Физикохимия поверхности и защита материалов, 2019, T. 55, № 2, стр. 204-208
Модифицирование поверхности волокон хризотила и его влияние на физико-механические характеристики хризотилцемента
Л. Н. Наумова 1, В. И. Павленко 1, Н. И. Черкашина 1, *
1 Белгородский государственный технологический университет им. В.Г. Шухова
308012 Белгород, ул. Костюкова, 46, Россия
* E-mail: natalipv13@mail.ru
Поступила в редакцию 15.12.2017
После доработки 12.02.2018
Принята к публикации 20.03.2018
Аннотация
В работе представлены данные по модифицированию поверхности волокон хризотила серной кислотой, а также влияние модифицирования на конечные свойства хризотилцемента. Показано, что обработка исходного хризотила раствором серной кислоты способствует повышению степени распушки его волокон. Степень распушки волокон исходного хризотила составила 34%, обработанного кислотой – 47%. Установлено, что модифицирование повышает на 38% адсорбционную активность хризотила, а также приводит к перезарядке поверхности волокна и уменьшению абсолютной величины отрицательного заряда поверхности (электрокинетического потенциала). Представлены данные основных физико-механических характеристик хризотилцемента на основе исходного и модифицированного хризотила полученного методом фильтрации. Методом рентгенофазового анализа показано, что при использовании модифицированного хризотила степень гидратации цемента несколько увеличивается, что обусловлено обработкой хризотила.
ВВЕДЕНИЕ
В асбестоцементной промышленности используют асбесты серпентинитовой группы и прежде всего хризотил-асбест (природный хризотил). Хризотил представляет собой водный гидросиликат магния с химическим составом Mg3Si2O5(OH)4. Крупнейшие месторождения асбеста находятся в Канаде (хризотил), ЮАР (крокидолит, амозит, хризотил) и в России (хризотил) на Урале – Баженовское и Киембаевское месторождения. Кроме того, многочисленные опыты показали, что хризотил может быть синтезирован в гидротермальных условиях [1–5].
Внешний и внутренний слой в кристаллической структуре пачки хризотила образованы плоскими сетками SiO4-тетраэдров и чередующимися с ними бруситовыми слоями. Вследствие различных параметров кремнекислородных бруситовых слоев происходит деформация слоистой структуры, слои свертываются с образованием трубчатых кристаллов диаметром 20–50 нм, определяющих все свойства хризотила [6]. Таким образом, кристаллы хризотила представляют собой тончайшие полые трубочки-нановолокна, которые собраны в пучки [7, 8]. Широкое применение в строительстве волокна хризотила получили благодаря своим уникальным свойствам, таким как негорючесть, высокая термостойкость и электроизоляционные свойства [9, 10]. Кроме того, волокна хризотила обладают высокой прочностью на разрыв и гибкостью [11].
Хризотил играет активную роль в процессах гидратации и твердения цемента: в результате хемосорбции поглощает из жидкой фазы гидрат окиси кальция, выделяющегося при гидратации алита (C3S); адсорбирует и удерживает на своей поверхности слой гидросиликатов кальция и других новообразований. Эти процессы ведут к ускорению процесса гидратации цемента. Тонкораспушенные волокна хризотила армируют цементный камень и улучшают его физико-механические характеристики [12, 13]. Большая удельная поверхность хризотила предопределяет его высокую адсорбционную активность, особенно хорошо адсорбируются гидроксиды щелочных и щелочноземельных металлов: Ca(OH)2, Ba(OH)2, NaOH, KOH. Основная роль хризотилового волокна заключается в том, что он воспринимает растягивающие напряжения и придает цементному камню некоторую эластичность. Хризотил является не только армирующим элементом, но и одновременно изменяет физико-химические процессы, ускоряет твердение цементного раствора.
Для максимального использования армирующих свойств волокон хризотила необходимо увеличить поверхность их связи с цементом, т.е. распушить волокна. Исследования показывают, что модифицирование поверхности хризотила приводит к распушке его волокон и усиливает развитие и прочность структур в суспензиях, повышая качество хризотилцемента [14]. Известно, что модифицирование волокон, армирующих композиционный материал, значительно улучшает их поверхностные свойства, что в конечном итоге приводит к улучшению физико-механических характеристик композита [15–21].
В данной работе представлены данные по модифицированию поверхности волокон хризотила серной кислотой (H2SO4) и его влиянию на конечные свойства хризотилцемента.
МЕТОДИЧЕСКАЯ ЧАСТЬ
В качестве исследуемого материала использовали природный хризотил состава Mg3Si2O5(OH)4, химический состав которого представлен в табл. 1.
Таблица 1.
Химический состав используемого хризотила
Содержание оксидов, мас. % | |||||||
---|---|---|---|---|---|---|---|
MgO | SiO2 | Al2O3 | СаО | Cr2O3 | MnO | Fe2O3 | NiO |
43.3 | 46.7 | 1.0 | 0.3 | 0.5 | 0.2 | 7.6 | 0.4 |
Исследуемый хризотил обрабатывали 0.3% раствором серной кислоты (H2SO4). Модифицирование проводили в течение 24 ч при комнатной температуре. После модифицирования хризотил промывали дистиллированной водой и сушили в сушильном шкафу по постоянной массы.
Изображения микроструктуры поверхности волокон хризотила получали с помощью сканирующего электронного микроскопа (СЭМ) высокого разрешения TESCAN MIRA 3 LMU в Центре высоких технологий БГТУ им. В.Г. Шухова.
Для определения степени распушки хризотила его предварительно обрабатывали в лабораторных бегунах. Условную степень распушки исходного и модифицированного хризотила определяли по величине осадка, образующегося в водной суспензии после отстаивания в цилиндре объемом 1 л в течение 15 мин. Масса сухого хризотила в суспензии составляла 10 г.
Измерения электрокинетического потенциала (ζ-потенциала) исходной и модифицированной поверхности хризотила проводили с помощью лазерного анализатора частиц Zetatrac, Microtrac (США). Для обработки результатов использовали программу Microtrac FLEX. Данный прибор определяет ζ-потенциал измерением отклика заряженных частиц на электрическое поле. В постоянном электрическом поле частицы дрейфуют с постоянной скоростью. Заряд и ζ-потенциал определяются через скорость.
Рентгенофазовый анализ выполняли на дифрактометре Дрон-3 (CuKα-излучение, Ni-фильтр) по стандартной методике. Напряжение на трубке составляло 20 кВ; анодный ток 20 мА; предел измерений 1000–4000 имп./с; скорость поворота детектора 2.4 град/мин; шаг 1°. Анализ и первичную обработку данных проводили с помощью пакета программ PDWin (DrWin, Qual), используя базу данных PDF JCPDS (version 2.02 1999).
Сорбционную активность хризотила определяли ускоренным методом поглощения волокнами гидроксида кальция из известкового раствора в течение определенного периода времени.
Щелочестойкость образцов определяли по потере массы после кипячения в 25% растворе гидроксида калия (KOH). Обработку щелочью проводили в течение 4-х ч с последующей промывкой дистиллированной водой и сушкой в сушильном шкафу до постоянной массы.
Аналогичную методику использовали для определения кислотоустойчивости образцов. Кислотоустойчивость определяли по потере массы образцов после испытания в течение 4-х ч в 20%-ном растворе соляной кислоты (HCl) при температуре кипения – 108°C. После охлаждения образцы промывали дистиллированной водой и высушивали до постоянной массы.
Изготовление образцов хризотилцемента проводили методом фильтрации. Метод фильтрации заключался в следующем: готовили сырьевую смесь из 12.5% хризотила и 87.5 мас. % портландцемента марки М500. Навеску хризотила помещали в бачок с водой и перемешивали хризотиловую суспензию в пропеллерной мешалке в течение 5 мин. По истечении этого времени, не останавливая мешалки, в суспензию высыпали портландцемент и продолжали перемешивание в течение 5–7 мин. Полученную хризотилцементную суспензию фильтровали с помощью вакуум-насоса. Формование образцов проводили на ручном прессе при удельном давлении 5 МПа.
РЕЗУЛЬТАТЫ И ОБСУЖДЕНИЯ
На рис. 1 представлены микрофотографии поверхности волокон исходного и модифицированного хризотила.
Анализ микрофотографии поверхности волокон исходного хризотила (рис. 1а) показал, что внешний диаметр монокристаллов хризотила равен 35.0–38.0 нм, внутренней – 2–3 нм. Часто присутствуют сростки 2-х, 3-х и более монокристаллов. Можно заметить, что модифицирование хризотила приводит к расщеплению волокон (рис. 1б).
Степень распушки волокон исходного хризотила составила 34%, обработанного кислотой – 47%. Таким образом, обработка исходного хризотила раствором серной кислоты способствует повышению степени распушки волокон хризотила.
Результаты измерения электрокинетического потенциала волокон хризотила представлены в табл. 2.
Таблица 2.
Значения ζ-потенциала исходного и модифицированного хризотила
Вид хризотила | Длина волокон, см | ζ-потенциал, мВ |
---|---|---|
Исходный | 0.4–2.1 | +21.79 |
Модифицированный | 0.4–2.1 | –16.15 |
Значение электрокинетического потенциала поверхности исходного хризотила имеет положительный заряд (ζ = +21.79 мВ), ввиду преимущественной диссоциации ионов ОН–, что приводит к возникновению положительного заряда на поверхности его волокон, обусловленного избытком ионов Mg+2. Модифицирование волокон хризотила 0.3%-ным раствором серной кислоты приводит к перезарядке поверхности волокна и уменьшению абсолютной величины отрицательного заряда поверхности, что объясняется выщелачиванием магния из поверхностного слоя волокон хризотила.
На основе рентгеновских дифракционных характеристик исходного и модифицированного серной кислотой хризотила были рассчитаны параметры элементарной ячейки (табл. 3).
Таблица 3.
Параметры элементарной ячейки исходного и модифицированного хризотила
Вид хризотила | Параметры элементарной ячейки | |||
---|---|---|---|---|
a, нм | b, нм | c, нм | β, 0 | |
Исходный | 0.5331 0.5316 |
0.9222 0.9198 |
1.4775 | 930 20I |
Модифицированный | 0.5331 0.5306 0.5299 |
0.9222 0.9180 0.9168 |
1.4775 | 930 20I |
Анализ данных табл. 3 показал, что, параметры с и β исходного и модифицированного хризотила остались неизменными, а параметры a и b уменьшились. Выявленные изменения дифракционных характеристик хризотила до и после модифицирования дают возможность говорить о начале нарушений в октаэдрическом бруситоподобном слое структуры хризотила.
Результаты испытаний сорбционной активности волокон исходного и обработанного кислотой хризотила показали (табл. 4), что в начальный момент времени (10 мин) исходный хризотил обладает большей адсорбционной активностью, однако в последующий период активность модифицированного хризотила увеличивается быстрее, чем у исходного и достигает максимального значения – 0.0359 мг/г. Модифицированный хризотил имеет на 38% большую адсорбционную активность.
Таблица 4.
Сорбционная активность волокон исходного и модифицированного хризотила
Время, мин | Количество поглощенного Са(OH)2, мг/г хризотила | |
---|---|---|
исходный | модифициро-ванный | |
10 | 0.0047 | 0.0044 |
30 | 0.0061 | 0.0083 |
60 | 0.0083 | 0.0146 |
90 | 0.0116 | 0.0204 |
120 | 0.0163 | 0.0246 |
150 | 0.0191 | 0.0285 |
180 | 0.0240 | 0.0323 |
210 | 0.0260 | 0.0359 |
Вследствие того, что диаметр хризотиловых волокон чрезвычайно мал, его удельная поверхность очень велика и достигает (15–20) × 103 м2/кг. Этим и объясняется высокая адсорбционная способность (активность) хризотила, который используется при производстве асбестоцементных изделий.
Для оценки анализа адгезии (прочности сцепления) волокон исходного и модифицированного хризотила с цементным камнем использовали корреляцию с щелочестойкостью. Щелоче- и кислотоустойчивость исходного и модифицированного хризотила представлены в табл. 5. Анализ полученных данных показал, что щелоче- и кислотоустойчивость модифицированного хризотила практически на уровне исходного (табл. 5). Низкая кислотоустойчивость исследованных образцов объясняется высоким содержанием в исходном хризотиле немалита, брусита и магнезита.
Таблица 5.
Химическая устойчивость волокон исходного и модифицированного хризотила
Вид хризотила | Потеря массы, % |
---|---|
Щелочестойкость | |
Исходный Модифицированный |
8.74 8.80 |
Kислотостойкость | |
Исходный Модифицированный |
64.85 64.27 |
Исходный и модифицированный хризотил использовали для получения хризотилцемента. В табл. 6 представлены основные физико-механические характеристики полученных изделий. Анализ полученных данных (табл. 6) показал, что плотность хризотилцемента на модифицированном хризотиле, выше по сравнению с использование немодифицированного хризотила. Можно предположить, что это связано с более прочным сцеплением модифицированны волокон хризотила с цементным камнем и ссоотвественно уменьшением пористости изделия.
Таблица 6.
Физико-механические характеристики хризотилцемента
Вид хризотила | Плотность, кг/м3 | Водопогло-щение, % | Предел прочности при изгибе, МПа |
---|---|---|---|
Исходный Модифицированный |
2050 2080 |
12.22 10.95 |
13.3 14.8 |
Из данных табл. 6 видно, что с увеличением плотности хризотилцемента на основе модифицированного хризотила уменьшается водопоглощение по сравнению с хризотилцементом на немодифицированном волокне. В результате увеличения плотности наблюдается повышение прочности хризотилцементных образцов.
Для изучения влияния различных видов волокон хризотила на степень гидратации цемента использовали метод рентгенофазового анализа. Рентгеновская порошковая дифрактограмма хризотилцементных изделий, изготовленных на исходном и модифицированном хризотиле представлена на рис. 2.
Рис. 2.
Рентгеновские порошковые дифрактограммы: 1 – хризотилцемент на исходном хризотиле; 2 – хризотилцемент на модифицированном хризотиле. Условные обозначения: А – алит; П – портландит; Х – хризотил.
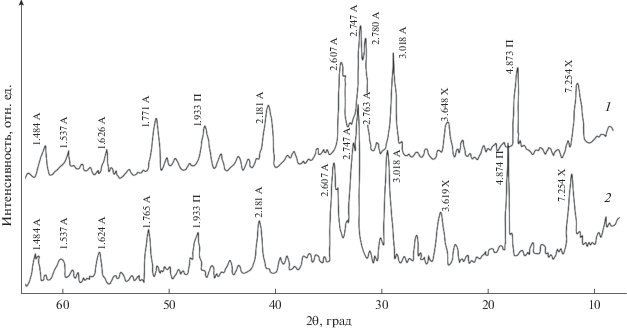
Исследования фазового состава хризотилцемента на основе исходного хризотила показали наличие большого количества непрореагировавшего алита (d/n = 0.3018; 0.2780; 0.2747; 0.2607; 0.2181; 0.1771; 0.1626; 0.1537; 0.1484 нм), что свидетельствует о малой степени гидратации цемента. О наличии гидроксида кальция, как первичного продукта гидратации, свидетельствуют дифракционные отражения (d/n = 0.4874; 0.1933 нм). Для хризотилцемента на основе модифицированного хризотила характерно уменьшение интенсивности пиков непрореагировавшего алита (d/n = = 0.2748; 0.2181; 0.1765 нм) и увеличение пика гидроксида кальция (d/n = 0.2873 нм).
Таким образом можно сказать, что при использовании модифицированного хризотила степень гидратации цемента несколько увеличивается, что обусловлено обработкой хризотила серной кислотой. Активные волокна модифицированного хризотила способствуют отводу продуктов гидратации из зоны реакции, поглощая на своей поверхности гидроксид кальция, способствуя гидратации алита.
ЗАКЛЮЧЕНИЕ
Модифицирование поверхности волокон хризотила раствором серной кислоты способствует повышению степени их распушки с 34 до 47%. Значение электрокинетического потенциала исходного хризотила имеет положительный заряд (ζ = +21.79 мВ). Модифицирование поверности волокон хризотила приводит к перезарядке поверхности волокна и уменьшению абсолютной величины отрицательного заряда поверхности.
Анализ рентгеновских дифракционных характеристик хризотила показал изменение параметров элементарной ячейки до и после модифицирования. Выявленные изменения дифракционных характеристик хризотила до и после модифицирования дают возможность говорить о начале нарушений в октаэдрическом бруситоподобном слое структуры хризотила.
Результаты испытаний сорбционной активности волокон исходного и обработанного кислотой хризотила показали, что в начальный момент времени (10 мин) исходный хризотил обладает большей адсорбционной активностью, однако в последующий период активность модифицированного хризотила увеличивается быстрее, чем у исходного и достигает максимального значения – 0.0359 мг/г. Модифицированный хризотил имеет на 38% большую адсорбционную активность.
В работе на основе экспериментальных данных показано, что щелоче- и кислотоустойчивость модифицированного хризотила практически на уровне исходного. Низкая кислотоустойчивость исследованных образцов объясняется высоким содержанием в исходном хризотиле немалита, брусита и магнезита.
Методом рентгеновской дифракции установлено, что при использовании модифицированного хризотила степень гидратации цемента несколько увеличивается, что обусловлено обработкой хризотила. Активные волокна модифицированного хризотила способствуют отводу продуктов гидратации из зоны реакции, поглощая на своей поверхности гидроксид кальция, способствуя гидратации алита.
Статья подготовлена в рамках программы развития опорного университета на базе БГТУ им. В.Г. Шухова.
Список литературы
Korytkova E.N., Maslov A.V., Pivovarova L.N. et al. // Neorganiceskie materialy. 2005. V. 41. № 7. P. 849.
Korytkova E.N., Pivovarova L.N., Drosdova I.A. et al. // Russian J. of General Chemistry. 2007. V. 77. Issue 10. P. 1669.
Bloise A., Belluso E., Catalano M. et al. // J. Am. Ceram. Soc. 2005. V. 95. P. 3050.
Maslennikova T.P., Korytkova E.N. // Glass Physics and Chemistry. 2011. V. 37. P. 418.
Anastasiadou K., Axiotis D., Gidarakos E. // J. of Hazardous Materials. 2010. V. 179. P. 926.
Горная энциклопедия. Том 5 / Под редакцией Козловского Е.А. М.: Советская энциклопедия, 1991. С. 541.
Свергунов П.В. // Известия Уральского государственного горного университета. 2003. Вып. 18. С. 71.
Liu K., Feng Q., Yang Y. et al. // Journal of Noncrystalline Solids. 2007. V. 353. P. 1534.
Перлин В.Д. // Итого науки и техники. Cерия Неметаллические полезные ископаемые. Том 2. М.: ВНИТИ. 1973. С. 74.
Bonneau L., Malard C., Pezerat H. // Environmental Research. 1986. V. 41. № 1. P. 268.
Foresti E., Gazzano M., Gualtieri A.F. et al. // Analytical and Bioanalytical Chemistry. 2003. V. 376. P. 653.
Нудельман Б.И. // Сборник докладов и выступлений: Современное состояние и перспективы развития асбестоцементной промышленности. 2004. С. 86–90.
Harwood C., Yates B., Badami D.V. // Journal of Materials Science. 1979. V. 14. № 5. P. 1126.
Naumova L.N. // 2nd International Scientific Conference “European Applied Sciences: modern approaches in scientific researches” Stuttgart, Germany, 18–19 February 2013. V. 3. P. 71.
Кнотько А.В., Пустовгар Е.А., Гаршев А.В. и др. // Физикохимия поверхности и защита материалов. 2011. Т. 47. № 5. С. 545.
Chukov D.I., Stepashkin A.A., Gorshenkov M.V. et al. // Journal of Alloys and Compounds. 2014. V. 586. P. 459.
Sui G., Zhong W.H., Ren X. et al. // Materials Chemistry and Physics. 2009. V. 115. P. 404.
Zhou M., Fang D., Jiang D. // Advances in Materials Science and Engineering. 2016. V. 2016. Article ID 5163702.
Rout J.,Tripathy S.S.,Misra M. et al. // Polymer Composites. 2001. V. 22. Issue 4. P. 468.
Ревина А.А., Баранова Е.К. // Физикохимия поверхности и защита материалов. 2010. Т. 46. № 4. С. 376.
Бабаев В.Б., Строкова В.В., Нелюбова В.В. // Вестник Белгородского государственного технологического университета им. В.Г. Шухова. 2012. № 4. С. 58.
Дополнительные материалы отсутствуют.
Инструменты
Физикохимия поверхности и защита материалов