Теоретические основы химической технологии, 2019, T. 53, № 6, стр. 664-675
Влияние агрегатного состава питания на эффективность применения колонн с перегородками для ректификации смесей углеводородов
С. О. Кочарян a, Д. Г. Рудаков a, П. С. Клаузнер a, А. В. Тимошенко a, *
a МИРЭА – Российский технологический университет
Москва, Россия
* E-mail: timoshenko@mitht.ru
Поступила в редакцию 10.07.2019
После доработки 16.07.2019
Принята к публикации 18.07.2019
Аннотация
Рассмотрено применение колонн с перегородками для разделения фракции С4+ пиролиза. Исследовано влияние агрегатного состояния потока питания на энергозатраты в кипятильниках колонн. Впервые показано, что применение колонн с перегородками является более эффективным при использовании потока питания с высокой долей пара, равной 80–100%. При этом наибольший энергетический эффект колонны перегородкой обеспечивают при использовании питания в виде пара, в этом случае экономия энергоресурсов может достигать 30%. Помимо этого, показано, что применение колонн с перегородкой обеспечивает снижение капитальных затрат на 18–21%.
ВВЕДЕНИЕ
В химической технологии для разделения и очистки широко применяется процесс ректификации. Известно, что он характеризуется относительно невысоким коэффициентом полезного действия и высокими удельными затратами энергии. Процесс ректификации является термодинамически необратимым, что приводит к зависимости затрат энергии и производства энтропии от последовательности выделения фракций, т.е. от пути его проведения. Поэтому структура технологической схемы ректификации предопределяет энергетическую эффективность процесса [1], а задача синтеза оптимальной технологической схемы является одной из важнейших в химической технологии [2]. Повысить эффективность ректификации можно в рамках нескольких направлений совершенствования этого объекта. Наиболее интенсивно развиваются два направления. Первое из них связано с применением тепловых насосов как в обычной ректификации, так и в системах HIDiC (heat integrated distillation column) [3–10], а второе – с использованием сложных колонн с перегородками DWC (dividing wall column). В последнем случае повышение эффективности процесса достигается за счет исключения одной или нескольких зон необратимого смешения за счет применения систем с частично или полностью связанными тепловыми и материальными потоками. При этом происходит приближение реального процесса к гипотетическому термодинамически обратимому. Такой подход был впервые предложен отечественными исследователями [11] и реализуется в виде комплексов с полностью связанными тепловыми и материальными потоками (fully thermally coupled distillation system, FTCDS). Промежуточными вариантами по термодинамической эффективности между классической ректификацией (SD) и FTCDS служат технологические схемы, включающие комплексы с частично связанными тепловыми и материальными потоками (partially thermally coupled distillation system, PTCDS). FTCDS и PTCDS в промышленности реализуются в виде DWC, которые в ряде случаев являются их термодинамическими аналогами. Примером, когда DWC не являются полными термодинамическими эквивалентами FTCDS или PTCDS, могут служить некоторые из колонн Кайбеля [12–15]. Одним из лидеров в промышленной разработке и реализации колонн с перегородками является компания BASF [16]. В настоящее время организация процесса в виде DWC считается одной из наиболее перспективных, поскольку позволяет снизить как эксплуатационные, так и капитальные затраты на разделение. Исследованию и совершенствованию работы DWC посвящено значительное число работ, в которых рассматриваются разделение различных смесей [17–25 ], общие вопросы дизайна этих аппаратов [26–38], устойчивость и управляемость [39–42], вопросы активного регулирования потоков пара [43, 44], а также полистационарности процесса [26].
Достаточно давно сформировалось представление о термодинамически эквивалентных процессах (схемах) ректификации [45]. Подразумевается, что вне зависимости от геометрического (в разных или в одном аппарате) расположения секций, их топология остается неизменной. Очевидно, что режимы работы отдельных секций при заданных параметрах процесса также будут сохраняться. Следовательно, имеются существенные предпосылки для того, чтобы, используя принцип термодинамической эквивалентности, преобразовать FTCDS и PTCDS в DWC. Отметим, что для DWC, термодинамически эквивалентной FTCDS, такие решения были предложены еще Ф.Б. Петлюком и Л.А. Серафимовым [46].
Ранее нами было предложено использовать теорию графов для преобразования технологических схем обычной [47–49] и экстрактивной ректификации [50–53] в системы с частично связанными тепловыми и материальными потоками. Показано, что применение таких PTCDS как элементов технологической схемы ректификации в ряде случаев обеспечивает значительное (30% и более) снижение энергозатрат на разделение [54–58].
Таким образом, предлагается, используя традиционную технологическую схему ректификации из простых двухсекционных колонн в качестве прообраза, сформировать PTCDS, а затем, используя принцип термодинамической эквивалентности, превратить ее в колонну с перегородкой, с обеспечением сохранения концентрационных и температурных профилей в каждой из секций. Такой метод синтеза DWC назван репрографией, т.е. сжатием технологической схемы в один аппарат [54]. При этом обеспечивается полное при трансформации PTCDS в DWC или частичное при переходе от SD к PTCDS сохранение топологии секций, тепловых и материальных потоков в зависимости от глубины преобразований. Максимальная преемственность структуры потоков на основе анализа исходной технологической схемы позволяет эффективно организовать внутренние потоки в сложной колонне и обеспечивает значительное снижение энергозатрат на разделение, а переход к DWC ведет и к снижению капитальных затрат. В качестве объекта исследования нами рассмотрено разделение фракции С4+ парафиновых углеводородов. Эта задача имеет широкое прикладное значение, поскольку такой узел характерен для всех газофракционирующих установок нефтехимических предприятий. В данном случае рассмотрено разделение фракции на три продуктовых потока: фракции изобутана, н-бутана и С5+.
РАСЧЕТНАЯ ЧАСТЬ
Исходная смесь представляет собой смесь парафиновых углеводородов с составом, представленным в табл. 1. Общий объем исходного питания задан равным 55800 кг/ч. Исходя из возможности применения в качестве хладагента оборотной воды в PTCDS выбрано рабочее давление, равное 6.6 атм. Здесь и далее используется абсолютное давление. Температура начала кипения исходной смеси при указанном давлении составляет TIBP = = 83.74°C, конца кипения – ТEP = 101.33°C.
Таблица 1.
Состав смеси парафиновых углеводородов
Компонент | Содержание, мас. д. |
---|---|
Пропан | 0.0009 |
Изобутан | 0.2084 |
н-бутан | 0.0521 |
Изопентан | 0.1563 |
н-пентан | 0.4167 |
н-гексан | 0.1656 |
Расчеты проводили в проектно-поверочном варианте. Качество продуктовых потоков поддерживали на одинаковом уровне, придерживаясь следующих спецификаций: суммарная концентрация изобутана в изобутановой фракции 99.15 мас. %, суммарная концентрация н-бутана в н-бутановой фракции 99.2 мас. %, концентрация бутанов в пентановой фракции 0.04 мас. %. Для расчета использовали программный комплекс Aspen Plus v.9. В качестве модели описания парожидкостного равновесия была выбрана модель SRK со встроенными параметрами Aspen Plus, поскольку известно, что эта модель хорошо описывает парожидкостное равновесие в указанной системе в широком интервале температур и давлений [56]. Общее число тарелок в колоннах выбирали по графику Джиллиленда. При организации схемы по первому заданному разделению (I ЗР) общее число тарелок в первой колонне принято равным 69, во второй – 36. Для схемы по второму заданному разделению (II ЗР) общее число тарелок в первой колонне – 36, во второй – 69. Коэффициент полезного действия тарелки принят равным 0.6. Поскольку требований единства давлений в технологической схеме из отдельных ректификационных колонн нет, то для простой ректификации были приняты давления, равные 6.6 и 6.1 атм соответственно для первой и второй колонн схемы, работающей по первому заданному разделению, и 6.1 и 6.6 атм для схемы, работающей по второму заданному разделению. В качестве переменных оптимизации выступали номера тарелок питания колонн.
Вторым объектом исследования являлись сложные колонны с перегородкой, термодинамически эквивалентные колоннам с боковой укрепляющей (PTCDS D/DWC) или исчерпывающей (PTCDS I/DWC) секцией (рис. 1д–1е). Репрографический метод синтеза сложных колонн такого типа для ректификации зеотропных смесей описан выше.
Рис. 1.
Схемы из простых колонн, работающие по I ЗР (а) и II ЗР (в); PTCDS на основе I ЗР (б) и II ЗР (г); сложная колонна с перегородкой на основе PTCDS I ЗР (д) и II ЗР (е).
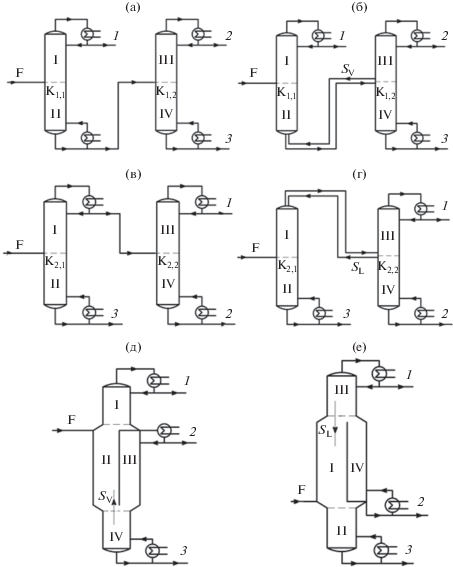
Системы DWC по структуре потоков полностью идентичны PTCDS, поэтому при расчете и оптимизации использовали представление DWC в виде отдельных аппаратов, связанных тепловыми и материальными потоками (рис. 1б–1г). Для сохранения основных характеристик традиционных схем при репрографии применяли поэтапное преобразование SD в DWC/PTCDS. Например, в схему SD, работающую по первому заданному разделению (рис. 1а), дополнительно вводили обратный паровой поток с тарелки питания колонны К1,2 в куб первой колонны К1,1 (рис. 1б). Величину потока увеличивали постепенно от нуля до такого уровня, при котором энергетические затраты в кипятильнике первой колонны становились практически равными нулю. Одновременно для соблюдения материального баланса увеличивали жидкостный поток из куба первой колонны во вторую. При этом нагрузка на кипятильник К1,2 увеличивается, однако суммарное энергопотребление кипятильников К1,1, К1,2 снижается. Этот подход позволил определить величину бокового отбора из основной колонны в боковую секцию.
Переход к комплексам DWC/PTCDS от схемы SD, работающей по второму заданному разделению, проводили аналогичным образом. Единственное отличие состояло в том, что перед процедурой связывания колонн обратным потоком, в данном случае жидкостным, полный конденсатор К2,1 заменяли на парциальный.
По структуре потоков колонна с перегородкой в соответствии с правилами репрографии технологических схем должна быть полностью идентична своему прообразу – комплексу с частично связанными тепловыми и материальными потоками, т.е. внутренние потоки, температурные и концентрационные профили должны быть идентичны для соответствующих пар схем (рис. 1б–1д и рис. 1г–1е).
Затем оптимизацию схем DWC/PTCDS осуществляли по трем параметрам. Переменными оптимизации были: величина обратного потока (с учетом материального баланса и на основе предварительно полученного хорошего начального приближения, описанного выше), положения тарелок подачи питания в основные колонны, а также положения тарелки бокового отбора. Поскольку для всех комплексов PTCDS тарелка отбора потока из основной колонны в боковую секцию и возврата потока из боковой секции совпадают по условиям преобразования SD в DWC/PTCDS, то они варьировались одновременно до достижения минимального значения величины критерия оптимизации Q = ΣQi → min, где Qi – это тепловая нагрузка на кипятильник i колонны.
РЕЗУЛЬТАТЫ И ИХ ОБСУЖДЕНИЕ
Были получены оптимальные тарелки питания и отборов в системах DWC/PTCDS, а также массив данных по тепловым нагрузкам на конденсаторы и кипятильники для всех рассматриваемых технологических решений. Температуру исходного состава питания изменяли от 75 до 120°С. При разделении в простых колоннах, поскольку отсутствуют обратные тепловые и материальные связи, режим работы второй колонны не зависит от температуры и агрегатного состояния питания первой колонны, а только от температуры в кубе первой колонны для первого и температуры дистиллята для второго заданных разделений. Параметры работы технологических схем, обеспечивающие минимальные нагрузки на кипятильники колонн, приведены в табл. 2 и 3, где TF – температура питания, VF – доля пара в питании, NF –оптимальная тарелка питания, R – флегмовое число, d – расчетный диаметр секций колонн, H – высоты секций. Нумерация секций: укрепляющие I и III, исчерпывающие II и IV по ходу колонн в разделении).
Таблица 2.
Основные параметры схемы, работающей по первому заданному разделению
Первая колонна (К1,1) | |||||||||
---|---|---|---|---|---|---|---|---|---|
TF , °С | VF | NF | Qreb, кВт | Qcond, кВт | R | dI, м | dII, м | HI, м | HII, м |
75 | 0 | 24 | 12 877 | –12 195 | 9.84 | 2.75 | 3.15 | 14.4 | 27 |
80 | 0 | 24 | 12 815 | –12 343 | 9.97 | 2.76 | 3.13 | 14.4 | 27 |
83.74 | 0 | 24 | 12 768 | –12 454 | 10.07 | 2.78 | 3.13 | 14.4 | 27 |
85 | 0.07 | 24 | 12 658 | –12 682 | 10.27 | 2.80 | 3.12 | 14.4 | 27 |
90 | 0.34 | 25 | 12 256 | –13 667 | 11.15 | 2.92 | 3.08 | 15.0 | 26.4 |
95 | 0.62 | 26 | 11 895 | –14 806 | 12.16 | 3.04 | 3.04 | 15.6 | 25.8 |
101.33 | 1 | 27 | 11 498 | –16 425 | 13.60 | 3.21 | 3.00 | 16.2 | 25.2 |
110 | 1 | 27 | 11 441 | –16 655 | 13.80 | 3.23 | 2.99 | 16.2 | 25.2 |
120 | 1 | 27 | 11 377 | –16 927 | 14.04 | 3.26 | 2.98 | 16.2 | 25.2 |
Вторая колонна (К1,2) | |||||||||
TF, °С | VF | NF | Qreb, кВт | Qcond, кВт | R | dIII, м | dIV, м | HIII, м | HIV, м |
101.91 | 0 | 17 | 3219 | –3353 | 10.95 | 1.42 | 1.87 | 10.2 | 11.4 |
Таблица 3.
Основные параметры схемы, работающей по второму заданному разделению
Первая колонна (К2,1) | |||||||||
---|---|---|---|---|---|---|---|---|---|
TF, °С | VF | NF | Qreb, кВт | Qcond, кВт | R | dI, м | dII, м | HI, м | HII, м |
75 | 0 | 17 | 6282 | –4723 | 2.35 | 1.63 | 2.19 | 10.2 | 11.4 |
80 | 0 | 17 | 6173 | –4824 | 2.42 | 1.65 | 2.17 | 10.2 | 11.4 |
83.74 | 0 | 17 | 6094 | –4904 | 2.48 | 1.66 | 2.16 | 10.2 | 11.4 |
85 | 0.07 | 17 | 5930 | –5077 | 2.60 | 1.69 | 2.13 | 10.2 | 11.4 |
90 | 0.34 | 17 | 5380 | –5914 | 3.19 | 1.84 | 2.04 | 10.2 | 11.4 |
95 | 0.62 | 17 | 4961 | –6996 | 3.96 | 2.01 | 1.97 | 10.2 | 11.4 |
101.33 | 1 | 17 | 4592 | –8643 | 5.13 | 2.26 | 1.91 | 10.2 | 11.4 |
110 | 1 | 17 | 4551 | –8889 | 5.30 | 2.29 | 1.90 | 10.2 | 11.4 |
120 | 1 | 17 | 4506 | –9180 | 5.51 | 2.33 | 1.89 | 10.2 | 11.4 |
Вторая колонна (К2,2) | |||||||||
TF, °С | VF | NF | Qreb, кВт | Qcond, кВт | R | dIII, м | dIV, м | HIII, м | HIV, м |
50.89 | 0 | 30 | 7804 | –7834 | 5.99 | 1.72 | 2.87 | 18.0 | 23.4 |
С повышением температуры питания затраты тепла в кубах в обоих случаях падают. Как было отмечено ранее, это достаточно известный факт. Падение тепловых нагрузок не является линейным, а имеет перегибы в точках изменения фазового состояния питания. Первый перегиб соответствует появлению паровой фазы, а второй – исчезновению жидкой фазы в питании. Практически наблюдается три линейных участка. Видно, что с точки зрения потребления энергоресурсов для всех режимов второе заданное разделение является предпочтительным (рис. 2).
Рис. 2.
Зависимости нагрузок на кипятильник (Qreb) первой колонны схемы, работающей по I ЗР (а) и II ЗР (б) от температуры потока питания.
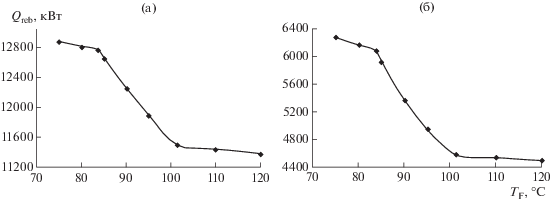
Для обеспечения единства давления в сложной колонне было установлено общее давление, равное 6.5 атм. В качестве дополнительного параметра при оптимизации использована величина потока пара SV (жидкости – SL) поступающего в боковую секцию сложной колонны. Оптимальные режимные параметры работы колонн с перегородками представлены в табл. 4, 5.
Таблица 4.
Основные параметры схемы PTCDS/DWC, работающей по первому заданному разделению
TF, °C | VF | NV | NF | SV, кг/ч | $Q_{{{\text{cond}}}}^{{{\text{K}}1,1}}$, кВт | RК1,2 | $Q_{{{\text{reb}}}}^{{{\text{K}}1,2}},$ кВт | $Q_{{{\text{cond}}}}^{{{\text{K}}1,2}},$ кВт | RК 1,2 |
---|---|---|---|---|---|---|---|---|---|
75 | 0 | 17 | 24 | 115 038 | –11 490 | 9.20 | 13 201 | –948 | 2.16 |
80 | 0 | 17 | 24 | 114 612 | –11 643 | 9.34 | 13 169 | –971 | 2.24 |
83.74 | 0 | 17 | 24 | 114 514 | –11 805 | 9.48 | 13 118 | –941 | 2.31 |
85 | 0.07 | 17 | 24 | 113 527 | –12 042 | 9.69 | 13 016 | –934 | 2.31 |
90 | 0.34 | 17 | 25 | 109 694 | –13 029 | 10.61 | 12 759 | –925 | 2.30 |
95 | 0.62 | 17 | 26 | 105 512 | –14 111 | 11.53 | 12 253 | –918 | 2.48 |
101.33 | 1 | 17 | 27 | 102 219 | –15 790 | 13.01 | 11 886 | –916 | 2.37 |
110 | 1 | 17 | 27 | 101 952 | –16 106 | 13.30 | 11 752 | –910 | 2.31 |
120 | 1 | 17 | 27 | 101 566 | –16 301 | 13.61 | 11 621 | –904 | 2.31 |
Таблица 5.
Основные параметры схемы PTCDS/DWC, работающей по второму заданному разделению
TF, °C | VF | NSL | NF | SL, кг/ч | $Q_{{{\text{reb}}}}^{{{\text{K2}},1}},$ кВт | $Q_{{{\text{reb}}}}^{{{\text{K2}},2}},$ кВт | $Q_{{{\text{cond}}}}^{{{\text{K2}},2}},$ кВт | RК2,2 | Qsum, кВт |
---|---|---|---|---|---|---|---|---|---|
75 | 0 | 33 | 18 | 50 547 | 6466 | 5185 | –10 127 | 8.06 | 11 651 |
80 | 0 | 33 | 18 | 52 127 | 6373 | 5129 | –10 186 | 8.14 | 11 501 |
83.74 | 0 | 33 | 18 | 52 991 | 6277 | 5114 | –10 235 | 8.18 | 11 391 |
85 | 0.07 | 33 | 18 | 55 552 | 6135 | 5032 | –10 341 | 8.28 | 11 167 |
90 | 0.34 | 33 | 18 | 66 717 | 5562 | 4748 | –10 878 | 8.75 | 10 309 |
95 | 0.62 | 33 | 18 | 82 446 | 5222 | 4359 | –11 650 | 9.46 | 9581 |
101.33 | 1 | 33 | 18 | 104 982 | 4875 | 3919 | –12 879 | 10.55 | 8794 |
110 | 1 | 33 | 18 | 108 276 | 4833 | 3874 | –13 079 | 10.73 | 8707 |
120 | 1 | 33 | 18 | 112 074 | 4780 | 3843 | –13 331 | 10.97 | 8623 |
В случае применения для разделения сложной колонны с укрепляющей боковой секцией (рис. 1д) наблюдается практически прямо пропорциональная зависимость между снижением потока пара, направляемого в боковую секцию из главной колонны, и падением тепловой нагрузки на кипятильник (рис. 3а). Напротив, при снижении потока жидкости в боковую секцию суммарное потребление энергии растет (рис. 3б).
Рис. 3.
Зависимости: (а) – нагрузок на кипятильник (Qreb) и отбора потока пара (SV) от температуры потока питания; (б) – нагрузок на кипятильник (Qreb) и отбора потока жидкости (SL) от температуры потока питания.

Обратим внимание, что эти зависимости связаны с температурой исходного питания и его агрегатного состояния. Во всех случаях суммарное потребление энергии в кипятильниках падает с увеличением температуры исходного питания. Практически этот параметр мало зависит от температуры захоложенной жидкости или перегретого пара, но существенно зависит от доли пара в питании при переходе с повышением температуры от состояния кипящая жидкость к состоянию насыщенный пар.
Сравнение тепловых нагрузок на кипятильники колонн для комплексов с частично связанными тепловыми и материальными потоками и схем из простых двухсекционных колонн приведено в табл. 6 и на рис. 4.
Таблица 6.
Нагрузки на кипятильники колонн для схем обычной ректификации (QSD) и PTCDS (QPTCDS) в зависимости от типа разделения, температуры и доли пара в питании
TF, °C | VF | Первое заданное разделение | Второе заданное разделение | ||||
---|---|---|---|---|---|---|---|
QSD, кВт | QPTCDS, кВт | ΔQ, % | QSD, кВт | QPTCDS, кВт | ΔQ, % | ||
75 | 0 | 16 096 | 13 201 | 17.98 | 140 86 | 11 651 | 17.29 |
80 | 0 | 16 034 | 13 169 | 17.87 | 13 977 | 11 501 | 17.71 |
83.74 | 0 | 15 987 | 13 118 | 17.94 | 13 898 | 11 391 | 18.04 |
85 | 0.07 | 15 877 | 13 016 | 18.02 | 13 34 | 11 167 | 18.69 |
90 | 0.34 | 15 475 | 12 759 | 17.55 | 13 184 | 10 309 | 21.80 |
95 | 0.62 | 15 114 | 12 253 | 18.93 | 12 765 | 9581 | 24.94 |
101.33 | 1 | 14 717 | 11 886 | 19.24 | 12 396 | 8794 | 29.06 |
110 | 1 | 14 660 | 11 752 | 19.83 | 12 355 | 8707 | 29.53 |
120 | 1 | 14 596 | 11 621 | 20.38 | 12 310 | 8623 | 29.95 |
Рис. 4.
Изменение нагрузок на кипятильники колонн (Qreb) от температуры исходного питания: 1 – схема из простых колонн I ЗР, 2 – схема из простых колонн II ЗР, 3 – схема PTCDS/DWC I ЗР, 4 – схема PTCDS/DWC II ЗР.
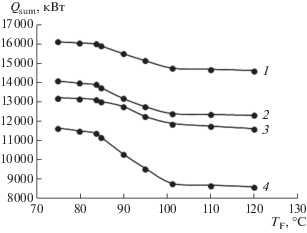
Так же как и на примере разделения фракции продуктов пиролиза [54], наблюдается зависимость величины снижения энергопотребления в кубах колонн при применении DWC (рис. 5). При этом максимальная эффективность достигается при использовании питания в паровой фазе.
Рис. 5.
Снижение нагрузок на кипятильники колонн (ΔQ) при использовании для разделения DWC в зависимости от температуры питания.
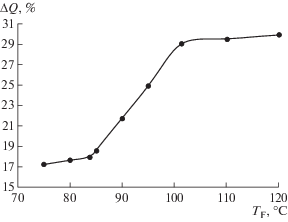
Приведенные выше данные не учитывают затрат тепла на подогрев или охлаждение исходного питания. Исходя из технологических данных, в схемах газофракционирующих установок после депропанизации сырьевой поток, как правило, имеет давление 15 атм и температуру 140°С. При дросселировании до рабочего давления в аппаратах, равного 6.6 атм, температура снижается до 128.25°С, а образование жидкой фазы не происходит.
Если на предприятии имеется возможность использования низкопотенциального тепла с температурой 70–100°С, то следует рассмотреть возможность отвода тепла от исходного питания, поскольку это дает существенную суммарную экономию тепла (табл. 7).
Таблица 7.
Тепловые нагрузки кипятильников, теплообменника и общая тепловая нагрузка схемы c PTCDS (II ЗР) в зависимости от доли пара и температуры питания
VF | TF, °C | QHE, кВт | QPTCDS, кВт | Qsum, кВт |
---|---|---|---|---|
0 | 75 | –6514 | 11 651 | 5137 |
0 | 80 | –6305 | 11 501 | 5196 |
0 | 83.74 | –6146 | 11 391 | 5245 |
0.07 | 85 | –5808 | 11 167 | 5359 |
0.34 | 90 | –4421 | 10 309 | 5888 |
0.62 | 95 | –2921 | 9581 | 6660 |
1 | 101.33 | –905 | 8794 | 7889 |
1 | 110 | –618 | 8707 | 8089 |
1 | 120 | –282 | 8623 | 8341 |
Данные из табл. 7 свидетельствуют о том, что для рассматриваемого случая, при возможности использования низкопотенциального тепла, наилучшим вариантом будет организация питания кипящей жидкостью с долей пара, равной нулю, поскольку дополнительное захолаживание питания не приводит к существенному снижению суммарного потребления тепла (Qsum).
Выбор варианта организации процесса с точки зрения конкретного предприятия должен осуществляться исходя из температуры водяного конденсата, который может быть направлен для выработки пара в теплообменнике. Например, при температуре водяного конденсата, поступающего в теплообменник, равной 90°С, целесообразно выбрать температуру питания 110°С для обеспечения необходимой движущей силы теплопередачи.
Для сравнительного анализа объема капитальных затрат на создание установки ректификации были определены основные конструкционные параметры колонн с перегородками (рис. 6), в том числе были определены размеры и положение перегородки (табл. 8 и 9).
Рис. 6.
Геометрические характеристики сложных колонн с перегородками, полученных методом репрографии: (а) – на основе схем по I ЗР, (б) – на основе схем по II ЗР.
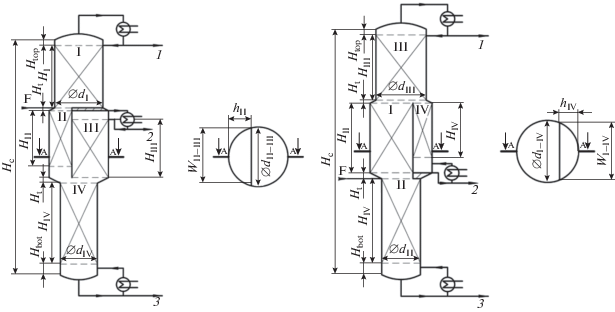
Таблица 8.
Конструкционные параметры* колонны с перегородкой (первое заданное разделение, рис. 6а)
TF, °C | VF | dI | dII | dIII | dIV | dII–III | hII–III | NII–III | Нс | HI | НII | НIII | НIV | Нtop | Нbot |
---|---|---|---|---|---|---|---|---|---|---|---|---|---|---|---|
75 | 0 | 2.67 | 2.93 | 0.73 | 3.35 | 3.02 | 0.03 | 0.56 | 52.8 | 13.8 | 27.6 | 10.2 | 11.4 | 1 | 2 |
80 | 0 | 2.68 | 2.92 | 0.72 | 3.34 | 3.00 | 0.02 | 0.53 | 52.8 | 13.8 | 27.6 | 10.2 | 11.4 | 1 | 2 |
83.74 | 0 | 2.70 | 2.92 | 0.71 | 3.34 | 3.00 | 0.02 | 0.52 | 52.8 | 13.8 | 27.6 | 10.2 | 11.4 | 1 | 2 |
85 | 0.07 | 2.73 | 2.91 | 0.70 | 3.33 | 2.99 | 0.02 | 0.51 | 52.8 | 13.8 | 27.6 | 10.2 | 11.4 | 1 | 2 |
90 | 0.34 | 2.85 | 2.87 | 0.70 | 3.28 | 2.95 | 0.02 | 0.51 | 52.8 | 14.4 | 27 | 10.2 | 11.4 | 1 | 2 |
95 | 0.62 | 2.97 | 2.82 | 0.70 | 3.25 | 2.90 | 0.02 | 0.52 | 52.8 | 15.0 | 26.4 | 10.2 | 11.4 | 1 | 2 |
101.33 | 1 | 3.14 | 2.78 | 0.69 | 3.20 | 2.86 | 0.02 | 0.51 | 52.8 | 16.2 | 25.8 | 10.2 | 11.4 | 1 | 2 |
110 | 1 | 3.15 | 2.74 | 0.68 | 3.20 | 2.82 | 0.02 | 0.51 | 52.8 | 16.2 | 25.8 | 10.2 | 11.4 | 1 | 2 |
120 | 1 | 3.15 | 2.71 | 0.68 | 3.18 | 2.79 | 0.02 | 0.51 | 52.8 | 16.2 | 25.8 | 10.2 | 11.4 | 1 | 2 |
Таблица 9.
Конструкционные параметры* колонны с перегородкой (второе заданное разделение, рис. 6б)
TF, °C | VF | dI | dII | dIII | dIV | dI–IV | hI–IV | NI–IV | Нс | HI | НII | НIII | НIV | Нtop | Нbot |
---|---|---|---|---|---|---|---|---|---|---|---|---|---|---|---|
75 | 0 | 1.66 | 2.21 | 2.52 | 1.88 | 2.51 | 1.01 | 2.46 | 55.2 | 10.8 | 10.8 | 19.8 | 21.6 | 1 | 2 |
80 | 0 | 1.68 | 2.19 | 2.52 | 1.86 | 2.51 | 1.06 | 2.48 | 55.2 | 10.8 | 10.8 | 19.8 | 21.6 | 1 | 2 |
83.74 | 0 | 1.71 | 2.19 | 2.53 | 1.84 | 2.51 | 1.39 | 2.49 | 55.2 | 10.8 | 10.8 | 19.8 | 21.6 | 1 | 2 |
85 | 0.07 | 1.72 | 2.15 | 2.54 | 1.84 | 2.52 | 1.39 | 2.51 | 55.2 | 10.8 | 10.8 | 19.8 | 21.6 | 1 | 2 |
90 | 0.34 | 1.86 | 2.06 | 2.62 | 1.79 | 2.58 | 1.22 | 2.58 | 55.2 | 10.8 | 10.8 | 19.8 | 21.6 | 1 | 2 |
95 | 0.62 | 2.03 | 2.01 | 2.71 | 1.72 | 2.66 | 0.99 | 2.57 | 55.2 | 10.8 | 10.8 | 19.8 | 21.6 | 1 | 2 |
101.33 | 1 | 2.29 | 1.95 | 2.86 | 1.63 | 2.82 | 0.71 | 2.45 | 55.2 | 10.8 | 10.8 | 19.8 | 21.6 | 1 | 2 |
110 | 1 | 2.30 | 1.94 | 2.89 | 1.62 | 2.82 | 0.70 | 2.43 | 55.2 | 10.8 | 10.8 | 19.8 | 21.6 | 1 | 2 |
120 | 1 | 2.34 | 1.93 | 2.92 | 1.61 | 2.85 | 0.67 | 2.41 | 55.2 | 10.8 | 10.8 | 19.8 | 21.6 | 1 | 2 |
Для оценки капитальных затрат использовали оценку металлоемкости обечаек аппаратов традиционной технологической схемы и колонны DWC. Высота каждой из секций DWC была зафиксирована равной соответствующей секции традиционной схемы. В качестве допущения на данном этапе исследования принимали высоту части колонны с перегородкой равной высоте секции с большей протяженностью. При этом высоты отдельных секций оставляли без изменений. Исходя их полученных данных, установлено, что DWC обеспечивает существенное снижение капитальных затрат (рис. 7), которое во всем исследованном интервале составляет 18–21%. Следует обратить внимание, что с ростом доли пара в питании для DWC происходит более быстрый рост металлоемкости по сравнению с традиционными технологическими схемами ректификации.
Рис. 7.
Зависимости суммарной поверхности цилиндрических частей обечайки (A) без учета сепарационных пространств от температуры потока питания, при допущении о равенстве высот секций I и IV сложной колонны, полученной на основе структуры PTCDS (точки) и схемы из простых двухсекционных колонн (линия).
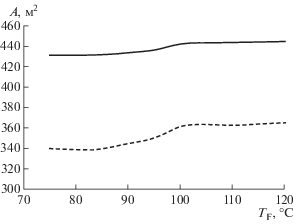
Таким образом, предложены конструкционные параметры колонн DWC для разделения фракции легких углеводородов. Выявлено, что наибольший энергетический эффект DWC обеспечивают при использовании питания в виде пара, при этом экономия энергоресурсов может достигать 30%. При этом в условиях реального промышленного предприятия выбор агрегатного состояния питания определяется возможностью использования низкопотенциальных тепловых ресурсов. В отсутствие такой возможности для рассматриваемой смеси, следует рекомендовать питание при температуре 110°С.
ЗАКЛЮЧЕНИЕ
Полученные технические решения позволяют существенно снизить как энергетические, так и капитальные затраты на разделение фракции С4+ пиролиза. Впервые показано, что применение колонн с перегородками является более эффективным при использовании потока питания с высокой долей пара, равной 80–100%. Для заданной смеси и состава питания лучшей энергетической эффективностью обладают колонны с перегородкой, являющиеся образом второго заданного разделения и представляющие собой колонну с расположенной внутри аппарата боковой исчерпывающей секцией. Выявлено, что наибольший энергетический эффект колонны с перегородкой обеспечивают при использовании питания в виде пара, при этом экономия энергоресурсов может достигать 30%. Помимо этого, показано, что применение колонн с перегородкой обеспечивает снижение капитальных затрат на 18–21%.
Работа выполнена при финансовой поддержке Российского фонда фундаментальных исследований (проект № 17-03-00347).
ОБОЗНАЧЕНИЯ
А | поверхность обечайки, м2 |
d | диаметр секции, м |
H | высота секции, м |
h | высота сегмента, м |
N | номер тарелки |
Q | тепловая нагрузка, кВт |
R | флегмовое число |
S | количество отбора, кг/ч |
T | температура, °C |
V | доля пара |
W | ширина перегородки, м |
ИНДЕКСЫ
Список литературы
Timoshenko A.V., Anokhina E.A., Buev D.L. Application of graphs of distillation trajectories to synthesis of separation flowsheets // Theor. Found. Chem. Eng. 2004. V. 38. № 2. P. 1.
Timoshenko A.V., Serafimov L.A. Graphs analysis as a method of systems analysis of structural multiplicity of rectification separation flow sheets // Theor. Found. Chem. Eng. 1997. V. 31. № 5. P. 480.
Wakabayashi T., Yoshitani K., Takahashi H., Hasebe S. Verification of energy conservation for discretely heat integrated distillation column through commercial operation // Chem. Eng. Res. Des. 2019. V. 142. P. 1.
Fang J., Cheng X., Li Z., Li H., Li C. A review of internally heat integrated distillation column // Chin. J. Chem. Eng. 2019. V. 27. № 6. P. 1272.
Marin M.D., Meyer M., Mizzi B., Rouzineau D. New conceptual design methodology for a concentric heat integrated distillation column (HIDiC) // Chem. Eng. Trans. 2018. V. 69. P. 883.
Yala O., Rouzineau D., Thery-Hetreux R., Meyer M. Design and optimization of Heat Integrated Distillation Column “HIDiC” // Chem. Eng. Trans. V. 40. P. 1783.
Bisgaard T., Skogestad S., Abildskov J., Huusom J.K. Optimal operation and stabilising control of the concentric heat-integrated distillation column (HIDiC) // Comput. Chem. Eng. 2017. V. 96. P. 196.
Cong H., Li X., Li H., Murphy J.P., Gao X. Performance analysis and structural optimization of multi-tube type heat integrated distillation column (HIDiC) // Sep. Purif. Technol. 2017. V. 188. P. 303.
Ponce, G.H., Alves, M., Miranda, J.C., Maciel F.R., Wolf M.R. Using an internally heat-integrated distillation column for ethanol-water separation for fuel applications // Chem. Eng. Res. Des. 2015. V. 95. P. 55.
Kiss A.A., Olujić T. A review on process intensification in internally heat-integrated distillation columns // Chem. Eng. Process. Process Intensif. 2014. V. 86. P. 125.
Петлюк Ф.Б., Платонов В.М., Славинский Д.М. Термодинамически оптимальный способ разделения многокомпонентных смесей // Хим. пром-сть. 1965. № 3. С. 206.
Qian X., Huang K., Chen H., Yuan Y., Zhang L., Wang S. Intensifying Kaibel dividing-wall column via vapor recompression heat pump // Chem. Eng. Res. Des. 2019. V. 142. P. 195.
Wang X., Yu X., Xie L., Li M., Zhang Y. Energy-saving columns: Design and control of a Kaibel and a multi-sidestream column for separating hydrocarbon mixture // Chem. Eng. Process. Process Intensif. 2018. V. 133. P. 66.
Lopez-Saucedo E.S., Chen Q., Grossmann I.E., Caballero J.A. Kaibel Column: Modeling and Optimization // Proc. 13th International Symposium on Process Systems Engineering (PSE 2018) (San Diego, California, 2018) (Elsevier Series in Computer Aided Chemical Engineering. V. 44) / Eds. Eden M.R., Ierapetritou M.G., Towler G.P. Amsterdam: Elsevier, 2018. P. 1183.
Tututi-Avila S., Domínguez-Díaz L.A., Medina-Herrera N., Jiménez-Gutiérrez A., Hahn J. Dividing-wall columns: Design and control of a Kaibel and a satellite distillation column for BTX separation // Chem. Eng. Process. Process Intensif. 2017. V. 114. P. 1.
Olujić Ž., Jödecke M., Shilkin A., Schuch G., Kaibel B. Equipment improvement trends in distillation // Chem. Eng. Process. Process Intensif. 2009. V. 48. № 6. P. 1089.
Dejanovića I., Matijaševića L., Olujićb Ž. Dividing wall column application for platformate splitter – A case study // Proc. 20th European Symposium on Computer Aided Process Engineering (Elsevier Series in Computer Aided Chemical Engineering. V. 28) / Eds. Pierucci S., Buzzi Ferraris G. Amsterdam: Elsevier, 2010. P. 655.
Patrascu, I., Bildea, C.S., Kiss, A.A. Dynamics and control of a heat pump assisted azeotropic dividing-wall column (HP-A-DWC) for biobutanol purification // Comput. Aided Chem. Eng. V. 46. 2019. P. 1339.
Massimiliano E., Giuseppe T., Ben-Guang R., Daniele D., Ilkka T. Energy saving and capital cost evaluation in distillation column sequences with a divided wall column // Chem. Eng. Res. Des. 2009. V. 87. P. 1649.
Fang J., Zhao H., Qi J., Li C., Qi J., Guo J. Energy conserving effects of dividing wall column // Chin. J. Chem. Eng. 2015. V. 23. P. 934.
Van L.N., Pham T.N., Lee M. Optimal retrofit and debottlenecking using novel multi-effect dividing wall column // Chem. Eng. Process. Process Intensif. 2018. V. 127. P. 65.
Tarjani A.J., Toth A.J., Nagy T., Haaz E., Valentinyi N., Andre A., Fozer D., Mizsey P. Thermodynamic and Exergy Analysis of Energy-Integrated Distillation Technologies Focusing on Dividing-Wall Columns with Upper and Lower Partitions // Ind. Eng. Chem. Res. 2018. V. 57. № 10. P. 3678.
Li C.L., Peng F., Xie J.W. Simulation and control on separation of three-component mixtures by hot modelled dividing wall column // Xiandai Huagong. 2018. V. 38. № 1. P. 183.
Lorenz H.M., Staak D., Grützner T., Repke J.U. Divided wall columns: Usefulness and challenges // Chem. Eng. Trans. 2018. V. 69. P. 229.
Xiaolong G., Botong L., Xigang Y., Yiqing L., Kuo-Ksong Y. Application of the dividing wall column to olefin separation in fluidization methanol to propylene (FMTP) process // Chin. J. Chem. Eng. 2017. V. 25. № 8. P. 1069.
Song E., Wang E. Design of a Dividing-Wall Column Considering its Multiple Steady State Characteristic // Chem. Eng. Technol. 2018. V. 41. № 3. P. 517.
Wu S., Guo K., Liu C., Qi W., Zhang T., Liu H. Design and control for a dividing-wall column with a partial condenser for pretreating an industrial multi-component reformed gasoline mixture // Can. J. Chem. Eng. 2018. V. 96. № 11. P. 2431.
Ge X., Liu B., Yuan X., Liu B. Simplifying and synthesizing practical four-product dividing wall column configurations // Chem. Eng. Res. Des. 2017. V. 125. P. 433.
Jia S., Qian X., Yuan X. Optimal design for dividing wall column using support vector machine and particle swarm optimization // Chem. Eng. Res. Des. 2017. V. 125. P. 422.
Oliveira P.B., Nascimento M.L., Pontes K.V. Optimal Design of a Dividing Wall Column for the Separation of Aromatic Mixtures using the Response Surface Method // Proc. 28th European Symposium on Computer Aided Process Engineering (Elsevier Series in Computer Aided Chemical Engineering. V. 43) / Eds. Friedl A., Klemeš J.J., Radl S., Varbanov P.S., Wallek T. Amsterdam: Elsevier, 2018. P. 361.
Seihoub F.Z., Benyounes H., Shen W., Gerbaud V. An Improved Shortcut Design Method of Divided Wall Columns Exemplified by a Liquefied Petroleum Gas Process // Ind. Eng. Chem. Res. 2017. V. 56. № 34. P. 9710.
Zhang W.J., Meng Y., Xu J. Design and optimization of dividing wall column for a methyl methacrylate separation process // Xiandai Huagong. 2017. V. 37. № 2. P. 161.
Minh L.Q., Pham T.N., Long N.V., Shin J., Lee M. A cost-effective retrofit of conventional distillation sequence to dividing-wall prefractionator configuration // Comput. Chem. Eng. 2018. V. 110. P. 93.
Madenoor R.G., Tawarmalani M., Agrawal R. A systematic method to synthesize all dividing wall columns for n-component separation – Part I // AIChE J. 2018. V. 64. № 2. P. 649.
Franke M.B. Design of Dividing-Wall Columns by Mixed-Integer Nonlinear Programming Optimization // Chem. Ing. Tech. 2017. V. 89. № 5. P. 582.
Waltermann T., Skiborowski M. Conceptual Design of Highly Integrated Processes – Optimization of Dividing Wall Columns // Chem. Ing. Tech. 2017. V. 89. № 5. P. 562.
Ng Q.H., Sharma S., Rangaiah G.P. Design and analysis of an ethyl benzene production process using conventional distillation columns and dividing-wall column for multiple objectives // Chem. Eng. Res. Des. 2017. V. 118. P. 142.
Benyounes H., Benyahia K., Shen W., Gerbaud V., Dong L., Wei S. Novel procedure for assessment of feasible design parameters of dividing-wall columns: Application to non-azeotropic mixtures // Ind. Eng. Chem. Res. 2015. V. 54. № 19. P. 5307.
Luo J., Xu C., Zhang Y., Yan K., Zhu J. A steady-state analysis method for optimal operation of dividing-wall column // Comput. Chem. Eng. 2018. V. 119. P. 112.
Ge X., Liu B., Liu B., Wang H., Yuan X. Investigation of the operability for four-product dividing wall column with two partition walls // Chin. J. Chem. Eng. 2018. V. 26. № 8. P. 1670.
Kalita R., Gentry J.C. Dividing wall columns in operation // Chem. Eng. Trans. 2018. V. 69. P. 547.
Donahue M.M., Roach B.J., Downs J.J., Blevins T., Baldea M., ldridge R.B. Dividing wall column control: Common practices and key findings // Chem. Eng. Process. Process Intensif. 2016. V. 107. P. 106.
Kang K.J., Harvianto G.R., Lee M. Hydraulic Driven Active Vapor Distributor for Enhancing Operability of a Dividing Wall Column // Ind. Eng. Chem. Res. 2017. V. 56. № 22. P. 6493.
Harvianto G.R., Kim K.H., Kang K.J., Lee M. Optimal operation of dividing wall column using enhanced active vapor distributor // Chem. Eng. Trans. 2018. V. 69. P. 835.
Hernandez S., Segovia-Hernandez J.G., Rico-Ramırez V. Thermodynamically equivalent distillation schemes to the Petlyuk column for ternary mixtures // Energy. 2006. V. 31. P. 1840.
Петлюк В.Б., Серафимов Л.А. Многокомпонентная ректификация. Теория и расчет. М.: Химия, 1983.
Timoshenko A.V., Serafimov L.A. Flowsheet synthesis strategy for irreversible zeotropic distillation // Theor. Found. Chem. Eng. 2001. V. 35. № 6. P. 567.
Timoshenko A.V., Patkina O.D., Serafimov L.A. Synthesis of optimal distillation flowsheets consisting of columns with various numbers of sections // Theor. Found. Chem. Eng. 2001. V. 35. № 5. P. 458.
Тимошенко А.В., Серафимов Л.А. Стратегия синтеза множества схем ректификации зеотропных смесей // Хим. технол. 2001. № 6. С. 36.
Timoshenko A.V., Anokhina E.A., Ivanova L.V. Extractive distillation systems involving complex columns with partially coupled heat and material flows // Theor. Found. Chem. Eng. 2005. V. 39. № 5. P. 463.
Timoshenko A.V., Morgunov A.V., Anokhina E.A. Flowsheet synthesis for the extractive distillation of azeotropic mixtures in systems consisting of columns with partially coupled heat and material flows // Theor. Found. Chem. Eng. 2007. V. 41. № 6. P. 845.
Ivanova L.V., Timoshenko A.V., Timofeev V.S. Synthesis of flowsheets for extractive distillation of azeotropic mixtures // Theor. Found. Chem. Eng. 2005. V. 39. № 1. P. 16.
Timoshenko A.V., Anokhina E.A., Morgunov A.V., Rudakov D.G. Application of the partially thermally coupled distillation flowsheets for the extractive distillation of ternary azeotropic mixtures // Chem. Eng. Res. Des. 2015. V. 104. P. 139.
Кочарян С.О., Рудаков Д.Г., Тимошенко А.В. Энергетическая эффективность сложной колонны при разделении продуктов пиролиза в зависимости от состава питания // Тонкие хим. технол. 2017. Т. 12. № 3. С. 33.
Анохина Е.А., Тимошенко А.В. Синтез схем ректификации со связанными тепловыми и материальными потоками // Тонкие хим. технол. 2017. Т. 12. № 6. С. 46.
Тимошенко А.В. Ахапкина О.А., Анохина Е.А., Аристович Ю.В. Энергосберегающие подсистемы ректификации бутанов и пентанов // Хим. технол. 2012. № 11. С. 681.
Anokhina E.A., Timoshenko A.V. Criterion of the energy effectiveness of extractive distillation in the partially thermally coupled columns // Chem. Eng. Res. Des. 2015. V. 99. P. 165.
Timoshenko A.V., Anokhina E.A., Akhapkina O.A. Energy-saving hydrocarbons distillation with the coupled heat and material flows // Chem. Eng. Technol. 2016. V. 39. № 12. P. 2251.
Дополнительные материалы отсутствуют.
Инструменты
Теоретические основы химической технологии