Физикохимия поверхности и защита материалов, 2020, T. 56, № 4, стр. 440-448
Термический анализ окисления порошков TiB2 в композиции защитного смачиваемого покрытия для катодов алюминиевых электролизеров
И. А. Кириллова 1, *, Л. С. Тарасова 4, **, Е. Н. Федорова 1, 3, ***, А. О. Гусев 2, Д. А. Симаков 2, ****, Г. Е. Нагибин 1
1 Федеральное государственное автономное образовательное учреждение высшего образования
“Сибирский федеральный университет”
660041 Красноярск, пр. Свободный, 79, Россия
2 Общество с ограниченной ответственностью Объединенная компания РУСАЛ Инженерно-технологический центр (ООО “РУСАЛ ИТЦ”)
660067 Красноярск, ул. Пограничников, 37, стр. 1, Россия
3 Институт вычислительных технологий СО РАН (ИВТ СО РАН),
Красноярский филиал
660049 Красноярск, пр. Мира, 53, Россия
4 Федеральное государственное бюджетное научное учреждение “Федеральный исследовательский центр “Красноярский научный центр СО РАН”
660036 Красноярск, ул. Академгородок, 50, Россия
* E-mail: iakirillova17@gmail.com
** E-mail: luma10@yandex.ru
*** E-mail: efedorova@sfu.-kras.ru
**** E-mail: Dmitriy.Simakov@rusal.com
Поступила в редакцию 13.06.2019
После доработки 26.02.2020
Принята к публикации 03.03.2020
Аннотация
Методом синхронного термического анализа проведено исследование устойчивости различных порошков TiB2 к окислительной деградации. Установлено, что характер температурной зависимости скорости окисления порошков определяется их гранулометрическим составом и морфологией. Полученные результаты могут быть использованы для подбора оптимальных структурно-морфологических характеристик порошкового диборида титана для его использования в составе композиции защитного смачиваемого покрытия углеграфитовой подины алюминиевого электолизера.
ВВЕДЕНИЕ
Постоянно растущий спрос на товарный алюминий требует повышения производительности действующих электролизеров [1–3]. В свою очередь, увеличение амперной нагрузки и плотности тока приводит к изменению кинетики физико-химических процессов взаимодействия криолит-глиноземного расплава с материалом катодных блоков [4].
Поскольку в современных электролизных ячейках расплавленный алюминий не смачивает углеграфитовую подину, на ее поверхности образуется пленка электролита, что является причиной увеличения скорости электрохимического и механического износа катодных блоков, а также вызывает снижение выхода по току [1, 4, 5]. Реализация конструкции подины с защитным смачиваемым алюминием покрытием позволила бы продлить срок службы ванны, снизить удельный расход электроэнергии до 10–12 кВт ч/кг Al и сократить расходы на обслуживание алюминиевого электролизера [5, 6].
На сегодняшний день, все применяемые на практике защитные смачиваемые покрытия, представляют собой композиты на основе диборида титана (TiB2), который характеризуется высокой твердостью (3350 Hv при нагрузке 0.5 Н), низким удельным электрическим сопротивлением (0.09 мОм × м), химической стойкостью в криолит-глиноземном расплаве и, что наиболее важно, смачивается расплавом алюминия [2, 6–8].
Основными ограничениями для промышленного внедрения смачиваемых покрытий на основе диборида титана являются его высокая стоимость (30–150 $/кг) и интенсивное взаимодействием с кислородом, особенно на этапе пуска электролизера. Снижение себестоимости материала на основе диборида титана достигается путем уменьшения его содержания в составе композиции до 40 об. %, достаточного для сохранения смачиваемости. В отношении окислительной деградации порошков TiB2, результаты исследований [9–11] показали, что ее скорость в значительной мере зависит от их гранулометрического состава. Так, мелкие фракции (<5 мкм), интенсивно окисляются даже при крайне малом содержании кислорода 0.002 ppm, в то время как крупнодисперсные порошки (средний размер частиц >10 мкм), окисляются в два раза медленнее [9].
Таким образом, целью данной работы является исследование влияния дисперсности и морфологии порошков диборида титана на их устойчивость к окислительной деградации методом синхронного термического анализа для оптимизации гранулометрического состава TiB2 в композиции материала защитного смачиваемого покрытия катодных блоков алюминиевого электролизера.
МАТЕРИАЛЫ И МЕТОДЫ ИССЛЕДОВАНИЙ
В качестве исходных материалов использовались порошки диборида титана различного гранулометрического состава. Порошок ПР-2 получен методом самораспространяющегося высокотемпературного синтеза (СВС) (ТУ 113-07-11.040-89 и ТУ 6-09-03-75, ФГУП “УНИХИМ с ОЗ”, г. Екатеринбург). Порошки китайского производства ПК-1, ПК-3, ПК-6, ПК-5 и ПК-6 получены методом промышленного карботермического синтеза (КТС).
Качественный анализ кристаллических фаз исходных порошков диборида титана методом рентгенофазового анализа (РФА) проводился на рентгеновском дифрактометре D8 ADVANCE Bruker (Германия) с применением CuKα излучения (λ = 0.15406 Å), диапазон съемки по 2θ от 10° до 75° с шагом 0.07°.
Гранулометрический состав исходных порошков TiB2 определялся с использованием лазерного прибора для измерения размера частиц Analysette 22 MicroTec plus Fritsch (Германия) согласно методике ISO13320:2009.
Исследования морфологии поверхности, формы и размеров частиц порошков TiB2 проводились с использованием сканирующего электронного микроскопа (СЭМ) JEOL JSM 6490-LV (Япония).
Синхронный термический анализ (термогравиметрию (ТГ) и дифференциальную сканирующую калориметрию (ДСК)) порошков диборида титана проводили на приборе Netzsch STA 449 С Jupiter. Поскольку значения плотности порошковых образцов отличаются в зависимости от способа их получения, массу навески (20–25 мг) подбирали таким образом, чтобы высота образца в тигле не превышала 2 мм. Навеску порошка TiB2 разравнивали по дну корундового тигля (Ø 0.6 мм). Термическую обработку образцов проводили в условиях динамического линейного нагрева до 950°С со скоростью (q) 10 К/мин с последующей изотермической выдержкой в течение 30 мин в газовой среде совмещенных потоков товарного аргона (поток 10 мл/мин, ГОСТ 10157-79, высший сорт, объемная доля Ar не менее 99.994%, объемная доля O2 не более 0.0004%) и воздуха (поток 30 мл/мин, относительная влажность при Ткомн около 60–70%). Приборная погрешность контроля массы и температуры образца составляла 10–5 г и ±1°С, соответственно.
РЕЗУЛЬТАТЫ И ОБСУЖДЕНИЯ
Гранулометрический состав и морфология поверхности
Результаты РФА показали, что все используемые порошки представляют собой TiB2. Результаты гранулометрического состава исследуемых порошков приведены на рис. 1. СЭМ-фотографии проб различных порошков TiB2 приведены на рис. 2.
Как видно при анализе гистограмм (рис. 1) и результатов СЭМ (рис. 2), наиболее крупными являются порошки ПК-1 и ПК-6, которые характеризуются средним размером частиц dср = 70 мкм и dср = 53 мкм, соответственно. Порошок ПК-1 в основном представлен частицами правильной геометрической формы, объединенными в цепочки (рис. 2, 3), наблюдаются отдельные частицы размером ~100 мкм (рис. 3) Видно, что частицы монолитные, имеют четкую огранку. Объединение частиц, по-видимому, произошло в результате сплавления в местах контакта в процессе получения. Частицы порошка ПК-6 характеризуются схожей морфологией поверхности, однако имеют более округлую форму без четко выраженной огранки (рис. 2).
Порошки ПР-2, ПК-2 и ПК-3 характеризуются широким распределением частиц по размерам: от субмикронных до десятков микрометров (рис. 1). Порошки ПР-2 и ПК-2 имеют близкий гранулометрический состав со средним размером частиц ~10 мкм (рис. 1). При этом, по сравнению с более однородным переходом между фракциями, характерным для ПР-2, порошок ПК-2 имеет ярко выраженное тримодальное распределение частиц по размерам с максимумами ~3, 10 и 35 мкм соответственно. Наличие различных фракций также отчетливо наблюдатся при анализе микрофотографий. Согласно результатам исследований методом СЭМ, порошки ПК-2 и ПР-2 представлены частицами неправильной формы со схожей морфологией (рис. 2). На рис. 4 в качестве примера приведены СЭМ-фотографии частиц порошка ПК-2 на больших увеличениях, частицы имеют достаточно развитую поверхность и представляют собой агломераты относительно мелких частиц, прошедших через расплав.
Порошок ПК-3 (dср = 21 мкм) имеет достаточно широкое распределение по размерам, содержит как крупные, так и мелкие частицы, и постепенный переход между фракциями. Морфология поверхности частиц порошка ПК-3 отличается от ПК-2 и ПР-2: частицы имеют пластинчатую форму, схожую с ПК-6 (рис. 2).
Наиболее мелким из всех исследуемых порошков является ПК-5, средний размер частиц которого 2.6 мкм, содержание мелкой фракций (до 10 мкм) составляет 100% (рис. 2). Морфология поверхности частиц ПК-5 наиболее сравнима с порошком ПР-2.
Синхронный термический анализ
На рис. 5 приведены термограммы окислительных экспериментов различных порошков TiB2. В целом характер кривых термогравиметрии схож для всех образцов, однако значения остаточной массы (∆mост) незначительно отличаются (табл. 1 ).
Рис. 5.
Первичные термограммы изменения массы порошков TiB2 в кислородсодержащей среде: сегмент 1 – режим линейного нагрева до 950°С, q = 10 К/мин; сегмент 2 – изотермическая выдержка 30 мин.
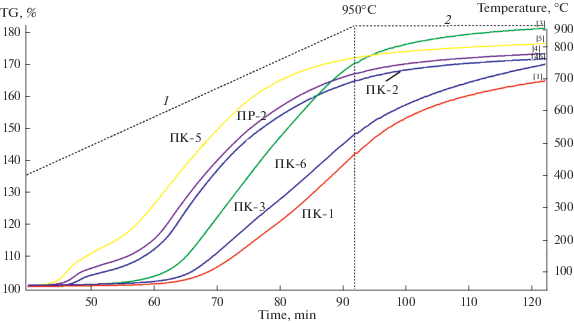
Для оценки полноты протекания реакции окисления, полученные значения ∆mост образцов представлены в виде степени превращения (α). Степень превращения вычисляли, предполагая полное окисление диборида титана (α = 1) в соответствии с уравнением
(1)
${\text{Ti}}{{{\text{B}}}_{2}} + {5 \mathord{\left/ {\vphantom {5 2}} \right. \kern-0em} 2}{{{\text{O}}}_{2}} = {\text{Ti}}{{{\text{O}}}_{{2(}}}_{{{\text{тв)}}}} + {{{\text{B}}}_{2}}{{{\text{O}}}_{{3(}}}_{{{\text{ж)}}}},$Исходя из полученных результатов термогравиметрии (рис. 5), по характеру поведения в окислительной среде, исследуемые порошки можно разделить на три группы.
Первую группу составляет пара самых крупных из исследуемых порошков ПК-1 и ПК-6 с наименьшими величинами ∆mост (табл. 1 ). Интенсивный прирост массы для порошков ПК-1 и ПК-6 начинается при Т ≈ 600°С (рис. 5). Этой же температуре соответствует начало экзо-эффекта на кривой ДСК, наличие которого свидетельствует об активном протекании процесса окисления (рис. 6).
Рис. 6.
Термограммы окисления порошков первой группы ПК-1 и ПК-6 (ТГ – сплошная линия и ДСК – штриховая линия).
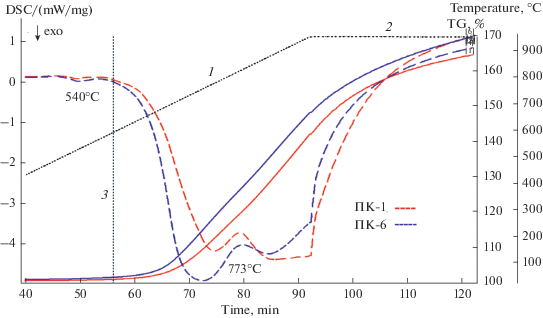
Ко второй группе относятся порошки с широким распределением частиц по размерам – ПК-2, ПР-2 и мелкодисперсный ПК-5. В отличие от первой группы, характеризующейся монотонным приростом массы на протяжении всего эксперимента, на термограммах окисления порошков второй группы ПК-2, ПР-2 и ПК-5 наблюдаются две ступени (интервалы 435–540 и 540–950°С) и соответствующие им экзотермические эффекты (рис. 5, 7).
Рис. 7.
Кривые термогравиметрии (сплошные линии) и ДСК (штриховые линии) окисления порошков второй группы ПК-2, ПР-2 и ПК-5 (динамический сегмент).
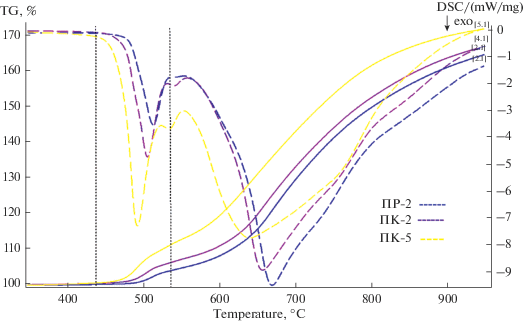
Образец ПК-3 можно выделить в отдельную третью группу. На ТГ-кривой рост массы, как и у первой группы, начинается около 600°С, однако скорость процесса значительно выше, о чем свидетельствует более крутой наклон ТГ-кривой (рис. 5).
Полученные экспериментальные данные термоанализа дают основание полагать, что несмотря на сравнимые значения α и ∆mост, макромеханизм и кинетика процесса окисления порошков TiB2 определяются их гранулометрическим составом и структурной морфологией.
Кинетические особенности взаимодействия порошков диборида титана с кислородом можно объяснить, основываясь на температурной зависимости скорости их окисления i = Δα/Δτ (рис. 8) и модели формирования защитного оксидного слоя на боридах [12, 13].
Рис. 8.
Зависимость скорости окисления i всех исследуемых порошков диборида титана от температуры: первая группа (ПК-1, ПК-6) – красные линии; вторая группа (ПК-2, ПР-2, ПК-5) – синие линии; третья группа (ПК-3) – зеленая линия.
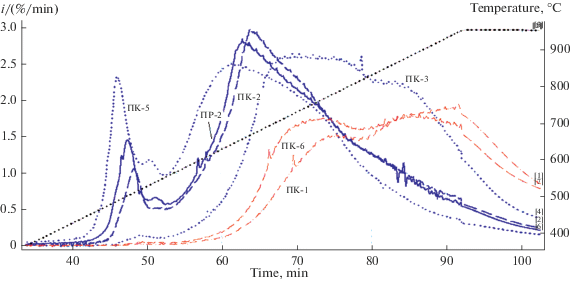
Известно [14], что жаростойкость TiB2 обуславливается формированием на его поверхности защитных пленок, образующихся в результате взаимодействия продуктов реакции (1). На первом этапе при низкой температуре, скорость окисления мелких частиц порошка относительно велика, а ее температурная зависимость определяется энергией активации химического акта взаимодействия (порядка 300–400 кДж/моль), в результате чего на поверхности образуется защитная пленка, состоящая из TiО2(тв) и B2O3(ж). Эта стадия соответствует первому экзо-эффекту на ДСК-кривых (рис. 6, 7) и первому максимуму на кривых скорости окисления (рис. 8) для всех порошков, однако их интенсивность сильно отличается, что обусловлено долей субмикронной фракции. В интервале 450–580°С ожидаемо наибольшую величину i среди исследуемых порошков имеет самый мелкий – ПК-5. В свою очередь, отсутствие мелких фракций у крупных порошков ПК-1 и ПК-6 со среднем размером частиц 70 и 53 мкм соответственно, обуславливает минимальную, по сравнению с остальными порошками, скорость окисления (рис. 1, 8).
На графиках рис. 8 в интервале 580–600°С для всех порошков TiB2 зафиксирован минимум величины i и последующий ее рост при Т > 600°С. Снижение скорости окисления обусловлено формированием на поверхности порошка оксидного защитного слоя, доставка кислорода через который может быть осуществлена одним из трех конкурирующих механизмов: диффузией в жидком B2O3, диффузией в твердом TiO2 и диффузией в газовой фазе по порам и трещинам [14]. Поскольку величина коэффициента диффузии кислорода ${{D}_{{{\text{(}}{{{\text{B}}}_{{\text{2}}}}{{{\text{O}}}_{{\text{3}}}}{\text{)}}}}}$ и ${{D}_{{{\text{(Ti}}{{{\text{O}}}_{2}})}}}$ в жидком B2O3 при 1000°С D = 3.8 ×10–11 м2/с и в рутиле D = 2.3 × 10–14 м2/с [15] сильно отличаются, очевидно, что доставка кислорода в реакционную область идет через В2О3, а также имеющиеся поры и трещины. Таким образом в интервале 580–600°С реакция окисления лимитируется диффузионной доставкой кислорода через жидкий В2О3 к диборидной основе.
Выше 600°С скорость реакции окисления всех исследуемых порошковых образцов растет, однако характер ее температурной зависимости сильно отличается и, по-видимому, объясняется индивидуальными структурно-морфологическими особенностями порошков. Поскольку с ростом температуры летучесть B2O3 растет, он освобождает поверхность и удаляется из пор. Удаление B2O3 способствует спеканию слоя TiО2, структура которого определяется исходными дисперсностью и морфологией порошка TiB2. Таким образом, выше 600°С кинетика и макромеханизм окисления определяется сформировавшейся на начальном этапе структурой оксидного слоя и механизмом доставки кислорода через него.
С ростом температуры спекание оксидного слоя TiО2, вызывает его растрескивание, кислород получает доступ к дибориду и скорость окисления возрастает. Этим можно объяснить увеличение скорости реакции, максимальное значение которой для крупных порошков первой группы ПК-1 и ПК-6 достигается при Т = 770°С и составляет 1.75%/мин. Для порошков ПК-2 и ПР-2 с меньшим значением dср максимальные величины i (2.9 и 2.75%/мин соответственно) ожидаемо достигаются в диапазоне температур ниже (640–670°С), чем для первой группы.
При дальнейшем нагреве сколы и трещины в слое TiО2 залечиваются вновь образующимися продуктами реакции (1) и скорость процесса замедляется, что объясняет снижение величины i и размытую, зубчатую форму кривых ДТГ выше 800°С (рис. 8), порожденную скачкообразными изменениями скорости окисления за счет беспорядочного растрескивания защитного слоя и частиц с последующим залечиванием. При этом, интенсивность и продолжительность микро- и макроэффектов на кривой ДТГ зависит от температуры, а также от дисперсности и морфологии порошка.
Несмотря на прогнозируемую степень окисления порошков в зависимости от их гранулометрического состава (более интенсивное окисление мелкодисперсных порошков по сравнению с крупнодисперсными), порошки ПК-5 и ПК-3 имеют нехарактерное поведение в окислительной среде. Так ПК-5 – самый мелкий порошок со средним размером частиц 2.6 мкм предполагает его полное окисление при заданных условиях эксперимента. Однако величина степени глубины протекания реакции окисления α порошка ПК-5 составляет 0.67 и незначительно отличается от величин, полученных для порошков ПК-2 и ПР-2 со средним размером частиц около 20 мкм (табл. 1, 2 ). Кроме того, для ПК-5 величина скорости окисления imax= 2.5%/мин, т.е. меньше, чем у ПК-2 и ПР-2 (рис. 8).
Также порошок ПК-3 с широким распределением частиц по размерам, выделенный в отдельную группу по характеру термического поведения, имеет гранулометрический состав схожий с ПР-2 и ПК-2, но, в отличие от них, содержит очень крупные частицы (табл. 1), что позволяет прогнозировать величину остаточной массы близкую к ней для ПР-2 и ПК-2, и скорость окисления ниже, чем у мелкодисперсного порошка ПК-5. Однако порошок ПК-3 имеет наибольшие значения ∆mост и α (табл. 2 ). Полученные нехарактерные результаты окислительных экспериментов на порошках ПК-3 и ПК-5 могут быть связаны с особенностями их морфологии.
Таблица 1.
Остаточная масса (∆mост) и глубина протекания реакции (α) образцов TiB2 после окислительных экспериментов
Порошковый образец TiB2 | Остаточная масса (∆mост), % | Глубина протекания реакции, α |
---|---|---|
ПК-1* | 165 | 0.57 |
ПК-2 | 171 | 0.63 |
ПК-3* | 181 | 0.71 |
ПР-2 | 173 | 0.64 |
ПК-5 | 176 | 0.67 |
ПК-6 | 170 | 0.61 |
Как было описано выше, неоднородный порошок ПК-3 представлен плоскими частицами неправильной формы (рис. 1), что, по-видимому, способствует формированию рыхлого слоя диоксида титана и свободному удалению В2О3 из пор. Как следствие, механизм доставки кислорода осуществляется через твердый TiО2 и газовую фазу, что объясняет высокую скорость окисления порошка.
Напротив, неполное окисление однородного мелкодисперсного порошка ПК-5 с большой площадью контакта частиц (рис. 2, 5), можно связать с быстрым формированием на начальном этапе нагрева плотного слоя TiO2 с закрытыми порами, в которых остается жидкий В2О3. Образование этого слоя оксидов блокирует доступ кислорода к TiB2, обуславливая относительно невысокую скорость окисления (2.5%/мин).
ЗАКЛЮЧЕНИЕ
Результаты проведенной серии термических экспериментов по окислению порошков диборида титана, показали, что кинетика процесса существенно зависит от их гранулометрического состава и морфологии.
Структурно-морфологические особенности порошков (гранулометрический состав, распределение частиц по размерам и форма частиц) определяют структуру, состав и макромеханизм роста защитного оксидного слоя на поверхности частиц порошка TiB2. В свою очередь, структура защитного оксидного слоя (плотность, открытая/закрытая пористость, размер пор, присутствие в закрытых порах жидкого В2О3) определяет скорость и механизм транспорта кислорода в реакционную зону.
Несмотря на то, что по результатам проведенных экспериментов наилучшую устойчивость к окислительной деградации демонстрируют крупные порошки со средним размером частиц 50–70 мкм (ПК-6, ПК-1), использование в составе материала защитного смачиваемого покрытия порошков только крупной фракции может негативно сказываться на его механических свойствах. Также нецелесообразно использование исключительно мелких порошков со средним размером частиц до 10 мкм, таких как ПК-5, поскольку их свободное распределение в матрице материала покрытия и на его поверхности в зоне контакта с расплавом металла и электролита приведет к их полному окислению уже на начальном этапе запуска ванны.
Таким образом, для повышения стойкости к окислительной деградации в составе защитного смачиваемого покрытия для углеграфитовой подины алюминиевого электролизера предпочтительно использовать порошок диборида титана с широким распределением частиц по размерам однородной морфологии.
Список литературы
Sorlie M., Øye H.A. Cathodes in Aluminium Electrolysis. 3-rd ed. Dusseldorf: Aluminium – Verlag Marketing and Kommunikation GmbH, 2010. P. 699.
Сизяков В.М., Власов А.А., Бажин В.Ю. // Цветные металлы. 2016. № 1. С. 32–38.
Юрков А.Л. // Российский химический журнал. 2006. Т. 50. № 1. С. 35–42.
Rafiei P., Hiltmann F., Hyland M. et al. // Light Metals. 2001. P. 747–752.
Øye H.A., Welch B.J. // JOM. 1998. V. 50. P. 18–23.
Li T., Jonasen S.T., Solheim A. // Light Metals. 2015. P. 831–836.
Hou J., LÜ X., Zhang Y. H. et al. // Light metals. TMS. 2011. P. 1017–1021.
Novak B., Tschope K., Ratvik A.P., Grande T. // Light Metals. 2012. P. 1343–1348.
Иванов В.В., Блохина И.А., Кирик С.Д. // Огнеупоры и техническая керамика. 2013. № 4–5. С. 10–15.
Ivanov V.V., Blokhina I.A., Kirik S.D. // Oxidation of metals. 2014. V. 81(3/4). P. 71–84.
Blokhina I.A., Ivanov V.V. // J. Thermal Analysis and Calorimetry. 2015. V. 119. № 1. P. 123–130.
Chang Min Chun, Narasimha-Rao V. Bangaru, Neeraj Thirumalai et al. // Int. J. Appl. Ceram. Technol. 2008. V. 5 [6]. P. 597–609.
Murthy T.S.R.Ch., Sonber J.K., Subramanian C. et al. // Int. J. Refractory Metals & Hard Materials. 2009. V. 27. P. 976–984.
Серебрякова Т.И., Неронов В.А., Пешев П.Д. Высокотемпературные бориды. М.: Металлургия, 1991. С. 368.
Derry D.J., Lees D.G., Calvert J.M. // J. Physics and Chemistry of Solids. 1981. V. 42. № 1. P. 57–64.
Дополнительные материалы отсутствуют.
Инструменты
Физикохимия поверхности и защита материалов