Физикохимия поверхности и защита материалов, 2020, T. 56, № 1, стр. 91-103
Механизм получения и защитные свойства конверсионных покрытий на основе соединений марганца на поверхности сплава алюминия АД31
Д. С. Харитонов 1, 2, 3, *, **, И. В. Макарова 1, 4, М. А. Осипенко 1, В. И. Янушевский 1, A. Wrzesińska 2, I. Bobowska 2, И. И. Курило 1
1 Белорусский государственный технологический университет
220006 Минск, ул. Свердлова, 13а, Беларусь
2 Lodz University of Technology, Department of Molecular Physics
90-924 Lodz, Zeromskiego st., 116, Poland
3 Jerzy Haber Institute of Catalysis and Surface Chemistry of Polish Academy of Sciences
30-239 Krakow, Niezapominajek 8, Poland
4 Lappeenranta University of Technology
FI-53850 Lappeenranta, Skinnarilankatu 34, Finland
* E-mail: kharitonov@belstu.by
** E-mail: nckharyt@cyf-kr.edu.pl
Поступила в редакцию 13.11.2018
После доработки 20.03.2019
Принята к публикации 02.04.2019
Аннотация
Методами сканирующей электронной микроскопии, энергодисперсионного рентгеновского микроанализа, спектроскопии комбинационного рассеивания, UV-Vis спектрофотометрии, электрохимической импедансной спектроскопии, потенциодинамической поляризации и испытаниями в камере соляного тумана изучен стадийный механизм формирования на сплаве АД31 (АА6063) в кислых (pH 3) растворах KMnO4 марганецсодержащих конверсионных покрытий (МКП), а также их структура, состав и антикоррозионные свойства. Оптимизированы условия получения МКП и показана целесообразность их использования в многокомпонентных системах защиты от коррозии сплава алюминия АД31.
ВВЕДЕНИЕ
Алюминиевые сплавы представляют собой негомогенные структуры, содержащие в своем составе интерметаллические частицы (ИМЧ), окислительно-восстановительный потенциал которых может сильно отличаться от стандартного потенциала алюминия [1]. При введении в алюминиевую матрицу более электроположительных металлов (например, меди и цинка) образуются катодные частицы, на которых в процессе коррозии протекает восстановление кислорода, а в области, прилегающей к ним, – локальное растворение алюминия [2–4]. С другой стороны, при введении в состав сплава легирующих металлов с более электроотрицательным потенциалом (например, магния) формируются анодные участки. Подобная неоднородность структуры сплавов способствует развитию питтинговой коррозии. Склонностью к данному виду коррозии обладает сплав АД 31 [2, 5, 6], который в настоящее время широко используется в авиационной, автомобильной и легкой промышленности, в строительстве и при производстве мебели.
Для защиты алюминиевых сплавов от коррозии широко применяются методы, основанные на предварительной химической пассивации поверхности или введении в рабочую среду растворимых ингибиторов [7–11]. Конверсионные покрытия, как правило, используются в многокомпонентных системах защиты от коррозии в качестве подготовительного слоя для последующего нанесения финишных лакокрасочных покрытий (ЛКП), рис. 1. При этом основными функциями конверсионных пленок являются улучшение адгезии, а также обеспечение коррозионной стойкости поверхности в случае повреждения внешнего слоя ЛКП.
Для алюминиевых сплавов в промышленности долгое время преимущественно использовались хроматные конверсионные покрытия (ХКП), которые обладают повышенной коррозионной стойкостью, эффектом “самозалечивания” и высокой адгезией к подложке и финишным ЛКП [12–14]. Однако соединения хрома(VI), применяемые для формирования ХКП, обладают канцерогенными и токсичными свойствами, а нейтрализация и утилизация хромсодержащих сточных вод требует больших затрат [15]. Несмотря на то, что принятие новых международных экологических норм (Европейские директивы 2000/53/EC и 2002/95/EC для автомобильной и электронной промышленности, соответственно) существенно ограничило использование соединений Cr(VI) и обусловило поиск менее токсичных составов для защиты от коррозии, доля ХПК в авиа- и космической промышленности по-прежнему достаточно высока [8]. Поэтому актуальной задачей является разработка новых эффективных и более экологически безопасных растворов пассивации алюминиевых сплавов.
Предложено достаточно большое количество способов получения и составов электролитов для формирования на поверхности сплавов алюминия конверсионных покрытий на основе соединений Cr(III) [16–18], молибдатов [19, 20], перманганатов [21] и ванадатов [22, 23], а также солей переходных (Zr, Ti, Y, Hf, Ta) и редкоземельных (Ce, Y) металлов [24–28]. Основными недостатками предложенных способов являются многостадийность процесса, комплексный состав и малый ресурс работы электролитов, что делает их внедрение в производство нерентабельным.
Перманганат-ион по своим химическим свойствам близок к хромат-ионам. Однако в отличие от последних ${\text{MnO}}_{4}^{ - }$ нетоксичен и не имеет канцерогенных свойств. Свойства марганецсодержащих конверсионных покрытий (МКП), полученных из растворов перманганата, близки к ХКП. Микроструктура сплавов алюминия оказывает значительное влияние на механизм и защитные свойства сформированных на их поверхности конверсионных покрытий [7, 29]. В ряде работ описывается получение МКП на алюминиевых сплавах AA2024 (Д16) из щелочных рабочих растворов [21, 29]. При этом, в некоторых областях применения сплавов алюминия, особенно в химической промышленности, получение покрытий из кислой среды является более целесообразным, поскольку соответствует условиям эксплуатации сплавов. Известно, что перманганат калия может быть использован в качестве растворимого ингибитора коррозии сплава АД31 в кислых средах [30, 31], однако в литературе отсутствуют сведения о получении на сплаве алюминия АД31 МКП из кислых рабочих растворов. Целью работы было изучение механизма получения и физико-химических свойств марганецсодержащих конверсионных покрытий на сплаве алюминия АД31.
МЕТОДИКА ЭКСПЕРИМЕНТА
В работе использовали образцы сплава АД31 (марка АА6063 по классификации ANSI), полученные методом горячей деформации, круглой формы диаметром 40 мм и толщиной 1 мм. Номинальный (ГОСТ 4784-97) и определенный методом рентгенофлуорисцентного анализа (анализатор X-Met 7500) составы исследуемого сплава представлены в табл. 1. Перед нанесением покрытий образцы механически шлифовали наждачной бумагой с финальным размером зерна 15 мкм, после чего промывали дистиллированной водой и высушивали. Химическая подготовка поверхности проводилась согласно ASTM D1730-09. Получение МКП осуществляли из кислых (pH 3) растворов KMnO4 с концентрацией 0.0005 и 0.005 моль дм–3 при температуре 20°С в течение 5, 60 мин и 24 ч. Для приготовления растворов использовали KMnO4 марки х. ч. (Белреахим) и дистиллированную воду. Необходимое значение pH рабочих растворов устанавливали 0.1 М раствором HNO3 c помощью автоматического титратора Schott Titroline® 5000 c точностью до ±0.01. Для осаждения покрытий использовали свежеприготовленную порцию раствора. Соотношение объема раствора к площади образца для всех опытов составляло 100 мл : : 25.2 см2. Покрытие наносили с двух сторон при вертикальном погружении в раствор. После осаждения покрытия образцы извлекали из рабочих растворов, промывали ламинарным потоком дистиллированной воды и сушили в эксикаторе в течение 24 ч.
Таблица 1.
Номинальный состав сплава АД31 (мас. %)
Элемент | Состав, мас. % | ||||||||
---|---|---|---|---|---|---|---|---|---|
Si | Fe | Cu | Mn | Мg | Cr | Zn | Тi | Al | |
ГОСТ 4784-97 | 0.45 | 0.50 | 0.10 | 0.10 | 0.60 | 0.10 | 0.20 | 0.15 | Баланс |
Рентгенофлуоресцентный анализ | 0.21 | 0.18 | 0.01 | 0.01 | 0.40 | 0.02 | 0.01 | 0.01 | 98.70 |
Морфологию и элементный состав покрытий изучали методами сканирующей электронной микроскопии (СЭМ) и энергодисперсионного рентгеновского микроанализа (EDX) с использованием микроскопа JEOL JSM-5610 LV, оснащенного системой химического микрорентгеноспектрального анализа EDX JED-2201.
Фазовый состав полученных покрытий изучали методом конфокальной спектроскопии комбинационного рассеяния (КСКР) и UV-Vis спектроскопии. Спектры КСКР снимали в диапазоне Рамановского сдвига 100‒1000 см‒1 при комнатной температуре на спектрометре JobinYvon T64000, оснащенном конфокальным микроскопом Olympus BX40 с объективом 50× (NA 0.75). В качестве источника возбуждения использовали Ar+-лазер с длиной волны 514.5 нм, мощностью ~5 мВт. Время накопления сигнала составляло 300 с, количество накоплений ‒ 2. Достоверность результатов обеспечивалась снятием спектров на трех характерных участках поверхности как минимум двух образцов. Расшифровку результатов проводили путем сравнения полученных спектров с представленными в литературе данными для соединений Mn. Электронные спектры поглощения (UV-Vis) регистрировали на спектрофотометре Carry 5000 (Agilent) в области длин волн 200‒700 нм со скоростью регистрации 1 нм/с.
Исследование коррозионной стойкости полученных покрытий электрохимическими методами осуществляли в 0.5 М растворе хлорида натрия (рН ~ 5.70) в трехэлектродной ячейке объемом 50 мл с боковым расположением рабочего электрода. В исследованиях использовали потенциостат/гальваностат PGSTAT 302N (Methrom Autolab), оснащенный модулем анализа частот FRA32M. В качестве рабочего электрода использовали сплав АД31 без и с нанесенным на него конверсионным покрытием, вспомогательный электрод – графитовый, электрод сравнения – насыщенный хлоридсеребряный. Снятие потенциодинамических поляризационных кривых осуществляли при скорости развертки потенциала 1 мВ/с в диапазоне от ‒300 до +300 мВ от установившегося в растворе стационарного потенциала. Токи коррозии рассчитывали по пересечению прямолинейных тафелевских участков катодных и анодных кривых при поляризации больше ±10 мВ. Спектры импеданса регистрировали при значениях стационарного потенциала в диапазоне частот от 10 кГц до 0.01 Гц с амплитудой переменного напряжения 10 мВ. Обработку полученных данных, подбор и расчет параметров элементов эквивалентных схем проводили с использованием программного обеспечения (ПО) Nova 2.1 и ZView 3.2. Значения потенциалов пересчитывали в шкалу стандартного водородного электрода. Все электрохимические исследования, представленные в работе, проводили не менее трех раз.
Полученные покрытия были исследованы в камере соляного тумана S120is (ASCOTT) в соответствии с методикой ASTM B117-16. Испытанию подвергали одну сторону образца, оборотную изолировали кремнийорганическим лаком КО-85. Испытания в камере соляного тумана (5% NaCl) проводили в течение 168 ч при температуре 35 ± 2°C. Каждые 24 ч образцы вынимали из камеры, промывали дистиллированной водой и фотографировали цифровой камерой Nikon D60.
Термодинамические равновесные диаграммы для соединений марганца в водных растворах строили с использованием ПО Medusa (KTH Royal Institute of Technology) на основе алгоритма SOLGASWATER. Начальные условия и параметры расчетов выбирали с учетом максимального соответствия реально используемым системам, что делало возможным применение полученных диаграмм для анализа и описания экспериментальных результатов.
РЕЗУЛЬТАТЫ И ИХ ОБСУЖДЕНИЕ
При погружении в растворы осаждения МКП образцов сплава АД31 на их поверхности формируется покрытие темного цвета, интенсивность окраски которого возрастает при увеличении времени выдержки и концентрации KMnO4. Анализ микрофотографий сформированных покрытий (рис. 2) показал, что независимо от времени получения и содержания перманганат-ионов в растворе морфология поверхности достаточно неоднородна. При получении покрытий в течение 5 и 60 мин на поверхности образцов хорошо заметны шлифовальные полосы, а МКП осаждается в виде глобул неправильной формы с размерами до ≈3 мкм. Это, вероятно, обусловлено гетерогенной структурой сплава с большим количеством интерметаллических частиц преимущественно катодного характера [2, 3], которые являются активными центрами формирования покрытия [28, 32]. При увеличении времени получения до 24 ч на поверхности формируется практически сплошное конверсионное покрытие.
Рис. 2.
Микрофотографии марганецсодержащих конверсионных покрытий, полученных из 0.5 (а–в) и 5 ммоль дм–3 (г–е) растворов KMnO4 с рН 3 в течение 5 мин (а, г), 60 мин (б, д) и 24 ч (в, е).
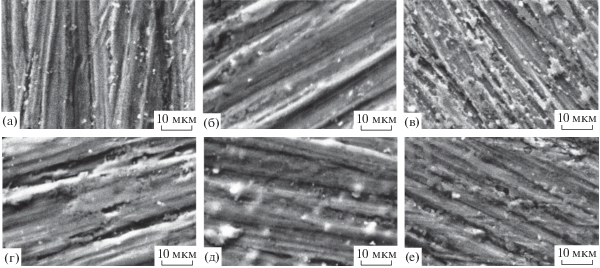
Элементный анализ поверхности методом EDX показал, что увеличение концентрации перманганат-ионов в растворе и времени формирования МКП приводят к ожидаемому росту удельного содержания Mn в покрытии (табл. 2). При увеличении времени формирования МКП от 5 мин до 24 ч на поверхности образцов размером 250 × 250 мкм содержание марганца увеличивалось от 0.24 до 5.12 мас. % и от 0.83 до 7.30 мас. % в растворах с концентрацией KMnO4 0.5 и 5.0 ммоль дм–3 соответственно.
Таблица 2.
Элементный состав поверхности сплава АД31 после получения МКП
C (KMnO4), ммоль дм–3 |
Время получения покрытия | Элементный состав, мас. % | |||||
---|---|---|---|---|---|---|---|
Al | Mg | Si | Fe | Mn | O | ||
0.5 | 5 мин | 94.76 | 0.58 | 0.40 | 0.53 | 0.24 | 3.49 |
60 мин | 91.14 | 0.41 | 0.36 | 0.47 | 2.46 | 5.16 | |
24 ч | 75.31 | 0.28 | 0.29 | 0.32 | 5.12 | 18.58 | |
5 | 5 мин | 93.80 | 0.64 | 0.35 | 0.41 | 0.83 | 3.97 |
60 мин | 86.48 | 0.58 | 0.37 | 0.36 | 3.85 | 8.36 | |
24 ч | 68.18 | 0.37 | 0.25 | 0.28 | 7.30 | 22.62 |
Железо и кремний по отношению к алюминию являются катодными легирующими добавками [2, 3, 11], и их окисления в кислых средах в исследованном интервале времени, как правило, не происходит [33]. Содержание указанных компонентов в поверхностном слое определяется количеством интерметаллических частиц на выбранном для анализа участке поверхности, а также степенью экранирования таких частиц осаждаемым МКП. Следовательно, уменьшение массового содержания железа и кремния в процессе получения покрытий (табл. 1) свидетельствует о пассивации сформированным покрытием участков, содержащих эти элементы. Установленное снижение удельного содержания магния, наоборот, можно объяснить быстрым селективным растворением в кислых средах [33]. Достаточно высокое содержание кислорода на поверхности образцов свидетельствует о том, что сформированное покрытие преимущественно состоит из оксидов и гидроксидов марганца.
Для изучения фазового состава полученных покрытий были сняты спектры КСКР, представленные на рис. 3. Как видно из представленных данных на спектрах КСКР исследуемых образцов присутствуют характерные для оксидов марганца пики (табл. 3) [34–41]. Для оксидов марганца основные полосы КР находятся в диапазоне комбинационного сдвига 500–700 см–1 (симметричные колебания связи Mn–O [29]) и частично перекрываются (табл. 3), что затрудняет идентификацию валентных форм марганца в сформированных МКП. Известно, что оксид MnO обладает структурой, аналогичной NaCl, поэтому для него комбинационное рассеивание первого порядка имеет очень малую интенсивность [36]. На спектрах КСКР, полученных с поверхности образцов сплава АД31 после их выдерживания в исследуемых растворах в течение 5 мин (рис. 3а, 3б), отсутствуют интенсивные полосы поглощения, что характерно для металлических поверхностей [30]. В данном случае, отсутствие на спектрах КСКР полос поглощения, характерных для соединений марганца, может быть объяснено малыми толщинами (≈80 нм [42]) и неоднородной глобулярной структурой покрытий. Глубина детектирования сигнала при снятии спектров КСКР составляла порядка 100 нм, размер пятна лазера – порядка 800 нм, при этом возможно наложение сигналов от металлической подложки и МКП. Высказанные предположения подтверждаются данными СЭМ и EDX-анализа, которые показали наличие на поверхности сплава МКП (рис. 2, табл. 2), а также коррозионными испытаниями полученных в этих условиях образцов.
Рис. 3.
Слева: спектры комбинационного рассеивания марганецсодержащих конверсионных покрытий, полученных из 0.5 мМ (а) и 5 мМ (б) растворов KMnO4 с рН 3 в течение 5 мин (1), 60 мин (2) и 24 ч (3). Справа: оптические микрофотографии поверхности, иллюстрирующие характерные участки снятия спектров.
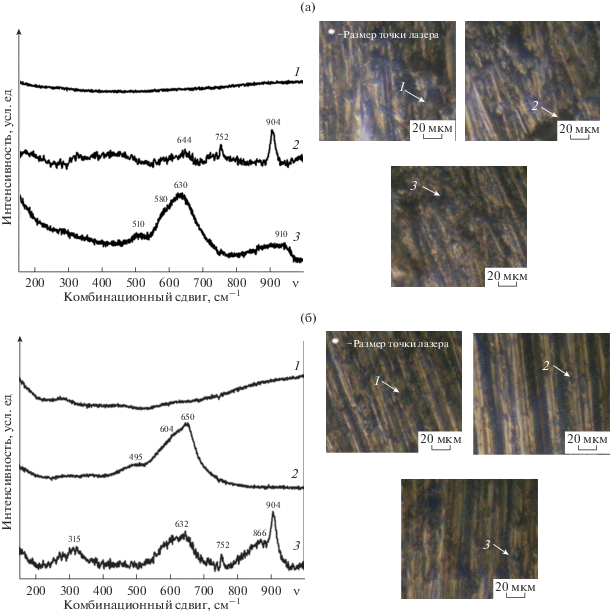
Таблица 3.
Положение основных пиков комбинационного рассеивания для соединений марганца
Соединение | Валентность Mn | Характерные позиции пиков комбинационного рассеяния, см–1* | Источники |
---|---|---|---|
MnO2 | IV | 392, 490, 523, 576, 650, 776 497, 592 510, 580, 633–640 |
[34] [37] [38] |
Mn2O3 | III | 509, 581, 630,650 192, 314, 481, 592, 645, 698 565, 620, 672 310, 360, 390, 650, 680 |
[34] [37] [40] [38] |
MnOOH | III | 358, 388, 528, 555, 620 142, 352, 384, 528, 552, 615 |
[34] [35] |
Mn3O4 | II, III | 319, 374, 659 316, 368, 654 315, 365, 651 310, 315, 370, 650 |
[41] [35] [34] [38] |
MnO | II | 647 531, 654 |
[39] [35] |
Спектры образцов, выдержанных в растворе KMnO4 в течение 60 мин и 24 ч подтверждают формирование МКП, содержащих соединения марганца(II–IV). Широкая полоса поглощения с максимумом интенсивности в области комбинационного сдвига 630–650 см‒1 включает в себя отклик нескольких валентных форм марганца в виде MnO2 (580, 630–640 см–1), Mn2O3 (630–650 см–1), Mn3O4 (650 см–1) и MnO (647 см–1) [29, 35, 38, 41]. Полоса поглощения в области 315 см–1 была определена как Mn3O4 [34, 36, 38], в области 510 см–1 – Mn2O3 [38], а полоса поглощения с максимумом комбинационного сдвига 752 см–1 соответствует β-MnO2 [35]. Ширина полос лежит в пределах от 25 до 150 см‒1.
В литературе описано существование большого числа смешанных оксидных фаз MnO2–Mn2O3–Mn3O4 [34, 37]. Присутствие таких фаз в структуре полученного покрытия, вероятно, и объясняет наблюдаемое смещение позиций максимумов комбинационного сдвига в спектрах. При этом величина и направление сдвига зависят от стехиометрического соотношения соединений марганца в различных валентных состояниях в исследуемой точке поверхности. Дополнительные пики в диапазоне 866–910 см–1 были идентифицированы как сигнал от Al2O3 [43], который может образовываться в ходе растворения матрицы сплава в кислой среде [44].
Снятие электронных спектров поглощения марганецсодержащих покрытий на сплаве АД31 проводилось для установления фазового состава и защитных свойств покрытия. Был выбран именно данный метод анализа, поскольку рентгенофазовый анализ полученных покрытий не позволил получить сигнал достаточной интенсивности для точной идентификации фаз. Полученные спектры (рис. 4) представляют собой уширенную VIS-полосу поглощения с максимумами в области 348 нм, что соответствует оксиду MnO2 [45, 46], и полосу меньшей интенсивности при 245 нм, соответствующую Mn2O3 [46]. На спектрах образцов, полученных в 0.5 мМ растворе перманганата калия в течение 5 мин, отсутствуют характерные полосы поглощения, что, вероятно, также связано с малой толщиной и неоднородностью сформированных МКП.
Рис. 4.
UV-Vis спектры абсорбции (а, в) и диаграммы Таука (б, г) марганецсодержащих конверсионных покрытий, полученных из 0.5 (а, б) и 5 ммоль дм–3 (в, г) растворов KMnO4 в течение 5 мин (1), 60 мин (2) и 24 ч (3).
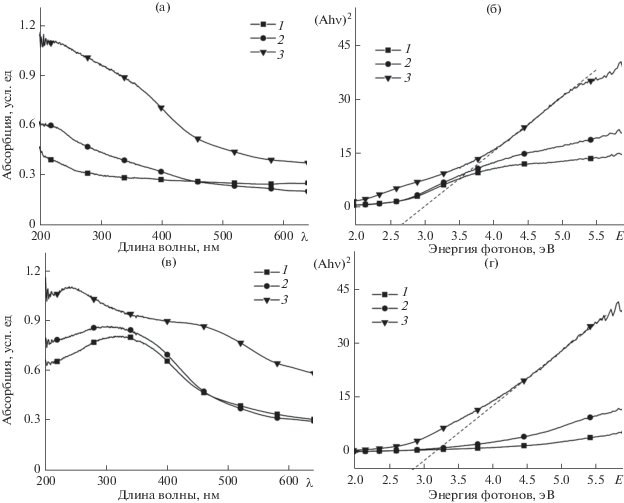
Для расчета ширины запрещенной зоны использовали функцию Кубелки–Мунка, которую можно представить в виде:
где $\alpha $ – оптический коэффициент абсорбции, R – измеренный отраженный свет, K – коэффициент абсорбции, S – коэффициент рассеяния. Абсорбционная способность материала A пропорциональна коэффициенту абсорбции, в результате чего можно построить т. н. диаграмму Таука (рис. 4б, 4г). Определение ширины запрещенной зоны проводили путем экстраполяции линейного участка кривой на диаграмме Таука до пересечения с осью x. Результаты показывают, что увеличение времени получения МКП приводит к возрастанию значений энергии электронов, что свидетельствует о большей толщине сформированного покрытия. Значения ширины запрещенной зоны составили от 0.25 эВ для покрытий, полученных в течение 5 мин, до 2.85 эВ для покрытий, полученных в течение 24 ч. Для оксидов марганца в литературе значения ширины запрещенной зоны находятся в достаточно широком интервале: ≈1.5 эВ для MnO2, 0.0–4.1 и 0.0–2.4 эВ для Mn2O3 и Mn3O4 соответственно [47, 48]. Увеличение ширины запрещенной зоны в теории коррозии свидетельствует о большей коррозионной устойчивости поверхности металла [49]. При этом защитные покрытия на основе полупроводников n-типа более подвержены питтинговой коррозии по сравнению с покрытиями р-типа [50], из-за наличия в их структуре большого числа т. н. дефектных участков, характеризующихся глубокими локализованными уровнями. Оксиды марганца, составляющие основу МКП относятся к типичным полупроводникам p-типа. Данные UV-Vis спектрофотомерии согласуются с данными, полученными методом КСКР. Таким образом, полученные результаты показывают, что формирование покрытия протекает в несколько стадий, при этом на поверхности сплава последовательно образуются оксиды марганца(II–IV).Для описания возможных валентных превращений соединений марганца и механизма формирования МКП для 5 мМ водных растворов KMnO4 построены термодинамические равновесные диаграммы, представленные на рис. 5. Для растворов, содержащих 0.5 ммоль дм–3 перманганата калия, диаграммы имели аналогичный вид (не показаны).
Рис. 5.
E-pH (а) и фазовая (б) диаграммы для соединений марганца в водном растворе, содержащем 5 ммоль дм–3 KMnO4. Фазовая диаграмма построена при стационарном потенциале –0.480 В.
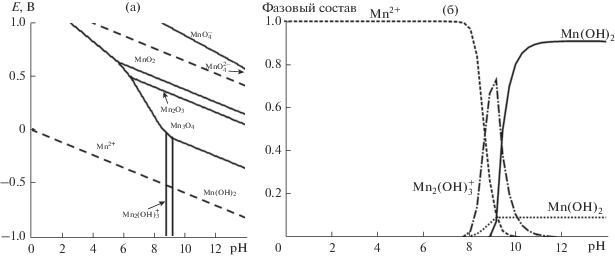
В кислых средах (рН 3) оксидная пленка на поверхности сплава алюминия неустойчива, что приводит к быстрой ионизации активных компонентов сплава по многостадийному механизму [44], который можно условно выразить реакцией:
Процесс преимущественно инициируется на участках поверхности, содержащих дефекты кристаллической решетки, и на границах раздела фаз алюминиевая матрица/интерметаллическая частица [2, 3]. При этом большинство интерметаллидов в структуре сплава АД31 имеют катодный характер [2–4], т.е. являются участками, на которых преимущественно протекают процессы восстановления. При погружении в рабочие растворы перманганата калия образцов сплава АД31, на границе раздела фаз электрод/электролит устанавливается значение стационарного потенциала –0.398 В. Согласно построенным диаграммам (рис. 5) в диапазоне рН от 0 до 8 при данном значении потенциала присутствующий в растворе ион ${\text{MnO}}_{{\text{4}}}^{ - }$ восстанавливается до иона Mn2+. Процесс протекает стадийно, при этом на первом этапе происходит восстановление Mn(VII) до Mn(IV) по реакции:
(3)
${\text{MnO}}_{{\text{4}}}^{ - } + {\text{4}}{{{\text{Н}}}^{ + }} + {\text{3}}{{е}^{ - }} \leftrightarrow {\text{Mn}}{{{\text{O}}}_{{\text{2}}}} + {\text{2}}{{{\text{H}}}_{{\text{2}}}}{\text{O}}{\text{.}}$Процесс восстановления MnO2 протекает через стадию образования оксида Mn(III), который затем переходит в смешанный оксид Mn(II, III) и восстанавливается до оксида Mn(II) [30]:
(4)
${\text{2Mn}}{{{\text{O}}}_{{\text{2}}}} + {{{\text{H}}}_{{\text{2}}}}{\text{O}} + {\text{2}}{{е}^{ - }} \leftrightarrow {\text{M}}{{{\text{n}}}_{{\text{2}}}}{{{\text{O}}}_{{\text{3}}}} + {\text{2O}}{{{\text{H}}}^{ - }},$(5)
${\text{3M}}{{{\text{n}}}_{{\text{2}}}}{{{\text{O}}}_{{\text{3}}}} + {{{\text{H}}}_{{\text{2}}}}{\text{O}} + {\text{2}}{{е}^{ - }} \leftrightarrow {\text{2M}}{{{\text{n}}}_{{\text{3}}}}{{{\text{O}}}_{{\text{4}}}} + {\text{2O}}{{{\text{H}}}^{ - }},$(6)
${\text{M}}{{{\text{n}}}_{{\text{3}}}}{{{\text{O}}}_{{\text{4}}}} + 2{{{\text{Н}}}^{ + }} + {\text{2}}{{е}^{ - }} \leftrightarrow {\text{3MnO + }}{{{\text{H}}}_{{\text{2}}}}{\text{O }}{\text{.}}$В кислых средах полученный оксид MnO может растворяться с образованием ионов Mn2+. Однако процессы (3)–(6) приводят к локальному увеличению значений рН в приэлектродной области у катодных участков поверхности сплава, что, в свою очередь, делает возможным формирование на поверхности устойчивых нерастворимых оксидно-гидроксидных пленок соединений марганца.
Результаты КСКР и UV–Vis спектроскопии показывают, что в процессе формирования покрытия присутствует вторая стадия, которая заключается в окислении сформированного по реакциям (3)–(6) оксида MnO до соединений марганца(III, IV), что сопровождается катодным процессом восстановления кислорода:
(7)
$\begin{gathered} n{\text{MnO}} + {{{\text{H}}}_{2}}{\text{O }} - 2{{e}^{ - }} \to {\text{M}}{{{\text{n}}}_{n}}{{{\text{O}}}_{{n + 1}}} + 2{{{\text{H}}}^{{\text{ + }}}} \\ (n = 1{\text{,2,3}}), \\ \end{gathered} $(8)
${{{\text{O}}}_{2}} + 2{{{\text{H}}}_{2}}{\text{O}} + 4{{e}^{ - }} \to 4{\text{O}}{{{\text{H}}}^{ - }}.$Также возможно протекание процессов репропорционирования при взаимодействии MnO с MnO2 или ${\text{MnO}}_{4}^{ - }$ с образованием фаз смешанного состава, содержащих оксиды марганца(II–IV), существование которых в структуре сформированных МКП было установлено методами КСКР и UV–Vis (рис. 3, 4).
Поляризационные исследования (рис. 6, табл. 4) показали, что в 0.5 М растворе NaCl для образцов без покрытия на границе раздела фаз электрод/электролит устанавливается значение стационарного потенциала –0.480 В. Для образцов с МПК стационарный потенциал в основном смещается в область положительных значений. При увеличении до 60 мин времени формирования покрытия в 0.5 мМ растворе KMnO4 значение Екор увеличивается, а для образцов, полученных в 5 мМ растворе KMnO4, – снижается. Для покрытий, полученных в течение 24 ч, независимо от содержания в растворе перманганата калия значение стационарного потенциала в 0.5 М NaCl составляло –0.470 В.
Рис. 6.
Потенциодинамические поляризационные кривые образцов сплава АД31 со сформированным конверсионным покрытием (1–3) и без покрытия (4) в 0.5 М растворах NaCl. Концентрация KMnO4, ммоль дм–3: (а) 0.5; (б) 5. Время получения покрытий: 1 – 5 мин, 2 – 60 мин, 3 – 24 ч.
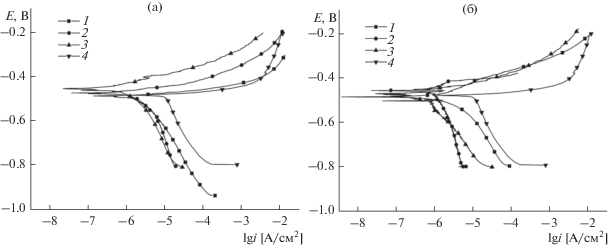
Таблица 4.
Электрохимические параметры, полученные из анализа поляризационных кривых образцов сплава АД31 с МКП в 0.5 М растворе NaCl
C (KMnO4), ммоль дм–3 |
Время получения покрытия | |bк|, В | aк, В | bа, В | aa, В | iкор, мкА см–2 | Eкор, В |
---|---|---|---|---|---|---|---|
Без покрытия | 0.3575 | –2.2707 | 0.0126 | –0.413 | 9.56 | –0.480 | |
0.5 | 5 мин | 0.1214 | –1.1978 | 0.0103 | –0.419 | 1.21 | –0.483 |
60 мин | 0.0560 | –0.8132 | 0.0428 | –0.169 | 0.30 | –0.450 | |
24 ч | 0.0225 | –0.6202 | 0.0190 | –0.346 | 0.25 | –0.470 | |
5 | 5 мин | 0.0756 | –0.9377 | 0.0489 | –0.148 | 0.45 | –0.458 |
60 мин | 0.0242 | –0.6485 | 0.0113 | –0.407 | 0.16 | –0.486 | |
24 ч | 0.0154 | –0.5919 | 0.0165 | –0.354 | 0.03 | –0.470 |
Наличие на поверхности сплава алюминия марганецсодержащих пленок приводит к существенному изменению кинетики парциальных электрохимических реакций. Как анодная, так и катодная поляризация образцов приводят к увеличению поляризуемости обоих электродных процессов, что позволяет утверждать, что входящие в состав МПК соединения являются ингибиторами смешанного типа и тормозят как анодную, так и катодную реакцию. Анализ хода поляризационных кривых показывает, что увеличение времени формирования МКП в 0.5 мМ растворе KMnO4 в меньшей степени влияет на ход катодных поляризационных кривых, но существенно увеличивает поляризуемость анодного процесса. Для покрытий, полученных в 5 мМ растворе KMnO4, зависимость обратная: ход анодных поляризационных кривых мало зависит от времени формирования МКП, но при этом значительно увеличивается поляризуемость катодного парциального процесса. Это позволяет высказать предположение, что торможение коррозионного процесса в первом случае в большей степени обусловлено снижением скорости анодного растворения металла, а во втором – ассимиляции электронов деполяризатором.
Рассчитанные значения основных электрохимических параметров коррозионных процессов, протекающих для исследуемых образцов в растворе хлорида натрия, представлены в табл. 4. Анализ полученных данных показывает, что МКП, сформированные в 0.5 мМ KMnO4, снижают плотность тока коррозии в ≈8, 31 и 38 раз, а в 5 мМ KMnO4 – в ≈21, 60 и 319 раз при времени получения покрытий 5, 60 мин и 24 ч соответственно.
Результаты электрохимической импедансной спектроскопии исследованных образцов в 0.5 М растворе NaCl в виде диаграмм Найквиста представлены на рис. 7. На спектрах образцов с МКП, сформированным в течение 5 мин из растворов перманганата калия с концентрацией 0.5 и 5.0 ммоль дм–3, можно выделить две временные константы: емкостную полуокружность в диапазоне высоких и средних частот и индукционную область в диапазоне низких частот. Наличие индукционной области на диаграммах Найквиста свидетельствует о процессе ионизации активных компонентов сплава в хлоридсодержащей среде [3, 33]. На спектре образца сравнения без конверсионного покрытия также присутствовала индукционная область. В этом случае, сравнение диаметров полуокружностей спектров показало, что в отличие от образца без покрытия образцы с МКП имеют более высокие значения модуля импеданса |Z|, что свидетельствует о большей коррозионной устойчивости. Тем не менее, такие покрытия не обеспечивают достаточный защитный эффект.
Рис. 7.
Спектры импеданса образцов сплава АД31 с марганецсодержащим конверсионным покрытием в виде диаграмм Найквиста в 0.5 М растворах NaCl (а, б) и эквивалентные схемы, использовавшиеся для интерпретации спектров импеданса (в). Символами обозначены экспериментальные данные, линиями – результаты подбора параметров эквивалентных схем.
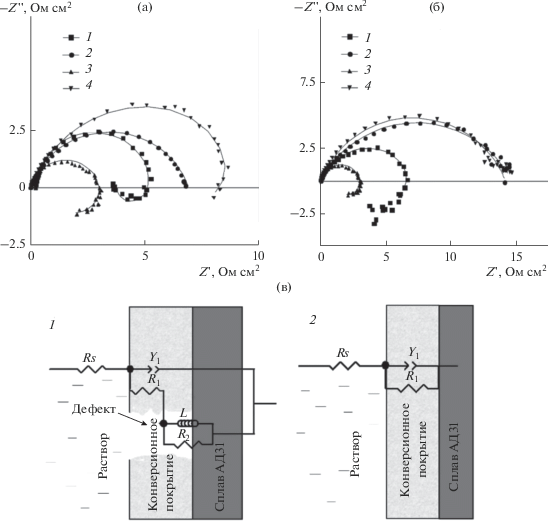
На диаграммах Найквиста для образцов с покрытиями, сформированными в течение 60 мин и 24 ч, индукционная область отсутствует. На спектре можно выделить только одну емкостную константу времени, что говорит о пассивации поверхности сформированным МКП и хорошо согласуется с данными поляризационных исследований (рис. 6). Необходимо отметить, что диаметр полуокружностей на диаграммах Найквиста возрастал при увеличении времени формирования МКП и во всех случаях был больше на спектрах образцов, выдержанных в растворах с концентрацией перманганата калия 5 ммоль дм–3, что свидетельствует о большей коррозионной стойкости покрытий, сформированных в данных условиях.
Для количественного описания полученных спектров импеданса использовали эквивалентные схемы, представленные на рис. 7в. Схема 1 описывает спектры с двумя, а схема 2 – спектры с одной временной константой. В предложенных схемах вместо элемента конденсатора С использовался элемент постоянной фазы CPE, который применяется для описания систем со значительной микрошероховатостью поверхности и учитывает их неидеальный емкостной отклик [3, 11, 33]. Импеданс элемента постоянной фазы может быть выражен формулой:
где ${{Y}_{0}}$ – константа элемента постоянной фазы, n – математический фактор. Значение фактора n (0 ≤ n ≤ 1) определяет степень гетерогенности поверхности металла и/или сформированного конверсионного покрытия. В случае n = 0 константа ${{Y}_{0}}$ описывает идеальный резистор, при n ≈ 0.5 – диффузионный элемент Варбурга, а при n = 1 – идеальный конденсатор. В предложенных схемах Rs соответствует сопротивлению растворов, Y1 и R1 – соответственно емкости двойного электрического слоя и поляризационному сопротивлению, а L и R2 – параметрам индукционного процесса. Результаты подбора параметров эквивалентных схем представлены в табл. 5. Поскольку для описания спектров импеданса использовались различные эквивалентные схемы, прямое сравнение их параметров не всегда корректно. Для расчета общего сопротивления в схеме с двумя временными константами предполагали, что общее сопротивление в схеме 1 можно рассчитать как алгебраическую сумму R1 и R2. Анализ полученных данных показал, что формирование на поверхности сплава МКП позволяет увеличить общее сопротивление поверхности в ≈6, 8 и 13 раз (0.5 ммоль дм–3 KMnO4) и ≈9, 17 и 17.5 раз (0.5 ммоль дм–3 KMnO4) при времени получения покрытий соответственно 5 мин, 60 мин и 24 ч.Таблица 5.
Параметры эквивалентных схем спектров импеданса для сплава АД31 с МКП в исследуемых растворах
Время получения покрытия | Rs (Ом cм2) | R1 (Ом cм2) | Y1 (Ом–1 cм–2 сn) | n1 | R2 (Ом cм2) | L (Гн cм–2) |
---|---|---|---|---|---|---|
Без покрытия | ||||||
– | 2.7 | 835 | 6.93 × 10–5 | 0.87 | 2177 | 8689 |
0.5 ммоль дм–3 KMnO4 | ||||||
5 мин | 3.2 | 3553 | 1.02 × 10–6 | 0.97 | 1573 | 1195 |
60 мин | 2.5 | 6923 | 1.76 × 10–6 | 0.79 | – | – |
24 ч | 2.6 | 7049 | 1.42 × 10–6 | 0.77 | 3641 | 1428 |
5 ммоль дм–3 KMnO4 | ||||||
5 мин | 3.5 | 3854 | 9.84 × 10–6 | 0.81 | 3547 | 2377 |
60 мин | 2.9 | 14 083 | 9.03 × 10–6 | 0.70 | – | – |
24 ч | 2.6 | 14 610 | 1.83 × 10–6 | 0.77 | – | – |
На рис. 8 представлены микрофотографии поверхности образцов сплава АД31 без и с нанесенным конверсионным покрытием после испытаний в камере соляного тумана. Для образца сравнения без покрытия уже через 24 ч испытаний на поверхности заметны значительные очаги коррозии; через 168 ч – неоднородность поверхности существенно увеличилась, на ней наблюдается большое количество продуктов коррозии белого цвета. Образцы с МКП показали высокую коррозионную стойкость в хлоридсодержащей среде. После 168 ч испытаний структура их поверхности практически не изменилась, на отдельных образцах наблюдались очаги питтинговой коррозии, что связано с описанной выше неоднородностью структуры МКП. В ходе испытаний интенсивность окраски МКП несколько снизилась.
Рис. 8.
Микрофотографии поверхности образцов сплава АД31 после испытаний в камере соляного тумана в течение 168 ч.
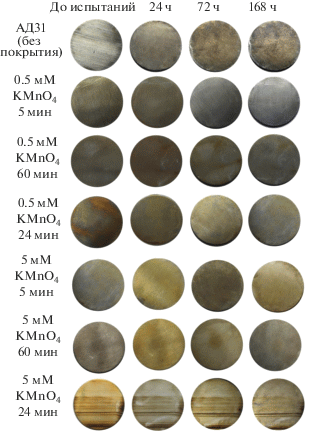
Таким образом, анализ данных, полученных различными методами, показал, что марганецсодержащее конверсионное покрытие, полученное химическим путем на поверхности сплава АД31, значительно снижает скорость коррозии сплава в нейтральных хлоридсодержащих средах и может быть использовано в многокомпонентных системах защиты от коррозии исследуемого сплава алюминия.
ВЫВОДЫ
1. Процесс формирования МКП на сплаве алюминия АД31 в кислых (рН 3) растворах перманганата калия преимущественно инициируется на участках поверхности, содержащих дефекты кристаллической решетки, и на границах раздела фаз алюминиевая матрица/катодная интерметаллическая частица. На начальном этапе на поверхности образца наблюдается образование МКП в виде глобул неправильной формы с размерами до ≈3 мкм. Во всех исследуемых растворах сплошные конверсионные пленки формируются в течение 24 часов.
2. Данные EDX-анализа, Uv-Vis спектрофотометрии, полученные спектры комбинационного рассеяния, а также анализ построенных термодинамических равновесных диаграмм для соединений марганца в водном растворе (5 ммоль дм–3 KMnO4) показали, что в кислых растворах перманганата калия процесс формирования МКП на поверхности сплава АД31 протекает в несколько стадий. На первом этапе при погружении в рабочие растворы образцов сплава происходит восстановление Mn(VII) до Mn(IV). Затем полученный MnO2 через стадии образования оксида Mn(III) и смешанного оксида Mn(II, III) постепенно восстанавливается до оксида Mn(II). На втором этапе полученный оксид MnO частично окисляется до соединений марганца(III, IV), что сопровождается катодным процессом восстановления кислорода и приводит к формированию фаз смешанного состава, содержащих оксиды марганца(II–IV).
3. Поляризационные исследования полученных образцов в 0.5 М растворе NaCl показали, что входящие в состав МКП соединения являются ингибиторами смешанного типа и тормозят как анодную, так и катодную реакцию. Для покрытий, сформированных в 0.5 мМ растворе KMnO4, торможение коррозионного процесса в большей степени обусловлено снижением скорости анодного растворения металла, а для покрытий, сформированных в 5 мМ растворе KMnO4 – ассимиляции электронов деполяризатором. МКП снижают ток коррозии в ≈8, 31 и 38 раз (0.5 ммоль дм–3 KMnO4) и в ≈ 21, 60 и 319 раз (0.5 ммоль дм–3 KMnO4) при времени получения покрытий в течение 5, 60 мин и 24 ч соответственно.
4. Результаты электрохимической импедансной спектроскопии исследованных образцов в 0.5 М растворе NaCl показали, что формирование на поверхности сплава МКП позволяет увеличить общее сопротивление поверхности в ≈6, 8 и 13 раз (0.5 ммоль дм–3 KMnO4) и в ≈9, 17 и 17.5 раз (0.5 ммоль дм–3 KMnO4) при времени получения покрытий соответственно 5, 60 мин и 24 ч. Наиболее высокой коррозионной стойкостью обладает МКП, полученное в растворах с концентрацией перманганата калия 5 ммоль дм–3 в течение 24 ч.
5. Испытания в камере соляного тумана показали, что для образца сравнения без покрытия уже через 24 ч испытаний на поверхности заметны значительные очаги коррозии. В то же время, структура поверхности образцов с МКП, подвергшихся испытаниям в течение 168 ч, практически не изменилась.
Список литературы
Birbilis N., Buchheit R.G. // J. Electrochem. Soc. 2005. V. 152. P. B140–B151.
Kharitonov D.S., Dobryden I.B., Sefer B. et al. // Prot. Met. Phys. Chem. Surf. 2018. V. 54. P. 291–300. (Харитонов Д.С., Добрыдень И.Б., Сефер Б. и др. // Физикохимия поверхности и защита материалов. 2018. Т. 54. С. 183–193.)
Kharitonov D.S., Ornek C., Claesson P.M. et al. // J. Electrochem. Soc. 2018. V. 165. P. C116–C126.
Zhang F., Nilsson J.-O., Pan J. // J. Electrochem. Soc. 2016. V. 163. P. C609–C618.
Kazemi M., Danaee I., Zaarei D. // Mat.-Wiss. u. Werkstofftech. 2014. P. 574–581.
Scamans G.M., Birbilis N., Buchheit R.G. Shreir’s Corrosion. Corrosion of aluminum and its alloys. Amsterdam: Elsiever, 2010. 1973 p.
Yasakau K.A., Tedim J., Zheludkevich M.L., Ferreira M.G.S. Handbook of Smart Coatings for Materials Protection: Smart coatings for corrosion protection: an overview. Cambridge: Woodhead Publishing, 2014. P. 224–274.
Pokorny P., Tej P., Szelag P. // Metalurgija. 2016. V. 55. P. 253–256.
Ates M. // J. Adhes. Sci. Technol. 2016. V. 30. P. 1510–1536.
Twite R.L., Bierwagen G.P. // Prog. Org. Coatings. 1998. V. 33. P. 91–100.
Kharitonov D.S., Kurilo I.I., Wrzesinska A., Zharskii I.M. // Mat.-Wiss. u. Werkstofftech. 2017. V. 48. P. 646–660.
Zhao J., Xia L., Sehgal A. et al. // Surf. Coatings Technol. 2001. V. 140. P. 51–57.
Xia L., Akiyama E., Frankel G., McCreery R. // J. Electrochem. Soc. 2000. V. 147. P. 2556.
Buchheit R.G., Mamidipally S.B., Schmutz P., Guan H. // Corrosion. 2002. V. 58. P. 3–14.
U.S. Department of Health and Human Services. Toxicological profile for chromium. Atlanta, 2012. 592 p.
Qi J., Hashimoto T., Thompson G.E., Carr J. // J. Electrochem. Soc. 2016. V. 163. P. C131–C138.
Shruthi T.K., Swain G.M. // J. Electrochem. Soc. 2018. V. 165. P. C103–C105.
Li L., Kim D.Y., Swain G.M. // J. Electrochem. Soc. 2012. V. 159. P. C326–C333.
Liang C.S., Lv Z.F., Zhu Y.L. et al. // Appl. Surf. Sci. 2014. V. 288. P. 497–502.
Yao Y., Zhou Y., Zhao C. et al. // J. Electrochem. Soc. 2013. V. 160. P. C185–C188.
Kulinich S.A., Akhtar A.S., Wong P.C. et al. // Thin Solid Films. 2007. V. 515. P. 8386–8392.
Zou Z., Li N., Li D. et al. // J. Alloys Compd. Elsevier B.V., 2011. V. 509. P. 503–507.
Guan H., Buchheit R.G. // Corrosion. 2004. V. 60. P. 284–296.
Milošev I., Frankel G.S. // J. Electrochem. Soc. 2018. V. 165. P. C127–C144.
Li L., Whitman B.W., Munson C.A. et al. // J. Electrochem. Soc. 2016. V. 163. P. C718–C728.
Li L., Whitman B.W., Swain G.M. // J. Electrochem. Soc. 2015. V. 162. P. C279–C284.
Hughes A.E., Harvey T.G., Birbilis N. et al. // Rare Earth-Based Corrosion Inhibitors: Coatings for corrosion prevention based on rare earths. Cambridge: Woodhead Publishing, 2014. P. 186–232.
Harvey T.G. // Corros. Eng. Sci. Technol. 2013. V. 48. P. 248–269.
Yoganandan G., Balaraju J.N., William Grips V.K. // Appl. Surf. Sci. 2012. V. 258. P. 8880–8888.
Madden S.B., Scully J.R. // J. Electrochem. Soc. 2014. V. 161. P. C162–C175.
Осипенко М.А., Янушевский В.И., Харитонов Д.С. и др. // Вестник технологического университета. 2017. Т. 20. С. 5–9.
Lopez-Garrity O., Frankel G.S. // J. Electrochem. Soc. 2013. V. 161. P. C95–C106.
Prabhu D., Rao P. // Arabian. J. Chem. 2017. V. 10. P. S2234–S2244.
Bernard M., Goff A.H., Thi B.V. et al. // J. Electrochem. Soc. 1993. V. 140. P. 3065–3070.
Julien C.M., Massot M., Poinsignon C. // Spectrochim. Acta – Part A Mol. Biomol. Spectrosc. 2004. V. 60. P. 689–700.
Mironova-Ulmane N., Kuzmin A., Grube M. // J. Alloys Compd. 2009. V. 480. P. 97–99.
Julien C., Massot M., Baddour-Hadjean R. et al. // Solid State Ionics. 2003. V. 159. P. 345–356.
Buciuman F., Patcas F., Craciun R., Zahn D.R.T. // Phys. Chem. Chem. Phys. 1999. V. 1. P. 185–190.
Gu X., Yue J., Chen L. et al. // J. Mater. Chem. A. 2015. V. 3. P. 1037–1041.
White W.B., Keramidas V.G. // Spectrochim. Acta - Part A Mol. Biomol. Spectrosc. 1971. V. 28. P. 501–509.
Strohmeier B.R., Hercules D.M. // J. Phys. Chem. 1984. V. 88. P. 4922–4929.
Hughes A.E., Gorman J.D., Harvey T.G. et al. // Corrosion. 2006. V. 62. P. 773–780.
Li J., Hurley B., Buchheit R. // J. Electrochem. Soc. 2015. V. 162. P. C219–C227.
Kharitonov D.S., Kurilo I.I., Zharskii I.M. // Russ. J. Appl. Chem. 2017. V. 90. P. 1089–1097. (Харитонов Д.С., Курило И.И., Жарский И.М. // Журн. прикладной химии. 2017. Т. 90. С. 877–885.)
Jaganyi D., Altaf M., Wekesa I. // Appl. Nanosci. 2013. V. 3. P. 329–333.
Butterfield C.N., Soldatova A.V., Lee S.-W. et al. // Proc. Natl. Acad. Sci. 2013. V. 110. P. 11731–11735.
Li T., Wu J., Xiao X. et al. // RSC Adv. 2016. V. 6. P. 13914–13919.
Jin Q., Arimoto H., Fujishima M., Tada H. // Catalysts. 2013. V. 3. P. 444–454.
Guo L.Q., Qin S.X., Yang B.J. et al. // Sci. Rep. 2017. V. 7. P. 8–13.
Craig B.D. Fundamental Aspects of Corrosion Films in Corrosion Science. New York: Springer, 1990. 200 p.
Дополнительные материалы отсутствуют.
Инструменты
Физикохимия поверхности и защита материалов