Теплофизика высоких температур, 2020, T. 58, № 4, стр. 536-562
Плазменная утилизация в проблемах экологии (обзор)
Э. Е. Сон 1, *, М. Х. Гаджиев 1, Ю. М. Куликов 1
1 Объединенный инстиут высоких температур РАН
Москва, Россия
* E-mail: son.eduard@gmail.com
Поступила в редакцию 10.03.2020
После доработки 16.03.2020
Принята к публикации 30.03.2020
Аннотация
Обсуждаются современное состояние и актуальные вопросы плазменной утилизации. Описываются различные типы плазмотронов, применяемых при утилизации, технологические схемы действующих плазменных установок, а также плазмотрон с расширяющимся выходным электродом, характеристики оборудования, методы диагностики для создания эффективного генератора низкотемпературной плазмы и исследования воздействия высокоэнтальпийной плазменной струи, создаваемой плазмотроном постоянного тока, на мишень из твердого материала. Приведены результаты, полученные методами скоростной визуализации, микропирометрии, лазерной профилометрии, спектроскопии и стереоскопии. Проанализированы данные о характере изменения во времени и пространстве поля температур на поверхности образца, данные о динамике убыли материала, об изменениях параметров (температура и концентрация электронов, температура тяжелых частиц) набегающей на образец плазменной струи. Собранные теоретические и экспериментальные результаты и инженерные решения могут использоваться для проектирования различных генераторов низкотемпературной плазмы с мощностью до 1 МВт и выше.
ОГЛАВЛЕНИЕ
Введение
1. Современное состояние плазменной переработки отходов
2. Типы плазмотронов, применяемых для утилизации отходов
3. Технологические схемы плазменных установок для утилизации отходов
4. Плазменная утилизация с использованием плазмотрона с расширяющимся каналом
5. Диагностический комплекс для исследования взаимодействия плазменной струи с образцом
6. Численное моделирование и оптимизация ГНП азота с расширяющимся каналом
7. Генератор низкотемпературной плазмы азот-пропановой смеси
Заключение
Список литературы
ВВЕДЕНИЕ
Плазменная утилизация отходов как новый метод переработки начал развиваться в 1980–90-х гг. в связи с выбросами промышленных отходов при различных видах производства материалов, на ТЭЦ при генерации электрической энергии, различных производствах с синтезированием хлорных соединений и фреонов, которые связаны с образованием стойких загрязнителей, трудно разрушаемых горением. Это приводило к необходимости использования более высокоэнергетических источников энергии, в том числе плазменных. Например, для Э.Е. Сона знакомство с плазмеными методами началось в 1990 г., когда появилась возможность не только познакомиться с плазменными методами в лучших зарубежных лабораториях, но и поработать в творческих коллективах. Первый такой опыт был в Великобритании, в лаборатории Таунсенда (именно в этой лаборатории родилась физика неравновесной плазмы), которой в конце 1980-х гг. руководил Дж. Даттон11. После успешной работы в Великобритании, Кембридже в DAMPT (английская школа по гидродинамике и турбулентности) были работы по гранту Фулбрайта в 1991 г. в США (Massachusetts Institute of Technology, MIT) с Л. Бромбергом (по мнению многих специалистов, лучшим изобретателем в области физики плазмы в мире), Р. Петрассо (лауреатом премии Эдварда Теллера 2018 г.) и другими специалистами мирового уровня в области физики плазмы, что дало импульс к исследованиям в данной области. Впервые тогда были предложены гибридные плазменные реакторы, новые методы диагностики, актуальные и сегодня, не говоря уже о численном моделировании плазмы, кинетики, плазмохимии, представляющих основы применения плазмы в самых различных областях.
Идея настоящего обзора появилась на основе не только работ, выполненных в MIT, за которыми последовали работы сотрудников кафедры физической механики МФТИ Александрова Н.Л., Добкина С.В., Вахрамеева К. и других, но и следующих проектов, выполненных в России: проекты по удалению хлорорганических отходов совместно с Центром Келдыша (Коротеев А.С., Свирчук Ю.С.), где плазменные методы оказались практически единственными результативными для удаления устойчивых хлорных соединений; работа по гранту РФФИ, ведущаяся в настоящее время, и другие проекты в этом направлении совместно с различными научными коллективами: Шарафутдинов Р.Г. – ИТ СО РАН, Кунаков С.К. – ИЯФ, КазГУ, Казахстан) и др. Перечисленные работы практически не вышли в свет. Поэтому в настоящее время ввиду важности работ по санитарии и утилизации продуктов техногенного производства представляется полезной публикация работ, выполненных в разное время, но не потерявших актуальности и сейчас, а также их сравнение с современными достижениями.
Самыми распространенными способами утилизации отходов во всем мире являются накопление (самый неэкологичный вариант), сжигание, сортировка и переработка. Термические методы являются одним из самых действенных способов переработки отходов, поскольку решают проблему уничтожения вредных веществ, а не откладывают ее, что имеет место в случае захоронения, капсулирования или контейнеризации опасных веществ. Вместе с тем большинство термических методов использует процессы сжигания топлива, происходящие с образованием продуктов сгорания, среди которых вследствие множества протекающих химических реакций присутствуют различные, в том числе и высокотоксичные соединения. Уловить и нейтрализовать их – достаточно трудоемкий, энергозатратный процесс, требующий создания специального оборудования.
В связи с этим некоторые специалисты по охране окружающей среды настороженно относятся к уничтожению таким способом ряда отходов. Более прогрессивным, энерго- и ресурсоэффективным, безопасным для окружающей среды видом переработки промышленных и бытовых отходов является плазменный метод. Это связано с тем, что при температуре 4000–5000 К происходит расщепление любого вещества до электронов, ионов и радикалов. Степень разложения при этом может достигать 99.9998%. Таким образом возможно преобразовать различные виды топлива, такие как промышленные, медицинские или муниципальные отходы, низкосортные угли, биомасса, в синтез-газ [1].
С точки зрения выбора оптимального процесса переработки отходов можно предложить следующую классификацию [2].
1. Загрязнения с высокой долей органических веществ и высокой теплотой сгорания. Задействование этой теплоты для производства синтез-газа, появляющегося при плазменной газификации, позволяет организовать процесс его последующего сжигания и генерацию пара. В лабораторных условиях для проверки возможности получения синтез-газа из твердых отходов часто используется целлюлоза.
2. Загрязнения с высокой концентрацией галогенов (бóльшая часть пластмасс), которые требуют высоких температур в зоне реакции, а также последующего гашения продуктов разложения в воде. Быстрое гашение отходящих газов обычно используется для управления составом смеси.
3. Неорганические твердые отходы, из которых могут быть извлечены полезные составляющие, а их объем может быть уменьшен плавлением (спеканием), окислением и иммобилизацией в беззольный шлак.
В настоящее время плазменный метод еще не получил широкого распространения, в первую очередь из-за отсутствия надежных и эффективных плазмотронов. Некоторой альтернативой могут служить СВЧ-плазмотроны, используемые в реакторах и имеющие большой ресурс. Однако для достижения приемлемого теплового КПД плазменного потока, достаточного для полного расщепления отходов, необходимо затратить значительно больше электроэнергии, чем для плазмотрона постоянного тока. Кроме того, существено усложняется и конструкция источников питания для данного типа плазмотронов. Высокие тепловые потоки в плазме, генерируемой плазмотроном постоянного тока, позволяют достичь благоприятных условий для реагирующих компонентов, необходимых для проведения реакций окисления, хлорирования, фторирования, испарения и разделения радиоактивных компонентов. Селективное хлорирование и фторирование оксидов используется для обработки металлических сплавов, загрязненных радиоактивными веществами. Примерами являются фторирование и газификация урана из строительного мусора, фторирование кобальта и его последующее удаление водой.
1. СОВРЕМЕННОЕ СОСТОЯНИЕ ПЛАЗМЕННОЙ ПЕРЕРАБОТКИ ОТХОДОВ
Любой материал, подвергнутый воздействию термической плазмы ($T\sim {{10}^{4}}$ К), будет разлагаться на свои элементарные составляющие, что делает целесообразным использование плазменной переработки для разрушения стойких токсичных химических соединений. В сравнении с существующими технологиями обработка термической плазмой имеет следующие преимущества.
1. Высокие температуры вызывают быстрый и полный пиролиз опасных органических загрязнений, а также плавление или стеклование неорганических отходов, что приводит к сильному уменьшению объема отходов и капсулированию трудноразрушаемых загрязнений.
2. Высокая плотность энергии, получаемая в плазменном реакторе (порядка 200 ГДж/м3), позволяет использовать установки меньшего размера при схожей производительности, таким образом снижая капитальные затраты и позволяя возводить мобильные комплексы небольшого размера.
3. Использование электрических дуг уменьшает полный расход газа вместе с необходимостью подогревать его избыточное количество при сжигании. Как следствие, снижаются требования к производительности систем по переработке газа, отходящего из плазменного реактора. Также имеется достаточно большой выбор плазмообразующих газов, позволяющих организовать различные химико-технологические процессы во время обработки.
4. Компактные размеры и высокая плотность энергии дают возможность существенно сократить времена выхода на режим и отключения.
5. Ультрафиолетовое излучение, создаваемое плазмой, приводит к ускорению разложения отходов, что оказывается особенно действенным при пиролизе органических хлоридов.
6. Использование электричества в качестве источника энергии позволяет отделить процесс тепловыделения от процесса кислородного окисления, он оказывается не зависящим от расхода окислителя или воздуха [2].
Высокие температуры [3, 4] в реакторах на основе термической плазмы обеспечивают короткое время температурной обработки, что позволяет достичь высокой производительности переработки отходов. При этом главным недостатком остается высокая цена в сравнении с другими технологиями утилизации, вызванная в первую очередь использованием электричества в качестве источника энергии. Кроме того, управление плазменным процессом требует задания значительно большего числа параметров в сравнении с традиционными (более распространенными) процессами переработки и существенно большей степени автоматизации всего процесса. Экономическую эффективность плазменных методов переработки может повысить плазменный синтез каких-либо побочных веществ с высокой добавленной стоимостью.
Требования обеспечения безопасности окружающей среды делают необходимым уничтожение накопленных стойких органических загрязнителей (СОЗ), каковыми являются полихлорированные дифенилы (ПХД). ПХД представляют собой [5] широкий класс соединений и образованы замещением одного или нескольких атомов водорода в исходном веществе – дифениле, который в свою очередь относится к ароматическим углеводородам. Всего в ПХД атомы хлора могут занять 209 положений, что дает большой класс родственных веществ. ПХД являются слабогорючими веществами с хорошими электроизоляционными свойствами. Они широко использовались в качестве хладагентов и смазок в трансформаторах, конденсаторах и другом электротехническом оборудовании. ПХД могут содержаться и в старых приборах: люминесцентных светильниках, электрических приборах, содержащих конденсаторы в печатных платах, старом масле для микроскопов и гидравлических жидкостях. Данные соединения могут встречаться в воске, теплообменных жидкостях, масле для резки, антипиренах, изоляционной бумаге для электрических кабелей, клеях, средствах для удаления пыли, специальных смазочных составах, красках, масле для вакуумных насосов, гидроизоляционных материалах и некоторых видах пластмасс. По оценкам экологов, запасы СОЗ включают более миллиона тонн ПХД, распределенных по всему миру, и более 100 тыс. тонн устаревших пестицидов в странах, не являющихся членами Организации экономического сотрудничества и развития. Установлено, что 31% от общего объема производства ПХД в мире (370 тыс. т) уже выпущено в окружающую среду. Более 60% остаются в использовании или на хранении и только 4% уничтожены.
Методы утилизации ПХД включают в себя высокотемпературное сжигание и различные химические методы. В настоящее время трудно сказать, какая из технологий является предпочтительной. На самом деле, в большинстве случаев именно форма отходов (агрегатное состояние), а не конкретное соединение или их композиция определяют применимость конкретной технологии обработки. Неорганические пестициды или жидкие отходы от производства пестицидов, содержащие около 5% органики, могут быть отверждены и переведены в стабильную форму перед захоронением на свалке. Современные мусоросжигательные заводы имеют достаточно разнообразную конструкцию и оснащаются плазменными реакторами, вращающимися печами, камерами сгорания с дожигателями, башенными охладителями и системой контроля загрязнения воздуха. Эффективность удаления достигает 99.99%. Для ПХД и диоксинов в высокотемпературных мусоросжигателях может быть достигнута эффективность разрушения и удаления 99.9999%.
2. ТИПЫ ПЛАЗМОТРОНОВ, ПРИМЕНЯЕМЫХ ДЛЯ УТИЛИЗАЦИИ ОТХОДОВ
Генераторы низкотемпературной плазмы (ГНП) используются в различных приложениях [3]: сварка, резка, напыление под атмосферным давлением или под небольшим вакуумом, обработка поверхности прямой дугой, нагревание в электропечах, увеличение чистоты металлов и сплавов, исследования в индуктивно связанной плазме, металлургическое извлечение, переработка железной пыли, производство оптоволокна. Большинство этих приложений было развито со слабыми знаниями деталей химического взаимодействия между плазмой и обрабатываемым материалом (за исключением электрометаллургии, очистки металлов, производства оптоволокна).
ГНП с косвенной дугой [2] создают высокоскоростной плазменный поток, обдувающий отходы. Плазма, истекающая из водоохлаждаемого плазмотрона, имеет максимальную температуру (10–14) × 103 К в зависимости от мощности плазмотрона, его конструкции, типа плазмообразующего газа. Однако вследствие рекомбинации заряженных частиц в плазме снаружи плазмотрона обрабатываемый материал не подвергается воздействию таких высоких температур. Целесообразнее говорить о средних значениях скорости, температуры и энтальпии плазменного потока. В плазмотронах с косвенной дугой, как правило, 10–30% электрической мощности уходит на потери в водоохлаждаемые части устройства. Для обеспечения устойчивой работы плазмотрона часто используется вихревая стабилизация (закрутка) наряду с холодным или точечным (button-type) катодом, утопленным в медь. Чтобы быть достаточно эффективной, закрутка должна быть большой, диаметр ввода должен быть в четыре–шесть раз больше диаметра анода, а скорости при этом достигают 200 м/с.
В случае прямой дуги воздействие на обрабатываемый объект оказывается гораздо интенсивнее вследствие нагрева диффузионным движением электронов, а также ультрафиолетовым излучением. Некоторые дуговые печи по переработке отходов вначале используют косвенную дугу [2], а затем, когда образуется проводящая среда, переходят на режим с прямой дугой, который позволяет получить более интенсивные тепловые потоки.
Оба типа плазмотронов (и с прямой, и с косвенной дугой) могут использоваться как с термоэмиссионными, так и с водохлаждаемыми “холодными” катодами. Разработка специальных электродных сплавов позволяет увеличить время их жизни при работе на воздухе до 1000 ч.
Большинство современных плазмотронов для утилизации работают на постоянном токе, так как они создают условия для лучшего контроля поведения дуги в потоке и в точке анодной привязки, уменьшают или сокращают необходимость коррекции коэффициента мощности, а также установки фильтров помех для защиты внешней электросети. Иногда используются азот или углекислый газ, позволяющие достичь больших напряжений горения дуги, тем самым увеличивая КПД плазмотрона.
Очень высокие температуры в плазменной струе дают возможность использовать плазменные реакторы для обработки мусора неизвестного или переменного состава [6]. Короткое время прохождения реакции позволяет получить высокую эффективность преобразования. Для обеспечения интенсивного смешения необходимы высокие входные скорости и малые диаметры сопла в смесительной камере. Таким образом, эти реакторы подходят для обработки газов, жидкостей, в том числе с высоким содержанием частиц. Другим путем для получения интенсивного смешения является использование турбулентных плазменных струй. В этом случае объект переработки инжектируется в реактор, а не непосредственно в струю.
Идеальный плазмообразующий газ для переработки должен удовлетворять следующим условиям:
– уже содержаться в отходах;
– не вызывать дополнительных загрязнений;
– не требовать сепарации после реакции;
– не требовать специальных мер предосторожности;
– повышать эффективность всего технологического процесса переработки;
– иметь высокую теплоемкость;
– уменьшать скорость износа электродов в ГНП;
– быть нетоксичным и не создавать токсичных производных соединений;
– увеличивать эффективность работы реактора;
– быть легкодоступным и дешевым.
К сожалению, ни один из имеющихся плазмообразующих газов не отвечает в полной мере всем этим требованиям. Например, высокое содержание азота представляет собой определенный технологический недостаток, так как он непосредственно не участвует в процессе химического разрушения мусора. Чистый кислород существенно увеличивает эффективность процесса разрушения, однако обращение с ним гораздо труднее и приводит к ускоренному износу оборудования. Атомарный водород существенно способствует разрушению галоген-углеродных связей и вызывает ускоренное разложение углеводородов.
Энергоэффективность переработки может быть значительно повышена при использовании водяной плазмы, когда большую роль в теплопереносе играет пар. Использование молекулярного водорода также заслуживает внимания, так как он имеет большую энергию связи и его рекомбинация приводит к выделению большого количества теплоты, а атомарный водород является химически активным.
Разрушения электродов можно избежать, если использовать радиочастотный индукционный плазменный реактор. В таком устройстве плазма создается током высокой частоты (2–27 МГц), протекающем в катушке, окружающей рабочую камеру. Для работы такого плазмотрона требуется специальная методика ввода отходов в камеру плазмообразующего газа. Радиочастотные плазмотроны могут успешно использоваться для разложения опасных жидкостей, которые впрыскиваются в область разряда.
Мощности [3] ВЧ-плазмотронов варьируются от 0.5 кВт до 1 МВт, а частоты – от 9.6 кГц (для мощностей меньше 200 кВт) и до 40 МГц. Большинство промышленных источников питания (до 150 кВт) работает на частоте 2.6 МГц. Плазмотрон состоит из двух концентрических трубок, близко расположенных друг к другу. Внешняя трубка ограничивает плазму. Для маломощных плазмотронов трубка делается из кварца и охлаждается сжатым воздухом или водой. Для мощностей от 30 до 150 кВт трубка выполняется из керамического материала, охлаждаемого водой, при еще больших мощностях она заключается в водоохлаждаемые медные упоры – пальцы (fingers).
Пальцы исполняют роль трансформаторов, связывая плазму с полем катушки. Внутренняя трубка также исполняется из кварца или керамики и находится на уровне первого витка индукционной катушки. Для получения правильного импеданса используются корректирующие кабели нужной длины, таким образом, сама установка является неподвижной в отличие от плазмотрона постоянного тока.
В сравнении с последними тепловой КПД составляет от 40 до 60%. Основные потери происходят на источнике питания, также имеются потери на индукцию между плазмой и катушкой, которые являются функцией отношения между радиусом плазмы и радиусом индукционной катушки. Потери происходят и вследствие передачи энергии стенкам ограничивающей трубки.
При одной и той же величине потерь внутренний диаметр ВЧ-плазмотрона примерно на порядок больше диаметра газового тракта плазмотрона постоянного тока. В ВЧ-плазмотроне достигаются температуры 6000–10 000 К против 7000–14 000 К для плазмотрона постоянного тока. Важное отличие состоит в скоростях плазмы: в ВЧ-плазмотронах она не превышает 100 м/с, что существенно меньше, чем в плазмотронах постоянного тока.
Основной нагрев происходит в поверхностном слое плазмы вследствие скин-эффекта. Важно помнить, что электропроводность плазмы пропорциональна концентрации электронов и для большинства используемых газов, за исключением чистого гелия, проводимость имеет существенное значение при температурах 6000–7000 К при атмосферном давлении.
Следует отметить, что более 99.99% из имеющихся на сегодняшний день плазменных установок работают на постоянном токе.
3. ТЕХНОЛОГИЧЕСКИЕ СХЕМЫ ПЛАЗМЕННЫХ УСТАНОВОК ПО УТИЛИЗАЦИИ ОТХОДОВ
Накопленный опыт создания плазменных установок по переработке (твердых) отходов показал, что подобные системы должны состоять из нескольких основных узлов [2]:
1) плазменного реактора со сбором расплавленного металла снизу (если это необходимо), источника питания, системы водяного охлаждения, системы сбора данных и управления плазменным реактором;
2) вторичной камеры сгорания, в которой скапливаются продукты разложения при достаточно высокой температуре для полного прохождения реакций и газификации сажи;
3) камеры для гашения продуктов переработки – в зависимости от типа загрязнения (обычно водяная), чтобы предотвратить формирование диоксинов и фуранов;
4) циклонного фильтра для удаления частиц, скруббера для поглощения кислотных газов;
5) сульфидного поглотителя галогенов, высокоэффективных фильтров или осадителей для удаления микрочастиц.
На рис. 1 показана схема промышленной установки для пиролиза медицинских отходов. Тепловой источник для печи представляет собой работающий в режиме прямой дуги плазмотрон мощностью 300 кВт со вторым электродом в виде расплавленного до этого плазмотроном поддона (или ковша) жидкого железа при температуре 2000°С. Производительность установки составляет примерно 250 кг/ч. Медицинские отходы загружаются в верхнюю секцию печи, а затем падают в область плазменной дуги, где происходит их пиролиз с образованием таких устойчивых газов, как водород, оксид углерода, метан и др. Металлические включения или включения, содержащие соединения кремния, расплавляются, причем более легкая фракция будет плавать на поверхности ковша. Периодически из него сливаются расплавленный металл и другой шлак.
Рис. 1.
Схема установки для пиролиза медицинских отходов: 1 – канал ввода медицинских отходов; 2 – выход смеси пиролизных газов и буферного природного газа; 3 – твердые медицинские отходы; 4 – факел плазмотрона; 5 – плазмотрон; 6 – ковш с расплавом твердых отходов, а также система их отведения; 7 – ввод топливного газа.
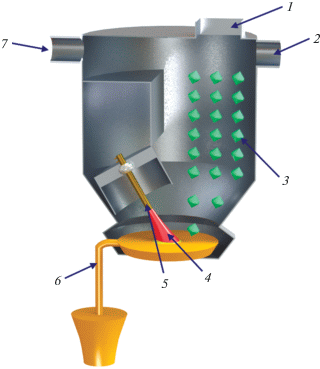
Реактор для плазменного пиролиза компании Вестингауз (рис. 2) состоит из одного плазмотрона с косвенной дугой мощностью 1 МВт [3], а также канала реактора, выложенного футеровкой, через который продукты разложения попадают в больший резервуар, откуда они уже направляются в скруббер (поглотитель газов). Данный плазмотрон состоит из двух цилиндрических водоохлаждаемых электродов, имеющих почти одинаковый диаметр. В небольшой зазор между ними поступает плазмообразующий газ (воздух). Магнитное поле смещает точку привязки дуги, уменьшая износ электродов.
Рис. 2.
Схема плазмотрона с коаксиальными электродами: 1 – ввод ПХД-содержащего газа, 2 – кольцевой вольфрамовый катод, 3 – кольцевой медный анод, 4 – реактор, 5 – скруббер, 6 – ввод воды, 7, 8 – каналы отвода продуктов гашения.
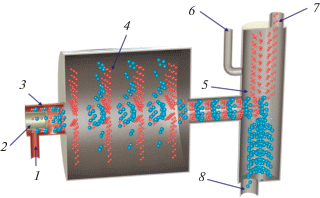
В [6] использовался трехструйный плазменный реактор для разложения жидких токсичных отходов в безвредные вещества. Поток жидких отходов инжектировался в три плазменные воздушные струи в конической или цилиндрической смесительной камере и проходил через цилиндрический реактор. Анализ исходящих газов показал полное разрушение органических веществ. Пиролиз органических отходов существенным образом зависит от времени обработки плазменной струей и, соответственно, времени реакции. Короткие времена реакции (от 0.001 до 0.01 с) не позволяют конденсироваться углероду, а значит, образовываться саже, а также формировать такие соединения, как бензин.
Вследствие очень высокой и почти постоянной температуры смешение плазменного газа с потоком мусора происходит почти сразу за выходом из смесительной камеры на дистанции 2.4–3 калибра.
В работе [7] описан индукционный плазмотрон, а также достоинства PERC-процесса переработки опасных, в том числе военных, отходов. В данном индукционном плазмотроне могут быть достигнуты температуры от 6000 до 17 000 градусов, в нем нет движущихся частей, разрушаемых электродов. Система работает на частоте от 330 до 440 кГц. Потребляемая мощность составляет 750 кВт. В плазменном реакторе могут создаваться различные среды: инертная (бескислородная), восстановительная, окислительная – может проводиться паровой риформинг, крекинг. Например, термическое разрушение азотсодержащего ракетного топлива – несимметричного диметилгидразина в установках по сжиганию приводит к появлению углекислого газа, воды и оксидов азота. В PERC-процессе по схеме парового риформинга происходит его переработка в оксид углерода, водород и азот. Монооксид углерода и водород могут быть отделены от азота путем создания синтез-газа. Кроме того, эти реагирующие вещества могут быть использованы для производства метанола, уксусной кислоты, аммиачных удобрений, продуктов нефтеперегонки.
Установлено, что при переработке токсичных материалов максимальная концентрация оксидов азота в отходящих газах находится в пределах 10–43 ppm. Установка с вакуумным осциллятором в качестве источника питания работоспособна в диапазоне вкладываемой мощности 20–750 кВт. КПД находится в пределах 15–27%. Таким образом, передаваемая плазмотроном в плазму мощность может составлять до 200 кВт. Производительность установки достигает 115 кг/ч. В работе [8] детально изложен проект плазмотрона постоянного тока для переработки отходов мощностью до 200 кВт, максимальным напряжением в дуге до 1000 В, током 50–200 А, объемным расходом газа 100 м3/ч с вольфрамовым катодом и медным анодом диаметром 12 см и длиной 25 см. Расход воды в системе охлаждения составлял до 4 м3/ч.
Для изучения экспериментально наблюдаемых явлений необходимо [9] также и трехмерное моделирование газовой фазы в реакторе с термической плазмой. На его основе авторы статьи разработали плазмохимический реактор (рис. 3) для переработки медицинских (инфекционных) отходов. Система должна удовлетворять общим требованиям по содержанию органического углерода (TOC) в термообработанных отходах – не более 3%.
Рис. 3.
Общее устройство плазменного ректора – взаимное расположение плазмотрона, системы подачи и входного отверстия для подачи кислорода: 1 – шнековый конвейер, 2 – зона плазменной реакции, 3 – плазмотрон, 4 – кислородная линия, 5 – канал отвода шлака, 6 – зона концентрации твердого расплава.
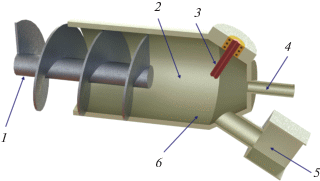
Особенностью реактора является наличие дополнительного регенеративного контура для отработанного газа: после нескольких стадий переработки (скруббер, водяной теплообменник, компрессор) газ снова проходит через плазмотрон. Такой способ организации газового тракта представляется выгодным с экономической точки зрения, так как позволяет снизить расход плазмообразующего газа. Авторами разработан “плазмотрон с обратным током газа” (рис. 4), в котором сильная тангенциальная закрутка газа сочетается с конфузорным газовым трактом.
Рис. 4.
Организация дополнительного ввода газа в плазмотрон: 1 – катод, 2 – зона вторичной закрутки, 3 – зона первичной закрутки, 4 – направление движения основного потока газа, 5 – анод, 6 – дуга, 7 – кожух катода.
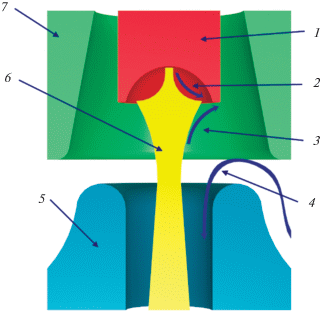
Рис. 5.
Принципиальная схема реактора для переработки медицинских отходов: 1 – отверстие для ввода мусора, 2 – загрузочный канал, 3 – основной реактор, 4 – плазмотрон, 5 – канал отвода газов, 6 – вторичная реакционная камера, 7 – плазмотрон, 8 – вытяжной вентилятор, 9 – скруббер, 10 – бак и линии подачи воды.
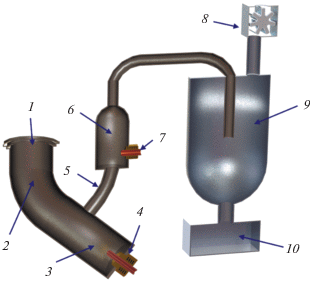
Кроме того, генерируется дополнительная закрутка ниже по течению, что приводит к сильному охлаждению дуги и увеличению плотности тока. В соответствии с правилом правой руки сила Лоренца действует в направлении оси симметрии и увеличивает магнитное давление в этом месте. Это приводит к появлению компоненты скорости внутри дуги в направлении, противоположном основному потоку, что и наблюдается экспериментально. Другим эффектом является возникновение вторичного вихря в окрестности прикрепления дуги к катоду. Если вольфрамовый стержень новый (плоская вершина), то этот вторичный вихрь вызывает повышение эрозии катода и появление выемки. Однако после этого эрозия катода существенно уменьшается. Концентрации паров вольфрама или его оксидов становятся равновесными, и процесс эрозии почти полностью прекращается.
Поле скорости внутри плазмотрона является завихренным, что необходимо для вращения дуги. Использование лазерной допплеровской анемометрии позволило получить реальный профиль скорости в устройстве. Эти результаты показали, что существенными являются только тангенциальная компонента скорости в окрестности выходного сечения плазмотрона.
Моделирование проводилось в программном комплексе FloTran на основе решения сопряженной системы дифференциальных уравнений в частных производных, описывающей законы сохранения массы, импульса и энергии. Кроме того, использовалась k–ε-модель турбулентности, решение проводилось с помощью алгоритма SIMPLE и метода конечных элементов.
Что касается состава отработанных газов, то моделирование выполнялось с использованием 100% объемной концентрации диоксида углерода, так как в работающем процессе его концентрация должна достигать 70–80 об. %. В расчете учитывалась зависимость вязкости, плотности, теплопроводности и других материальных коэффициентов от температуры в диапазоне $273 \leqslant T \leqslant 6500$ К с учетом эффектов термической диссоциации. Проходящие химические реакции или межфазные взаимодействия не учитывались. Поэтому тепловыделение от химических реакций включалось в энергетический баланс в виде специальной зоны тепловыделения. Стенки водоохлаждаемого реактора моделировались с помощью коэффициента теплопередачи. Когда кислород достигает смесительной камеры, он нагревается очень быстро и реагирует с горячими продуктами разложения, однако детали этого процесса еще недостаточно изучены. Для лучшей аппроксимации поведения реагирующего кислорода при высоких температурах моделировались два режима: холодная и горячая инжекция.
Установлено, что предпочтительной является подача кислорода в камеру при достаточно высокой температуре, что позволяет увеличить скорости движения, улучшить перемешивание и ускорить протекание реакции. Подача вдоль стенки оказывается нежелательной, так как происходит растяжение зоны реакции или даже ее перенос в другие узлы установки (кислород стремится к выходу из камеры). В работе [10] представлены результаты анализов выбросов плазменной установки при переработке жидких отходов, зараженных почв. Приводятся результаты по остаточному содержанию тяжелых металлов.
Введение дополнительных ограничений на традиционные технологии сжигания мусора в некоторых странах (Австралия) открыло новые возможности для внедрения процессов плазменной переработки [11].
Технологический процесс PLASCON, в частности, используется для утилизации 2,4-дихлорфеноксиуксусной кислоты, селективного гербицида. Поток отходов представляет собой жидкость с высоким содержанием органики, включающей дихлорфенолы, диоксины и другие органические вещества. Данная система демонстрирует 99.9999% эффективность разрушения и удаления, остаточные количества вредных веществ составляют менее ${{10}^{{ - 6}}}$ от вводимого количества, а выбросы диоксинов и фуранов – менее 0.01 нг/м3 токсического эквивалента, что значительно ниже самых строгих экологических стандартов в мире.
Если температуры перемешивания в камере плазмотрона достигают около 3000°С, то разрушение достигает 99.9999% (остаток – ${{10}^{{ - 6}}}$), а температуры около 2000°С дают 99.99% (остаток – ${{10}^{{ - 4}}}$).
Как уже отмечалось выше, эффективность плазменной переработки может быть существенно повышена, если в результате появляются продукты с высокой добавленной стоимостью. Подобная ситуация складывается при переработке автомобильных катализаторов [12] с целью извлечения платиноидных материалов или переработки пыли на металлургических заводах, извлечения других ценных металлов (цинка и меди), а также получения инертного шлака. Обработка пепла придает ему стекловидную или камневидную форму, пригодную для захоронения. Для этих целей разработан плазмотрон постоянного тока компании Tetronics Plasma Systems. Всего существует четыре модификации таких плазменных дуговых нагревателей: 1) плазмотрон с водяным охлаждением, 2) система с одним полым графитовым электродом, 3) система со сдвоенным водоохлаждаемым плазмотроном, 4) плазменный подогреватель с двумя полыми графитовыми электродами. Все модификации могут работать в режиме прямой и обратной полярности.
ГНП с прямой полярностью состоит из торированного вольфрамового или лантанированного катода, установленного в сопловую насадку. Сопло создает защитный кожух для катода и ограничивает зону прикрепления дуги на электроде. ГНП с обратной полярностью рекомендуется в некоторых случаях, в частности там, где вольфрамовое загрязнение недопустимо (плавление титана), или для подавления вредных электролитических эффектов (плавление стекла). Кроме того, он представляет возвратный электрод в плазменной системе с двумя ГНП. Сопловой блок аналогичен плазмотрону прямой полярности.
В сдвоенной системе используются одновременно два плазмотрона прямой и обратной полярности. Существует два способа сопряжения электрических дуг: расположение плазмотронов под углом друг к другу (прямая дуговая связь в газовой среде), либо соединение дуг через расплав. Двойной ГНП имеет ряд преимуществ по сравнению с обычными плазмотронами с одной плазменной дугой, а именно: 1) отсутствует твердотельный анод, контактирующий с обрабатываемым материалом, что позволяет избежать затрат на обслуживание нижнего электрода и возможного загрязнения расплава; 2) система особенно эффективна при нагревании газов и паров; 3) существенным образом увеличивается напряжение в дуге (и, следовательно, мощность); 4) возможен запуск в холодной, покрытой шлаком печи. Кроме того, обрабатываемые отходы, будь то жидкость, газ или твердое вещество, могут вводиться непосредственно в зону соединения дуг.
В работе [13] описана еще одна установка по переработке галогенированных химикатов. Эффективность разрушения превысила 99.999999% при обработке ПХД. Предварительные испытания с тетрахлорметаном показали эффективность разрушения, превышающую 99.99%. Процесс плазменного пиролиза включал создание плазмы в установке мощностью 250 кВт с температурой, превышающей 25000°C. Токсичный материал вводился в плазменную область со скоростью от 1 до 2 л/мин. В результате термохимической и фотохимической диссоциации токсичных материалов образуются атомы и ионы, которые впоследствии рекомбинируют, образуя в основном H2, CO, HCl и углерод в виде частиц. Нейтрализация HCl проводится с помощью NaOH. Сжигание H2 и СО должно в значительной степени уничтожить любые остаточные концентрации вредных веществ. Исследован также плазменный пиролиз для окончательной утилизации токсикологических отходов – тушек крыс, содержащих среднюю летальную дозу ПХД. В установке достигнута эффективность разрушения ПХД, превышающая 99.999999%, т.е. ниже аналитического предела 0.17 нг/г по содержанию в воде, используемой для гашения отходящих газов. Испытание пиролиза CCl4 также было весьма успешным: остаточная концентрация 4 нг/г в очищающей воде показала эффективность разрушения, превышающую 99.99%.
Работа [14] посвящена исследованию химического состава отходящих газов из плазменного реактора для потенциально радиоактивного технологического мусора следующего характерного состава: ПВХ – 48.5%, целлюлоза – 9.6%, неопрен – 17%, полиэтилен – 7.9%, латекс – 17%; с добавлением порошка малой насыпной плотности, содержащего изотопы Sr, Co, Ce и Cr. Скорость ввода отходов в печь с расплавленной базальтовой ванной весом 15 кг составляла 2.5 кг/ч. Что касается индикаторов, то Ce, Co и Sr в основном удерживаются в стекле. Отходящий газ до того, как он достигнет фильтра, содержит только 1 мас. % введенных индикаторов. Вследствие низкой стабильности Cs20 и высокой летучести только четверть массы (23.5%) Cs находится в стекле, 52.4% накапливаются на стенках печи, оставшаяся четверть покидает камеру, а 12.6% достигают фильтра.
Установка размещена в одном здании, которое содержит несколько подсистем, таких как станция приема барабанов, отсек для их хранения, печь с вращающимся поддоном, камера охлаждения расплавленных отходов, устройство для их упаковки, системы утилизации отходящих газов и обработки остаточной воды, несколько источников питания и пост управления. Сжигаемые материалы уничтожаются либо в чистых пиролитических условиях (только азот в качестве плазмообразующего газа), либо при частичном пиролизе (например, при добавлении 30% кислорода).
Для плавки металла печь работает как обычный плазмотрон с косвенной дугой и плазмообразующим газом – азотом. Отходящие газы покидают печь через нижнее отверстие и попадают во вторичную камеру сгорания, в которой газ пребывает не менее 2 с при температуре выше 1200°C до полного сгорания. Отходящие газы из вторичной камеры сгорания предварительно охлаждаются воздухом или водой до примерно 1100°C, чтобы избежать повреждения котла для их дожигания. В этом котле температура газа снижается приблизительно до 450°C. Часть отобранного тепла может быть использована для нагревания газа перед поступлением в катализатор. Затем газ быстро охлаждают до примерно 70°C, что предотвращает появление диоксинов. После системы охлаждения следует многоступенчатый скруббер. После него газы проходят через специальный НЕРА-фильтр, в котором в конечном итоге задерживаются оставшиеся опасные аэрозоли. Очищенные газы поступают на вентилятор, который создает пониженное давление во всей системе. Затем газ нагревается приблизительно до 300°C и поступает в катализатор DeNOx, в котором NOx и NH3 каталитически реагируют с азотом и водой. Производится постоянный контроль выбросов HC1, SO2, NOx, CO, CO2, пыли, O2, радиоактивности (рис. 6).
4. ПЛАЗМЕННАЯ УТИЛИЗАЦИЯ С ИСПОЛЬЗОВАНИЕМ ПЛАЗМОТРОНА С РАСШИРЯЮЩИМСЯ КАНАЛОМ
Многообразие механических и теплофизических процессов, протекающих в высокоскоростных потоках термической плазмы, предъявляет повышенные требования к уровню теоретических исследований и измерительному оборудованию. Расчет процессов тепломассообмена в высокоскоростных потоках горячего газа представляет собой проблему в энергетике, двигателестроении, авиации и космонавтике. Поэтому использование инертного аргона в качестве плазмообразующего газа на первом этапе работы с экспериментальной точки зрения позволяет наблюдать только продукты химического разложения исследуемого образца, что также упрощает численное моделирование. Кроме этого, отсутствие внутренних степеней свободы, а также высокое значение потенциала ионизации (15.76 эВ) позволяют достигнуть более высоких температур в плазменной струе по сравнению с другими газами, увеличить КПД всей системы и уменьшить эрозионное разрушение электродов. Важно, что аргон не играет заметной биологической роли и безопасен для человека. Большой цикл исследований свойств аргоновой плазмы стабилизированной дуги (электропроводности, вязкости, теплопроводности, оптических свойств) выполнен еще в начале 1960-х годов в ОИВТ РАН [15], и имеется большое количество данных при температуре плазмы до 30 000 К [16].
Таким образом, начальный этап исследований проведен в потоке химически неактивной плазмы. Для этого был разработан надежный ГНП, в разрядном промежутке которого создается высокоэнтальпийный плазменный поток инертных газов (аргона) с температурой от тысяч до десятков тысяч градусов.
В разработку основ таких плазмотронов могут быть положены ГНП с самоустанавливающейся длиной дуги для плазмообразующего газа азота с расширяющимся каналом выходного электрода [17, 18]. Выбор в пользу этого типа плазмотрона связан с тем, что такая конструкция обеспечивает горение дуги в ламинарном потоке при высокой скорости газа на входе в сопло, а также эффективность нагрева рабочей среды при малых тепловых потерях в водоохлаждаемые части устройства [17]. Ранее проведенные экспериментальные исследования генератора плазмы азота с расширяющимся каналом выходного электрода показали, что оптимальный угол раскрытия по направлению потока с углом 6° между образующей и осью канала приводит к повышению устойчивости дуги по сравнению с цилиндрическим каналом постоянного сечения [18]. При этом длина дуги уменьшается, а тепловые потоки в стенки становятся более равномерными. В расширяющемся канале при относительно больших скоростях газа дуговой столб вблизи анодной привязки дуги может занимать значительную часть поперечного сечения и протекание тока в этом случае осуществляется посредством коротких дуг между анодом и электропроводным ядром потока. Значительное уменьшение плотности тока и удельного теплового потока на анод способствуют уменьшению эрозии выходного электрода.
Недостатками большинства ГНП с продольным потоком газа и самоустанавливающейся длиной дуги является падающий характер вольт-амперной характеристики (ВАХ), так как с увеличением силы тока уменьшается длина дуги, приводящая к снижению напряжения горения дуги [19, 20]. Вследствие этого мощность дуги увеличивается гораздо медленнее, чем сила тока, в то время как ресурс ГНП во многом определяется величиной силы тока дуги. Падающая ВАХ влечет за собой также жесткие требования к источнику электрического питания для стабилизации дуги. В таких генераторах для стабилизации дуги и термоизоляции ее от стенок канала применяются пористый вдув, аксиальные потоки или закрутка газа [16, 19–22], а также создаются различные полости, уступы, диафрагмы, межэлектродные вставки, что усложняет общую конструкцию. Кроме этого, каждая схема имеет преимущество только в определенном диапазоне силы тока и расхода газа.
Для исследования роли формы канала проведены исследования ВАХ и КПД ГНП с цилиндрическим (диаметр – 4 мм, рис. 7) и расширяющимся каналами газоразрядного тракта с углом раскрытия 6° между образующей и осью канала (диаметр критического сечения – 4 мм, рис. 8) длиной 35 мм.
В табл. 1 представлены электрофизические характеристики дуги в цилиндрическом и расширяющемся газоразрядных трактах длиной 35 мм, где G – расход плазмообразующего газа, I – сила тока, U – напряжение горения дуги, Q – тепловой поток в охлаждаемые части ГНП, P – мощность, вкладываемая в дугу, η – КПД плазмотрона. Подбор диаметра цилиндрического канала произведен экспериментально из условия исключения теплового запирания канала при данных режимах работы ГНП. Оценка η проводилась калориметрическим методом: автоматизированным измерением расходов и температуры воды на входах и выходах автономно охлаждаемых частей узлов плазмотрона.
Таблица 1.
Электрофизические характеристики электрической дуги в длинном цилиндрическом и расходящемся газоразрядном тракте [23]
Длинный анод цилиндрический, диаметр – 4 мм | ||||||
---|---|---|---|---|---|---|
G, г/с | I, А | U, В | Q, кВт | P, кВт | η, % | Примечания |
1.5 | 100 | 25 | 1.45 | 2.5 | 42 | Нестабильный, пульсации U + 4 В |
150 | 24 | 2.2 | 3.6 | 38 | Нестабильный, пульсации U + 3 В | |
200 | 18 | 3.1 | 3.6 | 14 | Стабильный, пульсации U + 1 В | |
250 | 19 | 3.95 | 4.75 | 17 | ||
300 | 20 | 4.8 | 6 | 20 | ||
2 | 100 | 28 | 1.5 | 2.8 | 46 | Нестабильный, пульсации U + 3 В |
150 | 29 | 2.2 | 4.35 | 49 | Нестабильный, пульсации U + 2 В | |
200 | 29 | 3 | 5.8 | 48 | ||
250 | 23 | 3.8 | 5.75 | 34 | ||
300 | 22 | 4.9 | 6.6 | 26 | Стабильный, пульсации U + 1 В | |
2.5 | 100 | 34 | 1.55 | 3.4 | 54 | Стабильный, пульсации U + 1 В |
150 | 35 | 2.2 | 5.25 | 58 | ||
200 | 36 | 3.2 | 7.2 | 56 | ||
250 | 35 | 4.1 | 8.75 | 53 | ||
300 | 33 | 4.8 | 9.9 | 52 | ||
3 | 100 | 37 | 1.7 | 3.7 | 54 | Стабильный, пульсации U + 1 В |
150 | 38 | 2.7 | 5.7 | 53 | ||
200 | 39 | 3.6 | 7.8 | 54 | ||
250 | 40 | 4.7 | 10 | 53 | ||
300 | 37 | 5.3 | 11.1 | 52 | ||
Длинный анод расширяющийся, критический диаметр – 4 мм, выходной диаметр – 9.8 мм | ||||||
G, г/с | I, А | U, В | Q, кВт | P, кВт | η, % | Примечания |
1.5 | 100 | 28 | 1.35 | 2.8 | 52 | Стабильный, пульсации U + 0.5 В |
150 | 27 | 2.1 | 4.05 | 48 | ||
200 | 26 | 3 | 5.2 | 42 | ||
250 | 23 | 3.7 | 5.75 | 36 | ||
300 | 21 | 4.5 | 6.3 | 29 | ||
2 | 100 | 29 | 1.4 | 2.9 | 52 | |
150 | 29 | 2 | 4.35 | 54 | ||
200 | 30 | 2.7 | 6 | 55 | ||
250 | 31 | 3.5 | 7.75 | 55 | ||
300 | 31 | 4.4 | 9.3 | 53 | ||
2.5 | 100 | 30 | 1.45 | 3 | 52 | |
150 | 31 | 2.1 | 4.65 | 55 | ||
200 | 31.5 | 2.9 | 6.3 | 54 | ||
250 | 32 | 3.7 | 8 | 54 | ||
300 | 32.5 | 4.4 | 9.75 | 55 | ||
3 | 100 | 31 | 1.5 | 3.1 | 52 | |
150 | 31.5 | 2.3 | 4.725 | 51 | ||
200 | 32 | 3.1 | 6.4 | 52 | ||
250 | 32.5 | 4 | 8.125 | 51 | ||
300 | 33 | 4.8 | 9.9 | 52 |
Из данных табл. 1 видно, что расширяющийся канал обеспечивает стабильную работу ГНП во всем диапазоне изменения тока и расхода плазмообразующего газа. Горение дуги в цилиндрическом канале при малых токах и расходе плазмообразующего газа (см. Примечания в табл. 1) сопровождается периодическими кратковременными пульсациями напряжения, обусловленными крупномасштабным шунтированием [22].
Эксперимент показал, что расширяющийся канал лишен вышеуказанных недостатков цилиндрического канала, способствует стабильности работы ГНП во всем диапазоне изменения тока и расхода газа, при этом уровень кратковременных пульсаций напряжения на всех режимах работы не более 0.5 В.
Единственный недостаток исследуемого расширяющегося канала – это необходимость при больших токах (I > 250 А) увеличивать расход газа для увеличения длины дуги и, соответственно, напряжения горения, о чем свидетельствует уменьшение напряжения горения при 300 А (табл. 1).
Анализ зоны максимальной привязки дуги в аноде показал, что при данных режимах работы для горения дуги в аргоне нет необходимости в такой длине газоразрядного тракта. Как результат, длина газоразрядного тракта была уменьшена до 15 мм. Дальнейшее уменьшение ухудшало охлаждение анода из-за конструктивных особенностей ГНП, хотя анализ показывает возможность уменьшения анода до ~10 мм. В табл. 2 приведены электрофизические характеристики электрической дуги в цилиндрическом и расширяющемся газоразрядных трактах длиной 15 мм.
Таблица 2.
Электрофизические характеристики электрической дуги в цилиндрическом и расходящемся газоразрядных трактах длиной 15 мм [23]
Короткий цилиндрический анод | ||||||
---|---|---|---|---|---|---|
G, г/с | I, A | U, В | Q, кВт | P, кВт | η, % | Примечания |
1.5 | 100 | 24 | 1.3 | 2.4 | 46 | Нестабильный, пульсации U + 4 В |
150 | 23 | 1.8 | 3.45 | 48 | Нестабильный, пульсации U + 3 В | |
200 | 20 | 2.5 | 4 | 38 | Стабильный, пульсации U + 1 В | |
250 | 18 | 3.2 | 4.5 | 29 | ||
300 | 18 | 3.8 | 4.4 | 30 | ||
2 | 100 | 27 | 1.3 | 2.7 | 52 | Нестабильный, пульсации U + 3 В |
150 | 26 | 1.8 | 3.9 | 54 | Нестабильный, пульсации U + 2 В | |
200 | 26 | 2.5 | 5.2 | 52 | ||
250 | 26 | 3.3 | 6.5 | 49 | ||
300 | 23 | 4.2 | 6.9 | 39 | Стабильный, пульсации U + 1 В | |
2.5 | 100 | 35 | 1.4 | 3.5 | 57 | |
150 | 36 | 2.1 | 5.4 | 61 | ||
200 | 36 | 2.7 | 7.2 | 63 | ||
250 | 35 | 3.45 | 8.75 | 61 | ||
300 | 34 | 4.25 | 10.2 | 58 | ||
3 | 100 | 38 | 1.4 | 3.8 | 63 | |
150 | 39 | 2 | 5.85 | 66 | ||
200 | 40 | 2.7 | 8 | 66 | ||
250 | 39 | 3.4 | 9.75 | 65 | ||
300 | 38 | 4.2 | 11.4 | 63 | ||
Короткий расширяющийся анод | ||||||
G, г/с | I, A | U, В | Q, кВт | P, кВт | η, % | Примечания |
1.5 | 100 | 28 | 1.2 | 2.8 | 57 | Стабильный, пульсации U + 0.5 В |
150 | 27 | 1.7 | 4.05 | 58 | ||
200 | 24 | 2.4 | 4.8 | 50 | ||
250 | 23 | 3 | 5.75 | 49 | ||
300 | 21 | 3.5 | 6.3 | 44 | ||
2 | 100 | 29 | 1.3 | 2.9 | 55 | |
150 | 29 | 1.8 | 4.35 | 59 | ||
200 | 30 | 2.4 | 6 | 60 | ||
250 | 30.5 | 2.9 | 7.625 | 63 | ||
300 | 31 | 3.7 | 9.3 | 60 | ||
2.5 | 100 | 30 | 1.3 | 3 | 57 | |
150 | 30 | 1.9 | 4.5 | 58 | ||
200 | 30.5 | 2.4 | 6.1 | 61 | ||
250 | 31 | 3 | 7.75 | 61 | ||
300 | 31.5 | 3.7 | 9.45 | 61 | ||
3 | 100 | 31 | 1.2 | 3.1 | 61 | |
150 | 31 | 1.7 | 4.65 | 63 | ||
200 | 31.5 | 2.2 | 6.3 | 65 | ||
250 | 32.5 | 2.8 | 8.125 | 66 | ||
300 | 33 | 3.4 | 9.9 | 66 |
В расширяющемся канале ВАХ слабовозрастающая, кроме режима работы при расходе 1.5 г/c, что связано с уменьшением длины дуги при увеличении тока и невозможностью ее выдувания. При больших расходах газа (≥2 г/c), как и с длинным анодом, лучшими характеристиками обладает расширяющийся канал во всем диапазоне изменения тока и расхода плазмообразующего газа (табл. 2). Укорачивание длины газоразрядного тракта привело к увеличению КПД плазмотрона в среднем на 10–15%.
На основе проведенных исследований и выбора оптимальной конфигурации узлов был создан генератор низкотемпературной плазмы аргона постоянного тока с самоустанавливающейся дугой и расширяющимся каналом газоразрядного тракта, конструкция которого приведена на рис. 9.
5. ДИАГНОСТИЧЕСКИЙ КОМПЛЕКС ДЛЯ ИССЛЕДОВАНИЯ ВЗАИМОДЕЙСТВИЯ ПЛАЗМЕННОЙ СТРУИ С ОБРАЗЦОМ
Для исследования электрофизических характеристик разрабатываемых ГНП и генерируемого ими плазменного потока был модернизирован и автоматизирован экспериментальный стенд, представленный на рис. 10. Синхронизированная система измерений позволяет методами скоростной визуализации, микропирометрии, лазерной профилометрии, спектроскопии, стереоскопии и калориметрирования получить данные о характере изменения во времени и пространстве поля температур на поверхности образца, динамике убыли материала, изменениях параметров (температура и концентрация электронов, температура тяжелых частиц) набегающей на образец плазменной струи.
Рис. 10.
Синхронизированная система измерений: 1 – плазмотрон, 2 – высокоскоростной микропирометр, 3 – образец, 4 – цилиндрическая линза, 5 – телескоп, 6 – импульсно-периодический лазер, 7 – светофильтр, 8 – MS-257-Andor, 9 – черно-белая высокоскоростная камера VS-Fast, 10 – треки частиц, 11 – пограничный слой, 12 – трехканальный спектрометр AvaSpec 2048, 13 – одноканальный спектрометр AvaSpec 3648, 14 – видеокамера Motion Pro, 15 – нейтральный светофильтр, 16 – интерференционный фильтр, 17 – система синхронизации (генератор управляющих импульсов).
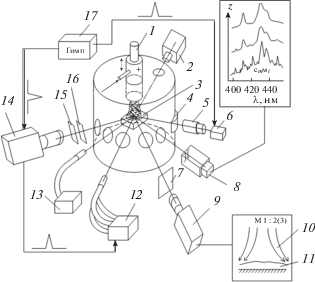
Наличие и значения тока и напряжения определяются с помощью системы, основанной на использовании аналого-цифровых плат L-Card L761, L783 с возможностью одновременного опроса 16 измерительных каналов с частотой опроса до 3000 кГц, позволяющей измерять как мгновенные значения токов и напряжений, так и осредненные значения по времени с цифровым и графическим отображением информации.
Удельные тепловые потоки плазмы определяются с помощью многосекционного калориметра (рис. 11). В стационарном режиме теплообмена “струя–калориметр” выполнены калибровочные измерения тепловой мощности WQ = $ = {{C}_{p}}{{q}_{{{{{\text{H}}}_{2}}{\text{O}}}}}\left( {{{t}_{{{\text{вых}}}}} - {{t}_{{{\text{вх}}}}}} \right),$ сообщаемой плазменным потоком поверхности ${{S}_{{{\text{кал}}}}} = {{\pi d_{0}^{2}} \mathord{\left/ {\vphantom {{\pi d_{0}^{2}} 4}} \right. \kern-0em} 4}$ при варьируемых значениях мощности дуги, расхода газа и расстояния h, где площади секций соответственно равны S1 = 1 см2, S2 = 3, S3 = 9.
Проверки расходных характеристик профилированного сопла плазмотрона, а также скорости истечения газа проводятся по измерению полного давления с помощью трубки Пито, представляющей собой изогнутую капиллярную трубку, заключенную в медный корпус, который охлаждался проточной водой (рис. 12). Непосредственно давление измерялось токовым датчиком Honeywell Eclipse OEM Pressure Transducer с рабочим диапазоном P = 0–20.413 атм с холостым током i0 = 4 мA и линейной зависимостью перепада давления от тока dP/di = 1.2927 × 108 Пa/A. Ток измерялся цифровым микроамперметром с точностью δi = 1 мкА [24]. По полученным данным на основе линейной зависимости тока датчика от давления и данным спектроскопических измерений температуры определяется плотность потока $\rho = \frac{{p{\kern 1pt} \mu \left( T \right)}}{{RT}}$ (p – статическое (атмосферное) давление, T – температура, $\mu = \mu \left( T \right)$ – средняя молярная масса смеси по данной температуре, R – универсальная газовая постоянная) и скорость потока v = $ = {{\left[ {2\frac{{{{p}_{0}} - p}}{\rho }} \right]}^{{{1 \mathord{\left/ {\vphantom {1 2}} \right. \kern-0em} 2}}}}$, где (${{p}_{0}} - p$) измеряется токовым датчиком.
Рис. 12.
Трубка Пито: 1 – источник питания, 2 – токовый датчик, 3 – измерительная трубка, 4 – водоохлаждающая трубка.
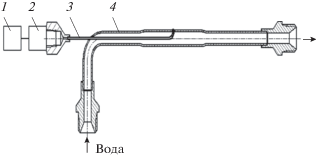
Информацию о характере движения и средней скорости плазмы дает также скоростная видеосъемка потока при подмешивании в плазменную струю (в верхнюю ее часть) небольшого количества порошка графита с частицами размером 10–20 мкм с транспортирующим его газом. Нагретые высокоэнтальпийным потоком частицы графита оставляют на видеокадрах треки движения. При выбранных размерах частиц они будут практически без проскальзывания двигаться с плазменной струей, а по времени экспозиции съемки и длине трека можно оценить скорость частиц и транспортирующего их потока.
Определение плазмохимического состава и параметров плазмы проводится спектральными методами с использованием как одноканального оптоволоконного спектрометра AvaSpec 2048 (со спектральным разрешением около 1 нм, выполняет мониторинг излучения плазмы в спектральном диапазоне 240–1000 нм с периодичностью 2–4 спектр/с), так и трехканального оптоволоконного спектрометра AvaSpec 3648 (с диапазоном 220–1100 нм и спектральным разрешением 0.2–0.5 нм).
Исследование временнόй эволюции потока плазмы проводится с помощью высокоскоростной камеры типа Motion Pro X3 (США) с 1.3 мегапиксельным (1248 × 1008 пикселей) цветным CMOS-сенсором фирмы Micron с диагональю 19.7 мм, частотой кадров 1–10 кГц и минимальной экспозицией 1 мкс. Микропирометрия выбранной зоны (диаметром 1.5–2 мм) на поверхности образца с целью измерения локальных значений яркостной температуры проводится высокоскоростным (временнóе разрешение до 1 мкс) трехдлиноволновым микропирометром FMP1001 с температурным диапазоном 1200–5000 К.
Для измерения скорости уноса массы обрабатываемого образца можно использовать методы “лазерного ножа” и двухпозиционной томографии. Импульсный лазер LCM-DTL-319QT с частотой импульсов до 10 кГц, длительностью импульса 7 нс, длиной волны 527 нм и энергией импульса 100 мкДж с системой фокусировки (телескоп и цилиндрическая линза) формирует в зоне поверхности образца “лазерный нож” шириной 1 мм и высотой 20–25 мм. С помощью двухпозиционной стереоскопии синхронизованными видеокамерами Phantom и VS-Fast (частота кадров – 30–50 с–1, время экспозиции – 10–100 мкс) устанавливается изменение во времени границ образца и, в конечном счете, его изменяющийся объем. Тем самым устанавливается составляющая убыли материала образца во времени. Одновременно с двухпозиционной визуализацией третья скоростная камера Motion Pro в режиме 10 кадр/с и экспозицией 1 мкс регистрирует след “лазерного ножа” на поверхности образца. При этом для определения температуры поверхности образца в области кратера и вне его в световые тракты видеокамер периодически вводятся интерференционные фильтры 590 и 525 нм с полосой пропускания δλ1/2 = 10 нм [25], последний одновременно позволяет улучшить “контрастность” наблюдения следа “лазерного ножа”.
С помощью спектральных методов анализировался состав высокоэнтальпийного плазменного потока [17, 24]. Исследования проводились с использованием трехканального оптоволоконного спектрометра AvaSpec 2048 со спектральным разрешением 0.2–0.5 нм, который выполнял мониторинг излучения (с периодичностью 3–4 спектр/с) вдоль оси потока плазмы в спектральном диапазоне 240–1000 нм. Примеры характерных спектров аргона представлены на рис. 13.
Наличие в исследуемых спектрах плазмы аргона большого числа линий атомарного аргона ArI позволяет использовать метод “больцмановской экспоненты” для определения температуры электронов Те [25, 26]. Концентрацию электронов в приосевой области плазменной струи можно оценить по полуширине линий Hα и Hβ. Так, например, на срезе сопла при токе 250 А и расходе газа 2.5 г/c температура и концентрация электронов в приосевой плазме аргона равны Те ≈ 12 кК, ne ~ ~ 1017 cм–3.
Скорость плазменного потока определялась измерением полного давления с помощью трубки Пито (рис. 12), закрепленной на стальной координатной рампе с тремя степенями свободы с точностью позиционирования $\delta \bar {x}$ = $~\delta \bar {y} = \delta \bar {z} = 0.1$ мм. Измерение полного давления при расходе аргона 2.5 г/c производилось вдоль оси струи с шагом $\Delta x = 10 \pm 1$ мм при двух различных значениях тока I1 = 200 А и I2 = 250 А. При расчете погрешностей измеряемых и рассчитываемых величин учитывалось, что точность установки положения (абсолютная погрешность) по оси z $\delta z = 1$ мм, остальные погрешности определялись из следующих соотношений:
В табл. 3 приведены полученные спектральными методами зависимости температуры от расстояния от среза сопла в плазме аргона при расходе 2.5 г/c. Для расчета температуры на различных расстояниях для значения тока 200 А использовалось значение температуры Т1 = 11 902 ± 497 К, осредненное по области вблизи выходного сечения сопла. А для расчета температуры на различных расстояниях для значения тока 250 А применялось осредненное аналогичным образом значение температуры Т2 = 11 983 ± 941 К.
Таблица 3.
Зависимость температуры от расстояния от среза сопла
200 A | 250 A | ||
---|---|---|---|
Z, м | Т, К | Z, м | Т, К |
0.001 | 13 003.21 | 0.001 | 13 498.91 |
0.0012 | 13 001.43 | 0.0012 | 12 916.18 |
0.0014 | 12 645.56 | 0.0014 | 12 034.78 |
0.0016 | 12 233.3 | 0.0016 | 12 188.93 |
0.0018 | 11 800.88 | 0.0018 | 12 564.45 |
0.002 | 11 944.86 | 0.002 | 10 695.67 |
0.0022 | 11 002.34 | 0.0022 | 10 882.34 |
0.0024 | 11 498.81 | 0.0024 | 11 908.96 |
Следует обратить внимание на то, что из-за малой зоны измерения температуры невозможно выполнить линейную экстраполяцию температуры на дальние расстояния от сопла (происходит переход через нуль). Вследствие больших температурных погрешностей были выбраны приведенные в табл. 4 следующие данные, полученные по оцифрованным кривым (рис. 14–16).
Таблица 4.
Обобщенные данные по выбранным температурам [23]
I, A | 200 | 250 |
T, К | 11 815.7 | 12 181.1 |
Cp, Дж/(моль К) | 163.1 | 182.1 |
Cp, Дж/(кг К) | 4082.9 | 4559.9 |
Cv, Дж/(моль К) | 154.8 | 173.8 |
Показатель адиабаты k | 1.053 | 1.047 |
Скорость звука a, м/с | 1608.6 | 1628.7 |
Плотность, кг/м3 | 0.0412 | 0.04002 |
ln(k) | 0.052 | 0.04669 |
Первая производная от ln(k) | 0.000021648 | 0.000014873 |
Рис. 15.
Зависимость показателя адиабаты аргона при атмосферном давлении от температуры по данным работы [27].
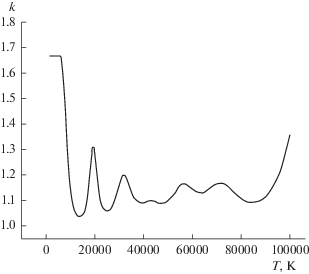
На рис. 14 приведены зависимости теплоемкости аргона от температуры по данным различных авторов [27–29]. На рис. 15 и 16 представлены зависимость показателя адиабаты аргона при атмосферном давлении от температуры и зависимость скорости звука от температуры при атмосферном давлении по данным работы [27].
В табл. 5 и рис. 17 представлены результаты измерений скорости плазменного потока для двух значений тока.
Таблица 5.
Измерения для I = 200 A [23]
Z, м | i, мА | i – i0, 10–5 A | P0 – P, Па | v, м/с | λ* |
---|---|---|---|---|---|
I = 200 A | |||||
0.027 | 4.07 | 4.00 | 5103.25 | 351.689 | 0.21862 |
0.0255 | 4.07 | 4.00 | 5103.25 | 351.689 | 0.21862 |
0.024 | 4.08 | 5.00 | 6379.063 | 393.2003 | 0.24443 |
0.0225 | 4.09 | 6.00 | 7654.875 | 430.7293 | 0.26776 |
0.021 | 4.1 | 7.00 | 8930.688 | 465.2408 | 0.28921 |
0.0195 | 4.11 | 8.00 | 10 206.5 | 497.3634 | 0.30918 |
0.018 | 4.12 | 9.00 | 11 482.31 | 527.5335 | 0.32793 |
0.0165 | 4.14 | 11.0 | 14 033.94 | 583.2103 | 0.36254 |
0.015 | 4.15 | 12.0 | 15 309.75 | 609.1433 | 0.37866 |
0.0135 | 4.16 | 13.0 | 16 585.56 | 634.0164 | 0.39413 |
0.012 | 4.18 | 15.0 | 19 137.19 | 681.0429 | 0.42336 |
0.0105 | 4.21 | 18.0 | 22 964.63 | 746.0451 | 0.46377 |
0.009 | 4.22 | 19.0 | 24 240.44 | 766.4885 | 0.47647 |
0.0075 | 4.22 | 19.0 | 24 240.44 | 766.4885 | 0.47647 |
I = 250 A | |||||
0.027 | 4.1 | 6.00 | 7654.875 | 437.3514 | 0.26851 |
0.0255 | 4.11 | 7.00 | 8930.688 | 472.3935 | 0.29003 |
0.024 | 4.12 | 8.00 | 10 206.5 | 505.0099 | 0.31005 |
0.0225 | 4.14 | 10.0 | 12 758.13 | 564.6182 | 0.34665 |
0.021 | 4.17 | 13.0 | 16 585.56 | 643.7638 | 0.39524 |
0.0195 | 4.19 | 15.0 | 19 137.19 | 691.5133 | 0.42456 |
0.018 | 4.21 | 17.0 | 21 688.81 | 736.1721 | 0.45198 |
0.0165 | 4.23 | 19.0 | 24 240.44 | 778.2725 | 0.47782 |
0.015 | 4.28 | 24.0 | 30 619.5 | 874.7028 | 0.53703 |
0.0135 | 4.29 | 25.0 | 31 895.31 | 892.7398 | 0.5481 |
0.012 | 4.32 | 28.0 | 35 722.75 | 944.787 | 0.58006 |
0.0105 | 4.33 | 29.0 | 36 998.56 | 961.5102 | 0.59032 |
0.009 | 4.33 | 29.0 | 36 998.56 | 961.5102 | 0.59032 |
0.0075 | 4.35 | 31.0 | 39 550.19 | 994.113 | 0.61034 |
Рис. 17.
Зависимость скорости потока плазмы аргона от расстояния от среза сопла при двух значениях тока: 1 – 250 А, 2 – 200.
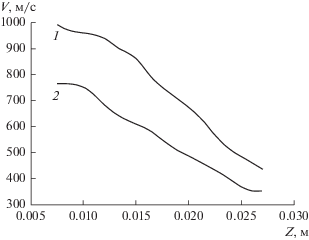
Измерения показали, что в зависимости от начальных условий на расстоянии 0–30 мм от среза сопла скорость потока плазмы изменяется от 990 до 300 м/c (рис. 17).
Оценка погрешностей измеряемых и рассчитываемых параметров
Погрешность установки осевой координаты –10–4 м.
На основе калориметрических измерений определены тепловые потоки, отводимые водой при охлаждении цилиндрических торцов калориметра из меди (рис. 11). Результаты измерений приведены в табл. 6.
Таблица 6.
Калориметрические измерения [23]
G, г/с; h, мм | I, A | U, В | q1, кВт/см2 | q2, кВт/см2 | q3, кВт/см2 |
---|---|---|---|---|---|
2.5; 30 | 200 | 30.3 | 0.02 | 0.0233333 | 0.0232203 |
250 | 31 | 0.05 | 0.05 | 0.0348304 | |
300 | 31.8 | 0.1 | 0.0766667 | 0.0425705 | |
2.5; 25 | 200 | 30.3 | 0.04 | 0.0233333 | 0.0270903 |
250 | 31.1 | 0.08 | 0.05 | 0.0387005 | |
300 | 31.7 | 0.14 | 0.0833333 | 0.0541806 | |
2.5; 20 | 200 | 30.5 | 0.1 | 0.05 | 0.0251553 |
250 | 31.2 | 0.17 | 0.0866667 | 0.0387005 | |
300 | 31.8 | 0.25 | 0.14 | 0.0522456 | |
2.5; 15 | 200 | 30.5 | 0.2 | 0.0866667 | 0.0270903 |
250 | 31.2 | 0.3 | 0.1533333 | 0.0425705 | |
300 | 31.7 | 0.41 | 0.2233333 | 0.0541806 |
При изменении мощности плазмотрона P ~ 5–10 кВт и расстояния от среза сопла 15–30 мм плазменная струя при нормальном ее падении на калориметр обеспечивает удельные тепловые потоки в пределах 0.02–0.41 кВт/cм2 (табл. 6). С увеличением расстояния тепловой поток на все секции калориметра становится практически равномерным из-за слабо расходящейся струи благодаря углу раскрытия канала газоразрядного тракта.
Отличительной особенностью данной плазмы является ее движение в канале с дозвуковой скоростью (максимум на оси ~103 м/с [30]), профиль которой имеет параболическую форму. При этом радиальное распределение давления потока плазмы в канале (I = 160 A, G = 1.25 г/с) также имеет параболическую форму со значением полного напора в центре до 100 Па, спадающего на периферии до 10 Па [31]. Ранее проведенные эксперименты [32] в широком диапазоне изменения тока разряда (150–500 А), расхода плазмообразующего газа (аргона и азота атмосферного давления с расходом 1–6 г/с), входного диаметра канала (3–6 мм) позволили установить, что около 95% полного тока (до 500 A) отводится начальной (обращенной к катоду) поверхностью анода длиной 1 см, а оставшаяся часть анода отводит 5% тока дуги (в случае секционированного анода). Такой характер распределения тока обусловлен тем, что в переходном слое между токопроводящим плазменным шнуром и водоохлаждаемой стенкой анода имеется поперечное (по отношению к стабилизирующему дугу вихревому потоку) электрическое поле напряженностью ~30 В/см, обеспечивающее дрейфовую скорость электронов ~106 м/c, значительно превышающую среднемассовую скорость поперечного току газового потока [33]. При этом режим течения стабилизирующего вихревого потока на входном участке расширяющегося анода – ламинарный, а в зоне преимущественного токоотбора (длиной 1–2 входных диаметра анода) – переходный от ламинарного к турбулентному, с характерными числами Rе ~ 103. Это обеспечивает гидродинамически устойчивое, без развития крупномасштабной турбулентности течение плазмы в области замыкания основного (~90–96%) тока дуги на поверхности анода. Наличие поперечного электрического поля и тока в переходной области “плазма–стенка анода”, по-видимому, является дополнительным ламинаризирующим фактором воздействия электрического тока на поток газа в токопроводящем канале [34, 35]. Диффузному характеру токоотбора на входном участке анодного канала способствуют как наличие значительной (соизмеримой с осевой) тангенциальной составляющей скорости вихревого потока (при скорости ~500 м/с частота вращения – 5–25 кГц), так и объемная фотоионизация нейтрального газа на границе плазменного шнура потоком распространяющегося в радиальном направлении вакуумного ультрафиолетового излучения (ВУФ-излучения), генерируемого сильноионизованным ядром дуги с температурой 20–30 кК [33]. Достигшее границы плазмы ВУФ-излучение осуществляет фотоионизацию холодного пристеночного слоя и последующий (в процессах фото- и тройной или диссоциативной рекомбинации) его нагрев. Вследствие высокой оптической плотности ВУФ-излучения его энергия не достигает стенки и полностью расходуется на нагрев газа. Таким образом, ВУФ-излучение обеспечивает плазмотронам данного типа энергетически выгодный режим работы, без развития колебаний и турбулизации плазмы на коротком (2–3 входных диаметра анода) самоустанавливающемся участке дуги: лишь четверть энергии джоулева нагрева попадает на охлаждаемую стенку. Остальные три четверти энергии затрачиваются на повышение энтальпии (среднемассовой температуры) рабочего газа [32]. Анализ картин радиальных распределений интенсивности свечения плазмы в сечении анода показывает, что при расходе плазмообразующего газа G < 3 г/с наблюдается цилиндрическая симметрия этого распределения, нарушающаяся при увеличении расхода, возможно, вследствие появления отрывных течений и турбулизации потока [32]. Согласно [16, 32], исследуемая плазма аргона находится в состоянии частичного локального термодинамического равновесия с температурой и концентрацией электронов на оси дуги Те ≈ (2.5–2.9) × 104 К, ne ~ 1017 см–3. В переходной области “электродуговая плазма–охлаждающий газовый поток” температура электронов и концентрация составляет Те ~ 104 К, ne ~ 1015 см–3. При этой температуре вязкость аргоновой плазмы достигает максимальных значений μ ≈ 2.5 × 10–4 Па с. В результате возрастания вязкости на периферии дуги в переходном слое происходит интенсивное демпфирование возникающих в газовом потоке турбулентных пульсаций. Кроме того, уменьшение концентрации электронов на периферии приводит к уменьшению эффективности электрон-атомных столкновений, частота столкновений падает, что приводит к отрыву электронной температуры от температуры тяжелых частиц [16, 32].
Таким образом, для исследования теплофизических, электродинамических и оптических свойств аргона, а также осуществления различных плазмохимических реакций создан генератор постоянного тока высокоэнтальпийной плазменной струи аргона с самоустанавливающейся длиной дуги и расширяющимся каналом выходного электрода с КПД ~60%. ГНП позволяет получать на выходе слаборасходящуюся плазменную струю аргона (с углом раскрытия 2α = 12°) с энтальпией 5–10 кДж/г и среднемассовой температурой 5–12 × 103 К с концентрацией электронов в приосевой плазме 1017 cм–3 при полной электрической мощности дугового разряда 2–10 кВт и расходе плазмообразующего газа 1.5–3 г/c. В зависимости от начальных условий на расстоянии 0–30 мм от среза сопла генератора низкотемпературной плазмы скорость потока плазмы меняется в пределах от 990 до 300 м/c. При этом обеспечиваются удельные тепловые потоки на расстояния от среза сопла 15–30 мм в пределах 0.02–0.41 кВт/cм2. Увеличить тепловую мощность и удельные тепловые потоки плазменной струи при данных значениях тока и расходах плазмообразующего газа можно увеличением длины дуги (соответственно, и напряжения горения), что возможно осуществить, например, вводом в конструкцию плазмотрона дополнительной межэлектродной вставки.
6. ЧИСЛЕННОЕ МОДЕЛИРОВАНИЕ И ОПТИМИЗАЦИЯ ГНП АЗОТА С РАСШИРЯЮЩИМСЯ КАНАЛОМ
Оптимизация основана на совместном экспериментальном исследовании и численном решении задачи истечения струи плазмы в открытое пространство из плазмотрона, использующего в качестве рабочего тела молекулярный азот [36]. Данный интерес обусловлен необходимостью учета явлений, связанных с высокоскоростными потоками (ударные волны и скачки уплотнения), и значительного числа молекулярных реакций, в том числе диссоциации и ионизации [37], процессов взаимодействия излучения с веществом, его влияния на процессы теплопереноса, а также плазменной турбулентности. Таким образом, решение подобных задач требует значительных вычислительных мощностей для учета процессов, различающихся по времени и по пространству на несколько порядков.
Для решения этой задачи предложена простая методика итерационного профилирования сопла для плазмотрона, использующего в качестве рабочего тела молекулярный азот с учетом процессов равновесной диссоциации и ионизации. Хорошо известно, что в температурных зонах химических реакций происходит резкий всплеск теплоемкости и химической теплопроводности смеси, связанный с переносом энергии химической связи диффузионными и конвективными потоками. Подобные процессы приводят к тому, что зависимость показателя адиабаты газовой смеси (N2, N, N+) становится немонотонной, вследствие чего применение отработанных элементарных методик расчета сопла становится неприемлемым.
На предварительном этапе работы авторами рассчитаны зависимости удельной теплоемкости, молярной массы (рис. 18 и 19) газовой смеси азота и его производных от температуры. Для этого использовались уравнения диссоциативного и ионизационного равновесия Саха без учета неидеальности для двух реакций:
Рис. 18.
Зависимость теплоемкости смеси молекулярного азота и производных от равновесных реакций диссоциации и ионизации от температуры при атмосферном давлении.
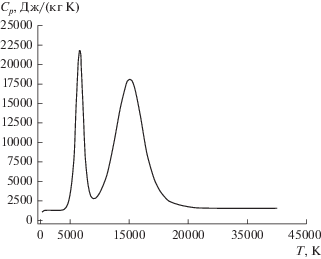
В результате решения находятся коэффициенты равновесной диссоциации αD и ионизации αI бинарной смеси. Теплоемкость при постоянном давлении (1 атм) рассчитывалась как производная удельной энтальпии смеси по температуре. Средняя молярная масса смеси находилась из соотношения
Показатель адиабаты вычислялся по формуле Майера
Зависимость показателя адиабаты от температуры представлена на рис. 20.
Рис. 20.
Зависимость показателя адиабаты от температуры для N2: 1 – область теплоемкости двухатомного газа без внутренних степеней свободы, 2 – область возбуждения внутренних степеней свободы, 3 – проявление изотермичности вследствие высокой теплопроводности в области диссоциации, 4 – аналогично в области ионизации, 5 – выход на теплоемкость одноатомного газа.
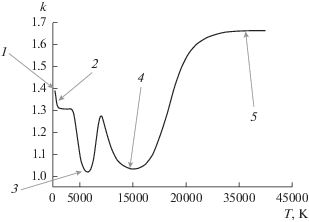
При профилировании сопла необходимо знать следующие величины: массовый расход газа $G$, давление ${{P}_{1}}$ и температуру ${{T}_{1}}$ во входном сечении (форкамере сопла), начальный диаметр сопла ${{D}_{1}}$, а также число Маха выходного потока. На начальном этапе необходимо найти остальные термодинамические параметры потока во входном сечении, по которым затем определяются параметры заторможенного потока (энтальпия ${{H}_{0}}$, соответствующая ей температура ${{T}_{0}}$, давление ${{P}_{0}}$, плотность ${{\rho }_{0}}$, скорость звука ${{a}_{0}}$) и далее аналогично рассчитываются параметры в критическом сечении.
В предположении линейного роста числа Маха М по длине канала начиная с входного сечения определяются газодинамические параметры, а также диаметр сопла путем поиска минимума функции
Следует отметить, что при расчете газодинамических параметров используется средний показатель адиабаты по соседним сечениям. На рис. 21 представлен пример расчета соплового профиля для выбранного набора параметров.
Рис. 21.
Зависимость диаметра сопла от числа Маха при T1 = 14020 К, P = 4 атм, G = 0.016 г/с: 1 – безытерационный расчет диаметра критического и выходного сечения, 2 – расчет по книге [38], 3 – профиль построен по 100 сечениям, 4 – 200.

На основе предложенного метода рассчитан и создан оптимальный профиль расширяющегося сопла плазмотрона, представленного на рис. 22.
Рис. 22.
Конструкция плазмотрона, рабочий газ – азот и воздух: 1 – вставка из тугоплавкого материала, 2 – катод, 3 – изолятор, 4 – трубка охлаждения катода, 5 – катододержатель, 6 – корпус плазмотрона, 7 – сопло-анод.
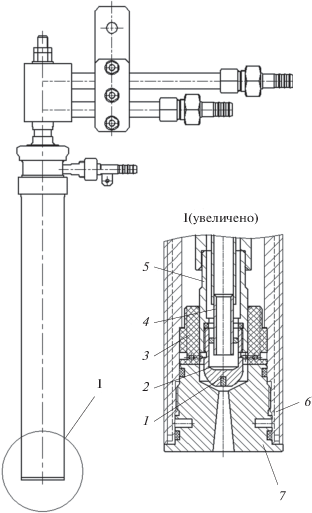
Данная конструкция позволила увеличить КПД до 80% для азота, получить на выходе расширяющуюся струю с энтальпией 5–50 кДж/г и среднемассовой температурой 5–10 кК при полной электрической мощности дугового разряда 5–50 кВт и расходе плазмообразующего газа 1–3 г/c.
На рис. 23 и 24 показаны ВАХ и КПД плазмотрона при различных значениях расхода газа. Видно, что ВАХ имеет слабо меняющееся с изменением тока напряжение горения дуги с расширенной (по сравнению с дугами в цилиндрических каналах) зоной устойчивого горения в области малых токов и КПД плазмотрона увеличивается с увеличением тока и расхода плазмообразующего газа азота.
Определение удельных тепловых потоков плазмы выполнено калориметрическим измерением тепловых потоков плазмы, отводимых водой при охлаждении многосекционного торца калориметра из меди, для различных значений силы тока, расхода газа и расстояния от среза сопла плазмотрона (рис. 11). При изменении мощности плазмотрона в диапазоне 20–50 кВт, а также расстояния от среза сопла в пределах 10–30 мм плазменная струя при нормальном ее падении на калориметр обеспечивает удельные тепловые потоки 0.1–10 кВт/cм2 плазмы азота.
Оценка скорости потока методом ввода порошка графита с частицами размером 10–20 мкм с транспортирующим его газом (рис. 25) и измерение полного давления с помощью трубки Пито (рис. 12) показали, что в зависимости от начальных условий на расстоянии 0–30 мм от среза сопла скорость потока плазмы меняется в пределах 900–300 м/c.
Определение плазмохимического состава, а также параметров потока высокоэнтальпийной плазмы проводилось спектральными методами с использованием трехканального оптоволоконного спектрометра AvaSpec 2048 со спектральным разрешением 0.2–0.5 нм, который выполнял мониторинг излучения (с периодичностью 3–4 спектр/с) вдоль оси потока плазмы в спектральном диапазоне 240–1000 нм. На рис. 26 приведен спектр излучения плазмы азота.
Наличие в исследуемых спектрах плазмы азота большого числа линий атомарного азота NI позволяет использовать метод “больцмановской экспоненты” [33, 34] для определения Те. Концентрацию электронов в приосевой области плазменной струи можно оценить по полуширине линий Hα и Hβ. Так, например, на срезе сопла при токе 250 А температура и концентрация электронов в приосевой плазме азота составляют Те = = 10 кK, ne = 5 × 1016 cм–3.
Для исследования теплофизических, электродинамических и оптических свойств азота, а также осуществления различных плазмохимических реакций разработан газоразрядный тракт с совмещенным соплом-анодом для генератора постоянного тока с самоустанавливающейся длиной дуги и расширяющимся каналом выходного электрода, что позволило повысить КПД плазмотрона до ~80%. Плазмотрон генерирует на выходе слаборасходящуюся плазменную струю азота диаметром D = 8–10 мм с энтальпией до 50 кДж/г, среднемассовой температурой 7–11 кK и концентрацией электронов ~1015–1016 cм–3 при полной электрической мощности дугового разряда 20–50 кВт и расходе плазмообразующего газа 1–3 г/c. При изменении мощности плазмотрона от 20 до 50 кВт и расстояния h от 10 до 30 мм плазменная струя при нормальном ее падении на калориметр обеспечивала удельные тепловые потоки от 0.1 до 10 кВт/см2, при этом скорость потока плазмы меняется в пределах от 900 до 300 м/c.
7. ГЕНЕРАТОР НИЗКОТЕМПЕРАТУРНОЙ ПЛАЗМЫ АЗОТ-ПРОПАНОВОЙ СМЕСИ
Основным преимуществом плазмохимической технологии является универсальность в отношении перерабатываемых веществ и относительно малые габариты, позволяющие создать передвижные технологические модули. С ее помощью возможно преобразование различных видов топлива, таких как промышленные, медицинские или муниципальные отходы, низкосортные угли, биомасса, в синтез-газ [2]. Полученный синтез-газ может использоваться в качестве топлива в системах сжигания для выработки электроэнергии и для производства водорода.
Литературный анализ созданных генераторов плазмы самых разных конструкций, работающих при мощностях от нескольких киловатт до десятков мегаватт, показывает, что наиболее устойчивый режим работы и максимальный ресурс имеют ГНП, работающие на аргоне. При утилизации отходов применение аргона в промышленных масштабах экономически нецелесообразно, поэтому выгодно использовать доступные смеси газов, например азот или воздух с добавлением смеси пропана или бутана. Использование такого плазмообразующего газа [39] приводит к образованию в полости катода и на внутренней поверхности анода преимущественно среды из углеродосодержащего газа. Образовавшиеся в результате диссоциации молекул пропана или бутана и ионизации атомов углерода положительные ионы углерода под действием прикатодного падения потенциала осаждаются на медной водоохлаждаемой поверхности, образуя углеродный наноструктурированный слой, т.е. происходит регенерация материала электродов, что в разы увеличивает ресурс ГНП. Кроме этого, при использовании молекулярных газов в качестве плазмообразующего газа в ГНП необходимо затрачивать энергию на процессы ионизации и диссоциации, что приводит к увеличению энтальпии плазмы и многократному увеличению ее теплопроводности (при соединении метана и углекислого газа как 1 : 2 в 20 раз больше, чем у аргона) [40].
В связи с вышесказанным разработан генератор низкотемпературной плазмы на смеси азота и пропана мощностью до 50 кВт (рис. 27), где плазменный поток из расширяющегося канала попадает в водоохлаждаемый цилиндрический анод. Такая конструкция плазмотрона обеспечивает горение дуги в ламинарном потоке при высокой скорости газа на входе в сопло, эффективность нагрева рабочей среды при малых тепловых потерях в водоохлаждаемой части устройства и способствует повышению устойчивости потока [17, 18].
Проведено исследование влияния пропана на работу ГНП и получаемых продуктов распада при силе тока дуги 100 А при максимально возможном расходе пропана для данного расхода азота, при котором не нарушается стабильность горения дуги. Подача пропана осуществлялась как вместе с рабочим газом (азотом) в разрядный промежуток, так и между соплом и анодом, а также в середине анода ниже зоны привязки дуги (табл. 7).
Таблица 7.
Параметры эксперимента
Место ввода пропана | I, A | U, B | G, г/c (азот) | G, г/c (пропан) |
---|---|---|---|---|
Через зазор катод-сопло вместе с плазмообразующим азотом | 100 | 85–90 | 0.45 | 0.33 |
Через зазор сопло-анод | 100 | 75–80 | ||
Через отверстия в середине анода | 100 | 70 |
Эксперимент показал, что при подаче пропана в анод за привязкой дуги осаждение продуктов распада происходит в основном не на электродах, а на выходе из анода. Характерные картины микроструктур продуктов распада приведены на рис. 28.
При подаче пропана с плазмообразующим газом в разрядный промежуток осаждение продуктов распада происходит в основном на электродах (особенно на аноде). Микроструктуры полученных компонентов порошков изучались на растровом электронном микроскопе по стандартной методике. Наиболее крупными оказались фракции в препаратах порошков из анода (до ~2 мм в поперечнике) при подаче пропана в зазор сопло-анод за время работы плазмотрона ~2 мин. При увеличении времени работы плазмотрона до 4 мин размер фракций в поперечнике уменьшился до ~1 мм. Самые мелкие фракции получились при подаче пропана вместе с плазмообразующим газом и времени работы 2.5 мин (до ~0.3 мм в поперечнике).
Анализ фазового состава углеродных образцов проводился методом рентгеноструктурного анализа на установке ДРОН-2 (CuKα-излучение). Установлено, что основу образцов составляют:
• графит, представленный несколькими компонентами, различающимися степенью трехмерной упорядоченности кристаллической структуры;
• углерод с турбостратной графитовой структурой, содержащий одиночные хаотически ориентированные слои графита и пакеты параллельных, эквидистантных, но кристаллографически между собой не связанных слоев;
• значительное количество металла (медь) с кубической гранецентрированной кристаллической решеткой;
• неустановленные неизвестные примесные фазы.
Для исследования влияния пропана на работу плазмотрона и состав продуктов распада в плазме азота создан генератор низкотемпературной плазмы смеси азота и пропана. Показано, что для данной конструкции ГНП расход пропана имеет верхний предел при вводе вместе с плазмообразующим газом и в зону привязки дуги (не более ~73% от расхода плазмообразующего газа), где не нарушается стабильность горения дуги. При подаче пропана в зону привязки дуги осаждение продуктов распада происходит в основном на электродах (особенно на аноде), что может иметь восстановительный эффект электродов при правильном подборе смеси. При подаче пропана через отверстия в аноде за привязкой дуги осаждение продуктов распада происходит в основном на выходе из анода.
ЗАКЛЮЧЕНИЕ
Анализ современного состояния плазменных технологий утилизации показывает, что чем больше коммерческий успех технологии, тем меньше появляется публикаций, раскрывающих различные технические новации, в основном информация распространяется на узкоспециальных конференциях, через Интернет и в частных беседах. Анализ данных из существующих открытых источников показал характерные особенности высокотемпературного разложения отходов, достоинства и недостатки плазменной переработки.
1. Высокие температуры вызывают быстрый и полный пиролиз опасных органических загрязнений, а также плавление или стеклование неорганических отходов, что приводит к сильному уменьшению объема отходов и капсулированию трудноразрушаемых другими способами (горением, пиролизом) загрязнений.
2. Высокая плотность энергии, получаемая в плазменном реакторе (порядка 200 ГДж/м3), позволяет использовать установки меньшего размера при схожей производительности, таким образом снижая капитальные затраты и позволяя мобильные комплексы небольшого размера.
3. Использование электрических дуг уменьшает полный расход газа вместе с необходимостью подогревать его избыточное количество при сжигании. Как следствие, снижаются требования по производительности систем по переработке газа, отходящего из плазменного реактора. Также имеется достаточно большой выбор плазмообразующих газов, позволяющих организовать различные химико-технологические процессы во время обработки.
4. Компактные размеры и высокая плотность энергии позволяют существенно сократить времена выхода на режим и отключения.
5. Ультрафиолетовое излучение плазмы приводит к ускорению разложения отходов, что оказывается особенно действенным при пиролизе органических хлоридов.
6. Использование электричества в качестве источника энергии позволяет отделить процесс тепловыделения от процесса кислородного окисления, он оказывается независящим от расхода окислителя или воздуха.
7. Более высокая цена по сравнению с другими технологиями утилизации может быть снижена за счет того, что при плазменной утилизации возможно параллельное получение веществ и материалов, цена которых сопоставима с затратами на утилизацию.
8. Требования к высокой степени автоматизации процесса, так как процесс плазменной переработки требует задания значительно большего числа параметров в сравнении с традиционными (более распространенными) процессами переработки.
9. Существенное различие эффективности при обработке различных классов отходов (неуниверсальность).
Сдерживающим фактором широкого распространения плазменных методов утилизации отходов является отсутствие надежных и эффективных генераторов низкотемпературной плазмы.
С целью создания эффективного ГНП и исследования воздействия высокоэнтальпийной плазменной струи, образуемой плазмотроном постоянного тока, на мишень из твердого материала проведена модернизация и автоматизация экспериментального стенда, позволяющая методами скоростной визуализации, микропирометрии, лазерной профилометрии, спектроскопии и стереоскопии получить данные о характере изменения во времени и пространстве полей температур на поверхности образца, а также данные о динамике убыли материала, об изменениях параметров (температура и концентрация электронов, температура тяжелых частиц) набегающей на образец плазменной струи.
Первый этап подобных исследований проведен в потоке химически неактивной плазмы – в инертном аргоне. Для исследования теплофизических, электродинамических и оптических свойств аргона, а также осуществления различных плазмохимических реакций был создан генератор постоянного тока высокоэнтальпийной плазменной струи аргона с самоустанавливающейся длиной дуги и расширяющимся каналом выходного электрода с КПД ~ 60%. ГНП позволяет получать на выходе слаборасходящуюся плазменную струю аргона. В зависимости от начальных условий на расстоянии 0–30 мм от среза сопла генератора низкотемпературной плазмы скорость потока плазмы меняется в пределах от 990 до 300 м/c. При этом обеспечиваются удельные тепловые потоки на расстояния от среза сопла 15–30 мм в пределах 0.02–0.41 кВт/cм2. Повысить тепловую мощность и удельные тепловые потоки плазменной струи при данных значениях тока и расходах плазмообразующего газа можно увеличением длины дуги (соответственно и напряжения горения), что возможно осуществить, например, вводом в конструкцию плазмотрона дополнительной межэлектродной вставки.
Далее проведены исследования теплофизических, электродинамических и оптических свойств азота, где с использованием методики итерационного профилирования сопла разработан газоразрядный тракт с совмещенным соплом-анодом для генератора постоянного тока с самоустанавливающейся длиной дуги и расширяющимся каналом выходного электрода, что позволило повысить КПД плазмотрона до ~80%. Плазмотрон генерирует на выходе слаборасходящуюся плазменную струю азота диаметром 8–10 мм с энтальпией до 50 кДж/г, среднемассовой температурой 7–11 кK и концентрацией электронов ~1015–1016 cм–3 при полной электрической мощности дугового разряда 20–50 кВт и расходе плазмообразующего газа 1–3 г/c. При изменении мощности плазмотрона от 20 до 50 кВт и расстояния от 10 до 30 мм плазменная струя при нормальном ее падении на калориметр обеспечивала удельные тепловые потоки от 0.1 до 10 кВт/см2, при этом скорость потока плазмы менялась в пределах от 900 до 300 м/c.
Также проанализировано влияние пропана на работу плазмотрона и состав продуктов распада в плазме азота для созданного генератора низкотемпературной плазмы на смеси азота и пропана. Показано, что для данной конструкции ГНП расход пропана имеет верхний предел при вводе вместе с плазмообразующим газом и в зону привязки дуги (не более ~73% от расхода плазмообразующего газа), где не нарушается стабильность горения дуги. При подаче пропана в зону привязки дуги осаждение продуктов распада происходит в основном на электродах (особенно на аноде), что может иметь восстановительный эффект электродов при правильном подборе смеси. При подаче пропана через отверстия в аноде за привязкой дуги осаждение продуктов распада происходит в основном на выходе из анода.
Полученные теоретические, а также экспериментальные данные и инженерные решения могут служить исходными для проектирования различных ГНП с мощностью до 1 МВт и выше.
Работа выполнена при поддержке гранта РФФИ № 18-29-24 203 мк.
Список литературы
Sanlisoy A., Carpinlioglu M.O. A Review on Plasma Gasification for Solid Waste Disposal // Int. J. Hydrogen Energy. 2017. V. 42. № 2. P. 1361.
Heberlein J., Murphy A.B. Thermal Plasma Waste Treatment // J. Phys. D. Appl. Phys. 2008. V. 41. № 5. P. 053001.
Fauchais P., Coudert J.F., Pateyron B. Production of Thermal Plasmas // Thermal Plasmas for Hazardous Waste Treatment. World Scientific, 1996. P. 1.
Rahuman M., Pistone L., Trifirò F., Miertus S. Destruction Technologies For Polychlorinated Biphenyls (PCBs) // Proc. Expert Group Meetings on POPs and Pesticides Contamination. Bologna, 2000. P. 10.
Janasz Z.A., Hebecker D., Mossé A.L. Coversion of Liquid Toxic Waste by Means of a Plasma Reactor // Thermal Plasmas for Hazardous Waste Treatment. World Scientific, 1996. P. 146.
Pfender E. Thermal Plasma Technology: Where do We Stand and Where are We Going? // Plasma Chem. Plasma Process. 1999. V. 19. № 1. P. 1.
Blutke A.S., Vavruska J.S., Serino J.F. The PERCTM Process for Hazardous Waste Treatment // Thermal Plasmas for Hazardous Waste Treatment. World Scientific, 1996. P. 104.
Bonizzoni G. Design of a Plasma Torch for Toxic Waste Treatments // Thermal Plasmas for Hazardous Waste Treatment. World Scientific, 1996. P. 93.
Fiedler J., Lietz E., Bendix D. Experimental and Numerical Investigations of a Plasma Reactor for the Thermal Destruction of Medical Waste Using a Model Substance // J. Phys. D. Appl. Phys. 2004. V. 37. № 7. P. 1031.
Anyaegbunam F.N.C. Thermal Plasma Process for Hazardous Waste Treatment // Int. J. Eng. Res. Technol. 2014. V. 3. № 3. P. 1769.
Murphy A.B., McAllister T. Modeling of the Physics and Chemistry of Thermal Plasma Waste Destruction // Phys. Plasmas. 2001. V. 8. № 5. P. 2565.
Williams J.K., Iddles D.M., Chapman C.D. Industrial Treatment of Waste Materials Using Tetronics Plasma Systems // Thermal Plasmas for Hazardous Waste Treatment. World Scientific, 1996. P. 112.
Barton T.G., Mordy J.A. The Destruction of Halogenated Organic Chemicals by Plasma Pyrolysis // Can. J. Physiol. Pharmacol. 1984. V. 62. № 8. P. 976.
Girold C., Cartier R., Taupiac J.P. et al. Arc Plasma Incineration of Surrogate Radioactive Wastes // Thermal Plasmas for Hazardous Waste Treatment. World Scientific, 1996. P. 160.
Шейндлин А.Е., Асиновский Э.И., Батурин В.А., Батенин Б.М. Установки для получения плазмы и изучения ее свойств // ЖТФ. 1963. Т. 33. № 10. С. 1169.
Асиновский Э.И., Кириллин А.В., Низовский В.Л. Стабилизированные электрические дуги и их применение в теплофизическом эксперименте. 2-е изд. испр. и доп. М.: Физматлит, 2008. 264 с.
Исакаев Э.Х., Синкевич О.А., Тюфтяев А.С., Чиннов В.Ф. Исследование генератора низкотемпературной плазмы с расширяющимся каналом выходного электрода и некоторые его применения // ТВТ. 2010. Т. 48. № 1. С. 105.
Исакаев Э.Х., Тюфтяев А.С., Гаджиев М.Х. Оценка влияния угла раскрытия газоразрядного тракта на энергоэффективность плазмотрона // ФХОМ. 2016. Т. 3. С. 27.
Глебов И.А., Рутберг Ф.Г. Мощные генераторы плазмы. М.: Энергоатомиздат, 1985. 264 с.
Жуков М.Ф., Коротеев А.С., Урюков Б.А. Прикладная динамика термической плазмы. 1975. 298 с.
Коротеев А.С., Миронов В.М., Свирчук Ю.С. Плазмотроны: конструкции, характеристики, расчет. М.: Машиностроение, 1993. 296 с.
Жуков М.Ф., Засыпкин И.М., Тимошевский А.Н. и др. Электродуговые генераторы термической плазмы. Новосибирск: Наука, 1999. 712 с.
Гаджиев М.Х., Куликов Ю.М., Сон Э.Е., Тюфтяев А.С., Саргсян М.А., Юсупов Д.И. Эффективный генератор низкотемпературной плазмы аргона с расширяющимся каналом выходного электрода // ТВТ. 2020. Т. 58. № 1. С. 15.
Gadzhiev M.K., Sargsyan M.A., Tereshonok D.V., Tyuftyaev A.S. Investigation of the Argon Arc Binding to the Lanthanated Tungsten Cathode // EPL (Europhysics Lett.) 2015. V. 111. № 2. P. 25001.
Очкин В.Н. Спектроскопия низкотемпературной плазм. М.: Физматлит, 2006. 472 с.
Чиннов В.Ф. Излучательные свойства и спектроскопия низкотемпературной плазмы. М.: Изд. дом МЭИ, 2012. 168 с.
Eisazadeh-Far K., Metghalchi H., Keck J.C. Thermodynamic Properties of Ionized Gases at High Temperatures // J. Energy Resour. Technol. 2011. V. 133. № 2. P. 022201.
Дресвин С.В., Иванов Д.В. Физика плазмы. Учеб. пособ. СПб.: Изд-во Политехн. ун-та, 2013. 544 с.
Tanaka M., Tashiro S., Satoh T., Murphy A.B., Lowke J.J. Influence of Shielding Gas Composition on Arc Properties in TIG Welding // Sci. Technol. Weld. Join. 2008. V. 13. № 3. P. 225.
Асиновский Э.И., Пахомов Е.П., Ярцев И.М. Определение вязкости плазмы аргона с помощью стабилизированной электрической дуги // ТВТ. 1978. Т. 16. № 1. С. 28.
Асиновский Э.И., Пахомов Е.П., Ярцев И.М. Исследование характеристик течения плазмы в канале дуги // ТВТ. 1971. Т. 9. № 6. С. 1119.
Чиннов В.Ф. Экспериментальное исследование термической и неравновесной плазмы инертных и молекулярных газов. Дис. … докт. физ.-мат. наук. М.: ОИВТ РАН, 2002. 261 с.
Белевцев А.А., Исакаев Э.Х., Маркин А.В., Чиннов В.Ф. Спектроскопический анализ пространственных распределений параметров плазмы в высокоэнтальпийных потоках аргона и азота // ТВТ. 2002. Т. 40. № 1. С. 21.
Энгельшт В.С., Урюков Б.А. Низкотемпературная плазма. Т. 1. Теория столба электрической дуги. Новосибирск: Наука, 1990. 376 с.
Артемов В.И., Левитан Ю.С., Синкевич О.А. Неустойчивости и турбулентность в низкотемпературной плазме. М.: Изд-во МЭИ, 1994. 402 с.
Gadzhiev M.K., Kulikov Yu.M., Panov V.A., Son É.E., Tyuftyaev A.S. Supersonic Plasmatron Nozzle Profiling with the Real Properties of High Temperature Working Gas // High Temp. 2016. V. 54. № 1. P. 38.
Capitelli M., Colonna G., D’Angola. A. Fundamental Aspects of Plasma Chemical Physics: Thermodynamics // Springer Series on Atomic, Optical, and Plasma Physics, V. 66. N.Y.: Springer, 2012. 310 p.
Абрамович Г.Н. Прикладная газовая динамика. Т. 1. 5-е изд., перераб. и доп. М.: Наука, Гл. ред. физ-мат. лит, 1991. 600 с.
Голыш В.И., Карпенко Е.И., Лукьященко В.Г., Мессерле В.Е., Устименко А.Б. Плазмохимическая активация горения твердых топлив // ХВЭ. 2009. Т. 43. № 4. С. 371.
Pershin L., Chen L., Mostaghimi J. Plasma Spraying of Metal Coatings Using CO2-Based Gas Mixtures // J. Therm. Spray Technol. 2008. V. 17. № 5–6. P. 608.
Дополнительные материалы отсутствуют.
Инструменты
Теплофизика высоких температур