Физикохимия поверхности и защита материалов, 2020, T. 56, № 3, стр. 330-336
Комплексная оценка состояния поверхностного слоя нержавеющей аустенитной стали после абразивного воздействия
А. П. Митрофанов 1, *, К. А. Паршева 1
1 Волжский политехнический институт (филиал) ФГБОУ ВО “Волгоградский государственный университет”
404121 Волжский, ул. Энгельса, 42а, Россия
* E-mail: vto@vpi.ru
Поступила в редакцию 02.04.2018
После доработки 03.10.2018
Принята к публикации 10.10.2018
Аннотация
Исследовано влияние различных способов абразивного воздействия (шлифование стандартным и импрегнированным абразивным инструментом) на поверхностный слой нержавеющей аустенитной стали 12Х18Н10T, в том числе проведен анализ взаимосвязи измеренных свойств полученных с помощью методов прямого индентирования, зонда Кельвина, микрорентгеноспектрального анализа и растровой микроскопии. Результаты исследования показывают наличие взаимосвязи полученных значений работы выхода электрона исследуемых поверхностей с измеренным модулем упругости и коррозионной стойкостью образцов после абразивного воздействия. Наблюдается значительное изменение свойств тонкого поверхностного слоя после шлифования импрегнированным абразивным инструментом.
ВВЕДЕНИЕ
В настоящее время тематика исследований по влиянию механической, и в том числе абразивной обработки на поверхностный слой нержавеющих аустенитных сталей с анализом их дальнейших эксплуатационных свойств довольно актуальна и востребована [1–4].
Специфика абразивной обработки нержавеющих сталей аустенитного класса, вязких и труднообрабатываемых материалов, связана с процессом высокой пластической деформации, которая сопровождается циклическим адгезионным схватыванием с разрушением поверхности и общим напряженно-силовым характером обработки [5].
Для устранения проявления данных факторов, на практике при абразивной обработке применяют специальную внешнюю среду, обеспечивая ее доставку непосредственно в зону контактного взаимодействия. Одним из способов внесения в зону резания активной внешней среды зарекомендовавшим себя для повышения эффективности процесса шлифования, как в России, так и за рубежом является импрегнирование абразивного инструмента. В процессе шлифования импрегнированным абразивным инструментом изменяются условия контактного взаимодействия, что оказывает влияние на физико-механические процессы.
В зоне контактного взаимодействия происходит упрочнение или разупрочнение поверхностного слоя, формируются остаточные напряжения (в большинстве случаев растяжения) [3, 6], наблюдается измельчение зерна в приповерхностной зоне [7] вплоть до формирования наноструктурного состояния [1, 3, 8].
Особенности микроструктуры материала и физико-механическое состояние поверхности оказывают значимое влияние на износостойкость и другие свойства поверхностей, в том числе и на коррозионную стойкость [9]. Исследование микроструктуры в рамках анализа кристаллической ориентации и размеров зерен позволит дать оценку о природе полученных механических свойств поверхности.
Одним из фундаментальных параметров энергетического состояния поверхностного слоя является работа выхода электрона (РВЭ), которая определяется разницей между минимальной энергией, необходимой для перемещения электрона из объема твердого тела, и энергией Ферми.
Знание действительной величины РВЭ дает возможность с большой точностью определить поверхностную энергию металлов и других твердых тел, и таким образом, проследить за изменением состояния их поверхностных слоев, а, значит, выявить зарождение и развитие в нем дефектов.
Многочисленные исследования показали, что функция РВЭ неразрывно связана со многими механическими свойствами металлов [10–12]. Например, модуль упругости чистых металлов коррелирует с функцией работы выхода [11]. Как следствие, функция РВЭ может быть использована для определения начала пластической деформации, и таким образом, точки бифуркации. В работе [13] Y. Zhou, J.Q. Lu c соавторами экспериментально доказано влияние деформации на РВЭ: упругие деформации вызывают рост РВЭ, а в области пластического деформирования работа выхода уменьшается. Кроме того, функция работы отражает адгезию поверхности, и следовательно, влияние на трение и трибологические процессы и др. [14].
Экспериментальные наблюдения и теоретические исследования показывают, что функция РВЭ также тесно связана с потенциалом коррозии и может, таким образом, быть чувствительным параметром для исследования коррозионного поведения металлов [15–18].
Следовательно, функция РВЭ может быть использована для прогнозирования и оценки механических свойств металлов и их коррозионной стойкости. Кроме того, знание общей РВЭ дает дополнительную информацию о поверхностных слоях материалов, что позволит управлять адаптацией материалов и их свойств.
Ввиду того, что в процессе абразивной обработки наиболее активное воздействие на себе испытывают тончайшие приповерхностные слои, соответственно именно в них происходит градиентное изменение свойств. Для проведения исследований механических свойств поверхности предлагается использовать известный в научном сообществе метод инструментального индентирования [19, 20]. Используя данный метод, можно определить значения твердости и модуля Юнга, в том числе в нано метровых слоях, что позволит получить более объективную информацию о процессах происходящих именно на поверхности.
В результате экстремального взаимодействия наблюдаемого в зоне резания, происходят также и химические превращения в обрабатываемом металле. Без анализа этих процессов невозможно составить полное представление о механизме трансформации свойств поверхностного слоя. С этой целью необходимо провести элементный анализ поверхностного слоя, в том числе исследовать распределение химических элементов по глубине поверхности.
Совокупность полученных результатов по предлагаемым для исследования параметрам, позволит дать более глубокую оценку свойствам поверхностного слоя нержавеющей аустенитной стали, появившимся в результате абразивного воздействия, в том числе после применения импрегнированного абразивного инструмента. При этом анализ взаимосвязей между исследуемыми свойствами поверхностного слоя представляет научный и практический интерес.
МЕТОДИКА ИССЛЕДОВАНИЙ
Поверхности для дальнейшего проведения комплекса исследований получали с использованием экспериментального стенда на базе плоскошлифовального станка методом врезания. В качестве исследуемого материала выбрана аустенитная нержавеющая сталь марки 12Х18Н10Т (аналог AISI 321) со следующим химическим составом: 0.10 мас. % С; 0.9 Mn; 18.7 Cr; 9.10 Ni; 0.55 Si; 0.6 Ti; 0.2 Mo; 0.05 P; 0.02 S. Из толстолистовой стали были подготовлены образцы размером 30 × × 12 × 10 мм с исходной твердостью 180 НВ. Характеристика применяемого абразивного инструмента – 24АF60K7V5. Режимы обработки: скорость круга – 30 м/с; продольная подача стола – 12 м/мин; подача на глубину t – 0.01 мм за каждый проход; величина съема материала – 0.8 мм. Обработку осуществляли с охлаждением, методом полива водным раствором кальцинированной соды (0.3%). Исследуемая поверхность получена двумя способами: после шлифования стандартным абразивным инструментом и импрегнированным абразивным инструментом. Методика импрегнирования и химический состав разработанных импрегнаторов подробно представлены в работе [5].
Исследование морфологии поверхностей обработанных образцов проведены с использованием двухлучевого электронного растрового микроскопа Versa 3D LoVac при ускоряющем напряжении U = 15 кВ. С целью оценки изменений в приповерхностном слое формировали поперечный срез ионным травлением, для чего с помощью газоинжекционной системы наносится слой платины, необходимый для защиты поверхности от воздействия ионного пучка. Далее проводится травление сфокусированным пучком ионов Ga+ на черновых и чистовых режимах. Затем, применяя сфокусированный ионный пучок, получали изображение поверхности с информацией о кристаллической ориентации и структуре зерна металла. Используя интегрированную систему микрорентгеноспектрального энергодисперсионного анализа EDAX Apollo X, определяли элементный состав поверхностного слоя с высокой степенью локализации.
Измерение контактной разности потенциалов осуществляли на атомно-силовом микроскопе “ИНТЕГРА Прима” (производства NT–MDT) методом Зонда Кельвина. Измеряемой величиной для зонда Кельвина является контактная разность потенциала, определяемая разностью значений работы выхода электрона поверхностей образца и зонда и зависящая от целого ряда факторов физико-химического состояния поверхности: отклонений химического состава, механических напряжений и пр. Применяемый метод основывается на двухпроходной методике. В первом проходе определяется рельеф поверхности образца с использованием прерывисто-контактного метода (колебания кантилевера возбуждаются механически). На втором проходе этот рельеф отслеживается при прохождении над образцом на некоторой высоте для определения поверхностного электрического потенциала φ(x). Для проведения исследований использовали токопроводящий кантилевер (CSG10/Au) с покрытием из золота с резонансной частотой колебаний 30 кГц. Известно выражение вида (1) [16], которое связывает РВЭ исследуемого образца, через значение контактной разности потенциалов измеренное методом зонда Кельвина:
где φ – значение КРП, W1 – РВЭ образца, W2 – РВЭ материала зонда, e – заряд электрона.С учетом того, что РВЭ зонда W2 при измерениях является величиной постоянной, пространственное распределение контактной разности потенциалов φ по поверхности образца имеет аналогичную тенденцию распределения значений РВЭ поверхности образца W1, отражающему неоднородность физико-химических свойств поверхности и распределение ее дефектов. Таким образом, мы будем иметь некоторую оценочную величину изменения электрических свойств поверхности, которую обозначим через РВЭ*.
Твердость и модуль упругости поверхностного слоя замеряли на сканирующем нанотвердомере “НаноСкаН-4D” (производства ФГБНУ “ТИСНУМ”) методом инструментального индентирования в соответствии с ГОСТ Р 8.748-2011 (ISO 14577-1:2002). Исследования проводили с применением в качестве индентора алмазной пирамиды Берковича при усилии нагрузки Р равным 10 и 1000 мН с 30-кратным повторением в случайном порядке.
Стойкость поверхности к питтинговой коррозии определяли погружением образцов в 20% водный раствор хлористого железа (FeCl2 ⋅ 2H2O), при комнатной температуре с продолжительностью в 100 ч. Далее проводили визуальное оценивание полученных результатов с помощью стереомикроскопа Альтами СМ0870-Т.
Перед проведением всех перечисленных исследований для удаления загрязнений с поверхности, образцы очищали в этаноле с использованием ультразвуковой ванны (мощность 50 Вт, продолжительность 3 мин).
РЕЗУЛЬТАТЫ ИССЛЕДОВАНИЙ
При визуальной оценке состояния поверхностного слоя после шлифования стандартным абразивным инструментом (рис. 1а), можно наблюдать значительную неоднородность рельефа, дефектную структуру и следы адгезионного схватывания. Поверхность, полученная после шлифования импрегнированным абразивным инструментом, более однородна и сглажена (рис. 1б), хотя и на ней также присутствуют видимые участки адгезионного схватывания.
Рис. 1.
СЭМ фотографии поверхности образцов после шлифования стандартным абразивным инструментом (а) и импрегнированным абразивным инструментом (б) при увеличении 30000×.
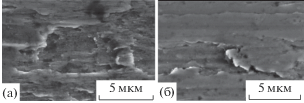
При измерении твердости и модуля упругости у исследуемых образцов обнаружена существенная разница в значениях (табл. 1). Так, в тонких поверхностных слоях при глубине внедрения индентора 0.3–0.4 мкм среднее значение твердости практически на 1 ГПа выше у поверхности полученной после шлифования импрегнированным абразивным инструментом. Тем не менее, при этом наблюдается значительный разброс в значениях на обоих образцах, что подтверждает структурную неоднородность морфологии поверхности наблюдаемую при электронно-микроскопических исследованиях. При увеличении величины нагрузки на индентор до значений 1000 мН, можно отметить обратный эффект, поверхность обработанная стандартным абразивным инструментом обладает более высокими значениями твердости, тогда как твердость поверхности после шлифования импрегнированным абразивным инструментом приближается к исходным значениям у данной стали (2 ГПа). Относительно высокие усилия нагрузки обеспечивают проникновения индентора на глубину от 3 до 5 мкм и значительную контактную площадь, в результате чего усредняется влияние исходного состояния поверхности, что уменьшает диапазон варьирования полученных значений.
Таблица 1.
Механические характеристики поверхностного слоя после операций шлифования стандартным абразивным инструментом и шлифования импрегнированным абразивным инструментом при разных усилиях нагрузки в процессе индентирования
Параметр | Шлифование стандартным абразивным инструментом | Шлифование импрегнированным абразивным инструментом | ||
---|---|---|---|---|
нагрузка при индентировании, мH | ||||
10 | 1000 | 10 | 1000 | |
HIТ, ГПа | 3.9 ± 1.2 | 2.87 ± 0.3 | 4.87 ± 0.9 | 2.2 ± 0.4 |
EIТ, ГПа | 214 ± 24 | 257 ± 28 | 147 ± 27 | 131 ± 10 |
Следует особо отметить то обстоятельство, что у поверхности после шлифования импрегнированным абразивным инструментом значительно снижается модуль упругости EIT, как непосредственно на поверхностном слое, так и в глубине равной величине проникновения индентора при высоких усилиях нагрузки (табл. 1). При этом модуль упругости EIT поверхности полученной обработкой стандартным абразивным инструментом имеет близкие значение с принятым показателем для стали 12Х18Н10Т (E = 198 ГПа), и даже несколько повышается по мере увеличения глубины исследования.
Трехмерное АСМ изображение поверхностей полученных абразивной обработкой, подтверждает результат анализа СЭМ фотографий, что поверхностный слой образца после цикла выхаживания геометрически более качественный (рис. 2а, 2б).
Рис. 2.
АСМ изображения поверхности (а, б) и распределение контактной разности потенциалов (в, г) после операции шлифования стандартным абразивным инструментом (а, в) и импрегнированным абразивным инструментом (б, г).
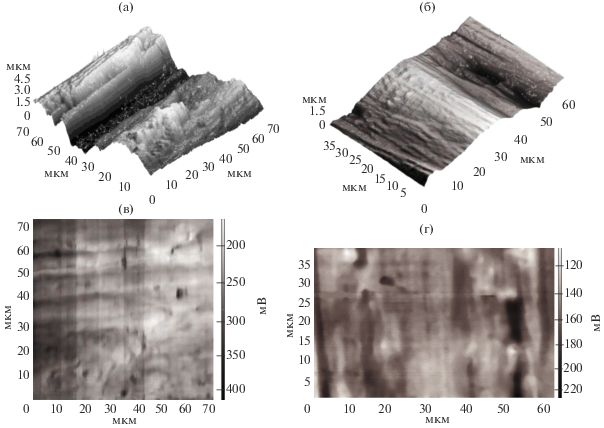
Полученные при исследовании отрицательные значения контактной разности потенциалов говорят о том, что РВЭ* наших образцов больше РВЭ зонда (рис. 2в, 2г). Соответственно более высокие отрицательные значения контактной разности потенциалов поверхности после шлифования стандартным абразивным инструментом, означают, что РВЭ* по сравнению с поверхностью после шлифования импрегнированным абразивным инструментом значительно выше. Численно это выражается изменением РВЭ* поверхности после шлифования стандартным абразивным инструментом относительно РВЭ зонда увеличением значений на 0.56–0.29 эВ, тогда как значение РВЭ* поверхности после шлифования импрегнированным абразивным инструментом выше только на 0.30–0.19 эВ. Важным моментом является тот факт, что размах в значениях РВЭ* поверхности после шлифования импрегнированным абразивным инструментом составляет всего 0.11 эВ, против 0.27 эВ у поверхности после шлифования стандартным абразивным инструментом.
Анализируя распределение контактной разности потенциалов по исследуемой поверхности образцов можно выделить в целом неравномерный характер с наличием небольших локальных участков (темная область) где значения РВЭ* существенно выше относительно остальной поверхности (рис. 2в, 2г).
Рассматривая полученные результаты исследования зеренной структуры поверхностного слоя, определенной за счет высокой контрастности ионного пучка к кристаллографическим плоскостям, можно увидеть значительные изменения в распределение размеров зерен и их расположении по глубине при сравнении влияния двух вариантов абразивного воздействия (рис. 3а, 3б). Так, имеющиеся в процессе шлифования стандартным абразивным инструментом высокие напряжения и значительные температуры способствуют измельчению зерен металла, что особенно ярко проявляется в тонком поверхностном слое (порядка 1.5 мкм), где можно наблюдать наноразмерные характеристики зерен. Далее, по мере роста глубины исследования, размеры зерен плавно увеличиваются при значительной фрагментации кристаллов и отсутствие их ориентировки относительно вектора пластической деформации (рис. 3а). Совершенно иная картина зеренной структуры наблюдается при анализе поверхностного слоя полученного после шлифования импрегнированным абразивным инструментом. Здесь в самом начале, так же имеется небольшой слой наноструктуированного зерна, но он несколько меньше по величине (около 1 мкм). Затем до глубины в 3 мкм, где прослеживается резкая граница, размер зерен немного увеличивается, а далее довольно отчетливо наблюдаются достаточно крупные вытянутые кристаллы, которые, скорее всего, представляют собой полосы скольжения направленные вдоль вектора приложенного напряжения, в результате чего формируется текстура. Между ними и низлежащими зернами имеется некоторый промежуточный слой, преимущественно состоящий из крупно фрагментированных кристаллов (рис. 3б).
Рис. 3.
Зеренная структура поверхностного слоя, полученного после шлифования стандартным абразивным инструментом (а) и импрегнированным абразивным инструментом (б).
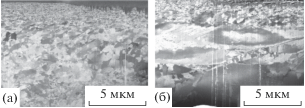
Элементный анализ поверхностного слоя исследуемого сечения показал что, непосредственно на самой поверхности и до значения приблизительно в 0.5 мкм вглубь при сравнении двух образцов имеется различие в распределении атомов никеля и кислорода. Так, поверхностный слой после шлифования импрегнированным абразивным инструментом обогащен атомами никеля практически до 14% при двукратном увеличении количество атомов кислорода (рис. 4). Соответственно такое перераспределение атомов компенсировалось за счет снижения атомов железа. Атомная концентрация остальных элементов практически не изменилась.
Рис. 4.
Атомная концентрация никеля и кислорода по глубине поверхностного слоя, полученного после шлифования стандартным абразивным инструментом (пунктирная линия) и импрегнированным абразивным инструментом (непрерывная линия).
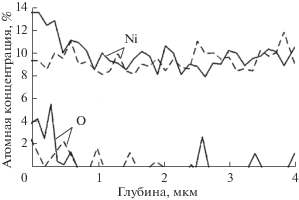
При исследовании стойкости обработанной поверхности к питтинговой коррозии, установлено, что количество крупных коррозионных язв практически одинаково на поверхности обоих образцов, однако общее количество очагов коррозии, в том числе небольших, существенно меньше на поверхности полученной после шлифования импрегнированным абразивным инструментом (рис. 5).
ОБСУЖДЕНИЕ РЕЗУЛЬТАТОВ
Непосредственно на поверхности обоих образцов формируется тонкий наноструктурированный слой, за счет чего имеется эффект упрочнения, что также отмечается в работах [2, 3]. Однако твердость поверхностного слоя после шлифования импрегнированным абразивным инструментом несколько выше (около 1 ГПа), что можно объяснить повышенной концентрации кислорода отмеченной при элементном анализе. Рядом исследователей [2, 7, 8] установлено, что на поверхности нержавеющей стали после механического воздействия образуется окисные соединения хрома или высокопрочные наночастицы Fe3О4. Соответственно можно предположить, что аналогичный механизм повышения твердости наблюдается в процессе шлифования импрегнированным абразивным инструментом за счет увеличения количество окислов. Проникновение индентора при нагрузке 10 мН на величину 0.3–0.4 мкм совпадает с величиной окисного слоя в 0.5 мкм, величину которого определи при элементном анализе. Более низкая твердость при нагрузке в 1000 мН хорошо согласуется по результатам исследования зеренной структуры, так у поверхности после шлифования импрегнированным абразивным инструментом при глубине проникновения индентора в 3–5 мкм структура зерна иная, преобладают вытянутые формы и крупные кристаллы, что в итоге отражается на значении твердости – в два раза ниже, чем на поверхности. Несколько более высокая твердость поверхности после шлифования стандартным абразивным инструментом на исследуемой глубине подтверждается сохранением дробления зерна. При этом на исследуемой глубине не зафиксировано наличие кислорода, упрочнение происходит только за счет величины зерна.
Интересным результатом является отмеченное понижение модуля упругости поверхностного слоя после шлифования импрегнированным абразивным инструментом. Одной из вероятных причин может быть высокое содержание кислорода с вероятным образованием твердых и хрупких окислов на поверхности после шлифования импрегнированным абразивным инструментом. Рассматривая значение модуля упругости в глубине поверхностного слоя можно предположить иной механизм изменения его величины. Здесь первостепенное влияние будет оказывать сформированная в результате пластической деформации текстура и в свою очередь анизотропия полученных механических свойств. При индентировании поверхности после шлифования импрегнированным абразивным инструментом проникновение индентора с усилием 1000 мН составляет 4–5 мкм, что как раз попадает в область с текстурой, причем процесс внедрения индентора происходит перпендикулярно преимущественному направлению расположения кристаллов. Отсюда возможно мы и имеем наблюдаемые низкие значения модуля упругости в подповерхностном слое. При шлифовании стандартным абразивным инструментом, формирование текстуры в глубине поверхности не обнаружено, в связи с этим модуль упругости практически не меняется и имеет значение близкое к принятому для данной стали.
При исследовании чистых металлов в работах [10, 11] установлено, что значение РВЭ прямопропорционально модулю упругости функцией в шестой степени. Результаты, полученные нами при исследовании обработанной поверхности нержавеющей стали, которая представляет собой многокомпонентную систему, также подтверждают данную зависимость. Поверхность после шлифования стандартным абразивным инструментом с более высоким средним значением РВЭ* по результатам индентирования обладает более высоким модулем упругости. Примечательно, то обстоятельство, что при исследовании одного и того же материала имеет место существенное отличие в значениях РВЭ* поверхности после абразивного воздействия различными способами. Что может быть связано, как предполагалось выше, с образование новых фаз или изменение кристаллической структуры поверхности. Так, в работе [12] экспериментально обнаружена тенденция к уменьшению значения РВЭ, модуля упругости и твердости сплава при формировании новой фазы в сплаве X70-Ni с увеличением концентрации Ni. В отличие от модуля упругости, величина которого в большей степени зависит от атомной структуры, значение твердости определяет не столь один фундаментальный параметр, а некая совокупность факторов. В связи с этим аналогичной связи РВЭ* со значением твердости обработанной поверхности полученной в результате абразивного воздействия нами не обнаружено. Учитывая принятую и определенную взаимосвязь РВЭ* и модуля упругости материала, и возвращаясь к карте распределения потенциала, можно констатировать неоднородность механических свойств по поверхности и локальность их контраста. Соответственно эти участки с резким изменением РВЭ* будут концентраторами трансформации эксплуатационных свойств обработанной поверхности.
Помимо механических свойств к сталям данного класса предъявляют высокие требования по коррозионной стойкости. Имеются публикации, в которых установлено, что поверхности с высокими значениями РВЭ обладают повышенной реакционной способностью [14] и склонностью к проявлению коррозии [15, 22]. Причем коррозионная активность зависит также от градиента значений РВЭ по поверхности, чем меньше по величине разброс в значениях, тем выше коррозионная стойкость [18, 23]. У поверхности после шлифования стандартным абразивным инструментом имеет место проявление сразу двух данных факторов. Так, в среднем, значения РВЭ* выше на 0.2–0.3 эВ, при более чем двукратном превышении амплитуды варьирования значений, относительно результатов полученных при измерении РВЭ* поверхности после шлифования импрегнированным абразивным инструментом. При исследовании стойкости образцов к питтинговой коррозии установлено, что поверхность после шлифования стандартным абразивным инструментом поражена очаговой коррозией существенно больше. Данный факт находиться в согласовании с принятой взаимосвязью РВЭ с коррозионной активностью и распространяется также, по результатам наших исследований, на случай абразивного воздействия на исследуемую поверхность. Кроме того, элементный анализ поверхностного слоя после шлифования импрегнированным абразивным инструментом показал повышенное содержание никеля и кислорода, что дает основание к более значительной стойкости к проявлению коррозии, т.к. образовавшийся окисный слой и высокая концентрация никеля сдерживает дальнейшее окисление поверхности.
ЗАКЛЮЧЕНИЕ
Установлено, что на поверхностях, вне зависимости от способа воздействия, имеется тонкий наноструктурированный слой величиной около 1 мкм, причем его твердость после шлифования импрегнированным абразивным инструментом выше на 1 ГПа. При этом модуль упругости значительно снижается вплоть до значений в 147 ГПа. Таким образом, в результате применения импрегнированного абразивного инструмента пластичность обработанной поверхности уменьшается.
Результаты исследования показывают наличие взаимосвязи полученных значений контактной разности потенциалов, с измеренным модулем упругости анализируемых образцов после абразивного воздействия. У поверхности после шлифования импрегнированным абразивным инструментом значения РВЭ* существенно меньше, соответственно модуль упругости также значительно снижается, при обработке стандартным абразивным инструментом наблюдается аналогичная зависимость только в сторону увеличения показателей. По результатам наших исследований установлено, что поверхность после абразивного воздействия с более низким значением РВЭ обладает меньшей склонностью к питтинговой коррозии, что согласуется с большинством имеющихся публикаций.
Полученные механические характеристики поверхности в значительной мере зависят от приобретенной в результате пластической деформации зеренной структурой и химическим составом тонкого поверхностного слоя. При шлифовании импрегнированным абразивным инструментом наблюдаются значительные изменения зеренной структуры на глубине поверхностного слоя 3–5 мкм, и увеличение концентрации атомов кислорода и никеля непосредственно на самой поверхности.
“Исследование выполнено при финансовой поддержке РФФИ в рамках научного проекта № 16-38-00841 мол_а”.
Список литературы
Hinds G., Wickström L., Mingard K. et al. // Corrosion Science. 2013. V. 71. P. 43–52.
Ghosh S., Kumar M.K., Kain V. // Applied Surface Science. 2013. V. 264. P. 312–319.
Turnbull A., Mingard K., Lord J.D. et al. // Corrosion Science. 2011. V. 53. P. 3398–3415.
Gupta R.K., Birbilis N. // Corrosion Science. 2015. V. 92. P. 1–15.
Митрофанов А.П., Паршева К.А. // Вестник машиностроения. 2017. № 6. С. 75–79.
Osamu Takakuwa, Hitoshi Soyama // Advances in Chemical Engineering and Science. 2015. V. 5. P. 62–72.
Swati Ghosh, Vivekanand Kain // J. Nuclear Materials. 2010. V. 403. Iss. 1–3. P. 62–67.
Коршунов Л.Г., Черненко Л.Н. // Физика металлов и металловедение. 2016. Т. 117. № 3. С. 318–329.
Берсудский А.Л. // Проблемы машиностроения и надежности машин. 2006. № 6. С. 52–59.
Li W. //Scripta Materialia. 2006. V. 54. Is. 5. P. 921–924.
Guomin Hua, Dongyang Li // Applied Physics Letters. 2011. V. 99. P. 041907-1–041907-3.
Lu H. // Sci. Rep. 2016. V. 6. P. 1–11. https://doi.org/10.1038/srep24366
Zhou Y., Lu J.Q., Qin W.G. // Materials Chemistry and Physics. 2009. V. 118. P. 12–14.
Shiyi Liu, Hao Lu, Li D.Y. // Applied Surface Science. 2015. V. 351. P. 316–319.
Rohwerder M., Florin Turcu // Electrochimica Acta. V. 53. Is. 2. 1. December 2007. P. 290–299.
Deepak Dwivedi, Katěrina Lepkova, Thomas Becker // RSC Adv. 2017. V. 7. P. 4580.
Pan T. // J. Applied Electrochemistry. V. 42. Is. 12. P. 1049–1056.
Örnek C., Engelberg D.L. // Corrosion Science. V. 99. 2015. P. 164–171.
Oliver W.C., Pharr G.M. // J. Materials Research. 2004. V. 19. Is. 1. P. 3–20.
Головин Ю.И. // Физика твердого тела. 2008. Т. 50. № 12. С. 2113–2142.
Melitz W., Shen J., Kummel A.C., Lee S. // Surface Science Reports. 2011. V. 66. P. 1–27.
Frankel G.S., Guillaumin V., Schmutz P. // J. Electrochem. Soc. 2001. V. 148. P. B163–B173.
Su Kyeng Kim et al. // J. Appl. Electrochem. 2013. V. 43. P. 507–514.
Дополнительные материалы отсутствуют.
Инструменты
Физикохимия поверхности и защита материалов