Теоретические основы химической технологии, 2021, T. 55, № 5, стр. 578-586
Очистка бензола от тиофена экстрактивной ректификацией с применением колонн с боковым отбором в паровой фазе
Е. А. Анохина a, *, Р. И. Якутин a, А. В. Тимошенко a
a МИРЭА – Российский технологический университет
Москва, Россия
* E-mail: anokhina.ea@mail.ru
Поступила в редакцию 15.03.2021
После доработки 22.03.2021
Принята к публикации 23.03.2021
Аннотация
Серосодержащие соединения присутствуют в сыром бензоле, получаемом при производстве кокса. Одно из таких соединений – тиофен. Для удаления его из сырого бензола можно использовать экстрактивную ректификацию с диметилформамидом в качестве разделяющего агента. Относительная летучесть в бинарной системе бензол–тиофен увеличивается в присутствии диметилформамида с 1.13 до 1.46–2.18. Целью данной работы является исследование возможности использования схемы, включающей сложную экстрактивную колонну с боковым отбором в паровой фазе. Синтезированы новые схемы экстрактивной ректификации, проведены математическое моделирование и их оптимизация. Показано, что предложенная схема экстрактивной ректификации обеспечивает снижение энергозатрат на 29.5% и количествa циркулирующего экстрактивного агента на 47.8% по сравнению с двухколонной схемой при одинаковой степени извлечения бензола из исходной бензол-тиофеновой фракции. При этом выполняются требования к качеству очистки бензола.
ВВЕДЕНИЕ
Бензол – одно из наиболее востребованных сырьевых соединений для органического синтеза и нефтехимии. Основными процессами производства бензола являются коксование угля, паровой крекинг и риформинг нефтяного сырья, а также гидродеалкилирование ароматических фракций. Для получения бензола, отвечающего требованиям промышленных каталитических процессов, необходимо его очистить от неароматических [1–5] и серосодержащих соединений [6–8]. Все серосодержащие соединения являются каталитическими ядами для большинства процессов органического синтеза, их присутствие в исходной реакционной смеси приводит к коррозии технологического оборудования, снижению качества продукции и загрязнению окружающей среды. Тиофен является одним из наиболее трудно удаляемых компонентов фракции сырого бензола, полученного путем коксования угля. Следовательно, очистка бензола от тиофена является важной промышленной задачей. Тиофен практически невозможно удалить тиофен из сырого бензола простой ректификацией, поскольку относительная летучесть в бинарной системе бензол–тиофен близка к 1 и составляет 1.13. Очистка серной кислотой, каталитическое гидрообессеривание, экстракция и экстрактивная ректификация используются в качестве альтернативы простой ректификации [8]. Для процесса экстрактивной ректификации бинарной системы бензол–тиофен был предложен ряд экстрактивных агентов (ЭА) [9, 10]. Каждое из этих соединений обеспечивает увеличение относительной летучести разделяемых компонентов, например, в присутствии диметилформамидa (ДМФА) она возрастает до 1.8–2.18 [9], 1.46–1.5 [10], в присутствии N-метилпирролидонa – до 1.64–2.08 [9], 1.58–1.61 [10], в присутствии сульфоланa – до 1.59–1.95 [9], 1.6–1.63 [10], диэтиленгликоля – до 1.45–1.63 [9], 1.45–1.5 [10], триэтиленгликоля – до 1.55–1.71 [9], 1.44–1.49 [10]. Некоторое различие в значениях коэффициентов относительной летучести, скорее всего, связано с тем, что авторы [10] оценивали эффективность разделяющего агента, используя предельные коэффициенты активности при бесконечном разбавлении.
Среди этих соединений ДМФА обладает наибольшим эффектом увеличения относительной летучести, имеет самую низкую температуру кипения, но несколько более токсичен. Более высокие температуры кипения ЭА требуют использования более дорогих источников энергии для обогрева кипятильников колонн, что может увеличить общие годовые затраты. Имеются данные о возможности использования бинарных ЭА на основе ДМФА или N-метилпирролидона и ионной жидкости для разделения пары бензол–тиофен [11, 12]. Поскольку стоимость ионных жидкостей довольно высока, это препятствует их применению в качестве промышленных ЭА. В настоящее время ДМФА является наиболее широко используемым промышленным ЭА для выделения тиофена из сырого бензола [7].
В частности, этот процесс используется на предприятиях России и Эстонии и предшествует сернокислотной очистке бензола. Сырой бензол, полученный путем коксования угля, помимо тиофена, содержит ряд примесей, таких как толуол, ксилолы, метилциклогексан, диены и др. После первой стадии очистки их общая концентрация не превышает 0.4 мас. %. Второй этап очистки сырого бензола – экстрактивная ректификация, которая обеспечивает практически полное отделение тиофена.
Существующая на предприятиях (традиционная) схема экстрактивной ректификации для разделения смеси бензол–тиофен состоит из двух колонн: колонны экстрактивной ректификации (EC) и колонны регенерации (RC). В дистилляте EC выделяется бензол с чиситотой 99.78 мас. %, а в дистилляте RC – тиофеновая фракция (TF), которая содержит до 90 мас. % бензола. Высокое содержание бензола во фракции тиофена объясняется требованиями стабильной работы колонны. В традиционном двухколонном комплексе из исходной фракции можно выделить только 93 мас. % очищенного бензола. Таким образом, возникает задача увеличения выходa чистого бензола в процессе ЭР фракции бензол–тиофен [7]. Для решения этой задачи было предложено использовать последовательность из трех традиционных подсистем экстрактивной ректификации. В каждой из них очищенный бензол получают в виде дистиллята экстрактивной колонны, а регенерированный ЭА – как кубовый продукт колонны регенерации. Дистиллятом колонны регенерации является тиофеновая фракция, которая поступает на разделение в экстрактивную колонну следующей подсистемы ЭР. Эта схема последовательного концентрирования позволила получить фракцию тиофена с его концентрацией до 95 мас. % [7]. К сожалению, эта схема содержит шесть ректификационных колонн и требует значительных капитальных затрат.
Авторы [11] предложили упростить схему из шести колонн, используя только четыре колонны. Вместо первых двух подсистем ЭР использовали сложные ректификационные колонны с боковым отбором. В этой схеме ЭА, содержащийся в боковом отборе, поступает на следующую стадию. Однако это нельзя считать недостатком, потому что боковой отбор из-за высокого содержания высококипящего компонента несет дополнительное тепло, которое может быть использовано для выполнения работы разделения. С другой стороны, дополнительное количество поступающего на последующую стадию ЭА также может облегчить разделение. Предложенная схема действительно позволила снизить тепловые нагрузки на кипятильники и конденсаторы на 6.47 и 6.41% соответственно по сравнению с шестиколонным вариантом [11].
К сожалению, из данных работы [11] не ясно, в каком агрегатном состоянии осуществлялся отбор бокового потокa. Исходя из того, что концентрация ДМФА в боковом отборе составляла 92.4–93.0 мас. %, можно предположить, что боковой поток осуществлялся в жидкой фазе. В случае отбора в паровой фазе, из-за высокой разницы в летучести ЭА и компонентов смеси, концентрация ЭА должна быть намного ниже. Таким образом, можно предположить, что организация бокового отбора в паровой фазе снизит энергозатраты на очистку бензола от тиофена экстрактивной ректификацией с ДМФА.
Целью данной работы является исследование эффективности использования сложной колонны с боковым отбором в паровой фазе при ЭР смеси бензол–тиофен с диметилформамидом.
РАСЧЕТНАЯ ЧАСТЬ
Синтез схем. Пошаговое преобразование четырехколонной схемы из двухотборных колонн в схемы с боковым отбором в соответствии с алгоритмом [13] показано на рис. 1. Четырехколонная технологическая схема ЭР для выделения тиофенового концентрата из смеси бензол–тиофен представлена на рис. 1а. Исходная схема (рис. 1а) преобразуется в граф (рис. 1б). В этом графе ребра представляют потоки пара и жидкости внутри колонн и между ними. Вершины – это поперечные сечения, ограничивающие секции колонны. Упрощение графа путем объединения двух вершин, смежных по ориентированному ребру, приводит к графу (рис. 1в), который отображает схему с частично связанными тепловыми и материальными потоками, то есть включает сложную колонну с укрепляющей боковой секцией (SS1) (рис. 1г). Выполнение операции упрощения над графом (рис. 1в) по неориентированному ребру S1 приводит к графу (рис. 1д), который отображает схему, включающую сложную колонну (EW1) с боковым отбором в паровой фазе (TF(V)), расположенным ниже зоны питания (рис. 1е). Поскольку значительное количество диметилформамида поступает на вторую ступень вместе с потоком TF(V), добавляется рециркуляционный поток, соединяющий RC2 и EW1, для балансировки технологической схемы.
Рис. 1.
Схемы и графы экстрактивной ректификации для выделения тиофеновой фракции: (а) – четырехколонная схема, (б) – граф четырехколонной схемы, (в) – граф трехколонной схемы со сложной колонной с боковой секцией, (г) – трехколонная схема со сложной колонной с боковой секцией, (д) – граф трехколонной схемы со сложной колонной с боковым отбором, (е) – трехколонная схемы со сложной колонной с боковым отбором.
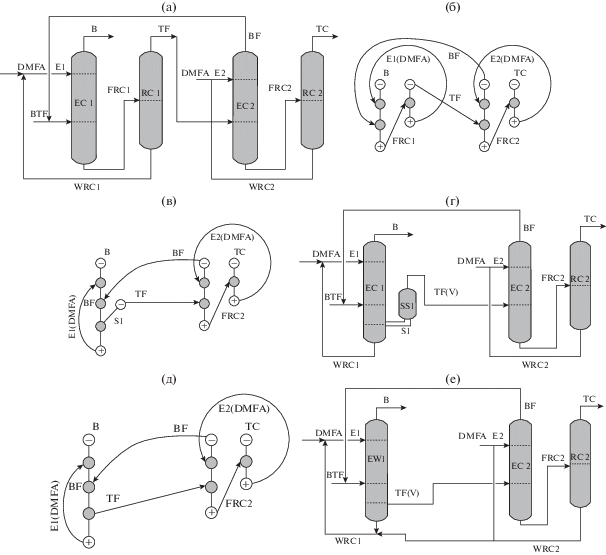
Были определены оптимальные рабочие параметры трех- и четырехколонной схем очистки бензола от тиофена. В качестве критерия оптимизации использовали суммарную тепловую нагрузку в кипятильниках колонн.
Для получения сопоставимых результатов для всех схем были заданы следующие параметры: скорость подачи исходной бензол-тиофеновой фракции – 10 000 кг/ч, концентрация бензола в потоках BTF и BF – 99.0 мас. %, концентрация бензола в потоке B – 99.78 мас. %, концентрация ДМФА в TC – 0.001 мас. %. Концентрация ДМФА в потоке ЭА – 99.99 мас. %, концентрация тиофена в потоке ТС – 50 мас. % (при этом степень извлечения бензола из исходной фракции составляет 99 %). Здесь и далее обозначения потоков и колонн приведены в соответствии с рис. 1. Во всех случаях давление в верхней части колонн принималось равным 101.3 кПа, гидравлическое сопротивление одной теоретической тарелки составляло 0.3 кПа. Моделирование и оптимизацию технологических схем проводили в программном комплексе Aspen Plus. Для описания парожидкостного равновесия использовали модель Вильсона с параметрами, приведенными в [14, 15].
Оптимизация второй стадии четырехколонной схемы. Оптимальные параметры первой стадии ЭР четырехколонной схемы (рис. 1a) были определены ранее в [14 , 15]. Для решения поставленной задачи потребовалось провести расчет и оптимизацию второй стадии ЭР четырехколонной схемы. Все расчеты проводились при наличии рециркуляционного потока BF, связывающего вторую и первую стадии процесса.
Процедура оптимизации включала следующие шаги:
1) Определение оптимального количества тарелок в EC2 и RC2;
2) Определение оптимального расхода ЭА в EC2;
3) Выбор оптимальной тарелки питания для RC2 в зависимости от расхода ДМФА;
4) Определение оптимального значения расхода ЭА для второй ступени ЭР в целом.
Изначально при фиксированном соотношении потоков TF(V)/E2, равном 1 : 3, и температуре ЭА, равной 80°C, были получены зависимости тепловой нагрузки в кипятильниках EC2 и RC2 от количества теоретических тарелок (т.т.). Для каждого заданного количества теоретических были определены оптимальные положения тарелок питания (а для EC2 и тарелки подачи ЭА).
На основании полученных данных были подобраны значения общего числа теоретических тарелок – 65 и 28 соответственно, в EC2 и RC2. Затем для EC2 был определен оптимальный расход ДМФА при различном положении тарелок подачи питания и ЭА. Использовали встроенный инструмент Aspen Plus “Sensitivity Analysis”. Величину потока ЭА варьировали с шагом 50 кг/ч для каждого фиксированного заданного NЭА и NF. Минимальное значение тепловых нагрузок $Q_{{\text{r}}}^{{{\text{EC2}}}}$ = 695.2 кВт и $Q_{{\text{c}}}^{{{\text{EC2}}}}$ = −586.6 кВт было достигнуто при подаче потока TF и экстрактивного агента (Е2) на 42 и 6 тарелки, соответственно, расходе ЭА 2350 кг/ч и флегмовом числе 7.25. Затем была определена зависимость оптимального положения тарелки питания в колонне регенерации от расхода ЭА. Выявлено, что оптимальное значение $N_{{{\text{FRC2}}}}^{{{\text{RC2}}}}$ = 11 и не изменяется в диапазоне изменения расхода ЭА 1500–3000 кг/ч. Это дало возможность в дальнейшем исключить этот параметр оптимизации из рассмотрения. Затем с помощью встроенных в Aspen Plus инструментов “Optimization” и “Sensitivity Analysis” был определен оптимальный расход ЭА на второй стадии разделения в целом (табл. 1).
Таблица 1.
Зависимость энергозатрат в кипятильниках колонн второй ступени схемы от $N_{{\text{E}}}^{{{\text{EC2}}}},$ $N_{{\text{F}}}^{{{\text{EC2}}}}$ и расхода ЭА
${{N_{{\text{E}}}^{{{\text{EC2}}}}} \mathord{\left/ {\vphantom {{N_{{\text{E}}}^{{{\text{EC2}}}}} {N_{{\text{F}}}^{{{\text{EC2}}}}}}} \right. \kern-0em} {N_{{\text{F}}}^{{{\text{EC2}}}}}}$ | $F_{{\text{E}}}^{{{\text{RC2}}}}$, кг/ч | REC2 | RRC2 | $Q_{{\text{r}}}^{{{\text{EC2}}}}$, кВт | $Q_{{\text{r}}}^{{{\text{RC2}}}}$, кВт | ∑Qr, кВт |
---|---|---|---|---|---|---|
5/41 | 1888.79 | 7.70 | 3.63 | 703.6 | 86.2 | 789.9 |
5/42 | 1839.66 | 7.74 | 3.52 | 704.6 | 84.5 | 789.1 |
5/43 | 1887.37 | 7.69 | 3.62 | 703.4 | 86.2 | 789.5 |
6/41 | 1912.57 | 7.65 | 3.68 | 701.7 | 87.0 | 788.7 |
6/42 | 1908.71 | 7.65 | 3.67 | 701.2 | 86.9 | 788.0 |
6/43 | 1922.64 | 7.63 | 3.70 | 701.1 | 87.3 | 788.4 |
7/41 | 1924.63 | 7.67 | 3.71 | 703.9 | 87.4 | 791.3 |
7/42 | 1920.33 | 7.67 | 3.70 | 703.3 | 87.3 | 790.5 |
7/43 | 1941.86 | 7.65 | 3.74 | 702.9 | 88.0 | 790.9 |
Расположение тарелок питания ($N_{{\text{F}}}^{{{\text{EC2}}}},$ $N_{{\text{E}}}^{{{\text{EC2}}}}$), расход ЭА (Е2) и флегмовые числа (REC2, RRC2) использовались в качестве параметров оптимизации для получения минимального ΣQr. Определено, что минимум энергопотребления в кипятильниках колонн второй стадии ЭР достигается при расходе экстрактивного агента (Е2), равном 1908.71 кг/ч, и подаче потоков E2 и TF(V) в колонну EC2 на 6 и 42 тарелки соответственно. Суммарная тепловая нагрузка на кипятильники составляет 788.0 кВт. С использованием полученных данных были определены оптимальные параметры для схемы, изображенной на рис. 1а, которые приведены в табл. 2. Общая тепловая нагрузка в кипятильниках колонн всей четырехколонной схемы при оптимальных параметрах ее работы составляет ΣQr = 9894.9 кВт.
Таблица 2.
Оптимальные рабочие параметры четырехколонной схемы выделения тиофенового концентрата
Параметр | EC1 | RC1 | EC2 | RC2 |
---|---|---|---|---|
NS, т.т. | 55 | 26 | 65 | 28 |
Диаметр, м | 2.35 | 0.75 | 0.68 | 0.25 |
${{{{N_{{\text{E}}}^{{{\text{EC}}}}} \mathord{\left/ {\vphantom {{N_{{\text{E}}}^{{{\text{EC}}}}} {N_{{\text{F}}}^{{{\text{EC}}}}}}} \right. \kern-0em} {N_{{\text{F}}}^{{{\text{EC}}}}}}} \mathord{\left/ {\vphantom {{{{N_{{\text{E}}}^{{{\text{EC}}}}} \mathord{\left/ {\vphantom {{N_{{\text{E}}}^{{{\text{EC}}}}} {N_{{\text{F}}}^{{{\text{EC}}}}}}} \right. \kern-0em} {N_{{\text{F}}}^{{{\text{EC}}}}}}} {N_{{\text{F}}}^{{{\text{RC}}}}}}} \right. \kern-0em} {N_{{\text{F}}}^{{{\text{RC}}}}}}$ | 7/29/– | –/–/11 | 6/42/– | –/–/11 |
R | 5.85 | 7.2 | 7.64 | 3.67 |
Расход ЭА, кг/ч | 19917.6 | – | 1908.7 | – |
Температура в кубе, °С | 149.1 | 154.4 | 144.6 | 154.6 |
Qr, кВт | 8347.3 | 759.7 | 701.0 | 86.9 |
Определение оптимальных параметров трехколонной схемы выделения тиофенового концентрата. Схема состоит из сложной колонны с боковым отбором (TF(V)) в паровой фазе, расположенным ниже зоны подачи питания (рис. 1е). Как отмечалось ранее, предложение использовать отбор в паровой фазе следует из алгоритма [13]. В соответствии с этим алгоритмом количество теоретических тарелок в колонне с боковым отбором должно быть равно сумме количества тарелок в колонне EC1 и в исчерпывающей секции колонны RC1 (55 + 15 = 70). Поскольку вторая ступень не подвергалась модификации, количество теоретических тарелок в колоннах осталось неизменным. Параметры потоков сырья и продуктов, давление в верхней части колонн и перепад давления на теоретической тарелке задавали такими же, как и для четырехколонной схемы.
В результате моделирования трехколонной схемы с замкнутым рециклом бензольной фракции был определен расход потока BF, а также состав и расход потока ТF(V) для каждого положения тарелки отбора.
В первую очередь, с помощью инструмента “Sensitivity Analysis”, был определен расход ЭА в EC2 (рис. 1е) при NTF(V) = 64 в EW1 и расходe TF(V), равном 450 кг/ч при различном положении тарелок подачи питания и E2 в EC2. Полученные результаты представлены в табл. 3.
Таблица 3.
Определение оптимального расхода ЭА в EC2 при NTF(V) = 64 т.т. и расходе TF(V) 450 кг/ч
NE/NF | Оптимальный расход ЭА, кг/ч | REC2 | $Q_{{\text{c}}}^{{{\text{EC2}}}}$, кВт | $Q_{{\text{r}}}^{{{\text{EC2}}}}$, кВт |
---|---|---|---|---|
5/51 | 1150 | 9.12 | –277.2 | 273.2 |
5/52 | 1150 | 9.12 | –277.1 | 273.1 |
5/53 | 1150 | 9.13 | –277.5 | 273.5 |
6/51 | 1150 | 9.11 | –277.1 | 273.0 |
Перед тем как определить оптимальный расход ЭА для подсистемы EC2–RC2 в целом, необходимо исследовать зависимость оптимального положения тарелки питания в RC2 от расхода ЭА. Установлено, что оптимальное расположение тарелки питания RC2 мало зависит от величины расхода ЭА (табл. 4).
Таблица 4.
Зависимость оптимальной тарелки подачи питания в RC2 от величины расхода ЭА при NTF(V) = 64 и расходе TF(V) 450 кг/ч
Расход ЭА, кг/ч | NF | RRC2 | $Q_{{\text{c}}}^{{{\text{RC2}}}}$, кВт | $Q_{{\text{r}}}^{{{\text{RC2}}}}$, кВт |
---|---|---|---|---|
3000 | 11 | 6.07 | –120.3 | 125.9 |
2500 | 11 | 5.00 | –102.2 | 108.7 |
2000 | 11 | 3.95 | –84.1 | 91.5 |
1500 | 11 | 2.91 | –66.5 | 74.3 |
1200 | 11 | 2.32 | –56.4 | 64.3 |
1150 | 12 | 2.22 | –54.8 | 62.7 |
1100 | 12 | 2.12 | –53.1 | 61.0 |
1000 | 12 | 1.93 | –49.8 | 57.6 |
В диапазонах 1200–3000 кг/ч и 1150–800 кг/ч определено оптимальное положение тарелки питания в RC2, равное 11 и 12 соответственно. Это позволяет исключить указанный параметр при дальнейшей оптимизации. Далее был определен расход ЭА для второй ступени ЭР в целом. Для этого использовали встроенные в программный комплекс Aspen Plus инструменты “Optimization” и “Sensitivity Analysis”. $N_{{\text{E}}}^{{{\text{EC2}}}}$ и $N_{{\text{F}}}^{{{\text{EC2}}}}$ варьировали при фиксированном расположении тарелки бокового отбора NTF(V) = 64 и расходе TF(V), равном 450 кг/ч. Параметры оптимизации включали номера тарелок питания ($N_{{\text{F}}}^{{{\text{EC2}}}},$ $N_{{\text{E}}}^{{{\text{EC2}}}}$), расход ЭА (E2), флегмовые числа в EC2 и RC2 (табл. 5). Установлено, что минимальное суммарное потребление энергии в подсистеме EC2-RC2 достигается при расходе E2 = 911.86 кг/ч, $N_{{\text{E}}}^{{{\text{EC2}}}}$ = 5 и $N_{{\text{F}}}^{{{\text{EC2}}}}$ = 52.
Таблица 5.
Определение оптимальных параметров второй ступени ЭP трехколонной последовательности при NTF(V) = 64 и расходе TF(V) 450 кг/ч
${{N_{{\text{E}}}^{{{\text{EC2}}}}} \mathord{\left/ {\vphantom {{N_{{\text{E}}}^{{{\text{EC2}}}}} {N_{{\text{F}}}^{{{\text{EC2}}}}}}} \right. \kern-0em} {N_{{\text{F}}}^{{{\text{EC2}}}}}}$ | Расход EEC2 , кг/ч | REC2 | RRC2 | $Q_{{\text{r}}}^{{{\text{EC2}}}}$, кВт | $Q_{{\text{r}}}^{{{\text{RC2}}}}$, кВт | ΣQr, кВт |
---|---|---|---|---|---|---|
4/51 | 889.45 | 9.97 | 1.75 | 284.0 | 54.6 | 338.6 |
4/52 | 891.65 | 9.96 | 1.75 | 283.7 | 54.6 | 338.3 |
4/53 | 893.31 | 9.97 | 1.75 | 284.0 | 54.7 | 338.7 |
5/51 | 927.79 | 9.60 | 1.82 | 275.7 | 55.7 | 331.4 |
5/52 | 911.86 | 9.64 | 1.79 | 276.1 | 55.2 | 331.2 |
5/53 | 925.02 | 9.63 | 1.82 | 276.2 | 55.6 | 331.8 |
6/51 | 924.17 | 9.62 | 1.81 | 275.9 | 55.6 | 331.5 |
6/52 | 930.43 | 9.60 | 1.83 | 275.6 | 55.7 | 331.4 |
6/53 | 927.02 | 9.62 | 1.82 | 276.2 | 55.6 | 331.9 |
Аналогичным образом были определены параметры, при которых достигается минимальная тепловая нагрузка в подсистеме EC2–RC2 трехколонной схемы при фиксированном расходе TF(V), равном 500 и 550 кг/ч, и той же тарелке бокового отбора в EW1. Параметрическую оптимизацию схемы проводили в Aspen Plus посредством использования ранее названных встроенных инструментов, результаты представлены в табл. 6.
Таблица 6.
Оптимальные параметры трехколонной схемы при NTF(V) = 64 т.т. и различных величинах потока TF(V)
TF(V), кг/ч | ${{N_{{\text{E}}}^{{{\text{EC2}}}}} \mathord{\left/ {\vphantom {{N_{{\text{E}}}^{{{\text{EC2}}}}} {N_{{\text{F}}}^{{{\text{EC2}}}}}}} \right. \kern-0em} {N_{{\text{F}}}^{{{\text{EC2}}}}}}$ | Расход EEC2, кг/ч | REC2 | RRC2 | $Q_{{\text{r}}}^{{{\text{EC2}}}}$, кВт | $Q_{{\text{r}}}^{{{\text{RC2}}}}$, кВт | ΣQr, кВт |
---|---|---|---|---|---|---|---|
450 | 5/52 | 911.86 | 9.64 | 1.79 | 276.0 | 55.2 | 331.2 |
500 | 5/50 | 1035.74 | 9.37 | 2.02 | 320.1 | 59.2 | 379.3 |
550 | 6/49 | 1157.74 | 9.12 | 2.25 | 362.5 | 63.3 | 425.8 |
Полученные данные использовали для моделирования трехколонной схемы в целом. Оптимальные параметры трехколонной схемы в целом при различных значениях номера тарелки отбора и величины бокового отбора TF(V) представлены в табл. 7.
Таблица 7.
Оптимальные параметры трехколонной схемы в целом при различных NTF(V) и значениях расхода TF(V)
TF(V), кг/ч | ${{N_{{\text{E}}}^{{{\text{EC2}}}}} \mathord{\left/ {\vphantom {{N_{{\text{E}}}^{{{\text{EC2}}}}} {N_{{\text{F}}}^{{{\text{EC2}}}}}}} \right. \kern-0em} {N_{{\text{F}}}^{{{\text{EC2}}}}}}$ | Расход E2, кг/ч | TF(V) : E2 | REC2 | RRC2 | $Q_{{\text{r}}}^{{{\text{EC2}}}}$, кВт | $Q_{{\text{r}}}^{{{\text{RC2}}}}$, кВт | $Q_{{\text{r}}}^{{{\text{EW1}}}}$, кВт | ΣQr, кВт |
---|---|---|---|---|---|---|---|---|---|
NTF(V) = 64 | |||||||||
450 | 5/52 | 911.9 | 1 : 2.03 | 9.6 | 1.8 | 276.1 | 55.2 | 8377.8 | 8709.1 |
500 | 5/50 | 1035.7 | 1 : 2.07 | 9.4 | 2.0 | 320.1 | 59.2 | 8318.0 | 8697.3 |
550 | 6/49 | 1157.7 | 1 : 2.11 | 9.1 | 2.3 | 362.5 | 63.3 | 8274 | 8699.8 |
NTF(V) = 65 | |||||||||
500 | 5/54 | 769.14 | 1 : 1.54 | 10.1 | 1.7 | 219.4 | 53.7 | 8386.1 | 8659.2 |
550 | 5/52 | 872.78 | 1 : 1.59 | 9.9 | 1.9 | 256.5 | 57.3 | 8330.7 | 8644.5 |
600 | 5/51 | 974.77 | 1 : 1.62 | 9.6 | 2.1 | 291.9 | 60.9 | 8291.2 | 8644.0 |
650 | 5/51 | 1068.18 | 1 : 1.64 | 9.4 | 2.3 | 327.2 | 64.3 | 8257.7 | 8649.2 |
700 | 5/50 | 1156.25 | 1 : 1.65 | 9.2 | 2.5 | 361.0 | 67.7 | 8235.7 | 8664.4 |
NTF(V) = 66 | |||||||||
1000 | 5/57 | 675.2 | 1 : 0.68 | 11.6 | 2.5 | 148.0 | 67.1 | 8413.5 | 8628.6 |
1100 | 5/56 | 762.2 | 1 : 0.69 | 11.2 | 2.8 | 183.1 | 72.1 | 8369.7 | 8624.9 |
1200 | 5/55 | 834.5 | 1 : 0.70 | 10.9 | 3.0 | 217.3 | 76.6 | 8339.1 | 8633.0 |
NTF(V) = 67 | |||||||||
3000 | 5/64 | 72 | 1 : 0.02 | 28.0 | 5.9 | 0.6 | 116.3 | 8747.2 | 8864.1 |
3100 | 5/64 | 156 | 1 : 0.05 | 26.3 | 6.3 | 0.5 | 122.6 | 8734.5 | 8857.6 |
3200 | 5/64 | 263 | 1 : 0.08 | 25.2 | 6.3 | 0.5 | 129.4 | 8724.7 | 8854.6 |
3300 | 5/64 | 426 | 1 : 0.13 | 23.6 | 6.8 | 0.5 | 137.9 | 8717.3 | 8855.7 |
РЕЗУЛЬТАТЫ И ИХ ОБСУЖДЕНИЕ
При увеличении NTF(V), количество TF(V), обеспечивающее минимальные тепловые нагрузки для всей схемы в целом, резко возрастает. Боковой поток колонны EW1 возрастает более чем в 6 раз при увеличении номера тарелки бокового отбора всего на 3 т.т. Поскольку TF(V) является паровым потоком, это приводит к снижению тепловой нагрузки на кипятильник EC2 с одновременным увеличением флегмы. При NTF(V) = 67 тепловая нагрузка на кипятильник этой колонны практически отсутствует (табл. 7). Практически все увеличение TF(V) с ростом NTF(V) происходит за счет увеличения количества и концентрации ДМФА в этом потоке (рис. 2). При этом для любого значения NTF(V) значения величин потоков бензола и тиофенового концентрата остаются постоянными. Существенно изменяется только величина рециркуляционного потока BF, что связано с уменьшением количества бензола в боковом потоке с увеличением номера тарелки бокового отбора. Таким образом, было обнаружено, что изменение уровня бокового отбора значительно влияет на величину его потока. В то же время на второй стадии процесса наблюдается значительное снижение энергозатрат. С другой стороны, использование парового потока в качестве питания второй стадии процесса может значительно повысить энергоэффективность схемы в целом. Как отмечалось ранее, алгоритм, предложенный авторами [13] и проиллюстрированный на рис. 1, позволяет предварительно определить фазовое состояние бокового отбора.
Рис. 2.
Состав (а) и расход (б) компонентов в зависимости от расположения тарелки бокового отбора колонны EW1: 1 – бензол, 2 – тиофен, 3 – ДМФА.
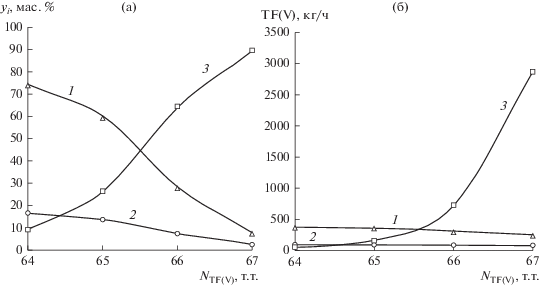
Таким образом, было обнаружено, что изменение уровня бокового отбора значительно влияет на величину его расхода. Также наблюдается и значительная зависимость энергопотребления второй стадии экстрактивной ректификации от величины и уровня бокового отбора.
Полученные результаты целесообразно сравнить с результатами, полученными ранее (табл. 8). Во всех случаях данные приводятся для продуктовых потоков с одинаковыми концентрационными параметрами. Видно, что разделение смеси в традиционной двухколонной схеме ЭР потребляет наибольшее количество энергоресурсов. Далее в ряду снижения энергопотребления идет четырехколонная схема. Очевидно, что большое количество ректификационных колонн и сопутствующего технологического оборудования делает такое решение наиболее дорогим по капитальным затратам. Использование одной сложной колонны с боковой секцией позволяет несколько улучшить энергетические характеристики процесса за счет повышения термодинамической эффективности процесса путем исключения одной из зон термодинамически необратимого смешения, присутствующей в традиционной последовательности ЭР. Однако энергопотребление оказывается практически на уровне, полученном для четырехколонной схемы. Это технологическое решение, которое также может быть реализовано в виде колонны с перегородкой, может иметь перспективу, поскольку обеспечит существенное снижение затрат сравнению с традиционной двухколонной схемой и значительное снижение капитальных затрат по сравнению с четырехколонной схемой. Однако лучшими энергетическими характеристиками обладает трехколонная схема (рис. 1е), которая при достижении той же степени извлечения бензола потребляет на 29.5% меньше энергии, чем традиционная схема (табл. 8), и, очевидно, имеет более низкие капитальные затраты, чем четырехколонная схема. Еще одним преимуществом такой схемы экстрактивной ректификации является резкое, почти двукратное снижение количества циркулирующего в системе экстрактивного агента, по сравнению со схемами, рассмотренными в [14, 15].
Таблица 8.
Характеристики различных вариантов организации процесса экстрактивной ректификации для очистки сырого бензола от тиофена при степени извлечения бензола из исходной фракции 99 мас. %
Параметр | Четырех-колонная схема (рис. 1а) |
Трех-
колонная схема (рис. 1е) |
Традиционная двухколонная схема [14, 15] | Сложная колонна с боковой секцией [14, 15] |
---|---|---|---|---|
Общее число теоретических тарелок в колоннах схемы | 174 | 163 | 81 | 81 |
Суммарный расход экстрактивного агента в колоннах схемы, кг/ч | 21826 | 19895 | 38115 | 38115 |
Рециркуляционный поток бензольной фракции, кг/ч | 650.2 | 230.2 | – | – |
Суммарные тепловые нагрузки на кипятильники колонн, кВт | 9895 | 8627 | 12230 | 9687 |
ЗАКЛЮЧЕНИЕ
В настоящей работе нами предложен вариант организации технологического процесса экстрактивной ректификации для очистки бензола от тиофена, который характеризуется минимальными энергозатратами на разделение и минимальным расходом экстрактивного агента среди изученных на сегодняшний день технических решений, при обеспечении заданного качества очищенного бензола. Правильный выбор агрегатного состояния потока бокового отбора позволяет существенно улучшить энергетические показатели технологического процесса.
Работа выполнена при финансовой поддержке Минобрнауки России в рамках государственного задания РТУ МИРЭА, тема № 0706-2020-0020.
ОБОЗНАЧЕНИЯ
B | поток бензола |
BF | поток бензольной фракции |
BTF | поток бензол-тиофеновой фракции |
DMFA | поток диметилформамида |
N | номер тарелки |
NS | общее число тарелок |
Q | тепловая нагрузка |
R | флегмовое число |
TC | поток тиофенового концентрата |
TF | поток тиофеновой фракции |
TF(V) | боковой отбор тиофеновой фракции |
y | концентрация компонентов в паре |
ИНДЕКСЫ
АББРЕВИАТУРЫ
Список литературы
Berg L. Separation of benzene and toluene from close boiling nonaromatics by extractive distillation // AIChE J. 1983. V. 29. № 6. P. 961.
Chen B., Lei Z., Li J. Separation of aromatics and non-aromatics by extractive distillation with NMP // J. Chem. Eng. Jpn. 2003. V. 36. № 1. P. 20.
Ghaee A., Sotudeh-Gharebagh R., Mostoufi N. Dynamic optimization of the benzene extractive distillation unit // Braz. J. Chem. Eng. 2008. V. 25. № 4. P. 765.
Abushwireb F., Elakrami H., Emtir M. The effect of solvent selection on energy-integrated extractive distillation for aromatics recovery from pyrolysis gasoline: Simulation and optimization // Chem. Eng. Trans. 2009. V. 18. P. 243.
Li W., Xu B., Lei Zh., Dai Ch. Separation of benzene and cyclohexane by extractive distillation intensified with ionic liquid // Chem. Eng. Process. 2018. V. 126. P. 81.
Zaretskii M.I., Mozzuhin A.S., Pershina L.A., Taytz S.Z., Golub V.B., Chartov E.M. Evaluation of process parameters for production of the thiophene fraction and isolation of pure thiophene by extractive rectification // Coke Chem. 1989. V. 2. P. 35.
Zaretskii M.I. Cleaning of coke-chemical benzene from thiophene. Preparation of pure thiophene from thiophene fraction by extractive rectification. Calculation of industrial plant // Coke Chem. 2004. V. 6. P. 20.
Vagner S.E., Tryasunov B.G. Nontraditional methods for the purification of raw coke-chemical benzene // Solid Fuel Chem. 2012. V. 46. P. 225.
Кононов Н.Ф., Тайц С.З., Коган В.Б. Сапунов В.А. Способ выделения тиофена из его смесей с бензолом. Пат. 245134 СССР. 1969.
Wehner K., Kisan W., Kunz G. Method for separating thiophene from mixtures thereof with benzene. Pat. 3879268 US. 1975.
Han J., Lei Zh., Dong Y., Dai Ch., Chen B. Process intensification on the separation of benzene and thiophene by extractive distillation // AIChE J. 2015. V. 61. P. 4470.
Dai Ch., Dong Y., Han J., Lei Zh. Separation of benzene and thiophene with a mixture of N-methyl-2-pyrrolidinone (NMP) and ionic liquid as entrainer // Fluid Phase Equilib. 2015. V. 388. P. 142.
Timoshenko A.V., Anokhina E.A., Ivanova L.V. Extractive distillation systems involving complex columns with partially coupled heat and material flows // Theor. Found. Chem. Eng. 2005. V. 39. № 5. P. 463. https://doi.org/10.1007/s11236-005-0103-7 [Тимошенко A.В., Анохина Е.А., Иванова Л.В. Комплексы экстрактивной ректификации, включающие сложные колонны с частично связанными тепловыми и материальными потоками // Теорет. основы хим. технол. 2005. Т. 39. № 5. С. 491–498.]
Timoshenko A.V., Anokhina E.A., Akishin A.Yu., Remizova A.V. Benzene Purification from Thiophene by Extractive Distillation with Dimethylformamide // Chem. Eng. Trans. 2018. V. 69. P. 877.
Anokhina E.A., Timoshenko A.V., Akishin A.Yu., Remizova A.V. Benzene Purification from Thiophene Using Dimethylformamide as an Entrainer in Thermally Coupled Extractive Distillation Columns // Chem. Eng. Res. Des. 2019. V. 146. P. 391.
Дополнительные материалы отсутствуют.
Инструменты
Теоретические основы химической технологии