Физикохимия поверхности и защита материалов, 2019, T. 55, № 3, стр. 324-331
Исследование защитного действия покрытия на основе иттрийалюмосиликатной системы на карбидокремниевом материале при температуре до 1500°С
В. А. Воронов 1, *, Ю. Е. Лебедева 1, О. Ю. Сорокин 1, М. Л. Ваганова 1, Д. В. Гращенков 1, Н. И. Артеменко 1, А. В. Заводов 1
1 ФГУП “Всероссийский научно-исследовательский институт авиационных материалов”
105005 Москва, ул. Радио, 17, Россия
* E-mail: voronovvs89@gmail.com
Поступила в редакцию 25.05.2018
После доработки 28.09.2018
Принята к публикации 10.10.2018
Аннотация
Шликерно-обжиговым методом и атмосферно-плазменным напылением получено покрытие на основе прекурсоров иттрийсиликатной и иттрийалюмосиликатной систем на керамическом композиционном материале на основе карбида кремния, а также установлены закономерности влияния окислительной среды на жаростойкость данного покрытия при температуре до 1500°С включительно.
ВВЕДЕНИЕ
В настоящее время прогресс во многих областях техники определяется эксплуатационными характеристиками разрабатываемых материалов и изделий на их основе [1]. В частности, повышение технических параметров узлов и деталей авиационной и космической техники, теплонагруженных систем в области тепло- и атомной энергетики осуществляется благодаря внедрению материалов нового поколения, отвечающих в наибольшей степени комплексу требований, предъявляемых к конструкциям современной и перспективной техники [2, 3].
Мировые усилия исследователей по повышению эффективности авиационных газотурбинных двигателей приводят к необходимости увеличения температуры горения топлива в камере сгорания газотурбинного двигателя. Планируемое увеличение температуры в камере сгорания и турбине высокого давления требует разработки и применения материалов следующего поколения. При этом наиболее подходящими кандидатами являются керамические композиционные материалы (ККМ) на основе карбида кремния (SiC) [4]. Однако применение ККМ на основе SiC в условиях окислительной среды ограничено температурами 1300°С, вследствие их активной коррозии при воздействии продуктами разложения топлива и парами воды, для их защиты необходимо использование функциональных покрытий, которые должны обладать требуемыми свойствами:
– высокая температура плавления (более 1800°C) и высокая стойкость к окислительной атмосфере и водяным парам, низкая кислородная проницаемость;
– химическая совместимость между слоями покрытия и подложкой во всем рабочем диапазоне температур;
– низкая теплопроводность (<3.0 Вт/м К при температуре выше 300°C);
– близкие значения (±10%) температурного коэффициента линейного расширения (ТКЛР) слоев покрытия и материала подложки (~4–6 × 10–6/°C в интервале 200–1600°C); и выполнять следующие функции:
– увеличить долговечность и надежность эксплуатации ККМ и изделий на их основе, стойкостью к длительному окислению и циклическому термическому удару, снижать воздействие химических процессов окисления данных композитов;
– обеспечить сохранение механических свойств SiC-подложки в условиях воздействия градиента температур;
– регулировать изменение температуры на поверхности ККМ с помощью изменения теплопроводности покрытий различного химического состава;
– снижать уровень воздействия процессов эрозии, вибрации и истирания [5, 6].
В настоящее время для достижения целевых значений эксплуатационных характеристик защитных покрытий целесообразно применение концепции многослойных покрытий (на основе оксида циркония, стабилизированного оксидом иттрия; оксидов тугоплавких металлов; муллита, кордиерита; алюмосиликатов стронция и бария; силикатов редкоземельных металлов), однако, результаты мировых исследований показывают, что ряд основных проблем, связанных с выбором материалов, оптимизацией условий методов их получения и нанесения, до сих пор полностью не решен [7–14]. В основном, это приводит к возникновению различных дефектов и термических напряжений как внутри покрытия, так и на границе раздела подложка/покрытие, а, следовательно, к образованию трещин и расслоению, и далее к полному разрушению покрытия в процессе эксплуатации.
Прекурсоры иттрийсиликатной и иттрийалюмосиликатной систем акцентируют на себе внимание, благодаря кристаллизующимся основным фазам: силикатам иттрия Y2SiO5 (Х1 и Х2), Y2Si2O7 (α, δ, β, γ и др.), муллиту 3Al2O3 ⋅ 2SiO2 и иттрийалюминиевому гранату Y3Al5O12, которые обладают высокими значениями необходимых свойств [15–20].
Целью данной работы является разработка высокотемпературного покрытия на основе прекурсоров иттрийсиликатной и иттрийалюмосиликатной систем и исследование процесса его формирования на карбидокремниевом материале, с целью исследования защитных свойств покрытия при воздействии окислительной среды при температуре до 1500°С.
Работа выполнена в рамках реализации комплексного научного направления 14.1: Конструкционные керамические композиционные материалы (“Стратегические направления развития материалов и технологий их переработки на период до 2030 г.”) [1].
ЭКСПЕРИМЕНТАЛЬНАЯ ЧАСТЬ
В настоящей научной работе для получения прекурсоров иттрийсиликатной и иттрийалюмосиликатной систем с различным химическим составом (Y2O3 – 56–83 мас. %; Al2O3 – 0–18 мас. %; SiO2 – 17–39 мас. %) использовался модифицированный твердофазный метод.
В данном методе для высокоэнергетического смешивания и измельчения исходных порошков (оксида иттрий (х. ч., D50 = 26.43 мкм), оксида кремния (х. ч., D50 = 18.26 мкм) и оксида алюминия (х. ч., D50 = 61.71 мкм)) в необходимом соотношении использовали планетарную мельницу в условиях мокрого и “полумокрого” помола с использованием дополнительных хелатирующих агентов в реакционной смеси.
Для нанесения покрытий применяли шликерно-обжиговый метод, который является наиболее широкоприменяемым и универсальным методом. Для его осуществления использовался шликер с гранулометрическим размером частиц до 5 мкм, который стабилизировали и диспергировали в различных растворителях и наносили на подложку ККМ SiC в специальной покрасочной камере. Подложку с нанесенным покрытием подвергали обжигу в электрической печи в среде воздуха или в защитной атмосфере.
Также нанесение покрытий осуществлялось атмосферно-плазменным напылением (АПН) (AMT MP200, Швейцария), которое представляет собой высокоэнергетический процесс нанесения покрытий с температурой плазмы в области 10 000 К и скоростью частиц порошка до 450 м/с. Средний размер используемых части составлял 58.32 мкм.
Изучение фазового состава, морфологии и других физико-химических свойств прекурсоров иттрийалюмосиликатной системы на их основе проводилось в центре коллективного пользования ФГУП “ВИАМ” с помощью метода рентгенофазового анализа (Empyrean PANalytical (Нидерланды) (CuKα-излучение)), электронной микроскопии (Verios 460 XHR (Нидерланды) с приставками для рентгеноспектрального микроанализа и анализа дифракции отраженных электронов), дилатометрии и термогравиметрического анализа (NETZSCH, Германия) и лазерного анализатора размера частиц (Fritsch, Германия).
Исследование жаростойкости высокотемпературных покрытий в диапазоне температур 20–1500°С проводилось в высокотемпературных камерных печах СНОЛ и Nabertherm.
При исследовании окислительной стойкости предполагается контролировать изменение массы (Δm/m0, мас. %, Δm = m1 – m0, где m0 – масса исходного образца, m1 – масса образца после испытания в высокотемпературной печи).
РЕЗУЛЬТАТЫ И ИХ ОБСУЖДЕНИЕ
Подбирая наиболее оптимальные составы защитных покрытий, которые позволяют снизить негативное воздействие продуктов сгорания топлива и паров воды на подложке из ККМ на основе SiC, необходимо учитывать несколько основных характеристик: 1) ТКЛР, который должен быть приближен к значению подложки и/или нижнего слоя (ТКЛР ~4–6 × 10–6/°C), что необходимо для снижения вероятности растрескивания или расслоения при нагревании и охлаждении в широком температурном диапазоне для предотвращения попадания паров воды на подложку; 2) материалы должны быть стабильными и химически совместимыми во всем рабочем диапазоне температур, чтобы между ними или с подложкой не образовывались побочные продукты; 3) толщина защитных покрытий должна составлять порядка 100–250 мкм; 4) скорость деградации защитного слоя должна составлять не более 6–14 мкм на тысячу ч [21].
Бинарная система Y2O3–SiO2 была изучена Н.А. Тороповым и А.М. Бондарем. Диаграмма состояния системы показана на рис. 1 [22]. В данной системе известны три двойных соединения: Y2O3 · SiO2 – оксиортосиликат, 2Y2O3 · 3SiO2 – ортосиликат и Y2O3 · 2SiO2 – пиросиликат иттрия. Основными фазами данной системы являются Y2SiO5 (плавится конгруэнтно при 1980°С) и δ-Y2Si2O7 (плавится инконгруэнтно при ~1790°С). Соединение 2Y2O3 · 3SiO2 устойчиво в температурной области 1350–1650°С. При 1650°С это соединение претерпевает распад с образованием смеси двух соединений: Y2O3 · SiO2 и Y2O3 · 2SiO2, причем указанный процесс является обратимым [23].
Y2SiO5 встречается в виде двух модификаций (Х1 и Х2). Высокотемпературная фаза (Х2-фаза) силиката иттрия (Y2SiO5) обладает рядом преимуществ: хорошим сопротивлением эрозии и пониженной кислородной проходимостью при высоких температурах, что дает возможным использовать Y2SiO5 в антиокислительных защитных покрытиях для ККМ SiC. Однако, коэффициент термического расширения у Y2SiO5 выше, чем у карбида кремния, поэтому и высока вероятность возникновения микротрещин вдоль границ раздела фаз. В связи с этим необходимо высокое процентное содержание Y2Si2O7 в покрытиях для максимального приближения к ТКЛР SiC и обеспечения стабильности при термическом воздействии.
Y2Si2O7 имеет шесть различных модификаций (y, α, β, γ, δ и z). В табл. 1 указаны объемные изменения, связанные с фазовыми переходами между полиморфными модификациями дисиликата иттрия при нагревании [24].
Таблица 1.
Объемные изменения, связанные с фазовыми переходами между полиморфными модификациями дисиликата иттрия Y2Si2O7 при нагревании [24]
Переход полиморфных модификаций | Температура, °С | Изменение объема, % |
---|---|---|
α → β | 1225 | +6.233 |
β → γ | 1445 | –0.198 |
γ → δ | 1535 | –1.733 |
β → δ | – | –1.984 |
Y2Si2O7 является тугоплавким соединением и устойчив в окислительной атмосфере. Из шести полиморфных модификаций γ-Y2Si2O7 является высокотемпературной фазой, устойчивой в области температур 1445–1535°С, имеет низкий ТКЛР (3.9 × 10–6/°С в интервале температур 200–1300°C) и низкую теплопроводность (<3.0 Вт/м К при температуре выше 300°C) [25].
Высокая температура плавления, низкая кислородная проницаемость, коэффициент термического расширения, близкий по значению к ТКЛР карбида кремния – все это делает силикаты иттрия превосходными компонентами для защиты материалов на основе карбида кремния от воздействия высоких температур в окислительной атмосфере [26].
Диаграмма состояния системы Y2O3–Аl2О3–SiO2 (рис. 2) состоит из 11 полей устойчивости следующих фаз: I – области двух стекол; II – кристобалита; III – диорто- (пиро-) силиката иттрия (Y2O3 · 2SiO2); IV – ортосиликата (2Y2O3 · 3SiO2); V – оксиортосиликата (Y2O3 · SiO2); VI – окиси иттрия (Y2O3); VII – алюмината иттрия (2Y2О3 · А12О3); VIII – соединения типа перовскита (Y2О3 · А12О3); IX – соединения типа граната (3Y2O3 · 5А12О3); X – корунда; XI – муллита (3А12О3 · 2SiO2). Тройных соединений в данной системе пока не обнаружено, эвтектическая температура составляет 1370–1387°С [35 ] . На диаграмме состояния иттрийалюмосиликатной системы установлено восемь тройных точек, две из которых являются эвтектическими и шесть – реакционными.
Модифицированным твердофазным методом был получен ряд прекурсоров иттрийалюмосиликатной и иттрийсиликатной системы (табл. 2).
Таблица 2.
Исследуемые составы систем Y2O3–SiO2 и Y2O3–Al2O3–SiO2
Обозначение | Y2O3 | Al2O3 | SiO2 | |||
---|---|---|---|---|---|---|
мол. % | мас. % | мол. % | мас. % | мол. % | мас. % | |
Y-25 | 25 | 61 | – | – | 75 | 39 |
Y-33 | 33 | 70 | – | – | 67 | 30 |
Y-50 | 50 | 82.6 | – | – | 50 | 17.4 |
YAS-15 | 11.1 | 29 | 15.92 | 20.3 | 72.98 | 50.7 |
YAS-30 | 20 | 41.7 | 30 | 30.5 | 50 | 27.8 |
Процессы фазообразования и исследование поведения прекурсоров при термической обработки в диапазоне 900–1300°С изучали с помощью рентгенофазового анализа (РФА) и термогравиметрического анализа (ТГА).
Дериватографические кривые прекурсоров YAS-15 и YAS-30 представлены на рис. 3. Для состава YAS-15 наблюдалось наличие экзоэффекта при температуре 1015–1020°С, связанного с образованием β-модификации дисиликата иттрия (β-Y2Si2O7). При температуре 1156°С образуется муллит. При температуре 1260°С кристаллизация высокотемпературной модификации оксиортосиликата иттрия Х2-Y2SiO5 сопровождается значительным поглощением тепла. При температуре 1357°С β-Y2Si2O7 полностью переходит в δ-Y2Si2O7, что подтверждается наличием эндотермического эффекта на дериватограмме при указанной температуре, а при 1387°С происходит образование эвтектики. При температуре 1408°С остаточная стеклофаза размягчается и происходит плавление в ней кристаллических фаз.
Для состава YAS-30 с содержанием Y2O3 20 мол. % пик при температуре 1085°С сдвигается в сторону более высоких температур. При температуре 1260°С в обоих составах начинает образовываться твердый раствор дисиликата иттрия Y2Si2O7, а при температуре 1356°С образуется фаза иттрийалюминиевого граната. Температура 1418°С является температурой инвариантной точки, при которой твердые растворы силикатов иттрия полностью переходят в кристаллические фазы высокотемпературных модификаций: X2-Y2SiO5 и δ-Y2Si2O7, образуется стеклофаза. Данные составы попадают на диаграмме состояния вблизи инвариантной точки и в области кристаллизации силикатов иттрия и иттрийалюминиевого граната. При температуре 1500 и 1507°С происходит растворение всех кристаллических фаз в образовавшейся стеклофазе.
Для прекурсоров Y-25, Y-33, Y-50 наблюдались экзотермические эффекты, обусловленные фазовыми превращениями, которые проявлялись при температурах 1050–1180°С. Начало кристаллизации отмечено при температуре 900°С.
Идентификацию образующихся кристаллических фаз проводили посредством РФА. Процесс кристаллизации начинается при температуре 900°С в составах Y-33 и Y-50, отвечающих стехиометрическим составам Y2Si2O7 и Y2SiO5 соответственно. Структура остальных образцов в основном аморфна, кристаллическая фаза присутствует в них в незначительном количестве независимо от состава. При увеличении температуры термообработки содержание аморфной фазы в большинстве образцов резко снижается, это подтверждается значительным сокращением на дифрактограммах диффузной области, появлением четких интенсивных линий, соответствующих различным кристаллическим фазам. В табл. 3 приведены обобщенные данные по кристаллизации исследованных иттрийсиликатных составов в интервале температур 900–1300°С.
Таблица 3.
Характер кристаллизации системы Y2O3–Al2O3–SiO2 и Y2O3–SiO2 при термообработке в интервале 900–1300°С
Температура термообработки, °С | Состав | ||||
---|---|---|---|---|---|
Y-25 | Y-33 | Y-50 | YAS-15 | YAS-30 | |
900 | Aморфная фаза | α-Y2Si2O7, аморфная фаза |
X1-Y2SiO5, аморфная фаза |
Aморфная фаза | X1-Y2SiO5, аморфная фаза |
1000 | α-Y2Si2O7, аморфная фаза |
α-Y2Si2O7, аморфная фаза |
X1-Y2SiO5, аморфная фаза |
α-Y2Si2O7, аморфная фаза |
α-Y2Si2O7, X1-Y2SiO5, аморфная фаза |
1100 | δ-Y2Si2O7, α-Y2Si2O7, аморфная фаза |
δ-Y2Si2O7, α-Y2Si2O7, аморфная фаза |
X1-Y2SiO5, аморфная фаза |
δ-Y2Si2O7, α-Y2Si2O7, X1-Y2SiO5, аморфная фаза |
δ-Y2Si2O7, α-Y2Si2O7, X1-Y2SiO5, аморфная фаза |
1200 | δ-Y2Si2O7, SiO2 |
δ-Y2Si2O7 | X2-Y2SiO5 | δ-Y2Si2O7, X2-Y2SiO5 | δ-Y2Si2O7, X2-Y2SiO5 |
1300 | δ-Y2Si2O7, SiO2 |
δ-Y2Si2O7 | X2-Y2SiO5 | Муллит, δ-Y2Si2O7, X2-Y2SiO5 | δ-Y2Si2O7, Y3Al5O12, X1-Y2SiO5 |
Для состава, содержащего 25% Y2O3 и находящегося в поле кристаллизации дисиликата иттрия, в интервале температур 900–1300°С характерно образование именно этой фазы. Причем отмечается присутствие двух полиморфных форм: низкотемпературной α-Y2Si2O7 и высокотемпературной δ-Y2Si2O7, образующейся при температуре 1100°С. Кроме того, в образцах, термообработанных при 1200 и 1300°С, в небольших количествах присутствует α-кристобалит.
При более высоком содержании Y2O3, равном 33% (стехиометрический состав дисиликата иттрия), образуется однофазный продукт, состоящий из α- и δ-модификаций Y2Si2O7. На дифрактограммах указанным модификациям соответствуют рефлексы: для α – формы Y2Si2O7 – 3.01100 Å, 2.9180 Å и 2.8050 Å (ASTM № 38-0223), для δ – модификации Y2Si2O7 – 2.87100 Å, 3.0880 Å и 4.0770 Å (ASTM № 45-0043).
При максимальном содержании Y2O3 – 50% (стехиометрический состав оксиортосиликата иттрия) – в области температур выше 900°С образуется низкотемпературная форма Y2SiO5 (Х1, ASTM № 21-1456), которая в интервале температур 1200–1300°С переходит в доминирующую высокотемпературную модификацию Y2SiO5 (Х2, ASTM № 21-1458).
Однако, одним из недостатков применяемого твердофазового метода являются то, что на дифрактограммах полученных образцов присутствовали рефлексы оксида иттрия (менее 1.2 мас. %), даже в составах, содержащих SiO2 50 мол. %.
Для определения ТКЛР прекурсоров систем (Y2O3–SiO2 и Y2O3–Al2O3–SiO2), проводили термическую обработку порошков при 1300°С и измельчали в планетарной мельнице с шарами из оксида циркония до среднего размера частиц менее 5 мкм. Далее порошок был отпрессован на гидравлическом прессе при давлении 100 МПа в штабики с размером сечения 30 × 6 мм. В качестве связки использовался поливиниловый спирт в количестве 0.1 мас. %. После прессования образцы высыхали в течение суток, затем их подвергли термообработке при Т = 1300°С в течение 1 ч.
Значения ТКЛР исследуемых образцов представлены в табл. 4. Состав с наименьшим содержанием оксида иттрия Y-25 из-за присутствия α‑кристобалита имеет более высокий ТКЛР по сравнению с остальными. Так как значение ТКЛР подложки на основе SiC ККМ составляло 50.4 × 10–7, K–1, а у прекурсора Y-25 – 69.8 × 10–7, K–1, данный состав был исключен.
Таблица 4.
Фазовый состав и значения ТКЛР спеченных при Т = 1300°С образцов
Образец | Кристаллические фазы | ТКЛР × 10–7, K–1 |
---|---|---|
ККМ SiC | SiC | 50.4 |
Y-25 | δ-Y2Si2O7, SiO2 (α-кристобалит) | 69.8 |
Y-33 | δ-Y2Si2O7 | 49.6 |
Y-50 | X2-Y2Si2O5 | 58.3 |
YAS-15 | Муллит, δ-Y2Si2O7, X2-Y2SiO5 | 52.3 |
YAS-30 | δ-Y2Si2O7, Y3Al5O12, X1-Y2SiO5 | 55.7 |
На основании полученных результатов были предложены составы покрытий (табл. 5). С целью избегания расслаивания и растрескивания покрытия в ходе термического циклирования, выбор состава слоев покрытия подбирался из расчета +/–10% относительно значения ТКЛР нижнего слоя.
Таблица 5.
Составы покрытий
№ покрытия | Y-33 | YAS-15 | YAS-30 | Y-50 |
---|---|---|---|---|
1 | 1 слой (15–20 мкм) | 2 слой (35–40 мкм) | - | 3 слой (65–70 мкм) |
2 | 1 слой (35–40 мкм) | 2 слой (45–50 мкм) | - | 3 слой (85–90 мкм) |
3 | 1 слой (15–20 мкм) | – | 2 слой (35–40 мкм) | 3 слой (65–70 мкм) |
4 | 1 слой (35–40 мкм) | – | 2 слой (45–50 мкм) | 3 слой (85–90 мкм) |
Шликерным методом и атмосферно-плазменным напылением были нанесены покрытия в соответствии с табл. 5 и произведен их обжиг при температуре 1600°С в течение 1 ч, с целью достижения равномерного однородного покрытия.
В результате, на покрытиях № 3 и 4 отчетливо наблюдались поры и трещины. Вероятно, образование трещин и расслоение происходило из-за наличия фазы алюмоиттриевого граната, обладавшей повышенным значением ТКЛР (55.7 × 10–7, K–1) относительно нижнего слоя (49.6 × 10–7, K–1), и наличия избыточной фазы дисиликата иттрия, которая имеют тенденцию к трещинообразованию при работе и во время термического циклирования. Также дисиликаты иттрия склонны к выщелачиванию SiO2 и разрушению поверхности посредством химических взаимодействий с окислительной средой. Такое выщелачивание создает микропористую структуру в покрытие, и изначально плотное покрытие преобразуется в пористый слой раньше требуемого срока его службы (рис. 4а).
Рис. 4.
Микрофотографии покрытий после формирования на ККМ SiC a – покрытие № 4; б, в – покрытие № 2.
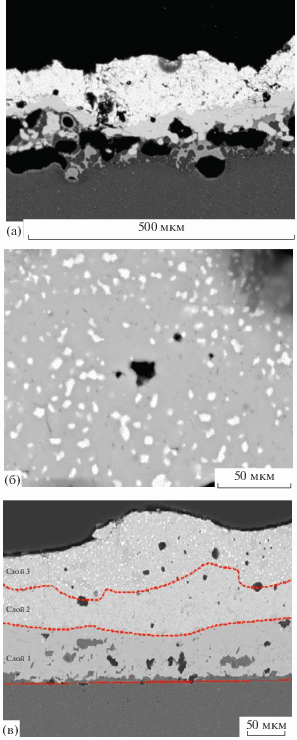
На покрытиях № 1 и 2 наблюдалось минимальное количество пор и микротрещин. По микрофотографиям покрытия № 2 (рис. 4б, 4в) можно сделать предположение, что благодаря оптимально выбранным фазовому составу, т.е. согласованию значений ТКЛР каждого слоя многослойного покрытия, и толщине каждого слоя покрытия, покрытие является отличным кандидатом для исследования характера воздействия окислительной атмосферы при температуре 1500°С в течение длительного времени.
РСМА анализом удалось установить химический состав каждого слоя покрытия № 2. Основой нижнего слоя (толщина ≈ 55 мкм) являлся дисиликат иттрия Y2Si2O7 c небольшими примесями иттрия, алюминия и кремния (до 5 ат. %). Размеры продолговатых зерен дисиликата иттрия не превышали 40 мкм. Также наблюдались мелкие светлые включения в зернах дисиликата иттрия, которые являлись зародышами моносиликата иттрия Y2SiO5. Средний слой (толщина ≈ 40 мкм) представлял собой плотно расположенные зерна муллита (средний состав Al6Si2O13), а в прослойках между ними находились области дисиликата иттрия Y2Si2O7. Верхний слой (толщина ≈ 70 мкм) характеризовался двумя основными фазами: дисиликатом иттрия Y2Si2O7 и моносиликом иттрия Y2SiO5, не превышавшими в размере 10 мкм. Помимо этого в слое присутствовали тонкие трещины, проходившие через обе фазы. Доля зерен моносиликата иттрия превышала 90%.
На рис. 5 представлена микрофотография шлифа покрытия № 2 после термической обработки при 1500°С в течение 100 ч. На снимке с общим видом покрытия отчетливо различаются три слоя: верхний, средний и нижний пористый слой, граничащий с керамической подложкой.
РСМА анализом удалось установить химический состав каждого слоя покрытия. Основной нижнего слоя (толщина от 30 до 100 мкм) являются дисиликат иттрия Y2Si2O7 и алюмосиликат иттрия со средним составом Y2AlSi4O13. При этом наблюдалось образование оксида кремния, размер зерен которого достигал 20 мкм, особенно данные зерна локализовались на границе подложка/покрытие. Также, в связи с разложением дисиликата иттрия, наблюдались дендритообразные участки, относившиеся к фазе оксида иттрия. Средний слой толщиной 20–50 мкм представлен плотно расположенными зернами муллита. Однако в образовавшихся пустотах и прослойках между зернами муллита находились области обогащенные фазой дисиликата иттрия Y2Si2O7. При этом в данной области происходило частичное разложение дисиликата иттрия с образованием оксида кремния и оксида иттрия, а также мелких зерен моносиликата иттрия с размером до 1.5 мкм. Верхний слой (толщина ≈ 70 мкм) характеризовалась двумя основными фазами: дисиликатом иттрия Y2Si2O7 и моносиликом иттрия Y2SiO5. Однако размер областей, обогащенных дисиликатом иттрия значительно увеличился и достигал до 30 мкм. Это привело к образованию пор и трещин в верхнем слое покрытия. Доля зерен моносиликата иттрия снизилась до 83%.
После термической обработки 100 ч при 1500°С в окислительной атмосфере потеря массы образца с покрытием № 2 составила только 0.57%, при этом потеря массы образцов не фиксировалась до 63 ч.
ЗАКЛЮЧЕНИЕ
Таким образом, в настоящей работе показана возможность получения высокотемпературного покрытия на основе иттрийсиликатной и иттрийалюмосиликатной системы на карбидокремниевых материалах. Разработанное покрытие № 2 обладает наиболее сплошным покрытием с минимальным количеством пор и микротрещин, а также повышенной термической стойкостью, потеря массы образца с покрытием после термической обработки 100 ч при 1500°С в окислительной атмосфере составила только 0.57%.
Список литературы
Каблов Е.Н. // Авиационные материалы и технологии. 2015. № 1. С. 3–33. https://doi.org/10.18577/2071-9140-2015-0-1-3-33
Naslain R., Christin F. // MRS Bull. 2003. V. 28. P. 654–658.
Schmidt S., Beyer S., Knabe H., Immich H., Meistring R., Gessler A. // Acta Astronaut. 2004. V. 55. P. 409–420.
Dong J.P., Yang J., Kim H.G., Park J.Y., Yang H.K. // Corros. Sci. 2014. V. 88. P. 416–422.
Kablov E.N., Zhestkov B.E., Grashchenkov D.V., Sorokin O.Yu., Lebedeva Yu.E., Vaganova M.L. // High Temperature. 2017. V. 55. № 6. P. 857–863.
Wang Y.G., Wu Y.H., Cheng L.F., Zhang L.T. // J. Am. Ceram. Soc. 2009. V. 93. P. 204–208.
Richards B.T., Sehr S., Foucault de Franqueville, Begley M.R., Wadley H.N. // Acta Mater. 2016. V. 103. P. 448–460.
Lee K.N. Protective coatings for gas turbines, in: R. Dennis Ed., The Gas Turbine Handbook, United States Department of Energy DOE, 2006.
Lee K.N., Fox D.S., Bansal N.P. // Corros. Ceram. Matrix Compos. 2005. V. 25. P. 1705–1715.
Jacobson N.S., Fox D.S., Smialek J.L., Deliacorte C., Lee K.N. in: GRC Ed., Performance of Ceramics in Severe Environments, NASA Glenn Research Center, Cleveland, OH, USA, 2005.
Lee K.N., Fox D.S., Eldridge J.I., Zhu D., Robinson R.C., Bansal N.P., Miller R.A. // J. Am. Ceram. Soc., 2003. V. 86. P. 1299–1306.
Patent 7 357 994 US, Int/. Cl. B 32 B 9/04. Thermal/ environmental barrier coating system for silicon-based materials / Brian Thomas Hazel, Irene Spitsberg; General Electric Company, 2005.
Fernandez-Carrion A.J., Allix M., Becerro A.I. // J. Am. Ceram. Soc. 2013. V. 96. P. 2298–2305.
Al Nasiri N., Patra N., Horlait D., Jayaseelan D.D., Lee W.E. // J. Am. Ceram. Soc. 2016. V. 99. P. 589–596.
Liddell K., Thompson D.P. // Br. Ceram. Trans. 1986. V. 85. P. 17–22.
Kolitsch U., Seifert H.J., Ludwig T., Aldinger F. // J. Materials Research. 1999. V. 14. № 2. P. 447–455.
Fukuda K., Matsubara H. // J. Amer. Ceram. Soc. 2004. V. 87. № 1. P. 89–92.
Саркисов П.Д., Попович Н.В., Орлова Л.А., Лебедева Ю.Е., Уварова Н.Е. // Все материалы. Энциклопедический справочник. 2011. № 6. С. 2–8.
Lebedeva Yu.E., Popovich N.V., Orlova L.A., Chainikova A.S., Sorokin O.Yu., Vaganova M.L., Grashchenkov D.V. // Russian J. Inorganic Chemistry. 2017. V. 62. № 8. P. 1032–1037.
Lebedeva Yu.E., Popovich N.V., Orlova L.A., Chainikova A.S. // Glass and Ceramics. 2015. V. 71. № 11–12. P. 400–404.
Aparicio M., Durán A. // J. Am. Ceram. Soc. 2000. V. 83. P. 1351–1355.
Торопов И.А. и др. Диаграммы состояния силикатных систем. Справочник, М.–Л., Наука. 1965. 258 с.
Emilie Courcot, Francis Rebillat, Francis Teyssandier // J. European Ceramic Society. 2010. V. 30. P. 905–910.
Рабухин А.И., Савельев В.Г. Физическая химия тугоплавких неметаллических и силикатных соединений. М.: ИНФРА-М, 2008. 296 с.
Ziqi Sun, Meishuan Li, Yanchun Zhou // J. Am. Ceram. Soc. 2008. V. 917. P. 2236–2242.
Webster J.D., Westwood M.E., Hayes F.H. // J. Eur. Ceram. Soc. 1998. V. 18. P. 2345–2350.
Дополнительные материалы отсутствуют.
Инструменты
Физикохимия поверхности и защита материалов