Физикохимия поверхности и защита материалов, 2020, T. 56, № 5, стр. 523-529
Легированный лантаном(III) наноструктурированный анодный материал на основе Li4Ti5O12 для литий-ионных источников тока
В. И. Иваненко 1, *, М. В. Маслова 1, Г. Б. Куншина 1, С. В. Владимирова 1, Д. В. Агафонов 2, **
1 Институт химии и технологии редких элементов и минерального сырья им. И.В. Тананаева – обособленное подразделение Федерального государственного учреждения науки Федерального исследовательского центра “Кольский научный центр Российской академии наук” (ИХТРЭМС КНЦ РАН)
184209 Мурманская область, Апатиты, Академгородок, 26а, Россия
2 Санкт-Петербургский государственный технологический институт (технический университет)
190013 С.-Петербург, Московский пр., 26, Россия
* E-mail: ivanenko@chemy.kolasc.net.ru
** E-mail: phti@lti-gti.ru
Поступила в редакцию 21.06.2018
После доработки 17.10.2018
Принята к публикации 24.10.2018
Аннотация
Изучен процесс кристаллизации порошков титаната лития состава Li4Ti5O12 при легировании катионами лантана(III). Введение до 4 мас. % La(III) не меняет кристаллическую структуру материала и увеличивает дисперсность порошка, что может быть обусловлено образованием структурных дефектов, которые создают микронапряжения и не позволяют формировать относительно крупные кристаллиты. Увеличение содержания введенных в состав материала катионов лантана(III) позволяет получить композитный материал на основе титаната лития Li4Ti5O12 и твердого электролита Li0.5La0.5TiO3. Уменьшение размеров частиц порошков при получении модифицированных кристаллических порошков титаната лития состава Li4Ti5O12 легированием катионами лантана(III) и формирование композитов, содержащих твердый электролит, обеспечивает повышение литий-ионной проводимости. Полученные материалы характеризуются высокими и стабильными значениями емкости макета аккумулятора при циклировании в режиме “заряд–разряд”.
ВВЕДЕНИЕ
В ряду различных электрохимических источников энергии литий-ионные аккумуляторы характеризуются наиболее высокой плотностью энергии и представляют особый интерес [1, 2]. Именно разработка этих аккумуляторов обеспечила бурное развитие современных средств связи, компьютерной техники, широкого круга оборудования гражданского и специального назначения. Однако развитие современной техники требует создания автономных источников энергии с повышенными рабочими параметрами. Разрабатываемые литий-ионные аккумуляторы наряду с достоинствами по ряду параметров не в полной мере соответствуют современным требованиям, поскольку существующие промышленные технологии анодных и катодных материалов не обеспечивают необходимое количество рабочих циклов, взрыво- и пожаробезопасность источников энергии и другие, требуемые для практического использования характеристики.
Среди анодных материалов для литий-ионных химических источников тока одним из наиболее перспективных является титанат лития состава Li4Ti5O12 со структурой шпинели [1–6]. К преимуществам использования такого материала относят отсутствие объемных изменений в структуре при интеркаляции и деинтеркаляции лития в процессе эксплуатации аккумуляторных батарей, обеспечение их взрыво- и пожаробезопасности, а также возможность заряда при низких (“минусовых”) температурах. Главное преимущество титаната лития перед другими материалами отрицательного электрода состоит в том, что в процессе заряда или разряда титанатных электродов происходит фазовое превращение практически без участия фаз переменного состава, что обеспечивает постоянство потенциала по мере циклирования. Рабочий потенциал электродов с титанатом лития примерно на 1.5 В положительнее потенциала литиевого электрода, поэтому при заряде аккумуляторов с такими электродами их потенциал не смещается отрицательнее +1.0 В. Именно это качество электродов на основе титаната лития исключает вывод из строя аккумуляторов из-за осаждения металлического лития с образованием дендритов и восстановления электролита, обусловливает возможность эксплуатации литий-ионных аккумуляторов с анодом на основе титаната лития в форсированных режимах.
Вместе с тем, основным недостатком титаната лития состава Li4Ti5O12, как и других используемых в литий-ионных аккумуляторах электродных материалов, является низкая электронная и ионная проводимость [4–8]. Так, полученные в работах [7, 8] значения проводимости Li4Ti5O12 составляют 1.3 × 10–7 и 5.7 × 10–7 См см–1. Низкие значения проводимости являются причиной, обусловливающей недостаточную и нестабильную емкость аккумулятора и, как следствие, неудовлетворительную циклируемость при интеркаляции-деинтеркаляции ионов лития в режиме “заряд–разряд”.
Улучшение этих показателей может быть достигнуто путем разработки методов синтеза, обеспечивающих получение необходимых материалов в виде высокодисперсных порошков, а также разработки методов получения твердых растворов, допирования гетеровалентными компонентами и создания композитов электродный материал – твердый электролит. Уменьшение размеров частиц при получении материалов в виде порошков заданных узких гранулометрических классов позволит сократить диффузионное расстояния для литий-ионного транспорта и увеличить площадь контакта для переноса электронов между частицами. Получение твердых растворов или легирование гетеровалентными ионами будет способствовать повышению дефектности структуры а, следовательно, и катионной проводимости. Такие подходы к синтезу позволят устранить анизотропию свойств материала, улучшить его электрохимические характеристики.
Вместе с тем, исследования влияния гетеровалентного допирования титаната лития пока не позволяют дать какие-нибудь определенные рекомендации по выбору допанта и замены чистого титаната лития на модифицированный материал. Эта проблема еще далека от своего окончательного решения и требует накопления обширного экспериментального материала.
Для получения ультрадисперсных порошков на основе титаната лития состава Li4Ti5O12 перспективен синтез в жидких средах, обеспечивающий высокую степень гомогенизации компонентов в системе. Золь-гель синтез сложных оксидов титана(IV) предполагает гидролиз солей с образованием оксогидроксокомплексов состава TiО2 –x(ОН)2x · nН2О, взаимодействие которых с катионами металлов должно приводить к получению гидратированных соединений с необходимым соотношением содержания в них металлов. Однако, при протекании реакций оляции-оксоляции, характерных для оксогидроксосоединений титана(IV), число протонов гидроксильных групп, замещаемых катионами металлов, уменьшается, что влечет за собой нарушение стехиометрии синтезируемых целевых соединений и появление примесных фаз.
Для предотвращения процессов оляции-оксоляции и сохранения ионообменных центров в синтезе сложных оксидов предложено использовать в качестве прекурсоров высокогидатированные соединения состава TiO1 –x(ONH4)2 + 2x ⋅ aq с молярным отношением ${\text{NH}}_{4}^{ + }$ : Ti(IV), не меньшим, чем отношение катионов щелочного металла и титана в целевом продукте, то есть при синтезе Li4Ti5O12 должно быть отношение ${\text{NH}}_{4}^{ + }$ : : Ti(IV) ≥ 4 : 5) [9]. Такой гидратированный титанаммониевый прекурсор может быть получен, в частности, гидролизом аммоний титанил сульфата состава (NH4)2TiO(SO4)2 · H2O, являющегося продуктом переработки титанового сырья. Замещение в нем катионов аммония на катионы лития обеспечивает заданное соотношение металлов, а термическая обработка позволяет удалить аммиак и получить целевой продукт без посторонних катионных примесей.
Целью настоящей работы явилось изучение влияния легирования катионами лантана(III) порошков титаната лития состава Li4Ti5O12 на их дисперсность, фазовый состав и морфологию, оценка электрохимических свойств и перспективности использования синтезированных порошков в качестве анодного материала литий-ионных аккумуляторов. Выбор в качестве допанта лантана(III) обусловлен возможностью создания, как дефектной структуры материала, так и композита с равномерно распределенным твердым электролитом – тройным оксидом состава Li3xLa2/3 –xTiO3 со структурой перовскита, обладающим высокой литий-ионной проводимостью [10–17].
ЭКСПЕРИМЕНТАЛЬНАЯ ЧАСТЬ
В качестве исходных веществ для синтеза порошков на основе Li4Ti5O12 использовали: (NH4)2TiO(SO4)2 ⋅ H2O, NH4OH, LiOH, LiNO3 ⋅ · 3H2O ч. д. а, La(NO3)3 ⋅ 9H2O х. ч.
Титанаммониевый прекурсор синтезировали гидролизом при введении раствора (NH4)2TiO(SO4)2 · · H2O в концентрированный раствор аммиака. Отличительной особенностью исходных титансодержащих растворов является присутствие ${\text{NH}}_{4}^{ + }$-ионов и низкое концентрационное отношение H2SO4 к TiO2, что значительно сокращает расход реагенов на получение целевого продукта. Полученный после гидролиза осадок отмывали от сульфат-ионов раствором 3%-ного аммиака. Изучение процесса замещения катионов аммония на катионы лития проводили в интервале температур 20–95°С. С этой целью твердую фазу гидратированного титанаммониевого прекурсора отмывали от избытка аммиака репульпированием в воде до pH 8–8.5 при Ж : Т = 6–20, а затем обрабатывали раствором гидроксида и нитата лития, варьируя отношение Li : Ti(IV) от 0.8 до 1.04 моль/моль, что составляло 100–130% от стехиометрии целевого продукта. Время гидрохимической обработки варьировали от 0.5 до 4 ч. Полученный таким образом замещнный литием прекурсор отделяли фильтрованием с последующей промывкой осадка на фильтре от маточного раствора электролита.
Дипирование катионами лантана(III) синтезируемого материала осуществляли введением в суспензию раствора нитрата лантана при контролируемых значениях pH. Кристаллизацию синтезируемых порошков проводили термообработкой.
Анализ содержания титана в растворе проводили фотоколориметрически с пероксидом водорода. При определении состава твердых фаз и растворов в работе также использовали атомно-адсорбционный спектрофотометр AAS 300 Perkin-Elmer, массспектрометрометрическую систему с индуктивно-связанной плазмой (ИСП-МС) с динамической реакционной системой “ELAN 9000 DRC-e” фирмы PerkinElmer (США) и плазменный эмиссионный спектрометр ICPS-9000 фирмы Shimadzu (Япония).
Содержание воды, гидроксо-групп в твердой фазе определяли сопоставлением результатов химического, дифференциально-термического и термогравиметрического анализов.
При измерении pH водных растворов и суспензий, содержащих синтезированные соединения, в качестве равновесных значений принимались стационарные во времени значения рН, полученные с использованием иономера И-130.2М.1 с точностью ±0.02. Индикаторным электродом служил селективный по отношению к ионам водорода электрод марки ЭСЛ-43-07 с координатами изопотенциальной точки рНи 7 ± 0.3 рН, а в качестве вспомогательного был выбран хлорсеребрянный электрод (Ag|AgCl, нас. р-р KCl) марки ЭВЛ-1М3, потенциал которого при 20°С составляет 202 ± 2 мВ относительно нормального водородного электрода.
Для проведения измерений дифференциально-термического (ДТА) и термогравиметрического (ТГА) анализов использовали синхронный термический анализатор NETZSCH STA 409 PC/PG Luxx в интервале 25–1000°C.
Исследования фазового состава синтезированных соединений проводили на дифрактометре ДРОН-2 и ДРОН-3 с CuKα-излучением и графитовым монохроматором, в большинстве определений скорость движения счетчика составляла 2 град мин–1. Для идентификации фаз использовали банк данных JCPDS.
При изучении морфологии и гранулометрического состава частиц синтезируемых порошковых материалов использовали сканирующий электронный микроскоп SEM LEO-420. Особенности изучения объектов заключались в получении изображения за счет эмиссии вторичных электронов.
Контроль размера частиц и величины удельной поверхности твердых фаз проводили методом термической десорбции азота на электронном измерителе удельной поверхности “FlowSorb II 2300” фирмы Micrometritics (США). Средний размер частиц по удельной поверхности порошкообразных образцов вычисляли по формуле d = K/Sρ, где d – средний диаметр частиц; K – коэффициент формы частиц, равный 6 для сферических и кубических частиц; S – величина удельной поверхности; ρ – плотность вещества.
Размер областей когерентного рассеяния (ОКР) DOKP определяли по формуле Селякова–Шерера: DOKP = $\frac{{0.94\lambda }}{{{{\beta }_{{hkl}}}\cos \theta }}$, где λ – длина волны используемого излучения (λСu = 1.54178 Å); βhkl – величина физического уширения соответствующего дифракционного максимума, θ – угол дифракции. Основные линии рентгеновских спектров были аппроксимированы функцией Гаусса. Величину физического уширения рассчитывали по формуле: βhkl = β – s, где β – полная ширина рентгеновского пика на его полувысоте, s – инструментальное уширение (0.09 ± 0.01). В качестве эталонного образца для определения инструментального уширения использовали металлический Zn.
Измерения проводимости (σ) синтезированных образцов выполняли прибором “Измеритель L, C, R цифровой Е7-12” на фиксированной частоте 1 МГц в ячейке с графитовыми электродами на нескольких таблетах разной высоты, а также методом спектроскопии электрохимического импеданса [18]. Спектры электрохимического импеданса синтезированных материалов регистрировали импедансметром Elins Z-2000 производства ООО “Элинс” с амплитудой переменного сигнала 50–100 мВ в диапазоне частот 102–2 × 106 Гц. Образцы для измерения готовили по керамической технологии в виде прессованных цилиндрических таблет (d = 10–12 мм, h = 2–3 мм), на торцы которых после спекания при температуре 800–900°С наносили электроды натиранием мелкодисперсного графитового порошка. Относительная плотность таблет, т.е. отношение измеренной методом Архимеда плотности к теоретической, составляла 85–88%.
Для термообработки твердых фаз использовали сушильный шкаф 2В-151 и муфельные печи типа СНОЛ-1,6.2,5.1/11-М1 и МП-2УМ.
РЕЗУЛЬТАТЫ И ИХ ОБСУЖДЕНИЕ
Исследования показали, что высокая степень гидратации синтезированного титанаммониевого прекурсора обеспечивает, согласно [9], при температуре 90–95°C и отношении Li : Ti(IV) = = 1–1.04 моль/моль в течение 0.5–1 часа замещение катионов аммония на катионы лития с получением гидратированного сложного оксида титана и лития, при термообработке которого образуются кристаллические порошки с отношением Li : Ti, равным 4 : 5. Так, согласно химическому анализу, отожженный при 800°С продукт содержал 13.5 мас. % Li2О и 86.3 мас. % TiO2, что соответствует химическому составу Li4Ti5O12. Рентгенофазовый анализ подтверждает монофазность получаемых порошов и указывает на структуру, соответствующую кубической шпинели.
При изучении продуктов синтеза установлено, что твердая фаза, образующаяся в водной среде в результате катионообменного взаимодействия при 90–95°C, рентгеноаморфна. Ее термическое разложение носит ступенчатый характер и сопровождается несколькими тепловыми эффектами. При термолизе в интервале температур 50–300°C наблюдается эндотермический эффект, отвечающий удалению координационной воды. В этой области температур происходит практически полная дегидратация. Экзотермический эффект в интервале температур 320–350°C обусловлен кристаллизацией целевого продукта. Незначительная потеря массы в этом диапазоне температуры может быть связана с разрушением остаточных количеств катионов аммония, выделением аммиака и конституционной воды, образующейся при разрушении гидроксо-групп. В этой области температур завершается кристаллизация титаната лития. Термическая обработка гидратированного прекурсора позволяет, удалив воду и аммиак, получить монофазные порошки титаната лития заданного состава без катионных примесей.
Процессы термолиза хорошо коррелируют с картиной формирования рефлексов на дифрактограммах образцов при повышении температуры термообработки порошков (рис. 1), из которой следует, что увеличение температуры термообработки порошков приводит к увеличению их кристалличности. При этом наблюдается постепенное проявление всех дифракционных линий, отвечающих кристаллической структуре синтезируемого соединения, и отсутствие посторонних рефлексов.
Рис. 1.
Дифрактограммы прекурсора Li4Ti5O12 после трмообработки: 1 – 200°С (10 ч); 2 – 250°С (1 ч); 3 – 300°С (0.5 ч); 4 – 350°С (без выдержки); 5 – 400°С (без выдержки); 6 – 500°С (без выдержки).
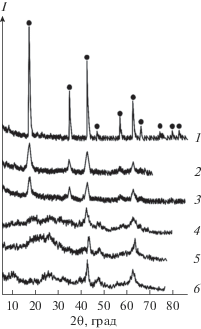
Отсутствие посторонних рефлексов на дифрактограмме, связанных с кристаллизацией индивидуальных оксидов, подтверждает, что при использовании свежеосажденного гидратированного титанаммониевого прекурсора происходит химическое взаимодействие между компонентами в суспензии с образованием гидратированного аморфного продукта, содержащего заданное соотношение Li : Ti.
Разработанный подход по сравнению с традиционным керамическим способом позволяют значительно (на 300–600°C) снизить температуру и время синтеза Li4Ti5O12, увеличить гомогенизацию компонентов в целевом продукте. Это объясняется высокой химической активностью исходных прекурсоров, а также низкой температурой распада переходного комплекса с последующим образованием титаната лития.
Увеличение концентрации катионов лития в суспензии на стадии гидрохимической обработки титанамониевого прекурсора приводит к уменьшению частиц синтезируемых порошков, увеличение времени и температуры улучшает их кристалличность.
Повышение температуры и времени термообработки при дегидратации и кристаллизации прекурсора приводит к укрупнению частиц. Так, при температуре 320–350°C, соответствующей экзотермическому эффекту кристаллизаци Li4Ti5O12, получаемый порошок характеризуется удельной поверхностью, равной 88 м2 г–1, что соответствует среднему размеру частиц 20 нм. Прокаливание при 800°C в течение 0.5 часа приводит к формироваию порошка состава Li4Ti5O12 с удельной поверхностью 17–19 м2 г–1, что соответствует среднему размеру частиц 80–90 нм. Двухчасовая прокалка при той же температуре приводит к образованию порошка с удельной поверхностью 3.2–3.4 м2 г–1 и размером частиц 500–550 нм, а при 4-х часовой прокалке при 800°C удельная поверхность порошка уменьшается до 2.5–2.7 м2 г–1 (600–680 нм). Таким образом, показана возможность управления дисперсностью синтезируемых порошков.
На рис. 2 представлены графические зависимости среднего размера частиц (d, нм) порошка титаната лития состава Li4Ti5O12 от температуры и времени термообработки прекурсора. Повышение температуры и времени термообработки прекурсора существенно влияют на морфологию образующихся порошков, увеличивая размер их зерен (рис. 3).
Рис. 2.
Влияние температуры и продолжительности термообработки на дисперсность порошка Li4Ti5O12: 1 – 2 ч; 2 – 8 ч; 3 – 2 ч (порошок, легированный 0.5 мас. % лантана).
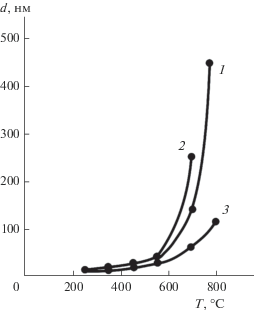
Рис. 3.
SEM-изображение порошка Li4Ti5O12, полученного при выдержке 2 ч и различной температуре. t, °C: (а) 250, (б) 500, (в) 700.
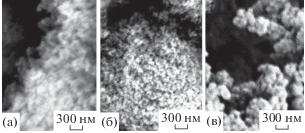
Поскольку разработанные подходы позволяют на стадии катионного замещения в водной суспензии одновременно с процессом формирования литий-титанового прекурсора проводить легирование твердой фазы различными компонентами, в настоящей работе проведено легирование порошка титаната лития катионами лантана(III). Введение до 4 мас. % La(III) не меняет кристаллическую структуру материала, однако при этом увеличивается дисперсность порошка. Легированные лантаном(III) порошки менее восприимчивы к условиям термической обработки. Введение легирующего компонента стабилизирует размер зерен порошков, который незначительно изменяется с повышением температуры прокалки (рис. 2). В результате синтеза образуются однородные по форме и по размеру частицы. Синтезируемые порошки имеют узкие гранулометрические классы крупности частиц. Увеличение содержания введенных в состав материала катионов лантана(III) позволяет получить композитный материал на основе титаната лития Li4Ti5O12 с равномерным распределением твердого электролита Li0.5La0.5TiO3 в анодном материале (рис. 4).
Рис. 4.
Дифрактограмма композитного порошка титаната лития и твердого электролита. Температура обработки 800°С в течение 2 ч.

С целью повышения дисперсности порошков изучены условия формирования титаната лития состава Li4Ti5O12 в разряженной атмосфере (при остаточном давлении 1–2 × 10–2 мм рт. ст.). Показано, что в сравнении с термолизом при атмосферном давлении термолиз гидратированного прекурсора в разряженной атмосфере позволяет получить более дисперсную кристаллическую фазу Li4Ti5O12 при более низких температурах. Так, удельная поверхность порошков (Sуд), полученных после 4-х часовой термообработки при 350, 450, 550 и 650°С, составляет 112, 83, 40 и 17 м2 г–1, что соответствует среднему размеру частиц, равному 15, 21, 43 и 103 нм.
Исследования показали, что увеличение диперсности и легирование лантаном(III) позволяют повысить проводимость керамики на основе Li4Ti5O12 с 1.7 × 10–7 до 1 × 10–5 См см–1.
На рис. 5 предсталены годографы импеданса (комплексной перемнной сопротивления переменному току) Li4Ti5O12 (кривая 1) и композита Li4Ti5O12, содержащего твердый электролит Li0.5La0.5TiO3 (кривая 2). В соответствии со спектром электрохимического импеданса в композите повышается проводимость в сравнении с проводимостью Li4Ti5O12. Повышение ионной проводимости и диффузии ионов лития в модифицированном образце обусловливает улучшенные зарядно-разрядные характеристики и стабильность при циклировании композита. Причина может состоять в том, что некоторые ионы лантана(III) встраиваются в кристаллическую решетку титаната лития и расширенные каналы уменьшают препятствия для диффузии Li+.
Рис. 5.
Годографы импеданса (Ом) при 25оC титаната лития состава Li4Ti5O12 (1) и композита Li4Ti5O12 и Li0.5La0.5TiO3 (2).
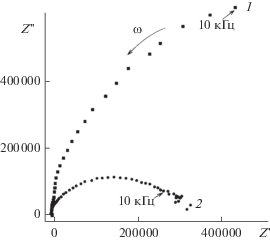
Апробация образцов порошков литиевой шпинели в качестве анодного материала показала хорошую циклируемость (рис. 6, 7): емкость макетов оказалась близкой к теоретической и практически не снижалась при многократном циклировании в режиме “заряд–разряд”.
ЗАКЛЮЧЕНИЕ
Проведенные исследования показали, что допирование гетеровалентными катионами лантана(III) гидратированных прекурсоров на стадии их получения в водных средах и дальнейшая температурная обработка приводят к увеличению дисперсности синтезируемого порошкового материала. При этом, порошки становятся менее восприимчивыми к условиям термической обработки. Такая зависимость может быть связана с образованием структурных дефектов, которые создают микронапряжения и не позволяют формировать относительно крупные кристаллиты, а также со специфической адсорбцией катионов допанта и локализацией его преимущественно на межзеренных поверхностях, что обусловливает образование избыточных дефектов и в приповерхностной области формирующихся частиц порошка.
Уменьшение размеров частиц порошков при получении модифицированных кристаллических порошков титаната лития состава Li4Ti5O12 легированием катионами лантана(III) и формирование композитов, содержащих твердый электролит обеспечивает повышение литий-ионной проводимости на 2–3 порядка.
Уменьшение размеров частиц сокращает диффузионное расстояние для ионного транспорта и увеличивает площадь контакта для переноса заряда между частицами, что позволяет устранить анизотропию поверхностных свойств материала.
Генерация дефектов способствует образованию ионных вакансий, приводит к перераспределению заряда в решетке и повышению ионной проводимости при циклировании в процессе интеркаляции-деинтеркаляции катионов щелочного металла.
Образование в межзеренном пространстве твердого электролита со структурой типа перовскита ускоряет доставку ионов щелочного металла к грани, по которой происходит его внедрение в решетку электродного материала. Все это приводит к повышению и стабилизации емкости, предотвращает деградацию материала при циклировании.
Полученные материалы характеризуются высокими и стабильными значениями емкости макета аккумулятора при циклировании в режиме “заряд–разряд”.
Исследования выполнены при финансовой поддержке Российского научного фонда (РНФ) в рамках научного проекта № 17-19-01522.
Список литературы
Косова Н.В., Девяткина Е.Т. // Электрохимия. 2012. Т. 48. № 3. С. 351–361 (Kosova N.V., Devyatkina E.T. // Russ. J. Electrochem. 2012. V. 48. № 3. P. 320–329).
Стенина И.А., Кулова Т.Л., Скундин А.М. и др. // Журн. неорган. химии. 2015. Т. 60. № 11. С. 1506–1510 (Stenina I.A., Kulova T.L., Skundin A.M. et al. // Russ. J. Inorg. Chem. 2015. V. 60. № 11. P. 1380–1383).
Kataoka K., Takahashi Y., Kijima N. et al. // J. Phys. and Chem. Solids. 2008. V. 69. P. 1454–1456.
Сафронов Д.В., Новикова С.А., Скундин А.М. и др. // Неорганические материалы. 2012. Т. 48. № 1. С. 63–68.
Сибиряков Р.В., Кудрявцев Е.Н., Агафонов Д.В. и др. // Фундаментальные исследования. 2012. № 9. С. 707–713.
Леонидов И.А., Леонидова О.Н., Переляева Л.А. и др. // Физика твердого тела. 2003. Т. 45. № 11. С. 2079–2084.
Wilkening M., Amade R., Iwaniak W. et al. // Phys. Chem. Chem. Phys. 2007. V. 9. P. 1239–1246.
Wang Y., Zhou A., Dai X. et al. // J. Power Sources. 2014. V. 266. P. 114–120.
Иваненко В.И., Локшин Э.П., Владимирова С.В. и др. / Пат. 2542273 РФ // Б. И. 2015. № 5.
Куншина Г.Б., Бочарова И.В., Иваненко В.И. // Журн. прикладной химии. 2016. Т. 89. № 6. С. 749–755.
Куншина Г.Б., Ефремов В.В., Локшин Э.П. // Электрохимия. 2015. Т. 51. № 6. С. 630–635.
Белоус А.Г., Клобасов Г.Я., Болдырев Е.И., Коваленко Л.Л. // Электрохимия. 2015. Т. 51. № 12. С. 1303–1308.
Фортальнова У.Ф., Гавриленко О.Н., Белоус А.Г., Политова Е.Д. // Российский химический журнал. 2008. Т. 52. № 5. С. 43–51.
Liao C.-L., Wen C.-H., Fung K.-Z. // J. Alloys a. Compounds. 2007. V. 432. P. L22–L25.
Vidal K., Ortega-San-Martin L., Larranaga A. et. al. // Ceram. Int. 2014. V. P. 8761–8768.
Куншина Г.Б., Бочарова И.В., Локшин Э.П. // Неорг. материалы. 2015. Т. 51. № 4. С. 422–427 (Kunshina G.B., Bocharova I.V., Lokshin E.P. // Inorg. Mater. 2015. V. 51. № 4. P. 369–374).
Yi T.-F., Yang S.-Y., Tao M. et al. // Electrochem. Acta. 2014. 134. P. 377–383.
Иванов-Шиц Ф.К., Мурин И.В. Ионика твердого тела. Т. 1. СПбГУ. 2000. 616 с.
Дополнительные материалы отсутствуют.
Инструменты
Физикохимия поверхности и защита материалов