован первый этап для удаления медьсодержащих отложений при рН 10.5–11.0. На втором этапе производили отмывку от отложений магнетита с помощью раствора, содержащего аммонийную соль ЭДТК и гидразин, при рН = 9.0 и на третьем этапе – доотмывку от остатков меди под отложениями и одновременно пассивацию отмытых поверхностей раствором первого этапа при пониженной концентрации реагентов. Продолжительность каждого этапа составляла 5–6 ч. Данная технология была многократно успешно применена на РУ БН-600 и доказала свою эффективность по раздельному удалению магнетита и соединений меди и предотвращению развития локальной коррозии стали 10Х2М под накапливающимися отложениями. Общее количество удаленной меди выросло с 5–7 до 20–35 кг за одну промывку, а магнетита – с 200–300 до 600–800 кг. Опыт применения данной технологии показал, что на первом этапе эффективность удаления меди из отложений составляла 90% и более, прекратилось повторное высаждение меди из раствора, поэтому впоследствии от проведения третьего этапа отказались. Схема химических промывок показана на рис. 1.
Рис. 1.
Схема химической промывки испарителей парогенератора ПГН-200М. 1 – модуль испарителя; 2 – деаэратор; 3 – ПЭН; 4 – ПВД; 5 – байпас ПВД; 6 – насос-дозатор реагентов; 7 – бак раствора ЭДТК; 8 – бак растворов ацетата аммония и нитрита натрия; 9 – подача обессоленной воды или греющего пара; 10 – сброс промывочного раствора в бак-нейтрализатор; 11 – временные трубопроводы; 12 – подача промывочных растворов в испарители соседних петель; 13 – сброс газов из деаэратора; 14 – теплообменник выпара деаэратора; 15, 16 – растопочный сепаратор стороны А и Б испарителя петли; 17 – насос дозировки исходного промывочного раствора; 18 – подача исходного промывочного раствора в контур промывки испарителя
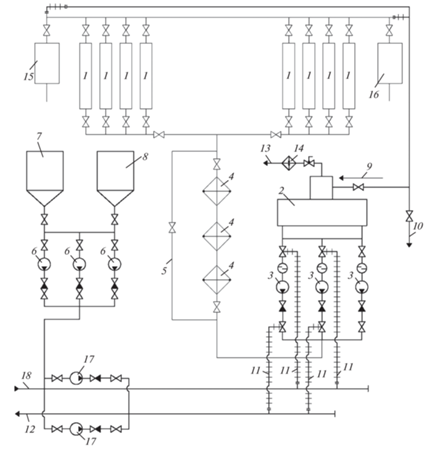
В 2003–2005 гг. была произведена замена медьсодержащих конструкционных материалов в III контуре (подогреватель низкого давления) на нержавеющую сталь 08Х18Н10Т, по этой причине в водяном контуре практически исчез источник поступления меди в парогенератор. Применение новых конструкционных материалов потребовало изменения состава моющих растворов, поэтому последние промывки испарителей проводились в один этап. При этом для растворения отложений магнетита использовали раствор на основе аммонийной соли ЭДТК и гидразина, для последующей пассивации отмытых поверхностей – раствор гидразина. Схема циркуляции моющего раствора в контуре промывки осталась той же.
Исходя из опыта эксплуатации РУ БН-600, можно провести сравнительный анализ эффективности двух отработанных технологий. Для исследования использовали объем данных, содержащихся в актах о проведении эксплуатационных промывок модулей испарителей парогенератора с 1981 по 2021 г. Основные показатели эффективности промывок сопоставляли с изменением состава моющих растворов и методологией проведения процесса.
В результате анализа данных было выявлено, что масса продуктов коррозии G, удаленных по технологии промывки в один этап, значительно превышает аналогичный показатель, достигнутый при проведении промывок в два и три этапа (рис. 2). Следует отметить, что для 2005–2021 гг. характерен более длительный межпромывочный период в сравнении с промывками в 1981–2004 гг.
Рис. 2.
Эффективность химических эксплуатационных промывок 4-й (а), 5-й (б), 6-й (в) петель испарителей парогенератора РУ БН-600
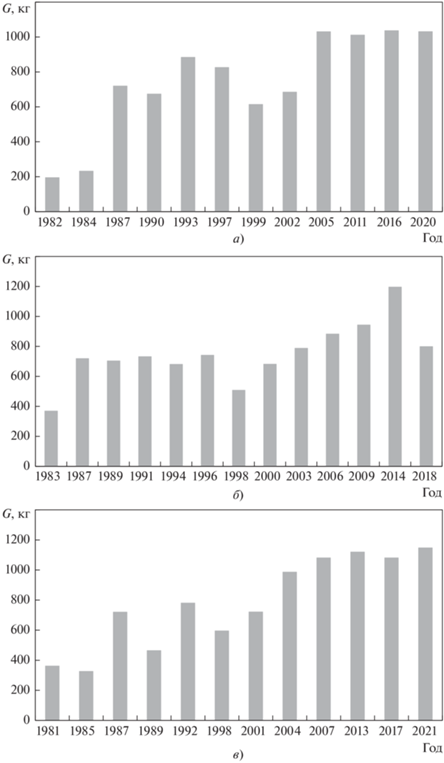
Анализ скоростей коррозии при промывках испарительных модулей (по выделению водорода в раствор) показывает, что повышение эффективности промывки не увеличивает агрессивное воздействие на конструкционные материалы (рис. 3). Однако утверждение о том, что присутствие водорода в растворе обусловлено только коррозионными процессами, не корректно, так как гидразин также является источником водорода при термическом разложении. Исходя из обработанного массива данных, можно сделать вывод, что при эксплуатационной промывке в один этап обеспечивается эффективная очистка модулей испарителей и при этом не повышаются скорость коррозии и износ конструкционного материала.
ОПТИМИЗАЦИЯ ХИМИЧЕСКОГО КОНТРОЛЯ ПРОЦЕССА ПРОМЫВКИ
При проведении химической промывки испарителей возрастает нагрузка на персонал по выполнению химических анализов, требуемых для оперативного управления процессом. Отбор проб для определения пяти-шести показателей осуществляется 1 раз в 1 ч. Кроме того, прохождение раствора по пробоотборной линии и выполнение последующего анализа происходят в течение длительного времени, что снижает оперативность контроля.
По мнению авторов, продолжительность процесса химического контроля промывки может быть существенно сокращена для оперативного управления ею. Например, как это следует из практических данных на рис. 4, различие между концентрациями железа в растворе на входе в испаритель и выходе из него составляет 10–15%, редко 20%, особенно во второй половине промывки. В то же время хорошо известно, что погрешность выполнения химических анализов на содержание общего железа и ЭДТК составляет 10%. Поэтому нет смысла осуществлять химический анализ сразу в двух точках контура, достаточно в одной, например в питательной воде. Таким образом, объем работы самого трудоемкого химического анализа снижается в 2 раза. Остальные показатели также нужны, но они не являются оперативно необходимыми и могут быть выполнены позднее. Кроме того, нет необходимости выполнять химический анализ на содержание меди в промывочном растворе, так как значения этого показателя стабильно ниже предела чувствительности метода анализа.
Рис. 4.
Зависимость концентрации железа CFe в растворе на входе в испаритель (1) и выходе из него (2) от продолжительности ЭХП τ
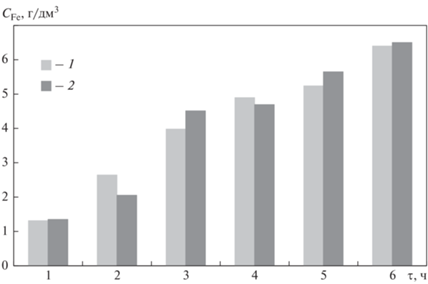
Применение гидразина в моющем растворе на базе ЭДТК требуется для перевода закомплексованного Fe+3 в Fe+2, что на треть повышает железоемкость раствора и экономит расход ЭДТК [5]. Общее стехиометрическое количество гидразина для осуществления этой реакции в реальных условиях химической промывки (во всем объеме раствора в контуре) составляет примерно 70–80 кг. Но с исходным концентрированным промывочным раствором в контур промывки вводится (и затрачивается), как правило, 500–600 кг гидразина. Этот избыток необходим для поддержания восстановительной среды и “концентрационного напора” при восстановлении железа в растворе. Таким образом, эффективность использования гидразина по его прямому назначению низкая (около 12–15%). Избыточный гидразин разлагается с образованием аммиака и азота (и, может быть, водорода), а также выводится из контура неиспользованным после окончания промывки (примерно 100–150 кг). Гидразин также используется на этапе пассивации, причем в сопоставимых количествах (1.3 м3 концентрированного раствора для промывки и 1.0 м3 для пассивации).
В связи с тем что гидразин является канцерогеном, по-видимому, имеет смысл найти ему замену. Например, гидроксиламин NH2OH является щелочным восстановителем в водных растворах, хотя его восстановительные свойства слабее, чем свойства гидразина. Он более термостоек, а его производные, например диэтилгидроксиламин, давно применяются в теплоэнергетике в качестве корректирующей добавки в питательную воду для пассивации парогенерирующих поверхностей котлов докритического давления [6]. Конечно, гидроксиламином и его производными поиск не должен ограничиваться. Решение данного вопроса требует химико-аналитических и коррозионных исследований. Но рано или поздно от применения гидразина придется отказаться.
КОСВЕННЫЕ ПОКАЗАТЕЛИ ЭТАПОВ ПРОТЕКАНИЯ ПРОЦЕССА ЭКСПЛУАТАЦИОННОЙ ПРОМЫВКИ
Любые отложения на поверхностях конструкционных материалов всегда имеют неоднородный характер. Поэтому продолжительность растворения отложений будет различной в зависимости от их толщины. После начала этапа растворения отложений по всей длине трубы неизбежно будут протекать параллельные процессы растворения более плотных отложений, коррозии отмытых поверхностей и сорбционной пассивации уже очищенной поверхности. Все эти стадии сопровождаются увеличением или уменьшением концентрации выделяющегося водорода.
На рис. 5 показана условная схема химической промывки испарителя РУ БН-600 и ее контроля по концентрации коррозионного водорода ${{С}_{{{{{\text{Н}}}_{{\text{2}}}}}}}.$ Данный параметр легко отслеживать в on-line режиме, что позволяет сделать обоснованный вывод о продолжении или окончании эксплуатационной химической промывки. Наличие третьего пика содержания водорода в растворе во времени, по мнению авторов, свидетельствует об окончании отмывки от отложений на участке выхода из испарителя, т.е. о максимально возможном растворении отложений.
На рис. 6 показана зависимость содержания водорода в III контуре РУ БН-600 от времени проведения следующей химической эксплуатационной промывки. Первый экстремум соответствует окончанию стадии растворения тонких отложений и пассивации очищенной поверхности. Повторный рост концентрации водорода свидетельствует о следующем этапе растворения более плотных отложений, но процесс промывки завершается, так и не достигнув своей финишной стадии. Соответственно, если процесс не доведен до конца, то испаритель остался загрязненным.
Предложенная схема оперативного химического контроля процесса отмывки испарителя по концентрации растворенного водорода обеспечивает только качественную оценку химической промывки. Для разработки количественных рекомендаций необходимы непрерывные измерения в ходе предстоящих промывок испарителей. Хотя выделение коррозионного водорода служит косвенным показателем промывки, но оперативность его получения позволяет при накоплении опыта его интерпретации определять степень отмывки испарителя от отложений продуктов коррозии. Анализ на водород в растворе является более быстрым и значительно менее трудоемким, чем анализ на железо.
ВЫСОКОТЕМПЕРАТУРНАЯ ПАССИВАЦИЯ ПАРОГЕНЕРАТОРА ПОСЛЕ ХИМИЧЕСКОЙ ПРОМЫВКИ
После окончания химической промывки практически вся внутренняя поверхность труб находится в коррозионно-активном состоянии. Для предотвращения усиленной коррозии труб испарителя на РУ БН-600 в последние годы применяется пассивация отмытых поверхностей щелочным раствором гидразина при температуре 160–165°С при его циркуляции по замкнутому контуру. Процесс заканчивается при стабилизации содержания железа в растворе. Затем отработанный пассивирующий раствор дренируется и контур промывается химически обессоленной водой. Важно подчеркнуть, что данная методика пассивации на РУ БН-600 соответствует гидразинно-аммиачному водно-химическому режиму (ВХР) III контура. Защитная пленка структуры магнетита, образовавшаяся при пассивации в восстановительной среде на стальных поверхностях, не подвергается трансформации и структурной перестройке в восстановительном гидразинно-аммиачном ВХР при пуске энергоблока. Утилизация отработанных гидразинных растворов трудности для эксплуатации не вызывает.
В парогенераторах РУ БН-800, которые полностью изготовлены из стали 10Х2М, после гидразинной пассивации происходит коррозия при последующем пуске энергоблока, так как на этапе пассивации оксидная пленка, созданная в восстановительной среде, склонна к перестройке в окислительном кислородно-аммиачном ВХР III контура. Это неизбежно приводит к усилению коррозии стали и выносу продуктов коррозии в водный теплоноситель. Поэтому этап пассивации парогенераторов ПГН-272 следует проводить с применением окислительного раствора, например на основе ацетата аммония и нитрита натрия. Опыт проведения такой пассивации на РУ БН-600 имеется, он положительный и по времени занимает только несколько часов. Исследован также вопрос об утилизации пассивирующего раствора. Для доведения содержания нитрита натрия в отработанном растворе до предельно допустимой концентрации (1 мг/кг) возможно применение дополнительного ионообменного фильтра в контуре циркуляции в конце этапа пассивации для удаления отработанных солей.
Кроме того, известно несколько химических способов утилизации нитритных солей: разложение нитрита натрия с помощью карбамида (NH2)2CO в кислой среде (H2SO4), сульфаминовой кислоты NH2SO3H, сульфата железа на катализаторе (сульфоуголь), перманганата калия с добавлением серной кислоты (при этом на определенной стадии процесса ацетат аммония разлагается до газообразных продуктов), а также фильтрование раствора через стружку алюминия (или его сплавов) или магния с добавлением в исходный раствор щелочи (NaOH).
Рассматривались также варианты пассивации с применением растворов на основе ЭДТК и ее солей с различными добавками. Эти растворы после применения тоже требуют дополнительной утилизации. Например, при фильтровании растворов через порошкообразный активированный пиролюзит MnO2 (сильный твердый окислитель, не растворимый в воде) их органическая часть разлагается до газообразных продуктов [7]. Все перечисленные способы имеют свои достоинства и недостатки, требуют экспериментальной проработки и химико-аналитического обоснования применительно к конкретной задаче.
Не исключается вариант пассивации отмытых от отложений поверхностей парогенератора ПГН-272 с помощью растворов, имеющих повышенные концентрации кислорода и аммиака. Этот вариант наиболее простой и технологичный, а кроме того, наиболее экологичный (отсутствуют соли, требующие утилизации) и дешевый. В таком варианте пассивация будет наиболее полно соответствовать окислительному ВХР III контура [8] и при последующем пуске энергоблока не будет оснований опасаться возникновения коррозионных проблем. Однако при этом требуемая длительность пассивации в III контуре РУ БН-800 пока не определена.
ВЫВОДЫ
1. Благодаря регулярно проводимым промывкам и замене медьсодержащих сплавов в оборудовании III контура РУ БН-600 на нержавеющую сталь межпромывочный период эксплуатации парогенераторов ПГН-200М увеличен с 15–20 до 30–33 тыс. ч. Повышена эффективность удаления отложений магнетита с 200–400 до 1100–1200 кг. Оптимизированы состав промывочного раствора и способ ввода моющей композиции в контур промывки. Снижена скорость коррозии труб испарителей, изготовленных из стали 10Х2М, с 10–18 до 1–4 г/(м2 · ч) во время химической промывки. Обеспечена межконтурная плотность испарителей парогенераторов во время промывки и эксплуатации. Отработанная технология химических промывок на РУ БН-600 способствует повышению ресурса эксплуатации парогенераторов и энергоблока в целом.
2. Оперативный химический контроль проведения химических промывок может быть оптимизирован в сторону сокращения числа контролируемых показателей. Предлагается ограничиться одной точкой для анализа раствора по содержанию Fe и ЭДТК в контуре промывки (например, только в питательной воде 1 раз в 1 ч), прекратить выполнение анализа на содержание Cu, анализ на содержание кремнекислоты выполнять только в конце промывки в одной точке контура. Таким образом резко сократится нагрузка на химический персонал. Предлагается разработать оперативную методику оценки степени отмывки испарителей от отложений продуктов коррозии по кинетике выделения коррозионного водорода в раствор.
3. Применение гидразина при химической промывке является необходимым, но его эффективность низкая (10–15%). Кроме того, сопоставимое количество гидразина используется для последующей пассивации отмытых поверхностей. Гидразин является канцерогеном, поэтому имеет смысл найти и обосновать применение более безопасного химического восстановителя.
4. Для III контура РУ БН-800 актуален вопрос пассивации отмытых поверхностей. В случае его решения, актуальным становится вопрос нейтрализации отработанного промывочного и пассивирующего раствора.
Список литературы
Гиде Ж. Последствия загрязнения подогревателей-испарителей парогенераторов “Феникс” для их функционирования. Улучшения, внесенные химической промывкой, проведенной на подогревателе-испарителе I в 1984 г. // Сотрудничество ГКАЭ-СЕА в области быстрых реакторов по теме “Парогенераторы”. Обнинск: ФЭИ, 1986.
Ермолаев В.Н., Смыков В.В., Шевченко Н.Н. Опыт эксплуатационных химических промывок испарителей парогенераторов энергоблоков с реакторами на быстрых нейтронах БН-600 и БН-350 // Теплоэнергетика. 1997. № 8. С. 25–30.
Dow B., Thomas R. Chemical cleaning review // Nucl. Eng. Int. 1995. V. 40. № 495. P. 38–39.
Applicability of chemical cleaning process to steam generator side / K. Fujiwara, H. Kawamura, H. Kanbe, H. Takiguchi K. Yoshino, S. Yamavoto, T. Shibata, K. Ishigure // J. Nucl. Sci. Technol. 2004. V. 41. № 1. P. 44–54.https://doi.org/10.1080/18811248.2006.9711229
Маргулова Т.Х. Применение комплексонов в теплоэнергетике. М.: Энергоатомиздат, 1986.
Baker J.G. Application of N, N-DEHA in water-stream cycle at TPP with OTFF generators // Anti-Corros. Methods Mater. 1983. V. 30. № 2. P. 5–6.
Пат. РФ № 2597242. Способ очистки ЖРО от органических примесей / В.Б. Смыков, К.Г. Легких. 2016.
РД ЭО 1.1.2.11.0822-2010. Водно-химический режим 3-го контура атомных станций с реактором БН-800. Нормы качества рабочей среды и средства их обеспечения. М.: Росэнергоатом, 2010.
Дополнительные материалы отсутствуют.
Инструменты
Теплоэнергетика