Физикохимия поверхности и защита материалов, 2019, T. 55, № 1, стр. 25-32
Окисление порошкообразного алюминия после модификации поверхности формиатами Mn, Fe, Co и Ni
В. Г. Шевченко 1, *, В. Н. Красильников 1, Д. А. Еселевич 1, А. В. Конюкова 1
1 Институт химии твердого тела УрО РАН
620990 Екатеринбург, Россия
* E-mail: shevchenko@ihim.uran.ru
Поступила в редакцию 16.10.2017
После доработки 16.01.2018
Принята к публикации 15.02.2018
Аннотация
Исследовано влияние малых добавок оксидов марганца, железа, кобальта и никеля на окисление порошка алюминия марки АСД-4 при нагревании в воздушной среде. Приготовление композитов Al/MOx осуществляли путем пропитки порошка металла насыщенными растворами формиатов M(HCOO)2 ⋅ 2H2O (M = Mn, Fe, Co, Ni) и термообработки полученных смесей на воздухе с максимальной температурой отжига 375°С. Установлено, что влияние модификаторов на интенсивность окисления зависит от характера межфазного взаимодействия на поверхности частиц. Образование жидкой фазы при взаимодействии оксидов алюминия и железа приводит к потере защитных свойств барьерным слоем продуктов окисления и ускорению процесса.
ВВЕДЕНИЕ
Порошки алюминия, благодаря высокой удельной теплоте сгорания, находят широкое применение в области взрывотехники, производстве высокоэнергетических горючих смесей и твердых топлив ракетных двигателей [1–5], оптимизация параметров горения которых является очень важной и актуальной задачей. Однако высокие защитные свойства оксидной пленки на поверхности частиц металла не позволяют полностью реализовать его потенциальные возможности. Для решения этой проблемы в последние годы большое внимание уделяют разработке методов активации порошков алюминия и оптимизации процессов их горения.
На наш взгляд среди существующих на данный момент методов активации заслуживает внимания подход, основанный на использовании добавок оксидов WO3, MoO3, V2O5, MnO2, Ta2O5, Fe2O3, Bi2O3, NiO, CuO, являющихся сильными окислителями и направляющими реакцию на поверхности по термитному типу [6–12]. Высокую эффективность показали добавки пентоксида ванадия и поливанадатов, которые влияют на энергетические свойства системы, а также рассматриваются как активные переносчики кислорода и катализаторы окисления алюминия [14–17]. В связи с развитием методов получения ультра- и наноразмерных порошков алюминия, привлекает внимание вариант повышения реакционной способности за счет увеличения дисперсности металлического горючего [18–21], однако при этом возникают проблемы, связанные со стабильностью ультра- и наноразмерных частиц металла при хранении и в условиях совмещения с компонентами энергетических конденсированных систем, а также высокой стоимостью порошков. В этой связи целесообразным является применение микроразмерных порошков алюминия типа АСД с размерами зерен порядка 5–10 мкм, совмещающихся с модификаторами, в частности с гидрогелями V2O5 ⋅ nH2O [15, 17], без заметного изменения содержания металлического (активного) алюминия. Известно модифицирование горючих свойств порошков алюминия путем их совмещения с ксерогелями MoO3 ⋅ nH2O [22] и Fe2O3 ⋅ nH2O [23]. Использование гелеобразных предшественников для нанесения модификаторов позволяет проводить процедуру смешения компонентов энергетической смеси практически без механического воздействия, то есть без изменения морфологии частиц металла, которое может ухудшить его реологические свойства.
Следует также отметить, что добавки оксидов металлов и сами металлы, оказывают положительное воздействие не только на горение алюминия в смесевых составах энергетических конденсированных систем (ЭКС), но и на кинетику разложения окислителей и других составляющих ЭКС, что в конечном итоге позволяет оптимизировать скорость горения топлив [24, 25]. В связи с этим целью настоящей работы явилось изучение окисления порошка алюминия микронной размерности, модифицированного добавками малых количеств оксидов марганца, железа, кобальта и никеля. Модифицирование осуществляли путем пропитки порошка алюминия насыщенными растворами формиатов M(HCOO)2 ⋅ 2H2O (M = = Mn, Fe, Co, Ni), разлагающимися при нагревании на воздухе выше 300°С с образованием оксидов [26].
МЕТОДИКА ЭКСПЕРИМЕНТА
В качестве объекта модификации нами был использован порошок алюминия марки АСД-4 со средним размером частиц 5–10 мкм, полученный методом распыления расплавленного металла азотом [27]. Процесс модифицирования включал стадии смешения порошка металла с насыщенными водными растворами M(HCOO)2 ⋅ 2H2O (M = = Mn, Fe, Co и Ni), сушки полученных смесей при 150°С и нагревания в течение 30 мин на воздухе при температуре 350°С, которая согласно [26, 28–34] отвечает полному разложению данных формиатов. Концентрация модификаторов в пересчете на металл была для всех образцов одинаковой и составляла 2 мас. %.
Формиаты марганца, железа, кобальта и никеля синтезировали согласно следующим реакциям:
(1)
$\begin{gathered} {\text{MnC}}{{{\text{O}}}_{{\text{3}}}}{\text{ + 2HCOOH + }}{{{\text{H}}}_{{\text{2}}}}{\text{O = }} \\ {\text{ = }}\,\,{\text{Mn}}{{\left( {{\text{HCOO}}} \right)}_{{\text{2}}}} \cdot \,\,{\text{2}}{{{\text{H}}}_{{\text{2}}}}{\text{O + C}}{{{\text{O}}}_{{\text{2}}}}, \\ \end{gathered} $(2)
$\begin{gathered} {\text{Fe + 2HCOOH + }}{{{\text{H}}}_{{\text{2}}}}{\text{O = }} \\ {\text{ = }}\,\,{\text{Fe}}{{\left( {{\text{HCOO}}} \right)}_{{\text{2}}}} \cdot \,\,{\text{2}}{{{\text{H}}}_{{\text{2}}}}{\text{O + }}{{{\text{H}}}_{{\text{2}}}}, \\ \end{gathered} $(3)
$\begin{gathered} {\text{Co}}{{\left( {{\text{N}}{{{\text{O}}}_{{\text{3}}}}} \right)}_{{\text{2}}}} \cdot \,\,{\text{6}}{{{\text{H}}}_{{\text{2}}}}{\text{O + 8HCOOH = }} \\ {\text{ = }}\,\,{\text{Co}}{{\left( {{\text{HCOO}}} \right)}_{{\text{2}}}} \cdot \,\,{\text{2}}{{{\text{H}}}_{{\text{2}}}}{\text{O + }}{{{\text{N}}}_{{\text{2}}}}\,\,{\text{ + }}\,\,{\text{6C}}{{{\text{O}}}_{{\text{2}}}}\,\,{\text{ + }}\,\,{\text{10}}{{{\text{H}}}_{{\text{2}}}}{\text{O,}} \\ \end{gathered} $(4)
$\begin{gathered} {\text{Ni}}{{\left( {{\text{OH}}} \right)}_{{\text{2}}}}{\text{ + 2HCOOH + }}{{{\text{H}}}_{{\text{2}}}}{\text{O = }} \\ {\text{ = }}\,\,{\text{Ni}}{{\left( {{\text{HCOO}}} \right)}_{{\text{2}}}} \cdot {\text{2}}{{{\text{H}}}_{{\text{2}}}}{\text{O}}{\text{.}} \\ \end{gathered} $В качестве реактивов в эксперименте использовали аналитически чистые MnCO3, Fe, Co(NO3)2 ⋅ 6H2O, Ni(OH)2, муравьиную кислоту HCOOH (97%). Все реактивы растворяли в разбавленной (20%) муравьиной кислоте, взятой в количестве немного превышающем стехиометрическое соотношение для M(HCOO)2 ⋅ 2H2O, при температуре 80°C. Нагревание продолжали до выделения из растворов кристаллических осадков формиатов. После чего температуру понижали до 50°C и растворы формиатов Mn, Co и Ni упаривали до сухих остатков в обычных условиях. Учитывая возможность окисления Fe2+ до Fe3+ при нагревании раствора Fe(HCOO)2 ⋅ 2H2O на воздухе [35], его упаривание проводили при добавлении железных стружек и небольшого количества муравьиной кислоты. В этом случае выделение водорода согласно реакции (2) предотвращало окисление Fe2+. Непрореагировавшие с муравьиной кислотой железные стружки удаляли из воздушно сухого продукта с помощью магнита.
Типичная процедура приготовления модифицированных образцов АСД-4 включает следующие операции. Синтезированные формиаты, взятые в требуемых количествах (Mn – 3.29, Fe – 3.25, Co – 3.14, Ni – 3.15 г), растворяли в 20 мл дистиллированной воды при температуре 80°С и добавляли глицерин в объемном соотношении C3H8/H2O = 1/25. Глицерин добавляли в растворы для подавления кристаллизации формиатов и гелеобразования. Затем растворы упаривали до минимально возможного объема, охлаждали до комнатной температуры и смешивали с алюминием. Полученные смеси подвергали термообработке на электроплите для удаления компонентов растворителя и отжигу в муфельной печи для разложения формиатов.
Рентгенофазовый анализ образцов осуществляли с помощью рентгеновского порошкового автодифрактометра STADI-P (STOE, Germany) в CuKα1-излучении с использованием библиотеки рентгеноструктурных данных PDF-2 (Release 2009). Микроскопический фазовый анализ проводили с использованием поляризационного микроскопа ПОЛАМ С-112 в проходящем свете, показатели преломления кристаллических образцов измеряли иммерсионным методом. Термогравиметрический анализ выполняли на термоанализаторе NETZSH STA 409 PC/PE при скорости нагревания 10°С/мин в тонкостенных корундовых тиглях тарельчатого типа при одинаковой исходной массе образцов 15 мг. Форму и размер частиц порошков определяли методом сканирующей электронной микроскопии на приборе JSM JEOL 639LA. Удельную площадь поверхности исходных и активированных порошков алюминия оценивали методом низкотемпературной сорбции азота в варианте метода БЭТ на автоматическом анализаторе TriStar (Micromeritics, USA).
РЕЗУЛЬТАТЫ ЭКСПЕРИМЕНТОВ
Порошки синтезированных формиатов марганца, железа, кобальта и никеля имеют бледно-розовую, светло-зеленую, темно-розовую и зеленую окраску, соответственно. Согласно данным микроскопического анализа кристаллы M(HCOO)2 ⋅ ⋅ 2H2O образуются в виде ромбических призм, шестиугольных или тонких бесформенных пластинок. Показатели преломления кристаллов: Ng = = 1.561, Nm = 1.548, Np = 1.534 (Mn); Ng = 1.563, Nm = 1.537, Np = 1.524 (Fe); Ng = 1.587, Nm = = 1.576, Np = 1.561 (Co); Ng = 1.571, Nm = 1.557, Np = 1.540 (Ni). По данным рентгеноструктурного анализа M(HCOO)2 ⋅ 2H2O изоструктурны и кристаллизуются в моноклинной сингонии с пространственной группой P21/c. Параметры решетки синтезированных согласно реакциям (1–4) формиатов M(HCOO)2 ⋅ 2H2O (M – Mn, Fe, Co, Ni), уточненные методом полномасштабного анализа (Rietveld) с использованием программного пакета FULLPROF [33, 36–41], приведены в табл. 1 в сравнении с опубликованными ранее данными [33, 36–41].
Таблица 1.
Параметры решетки M(HCOO)2 ⋅ 2H2O, где M = Mn, Fe, Co, Ni (P21/c Z = 4)
M | a, Å | b, Å | c, Å | β (°) | Источник |
---|---|---|---|---|---|
Mn | 8.8279(3) 8.86 8.86 |
7.2793(1) 7.29 7.18 |
9.6030(1) 9.60 9.39 |
97.67(1) 97.7 97.6 |
Наши данные [32, 37] [28] |
Fe | 8.7192(1) 8.61 8.740 |
7.1811(2) 7.34 7.192 |
9.3952(2) 9.27 9.428 |
97.45(1) 96.16 97.47 |
Наши данные [39] [38] |
Co | 8.6740(3) 8.680 8.63 |
7.1619(1) 7.160 7.06 |
9.2723(1) 9.272 9.21 |
97.42(1) 97.43 96.0 |
Наши данные [26, 37] [28] |
Ni | 8.5951(1) 8.60 8.60 |
7.0688(2) 7.06 7.06 |
9.2152(1) 9.21 9.21 |
97.41(1) 96.83 96.8 |
Наши данные [38] [28] |
Разложение M(HCOO)2 ⋅ 2H2O при нагревании на воздухе протекает в два основных этапа, сопровождающихся убылью массы (рис. 1).
Эндотермические эффекты с минимумами на кривых ДТА при 146 (Mn), 175 (Fe), 186 (Co) и 204°C (Ni), характеризующие процессы дегидратации образцов, коррелируют с увеличением радиусов катионов M2+ [42], то есть закономерно смещаются в высокотемпературную область. Экспериментальные значения убыли массы для всех образцов на стадии дегидратации хорошо согласуются с данными расчетов при условии удаления 2H2O: 20.34 и 19.9% (Mn), 20.45 и 19.79% (Fe), 20.08 и 19.47% (Co), 20.12 и 19.49% (Ni). Разложение продуктов дегидратации M(HCOO)2 ⋅ 2H2O, где M = Mn и Fe, сопровождается экзотермическими эффектами с максимумами при температурах 314 и 279°C на кривых ДТА (рис. 1а, б). Максимумы экзотермических эффектов на кривых ДТА формиатов кобальта и никеля располагаются при 334 и 378°С, т.е. смещены в высокотемпературную область, и их можно отнести не только к процессам, сопряженным с распадом HCOO–, но и с увеличением массы первичных продуктов термолиза за счет их окисления кислородом воздуха (рис. 1в, г). Убыль массы образца Mn(HCOO)2 ⋅ 2H2O, оцененная для температуры 450°C (37.73 мас. %), незначительно отличается от рассчитанной при условии образования Mn3O4 (37.95 мас. %), а для Fe(HCOO)2 ⋅ 2H2O она соответствует образованию Fe2O3. Величины убыли массы в точках минимума на кривых ТГ M(HCOO)2 ⋅ 2H2O (M = Co, Ni) превышают таковые при расчете на образование оксидов (рис. 1в, г). Для точки минимума на кривой ТГ формиата никеля потеря массы составляет 45.38 мас. %, что отличается от рассчитанных в случае образования NiO (40.06 мас. %) и Ni (48.93 мас. %).
Согласно немногочисленным литературным данным фазовый состав продуктов термолиза карбоксилатов d-металлов зависит от их состава и условий термообработки. Так, по данным термогравиметрического и рентгенофазового анализа, разложение Mn(HCOO)2 ⋅ 2H2O [24, 32], Fe(HCOO)2 ⋅ 2H2O [27, 28] в инертной газовой среде при температуре 350°C происходит с образованием MnO и Fe3O4. Для формиатов кобальта и никеля в этих условиях характерно разложение, сопровождающееся восстановлением Co2+ и Ni2+ до элементарного состояния [26, 28–31]. При термолизе малоната железа(III) [27, 43] и оксалатов железа(II) и (III) [42] на воздухе образуется нанодисперсный магнетит γ-Fe2O3. На рис. 2 представлены дифрактограммы продуктов термолиза M(HCOO)2 ⋅ 2H2O, полученных путем их отжига при температуре 350°C на воздухе.
Рис. 2.
Дифрактограммы продуктов термолиза M(HCOO)2 ⋅ 2H2O, где M = Mn (а), Fe (б), Co (в), Ni (г) при температуре 350°C на воздухе.
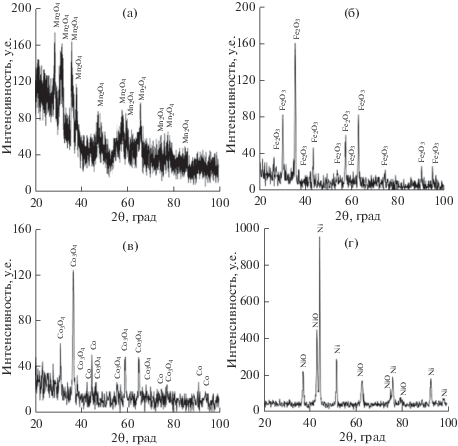
Видно, что термическое разложение формиатов Mn, Fe, Co и Ni на воздухе с удалением органической составляющей сопровождается образованием Mn3O4, как основной фазы, и примеси Mn2O3 (рис. 2а), сесквиоксида железа со структурой γ-Fe2O3 (рис. 2б), Co3O4 + Co (рис. 2в) и NiO + Ni (рис. 2г). При температуре отжига 400°C и выше γ-Fe2O3 превращается в α-Fe2O3, а Co и Ni окисляются кислородом воздуха до Co3O4 и NiO. Это согласуется с данными термогравиметрического анализа (рис. 1в, г). Аналогичных превращений можно ожидать при нагревании на воздухе образцов АСД-4, пропитанных растворами M(HCOO)2 ⋅ 2H2O из расчета 2 мас. % на содержание металла. На рис. 3 представлены кривые ТГ и ДТА образцов порошка АСД-4, модифицированного формиатами Mn, Fe, Co и Ni.
Рис. 3.
Кривые ДТА и ТГ образцов порошка АСД-4, модифицированных пропиткой растворами M(HCOO)2 ⋅ 2H2O, где M = Mn (а), Fe (б), Co (в), Ni (г), с нагреванием на воздухе при 350°C в течение 30 мин.
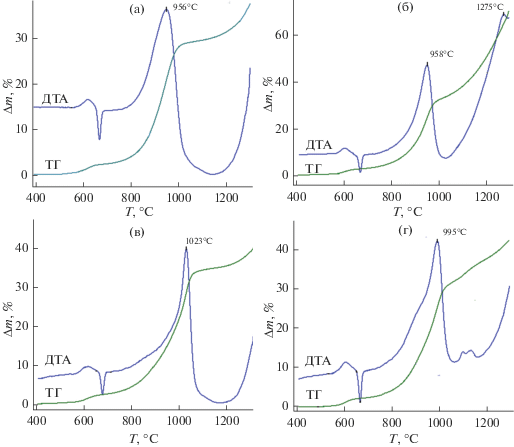
При окислении исходного порошка АСД-4 температурный максимум на кривой ДСК наблюдается при температуре 1045°С [16]. Как видно из рис. 3, модифицирование АСД-4 оксидами марганца, железа, кобальта и никеля приводит к смещению максимумов температурных эффектов в область более низких температур: 956 (Mn), 958 (958), 1023 (Co) и 995°C (Ni). Однако этот сдвиг менее существен, чем в случае модифицирования пентоксидом ванадия (797°С) [16]. Заметное повышение степени окисления имеет место только для порошка, модифицированного железом (~70%), (рис. 3б). При этом, на кривой ДСК образца наблюдается формирование высокотемпературного максимума при температуре около 1270°С, что связано с активацией окисления не окислившегося на первом этапе алюминия.
Как упоминалось выше [6–12] и следует из работ [45–53] оксиды марганца, железа, кобальта и никеля входят в состав известных термитных смесей. При малом содержании этих оксидов на поверхности частиц алюминия вряд ли следует ожидать существенного влияния теплоты термитной реакции на динамику прогрева частиц. Необходимо также отметить, что сами величины теплот не столь значительно отличаются по своим значениям [45]. Из общих представлений и исходя из анализа литературных данных по диаграммам состояния в системах Al2O3 с оксидами Mn, Fe, Co и Ni [54], образовавшимися в результате термолиза, следует, что активность окисления алюминия в основном будет определяться физико-химическими свойствами слоя продуктов взаимодействия, образующихся в результате нагрева в воздушной среде. Для взаимодействия оксида алюминия с оксидами Mn, Co и Ni характерно образование шпинелей состава MeAl2O4, имеющих высокие температуры плавления (выше 1900°С). Лишь в системе Al2O3–Fe2O3 образуется соединение FeAlO3 с температурой плавления 1318°С [54]. Вероятно, этим объясняется более высокая активность окисления АСД-4 модифицированного Fe2O3. Появление жидкой фазы в твердом слое продуктов окисления на поверхности окисляющегося алюминия, вызванное термитным взаимодействием жидкого алюминия и твердого оксида Fe2O3, снижает диффузионные ограничения и ускоряет окисление алюминия. Этому способствует также то, что согласно [50–53] термитная реакция в системе Al–Fe2O3 является сложным многостадийным процессом, протекающим с участием следующих промежуточных фаз: Fe, Fe3Al, AlFe, FeAl2O4, Fe3O4, α-Fe2O3, Al, γ-Fe2O3, Al2.667O4, FeO и α-Al2O3. При этом, температура воспламенения этой системы в вакууме составляет 965°С [49]. Для других изученных оксидов эта температуры достаточно близки. Так для системы AlCo3O4 температура воспламенения составляет 971°С.
О более высокой активности окисления модифицированного железом порошка, различии процессов, сопровождающих окисление, свидетельствуют данные сканирующей электронной микроскопии (рис. 4 и 5). После нагрева до 950°С на воздухе модифицированный порошок теряет сферическую форму за счет интенсивного взаимодействия и образования кристаллитов продуктов взаимодействия. Разнообразие фаз, образующихся в процессе термитной реакции, наряду с высокими окислительными свойствами самого оксида железа, способствуют снижению защитных характеристик барьерного слоя продуктов окисления и увеличению полноты и скорости окисления модифицированного порошка. Наряду с этим, оксид Fe2O3, как отмечалось выше [25, 26], обладает наибольшей каталитической активностью при распаде энергетических добавок, входящих в состав смесевых композиций ракетных топлив.
ЗАКЛЮЧЕНИЕ
Модификация порошка алюминия марки АСД-4 формиатами Mn, Fe, Co и Ni приводит к образованию на его поверхности, в процессе нагрева на воздухе, соответствующих оксидов.
Термитные реакции алюминия с оксидами металлов инициируют начало активного взаимодействия алюминия с кислородом воздуха.
Влияние модификаторов на интенсивность окисления алюминия зависит от характера межфазного взаимодействия на поверхности частиц, определяемого диаграммами состояния двойных систем Al2O3–MOx.
Значительное ускорение окисления алюминия установлено при модификации поверхности оксидом железа, что связано с образованием в барьерном слое продуктов окисления жидкой фазы двойного оксида FeAlO3.
Работа выполнена в соответствии с государственным заданием и планами НИР ИХТТ УрО РАН, тема № ААА-А16-116122810219-4.
Работа частично поддержана РФФИ № 16-32-00061 мол_а.
Список литературы
Kwon Y.S., Gromov A.A., Ilyin A.P. et al. // Combustion and Flame. 2003. V. 133. P. 385–391.
DesJardin P.E., Felske J.D., Carrara M.D. // J. Propulsion and Powder. 2005. V. 21. P. 478–485.
Ягодников Д.А. Воспламенение и горение порошкообразных металлов. М.: Изд-во МГТУ им. Н.Э. Баумана, 2009. 432 с.
Zang F., Keith G. // J. Propulsion and Powder. 2009. V. 25. P. 845–858.
Gan Y., Qiao L. // Combustion and Flame. 2011. V. 158. P. 354–368.
Woo K.D., Kim J.H., Kwon E.P. et al. // Met. Mater. Int. 2010. V. 16. P. 218–313.
Yeh C.L., Wang H.J. // J. Alloys Compd. 2010. V. 491. P. 153–158.
Martirosyan K.S. // J. Mater. Chem. 2011. V. 21. P. 9400–9405.
Stamatis D., Zhu X., Schoenitz M. et al. // Powder Technology. 2011. V. 208. P. 181–186.
Kumar S., Krishnamurthy N. // Processing and Application of Ceramics. 2011. V. 5. P. 181–186.
Zhang K., Fen W., Zhu J., Wu H. // Science of Sintering. 2012. V. 44. P. 73–80.
Poda A.R., Moser R.D., Cuddy M.F. et al. // J. Nanomater. Mol. Nanotechnol. 2013. V. 2. P. 100105.
Шевченко В.Г., Волков В.Л., Кононенко В.И. и др. // Физика горения и взрыва. 1996. Т. 32. С. 91–94.
Пат. № 2509790 РФ. Способ активации порошка алюминия / Шевченко В.Г., Еселевич Д.А., Конюкова А.В., Красильников В.Н. Опубл. 20.03.2014. Бюл. № 8.
Шевченко В.Г., Еселевич Д.А., Конюкова А.В., Красильников В.Н. // Химическая физика. 2014. Т. 33. № 10. С. 10–17.
Shevchenko V.G., Krasil’nikov V.N., Eselevich D.A. et al. // Explosion and Shock Waves. 2015. V. 51. P. 572–577.
Шевченко В.Г., Красильников В.Н., Еселевич Д.А., Конюкова А.В. // Физикохимия поверхности и защита материалов. 2017. Т. 53. С. 508–513.
Pivkina A., Streletskii A., Kolbanev I. et al. // J. Mater. Sci. 2004. V. 39. P. 5451–5453.
Фёдоров С.Г., Гусейнов Ш.Л., Стороженко П.А. // Российские нанотехнологии. 2010. Т. 5. С. 27–39.
Li Q., Lin B., Li W. et al. // Powder Technology. 2011. V. 212. P. 303–309.
Badiola C., Gill R.J., Dreizin E.L. // Combustion and Flame. 2011. V. 158. P. 2064–2070.
Seo H.S., Kim J.K., Kim J.W. et al. // J. Industrial Eng. Chem. 2014. V. 20. P. 189–193.
Wang Y., Song I., Jiang W. et al. // Trans. Nonferrous Met. Soc. China. 2014. V. 24. P. 263−270.
Buzdov K.A., Antonov B.D. // Russ. J. Inorg. Chem. 2012. V. 57. P. 1599–1605.
Степанов Р.С., Круглакова Н.А., Асбсехов А.М., Пехотин К.В. // Физика горения и взрыва. 2004. Т. 40. № 5. С. 80–90.
Коротких А.Г., Архимов В.А., Глотов О.Г. и др. // Горение и взрыв. 2015. Т. 8. № 2. С. 129–137.
Гопиенко В.Г., Осипов Б.Р., Назаров Б.П. и др. Производство и применение алюминиевых порошков и пудр. М.: Металлургия, 1980. 68 с.
Fox P.G., Ehretsmann J., Brown C.E. // J. Catal. 1971. V. 20. P. 67–73.
Muraishi K., Takano T., Nagase K., Tanaka N. // J. Inorg. Nucl. Chem. 1981. V. 43. P. 2293–2297.
Vecher A.A., Davidovich S.V., Gusev E.A. // Thermochim. Acta. 1985. V. 89. P. 383–386.
Morando P.J., Piacquadio N.H., Blesa M.A. // Thermochim. Acta. 1987. V. 117. P. 325–330.
Qusti A.H., Samarkandy A.A., Al-Thabaiti et al. // JKAU: Sci. 1997. V. 9. P. 73–81.
Leyva A.G., Polla G., Vega D. // J. Solid State Chem. 2001. V. 157. P. 23–29.
Ергалиев Р.Т., Корзанов В.С., Красновских М.П., Лущиков А.А. // Вестник Пермского университета. Серия “Химия”. 2017. Т. 7. С. 152–158.
Pierce R.D., Friedberg S.A. // Physical Review. B. 1971. V. 3. P. 934–942.
Osaki K., Nakai Y., Watanabe T. // J. Phys. Soc. Jap. 1964. V. 19. P. 717–723.
Thomas J.M., Williams J.O., Clarke T.A. // J. Chem. Soc. (A). 1970. P. 2938–2939.
Takeda K., Kawasaki K. // J. Phys. Soc. Jpn. 1971. V. 31. P. 1026–1036.
Kaufman A., Afshar C., Rossi M., Zacharias D.E., Glusker J.P. // Struct. Chem. 1993. V. 4. P. 191–198.
Vassileva V. // Cryst. Res. Technol. 1996. V. 31. P. 993–1000.
Masuda Y., Hatakeyama M. // Thermochim. Acta. 1998. V. 308. P. 165–170.
Shannon R.D. // Acta Cryst. 1976 (A). V. 32. P. 751–767.
Rahman M.M., Mukhedkar V.A., Venkataraman A. et al. // Thermochim. Acta. 1988. V. 125. P. 173–190.
Music M., Gotic S., Popovic I., Czako-Nagy I. // Mater. Lett. 1994. V. 20. P. 143–148.
Martirosyan K.S. // J. Mater. Chem. 2011. V. 21. P. 9400–9405.
Asif Khan R.M., Malik A.Q. // NUST J. Eng. Sci. 2012. V. 5. P. 1–6.
Wen J.Z., Ringuette S., Bohlouli-Zanjani G. et al. // Nanoscale Res. Lett. 2013. V. 8. P. 184 (1–9).
Patel V.K., Saurav J.R., Gangopadhyay K. et al. // RSC Adv. 2015. V. 5. P. 21471–21479.
Monogarov K.A., Pivkina A.N., Grishin L.I. et al. // Acta Astronautica. 2017. V. 135. P. 69–75.
Duraes L., Costa D.F.O., Santos R. et al. // Mater. Sci. Eng. A. 2007. V. 465. P. 199–210.
Liu Y., Qian Q., Xu C. et al. // Asian J. Chem. 2013. V. 25. P. 5550–5552.
Wang Y., Song X.I., Jiang W. et al. // Trans. Nonferrous Met. Soc. China. 2014. V. 24. P. 263–270.
Woo K.D., Kim J.H., Kwon E.P. et al. // Met. Mater. Int. 2010. V. 16. P. 213–218.
Data of Geochemistry. Sixth Edition. Chapter L. Phase-Equilibrium Relations of the Common Rock-Forming Oxides Except Water // By George W. Morey and Michael Fleischer, Technical Editor, Superintendent of Documents, U. S. Government Printing Office, Washington, D. C. 1964. 158 p.
Дополнительные материалы отсутствуют.
Инструменты
Физикохимия поверхности и защита материалов