Физикохимия поверхности и защита материалов, 2020, T. 56, № 3, стр. 323-329
Влияние ионной формы вводимого диатомита на катодное отслаивание битумно-полимерных покрытий
Н. Н. Петров 1, 2, *, А. С. Аловягина 2, М. Н. Михеев 1, Н. Н. Буков 2, В. Т. Панюшкин 2
1 ООО “Интеллектуальные композиционные решения”
Краснодар, Россия
2 ФГБОУ ВПО “Кубанский государственный университет”, Факультет химии и высоких технологий
Краснодар, Россия
* E-mail: nikpetrov@intelcor.ru
Поступила в редакцию 23.06.2018
После доработки 26.01.2019
Принята к публикации 05.02.2019
Аннотация
Изучено влияние вводимого в качестве активного наполнителя диатомита в никель 2(+) и натрий (+) ионных формах на адгезионную стойкость битумно-диатомитовых защитных систем при их катодной поляризации. Показано существенное влияние вводимой диатомитовой глины, способа ее активации и ее ионной формы на катодное отслаивание, и как следствие адгезионную долговечность битумно-полимерных защитных покрытий при их катодной поляризации. Данный эффект может быть использован при создании защитных противокоррозионных покрытий с повышенной долговечностью.
ВВЕДЕНИЕ
Торможение коррозионных процессов металлов под различными покрытиями и практическая простота их применения обусловила широкое применение различных покрытий для противокоррозионной защиты. Надежность адгезионной связи субстрата с покрытием в данном случае во многом определяет эффективность их противокоррозионной защиты.
Одними из сложных объектов для противокоррозионной защиты являются подземные магистральные трубопроводы [1, 2]. На сегодняшний день задача их противокоррозионной защиты решается совместным действием гидроизоляционных покрытий, препятствующих доступу коррозионных агентов к металлу трубы и электрохимзащиты, работающей при наличии дефектов и повреждений покрытия. Однако, обзор работ, посвященных оценке действия катодной защиты в щелевом элементе, в том числе, смоделированном на реальных моделях трубопроводов, показывает, что потенциал станции катодной защиты поддерживается на необходимом уровне только в устье отслаивания покрытия. С удалением от устья более чем на 50–100 мм, наложенный потенциал резко падает и не соответствует требованиям защиты, тем самым не обеспечивая противокоррозионную защиту металла труб [4, 5]. Опыт эксплуатации магистральных газопроводов показывает, что несмотря на практически 100%-ную защищенность трубопроводов от коррозии по протяженности средствами электрохимической защиты (ЭХЗ), около 90% всех выявляемых средствами диагностики повреждений являются повреждениями коррозионного характера, расположенными в отслаиваниях гидроизоляционных покрытий [3–5].
Широко применяемыми покрытиями являются различные битумно-полимерные покрытия, обеспечивающие гидроизоляцию стальных трубопроводов. Согласно [6] используют битумно-полимерные мастики в качестве адгезионно-связывающего и армированного стеклосеткой слоя в двухслойном защитном пакете с защитной термоусаживающейся пленкой, наносимой выше температуры текучести.
Многолетняя практика эксплуатации известных изоляционных битумных и битумно-полимерных покрытий трубопроводов свидетельствует о том, что физическая природа адгезионных связей покрытия с металлом не может обеспечить их сохранение в течение длительного срока. При применении данных покрытий в условиях катодной поляризации существенным фактом ослабления эффективности, приводящим к выше перечисленным проблемам, является их высокое катодное отслаивание. При этом начинается проникновение электролита под отслаивающееся покрытие и анодное растворение металла с проникновением в отслоившийся дефект катодно восстанавливающегося кислорода. Щелочная среда, формирующаяся в этом коррозионном элементе, способствует отслоению покрытия за счет растворения слоя амфотерных оксидов, распада полимера, и гидролиза межфазных адгезионных связей, что в итоге существенно уменьшает эффективность защиты и приводит к образованию коррозионных очагов [7, 8].
В последнее время развивается подход к получению защитных материалов с самовосстанавливающейся адгезионной связью. При этом термин “самовосстановление” означает самовосстановление исходных свойств поврежденного материала, повреждение в котором индуцировано внешними факторами или внутренними напряжениями.
Существует два подхода к восстановлению: первый – за счет инкапсулирования включений с повышенной плотностью лечащего материала, второй – за счет взаимодействия активных фазовых элементов материала покрытия с исходными или индуцированными соединениями внешней агрессивной среды. Однако независимо от пути “самовосстановления” конечным продуктом будет новая когезионно совместимая фаза на межслойной границе субстрат/покрытие [9, 10].
Перспективной системой здесь, как показано в работе [11] является сопряженная система катионообменник‒ион никеля(2+). В отличие от ионов других металлов ион никеля может образовывать стабильные даже в сильнощелочной среде (что актуально при катодной поляризации) твердые нерастворимые гидроокиси.
Таким образом, исходя из вышеизложенного целью настоящей работы является изучение адгезионного поведения при катодной поляризации битумно-диатомитовых защитных композитов, где будет варьироваться ионная форма недорогого природного ионообменного материала ‒ диатомитовой глины.
ЭКСПЕРИМЕНТАЛЬНАЯ ЧАСТЬ
Используемые материалы. Объектами исследований являлись: порошок природной диатомитовой глины месторождения в Московской области (производство АО “Базальтопластик”, Россия) и ее активированные и модифицированные образцы; битумное связующее и полиэтиленовая пленка (толщиной 1 мм) образующие двуслойное битумно-полимерное покрытие (производство АО “Делан”, Россия) [6]; двуслойные покрытия на основе приготовляемых по ниже описанной методике битумно-диатомитовых связующих.
Химический состав используемой глины полученный методом рентгено-флуоресцентного анализа на приборе EDX-800HS2 (Shimadzu) представлен в табл. 1, а табл. 2 представлены характеристики используемого битумного связующего.
Таблица 2.
Характеристики используемого битумного компаунда [6]
№ п/п | Наименование показателя | Значения | Нормативный документ на метод измерения |
---|---|---|---|
1 | Внешний вид | Однородная масса черного цвета без визуально–наблюдаемых включений и посторонних частиц | ТУ 5775-004-32989231-2010 П. 5.2. |
2 | Температура размягчения, °С | 100 ± 5 | ГОСТ 11506 |
3 | Глубина проникания иглы 0.1 мм, при температуре 23 ± 2°С | 25 ± 5 | ГОСТ 11501 |
4 | Растяжимость (дуктильность) при температуре 23 ± 2°С, см, не менее | 4 | ГОСТ 11505 |
5 | Температура хрупкости °С, не выше | –20 | ГОСТ 11507 |
6 | Адгезионная прочность покрытия через сутки после нанесения: | ТУ 5775-004-32989231-2010 П.п. 5.8 – 5.9. |
|
Методом сдвига (МПа) при 23 ± 2°С, не менее | 0.2 | ||
Методом отслаивания (Н/см), при 23 ± 2°С, не менее | 30.0 |
Активация диатомитовой глины. Известно [12, 13], что глинистые материалы достаточно активны в естественном состоянии, но большую часть из них целесообразно активировать химическим способом для увеличения и регулирования их ионообменных характеристик. В настоящей работе для активации использовали 5 мас. % водные растворы следующих соединений приготовленные из реагентов квалификации х. ч.: NaOH, NaCl и Na2CO3. На 100 г глины использовали 400 см3 соответствующего раствора при выстаивании при температуре окружающего воздуха в течение 7 сут. После этого отфильтровывали глину и фильтрат промывали 5-ти кратным избытком дистиллированной воды.
Для оценки влияния процедуры активации, после ее проведения, отбирали пробы глинистой суспензии, высушивали ее до воздушно-сухого состояния, определяли влажность полученной глины и ее статическую обменную емкость (СОЕ, мг экв/г), которую определяли методом обратного кислотно-основного титрования [14] после перевода глины в кислую форму 1 М раствором серной кислоты. Были получены следующие результаты СОЕ: нативная глина (не активированная) – 0.33 ± 0.02; NaOH – 0.55 ± 0.03; Na2CO3 – 0.63 ± 0.03; NaCl – 0.70 ± 004 мг экв/г.
Перевод глины в Ni(2+)-ионную форму. Диатомитовую глину после процедуры активации (за исключением нативной) помещали в 5 мас. % водный солевой раствор сульфата никеля при объемном соотношении глина : раствор 1 : 4 и выдерживали при температуре окружающего воздуха 7 сут, после этого глинистую суспензию отфильтровывали и промывали 5-ти кратным избытком дистиллированной воды.
Для контроля количественности процесса ионного замещения, после процедуры описанной выше, полученный диатомит анализировали на содержание подвижного иона никеля 2(+). Для этого навеску ионита помещали в 1 М раствор серной кислоты и выстаивали при легком перемешивании 5 ч, затем отбирали аликвоту и фотометрировали ее при длине волны 540 нм. По полученной заранее калибровочной зависимости находили концентрацию никель(2+) в полученном растворе, а затем пересчитывали на содержание в фазе диатомита. Меру количественности процесса замещения (замещенность) определяли по формуле:
где СОЕ – статическая обменная емкость ионита, мг экв/г, Z – заряд подвижного иона (для иона никеля – 2), СNi – найденное содержание никеля, ммоль/г.Полученные значения замещенности для всех образцов диатомитовой глины находились в интервале 98 ± 4%.
Приготовление битумно-диатомитового связующего. Осуществляли смешивание предварительно подготовленного порошка глины (в Na+- или Ni2+-форме) с битумным компаундом при температуре текучести битума в заранее подобранных условиях, обеспечивающих гомогенность распределения наполнителя в полимерной матрице (рис. 1а, 1б). При этом наполнитель вводился в максимально возможной концентрации (10 мас. %) обеспечивающей неизменность начальных физико-механических характеристик битума.
Рис. 1.
Микрофотографии поперечного среза изучаемых битумных связующих (ИК-микроскоп с оптической визуализацией Hyperion 2000, Bruker).
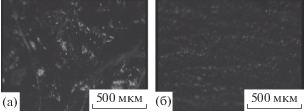
Перед введением полученную диатомитовую глину высушивали при температуре 110°С до воздушно-сухого состояния и просеивали полученный перемолом на планетарной мельнице порошок. В дальнейшем использовали фракцию частиц, прошедших сито 25 мкм.
Нанесение покрытия на сталь. На предварительно подготовленные до степени Sa 3 стальные пластины (низкоуглеродистая сталь Ст. 3, Россия) подогретые до температуры 100 ± 20°С наносили изучаемый битумный расплав толщиной 1–2 мм (температура расплава 180–190°С) при одновременном нанесении (без потери текучести битума) полимерной обертки при прокатке ее валиком до сцепления со связующим. Полученные образцы 100 × 100 мм оставляли охлаждаться при температуре 25 ± 5°С в условиях открытой атмосферы в течении 3-х сут, а затем проводили процедуру по определению их стойкости к катодному отслаиванию.
Определение катодного отслаивания образцов. Испытания проводили по методике, изложенной в ГОСТ 51164-98 (Россия). Для этого собирали ячейку, изображенную на рис. 2. В центре образца в изучаемом защитном покрытии сверлили цилиндрическое отверстие диаметром 0.6 см до образования в металле конического углубления. На пластину с помощью пластилина устанавливали трубу из полиэтилена таким образом, чтобы ось трубы совпала с центром высверленного в покрытии отверстия. Далее в трубу заливали электролит (раствор хлористого натрия) до уровня 50 мм от поверхности покрытия. Образец с помощью проводов соединяли с магниевым анодом, как показано на рис. 2. При этом на образце устанавливали потенциал минус 1.35–минус 1.45 В по хлорсеребряному электроду сравнения. Образцы выдерживали в растворе электролита под действием наложенного катодного тока в течение 30 дней при температуре 25 ± 5°С. Периодически через каждые 7 дней испытаний производили замену раствора электролита. По окончании испытаний образец с покрытием демонтировали, промывали водой и вытирали ветошью. Площадь отслоившегося участка покрытия оголяли, осторожно поддевая и срезая покрытие скальпелем. Площадь отслаивания переводили на кальку, а затем вычисляли методом взвешивания. Относительная погрешность определения при этом не превышала 5%.
РЕЗУЛЬТАТЫ И ИХ ОБСУЖДЕНИЕ
Изучение адгезионной долговечности материалов, в том числе, в условиях катодной поляризации проводилось с помощью теста на катодное отслаивание. Данный метод хорошо имитирует реальные условия жизненного цикла покрытия [15–18]. При этом скорость отслоения зависит от природы испытываемой системы и ее адгезионной стойкости, и, долговечности.
Полученные экспериментальные данные по отслаиванию приведены на рис. 3а, 3б. Общей тенденцией при переходе вводимого диатомита из Na+- в Ni2+-форму является существенное уменьшение площади отслаивания изучаемых систем. Причем, наибольшая (в Na+-форме) и наименьшая (в Ni2+-форме) величина отслаивания наблюдаются для диатомита, активированного NaCl и имеющего наибольшую СОЕ. Ингибирование отслаивания относительно исходного битумно-полимерного покрытия составляет 97% (рис. 4), тогда как для системы с диатомитом в Na+-форме наблюдаемое промотирование составляет 200%.
С целью сопоставления величин отслаивания и ионообменных свойств вводимого в битум диатомита по формуле (2) нами рассчитано количество обменных ионов, приходящихся на мм3 связующего.
где Сion – содержание подвижных обменных ионов в объеме связующего, мкмоль/мм3, σ – массовая доля диатомита, м. ч., Z – заряд подвижного иона, ρ – плотность материала, г/см3.Полученные зависимости представлены на рис. 5а, 5б. Как видно, в обоих случаях площадь отслоившегося покрытия не имеет прямолинейной зависимости от величин содержания подвижных обменных ионов в объеме битумного связующего. В диапазоне от 0.015 до 0.025 мкмоль/мм3 иона никеля (от 0.03 до 0.042 для иона натрия) она практически постоянна, однако при дальнейшем росте содержания подвижного Ni2+ или подвижного Na+, обусловленной активацией материала, площадь отслаивания битум-неорганической композиции имеет тенденцию к снижению (в Na+-форме к повышению).
Полученные зависимости (рис. 6) объясняются нами следующим образом. Ионы натрия, введенные в диатомит, способствуют тому, что щелочь, образованная при взаимодействии кислорода с водой в результате катодной поляризации, проникает сквозь толщу покрытия и не образует нерастворимой фазы, которая блокировала бы массобмен и деструкцию в адгезионном слое, в то время как ионный обмен наполнителя, переведенного в Ni-форму, с внешним электролитом обусловливает подавление отслаивания за счет образования на адгезионном слое нерастворимого твердого основания Ni(OH)2 (уравнения (3), (4)) которое блокирует негативную электрохимическую реакцию и дополнительно защищает металлическую поверхность.
(3)
$\begin{gathered} {{({\text{Диатомит}}{\kern 1pt} - {\kern 1pt} {\text{N}}{{{\text{i}}}^{{2 + {\text{\;\;}}}}})}_{{{\text{твердая\;фаза}}}}} + 2{\text{Na}}_{{{\text{раствор}}}}^{ + } \to \\ \to {{({\text{Диатомит}}{\kern 1pt} - {\kern 1pt} {\text{N}}{{{\text{a}}}^{{ + {\text{\;\;}}}}})}_{{{\text{твердая\;фаза}}}}} + {\text{Ni}}_{{{\text{раствор}}}}^{{2 + }}, \\ \end{gathered} $(4)
${\text{N}}{{{\text{i}}}^{{2 + }}} + 2{\text{O}}{{{\text{H}}}^{ - }} \to {{\left. {{\text{Ni(OH}}} \right)}_{{2{\text{\;твердый}}}}}.$Рис. 6.
Механизм связывания агрессивных ионов внешней среды ионообменным микрорезервуаром (диатомитовой глиной) в Ni2+-форме на границе покрытие/субстрат, (а) самодиффузия внешних ионов в толще покрытия, (б) ионный обмен в микрорезервуаре и высвобождение иона никеля 2(+), (в) связывание внешней щелочи в нерастворимую твердую фазу.
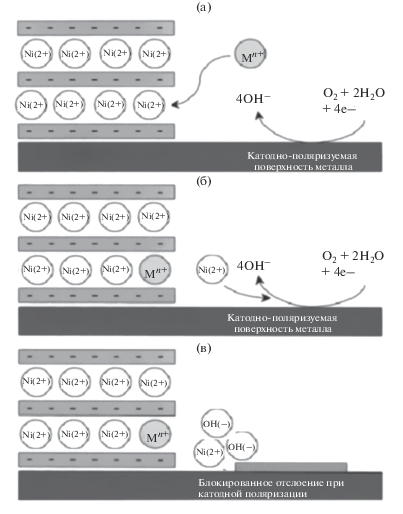
Таким образом, внедрение в практику противокоррозионной защиты покрытий, содержащих ионообменные микрорезервуары (на примере диатомитовой глины в Ni2+-форме) позволяет предотвратить катодное отслаивание битумно-полимерных и других покрытий, существенно увеличить срок его службы с одновременным увеличением долговечности адгезионной связи с металлической поверхностью и, как следствие, повысить надежность и эффективность противокоррозионной защиты металлических (стальных) конструкций, находящейся под активной катодной противокоррозионной защитой.
ЗАКЛЮЧЕНИЕ
Показано существенное влияние вводимой диатомитовой глины, способа ее активации и ее ионной формы на катодное отслаивание, и как следствие адгезионную долговечность битумно-полимерных защитных покрытий при их катодной поляризации. Данный эффект может быть использован при создании защитных противокоррозионных покрытий с повышенной долговечностью.
Данная работа выполнена с использованием оборудования ЦКП “Эколого-аналитический центр” Кубанского госуниверситета, уникальный идентификатор RFMEF159317X0008.
Список литературы
Колотовский А.Н., Кузьбожев А.С., Агиней Р.В. и др. // Защита окружающей среды в нефтегазовом комплексе. 2009. № 3. С. 26–30.
Maocheng Yan, Shuang Yang, Cheng Sun, Jin Xu, Tangqing Wu, Wei Ke // Corrosion Science. 2015. V. 93. P. 27–38.
Агиней Р.В., Александров Ю.В. // “Территория НЕФТЕГАЗ”. 2010. № 2. С. 23–26.
Колотовский А.Н., Кузьбожев А.С., Агиней Р.В. и др. // Защита окружающей среды в нефтегазовом комплексе. 2009. № 3. С. 31–35.
Кузьбожев А.С., Агиней Р.В., Александров Ю.В., Глотов И.В. // Коррозия: материалы, защита. 2007. № 6 . С. 21–25.
Арабей А.Б. и др. Патент RU2325586, Изоляционная битумно-полимерная мастика, опубл. 27.05.2008.
Черкасов Н.М., Гладких И.Ф., Филимонов В.А. // Нефтегазовое дело. 2010. С. 1–9.
Williams G., McMurray H.N., Loveridge M.J. // Electrochimica Acta. 2010. V. 55. P. 1740–1748.
Lorenzo Fedrizzi, Wolfram Fürbeth, Fátima Montemor. Self-healing properties of new surface treatments. Published by Maney Publishing on behalf of the European Federation of Corrosion and The Institute of Materials, Minerals & Mining, 2011. 305 c.
Panyushkin V., Petrov N., Sokolov M., Bukov N. Highly Efficient Hybrid Protective Materials for Technically Complicated Systems in Natural Aggressive Conditions. In: Martínez L., Kharissova O., Kharisov B. (eds) Handbook of Ecomaterials. Springer. Cham. 2017. P. 1–61.
Petrov N.N., Koval T.V., Shel’deshov N.V., Bukov N.N. // Protection of Metals and Physical Chemistry of Surfaces. 2017. V. 53. № 1. P. 133–138.
Wan Ngah W.S., Hanafiah M.A. // Bioresource. Technol. 2008. V. 99. P. 3935–3948.
Везенцев А.И., Королькова С.В., Воловичева Н.А., Худякова С.В. // Сорбционные и хроматографические процессы. 2009. Т. 9. Вып. 6. С. 830–834.
Полянский Н.Г. Методы исследования ионитов / Горбунов Г.В., Полянская Н.Л. // М.: Химия, 1976. 208 с.
Chen J., Bull S. // J. Physics D: Applied Physics. 2011. V. 44. P. 3.
Guedes Soares C., Garbatov Y., Zayed A. // Corrosion Engineering, Science and Technology. 2011. V. 46. P. 524–541.
Nguyen T., Hubbard J.B., McFadden G.B. // The J. Coatings Technology. 1991. V. 63. P. 43–52.
Старостина И.А. Кислотно-основные взаимодействия и адгезия в металлполимерных системах / Старостина И.А., Стоянов О.В. // Монография / КГТУ. Казань, 2010. 195 с.
Дополнительные материалы отсутствуют.
Инструменты
Физикохимия поверхности и защита материалов