Теплофизика высоких температур, 2020, T. 58, № 2, стр. 266-274
Экспериментальные исследования разбросов теплозащитных характеристик резиноподобной теплозащиты
В. В. Кошлаков 1, *, В. В. Миронов 1, К. А. Чумакин 1, М. А. Толкач 1
1 ГНЦ РФ – ФГУП “Исследовательский центр
им. М.В. Келдыша” (Центр Келдыша)
Москва, Россия
* E-mail: kerc@elnet.msk.ru
Поступила в редакцию 05.07.2019
После доработки 30.09.2019
Принята к публикации 22.10.2019
Аннотация
Разбросы теплозащитных характеристик материала, используемого в качестве тепловой защиты высокотемпературных установок, в частности ракетных двигателей твердого топлива, существенно влияют на проектные толщины и массу тепловой защиты, а следовательно, на эффективность и надежность работы установки. С помощью результатов измерений в процессе огневых стендовых испытаний материалов показано, что величина получаемых разбросов существенным образом зависит от метода вычисления глубин прогрева и/или глубины термической деструкции. На основании анализа экспериментальных данных выполнены оценки разбросов теплозащитных характеристик резиноподобного теплозащитного материала.
ВВЕДЕНИЕ
Энергомассовое совершенство и надежность работы высокоэнергетических, высокотемпературных установок различного назначения существенно зависят от правильного выбора материалов и конструкции внутреннего теплозащитного покрытия (ТЗП) [1–7]. В последние годы все более широкое использование при формировании внутренних ТЗП различных высокотемпературных установок находят резиноподобные теплозащитные материалы (ТЗМ) [6, 7]. Резиноподобные ТЗМ, в первую очередь, создаются на основе бутадиен-нитрильных, полиуретановых и бутиловых каучуков (бутадиен-нитрильные и этиленпропиленовые резины).
В качестве основной теплозащитной характеристики (ТЗХ) теплозащитных материалов используется глубина прогрева до заданной температуры (допустимой для защищаемой конструкции) и/или глубина термодеструкции (характеристика прогрева и разрушения материала) [8, 9]. При заданных условиях прогрева указанные ТЗХ резиноподобного теплозащитного покрытия определяются теплофизическими и оптическими свойствами материала, а также механизмом разрушения прококсованного слоя, образующегося в процессе прогрева ТЗП [6, 7].
Необходимая толщина ТЗП в высокотемпературных энергетических установках (например, в ракетных двигателях твердого топлива – РДТТ) рассчитывается по формуле [10]
где δтзп – толщина ТЗП, определяемая расчетными методами для номинального режима работы установки или в результате анализа данных дефектации ТЗП после натурных испытаний установки; σтд – среднеквадратическое отклонение глубины термодеструкции или прогрева до заданной температуры, определяемое при огневых стендовых испытаниях (ОСИ) образцов ТЗМ или при дефектации ТЗП после натурных испытаний; γ – толерантный множитель, определяемый исходя из обеспечения требуемой надежности.Проектную толщину ТЗП назначают на основании необходимой толщины δн, рассчитанной по формуле (1), с учетом технологии изготовления тепловой защиты, возможного изменения толщины покрытия в процессе и после изготовления высокотемпературной установки, полноты и качества контроля толщины покрытия после изготовления.
Из формулы (1) следует, что разбросы ТЗХ существенно влияют на толщину и массу покрытия. Например, снижение коэффициента вариации глубины термодеструкции с 15–30% до 7–15% позволяет уменьшить начальную массу и объем, занимаемый покрытием, на 20–25% [10]. Коэффициент вариации Kv для ТЗХ определяется как
где δс – среднее значение глубины термодеструкции или прогрева до заданной температуры. В связи с этим определение среднеквадратичного отклонения σтд в процессе ОСИ теплозащитных материалов является важной задачей.МЕТОД ИССЛЕДОВАНИЙ РАЗБРОСОВ ТЕПЛОЗАЩИТНЫХ ХАРАКТЕРИСТИК РЕЗИНОПОДОБНОГО ТЗМ
Термин “разброс” введен по аналогии с ГОСТ Р МЭК 60 269-1–2010 и обозначает предельные значения, между которыми находятся ТЗХ образцов. У материалов одной и той же партии, изготовленных по одной и той же технологии, при испытаниях в идентичных условиях могут быть различные выходные ТЗХ. Это явление именуется случайными разбросами ТЗХ. Свойства ТЗМ (плотность, теплоемкость, теплопроводность) изменяются в пределах соответствующих допусков, поэтому и результирующая ТЗХ колеблется в некоторых пределах, подчиняясь вероятностным законам распределения.
Для исследования ТЗХ резиноподобных ТЗМ используются различные установки на основе газогенераторов твердого топлива [7, 10, 11], имитирующих условия прогрева ТЗМ в высокотемпературных установках. В ГНЦ “Центр Келдыша” в течение многих лет огневые испытания разных марок ТЗМ проводятся на установке, схема которой приведена на рис. 1 (согласно [10]).
Рис. 1.
Схема экспериментальной установки: 1 – газогенератор, 2 – входная часть; 3 – переходник; 4 – корпус рабочего отсека; 5 – образец ТЗМ; 6 – пробка с термопарой; 7 – сопловой блок; d = 0.06 м; L = 0.16 м.
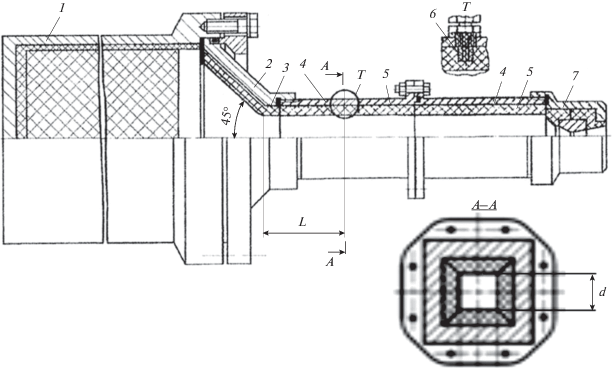
Как правило, использовалась установка с квадратным сечением проточного тракта размером 0.06 × 0.06 м2 (рис. 1), переходником (выравнивающим участком 3) длиной 0.09 м и с пятью рабочими отсеками-секциями каждая длиной по 0.12 м. Образцы устанавливались на каждой стороне рабочего отсека-секции. Скорость обтекания образцов высокотемпературными продуктами сгорания твердых топлив варьировалась в экспериментах изменением диаметра критического сечения соплового блока и/или размера сечения проточного тракта.
В экспериментах измерялись изменение давления в газогенераторе во времени, начальные и конечные вес и размеры образцов. Кроме этого, в образцах, располагаемых по трем сторонам сечения канала (боковые и низ) в секциях со второй по пятую с помощью термопар, установленных на различных глубинах, измерялось изменение температуры за время работы установки. Устанавливалось по пять термопар на разных глубинах каждого из образцов. Схема образца и положение термопар в образце показано на рис. 2.
По данным выполненных измерений проводится анализ ТЗХ образцов (глубин термодеструкции и глубин прогрева до 100°С), прошедших ОСИ.
РЕЗУЛЬТАТЫ АНАЛИЗА ГЛУБИН ТЕРМИЧЕСКОЙ ДЕСТРУКЦИИ
Ниже приведены результаты испытаний характерного резиноподобного материала на основе этиленпропиленового каучука, близкого по составу и свойствам (теплофизическим характеристикам) к ТЗМ Р-864 [5, 12, 13]. Для анализа отобраны четыре испытания с наиболее полным набором измерений. Температура продуктов сгорания используемого в газогенераторе твердого топлива составляла 3500°С. Другие параметры огневого испытания для каждого эксперимента приведены в табл. 1.
Таблица 1.
Параметры ОСИ ТЗМ
Номер эксперимента |
τоп, с | Nter | Pср, МПа | Uпс, м/с |
---|---|---|---|---|
1 | 48 | 59 | 5.44 | 10.7 |
2 | 45.6 | 55 | 12.09 | 4.6 |
3 | 56 | 60 | 4.45 | 27.6 |
4 | 55.6 | 60 | 9 | 22.8 |
Примечание: τоп – продолжительность эксперимента; Nter – количество термопар в испытании с учетом исключенных отказов и промахов по ГОСТ Р 8.736–2011; Pср – среднеинтегральное давление; Uпс – среднерасходная скорость продуктов сгорания твердого топлива на входе в рабочую часть канала с образцами ТЗМ.
Глубины термодеструкции δтд образцов ТЗМ определялись как разность начальных и конечных (тщательно очищенных после испытания от коксового слоя) толщин образцов в 18 точках и вычислялось их среднее значение δтдс. Масса унесенной части образца рассчитывалась как разность между начальной и конечной (с очищенным коксовым слоем) массами образца ΔМ (взвешиванием). С учетом формы образца (см. рис. 2) по значениям δтдс и ΔМ вычислялась характерная плотность материала ρх0 для части образца, претерпевшей термодеструкцию:
(3)
${{\rho }_{{х0}}} = \frac{{2\Delta M}}{{L\left( {2b{{\delta }_{{{\text{тдс}}}}} + \frac{{B - b}}{h}\delta _{{{\text{тдс}}}}^{2}} \right)}}.$Схема процесса коксования образца при наличии и отсутствии термического расширения в области его прогрева ниже температур деструкции приведена на рис. 3.
На рис. 3 приняты следующие обозначения: l0 – измеренная начальная толщина образца в данном сечении; lк, lкр – измеренная конечная толщина образца в данном сечении при отсутствии и наличии термического расширения непрококсованного слоя соответственно; δд – глубина термической деструкции при отсутствии термического расширения, вычисляемая как разность (l0 – lк); δтд – глубина термической деструкции при наличии термического расширения, вычисляемая как разность (l0 – lкр); δр – толщина, на которую увеличивается прогретый, но непрококсованный слой ТЗМ в рассматриваемом сечении из-за термического расширения.
Из соотношения (3) и рис. 3 следует, что если слой материала, не подвергавшегося термической деструкции, не изменяет своих размеров (толщины), то значение вычисленной плотности ρх0 должно быть равно величине плотности исходного материала ρ0.
Если область образца ниже температур деструкции претерпит расширение, то величина δтд уменьшается (так как lкр увеличится, рис. 3), и характерная плотность ρх0, согласно соотношению (3), увеличивается. Как видно, значение плотности ρх0 может использоваться для определения наличия/отсутствия термического расширения/усадки в области образца, не подвергнутой термической деструкции:
если ρх0 > ρ0, имеет место термическое расширение;
если ρх0 < ρ0, имеет место усадка;
если ρх0 = ρ0, материал остатка соответствует исходному состоянию.
Аналогичный метод обработки результатов ОСИ использован ранее в работе [14].
При известных ρх0, ρ0 и δтдс фактическая (т.е. вычисленная с учетом термического расширения) глубина термической деструкции δф для рассматриваемого образца может быть определена с использованием соотношения
В предположении равномерности уноса массы по всей поверхности образца определялась также глубина деструкции δmi для каждого i-го образца, вычисляемая по потерям массы и с учетом индивидуальной формы каждого образца (параметров L, b, B и h – см. рис. 2):
Результаты обработки экспериментальных данных для групп образцов, расположенных по каждой из сторон рабочего канала (по пять образцов в группе) представлены в табл. 2.
Таблица 2.
Результаты обработки экспериментальных данных, сгруппированных по сторонам канала (по группам)
Номер эксперимента | Параметр | Группа и поверхность канала | Значение среднее по всем образцам | |||
---|---|---|---|---|---|---|
1 левая |
2 верх |
3 правая |
4 низ |
|||
1 | ΔМ, г | 30.54 | 31.98 | 32.06 | 29.48 | 31.02 |
δm × 103, м | 3.67 | 3.85 | 3.78 | 3.32 | 3.6 | |
δтдс × 103, м | 3.28 | 3.67 | 3.59 | 3.42 | 3.49 | |
ρхо/ρ0 | 1.145 | 1.055 | 1.057 | 1.021 | 1.070 | |
δф × 103, м | 3.76 | 3.87 | 3.80 | 3.50 | 3.71 | |
2 | ΔМ, г | 35.16 | 34.58 | 29.12 | 32.68 | 32.88 |
δm × 103, м | 4.12 | 3.96 | 3.39 | 3.70 | 3.79 | |
δтдс × 103, м | 3.65 | 3.05 | 2.96 | 3.24 | 3.22 | |
ρхо/ρ0 | 1.134 | 1.324 | 1.154 | 1.110 | 1.18 | |
δф × 103, м | 4.15 | 4.02 | 3.41 | 3.78 | 3.84 | |
3 | ΔМ, г | 45.66 | 44.12 | 42.90 | 46.30 | 44.75 |
δm × 103, м | 5.75 | 5.72 | 5.56 | 5.39 | 5.60 | |
δтдс × 103, м | 5.80 | 5.62 | 5.38 | 5.97 | 5.69 | |
ρхо/ρ0 | 0.99 | 1.02 | 1.04 | 0.97 | 1.01 | |
δф × 103, м | 5.74 | 5,73 | 5.57 | 5.74 | 5.7 | |
4 | ΔМ, г | 40.42 | 33.80 | 38.84 | 40.80 | 38.47 |
δm × 103, м | 6.10 | 5.16 | 5.86 | 6.24 | 5.84 | |
δтдс × 103, м | 6.43 | 5.3 | 6.23 | 6.42 | 6.1 | |
ρхо/ρ0 | 0.946 | 0.97 | 0.94 | 0.96 | 0.954 | |
δф × 103, м | 6.05 | 5.15 | 5.82 | 6.18 | 5.8 |
На рис. 4 для наглядности показаны распределения уточненных (фактических) глубин деструкции δф образцов ТЗМ по группам.
Рис. 4.
Значения фактической глубины деструкции δф на разных сторонах канала: 1 – опыт № 1, 2 – № 2, 3 – № 3, 4 – № 4.
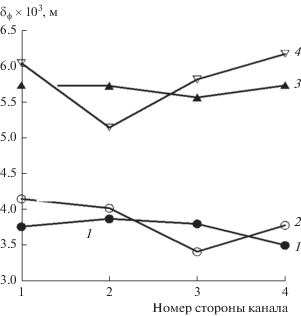
Из сопоставления данных табл. 2 и рис. 4 следует, что влияние ориентации образцов относительно вертикали (стороны канала) отсутствует: если значение δф в испытании № 1 выше на второй и третьей сторонах, то в испытании № 2 величина δф выше на первой и второй (здесь максимально отношение ρхо/ρ0) сторонах, а на третьей – заметно ниже и т.п.
Поскольку влияние того, на какой стороне канала размещены образцы, закономерным образом не проявляется, была выполнена обработка экспериментальных данных в зависимости от длины канала, т.е. по секциям (рабочим отсекам), в каждой секции размещены четыре образца по ее сторонам. В каждом образце, как и прежде, по измерениям в 18 точках определяются величины δтдс и δф. Результаты анализа по секциям представлены в табл. 3 и на рис. 5, где распределение δф изображено сплошной линией, δтдс – штриховой.
Таблица 3.
Результаты обработки опытных данных сгруппированных по секциям (по длине проточного тракта)
Номер испытания | Параметр | Номер секции | Среднее по всем секциям | ||||
---|---|---|---|---|---|---|---|
1 | 2 | 3 | 4 | 5 | |||
1 | δтдс × 103, м | 3.78 | 3.27 | 3.59 | 3.48 | 3.34 | 3.49 |
${{\sigma }_{{{\text{тд}}}}}$ × 103, м | 0.57 | 0.71 | 0.395 | 0.42 | 0.32 | 0.53 | |
Кv, % | 15.1 | 21.9 | 11.0 | 12.1 | 9.5 | 15.3 | |
δф × 103, м | 4.14 | 3.74 | 3.76 | 3.46 | 3.45 | 3.71 | |
2 | δтдс × 103, м | 3.45 | 3.50 | 3.23 | 2.93 | 3.00 | 3.22 |
${{\sigma }_{{{\text{тд}}}}}$ × 103, м | 0.50 | 1.0 | 0.47 | 0.62 | 0.31 | 0.67 | |
Кv, % | 14.7 | 29.0 | 14.5 | 21.1 | 10.3 | 20.7 | |
δф × 103, м | 4.29 | 4.09 | 3.87 | 3.29 | 3.66 | 3.84 | |
3 | δтдс × 103, м | 6.87 | 5.84 | 5.58 | 5.23 | 4.95 | 5.69 |
${{\sigma }_{{{\text{тд}}}}}$ × 103, м | 0.67 | 0.51 | 0.65 | 0.40 | 0.44 | 0.86 | |
Кv, % | 9.8 | 8.8 | 11.6 | 7.7 | 8.8 | 15.0 | |
δф × 103, м | 6.68 | 5.90 | 5.47 | 5.28 | 5.16 | 5.7 | |
4 | δтдс × 103, м | 7.66 | 6.4 | 5.89 | 5.4 | 5.13 | 6.1 |
${{\sigma }_{{{\text{тд}}}}}$ × 103, м | 1.2 | 0.9 | 0.56 | 0.48 | 0.4 | 1.18 | |
Кv, % | 15.9 | 14.2 | 9.5 | 8.87 | 7.84 | 19.38 | |
δф × 103, м | 7.24 | 6.09 | 5.46 | 5.04 | 5.17 | 5.8 |
Из данных табл. 3 и на рис. 5 следует наличие влияния местоположения образца (расстояния от входа в рабочую часть) на глубину деструкции образцов.
В табл. 4 приведены средние значения δтдс и δф по всем образцам в испытании, их среднеквадратичные отклонения и коэффициенты вариации. Разбросы (коэффициент вариации), определяемые по глубинам деструкции, с поправкой на распухание в области образца ниже температур деструкции заметно ниже (на 20–50%), чем определяемые по глубинам деструкции, полученным только по замерам толщин образца до и после испытания. Это указывает на необходимость учета распухания при экспериментальном определении деструкции и соответствующих разбросов ТЗХ.
Таблица 4.
Коэффициент вариации для измеренной и уточненной (фактической) глубин деструкции в проведенных ОСИ
Номер испытания | Измеренная деструкция | Фактическая деструкция | ||||
---|---|---|---|---|---|---|
δтдс × 103, м | ${{\sigma }_{{{\text{тд}}}}}$ × 103, м | Кv, % | δф × 103, м | ${{\sigma }_{{\text{ф}}}}$ × 103, м | Кv, % | |
1 | 3.49 | 0.53 | 15.3 | 3.71 | 0.41 | 11.2 |
2 | 3.22 | 0.67 | 20.7 | 3.84 | 0.51 | 13.4 |
3 | 5.69 | 0.85 | 15.0 | 5.70 | 0.61 | 10.7 |
4 | 6.10 | 1.18 | 19.4 | 5.8 | 0.96 | 16.6 |
Как видно, с поправкой глубин деструкции на термическое расширение в области образца ниже температур деструкции коэффициент вариации заметным образом снижается: на 2.8% в испытании № 4 и на 7.3% – в № 2.
РЕЗУЛЬТАТЫ АНАЛИЗА ТЕРМОПАРНЫХ ИЗМЕРЕНИЙ
При анализе результатов термопарных измерений в качестве искомого параметра, характеризующего ТЗХ, была выбрана временнáя зависимость глубины прогрева δ100(τ) образца до температуры 100°С. Эта температура находится на уровне допустимых значений для силовых оболочек корпусов высокотемпературных установок, защищаемых ТЗП.
На рис. 6 показаны результаты измерений ${{\delta }_{{100}}}\left( \tau \right)$ в одном образце испытания № 1 (точки) и одном образце испытания № 3 (треугольники).
Прямые линии δ = a0 + a1√τ, соединяющие экспериментальные данные на рис. 6, построены методом наименьших квадратов.
Чтобы учесть выявленное выше влияние расстояния Z от начала рабочей части на тепловое состояние образцов, обработка опытных данных выполнена в соответствии с разделом 6 ГОСТ Р ИСО 5725-3-2002 с помощью статистической модели
здесь L – фактор влияния места положения образца по продольной координате Z, учитывающий изменение теплового воздействия по длине рабочей части установки.Согласно [15], дифференциальное уравнение теплоотдачи может быть представлено в форме
где $\bar {t} = \frac{{t - {{t}_{f}}}}{{{{t}_{w}} - {{t}_{f}}}}$ и $n = \frac{x}{l}$ – безразмерные температура потока в пограничном слое и нормаль к поверхности образца; Nu – число Нуссельта; tw – температура поверхности образца; tf – температура на внешней границе пограничного слоя; x – координата в направлении нормали от поверхности образца; l – характерный размер проточного тракта (l = b/2).В силу неопределенности величин l, tf, tw, в качестве фактора L в соотношении (4) для каждого образца из i-й секции используется отношение градиентов Li = gradi/grad1, где gradi = ($\partial{ \bar {t}}$/δn). Поскольку в образцах первой секции термопары не устанавливались, фактор ${{L}_{i}}$ вычисляется для образцов с термопарами, начиная со второй секции, т.е. для $i = 2{\kern 1pt} - {\kern 1pt} 5.$ Нумерация секций ведется со стороны газогенератора.
Значения ${\text{gra}}{{{\text{d}}}_{i}}$ в центре каждого из испытуемых образцов у его поверхности определялись при расчете течения и теплообмена в канале экспериментальной установки по программе CFX ANSYS (лиц. № 002590e6d672) с учетом зависимости характеристик продуктов сгорания твердого топлива от температуры и давления. Полученная зависимость фактора ${{L}_{i}}$ от условий испытаний (среднерасходной скорости продуктов сгорания твердого топлива на входе в рабочую часть канала) приведена на рис. 7.
С помощью регрессионного анализа, согласно работе [16], могут быть получены коэффициенты b0, b1 и b2 в соотношении (4). Коэффициенты, вычисленные при обработке полученных экспериментальных данных, приведены в табл. 5.
Таблица 5.
Значения коэффициентов регрессионного анализа (см. соотношение (4)) и соответствующих коэффициентов вариации
Номер испытания | b0 × 103, м | b1 × 103, м/с1/2 | b2 × 103, м | Kvar, % |
---|---|---|---|---|
1 | –0.6511 | 0.8874 | 0.2927 | 4.4 |
2 | –0.6021 | 0.8641 | 0.6328 | 4.1 |
3 | –1.4577 | 1.061 | 1.7 | 7.9 |
4 | –2.017 | 1.2318 | 1.89929 | 5.6 |
Коэффициент вариации Kvar для данных в табл. 5 определен по аналогии с параметром Кv (2) с использованием следующего соотношения:
Разбросы ТЗХ исследованного ТЗМ на основе этиленпропиленового каучука при скоростях продуктов сгорания топлива на входе в рабочую часть установки до 11 м/с (см. табл. 1) находятся на уровне Kvar = 4% (табл. 5). При этом плотность потока продуктов сгорания на входе в рабочую часть G ≤ 52 кг/(м2 с), G = ρUпс.
Величины ${{K}_{{{\text{var}}}}}$ в табл. 5 включают экспериментальные погрешности системы измерений (в том числе в положении термопар, непостоянство временнóй зависимости давления в газогенераторе, разбросы в исходной толщине образцов). Цель данной работы состоит в исключении наиболее значимой составляющей экспериментальной погрешности (связанной с изменением условий прогрева по длине рабочей части экспериментальной установки) из результата измерений ТЗХ ТЗП. Значение разброса ТЗХ ТЗМ в 4% является завышенной оценкой. При высоких скоростях Uпс = 22.8–27.6 м/с (G = 110–82 кг/(м2 с)) доля экспериментальных погрешностей возрастает, но разбросы ТЗХ не изменяются. Они могли бы измениться, если бы при сравнительно высоких скоростях появился механический унос коксового слоя со стороны прогрева, но этого не происходит, что подтверждают данные на рис. 6: сохраняется линейная зависимость глубины прогрева от √τ.
На рис. 8 представлена зависимость коэффициента b1, характеризующего скорость продвижения изотермы 100°С вглубь ТЗП, от плотности потока G продуктов сгорания на входе в канал. Такое представление является более корректным по сравнению с зависимостью b1 только от скорости потока Uпс, поскольку учитывается и влияние давления.
Рис. 8.
Зависимость коэффициента ${{b}_{1}}$ от плотности потока G продуктов сгорания на входе в рабочий канал: цифры – номер испытания.
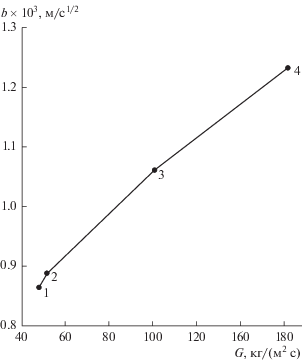
Максимальное значение плотности потока продуктов сгорания на входе в рабочий канал имело место в испытании № 4: G = 182 кг/(м2 с). При этом величина скорости продуктов сгорания была на 20% ниже, чем в испытании № 3 и составляла ${{U}_{{{\text{пс}}}}} = 22.8$ м/с, а давление было в два раза выше (см. табл. 1).
ЗАКЛЮЧЕНИЕ
В результате пофакторного анализа экспериментальных временны́х зависимостей глубины прогрева образцов ТЗМ до температуры в 100°С, полученных в процессе испытаний теплозащитного материала на основе этиленпропиленового каучука одной партии изготовления, установлено, что разбросы его теплозащитных характеристик находятся в пределах 4%.
Для определения разбросов теплозащитных характеристик ТЗМ при проектировании высокотемпературных установок необходимо проводить испытания образцов, изготовленных по технологии штатного ТЗП, в том числе из разных партий ТЗМ.
При анализе деструкций ТЗМ после ОСИ необходимо учитывать неравномерность воздействия нагревающего потока по поверхности образцов и деформацию (термическое расширение) недеструктировавших остатков образцов.
Использование термопарных измерений теплового состояния образцов ТЗМ в процессе испытаний для определения его теплозащитных характеристик предпочтительнее по сравнению с анализом глубин термической деструкции.
Список литературы
Валеев Н.С., Бабушкин О.Н. Принципы выбора внутреннего ТЗП на РДТТ // Матер. докл. Всерос. науч.-техн. конф. “Ракетные двигатели и энергетические установки”. Казань: Изд-во Казанск. ун-та, 2015. С. 67.
Белов В.П. Тепловая защита элементов конструкции ракетных двигателей на твердом топливе. Учеб. пособ. СПб.: Балт. гос. техн. ун-т, 2010. 51 с.
Шишков А.А. Рабочие процессы в ракетных двигателях на твердом топливе. Спр. / Шишков А.А., Панин С.Д., Румянцев Б.В. М.: Машиностроение, 1989. 240 с.
Волков В.Т., Ягодников Д.А. Исследование и стендовая отработка ракетных двигателей на твердом топливе. М.: Изд-во МГТУ им. Н.Э. Баумана, 2007. 296 с.
Яскин А.В. Конструкции и отработка ракетных двигателей на твердом топливе. Учеб. пособ. Бийск: Изд-во Алт. гос. техн. ун-та, 2010. 200 с.
Страхов В.Л., Атаманов Ю.М., Кузьмин И.А., Бакулин В.Н. Математическое моделирование высокотемпературных теплофизических характеристик резиноподобных теплозащитных материалов // ТВТ. 2017. Т. 55. № 4. С. 528.
Гаращенко А.Н., Кузнецов Г.В., Ткачев А.И. Механизм высокотемпературного разрушения резиноподобных теплозащитных материалов в поле массовых сил // ТВТ. 1995. Т. 33. № 3. С. 458.
Панкратов Б.М., Полежаев Ю.В., Рудько А.К. Взаимодействие материалов с газовыми потоками / Под ред. Зуева В.С. М.: Машиностроение, 1975. 224 с.
Полежаев Ю.В., Юревич Ф.Ф. Тепловая защита / Под ред. Лыкова А.В. М.: Энергия, 1976. 396 с.
Губертов A.M., Миронов В.В., Борисов Д.М. и др. Газодинамические и теплофизические процессы в ракетных двигателях твердого топлива / Под ред. Коротеева А.С. М.: Машиностроение, 2004. 512 с.
Кузнецов Г.В. Высокотемпературное разрушение резиноподобных теплозащитных материалов в условиях высоких давлений // ТВТ. 1996. Т. 34. № 6. С. 919.
Конструкции ракетных двигателей на твердом топливе / Под общ. ред. Лаврова Л.Н. М.: Машиностроение, 1993. 215 с.
Полежаев Ю.В., Фролов Г.А. Тепловое разрушение материалов / Под ред. Скорохода В.В. Киев: Изд-во ИПМ НАНУ, 2005. 288 с.
Миронов В.В., Толкач М.А. Термическая деструкция резиноподобных теплозащитных материалов под слоем конденсированной фазы // ТВТ. 2019. Т. 57. № 2. С. 269.
Болгарский А.В., Мухачев Г.А., Щукин В.К. Термодинамика и теплопередача. Учебн. для вузов. Изд. 2-е, перераб. и доп. М.: Высшая школа, 1975. 495 с.
Зажигаев Л.С., Кишьян А.А., Романиков Ю.И. Методы планирования и обработки результатов физического эксперимента. М.: Атомиздат, 1978. С. 232.
Дополнительные материалы отсутствуют.
Инструменты
Теплофизика высоких температур