Теоретические основы химической технологии, 2022, T. 56, № 3, стр. 300-304
Получение порошков вольфрама, титана, молибдена при их диспергировании в импульсных разрядах в водных растворах
Р. К. Байрамов a, *, М. Ю. Григорьев b, Г. П. Панасюк c, И. В. Козерожец c, И. В. Татаринова b
a ООО “Олимпия”
301650 Тульская область, г. Новомосковск, Транспортная улица, 26, Россия
b АО “АК "Туламашзавод”
300041 Тульская область, г. Тула, ул. Мосина, 2, Россия
c Институт общей и неорганической химии им. Н. С. Курнакова РАН
119991 Москва, Ленинский пр-т, 31, Россия
* E-mail: rbairamovintech@yandex.ru
Поступила в редакцию 24.10.2021
После доработки 28.11.2021
Принята к публикации 15.02.2022
- EDN: DZETQP
- DOI: 10.31857/S0040357122030046
Аннотация
Продолжены исследования процесса диспергирования металлов в импульсных разрядах в растворах азотной и серной кислоты. Выявлено, что основным продуктом, образующимся при диспергировании вольфрама, титана, молибдена являются порошки металлов. Обнаружено существенное влияние на производительность процесса частоты импульсов тока, подаваемого на электроды. Термодинамическими расчетами показано, что получающийся в процессе атомарный кислород окисляет диспергированные частицы металла с образованием на их поверхности пленки, содержащей устойчивые формы оксидов металлов. Полученные результаты подтверждают высказанные ранее предположения: образование атомарного кислорода при терморазложении рабочего раствора в зоне искрового разряда, его участие в окислении диспергированных частиц металла с образованием на поверхности защитной оксидной пленки, которая предохраняет металл от взаимодействия с окружающей средой.
ВВЕДЕНИЕ
В промышленности порошки вольфрама, титана, молибдена получают восстановлением прекурсоров, что представляет собою многостадийный, сложный технологический процесс [1]. При получении порошков вольфрама и молибдена в качестве исходного сырья применяют триоксиды этих металлов, которые восстанавливают с помощью водорода. В литературе упоминается об использовании в процессе восстановления также оксида углерода (II). В качестве исходного сырья при получении порошка титана используют оксид титана, который восстанавливают с помощью кальция. Для полного восстановления диоксида титана восстановитель берут в количестве в 1.2–2.0 раза больше, чем требуется по реакции TiO2 + + 2Ca = Ti + 2CaO [1].
В работе [2] при получении порошка вольфрама в качестве исходного сырья используют паравольфрамат аммония, который сначала восстанавливают с помощью газообразного аммиака с последующей обработкой промежуточного продукта водородом. При этом получают кристаллиты вольфрама с размерами до ~30 нм. Паравольфрамат применяют также в процессе восстановления с образованием оксида вольфрама [3], который обрабатывают в кислом растворе и далее восстанавливают его сухим водородом до получения вольфрамового порошка. Полученный порошок с хорошими физико-механическими свойствами используют при изготовлении вольфрамовой проволоки. Интересный способ получения порошка вольфрама был предложен в [4], по которому осуществляют плазменное восстановление триоксида вольфрама (WO3). Были оценены три конфигурации плазмы: полый катод с порошком, погруженным в плазму, полый катод без прямого контакта между плазмой и порошком и реактор с псевдоожиженным слоем. Опыты проводились в сухом водороде при давлении 700 Па, при температуре 800–1000°С с использованием плазмы, генерируемой постоянным током. Быстрое восстановление WO3 наблюдалось при погружении порошка в плазму. В отсутствие прямого контакта между порошком и плазмой требовалось длительное время восстановления. Опыты с плазмой в псевдоожиженном слое с коротким временем обработки приводили к тому, что частицы показывали различные уровни восстановления. В [5, 6] при получении порошка вольфрама в качестве исходного сырья используют шеелитовый концентрат. Из шеелитового концентрата [5] после его кислотного выщелачивания с добавлением хелатов осаждают соли вольфрама, затем оксид вольфрама восстанавливают водородом до порошка металла. В работе [6] изучены условия получения порошка вольфрама разложением шеелитового концентрата в среде солевых расплавов и восстановлением образующегося вольфрамата натрия алюминием. Установлено, что выход порошка вольфрама составляет 95%, при чистоте вольфрама – 97%.
Порошок молибдена получают восстановлением парамолибдата аммония в две стадии. На первой стадии его восстанавливают газообразным аммиаком с получением промежуточного соединения, которое на второй стадии восстанавливают водородом. При этом в порошке молибдена примеси не превышают 0.05% [7]. Авторами работы [8] разработан процесс получения микрокристаллических порошков молибдена [(NH4)6Mo7O24 ⋅ 4H2O] и рения [NH4ReO4] высокой чистоты путем прямого одностадийного восстановления соединений молибдена и рения в водородно-азотных средах. Выявлено влияние технологических параметров на качество целевых продуктов. Определен оптимальный режим процесса восстановления, обеспечивающий производство микрокристаллических порошков молибдена и рения. При получении порошков металлов в [9, 10] используют металлотермический метод. В [9] исследованы условия восстановления оксида молибдена до металлического порошка с использованием алюминия и магния в расплаве хлорида натрия. Установлено, что для достижения выхода порошка молибдена 95–97% необходимо превышение восстановителя ~ на 30% по отношению к расчетному. В работе [10] реактор с загруженным NaCl нагревают с образованием хлоридного расплава и растворяют в нем вольфрамат натрия. Далее в реактор добавляют порошок магния, который взаимодействует с оксидным соединением вольфрама и восстанавливает его до металла в расплаве хлорида натрия. Затем расплав сливают, отстоявшийся порошок вольфрама отмывают от солей до нейтрального состояния и сушат. В [11, 12] при получении порошков металлов используют электролитический метод. При получении порошков молибдена и рения в завершающей стадии технологического процесса применяют электролитический метод разложения фторидов этих металлов в фторидных солях щелочных металлов. Порошки титана в [12] получают электролизом тетрафторида титана во фторидном расплаве. По мнению авторов работ [11, 12] применение данных способов в промышленности позволит исключить загрязнение окружающей среды.
В работе [13] подготовлен обзор по традиционным и перспективным методам получения порошков титана. Традиционные методы производства титана имеют высокие производственные затраты. Целью обзора является анализ современных методов производства порошка титана и изучение новых методов непрерывного прямого синтеза, который в настоящее время разрабатывается и расширяется.
По мере накопления экспериментальных данных, полученных при исследовании диспергирования алюминия, выявлены основные закономерности этого процесса [14]. В зоне искрового разряда, как известно, развивается высокая температура, при которой, происходит не только диспергирование металла, но и термическое разложение рабочего раствора с образованием, в том числе атомарного кислорода (АК). Авторами работы [14] показано, что на состав продуктов диспергирования существенное влияние оказывает природа и концентрация рабочего раствора, электропараметры используемого в процессе импульсов тока. При образовании в процессе АК в небольших количествах, АК взаимодействует с диспергированными частицами металла с получением промежуточного продукта, который в объеме реагирует с водой с образованием двух модификаций гидроксида алюминия: байерита [15–17] и бемита [17–19]. В случае получения АК в значительных количествах, АК окисляет металлические частицы с образованием на поверхности защитной оксидной пленки, которая предохраняет металл от взаимодействия с окружающей средой. В этих условиях в процессе получают порошок металла, не обладающий пирофорными свойствами [20].
В настоящей работе исследован процесс диспергирования вольфрама, титана, молибдена в импульсных разрядах в водных растворах азотной и серной кислоты с получением порошков металлов.
ЭКСПЕРИМЕНТАЛЬНАЯ ЧАСТЬ
Опыты проводили на установке и по методике, описанной ранее в [14]. Диспергирование металла с использованием генератора импульсов тока (мощностью 1 кВт) позволяет получать в течение одного часа порошки металлов от нескольких десятков до сотен граммов. Необходимо отметить, что производительность диспергирования металлов существенно зависит от поверхности электродов, участвующих в процессе диспергирования. В опытах применяли электроды с поверхностью равной 12 см2. После диспергирования металла, полученная в процессе пульпа (смесь рабочего раствора и диспергированного металла) подвергалась фильтрации. Фильтрат возвращался в емкость исходного рабочего раствора, а отфильтрованный осадок высушивался на воздухе. Далее с помощью дифрактометра (ДРОН – 3) определялся фазовый состав полученного осадка. Форма и размеры диспергированных частиц металла определялись с помощью электронного микроскопа (ЭВМ – 100ЛМ) Предварительно порошки исследуемых металлов суспендировали в изопропиловом спирте, затем суспензию диспергировали на ультразвуковом диспергаторе УЗДН-1 и далее наносили на органическую пленку-подложку. Фотографирование образцов проводили при разных увеличениях. По полученным снимкам определяли форму и размеры исследуемых кристаллитов. Чтобы не внести примеси в полученный продукт в процессе диспергирования применяли электроды из искомого металла. Как отмечалось, в зоне искрового разряда развивается высокая температура, достигающая ~10 000°С. В объеме реактора, за счет регулирования скорости подачи рабочего раствора, температура не превышала 40°С. Вследствие большой разницы температур в зоне искрового разряда и в объеме реактора, происходило сверхбыстрое охлаждение диспергированного металла, приводящего к образованию частиц ультрадисперсной структуры.
Большой интерес, проявляемый исследователями к данному способу получения металлических порошков, способствовал разработке и созданию новых конструкций реакторов и генераторов импульса тока. Конструкции реакторов, описанные в [21, 22], позволят резко повысить производительность процесса диспергирования металлов. Авторами [23] разработан и создан генератор импульсов тока мощностью 20 кВт, который прошел испытания. Продолжаются работы по разработке генераторов еще большей мощности (50–80 кВт). Применение в производстве разработанных реакторов в сочетании с генераторами большей мощности приведут к получению сотни–тысячи килограмм порошка в течение одного часа.
РЕЗУЛЬТАТЫ И ОБСУЖДЕНИЕ
Установлено, что частицы диспергированных металлов имеют шарообразную форму, размеры которых, в зависимости от природы металлов колеблются в пределах 20–100 нм. Со временем кристаллиты металлов коагулируют во вторичные агрегаты (зерна порошков металла) и достигают размеров 0.3–5.0 мкм. Вторичные агрегаты содержат в небольших количествах некоагулированные кристаллиты металла (15–20%). В связи с чем их часто называют наноструктированные порошки металлов.
Отфильтрованный из пульпы осадок сушат на воздухе, как при комнатной температуре, так и при температуре (до +80°С.) Состав полученного металлического порошка практически не зависит от температуры просушивания. Это может свидетельствовать о том, что диспергированные металлические частицы уже в зоне искрового разряда окисляются АК с образованием на поверхности оксидной пленки, предохраняющей взаимодействие кристаллитов металла с окружающей средой.
Применением при диспергировании алюминия импульсов тока с частотой (F) равной 1000 Гц достигалось протекание процесса с оптимальной производительностью [14]. В противоположность этому при подаче на электроды импульсов тока F = 1000 Гц производительность диспергирования исследуемых металлов (молибдена, титана, вольфрама) оказывалась небольшой, а иногда процесс вовсе прекращался. В естественных условиях исследуемые металлы образуют на поверхности оксидные пленки с низким контактным сопротивлением. Вследствие этого возникает необходимость определения оптимальных параметров импульсов тока, подаваемых на электроды в процессе диспергирования. Данные по влиянию подаваемого на электроды частоты импульсов тока на производительность процесса диспергирования металлов приведены на рис. 1.
Рис. 1.
Зависимость производительности процесса (N) вольфрама (1), молибдена (2), титана (3) при диспергировании их в растворе кислоты от частоты импульса тока, подаваемого на электроды. Рабочий раствор: 1 – 0.12 М H2SO4, 2, 3 – 0.09 М HNO3.
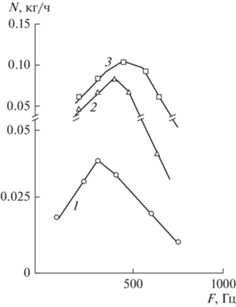
Из рис. 1. видно, что с повышением частоты импульсов тока производительность диспергирования металлов сначала растет, достигает максимального значения, а затем падает. Такой ход зависимости N–F кривых при диспергировании металлов, по-видимому, связан, как с разным распределением поступающей энергии на поверхности и в объеме металла, так и с утечкой тока по не эродирующим контактам. Наблюдаемое некоторое смешение производительности процесса диспергирования, может быть вызвано, как с природой самих металлов, так и с образующейся на их поверхности оксидной пленкой. При этом в процессе диспергирования получаются порошки металлов. В отличие от существующей в литературе точки зрения о трудности диспергирования металлов, образующих на поверхности оксидные пленки с низким контактным сопротивлением при использовании в процессе электродов из рассматриваемых металлов, полученные экспериментальные данные позволяют заключить, что при условии подачи на электроды импульса тока оптимальной частоты эти металлы также подвергаются диспергированию.
В [14] было высказано предположение, что получение порошков металлов при их диспергировании в слабых растворах кислот происходит вследствие образования в процессе большего количества атомарного кислорода (АК). Ранее расчетами было показано, что энергия образования атомарного кислорода (ΔЕ) при терморазложении ионов гидроксония имеет гораздо меньшее значение ($\Delta Е_{{{{{\text{Н}}}_{{\text{3}}}}{\text{О}}}}^{ + }$ = 210 кДж/моль) по сравнению с $\Delta {{F}_{{{{{\text{H}}}_{{\text{2}}}}{\text{O}}}}}$ равной 910 кДж/моль. Другими словами, терморазложение ионов гидроксония будет идти легче с получением большего количества АК, окисляющего диспергированные металлические частицы с образованием на поверхности защитной оксидной пленки, с получением порошков металлов.
Для выяснения степени окисления диспергированных металлических частиц были определены термодинамические возможности протекания этих реакций с образованием оксидов. Как отмечалось в [14] окисление частиц алюминия происходит атомарным кислородом. При расчетах были применены данные, взятые из [24, 25]. По аналогии, описанной в [26] методике расчеты проводили с использованием в реакциях атомарного кислорода. Результаты расчетов приведены в табл. 1.
Таблица 1.
Изменение стандартной энергии Гиббса для реакций взаимодействия диспергированных металлических частиц с кислородом
№ п/п | Реакция | Изменение стандартной энергии Гиббса (ΔG), кДж/моль |
---|---|---|
1 | W(кр.) + 2О(г.) = WО2(кр.) | –972.4 |
2 | W(кр.) + 3О(г.) = WО3(кр.) | –1456.3 |
3 | W(кр.) + 1.5О2(г.)=WО3(кр.) | –764.0 |
4 | Ti + О(г.) = TiO(кр.) | –716.8 |
5 | Ti + 2О(г.) = TiO2(кр.) | –1362.3 |
6 | Ti + О2(г.) = TiO2(кр.) | –885.3 |
7 | Mo + 2О(г.) = MoO2 (кр). | –997.9 |
8 | Mo + 3О(г.) = MoO3 (кр.) | –1371.5 |
9 | Mo + 1.5О(г.) = MoO3 (кр.) | –676.3 |
Из табл. 1 видно, что, более вероятным является протекание реакций 2, 5, 8 для которых при стандартных условиях изменение стандартной энергии Гиббса значительно меньше, чем для реакций 1, 4, 7. Из таблицы также следует, что во всех случаях окисление диспергированных металлических частиц происходит с образованием устойчивых форм оксидов металлов.
Для выяснения в какой форме кислород участвует в окислении диспергированных металлических частиц с образованием на их поверхности оксидной пленки показано, что термодинамическая вероятность протекания реакций окисления частиц металла имеет следующие значения, которые представлены в табл. 1.
Как видно из табл. 1, изменение энергии Гиббса имеет отрицательную величину для всех реакций, в которых в процессе окисления участвуют, как атомарный, так и молекулярный кислород. Однако наиболее вероятно протекание реакций 2, 5, 8 для которых ΔG имеет гораздо меньшее значение, чем для реакций 1, 4, 7. Образующиеся в процессе диспергированные частицы металла реагируют только с атомарным кислородом (АК) и подтверждают ранее высказанные предположения участия в окислении диспергированных металлических частиц атомарного кислорода [14].
ЗАКЛЮЧЕНИЕ
Таким образом, экспериментальные и расчетные данные показывают, что при диспергировании вольфрама, титана, молибдена в импульсных разрядах в водных растворах кислот в процессе образуются в основном порошки этих металлов. Полученные результаты подтверждают ранее высказанные предположения об образовании на поверхности металлических частиц защитной оксидной пленки, предохраняющей частицы от взаимодействия с окружающей средой и приводящей в конечном итоге к получению порошков металлов, не обладающих пирофорными свойствами.
Список литературы
Либенсон Г.А., Лопатин В.Ю., Комарницкий Г.В. Процессы порошковой металлургии. Т. 1. Производство металлических порошков. М.: МИСИС, 2001. 368 с.
Патент RU 2448809. Воробьева М.В., Едренникова Е.Е., Иванов В.В. и др. Способ получения порошка вольфрама. Опубликовано 27.04.2012.
Патент RU 2362654. Калмыкова Л.П., Довженко Н.Н., Ковтун О.П. и др Способ получения вольфрамового порошка. Опубликовано 27.07.2009.
Silva da G.G., Alves C., Hajek V. et al. Production of tungsten powder by plasma reduction of WO3: Structure and morphology. // INT J POWDER METALL. 2005. V. 41. № 4. P. 43–50.
Gurmen S., Orhan C., Timur S. Tungsten powder production from scheelite concentrates // Met. 2003. V.57. № 12. P.789–793.
Гостищев В.В. Физико-химические аспекты получения порошка вольфрама металлотермией шеелитового концентрата в ионных расплавах // Известия вузов. Цветная металлургия. 2015. № 3. С. 22–24.
Патент RU 2367543 Воробьева М.В., Едренникова Е.В., Иванов В.В. и др. Способ получения нанодисперсных порошков молибдена. Опубликовано 20.09.2009.
Rakova N.N., Edrennikova E.E., Vorob`eva M.V. et al. Production of high purity microcrystalline molybdenum and rhenium powders by reduction in hydrogen – nitrogen media. // RUSS J NON-FERR MET+. 2011. V. 52. № 6. P. 532-537. https://doi.org/10.3103/S1067821211060113
Gostishev V.V., Khosen R.I., Khimukhin S.N. et al. Obtaining molybdenum powder metallothermy of its compounds in sodium chloride melt // RUSS J NON-FERR MET+. 2010. V.51. № 6. P. 490–493. https://doi.org/10.3103/S1067821210060106
Гостищев В.В., Бойко В.Ф. Получение порошков молибдена и вольфрама. // Химическая технология. 2006. № 8. С. 15–17.
Карелин В.А., Ковалев С.В. Синтез высокочистого порошка молибдена электролитическим методом из фторидных расплавов. // Изв. Томск. Политех. Унив. 2005. Т. 308. № 3. С. 97–100.
Сорокина Е.А., Карелин В.А. Применение фторидных расплавов для получения титана из фторидных расплавов. // Успехи современного естествознания. 2014. № 8. С. 82–87.
McCracken C.G., Motchenbacher C., Barbis D.P. Review of titaniumpowder production methods. // INT J POWDER METALL. 2010. V. 46. № 5. P. 19–26.
Bayramov R.K., Somova Yu.Yu. Mechanism of electric spark dispersion of aluminum in aqueous solutions. // Russ. J. Inorg. Chem. 2014. V. 5. № 4. P. 368–372. https://doi.org/10.1134/S0036023614040020
Байрамов Р.К., Ведерникова Н.Р., Ермаков А.И. Электроискровое диспергирование алюминия и его последующая гидратация // Журн. прикладной химии. 2001. Т. 74. № 7. С. 1703–1705.
Ishibashi W., Araki N., Kishimoto K. et al. Method of producing Pure Alumina by Spark Discharge process at the Characteristics Thetoret // Ceramics Jap. 1971. V. 6. P. 461–463.
Ishibashi W. The Reaction between Powder and Liquid Medium at Spark Discharge Point // J. Jap. Soc. Powd. and Powd. Met. 1977. V. 24. P. 113–117. https://doi.org/10.2497/JJSPM.24.113
Патент СССР 919278. Байрамов Р.К., Сабанин А.В., Горожанкин Э.В. и др. Способ получения псевдобемитной гидроокиси алюминия. Опубликовано 07.12.81.
Патент СССР 592753. Цой А.Д., Петренко Б.Я., Асанов У.А. и др. Способ получения гидроокиси алюминия. Опубликовано 15.02.78.
Патент СССР 1548950. Байрамов Р.К. Способ получения алюминиевого порошка. Опубликовано 08.11.89.
Патент RU 2255837. Магницский Я.Ю., Козярук О.И., Журавель С.Н. Устройство для электроэрозионного диспергирования металлов. Опубликовано 07.10.2005.
Патент RU 2200589. Тарасов В.И., Козярук О.И., Фоминский Л.П. Устройство для электроэрозионного диспергирования металлов. Опубликовано 15.11.93.
Патент СССР 1197066. Милях А.Н., Щерба А.А., Муратов В.А. и др. Генератор импульсов для электроэрозионного диспергирования токопроводящих материалов. Опубликовано 12.07.85.
Справочник химика. Т. 1. М. 1982. ГНТИХЛ. 1071 с.
Краткий справочник физико-химических величин / Под ред. Равделя А.А., Пономаревой А.М. Л. Химия. 1983. 231 с.
Байрамов Р.К., Бугров А.В. Термодинамическая вероятность протекания возможных реакций в зоне искрового разряда // Цветные металлы. 2009. № 12. С. 87–90.
Дополнительные материалы отсутствуют.
Инструменты
Теоретические основы химической технологии