Теоретические основы химической технологии, 2019, T. 53, № 4, стр. 363-371
Обобщенная модель инжиниринга и управления сложной многостадийной химико-энерготехнологической системой переработки отходов апатит-нефелиновых руд
В. П. Мешалкин 1, А. Ю. Пучков 2, М. И. Дли 2, В. И. Бобков 2, *
1 Российский химико-технологический университет им. Д.И. Менделеева
Москва, Россия
2 Национальный исследовательский университет “МЭИ” в г. Смоленске
Смоленск, Россия
* E-mail: vovabobkoff@mail.ru
Поступила в редакцию 04.02.2019
После доработки 04.03.2019
Принята к публикации 06.03.2019
Аннотация
Представлена содержательная постановка задачи инжиниринга многостадийной химико-энерготехнологической системы производства фосфора из техногенных отходов апатит-нефелиновых руд. Основной целью исследований, осуществляемых в рамках процедуры инжиниринга, выступает определение параметров технологии получения фосфора, обеспечивающих снижение энергоресурсоэффективности за счет оптимизации величины энергопотребления всех рассматриваемых многостадийных химико-энерготехнологических процессов, а не отдельных этапов. Разработана обобщенная модель инжиниринга химико-энерготехнологической системы производства фосфора в нотации международного стандарта функционального моделирования IDEF0, конкретизированы параметры многостадийных химико-энерготехнологических процессов, использование которых целесообразно в дальнейшем при проведении процедуры минимизации энергоресурсоэффективности этого производства. Предложена концептуальная основа для создания единой оптимизационной программной модели химико-энерготехнологической системы, использующая методы теории автоматического управления – представление описания объектов управления в терминах пространства состояний. Приведены результаты имитационного эксперимента в среде моделирования динамических систем Simulink, показавшие целесообразность применения предложенных подходов к оптимизации многостадийных химико-энерготехнологических процессов.
ВВЕДЕНИЕ
Экологическая безопасность планируемых к применению технологических процессов становится первостепенным фактором, влияющим на решение о начале проектирования и дальнейшего развертывания новых производств. Для уже функционирующих предприятий становится актуальной задача инжиниринга технологических процессов с целью выявления в них стадий, в наибольшей степени наносящих урон окружающей среде.
Данная задача особенно актуальна для крупных предприятий, таких как металлургические, химические и горно-обогатительные производства. Истощение ресурсной базы минерального сырья и экологические проблемы хранения техногенных отходов апатит-нефелиновых руд горнопромышленных предприятий обусловливают необходимость создания комплексной системы их переработки и утилизации.
Процесс получения фосфора является многостадийной энергоемкой технологической операцией, включающей, с точки зрения аппаратно-технической составляющей: грануляторы, обжиговые машины конвейерного типа, далее по тексту обжиговоконвейерные машины, и рудно-термические печи [1]. Очевидно, что формирование и эффективное функционирование такой производственной цепочки должно базироваться на методах системного анализа и обеспечиваться использованием методологии инжиниринга энергоресурсоэффективных экологически безопасных производств переработки отходов апатит-нефелиновых руд на горно-обогатительных комбинатах, которая непосредственно связана с реализацией междисциплинарного подхода [2, 3].
Предлагаемая работа направлена на решение актуальной фундаментальной задачи формирования научных основ инжиниринга энергоресурсоэффективных экологически безопасных многостадийных систем переработки отходов апатит-нефелиновых руд на горно-обогатительных комбинатах в обжиговоконвейерных машинах для производства окатышей с последующим их использованием в рудно-термических печах [4]. Данная задача непосредственно связана с разработкой фундаментальных методов управления энергоресурсоэффективностью многостадийных химико-энерготехнологических процессов (ХЭТП) на основе иерархических моделей тепломассообмена при реализации отдельных подпроцессов, с учетом свойств перерабатываемого сырья и необходимости рационального использования вторичных энергетических ресурсов, при замыкании и перераспределении энергетических потоков в сложной химико-энерготехнологической системе (ХЭТС) [5, 6].
МАТЕРИАЛЫ И МЕТОДЫ
Задача адаптации оборудования к изменениям режима работы при вариациях химико-технологических свойств сырья относится к классу ресурсосберегающих и экологических, поскольку непредвиденные смены условий функционирования агрегатов в энергоемких производствах приводят, как правило, к увеличению энергозатрат на единицу продукции и вариации выбросов. Вопросам энергоресурсосбережения и экологии в металлургии, химической промышленности и горно-обогатительной индустрии придается большое значение [7–10].
Совершенствование аппарата инжиниринга сложного технологического оборудования переработки твердых техногенных отходов горно-обогатительных комбинатов, обеспечивающего комплексный подход к алгоритмам оптимального управления взаимосвязанными процессами, реализуемыми в обжиговоконвейерных машинах и рудно-термических печах (РТП), является актуальной задачей в процессе повышения энергоэффективности производств. Междисциплинарность научных исследований в области создания научных основ комплексной энергоресурсоэффективной экологически безопасной переработки отходов апатит-нефелиновых руд определяется необходимостью применения фундаментальных методов системного анализа физико-химических превращений, тепломассообменных и сложных многостадийных химико-энерготехнологических процессов.
Неотъемлемой частью процедуры инжиниринга рассматриваемых производств является разработка и применение многомасштабных математических моделей химико-технологических процессов (ХЭТП), а также методов оптимального управления энергоресурсоэффективностью многостадийных химических, металлургических и горных производств как сложных ХЭТС [11].
Содержательная постановка задачи повышения энергоресурсоэфективности ХЭТС и ее многомасштабная математическая модель (ММ) в процессе инжиниринга находятся во взаимодействии друг с другом, обеспечивают динамичность самой процедуры моделирования и принятия решений (рис. 1).
Рис. 1.
Схема взаимосвязи задач многомасштабного математического моделирования и оптимизации энергоресурсоэффективности ХЭТС.
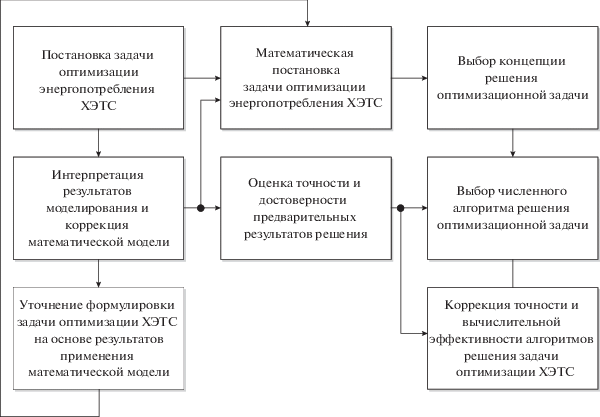
Исходная постановка задачи и начальная ММ претерпевают значительные изменения в процессе исследования, что приводит к итерационному характеру всей процедуры моделирования и дальнейшего использования его результатов. В процессе разработки адекватной модели уточняется как постановка самой общей задачи, так и сама ММ. Одна и та же задача может иметь различные ММ, в зависимости от выбранной концепции. Поэтому необходим поиск такого варианта ММ, для которой решение задачи исследований было бы наиболее простым, но обеспечивало бы требуемую глубину анализа.
Общая структура многостадийной сложной ХЭТС предполагает систематизацию и использование фундаментальных моделей физико-химических, химико-технологических и теплофизических процессов при переработке отходов из отвалов горно-обогатительных комбинатов в конкурентоспособную продукцию и учитывает четыре укрупненных уровня явлений и процессов:
1-й уровень описывает ХЭТП в отдельном окатыше;
2-й уровень отражает взаимодействия в вертикальной многослойной укладке окатышей;
3-й уровень охватывает ХЭТП в движущейся вертикальной многослойной укладке окатышей;
4-й уровень базируется на моделях первых трех уровней для решения задачи описания ХЭТП переплавки окатышей в энергоемких РТП.
Модели ХЭТП учитывают наличие множества управляющих воздействий и факторов, как для каждой вакуум-камеры обжиговоконвейерной машины, так и для РТП (характеристики исходного сырья, промежуточного и конечного продукта для РТП, функциональные зависимости параметров конечной продукции рассматриваемой ХЭТС от этих характеристик и др.). Кроме этого, необходимо учитывать возможность рационального использования вторичных энергетических ресурсов при замыкании и перераспределении энергетических потоков в системе.
Для всестороннего рассмотрения процедуры реинжиниринга для обеспечения энергоресурсоэффективности ХЭТС производства фосфора целесообразно построение для нее иерархической структуры моделей, позволяющих акцентировать внимание на разных концептуальных особенностях.
На верхнем уровне разрабатываемых моделей находятся модели международных стандартов IDEF (Icam DEFination, ICAM – Integrated Computer-Aided Manufacturing), в частности, IDEF0 (методология функционального моделирования, подкласс стандартов IDEF, которым присвоен индекс ноль), отражающего укрупненные функции инжиниринга и их взаимосвязи, осуществляемые для достижения указанных целей повышения энергоэффективности.
Разработка моделей IDEF0 предполагает последовательную декомпозицию общей задачи инжиниринга на отдельные функции до тех пор, пока состав и способ реализации их не станет окончательно ясен заинтересованным сторонам процедуры достижения поставленных целей. В начале разработки модели формируется так называемая контекстная диаграмма, отражающая самый верхний уровень иерархии исследуемых процедур, которые можно рассматривать с разных точек зрения, например, организационной, функциональной, обрабатываемых данных, структуры процессов инжиниринга, продуктов и услуг. Каждая из этих точек зрения разделяется еще на три подуровня: описание требований, описание спецификации, описание внедрения. Наиболее информативное представление для дальнейшего исследования направлений повышения энергоресурсоэффективности дает функциональная точка зрения, поэтому модель IDEF0 будет разработана именно для нее. Первый уровень декомпозиции контекстной диаграммы IDEF0 представлен на рис. 2.
Рис. 2.
Структура модели IDEF0 инжиниринга процедуры обеспечения энергоресурсоэффективности ХЭТС производства фосфора.
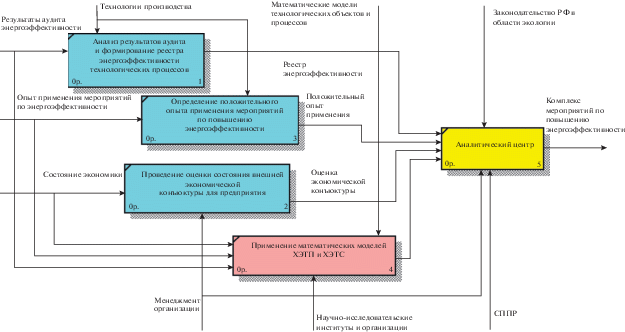
Описывающие ХЭТП ММ на представленных уровнях и реализованные в компьютерных симуляторах представляют собой сложные системы дифференциальных уравнений в частных производных, замыкаемые различными граничными условиями [12]. При этом результаты их решения для одного ХЭТП будут являться исходными данными для дифференциальных уравнений, описывающих следующий ХЭТП. Такая последовательная передача информационных потоков (сигналов) делает возможным применение методов теории автоматического управления к расчету всей многостадийной ХЭТС. С точки зрения теории автоматического управления ХЭТС представляет собой совокупность объектов с заданными наборами управляющих воздействий, помех, выходных величин (см. рис. 3).
Дальнейший анализ требует детализации входных и выходных параметров представленных на рис. 3 объектов ХЭТС производства фосфора.
На вход гранулятора подается сырье (техногенные отходы флотации апатит-нефелиновых руд в виде мелкодисперсной фракции) с заданным химическим составом, изменяющимся в зависимости от месторождения.
В грануляторе производится грануляция округлых окатышей за счет увлажнения мелкодисперсной фракции водой и окомкования на вращающихся тарельчатых дисках, наклоненных под определенным углом. Входными параметрами для объекта управления № 1 (гранулятор) выступают массовый расход воды ${{G}_{{{{{\text{H}}}_{{\text{2}}}}{\text{O}}}}}$ и сырья Gc, угол наклона тарелок α, напряжение питания электродвигателей привода тарелок Uт. Выходные величины: массовый расход окатышей Gk, влагосодержание в окатыше u0 и их диаметр d. Кроме указанных выходных величин при решении задачи энергосбережения следует выделять такой параметр, как энергопотребление первого объекта ХЭТС, обозначим его Е1.
После гранулятора сырые окатыши поступают на обжиговоконвейерную машину, которая представляет собой последовательно соединенные 44 вакуум-камеры, общей протяженностью 130 м. В каждой камере осуществляется продувка движущейся на конвейере многослойной массы окатышей нагревающим газом-теплоносителем, поступающим из горна, где за счет сгорания топлива обеспечивается высокая температура теплоносителя. Он распределяется по вакуум-камерам за счет принудительной тяги, создаваемой эксгаустерами, по технологическим зонам: сушки, предварительного подогрева, высокотемпературного обжига, рекуперации и охлаждения. Наличие большого числа вакуум-камер объясняется технологическими особенностями протекания тепломассообменных и химико-энерготехнологических процессов в обжиговоконвейерной машине. С другой стороны, это приводит к тому, что увеличивается количество контролируемых параметров (в соответствии с числом вакуум-камер) – для каждой вакуум-камеры входными воздействиями выступают температура газа-теплоносителя, на входе в нее $T_{{gi}}^{0},$ i = 1, …, nк, где nк – количество камер, а выходными: температура воздуха на выходе Tgi и расход воздуха Wgi.
Выходными параметрами всей обжиговой машины являются массовый расход Gko и конечные прочность окатышей σк и степень реагирования ηк для реакций диссоциации карбонатов MgCO3 → → MgO + CO2 и СаCO3→ СаO + CO2. В результате нагрева окатышей активируется процесс декарбонизации с выделением углекислого газа. На этот процесс затрачивается энергия, которая учитывается в общем энергобалансе производства.
Для обеспечения работы обжиговой машины затрачивается как тепловая, так и электрическая энергия (ее потребляют эксгаустеры), которую можно учесть как обобщенную величину потребляемой энергии E2 = λEт + Eэл, где Eт – тепловая энергия, входящая с весовым коэффициентом λ, учитывающим неравнозначность затрат на получение электрической Eэл и тепловой энергии.
Удельное потребление энергии в объекте № 2 ХЭТС составляет 615 МДж на тонну готовых обожженных окатышей. Интерес представляет исследование ХЭТС производства фосфора с точки зрения повышения его энергоэффективности.
Объект управления № 3 представляет собой рудовосстановительную электрическую дуговую печь, в которой происходит нагрев окатышей (температура в реакционной зоне 1500–2000°С). Расход фосфора Gp является выходной величиной РТП. На энергоресурсоэффективность функционирования РТП влияют параметры поступающих из обжиговоконвейерной машины обожженных окатышей, прочность и степень реагирования, а также глубина погружения электродов hэ вглубь печи, управляющая температурой в зоне реакции. Затраты электрической энергии для обеспечения технологического процесса плавки окатышей в РТП обозначим E3. При этом следует учесть то, что часть тепловой энергии возвращается в ХЭТС за счет перераспределения тепловых потоков и рекуперации. Удельный расход электроэнергии в РТП составляет 14.6 МВт ч на тонну готового продукта.
Общее удельное энергопотребление всей ХЭТС составляет 52755 МДж на тонну готового продукта – желтого фосфора.
Анализ тепломассообменных, химико-энерготехнологических процессов и их параметров в трех объектах декомпозиции ХЭТС позволяет конкретизировать вектора их входных (будем обозначать эти параметры символом V) и выходных параметров (обозначим символом Y), а также сформулировать критерий оптимизации с точки зрения энергоресурсоэффективности всей ХЭТС:
(1)
$\begin{gathered} {\mathbf{V}}1 = {{\left( {{{G}_{{{{{\text{H}}}_{{\text{2}}}}{\text{O}}}}},\,\,{{G}_{c}},\,\,\alpha ,\,\,{{U}_{Т }}} \right)}^{Т }}{\text{,}} \\ {\mathbf{Y}}1 = {{\left( {{{G}_{k}},\,\,{{u}_{0}},\,\,d} \right)}^{Т }}, \\ \end{gathered} $(2)
$\begin{gathered} {\mathbf{V}}2 = {{\left( {T_{g}^{0},\,\,{{G}_{k}},\,\,d,\,\,{{u}_{0}}} \right)}^{Т }}, \\ {\mathbf{Y}}2 = {{\left( {{{T}_{g}},\,\,{{G}_{{ko}}},\,\,{{\sigma }_{k}},\,\,{{\eta }_{k}}} \right)}^{Т }}, \\ \end{gathered} $(3)
$\begin{gathered} {\mathbf{V}}3 = {{\left( {{{G}_{{{\text{kщ }}}}},\,\,{{\sigma }_{k}},\,\,{{\eta }_{k}},\,\,{{h}_{{\text{э }}}}} \right)}^{Т }}, \\ {\mathbf{Y}}3 = {{\left( {{{G}_{p}},\,\,{{\sigma }_{k}},\,\,{{\eta }_{k}}} \right)}^{Т }}. \\ \end{gathered} $В (2) температуры на входе и выходе в каждую вакуум-камеру обозначены векторами:
Известные математические модели для оптимизации затрат энергии в каждом из объектов управления рассматривают их изолированно от всей технологической цепочки получения фосфора [12–17]. Так, оптимальные режимы обжига окомкованного сырья на обжиговых машинах конвейерного типа получены в [15] (в частности, для обжиговой машины ОК-520/536Ф получен режим, обеспечивающий требуемое качество готового продукта, экономию энергоресурсов и снижающий долю возврата). Режимы оптимального энергопотребления для РТП определены в [12]. В то же время для экономики представляет интерес оптимизация энергопотребления для всего многостадийного процесса получения фосфора, определение не столько локальных минимумов энергопотребления для каждого из рассматриваемых объектов, сколько глобального экстремума, возможно и с отклонением от оптимальности для отдельно взятого объекта.
Наличие большого числа влияющих факторов, сгруппированных в вектора (1–3), на рассматриваемые технологические процессы повышает вероятность полиэкстремальности поверхности функции отклика целевой функции оптимизации [18]. Данное обстоятельство делает актуальной задачу комплексного исследования рассматриваемой ХЭТС с целью разработки методов и алгоритмов определения оптимальных с точки зрения энергоэффективности параметров объектов ХЭТС производства фосфора. Целевая функция оптимизации энергоресурсоэффективности многостадийной ХЭТС получения фосфора должна учитывать энергопотребление Ei, i = 1… 3, каждого объекта управления ХЭТС, но при этом необязательно обеспечивать частные минимумы Ei.
Общий критерий энергоресурсоэффективности представляется в виде линейной комбинации частных критериев Ei объектов управления
где λi – весовые коэффициенты, задаваемые для обеспечения возможности настройки процедуры оптимизации.Ограничения в задаче оптимизации формируются с учетом технических особенностей и режимов функционирования агрегатов ХЭТС и специфики протекания тепломассообменных и химико-энерготехнологических процессов [15, 17].
Задача поиска экстремума (4) требует расчета вектора (E1, E2, E3) с дальнейшим выбором вектора, обеспечивающего минимизацию критерия Е. Эта задача разбивается на несколько подзадач:
1. Получение математического описания частных ХЭТП с точки зрения расчета их энергоэффективности.
2. Разработка и тестирование программных моделей ХЭТП на основе их математического описания.
3. Агрегация частных моделей в единую программную модель (ЕПМ) многостадийных ХЭТП и ее тестирование.
4. Использование ЕПМ для расчета векторов (E1, E2, E3).
5. Применение оптимизационной процедуры для выявления оптимальных параметров обобщенной ХЭТС.
В представленном списке пункты 1 и 2 уже имеют свое решение и представлены в [1, 15–17]. Исследования и разработки требуют пункты 3–5. Остановимся подробнее на методологических аспектах их реализации.
Для выполнения агрегации разработанных программных моделей частных ХЭТП в п. 3 необходима среда их развертывания. Такой средой может быть выбран пакет моделирования динамических систем Simulink, входящий в состав программной среды MatLAB [19]. Для его использования целесообразно преобразовать частные математические модели к форме, пригодной для расчетов в Simulink, например, к форме описания систем управления в терминах пространства состояний, применяемой к решению задач оценивания, как для непрерывного, так и для дискретного времени [20, 21].
Локальные модели объектов управления представляют собой системы дифференциальных уравнений в частных производных разных порядков, и перейти от них к форме описания в терминах пространства состояний весьма проблематично. Поэтому было принято решение использовать эти модели для получения разгонных характеристик объектов по различным каналам (1–3), а затем осуществить их аппроксимацию [22]. Совокупность таких разгонных характеристик дала возможность получить линеаризованные (вблизи точек стационарного режима) модели объектов управления в форме передаточных функций и от них осуществить переход к описанию в терминах пространства состояний. Если ввести вектор переменных состояния X(t), то систему управления можно описать в форме векторно-матричного дифференциального уравнения первого порядка:
дополненного уравнением выхода:
где А – матрица системы, B, D – вектора передачи управления, V – входное воздействие по данному каналу, Y – вектор входных переменных, C – матрица наблюдения.Распространение изложенного подхода на все каналы управления дает возможность рассчитать параметры энергопотребления при различных комбинациях входных данных и учесть перекрестное взаимовлияние переменных ХЭТП.
ПРОГРАММНАЯ РЕАЛИЗАЦИЯ И РЕЗУЛЬТАТЫ
Применяя предложенный подход описания объектов управления в терминах пространства состояний, была разработана структура ЕПМ ХЭТC производства фосфора в среде Simulink. Последовательное соединение программных моделей гранулятора, обжиговоконвейерной машины и РТП отражает многостадийность и последовательность функционирования ХЭТС, поддерживая адекватность всей программной модели. Общая структура компьютерной программной модели отражена на рис. 4.
Схема, представленная на рис. 4, позволяет проводить моделирование при различных комбинациях исходных данных, параметров и управлений за счет применения таких структурных элементов, как входные и выходные порты (обозначены на рис. 4 числами 1, 2, 3, 4 с соответствующим их назначению направлением стрелок).
Имитационный эксперимент в Simulink был проведен на фрагменте ЕПМ с целью исследования влияния двух факторов (радиуса окатыша и его влагосодержания) на величину энергопотребления ХЭТП. Моделирование проводилось для значений этих параметров, лежащих в следующих пределах: радиус окатыша от 0.9 до 1.1 см, влагосодержание от 12.6 до 13.4%. Результаты эксперимента, в виде карты линий уровня поверхности величины энергопотребления (МДж) ХЭТП в зависимости от радиуса окатыша и его влагосодержания, показаны на рис. 5.
На рис. 5 прямоугольником выделена область, соответствующая допустимым технологическим отклонения радиуса окатыша и его влагосодержания. Исследование ее топологии позволяет найти те сочетания влияющих параметров, которые обеспечивают минимум энергопотребления ХЭТC, не выходя за пределы технологических нормативов по параметрам окатышей.
Визуальный анализ технологической зоны показывает, что в ней присутствуют минимумы энергопотребления (линия уровня со значением энергопотребления 53400 МДж на тонну готового продукта). Отметим, что изолированная оптимизация каждого объекта единой ХТЭС по отдельности и дальнейшее суммирование энергопотреблений объектов показало лишь уровень 54900 МДж на тонну готового продукта.
Следовательно, есть возможность устанавливать значения параметров отдельных ХЭТП таким образом, чтобы обеспечивался минимум энергопотребления всей обобщенной ХЭТС, а не отдельных ее объектов.
Дальнейшие работы в выбранном направлении исследований будут направлены на разработку программных модулей ЕПМ ХЭТП для других фрагментов агрегированной модели, рассчитывающих комплексное влияние на энергопотребление всех параметров ХЭТС [23, 24].
ЗАКЛЮЧЕНИЕ
В ходе проведенного исследования был предложен подход к построению обобщенной модели инжиниринга многостадийного производства фосфора на основе сжигания окатышей апатит-нефелиновых руд в высокотемпературных руднотермических печах, позволяющий оптимизировать энергопотребление этого производства. Следствием решения такой оптимизационной задачи является не только повышение энергоэффективности производства фосфора, но и снижение уровня техногенного загрязнения окружающей среды за счет уменьшения объемов отходов апатит-нефелиновых руд за счет более глубокой их переработки.
В основе предлагаемого подхода лежит исключение принципа изолированного рассмотрения задач минимизации энергопотребления отдельными технологическими установками и рассмотрение их в едином комплексе на основе многомасштабных математических моделей.
Для обобщенного восприятия всего комплекса мероприятий по инжинирингу ХЭТС была разработана его функциональная модель в соответствии с международным стандартом IDEF0, отражающая декомпозицию целевой задачи инжиниринга на более детализированные функции, а также результаты этих функций в процессе достижения заявленной цели оптимизации энергопотребления и снижения уровня техногенного загрязнения при производстве фосфора.
В работе представлена концепция направлений работ по программной реализации предложенного подхода к оптимизации энергопотребления ХТЭС и результаты имитационного эксперимента на фрагменте единой программной модели в среде Simulink с целью исследования влияния двух факторов (радиуса окатыша и его влагосодержания) на величину энергопотребления ХЭТП. Эксперимент показал, что оптимизация энергопотребления ХТЭС как единой, взаимосвязанной системы позволяет достигать лучших решений по сравнению с результатами, получаемыми при оптимизации каждого элемента ХЭТС по отдельности. В проведенном эксперименте, в области технологических допусков параметров окатышей, был достигнут минимум энергопотребления в 53.4 ГДж на тонну готового продукта, в то время как изолированная оптимизация энергопотребления каждого объекта единой ХТЭС по отдельности позволила достичь этот показателя лишь на уровне 54.9 ГДж на тонну готового продукта.
Исследование выполнено при финансовой поддержке Российского фонда фундаментальных исследований в рамках научного проекта № 18-29-24094 MK.
Список литературы
Bobkov V.I., Fedulov A.S., Dli M.I., Meshalkin V.P., Morgunova E.V. Scientific basis of effective energy resource use and environmentally safe processing of phosphorus-containing manufacturing waste of ore-dressing barrows and processing enterprises // Clean Technologies and Environmental Policy. 2018. V. 20. № 10. P. 2209.
Bobkov V.I., Borisov V.V., Dli M.I., Meshalkin V.P. Intensive Technologies for Drying a Lump Material in a Dense Bed // Theor. Found. Chem. Eng. 2017. V. 51. № 1. P. 72. [Бобков В.И., Борисов В.В., Дли М.И., Мешалкин В.П. Интенсивные технологии сушки кускового материала в плотном слое // Теорет. основы хим. технологии. 2017. Т. 51. № 1. С. 72.]
Pavlov S.Yu., Kerimov R.M., Kulov N.N. Improvement of chemical engineering processes using systems analysis // Theor. Found. Chem. Eng. 2014. V. 48. № 2. P. 117. [Павлов С.Ю., Кулов Н.Н., Керимов Р.М. Совершенствование химико-технологических процессов на основе системного анализа // Теорет. основы хим. технологии. 2014. Т. 48. № 2. С. 131.]
Meshalkin V.P., Panchenko S.V., Dli M.I., Panchenko D.S. Analysis of the Thermophysical Processes and Operating Modes of Electrothermic Reactor Using a Computer Model // Theor. Found. Chem. Eng. 2018. V. 52. № 2. P. 166. [Мешалкин В.П., Панченко С.В., Дли М.И., Панченко Д.С. Анализ теплофизических процессов и режимов работы электротермического реактора с использованием компьютерной модели // Теорет. основы хим. технологии. 2018. Т. 52. № 2. С. 141.]
Берсенев И.С., Клейн В.И., Матюхин В.И., Ярошенко Ю.Г. Снижение энергоемкости агломашин за счет совершенствования их тепловых схем // Энергобезопасность и энергосбережение. 2011. № 3. С. 22.
Bobkov V.I., Borisov V.V., Dli M.I., Meshalkin V.P. Multicriterial optimization of the energy efficiency of the thermal preparation of raw materials // Theor. Found. Chem. Eng. 2015. V. 49. № 6. P. 842. [Бобков В.И., Борисов В.В., Дли М.И., Мешалкин В.П. Многокритериальная оптимизация энергоэффективности технологических процессов термической подготовки сырья // Теорет. основы хим. технологии. 2015. Т. 49. № 6. С. 665.]
Yin R. Metallurgical Process Engineering. Berlin: Springer-Verlag, 2011.
Катаев А.А., Мелихов А.А. Вопросы управления затратами металлургического предприятия // Изв. вузов. Черная металлургия. 2006. № 5. С. 61.
Liu W., Yang J., Xiao B. Review on treatment and utilization of bauxite residues in China // International J. Mineral Processing. 2009. V. 93. P. 220.
Петрышев А.Ю., Берсенев И.С., Боковиков Б.А., Ярошенко Ю.Г. Исследование особенностей формирования оксидов азота при агломерации железных руд // Изв. вузов. Черная металлургия. 2016. Т. 59. № 4. С. 232.
Meshalkin V.P., Bobkov V.I., Dli M.I., Khodchenko S.M. Computer modeling of the chemical-power engineering process of roasting of a moving multilayer mass of phosphorite pellets // Doklady Chemistry. 2017. V. 477. № 2. P. 282. [Мешалкин В.П., Бобков В.И., Дли М.И., Ходченко С.М. Компьютерное моделирование химико-энерготехнологического процесса обжига движущейся многослойной массы фосфоритовых окатышей // Докл. АН. 2017. Т. 477. № 5. С. 559.]
Panchenko S.V., Meshalkin V.P., Dli M.I., Borisov V.V. Computer-visual model of thermophysical processes in electrothermal reactor // Tsvetnye Metally. 2015. № 4. P. 55.
Новичихин А.В., Шорохова А.В. Процедуры управления поэтапной переработкой железорудных отходов горнопромышленных районов // Изв. вузов. Черная металлургия. 2018. Т. 60. № 7. С. 565.
Panchenko S.V., Shirokikh T.V. Thermophysical processes in burden zone of submerged arc furnaces // Theor. Found. Chem. Eng. 2014. V. 48. № 1. P. 77. [Панченко С.В., Широких Т.В. Теплофизические процессы в шихтовой зоне электротермических рудовосстановительных реакторов // Теорет. основы хим. технологии. 2014. Т. 48. № 1. С. 83.]
Elgharbi S., Horchani-Naifer K., Férid M. Investigation of the structural and mineralogical changes of Tunisian phosphorite during calcinations // J. Thermal Analysis and Calorimetry. 2015. V. 119. № 1. P. 265.
Леонтьев Л.И. Физико-химические особенности комплексной переработки железосодержащих руд и техногенных отходов // ХХ Менделеевский съезд по общей и прикладной химии. Екатеринбург, 2016. С. 92.
Luis P., Van der Bruggen B. Exergy analysis of energy-intensive production processes: advancing towardsa sustainable chemical industry // J. Chemical Technology and Biotechonology. 2014. V. 89. № 9. P. 1288.
Захарова Е.М., Кузнецов Н.А., Минашина И.К. и др. Моделирование алгоритмов оптимизации мультиагентной системы управления перевозочным процессом // Вестник Международной академии системных исследований. Информатика, экология, экономика. 2014. Т. 16. № 1. С. 9.
Черных И.В. Simulink: среда создания инженерных приложений. М.: Диалог-МИФИ, 2003.
Олссон Г., Пиани Д. Цифровые системы автоматизации и управления. 3-е изд., перераб. и доп. СПб.: Невский диалект, 2001.
Бухалев В.А. Оптимальное сглаживание в системах со случайной скачкообразной структурой. М.: Физматлит, 2013.
Кулаков Г.Т. Анализ и синтез систем автоматического регулирования. Минск: Технопринт, 2003.
Bokovikov B.A., Bragin V.V., Shvydkii V.S. Role of the thermal-inertia zone in conveyer roasting machines // Steel in Translation. 2014. V. 44. № 8. P. 595.
Bragin V.V., Bokovikov B.A., Naidich M.I., Gruzdev A.I., Shvydkii V.S. Relation between the productivity and fuel consumption in roasting machines // Steel in Translation. 2014. V. 44. № 8. P. 590.
Дополнительные материалы отсутствуют.
Инструменты
Теоретические основы химической технологии