Физикохимия поверхности и защита материалов, 2019, T. 55, № 4, стр. 408-414
Химическое фосфатирование углеродистой стали
И. А. Казаринов 1, Л. А. Исайчева 2, *, А. Махммод Адиба 3, Н. М. Трепак 1
1 ФГБОУ ВО “Саратовский национальный исследовательский государственный университет
имени Н.Г. Чернышевского”
Саратов, Россия
2 ФГБОУ ВО “Саратовский государственный аграрный университет имени Н.И. Вавилова”
Саратов, Россия
3 Университет Дияла
Диял, Ирак
* E-mail: isaichevala@yandex.ru
Поступила в редакцию 30.10.2017
После доработки 12.10.2018
Принята к публикации 15.11.2018
Аннотация
Изучена кинетика формирования фосфатных покрытий (ФП) на углеродистой стали марки Ст3 в цинк-нитрат-фосфатном растворе (0.65 М Zn2+ + 0.3 М ${\text{PO}}_{{\text{4}}}^{{{\text{3}} - }}$ + 1.0 М ${\text{NO}}_{{\text{3}}}^{ - },$ рН 1.95) с различными добавками при температуре 25°С. Показано, что введение в фосфатирующий раствор эффективной кремнийсодержащей добавки и последующая обработка фосфатных пленок в водном растворе, содержащем соединения кремния, обеспечивало получение на Ст3 коррозионностойких ФП. С помощью метода математического планирования экстремального эксперимента Бокса–Уилсона оптимизирован процесс получения в данных условиях ФП с повышенной защитной способностью.
ВВЕДЕНИЕ
Возрастающие требования к эксплуатации стальных изделий и конструкций обусловливают необходимость усовершенствования методов защиты их от коррозии. Для этих целей применяются ингибиторы коррозии, защитные металлические и неметаллические покрытия. В настоящее время широкое развитие получил метод фосфатирования [1–6]. Применение ФП в качестве промежуточного слоя под окраску, промасливание, лакирование и другие операции позволяет увеличить коррозионную стойкость металлоконструкций, улучшить противозадирные и антифрикционные свойства, повысить адгезию лакокрасочных материалов и т.п.
Имеющиеся в литературе данные по фосфатированию стали предусматривают использование преимущественно растворов, в которых образование ФП происходит при повышенной температуре. Число предлагаемых составов для фосфатирования стали при температуре ниже 40°С ограничено, и, как правило, они являются многокомпонентными и токсичными [1, 2, 6, 7].
Задача данного исследования состояла в изучении кинетики процесса холодного фосфатирования углеродистой стали марки Ст3 с целью получения на ней ФП с повышенными защитными свойствами.
МЕТОДИКА ЭКСПЕРИМЕНТА
В качестве исследуемого материала использовалась углеродистая сталь марки Ст3. Предварительная обработка поверхности сводилась к зачистке наждачной бумагой р300 и обезжириванию этиловым спиртом, что позволяло по сравнению со стандартной подготовкой сохранить активные центры кристаллизации покрытия и оказывать минимальное влияние на изменение первоначальной структуры поверхности стальных образцов.
Процесс фосфатирования стали изучался в растворах на основе цинк-фосфат-содержащего (ЦФС) и цинк-нитрат-содержащего (ЦНС) сырья (0.65 М Zn2+ + 0.3 М ${\text{PO}}_{{\text{4}}}^{{3 - }}$ + 1.0 М ${\text{NO}}_{{\text{3}}}^{ - },$ рН 1.95) с различными добавками при температуре 25°С. Электрохимические исследования проводились в модельных растворах, имитирующих по содержанию фосфатов, нитратов, модифицирующих добавок и кислотности фосфатирующий раствор (0.3 М Н3РО4 + 1.0 М НNO3 + NaOH, pH 1.95).
Использовался комплекс различных экспериментальных методов: потенциодинамический (1 В/мин), методы определения массы растворившегося металла (m) и массы фосфатной пленки (Р) [8], капельный метод определения защитных свойств ФП (γ) [9], электронная микроскопия (MIRA 2LMU, х5000), рентгенофазовый анализ (ДРОН-3, фильтрованное FeKα-излучение), метод импедансной спектроскопии (измерительный комплекс “Autolab”, для обработки результатов которой применялась программа ZView) и др. В качестве электрода сравнения применялся насыщенный хлоридсеребряный электрод. В работе все потенциалы даны относительно нормального водородного электрода (НВЭ).
РЕЗУЛЬТАТЫ И ИХ ОБСУЖДЕНИЕ
Исследования были начаты с изучения возможности получения коррозионностойких ФП на стали марки Ст3 в стандартных растворах, в частности, на основе соли Мажеф и концентрата типа КФ, и в растворах, разработанных на кафедре физической химии СГУ [10–13]. Некоторые из используемых растворов приведены в табл. 1. Качество образующихся покрытий оценивалось на основании визуального осмотра пленки и определения массы ФП и их коррозионной стойкости.
Таблица 1.
Составы фосфатирующих растворов и характеристики полученных в них ФП на стали марки Ст3 (tфосф = 30 мин)
№ | Состав раствора | pH | P, г/м2 | γ, с |
---|---|---|---|---|
1 | Концентрат КФ-7 | 1.9 | 8.2 | 90 |
2 | ЦНС сырье – 200 г/л ФС сырье – 40 г/л Неорганическая солевая добавка (НСД-1) – 15 г/л |
1.7 | 8.5 | 90 |
3 | ЦНС сырье – 200 г/л ФС сырье – 40 г/л Неорганическая солевая добавка (НСД-1) – 15 г/л Неорганическая добавка (НД-Ц) – 9 г/л |
1.6 | 6.6 | 85 |
4 | ЦНС сырье – 150 г/л ЦФС сырье – 45 г/л |
2.0 | 7.0 | 90 |
Стандартный раствор 1 (табл. 1) предусматривал обработку деталей при повышенной температуре, что приводило к дополнительному расходу электроэнергии, создавало определенные трудности обработки крупногабаритных деталей и невозможность фосфатирования деталей, для которых нагрев недопустим. Раствор 2 (табл. 1), в отличие от состава КФ, хотя и позволял получать ФП с достаточной защитной способностью на стали при комнатной температуре, но был сложен в приготовлении. Для устранения этого недостатка был разработан фосфатирующий состав на основе цинк-фосфат-нитрат-содержащего сырья отечественного производства (раствор 4, табл. 1), который был выбран в качестве базового раствора. Защитная способность ФП, сформированных в данных условиях на стали марки Ст3, составляла 90 с.
С целью оптимизации условий получения на стали коррозионностойких покрытий на основе базового раствора была исследована серия новых растворов с измененной концентрацией основных его компонентов, а также с различными добавками, способствующими созданию условий для формирования покрытий улучшенного качества. Выбор добавок, учитывая электрохимическую природу процессов, протекающих при фосфатировании, был основан на их способности оказывать влияние на скорость электрохимических процессов, а также на процесс кристаллизации ФП [1–3]. Проведенные исследования процесса фосфатирования стали в цинк-нитрат-фосфатных растворах с различными модифицирующими добавками (оксидно-солевые добавки, соединения металлов более электроположительных, чем железо (Ni, Mn, Ca, Co), кремний- и бор-содержащие соединения) позволили выявить эффективную неорганическую кремнийсодержащую солевую добавку, условно обозначаемую СД-С (табл. 2).
Таблица 2.
Составы фосфатирующих растворов и коррозионная стойкость полученных в них ФП на стали марки Ст3. Время фосфатирования – 30 мин. Температура фосфатирования – 25°С
№ п/п | Состав раствора, г/л | рН | γ , с |
---|---|---|---|
1 | ЦНС сырье − 150 ЦФС сырье − 45 Mn(NO3)2 · 6H2O − 5 |
1.9 | 90 |
2 | ЦНС сырье − 150 ЦФС сырье − 45 MgSO4 − 4 |
2.0 | 95 |
3 | ЦНС сырье − 150 ЦФС сырье − 45 FeSO4 − 9 |
2.0 | 95 |
4 | ЦНС cырье − 150 ЦФС cырье − 45 Na2SiF6 − 8 |
2.4 | 70 |
5 | ЦНС сырье − 150 ЦФС сырье − 45 NH2HF2 − 1 |
1.9 | 60 |
6 | ЦНС сырье − 150 ЦФС сырье − 45 Na2B4O7 − 4 |
2.2 | 45 |
7 | ЦНС сырье − 150 ЦФС сырье − 45 Солевая добавка СД-С – 0.1 |
1.8 | 90 |
8 | ЦНС сырье −150 ЦФС сырье − 45 Солевая добавка СД-С − 1 |
1.9 | 95 |
9 | ЦНС сырье −150 ЦФС сырье − 45 Солевая добавка СД-С − 10 |
2.0 | 110 |
10 | ЦНС сырье −150 ЦФС сырье − 45 Солевая добавка СД-С − 20 |
2.0 | 150 |
11 | ЦНС сырье −150 ЦФС сырье − 45 Солевая добавка СД-С − 30 |
2.1 | 80 |
12 | ЦНС сырье −150 ЦФС сырье − 45 Na5P3O10 − 1 |
1.9 | 30 |
Изучение влияния концентрации добавки СД-С (0.1–30 г/л) на процесс фосфатирования показало, что наибольшая защитная способность фосфатной пленки прослеживалась при ее концентрации 20 г/л (табл. 2).
Учитывая положительное влияние кремнийсодержащей добавки СД-С на коррозионную стойкость ФП, именно в растворе 10 была подробно изучена кинетика формирования фосфатной пленки на стали. Полученные результаты сопоставлялись с результатами фосфатирования стали в базовом растворе (рис. 1, 2).
Рис. 1.
Изменение массы растворившегося металла (1, 2) и потенциала (3, 4) в процессе фосфатирования стали марки Ст3 в цинк-нитрат-фосфатном растворе (1, 3) и цинк-нитрат-фосфатном растворе с добавкой СД‑С (2, 4).
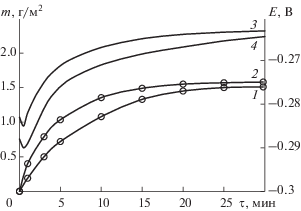
Рис. 2.
Изменение массы (1, 2) и коррозионной стойкости (3, 4) ФП, полученных на стали марки Ст3 в цинк-нитрат-фосфатном растворе (1,3) и цинк-нитрат-фосфатном растворе с добавкой СД-С (2, 4).
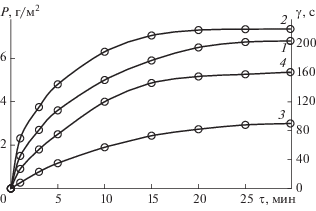
Как следует из рис. 1 и 2, характер изменения основных характеристик покрытий (m, Р, γ) в исследуемых растворах аналогичен. Протекающие электрохимические процессы анодного растворения стали и катодного восстановления окислителей, присутствующих в растворе, приводят к выпадению фосфатов уже на начальной стадии соприкосновения стали с фосфатирующим раствором. Первоначальный период фосфатирования сплава отличается синхронным изменением скорости роста ФП, скорости растворения фосфатируемого сплава, что подтверждает электрохимическую природу процесса их фосфатирования.
В цинк-нитрат-фосфатном растворе с выявленной добавкой СД-С в первые минуты фосфатирования на стали устанавливался более отрицательный потенциал, и отмечалось увеличение скорости протекания электрохимических процессов. Согласно данным электрохимических исследований добавка СД-С в области потенциала фосфатирования приводила к ускорению электрохимического растворения стали (рис. 3). Анализируя возможные причины влияния этой добавки, следует иметь в виду, что это связано, вероятно, с изменением свойств поверхности стали в ее присутствии. Образование покрытий в модифицированном фосфатирующем растворе на стали заканчивается уже к 15–20 мин против 20–30 мин в базовом растворе (рис. 2) и фосфатные пленки отличались большей коррозионной стойкостью (γ = = 150–170 с против γ = 90 с).
Рис. 3.
Анодные (1, 2) и катодные (1', 2') поляризационные кривые на стали марки Ст3 в модельных растворах (рН 1,95): 1, 1' – 0.3 М Н3РО4 + 1.0 М НNO3 + + NaOH; 2, 2' – 0.3 М Н3РО4 + 1.0 М НNO3 + 0.7 М СД-С +NaOH.
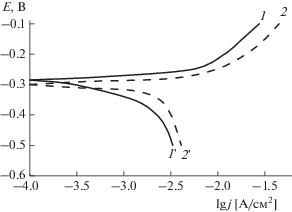
Подтверждением изменения защитной способности фосфатных пленок, сформированных на стали в цинк-нитрат-фосфатном растворе в присутствии добавки С-ДС, являются и результаты импедансных измерений ФП в 0.1 М растворе сульфата натрия. Фосфатное покрытие является пористым диэлектриком, обладающим в растворе электролита импедансом, хорошо описываемым эквивалентной схемой, состоящей из активного сопротивления (R1), представляющего собой сопротивление электролита, емкости двойного электрического слоя (С1), являющейся геометрической емкостью фосфатной пленки, активного сопротивления (R2), являющегося поляризационным сопротивлением фосфатного покрытия и диффузионного импеданса Варбурга (W), ответственного за диффузию ионов электролита в порах ФП (рис. 4). Рассчитанные значения элементов данной эквивалентной схемы для ФП, полученных в базовом фосфатирующем растворе и в растворе с кремнийсодержащей добавкой, приведены в табл. 3.
Рис. 4.
Эквивалентная схема для интерпретации импеданса стального электрода (сталь марки Ст3) в 0.1 М Na2SO4 с фосфатными покрытиями, сформированными в различных условиях: R1 – сопротивление раствора электролита, С1 – емкость двойного электрического слоя, R2 – поляризационное сопротивление, W – импеданс Варбурга, обусловленный проводимостью электролита в порах фосфатной пленки.
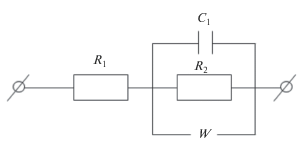
Таблица 3.
Рассчитанные значения элементов эквивалентной схемы, моделирующей импеданс стальных электродов (сталь марки Ст3) с фосфатными покрытиями в 0.1 М Na2SO4 при стационарном потенциале
Состав раствора, г/л | τфосф, мин | R1, Ом | C1, мкФ | R2, Ом |
---|---|---|---|---|
ЦНС сырье – 150 ЦФС сырье – 45 |
10 | 11.2 | 650 | 650 |
ЦНС сырье – 150 ЦФС сырье – 45 Солевая добавка СД-С − 20 |
3 | 9.4 | 150 | 500 |
10 | 12.9 | 0.7 | 5886 | |
30 | 14.1 | 0.5 | 11 100 |
Из сравнительного анализа годографов импеданса стальных электродов с фосфатными пленками, сформированными в различных по составу растворах (рис. 5), следует, что наибольшее сопротивление (R2 = 5886 Ом см2 – раствор 10 (табл. 2) против R2 = 650 Ом см2 – раствор 4 (табл. 1)) при одновременном уменьшении их электрической емкости имеют стальные электроды с фосфатными покрытиями, полученными в растворе с кремнийсодержащей добавкой. Это служит доказательством повышенной защитной способности ФП, сформированных в фосфатирующем растворе именно в присутствии эффективной модифицирующей добавки СД-С.
Рис. 5.
Годографы импеданса в 0.1 М Na2SO4 стальных электродов с фосфатными покрытиями, сформированными на стали марки Ст3 в различных растворах (время фосфатирования 10 мин): 1 – цинк-нитрат-фосфатный раствор, 2 – цинк-нитрат-фосфатный раствор с добавкой СД-С.
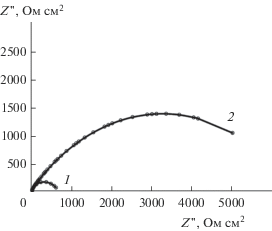
Согласно результатам кинетических исследований, увеличение времени выдержки стального электрода в фосфатирующем растворе, приводит к образованию более толстых и коррозионностойких ФП. Увеличение толщины фосфатных пленок, сформированных в данных условиях подтверждается уменьшением емкости С1 и ростом поляризационного сопротивления R2 фосфатной пленки. Наблюдаемое увеличение сопротивления электролита (R1) по мере возрастания времени фосфатирования стального электрода в фосфатирующем растворе 10 (табл. 2) может свидетельствовать об уменьшении размера пор фосфатной пленки.
Фосфатные покрытия, сформированные в растворе с неорганической солевой добавкой СД-С, были крупнокристаллическими, но для них характерна большая равномерность и однородность по сравнению с покрытиями, полученными в базовом растворе (рис. 6). Выявленная добавка, видимо, влияет не только на скорость электрохимических процессов, как отмечалось выше, но и на процесс кристаллизации. С помощью рентгенофазового анализа в ФП, образованных в модифицированном фосфатирующем растворе, зафиксирована фаза гопеита (Zn3(PO4)2 · 4H2O) с основными рефлексами, как и в случае базового раствора, но с перераспределениями их интенсивностей [14]. Образцы стали с ФП, полученными в растворе 10 (табл. 2), по защитным свойствам отвечали требованиям ГОСТ 9.302-88.
Рис. 6.
Микроструктура ФП, сформированных на стали марки Ст3 в различных растворах (время фосфатирования 30 мин): а – цинк-нитрат-фосфатный раствор, б – цинк-нитрат-фосфатный раствор с добавкой СД-С (MIRA 2LMUx5000).
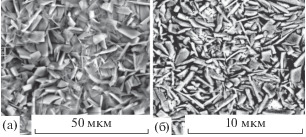
Этот фосфатирующий раствор можно рассматривать и как универсальный, в котором при комнатной температуре могут быть получены коррозионностойкие покрытия на низкоуглеродистых сталях разных марок: Ст3, 10, 45, 50, 17Г1С, 08КП. Однако, следует отметить, что скорость взаимодействия сталей с фосфатирующим раствором зависит от их состава, что сказывается впоследствии на скорости формирования фосфатных пленок. Так, в частности, на сталях марки 50, 17Г1С на начальной стадии фосфатирования устанавливается более положительный потенциал (Е = –0.240 В и Е = –0.245 В соответственно) по сравнению со сталью марки Ст3 (Е = –0.264 В), т.е. электрохимические процессы протекают с меньшей скоростью и процесс фосфатирования заканчивается к 25–30 мин против 15–20 мин на Ст3.
ФП пронизаны огромным количеством микропор, площадь которых составляет от 0.1 до 1% фосфатированной поверхности. Поэтому в практике противокоррозионной защиты металлов большое влияние уделяют дополнительным мерам повышения защитных свойств фосфатных пленок. Одна из них – заключительная обработка ФП пассиваторами, которые в дефектах покрытия химически взаимодействуют с непокрытым металлом [3].
В нашем случае повышение коррозионной стойкости покрытий прослеживалось при использовании последующей обработки ФП, сформированных в цинк-фосфатном растворе с солевой добавкой СД-С (С = 20 г/л, τфосф = = 15 мин, t = = 25°С), в водном растворе, содержащем соединения кремния (С = 0.1 г/л, τ = = 5 мин, t = 25°С). Исходя из этих начальных условий, для оптимизации процесса получения ФП с улучшенными характеристиками на стали марки Ст3 был использован метод математического планирования экстремального эксперимента Бокса–Уилсона [15], описываемый матрицей типа 23. В качестве варьируемых факторов были выбраны концентрации выявленной эффективной солевой добавки СД-С фосфатирующего раствора (Х1), кремнийсодержащей добавки в растворе для дополнительной обработки (Х2) и время дополнительной обработки (Х3). За параметр оптимизации принята коррозионная стойкость ФП (γ). Уровни факторов в натуральном масштабе и интервалы варьирования представлены в табл. 4.
Таблица 4.
Характеристика плана эксперимента
Факторы | Уровни | Интервал варьиро-вания, % | ||
---|---|---|---|---|
нижний | основной | верхний | ||
Х1, г/л | 16 | 20 | 24 | 20 |
Х2, г/л | 0.05 | 0.1 | 0.15 | 50 |
Х3, мин | 3.5 | 5.0 | 6.5 | 30 |
Пошаговое планирование эксперимента позволило получить функцию отклика и нахождение с ее помощью оптимальных условий:
В данных условиях были поставлены контрольные опыты. Коррозионная стойкость ФП соответственно была равной 2.4; 2.9; 3.7 мин. Расхождение с расчетными данными ($\hat {y}$ = 2.5; 3; 3.5 мин) лежит в пределах ошибки эксперимента. Далее было проведено сопоставление кинетики образования фосфатного покрытия в цинк-фосфатном растворе с добавкой СД-С без последующей и с последующей обработкой в водном растворе, содержащем соединения кремния (рис. 7). Дополнительная обработка фосфатных пленок в кремнийсодержащем растворе способствует формированию ФП, отличающихся при незначительном увеличении их массы повышенной защитной способностью (γ = 200–220 с против γ = 150–170 с). По-видимому, на ФП образуется силикатная пленка, имеющая адсорбционную природу и при дополнительной обработке в растворе силиката пленка самозалечивается. Кроме того, дополнительная обработка в растворе с силикатом исключала операции промывки после фосфатирования, то есть давала переход к малоотходной технологии.
Рис. 7.
Изменение массы (1, 2) и коррозионной стойкости (3, 4) ФП, полученных на стали марки Ст3 в цинк-нитрат-фосфатном растворе с добавкой СД-С: 1, 3 – без дополнительной обработки; 2, 4 – с дополнительной обработкой в кремнийсодержащем растворе.
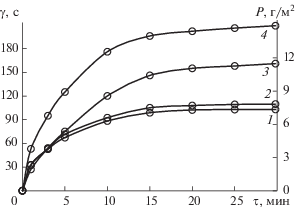
Таким образом, на основании проведенных исследований определены оптимальные состав фосфатирующего раствора и условия для получения при температуре 25°С на Ст3 ФП с заданными функциональными свойствами.
Список литературы
Лапатухин В.С. Фосфатирование металлов. М.: Машгиз, 1958. 255 с.
Грилихес С.Я. Оксидные и фосфатные покрытия металлов. М.: Машгиз, 1958. С. 8395.
Хаин И.И. Теория и практика фосфатирования металлов. Л.: Химия, 1978. 308 с.
Бабакина Н.А., Мачевская Р.А. // Исследования в области техники и технологии лакокрасочных покрытий: Сб. науч. тр. М., 1975. Вып. 4. С. 13–19.
Ильина Л.К., Лямина Л.А., Кучинская М.М. и др. // Защита металлов. 1991. Т. 27. № 3. С. 500–502.
Козлова Л.А., Окулов В.В. // Гальванотехника и обработка поверхности. 2000. Т. 8. № 3. С. 40–48.
Ваграмян Т.А., Григорян Н.С., Мазурова Д.В. и др. // Коррозия: материалы, защита. 2011. № 2. С. 20–27.
ГОСТ 9.402-2004. Покрытия лакокрасочные. Подготовка металлических поверхностей к окрашиванию. М. 2004. 38 с. (Единая система защиты от коррозии и старения).
ГОСТ 9.302-88. Покрытия металлические и неметаллические неорганические. Методы контроля. М. 1988. 38 с. (Единая система защиты от коррозии и старения).
Ильина Л.К., Фортунатов А.В., Дубровский А.П.// Защита металлов. 1968. Т. 4. № 2. С. 171–174.
Ильина Л.К., Трепак Н.М., Дворкина Р.М. и др. // Расширенные тез.докл. Конгресса “Защита – 92”. М., 1992. С. 94–95.
Трепак Н.М., Исайчева Л.А., Ильина Л.К. и др.// Тез. докл. III Междун. Конгресса “Защита – 98”. М., 1998. С. 67.
Исайчева Л.А., Трепак Н.М., Ильина Л.К. и др. // Физикохимия поверхности и защита материалов. 2006. Т. 42. № 4. С. 425–429.
JCPDC (Картотека Объединенного Комитета Дифракционных Стандартов). 1987.
Адлер Ю.П., Маркова Е.В., Грановский Ю.П. Планирование эксперимента при поиске оптимальных условий. М.: Наука, 1976. 279 с.
Дополнительные материалы отсутствуют.
Инструменты
Физикохимия поверхности и защита материалов