Физикохимия поверхности и защита материалов, 2020, T. 56, № 1, стр. 104-112
Получение и исследование композиционного материала на стеклотканевой основе с металл-оксидным покрытием
В. С. Руднев 1, 2, *, В. В. Кабанов 1, 3, **, П. М. Недозоров 1, Т. П. Яровая 1, В. И. Сергиенко 1
1 Институт химии Дальневосточного отделения РАН
Владивосток, Россия
2 Дальневосточный федеральный университет
Владивосток, Россия
3 ООО “Плазмоавтоматика”,
Владивосток, Россия
* E-mail: rudnevvs@ich.dvo.ru
** E-mail: plasma55@mail.ru
Поступила в редакцию 14.06.2018
После доработки 05.09.2019
Принята к публикации 10.09.2019
Аннотация
Многослойный материал получен на основе модифицированного слоем алюминия препрега, – прекурсора для формирования стеклотканевого композита. Слой алюминия предварительно наносили на препрег плазменным напылением. Далее применяя модифицированный препрег формировали стеклотканевый композит со слоями алюминия на внешних сторонах и методом плазменно-электролитического оксидирования получали на поверхности алюминия оксидное покрытие. Предложенная стратегия может составить основу технологии приготовления композитов с электропроводным слоем металла и повышенной огнестойкостью. В работе представлены данные о строении полученного материала, оценка его огнестойкости.
1. ВВЕДЕНИЕ
Как в отечественном, так и в зарубежном авиастроении все большее внимание уделяют применению полимерных композиционных материалов, в том числе на основе стекловолокон и углепластиков при изготовлении элементов конструкций летательных аппаратов [1–3]. При этом улучшается технологичность процесса изготовления, снижается масса изделий, повышаются прочностные характеристики, однако проявляются и отрицательные свойства пластиков, – низкая стойкость к местным ударным нагрузкам, пониженная стойкость к воздействию молний, абразивов, накопление статического электричества на поверхностях конструкций, огнеопасность. Решению этих проблем разработчики и авиастроители уделяют повышенное внимание.
Одно из направлений решения данных проблем – создание гибридных материалов, обеспечивающих повышение стойкости полимерного композиционного материала к вышеперечисленным воздействиям посредством ввода в материал дополнительных составляющих. Применяют, в частности, системы на основе закрепленных на композиционном материале металлической фольги, медных или алюминиевых шин и сеток или напыленных на композит слоев металлов [3–8]. Изучают введение в композиционный материал токопроводящих наполнителей, в том числе электропроводных полимеров [4, 9, 10], металлизированных полимерных волокон, металлических дисперсных частиц, углеродных нанотрубок [3, 4, 11–13].
В настоящей работе для решения выше обозначенных проблем начато обоснование подхода, включающего следующие основные операции:
1. Нанесение методом плазменного напыления покрытия из алюминия или его сплавов не на готовое изделие, а на исходный материал для получения полимерного композиционного материала – препрег (ткань на основе стекло- или углеволокна, пропитанная неотвержденными полимерными связующими). Дальнейшие действия с модифицированным препрегом предполагается осуществлять в соответствие с действующей технологией формования композитного материала при заданных температурах и давлении. В этом случае отпадают технологические операции прикрепления на сформированный композит алюминиевой фольги, сетки или нанесения на поверхность изделия токопроводящего слоя иными способами, что существенно упрощает технологический процесс.
2. Далее металлическое покрытие на отформованном изделии подвергается обработке методом плазменно-электролитического оксидирования (ПЭО) до получения на рабочей токопроводящей поверхности изделия керамической (оксидной) пленки заданной толщины и с нужными характеристиками, повышающей абразивную стойкость изделия и изолирующей слой алюминия от контакта с газовой атмосферой, сохраняя при этом возможность отвода статических зарядов с рабочей поверхности изделия через токопроводящий слой.
Полученный таким образом композит может обеспечить комплекс полезных свойств, в том числе, повышенную огнестойкость материала и стойкость к ударам молнии, снятие статического электричества с корпуса и несущих элементов летательных аппаратов. В дополнение к основным показателям плазменное покрытие и ПЭО-обработка могут обеспечить качественные укрываемость и гладкость поверхности при последующих грунтовке и окраске изделий, что упрощает технологический процесс и минимизирует затраты на очистные сооружения, необходимые при использовании традиционных гальванических технологий подготовки поверхности под окраску. Варьируя условия получения ПЭО покрытий (состав электролита, электрические и временные условия обработки) возникает возможность управляемого изменения свойств покрытий (микротвердость, химический состав, пористость, гидрофобные, магнитные свойства и т.д.), что существенно расширяет области возможного применения новых материалов в авиационной технике.
Для обоснования применимости предлагаемого решения необходимо провести комплекс исследований, в том числе как по оптимизации условий нанесения на препрег плазменным напылением слоев алюминия и определения возможности и условий последующей полимеризации и ПЭО-обработки, так и получить массив данных о строении, структуре, морфологии получаемых композиционных материалов, в том числе о его механических, электрических, магнитных и теплофизических свойствах.
В данной работе приведены данные о строении формируемых выше описанным путем слоистых композиционных материалов и оценка их огнестойкости.
2. МАТЕРИАЛЫ И МЕТОДЫ
2.1. Нанесение на препрег алюминиевого покрытия и формовка композита
В работе проведены эксперименты по нанесению алюминиевого покрытия на препрег (ткань Т-10-14 ГОСТ 19170-2001 – разработчик НПО “Стеклопластик” на связующем ЭДТ-69Н ТУ 1-595-12-584-2006 – разработчик ФГУП “ВИАМ”). Для напыления применяли серийно выпускаемый алюминиевый порошок ПА-4 ГОСТ 6058-73. При дисперсности порошка 65–100 мкм, сыпучесть на воронке Холла составляет 50 г за 70–80 с, что позволяет достаточно уверенно наносить покрытие методом плазменного напыления на установке ПЛ-04 (Россия). Основным рабочим элементом установки является хорошо зарекомендовавший себя в производственной практике плазмотрон ПН-21Р (Россия) с межэлектродными вставками (МЭВ) [14]. Повышенные стабильность и ресурс, возможность плавной регулировки мощности и скорости плазменной струи позволили контролируемо менять режим напыления по мере формирования покрытия с заданными электропроводностью и конечной толщиной. Подача порошка осуществлялась разработанным в ООО “Плазмоавтоматика” питателем 7103, оснащенным встроенным контроллером, позволяющим осуществлять управление подачей порошков в процессе напыления по заданной программе [15]. В качестве плазмообразующего и транспортирующего газа использован аргон. Покрытие наносилось на препреговую ткань, растянутую в плоскости на теплоизолирующей основе. Плазмотрон при этом перемещался в параллельной плоскости на расстоянии 160 мм от поверхности основы. Напыление проводилось в два прохода. Первоначально осуществлялось внедрение относительно холодных частиц порошка в поверхность компаунда. На втором же проходе формировался токопроводящий монослой из уже расплавленных частиц. Температура частиц порошка, их скорость при этом изменялись посредством смены режима работы плазмотрона. Расход порошка при переходе с первого прохода на второй изменялся с 0.1 до 0.3 г/с, что позволило снизить тепловое воздействия металла на свойства связующего и сохранить гибкость получаемого материала на уровне, достаточном для хранения в рулоне и для последующей формовки изделия в матрице. Металлизированный таким способом препрег может быть использован в различных комбинациях при формовке многослойных композиционных конструкций. В данной работе, с целью предварительной оценки свойств получаемых материалов, были отформованы трехслойные образцы. Между двумя слоями металлизированного препрега (с покрытием по внешней поверхности) был уложен еще один лист препрега в исходном состоянии. Формование осуществлялось в стальной пресс-форме с плоскими рабочими поверхностями под давлением 0.6–0.8 МПа при температуре 150оС в течение 4 ч, с последующим охлаждением при температуре 40оС в течение часа. В качестве разделительного слоя при формовке использован листовой фторопласт Ф-4М.
2.2. Формирование оксидных покрытий
Покрытия формировали методом ПЭО, – электрохимическим анодным окислением поверхности нанесенного слоя алюминия в условиях действия в приэлектродной области искровых и микродуговых электрических разрядов [16, 17]. ПЭО проводили согласно [18, 19] в электролите состава, г/л: 25Na3PO4 · 12H2O + 13Na2B4O7 · 10H2O + + 2Na2WO4 · 2H2O. Для приготовления электролита использовали дистиллированную воду и коммерческие реактивы квалификации “х. ч.”. Покрытия формировали в стальной ванне объемом 2 л с рубашкой водяного охлаждения, через которую пропускали холодную водопроводную воду. Температура электролита при обработке не превышала 30°С. Электролит в ванне перемешивали механической мешалкой. Противоэлектродом служил корпус ванны. В качестве источника тока использовали управляемый компьютером реверсивный тиристорный агрегат ТЕР4-63/460Н (Россия), работающий как в однополярном, так и в биполярном анодно-катодном режиме. Покрытия на образцах формировали в гальваностатических условиях в течение 30 мин. Эффективные плотности тока при анодной поляризации iа = 0.05 А/см2, при анодно-катодной iа = iк = 0.05 А/см2 с длительностями импульсов соответствующих токов 0.02 с. После обработки образцы с покрытиями промывали проточной водой, затем ополаскивали дистиллированной и сушили на воздухе при температуре 70°С.
2.3. Приготовление шлифов
Образцы заливали в цилиндрической обойме эпоксидной смолой. После отвердевания шлифы готовили по стандартным методикам.
2.4. Определение элементного и фазового составов, изучение морфологии образцов
Фазовый состав образцов определяли на рентгеновском дифрактометре D8 ADVANCE (Германия) CuKα-излучение. Для анализа рентгенограмм использовали поисковую программу EVA с банком данных PDF-2. Микрофотографии поверхности и сечения покрытий и элементный состав покрытий получали и определяли на рентгеноспектральном микроанализаторе JXA-8100 фирмы “JEOL” (Япония) с энергодисперсионной приставкой Oxford Instrument INCA-sight (Великобритания). Прибор позволяет проводить количественный элементный анализ состава образцов как в “точке” диаметром около 1 мкм (с неподвижным зондирующим электронным пучком), так и при сканировании определенных площадок на поверхности образца, получить снимки поверхности, строить карты распределения элементов по площади образца, профили распределения концентрации элементов на поверхности и по сечению образцов. Для определения элементного состава поверхности сканировали от 3 до 5 площадок размером 300 × 200 мкм2. Глубина проникновения зондирующего луча в зависимости от материала покрытия составляет 2–5 мкм.
3. РЕЗУЛЬТАТЫ И ОБСУЖДЕНИЕ
3.1. Характеристики композиционного материала
Слой алюминия напыляли на как полученный из препрега композит, рис. 1а, 1б, так и исследовали закономерности напыления слоя алюминия на препрег, рис. 1в, 1г. На рис. 1 показан внешний вид композиционного материала, полученного из трех слоев препрега без (в) и с предварительно напыленными на 2 внешних слоя препрега алюминием (г). Нанесенный на препрег слой алюминия при полимеризации трех слоев препрега визуально сохраняет сплошность и равномерность.
Рис. 1.
Композит (а) и композит с напыленным слоем алюминия (б). Композиционный материал, полученный из трех слоев препрега без (в) и с предварительно напыленным на 2 внешних слоя препрега алюминием (г).
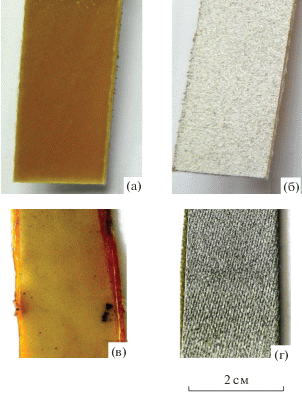
На снимке, рис. 2, видно, что полученная алюминиевая поверхность композита представляет собой плоские протяженные участки, разделенные впадинами. На поверхности видны многочисленные трещины и дефекты. Такая морфология поверхности – следствие выравнивания поверхности напыленного на препрег слоя порошка алюминия, при давлении на образец при полимеризации внешней металлической поверхности с прокладкой фторопластовой пленки.
Определенный с помощью микрозондового рентгеноспектального анализатора усредненный состав поверхности, ат. %: 7.8O; 91.3Al; 0.7Si; 0.2Fe. Наличие кислорода указывает на частичное окисление нанесенного слоя алюминия.
На рис. 3а показано сечение полученного композиционного материала. Толщина стеклотканевой матрицы из трех слоев препрега, ~625 мкм, толщина слоя алюминия, предварительно нанесенного на препрег, на полученном композите ~100 мкм.
Рис. 3.
ЭСМ-снимки сечения композиционного материала (а) и области контакта полимер/слой алюминия (фазовое представление). На снимке (б) показаны кривые распределения Al, Si и Ca по линии L сечения.
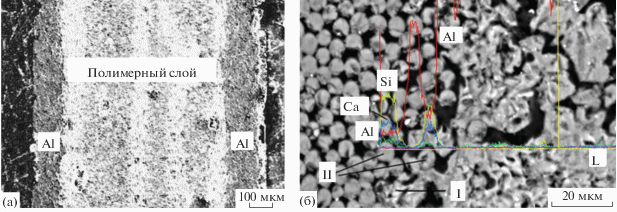
Из данных рис. 3б следует, что примененные условия плазменного напыления не приводят к деградации нитей стеклоткани в области контакта с алюминием. Они сохраняют свою форму и порядок расположения. С другой стороны, на границе контакта происходит взаимопроникновение областей алюминия и волокон стеклоткани. Например, в области I видно погружение алюминиевого участка в матрицу полимера. Т.е. адгезия напыленного слоя алюминия к полимеру носит в том числе и механический характер за счет взаимопроникновения в области контакта алюминия и волокна. Последнее также видно при анализе рис. 1г. Адгезия между стеклотканевой матрицей и алюминием может быть дополнительно обеспечена взаимодействием компаунда с нанесенным металлом.
На рис. 3б показаны кривые распределение элементов в области контакта по линии анализа L. Противофазное изменение в области контакта содержания алюминия с одной стороны, кремния и кальция с другой подтверждают факт взаимопроникновения участков стеклоткани в слой алюминия и наоборот.
По визуальным оценкам адгезия алюминия и полимерного слоя удовлетворительная, не наблюдается разделения металла и полимера при деформациях полученного гибридного материала.
Таким образом, подтверждено предположение о возможности предварительного плазменного напыления слоя алюминия на препрег. Используя модифицированный препрег можно осуществлять в соответствие с действующей технологией формование при заданных температурах и давлении стекловолоконного композитного материала со слоями алюминия на границах раздела с воздухом.
3.2. Формирование на поверхности полимер-алюминиевого композита керамического покрытия
Нам не известны предшествующие работы по плазменно-электролитическому оксидированию слоев алюминия, нанесенных на полимер. Выполненные эксперименты показали, что в изучаемом случае на слоях алюминия толщиной ~100 мкм на стеклотканевом композите, предварительно нанесенных плазменным напылением алюминиевого порошка на препрег, ПЭО осуществляется, хотя и протекает с отличиями от закономерностей обработки алюминиевого проката.
На рис. 4 приведены кривые изменения напряжения на электродах от длительности процесса обработки (формовочные кривые) при гальваностатической анодной (а) и переменно токовой анодно-катодной ПЭО обработке (б).
Рис. 4.
Изменение во времени напряжения на электродах и силы тока, протекающего через электроды в гальваностатическом анодном (а) и переменно-токовом анодно-катодном (б) ПЭО образцов.
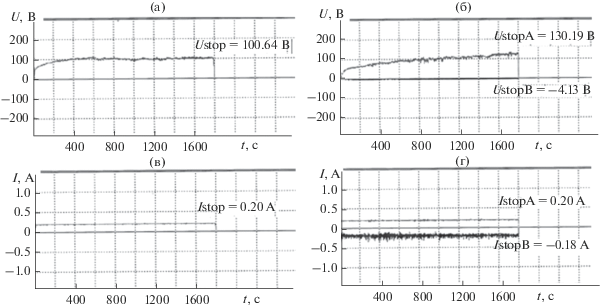
В обоих случаях функции U = f(t) имеют типичный при ПЭО алюминиевых сплавов вид. На основе точек перегиба кривых на них можно выделить характерные стадии ПЭО, а именно, доискрового оксидирования (первые десятки секунд), а также оксидирование в условиях действия искровых (примерно до 600 с) и микродуговых (более 600 с) электрических разрядов. Отличие полученных формовочных кривых от аналогичных при оксидировании компактного сплава алюминия (прокат) – относительно низкие напряжения начала искрения (около 50 В по поведению зависимостей U = f(t)) и напряжение на электродах в данный момент времени. Кроме того, заметно увеличенная длительность стадии искровых разрядов. Так при ПЭО обработке проката сплава АМцМ напряжение начала визуально видимых искровых разрядов в прианодной области составляет ~180 В, уже через десять минут ПЭО обработки в используемом электролите напряжение на электродах около 300 В и, согласно поведению формовочной кривой, процесс при этом времени обработки идет уже в стадии микродуговых разрядов [19].
На рис. 5 показана поверхность сформированных в анодном режиме покрытий. Снимки покрытий, сформированных в анодно-катодном режиме, аналогичны представленным на рис. 5. На поверхности выделяются два типа участков. Участки типа А, рис. 5в, с множеством поднятий с порами на вершинах характерны для покрытий, формируемых методом ПЭО в условиях действия электрических разрядов. Т.е. на этих участках сформировано ПЭО покрытие с характерной для него морфологией поверхности. Наряду с участками А, занимающих большую часть поверхности, имеются участки типа Б с непокрытой поднятиями и порами гладкой поверхностью. Согласно данным рис. 5б они отличаются по фазовому составу от основного массива покрытия. Вероятно, это участки, лежащие в углублениях нанесенного слоя алюминия (см. рис. 2), и, предположительно, не подвергнутые действию электрических разрядов при ПЭО. Подобная ситуация возможна из-за особенностей распределения электрических полей при ПЭО вследствие сложной развитой поверхности оксидируемого слоя алюминия, рис. 2. На поверхности таких участков может присутствовать либо тонкая оксидная пленка, либо это участки исходного слоя алюминия. Эти предположения косвенно подтверждает измеряемое тестером низкое омическое сопротивление покрытия в его плоскости и в поперечном сечении. Кроме того, они согласуются с поведением формовочных кривых, рис. 4. Пониженные в данный момент времени обработки величины напряжения на электродах по отношению к наблюдаемым при ПЭО проката могут быть связаны с шунтированием растущего оксидного слоя более хорошо проводящими электрический ток участками. Если сделанные предположения о размещении и составе поверхности участков А и Б верны, то соотношение площадей, занимаемых ими на поверхности можно регулировать как изменением рельефа напыленного слоя алюминия, так и условиями ПЭО обработки, например, длительностью и плотностью тока.
Рис. 5.
ЭСМ-снимки поверхности покрытий в амплитудном (а, в) и фазовом представлениях (б). На снимке (в) увеличены площадки А и Б покрытия.
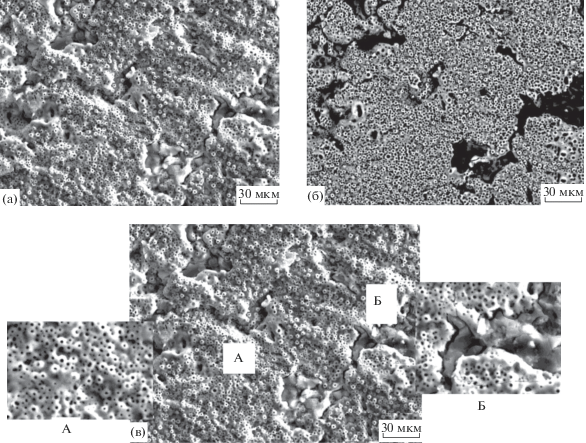
На рентгенограммах образцов с ПЭО покрытиями, рис. 6, присутствуют слабые рефлексы оксида алюминия. То есть в составе покрытий присутствует кристаллический оксид алюминия, что характерно для ПЭО покрытий. Значительные пики алюминия, свидетельствуют о достаточно небольшой толщине полученного оксидного слоя и, возможно, о наличии в нем участков не оксидированного алюминия.
Рис. 6.
Рентгенограммы исследуемых образцов: (а) исходный композит со слоем алюминия; (б) композит после ПЭО в анодном и (в) в переменно токовом анодно-катодном режиме.
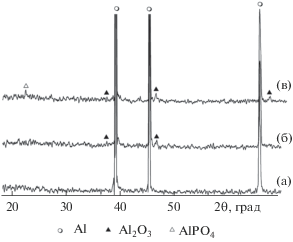
На рис. 7 представлены ЭСМ-снимки сечения образца с покрытием, сформированном в течение 30 мин в анодно-катодном режиме, и увеличенные области полимер/слой алюминия/оксидное покрытие и алюминий/оксидное покрытие. Образцы и упомянутые области сечения подобны и при получении ПЭО-покрытия в анодных условиях. Покрытия неоднородны по толщине. Толщина покрытий, полученных в переменно токовом анодно-катодном режиме по измерениям на ЭСМ-снимках находится в пределах 4–7 мкм, сформированном при анодной поляризации в интервале 5–9 мкм. В обоих случаях получены покрытия с большим числом каверн, как на поверхности, так и внутри оксидного слоя. Тем не менее покрытие нанесено на весь внешний слой алюминия, явных больших разрывов в оксидном слое не обнаружено.
Рис. 7.
Сечение образца с ПЭО-покрытием (а), увеличенные области полимер/алюминий/покрытие (б) и алюминий/покрытие (в, г). Амплитудное (а, в) и фазовые представления (б, г). Покрытие сформировано за 30 мин в анодно-катодном режиме.
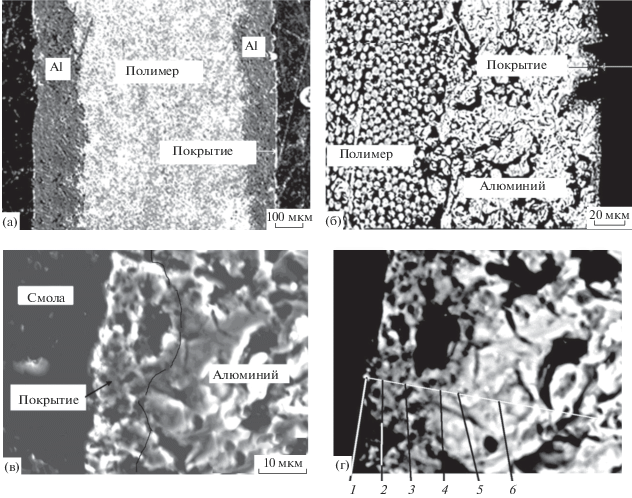
Отметим, что покрытие подобной толщины (~10 мкм) формируется на прокате сплава алюминия АМцМ в использованном электролите в течение 10 мин [19]. Т.е. скорость роста покрытий на поверхности проката примерно в три раза выше, чем на напыленном на полимер слое алюминия. Этот факт очевидно также, как это уже отмечено выше, определяется развитым рельефом оксидируемого слоя алюминия и сложным распределением в нем электрических полей, шунтированием растущего оксидного слоя проводящими электрический ток участками.
Сравнение кривых на рис. 4а, 4б, а также сравнение строения сечений покрытий дают основание полагать, что применение анодно-катодного режима обработки более предпочтительно по сравнению с анодным при ПЭО слоя напыленного алюминия на полимер.
В табл. 1 представлены данные по составу отдельных точек на сечении покрытие/алюминий для образца, сформированного в анодно-катодном режиме, рис. 7г). Определенный состав точек 1–4 соответствует составу покрытия, состоящего из оксида алюминия с примесью элементов из электролита фосфора, вольфрама и натрия. По-видимому, покрытие в виде примесей содержит фосфаты, например, фосфат алюминия, рис. 6, и либо оксид вольфрама, либо вольфраматы, например, алюминия. Такой элементный состав покрытий на алюминии характерен для покрытий на сплавах алюминия, формируемых в использованном электролите [18, 19].
Таблица 1.
Элементный состав сечения покрытие/алюминий
Точка | Содержание, ат. % | ||||
---|---|---|---|---|---|
O | Na | Al | P | W | |
1 | 61.5 | – | 36.5 | 1.8 | 0.2 |
2 | 61.9 | 0.3 | 33.4 | 4.1 | 0.3 |
3 | 60.6 | 0.5 | 35.7 | 3.0 | 0.2 |
4 | 63.3 | 0.2 | 33.1 | 3.2 | 0.2 |
5 | 19.0 | – | 80.3 | 0.7 | – |
6 | 6.2 | – | 93.8 | – | – |
Отметим, что согласно полученным данным между сформированным оксидным слоем (точки 1–4) и слоем алюминия (точка 6) есть переходная зона с промежуточным содержанием кислорода и алюминия (точка 5). Наличие переходной зоны с постепенным изменением состава от металла к покрытию подразумевает хорошую адгезию сформированного оксидного слоя к металлу.
3.3. Оценка огнестойкости образцов
На рис. 8 показано поведения образцов в пламени спиртовой горелки, температура в верхней части факела которой, как известно, ~900°С. Снимки (а–в) поведение композита из стеклоткани, снимки (г–е) – композита из стеклоткани со слоем алюминия и ПЭО покрытием на его поверхности. Снимок (а) – помещение композита в пламя спиртовки. Приблизительно через 40 с образец начал гореть, снимок (б), а через 80 с связующий компаунд выгорел до состояния “стекловолокно-сажа”, снимок (в).
Рис. 8.
Поведение образцов в пламени спиртовой горелки: (а–в) – поведение композита из стеклоткани; (г–е) – композита из стеклоткани со слоем алюминия и ПЭО покрытием на его поверхности.
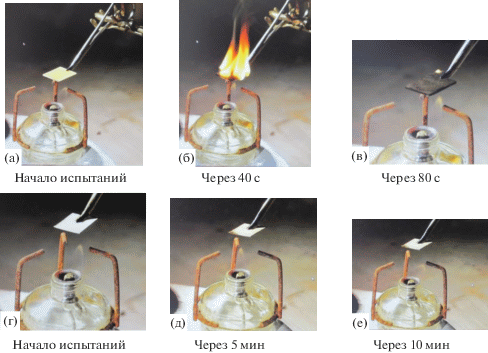
В случае образца композита со слоем алюминия и оксидным ПЭО покрытием, снимок (г) – помещение образца в пламя горелки. Снимок (д) – образец в пламени горелки через 5 мин и снимок (е) – через 10 мин. Во втором случае при испытании выгорела только смола на незащищенных гранях образца. То есть синергетический эффект плохо проводящего тепло и кислород оксидного слоя и слоя алюминия с высокой теплопроводностью в условиях эксперимента более чем в 10 раз увеличивают огнестойкость композита в условиях испытаний.
ЗАКЛЮЧЕНИЕ
Таким образом в работе впервые предложена и экспериментально подтверждена принципиально новая идея нанесения слоя алюминия плазменным напылением не на готовый композит из стеклоткани или углепластика, а на поверхность его предшественника – препрег. Из модифицированного препрега далее может быть отформован по существующим технологиям многослойный композит с металлизированной поверхностью, которая обеспечит изделию из композита поверхностный слой с электрической проводимостью.
Показано, что слой алюминия на формуемом композите закрывает всю поверхность равномерно, без явных разрывов и не покрытых промежутков.
Экспериментально показано, что полученный композит со слоем алюминия может быть обработан методом плазменно-электролитического оксидирования с целью получения на поверхности нанесенного алюминия оксидного слоя. В работе установлены особенности строения областей контакта композит/слой алюминия, слой алюминия/оксидный слой. Установлены особенности в образовании, строении и составе оксидных покрытий, формируемых методом плазменно-электролитического оксидирования на напыленном слое алюминия толщиной около 100 мкм на полимерной основе.
Экспериментально подтверждено, что полученный композит со слоем алюминия и оксидным слоем на поверхности более огнестоек, чем не модифицированный композит.
Полученный экспериментальный материал может составить основу оригинальной технологии формовки из модифицированного плазменным напылением препрега изделий из стеклотканевых композитов с металлической проводимостью поверхностного слоя. Дополнительная ПЭО обработка позволит повысить защитные свойства материала, а в перспективе получать на поверхности покрытия с определенным оксидным составом и свойствами, в том числе гидрофобными, биоцидными, ферромагнитными или цветовыми.
Работа выполнена в рамках государственного задания 0265-2018-0001 и поддержана грантом программы фундаментальных исследований ДВО РАН “Дальний Восток” № 18-3-034.
Список литературы
Каблов Е.Н. // Вестник Российской академии наук. 2012. Т. 82. № 6. С. 520–530.
Башаров Е.А., Вагин А.Ю. // Труды МАИ. 2017. № 92. http://www.trudymai.ru/published.php
Katunin A., Krukiewicz K., Herega A., Catalanotti G. // Mater. Sci. 2016. V. 16. № 2(48). P. 32–46.
Gagne M., Therriault D. // Progress in Aerospace Sciences. 2014. V. 64. P. 1–16.
Kawakami H., Feraboli P. // Composites Part A-Applied Science and Manufacturing. 2011. V. 42. № 9. P. 1247–1262.
Rajesh P.S.M., Sirois F., Therriault D. // Materials & Design. 2018. V. 139. P. 45–55.
Liu Z.Q., Yue Z.F., Wang F.S., Ji Y.Y. // Advanced Materials Research. 2014. V. 915–916. P. 698–703.
Зверев А.А., Солдатенков С.И. // Патент РФ № 2211257, опубл. 27.08.2003.
Katunin A., Krukiewicz, K. // J. Polymer Engineering. 2015. V. 35. № 8. P. 731–741.
Deng H., Lin. L., Ji M.Z., Zhang S.M., Yang M.B., Fu Q. // Progress in Polymer Science. 2014. V. 39. № 4. P. 627–655.
Chakravarthi D.K., Khabashesku V.N., Valery N., Vaidyanathan R., Blaine J., Yarlagadda S., Roseman D., Zeng Q., Barrera E.V. // Advanced Functional Materials. 2011. V. 21. № 13. P. 2527–2533.
Bauhofer W., Kovacs J.Z. // Composites Science and Technology. 2009. V. 69. № 10. P. 1486–1498.
Gohardani O., Elola M.C.A., Elizetxea C. // Progress in Aerospace Sciences. 2014. V. 70. P. 42–68.
Аксенов С.Н., Бурьяненко В.Д., Кабанов В.В., Клубникин В.С. // Труды ЛПИ. 1983. № 395. С. 41–44.
http://plasma-vl.ru/ru/products.php
Vladimirov B.V., Krit B.L., Lyudin V.B., Morozova N.V., Rossiiskaya A.D., Suminov I.V., Epel’feld A.V. // Surf. Eng. Appl. Electrochem. 2014. V. 50. № 3. P. 195–232.
Rudnev V.S., Lukiyanchuk I.V., Vasilyeva M.S., Medkov M.A., Adigamova M.V., Sergienko V.I. // Surface and Coatings Technology. 2016. V. 307. P. 1219–1235.
Руднев В.С., Гордиенко П.С., Курносова А.Г., Орлова Т.И. // Патент РФ № 2061107, опубл. 27.05.96. Бюлл. № 15.
Руднев В.С., Яровая Т.П., Лысенко А.Е., Недозоров П.М., Душина Н.Е. // Коррозия: материалы, защита. 2007. № 5. С. 38–42.
Дополнительные материалы отсутствуют.
Инструменты
Физикохимия поверхности и защита материалов