Физикохимия поверхности и защита материалов, 2019, T. 55, № 4, стр. 415-428
Влияние режимов термообработки на структуру и коррозионную стойкость плазменных покрытий из сплавов на основе никеля и железа
Ю. А. Пустов 1, *, В. И. Калита 2, **, ***, Д. И. Комлев 2, А. А. Радюк 2, А. Ю. Иванников 2
1 Национальный исследовательский технологический университет “МИСиС”
119049 Москва, Ленинский пр., 4, Россия
2 Институт металлургии и материаловедения им. А.А. Байкова РАН
119991 Москва, Ленинский пр., 49, Россия
* E-mail: pustov@misis.ru
** E-mail: vkalita@imet.ac.ru
*** E-mail: imet-lab25@yandex.ru
Поступила в редакцию 27.10.2018
После доработки 04.02.2019
Принята к публикации 07.02.2019
Аннотация
Изучены структурное состояние и коррозионная стойкость плазменных покрытий на основе железа (сплав ФБХ6-2) и никеля (сплав RW 12496 компании “Castolin”) в водных растворах гидроксида натрия и азотной кислоты после различных режимов термической обработки. Проведено сопоставление структурных и электрохимических характеристик покрытий из этих сплавов с их аналогами, находящимися в литом состоянии, прошедшими соответствующую термическую обработку. Показана определяющая роль морфологической гетерогенности поверхности покрытий в формировании их коррозионно-электрохимических характеристик. Описан специфический характер развития коррозионного процесса, обосновывающий значительное ухудшение их коррозионной стойкости по сравнению с литыми сплавами. Установлено, что влияние морфологических дефектов поверхности покрытий (каверн, микротрещин, шероховатостей, открытых пор и т.п.) на развитие коррозионного процесса может быть значительно ограничено, а в ряде случаев практически полностью исключено, пропиткой гидрофобизирующей жидкостью Анакрол-2501 с высокой проникающей способностью. Проведены коррозионные испытания покрытий. Показано, что пропитка приводит к значительному уменьшению скорости их коррозии, которая становится сопоставимой со скоростью коррозии отожженных литых образцов.
ВВЕДЕНИЕ
Плазменное напыление покрытий является высокоэффективным способом модифицирования поверхности металлических изделий, обеспечивающим существенное изменение физико-механических, физических и химических свойств исходного материала и, как результат, достижение требуемых функциональных характеристик изделий (например, повышенных (по отношению к основному материалу) механических характеристик, износостойкости, коррозионной стойкости, в том числе к кавитационной коррозии, и др.) [1–13]. При этом при выборе материалов для износостойких покрытий акцент делается на порошковые композиции, содержащие в своем составе повышенные концентрации хрома и никеля, а также неметаллов (углерода, кремния, бора, фосфора), которые при определенных технологических режимах распыления могут способствовать формированию аморфной или аморфно-нанокристаллической структуры покрытий [1–3, 11–18]. К таким композициям относятся, в частности, сплавы эвтектического состава (мас. %): ФБХ6-2 (Fe-основа; (32–35)Cr; (1.9–3.7)Mn; (4.0–4.2)C; (2.0–2.2)Si; (1.6–2.0)B; (0.1–0.2)S; (0.10–0.12)P), сплав SHS7574HV1 компании “Nanosteel” (Fe-основа; 25Cr; 3C; 5B; 10W; 15Mo; 5Mn; 2Si), сплав Eutalloy RW 12496 компании “Castolin” (Ni-основа; (14.5–15.0)Cr; (4.0–4.5)Si; (3.5–4.0)Fe; (3.1–3.5)B; (0.7–0.8)C). Однако структурное состояние и химический состав покрытий являются лишь одними из возможных факторов, определяющих функциональные свойства покрытий. Существенным недостатком покрытий, оказывающим влияние на их физико-механические и физико-химические свойства, является наличие пористости, которая частично устраняется оплавлением и термомеханической обработкой [1–3, 19]. При этом важно отметить, что уменьшение пористости покрытий этими способами возможно только для случаев несквозной, т.е. объемной, пористости в покрытии, в то время как при наличии сквозной пористости термомеханическое воздействие может приводить к разрушению покрытия. Одним из факторов, определяющих возможность существования сквозной пористости, является толщина плазменного покрытия. В работе [19] на примере покрытий из сплавов ФБХ6-2 (тип ПН-У45Х35ГСР) и SHS7574HV1 показано, что сквозная пористость и ее влияние на коррозионное поведение системы “металл-подложка (Ст. 3) – плазменное покрытие” уменьшается при увеличении толщины покрытий с 50 до 200 мкм. В “тонких” покрытиях (50–100 мкм) сквозная пористость обеспечивает доступ коррозионной среды к границе раздела “подложка – покрытие”, формирование коррозионного гальванического элемента подложка-“анод” – покрытие-“катод”, результатом работы которого является коррозионное разрушение подложки. Продукты электрохимической коррозии материала подложки обнаруживаются не только в области границы раздела, но и на поверхности покрытий, что обусловлено возможностью выхода металлических ионов (в основном, железа) через сквозные поры. Следствием такого развития коррозионного процесса являются потеря адгезионной прочности и отслаивание покрытия от подложки. Влияние сквозной пористости в тонких покрытиях практически полностью устраняется применением пропитки гидрофобизирующей жидкостью с высокой проникающей способностью АНАКРОЛ-2501. В более толстых покрытиях (150–200 мкм) возникают диффузионные ограничения проникновению коррозионной среды к границе раздела, а сквозные поры “забиваются” продуктами коррозии самого покрытия и существенно препятствуют доступу электролита к металлической подложке [19].
Полученные в работе [19] результаты дают основание полагать, что увеличение толщины плазменных покрытий может в значительной степени уменьшить вероятность возникновения сквозной пористости в покрытиях или даже полностью исключить ее образование. Вместе с тем функциональные характеристики покрытий (абразивный износ, устойчивость к эрозии, кавитации и кавитационной коррозии и др.) не ограничиваются только существованием или отсутствием сквозной пористости. Характерным и неустранимым полностью недостатком плазменных покрытий является их объемная пористость, которая по разным оценкам может колебаться в пределах от 10 до 15%. Ее частичное уменьшение путем применения “жестких” методов обработки (обкатка роликом с пропусканием и без пропускания электрического тока, термомеханическая обработка, оплавление) [20] может сопровождаться как механическим разрушением покрытий, так неконтролируемыми структурными превращениями, результатом которых является образование новых и увеличение доли существующих кристаллических фаз (по отношению к исходному аморфному или аморфно-кристаллическому состоянию покрытий).
Наиболее предпочтительным способом уменьшения объемной пористости представляется изотермический отжиг в области относительно умеренных температур (400–800°С) [9, 17, 20], но и в этом случае следует ожидать повышения гетерогенности структуры покрытий и, как следствие, ускорение развития коррозионных процессов. Однако вопросам изучения коррозионной стойкости покрытий, в том числе и влияния изменения структуры покрытий после термообработки на их сопротивление коррозии, не уделяется должного внимания. Это связано не только со сложностью интерпретации полученных результатов в многофазных и многокомпонентных системах, каковыми являются плазменные покрытия. Имеются основания полагать [19, 21], что на развитие коррозионных процессов в покрытиях в отсутствие сквозной пористости оказывают существенное влияние морфологические дефекты приповерхностных слоев покрытий (каверны, микротрещины, несквозные поры и т.п.) [8, 9, 23] роль которых исследователями даже не принимается во внимание. Более того, негативное влияние специфической морфологии поверхности на развитие коррозионных процессов может быть даже более значимым фактором, чем присутствие в составе покрытий таких компонентов как хром и никель, традиционно вводимых в состав компактных сталей и сплавов для повышения их коррозионной стойкости.
В связи с выше изложенным целью настоящей работы является изучение влияния режимов термической обработки плазменно-напыленных на металлическую подложку порошковых сплавов на основе железа (ФБХ6-2) и никеля (Eutalloy RW 12496 – далее сплав 12496) на структуру покрытий, их коррозионно-электрохимическое поведение и коррозионную стойкость в нейтральной и кислой средах, и сравнение со структурой и устойчивостью к коррозионному разрушению литых (компактных) аналогов этих сплавов.
Покрытия из сплавов ФБХ6-2 и 12496 используются для восстановления и упрочения поверхности, применяются в геологоразведочной и буровой технике в условиях работы с агрессивными средами. В частности, сплав ФБХ6-2, который относится к высокохромистым чугунам, используется для получения покрытий методами наплавки или плазменного напыления на деталях геологоразведочного, угледобывающего и торфоперерабатывающего оборудования, работающих в условиях абразивного изнашивания, в том числе в коррозионно-активных средах. Так при разработке торфяных месторождений торфоперерабатывающее оборудование находится не только под действием твердых дисперсных частиц (диаметром менее 250 мкм), но и имеет контакт с неорганической массой, состоящей из 50–60% углерода, 5–6.5% водорода, 30–40% кислорода, 1–3% азота и до 2.5% серы. Кроме того, для торфа характерно высокое влагосодержание, достигающее 96%. С учетом высокого влагосодержания неорганические компоненты, находясь в растворенном состоянии, могут образовывать жидкие среды повышенной коррозионной агрессивности.
ОБЪЕКТЫ ИССЛЕДОВАНИЯ И ЭКСПЕРИМЕНТАЛЬНЫЕ МЕТОДЫ
Исходные порошки для плазменного напыления покрытий из сплавов ФБХ6-2 и 12496 имели следующие химические составы (масс. доля, %):
• ФБХ6-2: Fe – основа; Cr – 32.0; С – 4.2; Si – 2.2; Mn – 1.9; B – 2.0; S – 0.2; P – 0.12.
• Сплав 12496: Ni – основа; Cr – 14.80; Si – 4.10; Fe – 3.88; B – 3.13; C – 0.78.
Технология получения покрытий, позволяющая обеспечить оптимальные режимы распыления (снижение влияния атмосферного кислорода, устранение теплового воздействия плазменного потока на покрытие, однородность фазового состава напыленных частиц, аморфизация структуры покрытия и т.п.) подробно описана в работе [20]. В качестве материала подложки использовали сталь марки Ст. 3. Покрытия наносили на внешнюю поверхность полых образцов цилиндрической формы (внешний диаметр – 15 мм; внутренний диаметр – 5 мм; высота – 5 мм). Напыление проводили только на внешний периметр образца, толщина напыленного слоя составляла около 400 мкм. Перед нанесением покрытия порошком сплава 12496 на поверхность подложки был нанесен подслой порошка нихрома (Ni-20% Cr) толщиной порядка 25 мкм.
Образцы с покрытиями отжигали в запаянных стеклянных ампулах с разряжением 13.3 Па в течение 3 ч при температурах 430 или 800°С (сплав 12496) и 550 или 800°С (ФБХ6-2). Отжиг при 430 и 550°С обеспечивал формирование аморфно-нанокристаллической структуры покрытий [23]. Отжиг при 800°С применяли для уменьшения объемной пористости и изучения влияния структурных превращений (микрокристаллизации) в покрытиях на их коррозионную стойкость.
С целью идентификации кристаллических фаз, формирующихся в процессе термообработки, проводили отдельный эксперимент по отжигу образцов с покрытиями при температуре 1000°С в течение 5 ч.
Для оценки влияния морфологии поверхности покрытий на их коррозионную стойкость изготавливали литые образцы сплавов путем расплавления исходных порошков в керамических тиглях в атмосфере аргона. Литые образцы сплавов подвергали отжигу при 800°С в течение 3 ч в условиях, аналогичных используемым для образцов с покрытиями.
Количественный рентгенофазовый анализ литых образцов и покрытий проводили с помощью дифрактометра ДРОН-УМ в монохроматизированном CoKα-излучении. Микроструктуру покрытий, количественный анализ состава покрытий и профиль распределения элементов по их толщине изучали с помощью растрового электронного микроскопа JEOL JSM – 6610 LV. Для выявления микроструктуры поперечные шлифы образцов с покрытиями подвергали травлению в водном растворе, содержащем 5 мг/л HNO3 и 2 мг/л HF.
Электрохимические исследования литых образцов и образцов с покрытиями проводили при комнатной температуре в растворах 3% NaCl и 0.5 н HNO3. Использовали трехэлектродную электрохимическую ячейку с разделенным электродным пространством. Применяли методы хронопотенциометрии и потенциодинамической вольтамперометрии со скоростью развертки 0.2 мВ/с. Анодную поляризацию образцов проводили после достижения стационарного потенциала в каждой из коррозионных сред. В качестве электрода сравнения использовали насыщенный хлорид-серебряный электрод, а в качестве вспомогательного электрода – платиновый электрод. При проведении измерений на образцах с покрытиями непокрытые участки стальной подложки защищали химически стойким лаком ХСК-2467, устойчивым в растворах солей, кислот и щелочей. В каждой серии опытов проводили по 3–4 измерения электрохимических характеристик.
Коррозионные испытания образцов проводили методом полного погружения в соответствующие растворы в течение 30 сут, достаточных для установления стационарных режимов коррозии, о которых судили по кинетике изменения электродных потенциалов образцов в процессе экспозиции. Оценку скорости коррозии проводили гравиметрическим методом по результатам измерения потерь массы образцов с последующим расчетом глубинного показателя коррозии (мм/год) [24]. Массу образцов измеряли с помощью аналитических электронных весов Adventurer OHAUS (чувствительность 0.001 г).
Для оценки влияния морфологического строения поверхностных слоев покрытий на коррозионную стойкость проводили их пропитку гидрофобизирущей жидкостью АНАКРОЛ-2501 [25], представляющей собой термореактивный раствор на основе акрилового полимера в смеси растворителей. Жидкость рекомендована для герметизации микропор и микротрещин на поверхности материалов (в т.ч. металлов) с размером дефектов до 0.1 мм. Состав не вызывает коррозии металлов и сплавов, проникая в микродефекты, отверждается с образованием высокопрочного, эластичного материала. В результате пропитки, на поверхности образца образуется пленка толщиной до 10 мкм. Пленка не ломка и выдерживает механические вибрации. Пропитку проводили методом “погружения в состав” при 25°С в течение 2 мин. Отверждение герметика осуществляли в сушильном шкафу при 80°С в течение 2 ч.
РЕЗУЛЬТАТЫ И ОБСУЖДЕНИЕ
Рентгенофазовый анализ
На рис. 1 представлены дифракционные спектры исходных и отожженных образцов сплавов, находящихся в состоянии напыленного плазменного покрытия.
Рис. 1.
Дифракционные спектры образцов покрытий из сплавов ФБХ6-2 (а) и 12496 (б); а: 1 – после напыления; 2 – после отжига при 550°С в течение 3 ч; 3 – после отжига при 800°С в течение 3 ч. б: 1 – после напыления; 2 – после отжига при 430°С в течение 3 ч; 3 – после отжига при 800°С в течение 3 ч.

Как видно, после напыления покрытия из обоих сплавов находятся практически полностью в аморфном состоянии, что подтверждается представленными в табл. 1 результатами рентгенофазового анализа.
Таблица 1.
Результаты рентгенофазового анализа покрытия из сплавов ФБХ6-2 и 12496 после напыления на подложку
Сплав | Фаза | Стр. тип | Об. доля, % | Вес. доля, % | Периоды, анг. |
---|---|---|---|---|---|
ФБХ6-2 | alpha-Fe (type A2) | cI2/1 | 2.0 ± 0.1 | 2.0 ± 0.1 | A = 2.869 |
(Fe,Cr)7C3 (type D10.2) | hP20/1 | 4.0 ± 0.1 | 4.0 ± 0.1 | A = 7.013; C = 4.463 | |
Аморфная фаза по типу Fe3C (type D0.11) | oP16/2 | 94.0 ± 0.4 | 94.0 ± 0.4 | – | |
12496 | alpha-Fe (type A2) | cI2/1 | 1.0 ± 0.1 | 1.1 ± 0.1 | A = 2.873 |
Аморфная фаза (type E9.3) | – | 97.1 ± 0.3 | 96.6 ± 0.3 | – | |
Тв. раствор на основе Ni (type A1) | cF4/1 | 1.9 ± 0.1 | 2.3 ± 0.1 | A = 3.551 |
Количественный анализ спектров образцов, отожженных при 430°С (сплав 12496), 550°С (ФБХ6-2) и 800°С (для обоих сплавов) был затруднен по причине их сложности. Как видно из наложенных друга на друга спектров, повышение температуры отжига приводит к распаду аморфной составляющей структуры (относительное уменьшение площади аморфного гало), увеличению доли основных кристаллических составляющих, присутствующих в небольшом количестве в структуре исходных покрытий, а также формированию новых фаз из компонентов, входящих ранее в состав аморфной фазы.
При этом даже после отжига при 800°С полностью кристаллическое состояние не достигается, что подтверждается качественным анализом спектров образцов с покрытиями (табл. 2) и сравнением с количественными данными, полученными с образцов с покрытиями после отжига при 1000°С в течение 5 часов (табл. 3).
Таблица 2.
Качественный фазовый состав образцов с покрытиями из сплавов ФБХ6-2 и 12496, отожженных при 800°С в течение 3 ч
Сплав | Фаза |
---|---|
ФБХ6-2 | Fe-Cr(bcc, type A2) |
(Fe,Cr)23C6 (type D8.4) | |
gamma-Fe(type A1) | |
Cr7C3(type D10.1) | |
Аморфная фаза по типу Fe3C(type D0.11) | |
12496 | Тв. раствор на основе Ni |
(Fe,Ni)3B | |
Ni31Si12 | |
Amorphous phase (type E9.3) |
Таблица 3.
Количественный фазовый состав образцов с покрытиями из сплавов ФБХ6-2 и 12496, отожженных при 1000°С в течение 5 ч
Сплав | Фаза | Стр. тип | Об. доля, % | Вес. доля, % | Периоды, анг. |
---|---|---|---|---|---|
ФБХ6-2 | Тв. р-р Fe(Cr) | cI2/1 | 28.7 ± 0.1 | 29.8 ± 0.1 | A = 2.865 |
(Fe,Cr)23C6 | cF116/1 | 40.3 ± 0.2 | 40.3 ± 0.2 | A = 10.576 | |
γ-Fe | cF4/1 | 1.8 ± 0.1 | 2.0 ± 0.1 | A = 3.588 | |
Cr7C3 | oP40/6 | 29.2 ± 0.2 | 27.8 ± 0.2 | A = 4.489 B = 7.001 C = 12.129 |
|
12496 | Тв. раствор на основе Ni (type А1) | cF4/1 | 29.6 ± 0.1 | 32.4 ± 0.1 | A = 3.538 |
(Fe,Ni)3 B (type D0.11) | oP16/2 | 56.1 ± 0.1 | 54.3 ± 0.1 | A = 5.319 B = 6.605 C = 4.408 |
|
Ni31Si12 | hP43/3 | 14.3 ± 0.1 | 13.3 ± 0.1 | A = 6.663 C =12.299 |
Микроструктура и распределение элементов по толщине покрытий
В исходном состоянии (до отжига) покрытия являются практически полностью аморфными, поэтому их микроструктура не проявляется даже несмотря на использование сильнодействующих травителей.
На рис. 2 представлены электронные микрофотографии шлифа образца с плазменным напыленным покрытием из сплава ФБХ6-2 в исходном (после напыления) и отожженном (при 550 или 800°С) состояниях, а также для сравнения электронные микрофотографии шлифов литого образца.
Рис. 2.
Микроструктура поперечных шлифов покрытия из сплава ФБХ6-2 в исходном состоянии (а), после отжига при 550°С (б–г), при 800°С (д, е) и литого образца сплава ФБХ6-2 в исходном состоянии (ж) и после отжига при 800°С (з).
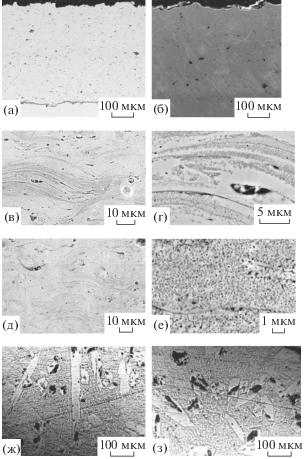
Как видно, морфология покрытия не меняется: как в исходном, так и отожженном состоянии сквозная пористость визуально не обнаруживается. Вместе с тем после отжига граница раздела “покрытие-подложка” становится менее выраженной, что может указывать на протекание диффузионных процессов, обеспечивающих диффузионную сварку. Обращает на себя внимание рельеф поверхностного слоя покрытия, который характеризуется наличием различных морфологических дефектов (неровностей, каверн, закрытых и открытых микрополостей и т.д.).
Микроструктура в поперечном срезе (рис. 2в–2е) является типичной для напыленных плазменных покрытий, которая вне зависимости от температуры отжига (550 или 800°С) имеет “волнообразный” характер распределения фаз, наследующих морфологию распыленных и затвердевших на поверхности чешуйчатых частиц сплава размерами 70–150 мкм. После отжига при 550°С фиксируется наноструктура покрытия, сформировавшаяся в результате частичного распада аморфной матрицы. Средний размер фаз составляет около 120 нм (рис. 2в, 2г). Отжиг при 800°С приводит к появлению фаз субмикронного размера (рис. 2д, 2е).
Микроструктура литого сплава (рис. 2ж, 2з) в исходном и отожженном при 800°С принципиально отличается от микроструктуры покрытия и характеризуется присутствием неравномерно распределенных достаточно крупных выделений вторых фаз различной морфологии и ориентации.
На рис. 3 представлены электронные микрофотографии поперечного шлифа образца с плазменным напыленным покрытием из сплава 12496 в исходном состоянии (после напыления, рис. 3а), после отжига при 430°С (рис. 3б) и при 800°С (рис. 3в, 3г) состояниях, а также для сравнения электронные микрофотографии шлифов литого образца сплава 12496 (рис. 3д, 3е).
Рис. 3.
Микрофотографии поперечных шлифов покрытия из сплава 12496 в исходном состоянии (а), после отжига при 430°С (б) и при 800°С (в, г), а также литого образца сплава 12496 в исходном состоянии (д) и после отжига при 800°С (е). На рис. 3в, 3г видны вытравленные границы зерен материала подложки.
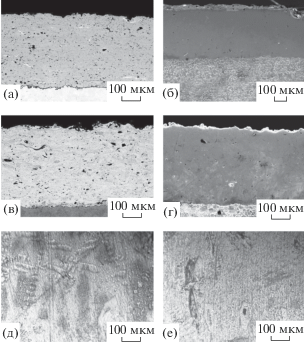
Как видно (рис. 3г), отжиг при 800°С привел к некоторому снижению объемной пористости (в основном за счет спекания мелких пор) и, также, как и в сплаве ФБХ6-2, уменьшению выраженности границы раздела “покрытие-подложка”. Такой характер изменения состояния области контакта может указывать на диффузионное взаимодействие на границе раздела, что должно приводить к увеличению прочности сцепления покрытия с подложкой.
Микроструктура покрытия (в поперечном срезе) из сплава 12496 как в исходном состоянии, так и после отжига при 430°С практически не выявляется (рис. 3а, 3б). Контраст проявляется только после отжига при 800°С, однако по его виду можно говорить только о структурной гетерогенности покрытия (рис. 3в, 3г).
Микроструктура шлифа литого сплава характеризуется присутствием как мелких (5–10 мкм), так и достаточно крупных (до 100 мкм), неравномерно распределенных выделений вторых фаз различной морфологии и ориентации (рис. 3д, 3е).
Согласно результатам растровой электронной микроскопии, профили концентраций элементов, водящих в состав покрытий из сплавов ФБХ6-2 и 12496, вне зависимости от режима отжига (при 550°С (ФБХ6-2), 430°С (12496) или 800°С) характеризуются незначительными флуктуациями по толщине покрытий, однако в среднем содержание каждого из элементов отвечает заданному составу в исходном порошке.
Электрохимические исследования
Как было показано в работе [19], наличие сквозной пористости не позволяет рассматривать коррозионно-электрохимическое поведение покрытий в отдельности от подложки, на которую оно наносится, так как проникновение коррозионной среды через сквозные поры до металла подложки, способствует формированию коррозионного гальванического элемента типа “покрытие (катод) – подложка (анод)”. При наличии сквозной пористости установившееся в процессе экспозиции образцов в коррозионно-активной среде значение стационарного потенциала (Ест) должно отвечать именно потенциалу коррозии (Екор) системы “покрытие-подложка”. Для доказательства отсутствия сквозной пористости в исследуемых системах были смоделированы условия, при которых обеспечивался прямой контакт через раствор материала покрытия и подложки, т.е. была реализована возможность протекания контактной коррозии. Для измерения потенциала непосредственно покрытия его механически отделяли от подложки и закрывали химически стойким лаком поверхность, контактирующую ранее с подложкой (Ст. 3).
На рис. 4 представлены хронопотенциограммы подложки (линии 1) , контактной пары “покрытие-подложка” (линии 2) и отделенных от основы покрытий из сплавов ФБХ6-2 и 12496 в растворах 3% NaCl и 0.5 н HNO3 (линии 3).
Рис. 4.
Хронопотенциограммы подложки их стали Ст. 3 (1), контактной пары “покрытие-подложка” (2) и покрытий (3) из сплавов ФБХ6-2 (а, в) и 12496 (б, г), измеренные в растворах 3% NaCl (а, б) и 0.5 н HNO3 (в, г).
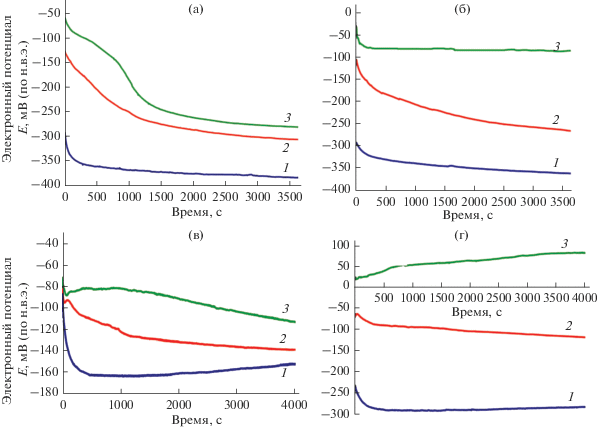
Как видно, вне зависимости от состава покрытия и природы коррозионной среды Ест контактной пары “покрытие-подложка” находится между потенциалами образцов с покрытиями и металла-подложки. При этом Ест образцов с покрытиями, как и следовало ожидать с учетом высокого содержания хрома (в сплаве ФБХ6-2) и никеля (в сплаве 12496), оказывается более положительным, чем Ест контактной пары “покрытие-подложка” и подложки (сталь Ст. 3). Промежуточное значение потенциала контактной пары “покрытие-подложка” устанавливается в процессе экспозиции в результате катодной поляризации покрытия и анодной поляризации металла-подложки. Полученные результаты подтверждают факт отсутствия сквозной пористости в покрытиях, а измеренные значения Ест образцов с покрытиями следует считать потенциалами коррозии покрытий.
Характер изменения потенциалов образцов в процессе экспозиции (смещение в отрицательную сторону) и установление Ест в области отрицательных значений косвенно указывает на развитие процесса коррозии по механизму активного растворения. Исключение представляет процесс электрохимической коррозии покрытия из сплава 12496 в азотной кислоте (рис. 4г, линия 3), который характеризуется самопроизвольной анодной поляризацией и установлением положительного значения Екор, что может свидетельствовать о повышении защитных свойств покрытия.
На рис. 5 представлены хронопотенциограммы образцов с покрытиями из сплавов ФБХ6-2 и 12496, находящихся в состоянии после напыления (линии 1) или пропитки напыленных покрытий жидкостью Анакрол-2501 (линии 2).
Рис. 5.
Типичные хронопотенциограммы образцов с покрытиями из сплавов ФБХ6-2 (а, б) и 12496 (в, г), измеренные в растворах 3% NaCl (а, в) и 0.5 н HNO3 (б, г): 1 – после напыления; 2 – после пропитки покрытий гидрофобизирующей жидкостью Анакрол-2501.
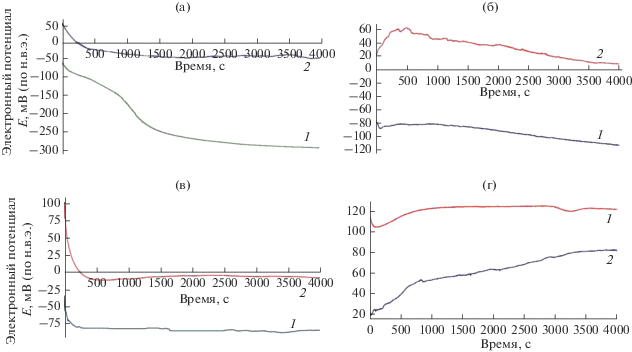
Как видно, вне зависимости от природы коррозионной среды, при общей тенденции изменения потенциалов образцов в процессе экспозиции, стационарные потенциалы (Ест) пропитанных покрытий оказываются значительно более положительными, чем Ест покрытий без пропитки.
Анакрол-2501 является органической жидкостью, устойчивой к действию кислот, щелочей и растворяющих солей [25], и, очевидно, не обладает электропроводящими свойствами. Однако возможность измерения электродного потенциала поверхности покрытия указывает на не полную герметизацию поверхностного слоя, что может быть связано с испарением компонентов полимера на отдельных участках поверхности покрытий в процессе просушивания при 80°С.
Наблюдаемое существенное “облагораживание” потенциала коррозии пропитанных покрытий дает основание полагать, что причиной значительного увеличения Ест покрытий после пропитки является уменьшение количества морфологических несовершенств в поверхностном слое покрытия – каверн, микротрещин, шероховатостей, открытых пор. В непропитанных покрытиях имеет место ограниченный доступ деполяризатора к катодным участкам, локализованным в этих дефектах. Это вызывает существенное торможение катодного процесса и, как следствие, приводит к более отрицательному значению Екор по сравнению с Екор областей покрытия, расположенных непосредственно на его поверхности. Следовательно, именно эти морфологические дефекты играют роль анодных структурных составляющих при протекании коррозионного процесса.
Заполнение морфологических неоднородностей жидкостью Анакрол-2501 обеспечивает значительное уменьшение доли анодных зон или полное их исчезновение и исключение из участия в реализации коррозионного процесса. В этом случае коррозионный процесс обеспечивается только фазовой гетерогенностью поверхности (табл. 1) и растворению подвергается анодная фаза, локализованная непосредственно на поверхности покрытия. Этой фазой в составе обоих покрытий, очевидно, является α-Fe. Другие фазы, входящие в состав покрытия, являются катодными структурными составляющими: в покрытии из сплава ФБХ6-2 это в основном аморфная фаза с высоким содержанием хрома, которая может находиться в пассивном состоянии, и смешанный карбид (Fe, Cr)7C3 [24]; в покрытии из сплава 12486 это в основном аморфная фаза с высоким содержанием никеля и твердый раствор на его основе.
Из рис. 5г видно, что изменение потенциала покрытия из сплава 12496 в процессе экспозиции в растворе 0.5 н HNO3 имеет принципиально иной характер. Как в состоянии после напыления, так и после пропитки покрытия испытывают самопроизвольную анодную поляризацию, что может указывать формирование защитного пассивирующего слоя. Возможность пассивирования поверхности может быть обусловлена рядом факторов: высокой окислительной способностью коррозионной среды, практически отсутствием диффузионных ограничений по доставке водорода (деполяризатора) к катодным участкам поверхности (т.е., низкой ионной концентрационной поляризации) и низким перенапряжением водорода на никеле [24]. Высокая катодная эффективность никельсодержащих фаз может обеспечить дополнительную анодную поляризацию и облегчить наступление пассивирования анодной фазы, что, очевидно, должно приводить к значительному уменьшению скорости коррозии [24].
В табл. 4 представлены результаты изучения влияния пропитки гидрофобизирующей жидкостью Анакрол-2501 и режимов термической обработки на потенциалы коррозии покрытий из сплавов ФБХ6-2 и 12496 в растворах 3% NaCl и 0.5 н HNO3.
Таблица 4.
Влияние режимов термической обработки и пропитки гидрофобизирующей жидкостью Анакрол-2501 на потенциал коррозии (по н. в. э.) образцов с покрытиями из сплавов ФБХ6-2 и 12496 в растворах 3% NaCl и 0.5 н HNO3
Коррозионная среда |
Покрытие из сплава ФБХ6-2 | Покрытие из сплава 12496 | ||||
---|---|---|---|---|---|---|
3% NaCl | состояние покрытия | стационарный электродный потенциал, мВ | характер поляризации в процессе экспозиции | состояние покрытия | стационарный электродный потенциал, мВ | характер поляризации в процессе экспозиции |
После напыления | –278 | Катодная | После напыления | –86 | Катодная | |
После напыления и пропитки | –54 | Катодная | После напыления и пропитки | –8 | Катодная | |
Отжиг при 555°С, 3 ч | –301 | Катодная | Отжиг при 430° С, 3 ч | –140 | Небольшая катодная (20 мВ) | |
Отжиг при 555°С, 3 ч + пропитка | –200 | Катодная | Отжиг при 430° С, 3 ч + пропитка | –81 | Небольшая катодная (10 мВ) | |
Отжиг при 800°С, 3 ч | –33 | Катодная | Отжиг при 800° С, 3 ч | –315 | Значительная катодная | |
Отжиг при 800°С, 3 ч + пропитка | –28 | Катодная | Отжиг при 800° С, 3 ч + пропитка | –74 | Катодная | |
0.5 н HNO3 | После напыления | –112 | Незначительная катодная | После напыления | +82 | Анодная |
После пропитки | +9 | Незначительная катодная | После пропитки | +121 | Анодная | |
Отжиг при 555°С, 3 ч | –362 | Незначительная катодная | Отжиг при 430° С, 3 ч | +142 | Значительная катодная | |
Отжиг при 555°С, 3 ч + пропитка | –125 | Незначительная катодная | Отжиг при 430° С, 3 ч + пропитка | +143 | Значительная анодная | |
Отжиг при 800°С, 3 ч | –48 | Вначале катодная (30 мВ), затем устойчивая анодная | Отжиг при 800° С, 3 ч | –119 | Значительная катодная | |
Отжиг при 800°С, 3 ч + пропитка | +11 | Вначале катодная (20 мВ), затем небольшая анодная | Отжиг при 800° С, 3 ч + пропитка | –87 | Вначале катодная, затем устойчивая анодная |
Отжиг образцов с покрытиями из сплава ФБХ6-2 при 550°С в течение 3 ч вызывает значительное “разблагораживание” Екор в обеих средах. При этом пропитка также оказывает положительное влияние на электрохимическое поведение покрытия, однако не устраняет негативного эффекта, связанного с наноструктуризацией покрытия.
Вместе с тем, отжиг при 800°С в течение 3 ч при сохранении общей тенденции к изменению потенциала в процессе экспозиции (катодная поляризация) приводит к значительному облагораживанию Екор в растворе 3% NaCl по сравнению с как с исходным, так и отожженным при 550°С покрытием. Характерно, что пропитка практически не влияет на Екор покрытия, отожженного при 800°С (табл. 4).
В растворе 0.5 н HNO3 в образцах покрытия из сплава ФБХ6-2, отожженных при 800°С, принципиально меняется характер протекания коррозионного процесса. После кратковременного (не более 100 с) сдвига потенциала в область отрицательных значений (на 10–30 мВ), как в исходных, так и пропитанных покрытиях наблюдается самопроизвольная анодная поляризация, а установившиеся значения потенциалов коррозии оказываются положительнее Екор покрытия, находящегося в состоянии после напыления (табл. 4). Наблюдаемая тенденция в кинетике изменения потенциала в процессе экспозиции и установившиеся значения Екор могут свидетельствовать о повышении коррозионной стойкости по отношению к исходному состоянию покрытия.
Как было отмечено ранее, количественный анализ структуры после отжига покрытий при 800°С затруднен в виду сложности рентгеновского спектра. Однако можно полагать, что причиной наблюдаемого эффекта может быть увеличение в структуре покрытия доли химически стойких карбидных фаз и твердого раствора на основе железа (с высоким содержанием хрома), склонного к пассивации в нейтральных средах. Эти структурные составляющие образуются в процессе распада аморфной фазы (табл. 2, 3) и на фоне незначительного количества анодной фазы γ-Fe играют определяющую роль в электрохимическом поведении покрытия.
Процесс коррозии покрытий из сплава 12496 в растворе 3% NaCl как после напыления (рис. 5в), так и после отжига при 430 и 800°С характеризуется катодной поляризацией образцов, что указывает на развитие процесса по механизму активного растворения. Пропитка покрытий приводит к существенному облагораживанию Екор, но не изменяет механизма коррозионного разрушения покрытия.
В растворе 0.5 н HNO3 не отожженные покрытия из сплава 12496 (в том числе и после их пропитки) демонстрируют склонность к самопассивации (рис. 5г), а повышение потенциала коррозии покрытий в результате их пропитки гидрофобизирующей жидкостью находится в соответствии с изложенными выше представлениями о роли морфологических дефектов поверхности в реализации коррозионного процесса.
Отжиг образцов с покрытиями (сплав 12496) при 430 и 800°С принципиально меняет характер развития коррозионного процесса в этом растворе по отношению к исходному состоянию покрытия.
На рис. 6 представлены результаты изучения влияния отжига и пропитки отожженных покрытий из сплава 12496 на кинетику изменения их электродных потенциалов в растворе 0.5 н HNO3. Как видно из рисунка, отожженные не пропитанные покрытия (линии 1) в процессе экспозиции подвергаются самопроизвольной катодной поляризации (в отличие от исходных покрытий), что указывает на протекание процесса коррозии по механизму активного растворения.
Рис. 6.
Хронопотенциограммы отожженных в течение 3 ч при 430°С (а) и при 800ºС (б) образцов с покрытиями из сплава 12496 в растворе 0.5 н HNO3: 1 – без пропитки; 2 – с пропиткой.
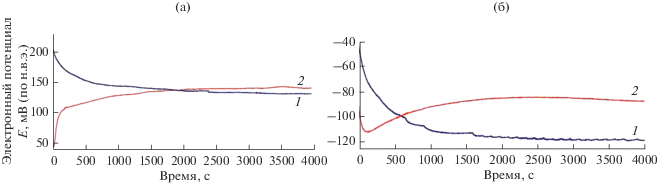
Главной причиной изменения механизма коррозионного процесса в отожженных покрытиях из сплава 12496, очевидно, является увеличение степени гетерогенности структуры, в частности, образование боридной фазы (Fe,Ni)3B. Известно, что боридные фазы железа неустойчивы в растворах неорганических кислот, в том числе азотной кислоте [26]. Как следует из результатов количественного рентгенофазового анализа, в составе полностью закристаллизованного покрытия из сплава 12496 объемная доля этой фазы составляет 56.1% (табл. 3). Это дает основание полагать, что, как в процессе нанокристаллизации (при 430°С), так и последующей микрокристаллизации (при 800°С) именно фаза (Fe,Ni)3B является основной анодной структурной составляющей. Низкая химическая устойчивость этой фазы должна приводить к низкому перенапряжению анодного процесса (высокой скорости растворения). При этом высокая катодная эффективность других никельсодержащих фаз будет способствовать дополнительному ускорению электрохимического растворения этой фазы, т.е. увеличению скорости коррозии покрытия. Зависимость потенциала коррозии от объемной доли этой фазы в составе покрытия подтверждается значительно более отрицательным значением Екор в образцах, отожженных при 800°С.
Пропитка отожженных образцов меняет характер развития коррозионного процесса. Электродный потенциал в процессе экспозиции облагораживается, что может свидетельствовать либо об увеличении доли электроположительных составляющих структуры по мере селективного растворения боридной фазы железа, либо о формировании на поверхности покрытий никельсодержащих солевых осадков, оказывающих защитное действие [27] . Реализация этих процессов возможна в том случае, если пропитка обеспечивает не только заполнение морфологических неоднородностей приповерхностного слоя (каверн, открытых пор, микротрещин, шероховатости), но и в значительной степени “блокирует” бòльшую часть выделений боридной фазы, локализованной непосредственно на поверхности покрытия. В этом случае электрохимическое поведение покрытия будет определяться устойчивостью других никельсодержащих фаз (в основном, твердого раствора хрома на основе никеля).
На основании анализа хронопотенциограмм и стационарных значений электродных потенциалов образцов в соответствующих растворах для изучения анодного поведения покрытий из исследуемых сплавов были выбраны наиболее интересные с практической точки зрения режимы их термической обработки, а именно, для сплава ФБХ6-2 – отжиг при 800°С в течение 3 ч (в обоих растворах), а для сплава 12496 – отжиг при 430°С (в растворе 0.5 н HNO3).
На рис. 7а представлены анодные поляризационные кривые (измеренные от потенциала коррозии) в растворе 3% NaCl отожженных (при 800°С, 3 ч) образцов сплава ФБХ6-2, находящихся в состоянии покрытий без пропитки (1) и с пропиткой (2). Для сравнения приведены анодные кривые литого сплава, отожженного по аналогичному режиму (3).
Рис. 7.
Анодные поляризационные кривые, снятые в растворах 3% NaCl (а) и 0.5 н HNO3 (б), отожженных (800°С, 3 ч) образцов сплава ФБХ6-2, находящихся в состоянии покрытий без пропитки (1), с пропиткой (2) и литом состоянии (3).
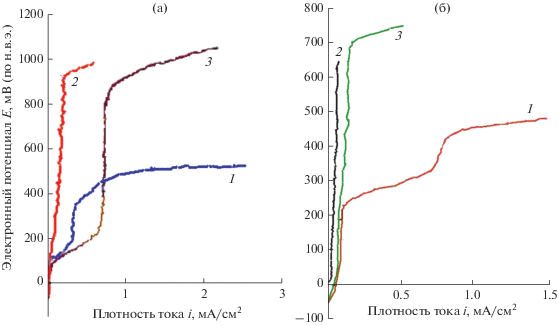
Как видно (рис. 7а), в растворе 3% NaCl для всех состояний сплава (линии 1–3) сдвиг потенциала в анодную область до значений на 180–200 мВ превышающих величину стационарного потенциала характеризуется достаточно низкими токами анодного растворения (10–30 мкА/см2), типичными для металлов и сплавов, находящихся в пассивном состоянии. При этом величина плотности тока в образце с плазменным покрытием без пропитки (линия 1) в 3–4 раза выше величины анодного тока в литом образце (линия 3). Однако устойчивость этого состояния ограничивается потенциалом порядка +100 мВ. Дальнейшая анодная поляризация сопровождается увеличением анодного тока для этих состояний сплава (линии 1 и 3) до постоянных, но достаточно высоких значений (300–700 мкА/см2), не характерных для пассивного состояния и обусловленных, по-видимому, так называемой солевой пассивностью. Сплав в покрытии выходит из этого состояния при достижении потенциала порядка +300 мВ, в то время литой сплав (линия 3) растворяется при постоянном значении тока (около 700 мкА/см2) вплоть до потенциала анодного выделения кислорода. Пропитка покрытия гидрофобизирующей жидкостью принципиально меняет характер анодного поведения сплава (линия 2). В широкой области потенциалов поляризации (100–900 мВ) величина анодного тока не превышает 100–200 мкА/см2. Возможной причиной низкой скорости растворения пропитанного покрытия, как было показано выше, может являться значительное уменьшение доли анодных зон, локализованных в морфологических неоднородностях поверхности, и исключение их значительной части из участия в реализации коррозионного процесса.
В растворе азотной кислоты даже в отсутствие пропитки отожженное покрытие демонстрирует высокую устойчивость пассивного состояния вплоть до потенциала поляризации на 300 мВ превышающего стационарное значение (рис. 7б, линия 1). Состояние же после пропитки характеризуется типичным для самопассивирующихся сплавов ходом анодной кривой (отсутствие активационной петли, низкий ток анодного растворения в широкой области потенциалов внешней поляризации). Следует отметить, что для отожженного литого сплава наблюдается аналогичный ход анодной кривой (линия 3), что также свидетельствует о пассивном состоянии сплава, однако, как видно (линия 2), значения плотностей анодного тока в пропитанном покрытии оказываются примерно в два раза меньше чем для литого сплава.
На рис. 8 представлены анодные поляризационные кривые (в растворе 0.5 н HNO3) образцов покрытий из сплава 12496, находящихся в исходном состоянии (после напыления) без пропитки (линия 1), и после пропитки гидрофобизирующей жидкостью Анакрол-2501 (линия 2), а также отожженных (430°С, 3 ч) образцов покрытия из этого сплава без пропитки (линия 3) и после пропитки (линия 4).
Рис. 8.
Анодные поляризационные кривые образцов покрытий из сплава 12496 в растворе 0.5 н HNO3: 1 – исходное состояние после напыления; 2 – исходное состояние покрытия с пропиткой гидрофобизирующей жидкостью Анакрол-2501; 3 – отжиг покрытия после напыления при 430°С, 3 ч; 4 – отжиг покрытия при 430°С, 3 ч, с последующей пропиткой.
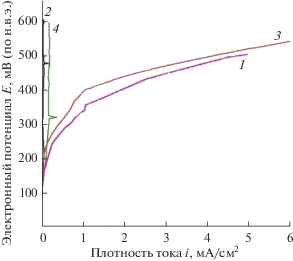
Как видно, как в исходном состоянии (линия 1), так и после отжига (430°С, 3 ч; линия 3), сопровождающегося нанокристаллизацией, анодный ток растворения покрытия вблизи стационарных потенциалов (100–200 мВ) находится в пределах 20–50 мкА/см2. Однако низкие значения плотностей тока и отсутствие активационной петли, характерных для самопассивирующихся сплавов, в данном случае не являются признаками нахождения покрытия в пассивном состоянии, так как, во-первых, дальнейший сдвиг потенциала внешней поляризации (выше 200 мВ) приводит к увеличению скорости анодного растворения покрытия, а во-вторых, в процессе экспозиции покрытия наблюдается устойчивая катодная поляризация (рис. 6а, линия 1).
Вместе с тем, пропитка исходных и отожженных покрытий практически полностью устраняет влияние фазовой гетерогенности и приповерхностных дефектов (пор, каверн, микротрещин и т.п.), а высокая окислительная способность коррозионной среды обеспечивает устойчивое пассивное состояние как исходным, так и отожженным покрытиям в широкой области потенциалов анодной поляризации. Полученные результаты подтверждают изложенные выше представления о механизме развития коррозионного процесса в покрытии из сплава 12496 и роли структурной гетерогенности и морфологических неоднородностей поверхности в его реализации.
В табл. 5 представлены результаты коррозионных испытаний в растворах 3% NaCl и 0.5 н HNO3 отожженных литых образцов из сплавов ФБХ6-2 и 12496, а также отожженных образцов с покрытиями из этих сплавов без пропитки и с пропиткой жидкостью Анакрол-2501.
Таблица 5.
Результаты коррозионных испытаний отожженных образцов сплавов ФБХ6-2 и 12496, находящихся в литом состоянии и в виде покрытия
Сплав | Состояние образцов | Режим термообработки | Глубинный показатель коррозии, мм/год | |
---|---|---|---|---|
3% NaCl | 0.5 н HNO3 | |||
ФБХ6-2 | Литой | 800°С, 3 ч | 0.12 ± 0.03 | 0.09 ± 003 |
Плазменное покрытие | 800°С, 3 ч | 0.70 ± 0.08 | 0.49 ± 0.06 | |
Плазменное покрытие с пропиткой | 800°С, 3 ч | 0.17 ± 0.05 | 0.12 ± 0.04 | |
12498 | Плазменное покрытие | 430°С, 3 ч | 0.35 ± 0.07 | 0.20 ± 0.03 |
Плазменное покрытие с пропиткой | 430°С, 3 ч | 0.021 ± 0.005 | 0.017 ± 0.003 | |
Литой | 800°С, 3 ч | 0.013 ± 0.002 | 0.029 ± 0.003 | |
Плазменное покрытие | 800°С, 3 ч | 0.075 ± 0.008 | 0.16 ± 0.02 | |
Плазменное покрытие с пропиткой | 800°С, 3 ч | 0.015 ± 0.003 | 0.032 ± 0.003 |
Как следует из полученных результатов (табл. 5), отожженные при 800°С, 3 ч, литые образцы сплава 12498 обладают в несколько раз более высокой коррозионной стойкостью по сравнению с литыми образцами сплава ФБХ6-2 в обеих средах. Скорость коррозии отожженных образцов, находящихся в состоянии покрытий без пропитки, более чем в 5 раз превышает скорость коррозии литых образцов. Пропитка покрытий приводит к значительному уменьшению скорости коррозии, которая становится сопоставимой со скоростью коррозии литых образцов. В процессе эксплуатации бурового оборудования с покрытиями из этих сплавов возможен частичный износ поверхностных слоев покрытий, связанный с абразивным воздействием коррозионно-активной среды. Однако высокая проникающая способность гидрофобизирующей жидкости Анакрол-2501 должна обеспечивать коррозионную стойкость покрытий, сопоставимую с коррозионной стойкостью литых сплавов.
ВЫВОДЫ
1. Методами рентгенструктурного и микроренгеноспектрального анализа, растровой электронной микроскопии, хронопотенциометрии, потенциодинамической вольтамперометрии и гравиметрии изучены структурное состояние после различных режимов термической обработки, коррозионно-электрохимическое поведение и коррозионная стойкость плазменных покрытий на основе железа (сплав ФБХ6-2) и никеля (сплав RW 12496 компании “Castolin”) в водных растворах хлористого натрия и азотной кислоты. Проведено сопоставление структурных и электрохимических характеристик покрытий из этих сплавов с их аналогами, находящимися в литом состоянии, прошедшими соответствующую термическую обработку.
2. Принципиальным отличием покрытий от их литых аналогов является морфологическая гетерогенность поверхности покрытий (каверн, микротрещин, шероховатостей, открытых пор и т.п.), определяющая специфический характер развития коррозионного процесса и значительное ухудшение их электрохимических характеристик в коррозионно-активных средах по сравнению с литыми сплавами. Ограниченный доступ деполяризатора к катодным участкам, локализованным в этих дефектах, приводит существенному торможению катодного процесса и, как следствие, к более отрицательному значению Екор по сравнению с Екор областей покрытия, расположенных непосредственно на его поверхности. Именно эти морфологические дефекты играют роль анодных структурных составляющих при протекании коррозионного процесса.
3. Установлено, что непосредственно после напыления на стальную подложку (сталь Ст. 3) оба покрытия находятся практически полностью в аморфном состоянии. Отжиг при температурах 430°С (сплав 12496) и 550°С (ФБХ6-2) в течение 3 ч приводит к образованию аморфно-нанокристаллической структуры покрытий, которая наиболее ярко проявляется в покрытии из сплава ФБХ6-2. Увеличение фазовой гетерогенности структуры покрытий вызывает ухудшение электрохимических характеристик покрытий.
4. Отжиг покрытий из обоих сплавов при 800°С в течение 3 ч вызывает уменьшение объемной пористости, уменьшение выраженности границы раздела “покрытие-подложка”, что указывает на протекание диффузионных процессов, обеспечивающих повышение адгезии покрытий к основе. Структура покрытий отличается ярко выраженным “волнообразным” характером распределения фаз, наследующих морфологию распыленных и затвердевших на поверхности чешуйчатых частиц и появлением фаз субмикронного размера, в то время как структура литых аналогов характеризуется достаточно крупными, неравномерно распределенными выделениями вторых фаз различной морфологии и ориентации.
5. Пропитка покрытий гидрофобизирующей жидкостью Анакрол-2501 приводит к снижению роли морфологических неоднородностей, обеспечивая значительное уменьшение доли анодных зон или полное их исчезновение и исключение из участия в реализации коррозионного процесса. В этом случае коррозионный процесс обеспечивается только фазовой гетерогенностью поверхности и растворению подвергается анодная фаза, локализованная непосредственно на поверхности покрытия. Этой фазой в составе обоих покрытий является α-Fe. Другие фазы, входящие в состав покрытия, являются катодными структурными составляющими: в покрытии из сплава ФБХ6-2 это в основном аморфная фаза с высоким содержанием хрома, которая может находиться в пассивном состоянии, и смешанный карбид (Fe,Cr)7C3; в покрытии из сплава 12486 это в основном аморфная фаза с высоким содержанием никеля и твердый раствор на его основе.
6. Пропитка отожженных (800°С, 3 ч) покрытий обеспечивает их значительно более высокую устойчивость при анодной поляризации в обеих средах, а отсутствие активационных петель на анодных поляризационных кривых и низкие значения плотностей токов анодного растворения свидетельствуют о склонности покрытий из обоих сплавов к самопассивации.
7. Коррозионная стойкость отожженных образцов, находящихся в состоянии покрытий без пропитки, более чем в 5 раз ниже коррозионной стойкости литых образцов. Пропитка покрытий приводит к значительному уменьшению скорости их коррозии, которая становится сопоставимой со скоростью коррозии отожженных литых образцов.
Список литературы
Калита В.И., Комлев Д.И. Плазменные покрытия с нанокристаллической и аморфной структурой: монография. М.: Лидер М, 2008. 388 с.
Кузьмин В.И., Ващенко С.П., Гуляев И.П. и др. // Вестник Югорского госуниверситета, 2015. Том. 37. Выпуск 2. С. 45–52.
Лясников В.Н., Лясникова А.В., Дударева О.А. // J. Thermal Spray Technology. 2016. V. 25. Issue 5. P. 1040–1055.
Milanti A., Koivuluoto H., Vuoristo P. et al. // Coatings. 2014. V. 4. P. 98–120, https://doi.org/10.3390/coatings4010098
Milanti A., Matikainen V., Koivuluoto H. et al. // Surface and Coatings Technology. 2015. V. 277. P. 81–90.
Ma H.R., Li J.W., Chang C.T. et al. // J. Therm. Spray Tech. 2017. doi.org/https://doi.org/10.1007/s11666-017-0647-1
Zhang S.D., Zhang W.L., Wang S.G. et al. // Corrosion Science. 2015. V. 93. P. 211–221.
Zheng Z.B., Zheng Y.G., Sun W.H., Wang J.Q. // Tribology International. 2015. V. 90. P. 393–403.
Wang Y., Xing Z.Z., Luo Q., Rahman A. et al. // Corrosion Science. 2015. V. 98. P. 339–353.
Haijun Zhang1, Yongfeng Gong, Botao Zhang et al. Corrosion and algal behaviors of HVOF sprayed Fe-based amorphous coatings for marine applications Fe53Cr19Zr7Mo2C18Si. International Termal Spray Conference and Exposition ITSC. 2018. P. 721.
Shujuan Dong, Bo Song, Hanlin Liao, Christian Coddet // Surface & Coatings Technology. 2015. V. 268. P. 36–45.
Koga G.Y., Junior A.M.J., Roche V. et al. // Metallurgical and materials transactions A. 2018. V. 49A. P. 4860–4870.
Jiang-hao Qiao, Xin Jin, Jia-hao Qin et al. // Surface & Coatings Technology. 2018. V. 334. P. 286–291.
Wenmin Guo, Jianfeng Zhang, Yuping Wu et al. // Materials and Design. 2015. V. 78. P. 118–124.
Wang L., Zhou Z., Yao H.H. et al. Microstructure and Thermal conductivity of Fe-based amorphous coatings prepared by HVOF thermal spraying. International Thermal Spray Conference & Exposition. ITSC 2016. May 10–12, Chanhai/P.R. China. P. 194.
Liang-Yu Chen, Tianxiang Xu, Sheng Lu. et al. // Surface & Coatings Technology. 2018. V. 350. P. 436–444.
Qian Z.H., Zhou Z., Yao H.H. et al. Microstructure and properties of Fe16% Cr7% Nb4% B2.5% Si1% C coating prepared by wire-arc spraying process. International Thermal Spray Conference & Exposition. ITSC 2016. May 10–12, Chanhai/P.R. China P. 707.
Комлев Д.И., Калита В.И., Меньшиков Г.А. и др. // ФХОМ. 2012. № 6. С. 40–50.
Пустов Ю.А., Золотарев А.С., Гладких Н.А. и др. // ФХОМ. 2015. № 3. С. 35–43.
Ivannikov A.Yu., Kalita V.I., Komlev D.I. et al. // Surface & Coatings Technology. 2018. V. 335. P. 327–333.
Пустов Ю.А., Калита В.И., Турсунбаева А.А. и др. // Перспективные материалы. 2018. № 7. С. 57–66.
Wu J., Zhang S.D., Sun W.H., Wang J.Q. // Surface & Coatings Technology. 2018. V. 335. P. 205–218.
Куракова Н.В., Молоканов В.В., Калита В.И. и др. // Физика и xимия обработки материалов. 2008. № 4. С. 18–25.
Жук Н.П. Курс теории коррозии и защиты металлов: Учебное пособие для вузов. – 2-е изд., стериотипное. Перепечатка с издания 1976 г. М.: ООО ТИД “Альянс”, 2006. 472 с.
www.anacrol.ru /АНАКРОЛ-2501_пропиточный_состав.
Самсонов Г.В., Серебряков Т.И., Неронов В.А. Бориды. М.: Атомиздат, 1975, 376 с.
Коррозия. Справочник. Под ред. Шрайера Л.Л. Пер. с англ. М.: Металлургия, 1981. 631 с. с ил. // Shreir L.L. Corrosion. In 2 vols. V. 1. Heаd of Department of Metallurgy and Materials, City of London Polytechnic.
Дополнительные материалы отсутствуют.
Инструменты
Физикохимия поверхности и защита материалов