Теоретические основы химической технологии, 2022, T. 56, № 5, стр. 607-614
Неадиабатические схемы экстрактивной ректификации смеси ацетон–хлороформ–н-бутанол
Д. Г. Рудаков a, *, П. С. Клаузнер a, Е. А. Анохина a, А. В. Тимошенко a
a МИРЭА – Российский технологический университет
Москва, Россия
* E-mail: rudakov@mirea.ru
Поступила в редакцию 05.04.2021
После доработки 05.04.2022
Принята к публикации 28.05.2022
- EDN: IJTGBD
- DOI: 10.31857/S0040357122050189
Аннотация
Проведена оценка энергетической эффективности применения неадиабатической ректификации в процессе экстрактивной ректификации смеси ацетон–хлороформ–н-бутанол с диметилформамидом в качестве разделяющего агента. Рассмотрено два варианта организации теплоинтеграции: 1) между колонной регенерации разделяющего агента и экстрактивной колонной; 2) между колонной регенерации, экстрактивной колонной и колонной выделения хлороформа. Показано, что применение схем неадиабатической ректификации позволяет снизить приведенные энергетические затраты на 7.4–12.7% при теплоинтеграции между колоннами экстрактивной ректификации и регенерации диметилформамида, а в случае теплоинтеграции всех колонн схемы – до 20%, по сравнению с исходной схемой.
ВВЕДЕНИЕ
Экстрактивная ректификация (ЭР) – наиболее широко распространенный метод разделения азеотропных смесей и смесей компонентов с относительной летучестью близкой к 1. Известно, что данный метод, также как и обычная ректификация, обладает низкой термодинамической эффективностью, и, как следствие, является крупным потребителем тепловой энергии. Повышение энергоэффективности процесса ректификации позволяет получить существенный экономический эффект, поэтому в химической технологии данному вопросу уделяется большое внимание. Один из подходов к снижению энергозатрат предполагает передачу тепла, отводимого из укрепляющей секции колонны, в отгонную секцию той же колонны. Однако его реализация требует искусственного повышения температуры потоков за счет их сжатия. На базе этой концепции предложено достаточно много различных вариантов схем ректификации с теплоинтеграцией. Самым простым и очевидным вариантом внешней тепловой интеграции являются схемы с тепловым насосом [1–5].
В качестве альтернативы схемам с тепловым насосом были предложены схемы с применением внутренней теплоинтеграции [6, 7], называемые в англоязычной литературе “HIDiC”, которые сочетают в себе концепцию схем с тепловым насосом и преимущества схем неадиабатической ректификации. Вместо передачи теплоты с верха колонны в куб, как в тепловом насосе, теплопередача в HIDiC осуществляется между тарелками отгонной и укрепляющей секций колонны, обеспечивая непрерывный ступенчатый подвод или отвод теплоты в каждой из секций. В этом случае, для обеспечения положительной разности температур между соответствующими тарелками, укрепляющая секция должна работать при более высоком давлении, чем отгонная секция. Концепция внутренней теплоинтеграции подробно рассмотрена авторами [8] в 1977 г., а первые работы, посвященные этому вопросу, были опубликованы еще раньше [9, 10]. Преимущества ряда схем с HIDiC были подтверждены, в том числе, и экспериментально [11]. Авторами [12] показано, что, с термодинамической точки зрения, конфигурации HIDiC могут быть более эффективными, чем схемы с тепловым насосом. Однако они пока не нашли широкого применения в промышленности из-за сложности организации эффективного теплообмена между двумя секциями колонны. Для решения этой проблемы предлагается использовать концентрические, многотрубные, разделенные перегородками с теплообменными панелями [13] или иные [14] конфигурации. Дополнительные трудности практической реализации схем с HIDiC связаны со сложной управляемостью процесса [15, 16], особенно в случае организации теплоинтеграции между паровым потоком дистиллята и питанием колонны [17, 18].
В качестве альтернативы схемам с тепловым насосом или с внутренней теплоинтеграцией можно предложить схемы неадиабатической ректификации, которые подразумевают внешний подвод (или отвод) теплоты на тарелки колонн за счет интеграции тепла потоков между различными аппаратами схемы. В этом случае нет необходимости в создании конструктивно сложных и дорогих аппаратов – для организации теплоинтеграции достаточно установить обычные циркуляционные теплообменники. Применение схем неадиабатической экстрактивной ректификации в настоящее время рассмотрено явно недостаточно [19]. В данной работе проведена оценка энергетической эффективности применения неадиабатической ректификации в схеме разделения смеси ацетон–хлороформ–н-бутанол с диметилформамидом в качестве разделяющего агента.
РАСЧЕТНАЯ ЧАСТЬ
Методы исследования. В качестве основного метода исследования применяли математическое моделирование и вычислительный эксперимент, все расчеты проводили в программном комплексе AspenPlus v.12.1. Моделирование и оптимизация традиционной схемы (Рис. 1) ЭР смеси ацетон–хлороформ–н-бутанол с диметилформамидом были проведены авторами работы [20], эти данные были взяты нами в качестве исходных (табл. 1) для разработки схем неадиабатической ректификации.
Рис. 1.
Традиционная схема ЭР из двухотборных колонн: К1 – экстрактивная колонна, К2 – колонна выделения хлороформа, К3 – колонна регенерации ДМФА 1 – исходная смесь, 2 – разделяющий агент, 3 – ацетон, 4 – хлороформ, 5 – н-бутанол.
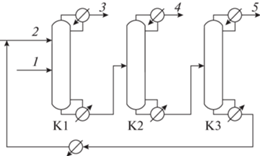
Таблица 1.
Оптимальные рабочие параметры традиционной схемы ЭР из двухотборных колонн [20]
Колонны | К1 | К2 | К3 |
---|---|---|---|
Nsum | 22 | 30 | 44 |
NF | 8 | 10 | 13 |
NS | 4 | – | – |
Qreb, кВт | 342.3 | 136.7 | 526.3 |
Qcond, кВт | –211.6 | –131.7 | –526.7 |
R | 1.09 | 12.35 | 22.20 |
Tcond, °С | 56.1 | 61.1 | 117.3 |
Treb, °C | 144.9 | 149.6 | 151.6 |
S, кг/ч | 2180 | – | – |
TS, °С | 60 | – | – |
Qsum, кВт | 1005.3 |
В качестве модели описания парожидкостного равновесия в системе ацетон–хлороформ–н-бутанол–диметилформамид выбрано уравнение NRTL с параметрами, опубликованными авторами [20].
Одним из ключевых условий для организации схем неадиабатической ректификации является положительная разность температуры потока, теплоту которого предполагается использовать (источник тепла), и температуры на тарелках отгонной секции колонн, в которые это тепло направлено (приемник тепла). Эта разность температур должна обеспечить достаточную движущую силу процесса теплообмена. Исходя из этого, при моделировании схем ΔT между источником и приемником тепла принимали равной не менее 10°С. С целью достижения наилучших условий теплопередачи выбирали такой режим работы теплообменника, чтобы в нем происходила полная конденсация потока пара с горячей стороны, и испарение жидкости с холодной. Для предварительной оценки возможности реализации схемы неадиабатической экстрактивной ректификации с заданными параметрами теплообмена и выбора необходимой степени сжатия E в компрессоре, были построены температурные профили для всех колонн (Рис. 2) традиционной схемы.
Рис. 2.
Профили температур по высоте колонн схемы ЭР из двухотборных колонн: а – экстрактивная колонна К1, б – колонна выделения хлороформа К2, в – колонна регенерации К3, NT – номер тарелки, NF – тарелка питания.
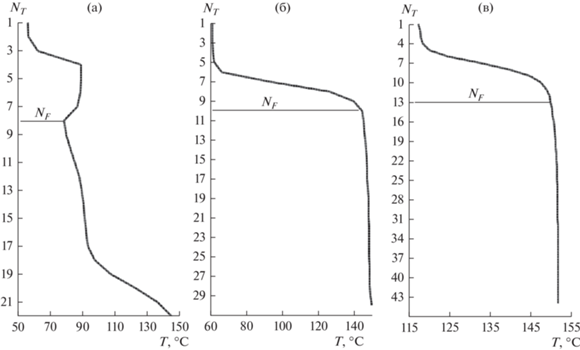
Видно, что наиболее высокие температуры наблюдаются в укрепляющей секции колонны К3, следовательно, именно теплоту потока пара, выходящего с ее верха, целесообразно использовать для обогрева отгонных секций других колонн схемы. Здесь можно рассмотреть несколько вариантов теплоинтеграции:
1) между колоннами К3 и K1 посредством установки одного теплообменника (рис. 3а). Колонна К1 выбрана исходя из того, что затраты тепла в ее кипятильнике вносят более существенный вклад в общие энергозатраты схемы, чем энергозатраты в кипятильнике колонны К2;
Рис. 3.
Неадиабатические схемы ЭР: 1 – исходная смесь, 2 – разделяющий агент, 3 – ацетон, 4 – хлороформ, 5 – н‑бутанол.
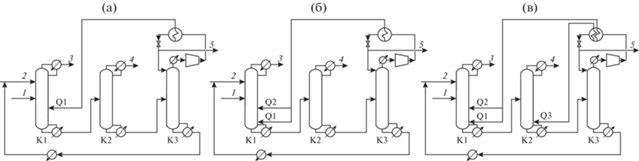
2) между колоннами К3 и K1 посредством установки двух теплообменников (организация ступенчатого подвода тепла для устранения зон возможного перегрева на тарелках, рис. 3б);
3) между колоннами К3 и K1 + К2, что является наиболее полным вариантом теплоинтеграции (рис. 3в).
Температура парового потока, выходящего с верха колонны К3 равна 117.3°С. Этого недостаточно для организации теплоинтеграции с отгонными секциями колонн К1 и К2 (см. рис. 2). Поэтому требуется установка компрессора с минимальной рабочей степенью сжатия E = 2.5 для вариантов (1) и (2) и степенью сжатия E = 3.0 для варианта (3), при этом температура потока пара после сжатия будет равна 155.1 и 164.2°С, соответственно. Для предотвращения возможной кавитации в компрессоре перед ним установлен дополнительный подогреватель, тепловая нагрузка которого обозначена QPH.
Определение оптимальных значений номера тарелки расположения циркуляционного теплообменника (NHE) и количества пропускаемой через него жидкости (SDHE), производили посредством комбинации методов последовательно квадратичного программирования и утилиты автоматического перебора Sensitivity Analysis, встроенных в программный комплекс Aspen Plus. Критерий оптимизации – энергозатраты в кипятильниках колонн Qreb.
Результаты оптимизации NHE и SDHE для варианта теплоинтеграции (1) приведены в табл. 2.
Таблица 2.
Определение NHE и SDHE для варианта теплоинтеграции (1) в колонне К1
NHE | SDHE, кг/ч | QHE, кВт | R | Qcond, кВт | Qreb, кВт |
---|---|---|---|---|---|
15 | 2815.2 | 415.5 | 2.46 | –350.1 | 65.2 |
16 | 2650.9 | 390.7 | 2.21 | –324.5 | 64.4 |
17 | 2406.7 | 354.5 | 1.85 | –287.8 | 63.9 |
18 | 2276.1 | 335.1 | 1.66 | –268.7 | 64.2 |
19 | 2162.8 | 318.5 | 1.51 | –253.5 | 65.6 |
20 | 2056.2 | 303.1 | 1.40 | –242.3 | 69.8 |
Из табл. 2 видно, что оптимальной точкой подвода теплоты в колонну К1 является тарелка 17. Поскольку неадиабатические схемы ЭР существенно отличаются от традиционных наличием “горячих” компрессоров, а также дополнительного теплообменного оборудования, то для сопоставления схем целесообразно использовать критерий приведенных энергетических затрат (Qcons) [21]:
где: Qsum – суммарные энергетические затраты в кипятильниках колонн, а Wcomp – потребляемая компрессором мощность.Оптимальные рабочие параметры неадиабатической схемы ЭР для варианта теплоинтеграции (1) приведены в табл. 3.
Таблица 3.
Рабочие параметры неадиабатической схемы ЭР для варианта теплоинтеграции (1)
Колонны | К1 | К2 | К3 |
---|---|---|---|
Nsum | 22 | 30 | 44 |
NHE | 17 | – | – |
Qreb, кВт | 63.9 | 136.7 | 526.3 |
Qcond, кВт | –287.8 | –131.7 | –595.4 |
R | 1.85 | 12.35 | 21.9 |
QНЕ, кВт | 354.5 | – | – |
Tcond/comp, °С | 56.1 | 61.1 | 155.1 |
Treb, °C | 144.9 | 149.6 | 151.6 |
QPH, кВт | – | – | 14.0 |
Ecomp | – | – | 2.5 |
Wcomp, кВт | – | – | 63.1 |
Qcons, кВт | 930.2 |
Далее был рассмотрен второй вариант теплоинтеграции, который предполагает подвод теплоты в К1 на два уровня. Результаты определения оптимальной совокупности номеров тарелок подвода теплоты ${\text{N}}_{{{\text{HE}}}}^{{\text{1}}}$ и ${\text{N}}_{{{\text{HE}}}}^{{\text{2}}}$, а также количества отбираемой жидкости ${\text{SD}}_{{{\text{HE}}}}^{{\text{1}}}$ и ${\text{SD}}_{{{\text{HE}}}}^{{\text{2}}}$ для варианта теплоинтеграции (2) приведены в табл. 4.
Таблица 4.
Определение ${\text{N}}_{{{\text{HE}}}}^{{\text{1}}}$, ${\text{N}}_{{{\text{HE}}}}^{{\text{2}}}$ и ${\text{SD}}_{{{\text{HE}}}}^{{\text{1}}}$, ${\text{SD}}_{{{\text{HE}}}}^{{\text{2}}}$ для варианта теплоинтеграции (2) в колонне К1
${\text{N}}_{{{\text{HE}}}}^{{\text{2}}}$ | ${\text{N}}_{{{\text{HE}}}}^{{\text{1}}}$ | ${\text{SD}}_{{{\text{HE}}}}^{{\text{1}}}$, кг/ч | ${\text{SD}}_{{{\text{HE}}}}^{{\text{2}}}$, кг/ч | $Q_{{{\text{HE}}}}^{{\text{1}}}$, кВт | $Q_{{{\text{HE}}}}^{{\text{2}}}$, кВт | R | Qcond, кВт | Qreb, кВт |
---|---|---|---|---|---|---|---|---|
13 | 19 | 892 | 2552 | 132.1 | 364.1 | 3.02 | –406.5 | 41.0 |
20 | 965 | 2641 | 143.3 | 375.6 | 3.10 | –414.9 | 26.6 | |
21 | 965 | 2640 | 142.1 | 375.4 | 3.11 | –415.7 | 27.8 | |
14 | 19 | 864 | 2221 | 127.8 | 316.9 | 2.56 | –359.9 | 45.8 |
20 | 914 | 2299 | 135.6 | 326.3 | 2.60 | –364.2 | 33.0 | |
21 | 1025 | 2292 | 152.6 | 324.4 | 2.54 | –357.7 | 11.4 | |
15 | 19 | 828 | 1948 | 122.3 | 280.2 | 2.19 | –322.7 | 50.8 |
20 | 846 | 2012 | 125.3 | 287.1 | 2.18 | –321.5 | 39.7 | |
21 | 963 | 2056 | 143.2 | 291.2 | 2.21 | –325.0 | 21.3 |
Из табл. 4 видно, что оптимальной точкой верхнего подвода теплоты ($Q_{{{\text{HE}}}}^{{\text{2}}}$) в отгонную секцию колонны К1 является тарелка 14. При этом второй ($Q_{{{\text{HE}}}}^{{\text{1}}}$) подвод теплоты оптимально направить на нижнюю тарелку К1. В результате за счет применения теплоинтеграции удалось снизить энергозатраты в кипятильнике К1 на 96.7%. Оптимальные рабочие параметры неадиабатической схемы ЭР для варианта теплоинтеграции (2) приведены в табл. 5.
Таблица 5.
Рабочие параметры неадиабатической схемы ЭР для варианта теплоинтеграции (2)
Колонны | К1 | К2 | К3 |
---|---|---|---|
Nsum | 22 | 30 | 44 |
${\text{N}}_{{{\text{HE}}}}^{{\text{1}}}$ | 21 | – | – |
${\text{N}}_{{{\text{HE}}}}^{{\text{2}}}$ | 14 | – | – |
Qreb, кВт | 11.4 | 136.7 | 526.3 |
Qcond, кВт | –357.7 | -131.7 | -595.4 |
R | 2.54 | 12.35 | 21.9 |
$Q_{{{\text{HE}}}}^{{\text{1}}}$, кВт | 152.6 | – | – |
$Q_{{{\text{HE}}}}^{{\text{2}}}$, кВт | 324.4 | – | – |
Tcond/comp, °С | 56.1 | 61.1 | 155.1 |
Treb, °C | 144.9 | 149.6 | 151.6 |
QPH, кВт | – | – | 14.0 |
Ecomp | – | – | 2.5 |
Wcomp, кВт | – | – | 63.1 |
Qcons, кВт | 877.7 |
На следующем этапе работы был рассмотрен вариант теплоинтеграции, максимально возможный для исследуемой схемы ЭР. Он предполагает двухуровневый подвод теплоты в К1 и подвод теплоты в К2. Оптимальные рабочие параметры экстрактивной колонны К1 были такими же, как во втором варианте теплоинтеграции. Процедура оптимизации колонны К2 в целом аналогична процедуре, рассмотренной для колонны К1. Отметим, что при реализации теплоинтеграции с колонной К2 появляется ряд ограничений. Во-первых, распределение температур в К2 не позволяет использовать прежнюю степень сжатия в компрессоре, ее необходимо повысить до E = 3. При этом возрастает мощность компрессора и тепловая нагрузка его вспомогательного предварительного нагревателя. Однако с 595 до 615 кВт возрастает и количество теплоты, которое можно направить для обогрева отгонных секций колонн К1 и К2. На обогрев колонны К1 при выбранном режиме ее работы расходуется 477 кВт, следовательно, на обогрев К2 можно направить не более 138 кВт. Исходя из этого было определено количество отбора жидкости ${\text{SD}}_{{{\text{HE}}}}^{{\text{3}}}$ = 900 кг/ч, циркулирующей через теплообменник с тем условием, чтобы количество теплоты на ее полное испарение не превысило 138 кВт. Определение оптимальной тарелки подвода теплоты (${\text{N}}_{{{\text{HE}}}}^{{\text{3}}}$) при фиксированном ${\text{SD}}_{{{\text{HE}}}}^{{\text{3}}}$ для колонны К2 приведено в табл. 6.
Таблица 6.
Определение ${\text{SD}}_{{{\text{HE}}}}^{{\text{3}}}$ в К2 для варианта теплоинтеграции (3)
${\text{N}}_{{{\text{HE}}}}^{{\text{3}}}$ | R | Qcond, кВт | Qreb, кВт |
---|---|---|---|
25 | 14.23 | –149.7 | 18.4 |
26 | 13.81 | –145.6 | 14.2 |
27 | 13.44 | –142.0 | 10.7 |
28 | 13.13 | –138.9 | 7.6 |
29 | 12.85 | –136.2 | 4.9 |
Из табл. 6 видно, что подвод теплоты В К2 оптимально направить на нижнюю тарелку, что обеспечит снижение нагрузки на ее кипятильник на 96.4% за счет теплоинтеграции между колоннами К3 и К2 и перехода к неадиабатической ректификации. В этом случае организации второй точки подвода теплоты (как это было для аппарата К1) не требуется. Итоговые оптимальные рабочие параметры неадиабатической схемы ЭР (вариант 3) приведены в табл. 7.
Таблица 7.
Рабочие параметры неадиабатической схемы ЭР для варианта с максимальной теплоинтеграцией
Колонны | К1 | К2 | К3 |
---|---|---|---|
Nsum | 22 | 30 | 44 |
${\text{N}}_{{{\text{HE}}}}^{{{\text{1(3)}}}}$) | 21 | 29 | – |
${\text{N}}_{{{\text{HE}}}}^{{\text{2}}}$ | 14 | – | – |
Qreb, кВт | 11.4 | 4.9 | 526.3 |
Qcond, кВт | –357.7 | –136.2 | –614.7 |
R | 2.54 | 12.85 | 21.9 |
$Q_{{{\text{HE}}}}^{{{\text{1(3)}}}}$, кВт | 152.6 | 136.3 | – |
$Q_{{{\text{HE}}}}^{{\text{2}}}$, кВт | 324.4 | – | – |
Tcond/comp, °С | 56.1 | 61.1 | 164.2 |
Treb, °C | 144.9 | 149.6 | 151.6 |
QPH, кВт | – | – | 21.0 |
Ecomp | – | – | 3.0 |
Wcomp, кВт | – | – | 80.1 |
Qcons, кВт | 803.9 |
ОБСУЖДЕНИЕ РЕЗУЛЬТАТОВ
В ходе проведенных исследований были рассмотрены три различных варианта теплоинтеграции между колоннами схемы ЭР смеси ацетон– хлороформ–н-бутанол с диметилформамидом в качестве разделяющего агента. Сопоставление предложенных схем неадиабатической ректификации с традиционной схемой ЭР из двухотборных колонн по критерию приведенных энергозатрат представлено в табл. 8. Снижение приведенных энергозатрат ∆Qcons рассчитывали по формуле:
(2)
$\Delta {{Q}_{{{\text{cons}}}}}~\,\, = ~{{({{Q}_{{{\text{sum}}}}}--{{Q}_{{{\text{cons}}}}})} \mathord{\left/ {\vphantom {{({{Q}_{{{\text{sum}}}}}--{{Q}_{{{\text{cons}}}}})} {{{Q}_{{{\text{sum}}}}}}}} \right. \kern-0em} {{{Q}_{{{\text{sum}}}}}}} \times 100\% ,$Таблица 8.
Энергетическая эффективность различных вариантов схем ЭР
Вариант схемы | RK1 | RK2 | $Q_{{{\text{cond}}}}^{{{\text{K1}}}}$, кВт | $Q_{{{\text{cond}}}}^{{{\text{K2}}}}$, кВт | Qcons (Qsum), кВт |
∆Qcons, % |
---|---|---|---|---|---|---|
Традиционная схема | 1.09 | 12.35 | –211.6 | –131.7 | (1005.3) | – |
Вариант (1) с теплоинтеграцией | 1.85 | 12.35 | –287.8 | –131.7 | 930.2 | 7.4 |
Вариант (2) с теплоинтеграцией | 2.54 | 12.35 | –357.7 | –131.7 | 877.7 | 12.7 |
Вариант (3) с теплоинтеграцией | 2.54 | 12.85 | –357.7 | –136.2 | 803.9 | 20.0 |
Из табл. 8 видно, что максимальное снижение приведенных энергозатрат обеспечивает вариант (3) неадиабатической схемы ЭР, который предполагает организацию теплоинтеграции колонны К3 с колоннами K2 и К1. Вместе с этим в колонне К1 возрастает флегмовое число и нагрузка на конденсатор, чего практически не наблюдается в колонне К2. Это объясняется тем, что при организации дополнительного подвода теплоты в отгонную часть экстрактивной колонны К1 снижается концентрация разделяющего агента ДМФА в жидкой фазе в экстрактивной секции (с 4 по 8 тарелки, см. рис. 4) примерно на 15% для варианта теплоинтеграции (1) и на 26% – для вариантов теплоинтеграции (2) и (3).
Рис. 4.
Профили концентраций ДМФА в жидкой фазе по высоте экстрактивной колонны К1: 1 – традиционная схема, 2 – вариант (1) теплоинтеграции, 3 – варианты (2) и (3) теплоинтеграции.
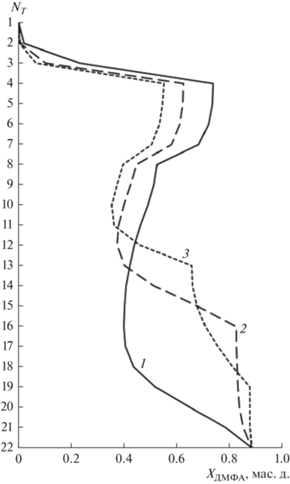
Такое снижение концентрации ДМФА в жидкой фазе приводит к некоторому ухудшению режима работы экстрактивной колонны, и для обеспечения заданного качества продуктовых потоков требуется повышение флегмового числа. Рост флегмового числа приводит к увеличению необходимого парового потока в колонне и, следовательно, к росту энергозатрат в конденсаторе. В свою очередь, увеличение парового потока в колонне приводит и к росту суммарного количества подвода теплоты, требуемого для его создания, на 18% для варианта теплоинтеграции (1) и на 30% – для варианта теплоинтеграции (2).
В случае применения теплоинтеграции технологическая схема несколько усложняется за счет появления дополнительных потоков между аппаратами и за счет использования горячего компрессора. Тем не менее, при выбранной степени сжатия E = 3 компрессор может быть одноступенчатым и, следовательно, его стоимость и стоимость технического обслуживания вполне приемлемы.
ЗАКЛЮЧЕНИЕ
В ходе проведенных исследований было установлено, что применение схем неадиабатической ректификации с теплоинтеграцией между различными колоннами позволяет снизить приведенные энергозатраты всей схемы на 7.4–20%. При этом энергозатраты в кипятильнике экстрактивной колонны удается снизить на 96.7%, а в колонне выделения хлороформа – на 96.4%. Важным преимуществом предложенного варианта схем неадиабатической ректификации является то, что теплоинтеграция осуществляется между различными колоннами схемы, что не требует существенного изменения их конструктивных параметров при модернизации действующих установок.
ОБОЗНАЧЕНИЯ
E | степень сжатия |
N | номер тарелки |
P | абсолютное давление, кПа |
Q | тепловая нагрузка, кВт |
R | флегмовое число |
S | расход разделяющего агента, кг/ч |
SD | отбор, кг/ч |
T | температура, °С |
W | потребляемая мощность, кВт |
ДМФА | диметилформамид |
ЭР | экстрактивная ректификация |
ИНДЕКСЫ
Список литературы
Tao S., Yue L., Haoshui Yu, Yang Ao, Shirui Sun, Weifeng S., Lee K.M., Jingzheng R. Improved design of heat-pump extractive distillation based on the process optimization and multi-criteria sustainability analysis // Computers and Chemical Engineering. 2022. V. 156. P. 107552. https://doi.org/10.1016/j.compchemeng.2021.107552
Yinggui X., Jinlong L., Qing Ye., Yudong Li. Design and optimization for the separation of tetrahydrofuran/isopropanol/water using heat pump assisted heat-integrated extractive distillation // Separation and Purification Technology. 2021. V. 277. P. 119498. https://doi.org/10.1016/j.seppur.2021.119498
Yinggui Xu, Jinlong Li, Qing Ye, Yudong Li. Energy efficient extractive distillation process assisted with heat pump and heat integration to separate acetonitrile/1,4-dioxane/water // Process Safety and Environmental Protection. 2021. V. 156. P. 144-159. https://doi.org/10.1016/j.psep.2021.09.042
Klauzner P.S., Rudakov D.G., Anokhina E.A., Timoshenko A.V. Use of Partially Thermally Coupled Distillation Systems and Heat Pumps for Reducing the Energy Consumption in the Extractive Distillation of an Isobutanol–Isobutyl Acetate Mixture Using Dimethylformamide // Theoretical Foundations of Chemical Engineering. 2020. V. 54. № 3. P. 397–406. https://doi.org/10.1134/S0040579520030070
Klauzner P.S., Rudakov D.G., Anokhina E.A., Timoshenko A.V. Optimal modes of side-section flow in heat-pump-assisted extractive distillation systems for separating allyl alcohol–allyl acetate mixtures with butyl propionate // Fine Chemical Technologies. 2021. V. 16. № 3. P. 213–224. /https://doi.org/10.32362/2410-6593-2021-16-3-213-224
Nakaiwa M., Huang K., Endo A., Ohmori T., Akiya T., Takamatsu T. Internally heat-integrated distillation columns: A review // Chemical Engineering Research and Design. 2003. V. 81 (A1). P. 162–177. https://doi.org/10.1205/026387603321158320
Olujic Z., Fakhri F., Rijke A., Graauw J., Jansens P.J. Internal heat integration: The key to an energy-conserving distillation column // Journal of Chemical Technology and Biotechnology. 2003. V. 78. № 2–3. P. 241–248. https://doi.org/10.1002/jctb.761
Mah R.S., Nicholas J.J., Wodnik R.B. Distillation with secondary reflux and vaporization: A comparative evaluation // AIChE Journal. 1977. V. 23. № 5. P. 651–658. https://doi.org/10.1002/aic.690230505
Teynham Woodward. Vapor Reheat Distillation // Principles of Desalination. 1966. P. 117–150. https://doi.org/10.1016/B978-0-12-395660-6.50009-4
Walker P.T., Newson I., Johnson K.D. Development of direct contact flash distillation concepts // Desalination. 1967. V. 2. № 7. P. 196–206. https://doi.org/10.1016/S0011-9164(00)84137-5
Naito K., Nakaiwa M., Huang K., Endo A., Aso K., Nakanishi T. Operation of a bench-scale ideal heat integrated distillation column (HIDiC): An experimental study // Computers & Chemical Engineering. 2000. V. 24. № 2–7. P. 495–499. https://doi.org/10.1016/S0098-1354(00)00513-5
Nakaiwa M., Huang K., Owa M., Akiya T., Nakane T., Sato M. Potential energy savings in ideal heat-integrated distillation column // Applied Thermal Engineering. 1998. V. 18. № 11. P. 1077–1087. https://doi.org/10.1016/S1359-4311(98)00030-1
Gadalla M., Jimenez L., Olujic Z., Jansens P.J. A thermohydraulic approach to conceptual design of an internally heat-integrated distillation column (i-HIDiC) // Computers and Chemical Engineering. 2007. V. 31. № 10. P. 1346–1354. https://doi.org/10.1016/j.compchemeng.2006.11.006
Hugill J.A., Hugill A., Anthony H.J. System for stripping and rectifying a fluid mixture. World Patent WO2003011418-A, 2003.
Nakaiwa M., Huang K., Owa M., Akiya T., Nakane T., Takamatsu T. Operating an ideal heat integrated distillation column with different control algorithms // Computers and Chemical Engineering. 1998. V. 22. P. 389–393. https://doi.org/10.1016/S0098-1354(98)00079-9
Nakaiwa M., Huang K., Endo A., Naito K., Owa M., Akiya T., Nakane T., Takamatsu T. Evaluating control structures for a general heat integrated distillation column (general HIDiC) // Computers and Chemical Engineering. 1999. V. 23. P. 851–854. https://doi.org/10.1016/S0098-1354(99)80209-9
Nakaiwa M., Huang K., Naito K., Endo A., Owa M., Akiya T., Nakane T., Takamatsu,T. A new configuration of ideal heat integrated distillation columns (HIDiC) // Computers and Chemical Engineering. 2000. 24(2–7), 239–245. https://doi.org/10.1016/S0098-1354(00)00464-6
Huang K.J., Shan L., Zhu Q.X., Qian J.X. A totally heat-integrated distillation column (THIDiC) – The effect of feed preheating by distillate // Applied Thermal Engineering. 2008. V. 28. № 8–9. P. 856–864. https://doi.org/10.1016/j.applthermaleng.2007.07.011
Nova-Rincón A., Ramos M.A., Gómez J.M. Simultaneous optimal design and operation of a diabatic extractive distillation column based on exergy analysis // International Journal of Exergy. 2015. V. 17. № 3. P. 287–312. https://doi.org/10.1504/IJEX.2015.070500
Anokhina E.A., Gracheva I.M., Akishin A.Yu., Timoshenko A.V. Acetone-chloroform-n-butanol mixture separation by the extractive distillation in schemes of two-outlet columns // Fine Chemical Technologies. 2017. V. 12. № 5. P. 34–46. (In Russ) https://doi.org/10.32362/2410-6593-2017-12-5-34-46
Aurangzeb Md., Jana A.K. Vapor recompression with interreboiler in a ternary dividing wall column: Improving energy efficiency and savings, and economic performance. App. Therm. Eng. 2018. V. 147. P. 1009–1023. https://doi.org/10.1016/japplthermaleng.2018.11.008
Дополнительные материалы отсутствуют.
Инструменты
Теоретические основы химической технологии