Теоретические основы химической технологии, 2019, T. 53, № 6, стр. 609-616
Автоматизированная система поддержки принятия решений по управлению энергоресурсоэффективностью химико-энерготехнологической системы обжига фосфоритовых окатышей
В. П. Мешалкин a, В. И. Бобков b, *, М. И. Дли b
a Российский химико-технологический университет им. Д.И. Менделеева
Москва, Россия
b Национальный исследовательский университет “МЭИ” в г. Смоленске
Смоленск, Россия
* E-mail: vovabobkoff@mail.ru
Поступила в редакцию 04.02.2019
После доработки 08.02.2019
Принята к публикации 21.02.2019
Аннотация
Разработаны математическая и компьютерная модели сложного химико-технологического процесса обжига как взаимозависимой совокупности трех процессов – сушки, прокалки и спекания движущейся плотной многослойной массы фосфоритовых окатышей в конвейерной обжиговой машине, отличающегося учетом интенсивности процессов внутреннего влагопереноса в окатыше и процессов переувлажнения отдельных горизонтов в нагреваемом слое окатышей, что позволяет определять технологические параметры режима обжига. Проведена проверка адекватности разработанной математической модели по результатам сравнительного анализа рассчитанных значений влагосодержания и температуры окатышей, характеристик газа-теплоносителя, а также значений интенсивности влагопереноса в окатышах при сушке в движущемся плотном слое с результатами промышленных испытаний. Проведены многочисленные вычислительные эксперименты по определению относительной степени высушивания, влагосодержания, интенсивности сушки окатышей и влагосодержания газа-теплоносителя при различных характеристиках сырых окатышей и параметрах технологического режима работы обжиговой машины. Разработана содержательная и математическая постановки задачи оптимизации химико-энерготехнологического процесса (ХЭТП) обжига движущейся плотной многослойной массы фосфоритовых окатышей в сложной химико-энерготехнологической системе (ХЭТС) конвейерной обжиговой машины как задачи дискретного динамического программирования, отличающаяся учетом пространственно-временной многостадийности процессов обжига движущейся многослойной массы окатышей, интенсивности процесса внутреннего влагопереноса в окатыше, процессов переувлажнения отдельных слоев окатышей и переменных управляющего потока газа-теплоносителя, что позволяет повышать энергоэффективность посредством интенсификации тепломассообменных процессов многослойной сушки, прокалки и спекания. Критерием эффективности служит минимум себестоимости электрической и тепловой энергии, затрачиваемой на ХЭТП обжига. Полученные результаты применялись для расчета энергоэффективного обжига окатышей в ХЭТС обжиговой конвейерной машины. Установлено, что в оптимальном режиме многослойного обжига окатышей отсутствует зона переувлажнения, интенсифицируются процессы тепло- и влагопереноса, снижается расход энергии и повышается качество готового продукта. Исследована проблема переувлажнения окатышей в отдельных горизонтах слоя в зоне сушки обжиговой машины. Решена актуальная научно-практическая задача энергоресурсосбережения при обжиге окомкованного рудного сырья в плотном слое. Представлена математическая модель тепломассообмена в слое окатышей и проверка ее адекватности. Решена задача оптимизации энергозатрат на основе интенсификации процессов обжига.
ВВЕДЕНИЕ
В последние годы в металлургической промышленности пришли к убеждению, что преимущество производства окатышей заключается не только в том, что на месторождениях и отвалах горно-обогатительных предприятий скопилось огромное количество рудной мелочи, но и в возможности их транспортировки практически на любое расстояние с минимальными потерями [1]. Именно это преимущество окатышей выделено как основное при прогнозировании развития производства. Можно сказать, что возить сырье придется в большей мере и на большие расстояния, а возить можно и выгодно окатыши [2, 3]. Понимание сильных и слабых сторон этого производства, приходит через проводимые широким фронтом теоретико-экспериментальные исследования и опытно-промышленные работы, совершенствование конструкций основных агрегатов и оборудования [4]. В производстве окатышей накоплен большой опыт, выявлены многие направления совершенствования производства, высказаны принципиально новые идеи, которые уже оказали и еще окажут в будущем сильное влияние на развитие технологических процессов окускования руд [5].
Основной причиной нарушения режима обжига окомкованного материала является изменение свойств сырых окатышей: влажности, прочности, гранулометрического состава [6, 7]. Поступление на обжиг окатышей с повышенной влажностью при установившемся режиме обжига приводит к перерасходу тепла и неполному удалению влаги в зоне сушки [8, 9]. Окатыши с повышенным количеством влаги в зоне подогрева разрушаются в результате интенсивного парообразования. Это приводит к забиванию слоя мелочью, снижению газопроницаемости, ухудшению качества и уменьшению выхода годного продукта [10, 11].
Поэтому реализация процессов сушки в режиме оптимума энергозатрат и максимума скорости имеет большое значение для практики [12]. Поскольку технологические ограничения существенно сужают диапазон варьирования параметров обжига, требуется системный анализ взаимовлияния всех факторов, определяющих режим обжига окатышей [13].
МНОГОМАСШТАБНОЕ МОДЕЛИРОВАНИЕ ПРОЦЕССОВ ОБЖИГА
Разработанные авторами и представленные в [3–5] многомасштабная математическая и компьютерная модели и алгоритмы оптимального управления химико-энерготехнологической системой (ХЭТС) производства фосфоритовых окатышей и многостадийной оптимизации по критерию энергоресурсоэффективности (см. рис. 1) с учетом сложной структурной схемы управления ХЭТС (см. рис. 2) иерархически включают в себя различные уровни.
Рис. 1.
Упрощенная блок-схема алгоритма многомасштабного моделирования и многоуровневой оптимизации ХЭТС производства фосфоритовых окатышей.
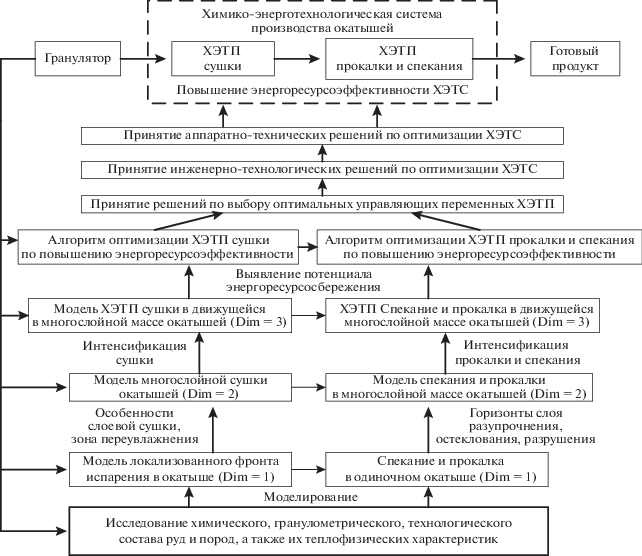
Наличие различных уровней определяет следующие обстоятельства. Во-первых, формирование критерия энергоресурсоэффективности ХЭТС обжига окатышей предполагает учет следующих показателей: завершенность химико-энерготехнологического процесса (ХЭТП) сушки (среднее по высоте многослойной укладки влагосодержание окатышей на выходе зоны сушки); завершенность ХЭТП прокалки (средняя по высоте многослойной укладки степень реагирования при покидании высокотемпературной зоны обжига); завершенность ХЭТП спекания (требуемая прочность окатышей, средняя по высоте слоя прочность окатышей на выходе из высокотемпературной зоны обжига); минимум стоимости энергозатрат на проведение и завершение этих ХЭТП [14, 15].
Во-вторых, необходимо провести дискретизацию ХЭТС по времени пребывания движущейся многослойной массы в различных локальных вакуум-камерах с использованием выбранного критерия повышения энергоресурсоэффективности и реализации процедуры дискретного динамического программирования представленную авторами в [5].
Такой системный подход позволит разработать методическое и программно-информационное обеспечение поддержки принятия решений по многоуровневой оптимизации энергоресурсоэффективности химико-энерготехнологической системы производства окатышей [16, 17].
АРХИТЕКТУРА, ПРОГРАММНО-ИНФОРМАЦИОННОЕ ОБЕСПЕЧЕНИЕ И РЕЖИМЫ ФУНКЦИОНИРОВАНИЯ АВТОМАТИЗИРОВАННОЙ СИСТЕМЫ ПОДДЕРЖКИ ПРИНЯТИЯ РЕШЕНИЙ ПО ОПТИМАЛЬНОМУ УПРАВЛЕНИЮ ЭНЕРГОРЕСУРСОЭФФЕКТИВ- НОСТЬЮ ХЭТС
Предложенные многоуровневые алгоритмы оптимизации энергоресурсоэффективности ХЭТС и разработанные многомасштабные математические модели ХЭТП были практически реализованы в виде комплекса программ, используемого для оптимального управления ХЭТС производства окатышей. Данный комплекс позволяет рассчитывать основные термически активируемые ХЭТП, протекающие в окатышах при высокотемпературном обжиге в движущейся многослойной массе на конвейере ХЭТС. Архитектура комплекса программ оптимизации энергоресурсоэффективности ХЭТС построена по модульному принципу с использованием среды программирования Borland C++ для Windows и пакета программ MathCad.
Разработанный комплекс программ, используемый для оптимизации энергоресурсоэффективности ХЭТС производства окатышей, включает в себя следующие основные модули (см. рис. 3):
Рис. 3.
Схема архитектуры информационно-аналитической системы обеспечения режимов функционирования автоматизированной системы поддержки принятия решений по оптимальному управлению энергоресурсоэффективностью ХЭТС.
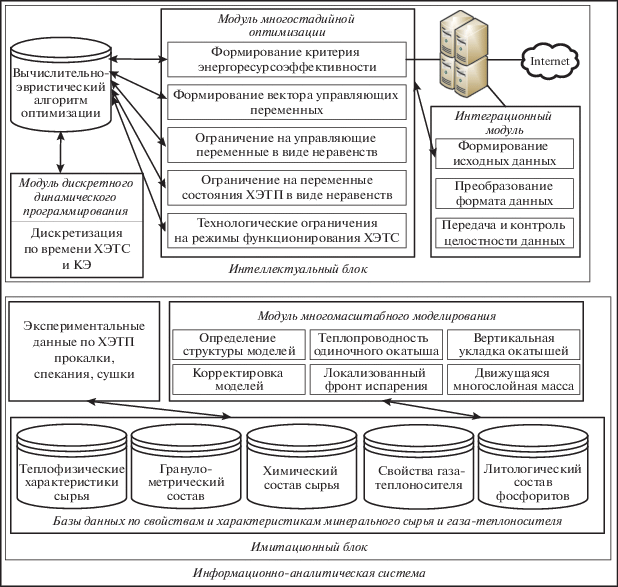
1. Модуль формирования базы данных, которая содержит информацию о литологическом, гранулометрическом, химическом составе исходного сырья, теплофизических характеристиках: коэффициенте теплопроводности, теплоемкости материала окатышей с учетом степени реагирования, так как в результате реакции диссоциации карбонатов образуются новые оксиды с иными теплофизическими характеристиками [19]. Подразумевается ввод информации в виде зависимостей от температуры теплофизических характеристик газа-теплоносителя и сырьевого материала для окатышей [20, 21].
2. Модуль многомасштабного моделирования ХЭТП сушки, прокалки и спекания, организованный в виде класса среды программирования Borland C++, включающий в себя следующие подклассы (см. рис. 4):
Рис. 4.
Упрощенная схема формирования иерархии классов при объектно-ориентированном программировании многомасштабной математической модели.
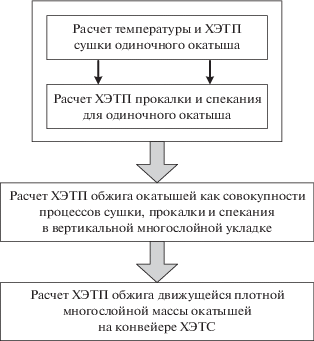
2.1. Подкласс для расчета уравнения теплопроводности для определения температуры окатыша по радиусу. Расчет продвижения вглубь окатыша локализованного фронта испарения, скорости, интенсивности влагопереноса, влагосодержания окатыша при проведении ХЭТП сушки [22].
2.2. Подкласс для расчета степени реагирования реакции диссоциации карбонатов, увеличение или уменьшение прочности окатыша, градиент температуры и скорости нагрева при проведении высокотемпературных ХЭТП обжига [23, 24].
2.3. Подкласс для расчета всех рассматриваемых ХЭТП в вертикальной многослойной укладке окатышей, иерархически включающий в себя подклассы 2.1 и 2.2. В этом подклассе организован расчет изменения переменных состояния газа-теплоносителя: температуры, давления, влагосодержания при его перекрестном движении вдоль вертикальной укладки окатышей.
2.4. Класс, включающий в себя иерархически подкласс 2.3. В нем организован расчет модели ХЭТП сушки, прокалки и спекания движущейся плотной многослойной массы окатышей на конвейере ХЭТС с перекрестной подачей газа-теплоносителя.
Интеллектуальный блок включает в себя модули: многостадийной оптимизации, дискретного динамического программирования и интеграционный модуль [25, 26].
3. Модуль многостадийной оптимизации организован в виде объектно-ориентированного класса, который иерархически включает в себя следующие подклассы:
3.1. В этом подклассе происходит формирование аддитивно-сепарабельного критерия энергоресурсоэффективности ХЭТС обжига фосфоритовых окатышей. В критерий энергоресурсоэффективности входят следующие показатели: завершенность ХЭТП сушки (влагосодержание окатышей), прокалки (степень реагирования реакций диссоциации карбонатов равна 1), спекания (достигнута требуемая прочность окатышей), минимум стоимости энергозатрат на проведение и завершение этих ХЭТП.
3.2. В этом подклассе формируется двумерный вектор управляющих переменных (Tg0; Wg), где Tg0 – температура газа-теплоносителя на входе в динамическую многослойную массу окатышей, Wg – скорость его перекрестной подачи.
3.3. Подкласс формирует, использует и проверяет выполнение наложенных ограничений в виде неравенств на управляющие переменные техническими (тепловыми и аэродинамическими) особенностями функционирования теплового и тягодутьевого оборудования ХЭТС.
3.4. В этом подклассе формируются и проверяются условия выполнения ограничений в виде неравенств на переменные состояния ХЭТП обжига движущейся многослойной массы окатышей: градиент температуры, скорость нагрева, интенсивность влагопереноса, скорость ХЭТП сушки, относительную степень высушивания, влагосодержание, степень реагирования реакции диссоциации карбонатов, спекания, обеспечивающего конечную прочность, остеклование, с целью недопущения формирования горизонтов переувлажнения и разрушения окатышей.
3.5. В данном подклассе учитываются теплотехнологические ограничения на функционирование ХЭТС: реверс перекрестной подачи газа-теплоносителя в динамическую многослойную массу, а также температуру газа в вакуум-камерах и тягодутьевых каналах.
4. Модуль, реализующий дискретизацию по времени пребывания многослойной массы в различных локальных вакуум-камерах ХЭТС с учетом критериев энергоресурсоэффективности с целью реализации процедуры дискретного динамического программирования.
АНАЛИЗ СТРУКТУРЫ И СВОЙСТВ ОБЖИГОВОЙ МАШИНЫ OK-520/536 КАК СЛОЖНОЙ ХЭТС
На основе системного анализа структуры и свойств ХЭТС представлено описание принятия технологических решений по усовершенствованию структуры обжиговой конвейерной машины как сложной ХЭТС, приведены результаты модернизации машин типа ОК-520/536, а также рассчитанного энергоресурсоэффективного технологического режима функционирования обжиговой конвейерной машины – ХЭТС. Системный анализ обжиговых машин позволил определить современный подход к исследованию технологических и тепловых параметров функционирования обжиговых агрегатов и оборудования, их технико-экономические показатели. Аппаратно-техническая модернизация привела к увеличению производительности и уменьшению энергозатрат.
В начале аппаратно-технической модернизации ХЭТС была использована многосекционная зона сушки, которая позволила существенно интенсифицировать ХЭТП сушки движущейся многослойной массы окатышей. Чтобы увеличить производительность ХЭТС и расширить возможности ее функционирования в условиях периодически изменяющихся исходных химико-технологических параметров сырья, были сформулированы перечисленные ниже технологические поправки:
скорректирован функциональный режим термической обработки динамической многослойной массы окатышей путем приведения его к балансу с внутренними источниками тепловой энергии;
повышено качество сушки окатышей на основе интенсификации температурно-фильтрационного функционального режима с последующей аппаратно-технической модернизацией зоны сушки и обеспечивающих ее тягодутьевых агрегатов и потоков газа-теплоносителя;
увеличена эффективность охлаждения многослойной массы фосфоритовых окатышей за счет изменения фильтрационного режима, перераспределения потоков газа-теплоносителя и реконструкции зоны охлаждения;
изменена тепловая схема и модернизирована система газоходов, переопределены площадь вакуум-камер и технологических газовоздушных зон, которые соединены с эксгаустерами и дымососами;
существенно увеличены циркуляция и рециркуляция объемов газа-теплоносителя и сушильного агента.
ЗАКЛЮЧЕНИЕ
Проведены исследования, выполнен анализ, а также качественная и количественная классификация основных конструктивных элементов обжиговых машин по их влиянию на производительность, расходы топлива и электроэнергии.
Практический опыт эксплуатации обжиговых машин показал, что, несмотря на повышенный расход тепла и электроэнергии при организации реверсивной схемы сушки, ее использование предотвращает снижение производительности обжиговой машины в целом за счет уменьшения усадки слоя при его сушке, что обеспечивает эффективную работу всех последующих зон за счет снижения газодинамического сопротивления слоя окатышей.
При исследовании различных систем возврата тепла из зоны охлаждения в зоны нагрева, включая вентиляторные, а также одно- и многопоточные безвентиляторные системы прямого перетока, установлено, что с точки зрения экономии топлива и электроэнергии в любом случае наиболее целесообразным является применение безвентиляторных систем.
В процессе изучения одно- и многопоточных схем перетока представлена методика расчета качества и количества потоков, на которые следует разъединять поток газа-теплоносителя при экономии тепловой энергии на обжиг окатышей. Поэтому формулируется ряд основополагающих и принципиальных требований по экономии тепловой энергии, топлива на функционирование ХЭТС:
поток газа-теплоносителя, выходящий из зоны охлаждения, необходимо формировать так, чтобы газ-теплоноситель с более высокой температурой, поступал в один коллектор, а с низкой – во второй, затем в третий и т.д.;
разделив таким образом поток газа-теплоносителя, выходящего из технологической зоны охлаждения, самый нагретый теплоноситель следует направлять в те участки конвейера, для которых необходимо получить самую высокую температуру газа-теплоносителя на входе в многослойную массу окатышей, а затем в зону с менее высокой температурой газа-теплоносителя и т.д.
Анализ результатов позволяет определить основные направления снижения затрат энергии.
Системный анализ энерготехнологических схем и оптимизация режимов функционирования и эксплуатации ХЭТС выявили, что на практике не используются такие важные принципы снижения удельного расхода энергии, как:
увеличение КПД работы тягодутьевых устройств – зачастую они работают в диапазоне КПД 25–35%; если же согласовать тягодутьевые агрегаты и сети газопроводов, то КПД доводится до 70–80%;
уменьшение объемов газа-теплоносителя, перекачиваемых насосами и эксгаустерами, неучтенных подсосов газа-теплоносителя;
существенное снижение аэродинамического сопротивления многослойной массы сырых окатышей, колосниковой “постели” обожженных окатышей;
уменьшение аэродинамического сопротивления газоходов, в которых снижается напор потока газа-теплоносителя, обеспечиваемого работой тягодутьевого оборудования;
обеспечение поставок газа-теплоносителя с менее низкой температурой.
Работа выполнена в рамках базовой части государственного задания Министерства образования и науки Российской Федерации на выполнение государственных работ в сфере научной деятельности (проект № 13.9597.2017/БЧ).
Список литературы
Panchenko S.V., Shirokikh T.V. Thermophysical processes in burden zone of submerged arc furnaces // Theor. Found. Chem. Eng. 2014. V. 48. № 1. P. 77. [Панченко С.В., Широких Т.В. Теплофизические процессы в шихтовой зоне электротермических рудовосстановительных реакторов // Теор. осн. хим. технол. 2014. Т. 48. № 1. С. 83.]
Bobkov V.I., Borisov V.V., Dli M.I., Meshalkin V.P. Intensive Technologies for Drying a Lump Material in a Dense Bed // Theor. Found. Chem. Eng. 2017. V. 51. № 1. P. 72. [Бобков В.И., Борисов В.В., Дли М.И., Мешалкин В.П. Интенсивные технологии сушки кускового материала в плотном слое // Теор. осн. хим. технол. 2017. Т. 51. № 1. С. 72.]
Bobkov V.I., Borisov V.V., Dli M.I., Meshalkin V.P. Study of the Thermal Characteristics of Phosphate Raw Materials in the Annealing Temperature Range // Theor. Found. Chem. Eng. 2017. V. 51. № 3. P. 307. [Бобков В.И., Борисов В.В., Дли М.И., Мешалкин В.П. Исследование тепловых характеристик фосфатного сырья в диапазоне температур обжига // Теор. осн. хим. технол. 2017. Т. 51. № 3. С. 295.]
Meshalkin V.P., Bobkov V.I., Dli M.I., Khodchenko S.M. Computer-aided modeling of the chemical process of drying of a moving dense multilayer mass of phosphorite pellets // Dokl. Chem. 2017. V. 475. № 2. P. 188. [Мешалкин В.П., Бобков В.И., Дли М.И., Ходченко С.М. Компьютерное моделирование химико-технологического процесса сушки движущейся плотной многослойной массы фосфоритовых окатышей // Докл. Акад. наук. 2017. Т. 475. № 4. С. 410.]
Meshalkin V.P., Bobkov V.I., Dli M.I., Khodchenko S.M. Computer modeling of the chemical-power engineering process of roasting of a moving multilayer mass of phosphorite pellets // Dokl. Chem. 2017. V. 477. № 2. P. 282. [Мешалкин В.П., Бобков В.И., Дли М.И., Ходченко С.М. Компьютерное моделирование химико-энерготехнологического процесса обжига движущейся многослойной массы фосфоритовых окатышей // Докл. Акад. наук. 2017. Т. 477. № 5. С. 559.]
Meshalkin V.P., Bobkov V.I., Dli M.I., Khodchenko S.M. Optimizing the energy efficiency of the chemical and energy engineering process of drying of a moving dense multilayer mass of phosphorite pellets // Dokl. Chem. 2017. V. 477. № 2. P. 286. [Мешалкин В.П., Бобков В.И., Дли М.И., Ходченко С.М. Оптимизация энергоэффективности химико-энерготехнологического процесса сушки движущейся плотной многослойной массы фосфоритовых окатышей // Докл. Акад. наук. 2017. Т. 477. № 6. С. 667.]
Мешалкин В.П., Бобков В.И. Ресурсосберегающие энергоэффективные технологии обработки фосфатного сырья // ХХ Менделеевский съезд по общей и прикладной химии. Екатеринбург, 2016. С. 299.
Леонтьев Л.И. Физико-химические особенности комплексной переработки железосодержащих руд и техногенных отходов // ХХ Менделеевский съезд по общей и прикладной химии. Екатеринбург, 2016. С. 92.
Elgharbi S., Horchani-Naifer K., Férid M. Investigation of the structural and mineralogical changes of Tunisian phosphorite during calcinations // J. Therm. Anal. Calorim. 2015. V. 119. № 1. P. 265.
Luis P., Van der Bruggen B. Exergy analysis of energy-intensive production processes: advancing towards a sustainable chemical industry // J. Chem. Technol. Biotechnol. 2014. V. 89. № 9. P. 1288.
Буткарев А.А., Буткарев А.П., Ащеулов В.Н., Жомирук П.А., Лазебная Ю.П. Оптимизация работы тракта эксгаустера обжиговой машины ОК-108 АО ССГПО для увеличения производства окатышей // Сталь. 2015. № 3. С. 12.
Зайнуллин Л.А., Дружинин Г.М., Буткарев А.А. Инновационные разработки ОАО ВНИИМТ для энергосбережения и экологии в металлургии // Черн. металл. 2014. № 7(1375). С. 79.
Abzalov V.M., Bragin V.V., Klein V.I., Solodukhin A.A. Efficiency of drying zones in roasting machines // Steel Transl. 2008. V. 38. № 12. P. 1008.
Melamud S.G., Yur’ev B.P. Oxidation of iron ore at moderate and high temperatures // Steel Transl. 2016. V. 46. № 6. P. 384.
Bokovikov B.A., Bragin V.V., Shvydkii V.S. Role of the thermal-inertia zone in conveyer roasting machines // Steel Transl. 2014. V. 44. № 8. P. 595.
Bragin V.V., Bokovikov B.A., Naidich M.I., Gruzdev A.I., Shvydkii V.S. Relation between the productivity and fuel consumption in roasting machines // Steel Transl. 2014. V. 44. № 8. P. 590.
Солодухин А.А., Боковиков Б.А., Спирин Н.А. Уменьшение переувлажнения окатышей в зоне сушки обжиговой конвейерной машины // Сталь. 2014. № 8. С. 14.
Брагин В.В., Боковиков Б.А., Найдич М.И., Груздев А.И., Швыдкий В.С. О взаимосвязи производительности обжиговой машины и удельного расхода топлива // Сталь. 2014. № 8. С. 38.
Павловец В.М., Герасимук А.В. Особенности движения зародыша сложной формы на тарельчатом окомкователе в производстве железорудных окатышей // Изв. высш. учебн. завед. Черн. металл. 2018. Т. 61. № 2. С. 87.
Акбердин А.А., Ким А.С., Султангазиев Р.Б. Планирование численного и физического эксперимента при моделировании технологических процессов // Изв. высш. учебн. завед. Черн. металл. 2018. Т. 61. № 9. С. 737.
Швыдкий В.С., Фатхутдинов А.Р., Девятых Е.А., Девятых Т.О., Спирин Н.А. К математическому моделированию слоевых металлургических печей и агрегатов. Сообщение 2 // Изв. высш. учебн. завед. Черн. металл. // 2018. Т. 60. № 1. С. 19.
Юрьев Б.П., Гольцев В.А. Изменение эквивалентной порозности слоя окатышей по длине обжиговой машины // Изв. высш. учебн. завед. Черн. металл. 2018. Т. 60. № 2. С. 116–123.
Швыдкий В.С., Ярошенко Ю.Г., Спирин Н.А., Лавров В.В. Математическая модель процесса обжига рудоугольных окатышей на конвейерной машине // Изв. высш. учебн. завед. Черн. металл. 2018. Т. 60. № 4. С. 329.
Новичихин А.В., Шорохова А.В. Процедуры управления поэтапной переработкой железорудных отходов горнопромышленных районов // Изв. высш. учебн. завед. Черн. металл. 2018. Т. 60. № 7. С. 565.
Леонтьев Л.И., Григорович К.В., Костина М.В. Фундаментальные исследования как основа создания новых материалов и технологий в области металлургии. Часть 1 // Изв. высш. учебн. завед. Черн. металл. 2018. Т. 61. № 1. С. 11.
Гурин И.А., Лавров В.В., Спирин Н.А., Никитин А.Г. Веб-технологии построения информационно-моделирующих систем технологических процессов в металлургии // Изв. высш. учебн. завед. Черн. металл. 2017. Т. 60. № 7. С. 573.
Дополнительные материалы отсутствуют.
Инструменты
Теоретические основы химической технологии