Теплофизика высоких температур, 2020, T. 58, № 3, стр. 454-464
Моделирование процессов электролизера для переработки отработанного ядерного топлива
А. Е. Галашев 1, 2, *, В. В. Стаханов 3, Ю. П. Зайков 1, 2
1 ФГБУН Институт высокотемпературной электрохимии
Уральского отделения РАН
г. Екатеринбург, Россия
2 Уральский федеральный университет им. первого Президента России Б.Н. Ельцина
г., Екатеринбург, Россия
3 ФГУП Российский федеральный ядерный центр – Всероссийский научно-исследовательский институт
технической физики им. Е.И. Забабахина
г. Снежинск, Россия
* E-mail: galashev@ihte.uran.ru
Поступила в редакцию 04.10.2019
После доработки 22.11.2019
Принята к публикации 24.12.2019
Аннотация
С использованием программного пакета ANSYS выполнено моделирование функционирующего электролизера для переработки отработанного ядерного топлива методом электролиза в расплавленной соли LiCl с добавлением Li2O. Рассмотрено семь типов конструкций электролизера, отличающихся взаимным размещением электродов и толщиной анодов. Рассчитаны температурное поле, а также распределения плотности тока и электрического потенциала. Определена оптимальная конструкция электролизера для достижения наилучших температурных и электрических характеристик.
ВВЕДЕНИЕ
С каждым годом проблема переработки отработанного ядерного топлива (ОЯТ) становится все острее. Одним из наиболее эффективных способов переработки ОЯТ (состоящего преимущественно из UO2), которое не подвергалось выдержке и имеет высокую степень выгорания, является электролиз при T = 650°C в расплавленной соли LiCl с добавлением Li2O. Способ реализуется с использованием компактного оборудования, и степень восстановления UO2 до металлического урана может достигать 100%. Экспериментальная разработка метода проводилась в течение последних 10 лет в Южной Корее [1–4]. Предполагается с помощью такого рода пиропереработки переводить отработанное оксидное топливо, извлекаемое из легководных реакторов, в металлическое топливо, которое будет облучаться в ядерном реакторе на быстрых нейтронах [5]. Однако до настоящего времени промышленная переработка отработанного ядерного топлива этим способом не практикуется. Многие проблемы до сих пор остаются нерешенными. Процесс электролиза все еще не оптимизирован, возникает много вопросов по материалам, которые могут выдерживать агрессивную среду при рабочей температуре. Многие вопросы можно снять благодаря фундаментальному изучению процессов восстановления, происходящих на катоде. В настоящей работе выполнено компьютерное моделирование функционирования электролитической ячейки при восстановлении UO2 до металлического урана с использованием программы ANSYS. В будущем на основании подобных расчетов, имитирующих процесс восстановления ОЯТ, может быть создан цифровой близнец работающего электролизера.
С применением программы ANSYS был выполнен анализ аварии потери теплоотвода в резервуаре с отработанным топливом [6]. ANSYS Fluent часто выбирается в качестве инструмента численной флюидной динамики, поскольку в нем имеются подходящие методы конечного объема для реалистичного моделирования теплового поведения транспортировочных контейнеров, в частности контейнера для сборки ОЯТ [7]. С помощью программного обеспечения ANSYS Fluent решалась проблема получения водорода с использованием ядерного реактора в качестве основного источника тепла [8]. Компьютерное моделирование электрохимической обработки ОЯТ может способствовать тому, что электролитический метод станет жизнеспособной технологией для закрытого ядерного топливного цикла.
Актуальность настоящего исследования продиктована тем, что метод электролитического восстановления ОЯТ, активно разрабатываемый с помощью сугубо экспериментальных исследований, столкнулся с трудностями, для преодоления которых нужны фундаментальные знания об этом процессе. До сих пор не было выполнено теоретических и расчетных работ, посвященных данной теме. В первую очередь работы такого типа необходимы для разработки новой технологии регенерирования ОЯТ, конечная цель которой замкнуть цикл использования ядерного топлива.
Цель настоящего исследования заключается в том, чтобы на основе компьютерного моделирования изучить зависимость основных параметров процесса переработки ОЯТ, протекающего при высокой температуре с применением электрохимической технологии.
ГЕОМЕТРИЧЕСКАЯ МОДЕЛЬ
Конструкция исследуемого электролизера для переработки ОЯТ представлена на рис. 1. Размеры высокотемпературного пространства модели электролизера, имеющего цилиндрическую форму и заполненного расплавом LiCl–Li2O, составляют $\emptyset $540 × 280 мм2. Прямоугольная корзина, в которой находится ОЯТ (т.е. UO2), имеет высоту 100 мм и горизонтальные размеры 100 × 100 мм2. Стальная (X18H10T) проволочная (диаметром 1 мм) катодная корзина с площадью квадратных ячеек менее 25 мм2 позволяет надежно сохранять внутри себя таблетки UO2, диаметр и высота которых обычно ~10 мм. Если принять, что при полной засыпке таблеток ОЯТ в корзину достигается 70%-ная упаковка, а средняя пористость таблеток составляет 40% [1, 4], то оказывается, что масса загружаемого UO2 в моделируемом электролизере составляет 4.6 кг. При такой загрузке и 100%-ном восстановлении UO2 после завершения электролитического процесса в корзине останется около 4 кг металлического урана. Этот объем приблизительно соответствует массе урана, получаемой в однократном процессе восстановления в реальных лабораторных установках [1, 4]. В проектируемом промышленном электролизере предполагается увеличение этого значения приблизительно в пять раз. Используется стальной токоподвод к корзине с диаметром стержня $d$ = 10 мм.
Рис. 1.
Схема электролизера для переработки ОЯТ: 1 – катодный токоподвод, 2 – анодные токоподводы, 3 – контакт токоподвода с торцом анода, 4 – анод, 5 – ОЯТ (UO2), 6 – катод, 7 – расплав LiCl–Li2O.
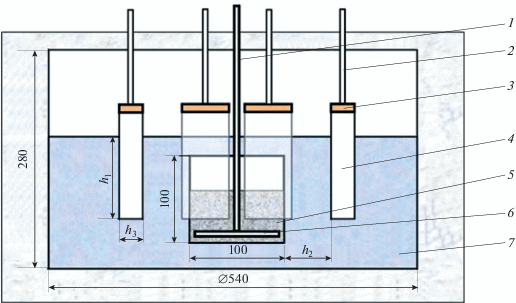
Материалом анода служит керамика на основе NiO с добавкой Li2O. Легирование NiO литием позволяет увеличить электропроводность этого материала. Керамический анод имеет высоту 150 мм, ширину 50 мм и толщину ${{h}_{3}}.$ Количество используемых анодов – 8. Токоподвод к анодам осуществляется через стальные стержни ($d$ = 5 мм). Контакт токоподвода с торцом анода создается через медную пластину толщиной 5 мм. Глубина погружения анода в расплав обозначена ${{h}_{{{\kern 1pt} 1}}},$ а расстояние от анодов до корзины – ${{h}_{2}}.$ Расстояние от корзины до дна тигля составляет 30 мм.
ФИЗИЧЕСКАЯ МОДЕЛЬ
Представление процессов конвективного течения гетерогенной смеси в электролизере [9, 10] (вблизи анода в электромагнитном поле) проводится в приближении монодисперсной смеси. При описании гидродинамических процессов используются следующие уравнения и соотношения.
Уравнения Навье–Стокса для случая зависимости плотности среды от температуры [11]:
Уравнение несжимаемости:
Уравнение теплопроводности с учетом объемного источника тепла, связанного с распадом ОЯТ, и джоулева тепловыделения [7]:
Закон Стефана–Больцмана для реального тела:
где S – энергетическая светимость, c0 = 5.67032 × × 10–8 Вт м–2 K–4 – постоянная Стефана–Больцмана, Значения коэффициента ε определяются природой тела, состоянием его поверхности и температурой.Первый закон Кирхгофа (закон сохранения электрического заряда) [12]:
(1)
$\frac{{\partial {{J}_{x}}}}{{\partial x}} + \frac{{\partial {{J}_{y}}}}{{\partial y}} + \frac{{\partial {{J}_{z}}}}{{\partial z}} = 0,$Уравнение Максвелла (rot E = 0) и закон Ома:
(2)
$\begin{gathered} \frac{{\partial {{E}_{z}}}}{{\partial y}} - \frac{{\partial {{E}_{y}}}}{{\partial z}} = 0,\,\,\,\,\frac{{\partial {{E}_{x}}}}{{\partial z}} - \frac{{\partial {{E}_{z}}}}{{\partial x}} = 0, \\ \frac{{\partial {{E}_{x}}}}{{\partial y}} - \frac{{\partial {{E}_{y}}}}{{\partial x}} = 0, \\ \end{gathered} $(3)
${{J}_{x}} = \varsigma {{E}_{x}},\,\,\,\,{{J}_{y}} = \varsigma {{E}_{y}},\,\,\,\,{{J}_{z}} = \varsigma {{E}_{z}},$Массу образующегося на электроде вещества можно рассчитать, используя первый закон электролиза Фарадея:
где m – масса образовавшегося на электроде вещества, F = 96 485.33(83) Кл/моль – постоянная Фарадея, M – молярная масса вещества, z – число электронов в реакции, t – время электролиза, I – ток электролиза.Реакция образования кислорода на аноде имеет вид
Удельный поток массы образующегося кислорода в единицу времени ${{q}_{m}}$ можно рассчитать согласно уравнению (4). Mолярная масса кислорода M = 32 × 10–3 кг/моль, z = 4. Следовательно, ${{q}_{m}}$ равен (в кг/(м2 с)):Программный комплекс ANSYS берет на себя функцию задания и реализации граничных условий. Для этого достаточно создать геометрическую модель задачи и ввести минимальное число параметров, связанных с граничными и начальными условиями. В этом пакете многие детали решения скрыты от пользователя, что существенно облегчает проведение исследования.
При решении уравнения теплопроводности полагалось, что на поверхности двух сред температура и поток тепла непрерывны. При этом на стенках конструкции либо задавалась одна из этих величин, либо условия непрерывности использовались для сопряжения решений в области течения и вне ее.
В гидродинамической части решаемой задачи задаются граничные условия на поверхности раздела жидкость–твердое тело, причем эти среды имеют различную электропроводность. Так как стенки электролизера и элементов его конструкции непроницаемы, то имеет место обычное граничное условие для скорости вязкой жидкости:
где vn и vτ – нормальная и касательная компоненты скорости соответственно.Условия (5) использовались как начальные граничные условия в настоящей модели.
Особый случай составляет моделирование течения в пористой среде, представляющей в модели ОЯТ (UO2). Полагалось, что на проницаемых стенках корзины выполняется условие
где vb – средняя скорость потока электролита в электролизере.На основе экспериментально установленного факта, что пористая среда ОЯТ полностью пропитывается электролитом, принято упрощение: электропроводность этой среды полностью соответствует электропроводности электролита.
Электродинамические члены в уравнениях (1)–(3) зависят от распределения тока и электрического потенциала во внутреннем пространстве электролизера и на его стенках. Расчет этих распределений представляет сложную задачу, особенно при неоднородном потоке. Если стенки электролизера состоят из участков идеальных проводников (σ = ∞) и изоляторов (σ = 0), то граничными условиями для области течения являются
где Eτ – тангенциальная компонента напряженности электрического поля; где Jn – нормальная компонента плотности тока.Исследование влияния конструкции анодов на поле температур и распределение плотности электрического тока в объеме электролизера проводилось путем варьирования величин ${{h}_{1}},$ ${{h}_{2}},$ ${{h}_{3}}$ (табл. 1), где ${{h}_{1}}$ – глубина погружения анода, ${{h}_{2}}$ – расстояние между плоскостями анода и катода, ${{h}_{3}}$ – толщина анода.
Таблица 1.
Параметры варьирования конструкции анодов
№ конструкции | ${{h}_{1}},$ мм | ${{h}_{2}},$ мм | ${{h}_{3}},$ мм |
---|---|---|---|
1 | 120 | 30 | 10 |
2 | 120 | 60 | 10 |
3 | 120 | 90 | 10 |
4 | 120 | 60 | 20 |
5 | 120 | 60 | 30 |
6 | 120 | 60 | 10 |
7 | 60 | 60 | 10 |
Для проведения расчетов используются следующие параметры:
– сила тока электролиза $I$ = 100 А;
– температура внешнего обогрева со стороны печи T = 650°С;
– температура окружающей среды T = 20°С;
– тепловыделение, связанное с радиоактивным распадом ОЯТ, ${{Q}_{{{\text{ОЯТ}}}}}$ = 9860 Вт/м3;
– коэффициент конвективного теплообмена частей электролизера с окружающей средой $\alpha $ = = 1 Вт/(м2 K).
Свойства материалов, используемых в расчете, (плотность, электропроводность, теплопроводность, теплоемкость, излучательная способность тела и пр.) задавались в зависимости от температуры [13–16].
Расчет проводимости расплава LiCl–Li2O в модели c учетом влияния присутствия кислорода осуществлялся при помощи выражения [9, 10]:
В представленной модели не было предпринято мер для локализации газожидкостной среды. Поэтому на аноде мог скапливаться не весь кислород, но значительная его часть была способна распространяться на весь объем, занятый электролитом. Задача решается в упрощенном варианте – без защитного кожуха на аноде. В реальных условиях анод заключается в кожух в виде цилиндра из MgO, который обеспечивает путь для выхода кислорода [1]. Однако присутствие кожуха затрудняет доступ ионов кислорода из солевого расплава к аноду, что замедляет процесс восстановления ОЯТ. Такая ситуация приводит к увеличению сопротивления расплава LiCl–Li2O.
РЕЗУЛЬТАТЫ РАСЧЕТОВ
Интенсивность потоков в электролите, рассчитанная в центральном сечении электролизера, показана на рис. 2. Области низких скоростей расположены вблизи днища, а также в промежутках между анодами и стенками корпуса электролизера. Слабое движение электролита наблюдается также в окрестности катодной корзины. Очаги с наиболее интенсивным движением находятся вблизи поверхности электролита в непосредственной близости от анодов. Достаточно высокая скорость движения электролита также регистрируется вдоль анодных пластин от их средней части до верха. Кроме того, существуют замкнутые контуры с повышенными скоростями движения электролита, которые расположены на небольшом отдалении от стенок, днища, анодных пластин и поверхности электролита.
Горизонтальное сечение вблизи дна корзины показывает (рис. 3а) наличие областей более сильного движения электролита вблизи стенок корпуса электролизера. Наибольшая интенсивность движения электролита достигается в промежутке между верхним анодом (рис. 3а) и катодной корзиной, где есть высокоскоростное вихревое образование. С противоположной стороны катодной корзины (между корзиной и нижним (рис. 3а) анодом) нет таких вихрей и электролит движется с меньшей скоростью. Непосредственно вблизи стенок катодной корзины движение электролита происходит с невысокими скоростями.
Рис. 3.
Поле скоростей электролита в горизонтальном срезе электролизера: (а) – вблизи дна катодной корзины, (б) – вблизи поверхности расплава (выше корзины).
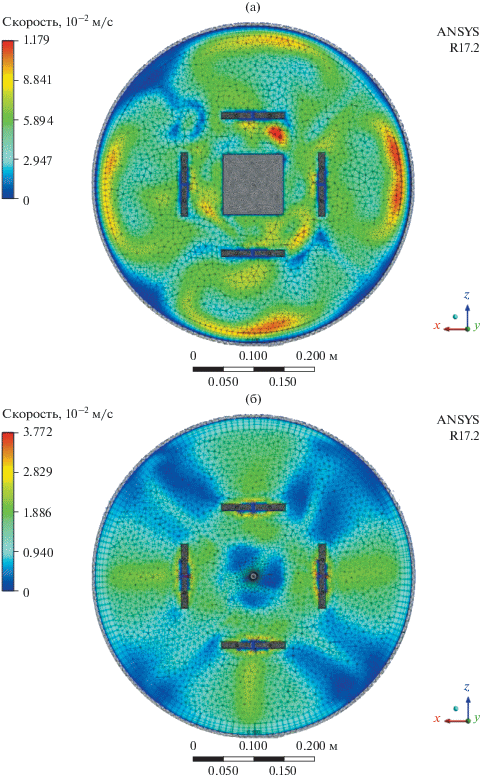
Горизонтальное сечение выше катодной корзины показывает достаточно симметричную картину распределения потоков скоростей в электролизере (рис. 3б). Видно, что присутствие анодов создает симметрично расположенные области более интенсивного движения электролита. Между этими областями и непосредственно над катодной корзиной движение электролита происходит с низкими скоростями.
На рис. 4–7 представлены типичные распределения температуры, электрического потенциала, плотности тока на аноде и в объеме электролизера с конструкцией № 2. Различие в температурах для различных участков электролита может достигать ~70°C (рис. 4). Столь значительный перепад температур в довольно ограниченном замкнутом объеме жидкого электролита может вызвать образование изолированной тепловой волны (теплового солитона) [17]. Солитон будет нагреваться до определенного уровня в области под катодной корзиной, а затем двигаться по холодному пространству в сторону какого-либо из анодов с уменьшающейся амплитудой. В области под корзиной устанавливается отрицательное значение потенциала (рис. 5). Наиболее высокие значения потенциала сосредоточены в областях, прилегающих к анодам, и над катодной корзиной.
Рис. 7.
Распределение плотности тока на поверхности анода, обращенной к катоду, в конструкции № 2: представлены две смежные анодные пластины.
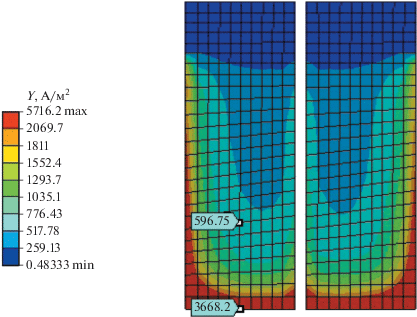
Полученные данные по каждой конструкции обобщены в табл. 2, где ${{T}_{{max}}}$ – максимальная температура в активной зоне электролизера, ${{J}_{{max}}}$ – максимальная плотность тока на аноде, ${{J}_{{mid}}}$ – плотность тока в центральной части поверхности анода, ${{U}_{{{\text{ohm}}}}}$ – вычисленное омическое падение напряжения, $\kappa $ – перенапряжение (В) на аноде, рассчитываемое по формуле [5, 6]
где $A = 0.5376,$ $B = 0.1495.$ Полное напряжение $U$ определяется следующим образом: где ${{U}_{{{\text{react}}}}}$ – напряжение разложения.Таблица 2.
Результаты расчета тепловых и электрических полей электролизера с различной конфигурацией анодов
${{T}_{{max}}},$ °С | ${{J}_{{max}}},$ A/см2 | ${{J}_{{mid}}},$ A/см2 | ${{U}_{{{\text{ohm}}}}},$ В | $\kappa ,$ В | ${{U}_{{{\text{react}}}}},$ В | $U,$ В |
---|---|---|---|---|---|---|
700 | 0.38 | 0.05 | 0.289 | 0.055 | 2.46 | 2.804 |
669 | 0.37 | 0.06 | 0.254 | 0.049 | 2.763 | |
682 | 0.36 | 0.065 | 0.261 | 0.044 | 2.765 | |
683 | 0.33 | 0.08 | 0.247 | 0.028 | 2.735 | |
671 | 0.31 | 0.09 | 0.248 | 0.018 | 2.726 | |
690 | 0.30 | 0.03 | 0.300 | 0.012 | 2.772 | |
688 | 0.605 | 0.12 | 0.318 | 0.176 | 2.954 |
Благодаря пристенной турбулентности, развиваемой в электролите ниже катодной корзины, в этой области жидкой проводящей среды наблюдается существенное усиление плотности тока (рис. 6). Это оказывает существенное влияние на турбулентный перенос тепла [18], и, как следствие, объем электролита под катодной корзиной перегревается (рис. 4). Наибольшие плотности токов присутствуют на несопряженных краях анодов, а также в их нижней части, находящейся ближе к дну электролизера (рис. 7). Более широкие зоны высоких плотностей тока расположены в несопряженных нижних углах анодных пластин.
ОБСУЖДЕНИЕ РЕЗУЛЬТАТОВ
При выборе оптимальной конструкции электролиза, предназначенного для переработки ОЯТ, следует избегать значительных локальных перегревов, а также участков на аноде, в которых плотность тока достигает 0.5 A/см2 и более, так как при таких плотностях тока на аноде выделяется Cl2, появление которого в процессе крайне нежелательно. Также значение омического падения напряжения необходимо минимизировать, чтобы уменьшить полное напряжение в электролизе, что в свою очередь сокращает потребление электроэнергии. По этим критериям в данной модели оптимальной будет конструкция анода № 2, которая отличается наименьшим омическим падением напряжения на электродах и в пространстве между ними, а также наименьшей максимальной температурой в активной зоне электролизера. При этом получаемые значения плотности тока не приводят к образованию хлора на анодах. Однако из рис. 7 видно, что на ребрах анодной пластины присутствуют локальные повышения плотности тока. Во избежание образования Cl2 на аноде предлагается выполнить скругление анодных пластин в указанных областях.
Основной особенностью полученных результатов является высокая плотность тока под катодной корзиной и низкая – над корзиной с ОЯТ. Это происходит по нескольким причинам. Для рассматриваемых конструкций электролизера плотность тока снаружи заполненной ОЯТ корзины должна быть существенно больше плотности токов вблизи анодов. Это связано с тем, что площадь активной поверхности восьми анодов превосходит таковую у катодной корзины в 1.98 раза для конструкций №№ 1–3 и 6, в 2.37 раза – для конструкции № 4, в 2.76 раз – № 5 и, наконец, в 1.02 раза – № 7. Однако в силу специфики взаимного расположения электродов, а также присутствия слабо проводящей пористой среды в корзине, плотность тока в окрестности корзины распределяется крайне неравномерно. Высокая плотность тока характерна для области под днищем корзины, а также для пространства около нижней части ее боковой поверхности и для окрестности нижней части анодов.
Такое распределение плотности тока можно объяснить следующим образом. Рассмотрим сначала задержку ионной проводимости при прохождении тока по загруженной UO2 катодной корзине. Электропроводность пористой среды, пропитанной электролитом, зависит от отношения массы твердого тела к массе содержащегося в нем электролита и особенно от условий пропитки. Как правило, очень низкая электропроводность погруженной в электролит пористой среды наблюдается до тех пор, пока пористость среды не достигнет величины в ~18% [19]. Этот результат можно интерпретировать и в такой форме: пропитка пористой среды электролитом начинается, когда пористость достигнет величины ~18%. Превышение порогового значения для проводимости приводит к ее экспоненциальному росту.
Прежде всего, электролит проникает в поры за счет капиллярных сил. Электролит, занимающий внешние поры, дает главный вклад в электропроводность пористого материала. В то же время внутренние нанопоры удерживают электролит внутри, не давая ему выйти из пористого материала. Причем доля задерживаемого электролита из-за потери непрерывного пути для ионов в пористой среде может достигать 50%. В действительности эффект снижения электропроводности пористой среды, образованной загруженными в катодную корзину таблетками диоксида урана, значительно усиливается за счет прохождения химических реакций, приводящих к образованию Li2O, а также выхода этого неустойчивого соединения из пористой среды в электролит.
Таким образом, корзина с ОЯТ представляет собой серьезное препятствие для прохождения ионов. Рассмотрим подробнее поверхностные явления, наблюдаемые в области под корзиной. Концентрация ионов на поверхности пористого материала (UO2) C * может быть представлена выражением [20]
где D – коэффициент диффузии ионов, C 0 – концентрация ионов в начальный момент времени.Ионы, диффундирующие из электролита в пористый UO2, расходуются электрохимической реакцией. Граничным условием на поверхности электрода может быть C 0 = 0, тогда выражение для плотности тока имеет вид
Данное выражение показывает, что возможен и обратный ток, т.е. от днища корзины вниз, если под днищем накапливается большое число ионов (C * > C 0). Этот ток уменьшается во времени как ${1 \mathord{\left/ {\vphantom {1 {\sqrt t }}} \right. \kern-0em} {\sqrt t }}.$ Вместе с поступающими из межэлектродного пространства ионами этот ток помогает собирать ионы под катодной корзиной. Плотность тока под корзиной оказывается очень высокой. Это вместе с сильным разогревом области, расположенной ниже корзины, является недостатком данных конструкций электролизера.Установка экранирующих керамических чехлов на аноды может сказаться на изменении плотности тока в нижней части катодной корзины, скорости расплава вблизи поверхности анодов, снижении значительных локальных перегревов элементов установки. В этом случае выход кислорода с поверхности расплава будет осуществляться преимущественно по керамическим цилиндрам, представляющим анодные чехлы.
ЗАКЛЮЧЕНИЕ
Выполненные расчеты показали, что изменение местоположения анодов и их толщины меняют максимальную температуру в активной зоне электролизера в пределах 4.6%, максимальную плотность тока до двух раз, плотность тока в центральной части поверхности анода в четыре раза, омическое падение напряжения на 28.7% и перенапряжение на аноде в 14.6 раза. При этом полное напряжение может изменяться в пределах 8.3%.
Показано, что конфигурация анодов из пластин с глубиной погружения ${{h}_{{{\kern 1pt} 1}}} = 120$ мм, толщиной ${{h}_{3}} = 10$ мм и межполюсным расстоянием ${{h}_{2}} = 60$ мм является оптимальной с точки зрения температурных и электрических факторов. При этом достигаются следующие значения основных параметров:
1) максимальная температура оптимальной конструкции составляет 669°С,
2) полное напряжение между анодом и катодом равно 2.763 В,
3) максимальная плотность тока на аноде устанавливается на значении 0.37 А/см2.
Вне зависимости от того, как размещаются друг относительно друга электроды, скругления на выступающих частях анодной пластины необходимы, чтобы избежать локального повышения плотности тока на аноде, приводящего к образованию Cl2 вместо O2.
Настоящие расчеты проведены для упрощенной модели электролизера с целью выявить главные закономерности его функционирования. С одной стороны, такая модель облегчает понимание происходящих в функционирующем электролизере процессов, а с другой – не отражает полной реальной картины восстановления ОЯТ. Подобный реальный физический эксперимент выполняется в герметическом боксе, защищающем исследователя от вредных испарений химических реагентов, образующихся при высокой температуре (650°C) проведения эксперимента. В этих условиях исследовать гидродинамические свойства электролита, заполняющего резервуар, а также теплофизические и электрические свойства всех участков в действующем электролизере достаточно сложно. Положение усугубляется высокой коррозионной способностью присутствующей здесь жидкой и паровой сред. Проведение компьютерного моделирования позволяет более глубоко изучить процессы, происходящие в действующем электролизере, что дает возможность усовершенствовать его конструкцию. Многие явления, наблюдаемые при восстановлении ОЯТ, по-прежнему остаются мало изученными.
Работа выполнена в рамках реализации НИОКР “Разработка технологии и оборудования для пирохимической переработки ОЯТ реакторов на быстрых нейтронах” проектного направления “Прорыв”.
Список литературы
Choi E.-Y., Kim J.-K., Im H.-S., Choi I.-K., Na S.-H., Lee J.W., Jeong S.M., Hur J.-M. Effect of the UO2 Form on the Electrochemical Reduction Rate in a LiCl–Li2O Molten Salt // J. Nucl. Mater. 2013. V. 437. P. 178.
Hur J.-M., Hong S.-S., Lee H. Electrochemical Reduction of UO2 to U in a LiCl–KCl–Li2O Molten Salt // J. Radioanal. Nucl. Chem. 2013. V. 295. P. 851.
Sakamura Y., Kurata M., Inoue T. Electrochemical Reduction of UO2 in Molten CaCl2 or LiCl // J. Electrochem. Soc. 2006. V. 153. № 3. P. D31.
Choi E.-Y.,Won C.Y., Cha J.-S., Park W., Im H.S., Hong S.-S., Hur J.-M. Electrochemical Reduction of UO2 in LiCl–Li2O Molten Salt Using Porous and Nonporous Anode Shrouds // J. Nucl. Mater. 2014. V. 444. P. 261.
Choi F.-Y., Jeong S.M. Electrochemical Processing of Spent Nuclear Fuels: An Overview of Oxide Reduction in Pyroprocessing Technology // Prog. Nat. Sci.: Mater. Int. 2015. V. 25. № 6. P. 572.
Grazevicius A., Kaliatka A. Modelling of the Spent Fuel Heat-up in the Spent Fuel Pools Using One-dimensional System Codes and CFD Codes // Kerntechnik. 2017. V. 82. № 3. P. 316.
Gokselkinav A.D., Ayhan H., Ergun S. Thermal Analysis of Spent Nuclear Fuel Shipping Cask // Ann. Int. Conf. Nuclear Power for the People. V. 18. Bulgaria, 2013. 12 p.
González D., Rojas L., Rosales J., Castro L., Abel Gámez A., Brayner C., García L., García C., de la Torre R., Sánchez D. Computational Model for a High Temperature Electrolyzer Coupled to a HTTR for Efficient Nuclear Hydrogen Production // Int. Nucl. Atlantic Conf. INAC 2015. São Paulo: SP, Brazil, 2015.
Нигматулин Р.И. Основы механики многофазных сред. М.: ГИФМЛ, 1987.
Нигматулин Р.И. Динамика многофазных сред. Т. 1, 2. М.: ГИФМЛ, 1987.
Ландау Л.Д., Лифшиц Е.М. Теоретическая физика. Т. VI. Гидродинамика. М.: Наука, 2001.
Ландау Л.Д., Лифшиц Е.М. Теоретическая физика. Т. VIII. Электродинамика сплошных сред. М.: Наука, 2005.
Bates J.L., Hinman C.A., Kawada T. Electrical Conductivity of Uranium Dioxide // J. Am. Ceram. Soc. 1967. V. 50. № 12. P. 652.
Степанов Г.К., Трунов А.M. Электропроводность системы NiO–Li2O в интервале температур от 20 до 900°С // Изв. CO АН СССР. 1961. № 6. С. 67.
Van Artsdalen E.R., Yaffe I.S. Electrical Conductance and Density of Molten Salt Systems: KCl–LiCl, KCl–NaCl, and KCl–KI // J. Phys. Chem. 1955. V. 59. № 2. P. 118.
Чиркин В.С. Теплофизические свойства материалов. Спр. М.: Физматгиз, 1959.
Формалев В.Ф., Колесник С.А. О тепловых солитонах при волновом теплопереносе в ограниченных областях // ТВТ. 2019. Т. 57. № 4. С. 543.
Поляков А.Ф. Турбулентный теплоперенос при подавлении пристенной турбулентности и соотношение между теплоотдачей и сопротивлением трения // ТВТ. 2019. Т. 57. № 1. С. 94.
Mizuhata M., Kitamura M., Deki S. Nano-pore Effect on Ionic Conduction of Non-aqueous LiClO4 Solution Coexisting with Porous Solid Materials // Electrochemistry. 2003. V. 71. № 12. P. 1093.
Gelloz B., Bsiesy A., Gaspard F., Muller F. Conduction in Porous Silicon Contacted by a Liquid Phase // Thin Solid Films. 1996. V. 276. P. 175.
Дополнительные материалы отсутствуют.
Инструменты
Теплофизика высоких температур