Физикохимия поверхности и защита материалов, 2019, T. 55, № 1, стр. 72-78
Коррозионные, механические и каталитические свойства покрытий на основе металлических стекол FeNiCrWMoCoCB
А. А. Бурков 1, *, А. В. Зайцев 1, А. В. Сюй 2, Е. Р. Зайкова 1, О. И. Каминский 1
1 Институт материаловедения Хабаровского научного центра Дальневосточного отделения
Российской академии наук
680042 г. Хабаровск, ул. Тихоокеанская, 153, Россия
2 Дальневосточный государственный университет путей сообщения
680021 г. Хабаровск, ул. Серышева, дом 47, Россия
* E-mail: burkovalex@mail.ru
Поступила в редакцию 04.07.2017
После доработки 28.09.2017
Принята к публикации 25.10.2017
Аннотация
Работа посвящена нанесению покрытий на основе FeNiCrWMoCoCB металлических стекол на подложку из стали 35 электроискровой обработкой в среде гранул из металлов и сплавов, используемых в качестве электродных материалов. Рентгеноструктурный анализ показал преобладание аморфной фазы в составе покрытий. При температуре 1100°С аморфная фаза кристаллизуется в борокарбид типа M23(C,B)6, интерметаллид железа никеля и хрома, а также в αFe. Поляризационные испытания покрытия в 3.5% растворе NaCl показало более низкий ток коррозии и более высокое сопротивление поляризации по сравнению со сталью 35. Изучение жаростойкости при температурах 600, 700 и 800°С показало, что применение FeNiCrWMoCoCB покрытия на стали 35 повышает стойкость ее поверхности к высокотемпературной газовой коррозии за 40 ч испытаний в 8.7, 6.3 и 3.0 раза соответственно. Износостойкость FeNiCrWMoCoCB покрытий в режиме сухого скользящего износа при нагрузках 10 и 25 Н была в 2.2 и 1.7 раз выше, соответственно, чем у стали 35. Образцы с покрытиями на основе FeNiCrWMoCoCB металлических стекол показали высокую каталитическую активность к разложению раствора метиленового синего, как в присутствии пероксида водорода так и без него.
ВВЕДЕНИЕ
Металлические стекла (МC), также называемые аморфными металлическими сплавами, привлекают большое внимание исследователей благодаря своим превосходным механическим, физическим и химическим свойствам, которые обусловлены отсутствием таких недостатков кристаллических материалов как дефекты, дислокации, границы зерен и т.д. В 60-х годах прошлого столетия впервые была описана каталитическая способность МС на основе благородных металлов к обесцвечиванию водных растворов органических красителей [1]. Позднее каталитические свойства были обнаружены у МС на основе алюминия [2], кобальта [3], магния [4]. Но наибольше распространение получили МС на основе железа [5, 6] по причине их низкой стоимости, отличных магнитно-мягких свойств, высокой твердости, коррозионной и трибологической устойчивости и т.д. Обычно катализаторы из МС изготавливают в виде тонких лент или ультрадисперсных порошков для достижения большой удельной поверхности. Аморфная природа и метастабильная термодинамическая особенность могут придавать МС более высокий уровень внутренней энергии по сравнению с их кристаллическими аналогами, что снижает энергию активации реакции разложения органических молекул, и соответственно, ускоряет ее [7]. В связи с этим, перспективным является создание катализаторов в виде покрытий из МС на носителе из недорогих конструкционных материалов. Покрытия на основе МС получают методами: лазерной наплавки [8], газопламенного напыления [9] и электроискрового легирования (ЭИЛ) [10], благодаря высоким скоростям охлаждения материала в процессе осаждения на подложку.
При электроискровом легировании материал анода подвергается электрической эрозии в условиях воздействия электрических разрядов, переносится на катод и образует покрытие, обладающее высокой адгезией с подложкой благодаря перемешиванию анодного материала с металлом подложки. Для автоматизации ЭИЛ нами была предложена технология нанесения покрытий в гранулах, которые выполняют функцию рабочего электрода (анода) из осаждаемого материала [11]. В работе [12] нами были получены покрытия из металлических стекол, используя набор кристаллических гранул из разных металлов и сплавов в одну стадию. В соответствии с этой технологией, гранулы обменивались материалом между собой и подложкой под действием многократных электрических разрядов, формируя гомогенный состав на поверхности катода, который не успевал кристаллизоваться за счет высоких скоростей охлаждения.
Поскольку к катализаторам очистки сточных вод на металлических носителях могут предъявляться высокие требования по стойкости к различным внешним воздействиям, то целью данной работы было изучение износостойкости, коррозионной устойчивости и каталитической активности покрытий из металлических стекол на подложке из стали 35, полученных методом электроискровой обработки в гранулах состава Fe33Ni8Cr8W8Mo8Co8C16B11.
МЕТОДИКА
Состав смеси гранул представлен в табл. 1. Сплавы Cr3C2 + 50% Fe, WC + 8% Co и B4C + + 80% Fe были приготовлены методом порошковой металлургии из химически чистых порошков карбонильного железа и карбидов хрома, вольфрама и бора. Гранулы из приготовленных сплавов, а также чистых металлов: никеля, молибдена, железа и кобальта изготавливались в форме куба с ребром 4 ± 1 мм. Схема установки для осаждения покрытий в среде гранул показана на рис. 1. Подложка из стали 35 в форме цилиндра диаметром 12 мм и высотой 10 мм помещалась в металлический контейнер высотой 45 мм и диаметром 45 мм, заполненный гранулами. Контейнер устанавливался под углом 45° и подсоединялся к двигателю. Частота вращения контейнера с гранулами составляла 60 об. мин–1. Образец (катод), на который осаждалось покрытие, закреплялся на стальной стержень, подключенный к отрицательному выводу генератора импульсов и подсоединялся к двигателю, вращающему образец в противоположную контейнеру сторону с частотой 30 об. мин–1. Положительный вывод генератора присоединялся к контейнеру. Генератор разрядных импульсов IMES-40 вырабатывал импульсы тока прямоугольной формы амплитудой 110 А, длительностью 100 мкс и частотой 1000 Гц при напряжении 30 В. Для предотвращения окисления поверхности образцов в рабочий объем контейнера подавался защитный газ – аргон со скоростью 7 л мин–1. Для выравнивания состава поверхности всех гранул осуществлялась электроискровая обработка смеси гранул с незаменяемым катодом т.н. “приработка”. В течение всех экспериментов гранулы не заменялись и не очищались.
Таблица 1.
Состав смеси гранул
Массовое соотношение сплавов в смеси гранул | Концентрация элементов в смеси гранул, ат. % | ||||||||
---|---|---|---|---|---|---|---|---|---|
состав сплава | мас. % | Fe | Cr | W | Mo | Co | Ni | B | C |
Cr3C2 + 50%Fe | 16.68 | 33 | 8 | 8 | 8 | 8 | 8 | 11 | 16 |
WC + 8%Co | 29.66 | ||||||||
Mo | 13.63 | ||||||||
Fe | 11.48 | ||||||||
Co | 5.99 | ||||||||
Ni | 9.32 | ||||||||
B4C + 80%Fe | 13.24 |
Структура покрытий исследовались с применением рентгеновского дифрактометра ДРОН-7 в Cu-Kα излучении и оптического микроскопа Altami. Шероховатость образцов измерялась на профилометре TR 200.
Поляризационные испытания проводились в трехэлектродной ячейке после 20-минутной выдержки образцов в 3.5%-ном растворе NaCl, с использованием потенциостата 8P-nano со скоростью сканирования 30 Мв с–1. Площадь образцов, контактирующая с раствором электролита, составляла 1 см2. Контр-электрод представлял собой платиновый электрод “ЭТП-02”, а электродом сравнения выступал стандартный хлорсеребряный электрод. Потенциал коррозии, а также плотность тока коррозии были извлечены с участков методом экстраполяции Тафеля. Испытания на жаростойкость проводили в печи при температурах 600, 700 и 800°С на воздухе. Общее время тестирования при каждой температуре составляло 40 ч. Образцы выдерживали при заданной температуре в течение ~6 ч, затем удаляли и охлаждали в эксикаторе до комнатной температуры. Во время испытания на окисление все образцы помещались в корундовый тигель для учета массы отслоившихся оксидов. Изменение массы всех образцов измеряли с использованием лабораторных весов с чувствительностью 10–4 г. Прирост массы Δm для стали 35 и покрытий после испытания на жаростойкость рассчитывали по формуле (1):
где Δw – увеличение массы (в г) и S – площадь образцов (в м2) соответственно. Для исследования фазовых превращений при отжиге образцы нагревались в вакуумной печи Carbolite STF до температуры 1100°C и выдерживались в течение 1 ч при давлении 1.3 Па, а затем медленно охлаждались. Износостойкость покрытий согласно стандарту ASTM G99 – 04 исследовалась при сухом трении скольжения с применением контртела в виде диска из быстрорежущей стали Р6М5 на скорости 12 мс–1 при нагрузках 10, 25 и 50 Н. Образцы с покрытием и сталь 35 подвергались трению попеременно после каждого акта измерения массы для устранения погрешности, вводимой возможным изменением свойств поверхности контртела.Каталитическая активность образцов определялась фотокалориметрическим методом, путем исследования изменения оптической плотности раствора красителя метиленового синего (Mb). С целью увеличения производительности каталитического процесса, одновременно использовалось 10 образцов, с общей площадью нанесенного покрытия 41.4 см2. Они помещались в 350 мл раствора метиленового синего с концентрацией 1.2 мг/л. К раствору (р-р) метиленового синего добавлялся 1 мл 30% раствора перекиси водорода (Н2О2). Параллельно исследовалась каталитическая активность при следующих комбинациях компонентов: образцы + р-р Mb + Н2О2; образцы + р-р Mb; р-р Mb + Н2О2; р-р Mb.
РЕЗУЛЬТАТЫ И ИХ ОБСУЖДЕНИЕ
В процессе пропускания электрических импульсов от стенок контейнера к образцу возникали электрические разряды между гранулами и подложкой, а также между самими гранулами. В результате протекания электрических разрядов происходил выброс материала с поверхности гранул в пространство контейнера, на поверхность стальной подложки и на поверхность других гранул. В результате эрозии масса смеси гранул уменьшалась с постоянной скоростью (рис. 2а). Благодаря взаимному обмену материалом между электродами и его конвективному перемешиванию, в процессе воздействия многократных электрических разрядов, происходило выравнивание состава поверхности гранул и поверхности образца, до момента наступления равновесия. Покрытие наносилось в течение 10 мин, поскольку при превышении этого времени масса образца начинала снижаться, из-за наступления порога хрупкого разрушения легированного слоя [13]. На рис. 2а показано, что масса смеси гранул уменьшалась линейно, а масса катода увеличивалась, за счет осаждения материала с поверхности гранул, с постепенным замедлением. При этом максимальная осажденная удельная масса составила 12 мг см–2 за 10 мин обработки, а коэффициент массопереноса составил 20%. Толщина покрытия составила в среднем 84 мкм.
Рис. 2.
(а) Кинетика изменения массы катода и гранул в процессе электроискровой обработки. (б) Рентгеновская дифрактограмма осажденного покрытия на стали 35 (спектр 1) и после отжига при температуре 1100°С (спектр 2).
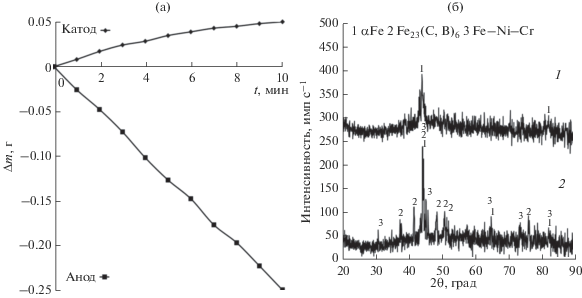
На рис. 2б(1) показана рентгеновская дифрактограмма полученного покрытия, которая указывает на формирование аморфной фазы, поскольку на ней отчетливо видно широкое гало в области углов 2θ = 43.3°. На вершине гало есть острый Брэгговский дифракционный максимум, соответствующий фазе альфа-железа. Учитывая низкую интенсивность данного рефлекса относительно фона, можно заключить, что в покрытии присутствует незначительное количество кристаллических фаз благодаря высокой стеклообразующей способности FeNiCrWMoCoCB состава и высокой скорости охлаждения материала (>105 K с–1) в условиях ЭИЛ. Отжиг покрытия при 1100°С привел к росту интенсивности рефлекса альфа-железа и появлению других рефлексов (рис. 2б(2)). Расшифровка дифрактограммы показала наличие интерметаллидов железа, никеля и хрома, а также сложного борокарбида типа M23(C,B)6. Благодаря большому числу элементов в покрытии интенсивность рефлексов данных фаз была низкой.
На рис. 3 показаны потенциодинамические поляризационные кривые покрытия и стали 35 в 3.5% растворе NaCl при комнатной температуре. На основе этих данных были рассчитаны ток коррозии Icorr, потенциал коррозии Ecorr и сопротивление поляризации Rp (табл. 3). Rp было рассчитано используя упрощенное выражение (2):
(2)
${{R}_{p}} = \frac{{{{b}_{a}}{{b}_{c}}}}{{2.303{{I}_{{{\text{corr}}}}}\left( {{{b}_{a}} + {{b}_{c}}} \right)}},$Таблица 2.
Характеристики покрытий
Толщина, мкм | 84 ± 45 |
Шероховатость, мкм | Ra = 13.8 ± 2.5; Rz = 62.1 ± 10.4; Rmax = 79.0 ± 10.1 |
Микротвердость, ГПа | 16.4 ± 2.2 |
Таблица 3.
Коррозионные параметры извлеченные из поляризационных кривых
Параметр | Ecorr, V vs.Ag/AgCl | Icorr, A см–2 | Rp, кОм см–2 |
---|---|---|---|
Сталь 35 | –0.96 | 4.69 × 10–5 | 0.99 |
Покрытие | –0.71 | 2.92 × 10–5 | 1.12 |
Эксперименты по определению жаростойкости стали 35 и электроискрового FeNiCrWMoCoCB покрытия при продолжительной изотермической выдержке при температурах (Т) 600, 700 и 800°С на воздухе показали, что наблюдалось непрерывное увеличение массы испытуемых образцов (рис. 4а). Причиной такого приращения массы является захват кислорода поверхностью образцов с образованием оксида железа Fе2O3 в модификации гематита [14]. Всего за 40 ч испытаний образцы прибавили в массе в 8.7, 6.3 и 3.0 раз меньше чем сталь 35 при температурах 600, 700 и 800°С соответственно. Таким образом, защитный эффект FeNiCrWMoCoCB покрытия на стали 35 снижался с повышением температуры. Это хорошо иллюстрируется на примере окисления образца при температуре 800°С, скорость окисления которого резко выросла после 13 ч испытаний (рис. 4а). Тогда как скорость приращения массы остальных образцов подчинялась параболическому закону [15].
Рис. 4.
Жаростойкость (а) покрытий (П), по сравнению со сталью 35 (С) при температурах 600, 700 и 800°С, на воздухе и (б) график Аррениуса.
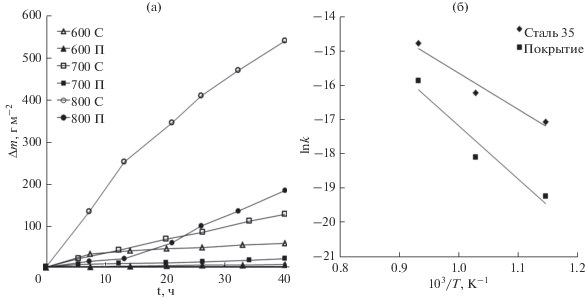
Энергия активации процесса окисления образцов и стали 35 может быть вычислена из уравнения Аррениуса (3):
где k – константа скорости реакции, Ea – энергия активации, R – универсальная газовая постоянная и А – предэкспонента. Для расчета Ea был построен график Аррениуса в координатах lnk относительно 1000/Т (рис. 4б). Вычисленная энергия активации окисления покрытий на основе FeNiCrWMoCoCB металлических стекол была на 26% выше, чем энергия активации окисления стали 35 (табл. 4).Таблица 4.
Значения энергии активации реакции окисления
Покрытие | Сталь 35 | |
---|---|---|
Энергия активации Ea, кДж моль–1 | 137.2 | 108.9 |
Предэкспоненциальный множитель | 0.17 | 5.9 × 10–3 |
Микротвердость покрытий из Fe33Ni8Cr8W8Mo8Co8C16B11 МС составила ~16 ГПа (табл. 2), тогда как у стали 35 составляет ~2.2 ГПа. Это хорошо иллюстрирует фотография отпечатков алмазного индентора в поперечном сечении покрытия и стальной подложки (рис. 5). Согласно литературным данным, значение микротвердости по Виккерсу для МС на основе железа находится в диапазоне от 7 до 10 ГПа, однако при отжиге твердость МС повышалась за счет релаксации структуры. Так в работе [16] отжиг аморфного сплава Fe40Ni40P14B6 при температуре 550°С привел к повышению его твердости с 9.8 до 16.3 ГПа. В связи с этим, высокое значение твердости покрытия может объясняться его нагревом в ходе электроискровой обработки.
Рис. 5.
Оптическое изображение отпечатков алмазного индентора при измерении микротвердости: слева – подложка, справа – покрытие.
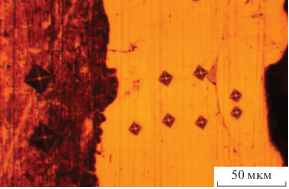
Износостойкость (Wr) обратно пропорциональна скорости износа, и соответственно, ее принято описывать через отношение нагрузки трения, которая является произведением нормальной нагрузки и пути трения, к массе или объему продуктов износа [17]:
где Δm – это изменение массы образца после прохождения пути трения l, а Р – это нормальная нагрузка. При трении образов относительно быстрорежущей стали Р6М5 реализовывался режим скользящего износа. Износостойкость образцов за 30 км испытаний при нагрузках 10 и 25 Н была в 2.2 и 1.7 раз выше, чем у стали 35, соответственно (рис. 6). Однако при нагрузке 50 Н покрытие изнашивалось на 25% быстрее стали. Характерно, что износостойкость покрытий хорошо подчинялась выражению (4) и практически не зависела от приложенной нагрузки, тогда как Wr стали 35 была пропорционально нагрузке (рис. 6). Это может объясняться упрочнением поверхности стали в условиях трения, т.н. “наклеп”. В соответствии с этим, защитное влияние покрытий из FeNiCrWMoCoCB МС на стали 35 снижалось с ростом приложенной нагрузки (рис. 6).Рис. 6.
Износостойкость покрытий на основе FeNiCrWMoCoCB МС по сравнению со сталью 35 при различных нагрузках.
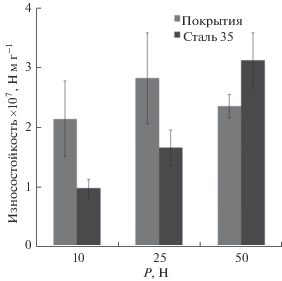
Для установления каталитической активности различных катализаторов, предназначенных для очистки сточных вод используют модельные водные растворы различных красителей [18], в т.ч. и метиленового синего [19].
На рис. 7 показана кинетика измененеия концентрации красителя Mb. Из него следует, что скорость разложения красителя в растворе с пероксидом водорода и без него практически одинаковая. В присутствии образцов с покрытиями на основе FeNiCrWMoCoCB МС и перекиси водорода краситель разлагался в 16 раз быстрее , чем раствор Mb c H2O2 без образцов. Перекись водорода не может эффективно разлагать Mb. Образцы в 4.5 раза ускоряли разложение раствора Mb даже без перекиси водорода. Каталитическая активность FeNiCrWMoCoCB МС объясняется аморфной природой, благодаря нуль валентному железу (Fe0), “замороженному” в атомном состоянии в FeNiCrWMoCoCB покрытии [5]. В процессе катализа Fe0 может реагировать непосредственно с молекулами метиленового синего ${\text{F}}{{{\text{e}}}^{0}} - 2{{{\text{e}}}^{ - }} = {\text{F}}{{{\text{e}}}^{{2 + }}},$ что приводит к обесцвечиванию красителя. Более того, реакция между Fe0 и H2O или H+ может генерировать атом [H], который имеет высокую реакционную способность к разрушению хромофорных структур в органических красителях [20]. В присутствии пероксида водорода происходило его взаимодействие с нуль валентным железом:
Рис. 7.
Кинетика изменения концентрации раствора красителя Mb: 1) р-р Mb; 2) р-р Mb + H2O2; 3) р-р Mb + образцы; 4) р-р Mb + H2O2 + образцы.
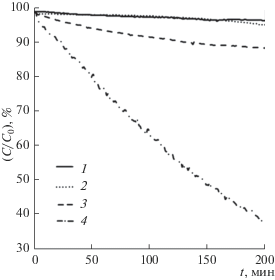
Радикал HO* обладает высокой активностью к разрушению хромофорных структур в органических красителях, и поэтому скорость разложения Mb в присутствии H2O2 была выше, чем без него. Большая шероховатость покрытия (табл. 2) обусловила его высокую каталитическую эффективность для разложения метиленового синего, с учетом малой геометрической площади катализатора 414 см2.
ЗАКЛЮЧЕНИЕ
Электроискровая обработка стали в смеси гранул состава Fe33Ni8Cr8W8Mo8Co8C16B11, собранной из кристаллических сплавов и чистых металлов, позволяет формировать покрытия толщиной около 80 мкм с преобладанием аморфной структуры. Износостойкость синтезированного покрытия была в 1.7–2.2 раза выше чем у стали 35 без покрытия. Образцы с покрытием из FeNiCrWMoCoCB металлических стекол в 16 раз повысили скорость обесцвечивания раствора метиленового синего в присутствии пероксида водорода и в 4.5 раза без него. Результаты показали, что предложенный подход может быть использован для получения катализатора из металлических стекол на носителе сталь 35 достаточно устойчивого к внешним воздействиям. Однако покрытие из FeNiCrWMoCoCB металлических стекол на стали 35 повышает ее устойчивость к коррозии в среде электролита всего на 11%. Поэтому целью дальнейших исследований будет поиск путей повышения коррозионной устойчивости МС в среде жидкого электролита.
Работа выполнена за счет средств гранта Правительства Хабаровского края (распоряжение от 19 мая 2017 г. № 319-рп).
Список литературы
Klement W., Willens R.H., Duwez P.O.L. // Nature. 1960. V. 187. P. 869.
Wang P., Wang J.-Q., Li H. et al. // J. of Alloys and Compounds. 2017. V. 701. P. 759.
Qin X.D., Zhu Z.W., Liu G. et al. // Scientific Reports. 2015. V. 5. P. 18226.
Ramya M., Karthika M., Selvakumar R. et al. // J. of Alloys and Compounds. 2017. V. 696. P. 185.
Liu P., Zhang J.L., Zha M.Q. et al. // ACS Applied Materials & Interfaces. 2014. V. 6. P. 5500.
Deng Z., Zhang X.H., Chan K.C. et al. // Chemosphere. 2017. V. 174. P. 76.
Zhang C., Zhu Z., Zhang H. et al. // J. of Physics and Chemistry of Solids. 2017. V. 110. P. 152.
Lan X., Wu H., Liu et al. // Materials Characterization. 2016. V. 120. P. 82.
Cheng J., Wang B., Liu Q. et al. // J. of Alloys and Compounds. 2017. V. 716. P. 88.
Burkov A.A., Pyacin S.A., Ermakov M.A. et al. // J. of Materials Engineering and Performance. 2017. V. 26. P. 901.
Бурков А.А., Пячин С.А., Метлицкая Л.П. и др. // Упрочняющие технологии и покрытия. 2013. Т. 5. № 101. С. 16.
Бурков А.А. Синтез аморфных электроискровых покрытий в среде гранул / В сборнике: Материалы XIV региональной научной конференции. Физика: фундаментальные и прикладные исследования, образование. Хабаровск. 2016. С. 217.
Верхотуров А.Д. Формирование поверхностного слоя металлов при электроискровом легировании / Владивосток: Дальнаука, 1995. С. 323.
Бурков А.А., Пячин С.А., Зайцев А.В. и др. // Письма о материалах. 2016. Т. 6. № 3 (23). С. 163.
Young D.J. High Temperature Oxidation and Corrosion of Metals / Elsevier Science S.A. London, 2008. P. 574.
Anis M., Rainforth W.M., Davies H.A. // Wear. 1994. V. 172. P. 135.
Bolelli G., Candeli A., Lusvarghi L. et al. // Wear. 2017. V. 378–379. P. 68.
Wang X., Pan Y., Zhu Z., Wu J. et al. // Chemosphere. 2014. V. 117. P. 638.
Serrà A., Grau S., Gimbert-Suriñach C. et al. // Applied Catalysis B: Environmental. 2017. V. 217. P. 81.
Sohn K., Kang S.W., Ahn S. et al. // Environmental Science & Technology. 2006. V. 40. P. 5514.
Дополнительные материалы отсутствуют.
Инструменты
Физикохимия поверхности и защита материалов