Высокомолекулярные соединения (серия А), 2022, T. 64, № 6, стр. 416-422
ВЛИЯНИЕ УСЛОВИЙ 3D-ПЕЧАТИ ПОЛИЭТИЛЕНТЕРЕФТАЛАТГЛИКОЛЯ НА МЕХАНИЧЕСКИЕ СВОЙСТВА ИЗДЕЛИЙ НА ЕГО ОСНОВЕ
С. В. Котомин a, b, *, Д. В. Крамарев a, c, И. М. Обидин a, c, С. В. Полунин c
a Институт нефтехимического синтеза им. А.В. Топчиева Российской академии наук
119991 Москва, Ленинский пр., 29, Россия
b Московский государственный технический университет им. Н.Э. Баумана
105005 Москва, ул. 2-я Бауманская, 5, Россия
c Российский химико-технологический университет им. Д.И. Менделеева
125047 Москва, Миусская пл., 9, Россия
* E-mail: svk@ips.ac.ru
Поступила в редакцию 19.07.2022
После доработки 25.08.2022
Принята к публикации 07.09.2022
- EDN: WXESSW
- DOI: 10.31857/S2308112022700213
Аннотация
Исследовано влияние условий 3D-печати (положения образца относительно плоскости стола принтера, а также температуры, диаметра сопла головки и плотности заполнения) на механические свойства образцов из полиэтилентерефталатгликоля. Основным фактором, определяющим упруго-прочностные свойства изделий, полученных 3D-печатью, является пористость образцов, связанная со степенью заполнения и ориентацией образца при печати относительно плоскости рабочего стола. Уменьшение диаметра сопла способствует снижению пористости и повышению механических свойств изделия, но увеличивает длительность печати.
Конструкционные термопласты широко используются в современных аддитивных технологиях, в частности в 3D-печати. [1, 2]. Одним из наиболее распространенных методов 3D-печати является послойное наплавление (FFF или FDM – Fused Deposition Modeling). Технология процесса заключается в экструзии расплавленной термопластичной нити с последующей послойной укладкой по заданной программой траектории. Применяемые для печати по этой технологии материалы, как правило, имеют форму нити (филамента) с диаметром 1.75 или 3 мм [3, 4]. Программное обеспечение (слайсер) при подготовке модели изделия и задания режима печати для 3D- принтера позволяет регулировать степень заполнения (плотность укладки слоев), что может существенно сказаться на механических свойствах получаемого изделия.
Среди современных термопластов, широко используемых для 3D-печати, выделяется полиэтиленфталатгликоль (ПЭТГ), который наряду с высокими механическими свойствами отличается стабильной аморфной структурой [5].
В работе [6] исследовано влияние ряда технологических факторов при 3D-печати изделий из ПЭТГ. Было показано, что свойства образцов, полученных методом 3D-печати, в целом уступают свойствам образцов, полученных традиционным методом литья под давлением, прежде всего вследствие повышенной пористости, возникающей при недостаточно плотной укладке расплавленных слоев из нитей при печати. Уменьшение диаметра сопла в печатающей головке снижает пористость изделий из ненаполненных термопластов, но может затруднять переработку наполненных термопластов. Снижение механических свойств изделий, полученных 3D-печатью термопластов по сравнению с литьем под давлением, также отмечалось в работах [7, 8]. Как известно, при традиционном формировании изделий литьем под давлением механические свойства существенно зависят от ориентации потока расплава термопласта, попадающего в литьевую форму, что связано с ее конструкцией [9, 10]. В отличие от литья под давлением в условиях 3D-печати течение расплава термопласта происходит с низкой скоростью и с минимальным проявлением ориентационных эффектов. В то же время при 3D-печати можно изменять положение образца относительно плоскости рабочего стола, что может сказаться на характеристиках получаемых изделий.
В известной литературе влияние технологических факторов при 3D-печати методом послойного наплавления на свойства получаемых изделий изучено явно недостаточно. В связи с этим целью настоящей работы является изучение влияния расположения детали относительно плоскости печати, плотности заполнения и размера диаметра печатающей головки на механические свойства изделий из ПЭТГ.
ЭКСПЕРИМЕНТАЛЬНАЯ ЧАСТЬ
Объектом исследования служил полиэтиленфталатгликоль в виде тонкого прутка (филамента) толщиной 1.75 мм производства “Shenzhen Esun Ind.Co.” химической формулы [7]
Показатель текучести расплава (ПTP) определяли на капиллярном вискозиметре постоянного давления типа ИИРТ-5М в соответствии с ASTM 1238 D (диаметр капилляра 2.090 мм, нагрузка 21.6 Н) в диапазоне температур 220–250°С.
Упруго-прочностные свойства изделий, полученные методом FDM-печати, зависят от параметров, которые задаются в программе, формирующей модель для печати (слайсере). Основными параметрами являются скорость и температура печати, а также плотность заполнения [11–15].
3D-печать образцов из ПЭТГ проводили на 3D-принтере модели “Creality Ender 5” (производства КНР) при следующих условиях: температура стола 60°С, скорость печати 50 мм/с, скорость печати первого слоя – 25 мм/с, толщина внешней границы 1.0 мм, скорость печати внешней границы 25 мм/с. Температура расплава при печати достигала 240–260°С.
В известных публикациях отмечается, что на свойства изделий при печати влияет диаметр сопла печатающей головки [16–19]. В настоящей работе использовали сопла с диаметром 0.2, 0.6, 0.8 и 1.0 мм; плотность заполнения варьировали от 50 до 100%.
Помимо роли температуры расплава полимера, диаметра сопла и плотности заполнения, изучали также влияние ориентации изделия к плоскости рабочего стола. Ниже представлены варианты расположения образцов при 3D-печати относительно плоскости стола.
3D-модели брусков на изгиб (80 × 4 × 10 мм) моделированы при помощи программного обеспечения SolidWorks. Для определения параметров печати использовали программу Creality Slicer.
Изучение механических свойств (модуля упругости и предела прочности при изгибе) образцов, полученных на разных режимах печати, проводили по ASTM 790 (ГОСТ 4648-2014). Испытания выполняли на универсальном испытательном стенде МИМ-10 с измерительной системой “ГОСТ-ТЕСТ”.
Плотность образцов оценивали по ISO 1183-1 (ГОСТ 15139-69). Пористость образцов определяли путем сравнения плотности образцов, напечатанных на 3D-принтере и полученных литьем под давлением, пористость которых условно принята за 0%. Расчет пористости проводили по уравнению
Теплофизические свойства материала оценивали методами ДСК на приборе “Netzsch DSC 214 Polyma” и ТГА на дериватографе фирмы MOM (Венгрия) 1500Q. С помощью метода ДСК определяли температуру стеклования, а также термоокислительную стабильность материала. Образец нагревали со скоростью 2 град/мин от комнатной температуры до 300°С, затем охлаждали с той же скоростью. Термоокислительные процессы изучали методом ДСК при выдерживании расплава при постоянной температуре 270°С в воздушной среде. Термогравиметрический анализ выполняли при скорости нагревания 10 град/мин. Литьевые образцы получали на литьевой машине марки “KuASY” при 240 и 250°С. Измерения проводили не менее, чем на 5 образцах, разброс результатов измерений составлял менее 10%.
РЕЗУЛЬТАТЫ И ИХ ОБСУЖДЕНИЕ
Зависимость ПТР расплава ПЭТГ от температуры представлена на рис. 1. Как видно, с повышением температуры значение ПТР увеличивается, что соответствует снижению вязкости. При низких скоростях сдвига, характерных для условий определения ПТР, расплав ПЭТГ проявляет свойства ньютоновской жидкости. Ожидалось, что температурная зависимость вязкости линейна в аррениусовских координатах [6]. Однако, судя по наблюдаемому нелинейному характеру изменения значения логарифма значения ПТР от обратной температуры (рис. 1, вставка), следует полагать, что неаррениусовский характер изменения вязкости связан не только с ростом температуры, но и с уменьшением ММ полимера, (что также было отмечено в работе [6]).
Рис. 1.
Зависимость ПТР расплава ПЭТГ от температуры. Цветные рисунки можно посмотреть в электронной версии.
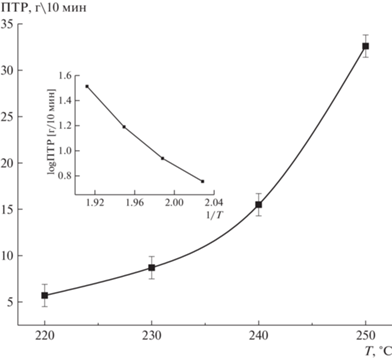
Проведенные исследования теплофизических свойств с помощью ДСК подтвердили стабильность аморфной структуры термопласта.
По результатам ДСК (рис. 2) температура стеклования ПЭТГ составляет 65°С, что совпадает с термомеханическими данными, полученными ранее на крутильном маятнике при той же скорости сканирования по температуре [6]. Отсутствие области плавления и кристаллизации свидетельствует о полностью аморфной структуре полимера.
Ранее было отмечено, что для расплава ПЭТГ при температуре выше 220°С уже через 15 мин заметно растет ПТР (снижается вязкость) [6]. Это указывает на то, что происходит деструкция полимера. Полученные методом ДСК результаты при термостатировании расплава при 270°С показали, что экзотермический эффект, характерный для процессов термоокисления, не проявляется в течение длительного времени. Данный факт свидетельствует о том, что снижение ММ полимера протекает, наиболее вероятно, по гидролитическому механизму, характерному для полиэфиров в присутствии следов воды. Это подтверждается и данными ТГА, представленными на рис. 3. Судя по этим результатам, заметной потери массы до 370°С не происходит, а потеря 5% массы наблюдается при 394°С.
Для литьевых образцов предел прочности при изгибе и модуль упругости при увеличении температуры переработки от 240 до 250°С изменяются незначительно, в интервалах 60–66 МПа и с 1.24–1.31 ГПа соответственно.
Для целей настоящей работы представляло существенный интерес изучить влияние ориентации (направления) печатающей головки относительно формуемого образца. Соответствующие результаты представлены на рис. 4 для 100%-ного заполнения образцов. Как видно, наибольшие значения предела прочности при изгибе (63 МПа) достигаются при вертикальной ориентации образцов (угол печати 90°), полученных при 250°С, и 100%-ном заполнении. В этих условиях характеристики образцов оказываются близкими к свойствам образцов, полученных литьем под давлением.
При горизонтальной ориентации предел прочности при изгибе составляет всего 39 МПа. На деталях, напечатанных под различными промежуточными значениями угла ориентации, предел прочности при изгибе практически не зависит от ориентации детали к поверхности стола 3D-принтера.
На образцах, напечатанных вертикально, также достигается максимальное значение модуля упругости при изгибе (1.20 ГПа). При этом модуль упругости образцов, напечатанных горизонтально (0.83 ГПа), уступает аналогичному показателю для образцов, напечатанных под углом 60° к поверхности стола 3D-принтера (0.89 ГПа).
Таким образом, механические свойства образцов, полученных методом 3D-печати, могут быть сопоставимы со свойствами литьевых образцов при оптимально выбранных условиях печати (рис. 5). Очевидно, что максимальные значения наблюдаются при максимальном заполнении.
Внешний вид образцов со степенью заполнения 100, 90, 80, 70, 50% (слева направо) показан ниже.
От диаметра сопла головки экструдера зависят скорость печати и плотность укладки экструдата (расплавленного филамента) в каждом слое. Наибольшее значение предела прочности при изгибе (47.4 МПа) достигнуто при печати образцов с использованием сопла диаметром 0.2 мм. При увеличении диаметра сопла (до 0.4–1.0 мм) предел прочности при изгибе практически остается постоянным (39 МПа), но при этом зависимость модуля упругости при изгибе от диаметра сопла проявляет экстремальный характер. Минимальное значение модуля (0.84 ГПа) получено на образцах при печати с соплом диаметром 0.6 мм (рис. 6).
Рис. 6.
Зависимости предела прочности (1) и модуля упругости при изгибе (2) образцов от диаметра сопла.
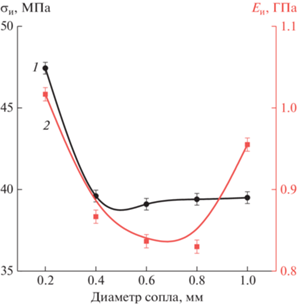
Температура печати определяет условия сплавления слоев при контакте расплавленной нити с поверхностью остывшего полимера при формировании изделия, от чего зависят монолитность и пористость изделия.
Максимальные значения упруго-прочностных свойств достигнуты для образцов, напечатанных при 250°С (рис. 7). При более высокой температуре физико-механические свойства изделия снижаются, скорее всего, в результате термодеструкции расплава.
Рис. 7.
Зависимость предела прочности (1) и модуля упругости при изгибе (2) образцов от температуры печати.
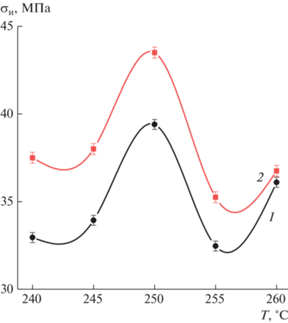
Основным фактором, определяющим физико-механические свойства конечного изделия, является пористость [20, 21]. Уже отмечалось, что при минимальном значении пористости (1.8%), полученном для образца при 100%-ном заполнении, температуре расплава 250°С и вертикальной ориентации образца, предел прочности при изгибе и модуль упругости при изгибе оказываются сопоставимыми с аналогичными характеристиками литьевых образцов. Для всех остальных образцов с плотностью заполнения 100% пористость находилась в пределах 6.7–13.9%.
В табл. 1 представлены сводные данные по влиянию параметров печати на свойства изделий. Как уже было сказано, наиболее высокие механические
Таблица 1.
Свойства образцов, полученных 3D-печатью по сравнению со свойствами образцов, полученных литьем под давлением
Образец, № | Ориентация детали, угол | Температура печати, оС | Диаметр сопла, мм | Плотность заполнения, % | Предел прочности на изгиб, МПа | Модуль упругости при изгибе, ГПа | Время печати, мин | Пористость, % |
---|---|---|---|---|---|---|---|---|
1 | 0 | 250 | 0.8 | 100 | 39.4 ± 0.1 | 0.83 ± 0.01 | 31 | 9.8 |
2 | 30 | 250 | 0.8 | 100 | 35.2 ± 1.0 | 0.77 ± 0.04 | 58 | 12.7 |
3 | 45 | 250 | 0.8 | 100 | 35.5 ± 1.9 | 0.75 ± 0.04 | 36 | 13.9 |
4 | 60 | 250 | 0.8 | 100 | 36.1 ± 1.6 | 0.89 ± 0.13 | 40 | 11.8 |
5 | 90 | 250 | 0.8 | 100 | 62.6 ± 0.6 | 1.20 ± 0.03 | 47 | 1.8 |
6 | 0 | 240 | 0.8 | 100 | 33.0 ± 0.2 | 0.75 ± 0.01 | 31 | 9.7 |
7 | 0 | 245 | 0.8 | 100 | 33.9 ± 1.1 | 0.76 ± 0.03 | 31 | 10.2 |
8 | 0 | 255 | 0.8 | 100 | 32.5 ± 0.2 | 0.72 ± 0.01 | 31 | 10.3 |
9 | 0 | 260 | 0.8 | 100 | 36.1 ± 1.4 | 0.74 ± 0.06 | 31 | 8.1 |
10 | 0 | 250 | 0.2 | 100 | 47.4 ± 2.5 | 1.02 ± 0.04 | 109 | 7.9 |
11 | 0 | 250 | 0.4 | 100 | 39.6 ± 2.3 | 0.87 ± 0.05 | 56 | 8.3 |
12 | 0 | 250 | 0.6 | 100 | 39.1 ± 0.3 | 0.84 ± 0.02 | 39 | 7.1 |
13 | 0 | 250 | 1.0 | 100 | 39.5 ± 5.9 | 0.96 ± 0.09 | 26 | 6.7 |
18 | 0 | 250 | 0.8 | 50 | 11.8 ± 0.2 | 0.22 ± 0.02 | 25 | 46.0 |
19 | 0 | 250 | 0.8 | 70 | 15.6 ± 0.5 | 0.36 ± 0.01 | 26 | 32.1 |
20 | 0 | 250 | 0.8 | 80 | 18.9 ± 0.5 | 0.41 ± 0.01 | 26 | 25.5 |
21 | 0 | 250 | 0.8 | 90 | 27.2 ± 0.4 | 0.59 ± 0.01 | 27 | 17.2 |
22 | 90 | 250 | 0.2 | 100 | 16.4 ± 2.2 | 0.55 ± 0.03 | 123 | 6.7 |
23 | Литье при 240°С | 60.4 ± 0.4 | 1.24 ± 0.06 | – | – | |||
24 | Литье при 250°С | 66.4 ± 1.7 | 1.31 ± 0.05 | – | – |
Уменьшение диаметра сопла печатающей головки в целом способствует снижению пористости и улучшению упруго-прочностных свойств, вероятно благодаря более плотной укладке тонких цилиндрических экструдатов, но в то же время приводит к значительному увеличению длительности печати. Этот результат очевиден ввиду снижения скорости экструзии пропорционально уменьшению диаметра сопла. Из приведенных данных видно, что длительность печати при использовании печатающей головки с соплом диаметра 0.2 мм увеличивается в 4 раза по сравнению с соплом 0.8 мм, что является определенным технологическим недостатком.
Таким образом, исследование влияния основных технологических факторов при 3D-печати на свойства образцов в виде брусков показало, что определяющей характеристикой служит пористость, зависящая от ориентации образца при печати и степени заполнения полимером изделия. Наименьшая пористость достигается при вертикальном расположении образца относительно плоскости рабочего стола. Оптимальный выбор основных технологических параметров (расположение детали относительно стола, температура и скорости печати) позволяет получить образцы с максимальными физико-механическими свойствами, близким к образцам, полученным методом литья под давлением. Уменьшение диаметра сопла печатающей головки приводит к повышению механических свойств изделий, но значительно увеличивает продолжительность печати.
Работа выполнена при финансовой поддержке Российского научного фонда (проект 17-79-30108).
Список литературы
Ligon S.C., Liska R., Stampfl J., Gurr M., Mülhaupt R. // J. Chem. Revs. 2017. V. 117. № 15. P. 10212.
Ngo T.D., Kashani A., Imbalzano G., Nguyen K.T.Q., Hui D. // J. Composites B. 2018. V. 143. P. 172.
Wickramasinghe S., Do T., Tran P. // Polymers. 2020. V. 12. № 7. P. 1529.
Mercado-Colmenero J.M., Mata-Garcia E., Rodriguez-Santiago M., Martin-Doñate C., Dolores La Rubia M. // Polymers. 2020. V. 12. № 10. P. 2202.
Шевлик Н.В., Строгонова С.С., Тычинская Л.Ю., Коваль В.Н., Щербина Л.А. // Полим. матер. технол. 2016. Т. 2. № 3. С. 35.
Обидин И.М., Котомин С.В. // Пласт. массы. 2021. № 3–4. С. 42.
Ali M.H., Batai S., Sarbassov D. // Rapid Prototyp. J. 2019. V. 25 № 6. P. 1108.
Дектярев А.В., Товпинец А.О., Гришин П.Р., Лейцин В.Н., Морозов ВН. // Наукоемкие технологии в машиностроении. 2020. № 2. С. 41.
Jansen K.M.B. // Int. Polym. Proc. 1998. V. 13. № 3. P. 309.
Malloy R.A. // Plastic Part Design for Injection Molding. Munich: Carl Hanser Verlag GmbH & Company KG, 2005.
Maloch J., Hnátková E., Žaludek M., Krátký P. // Mater. Sci. Forum. 2018. V. 919. P. 230.
Yao T., Deng Z., Zhang K., Li S. // J. Composites B. 2019. V. 163. P. 393.
Markiz N., Horváth E., Ficzere P. // Product. Eng. Archives. 2020. V. 26. № 3. P. 127.
Saenz F., Otarola C., Valladares K., Rojas J. // Additive Manufacturing, 2021. V. 39. P. 101841.
Gaweł A., Kuciel S. // Polymers. 2020. V. 12. № 12. P. 3056.
Radchenko V., Titov A., Khrapov S., Khoperskov A. // 2nd Int. Conf. Control Systems, Mathematical Modeling, Automation and Energy Efficiency (SUMMA). “Internal Geometry of Nozzles Adapted for 3D printing: Optimization using Computational Fluid Dynamics Methods”. Lipetsk, 2020. P. 533.
Petrov P., Agzamova D., Pustovalov V., Zhikhareva E., Saprykin B., Chmutin I., Shmakova N. // Abstrs 24th Int. Conf. Materi. Forming ESAFORM 2021. “Research Into the Effect of the 3D-printing Mode on Changing the Properties of PETG Transparent Plastic”. 2021.
Tlegenov Y., Hong G.S., Lu W.F. // Robotics and Computer-Integrated Manufacturing. 2018. V. 54. P. 45.
Płatek P., Rajkowski K., Cieplak K., Sarzyński M., Małachowski J., Woźniak R., Janiszewski J. // Polymers. 2020. V. 12. № 9. P. 2120.
Jakus A.E., Geisendorfer N.R., Lewis P.L., Shah R.N. // Acta Biomater. 2018. V. 72. P. 94.
Liao Y., Liu C., Lafdi K., Coppola B., Barra G., Di Maio L., Incarnato L. // Polymers. 2019. V. 11. № 9. P. 1487.
Дополнительные материалы отсутствуют.
Инструменты
Высокомолекулярные соединения (серия А)