Теоретические основы химической технологии, 2021, T. 55, № 1, стр. 3-15
Ректификация воды как метод разделения изотопов водорода и кислорода: состояние и перспективы
Э. П. Магомедбеков a, *, И. Л. Растунова a, Н. Н. Кулов b
a Российский химико-технологический университет им. Д.И. Менделеева
Москва, Россия
b Институт общей и неорганической химии им. Н.С. Курнакова РАН
Москва, Россия
* E-mail: eldar@muctr.ru
Поступила в редакцию 25.09.2020
После доработки 30.09.2020
Принята к публикации 05.10.2020
Аннотация
Ректификация воды под вакуумом является одним из наиболее экологически чистых и безопасных способов разделения изотопов водорода и кислорода. В статье представлен обзор литературных данных, описывающих современное состояние работ в области совершенствования процесса. Представлен анализ характеристик контактных устройств, использующихся в процессе ректификации, и показаны способы повышения их эффективности. Представлены данные о новых разработках, направленных на оценку эффективности использования солевой ректификации воды для изотопного разделения. Рассмотрены аспекты практического применения ректификации воды для концентрирования тяжелых изотопов водорода и кислорода, а также для получения воды с пониженным содержанием дейтерия.
ВВЕДЕНИЕ
Методы ректификации, основанные на фазовом равновесии, находят широкое применение для разделения стабильных изотопов водорода, кислорода, углерода и азота. Несмотря на невысокие значения коэффициента разделения, характерные для данных процессов, эти методы обладают целым рядом неоспоримых достоинств, таких как хорошо проработанная теоретическая основа, простота технологической реализации процесса, широкий диапазон возможностей масштабирования производства и ряд других [1].
В табл. 1 представлены сравнительные характеристики однократного разделительного эффекта при разделении изотопов водорода и кислорода методом ректификации.
Таблица 1.
Изотопный эффект при разделении изотопов водорода и кислорода методом ректификации [1]
Изотопная система | Рабочее вещество | Т, К | α |
---|---|---|---|
H–D | водород | 23 | 1.47 |
аммиак | 253 | 1.036 | |
вода | 333 | 1.047 | |
16О–18О | монооксид азота-14 | 120 | 1.037 |
кислород | 90 | 1.0047 | |
вода | 333 | 1.0063 |
Разработка технологии и создание установок для разделения изотопов водорода методом ректификации начались в 40-е гг. ХХ в. применительно к решению стратегической задачи получения тяжелой воды (D2O). Как видно из табл. 1, в качестве рабочих веществ при этом использовались водород, вода и аммиак. Несмотря на значительно более низкие значения коэффициента разделения, процессы ректификации оказываются во много раз экономичнее с точки зрения затрат энергии, вследствие чего они нашли достаточно широкое применение для разделения изотопов водорода [1–4].
Среди всех возможных ректификационных методов разделения изотопов водорода низкотемпературная ректификация водорода является наиболее привлекательной с термодинамической точки зрения вследствие аномально высокого коэффициента разделения [1–4]. Реализация процесса осложняется как его проведением при низких температурах (при 0.01 МПа температура кипения жидкого водорода нормального, орто- и пара-состава равна: для молекул Н2 – 20.39 К; HD – 22.14 K; D2 – 23.67 K; HT – 22.92 K; DT – 24.38 K; T2 – 25.04 K), так и необходимостью осуществления каталитической реакции гомомолекулярного изотопного обмена. Кроме того, необходима предварительная глубокая очистка водорода от кислорода (до уровня 10–10–10–11 об. д.) во избежание образования в аппарате-разделителе взрывоопасной смеси [1–6]. Впервые в промышленном масштабе процесс был реализован в СССР, где стал основным способом производства тяжелой воды из природного сырья [2, 6]. Подобные установки получения тяжелой воды в XX в. работали в Индии, Франции и ФРГ [2–4]. Следует отметить, что низкотемпературная ректификация водорода является единственным методом, реализованным в промышленном масштабе для получения высококонцентрированного трития [2, 6, 7].
Использование в качестве рабочего вещества аммиака, несмотря на значительно более низкие значения коэффициента разделения, является перспективным за счет больших масштабов его производства, что позволяет осуществлять выделение дейтерия транзитным методом. Наиболее масштабное производство тяжелой воды методом ректификации аммиака было также осуществлено в СССР в 1955–1962 гг., однако вследствие существенных затрат энергии и малой эффективности эксплуатировавшихся тарельчатых контактных устройств в дальнейшем его использовали только на стадии конечного концентрирования [2, 8].
Рабочие системы, использующиеся для концентрирования кислорода-18 путем ректификации, характеризуются значительно более низкими значениями однократного разделительного эффекта (см. табл. 1). Исключением является криогенная ректификация монооксида азота, обладающая аномально высоким значением коэффициента разделения по сравнению с ректификацией воды и молекулярного кислорода. Поэтому, несмотря на отсутствие надежных источников чистого NO, разделительные установки были построены в СССР и Румынии [1, 9, 10]. Высокие значения изотопного эффекта при ректификации оксида азота связаны с димеризацией оксида азота(II) в жидкой фазе (~25% N2O2), и, таким образом, имеет место химобменная ректификация. К числу недостатков данной системы относятся необходимость использования катализатора для осуществления реакции гомомолекулярного изотопного обмена NO с целью получения продукта с высоким содержанием 18O, повышенная стоимость рабочего вещества, а также его большая коррозионная активность, взрывоопасность и токсичность [1].
Криогенная ректификация молекулярного кислорода, несмотря на значительно более низкие значения коэффициента разделения, является достаточно простым и эффективным способом разделения изотопов кислорода. К недостаткам метода можно отнести отсутствие самопроизвольного протекания реакции гомомолекулярного изотопного обмена кислорода, что затрудняет получение высококонцентрированного 18О, а также сложность специального криогенного оборудования и взрывоопасность производства. Данный разделительный процесс наиболее выгодно комбинировать с работой воздухоразделительных установок с целью экономии затрат на сырье и поддержание криогенных температур [1, 11–13].
Наиболее экологически чистым и безопасным способом разделения изотопов как водорода, так и кислорода является ректификация воды. Несмотря на малые значения коэффициента разделения (см. табл. 1), ректификация воды стала одним из первых методов получения тяжелой воды в промышленном масштабе. Так, в США в 1943–1945 гг. работали три однотипные установки, каждая из которых включала в себя восьмиступенчатый ректификационный каскад начального концентрирования для повышения концентрации дейтерия от природного уровня до 90%, а также установку конечного концентрирования до 99.8% электролитическим методом [2–4]. В дальнейшем метод ректификации применялся на стадии конечного концентрирования тяжелой воды, для депротизации теплоносителя и замедлителя тяжеловодных реакторных установок [1, 2, 5, 14]. В настоящее время ректификация воды является основным способом получения тяжелокислородной воды и воды с пониженным содержанием дейтерия [10, 15, 16].
ОСНОВНЫЕ ХАРАКТЕРИСТИКИ МЕТОДА РЕКТИФИКАЦИИ ВОДЫ
Ректификация воды является самым отработанным способом разделения изотопов водорода. Вследствие близости к единице значений коэффициентов разделения (см. табл. 1), извлечение при однократном разделительном эффекте мало, что требует переработки больших потоков и большого числа теоретических ступеней разделения. Реакции изотопного обмена водорода и кислорода при ректификации воды описываются следующими уравнениями:
(1)
${\text{HD}}{{{\text{O}}}_{{\left( {\text{п}} \right)}}} + {{{\text{H}}}_{{\text{2}}}}{{{\text{O}}}_{{\left( {\text{ж}} \right)}}} \Leftrightarrow {{{\text{H}}}_{{\text{2}}}}{{{\text{O}}}_{{\left( {\text{п}} \right)}}} + {\text{HD}}{{{\text{O}}}_{{\left( {\text{ж}} \right)}}},$(2)
${\text{HT}}{{{\text{O}}}_{{\left( {\text{п}} \right)}}} + {{{\text{H}}}_{{\text{2}}}}{{{\text{O}}}_{{\left( {\text{ж}} \right)}}} \Leftrightarrow {{{\text{H}}}_{{\text{2}}}}{{{\text{O}}}_{{\left( {\text{п}} \right)}}} + {\text{HT}}{{{\text{O}}}_{{\left( {\text{ж}} \right)}}},$(3)
${\text{DT}}{{{\text{O}}}_{{\left( {\text{п}} \right)}}} + {{{\text{D}}}_{{\text{2}}}}{{{\text{O}}}_{{\left( {\text{ж}} \right)}}} \Leftrightarrow {{{\text{D}}}_{{\text{2}}}}{{{\text{O}}}_{{\left( {\text{п}} \right)}}} + {\text{DT}}{{{\text{O}}}_{{\left( {\text{ж}} \right)}}},$(4)
${\text{H}}_{{\text{2}}}^{{{\text{18}}}}{{{\text{O}}}_{{\left( {\text{п}} \right)}}} + {\text{H}}_{{\text{2}}}^{{{\text{16}}}}{{{\text{O}}}_{{\left( {\text{ж}} \right)}}} \Leftrightarrow {\text{H}}_{{\text{2}}}^{{{\text{16}}}}{{{\text{O}}}_{{\left( {\text{п}} \right)}}} + {\text{H}}_{{\text{2}}}^{{{\text{18}}}}{{{\text{O}}}_{{\left( {\text{ж}} \right)}}}.$Для данных реакций, исходя из представлений о разделении бинарных смесей, значения коэффициентов разделения в системе пар–вода могут быть рассчитаны как отношение парциальных давлений (P0) изотопных модификаций молекул воды, а также с помощью эмпирических уравнений, справедливых в диапазоне температур T = = 273–400 К [1, 2, 17]:
(5)
$\begin{gathered} {\text{ln}}{{\alpha }_{{{\text{H}} - {\text{D}}}}} = {\text{ln}}\frac{{P_{{{{{\text{H}}}_{{\text{2}}}}{\text{O}}}}^{0}}}{{P_{{{\text{HDO}}}}^{0}}} = \frac{{26398.8}}{{{{T}^{2}}}} - \\ - \,\,\frac{{89.6065}}{T} + 0.075802, \\ \end{gathered} $(6)
$\begin{gathered} \ln \left( {\alpha _{{{\text{H}} - {\text{T}}}}^{2}} \right) = \ln \frac{{P_{{{{{\text{H}}}_{{\text{2}}}}{\text{O}}}}^{0}}}{{P_{{{{{\text{T}}}_{{\text{2}}}}{\text{O}}}}^{0}}} = \frac{{68702.3}}{{{{T}^{2}}}} - \\ - \,\,\frac{{244.687}}{T} + 0.224388, \\ \end{gathered} $(7)
$\ln {{\alpha }_{{{\text{D}} - {\text{T}}}}} = \ln \frac{{P_{{{\text{D}}{}_{{\text{2}}}{\text{O}}}}^{0}}}{{P_{{{\text{DTO}}}}^{0}}} = \frac{{9918.5}}{{{{T}^{2}}}} - \frac{{40.68}}{T} + 0.0426,$(8)
${\text{ln}}{{\alpha }_{{{}^{{16}}{\text{O}} - {}^{{18}}{\text{O}}}}} = \frac{{{\text{1037}}}}{{{{T}^{2}}}} - \frac{{0.4156}}{T} - 0.00207.$С учетом снижения коэффициента разделения с ростом температуры (рис. 1) процесс проводят под вакуумом, при этом оптимальным считается давление на уровне 0.02−0.03 МПа, что соответствует температуре 333−343 К [1, 2, 4].
Рис. 1.
Зависимость коэффициента разделения при ректификации воды от температуры: 1 – αH–T; 2 – αH–D; 3 – αD–T; 4 – α16O–18O.
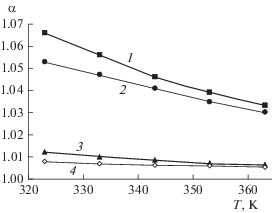
Следует также отметить, что поскольку в воде в общем случае могут присутствовать три изотопа водорода (Н, D, T) и кислорода (16O, 17O, 18O), то в общем случае разделению будут подвергаться молекулярные смеси, содержащие все возможные изотопные формы воды. В работах [18–20] изложен алгоритм расчета профиля концентрации нецелевого тяжелого изотопа при разделении трехкомпонентной смеси в установке ректификации воды “закрытого” типа с режимом отбора продукта. Алгоритм основан на принципах общей теории тонкого разделения смесей в области малых концентраций тяжелого компонента. Суть его сводится к расчету параметров процесса разделения бинарной смеси, содержащей легкий и целевой тяжелый изотоп одного из химических элементов, в результате которого определяют величины потоков, мольного отношения потоков λ и число теоретических ступеней разделения N в концентрирующей и исчерпывающей частях колонны. После этого, рассматривая бинарную смесь, содержащую легкий и нецелевой тяжелый изотоп второго химического элемента, с использованием рассчитанных значений потоков и числа теоретических ступеней разделения в концентрирующей части, методом последовательных итераций находят величину относительного отбора по нецелевому компоненту, соответствующему значению λ, найденному для целевого компонента. Далее рассчитывается значение N, необходимое для достижения значения концентрации нецелевого тяжелого изотопа в потоке отбора продукта, после чего из уравнений рабочих линий определяются концентрации компонента в потоке пара в сечении точки ввода питания и в отвале. Затем определяют соответственно значения степени разделения и N в исчерпывающей части колонны. Расчет числа теоретических ступеней разделения проводится методом “от ступени к ступени”.
По результатам моделирования процесса авторы делают вывод об отличии профиля концентраций по высоте колонны для тяжелых изотопов целевого и нецелевого компонента при одновременном разделении трехизотопных смесей [18–20].
На рис. 2 представлен профиль концентраций дейтерия и кислорода-18 для модельной задачи при следующих значениях концентрации дейтерия: в питающем потоке 0.01, в концентрате 0.0125 и в отвале 0.07. При этом концентрация кислорода-18 в потоке питания равна 0.001966, а среднее давление в колонне составляет 0.03 МПа [18].
Нетрудно убедиться, что для дейтерия, являющегося целевым изотопом, наблюдается монотонное изменение концентрации по мере удаления от точки питания с достижением балансовых значений в верхнем и нижнем сечениях колонны. При этом для кислорода-18 (линия 18Орасч) монотонный характер нарушается на некотором отдалении от точки питания (начало расчета) и далее его концентрация, достигнув балансовых значений, перестает изменяться. Таким образом, часть ступеней как в концентрирующей, так и в исчерпывающей частях не участвует в процессе разделения. Линия 18Опрогноз, полученная при расчете от верха колонны без учета смешения концентраций, показывает, что в данном случае концентрирующая часть колонны не будет работать на разделение изотопов кислорода, а все возможное разделение по 18О будет обеспечиваться исчерпывающей частью [18]. Таким образом, различный характер изменения концентраций в колонне и происходящее вследствие этого смешение изотопных концентраций нецелевого компонента в точке ввода питания следует учитывать при расчете разделительных установок.
Массообменные характеристики противоточного разделения изотопов методом ректификации воды. Изотопный обмен методом ректификации воды характеризуется близкими к единице значениями коэффициента разделения, вследствие чего для обеспечения высокой степени разделения необходимо многократное умножение разделительного эффекта, требующее большого числа теоретических ступеней разделения в противоточных колоннах. Для обеспечения эффективного массопереноса между паром и жидкостью требуется создание развитой поверхности контакта фаз, что реализуется с помощью контактных устройств различного типа.
Для осуществления процесса ректификации воды находят применение колонны с тарельчатыми и насадочными контактными устройствами.
Тарельчатые контактные устройства, характеризующиеся высокой пропускной способностью, используются в крупнотоннажном производстве в различных отраслях промышленности. Для разделения изотопов водорода колонны с колпачковыми тарелками использовались при создании каскадов ректификационных колонн с диаметром от 0.25 до 4.6 м для получения тяжелой воды из природного сырья в США [2, 4]. В настоящее время в России такие контактные устройства работают в колоннах диаметром от 0.25 до 0.7 м каскада депротизации тяжеловодного реактора ЛФ-2 на Производственном объединении “Маяк”, при этом высота, эквивалентная теоретической ступени разделения (ВЭТС), для этих колонн составляет 50 ± 5 см [14].
Кроме высоких значений ВЭТС, к недостаткам тарельчатых контактных устройств следует также отнести высокое гидравлическое сопротивление, приводящее к значительному градиенту температур по высоте колонны и, как следствие, снижению эффективности разделения в направлении от верха к низу колонны.
Насадочные контактные устройства также широко используются для разделения изотопов при ректификации. Их отличительной особенностью является непрерывный характер изменения состава разделяющихся смесей по высоте колонны за счет равномерного распределения элементов насадки в ее объеме. Различают регулярные насадки, образующие геометрически правильные каналы для прохода пара, и нерегулярные (насыпные), когда элементы насадки, располагаясь в слое стохастически, образуют извилистые каналы неправильной формы. В колоннах большой высоты слой насадки рекомендуется делить на несколько частей, устанавливая соответствующее число опорных решеток и распределителей орошения. Рекомендованная высота сплошного слоя насадки не должна превышать 2.5–3 диаметров колонны [1, 2, 21].
Нерегулярные насадки представляют собой элементы различной конфигурации, которые характеризуются большими значениями удельной поверхности и удерживающей способности жидкости. Обычно их подразделяют на промышленные (с размером элемента более 10 мм), предназначенные для переработки больших потоков (до 100 м3/(м2 ч)), и мелкие высокоэффективные насадки с размером элемента обычно не более 5–6 мм [1, 2, 21–28]. Кроме традиционных кольцевых и седлообразных промышленных насадок и мелкой спирально-призматической насадки Левина, для осуществления процессов разделения используют такие насадки, как кольца ГИАП [25], насадка “Инжехим” [28], а также насадки типа колец Диксона из гофрированной нержавеющей сетки [23, 24].
Сравнение параметров промышленных насадок затруднено вследствие того, что, в зависимости от задачи разделения, одни и те же насадки могут изготавливаться с использованием различных материалов (различные виды металла, керамика, фарфор, полимерные материалы и др.) при варьировании размерного ряда в широком диапазоне. Сведения о характеристиках промышленных нерегулярных насадок из различных материалов приведены в работе [2].
Попытка обобщения сведений о массообменных и гидравлических характеристиках различных насадок была предпринята в работе [21], однако приведенные данные без указания наименования, размера и материала насадок являются малоинформативными. Кроме того, учитывая специфику изотопного разделения, вопрос о возможности переноса данных, полученных с использованием других смесей, является весьма спорным.
В патентах [23, 24] приведены результаты сравнения крупных насадок из нержавеющей гофрированной сетки с перегородкой (рис. 3) с насадкой Диксона (рис. 3а), изготовленной из плоской сетки с близкими характеристиками – толщина проволоки 0.26 мм, просвет 0.26 мм. Размер элемента насадки для всех образцов составлял 15 × 15 мм. Испытания, проведенные в процессе ректификации воды при Р = 0.1 МПа, показали, что величина предельной пропускной способности для всех трех образцов одинакова и составляет 18000 кг/(ч м2), а при плотности орошения, равной 80% от предельной, в колоннах диаметрами 120, 200 и 300 мм значения ВЭТС составили: для насадки Диксона – 16, 20 и 28 см соответственно; для насадки из гофрированной сетки с одним зубчатым краем (рис. 3в) – 14, 16 и 20 см; а для насадки из гофрированной сетки с двумя зубчатыми краями (рис. 3б) – 12, 13 и 15 см [23, 24].
Применительно к процессу ректификации воды наибольшее использование находят насадки из нержавеющей стали, причем наиболее популярной является спирально-призматическая насадка (СПН). Данные об испытаниях мелкой высокоэффективной СПН в процессе ректификации воды относятся к разделению изотопов как водорода, так и кислорода [29–32].
В ряде работ отмечается значительное влияние способа предварительной подготовки насадки и способа заполнения и пуска колонны на эффективность массообмена [29–31]. В работе [29] показано, что в сопоставимых условиях для СПН из нержавеющей стали с размером элемента 2 мм при простой отмывке от масла с использованием поверхностно-активных веществ было получено значение ВЭТС, равное 6 см, в то время как ее последующее травление в разбавленном растворе смеси азотной и соляной кислот привело к снижению ВЭТС в 3 раза. Влияние способа заполнения колонны насадкой было исследовано в работе [31]. По данным работ [31, 32], наиболее предпочтительным является запуск заполненной мелкой нерегулируемой насадкой колонны в барботажном режиме с последующим постепенным переводом ее в пленочный режим или при предварительном затоплении насадки с последующим непрерывным ее орошением до окончания пускового периода.
Наиболее полное исследование гидравлических и массообменных характеристик СПН из нержавеющей стали с размером элемента от 2 до 10 мм в колоннах диаметром 60 и 120 мм представлено в работе [32]. На рис. 4 приведена построенная на основании данных этой работы зависимость предельной пропускной способности L* от давления в диапазоне 0.01–0.1 МПа. Показано, что для всех образцов увеличение давления в 10 раз приводит к росту пропускной способности колонны примерно в 2.5 раза, однако изменение диаметра колонны в 2 раза не приводит к изменению L*.
Определение ВЭТС проводилось при давлении 0.02 МПа и потоке жидкости, равном 0.8L* в безотборном режиме. В работе показано, что в колонне диаметром 120 мм при увеличении размера элемента насадки от 2 до 10 мм значение ВЭТС возрастает более чем в 7 раз (с 1.9 до 14.2 мм). При этом авторы отмечают совпадение с высокой точностью ВЭТС, полученных для систем H−D и 16O–18O [32]. Также в работе показана слабая зависимость ВЭТС от диаметра колонны – примерно в 1.1 раза при увеличении диаметра колонны с 60 до 120 мм, что, по мнению авторов, связано с использованием оптимальных способов обработки и загрузки насадки, а также режима пуска колонны.
Безусловный интерес представляют результаты исследования влияния диаметра колонны на эффективность разделения, полученные для СПН 3 × 3 × 0.2 мм при давлении 0.02 МПа и плотности орошения 830 кг/(ч м2) [31]. Заполнение колонн проводилось небольшими порциями с выравниванием и трамбовкой, а запуск осуществлялся в барботажном режиме с последующим медленным переводом в пленочный.
Данные по сравнению характеристик разделения при ректификации в традиционном пленочном и затопленном режимах представлены в работе [30] для СПН 2 × 2 × 0.2 мм и 3.5 × 3.5 × 0.22 мм при давлении Р = 0.1 МПа и различных плотностях орошения Lуд в колонне диаметром 40 мм и высотой 870 мм (табл. 2).
Таблица 2.
Зависимость ВЭТС от относительной нагрузки для пленочного режима и режима затопления [30]
Режим | Пленочный режим | Режим затопления | ||
---|---|---|---|---|
Размер элемента СПН, мм | 2 × 2 × 0.2 | 3.5 × 3.5 × 0.22 | 2 × 2 × 0.2 | 3.5 × 3.5 × 0.22 |
L*, кг/(ч м2) | 1220 | 1920 | 1920 | 3210 |
Lуд/L* | ВЭТС, см | |||
0.5 | 1.8 | 3.3 | – | 7.5 |
0.6 | 1.9 | – | – | – |
0.7 | – | 3.6 | 3.3 | 5.5 |
0.8 | 2.0 | 3.6 | 3.0 | 4.0 |
0.9 | – | 3.7 | – | 3.8 |
0.65 | 2.0 | – | 2.3 | 3.8 |
Следует отметить, что данные, полученные для пленочного режима в работе [30], хорошо согласуются с литературными данными для аналогичных насадок [15, 31, 32].
Регулярные насадки характеризуются упорядоченной структурой, обладают существенно большей пропускной способностью и меньшим гидравлическим сопротивлением по сравнению с нерегулярными и широко используются для осуществления различных тепло- и массообменных процессов.
Широкое применение нашли регулярные насадки различных типов (Rombopak, Mellapak, Gauze packing, Katapak), выпускаемые фирмой Sulzer и предназначенные для проведения процессов разделения различных смесей абсорбционными методами и ректификацией [34–36]. Насадка изготавливается из вертикальных полос гофрированной сетки из нержавеющей стали, которые располагаются параллельно на определенном расстоянии друг от друга и скрепляются между собой точечной сваркой. Упаковка полос в блоки осуществляется посредством жесткого бандажа из гладких лент или лент с “лепестками” (рис. 5).
Регулярная насадка Sulzer Mellapak 750 CY, изготовленная из гофрированных полос, с удельной поверхностью порядка 800 м2/м3 была разработана для разделения смесей с близкими свойствами (изомеров) и успешно использовалась в составе промышленных установок по производству тяжелой воды в Канаде. По данным [1], значения ВЭТС в этих установках составляли 10 см. При этом для лабораторной колонны диаметром 108 мм с насадкой такого типа в работе [37] приводится значение ВЭТС, равное 8 см, которое при нанесении на ее поверхность цеолита 13Х удалось снизить до 6 см.
Исследование эффективности разделения для насадки Sulzer Mellapak 750 CY из нержавеющей стали в процессе ректификации воды при атмосферном давлении проведено в работах [33, 38]. В колонне диаметром 60 мм и высотой слоя насадки 112 см (7 блоков по 16 см) проводилось сравнительное исследование влияния пусковых режимов на массообменные характеристики процесса при нагрузке по жидкости, равной 5660 кг/(ч м2), что составляло 80% от предельной пропускной способности насадки. Варианты пуска подразделялись на три группы, первая из которых включала режимы с захлебыванием колонны, вторая – пуск с предварительным заполнением всего слоя насадки жидкостью, а третья – с предварительным охлаждением насадки до температуры порядка 268 К для создания на ее поверхности пленки конденсата при подаче пара. Было показано, что при традиционном трехкратном захлебывании насадки значение ВЭТС составило 9.3 ± 0.3 см [33, 38], а в случае третьего варианта эта величина достигала 20 ± 0.7 см [33]. При втором варианте с предварительным заполнением колонны жидкостью значения ВЭТС изменялись в интервале от 12 до 16.5 см в случае полного слива воды из колонны и последующей подачи пара [33, 38]. При этом обеспечение непрерывного орошения слоя насадки во время слива жидкости из колонны приводило к снижению ВЭТС до 8.0 ± 0.5 см [33]. Также в работе отмечалось, что расчеты ВЭТС по результатам анализа по дейтерию и 18О в пределах точности совпадали. При этом следует отметить, что значения ВЭТС, полученные при ректификации и при фазовом изотопном обмене воды, в случае непрерывного орошения насадки во время пуска колонны в пределах точности совпали для насадки из нержавеющей стали, а для медной оксидированной насадки Sulzer Mellapak типа Y были получены значения ВЭТС на уровне 3.8 см [38].
Среди российских разработок в области регулярных насадок следует отметить рулонную ленточно-винтовую насадку (РЛВН) [39, 40]. Насадка изготавливается путем намотки под углом друг к другу гофрированных или поочередно гофрированных и плоских лент из нержавеющей сетки (рис. 5). Основной отличительной особенностью РЛВН является то, что блоки могут быть изготовлены высотой, соответствующей высоте царги колонны, в отличие от насадки Sulzer, выпускающейся в виде блоков стандартных размеров. Отсутствие стыков в местах соединения блоков внутри царги для РЛВН обеспечивает ей более равномерное распределение и стекание жидкости, что приводит к увеличению (примерно в 1.5–2 раза) пропускной способности по сравнению с прототипом [39].
В работе [40] представлены результаты исследования рулонной ленточно-винтовой насадки в колоннах диаметром 60 и 120 мм при ректификации воды. Показано, что при давлении P = 0.02 МПа предельная пропускная способность насадки составляет L* = 6600 кг/(ч м2), а значение ВЭТС возрастает с 16 до 18 см при увеличении диаметра колонны в 2 раза. При этом изменение плотности орошения от 80 до 30% от L* на величину ВЭТС не влияет. Сравнение с насадкой Sulzer Mellapak 750 CY в сопоставимых условиях показало, что значения ВЭТС для РЛВН оказались более чем в 2 раза выше (16 и 8 см соответственно), однако ее пропускная способность примерно в 1.5 раза выше, чем для насадки Sulzer [40]. Эти результаты хорошо согласуются с данными работы [38].
На основании приведенных данных можно считать, что, с учетом более высокой пропускной способности и практически полного отсутствия зависимости ВЭТС от потока жидкости и диаметра колонны, рулонная ленточно-винтовая насадка является перспективной для ее использования в процессе разделения изотопов методом вакуумной ректификации воды.
В работе [37] описана регулярная насадка, разработанная фирмой Tianjin SepTech Science and Technology Ltd. (Китай), которая при испытании в колонне диаметром 260 мм и высотой 12 м при давлении вверху 0.007 МПа показала значение ВЭТС, равное 16 см. Это, по мнению авторов, делает ее конкурентоспособной по сравнению с насадками, выпускаемыми фирмами Sulzer и Koch-Glitsch, а также с российской РЛВН. Следует отметить, что данная колонна рассматривается авторами как прототип промышленной установки детритизации водных потоков атомных электростанций.
НЕКОТОРЫЕ ПРИКЛАДНЫЕ АСПЕКТЫ ПРИМЕНЕНИЯ ВАКУУМНОЙ РЕКТИФИКАЦИИ ВОДЫ И ПЕРСПЕКТИВНЫЕ НАПРАВЛЕНИЯ СОВЕРШЕНСТВОВАНИЯ ПРОЦЕССА
Как было отмечено выше, малые значения однократного разделительного эффекта обусловливают необходимость реализации больших значений питающего и внутренних потоков, следствием чего являются большие энергетические затраты на испарение воды.
Одним из способов снижения энергозатрат при ректификации является использование схемы рекуперации тепла [1]. В работах [16, 41] предлагаются некоторые способы рекуперации тепла на основе теплового насоса компрессионного типа применительно к процессу ректификации воды под вакуумом. Одним из вариантов является схема с рекомпрессией пара, где в качестве рабочего вещества используется водяной пар из ректификационной колонны, участвующей в процессе изотопного разделения. Эта схема характеризуется наиболее высоким значением коэффициента преобразования энергии COP (coefficient of performance), но требует специализированного компрессионного оборудования для работы под вакуумом. Вторым вариантом является применение компрессионного теплового насоса с фреоновым циклом и одним или несколькими дополнительными водяными контурами. По данным [41], схема теплового насоса с фреоновым циклом реализована в составе опытной установки с ректификационной колонной диаметром 300 мм и высотой 3 м с электронагревом испарителя. В работах [16, 41] показано, что применение теплового насоса позволяет снизить расход электроэнергии на испарение до 2.7 раз.
Другим способом снижения затрат на энергообеспечение процесса является использование низкопотенциального греющего пара.
В последние годы возрос интерес к процессу ректификации воды применительно к решению задач изотопной очистки тяжелой и легкой воды. В ряде работ рассматривается возможность использования ректификации воды для детритизации легкой и тяжелой воды как самостоятельного процесса, так и в сочетании с другими методами, такими как химический изотопный обмен водорода с водой, газовая диффузия и др. [2, 14, 37, 42–45].
В работе [44] представлен расчет комплексной трехступенчатой установки детритизации легкой воды производительностью 10 кг/ч с обеспечением степени очистки и концентрирования трития 103 и 104 соответственно. Очистка от трития осуществляется на первой ступени методом вакуумной ректификации воды, а концентрирование радионуклида проводится методом изотопного обмена между водородом и водой на второй и третьей ступенях установки. Авторы отмечают, что энергетические затраты на стадии ректификации воды составляют более 97% от общего количества потребляемой энергии, при этом их стоимость может быть снижена за счет использования относительно дешевого пара низких параметров.
В работе [46] представлен расчет установки детритизации легкой воды методом вакуумной ректификации воды с использованием в качестве теплоносителя низкопотенциального пара атомной электростанции. Установка рассчитана на переработку 100 кг/ч тритийсодержащей легкой воды. Предложенная схема представляет собой каскад ректификационных колонн с исчерпыванием. Исчерпывающая часть установки состоит из четырех колонн с последовательно-параллельным соединением и предназначена для очистки воды от трития в 187 раз. Концентрирующую часть представляет двухступенчатый каскад с сокращением потоков, обеспечивающий концентрирование трития в 1000 раз [46]. В работах [14, 47] вакуумная ректификация воды рассматривается как метод депротизации и детритизации тяжеловодного теплоносителя.
Авторами [14] разработан алгоритм расчета каскада ректификационных установок, основанный на расчете бинарной смеси методом “от ступени к ступени” с учетом характеристик контактных устройств и предусматривающий вариант замены контактных устройств при переходе от одной колонны к другой. В рамках этого метода температура и величины потоков жидкости и пара принимаются постоянными в пределах одной теоретической ступени разделения, вследствие чего уравнения теплового баланса колонны не учитываются. Изотопные составы каждого из входящих и выходящих с теоретической ступени разделения потоков связаны соотношением материального баланса, а концентрации в потоках пара и жидкости, покидающих ступень разделения, находятся в термодинамическом равновесии. Моделирование каскада со ступенчатым сокращением потоков в итоге сводится к расчету одной колонны с промежуточными дефлегматорами и испарителями (рис. 6). При этом в качестве критерия разбиения колонны на ступени каскада может использоваться максимальная высота (если существенны ограничения по высоте) или максимальный перепад давления по высоте. Последний вариант является предпочтительным, когда наблюдается резкая зависимость коэффициента разделения от температуры.
Рис. 6.
Трехступенчатый каскад с сокращением потоков в концентрирующей и исчерпывающей части [14]: L – поток жидкости; G – поток пара; xi, yi – концентрация тяжелого изотопа в жидкости и паре соответственно, выходящих с i-й ступени разделения; F – поток питания; B – поток продукта.
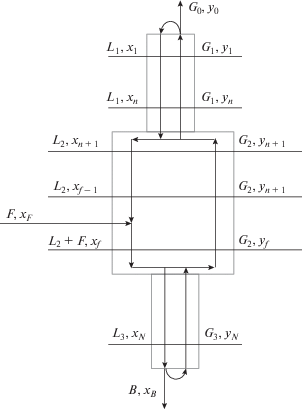
Алгоритм расчета включает в себя два цикла. В первом цикле проводится расчет каскада без сокращения потоков, при этом величина коэффициента кратности потоков σn, n – 1 принимается равной 1. Затем с использованием выбранного критерия проводится разбиение на отдельные колонны. На втором этапе вводятся значения коэффициентов кратности потока (рекомендуемые или произвольные), которые при переходе от одной колонны к другой в исчерпывающей части каскада σn, n – 1 > 1, а в концентрирующей – σn,n – 1 < 1. После этого проводится расчет каскада с сокращением потоков, сопровождающийся изменением формы каскада, в результате которого число колонн может увеличиться. Алгоритм предусматривает вариант замены контактных устройств при переходе от одной колонны к другой, а также изменение удельной нагрузки. Оптимизация проводится по критерию минимального объема разделительной части и осуществляется путем варьирования флегмового числа и коэффициентов кратности потока [14].
При верификации математической модели путем сравнения результатов расчета с экспериментальными данными, полученными на каскаде депротизации тяжелой воды, авторы [14] отмечают, что при выбранных значениях ВЭТС в тарельчатых и насадочных колоннах наблюдается хорошее согласие между теорией и экспериментом (различие не более 18%), что свидетельствует об адекватности выбранной модели расчета. В результате расчетной оптимизации каскада депротизации с заменой тарельчатых контактных устройств на регулярную насадку (РЛВН) была показана возможность уменьшения количества колонн с 5 до 4, при этом суммарный объем разделительной части установки снизился в 4.4 раза.
С использованием данного алгоритма в работе [47] был рассчитан ректификационный каскад тяжеловодного замедлителя реакторной установки с обеспечением вывода трития в количестве 220 кКи/год. В качестве критерия определения количества ступеней каскада использовалась максимальная высота. В результате расчета был получен пятиступенчатый каскад с сокращением потоков, первая ступень которого имеет исчерпывающую и концентрирующую части, а остальные колонны работают в режиме концентрирования. В первых четырех колоннах с диаметрами 500, 400, 310 и 200 мм используется РЛВН, а в последней, диаметром 200 мм – СПН с размером элемента 4 мм. Высота первых четырех колонн составляла около 20 м, а последней – 4.6 м. По данным расчета, суммарный объем разделительной части каскада детритизации тяжелой воды составил примерно 16 м3.
Несмотря на относительно небольшое потребление тяжелокислородной воды (около 2000 кг/год с концентрацией 18О 89–90%) [13], вследствие очень малого коэффициента разделения для ее получения требуется переработка больших исходных потоков воды. Ректификация воды была и остается в настоящее время основным методом получения ${\text{Н}}_{{\text{2}}}^{{{\text{18}}}}{\text{О}}{\text{.}}$ Производство тяжелокислородной воды путем ректификации было реализовано в СССР, США, Израиле, странах Европы и Китае [1, 10, 48]. Прототипом современных установок получения тяжелокислородной воды является каскад Достровского, который представлял собой соединенные между собой прямым и возвратным потоками два каскада – начального и конечного концентрирования – и позволял получать воду, обогащенную 18О и 17О. Первый каскад состоял из трех ступеней и включал в себя 20 и 6 концентрирующих колонн на первой и второй ступенях соответственно, а третья ступень представляла собой 2 концентрирующие и 1 исчерпывающую колонну. Второй каскад состоял из 11 колонн, связанных между собой в виде двух “ветвей”, и обеспечивал обогащение по 18О и 17О до 98 и 40% соответственно [1].
Учитывая большой объем разделительной аппаратуры, необходимой для реализации данного производства, ведутся работы по совершенствованию процесса. Так, например, в работе [49] предлагается вариант установки концентрирования кислорода-18 от природного уровня, предусматривающий сочетание вакуумной ректификации воды и химического изотопного обмена между углекислым газом и водой.
В работе [15] представлены результаты оптимизации работы установки кондиционирования тяжелокислородных отходов, образующихся в центрах позитронно-эмиссионной томографии. Показана возможность переработки воды с концентрацией 18О, равной 70%, в колонне высотой 6.7 м, заполненной СПН с размером элемента 1.5 или 3 см и работающей в периодическом режиме при давлении 0,015 МПа. Полученные в работе значения ВЭТС на уровне 1.2–1.3 см хорошо согласуются с данными работ [30, 32].
Среди подходов, направленных на совершенствование процесса вакуумной ректификации, весьма перспективным представляется использование для изотопного разделения метода солевой ректификации. По данным работ [50–53], введение в разделяемую изотопную систему разделяющего агента в виде растворимой в воде соли приводит к изменению равновесного состава пара и жидкости. Вследствие этого коэффициент разделения в системе водный солевой раствор–пар может отличаться от соответствующего значения для системы чистая вода–пар. Проведенные в работе [53] эксперименты по определению однократного разделительного эффекта в условиях фазового равновесия между водяным паром и солевыми растворами показали, что состав соли может оказывать как положительный, так и отрицательный эффект. В качестве одного из перспективных разделяющих агентов при разделении изотопов водорода использован карбамид, в присутствии которого наблюдалось наибольшее увеличение коэффициента разделения [53]. Однако для промышленной реализации противоточного процесса необходимо учитывать процесс частичной деструкции карбамида при температурах выше 60°С. В работе [54] описывается теоретическая модель, позволяющая определить вклад различных разделяющих агентов в величину коэффициента разделения изотопов кислорода.
ЗАКЛЮЧЕНИЕ
Проведенный в данной работе анализ литературных данных показывает широкое использование метода ректификации воды под вакуумом для разделения изотопов водорода и кислорода. Исследования по совершенствованию данного способа изотопного разделения и полученные положительные результаты свидетельствуют о возможности повышения эффективности и конкурентоспособности процесса.
Работа выполнена при финансовой поддержке Российского научного фонда (проект № 18-13-00475).
ОБОЗНАЧЕНИЯ
B | поток продукта, кмоль/ч |
F | поток питания, кмоль/ч |
G | поток пара, кмоль/ч |
L | поток жидкости, кмоль/ч |
Lуд | плотность орошения, кг/(ч м2) |
L* | предельная пропускная способность, кг/(ч м2) |
N | число теоретических ступеней разделения |
Р | давление, МПа |
Т | температура, K |
xi | концентрация тяжелого изотопа в жидкости, ат. д. |
yi | концентрация тяжелого изотопа в паре, ат. д. |
α | коэффициент разделения изотопов |
λ | мольное отношение потоков |
σn,n –1 | коэффициент кратности потоков |
ВЭТС | высота, эквивалентная теоретической ступени разделения, м |
Список литературы
Andreev B.M., Magomedbekov E.P., Raitman A.A., Rozenkevich M.B., Sakharovsky Yu.A., Khoroshilov A.V. Separation of Isotopes of Biogenic Elements in Two-Phase Systems. Amsterdam: Elsevier, 2007.
Андреев Б.М., Зельвенский Я.Д., Катальников С.Г. Тяжелые изотопы водорода в ядерной технике. М.: Энергоатомиздат, 1987.
Heavy Water Reactors: Status and Projected Development (Technical Reports Series No. 407). Vienna: International Atomic Energy Agency, 2002.
Производство тяжелой воды / Под ред. Зельвенского Я.Д. М.: Изд-во иностранной литературы, 1961.
Магомедбеков Э.П., Растунова И.Л., Розенкевич М.Б. Современные технологии разделения изотопов водорода // Вопр. ат. науки тех. Сер.: Материаловед. нов. матер. 2014. № 3(78). С. 70.
Малков М.П., Зельдович А.Г., Фрадков А.Б., Денисов И.Б. Выделение дейтерия из водорода методом глубокого охлаждения. М., 1960.
Niculescu A., Constantin T., Ana G., Draghia M. Dynamic simulation of a multicomponent distillation column for DT separation // Fusion Eng. Des. 2017. V. 124. P. 752.
Розен А.М. Производство тяжелой воды методом ректификации аммиака с тепловым насосом. Опыт пуска промышленной установки // Хим. пром-сть. 1995. № 4. С. 207.
Gligan M., Radot A., Dronca S., Bidian C. et al. Installatie experimentala pentru separarea izotopilor oxigenuluiprin distilarea oxidului de azot la temperaturi joase // Rev. Chim. (Bucharest, Rom.). 1997. V. 48. № 4. P. 335.
Полевой А.С. Состояние работ в области производства стабильных изотопов кислорода // VII Всероссийская (Международная) научная конференция “Физико-химические процессы при селекции атомов и молекул”. Сборник докладов (Звенигород, 2002). М.: ЦНИИатомнинформ, 2002. С. 280.
Зельвенский Я.Д. Выделение и концентрирование тяжелого изотопа кислорода криогенной ректификацией молекулярного кислорода // Хим. пром-сть. 1999. № 4. С. 236.
Kambe T., Kihara H., Hayashida S., Kawakami H. Development of oxygen-18 separation unit by oxygen distillation // Taiyo Nippon Sanso Tech. Rep. 2004. № 23. P. 20.
IMV Medical Information Division (2019) PET Imaging Market Summary Report 2019. https://imvinfo.com/product/pet-imaging-market-summary-report-2019. Cited 20 April 2019.
Magomedbekov E.P., Belkin D.Yu., Rastunova I.L., Sazonov A.B., Selivanenko I.L., Kulov N.N. Simulation and Optimization of the Deprotiation Cascade of a Heavy-Water Moderator // Theor. Found. Chem. Eng. 2017. V. 51. № 2. P. 133. [Магомедбеков Э.П., Белкин Д.Ю., Растунова И.Л., Сазонов А.Б., Селиваненко И.Л., Кулов Н.Н. Математическое моделирование и оптимизация каскада депротизации тяжеловодного замедлителя // Теор. осн. хим. технол. 2017. Т. 51. № 2. С. 131.]
Magomedbekov E.P., Selivanenko I.L., Kulov N.N., Veretennikova G.V. Conditioning heavy-oxygen water by rectification under vacuum // Theor. Found. Chem. Eng. 2019. V. 53. № 5. P. 719. [Магомедбеков Э.П., Селиваненко И.Л., Кулов Н.Н., Веретенникова Г.В. Кондиционирование тяжелокислородной воды методом ректификации под вакуумом // Теор. осн. хим. технол. 2019. Т. 53. № 5. С. 493.]
Селиваненко И.Л., Тимаков А.А. Устройство для получения воды с пониженным содержанием тяжелых молекул. Пат. 2612667 РФ. 2017.
Van Hook W.A. Vapor pressures of the isotopic waters and ices // J. Phys. Chem. 1968. V. 72. № 2. P. 1234.
Magomedbekov E.P., Rastunova I.L., Selivanenko I.L., Kulov N.N. Distribution of heavy hydrogen and oxygen isotopes in water distillation // Theor. Found. Chem. Eng. 2019. V. 53. № 2. P. 151. [Магомедбеков Э.П., Растунова И.Л., Селиваненко И.Л., Кулов Н.Н. Распределение тяжелых изотопов водорода и кислорода при ректификации воды // Теор. осн. хим. технол. 2019. Т. 53. № 2. С. 123.] https://doi.org/10.1134/S0040579519020118
Магомедбеков Э.П., Растунова И.Л., Селиваненко И.Л., Сарычев Г.А. Особенности распределения тяжелых изотопов водорода и кислорода при ректификации воды // Хим. пром-сть сегодня. 2018. № 4. С. 40.
Магомедбеков Э.П., Растунова И.Л., Селиваненко И.Л., Сарычев Г.А. Особенности распределения тяжелых изотопов водорода при детритизации легководных отходов методом ректификации воды // Вопр. ат. науки тех. Сер.: Материаловед. нов. матер. 2018. № 4. С. 62.
Музафарова А.Р., Емельянычева Е.А. Классификация, основные требования и конструктивные особенности современных насадочных контактных устройств // Вестн. технол. унив. 2016. Т. 19. № 2. С. 63.
Фарахов М.М., Фарахов Т.М., Лаптев А.Г. Гидравлические характеристики хаотичной насадки “Инжехим” для контакта газа и жидкости // Фундам. исслед. 2018. № 3. С. 24.
Магомедбеков Э.П., Селиваненко И.Л., Селиваненко О.И. Насыпная насадка для массообменных колонн. Пат. 2641920 РФ. 2018.
Магомедбеков Э.П., Селиваненко И.Л., Селиваненко О.И. Насыпная насадка для массообменных колонн. Пат. 2642572 РФ. 2018.
Каган А.М., Юдина Л.А., Пушнов А.С. Активная поверхность элементов нерегулярных тепло- и массообменных насадок // Теор. осн. хим. технол. 2012. Т. 46. № 2. С. 199.
Крылова А.Н., Башаров М.М. Сравнительные массообменногидравлические характеристики контактных устройств насадочных аппаратов // Изв. высш. учебн. завед. Пробл. энерг. 2010. № 11–12. С. 134.
Каган А.М., Пушнов А.С. Сравнительные характеристики промышленных нерегулярных насадок из полимерного материала для осуществления процессов абсорбции и ректификации // Хим. пром-сть сегодня. 2006. № 11. С. 30.
Фарахов Т.М., Фарахов М.М. Обобщенные гидравлические и массообменные характеристики новых контактных насадок колонных аппаратов // Хим. пром-сть сегодня. 2016. № 2. С. 50.
Андреев Б.М., Селиваненко И.Л. Ректификация воды как метод разделения изотопов водорода и кислорода // VII Всероссийская (Международная) научная конференция “Физико-химические процессы при селекции атомов и молекул”. Сборник докладов (Звенигород, 2002). М.: ЦНИИатомнинформ, 2002. С. 267.
Тхет М.А., Селиваненко И.Л. Эффективность разделения изотопов водорода ректификацией воды в колоннах с пленочным и затопленным режимах работы насадки // Хим. пром-сть сегодня. 2017. № 2. С. 3.
Разумовский Г.Н., Селиваненко И.Л. Масштабный фактор при разделении изотопов методом ректификации воды в колоннах диаметром до 300 мм // Усп. хим. хим. технол. 2017. Т. 31. № 10. С. 94.
Magomedbekov E.P., Belkin D.Yu., Selivanenko I.L., Rastunova I.L. Mass-transfer characteristics of spiral prismatic packings in isotope exchange columns of vacuum water distillation // Theor. Found. Chem. Eng. 2016. V. 50. № 5. P. 684. [Магомедбеков Э.П., Белкин Д.Ю., Селиваненко И.Л., Растунова И.Л. Массообменные характеристики спирально-призматической насадки в колоннах изотопного обмена при ректификации воды под вакуумом // Теор. осн. хим. технол. 2016. Т. 50. № 5. С. 502.]
Тхет М.А., Селиваненко О.И., Мосеев П.С., Меланьин Ф.В., Селиваненко И.Л. Влияние способа запуска колонны с регулярной насадкой из нержавеющей сетки на эффективность разделения модельной смеси протий-дейтерий методом ректификации воды // Усп. хим. хим. технол. 2014. Т. 28. № 9. С. 16.
Spiegel L., Meier W. Distillation columns with structured packings in the next decade // Chem. Eng. Res. Des. 2003. V. 81. P. 39.
Rejl F.J., Cmelíková T., Valenz L., Haidl J., Moucha T., Kracík T. Liquid phase axial mixing in distillation column packed with structured packing: Effect on column performance // Chem. Eng. Res. Des. 2019. V. 148. P. 129.
Valenz L., Rejl F.J., Linek V. Effect of Gas- and Liquid-Phase Axial Mixing on the Rate of Mass Transfer in a Pilot-Scale Distillation Column Packed with Mellapak 250Y // Ind. Eng. Chem. Res. 2011. V. 50. № 4. P. 2262.
Fukada S., Miho Y., Katayama K. Tritium separation performance of adsorption/exchange distillation tower packed with structured packing // Fusion Eng. Des. 2018. V. 133. P. 64.
Sumchenko A.S., Bukin A.N., Marunich S.A., Pak Y.S., Rozenkevich M.B., Selivanenko I.L., Aung T.M. Influence of packing columns starting modes on effectiveness of processes of water rectification and detritiation of gases by the method of phase isotopic exchange // Theor. Found. Chem. Eng. 2015. V. 49. № 3. P. 252. [Сумченко А.С., Букин А.Н., Марунич С.А., Пак Ю.С., Розенкевич М.Б., Селиваненко И.Л., Аунг Т.М. Влияние способа запуска насадочной колонны на эффективность процессов ректификации воды и детритизации газов методом фазового изотопного обмена // Теор. осн. хим. технол. 2015. Т. 49. № 3. С. 267.]
Селиваненко И.Л., Суворкин К.Д. Регулярная рулонная ленточно-винтовая насадка. Пат. 2424052 РФ. 2011.
Magomedbekov E.P., Belkin D.Y., Selivanenko I.L., Rastunova I.L. Characteristics of the mass transfer of structured rolled ribbon-screw packings in isotope exchange columns during vacuum water distillation // Theor. Found. Chem. Eng. 2016. V. 50. № 4. P. 398. [Магомедбеков Э.П., Белкин Д.Ю., Селиваненко И.Л., Растунова И.Л. Массообменные характеристики регулярной рулонной ленточно-винтовой насадки в колоннах изотопного обмена при ректификации воды под вакуумом // Теор. осн. хим. технол. 2016. Т. 50. № 4. С. 408.]
Разумовский Г.Н., Селиваненко И.Л. Применение компрессионного теплового насоса для рекуперации энергии в процессе ректификации воды под вакуумом // Хим. пром-сть сегодня. 2017. № 2. С. 17.
Egorov A.I., Tyunis V.M. Tritium-containing water decontamination by rectification methods // At. Energy (N.Y., NY, U. S.). 2002. V. 92. № 5. P. 386. [Егоров А.И., Тюнис В.М. Дезактивация вод, содержащих тритий, ректификационными методами // Ат. энерг. 2002. Т. 92. № 5. С. 355.]
Bonnett I., Busigin A., Shapiro A. Tritium Removal and Separation Technology Developments // Fusion Sci. Technol. 2008. V. 54. № 1. P. 209.
Kostylev A.I., Ledovskoi I.S., Magomedbekov E.P., Rozenkevich M.B., Sakharovsky Y.A., Selivanenko I.L, Sobolev A.I., Florya S.N. Technical and economic characteristics of processes for water detritiation by chemical isotope exchange in the water-hydrogen system // Radiochemistry. 2014. V. 56. № 5. P. 529. [Костылев А.И., Ледовской И.С., Магомедбеков Э.П., Розенкевич М.Б., Сахаровский Ю.А., Селиваненко И.Л., Соболев А.И., Флоря С.Н. Технико-экономические характеристики технологий очистки воды от трития методом химического изотопного обмена в системе вода-водород // Радиохимия. 2014. Т. 56. № 5. С. 450.]
Miho Y., Fukada S., Motomura T., Mizutani J., Hirano S., Arimoto M., Takeuchi T. Tritium Water Distillation Assisted with Adsorption and Isotopic Exchange // Fusion Sci and Tech. 2017. № 3. V. 71. P. 326.
Магомедбеков Э.П., Растунова И.Л. Обращение с тритийсодержащими водными отходами // Хим. пром-сть сегодня. 2019. № 3. С. 62.
Magomedbekov E.P., Belkin D.Y., Rastunova I.L., Sazonov A.B., Selivanenko I.L., Kulov N.N. Water distillation as a method of detritiation of heavy-water moderator // Theor. Found. Chem. Eng. 2017. V. 51. № 4. P. 384. [Магомедбеков Э.П., Белкин Д.Ю., Растунова И.Л., Сазонов А.Б., Селиваненко И.Л., Кулов Н.Н. Ректификация воды как метод детритизации тяжеловодного замедлителя // Теор. осн. хим. технол. 2017. Т. 51. № 4. С. 376.]
Gao Y., Xu Zh., Wu K., Wang X., Yu Zh., Fei W. The steady-state and dynamic simulation of cascade distillation system for the production of oxygen-18 isotope from water // Chin. J. Chem. Eng. 2016. V. 24. № 8. P. 979.
Костылев А.И., Мазгунова В.А., Покровский Ю.Г., Аляпышев М.Ю. Способ получения воды, обогащенной по кислороду-18, и установка для ее получения. Пат. 2632697 РФ. 2017.
Jakli G., Van Hook W.A. Isotope Effects in Aqueous Systems. 12. Thermodynamics of Urea-h4/H2O and Urea-d4/D2O Solutions // J. Phys. Chem. 1981. V. 85. № 23. P. 3480.
O’Neil J.R., Truesdell A.H. Oxygen isotope fractionation studies of solute-water interactions // Stable Isotope Geochemistry: A Tribute to Samuel Epstein (The Geochemical Society. Special Publication No. 3) / Eds. Taylor H.P.Jr., O’Neil J.R., Kaplan I.R. Washington, DC: Geochemical Society, 1991. P. 17.
Кулов Н.Н., Полковниченко А.В., Лупачев Е.В., Растунова И.Л., Магомедбеков Э.П. Фракционирование изотопов воды D/H и 18О/16О в насадочной ректификационной колонне // Теор. осн. хим. технол. 2020. Т. 54. № 3. С. 267.
Kulov N.N., Polkovnichenko A.V., Lupachev E.V., Voshkin A.A., Magomedbekov E.P. Distribution of hydrogen isotopes between phases at vapor–liquid equilibrium in aqueous salt solutions // Theor. Found. Chem. Eng. 2020. V. 54. № 1. P. 132. [Кулов Н.Н., Полковниченко А.В., Лупачев Е.В., Вошкин А.А., Магомедбеков Э.П. Распределение изотопов водорода между фазами при парожидкостном равновесии водных солевых растворов // Теор. осн. хим. технол. 2020. Т. 54. № 1. С. 3.]
Покальчук В.С., Магомедбеков Э.П., Растунова И.Л., Чеботов А.Ю., Кулов Н.Н. Оценка величины коэффициента разделения изотопов кислорода в водных солевых растворах // Теор. осн. хим. технол. 2020. Т. 54. № 6. С. 1.
Дополнительные материалы отсутствуют.
Инструменты
Теоретические основы химической технологии