Теоретические основы химической технологии, 2020, T. 54, № 5, стр. 584-591
Электрофлотационное извлечение малорастворимых соединений редкоземельных металлов в составе многокомпонентной смеси из водных растворов, содержащих хлорид-ионы
В. А. Колесников a, А. М. Гайдукова a, А. В. Колесников a, *, А. Ф. Губин a, Н. А. Ветлугин a
a Российский химико-технологический университет им. Д.И. Менделеева
Москва, Россия
* E-mail: artkoles@list.ru
Поступила в редакцию 27.11.2019
После доработки 09.12.2019
Принята к публикации 17.12.2019
Аннотация
Исследован процесс электрофлотационного извлечения малорастворимых соединений редкоземельных металлов из водных растворов, содержащих хлорид-ионы. Установлено, что в области значений pH 5–9 степень извлечения не превышает 15%. Также было исследовано влияние органических добавок различной природы на эффективность электрофлотационного процесса. Отмечено, что при введении в систему катионного флокулянта SUPERFLOC С-494 при рН 9 степень извлечения достигает 74%. Максимальная степень извлечения малорастворимых соединений всех элементов многокомпонентной системы наблюдается при рН 7 при введении СептаПАВ (к) (α = 97–98%) и ПЭО-1500 (н) (α = 86–98%). Высокая эффективность процесса сохраняется при высокой концентрации NaCl (100 г/л) в присутствии поверхностно-активных веществ и флокулянтов. Проведенные исследования показали, что электрофлотационный процесс позволяет эффективно извлекать малорастворимые соединения смеси редкоземельных металлов как из промывных вод при отмывке осадков редкоземельных металлов от ионов хлора, так и из солевых растворов (NaCl) фильтратов.
ВВЕДЕНИЕ
В настоящее время в связи с развитием достижений научно-технического прогресса применение редкоземельных элементов в таких отраслях промышленности, как радиоэлектроника, машиностроение, атомная энергетика, химическая промышленность, металлургия и др., стремительно растет [1, 2].
Редкоземельные металлы (РЗМ) очень рассеяны в почвах и твердых породах земной поверхности, что обусловливает сложности в их добыче и очистке, а также дефицитность на рынке. В настоящее время мировой спрос составляет десятки и сотни тысяч тонн редкоземельных оксидов, а к 2020 г. прогнозируется рост спроса до 185–200 тысяч тонн в год [3].
Важнейшая особенность месторождений РЗМ – большой разброс их процентного содержания в рудах и различный состав металлов. Рассеянный характер нахождения РЗМ в природе предопределил и возможные формы организации производства [4]:
в составе самостоятельных производств РЗМ производятся в качестве целевых продуктов (при освоении уникальных месторождений, число которых крайне мало, либо мелких и рассредоточенных объектов);
на крупных комплексных горнорудных производствах РЗМ извлекаются как попутные компоненты при добыче других полезных ископаемых (например, фосфоритов).
Основными минералами РЗМ являются бастнезит, монацит, лопарит и ионно-абсорбционные глины [5]. Существующие технологии получения редкоземельной продукции представляют собой комплексную переработку рудных материалов, включающую вскрытие руды кислотами (серной, соляной, азотной и др.) с получением хлоридов, сульфатов, нитратов редкоземельных элементов. После проводят обработку полученных растворов содой или щавелевой кислотой для получения малорастворимых карбонатов или оксалатов редкоземельных элементов. Полученный осадок фильтруют и промывают водой [6–9]. В результате чего с промывными водами теряется часть целевого продукта. Процесс разделения РЗМ требует дополнительного технологического оборудования и весьма трудоемок [10].
При переработке и добыче металлических руд образуется большое количество отходов, в том числе водных растворов, в которых содержатся редкоземельные металлы в значительных объемах. Поэтому создание технологии с наиболее полным выходом ценных компонентов является актуальной задачей.
Анализ существующих технологий по получению карбонатов редкоземельных металлов из кислых растворов РЗМ показывает, что процесс состоит из нескольких стадий осаждения, промывки (для удаления хлоридов) и трех стадий фильтрации осадка (целевой продукт). Принципиальная схема получения карбонатов редкоземельных металлов после вскрытия руды соляной кислотой представлена на рис. 1.
Рис. 1.
Принципиальная схема получения карбонатов из растворов HCl: 1 – емкость технологического раствора хлоридов РЗМ; 2 – емкость для приготовления раствора осадителя (карбонат натрия); 3 – реактор I стадии осаждения с дополнительной дозировкой CO2; 4 – реактор II стадии осаждения осадка РЗМ; 5 – фильтрационные модули.
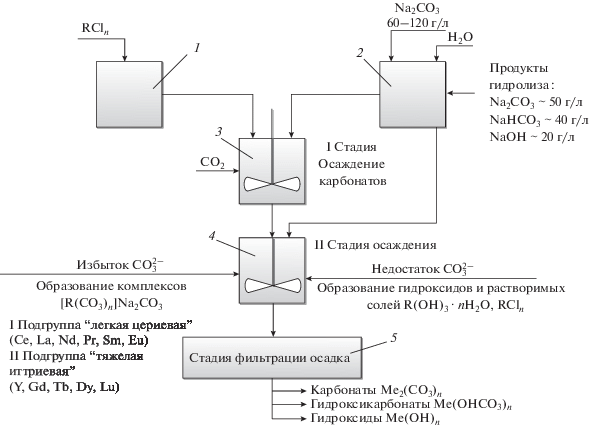
В процессе реализации данной технологии возникает ряд проблем.
1. Для получения осадка в виде карбонатов РЗМ, как правило, требуется избыток осадителя (карбонат-иона), с другой стороны, избыток Na2CO3 приводит к комплексообразованию в первую очередь подгруппы II (тяжелая иттриевая).
2. В связи с тем, что Na2CO3 в водном растворе гидролизуется раствор для осаждения содержит Na2CO3, NaHCO3, NaOH. Таким образом, на стадии фильтрации реально фильтруются Me2(CO3)3, Me(OH)CO3, Me(OH)3. Для исключения процессов комплексообразования реальное мольное соотношение Me : CO3 должно составлять 1 : 0.95. Для снижения гидролиза в раствор дополнительно вводят CO2.
3. Раствор для осаждения после нейтрализации имеет значение pH 4.5–5.0, что оптимально с точки зрения осаждения карбонатов, с другой стороны, до 5% РЗМ находится в виде ионов и остается в растворе. Для формирования осадков гидроксидов РЗМ необходимое значение pH как минимум 6–6.5, где формируются гидроксиды РЗМ. Растворимость осадков РЗМ (карбонаты, гидроксиды) возрастает с увеличением концентрации фонового электролита (NaCl ≈ 100–120 г/л) и уменьшается размер частиц дисперсной фазы.
4. С целью удаления коррозионно-агрессивных ионов хлора осадки карбонатов на стадии фильтрации дополнительно промывают горячей водой (50°С), что приводит к частичному растворению дисперсной фазы и потере мелкодисперсной фракции осадка (<10 мкм).
Таким образом, для повышения эффективности работы стадии фильтрации раствора и извлечения редкоземельных металлов из промывных вод необходимы новые технологические решения. Одним из перспективных направлений извлечения малорастворимых соединений из водных растворов является электрофлотация. Этот метод характеризуется высокой скоростью процесса и интенсивным выделением дисперсной фазы в пенный продукт [11–14]. В связи с этим целью работы является исследование процесса извлечения редкоземельных металлов из водных растворов, содержащих анионы Cl– электрофлотационным методом.
МЕТОДИЧЕСКАЯ ЧАСТЬ
В ходе работы были проведены экспериментальные исследования электрофлотационного извлечения малорастворимых соединений редкоземельных металлов в составе многокомпонентной смеси из модельных растворов в виде их карбонатов. Исследования проводили при различной концентрации соли: 0.25, 0.5 и 1 г/л Na2СO3. Для приближения модельных растворов к реальным промывочным растворам после операций кислотного вскрытия руды в растворы вводили NaCl с концентрацией 1 и 10 г/л.
Модельные растворы готовили разбавлением концентрата РЗМ, который был приготовлен из товарной продукции ОАО “Соликамский магниевый завод”.
Из проведенных ранее исследований установлено, что введение в раствор органических добавок в малых концентрациях (1–20 мг/л) способствует интенсификации электрофлотационного процесса [15, 16]. Поэтому в работе были использованы поверхностно-активные вещества (ПАВ) (СептаПАВ, NaDDS, ПЭО-1500 ) и флокулянты (SUPERFLOC С-494, SUPERFLOC A-137 ) с концентрацией в растворе до 20 мг/л.
Эффективность процесса извлечения малорастворимых соединений исследуемых металлов из раствора оценивали по степени извлечения α (%). Степень извлечения рассчитывали как отношение разности исходной (сin, мг/л) и конечной (сfin, мг/л) концентрации ионов в растворе после электрофлотационной обработки к исходной концентрации:
(1)
$\alpha = \frac{{{{с}_{{{\text{in}}}}} - {{с}_{{{\text{fin}}}}}}}{{{{с}_{{{\text{in}}}}}}} \times 100\% .$Процент дисперсной фазы определяли по анализу концентрации ионов металлов до и после фильтрации через фильтр “Синяя лента”:
(2)
$D = \frac{{{{с}_{{{\text{in}}}}} - {{с}_{{{\text{fin}}}}}}}{{{{с}_{{{\text{in}}}}}}} \times 100\% .$Измерение дзета-потенциала частиц и размеров частиц проводилось методом динамического рассеяние света на анализаторе Photocor Compact-Z.
Массовую концентрацию редкоземельных металлов измеряли на масс-спектрометре с индуктивно связанной плазмой Termo Scientific XSERIES II. Измерения были выполнены на оборудовании Центра коллективного пользования им. Д.И. Менделеева.
ЭКСПЕРИМЕНТАЛЬНАЯ ЧАСТЬ
Влияние pH раствора на формирование осадка смеси карбонатов редкоземельных металлов (La, Ce+4/Ce+3, Pr, Nd, Sm, Gd) представлено в табл. 1.
Таблица 1.
Процент дисперсной фазы малорастворимых соединений редкоземельных металлов в зависимости от pH раствора в присутствии NaCl
pH | D, % | |||||
---|---|---|---|---|---|---|
La | Ce+4/Ce+3 | Pr | Nd | Sm | Gd | |
4 | 5 | 31 | 15 | 12 | 10 | 17 |
5 | 15 | 45 | 25 | 24 | 26 | 32 |
6 | 29 | 68 | 42 | 43 | 49 | 46 |
7 | 81 | 87 | 80 | 80 | 77 | 83 |
8 | 82 | 89 | 80 | 81 | 77 | 82 |
9 | 80 | 89 | 80 | 80 | 77 | 83 |
10 | 81 | 88 | 80 | 80 | 47 | 82 |
11 | 80 | 88 | 80 | 79 | 76 | 83 |
12 | 81 | 88 | 80 | 80 | 76 | 83 |
Анализ показывает, что при pH 4–5 основной осадок формируется на основе карбонатов РЗМ. Для ионов церия в связи с возможностью формировать в растворе ионы Ce+4, Ce+3 возможно образование оксида (гидроксида) церия(IV) – Ce(OH)4, CeO2 в виде дисперсной фазы. В связи с этим фактом процент дисперсной фазы достигает 45% при pH 5. В области pH 6–7 образуются гидроксиды металлов, а также гидроксикарбонаты, процент дисперсной фазы возрастает до 87%.
В растворах, где концентрация NaCl < 0.1 г/л, при pH 8–10 процент дисперсной фазы составляет 95–100%. В то же время при добавлении в раствор 1 г/л NaCl при pH 8–12 процент дисперсной фазы составляет 80–90%, что связано с формированием растворимых комплексов в присутствии хлоридов натрия (табл. 1). Отмечено, что размер частиц дисперсной фазы РЗМ в присутствии хлоридов уменьшается (табл. 2).
Установлено, что в диапазоне pH 4–6 размер частиц соединений редкоземельных металлов менее 1 мкм. При увеличении pH до 7–9 размер частиц достигает ~10 мкм. При значениях pH > 10 наблюдается коагуляция дисперсной фазы, размер частиц более 200 мкм. Указанные процессы сопровождаются сменой величины и знака ζ-потенциала.
Был исследован процесс электрофлотационного извлечения соединений РЗМ в диапазоне рН 5–9. Результаты экспериментальных исследований представлены в табл. 3.
Из полученных экспериментальных данных видно, что в области значений pH 5–9 степень извлечения не превышает 15%. В то же время процент дисперсной фазы (табл. 1) составляет 80–90% при pH 7–9. Можно предположить, что низкие значения степени извлечения связаны с малым размером частиц <10 мкм (табл. 2), что затрудняет процесс электрофлотации.
Было исследовано влияние концентрации иона-осадителя на эффективность электрофлотационного процесса извлечения малорастворимых соединений редкоземельных металлов (табл. 4).
Таблица 4.
Влияние концентрации иона-осадителя и pH раствора на эффективность электрофлотационного процесса извлечения соединений редкоземельных металлов
Элемент | с(Na2CO3), г/л | |||||||||||
---|---|---|---|---|---|---|---|---|---|---|---|---|
0 | 0.25 | 0.5 | 1 | |||||||||
5 | 7 | 9 | 5 | 7 | 9 | 5 | 7 | 9 | 5 | 7 | 9 | |
La | 29 | 80 | 89 | 19 | 78 | 58 | 15 | 34 | 16 | 6 | 12 | 2 |
Ce | 23 | 84 | 92 | 22 | 79 | 48 | 16 | 24 | 9 | 9 | 10 | 6 |
Pr | 25 | 85 | 92 | 15 | 78 | 52 | 15 | 37 | 19 | 11 | 14 | 0 |
Nd | 26 | 85 | 91 | 14 | 78 | 56 | 10 | 36 | 23 | 10 | 13 | 1 |
Sm | 8 | 87 | 91 | 28 | 77 | 55 | 14 | 37 | 23 | 11 | 13 | 0 |
Gd | 30 | 82 | 88 | 21 | 76 | 45 | 10 | 34 | 17 | 9 | 13 | 5 |
Из полученных экспериментальных данных видно, что с увеличением концентрации карбонат-иона в растворе степень извлечения малорастворимых соединений РЗМ снижается. Из литературных данных [17] известно, что в присутствии карбонат-ионов в растворе возможно образование различных дисперсных соединений в зависимости от рН раствора, концентрации ионов металла и карбонат-ионов. Можно предположить, что с ростом концентрации карбонат-иона в исследуемом растворе изменяется природа дисперсной фазы, и при концентрации 1 г/л Na2CO3 дисперсная фаза представлена в виде карбонатов РЗМ, эффективность извлечения которых ниже, чем гидроксидов, область образования гидроксидов pH 6.5–10 [18, 19].
В целях повышения эффективности процесса, сокращения времени обработки и увеличения степени излечения исследовано влияние органических флокулянтов и поверхностно-активных веществ различной природы на электрофлотационное извлечение малорастворимых соединений редкоземельных металлов.
Был исследован процесс электрофлотационного извлечения малорастворимых соединений РЗМ в присутствии флокулянтов различной природы (катионный, анионный) при содержании карбонат-ионов в растворе 1 г/л (табл. 5).
Таблица 5.
Влияние флокулянтов на эффективность электрофлотационного процесса извлечения малорастворимых соединений редкоземельных металлов
Элемент | α, % | ||||||||
---|---|---|---|---|---|---|---|---|---|
Без добавки | SUPERFLOC С-494 (к) | SUPERFLOC A-137 (а) | |||||||
5 | 7 | 9 | 5 | 7 | 9 | 5 | 7 | 9 | |
La | 6 | 12 | 2 | 19 | 0 | 69 | 1 | 18 | 17 |
Ce | 9 | 10 | 6 | 11 | 2 | 72 | 3 | 15 | 18 |
Pr | 11 | 14 | 0 | 2 | 0 | 74 | 3 | 18 | 21 |
d | 10 | 13 | 1 | 3 | 0 | 73 | 4 | 19 | 23 |
Sm | 11 | 13 | 0 | 8 | 0 | 72 | 4 | 17 | 20 |
Gd | 9 | 13 | 5 | 4 | 1 | 71 | 6 | 20 | 15 |
Установлено, что при значениях рН 5 введение анионного и катионного (для некоторых элементов) флокулянта вызывает снижение степени извлечения малорастворимых соединений. Максимальная степень извлечения наблюдается при введении в систему катионного флокулянта SUPER FLOC С-494 при рН 9 – степень извлечения достигает 74%.
Экспериментальные данные, показывающие влияние ПАВ различной природы на процесс электрофлотационного извлечения малорастворимых соединений РЗМ, представлены в табл. 6.
Таблица 6.
Влияние поверхностно-активных веществ на эффективность электрофлотационного процесса излечения малорастворимых соединений редкоземельных элементов
Элемент | α, % | |||||||||||
---|---|---|---|---|---|---|---|---|---|---|---|---|
Без добавки | СептаПАВ (к) | NaDDS (а) | ПЭО-1500 (н) | |||||||||
5 | 7 | 9 | 5 | 7 | 9 | 5 | 7 | 9 | 5 | 7 | 9 | |
La | 6 | 12 | 2 | 30 | 90 | 20 | 1 | 87 | 11 | 4 | 90 | 29 |
Ce | 9 | 10 | 6 | 29 | 90 | 21 | 7 | 86 | 11 | 4 | 83 | 26 |
Pr | 11 | 14 | 0 | 35 | 90 | 23 | 5 | 87 | 9 | 9 | 90 | 29 |
Nd | 10 | 13 | 1 | 35 | 90 | 24 | 5 | 87 | 12 | 7 | 90 | 34 |
Sm | 11 | 13 | 0 | 35 | 90 | 23 | 6 | 86 | 10 | 8 | 90 | 35 |
Gd | 9 | 13 | 5 | 35 | 85 | 23 | 2 | 86 | 13 | 3 | 86 | 35 |
Из полученных данных видно, что максимальная степень извлечения малорастворимых соединений всех элементов многокомпонентной системы наблюдается при рН 7 при введении СептаПАВ (к) (α = 97–98%) и ПЭО-1500 (н) (α = 86–98%). Следует отметить, что при введении неионогенного ПАВ в процессе электрофлотационной обработки формировался устойчивый пенный продукт.
После первых промывок осадка фильтрат содержит достаточное количество хлорид-ионов (до 100 г/л). Концентрация редкоземельных элементов в таких стоках также повышена. Поэтому далее было исследовано влияние хлорид-ионов на процесс образования дисперсной фазы соединений редкоземельных металлов и ее электрофлотационное извлечение при увеличении концентрадии NaCl до 10 и 100 г/л.
В табл. 7 представлены экспериментальные данные определения процента дисперсной фазы при фильтрации осадка в растворах в интервале значений pH 4–12.
Таблица 7.
Процент дисперсной фазы соединений РЗМ в зависимости от pH раствора при увеличении концентрации NaCl до 10 г/л
рН | D, % | |||||
---|---|---|---|---|---|---|
La | Ce | Pr | Nd | Sm | Gd | |
4 | 4 | 5 | 4 | 4 | 5 | 2 |
5 | 5 | 6 | 5 | 6 | 5 | 5 |
6 | 6 | 6 | 8 | 8 | 5 | 6 |
7 | 6 | 7 | 5 | 6 | 5 | 7 |
8 | 6 | 6 | 6 | 6 | 5 | 2 |
9 | 4 | 5 | 4 | 5 | 3 | 4 |
10 | 3 | 3 | 3 | 4 | 4 | 2 |
11 | 5 | 6 | 6 | 6 | 7 | 7 |
12 | 5 | 5 | 4 | 5 | 2 | 6 |
Из полученных данных видно, что во всем диапазоне рН процент дисперсной фазы не превышает 8%. Можно предположить, что размер частиц составляет менее 1 мкм и частицы не могут задерживаться на фильтре.
Как известно, процесс электрофлотации связан не только с извлечением дисперсной фазы металлов, но и с укрупнением частиц за счет процессов флокуляции [20]. В табл. 8 представлены данные, показывающие зависимость степени извлечения частиц от рН раствора в процессе электрофлотационной обработки.
Таблица 8.
Влияние pH раствора на степень извлечения малорастворимых соединений редкоземельных металлов
рН | α, % | |||||
---|---|---|---|---|---|---|
La | Ce | Pr | Nd | Sm | Gd | |
5 | 20 | 22 | 23 | 20 | 24 | 21 |
6 | 25 | 65 | 66 | 68 | 79 | 70 |
7 | 41 | 46 | 56 | 62 | 73 | 45 |
8 | 33 | 30 | 29 | 30 | 31 | 22 |
9 | 15 | 21 | 29 | 23 | 23 | 24 |
10 | 1 | 6 | 9 | 11 | 10 | 43 |
Установлено, что в диапазоне значений pH 6–7 степень извлечения малорастворимых соединений редкоземельных металлов принимает максимальные значения, однако не превышает 79%.
Добавление в раствор флокулянтов различной природы приводит к повышению степени извлечения соединений до 80–90%. Аналогичное действие оказывают и поверхностно-активные вещества.
Высокая эффективность процесса сохраняется при высокой концентрации NaCl (100 г/л) в присутствии ПАВ и флокулянтов.
ЗАКЛЮЧЕНИЕ
Проведенные исследования показали, что электрофлотационный процесс позволяет эффективно извлекать малорастворимые соединения смеси РЗМ как из промывных вод при отмывке осадков РЗМ от ионов хлора, так и из солевых растворов (NaCl) фильтратов. Место и роль электрофлотационных процессов показано на схеме получения карбонатов РЗМ (рис. 2).
Рис. 2.
Схема выделения карбонатов РЗМ из хлорсодержащего технологического раствора: 1 – реактор образования карбонатов редкоземельных металлов; 2 – реактор для ввода дополнительного реагента СO2 для снижения скорости гидролиза Na2CO3; 3 – промывная вода (очищенная); 4–6 – фильтры (Ф1 – крупнопористый (~500 г/м2), Ф2 – среднепористый (~750 г/м2), Ф3 – мелкопористый (~1000 г/м2)); 7 – емкость для сбора фильтрата; 8 – накопитель промывной воды; 9 – электрофлотатор для очистки промывной воды; 10 – электрофлотатор для очистки фильтрата.
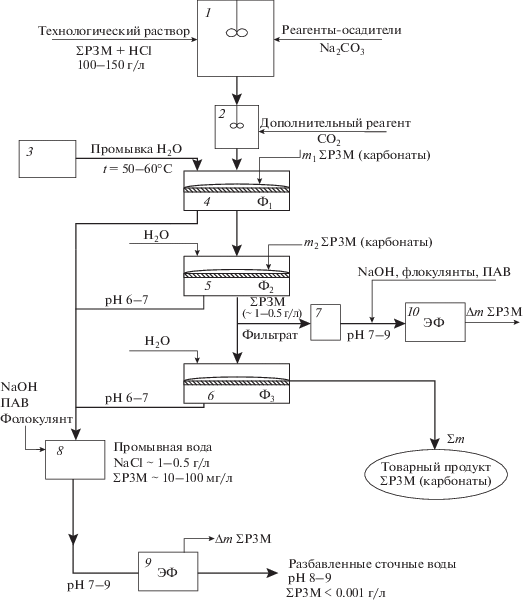
Базовая схема выделения ∑РЗМ включает три стадии фильтрации и промывку осадков. В связи с отмеченными проблемами схема дополнена двумя электрофлотационными установками 9 и 10. Электрофлотатор 9 обеспечивает извлечение из промывной воды редкоземельных элементов в виде карбонатов и гидроксидов. Электрофлотатор 10 обеспечивает высокоэффективную очистку фильтрата, содержащего до 100 г/л NaCl, от дисперсной фазы карбонатов и гидроксидов РЗМ. Указанный подход позволяет предотвращать потери редкоземельных элементов с промывными водами и в фильтрате после технологических операций.
Для реализации указанного процесса созданы электрофлотационные установки производительностью 5 и 10 м3/ч с нерастворимыми анодами на основе ОРТА. Затраты электроэнергии для очистки воды до 1 кВт/м3, для очистки фильтрата 0.2–0.5 кВт/м3.
Работа выполнена при финансовой поддержке РХТУ им. Д.И. Менделеева (проект № З-2020-004).
ОБОЗНАЧЕНИЯ
с | концентрация, г/л |
D | процент дисперсной фазы, % |
d | средний гидродинамический диаметр частиц, мкм |
iv | объемная плотность тока, А/л |
α | степень извлечения, % |
ζ | электрокинетический потенциал, мВ |
τ | продолжительность процесса, мин |
ИНДЕКСЫ
Список литературы
Saleem H.A. Social and environmental impact of the rare earth industries // Resources. 2014. V. 3. P. 123.
McLellan B.C., Glen D.C., Saleem H.A. Sustainability of rare earths – an overview of the state of knowledge // Minerals. 2013. V. 3. P. 304.
Веселова Э.Ш., Самсонов Н.Ю. Российская РЗМ-индустрия: ренессанс или воссоздание с нуля? // ЭКО. 2014. № 2. С. 5.
Крюков В.А., Зубкова С.А. Реиндустриализация без своих РЗМ // ЭКО. 2016. № 8. С. 5.
Никулин А.А. Металлы для высоких технологий: тенденции мирового рынка редкоземельных элементов // Пробл. нац. стратегии. 2014. № 1(22). С. 134.
Косенко В.П., Жуков В.Т., Пехов Г.Ф., Казанцев В.Н. Способ вскрытия монацитового концентрата. Пат. 2242528 РФ. 2004.
Постолатьева А., Твердов А., Жура А. Редкоземельные месторождения: особенности, сложности и перспективы // Золото технол. 2013. № 1(19). С. 5.
Черемисина О.В., Литвинова Т.Е., Сергеев В.В., Луцкий Д.С., Лобачева О.Л. Способ извлечения и разделения редкоземельных металлов при переработке апатитового концентрата. Пат. 2640479 РФ. 2018.
Буйновский А.С., Жиганов А.Н., Сачков В.И., Молоков П.Б. Способ переработки апатитовых руд и концентратов. Пат. 2614962 РФ. 2017.
Binnemansa K., Jones P.T., Blanpain B., Gervenc T.V., Yang Y., Waltone A., Buchertf M. Recycling of rare earths: a critical review // J. Cleaner Prod. 2013. V. 51. P. 1.
Kolesnikov V.A., Il’in V.I., Brodskiy V.A., Kolesnikov A.V. Electroflotation during wastewater treatment and extraction of valuable compounds from liquid technogenic waste: A review // Theor. Found. Chem. Eng. 2017. V. 51. P. 369.
Khelifa A., Moulay S., Naceur A.W. Treatment of metal finishing effluents by the electroflotation technique // Desalination 2005. V. 181. P. 27.
Kyzas G.Z., Matis K.A. Electroflotation process: A review // J. Mol. Liq. 2016. V. 220. P. 657.
Gaydukova A.M., Brodskii V.A., Kolesnikov V.A. Influence of pH of the medium on the physicochemical characteristics and efficiency of electroflotation recovery of poorly soluble cerium(III, IV) compounds from aqueous solutions // Russ. J. Appl. Chem. 2015. V. 88. P. 1446.
Kolesnikov A.V., Gaidukov E.N., Kolesnikov V.A. The role of surfactants in intensifying and increasing the efficiency of the electroflotation extraction of sparingly soluble lanthanum compounds // Theor. Found. Chem. Eng. 2016. V. 50. № 2. P. 142.
Kolesnikov A.V., Kuznetsov V.V., Kolesnikov V.A., Kapustin Yu.I. The role of surfactants in the electroflotation extraction of copper, nickel, and zinc hydroxides and phosphates // Theor. Found. Chem. Eng. 2015. V. 49. № 1. P. 1.
Колесников В.А., Ильин В.И., Капустин Ю.И. Электрофлотационная технология очистки сточных вод промышленных предприятий. М.: Химия, 2007.
Takeno N. Atlas of Eh-pH Diagrams. Geological Survey of Japan Open File Report. 2005.
Гайдукова А.М., Бродский В.А., Колесников В.А. Влияние рН среды на физико-химические характеристики и эффективность электрофлотационного извлечения малорастворимых соединений церия (III, IV) из водных растворов // Журн. прикл. хим. 2015. Т. 88. № 9. С. 1300.
Шуленина З.М., Багров В.В., Десятов А.В. и др. Вода техногенная: проблемы, технологии, ресурсная ценность. М.: МГТУ им. Н.Э. Баумана, 2015.
Дополнительные материалы отсутствуют.
Инструменты
Теоретические основы химической технологии