Теоретические основы химической технологии, 2021, T. 55, № 2, стр. 251-260
Разложение ацетилена на водород и углерод: опыты с ДВС и эксперименты с проточным реактором
М. С. Власкин a, В. М. Зайченко a, П. В. Белов a, b, *, А. В. Григоренко a, **, А. И. Курбатова b, А. В. Еремин a, В. Е. Фортов a
a Объединенный институт высоких температур РАН
Москва, Россия
b Российский университет дружбы народов
Москва, Россия
* E-mail: ecolog.pavel@gmail.com
** E-mail: presley1@mail.ru
Поступила в редакцию 01.10.2020
После доработки 25.11.2020
Принята к публикации 25.11.2020
Аннотация
Представлены результаты исследования процесса термического разложения ацетилена до водорода и ацетиленовой сажи. Были проведены опыты по разложению ацетилена в измененном для этого двигателе внутреннего сгорания (ДВС), а также эксперименты по разложению ацетилена при постоянной температуре (1000 ± 10°С) в проточном реакторе с внешним подводом тепла. Разложение ацетилена проводилось без добавки окислителя. В опытах с ДВС была показана принципиальная возможность работы двигателя на ацетилене и определен состав газообразных продуктов реакции. В экспериментах с проточным реактором определено влияние давления в реакторе, расхода ацетилена и наличия вольфрамовой сетки в рабочей зоне реактора на степень разложения ацетилена и состав газообразных продуктов реакции. В работе также проанализированы некоторые свойства сажи: удельная площадь поверхности, средний размер частиц, насыпная плотность и теплота сгорания.
ВВЕДЕНИЕ
В большинстве технологических процессов производства полезной энергии лежит процесс горения углеводородов, в результате которого образуются вода и диоксид углерода в соответствии с уравнением реакции
(1)
${{{\text{C}}}_{m}}{{{\text{H}}}_{n}} + \,\,\left( {m + {n \mathord{\left/ {\vphantom {n 4}} \right. \kern-0em} 4}} \right){{{\text{O}}}_{2}} = m{\text{C}}{{{\text{O}}}_{2}} + \left( {{n \mathord{\left/ {\vphantom {n 2}} \right. \kern-0em} 2}} \right){{{\text{Н}}}_{{\text{2}}}}{\text{O}} + {\text{Q}}.$В современном мире наблюдается тенденция к росту потребления энергии. При этом нефть, уголь и природный газ остаются наиболее потребляемыми первичными источниками энергии на сегодняшний день [1]. В связи с этим, непрерывно увеличиваются выбросы парниковых газов, в частности, диоксида углерода. В то же время наблюдаются попытки внедрения энергоустановок возобновляемой энергетики, которые преобразуют энергию природных процессов и не образуют при этом парниковых газов; однако, стоимость энергии, получаемой таким способом, остается пока выше, чем традиционные процессы сгорания углеводородов [2].
Поэтому, актуальной задачей является создание таких циклов, которые основываются на использовании традиционного (углеводородного) топлива, но при этом предусматривают значительное сокращение выбросов парниковых газов в атмосферу. Передовые компании и научные центры в области энергетики разрабатывают различные способы получения энергии без образования оксидов углерода [3].
Ацетилен является уникальным углеводородным соединением. Крайне примечательным является его экзотермичность. При пиролизе ацетилена образуется графитизированная сажа, молекулярный водород и выделяется значительное количество энергии [4]:
(2)
${{{\text{С}}}_{{\text{2}}}}{{{\text{Н}}}_{2}} \to 2С\left( {{\text{графит}}} \right) + {{{\text{Н}}}_{2}}\left( { + 227{\text{ }}{{{\text{кДж}}} \mathord{\left/ {\vphantom {{{\text{кДж}}} {{\text{моль}}}}} \right. \kern-0em} {{\text{моль}}}}} \right).$Ацетилен может быть получен как из природного газа [5, 6], так и с использованием угля. Возможность получения ацетилена путем гидролиза карбида кальция, который в свою очередь может быть получен путем прокаливания угля и оксида кальция (или карбоната кальция), является актуальной в свете постепенного сокращения потребления угля в традиционной для него области – энергетике. В процессе получения карбида кальция происходит избавление от угольной серы и зольной части, переход данных примесей в шлак [7].
Реакция получения ацетилена из карбида кальция описывается следующим уравнением:
(3)
${\text{Са}}{{{\text{С}}}_{2}} + 2{{{\text{Н}}}_{{\text{2}}}}{\text{О}} \to {\text{Са}}{{\left( {{\text{ОН}}} \right)}_{2}} + {{{\text{С}}}_{{\text{2}}}}{{{\text{Н}}}_{2}}.$В карбиде кальция содержится 21.23 кДж/кг химической энергии, большая часть которой при гидролизе переходит в ацетилен. Из 1 кг карбида кальция в соответствии с уравнением реакции образуется около 0.4 кг ацетилена.
Саморазложение ацетилена может происходить как в режиме “горения” со скоростями от 10 до 50 м/с, так и в режиме детонации со скоростями до 2000 м/с. Недавно было проведено исследование процесса формирования детонационной волны конденсации при саморазложении ацетилена [8–10]. Эксперименты проводились в ударной трубе диаметром 70 мм. Длина секции высокого давления составляла 3.5 м, секции низкого давления – 4.5 м. Изучалось распространение отраженной ударной волны в смесях, содержащих 20–30% C2H2 в аргоне при начальных температурах и давлении, варьируемых в диапазоне от 1300 до 2900 К и от 7 до 30 атм. Экспериментально наблюдалось формирование детонационной волны конденсации при термическом разложении ацетилена, инициированном ударной волной. Устойчивую волну детонации в смеси 20% С2Н2 + 80% Ar удалось получить при начальном давлении за ударной волной не менее 30 атм. Показано, что период индукции роста частиц не сопровождается заметным тепловыделением. Последующие стадии конденсации, характеризующиеся существенным выделением энергии, протекают в режиме “взрывной конденсации”. Анализ полученных данных показал, что лимитирующей стадией процесса, определяющей возможность формирования детонационной волны конденсации в ацетилене, являются реакции роста больших полиуглеводородных молекул, предшествующие образованию конденсированных углеродных частиц. Увеличение давления ведет к резкому сужению зоны индукции и переходу всего процесса в детонационную волну конденсации [8]. Установлено, что основное тепловыделение, определяющее положительный интегральный энергетический баланс детонационного пиролиза ацетилена, происходит на стадии образования и роста конденсированных углеродных наночастиц [10].
Процесс разложения ацетилена на углерод и водород может быть использован, как для выработки “экологически чистой” полезной энергии, так и для производства таких востребованных продуктов как водород и ацетиленовая сажа. Водород может быть использован как экологически чистое топливо, а ацетиленовая сажа, благодаря своим уникальным свойствам, незаменима в различных отраслях промышленности [11].
На настоящий момент не разработан эффективный непрерывный цикл пиролиза ацетилена. Разложение происходит либо в непрерывно-периодическом режиме (взрыв газа в сосуде (бомбе)) постоянного объема, с последующим заполнением сосуда ацетиленом, его взрывом и выгрузкой продуктов (очисткой рабочего объема бомбы) [12, 13], либо в установке с импульсным газодетонационным аппаратом, в которой ацетилен разлагается в среде с добавкой кислорода с коэффициентом избытка 0.4–0.8 [14, 15].
Исходя из анализа литературных данных, исследования процесса термического разложения ацетилена в бескислородной среде в непрерывном режиме крайне ограничены. Поэтому в данной работе были предприняты попытки организовать процесс термического разложения ацетилена в бескислородной среде в непрерывном режиме: первая часть работы заключалась в апробации использования ацетилена в качестве топлива для ДВС; во второй части работы, была создана экспериментальная установка для исследования термического разложения ацетилена до водорода и ацетиленовой сажи в непрерывном проточном режиме в реакторе с внешним подводом тепла без добавки окислителя. Задачами настоящего исследования являлись изучение степени разложения ацетилена и состава газообразных продуктов реакции в зависимости от режимов (параметров) работы установок (состава газа, давления, расхода ацетилена и наличия вольфрамовой сетки в рабочей зоне проточного реактора).
ЭКСПЕРИМЕНТАЛЬНАЯ ЧАСТЬ
Реактивы и материалы. При проведении экспериментов с ДВС использовались следующие реактивы и материалы:
• Растворенный ацетилен марки “А” (объемная доля ацетилена не менее 99.5%);
• ДВС “Д21” Владимирского тракторного завода, переработанный для работы на газовом топливе (диаметр поршня данного двигателя 105 мм, ход поршня 120 мм при степени сжатия равной 9);
• Высокотемпературный датчик давления “Метроникс-ДИ-В” для индицирования изменения давления в процессе реакции разложения ацетилена, поступающего в цилиндр;
• Штатная для дизельного варианта пусковая свеча накаливания (температура до 1100°С), которая служила дополнительным источником тепла;
• Датчик давления с линейной характеристикой 1В-2.0 МПа, датчик момента зажигания и двухканальный цифровой осциллограф DS-1052E.
При проведении экспериментов с проточным реактором с внешним подводом тепла использовались следующие реактивы и материалы:
• Растворенный ацетилен марки “А” (объемная доля ацетилена не менее 99.5%);
• Проточный реактор, изготовленный из нержавеющей стали (12Х18Н10Т) (его внутренний объем 600 см3 (длина реактора 20 см));
• Пропановая горелка Vorel;
• Термопара типа хромель–алюмель;
• Счетчика газа ВК G4, с помощью которого измерялся расход газа;
• Вольфрамовая проволока марки ВА (ГОСТ 18903-73) толщиной 0.3 мм.
Методика проведения экспериментов с ДВС. Для проведения экспериментов с ацетиленом в конструкцию двигателя внесены следующие изменения.
1. Удалены коромысла и штанги механизма газораспределения в одном из двух цилиндров, а именно, во втором; закрытые клапаны этого цилиндра обеспечивали поступление ацетилена только в исследуемый первый цилиндр.
2. В головку цилиндра в свечное отверстие, через специально изготовленную проставку устанавливался высокотемпературный датчик давления “Метроникс-ДИ-В” для индицирования изменения давления в процессе реакции разложения ацетилена, поступающего в цилиндр. В головке цилиндров также была установлена штатная для дизельного варианта пусковая свеча накаливания (температура до 1100°С), которая служила дополнительным источником тепла.
3. Во избежание получения взрывоопасной смеси “ацетилен–воздух” были установлены штуцеры с подводом через них азота для продувки перед началом каждого опыта впускного тракта, камеры сгорания и картера двигателя.
4. Впускной коллектор оснащался системой подачи ацетилена (или газовой смеси “аргон–ацетилен”), включающей соединительные рукава, разделительный кран, эластичный газгольдер объемом 0.05 м3, из которого осуществлялась подача испытуемых газов в двигатель.
Для регистрации индикаторных диаграмм давления в цилиндре ДВС были использованы: датчик давления с линейной характеристикой 1В-2.0 МПа, датчик момента зажигания и двухканальный цифровой осциллограф DS-1052E. Для регистрации давления газа, подаваемого в газгольдер и во впускной коллектор двигателя, использовались стрелочные образцовые манометры. Частота вращения коленчатого вала двигателя определялась расчетом по осциллограммам. Отбор проб продуктов разложения ацетилена из выпускной магистрали двигателя осуществлялся в стеклянные вакуумированные колбы. В процессе подготовки экспериментов проведены прокрутки двигателя стартером при подаче азота в цилиндр для уточнения величины давления сжатия и правильности установки датчика верхней мертвой точки.
Эксперименты проводились при концентрациях ацетилена 20 и 50% в смеси с аргоном и при 100% содержании ацетилена. Для обеспечения безопасности перед каждым экспериментом производилась продувка азотом всех полостей двигателя, в которые подавался ацетилен; продувка картера ДВС азотом осуществлялась постоянно.
Последовательность действий при каждом опыте была следующей:
1. Наддув ресивера ацетиленом до 0.3 атм.
2. Разогрев свечи перед прокруткой 8–10 с.
3. Прокрутка стартером при включенной свече в течение 3–5 с с одновременной подачей ацетилена в двигатель.
4. Регистрация полученных результатов.
Общий вид установки с ДВС приведен на рис. 1.
Методика проведения экспериментов с проточным реактором с внешним подводом тепла. Схема экспериментальной установки с непрерывной подачей ацетилена и его термического разложения до водорода и ацетиленовой сажи в проточном реакторе представлена на рис. 2.
Рис. 2.
Схема экспериментальной установки: 1 – баллон с ацетиленом, 2 – редуктор, 3 – пламегаситель, 4 – вентиль тонкой регулировки, 5 – проточный реактор, 6 – пропановая горелка, 7 – термопара, 8 – тканевый фильтр, 9 – манометр, 10 – вентиль тонкой регулировки, 11 – барботер, 12 – счетчик газа, 13 – резиновая камера.
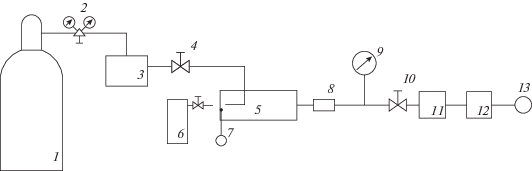
Основным элементом установки является проточный реактор (5). Реактор изготовлен из нержавеющей стали (12Х18Н10Т), его внутренний объем 600 см3 (длина реактора 20 см). В реактор ацетилен подается из баллона (1) через редуктор (2). Чтобы не допустить обратного удара пламени в баллон с ацетиленом (1) использовался пламегаситель (3), заполненный водой. Ацетилен подается внутри реактора на нагреваемую с помощью газовой горелки (6) торцевую поверхность. Расстояние между нагреваемой внутренней поверхностью реактора и концом подающей ацетилен трубки составляет 1 мм. Для нагрева реактора с внешней стороны используется пропановая горелка Vorel (6). С внутренней стороны температура стенки нагреваемой поверхности измеряется с помощью термопары типа хромель–алюмель (7). Выход газообразных продуктов осуществляется с противоположного нагреваемой поверхности торца реактора. Для отделения твердых продуктов реакции (сажи) внутри реактора используется тканевый фильтр (8). Давление в реакторе задается с помощью вентиля (4, 10) и измеряется с помощью манометра (9). Расход газа измеряется с помощью счетчика газа ВК G4 (12). Для отделения тонкодисперсных продуктов реакции мокрым способом использовался барботер (11), заполненный дистиллированной водой. Образующийся в результате разложения ацетилена газ закачивался в резиновую камеру (13) и передавался на количественный и качественный газохроматографический анализ.
Перед нагревом реактор продувался ацетиленом. С помощью редуктора и вентиля задавался определенный расход газа (100 или 250 см3/мин), а также устанавливалось определенное давление внутри реактора (абсолютные 1, 1.5 или 2 бар). Затем запускался нагрев реактора. Реактор разогревался до температуры 1000 ± 10°С. Конверсию ацетилена на водород и углерод наблюдали по изменению пламени на свече (свеча поджигалась на выходе из трубопровода до подключения резиновой камеры). В результате конверсии пламя переставало коптить. Спустя 5 мин после того, как пламя переставало коптить, следовал забор газа для газохроматографического исследования. Забор газа осуществлялся в течение 1 мин в специальную резиновую камеру.
При давлении близком к атмосферному (1 бар) были проведены эксперименты с расходом ацетилена 100 и 250 см3/мин. С расходом ацетилена 100 см3/мин были проведены эксперименты при абсолютных давлениях внутри реактора 1.5 и 2 бар. При давлении 1 бар и расходом ацетилена 100 см3/мин был проведен эксперимент, в котором во внутреннее пространство реактора была помещена сетка из вольфрамовой проволоки марки ВА (ГОСТ 18903-73) толщиной 0.3 мм. Вольфрамовая сетка была использована для увеличения активной горячей поверхности внутри реактора с целью достижения большей степени конверсии ацетилена.
Методы исследования продуктов термического разложения ацетилена. Химический состав получившегося в результате термического разложения ацетилена газа изучался на газовом хроматографе Хромос ГХ-1000. Общий принцип работы одной из аналитических схем при анализе компонентов модельной газовой смеси – Н2, O2/N2 (воздух), CO, СО2, углеводороды С1–C5 (парафино-олефинового класса с изомерами). Хроматографический комплекс включает три детектора, комплект многопортовых автоматических кранов, 6-ть хроматографических колонок; весь анализ проходит в изотермическом режиме при 80°С в течение 10 мин. При однократном запуске метода происходило программируемое переключение кранов, и начиналась запись по всем детекторам, по ходу анализа осуществлялось переключение и отдувка предколонок.
Удельная поверхность получившейся ацетиленовой сажи изучалась методом низкотемпературной адсорбции азота на приборе Сорби 4.1. Изотерма адсорбции азота строилась по четырем точкам. Удельная поверхность из изотермы адсорбции вычислялась с помощью уравнения Брунауэра–Эммета–Теллера (БЭТ) [16]. Рабочий объем ампулы, куда загружались образцы, составлял 2.5 см3. Относительная погрешность измерений удельной поверхности составляла 6%.
Удельная теплота сгорания образцов ацетиленовой сажи определялась с помощью калориметра IKA C6000. Для калибровки прибора использовалась бензойная кислота.
Исследования образцов сажи были выполнены с помощью сканирующего электронного микроскопа Nova NanoSem. Образцы были прикреплены к микроскопу с помощью электропроводящей ленты. Образцы не были покрыты проводящим покрытием во избежание возможного экранирования наноразмерных объектов. Сканирование проводилось с использованием вторичных электронов с ускоряющими напряжениями 2 и 3 кВ. Чтобы смягчить неизбежную зарядку образцов электронным зондом, РЭМ-изображения были получены методом многократного сканирования с использованием режима “коррекции дрейфа”.
РЕЗУЛЬТАТЫ И ИХ ОБСУЖДЕНИЕ
Результаты опытов с ДВС. В экспериментах со смесями ацетилен-аргон не выявлено сколь-нибудь заметного выделения энергии и повышения давления в области верхней мертвой точки на индикаторной диаграмме (рис. 3); в этом случае двигатель сразу останавливался после выключения стартера.
Рис. 3.
Индикаторная диаграмма прокрутки двигателя на смеси Ar (50%)–С2Н2 (50%), Рz = 0.9 МПа. Ось Х – время, цена 1 большого деления – 0.5 с. Ось Y – напряжение на датчике давления в цилиндре, цена 1 большого деления – 0.5 мВ, калибровка датчика давления – 1 мВ = 2.05 МПа. Данные в правом верхнем углу (1/Х1-Х2, Х1-Х2, Y1-Y2) – соответствующие величины времени и напряжения на датчике давления в цилиндре в характерных точках индикаторной диаграммы.
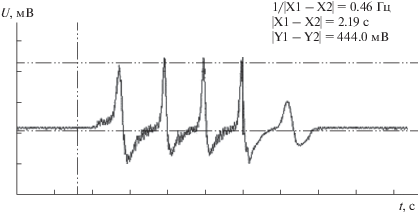
В экспериментах с подачей чистого ацетилена без свечи накаливания выделения энергии и повышения давления также не зафиксировано. В этих же условиях включение свечи накаливания приводило к выделению энергии в результате реакции разложения ацетилена. Двигатель продолжал работать после выключения стартера, увеличивая частоту вращения коленчатого вала (рис. 4), при этом наблюдался сильнейший выброс черного дыма (сажи) из выпускной системы двигателя. Однако, проработав 10–12 с на повышенных оборотах холостого хода, двигатель останавливался. Дальнейшие попытки запуска приводили к отдельным вспышкам без поддержания вращения коленчатого вала. Последующая разборка двигателя показала, что камера сгорания в поршне полностью заполнена сажей, ее оседание на фасках клапанов и седел не обеспечивало герметичной посадки клапана на седло.
Рис. 4.
Индикаторная диаграмма давления в цилиндре двигателя при его работе на чистом ацетилене: Рz = 4.1 МПа. Ось Х – время, цена 1 большого деления – 0.5 с. Ось Y – напряжение на датчике давления в цилиндре, цена 1 большого деления – 0.5 мВ, калибровка датчика давления – 1 мВ = 2.05 МПа. Данные в правом верхнем углу (1/Х1-Х2, Х1-Х2, Y1-Y2) – соответствующие величины времени и напряжения на датчике давления в цилиндре в характерных точках индикаторной диаграммы.
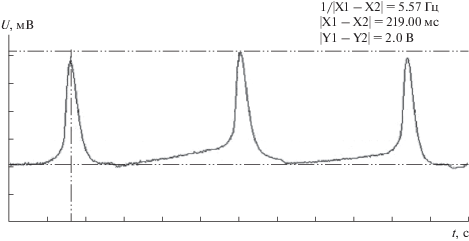
Вторая серия опытов проводилась с целью отбора газовых проб из выпускной трубы во время работы двигателя на ацетилене. Пробоотборник газа был расположен на расстоянии 1 м от головки цилиндра, а выпускная труба имела общую длину 5 м (для предотвращения заброса воздуха в отбираемые пробы). Выполнено 5 запусков двигателя на ацетилене с отбором проб газа.
В ходе определения состава продуктов реакции было установлено, что из постоянных газов в смеси присутствуют: водород (87.1 мол. %), небольшое количество кислорода (1.6 мол. %) и азота (15.7 мол. %), метан (3.46 мол. %), а также СО (2.61 мол. %). Наличие СО свидетельствует о присутствии воздуха в камере газового двигателя во время разложения ацетилена. Наличие кислорода и азота в соотношении, отличном от соотношения этих газов в воздухе, может быть результатом совместного действия двух причин: избыток азота – от продувочного азота, подаваемого в двигатель до и во время опыта, воздух – подсос во время отбора пробы в ходе опыта. Среди углеводородов в газовой фазе основными компонентами являются: остаточный ацетилен, метан, а также этилен. Наряду с ними обнаружены: этан, пропилен, гомологи ацетилена (метилацетилен, винилацетилен, диацетилен, диметилацетилен, этилацетилен), аллен, бутены, бутадиен, бензол и толуол. Результаты анализа газовой фазы (исключая азот и кислород) представлены в табл. 1. Остаточное содержание ацетилена около 22.3 мас. %. Следовательно, степень превращения ацетилена при разложении его в газовом двигателе в опыте составила около 77.7%.
Таблица 1.
Результаты анализа газовой фазы продуктов разложения ацетилена в ДВС
Вещество | Мол. % | Вещество | Мас. % |
---|---|---|---|
Н2 | 87.1 | Н2 | 37.4 |
С2Н2 | 4.03 | С2Н2 | 22.3 |
СН4 | 3.46 | СО | 15.5 |
СО | 2.61 | СН4 | 11.8 |
Н2О | 1.874 | Н2О | 7.179 |
С2Н4 | 0.854 | С2Н4 | 5.09 |
СО2 | 0.0362 | СО2 | 0.338 |
С2Н6 | 0.0295 | С2Н6 | 0.189 |
Остальные углеводороды | 0.01 | Остальные углеводороды | 0.2 |
∑ | 100.00 | ∑ | 100.00 |
Результаты экспериментов с проточным реактором с внешним подводом тепла. В результате газохроматографического анализа газообразных продуктов разложения ацетилена в проточном реакторе с внешним подводом тепла было установлено, что основным газообразным продуктом термического разложения ацетилена является водород. Остальную часть газа, который был получен в результате термического разложения ацетилена, составляют такие углеводороды, как метан, этан, этен, пропан, бутан, бутен, пентан, а также ацетилен.
В табл. 2 представлена концентрация водорода в газообразных продуктах термического разложения ацетилена, которая определена с помощью газохроматографического анализа. С увеличением расхода ацетилена с 100 см3/мин (табл. 2, образец А) до 250 см3/мин (табл. 2, образец В) концентрация водорода в продуктах реакции уменьшилась почти в 4 раза. Меньшая степень конверсии ацетилена при увеличении расхода говорит о том, что газ не успевает нагреваться до необходимой до полного разложения ацетилена температуры.
Таблица 2.
Концентрация водорода (Свод, %) в газообразном продукте термического разложения ацетилена
Образец | A | B | C | D | E |
---|---|---|---|---|---|
Концентрация водорода, % | 44.80 | 10.50 | 62.10 | 68.70 | 60.30 |
С увеличением давления внутри реактора концентрация водорода увеличивается (табл. 2, образцы С и D). С одной стороны, это объясняется тем, что при большем давлении уменьшаются линейные скорости потока внутри реактора, что способствует более полному прогреву газа. С другой стороны, как это известно, с увеличением давления скорость термического разложения ацетилена увеличивается [17].
Росту концентрации водорода также способствует наличие сетки внутри реактора. При одинаковом расходе и давлении (100 см3/мин и 1 бар) наличие сетки внутри реактора привело к увеличению концентрации водорода с 44.80% (табл. 2, образец А) до 60.30% (табл. 2, образец Е). Это может быть объяснено тем, что наличие сетки обеспечивает более полный прогрев газа, а также увеличивает поверхность нагретого металла, на котором и происходит разложение ацетилена.
Образец А – расход 100 см3/мин, давление 1 бар; образец В – расход 250 см3/мин, давление 1 бар; образец С – расход 100 см3/мин, давление 1.5 бар; образец D – расход 100 см3/мин, давление 2 бар; образец E – расход 100 см3/мин, давление 1 бар, наличие вольфрамовой сетки.
В табл. 3 представлена концентрация газообразных углеводородов в продукте термического разложения ацетилена за вычетом водорода. При большом расходе ацетилена (250 см3/мин) основным газом, кроме водорода, который выходит из реактора, является ацетилен. Это говорит о том, что основным каналом термического разложения ацетилена является реакция с образованием водорода и углерода. Кроме того, при большем расходе газа продукты термического разложения быстрее остывают, что способствует предотвращению обратных реакций, основанных на взаимодействии углерода с водородом и другими газообразными углеводородами.
Таблица 3.
Концентрация газообразных углеводородов (Cугл, %) в продукте термического разложения ацетилена (за вычетом водорода)
Газ А | Cугл, % | Газ В | Cугл, % | Газ C | Cугл, % | Газ D | Cугл, % | Газ E | Cугл, % |
---|---|---|---|---|---|---|---|---|---|
Ацетилен | 71.7 | Ацетилен | 98.2 | Ацетилен | 76.9 | Ацетилен | 82.2 | Ацетилен | 88.1 |
Этен | 16 | Этен | 1.1 | Метан | 10.8 | Метан | 12.8 | Метан | 9 |
Метан | 10.8 | Метан | 0.6 | Этен | 9.3 | Этан | 2.3 | Этен | 2.2 |
Этан | 1 | Этан | 0.04 | Этан | 1.9 | Этен | 2.0 | Этан | 0.4 |
Остальные углеводороды | 0.5 | Остальные углеводороды | 0.1 | Остальные углеводороды | 1.1 | Остальные углеводороды | 0.7 | Остальные углеводороды | 0.3 |
∑ | 100 | ∑ | 100 | ∑ | 100 | ∑ | 100 | ∑ | 100 |
Образец А (газ А) – расход 100 см3/мин, давление 1 бар; образец В (газ В) – расход 250 см3/мин, давление 1 бар; образец С (газ С) – расход 100 см3/мин, давление 1.5 бар; образец D (газ D) – расход 100 см3/мин, давление 2 бар; образец E (газ E) – расход 100 см3/мин, давление 1 бар, наличие вольфрамовой сетки. В категорию “остальные углеводороды” входят: пропан, пропилен, изобутилен, бутен-1, н-пентан, н-бутан, 1,3-бутадиен.
С увеличением давления в реакторе в продуктах реакции растет концентрация таких газов, как метан и этан. Присутствие данных газов в продуктах может быть связано с двумя обстоятельствами: гетерогенным взаимодействием ацетилена при высокой температуре с образующейся дисперсной фазой, а также вторичными реакциями взаимодействия образовавшихся водорода и сажи при более низких температурах в процессе остывания продуктов реакции [12].
Насыпная плотность сажи составила около 0.03 г/мл. Теплота сгорания сажи составила 32.791 МДж/кг, что соответствует теплоте сгорания чистого углерода. Удельная площадь поверхности сажи составила 74 м2/г. На рис. 5 представлены типичные РЭМ-изображения образца сажи, полученные сканирующим электронным микроскопом с различными разрешениями. Из снимков видно, что образец сажи имеет достаточно развитую поверхность и продукт представляет собой агломерированные между собой частицы средний размер которых составляет порядка 36 нм.
Рис. 5.
РЭМ-изображения образца сажи, полученные сканирующим электронным микроскопом с различными разрешениями: (а) – с разрешением 3 мкм; (б) – с разрешением 500 нм.
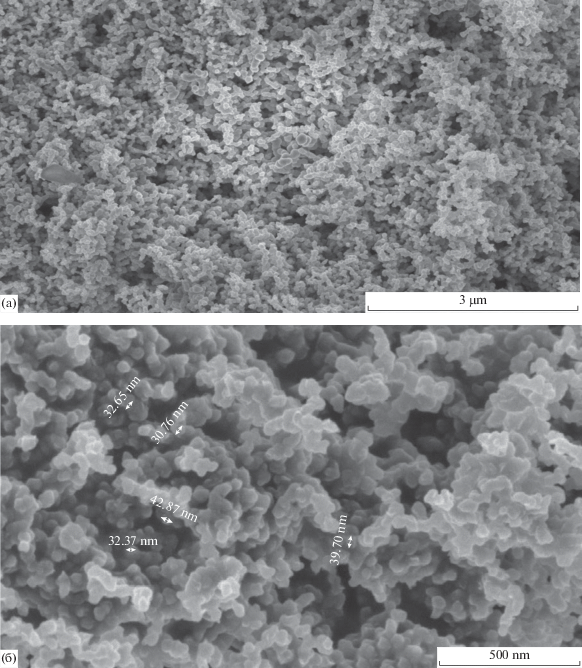
Сравнение сажи, полученной в данной работе, с сажей профильных мировых производителей показывает, что она обладает схожими свойствами. В частности, сажа, производимая компанией Denka, характеризуется средним размером частиц d = 35 нм, удельной поверхностью S = 68 м2/г и насыпной плотностью ρ = 0.04 г/мл [18].
ЗАКЛЮЧЕНИЕ
В ходе проведeнных экспериментов была показана принципиальная возможность работы ДВС на ацетилене. При этом использование ацетилена “в виде топлива” имеет ряд принципиальных отличий от других видов топлив. Энергия, необходимая для работы двигателя, выделяется не при сжигании топлива, а при его термическом разложении, которое может быть инициировано за счет повышения давления в объеме, содержащем ацетилен, либо местным нагревом с использованием, например, электрического разряда в автомобильной свече зажигания. В данном случае, для работы двигателя, используется энергия, которая выделяется при термическом разложении ацетилена. Традиционная схема работы двигателя заключается в сжигании топлива в кислородной среде. Основной проблемой работы ДВС на ацетилене является образование сажи, отложения которой в поршневой группе двигателя приводят к его остановке. В ходе экспериментов показано, что работа двигателя на ацетилене может быть осуществлена в течение весьма ограниченного промежутка времени. В принципе, можно предложить определенную модернизацию ДВС, при реализации которой получаемый технических углерод будет удаляться из цилиндров двигателя, например, при периодической продувке цилиндров двигателя в замкнутом контуре нейтрального газа. Однако, реализация данного решения требует существенной доработки двигателя, вернее разработки новой конструкции ДВС.
Недостатки поршневой системы могут быть устранены при переходе на проточный реактор с непрерывной подачей топлива (ацетилена) и выводом продуктов реакции (потока водорода и сажи) из реактора. В данной работе прототип такого устройства был создан и испытан. В экспериментах с проточным реактором термического разложения ацетилена с внешним подводом тепла определены степень разложения ацетилена и состав газообразных продуктов реакции при температуре 1000 ± 10°С в зависимости от давления в реакторе, расхода ацетилена и наличия вольфрамовой сетки в рабочей зоне реактора. Установлено, что с увеличением давления от 1 до 2 бар концентрация водорода в газообразном продукте разложения увеличивается с 44.8 до 68.7% (при одинаковом расходе 100 см3/мин). С увеличением расхода ацетилена с 100 до 250 см3/мин концентрация водорода в продуктах реакции уменьшается почти в 4 раза. Показано, что увеличению концентрации водорода до 60.30% также способствует наличие вольфрамовой сетки внутри реактора (при расходе 100 см3/мин и давлении 1 бар). Помимо водорода и ацетилена в состав газообразных продуктов входят метан, этан, этен, пропан, бутан, бутен и пентан. Установлено, что при большом расходе ацетилена (250 см3/мин) основным газом, кроме водорода, который выходит из реактора, является ацетилен, а с увеличением давления в реакторе в продуктах реакции растет концентрация таких газов, как метан и этан. Степень разложения ацетилена в проточном реакторе, вероятно, может быть увеличена за счет повышения давления. Для работы проточного реактора при более высоких давлениях требуется доработка его конструкции (усиление корпуса, а также переход от внешнего источника тепла к постоянно работающему внутреннему разогреву подаваемого в реактор ацетилена.
Планируется дальнейшая разработка способов использования ацетилена как экологически чистого топлива. Основная задача – создание энергетически чистых циклов на основе ацетилена, а также исследование возможности создания энергетической установки, которая в непрерывном режиме могла бы осуществлять работу, используя ацетилен, как основной вид топлива.
ОБОЗНАЧЕНИЯ
Свод | концентрация водорода, % |
Сугл | концентрация газообразных углеводородов, % |
d | диаметр, нм |
P | давление, бар |
Рz | давления в цилиндре двигателя при его работе на чистом ацетилене, МПа |
Q | объемный расход, см3/мин |
S | удельная поверхность, м2/г |
T | температура, °C |
t | время, с |
U | напряжение, мВ |
V | объем |
ρ | плотность, г/мл |
∑ | сумма |
Список литературы
IEA (2019) World energy outlook. https://www.iea.org/weo. Cited 17 December 2019.
Попель О.С., Фортов В.Е. Возобновляемая энергетика в современном мире. М.: МЭИ, 2015.
Dagle V., Dagle M., Bearden J., Holladay T., Krause S., Ahmed. R&D Opportunities for Development of Natural Gas Conversion Technologies. https://www.pnnl.gov/main/publications/external/ technical_reports/PNNL-26726.pdf. Cited 17 December 2019.
Динцес А.И., Потоловский Л.А. Основы технологии нефтехимического синтеза. М.: Гостоптехиздат, 1960.
Вынту В. Технология нефтехимических производств / Под ред. Исангулянц В.И. М.: Химия, 1968.
Порсин А.В., Куликов А.В., Амосов Ю.И., Рогожников В.Н., Носков А.С. Синтез ацетилена при пиролизе метана на вольфрамовой нити // Теор. осн. хим. технол. 2014. Т. 48. № 4. С. 426.
Егоров А.П., Шерешевский А.И., Шманенков И.В. Курс технологии минеральных веществ. М.: Государственное научно-техническое издательство химической литературы, 1950.
Еремин А.В., Фортов В.Е., Емельянов А.В. Формирование детонационной волны при термическом разложении ацетилена // Письма ж. эксп. теор. физ. 2010. Т. 92. № 2. С. 101.
Еремин А.В., Макеич А.А., Фортов В.Е., Емельянов А.В. Формирование детонационной волны конденсации // Письма журн. эксп. теор. физ. 2008. Т. 87. № 9. С. 556.
Еремин А.В., Емельянов А.В, Гуренцов Е.В., Голуб В.В., Фортов В.Е. Энергетика детонационного пиролиза ацетилена // Теплофиз. выс. темп. 2015. Т. 53. № 3. С. 383.
Комарова Т.В. Получение углеводородных материалов. М.: РХТУ им. Д.И. Менделеева, 2001.
Knorre V.G., Snegireva T.D., Tekunova T.V., Chulkov A.V. A study of the thermal decomposition of acetylene and the properties of the soot formed under the conditions of a constant volume bomb // Combust. Explos. Shock Waves. 1972. V. 8. P. 437. [Кнорре В.Г., Снегирева Т.Д., Текунова Т.В., Чулков А.В. Исследование термического разложения ацетилена и свойств образующейся сажи в условиях бомбы постоянного объема // Физ. горения взрыва. 1972. Т. 8. С. 437.]
Knorre V.G., Kopylov M.S., Tesner P.A. Formation of carbon black with the detonation of acetylene // Combust. Explos. Shock Waves. 1974. V. 10. № 5. P. 767. [Кнорре В.Г., Копылов М.С., Теснер П.А. Образование сажи при детонации ацетилена // Физ. горения взрыва. 1974. Т. 10. № 5. С. 767.]
Штерцер А.А., Ульяницкий В.Ю., Батраев И.С., Рыбин Д.К. Получение наноразмерного детонационного углерода на импульсном газодетонационном аппарате // Журн. тех. физ. 2018. Т. 44. № 9. С. 65.
Shtertser A.A., Rybin D.K., Ulianitsky V.Y., Park W., Datekyu M., Wada T., Kato H. Characterization of nanoscale detonation carbon produced in a pulse gas-detonation device // Diamond Relat. Mater. 2020. V. 101. https://doi.org/https://doi.org/10.1016/j.diamond. 2019.107553
Brunauer S., Emmett P.H., Teller E. Adsorption of Gases in Multimolecular Layers // J. Am. Chem. Soc. 1938. V. 60. № 2. P. 309.
Иванов Б.А. Физика взрыва ацетилена. М.: Химия, 1969.
Denka Company Limited (2020) Denka black. https://www.denka.co.jp/eng/product/detail_00025. Cited 18 April 2020.
Дополнительные материалы отсутствуют.
Инструменты
Теоретические основы химической технологии