Физикохимия поверхности и защита материалов, 2019, T. 55, № 1, стр. 79-85
Каталитические свойства и устойчивость композитов K2Ti2O5 + K2Ti4O9/TiO2/TiO2 + SiO2/Ti к воздействию факторов внешней среды в процессе окисления сажи
П. Г. Чигрин 1, *, Е. А. Кириченко 1, В. С. Руднев 2, 3, **, И. В. Лукиянчук 2, Т. П. Яровая 2
1 Институт материаловедения ХНЦ ДВО РАН
Хабаровск, Россия
2 Институт химии ДВО РАН
Владивосток, Россия
3 Дальневосточный федеральный университет
Владивосток, Россия
* E-mail: pal_chig@mail.ru
** E-mail: rudnevvs@ich.dvo.ru
Поступила в редакцию 07.02.2018
После доработки 26.04.2018
Принята к публикации 24.05.2018
Аннотация
В работе осуществлен синтез катализатора окисления сажистого углерода на основе дититаната калия. Катализатор получен пропиткой гидроксидом калия оксидированной и дополнительно модифицированной подслоем из наночастиц анатаза титановой поверхности. Показано, что полученные композиты обладают высокой способностью к окислению дизельной сажи, а нанесенный каталитический слой устойчив к адгезионному и когезионному разрушению, при удовлетворительной стойкости к термоудару и действию каталитических ядов. Диапазон температур начала и завершения каталитического процесса лежит в пределах 340–550°С и сопоставим с таковым для катализаторов, используемых на практике.
1. ВВЕДЕНИЕ
В связи с ежегодным увеличением потребления энергии, получаемой из углеродсодержащих топлив, и ухудшением экологической ситуации вследствие выброса вредных веществ, содержащихся в продуктах их сгорания, поиск эффективных способов очистки отработанных автомобильных и топочных газов является важной экологической проблемой.
Снижение токсичного воздействия продуктов сгорания органического топлива на окружающую среду достигается путем очистки отходящих газов. Среди методов обезвреживания особый интерес представляет каталитическое окисление продуктов неполного сгорания топлива, а именно: полулетучих органических соединений и сажистого углерода, компонентов выбросов, представляющих особую опасность для живых организмов.
В настоящее время наиболее изученными высокоэффективными катализаторами окисления углерода являются оксидоцериевые системы: Co–Ce, Mn–Ce, Cu–Ce и Sm–Ce [1–4]. Несмотря на очевидные достоинства предложенных катализаторов, отмечается их низкая термическая и механическая стойкость [5]. Эти недостатки частично нивелируют нанесением катализаторов на подложку [6] и стабилизацией включением в структуру катализатора ZrO2 [7]. Однако добавление оксида циркония существенно снижает каталитическую активность предложенных составов. Кроме того, несомненным минусом, препятствующим широкому использованию оксидоцериевых катализаторов, является их низкая устойчивость к воздействию сернистого ангидрида и водяного пара [8, 9].
Согласно данным работ [3, 10–14] включение в структуру широко известных оксидных катализаторов ионов калия приводит к резкому возрастанию каталитической активности последних. В нескольких недавних публикациях [15–17] представлены результаты, показывающие перспективность использования титанатов калия (K6Ti4O11, K2Ti2O5, K2Ti4O9, K2Ti6O13) в качестве катализаторов окисления сажи, поскольку они обладают высоким уровнем каталитических свойств, термической стабильностью, устойчивостью к действию паров воды и газообразного SO2. Эти качества делают титанаты калия перспективными для применения в качестве катализаторов очистки отработанных газов, в том числе дизельных выбросов. Следует отметить, что титанаты калия катализируют окисление углерода в условиях как “тесного”, так и “слабого” контакта сажи с их поверхностью [17]. Однако подавляющее большинство исследований каталитических свойств титанатов калия выполнено на порошкообразных образцах. Активность катализаторов на основе титанатов калия, закрепленных на поверхности носителя, в литературе не обсуждается. Между тем, именно нанесенные катализаторы используют на практике в конструкциях сажевых фильтров. Также остается неясным и влияние каталитических ядов, термических и механических нагрузок на фазовый состав и механическую стойкость нанесенного катализатора.
Отдельного рассмотрения заслуживают носители для катализаторов и методы их приготовления. В идеале, такие носители должны сочетать высокую термическую стабильность и механическую прочность с достаточно высокой площадью поверхности и химической совместимостью с каталитически активными компонентами. С этой точки зрения, особый интерес представляет применение в качестве носителей коррозионно-стойких металлов, обработанных специальным образом для получения промежуточного оксидного слоя с высокой адгезией к металлу основы, толщину, химический состав и пористость которого можно легко регулировать. К одним из наиболее технологичных и экологичных способов создания на поверхности металлов и сплавов оксидных слоев с регулируемыми толщиной, составом и морфологией поверхности является метод плазменного электролитического оксидирования (ПЭО), заключающийся в контролируемом анодном окислении металлического электрода в среде электролита за счет энергии плазменных электрических разрядов. Показано, что метод ПЭО перспективен как для получения металл-оксидных носителей каталитически активных соединений, так и для синтеза оксидных катализаторов на металлических основах [18–22].
В частности, используя сочетание методов ПЭО и пиролиза смесей экстрактов металлов, были сформированы композиты CuMoO4/TiO2 + + SiO2/Ti, активные в дожиге сажи при температурах выше 270°С, с максимальной скоростью горения при 410°С в условиях слабого контакта частиц сажи с поверхностью катализатора [23]. Создание на поверхности ПЭО-покрытия дополнительного слоя наночастиц анатаза размером 30–50 нм путем сольвотермической обработки привело к уменьшению размеров частиц молибдатов меди, увеличению механической стабильности композитов CuMoO4/TiO2/TiO2 + SiO2/Ti и снижению температуры максимальной скорости горения на ~50°С [24].
В связи с вышеизложенным, цель настоящей работы – формирование покрытий, содержащих титанаты калия, на титановых основах, предварительно обработанных методом ПЭО и сольвотермическим способом, и исследование их каталитической способности к дожигу сажи, термической стабильности, устойчивости к действию механических нагрузок и каталитических ядов.
2. ЭКСПЕРИМЕНТАЛЬНАЯ ЧАСТЬ
ПЭО-покрытия на проволочных образцах технического титана ВТ1-0 формировали в гальваностатическом режиме при эффективной плотности тока i = 0.2 А/см2 в течение 10 мин в силикатном электролите, содержащем 0.05 моль/л Na2SiO3 и 0.05 моль/л NaOH. Толщина сформированных покрытий находилась в пределах 10–12 мкм.
Перед синтезом калий-титанатных покрытий, оксидированный титан обрабатывали коллоидной суспензией, полученной гидротермальным синтезом [25], содержащей наночастицы анатаза (30–40 нм). Суспензию наносили методом окунания, затем удаляли ее избыток и подвергали оксидно-титановые образцы ступенчатой термообработке по 2 ч при температурах 120, 350 и 550°С.
Для формирования каталитических композиций K2Ti2O5 + K2Ti4O9/TiO2/TiO2 + SiO2/Ti применяли щелочной синтез [26]: модифицированное ПЭО-покрытие, в структуре которого присутствуют наночастицы TiO2, выдерживали в течение 10 мин в 40%-м растворe КОН, избыточное количество щелочи удаляли на беззольной фильтровальной бумаге (синяя лента) и подвергали последующей термообработке в среде Ar в течение 2 ч при температуре до 900°С. Данный метод позволяет проводить синтез титанатных фаз с высокой скоростью при относительно невысоких температурах в инертной атмосфере, без разрушения титановой основы.
Избыток гидроксидов и силикатов калия удаляли из образцов K2Ti2O5 + K2Ti4O9/TiO2/TiO2 + + SiO2/Ti путем промывания дистиллированной водой до нейтральной реакции среды промывных вод. Затем образцы высушивали в муфельной печи при 150°С в течение 1 ч, переносили в вакуумный эксикатор, где хранили при комнатной температуре.
Каталитическое горение сажи исследовали на приборе сканирующей термогравиметрии NETZSCH STA 449 F3 в потоке воздуха (50 мл/мин) при скорости нагрева 5°/мин. Композиты K2Ti2O5 + + K2Ti4O9/TiO2/TiO2 + SiO2/Ti покрывали сажей в пламени горелки при сжигании дизельного топлива (ГОСТ 305-82). Температуру начала горения сажи (To) определяли по термогравиметрическим (ТГ) кривым, температуру максимальной скорости процесса горения (Tmax) – по экстремумам дифференциальных калориметрических (ДСК) кривых, с точностью ±2°С.
Морфологию и элементный состав образцов исследовали методом сканирующей электронной микроскопии (СЭМ) (микроскоп EVO 40, оснащенный энергодисперсионным спектрометром типа Rontec, с уточнением содержания элементов на спектрометре с волновой дисперсией типа 35-SDS JEOL). Мольное отношение K : Ti в калий-титанатных фазах рассчитывали на основе атомных концентраций элементов, которые определяли с помощью микрозондового анализа.
Оценку стойкости нанесенного слоя к адгезионному и когезионному разрушению осуществляли гравиметрическим методом, взвешивая образцы до и после ультразвукового воздействия (УЗ) в водной среде (мощность генератора 100 Вт, частота звуковых колебаний 35 кГц), аналогично [23]. Характер разрушения покрытий оценивали визуализацией снимков СЭМ.
УЗ-обработку предварительно подготовленных образцов проводили в изотермических условиях при 25°С. Массу образцов определяли на весах прибора NETZSCH STA 449 F3 с точностью до 10–6 г. Начальную массу покрытия m0 определяли по разнице массы проволоки с покрытием и той же проволоки, очищенной от покрытия до металлического титана. Очистку проволоки от покрытия осуществляли за счет механического воздействия. Массу разрушенного покрытия Δm оценивали взвешиванием образца до и после УЗ-воздействия, последующего высушивания при 150°С и охлаждения до комнатной температуры. Длительность отдельных УЗ-обработок варьировали от 1 до 20 мин, при этом суммарное время действия УЗ в течение всех циклов, приходящихся на образец, составляло 30 мин.
Оценку химической стабильности титанатов калия в нанесенном слое к диоксиду серы (время контакта 4 ч) и водяному пару (1 ч) при 400°С выполняли путем сравнения каталитических свойств исходных образцов и подвергнутых отравлению. Испытания по воздействию реакционных газов проводили в трубчатой печи SNOL. Расход SO2 и H2O составлял 0.14 и 10 г/мин соответственно.
Стойкость образцов к тепловому удару оценивали на основе убыли массы образцов после одного цикла нагрев-охлаждение, сопоставления каталитической способности образцов до и после испытаний и изменения морфологии поверхности. Нагрев до заданной температуры (800°С) осуществляли в индукционной печи со скоростью 60°/мин. Создание высокого температурного градиента достигалось резким охлаждением образцов до 0°С на предварительно охлажденной массивной металлической пластине. Скорость охлаждения образцов составляла ~100–150°С/с.
3. РЕЗУЛЬТАТЫ И ИХ ОБСУЖДЕНИЕ
3.1. Состав и строение покрытий
Согласно данным СЭМ (рис. 1а), при обработке раствором КОН поверхности ПЭО-покрытия, модифицированного подслоем из наночастиц анатаза, формируется покрытие в котором можно выделить 2 основных участка: первый представлен равномерно распределенной по поверхности мелкокристаллической фазой, второй – плоскими кристаллами треугольной формы размером до 5 мкм и толщиной от 0.5 до 1 мкм. По данным рентгеноспектрального микрозондового анализа, соотношение ионов калия и титана соответствует фазам K2Ti2O5 (10.6–10.7 ат. % K, 12.2–12.3 ат. % Ti, 3.7–3.9 ат. % Si, остальное кислород) наблюдается на первом участке и K2Ti4O9 (14.0–14.5 ат. % K, 27.3–27.9 ат. % Ti, 8.3–8.8 ат. % Si, остальное кислород) на втором (табл. 1). Следует отметить, что в составе композиционного покрытия значительно снижено содержание кремния, что может быть связано с тем, что образцы отмывали после воздействия щелочи и растворимые силикаты калия удалялись вместе с промывочной жидкостью.
Рис. 1.
СЭМ изображение поверхности каталитического композита состава K2Ti2O5 + + K2Ti4O9/TiO2/TiO2 + SiO2/Ti. а – Исходное покрытие; б – подвергнутое 30 мин УЗ-обработке в воде; в – после термического удара.
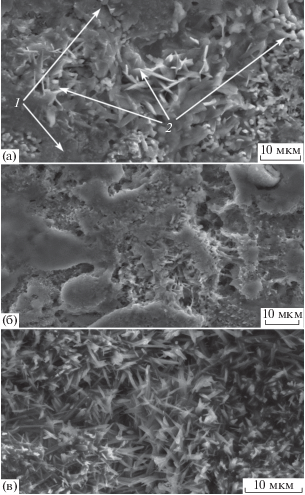
Таблица 1.
Элементный состав ПЭО оксидированных покрытий
Композит | Элементный состав, ат. % | ||
---|---|---|---|
K | Ti | Si | |
SiO2 + TiO2/Ti | – | 15.4 | 18.7 |
TiO2/SiO2 + TiO2/Ti | – | 20.3 | 12.4 |
K2Ti2O5 + K2Ti4O9/TiO2/TiO2 + + SiO2/Ti Участок 1 | 10.6 | 12.3 | 3.8 |
K2Ti2O5 + K2Ti4O9/TiO2/TiO2 + + SiO2/Ti Участок 2 | 14.3 | 27.6 | 8.5 |
ДСК кривая, соответствующая каталитическому горению (рис. 2, кривая 1) имеет один пик симметричной формы, что позволяет сделать вывод о том, что процесс протекает в одностадийном режиме, температура начала процесса 340°С, температура, соответствующая максимальной скорости, равна 390°С. Полученные результаты высокой каталитической активности для композиции K2Ti2O5 + K2Ti4O9/TiO2/TiO2 + SiO2/Ti подтверждаются литературными данными. Так согласно данным работы [27], уменьшение мольной доли калия в образце порошков перовскитов, соответствующих общей формуле xK2O · yTiO2, приводит к увеличению температуры максимальной скорости горения, поскольку механизм данного процесса обусловлен образованием поверхностных карбонатных интермедиатов на ионах K+, поэтому снижение доли калия в титанате приводит к снижению скорости процесса.
3.2. Оценка устойчивости к адгезионному и когезионному разрушению покрытия
В процессе эксплуатации нанесенных катализаторов окисления дизельной сажи в реальных условиях за счет различных механических нагрузок (вибрация, удары газовой струи и пр.) происходит отслаивание активного покрытия по типу когезионного и адгезионного разрушения. В настоящей работе предложено оценить устойчивость полученных композитов к данным типам разрушения по убыли массы образца с использованием известной методики [23]. Воздействие УЗ на каталитические композиции состава K2Ti2O5 + + K2Ti4O9/TiO2/TiO2 + SiO2/Ti (табл. 2) наблюдается лишь по прошествии 5 мин, убыль массы образца при этом достигает значения ~0.2% от начальной массы покрытия. Максимальная убыль массы покрытия 0.3% достигается через 10 мин УЗ-воздействия, причем дальнейшего падения массы образца не наблюдается даже после получасовой УЗ-обработки. По всей видимости, незначительное снижение массы композита происходит за счет отслоения части титанатов калия и непрореагировавших наночастиц подслоя анатаза.
Таблица 2.
Влияние времени τ ультразвуковой обработки на относительную убыль массы покрытия для композиции K2Ti2O5 + K2Ti4O9/TiO2/TiO2 + SiO2/Ti
τ, мин | 1 | 2 | 3 | 5 | 10 | 30 |
Δm/m0 × 100%, % | 0 | 0 | 0 | 0.2 | 0.3 | 0.3 |
Анализ СЭМ изображений исходных образцов (рис. 1а) и подвергнутых 30-минутному воздействию ультразвука (рис. 1б) не выявил значительных изменений морфологии поверхности каталитического слоя при воздействии ультразвука.
Термический анализ кривых сгорания сажи (кривые 1 и 2 на рис. 2) также показал идентичность каталитических свойств сравниваемых образцов K2Ti2O5 + K2Ti4O9/TiO2/TiO2 + SiO2/Ti. Окисление сажи в обоих случаях начинается от 340°С и протекает в одностадийном режиме, значения Тмакс сгорания сажистого углерода и температуры окончания процесса так же сопоставимы.
Таким образом, проведенные тесты показывают, что каталитические композиции K2Ti2O5 + + K2Ti4O9/TiO2 + TiO2 + SiO2/Ti обладают стойкостью к механическим воздействиям.
3.3. Исследование термостойкости
Анализ СЭМ-изображений образцов K2Ti2O5 + + K2Ti4O9/TiO2/TiO2 + SiO2/Ti, подвергнутых термоудару показал, что резкое охлаждение не сказывается на морфологии поверхности образца, покрытие после термических испытаний остается сплошным, отсутствуют разрушения и трещины (рис. 1в).
Согласно данным работ [28, 29], до температуры около 700°С нет активного проникновения кислорода через покрытие к титану и нет окисления тонкого переходного слоя и металла основы. При температуре около 750°С и выше начинается активная диффузия титана по трещинам и порам на поверхность, обогащение ее титаном и окисление последнего, вплоть до образования кристаллов рутила. В случае исследуемых покрытий также имеет место диффузия ионов калия вглубь оксидотитанового слоя и следующее за этим снижение концентрации калия на поверхности.
Действительно, в случае с термически обработанным до 800°С катализатором K2Ti2O5 + + K2Ti4O9/TiO2/TiO2 + SiO2/Ti, с помощью элементного анализа его поверхности было установлено наличие соединения, близкого по составу к K2Ti4O9 (5.4–6.5 ат. % K, 11.1–11.3 ат. % Ti, 7.0–7.5 ат. % Si, остальное кислород). Полная замена K2Ti2O5 на K2Ti4O9 в каталитическом слое приводит к заметному снижению каталитической активности, выражающемся в возрастании температурного интервала горения сажистого углерода на 70°С.
Термогравиметрическое исследование ДСК и ТГ-кривых окисления катализатора K2Ti2O5 + + K2Ti4O9/TiO2/TiO2 + SiO2/Ti в атмосфере кислорода воздуха представлено на рис. 3. Медленное окисление титановой основы начинается уже от 600°С. При температуре 882°С фиксируется фазовый переход низкотемпературного α-Ti в высокотемпературный β-Ti. Дальнейшее нагревание, начиная с 900°С, приводит к резкому возрастанию скорости окисления титановой основы и разрушению катализатора.
Рис. 3.
ТГ (пунктиром) и ДСК (сплошная) кривые термоокисления катализатора K2Ti2O5 + + K2Ti4O9/TiO2/TiO2 + SiO2/Ti в атмосфере воздуха.
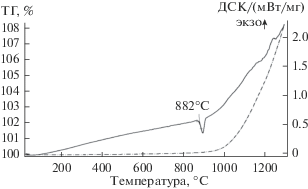
Таким образом, резкий нагрев до 800°С с последующим резким охлаждением композиции K2Ti2O5 + K2Ti4O9/TiO2/TiO2 + SiO2/Ti приводит к частичному окислению металлического основания, что сопровождается снижением концентрации ионов K+ на поверхности и, как следствие, уменьшением каталитической активности покрытия. Следует также отметить тот факт, что данное воздействие не сказывается на сплошности покрытия.
3.4. Воздействие каталитических ядов
Воздействие водяного пара на катализатор K2Ti2O5 + K2Ti4O9/TiO2/TiO2 + SiO2/Ti не оказывает существенного влияния на процесс окисления сажистого углерода. Значение температуры максимума 389°С (кривая 1 на рис. 4) близко к значению для исходного катализатора (кривая 1 на рис. 2), небольшое различие лежит в пределах погрешности прибора. Элементный анализ поверхности композиции не выявил существенного снижения доли калия в составе покрытия по сравнению с исходным, что объясняет сохранение каталитической активности, характерной для нанесенных титанатов K2Ti2O5 и K2Ti4O9
Рис. 4.
ТГ (пунктиром) и ДСК (сплошная) кривые окисления сажистого углерода в присутствии K2Ti2O5 + + K2Ti4O9/TiO2/TiO2 + SiO2/Ti, подвергнутого 1 – воздействию паров воды; 2 – ингибирующему воздействию сернистого газа.
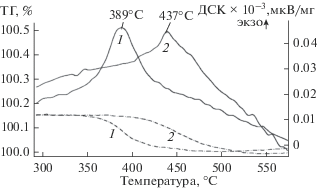
Таким образом, при длительном воздействии водяного пара на композит состава K2Ti2O5 + + K2Ti4O9/TiO2/TiO2 + SiO2/Ti заметных изменений в составе, морфологии и каталитической активности не выявлено.
Воздействие сернистого газа на каталитические композиции K2Ti2O5 + K2Ti4O9/TiO2/TiO2 + + SiO2/Ti приводит к существенному повышению температурного интервала каталитического горения сажистого углерода – температура начала реакции сдвигается на 50°С в область более высоких температур (кривая 2 на рис. 4). Это свидетельствует о понижении каталитической способности композиций.
Следует отметить, что среднее содержание сернистого ангидрида в дизельном выхлопе составляет 80 ppm [8], что при потоке выхлопных газов ~300 л/мин соответствует скорости подачи сернистого ангидрида 0.076 г/мин. Расход SO2 в нашем случае составлял 0.14 г/мин. Время воздействия – 240 мин.
Элементный анализ поверхности показал присутствие хемосорбированной серы в количестве от 1 до 2 ат. %. По-видимому, диоксид серы способен образовывать существенно более прочные соединения с калием по сравнению с углекислым газом, поэтому образование карбонатных интермедиатов на поверхности становится менее вероятным, что влечет за собой снижение каталитической активности. Однако, следует отметить тот факт, что диоксид церия CeO2, повсеместно используемый в качестве катализатора дожига сажистого углерода, испытывает существенно большее снижение активности при воздействии сернистого газа в концентрации более чем в три раза меньшей, а именно обработка цериевых катализаторов потоком чистого SO2 в течение 40 мин со скоростью 0.043 г/мин приводит к снижению температуры максимума скорости каталитического горения сажи на 111°С [9]. Таким образом, можно сделать вывод, что состав K2Ti2O5 + K2Ti4O9/TiO2/TiO2 + + SiO2/Ti обладает существенно большей стойкостью к воздействию сернистого ангидрида по сравнению с используемыми сегодня оксидоцериевыми катализаторами.
ВЫВОДЫ
Катализаторы состава K2Ti2O5 + K2Ti4O9/TiO2/ TiO2 + SiO2/Ti обладают высокой каталитической способностью к окислению сажевых частиц, сохраняющейся после механических испытаний и высокотемпературных воздействий в среде водяных паров.
Показано существенное увеличение температуры максимума сгорания сажи для композиции K2Ti2O5 + K2Ti4O9/TiO2/TiO2 + SiO2/Ti после изотермической выдержки при 800°С в течение 10 мин. По-видимому, оно обусловлено снижением концентрации поверхностного калия при температурном воздействии в воздушной атмосфере за счет перераспределения калия между внешними и внутренними слоями и перехода части K2Ti2O5 в менее активную титанатную фазу K2Ti4O9. Полученные результаты накладывают ограничения на температурный режим работы катализатора K2Ti2O5 + K2Ti4O9/TiO2/TiO2 + SiO2/Ti.
Установлено, что действие сернистого ангидрида на композиции состава K2Ti2O5 + K2Ti4O9/ TiO2/TiO2 + SiO2/Ti приводит к снижению температуры максимума скорости каталитического горения сажистого углерода на ~50°С, что обусловлено хемосорбцией серы и последующему отравлению катализаторов. Тем не менее, данные составы существенно более устойчивы к воздействию SO2, чем повсеместно используемые оксидоцериевые катализаторы. Таким образом, каталитическая композиция состава K2Ti2O5 + + K2Ti4O9/TiO2/TiO2 + SiO2/Ti представляется перспективным катализатором дожига сажистого углерода среди современных катализаторов, используемых в этой области.
Список литературы
Крылова А.В., Михайличенко А.И. // Химическая технология. 2003. № 2. С. 13.
Krishna K., Bueno-López A., Makkee M., Moulijn J.A. // Appl. Catal. B-Environ. 2007. V. 75. P. 201.
Guido S., Serra V., Badini C., Specchia V. // Ind. Eng. Chem. Res. 1997. V. 36. № 6. P. 2051.
Sui L., Yu L., Zhang Y. // Energy & Fuels. 2006. V. 20. P. 1392.
Doorn J., Varloud J., Moriaudeau P., Perrichon V. // Appl. Catal. B-Environ. 1992. V. 1. P. 117.
Banus E.D., Milt V.G., Miro E.E., Ulla M.A. // Appl. Cat. A: General. 2010. V. 379. P. 95.
Turakulova A.O., Zaletova N.V., Lunin V.V. // Russian J. of Physical Chemistry A. 2010. V. 84. № 8. P. 1309.
Gao Y., Wu X., Liu S. //RSC Adv. 2016. V. 6. P. 57033.
Flouty R., Abi-Aad E., Siffert S., Aboukaïs A. // Appl. Catal. B-Environ. 2003. V. 46. P. 145.
Gross M.S., Ulla M.A., Querini C.A. // Appl. Catal. A- Gen. 2009. V. 360. P. 81.
Zhang Z., Zhang Y., Wang Z., Gao X. // J. Catal. 2010. V. 271. P. 12.
Gong C., Song Ch., Pei Y. et al. // Ind. Eng. Chem. Res. 2008. V. 47. P. 4374.
Peng X., Lin H., Shangguan W., Huang Z. // Ind. Eng. Chem. Res. 2006. V. 45. P. 8822.
An H., Kilroy C., McGinn P.J. // Catal. Today. 2004. V. 98. P. 423.
Менг К., Ванг К. и др. // Кинетика и катализ. 2012. Т. 53. № 5. С. 588.
Wang Q., Chung J-Sh., Guo Z. // Ind. Eng. Chem. Res. 2011. V. 50. P. 8384.
Meng X., Gao Y. et al. // China Pet. Process. Petrochem. T. 2012. V. 14. № 2. P. 50.
Кондриков Н.Б., Руднев В.С., Васильева М.С. и др. // Химия в интересах устойчивого развития. 2005. Т. 13. № 6. С.851.
Васильева М.С., Руднев В.С., Тырина Л.М. и др. // Журн. прикладной химии. 2005. Т. 78. № 11. С. 1891.
Васильева М.С., Руднев В.С., Кондриков Н.Б. и др. // Журн. прикладной химии. 2004. Т. 77. № 2. С. 222.
Lukiyanchuk I.V., Rudnev V.S., Tyrina L.M. // Surf. Coat. Technol. 2016. V. 307. P. 1183.
Karakurkchi A., Sakhnenko M., Ved M. et al. // Eastern European Journal of Enterprise Technologies. 2017. V. 5. № 10–89. P. 12.
Lebukhova N.V., Rudnev V.S., Chigrin P.G. et al. // Surface and coatings technology. 2013. V. 231. P. 144.
Lebukhova N.V., Rudnev V.S., Kirichenko E.A. et al. // Surf. Coat. Technol. 2015. V. 261. P. 344.
Карпович Н.Ф., Корольков И.В., Макаревич К.С. и др. // Фундаментальные проблемы современного материаловедения 2012. Т. 9. № 1. С. 34.
Гороховский А.В. Патент № 2326051 РФ. 2008.
Wang Q., Guo Z., Chung J-Sh. // Mater. Res. Bull. 2009. V. 44. P. 1973.
Руднев В.С., Малышев И.В. и др. // Физикохимия поверхности и защита материалов. 2012. Т. 48. № 4. С. 391.
Vasilyeva M.S., Rudnev V.S., Wiedenmann F. et al. // Appl. Surf. Sci. 2011. V. 258. P. 719.
Дополнительные материалы отсутствуют.
Инструменты
Физикохимия поверхности и защита материалов